Quick Enquiry Form
Categories
- Agile and Scrum (216)
- BigData (32)
- Business Analysis (93)
- Cirtix Client Administration (53)
- Cisco (63)
- Cloud Technology (91)
- Cyber Security (54)
- Data Science and Business Intelligence (48)
- Developement Courses (53)
- DevOps (15)
- Digital Marketing (56)
- Emerging Technology (190)
- IT Service Management (76)
- Microsoft (54)
- Other (395)
- Project Management (491)
- Quality Management (139)
- salesforce (67)
Latest posts
Introduction to SAP Sales and..
Before You Take the PMP..
5 High Demand Cybersecurity Careers..
Free Resources
Subscribe to Newsletter
Quality Control The Key to Faultless Products
Nowadays, we simply take things for granted and expect them to work properly without even thinking about it. However, back in the early 1900s, it was not always possible and certain.
With time, professionals devised testing and product development techniques. This enabled the firms to adopt the best practices and ensure quality at scale.
What is Quality Control (QC)?
Quality can be different for every person. In business, Quality Control (QC) refers to the process of inspecting and testing products or services to make sure that they are of a specific quality. This is done in an effort to allow companies to maintain and enhance quality over time.
The primary purpose of QC is the detection and elimination of errors before products reach consumers. It does this through making detailed examinations of products or services at multiple levels of manufacturing. QC strives at preventing problems from occurring by improving the method of making things or offering.
Quality Control has two primary objectives: (1) to make the products as identical as possible and (2) to keep errors and differences between them to a minimum.

Key Components of Quality Control
Quality Control (QC) has many important elements, which include:
• Inspection: Quality testing of products, materials, or services to determine defects or anything that does not meet standard.
• Testing: Conducting tests to determine how well a product or service operates.
• Statistical Process Control (SPC): Utilizing figures and statistics to track production and maintain everything within quality limits.
• Records and Documents: Keeping accurate records of notes regarding inspections, tests, and actions taken for solving problems.
• Corrective Action: Correcting quality issues and making sure they do not occur again.
• Training and Education: Training the employees in the abilities needed for maintaining quality.
• Continuous Improvement: Ongoing efforts to enhance products and services through analyzing data and feedback.
QC is closely related to Quality Assurance (QA). QC identifies and corrects errors, whereas QA seeks to prevent errors from being made at all. QC and QA, in combination, enable firms to supply consistent products and services that meet customers' requirements and adhere to industry requirements and also in minitab .
Quality Check Process
Quality checks are carried out at various levels of a business or manufacturing process. Workers check raw materials, in-process, and finished goods to detect defects early. Detecting defects early eliminates bigger problems in the future.
For non-manufacturing organizations, quality testing could involve surveys, reviews, inspections, and audits. Whatever the industry, the objective remains the same—to ensure the end product or service is safe, as per customer specifications, and adheres to industry standards.

Industry trends in QC
Quality Control is crucial in most industries, but how it is carried out differs by industry:
• Production: Examining raw materials and finished goods to make sure they are identical and free from any defects.
• Food Industry: Checking food for safety, ensuring that there are no toxic compounds, and compliance with health rules.
• Pharmaceuticals: Ensuring that drugs are pure, potent, and safe for consumption.
• Software: Testing software to find and fix bugs before release.
No matter what the business, quality control makes clients happier, employees work more effectively, and generates trust.
Types of Quality Control
Since "quality" is variable, quality control practices are variable by industry. They range from strict scientific testing in food and medicine to overall experience and feedback in others, such as education or coaching.
The following are some general QC techniques:
• Control Charts: Charts indicating the fluctuation of a process with time to verify whether it remains constant.
• Process Control: Employing technology and feedback to track and improve production.
• Acceptance Sampling: Testing a small number of products to see if an entire group meets quality standards.
• Process Protocol: A methodical process that examines each step of production in order to streamline efficiency.
Some businesses employ in-house quality control staff to inspect products, whereas others hire third-party experts to conduct the tests. Within food processing and other businesses, firms will test products in-house and then validate the results with third-party test labs.
Why do we require quality control? What are the advantages?
Quality Control (QC) is important because it serves companies and consumers in various ways. The following are some of the important benefits:
• Customer Satisfaction: QC guarantees the products and services meet or exceed customers' expectations, ensuring they are satisfied and repeat customers.
• Defect Prevention: By detecting and fixing defects in the early stages, QC reduces the likelihood of expensive recalls or repairs.
• Cost Reduction: Good quality control lowers waste and cuts production costs, which helps businesses work better.
• Compliance and Regulations: QC ensures products follow industry rules and avoid legal trouble.
• Brand Reputation: Quality products enable companies to establish a reputable and reliable brand.
• Increased Efficiency: QC makes work smoother and faster, allowing companies to enhance their processes.
• Risk Mitigation: Ongoing tests and inspections prevent problems from developing.
• Ongoing Improvement: QC enables companies to continue improving products and services.
• Competitiveness: Quality products can enable companies to succeed in the global market.
• Customer Loyalty: Satisfied customers are loyal and recommend products to others.
Overall, QC ensures companies maintain good standards, prevent problems, and are competitive. It ensures customers receive reliable and high-quality products.
Quality Control Job Responsibilities and Tasks
Quality Control has many roles. It is distinct from Quality Assurance (QA)—QA tries to avoid mistakes from happening, while QC inspects products to detect and fix mistakes.

QC professionals utilize information and studies to inspect products against a norm. They also recommend alterations that must be made to improve quality. Unlike QA, QC targets the final product rather than the overall process.
A QC professional is crucial at the time of product design because they make sure that the company's product meets market standards. They also transmit the things they discover to the managers and key stakeholders in the company.
Quality Control and Quality Assurance
People tend to interchange Quality Control (QC) and Quality Assurance (QA), but they are not synonymous:
• QC deals with verifying whether a product is of quality.
• QA emphasizes process enhancement to avoid defects.
Over time, certain quality professionals transition from QA to QC as they progress in their career. QA teams make sure that products meet safety and quality standards, while QC is only a subset of the overall QA process.
Jobs in Quality Control
If you enjoy problem-solving and working with people, a career in Quality Control may be just right for you. Various industries require varying skill sets, but here are some of the most typical ones:
• A high school diploma for initial positions.
• An undergraduate degree (this varies with the industry).
• Experience in the field.
• Licenses or certificates, if applicable.
Important Skills for Quality Control Experts
• attention to detail
• Math and mechanical skills
• Technical knowledge
• Working under Pressure
Career Path in Quality Control
The career progression in QC is different in each industry, but generally, they start as quality assurance or QC associates. They can move to senior positions and become team leaders at a later point in time.
Some businesses require additional training, such as Six Sigma certification, to enable workers to be more proficient at their tasks. Certifications like Certified Quality Inspector can also assist individuals in establishing their careers.
Quality Control Salaries
Salaries of QC professionals also vary depending on experience and industry. With greater expertise and as managers, their salary increases. Based on the Bureau of Labor Statistics, average salaries are:
• Scientific and technology services: $46,280
• ufacturing: $40,020
• Wholesale trade: $37,800
• Office and support services: $30,070
What Does Quality Control Mean?
Quality Control is the way businesses verify and improve product quality. It is the process of comparing products to standards, testing, and improving manufacturing processes to minimize errors.
Examples of Quality Control
Following are three food industry examples of quality control:
1. Inspecting the quality of ingredients.
2. Ensuring that suppliers follow safety rules.
3. Keeping factories clean and hygienic.
How to obtain Quality Control certification?
We are an Education Technology company providing certification training courses to accelerate careers of working professionals worldwide. We impart training through instructor-led classroom workshops, instructor-led live virtual training sessions, and self-paced e-learning courses.
We have successfully conducted training sessions in 108 countries across the globe and enabled thousands of working professionals to enhance the scope of their careers.
Our enterprise training portfolio includes in-demand and globally recognized certification training courses in Project Management, Quality Management, Business Analysis, IT Service Management, Agile and Scrum, Cyber Security, Data Science, and Emerging Technologies. Download our Enterprise Training Catalog from https://www.icertglobal.com/corporate-training-for-enterprises.php and https://www.icertglobal.com/index.php
Popular Courses include:
-
Project Management: PMP, CAPM ,PMI RMP
-
Quality Management: Six Sigma Black Belt ,Lean Six Sigma Green Belt, Lean Management, Minitab,CMMI
-
Business Analysis: CBAP, CCBA, ECBA
-
Agile Training: PMI-ACP , CSM , CSPO
-
Scrum Training: CSM
-
DevOps
-
Program Management: PgMP
-
Cloud Technology: Exin Cloud Computing
-
Citrix Client Adminisration: Citrix Cloud Administration
The 10 top-paying certifications to target in 2025 are:
Conclusion:
Quality Control (QC) helps businesses make sure their products are good and safe to use. It checks for mistakes, saves money, and keeps customers happy. QC is important in many industries like food, medicine, and technology. When companies focus on quality, they build trust and make better products.
If you like solving problems and paying attention to details, a job in QC could be a great choice. With the right training, you can help businesses improve their products and make customers happy!
FAQs
1. What does Quality Control (QC) do?
Quality Control is the inspection and testing of goods or services to make sure they are up to some standard. Quality Control assists organizations in reducing errors and improving quality.
2. What are the four levels of Quality Control?
The four primary forms of Quality Control are:
• Process Control: Products are made properly.
• Control Charts: Monitoring change over time within a process.
• Acceptance Sampling: Sampling a few items to determine whether a whole batch is acceptable.
• Product Quality Control: Ensuring that final products meet quality standards.
3. Why do we need Quality Control?
Quality Control assists companies in maintaining a good image, gaining customer trust, and making their products reliable. It also saves money, makes things function better, and enhances customer satisfaction.
4. Can you give three examples of Quality Control?
An automaker inspects every part of an automobile before it is marketed.
A site examines how fast its pages load and corrects the slow ones.
• A store employs secret shoppers to inspect customer service.
5. What are the four steps of Quality Control?
1. Establish standards of quality and decide what is most critical.
2. Set procedures to achieve those standards.
3. Checking results and areas of improvement identification.
4. Receive comments and revise.
6. How do you control quality?
• Inspection: Quality check at various production stages.
• Statistical Quality Control (SQC): Applying mathematics and probability for controlling and enhancing product quality.
7. What is the difference between QA and QC?
• Quality Assurance (QA): Seeks to prevent errors by improving the process.
• Quality Control (QC): Finds and fixes mistakes by inspecting products.
QA is designed to avoid issues before they arise, while QC addresses issues that have already occurred.
Contact Us For More Information:
Visit : www.icertglobal.com Email : info@icertglobal.com
Read More
Nowadays, we simply take things for granted and expect them to work properly without even thinking about it. However, back in the early 1900s, it was not always possible and certain.
With time, professionals devised testing and product development techniques. This enabled the firms to adopt the best practices and ensure quality at scale.
What is Quality Control (QC)?
Quality can be different for every person. In business, Quality Control (QC) refers to the process of inspecting and testing products or services to make sure that they are of a specific quality. This is done in an effort to allow companies to maintain and enhance quality over time.
The primary purpose of QC is the detection and elimination of errors before products reach consumers. It does this through making detailed examinations of products or services at multiple levels of manufacturing. QC strives at preventing problems from occurring by improving the method of making things or offering.
Quality Control has two primary objectives: (1) to make the products as identical as possible and (2) to keep errors and differences between them to a minimum.
Key Components of Quality Control
Quality Control (QC) has many important elements, which include:
• Inspection: Quality testing of products, materials, or services to determine defects or anything that does not meet standard.
• Testing: Conducting tests to determine how well a product or service operates.
• Statistical Process Control (SPC): Utilizing figures and statistics to track production and maintain everything within quality limits.
• Records and Documents: Keeping accurate records of notes regarding inspections, tests, and actions taken for solving problems.
• Corrective Action: Correcting quality issues and making sure they do not occur again.
• Training and Education: Training the employees in the abilities needed for maintaining quality.
• Continuous Improvement: Ongoing efforts to enhance products and services through analyzing data and feedback.
QC is closely related to Quality Assurance (QA). QC identifies and corrects errors, whereas QA seeks to prevent errors from being made at all. QC and QA, in combination, enable firms to supply consistent products and services that meet customers' requirements and adhere to industry requirements and also in minitab .
Quality Check Process
Quality checks are carried out at various levels of a business or manufacturing process. Workers check raw materials, in-process, and finished goods to detect defects early. Detecting defects early eliminates bigger problems in the future.
For non-manufacturing organizations, quality testing could involve surveys, reviews, inspections, and audits. Whatever the industry, the objective remains the same—to ensure the end product or service is safe, as per customer specifications, and adheres to industry standards.
Industry trends in QC
Quality Control is crucial in most industries, but how it is carried out differs by industry:
• Production: Examining raw materials and finished goods to make sure they are identical and free from any defects.
• Food Industry: Checking food for safety, ensuring that there are no toxic compounds, and compliance with health rules.
• Pharmaceuticals: Ensuring that drugs are pure, potent, and safe for consumption.
• Software: Testing software to find and fix bugs before release.
No matter what the business, quality control makes clients happier, employees work more effectively, and generates trust.
Types of Quality Control
Since "quality" is variable, quality control practices are variable by industry. They range from strict scientific testing in food and medicine to overall experience and feedback in others, such as education or coaching.
The following are some general QC techniques:
• Control Charts: Charts indicating the fluctuation of a process with time to verify whether it remains constant.
• Process Control: Employing technology and feedback to track and improve production.
• Acceptance Sampling: Testing a small number of products to see if an entire group meets quality standards.
• Process Protocol: A methodical process that examines each step of production in order to streamline efficiency.
Some businesses employ in-house quality control staff to inspect products, whereas others hire third-party experts to conduct the tests. Within food processing and other businesses, firms will test products in-house and then validate the results with third-party test labs.
Why do we require quality control? What are the advantages?
Quality Control (QC) is important because it serves companies and consumers in various ways. The following are some of the important benefits:
• Customer Satisfaction: QC guarantees the products and services meet or exceed customers' expectations, ensuring they are satisfied and repeat customers.
• Defect Prevention: By detecting and fixing defects in the early stages, QC reduces the likelihood of expensive recalls or repairs.
• Cost Reduction: Good quality control lowers waste and cuts production costs, which helps businesses work better.
• Compliance and Regulations: QC ensures products follow industry rules and avoid legal trouble.
• Brand Reputation: Quality products enable companies to establish a reputable and reliable brand.
• Increased Efficiency: QC makes work smoother and faster, allowing companies to enhance their processes.
• Risk Mitigation: Ongoing tests and inspections prevent problems from developing.
• Ongoing Improvement: QC enables companies to continue improving products and services.
• Competitiveness: Quality products can enable companies to succeed in the global market.
• Customer Loyalty: Satisfied customers are loyal and recommend products to others.
Overall, QC ensures companies maintain good standards, prevent problems, and are competitive. It ensures customers receive reliable and high-quality products.
Quality Control Job Responsibilities and Tasks
Quality Control has many roles. It is distinct from Quality Assurance (QA)—QA tries to avoid mistakes from happening, while QC inspects products to detect and fix mistakes.
QC professionals utilize information and studies to inspect products against a norm. They also recommend alterations that must be made to improve quality. Unlike QA, QC targets the final product rather than the overall process.
A QC professional is crucial at the time of product design because they make sure that the company's product meets market standards. They also transmit the things they discover to the managers and key stakeholders in the company.
Quality Control and Quality Assurance
People tend to interchange Quality Control (QC) and Quality Assurance (QA), but they are not synonymous:
• QC deals with verifying whether a product is of quality.
• QA emphasizes process enhancement to avoid defects.
Over time, certain quality professionals transition from QA to QC as they progress in their career. QA teams make sure that products meet safety and quality standards, while QC is only a subset of the overall QA process.
Jobs in Quality Control
If you enjoy problem-solving and working with people, a career in Quality Control may be just right for you. Various industries require varying skill sets, but here are some of the most typical ones:
• A high school diploma for initial positions.
• An undergraduate degree (this varies with the industry).
• Experience in the field.
• Licenses or certificates, if applicable.
Important Skills for Quality Control Experts
• attention to detail
• Math and mechanical skills
• Technical knowledge
• Working under Pressure
Career Path in Quality Control
The career progression in QC is different in each industry, but generally, they start as quality assurance or QC associates. They can move to senior positions and become team leaders at a later point in time.
Some businesses require additional training, such as Six Sigma certification, to enable workers to be more proficient at their tasks. Certifications like Certified Quality Inspector can also assist individuals in establishing their careers.
Quality Control Salaries
Salaries of QC professionals also vary depending on experience and industry. With greater expertise and as managers, their salary increases. Based on the Bureau of Labor Statistics, average salaries are:
• Scientific and technology services: $46,280
• ufacturing: $40,020
• Wholesale trade: $37,800
• Office and support services: $30,070
What Does Quality Control Mean?
Quality Control is the way businesses verify and improve product quality. It is the process of comparing products to standards, testing, and improving manufacturing processes to minimize errors.
Examples of Quality Control
Following are three food industry examples of quality control:
1. Inspecting the quality of ingredients.
2. Ensuring that suppliers follow safety rules.
3. Keeping factories clean and hygienic.
How to obtain Quality Control certification?
We are an Education Technology company providing certification training courses to accelerate careers of working professionals worldwide. We impart training through instructor-led classroom workshops, instructor-led live virtual training sessions, and self-paced e-learning courses.
We have successfully conducted training sessions in 108 countries across the globe and enabled thousands of working professionals to enhance the scope of their careers.
Our enterprise training portfolio includes in-demand and globally recognized certification training courses in Project Management, Quality Management, Business Analysis, IT Service Management, Agile and Scrum, Cyber Security, Data Science, and Emerging Technologies. Download our Enterprise Training Catalog from https://www.icertglobal.com/corporate-training-for-enterprises.php and https://www.icertglobal.com/index.php
Popular Courses include:
-
Project Management: PMP, CAPM ,PMI RMP
-
Quality Management: Six Sigma Black Belt ,Lean Six Sigma Green Belt, Lean Management, Minitab,CMMI
-
Business Analysis: CBAP, CCBA, ECBA
-
Agile Training: PMI-ACP , CSM , CSPO
-
Scrum Training: CSM
-
DevOps
-
Program Management: PgMP
-
Cloud Technology: Exin Cloud Computing
-
Citrix Client Adminisration: Citrix Cloud Administration
The 10 top-paying certifications to target in 2025 are:
Conclusion:
Quality Control (QC) helps businesses make sure their products are good and safe to use. It checks for mistakes, saves money, and keeps customers happy. QC is important in many industries like food, medicine, and technology. When companies focus on quality, they build trust and make better products.
If you like solving problems and paying attention to details, a job in QC could be a great choice. With the right training, you can help businesses improve their products and make customers happy!
FAQs
1. What does Quality Control (QC) do?
Quality Control is the inspection and testing of goods or services to make sure they are up to some standard. Quality Control assists organizations in reducing errors and improving quality.
2. What are the four levels of Quality Control?
The four primary forms of Quality Control are:
• Process Control: Products are made properly.
• Control Charts: Monitoring change over time within a process.
• Acceptance Sampling: Sampling a few items to determine whether a whole batch is acceptable.
• Product Quality Control: Ensuring that final products meet quality standards.
3. Why do we need Quality Control?
Quality Control assists companies in maintaining a good image, gaining customer trust, and making their products reliable. It also saves money, makes things function better, and enhances customer satisfaction.
4. Can you give three examples of Quality Control?
An automaker inspects every part of an automobile before it is marketed.
A site examines how fast its pages load and corrects the slow ones.
• A store employs secret shoppers to inspect customer service.
5. What are the four steps of Quality Control?
1. Establish standards of quality and decide what is most critical.
2. Set procedures to achieve those standards.
3. Checking results and areas of improvement identification.
4. Receive comments and revise.
6. How do you control quality?
• Inspection: Quality check at various production stages.
• Statistical Quality Control (SQC): Applying mathematics and probability for controlling and enhancing product quality.
7. What is the difference between QA and QC?
• Quality Assurance (QA): Seeks to prevent errors by improving the process.
• Quality Control (QC): Finds and fixes mistakes by inspecting products.
QA is designed to avoid issues before they arise, while QC addresses issues that have already occurred.
Contact Us For More Information:
Visit : www.icertglobal.com Email : info@icertglobal.com
How Quality Control Assures Excellence
We take it for granted now that products and services should function well. We do not usually wonder how they are produced. However, back in the early 1900s, ensuring that products were reliable was not a simple task. Businesses, with time, found means to inspect and enhance quality. The trend Today, it is easier than ever for businesses to emulate and scale good quality standards.
How Does Quality Control Work?
Quality could be anything. Quality Control (QC) is a system that inspects products or services. It helps ensure that they follow certain standards. QC assists companies in testing, measuring, and enhancing products. The primary function of QC is to locate and correct faults prior to reaching the customers. This includes inspecting products at different production phases. Also, it's about the improvement to prevent repeating the same mistake.
Two key objectives of QC:
1. Ensuring products are as uniform as possible.
2. Minimizing errors and defects.
Key Elements of Quality Control :
Some of the most important elements of QC are:
- Inspection – Examining products or services to detect errors or flaws.
- Testing – Conducting tests to determine if products function properly.
- Statistical Process Control (SPC) – Employing numbers and data to monitor and regulate production.
- Record Keeping – Taking notes about inspections and repairs to monitor quality over time.
- Corrective Action – Repairing defects and ensuring they don't recur.
- Training – Educating employees on maintaining high quality.
- Continuous Improvement – Constantly seeking methods to improve products and services.
Quality Control has a close connection with Quality Assurance (QA). QC identifies and corrects problems. QA prevents problems from arising in the first place. Together, they assist companies in maintaining their products and services at high levels.
How Quality Control Works ?
Quality inspections occur at various stages of producing non-consumable products. Workers inspect raw materials, components, and finished products to detect defects early. In industries where they do not manufacture tangible products, QC may include the customer's feedback, questionnaires, and inspections to ensure that services are up to standards. The focus is on producing products or services that are safe, trustworthy, and of high quality, regardless of the means utilized.
QC is essential across various sectors:
- Manufacturing – Material and product inspection for preventing defects.
- Food Industry – Inspection of food for safety and quality.
- Pharmaceuticals – Ensuring medicines are safe and functioning correctly.
- Software Development – Identifying and correcting software bugs prior to release.
QC increases efficiency, customer satisfaction, and a company's reputation in various industries.
Types of Quality Control
There is no single approach to QC. Various industries apply varying approaches. For instance, food and drugs demand rigorous scientific testing, whereas education or mentoring might be more feedback- and performance-review-based.
QC techniques shared across the board include:
- Control Charts – Plotting how processes vary over time.
- Process Control – Modifying methods of production to ensure quality.
- Acceptance Sampling – Inspection of a sample of products to determine if they are up to standard.
- Process Protocol – Developing step-by-step blueprints to enhance the way things are done.
Some businesses have their own QC staff. Others employ independent experts to inspect their products. Food and pharmaceutical industries make use of in-house testing and third-party laboratories. They do this to guarantee their products are safe.
QC is detail-oriented. It makes sure that companies offer the best products and services to consumers.
Why Is Quality Control Important? What Are the Benefits?
Quality Control (QC) is highly crucial to companies and clients. It ensures products and services are of high quality. Some of the most significant reasons why QC is crucial include:
- Customer Satisfaction – QC ensures customers receive good-quality products and services, which makes them satisfied and loyal to a brand.
- Prevents Defects – QC identifies defects early. This reduces product recalls and additional repairs.
- Saves Money – QC helps companies waste less and work more efficiently, lowering costs.
- Follows Rules and Laws – QC makes sure businesses meet industry standards and avoid legal trouble.
- Builds a Good Reputation – High-quality products improve a company’s image and help it stand out from competitors.
- Improves Efficiency – QC finds areas that need improvement, making processes faster and better .
- Avoids Risks – Thorough testing avoids safety risks or product malfunction.
- Improves – QC enables companies to continuously improve products and services.
- Competes Globally – Quality products enable a company to sell globally.
- Enhances Customer Retention – Satisfied customers are likely to return and refer the company to others.
QC enables companies to offer excellent products. It enables them to prevent errors and remain competitive in the market.
Quality Control Roles and Responsibilities
Quality Control is distinct from Quality Assurance (QA). QA is used to avoid errors. QC measures and inspects product quality to locate errors.
A Quality Control Specialist has various responsibilities, including:
- Inspecting product quality through tests and tools.
- Comparing outcomes with company and industry standards.
- Locating and correcting issues to enhance quality.
- Reporting findings to managers and teams.
QC professionals assist companies to make sure that their products are good enough to go to the market.
Quality Control vs. Quality Assurance
Individuals sometimes confuse QC and QA, yet they are distinct:
- Quality Control (QC) ensures that a product is in accordance with quality standards.
- Quality Assurance (QA) establishes processes to avoid quality issues before they occur.
Both are components of a firm's quality management system. QC seeks out and corrects problems. QA, in contrast, works to avoid problems from occurring in the first place.
Professions in Quality Control
If you enjoy working with others, troubleshooting, and refining products, a career in QC might suit you.
Depending on the sector, you might need:
- A high school diploma for entry-level positions.
- A bachelor's degree in some areas.
- Manufacturing, food safety, or other industry experience.
- Certifications such as Six Sigma or Certified Quality Inspector for enhanced job prospects.
Skills required for QC positions:
- Carefulness to details
- Math and technical aptitude
- Physical endurance (for jobs that require physical labor)
- Problem-solving skills
- Pressure to work
Career Advancement
With experience, QC professionals can develop into senior specialists and team leaders. Some even acquire higher certifications to boost their job prospects.
Quality Control Salaries
Salaries in QC vary with the type of job, experience, and industry. Below are some average salaries:
- Science & tech services – $46,280
- Manufacturing – $40,020
- Wholesale trade – $37,800
- Office support services – $30,070
As individuals become more experienced and transition to management positions, their salaries rise.
What Does Quality Control Mean?
Quality Control is how businesses ensure and enhance product quality. Businesses test products, inspect processes, and verify results against industry standards. The aim is to ensure that products are consistent and dependable.
Examples of Quality Control
Below are three instances of QC in the food industry:
1. Ensuring ingredient quality for meeting safety standards.
2. Certifying suppliers to ensure that they deliver safe and quality materials.
3. Checking manufacturing plants in order to maintain food clean and safe.
How to obtain AWS certification?
We are an Education Technology company providing certification training courses to accelerate careers of working professionals worldwide. We impart training through instructor-led classroom workshops, instructor-led live virtual training sessions, and self-paced e-learning courses.
We have successfully conducted training sessions in 108 countries across the globe and enabled thousands of working professionals to enhance the scope of their careers.
Our enterprise training portfolio includes in-demand and globally recognized certification training courses in Project Management, Quality Management, Business Analysis, IT Service Management, Agile and Scrum, Cyber Security, Data Science, and Emerging Technologies. Download our Enterprise Training Catalog from https://www.icertglobal.com/corporate-training-for-enterprises.php and https://www.icertglobal.com/index.php
Popular Courses include:
-
Project Management: PMP, CAPM ,PMI RMP
-
Quality Management: Six Sigma Black Belt ,Lean Six Sigma Green Belt, Lean Management, Minitab,CMMI
-
Business Analysis: CBAP, CCBA, ECBA
-
Agile Training: PMI-ACP , CSM , CSPO
-
Scrum Training: CSM
-
DevOps
-
Program Management: PgMP
-
Cloud Technology: Exin Cloud Computing
-
Citrix Client Adminisration: Citrix Cloud Administration
The 10 top-paying certifications to target in 2024 are:
Conclusion
If you desire to be an expert in QC, then go for training in Lean Six Sigma. iCert Global offers a Post Graduate Program in Lean Six Sigma. This course helps you learn to enhance business processes and quality control systems.
A Six Sigma Black Belt certification trains you on how to manage teams and resolve quality problems. You will also be assisting companies in saving money. This training has the ability to enhance your professional life and make you marketable in the workplace.
Contact Us For More Information:
Visit : www.icertglobal.com Email : info@icertglobal.com
Read More
We take it for granted now that products and services should function well. We do not usually wonder how they are produced. However, back in the early 1900s, ensuring that products were reliable was not a simple task. Businesses, with time, found means to inspect and enhance quality. The trend Today, it is easier than ever for businesses to emulate and scale good quality standards.
How Does Quality Control Work?
Quality could be anything. Quality Control (QC) is a system that inspects products or services. It helps ensure that they follow certain standards. QC assists companies in testing, measuring, and enhancing products. The primary function of QC is to locate and correct faults prior to reaching the customers. This includes inspecting products at different production phases. Also, it's about the improvement to prevent repeating the same mistake.
Two key objectives of QC:
1. Ensuring products are as uniform as possible.
2. Minimizing errors and defects.
Key Elements of Quality Control :
Some of the most important elements of QC are:
- Inspection – Examining products or services to detect errors or flaws.
- Testing – Conducting tests to determine if products function properly.
- Statistical Process Control (SPC) – Employing numbers and data to monitor and regulate production.
- Record Keeping – Taking notes about inspections and repairs to monitor quality over time.
- Corrective Action – Repairing defects and ensuring they don't recur.
- Training – Educating employees on maintaining high quality.
- Continuous Improvement – Constantly seeking methods to improve products and services.
Quality Control has a close connection with Quality Assurance (QA). QC identifies and corrects problems. QA prevents problems from arising in the first place. Together, they assist companies in maintaining their products and services at high levels.
How Quality Control Works ?
Quality inspections occur at various stages of producing non-consumable products. Workers inspect raw materials, components, and finished products to detect defects early. In industries where they do not manufacture tangible products, QC may include the customer's feedback, questionnaires, and inspections to ensure that services are up to standards. The focus is on producing products or services that are safe, trustworthy, and of high quality, regardless of the means utilized.
QC is essential across various sectors:
- Manufacturing – Material and product inspection for preventing defects.
- Food Industry – Inspection of food for safety and quality.
- Pharmaceuticals – Ensuring medicines are safe and functioning correctly.
- Software Development – Identifying and correcting software bugs prior to release.
QC increases efficiency, customer satisfaction, and a company's reputation in various industries.
Types of Quality Control
There is no single approach to QC. Various industries apply varying approaches. For instance, food and drugs demand rigorous scientific testing, whereas education or mentoring might be more feedback- and performance-review-based.
QC techniques shared across the board include:
- Control Charts – Plotting how processes vary over time.
- Process Control – Modifying methods of production to ensure quality.
- Acceptance Sampling – Inspection of a sample of products to determine if they are up to standard.
- Process Protocol – Developing step-by-step blueprints to enhance the way things are done.
Some businesses have their own QC staff. Others employ independent experts to inspect their products. Food and pharmaceutical industries make use of in-house testing and third-party laboratories. They do this to guarantee their products are safe.
QC is detail-oriented. It makes sure that companies offer the best products and services to consumers.
Why Is Quality Control Important? What Are the Benefits?
Quality Control (QC) is highly crucial to companies and clients. It ensures products and services are of high quality. Some of the most significant reasons why QC is crucial include:
- Customer Satisfaction – QC ensures customers receive good-quality products and services, which makes them satisfied and loyal to a brand.
- Prevents Defects – QC identifies defects early. This reduces product recalls and additional repairs.
- Saves Money – QC helps companies waste less and work more efficiently, lowering costs.
- Follows Rules and Laws – QC makes sure businesses meet industry standards and avoid legal trouble.
- Builds a Good Reputation – High-quality products improve a company’s image and help it stand out from competitors.
- Improves Efficiency – QC finds areas that need improvement, making processes faster and better .
- Avoids Risks – Thorough testing avoids safety risks or product malfunction.
- Improves – QC enables companies to continuously improve products and services.
- Competes Globally – Quality products enable a company to sell globally.
- Enhances Customer Retention – Satisfied customers are likely to return and refer the company to others.
QC enables companies to offer excellent products. It enables them to prevent errors and remain competitive in the market.
Quality Control Roles and Responsibilities
Quality Control is distinct from Quality Assurance (QA). QA is used to avoid errors. QC measures and inspects product quality to locate errors.
A Quality Control Specialist has various responsibilities, including:
- Inspecting product quality through tests and tools.
- Comparing outcomes with company and industry standards.
- Locating and correcting issues to enhance quality.
- Reporting findings to managers and teams.
QC professionals assist companies to make sure that their products are good enough to go to the market.
Quality Control vs. Quality Assurance
Individuals sometimes confuse QC and QA, yet they are distinct:
- Quality Control (QC) ensures that a product is in accordance with quality standards.
- Quality Assurance (QA) establishes processes to avoid quality issues before they occur.
Both are components of a firm's quality management system. QC seeks out and corrects problems. QA, in contrast, works to avoid problems from occurring in the first place.
Professions in Quality Control
If you enjoy working with others, troubleshooting, and refining products, a career in QC might suit you.
Depending on the sector, you might need:
- A high school diploma for entry-level positions.
- A bachelor's degree in some areas.
- Manufacturing, food safety, or other industry experience.
- Certifications such as Six Sigma or Certified Quality Inspector for enhanced job prospects.
Skills required for QC positions:
- Carefulness to details
- Math and technical aptitude
- Physical endurance (for jobs that require physical labor)
- Problem-solving skills
- Pressure to work
Career Advancement
With experience, QC professionals can develop into senior specialists and team leaders. Some even acquire higher certifications to boost their job prospects.
Quality Control Salaries
Salaries in QC vary with the type of job, experience, and industry. Below are some average salaries:
- Science & tech services – $46,280
- Manufacturing – $40,020
- Wholesale trade – $37,800
- Office support services – $30,070
As individuals become more experienced and transition to management positions, their salaries rise.
What Does Quality Control Mean?
Quality Control is how businesses ensure and enhance product quality. Businesses test products, inspect processes, and verify results against industry standards. The aim is to ensure that products are consistent and dependable.
Examples of Quality Control
Below are three instances of QC in the food industry:
1. Ensuring ingredient quality for meeting safety standards.
2. Certifying suppliers to ensure that they deliver safe and quality materials.
3. Checking manufacturing plants in order to maintain food clean and safe.
How to obtain AWS certification?
We are an Education Technology company providing certification training courses to accelerate careers of working professionals worldwide. We impart training through instructor-led classroom workshops, instructor-led live virtual training sessions, and self-paced e-learning courses.
We have successfully conducted training sessions in 108 countries across the globe and enabled thousands of working professionals to enhance the scope of their careers.
Our enterprise training portfolio includes in-demand and globally recognized certification training courses in Project Management, Quality Management, Business Analysis, IT Service Management, Agile and Scrum, Cyber Security, Data Science, and Emerging Technologies. Download our Enterprise Training Catalog from https://www.icertglobal.com/corporate-training-for-enterprises.php and https://www.icertglobal.com/index.php
Popular Courses include:
-
Project Management: PMP, CAPM ,PMI RMP
-
Quality Management: Six Sigma Black Belt ,Lean Six Sigma Green Belt, Lean Management, Minitab,CMMI
-
Business Analysis: CBAP, CCBA, ECBA
-
Agile Training: PMI-ACP , CSM , CSPO
-
Scrum Training: CSM
-
DevOps
-
Program Management: PgMP
-
Cloud Technology: Exin Cloud Computing
-
Citrix Client Adminisration: Citrix Cloud Administration
The 10 top-paying certifications to target in 2024 are:
Conclusion
If you desire to be an expert in QC, then go for training in Lean Six Sigma. iCert Global offers a Post Graduate Program in Lean Six Sigma. This course helps you learn to enhance business processes and quality control systems.
A Six Sigma Black Belt certification trains you on how to manage teams and resolve quality problems. You will also be assisting companies in saving money. This training has the ability to enhance your professional life and make you marketable in the workplace.
Contact Us For More Information:
Visit : www.icertglobal.com Email : info@icertglobal.com
Lean Six Sigma Certification Explained How to Achieve It
Six Sigma certification is a highly recognized certification that assists professionals in handling processes and enhancing quality. Six Sigma is applied in various industries. Six Sigma assists companies in working with ease, avoiding errors, and enhancing processes. To become certified, you have to learn how to attain a Yellow, Green, or Black Belt in Six Sigma.
What is Six Sigma Certification?
Six Sigma Certification indicates that an individual can apply Six Sigma techniques to enhance business processes. This method emphasizes minimizing mistakes and making operations more efficient. The certification comes in different levels: Yellow Belt, Green Belt, Black Belt, and Master Black Belt. Every level indicates more proficiency.
Six Sigma improves performance and quality. It applies the DMAIC approach. DMAIC is an acronym for Define, Measure, Analyze, Improve, and Control. This practical approach resolves issues and reduces variability. It makes work more effective and smoother.
About DMAIC and DMADV
DMAIC is a step-by-step procedure in Six Sigma. It relies on using data to refine existing processes. It assists in discovering and eliminating defects so that processes become more efficient and of high quality.
DMAIC Steps:
• Define:
Define the problem, establish goals, and determine customer needs.
• Measure: Gather data on the current process to learn about its performance.
• Analyze: Examine the data to identify the root causes of issues.
• Improve: Create and implement solutions to correct the problems.
• Control: Sustain the improvements and avoid future issues.
DMADV (Define, Measure, Analyze, Design, Verify)
DMADV is a Six Sigma tool. It is used to design new processes or products rather than improve existing ones. It can be utilized in Lean Six Sigma when there's a requirement of innovation or new design.
Steps of DMADV:
• Define:
- Determine project objectives.
- Know the requirements of customers.
- Identify what the new process or product should produce.
• Measure: Determine key features, customer requirements, and key performance measures.
• Review: Examine different design options. Select the optimal one based on data and customer requirements.
• Design: Create the new process or product, making sure it adheres to all necessary standards.
• Verify: Validate the design through pilot runs or simulations to ensure it performs as intended.
Both DMAIC and DMADV are significant Six Sigma tools. DMAIC enhances current processes. DMADV, however, designs new processes from the ground up.
Six Sigma vs. Lean Six Sigma Certification
Six Sigma and Lean Six Sigma optimize processes and reduce errors. They focus on different things, though.
Six Sigma Certification:
• Reduces errors and enhances quality through data and statistics.
• Applics DMAIC (Define, Measure, Analyze, Improve, Control) to solve problems in current processes.
• Is focused on defect detection and correction to make things more reliable.
• Widely applied in manufacturing, healthcare, finance, and IT.
Lean Six Sigma Certification:
• Merges Lean, which eliminates waste, and Six Sigma, which minimizes errors. It makes work more efficient and quicker.
• Employs DMAIC and Lean tools to eliminate steps that aren't necessary and preserve time.
• Emphasizes speed, efficiency, and streamlining workflow with high-quality levels.
• Employed in the service industry, healthcare, logistics, and manufacturing.
Which One is Right for You?
• Select Six Sigma if you prefer data, solving problems, and enhancing quality.
• Select Lean Six Sigma to accelerate processes, reduce waste, and enhance efficiency.
Six Sigma Certification Levels
Six Sigma offers various levels of certification. Each level develops from the abilities of the previous one :
1. Yellow Belt Certification (Start-Up Level)
• What it is: An entry level for Six Sigma fundamentals learning.
• Role: Yellow Belts assist teams by gathering data, creating process maps, and fixing minor problems. They work under the guidance of Green or Black Belts.
• Principal Skills:
- Learning Six Sigma stages (DMAIC).
- Using basic tools such as the Fishbone Diagram in order to look for problems.
oKnowing how to quantify errors and inefficiencies.
2. Green Belt Certificate (Intermediate)
• What is it: Intensive Six Sigma for those with a desire to lead small-sized projects.
• Role: Green Belts pilot smaller projects or assist Black Belts with large ones. Green Belts will examine data, identify areas in processes that need improvement, and recommend changes.
• Principal Skills:
- The application of all DMAIC steps.
- The learning of tools such as control charts and root cause analysis.
- Improvement in processes and implementation of actual changes.
3. Black Belt Certification (Advanced Level)
•What it is: Advanced-level certification for individuals who would like to be in charge of large projects and train others.
•Role: Black Belts head large projects, mentor Green Belts, and implement major changes in a firm.
•Key Skills:
- Application of advanced data analysis and statistics.
- Team leadership and management of project issues.
- Ensuring improvements endure in the long term.
4. Master Black Belt Certification (Expert Level)
• What it is: The Six Sigma top certification level. It deals with leadership, training, and enhancing the entire company.
• Role: Master Black Belts train and mentor Black and Green Belts. They assist in developing Six Sigma strategies and ensuring projects align with company objectives.
• Primary Skills:
- Managing large projects and directing company-wide enhancements.
- Mentoring and instructing Black Belts and Green Belts.
- Employing sophisticated analysis of data and integrating Six Sigma with other practices such as Lean.
How Six Sigma Aids Quality Enhancement
1.Less Error: Six Sigma detects and removes the causes of mistakes. This produces improved products and services.
2.Work Processes Improved: It accelerates work and simplifies it. This reduces costs and delays.
3.Informed Decision-Making using Facts: Six Sigma relies on facts and figures to make sound decisions. This improves quality.
4. Happier Customers: If products are consistent and reliable, customers remain content.
5. Lower Costs: Companies save by eliminating waste and errors.
6. Teamwork and Growth: Workers collaborate to enhance processes and acquire new knowledge.
7. Long-Term Success: Six Sigma maintains improvement so quality does not degrade.
8. Following Rules: Companies can satisfy industry requirements and stay safe.
Where Six Sigma is Used ?
Six Sigma benefits numerous industries. It streamlines work, reduces errors, and improves quality.
1. Manufacturing: It assists in producing improved products with fewer errors, saving time and money.
2. Healthcare: Six Sigma improves patient care. It reduces errors and accelerates hospital procedures.
3. Finance & Banking: It assists banks in processing transactions accurately and providing better customer service.
4. Information Technology (IT): Six Sigma improves software and IT services to be more efficient and reliable.
5. Supply Chain & Logistics: It enhances shipping, inventory management, and delivery times.
6. Telecommunications: Six Sigma minimizes service outages and enhances customer support.
7. Aerospace & Defense: It maintains stringent safety standards and enhances project management.
8. Retail: Stores utilize it to control inventory, minimize waste, and enhance customer service.
Prerequisites for Six Sigma Certification
• Yellow Belt:
- No experience is necessary.
- Fundamental knowledge of business processes is desirable but not required.
• Green Belt:
- Some process improvement experience is useful.
- Basic statistics and business process knowledge may be needed.
• Black Belt:
- Certification as a Green Belt is normally required.
- Prior experience working on or leading process improvement initiatives.
- Significant data analysis, statistics, and Six Sigma methodologies knowledge.
• Master Black Belt:
- Mandatory certification as a Black Belt.
- Substantial experience as the leader on many Six Sigma initiatives.
- Exceptional leadership and mentoring abilities.
- Comprehensive understanding of Six Sigma tools and statistical techniques.
Top Reasons to Get Six Sigma Certification
• Career Development: Enhances employment opportunities in process improvement and leadership positions.
• Improved Skills: Enhances problem-solving, data analysis, and project management skills.
• Higher Pay: Certified professionals get higher pay due to their skillset.
• Greater Efficiency: Identifies inefficiencies, eliminates waste, and streamlines processes.
• Global Acceptance: Used globally, thus being a precious asset in various industries.
• Leadership Training: Higher certifications enable professionals for leadership and mentoring.
• Business Excellence: Facilitates organizations in enhancing quality, minimizing costs, and enhancing customer satisfaction.
• Versatility: Used across numerous industries such as manufacturing, healthcare, finance, IT, and supply chain.
• Personal Growth: Cultivates a spirit of perpetual improvement and confidence in problem-solving.
Benefits of Six Sigma Certification
• Career Growth: Improves career opportunities and enhances chances of promotion.
• Higher Salary: Higher-paying wages for certified professionals due to specialist abilities.
• Improved Business Processes: Reduces waste, makes operations more efficient, and enhances quality.
• Improved Problem-Solving Skills: Develops analytical skills to detect and rectify quality defects.
• Competitive Advantage: Companies with Six Sigma professionals are at a competitive edge.
• International Acceptance: Certification is respected globally, presenting opportunities across industries and geographies.
• Personal Growth: Enhances quality management, statistical, and decision-making abilities.
• Industry-Agnostic: Can be applied in manufacturing, healthcare, IT, finance, etc.
• Leadership Development: Trains professionals to become managers and team leaders.
• Healthy Work Culture: Promotes ongoing improvement and productivity within organizations.
Future of Six Sigma Certification
• Increased Demand: Companies still emphasize efficiency, quality, and cost savings.
• Data-Driven: Six Sigma remains relevant today. It flourishes in an analytics-driven and innovative world.
• Industry Acceptance: Six Sigma is implemented by numerous businesses to streamline processes and eliminate waste.
• High Employment Demand: Certified professionals are prized for their ability to solve problems and optimize processes.
• Combining with New Technologies: Six Sigma is expanding together with AI, automation, and big data analysis.
• Sustainability Focus: Six Sigma is employed by companies to facilitate environmentally friendly and cost-cutting solutions.
How to obtain Six Sigma certification?
We are an Education Technology company providing certification training courses to accelerate careers of working professionals worldwide. We impart training through instructor-led classroom workshops, instructor-led live virtual training sessions, and self-paced e-learning courses.
We have successfully conducted training sessions in 108 countries across the globe and enabled thousands of working professionals to enhance the scope of their careers.
Our enterprise training portfolio includes in-demand and globally recognized certification training courses in Project Management, Quality Management, Business Analysis, IT Service Management, Agile and Scrum, Cyber Security, Data Science, and Emerging Technologies. Download our Enterprise Training Catalog from https://www.icertglobal.com/corporate-training-for-enterprises.php and https://www.icertglobal.com/index.php
Popular Courses include:
-
Project Management: PMP, CAPM ,PMI RMP
-
Quality Management: Six Sigma Black Belt ,Lean Six Sigma Green Belt, Lean Management, Minitab,CMMI
-
Business Analysis: CBAP, CCBA, ECBA
-
Agile Training: PMI-ACP , CSM , CSPO
-
Scrum Training: CSM
-
DevOps
-
Program Management: PgMP
-
Cloud Technology: Exin Cloud Computing
-
Citrix Client Adminisration: Citrix Cloud Administration
The 10 top-paying certifications to target in 2024 are:
Conclusion
Six Sigma certification advances careers and enhances business processes. It imparts crucial problem-solving skills and quality improvement skills. Industries utilize Six Sigma to make working more efficient and minimize errors. As businesses continue to seek means of enhancing, Six Sigma will remain relevant. It will continue to enable businesses to thrive and remain competitive in the future.
Contact Us For More Information:
Visit : www.icertglobal.com Email : info@icertglobal.com
Read More
Six Sigma certification is a highly recognized certification that assists professionals in handling processes and enhancing quality. Six Sigma is applied in various industries. Six Sigma assists companies in working with ease, avoiding errors, and enhancing processes. To become certified, you have to learn how to attain a Yellow, Green, or Black Belt in Six Sigma.
What is Six Sigma Certification?
Six Sigma Certification indicates that an individual can apply Six Sigma techniques to enhance business processes. This method emphasizes minimizing mistakes and making operations more efficient. The certification comes in different levels: Yellow Belt, Green Belt, Black Belt, and Master Black Belt. Every level indicates more proficiency.
Six Sigma improves performance and quality. It applies the DMAIC approach. DMAIC is an acronym for Define, Measure, Analyze, Improve, and Control. This practical approach resolves issues and reduces variability. It makes work more effective and smoother.
About DMAIC and DMADV
DMAIC is a step-by-step procedure in Six Sigma. It relies on using data to refine existing processes. It assists in discovering and eliminating defects so that processes become more efficient and of high quality.
DMAIC Steps:
• Define:
Define the problem, establish goals, and determine customer needs.
• Measure: Gather data on the current process to learn about its performance.
• Analyze: Examine the data to identify the root causes of issues.
• Improve: Create and implement solutions to correct the problems.
• Control: Sustain the improvements and avoid future issues.
DMADV (Define, Measure, Analyze, Design, Verify)
DMADV is a Six Sigma tool. It is used to design new processes or products rather than improve existing ones. It can be utilized in Lean Six Sigma when there's a requirement of innovation or new design.
Steps of DMADV:
• Define:
- Determine project objectives.
- Know the requirements of customers.
- Identify what the new process or product should produce.
• Measure: Determine key features, customer requirements, and key performance measures.
• Review: Examine different design options. Select the optimal one based on data and customer requirements.
• Design: Create the new process or product, making sure it adheres to all necessary standards.
• Verify: Validate the design through pilot runs or simulations to ensure it performs as intended.
Both DMAIC and DMADV are significant Six Sigma tools. DMAIC enhances current processes. DMADV, however, designs new processes from the ground up.
Six Sigma vs. Lean Six Sigma Certification
Six Sigma and Lean Six Sigma optimize processes and reduce errors. They focus on different things, though.
Six Sigma Certification:
• Reduces errors and enhances quality through data and statistics.
• Applics DMAIC (Define, Measure, Analyze, Improve, Control) to solve problems in current processes.
• Is focused on defect detection and correction to make things more reliable.
• Widely applied in manufacturing, healthcare, finance, and IT.
Lean Six Sigma Certification:
• Merges Lean, which eliminates waste, and Six Sigma, which minimizes errors. It makes work more efficient and quicker.
• Employs DMAIC and Lean tools to eliminate steps that aren't necessary and preserve time.
• Emphasizes speed, efficiency, and streamlining workflow with high-quality levels.
• Employed in the service industry, healthcare, logistics, and manufacturing.
Which One is Right for You?
• Select Six Sigma if you prefer data, solving problems, and enhancing quality.
• Select Lean Six Sigma to accelerate processes, reduce waste, and enhance efficiency.
Six Sigma Certification Levels
Six Sigma offers various levels of certification. Each level develops from the abilities of the previous one :
1. Yellow Belt Certification (Start-Up Level)
• What it is: An entry level for Six Sigma fundamentals learning.
• Role: Yellow Belts assist teams by gathering data, creating process maps, and fixing minor problems. They work under the guidance of Green or Black Belts.
• Principal Skills:
- Learning Six Sigma stages (DMAIC).
- Using basic tools such as the Fishbone Diagram in order to look for problems.
oKnowing how to quantify errors and inefficiencies.
2. Green Belt Certificate (Intermediate)
• What is it: Intensive Six Sigma for those with a desire to lead small-sized projects.
• Role: Green Belts pilot smaller projects or assist Black Belts with large ones. Green Belts will examine data, identify areas in processes that need improvement, and recommend changes.
• Principal Skills:
- The application of all DMAIC steps.
- The learning of tools such as control charts and root cause analysis.
- Improvement in processes and implementation of actual changes.
3. Black Belt Certification (Advanced Level)
•What it is: Advanced-level certification for individuals who would like to be in charge of large projects and train others.
•Role: Black Belts head large projects, mentor Green Belts, and implement major changes in a firm.
•Key Skills:
- Application of advanced data analysis and statistics.
- Team leadership and management of project issues.
- Ensuring improvements endure in the long term.
4. Master Black Belt Certification (Expert Level)
• What it is: The Six Sigma top certification level. It deals with leadership, training, and enhancing the entire company.
• Role: Master Black Belts train and mentor Black and Green Belts. They assist in developing Six Sigma strategies and ensuring projects align with company objectives.
• Primary Skills:
- Managing large projects and directing company-wide enhancements.
- Mentoring and instructing Black Belts and Green Belts.
- Employing sophisticated analysis of data and integrating Six Sigma with other practices such as Lean.
How Six Sigma Aids Quality Enhancement
1.Less Error: Six Sigma detects and removes the causes of mistakes. This produces improved products and services.
2.Work Processes Improved: It accelerates work and simplifies it. This reduces costs and delays.
3.Informed Decision-Making using Facts: Six Sigma relies on facts and figures to make sound decisions. This improves quality.
4. Happier Customers: If products are consistent and reliable, customers remain content.
5. Lower Costs: Companies save by eliminating waste and errors.
6. Teamwork and Growth: Workers collaborate to enhance processes and acquire new knowledge.
7. Long-Term Success: Six Sigma maintains improvement so quality does not degrade.
8. Following Rules: Companies can satisfy industry requirements and stay safe.
Where Six Sigma is Used ?
Six Sigma benefits numerous industries. It streamlines work, reduces errors, and improves quality.
1. Manufacturing: It assists in producing improved products with fewer errors, saving time and money.
2. Healthcare: Six Sigma improves patient care. It reduces errors and accelerates hospital procedures.
3. Finance & Banking: It assists banks in processing transactions accurately and providing better customer service.
4. Information Technology (IT): Six Sigma improves software and IT services to be more efficient and reliable.
5. Supply Chain & Logistics: It enhances shipping, inventory management, and delivery times.
6. Telecommunications: Six Sigma minimizes service outages and enhances customer support.
7. Aerospace & Defense: It maintains stringent safety standards and enhances project management.
8. Retail: Stores utilize it to control inventory, minimize waste, and enhance customer service.
Prerequisites for Six Sigma Certification
• Yellow Belt:
- No experience is necessary.
- Fundamental knowledge of business processes is desirable but not required.
• Green Belt:
- Some process improvement experience is useful.
- Basic statistics and business process knowledge may be needed.
• Black Belt:
- Certification as a Green Belt is normally required.
- Prior experience working on or leading process improvement initiatives.
- Significant data analysis, statistics, and Six Sigma methodologies knowledge.
• Master Black Belt:
- Mandatory certification as a Black Belt.
- Substantial experience as the leader on many Six Sigma initiatives.
- Exceptional leadership and mentoring abilities.
- Comprehensive understanding of Six Sigma tools and statistical techniques.
Top Reasons to Get Six Sigma Certification
• Career Development: Enhances employment opportunities in process improvement and leadership positions.
• Improved Skills: Enhances problem-solving, data analysis, and project management skills.
• Higher Pay: Certified professionals get higher pay due to their skillset.
• Greater Efficiency: Identifies inefficiencies, eliminates waste, and streamlines processes.
• Global Acceptance: Used globally, thus being a precious asset in various industries.
• Leadership Training: Higher certifications enable professionals for leadership and mentoring.
• Business Excellence: Facilitates organizations in enhancing quality, minimizing costs, and enhancing customer satisfaction.
• Versatility: Used across numerous industries such as manufacturing, healthcare, finance, IT, and supply chain.
• Personal Growth: Cultivates a spirit of perpetual improvement and confidence in problem-solving.
Benefits of Six Sigma Certification
• Career Growth: Improves career opportunities and enhances chances of promotion.
• Higher Salary: Higher-paying wages for certified professionals due to specialist abilities.
• Improved Business Processes: Reduces waste, makes operations more efficient, and enhances quality.
• Improved Problem-Solving Skills: Develops analytical skills to detect and rectify quality defects.
• Competitive Advantage: Companies with Six Sigma professionals are at a competitive edge.
• International Acceptance: Certification is respected globally, presenting opportunities across industries and geographies.
• Personal Growth: Enhances quality management, statistical, and decision-making abilities.
• Industry-Agnostic: Can be applied in manufacturing, healthcare, IT, finance, etc.
• Leadership Development: Trains professionals to become managers and team leaders.
• Healthy Work Culture: Promotes ongoing improvement and productivity within organizations.
Future of Six Sigma Certification
• Increased Demand: Companies still emphasize efficiency, quality, and cost savings.
• Data-Driven: Six Sigma remains relevant today. It flourishes in an analytics-driven and innovative world.
• Industry Acceptance: Six Sigma is implemented by numerous businesses to streamline processes and eliminate waste.
• High Employment Demand: Certified professionals are prized for their ability to solve problems and optimize processes.
• Combining with New Technologies: Six Sigma is expanding together with AI, automation, and big data analysis.
• Sustainability Focus: Six Sigma is employed by companies to facilitate environmentally friendly and cost-cutting solutions.
How to obtain Six Sigma certification?
We are an Education Technology company providing certification training courses to accelerate careers of working professionals worldwide. We impart training through instructor-led classroom workshops, instructor-led live virtual training sessions, and self-paced e-learning courses.
We have successfully conducted training sessions in 108 countries across the globe and enabled thousands of working professionals to enhance the scope of their careers.
Our enterprise training portfolio includes in-demand and globally recognized certification training courses in Project Management, Quality Management, Business Analysis, IT Service Management, Agile and Scrum, Cyber Security, Data Science, and Emerging Technologies. Download our Enterprise Training Catalog from https://www.icertglobal.com/corporate-training-for-enterprises.php and https://www.icertglobal.com/index.php
Popular Courses include:
-
Project Management: PMP, CAPM ,PMI RMP
-
Quality Management: Six Sigma Black Belt ,Lean Six Sigma Green Belt, Lean Management, Minitab,CMMI
-
Business Analysis: CBAP, CCBA, ECBA
-
Agile Training: PMI-ACP , CSM , CSPO
-
Scrum Training: CSM
-
DevOps
-
Program Management: PgMP
-
Cloud Technology: Exin Cloud Computing
-
Citrix Client Adminisration: Citrix Cloud Administration
The 10 top-paying certifications to target in 2024 are:
Conclusion
Six Sigma certification advances careers and enhances business processes. It imparts crucial problem-solving skills and quality improvement skills. Industries utilize Six Sigma to make working more efficient and minimize errors. As businesses continue to seek means of enhancing, Six Sigma will remain relevant. It will continue to enable businesses to thrive and remain competitive in the future.
Contact Us For More Information:
Visit : www.icertglobal.com Email : info@icertglobal.com
Mastering Minitab A Practical Guide to Statistical Analysis
Minitab is a software tool that helps businesses analyze data. It also improves processes and cuts costs. Minitab helps quality control, data analysis, and statistics workers. They use it to find and fix problems in healthcare, manufacturing, and education.
Minitab has tools for analyzing data, making graphs, and calculating trends. It's very useful for Six Sigma. This method helps businesses enhance their processes and minimize errors. Minitab can track progress and confirm results after quality changes.
How Helps in Six Sigma
Six Sigma is a problem-solving method that uses data and math to find errors and make things better.
Minitab helps users by:
- Following DMAIC steps: Define, Measure, Analyze, Improve, and Control to enhance processes.Simplify complex calculations for easy understanding.
- Use graphs and charts: to display data and results.
Why Use Minitab?
Easy to Use – Minitab is simple to learn and has a user-friendly design. ️
Strong Data Analysis – It can analyze trends, compare numbers, and test ideas. ️
Works with Large Data – Minitab can handle big amounts of information quickly. ️
Creates Clear Reports – You can export data in PDF, Excel, or CSV and customize reports.
Great for Visualizing Data – Users can create charts and graphs. This makes data easier to understand.
Minitab is a strong tool for anyone working with data and improving quality. No matter if you’re a student, analyst, or business pro, it helps you solve problems and make decisions easily!
Minitab vs. Excel: Which One is Better?
Minitab and Excel are both computer programs for data analysis. However, they serve different purposes. Here are the main differences:
Excel is mainly for working with numbers. You can use it to create budgets, reports, and financial models. Minitab is made for statistical analysis. It helps people study trends and find patterns in data. Excel is easier to learn. Minitab requires more practice. It has advanced tools for data experts. Excel works on Windows and Mac, but Minitab only works on Windows. Minitab has more features for analyzing data but is also more expensive than Excel. Excel remains the top choice, but Minitab is gaining traction. It's especially popular in healthcare, manufacturing, and business analysis.
Key Features of Minitab
Minitab has many powerful tools for data analysis and quality control. Here are eight key features:
1. Basic Statistics Minitab helps analyze data using math and statistics. It includes descriptive statistics, correlation analysis, and regression analysis. It also lets users create charts and graphs to better understand the data.
2. Graphics and Visualization Minitab includes visual tools like histograms, scatterplots, and box plots. These help users see patterns, find outliers, and compare data easily.
3. Regression Analysis This feature helps users find relationships between different factors. For example, researchers can predict future results based on current data.
4. ANOVA, or Analysis of Variance, lets users compare data groups. It shows if there are significant differences among them.
5. Statistical Process Control (SPC) is a quality control tool. It helps track and improve processes in industries such as manufacturing. It helps find problems and fix them before they become serious.
6. Measurement System Analysis This tool checks if a measurement system is accurate. It helps businesses ensure that their tools and methods are reliable.
7. Design of Experiments (DOE) DOE helps study how different factors affect a process. It is useful for improving production methods and reducing errors.
8. Reliability and Survival Analysis This feature helps users model data effectively. It also aids in predicting future trends.
It is useful for understanding product reliability and performance over time.
Which One Should You Use?
Use Excel if you need a simple, easy-to-use tool for working with numbers. Use Minitab for advanced data analysis. It's great for research, quality control, and Six Sigma projects.
Both Excel and Minitab are great tools, but they have different purposes. If you want to study data in detail and improve processes, Minitab is the better choice.
How to obtain Minitab certification?
We are an Education Technology company providing certification training courses to accelerate careers of working professionals worldwide. We impart training through instructor-led classroom workshops, instructor-led live virtual training sessions, and self-paced e-learning courses.
We have successfully conducted training sessions in 108 countries across the globe and enabled thousands of working professionals to enhance the scope of their careers.
Our enterprise training portfolio includes in-demand and globally recognized certification training courses in Project Management, Quality Management, Business Analysis, IT Service Management, Agile and Scrum, Cyber Security, Data Science, and Emerging Technologies. Download our Enterprise Training Catalog from https://www.icertglobal.com/corporate-training-for-enterprises.php and https://www.icertglobal.com/index.php
Popular Courses include:
-
Project Management: PMP, CAPM ,PMI RMP
-
Quality Management: Six Sigma Black Belt ,Lean Six Sigma Green Belt, Lean Management, Minitab,CMMI
-
Business Analysis: CBAP, CCBA, ECBA
-
Agile Training: PMI-ACP , CSM , CSPO
-
Scrum Training: CSM
-
DevOps
-
Program Management: PgMP
-
Cloud Technology: Exin Cloud Computing
-
Citrix Client Adminisration: Citrix Cloud Administration
The 10 top-paying certifications to target in 2025 are:
Conclusion
Minitab is a powerful tool for data analysis, statistical evaluation, and process improvement. Its many features help businesses and individuals improve decision-making and quality control. By mastering Minitab, you can strengthen your project management skills and improve efficiency.
If you want to take your expertise further, consider Minitab training from iCert Global. You can also advance your career by becoming a Six Sigma expert with our Lean Six Sigma Green Belt program.
Contact Us For More Information:
Visit :www.icertglobal.com Email : 
Read More
Minitab is a software tool that helps businesses analyze data. It also improves processes and cuts costs. Minitab helps quality control, data analysis, and statistics workers. They use it to find and fix problems in healthcare, manufacturing, and education.
Minitab has tools for analyzing data, making graphs, and calculating trends. It's very useful for Six Sigma. This method helps businesses enhance their processes and minimize errors. Minitab can track progress and confirm results after quality changes.
How Helps in Six Sigma
Six Sigma is a problem-solving method that uses data and math to find errors and make things better.
Minitab helps users by:
- Following DMAIC steps: Define, Measure, Analyze, Improve, and Control to enhance processes.Simplify complex calculations for easy understanding.
- Use graphs and charts: to display data and results.
Why Use Minitab?
Easy to Use – Minitab is simple to learn and has a user-friendly design. ️
Strong Data Analysis – It can analyze trends, compare numbers, and test ideas. ️
Works with Large Data – Minitab can handle big amounts of information quickly. ️
Creates Clear Reports – You can export data in PDF, Excel, or CSV and customize reports.
Great for Visualizing Data – Users can create charts and graphs. This makes data easier to understand.
Minitab is a strong tool for anyone working with data and improving quality. No matter if you’re a student, analyst, or business pro, it helps you solve problems and make decisions easily!
Minitab vs. Excel: Which One is Better?
Minitab and Excel are both computer programs for data analysis. However, they serve different purposes. Here are the main differences:
Excel is mainly for working with numbers. You can use it to create budgets, reports, and financial models. Minitab is made for statistical analysis. It helps people study trends and find patterns in data. Excel is easier to learn. Minitab requires more practice. It has advanced tools for data experts. Excel works on Windows and Mac, but Minitab only works on Windows. Minitab has more features for analyzing data but is also more expensive than Excel. Excel remains the top choice, but Minitab is gaining traction. It's especially popular in healthcare, manufacturing, and business analysis.
Key Features of Minitab
Minitab has many powerful tools for data analysis and quality control. Here are eight key features:
1. Basic Statistics Minitab helps analyze data using math and statistics. It includes descriptive statistics, correlation analysis, and regression analysis. It also lets users create charts and graphs to better understand the data.
2. Graphics and Visualization Minitab includes visual tools like histograms, scatterplots, and box plots. These help users see patterns, find outliers, and compare data easily.
3. Regression Analysis This feature helps users find relationships between different factors. For example, researchers can predict future results based on current data.
4. ANOVA, or Analysis of Variance, lets users compare data groups. It shows if there are significant differences among them.
5. Statistical Process Control (SPC) is a quality control tool. It helps track and improve processes in industries such as manufacturing. It helps find problems and fix them before they become serious.
6. Measurement System Analysis This tool checks if a measurement system is accurate. It helps businesses ensure that their tools and methods are reliable.
7. Design of Experiments (DOE) DOE helps study how different factors affect a process. It is useful for improving production methods and reducing errors.
8. Reliability and Survival Analysis This feature helps users model data effectively. It also aids in predicting future trends.
It is useful for understanding product reliability and performance over time.
Which One Should You Use?
Use Excel if you need a simple, easy-to-use tool for working with numbers. Use Minitab for advanced data analysis. It's great for research, quality control, and Six Sigma projects.
Both Excel and Minitab are great tools, but they have different purposes. If you want to study data in detail and improve processes, Minitab is the better choice.
How to obtain Minitab certification?
We are an Education Technology company providing certification training courses to accelerate careers of working professionals worldwide. We impart training through instructor-led classroom workshops, instructor-led live virtual training sessions, and self-paced e-learning courses.
We have successfully conducted training sessions in 108 countries across the globe and enabled thousands of working professionals to enhance the scope of their careers.
Our enterprise training portfolio includes in-demand and globally recognized certification training courses in Project Management, Quality Management, Business Analysis, IT Service Management, Agile and Scrum, Cyber Security, Data Science, and Emerging Technologies. Download our Enterprise Training Catalog from https://www.icertglobal.com/corporate-training-for-enterprises.php and https://www.icertglobal.com/index.php
Popular Courses include:
-
Project Management: PMP, CAPM ,PMI RMP
-
Quality Management: Six Sigma Black Belt ,Lean Six Sigma Green Belt, Lean Management, Minitab,CMMI
-
Business Analysis: CBAP, CCBA, ECBA
-
Agile Training: PMI-ACP , CSM , CSPO
-
Scrum Training: CSM
-
DevOps
-
Program Management: PgMP
-
Cloud Technology: Exin Cloud Computing
-
Citrix Client Adminisration: Citrix Cloud Administration
The 10 top-paying certifications to target in 2025 are:
Conclusion
Minitab is a powerful tool for data analysis, statistical evaluation, and process improvement. Its many features help businesses and individuals improve decision-making and quality control. By mastering Minitab, you can strengthen your project management skills and improve efficiency.
If you want to take your expertise further, consider Minitab training from iCert Global. You can also advance your career by becoming a Six Sigma expert with our Lean Six Sigma Green Belt program.
Contact Us For More Information:
Visit :www.icertglobal.com Email :
Earnings Potential with Six Sigma Certification in 2025
Six Sigma is important for today’s businesses and organizations. Companies pay well for professionals with Six Sigma skills. These experts help improve workflows, product quality, and customer satisfaction. In this article, we will explore Lean Six Sigma salaries and the key factors that influence them.
What is Six Sigma?
Six Sigma is a set of principles and techniques. They help organizations reach their goals more efficiently. The main goal is to improve product quality and customer satisfaction. This, in turn, boosts revenue growth. Organizations use Six Sigma to increase profits. They improve customer experiences, simplify operations, and reduce product and process defects.
Key Components of Six Sigma Include:
- A Business Strategy: A clear plan to boost revenue, cut costs, and enhance operations.
- A Vision: Empowering management to envision a defect-free, productive, and positive work environment.
- A Benchmark: Setting performance standards helps us track and improve our process metrics.
- A Goal: Set clear objectives for the organization to reach using best practices.
- A Statistical Measure: Utilizing data-driven metrics to evaluate the organization’s success.
- A Problem-Solving Methodology: A systematic approach to identifying and addressing operational challenges.
Who is a Six Sigma Expert?
A Six Sigma expert is skilled in the Six Sigma method and its various techniques. You can gain this expertise by finishing a certified Six Sigma course or by practicing Six Sigma methods directly.
Six Sigma expertise is structured across different certification levels:
- Yellow Belt: Covers foundational knowledge of Six Sigma principles.
- Green Belt: Focuses on advanced tools and techniques for process improvement.
- Black Belt: Demonstrates mastery in leading projects and driving strategic improvements.
- Master Black Belt: This is the top level of Six Sigma expertise. They mentor Black Belts and oversee projects across the entire organization. Professionals at this level typically earn the highest Lean Six Sigma certified salaries.
Six Sigma Salary in 2025
Becoming a Six Sigma expert offers excellent career opportunities across various industries. Organizations aim to enhance efficiency. As a result, the need for Six Sigma professionals remains high. This strong need offers attractive salary prospects. Six Sigma-certified salaries differ by certification level, experience, job role, and employer. In this article, we’ll explore the Six Sigma salary landscape for 2025.
What is the Average Salary of a Six Sigma Professional?
Here’s an overview of the average salary for Six Sigma professionals:
- Hourly Salary: The average Six Sigma professional earns approximately $36 per hour.
- Monthly Salary: The average monthly salary is around $900.
- Annual Salary: On an annual basis, Six Sigma experts can expect to earn roughly $11,000.
Six Sigma Salary Based on Different Factors
1. Salary Based on Experience and Job Role
The salary of Six Sigma professionals depends a lot on their experience and job role. Here’s a breakdown of average monthly salaries for various job roles:

1.Salary Growth Based on Experience Level
Experience plays a crucial role in determining salary growth. The following table shows the increase in pay percentage compared to entry-level employees:

2. Six Sigma Salary Based on Employer/Company
The employer’s size, industry, and geographic location also influence Six Sigma salaries. The Six Sigma salary survey shows estimated annual salaries at top companies:

3. Six Sigma Salary Based on Certifications
Certification levels in Six Sigma play a significant role in salary potential. Here’s how different certifications impact earnings:
Certification

4. Six Sigma Salary: Based on Location
The average salary for Six Sigma professionals differs greatly by country. This change is due to demand, cost of living, and the presence of various industries. Here’s

a breakdown of the average annual salaries across different countries
This global comparison shows that the value of Six Sigma expertise varies by region. It depends on local market needs and economic conditions.
What Is the ROI for Adopting Six Sigma?
Using Six Sigma practices gives a strong return on investment (ROI). This includes both clear (hard) benefits and less obvious (soft) benefits.
Hard Returns:
- Operational Improvements: Enhanced efficiency through streamlined processes.
- Cost Reductions: Identifying and eliminating waste to reduce expenses.
- Revenue Growth: Optimizing product quality and service delivery, leading to increased sales.
Soft Returns:
- Cost Avoidance: Preventing future issues that could result in financial losses.
- Customer Loyalty: Improved customer satisfaction fosters long-term relationships.
- Employee Engagement: A culture of continuous improvement boosts productivity and morale.
Key Factors Contributing to Six Sigma ROI:
- Cultural Transformation: Fosters a customer-centric mindset and reduces operational waste.
- Strategic Alignment: Strengthens the connection between business strategies and task execution.
- Accelerated Change: Enhances the speed of process improvements, driving business growth.
- Employee Satisfaction: Motivated employees have clear goals, effective workflows, and receive recognition. This combination helps keep them longer and boosts their performance.
ROI Percentage Based on Six Sigma Methodologies:
Methodology
Average ROI (%)
Lean
50%
Lean Six Sigma
48%
Six Sigma
33%
Organizations that use Six Sigma see big gains in money and efficiency. This makes it a smart choice.
Why Are Certified Six Sigma Professionals Paid So Much?
Certified Six Sigma professionals are important. Their skills help boost an organization's profits. By applying Six Sigma methodologies, they help companies:
- Boost Revenue: Better processes and quality help businesses operate smoothly and increase profits.
- Reduce Operational Costs: Identifying and eliminating waste reduces expenses significantly.
- Enhance Customer Satisfaction: Quality products and services encourage customer loyalty, supporting long-term growth.
Hiring Six Sigma experts usually brings in much more money than their salaries. Organizations offer competitive pay to attract and keep these professionals. Their work delivers measurable, high-impact results.
The Future of Being a Six Sigma Expert
Becoming a Six Sigma professional is a big change. It requires little upfront investment but offers great long-term rewards. The need for Six Sigma experts is rising in many industries because of these reasons:
- Six Sigma works in many fields, like manufacturing, IT, healthcare, and finance. Its methods apply to various industries.
- Companies constantly seek ways to improve efficiency, reduce costs, and enhance customer satisfaction. This creates steady job opportunities for Six Sigma professionals.
- High ROI for Professionals: The skills you gain help your career grow. They also boost job security and lead to higher pay.
Now is a great time to start your journey to become a Six Sigma professional. Begin your path to a great career by signing up for an online Six Sigma Green Belt certification course.
How to obtain Six Sigma certification?
We are an Education Technology company providing certification training courses to accelerate careers of working professionals worldwide. We impart training through instructor-led classroom workshops, instructor-led live virtual training sessions, and self-paced e-learning courses.
We have successfully conducted training sessions in 108 countries across the globe and enabled thousands of working professionals to enhance the scope of their careers.
Our enterprise training portfolio includes in-demand and globally recognized certification training courses in Project Management, Quality Management, Business Analysis, IT Service Management, Agile and Scrum, Cyber Security, Data Science, and Emerging Technologies. Download our Enterprise Training Catalog from https://www.icertglobal.com/corporate-training-for-enterprises.php and https://www.icertglobal.com/index.php
Popular Courses include:
-
Project Management: PMP, CAPM ,PMI RMP
-
Quality Management: Six Sigma Black Belt ,Lean Six Sigma Green Belt, Lean Management, Minitab,CMMI
-
Business Analysis: CBAP, CCBA, ECBA
-
Agile Training: PMI-ACP , CSM , CSPO
-
Scrum Training: CSM
-
DevOps
-
Program Management: PgMP
-
Cloud Technology: Exin Cloud Computing
-
Citrix Client Adminisration: Citrix Cloud Administration
The 10 top-paying certifications to target in 2025 are:
Conclusion
No matter where you work, a Six Sigma certification boosts your career chances. It opens doors to better-paying jobs. It also gives you skills to create real change in organizations.
Ready to boost your career? iCert Global 's Six Sigma Courses can help you stand out in today’s competitive job market. These courses help you:
- Expand your current skill set
- Improve your organization’s workflows
- Boost your career growth with recognized certifications
Contact Us For More Information:
Visit :www.icertglobal.com Email : 
Read More
Six Sigma is important for today’s businesses and organizations. Companies pay well for professionals with Six Sigma skills. These experts help improve workflows, product quality, and customer satisfaction. In this article, we will explore Lean Six Sigma salaries and the key factors that influence them.
What is Six Sigma?
Six Sigma is a set of principles and techniques. They help organizations reach their goals more efficiently. The main goal is to improve product quality and customer satisfaction. This, in turn, boosts revenue growth. Organizations use Six Sigma to increase profits. They improve customer experiences, simplify operations, and reduce product and process defects.
Key Components of Six Sigma Include:
- A Business Strategy: A clear plan to boost revenue, cut costs, and enhance operations.
- A Vision: Empowering management to envision a defect-free, productive, and positive work environment.
- A Benchmark: Setting performance standards helps us track and improve our process metrics.
- A Goal: Set clear objectives for the organization to reach using best practices.
- A Statistical Measure: Utilizing data-driven metrics to evaluate the organization’s success.
- A Problem-Solving Methodology: A systematic approach to identifying and addressing operational challenges.
Who is a Six Sigma Expert?
A Six Sigma expert is skilled in the Six Sigma method and its various techniques. You can gain this expertise by finishing a certified Six Sigma course or by practicing Six Sigma methods directly.
Six Sigma expertise is structured across different certification levels:
- Yellow Belt: Covers foundational knowledge of Six Sigma principles.
- Green Belt: Focuses on advanced tools and techniques for process improvement.
- Black Belt: Demonstrates mastery in leading projects and driving strategic improvements.
- Master Black Belt: This is the top level of Six Sigma expertise. They mentor Black Belts and oversee projects across the entire organization. Professionals at this level typically earn the highest Lean Six Sigma certified salaries.
Six Sigma Salary in 2025
Becoming a Six Sigma expert offers excellent career opportunities across various industries. Organizations aim to enhance efficiency. As a result, the need for Six Sigma professionals remains high. This strong need offers attractive salary prospects. Six Sigma-certified salaries differ by certification level, experience, job role, and employer. In this article, we’ll explore the Six Sigma salary landscape for 2025.
What is the Average Salary of a Six Sigma Professional?
Here’s an overview of the average salary for Six Sigma professionals:
- Hourly Salary: The average Six Sigma professional earns approximately $36 per hour.
- Monthly Salary: The average monthly salary is around $900.
- Annual Salary: On an annual basis, Six Sigma experts can expect to earn roughly $11,000.
Six Sigma Salary Based on Different Factors
1. Salary Based on Experience and Job Role
The salary of Six Sigma professionals depends a lot on their experience and job role. Here’s a breakdown of average monthly salaries for various job roles:
1.Salary Growth Based on Experience Level
Experience plays a crucial role in determining salary growth. The following table shows the increase in pay percentage compared to entry-level employees:
2. Six Sigma Salary Based on Employer/Company
The employer’s size, industry, and geographic location also influence Six Sigma salaries. The Six Sigma salary survey shows estimated annual salaries at top companies:
3. Six Sigma Salary Based on Certifications
Certification levels in Six Sigma play a significant role in salary potential. Here’s how different certifications impact earnings:
Certification
4. Six Sigma Salary: Based on Location
The average salary for Six Sigma professionals differs greatly by country. This change is due to demand, cost of living, and the presence of various industries. Here’s
a breakdown of the average annual salaries across different countries
This global comparison shows that the value of Six Sigma expertise varies by region. It depends on local market needs and economic conditions.
What Is the ROI for Adopting Six Sigma?
Using Six Sigma practices gives a strong return on investment (ROI). This includes both clear (hard) benefits and less obvious (soft) benefits.
Hard Returns:
- Operational Improvements: Enhanced efficiency through streamlined processes.
- Cost Reductions: Identifying and eliminating waste to reduce expenses.
- Revenue Growth: Optimizing product quality and service delivery, leading to increased sales.
Soft Returns:
- Cost Avoidance: Preventing future issues that could result in financial losses.
- Customer Loyalty: Improved customer satisfaction fosters long-term relationships.
- Employee Engagement: A culture of continuous improvement boosts productivity and morale.
Key Factors Contributing to Six Sigma ROI:
- Cultural Transformation: Fosters a customer-centric mindset and reduces operational waste.
- Strategic Alignment: Strengthens the connection between business strategies and task execution.
- Accelerated Change: Enhances the speed of process improvements, driving business growth.
- Employee Satisfaction: Motivated employees have clear goals, effective workflows, and receive recognition. This combination helps keep them longer and boosts their performance.
ROI Percentage Based on Six Sigma Methodologies:
Methodology |
Average ROI (%) |
Lean |
50% |
Lean Six Sigma |
48% |
Six Sigma |
33% |
Organizations that use Six Sigma see big gains in money and efficiency. This makes it a smart choice.
Why Are Certified Six Sigma Professionals Paid So Much?
Certified Six Sigma professionals are important. Their skills help boost an organization's profits. By applying Six Sigma methodologies, they help companies:
- Boost Revenue: Better processes and quality help businesses operate smoothly and increase profits.
- Reduce Operational Costs: Identifying and eliminating waste reduces expenses significantly.
- Enhance Customer Satisfaction: Quality products and services encourage customer loyalty, supporting long-term growth.
Hiring Six Sigma experts usually brings in much more money than their salaries. Organizations offer competitive pay to attract and keep these professionals. Their work delivers measurable, high-impact results.
The Future of Being a Six Sigma Expert
Becoming a Six Sigma professional is a big change. It requires little upfront investment but offers great long-term rewards. The need for Six Sigma experts is rising in many industries because of these reasons:
- Six Sigma works in many fields, like manufacturing, IT, healthcare, and finance. Its methods apply to various industries.
- Companies constantly seek ways to improve efficiency, reduce costs, and enhance customer satisfaction. This creates steady job opportunities for Six Sigma professionals.
- High ROI for Professionals: The skills you gain help your career grow. They also boost job security and lead to higher pay.
Now is a great time to start your journey to become a Six Sigma professional. Begin your path to a great career by signing up for an online Six Sigma Green Belt certification course.
How to obtain Six Sigma certification?
We are an Education Technology company providing certification training courses to accelerate careers of working professionals worldwide. We impart training through instructor-led classroom workshops, instructor-led live virtual training sessions, and self-paced e-learning courses.
We have successfully conducted training sessions in 108 countries across the globe and enabled thousands of working professionals to enhance the scope of their careers.
Our enterprise training portfolio includes in-demand and globally recognized certification training courses in Project Management, Quality Management, Business Analysis, IT Service Management, Agile and Scrum, Cyber Security, Data Science, and Emerging Technologies. Download our Enterprise Training Catalog from https://www.icertglobal.com/corporate-training-for-enterprises.php and https://www.icertglobal.com/index.php
Popular Courses include:
-
Project Management: PMP, CAPM ,PMI RMP
-
Quality Management: Six Sigma Black Belt ,Lean Six Sigma Green Belt, Lean Management, Minitab,CMMI
-
Business Analysis: CBAP, CCBA, ECBA
-
Agile Training: PMI-ACP , CSM , CSPO
-
Scrum Training: CSM
-
DevOps
-
Program Management: PgMP
-
Cloud Technology: Exin Cloud Computing
-
Citrix Client Adminisration: Citrix Cloud Administration
The 10 top-paying certifications to target in 2025 are:
Conclusion
No matter where you work, a Six Sigma certification boosts your career chances. It opens doors to better-paying jobs. It also gives you skills to create real change in organizations.
Ready to boost your career? iCert Global 's Six Sigma Courses can help you stand out in today’s competitive job market. These courses help you:
- Expand your current skill set
- Improve your organization’s workflows
- Boost your career growth with recognized certifications
Contact Us For More Information:
Visit :www.icertglobal.com Email :
Six Sigma Certification: Benefits, Cost, and Future Outlook
Six Sigma certification is a well-known credential. It empowers professionals in process management and quality improvement. As industries aim to boost efficiency and reduce defects, Six Sigma is key. It helps optimize workflows. To earn a Yellow, Green, or Black Belt, you must know its methods well.
This article is a complete guide to Six Sigma certification. It covers its levels, benefits, exam prep, and uses. Use this knowledge to grow your career and impact your workplace.
DMAIC and DMADV
Six Sigma uses two main methods: DMAIC and DMADV. Each method aims for specific process improvements.
DMAIC (Define, Measure, Analyze, Improve, Control)
DMAIC is a method to improve processes. It is data-driven. It finds and fixes defects to enhance quality and efficiency.
- Define – Clearly outline the problem, project scope, goals, and customer requirements.
- Measure – Collect and analyze data to establish a performance baseline and quantify issues.
- Analyze – Identify the root causes of defects and inefficiencies in the current process.
- Improve – Find and fix the root causes to enhance the process.
- Control – Establish monitoring systems to sustain improvements and maintain process efficiency over time.
DMAIC is best for optimizing workflows. It ensures consistent performance and quality.
DMADV (Define, Measure, Analyze, Design, Verify)
DMADV is a Six Sigma method. It is for designing new processes or products, not improving existing ones. It is often used in Lean Six Sigma when innovation or new design is needed. The five phases of DMADV are:
- Define – Outline the goals and needs for the new process or product. Also, list the deliverables.
- Measure – Identify and measure key aspects of the process or product. Focus on customer goals and requirements.
- Analyze – Evaluate design options. Select the best one based on data and customer needs.
- Design - Create the new process or product, with specs. It must meet customer requirements.
- Verify – Test the design with pilot runs or simulations. This will ensure it performs as intended and meets customer expectations.
Both DMAIC and DMADV are part of Six Sigma. DMAIC improves existing processes. DMADV develops new processes or products. Six Sigma Vs. Lean Six Sigma Certification
Focus
- Mainly aims to minimize process variations and eliminate defects.
- It merges Six Sigma's aim to reduce defects with Lean's goal to cut waste and improve flow.
Methodology
- Adheres to the DMAIC methodology (Define, Measure, Analyze, Improve, Control).
- Follows the DMAIC process, emphasizing Lean principles like waste reduction.
Approach
- A data-driven approach to identifying and solving problems.
- Uses a data-driven approach to enhance process efficiency by eliminating non-value-adding steps.
Goal
- Reduces defects and variations to enhance product or service quality.
- Reduces waste and variation, enhances quality, and accelerates process speed.
Industry Use
- Commonly used in manufacturing, healthcare, and service sectors.
- Extensively applied in manufacturing, healthcare, IT, and service industries to enhance efficiency and quality
Tools & Techniques
- Focuses on tools such as statistical analysis, root cause analysis, and control charts."
- "Utilizes Six Sigma tools along with Lean methodologies like 5S, value stream mapping, and Kaizen to reduce waste
Certification Levels
- Includes Yellow Belt, Green Belt, Black Belt, and Master Black Belt certifications.
Main Benefit
- Boosts efficiency, cuts waste, and enhances both quality and speed.
- Deciding Between Six Sigma and Lean Six Sigma Certifications.
Choosing Between Six Sigma and Lean Six Sigma Certifications
- If you want to focus purely on improving quality by minimizing defects, Six Sigma is the ideal choice.
- Use Lean Six Sigma to improve quality and efficiency. It cuts waste and speeds up processes. It offers a better, more complete solution. Six Sigma aims to reduce defects. Lean Six Sigma combines Lean principles with Six Sigma's focus on quality. It has a broader scope for process improvement.
Levels of Six Sigma Certification
1. Yellow Belt Certification
- Role: Supports project teams by knowing Six Sigma principles. Assists with data collection, process mapping, and problem-solving.
- Focus Areas: Intro to Six Sigma, and basic tools like Fishbone and Pareto.
- Skills Gained: A basic understanding of Six Sigma concepts. The ability to help with process improvement projects.
2. Green Belt Certification
- Role: Leads small to medium-sized Six Sigma projects. Supports larger projects led by Black Belts.
- Focus Areas: In-depth training in DMAIC, statistics, root cause analysis, and hypothesis testing.
- Skills Gained: Ability to lead process improvement projects. Proficient in using Six Sigma tools for data analysis and control.
3. Black Belt Certification
- Role: Leads large, complex projects and mentors Green Belts. Focuses on solving critical business problems and ensuring sustainable improvements.
- Focus Areas: Advanced statistical analysis, regression analysis, project leadership, and change management.
- Skills Gained: Advanced leadership, Six Sigma expertise, and ability to implement large-scale improvements.
4. Master Black Belt Certification
- Role: Mentor Black Belts and Green Belts. Develop Six Sigma strategies and drive change.
- Focus Areas: Enterprise-level project management, Six Sigma program development, and training leadership.
- Skills Gained: I have strategic leadership in Six Sigma and process optimization. I can also lead company-wide process improvements.
Enroll in our Certified Lean Six Sigma Black Belt Course. It will help you lead complex projects with advanced problem-solving skills. Enroll now and be the change!
Master Black Belt Certification
The Master Black Belt is the top Six Sigma certification. It emphasizes strategy, mentoring, and large-scale improvements across the organization. Professionals at this level are experts in Six Sigma. They are vital in setting the direction for enterprise-level Six Sigma initiatives.
Role
- Master Black Belts mentor and coach Black Belts and Green Belts.
- They must develop Six Sigma strategies and drive change. They must ensure projects align with business goals.
Focus Areas
- Enterprise-level project management and leadership for Six Sigma programs.
- Training and mentoring Black Belts and Green Belts in Six Sigma.
- Advanced data analysis methods. Also, integrate Six Sigma with Lean and TQM.
Skills Gained
- Expertise in Six Sigma strategy and the ability to lead enterprise-wide improvements.
- Mastery of advanced process optimization and data analysis techniques.
- Proficiency in training and mentoring other Six Sigma practitioners at all levels.
- Lead large-scale, strategic process improvements. Integrate Six Sigma with other methods.
The Role of Six Sigma in Quality Management
Six Sigma plays a significant role in enhancing quality management within organizations. Here are the key points that highlight its importance:
1. Six Sigma aims to reduce defects: It aims to improve product and service quality by reducing variations. It targets their root causes. By systematically identifying and eliminating inefficiencies, Six Sigma ensures high consistency and reliability.
2. Improving Process Efficiency: The methodology optimizes processes by reducing variability. This leads to faster production and cost savings. This enhanced efficiency boosts overall organizational performance.
3.Data-Driven Decision Making: Six Sigma relies heavily on statistical tools to analyze data. These insights lead to better decisions. They improve quality and performance, enabling better problem-solving.
4. Customer Satisfaction: Six Sigma ensures better reliability and quality. This boosts customer satisfaction and loyalty. It does this by constantly refining processes and products.
5. Cost Reduction: Six Sigma aims to reduce waste, defects, and rework. It cuts costs, boosts efficiency, and increases profits.
Industry Applications of Six Sigma
- Six Sigma's versatility and data-driven approach make it valuable across numerous industries. Here’s how it is applied to drive efficiency, quality, and process optimization:
- Manufacturing Six Sigma was born in the manufacturing sector. It is a key tool for reducing defects and improving processes. It also enhances product quality. By minimizing variability, Six Sigma helps reduce costs and boosts operational efficiency.
- In healthcare, Six Sigma improves patient care. It reduces medical errors, speeds up billing, and boosts hospital efficiency. These improvements help enhance the quality of care while also reducing operational costs.
- Finance and Banking Six Sigma is used in banks. It reduces errors, improves customer service, and streamlines back-office work. It boosts accuracy in financial transactions. It helps institutions comply with regulations.
- In IT, Six Sigma aims to improve service delivery. It seeks to reduce downtime, enhance software development, and optimize support workflows. These improvements lead to more reliable IT services and better overall performance.
- Supply Chain and Logistics Six Sigma improves efficiency in supply chain management. It does this by enhancing inventory control and reducing shipping errors. It shortens lead times and optimizes the whole process. This leads to reduced costs and smoother operations.
Top Reasons to Get Six Sigma Certification
Six Sigma certification benefits both individuals and their employers. Here are some of the top reasons to pursue Lean Six Sigma certification:
-
- A Six Sigma certification can greatly boost your career. It opens doors to higher-level roles in process improvement and quality management. It applies to all industries, including leadership.
- Enhanced Skills Certification equips professionals with advanced problem-solving and project management skills. It makes them very valuable in a competitive job market.
- Higher Earning Potential Certified Six Sigma professionals often earn higher salaries. Their skills in process optimization, cost reduction, and efficiency improvements drive this.
- Improved Efficiency. Six Sigma training helps professionals spot inefficiencies in business processes. It reduces waste and optimizes operations. This makes businesses more efficient and effective.
- Increased Job Opportunities Many organizations prefer to hire Six Sigma-certified professionals. This is especially true in manufacturing, healthcare, IT, and finance. Those fields require process optimization.
Benefits of Obtaining Six Sigma Certification
Six Sigma certification has many benefits. They include career growth and improved efficiency for organizations. Here are the key benefits:
1. Career Advancement Six Sigma certification is highly valued across industries. It often plays a major role in promotions. It shows your skills in quality and efficiency. This makes you a better candidate for promotion.
2. Certified Six Sigma professionals tend to earn more than their non-certified peers. Six Sigma training gives specialized skills that are in high demand. This leads to better job opportunities and pay.
3. Improved Business Processes. Six Sigma cuts waste, boosts efficiency, and improves quality. These process improvements can cut costs and boost profits. They will benefit organizations in the long run.
4. Better Problem-Solving Skills. Six Sigma training gives you tools to analyze processes. You'll know their performance in depth. This lets you find, analyze, and fix quality issues. It makes you a valuable asset in solving problems.
5. Competitive Advantage Businesses with Six Sigma-certified employees gain a competitive edge. It shows a commitment to improvement, excellence, and quality. These are vital in today's competitive market.
6.Global Recognition Six Sigma is a globally recognized certification. It proves your skills in the global market. It helps you find jobs in many industries and countries. It boosts your career mobility.
7. skills essential for managing teams and projects. It prepares you for leadership roles. It gives you the experience needed for higher responsibilities.
8.Cultural Impact Six Sigma-certified professionals often drive a culture of improvement in organizations. They improve performance and engagement by refining processes. This boosts long-term success.
How to Choose the Right Six Sigma Training Provider
When choosing a Six Sigma training provider, consider these factors. They will help ensure you get a quality education:
1. Accreditation
- Check that the provider is accredited by IASSC or ASQ. Accredited providers meet specific standards and are trusted in the industry.
2. Course Content
- Check that the curriculum covers all key Six Sigma methods, tools, and real-world uses. A good program should cover DMAIC and statistical analysis.
3. Instructor Expertise
- Look for providers with experienced, certified instructors who have practical industry knowledge. Instructors must be certified and have real-world Six Sigma experience.
4. Certification Levels
- Choose a provider with the right certification, like Yellow, Green, or Black Belt. Some providers also offer advanced certifications like Master Black Belt.
5. Flexible Learning Options
- Choose providers that offer online, in-person, or hybrid courses. They will fit your schedule and learning style.
- Flexibility lets you learn at your own pace. You can balance work and other commitments.
Tips for Passing the Six Sigma Exam
To maximize your chances of passing the Six Sigma certification exam, here are some tips:
1. Understand the DMAIC Methodology
- Familiarize yourself with the DMAIC methodology, as it is the foundation of Six Sigma. Make sure you understand each stage and its application in real-world scenarios.
2. Focus on Key Tools and Techniques
- Study key tools and techniques, like control charts and root cause analysis. Also, learn process mapping. These are often integral to the exam.
3. Study Statistics and Data Analysis
- Six Sigma requires strong analytical skills. Study statistics and data analysis concepts thoroughly to solve quantitative problems effectively.
4. Practice with Mock Exams
- Take mock exams to familiarize yourself with the exam format. Timed practice will help you manage your time on the real exam.
5. Use Real-life Case Studies
- Review case studies to see how to use Six Sigma tools. This will enhance your ability to apply concepts to different scenarios.
6. Join Study Groups or Forums
- Join study groups or online forums to collaborate with other learners. Clarify doubts and share insights to deepen your understanding.
7. Review the Body of Knowledge (BoK)
- Review the Body of Knowledge (BoK) from your certifying body. This outlines all the topics covered in the exam.
8. Master Definitions and Key Terms
- Many exam questions test basic definitions and key terms. Study these thoroughly. They are vital for a strong exam foundation.
To get Six Sigma certification, use good study strategies and a top training provider.
Course Highlights:
- Master the DMAIC Methodology: Use its five phases to solve business problems.
- Leadership and Team Management: Learn to manage team dynamics and lead projects. Do it with confidence.
- Strategic Tools for Performance Measurement: Use key tools to measure and analyze performance. This will drive improvements in business processes.
- Hands-on Experience: The course includes real-world projects and simulations. They let you practice your skills while learning the theory.
- Global Recognition: This course prepares you for Lean Six Sigma Green Belt certification. It aligns with the IASSC exam. It will earn you global recognition.
- Practical Application: Use your learning in real-world scenarios. This will prepare you for any professional challenge.
How to obtain Six Sigma certification?
We are an Education Technology company providing certification training courses to accelerate careers of working professionals worldwide. We impart training through instructor-led classroom workshops, instructor-led live virtual training sessions, and self-paced e-learning courses.
We have successfully conducted training sessions in 108 countries across the globe and enabled thousands of working professionals to enhance the scope of their careers.
Our enterprise training portfolio includes in-demand and globally recognized certification training courses in Project Management, Quality Management, Business Analysis, IT Service Management, Agile and Scrum, Cyber Security, Data Science, and Emerging Technologies. Download our Enterprise Training Catalog from https://www.icertglobal.com/corporate-training-for-enterprises.php and https://www.icertglobal.com/index.php
Popular Courses include:
-
Project Management: PMP, CAPM ,PMI RMP
-
Quality Management: Six Sigma Black Belt ,Lean Six Sigma Green Belt, Lean Management, Minitab,CMMI
-
Business Analysis: CBAP, CCBA, ECBA
-
Agile Training: PMI-ACP , CSM , CSPO
-
Scrum Training: CSM
-
DevOps
-
Program Management: PgMP
-
Cloud Technology: Exin Cloud Computing
-
Citrix Client Adminisration: Citrix Cloud Administration
The 10 top-paying certifications to target in 2025 are:
Conclusion
Six Sigma certification is a powerful tool for professionals seeking to advance their careers and enhance organizational efficiency. By mastering methodologies like DMAIC and DMADV, individuals can optimize processes, reduce defects, and boost customer satisfaction. Whether pursuing Yellow, Green, Black, or Master Black Belt certifications, each level offers valuable skills for improving business performance.
Contact Us For More Information:
Visit :www.icertglobal.com Email : 
Read More
Six Sigma certification is a well-known credential. It empowers professionals in process management and quality improvement. As industries aim to boost efficiency and reduce defects, Six Sigma is key. It helps optimize workflows. To earn a Yellow, Green, or Black Belt, you must know its methods well.
This article is a complete guide to Six Sigma certification. It covers its levels, benefits, exam prep, and uses. Use this knowledge to grow your career and impact your workplace.
DMAIC and DMADV
Six Sigma uses two main methods: DMAIC and DMADV. Each method aims for specific process improvements.
DMAIC (Define, Measure, Analyze, Improve, Control)
DMAIC is a method to improve processes. It is data-driven. It finds and fixes defects to enhance quality and efficiency.
- Define – Clearly outline the problem, project scope, goals, and customer requirements.
- Measure – Collect and analyze data to establish a performance baseline and quantify issues.
- Analyze – Identify the root causes of defects and inefficiencies in the current process.
- Improve – Find and fix the root causes to enhance the process.
- Control – Establish monitoring systems to sustain improvements and maintain process efficiency over time.
DMAIC is best for optimizing workflows. It ensures consistent performance and quality.
DMADV (Define, Measure, Analyze, Design, Verify)
DMADV is a Six Sigma method. It is for designing new processes or products, not improving existing ones. It is often used in Lean Six Sigma when innovation or new design is needed. The five phases of DMADV are:
- Define – Outline the goals and needs for the new process or product. Also, list the deliverables.
- Measure – Identify and measure key aspects of the process or product. Focus on customer goals and requirements.
- Analyze – Evaluate design options. Select the best one based on data and customer needs.
- Design - Create the new process or product, with specs. It must meet customer requirements.
- Verify – Test the design with pilot runs or simulations. This will ensure it performs as intended and meets customer expectations.
Both DMAIC and DMADV are part of Six Sigma. DMAIC improves existing processes. DMADV develops new processes or products. Six Sigma Vs. Lean Six Sigma Certification
Focus
- Mainly aims to minimize process variations and eliminate defects.
- It merges Six Sigma's aim to reduce defects with Lean's goal to cut waste and improve flow.
Methodology
- Adheres to the DMAIC methodology (Define, Measure, Analyze, Improve, Control).
- Follows the DMAIC process, emphasizing Lean principles like waste reduction.
Approach
- A data-driven approach to identifying and solving problems.
- Uses a data-driven approach to enhance process efficiency by eliminating non-value-adding steps.
Goal
- Reduces defects and variations to enhance product or service quality.
- Reduces waste and variation, enhances quality, and accelerates process speed.
Industry Use
- Commonly used in manufacturing, healthcare, and service sectors.
- Extensively applied in manufacturing, healthcare, IT, and service industries to enhance efficiency and quality
Tools & Techniques
- Focuses on tools such as statistical analysis, root cause analysis, and control charts."
- "Utilizes Six Sigma tools along with Lean methodologies like 5S, value stream mapping, and Kaizen to reduce waste
Certification Levels
- Includes Yellow Belt, Green Belt, Black Belt, and Master Black Belt certifications.
Main Benefit
- Boosts efficiency, cuts waste, and enhances both quality and speed.
- Deciding Between Six Sigma and Lean Six Sigma Certifications.
Choosing Between Six Sigma and Lean Six Sigma Certifications
- If you want to focus purely on improving quality by minimizing defects, Six Sigma is the ideal choice.
- Use Lean Six Sigma to improve quality and efficiency. It cuts waste and speeds up processes. It offers a better, more complete solution. Six Sigma aims to reduce defects. Lean Six Sigma combines Lean principles with Six Sigma's focus on quality. It has a broader scope for process improvement.
Levels of Six Sigma Certification
1. Yellow Belt Certification
- Role: Supports project teams by knowing Six Sigma principles. Assists with data collection, process mapping, and problem-solving.
- Focus Areas: Intro to Six Sigma, and basic tools like Fishbone and Pareto.
- Skills Gained: A basic understanding of Six Sigma concepts. The ability to help with process improvement projects.
2. Green Belt Certification
- Role: Leads small to medium-sized Six Sigma projects. Supports larger projects led by Black Belts.
- Focus Areas: In-depth training in DMAIC, statistics, root cause analysis, and hypothesis testing.
- Skills Gained: Ability to lead process improvement projects. Proficient in using Six Sigma tools for data analysis and control.
3. Black Belt Certification
- Role: Leads large, complex projects and mentors Green Belts. Focuses on solving critical business problems and ensuring sustainable improvements.
- Focus Areas: Advanced statistical analysis, regression analysis, project leadership, and change management.
- Skills Gained: Advanced leadership, Six Sigma expertise, and ability to implement large-scale improvements.
4. Master Black Belt Certification
- Role: Mentor Black Belts and Green Belts. Develop Six Sigma strategies and drive change.
- Focus Areas: Enterprise-level project management, Six Sigma program development, and training leadership.
- Skills Gained: I have strategic leadership in Six Sigma and process optimization. I can also lead company-wide process improvements.
Enroll in our Certified Lean Six Sigma Black Belt Course. It will help you lead complex projects with advanced problem-solving skills. Enroll now and be the change!
Master Black Belt Certification
The Master Black Belt is the top Six Sigma certification. It emphasizes strategy, mentoring, and large-scale improvements across the organization. Professionals at this level are experts in Six Sigma. They are vital in setting the direction for enterprise-level Six Sigma initiatives.
Role
- Master Black Belts mentor and coach Black Belts and Green Belts.
- They must develop Six Sigma strategies and drive change. They must ensure projects align with business goals.
Focus Areas
- Enterprise-level project management and leadership for Six Sigma programs.
- Training and mentoring Black Belts and Green Belts in Six Sigma.
- Advanced data analysis methods. Also, integrate Six Sigma with Lean and TQM.
Skills Gained
- Expertise in Six Sigma strategy and the ability to lead enterprise-wide improvements.
- Mastery of advanced process optimization and data analysis techniques.
- Proficiency in training and mentoring other Six Sigma practitioners at all levels.
- Lead large-scale, strategic process improvements. Integrate Six Sigma with other methods.
The Role of Six Sigma in Quality Management
Six Sigma plays a significant role in enhancing quality management within organizations. Here are the key points that highlight its importance:
1. Six Sigma aims to reduce defects: It aims to improve product and service quality by reducing variations. It targets their root causes. By systematically identifying and eliminating inefficiencies, Six Sigma ensures high consistency and reliability.
2. Improving Process Efficiency: The methodology optimizes processes by reducing variability. This leads to faster production and cost savings. This enhanced efficiency boosts overall organizational performance.
3.Data-Driven Decision Making: Six Sigma relies heavily on statistical tools to analyze data. These insights lead to better decisions. They improve quality and performance, enabling better problem-solving.
4. Customer Satisfaction: Six Sigma ensures better reliability and quality. This boosts customer satisfaction and loyalty. It does this by constantly refining processes and products.
5. Cost Reduction: Six Sigma aims to reduce waste, defects, and rework. It cuts costs, boosts efficiency, and increases profits.
Industry Applications of Six Sigma
- Six Sigma's versatility and data-driven approach make it valuable across numerous industries. Here’s how it is applied to drive efficiency, quality, and process optimization:
- Manufacturing Six Sigma was born in the manufacturing sector. It is a key tool for reducing defects and improving processes. It also enhances product quality. By minimizing variability, Six Sigma helps reduce costs and boosts operational efficiency.
- In healthcare, Six Sigma improves patient care. It reduces medical errors, speeds up billing, and boosts hospital efficiency. These improvements help enhance the quality of care while also reducing operational costs.
- Finance and Banking Six Sigma is used in banks. It reduces errors, improves customer service, and streamlines back-office work. It boosts accuracy in financial transactions. It helps institutions comply with regulations.
- In IT, Six Sigma aims to improve service delivery. It seeks to reduce downtime, enhance software development, and optimize support workflows. These improvements lead to more reliable IT services and better overall performance.
- Supply Chain and Logistics Six Sigma improves efficiency in supply chain management. It does this by enhancing inventory control and reducing shipping errors. It shortens lead times and optimizes the whole process. This leads to reduced costs and smoother operations.
Top Reasons to Get Six Sigma Certification
Six Sigma certification benefits both individuals and their employers. Here are some of the top reasons to pursue Lean Six Sigma certification:
-
- A Six Sigma certification can greatly boost your career. It opens doors to higher-level roles in process improvement and quality management. It applies to all industries, including leadership.
- Enhanced Skills Certification equips professionals with advanced problem-solving and project management skills. It makes them very valuable in a competitive job market.
- Higher Earning Potential Certified Six Sigma professionals often earn higher salaries. Their skills in process optimization, cost reduction, and efficiency improvements drive this.
- Improved Efficiency. Six Sigma training helps professionals spot inefficiencies in business processes. It reduces waste and optimizes operations. This makes businesses more efficient and effective.
- Increased Job Opportunities Many organizations prefer to hire Six Sigma-certified professionals. This is especially true in manufacturing, healthcare, IT, and finance. Those fields require process optimization.
Benefits of Obtaining Six Sigma Certification
Six Sigma certification has many benefits. They include career growth and improved efficiency for organizations. Here are the key benefits:
1. Career Advancement Six Sigma certification is highly valued across industries. It often plays a major role in promotions. It shows your skills in quality and efficiency. This makes you a better candidate for promotion.
2. Certified Six Sigma professionals tend to earn more than their non-certified peers. Six Sigma training gives specialized skills that are in high demand. This leads to better job opportunities and pay.
3. Improved Business Processes. Six Sigma cuts waste, boosts efficiency, and improves quality. These process improvements can cut costs and boost profits. They will benefit organizations in the long run.
4. Better Problem-Solving Skills. Six Sigma training gives you tools to analyze processes. You'll know their performance in depth. This lets you find, analyze, and fix quality issues. It makes you a valuable asset in solving problems.
5. Competitive Advantage Businesses with Six Sigma-certified employees gain a competitive edge. It shows a commitment to improvement, excellence, and quality. These are vital in today's competitive market.
6.Global Recognition Six Sigma is a globally recognized certification. It proves your skills in the global market. It helps you find jobs in many industries and countries. It boosts your career mobility.
7. skills essential for managing teams and projects. It prepares you for leadership roles. It gives you the experience needed for higher responsibilities.
8.Cultural Impact Six Sigma-certified professionals often drive a culture of improvement in organizations. They improve performance and engagement by refining processes. This boosts long-term success.
How to Choose the Right Six Sigma Training Provider
When choosing a Six Sigma training provider, consider these factors. They will help ensure you get a quality education:
1. Accreditation
- Check that the provider is accredited by IASSC or ASQ. Accredited providers meet specific standards and are trusted in the industry.
2. Course Content
- Check that the curriculum covers all key Six Sigma methods, tools, and real-world uses. A good program should cover DMAIC and statistical analysis.
3. Instructor Expertise
- Look for providers with experienced, certified instructors who have practical industry knowledge. Instructors must be certified and have real-world Six Sigma experience.
4. Certification Levels
- Choose a provider with the right certification, like Yellow, Green, or Black Belt. Some providers also offer advanced certifications like Master Black Belt.
5. Flexible Learning Options
- Choose providers that offer online, in-person, or hybrid courses. They will fit your schedule and learning style.
- Flexibility lets you learn at your own pace. You can balance work and other commitments.
Tips for Passing the Six Sigma Exam
To maximize your chances of passing the Six Sigma certification exam, here are some tips:
1. Understand the DMAIC Methodology
- Familiarize yourself with the DMAIC methodology, as it is the foundation of Six Sigma. Make sure you understand each stage and its application in real-world scenarios.
2. Focus on Key Tools and Techniques
- Study key tools and techniques, like control charts and root cause analysis. Also, learn process mapping. These are often integral to the exam.
3. Study Statistics and Data Analysis
- Six Sigma requires strong analytical skills. Study statistics and data analysis concepts thoroughly to solve quantitative problems effectively.
4. Practice with Mock Exams
- Take mock exams to familiarize yourself with the exam format. Timed practice will help you manage your time on the real exam.
5. Use Real-life Case Studies
- Review case studies to see how to use Six Sigma tools. This will enhance your ability to apply concepts to different scenarios.
6. Join Study Groups or Forums
- Join study groups or online forums to collaborate with other learners. Clarify doubts and share insights to deepen your understanding.
7. Review the Body of Knowledge (BoK)
- Review the Body of Knowledge (BoK) from your certifying body. This outlines all the topics covered in the exam.
8. Master Definitions and Key Terms
- Many exam questions test basic definitions and key terms. Study these thoroughly. They are vital for a strong exam foundation.
To get Six Sigma certification, use good study strategies and a top training provider.
Course Highlights:
- Master the DMAIC Methodology: Use its five phases to solve business problems.
- Leadership and Team Management: Learn to manage team dynamics and lead projects. Do it with confidence.
- Strategic Tools for Performance Measurement: Use key tools to measure and analyze performance. This will drive improvements in business processes.
- Hands-on Experience: The course includes real-world projects and simulations. They let you practice your skills while learning the theory.
- Global Recognition: This course prepares you for Lean Six Sigma Green Belt certification. It aligns with the IASSC exam. It will earn you global recognition.
- Practical Application: Use your learning in real-world scenarios. This will prepare you for any professional challenge.
How to obtain Six Sigma certification?
We are an Education Technology company providing certification training courses to accelerate careers of working professionals worldwide. We impart training through instructor-led classroom workshops, instructor-led live virtual training sessions, and self-paced e-learning courses.
We have successfully conducted training sessions in 108 countries across the globe and enabled thousands of working professionals to enhance the scope of their careers.
Our enterprise training portfolio includes in-demand and globally recognized certification training courses in Project Management, Quality Management, Business Analysis, IT Service Management, Agile and Scrum, Cyber Security, Data Science, and Emerging Technologies. Download our Enterprise Training Catalog from https://www.icertglobal.com/corporate-training-for-enterprises.php and https://www.icertglobal.com/index.php
Popular Courses include:
-
Project Management: PMP, CAPM ,PMI RMP
-
Quality Management: Six Sigma Black Belt ,Lean Six Sigma Green Belt, Lean Management, Minitab,CMMI
-
Business Analysis: CBAP, CCBA, ECBA
-
Agile Training: PMI-ACP , CSM , CSPO
-
Scrum Training: CSM
-
DevOps
-
Program Management: PgMP
-
Cloud Technology: Exin Cloud Computing
-
Citrix Client Adminisration: Citrix Cloud Administration
The 10 top-paying certifications to target in 2025 are:
Conclusion
Six Sigma certification is a powerful tool for professionals seeking to advance their careers and enhance organizational efficiency. By mastering methodologies like DMAIC and DMADV, individuals can optimize processes, reduce defects, and boost customer satisfaction. Whether pursuing Yellow, Green, Black, or Master Black Belt certifications, each level offers valuable skills for improving business performance.
Contact Us For More Information:
Visit :www.icertglobal.com Email :
Kick start Your Career with Lean Six Sigma Yellow Belt!
In today's fast-changing world, businesses want to improve. They seek to save resources and provide better value to customers. Lean Six Sigma is a popular system that helps businesses do just that. It’s like a toolbox with special tools to fix problems, save time, and improve quality.
Lean Six Sigma has different levels, or “belts,” like in karate! The Yellow Belt is the starting level, where you learn the basics. This blog will explain Lean Six Sigma and the Yellow Belt. It will cover what you'll learn and how it helps people and organizations grow.
What Is Lean Six Sigma?
Lean Six Sigma is a mix of two great methods:
- Lean – Focuses on reducing waste in processes. Waste is anything that doesn't add value to the customer. This includes extra materials, waiting times, and defects.
- Six Sigma aims to improve quality by reducing errors and variability.
Together, these methods make processes faster, better, and more efficient.
What Is a Yellow Belt Certification?
The Yellow Belt is the first level of Lean Six Sigma. It’s like learning the basics of a new skill, where you understand how to use the tools and work as part of a team.
Yellow Belt holders support improvement efforts. They don't lead big projects. They work alongside more advanced levels like Green Belts and Black Belts.
What You Learn in Yellow Belt Training
Yellow Belt training focuses on four main things:
- Basic Concepts – You’ll learn the core ideas of Lean and Six Sigma, including the DMAIC process:
- Define: Find the problem and set clear goals.
- Measure: Collect data to understand the current situation.
- Analyze: Figure out what’s causing the problem.
- Improve: Make changes to fix the problem.
- Control: Keep the improvements going over time.
- Identifying Waste – You’ll learn to spot waste like waiting, overproduction, and defects.
- Working with Teams – Yellow Belts help their teams. They collect data, give ideas, and support improvement efforts.
- Problem-Solving Tools – You’ll use simple tools like:
- Process Maps: Diagrams that show how a process works.
- Fishbone Diagrams: Charts to find the root cause of a problem.
- Pareto Charts: Bar graphs to focus on the most important issues.
Key Ideas of Yellow Belt Training
- Customer First – Always think about what the customer wants. Every improvement should make things better for them.
- Remove Waste – Learn to spot and remove the 7 types of waste:
- Overproduction
- Waiting
- Transport (moving things unnecessarily)
- Over-processing (doing more work than needed)
- Extra Inventory
- Unnecessary Motion
- Defects (mistakes in products or services)
- Reduce Variation – Inconsistent processes cause problems. You’ll learn how to make processes more reliable.
- Use Data, Not Guesswork – Decisions should be based on facts and data, not assumptions.
How Yellow Belt Holders Help
Yellow Belt holders may not lead projects, but they are very important for team success. Here’s how they contribute:
- Helping on Projects – They help Green and Black Belts. They gather data and make charts. They also share insights.
- Promoting Change – They urge their teams to suggest small ways to improve. These can make a big difference.
- Daily Improvements – They use Lean Six Sigma in their work to solve small problems and save time.
Tools You’ll Learn
Yellow Belt training teaches easy-to-use tools like:
- Process Maps: Show every step in a process to find areas to improve.
- Fishbone Diagrams: Help you discover the root causes of problems.
- Pareto Charts: Help prioritize what issues to fix first.
- 5 Whys: A method to keep asking “Why?” until you find the real cause of a problem.
- SIPOC Diagrams: Show how suppliers, inputs, processes, outputs, and customers connect.
Benefits of a Yellow Belt Certification
For Individuals:
- Problem-Solving Skills – You’ll learn to solve problems step by step, which is useful in any job.
- Career Growth: Companies value Lean Six Sigma skills. A Yellow Belt can open doors to better jobs.
- Teamwork – You’ll learn how to work well with others on projects.
- Personal Growth – These tools aren’t just for work—they can help you stay organized in daily life too!
For Organizations:
- Better Processes – Yellow Belts help make work faster and more efficient.
- Save Money – Reducing waste and improving quality saves businesses a lot of money.
- Continuous Improvement – Yellow Belts motivate their teams to improve. This builds a culture of excellence.
- Happier Customers – With better processes, customers get better products and services.
Steps to Get Certified
Here’s how to get your Yellow Belt certification:
- Join a Training Program – Many schools, organizations, and websites offer Yellow Belt courses. Make sure the program is reliable.
- Learn and Practice – In training, you'll learn concepts and tools. You'll practice things like process mapping and problem-solving.
- Pass the Exam – Most certifications require you to pass a test to prove your knowledge.
- Apply What You Learn - After certification, use your new skills at work or in daily life.
How to obtain Lean Six Sigma Yellow Belt certification?
We are an Education Technology company providing certification training courses to accelerate careers of working professionals worldwide. We impart training through instructor-led classroom workshops, instructor-led live virtual training sessions, and self-paced e-learning courses.
We have successfully conducted training sessions in 108 countries across the globe and enabled thousands of working professionals to enhance the scope of their careers.
Our enterprise training portfolio includes in-demand and globally recognized certification training courses in Project Management, Quality Management, Business Analysis, IT Service Management, Agile and Scrum, Cyber Security, Data Science, and Emerging Technologies. Download our Enterprise Training Catalog from https://www.icertglobal.com/corporate-training-for-enterprises.php and https://www.icertglobal.com/index.php
Popular Courses include:
-
Project Management: PMP, CAPM ,PMI RMP
-
Quality Management: Six Sigma Black Belt ,Lean Six Sigma Green Belt, Lean Management, Minitab,CMMI
-
Business Analysis: CBAP, CCBA, ECBA
-
Agile Training: PMI-ACP , CSM , CSPO
-
Scrum Training: CSM
-
DevOps
-
Program Management: PgMP
-
Cloud Technology: Exin Cloud Computing
-
Citrix Client Adminisration: Citrix Cloud Administration
The 10 top-paying certifications to target in 2025 are:
conclusion
The best first step to improve processes is the Lean Six Sigma Yellow Belt certification. It teaches valuable skills that help both individuals and organizations grow. Whether you're starting your career or want to do more at work, the Yellow Belt gives you the tools to succeed. Start your Lean Six Sigma journey today. Be the reason your team and organization achieve excellence!
Contact Us For More Information:
Visit :www.icertglobal.com Email : 
Read More
In today's fast-changing world, businesses want to improve. They seek to save resources and provide better value to customers. Lean Six Sigma is a popular system that helps businesses do just that. It’s like a toolbox with special tools to fix problems, save time, and improve quality.
Lean Six Sigma has different levels, or “belts,” like in karate! The Yellow Belt is the starting level, where you learn the basics. This blog will explain Lean Six Sigma and the Yellow Belt. It will cover what you'll learn and how it helps people and organizations grow.
What Is Lean Six Sigma?
Lean Six Sigma is a mix of two great methods:
- Lean – Focuses on reducing waste in processes. Waste is anything that doesn't add value to the customer. This includes extra materials, waiting times, and defects.
- Six Sigma aims to improve quality by reducing errors and variability.
Together, these methods make processes faster, better, and more efficient.
What Is a Yellow Belt Certification?
The Yellow Belt is the first level of Lean Six Sigma. It’s like learning the basics of a new skill, where you understand how to use the tools and work as part of a team.
Yellow Belt holders support improvement efforts. They don't lead big projects. They work alongside more advanced levels like Green Belts and Black Belts.
What You Learn in Yellow Belt Training
Yellow Belt training focuses on four main things:
- Basic Concepts – You’ll learn the core ideas of Lean and Six Sigma, including the DMAIC process:
- Define: Find the problem and set clear goals.
- Measure: Collect data to understand the current situation.
- Analyze: Figure out what’s causing the problem.
- Improve: Make changes to fix the problem.
- Control: Keep the improvements going over time.
- Identifying Waste – You’ll learn to spot waste like waiting, overproduction, and defects.
- Working with Teams – Yellow Belts help their teams. They collect data, give ideas, and support improvement efforts.
- Problem-Solving Tools – You’ll use simple tools like:
- Process Maps: Diagrams that show how a process works.
- Fishbone Diagrams: Charts to find the root cause of a problem.
- Pareto Charts: Bar graphs to focus on the most important issues.
Key Ideas of Yellow Belt Training
- Customer First – Always think about what the customer wants. Every improvement should make things better for them.
- Remove Waste – Learn to spot and remove the 7 types of waste:
- Overproduction
- Waiting
- Transport (moving things unnecessarily)
- Over-processing (doing more work than needed)
- Extra Inventory
- Unnecessary Motion
- Defects (mistakes in products or services)
- Reduce Variation – Inconsistent processes cause problems. You’ll learn how to make processes more reliable.
- Use Data, Not Guesswork – Decisions should be based on facts and data, not assumptions.
How Yellow Belt Holders Help
Yellow Belt holders may not lead projects, but they are very important for team success. Here’s how they contribute:
- Helping on Projects – They help Green and Black Belts. They gather data and make charts. They also share insights.
- Promoting Change – They urge their teams to suggest small ways to improve. These can make a big difference.
- Daily Improvements – They use Lean Six Sigma in their work to solve small problems and save time.
Tools You’ll Learn
Yellow Belt training teaches easy-to-use tools like:
- Process Maps: Show every step in a process to find areas to improve.
- Fishbone Diagrams: Help you discover the root causes of problems.
- Pareto Charts: Help prioritize what issues to fix first.
- 5 Whys: A method to keep asking “Why?” until you find the real cause of a problem.
- SIPOC Diagrams: Show how suppliers, inputs, processes, outputs, and customers connect.
Benefits of a Yellow Belt Certification
For Individuals:
- Problem-Solving Skills – You’ll learn to solve problems step by step, which is useful in any job.
- Career Growth: Companies value Lean Six Sigma skills. A Yellow Belt can open doors to better jobs.
- Teamwork – You’ll learn how to work well with others on projects.
- Personal Growth – These tools aren’t just for work—they can help you stay organized in daily life too!
For Organizations:
- Better Processes – Yellow Belts help make work faster and more efficient.
- Save Money – Reducing waste and improving quality saves businesses a lot of money.
- Continuous Improvement – Yellow Belts motivate their teams to improve. This builds a culture of excellence.
- Happier Customers – With better processes, customers get better products and services.
Steps to Get Certified
Here’s how to get your Yellow Belt certification:
- Join a Training Program – Many schools, organizations, and websites offer Yellow Belt courses. Make sure the program is reliable.
- Learn and Practice – In training, you'll learn concepts and tools. You'll practice things like process mapping and problem-solving.
- Pass the Exam – Most certifications require you to pass a test to prove your knowledge.
- Apply What You Learn - After certification, use your new skills at work or in daily life.
How to obtain Lean Six Sigma Yellow Belt certification?
We are an Education Technology company providing certification training courses to accelerate careers of working professionals worldwide. We impart training through instructor-led classroom workshops, instructor-led live virtual training sessions, and self-paced e-learning courses.
We have successfully conducted training sessions in 108 countries across the globe and enabled thousands of working professionals to enhance the scope of their careers.
Our enterprise training portfolio includes in-demand and globally recognized certification training courses in Project Management, Quality Management, Business Analysis, IT Service Management, Agile and Scrum, Cyber Security, Data Science, and Emerging Technologies. Download our Enterprise Training Catalog from https://www.icertglobal.com/corporate-training-for-enterprises.php and https://www.icertglobal.com/index.php
Popular Courses include:
-
Project Management: PMP, CAPM ,PMI RMP
-
Quality Management: Six Sigma Black Belt ,Lean Six Sigma Green Belt, Lean Management, Minitab,CMMI
-
Business Analysis: CBAP, CCBA, ECBA
-
Agile Training: PMI-ACP , CSM , CSPO
-
Scrum Training: CSM
-
DevOps
-
Program Management: PgMP
-
Cloud Technology: Exin Cloud Computing
-
Citrix Client Adminisration: Citrix Cloud Administration
The 10 top-paying certifications to target in 2025 are:
conclusion
The best first step to improve processes is the Lean Six Sigma Yellow Belt certification. It teaches valuable skills that help both individuals and organizations grow. Whether you're starting your career or want to do more at work, the Yellow Belt gives you the tools to succeed. Start your Lean Six Sigma journey today. Be the reason your team and organization achieve excellence!
Contact Us For More Information:
Visit :www.icertglobal.com Email :
Boost Your Skills and Career with Lean Six Sigma Combo!
In today's competitive business world, firms must excel to grow and satisfy customers. Organizations in all industries seek to improve processes, reduce waste, and increase efficiency. These goals are at the heart of Lean Six Sigma. Both Green Belt and Black Belt certifications are very valuable. But, a combined Lean Six Sigma Green and Black Belt certification is best. It is a complete path to mastering process improvement.
This blog will explore the benefits of a Combo Lean Six Sigma Green and Black Belt certification. We'll cover the key differences between the two roles. We'll also discuss how the dual certification can speed up career growth. Finally, we'll explain what to expect from a combined training program.
Understanding Lean Six Sigma: An Overview
Lean Six Sigma is a data-driven method. It aims to improve processes by eliminating waste and reducing variation. It combines Lean and Six Sigma. Lean aims to maximize value by minimizing waste. Six Sigma focuses on reducing defects and improving quality.
The methodology follows a structured problem-solving framework known as DMAIC:
- Define: Identify the problem and set project goals.
- Measure: Collect data to establish baseline performance.
- Analyze: Identify root causes of process issues.
- Improve: Implement solutions to address root causes.
- Control: Maintain the gains through process controls.
There are four Lean Six Sigma belt levels: Yellow, Green, Black, and Master Black. Each level means a deeper grasp of Lean Six Sigma principles and their application.
Green Belt vs. Black Belt: Key Differences
First, we must define the roles of Lean Six Sigma Green and Black Belts. Then, we can explore the benefits of a combo certification.
Lean Six Sigma Green Belt
Green Belt professionals are trained in Lean Six Sigma. They lead small process improvement projects or help on larger ones led by Black Belts.
Key Responsibilities:
- Lead smaller-scale improvement projects.
- Assist Black Belts in collecting and analyzing data.
- Facilitate process improvement meetings.
- Apply Lean Six Sigma tools to identify and eliminate waste.
Skills Acquired:
- Basic statistical analysis.
- Process mapping and root cause analysis.
- Understanding of DMAIC methodology.
- Effective communication and team collaboration.
Lean Six Sigma Black Belt
Black Belt professionals have advanced knowledge of Lean Six Sigma. They can lead complex, cross-functional improvement projects. They mentor Green Belts and help drive change in the organization.
Key Responsibilities:
- Lead large-scale, cross-functional improvement projects.
- Mentor and coach Green Belts.
- Conduct advanced data analysis.
- Develop and implement strategies for sustained process improvement.
Skills Acquired:
- Advanced statistical and data analysis.
- Change management and leadership.
- Project management.
- Strategic decision-making.
Why Pursue a Combo Lean Six Sigma Green Belt and Black Belt Certification?
A combined Lean Six Sigma Green and Black Belt certification has benefits. It is better than getting the two certifications separately.
1. Comprehensive Knowledge and Skillset
The combo certification program covers both intermediate and advanced Lean Six Sigma concepts. It equips professionals with a complete toolkit for process improvement. By mastering both levels, candidates gain:
- A thorough understanding of the DMAIC framework.
- Skilled in advanced statistical tools. This includes regression analysis, hypothesis testing, and design of experiments (DOE).
- Expertise in identifying and eliminating different types of waste (muda) and process variation.
2. Accelerated Career Growth
Organizations highly value professionals who can lead strategic improvement initiatives. A combined Green and Black Belt certification shows a strong commitment to growth. It also proves mastery of process improvement. This makes candidates more appealing for leadership roles.
Certified professionals often transition into roles such as:
- Process Improvement Manager
- Operational Excellence Leader
- Quality Manager
- Business Analyst
- Lean Six Sigma Consultant
3. Cost and Time Efficiency
A combo certification saves time and money. It is better than getting Green and Black Belt certifications separately. Combined programs usually streamline the curriculum by cutting redundant topics. This lets candidates progress more quickly.
4. Enhanced Project Leadership Capability
Both certifications enable professionals to lead projects of varying complexity. Green Belts can handle small projects independently. Black Belts can tackle large, high-impact initiatives.
5. Greater Impact on Organizational Success
Professionals with dual certification are equipped to drive significant organizational improvements, such as:
- Reducing operational costs.
- Improving product and service quality.
- Enhancing customer satisfaction.
- Increasing overall productivity.
What to Expect from a Combo Lean Six Sigma Green Belt and Black Belt Training Program
A combo certification program usually merges Green and Black Belt training. It offers a complete learning experience. Below is a breakdown of what candidates can expect:
1. Core Curriculum
- Introduction to Lean Six Sigma methodology.
- Overview of DMAIC phases and their application.
- Tools for process improvement, including:
- Process mapping.
- Fishbone diagrams.
- Pareto charts.
- 5 Whys.
2. Advanced Statistical Tools and Techniques
- Descriptive and inferential statistics.
- Hypothesis testing.
- Analysis of variance (ANOVA).
- Regression analysis.
- Design of experiments (DOE).
3. Change Management and Leadership
- Principles of change management.
- Effective communication strategies.
- Stakeholder management.
- Conflict resolution and negotiation.
4. Practical Application
Most combo programs include hands-on projects. They require candidates to apply what they have learned. These projects may involve:
- Identifying a real-world process improvement opportunity.
- Collecting and analyzing data.
- Implementing solutions and monitoring results.
5. Certification Exam
Candidates must pass a comprehensive exam to earn their Lean Six Sigma Green Belt and Black Belt. The exam usually has multiple-choice questions and case studies. It tests both theoretical knowledge and practical skills.
How to Choose the Right Combo Certification Program
When choosing a combo Lean Six Sigma Green and Black Belt program, consider these factors:
- Accreditation: Check that a recognized body accredits the program. Examples are the IASSC and ASQ.
- Curriculum: Look for a comprehensive curriculum that covers both basic and advanced topics.
- Instructor Expertise: Choose a program with experienced instructors in Lean Six Sigma.
- Mode of Delivery: Many programs offer flexible learning. They include in-person, online, and hybrid options.
- Cost and Duration: Compare the cost and length of programs. Find one that fits your budget and schedule.
How to obtain Lean Six Sigma Green and Black Belts certification?
We are an Education Technology company providing certification training courses to accelerate careers of working professionals worldwide. We impart training through instructor-led classroom workshops, instructor-led live virtual training sessions, and self-paced e-learning courses.
We have successfully conducted training sessions in 108 countries across the globe and enabled thousands of working professionals to enhance the scope of their careers.
Our enterprise training portfolio includes in-demand and globally recognized certification training courses in Project Management, Quality Management, Business Analysis, IT Service Management, Agile and Scrum, Cyber Security, Data Science, and Emerging Technologies. Download our Enterprise Training Catalog from https://www.icertglobal.com/corporate-training-for-enterprises.php and https://www.icertglobal.com/index.php
Popular Courses include:
-
Project Management: PMP, CAPM ,PMI RMP
-
Quality Management: Six Sigma Black Belt ,Lean Six Sigma Green Belt, Lean Management, Minitab,CMMI
-
Business Analysis: CBAP, CCBA, ECBA
-
Agile Training: PMI-ACP , CSM , CSPO
-
Scrum Training: CSM
-
DevOps
-
Program Management: PgMP
-
Cloud Technology: Exin Cloud Computing
-
Citrix Client Adminisration: Citrix Cloud Administration
The 10 top-paying certifications to target in 2025 are:
Conclusion
The Combo Lean Six Sigma Green and Black Belt certification is for those looking to advance their careers in process improvement. Candidates who master both levels will fully understand the Lean Six Sigma methodology. They can then lead complex projects and drive change in their organizations.
This dual certification is for you. It suits aspiring quality managers and seasoned ops pros. It also suits anyone wanting to improve their problem-solving skills. It will give you the skills and credentials to succeed in today's business world. It is fast-changing. Start your journey today, and unlock the full potential of Lean Six Sigma!
Contact Us For More Information:
Visit :www.icertglobal.com Email : 
Read More
In today's competitive business world, firms must excel to grow and satisfy customers. Organizations in all industries seek to improve processes, reduce waste, and increase efficiency. These goals are at the heart of Lean Six Sigma. Both Green Belt and Black Belt certifications are very valuable. But, a combined Lean Six Sigma Green and Black Belt certification is best. It is a complete path to mastering process improvement.
This blog will explore the benefits of a Combo Lean Six Sigma Green and Black Belt certification. We'll cover the key differences between the two roles. We'll also discuss how the dual certification can speed up career growth. Finally, we'll explain what to expect from a combined training program.
Understanding Lean Six Sigma: An Overview
Lean Six Sigma is a data-driven method. It aims to improve processes by eliminating waste and reducing variation. It combines Lean and Six Sigma. Lean aims to maximize value by minimizing waste. Six Sigma focuses on reducing defects and improving quality.
The methodology follows a structured problem-solving framework known as DMAIC:
- Define: Identify the problem and set project goals.
- Measure: Collect data to establish baseline performance.
- Analyze: Identify root causes of process issues.
- Improve: Implement solutions to address root causes.
- Control: Maintain the gains through process controls.
There are four Lean Six Sigma belt levels: Yellow, Green, Black, and Master Black. Each level means a deeper grasp of Lean Six Sigma principles and their application.
Green Belt vs. Black Belt: Key Differences
First, we must define the roles of Lean Six Sigma Green and Black Belts. Then, we can explore the benefits of a combo certification.
Lean Six Sigma Green Belt
Green Belt professionals are trained in Lean Six Sigma. They lead small process improvement projects or help on larger ones led by Black Belts.
Key Responsibilities:
- Lead smaller-scale improvement projects.
- Assist Black Belts in collecting and analyzing data.
- Facilitate process improvement meetings.
- Apply Lean Six Sigma tools to identify and eliminate waste.
Skills Acquired:
- Basic statistical analysis.
- Process mapping and root cause analysis.
- Understanding of DMAIC methodology.
- Effective communication and team collaboration.
Lean Six Sigma Black Belt
Black Belt professionals have advanced knowledge of Lean Six Sigma. They can lead complex, cross-functional improvement projects. They mentor Green Belts and help drive change in the organization.
Key Responsibilities:
- Lead large-scale, cross-functional improvement projects.
- Mentor and coach Green Belts.
- Conduct advanced data analysis.
- Develop and implement strategies for sustained process improvement.
Skills Acquired:
- Advanced statistical and data analysis.
- Change management and leadership.
- Project management.
- Strategic decision-making.
Why Pursue a Combo Lean Six Sigma Green Belt and Black Belt Certification?
A combined Lean Six Sigma Green and Black Belt certification has benefits. It is better than getting the two certifications separately.
1. Comprehensive Knowledge and Skillset
The combo certification program covers both intermediate and advanced Lean Six Sigma concepts. It equips professionals with a complete toolkit for process improvement. By mastering both levels, candidates gain:
- A thorough understanding of the DMAIC framework.
- Skilled in advanced statistical tools. This includes regression analysis, hypothesis testing, and design of experiments (DOE).
- Expertise in identifying and eliminating different types of waste (muda) and process variation.
2. Accelerated Career Growth
Organizations highly value professionals who can lead strategic improvement initiatives. A combined Green and Black Belt certification shows a strong commitment to growth. It also proves mastery of process improvement. This makes candidates more appealing for leadership roles.
Certified professionals often transition into roles such as:
- Process Improvement Manager
- Operational Excellence Leader
- Quality Manager
- Business Analyst
- Lean Six Sigma Consultant
3. Cost and Time Efficiency
A combo certification saves time and money. It is better than getting Green and Black Belt certifications separately. Combined programs usually streamline the curriculum by cutting redundant topics. This lets candidates progress more quickly.
4. Enhanced Project Leadership Capability
Both certifications enable professionals to lead projects of varying complexity. Green Belts can handle small projects independently. Black Belts can tackle large, high-impact initiatives.
5. Greater Impact on Organizational Success
Professionals with dual certification are equipped to drive significant organizational improvements, such as:
- Reducing operational costs.
- Improving product and service quality.
- Enhancing customer satisfaction.
- Increasing overall productivity.
What to Expect from a Combo Lean Six Sigma Green Belt and Black Belt Training Program
A combo certification program usually merges Green and Black Belt training. It offers a complete learning experience. Below is a breakdown of what candidates can expect:
1. Core Curriculum
- Introduction to Lean Six Sigma methodology.
- Overview of DMAIC phases and their application.
- Tools for process improvement, including:
- Process mapping.
- Fishbone diagrams.
- Pareto charts.
- 5 Whys.
2. Advanced Statistical Tools and Techniques
- Descriptive and inferential statistics.
- Hypothesis testing.
- Analysis of variance (ANOVA).
- Regression analysis.
- Design of experiments (DOE).
3. Change Management and Leadership
- Principles of change management.
- Effective communication strategies.
- Stakeholder management.
- Conflict resolution and negotiation.
4. Practical Application
Most combo programs include hands-on projects. They require candidates to apply what they have learned. These projects may involve:
- Identifying a real-world process improvement opportunity.
- Collecting and analyzing data.
- Implementing solutions and monitoring results.
5. Certification Exam
Candidates must pass a comprehensive exam to earn their Lean Six Sigma Green Belt and Black Belt. The exam usually has multiple-choice questions and case studies. It tests both theoretical knowledge and practical skills.
How to Choose the Right Combo Certification Program
When choosing a combo Lean Six Sigma Green and Black Belt program, consider these factors:
- Accreditation: Check that a recognized body accredits the program. Examples are the IASSC and ASQ.
- Curriculum: Look for a comprehensive curriculum that covers both basic and advanced topics.
- Instructor Expertise: Choose a program with experienced instructors in Lean Six Sigma.
- Mode of Delivery: Many programs offer flexible learning. They include in-person, online, and hybrid options.
- Cost and Duration: Compare the cost and length of programs. Find one that fits your budget and schedule.
How to obtain Lean Six Sigma Green and Black Belts certification?
We are an Education Technology company providing certification training courses to accelerate careers of working professionals worldwide. We impart training through instructor-led classroom workshops, instructor-led live virtual training sessions, and self-paced e-learning courses.
We have successfully conducted training sessions in 108 countries across the globe and enabled thousands of working professionals to enhance the scope of their careers.
Our enterprise training portfolio includes in-demand and globally recognized certification training courses in Project Management, Quality Management, Business Analysis, IT Service Management, Agile and Scrum, Cyber Security, Data Science, and Emerging Technologies. Download our Enterprise Training Catalog from https://www.icertglobal.com/corporate-training-for-enterprises.php and https://www.icertglobal.com/index.php
Popular Courses include:
-
Project Management: PMP, CAPM ,PMI RMP
-
Quality Management: Six Sigma Black Belt ,Lean Six Sigma Green Belt, Lean Management, Minitab,CMMI
-
Business Analysis: CBAP, CCBA, ECBA
-
Agile Training: PMI-ACP , CSM , CSPO
-
Scrum Training: CSM
-
DevOps
-
Program Management: PgMP
-
Cloud Technology: Exin Cloud Computing
-
Citrix Client Adminisration: Citrix Cloud Administration
The 10 top-paying certifications to target in 2025 are:
Conclusion
The Combo Lean Six Sigma Green and Black Belt certification is for those looking to advance their careers in process improvement. Candidates who master both levels will fully understand the Lean Six Sigma methodology. They can then lead complex projects and drive change in their organizations.
This dual certification is for you. It suits aspiring quality managers and seasoned ops pros. It also suits anyone wanting to improve their problem-solving skills. It will give you the skills and credentials to succeed in today's business world. It is fast-changing. Start your journey today, and unlock the full potential of Lean Six Sigma!
Contact Us For More Information:
Visit :www.icertglobal.com Email :
Boost Your Career with Minitab Certification Today Now!
In today's data-driven world, industries are using statistical tools. They rely on them to make informed decisions. In any field, like manufacturing or healthcare, data analysis is key. It's a highly sought-after skill. One tool that stands out is Minitab. It is a leading, easy-to-use, and powerful statistical software. A Minitab certification can boost your analytics skills. It can open new job opportunities and help you stand out in a competitive market.This blog explores Minitab certification. It covers its levels, benefits, and exam prep.
What is Minitab?
Minitab is a statistical software package. It is for data analysis, quality improvement, and process optimization. Developed in 1972, it has grown to become one of the most trusted tools for Six Sigma and Lean practitioners. Minitab makes complex statistics easy. It is for both beginners and experts. Its user-friendly interface and powerful analytics make it ideal for professionals. They must interpret data and find actionable insights.
Some of Minitab's core functionalities include:
- Descriptive statistics
- Hypothesis testing
- Regression analysis
- Control charts
- Design of experiments (DOE)
- Measurement system analysis (MSA)
- Statistical process control (SPC)
What is Minitab Certification?
Minitab certification shows you can use the software for stats and process improvement. It shows you can apply statistics in the real world. You have mastered the necessary skills. There are typically two levels of Minitab certification:
1. Minitab Essentials Certification
This entry-level certification focuses on foundational concepts and basic functionalities of the software. It is for those new to Minitab or who use it infrequently. They need to learn how to do basic analyses.
Key topics covered in the Minitab Essentials Certification include:
- Importing and organizing data
- Basic statistical tools (mean, median, standard deviation)
- Creating graphs and charts
- Conducting hypothesis tests
- Running simple regression models
2. Minitab Advanced Certification
The advanced certification is for experienced users. It aims to deepen their knowledge and skills in complex analyses.
It covers advanced tools and techniques, including:
- multivariate analysis
- DOE
- advanced regression models.
Key topics covered in the Minitab Advanced Certification include:
- Advanced regression analysis (logistic regression, nonlinear regression)
- Analysis of variance (ANOVA)
- DOE (factorial, fractional factorial, response surface)
- Multivariate analysis (principal component analysis, cluster analysis)
- Statistical process control (advanced control charts)
Why Pursue Minitab Certification?
1. Career Advancement
Employers highly value Minitab certification, especially in data-driven fields. This credential can help you. It is for quality engineers, process improvement specialists, and data analysts. It can boost your career. It shows your commitment to growth and mastery of statistical tools.
2. Increased Earning Potential
Professionals with Minitab certification often command higher salaries compared to their non-certified peers. Certification shows a specialized skill set. It's valuable to employers who want to improve processes and drive efficiency.
4. Industry Recognition
A Minitab certification provides industry recognition of your expertise. It can set you apart when applying for jobs or promotions. It shows you are very skilled in using statistical software.
5. Support for Six Sigma and Lean Initiatives
Minitab is the preferred tool for Six Sigma and Lean practitioners. Certification proves you can use the software for quality improvement. This makes you a valuable asset to organizations seeking process optimization.
How to Prepare for Minitab Certification
1. Understand the Exam Format
Before you prepare, know the exam's format. The exam usually has multiple-choice questions. They test your knowledge of Minitab's features, statistical concepts, and their practical applications.
3. Enhanced Problem-Solving Skills
Minitab certification teaches you to use statistics. It helps you analyze data, find trends, and solve problems. This can be invaluable in roles that require critical thinking and data-driven decision-making.
2. Enroll in a Training Course
Many organizations offer Minitab training courses, both online and in-person. These courses provide hands-on experience with the software. They cover the exam topics you need to know. Some popular training providers include:
- Minitab itself
- Accredited Six Sigma training providers
- Online learning platforms such as Udemy and Coursera
3. Practice with Real Data
One of the best ways to prepare for the exam is to practice using real-world data sets. This will help you become familiar with Minitab’s interface and functionalities. You can find practice data sets online or use data from your workplace.
4. Use Minitab’s Help Resources
Minitab offers comprehensive documentation and help resources, including tutorials and guides. These resources can help you with features and issues in practice.
5. Join a Study Group
Joining a study group can be a great way to learn from others who are also preparing for the exam. You can exchange tips, clarify doubts, and stay motivated throughout your preparation.
Tips for Passing the Minitab Certification Exam
- Understand Statistical Concepts: You must know statistical concepts. The exam tests your theoretical knowledge and practical skills.
- Familiarize Yourself with the Software: Spend time using Minitab. It will help you learn its interface and tools.
- Review Sample Questions: They can show you the exam's question types.
- Time Management: During the exam, manage your time well. This will ensure you can answer all questions in the time allowed.
Maintaining Your Certification
After earning your Minitab certification, stay updated on new features in the software. Some certifications may require periodic renewal. This might mean retaking the exam or completing continuing education credits.
How to obtain Minitab certification?
We are an Education Technology company providing certification training courses to accelerate careers of working professionals worldwide. We impart training through instructor-led classroom workshops, instructor-led live virtual training sessions, and self-paced e-learning courses.
We have successfully conducted training sessions in 108 countries across the globe and enabled thousands of working professionals to enhance the scope of their careers.
Our enterprise training portfolio includes in-demand and globally recognized certification training courses in Project Management, Quality Management, Business Analysis, IT Service Management, Agile and Scrum, Cyber Security, Data Science, and Emerging Technologies. Download our Enterprise Training Catalog from https://www.icertglobal.com/corporate-training-for-enterprises.php and https://www.icertglobal.com/index.php
Popular Courses include:
-
Project Management: PMP, CAPM ,PMI RMP
-
Quality Management: Six Sigma Black Belt ,Lean Six Sigma Green Belt, Lean Management, Minitab,CMMI
-
Business Analysis: CBAP, CCBA, ECBA
-
Agile Training: PMI-ACP , CSM , CSPO
-
Scrum Training: CSM
-
DevOps
-
Program Management: PgMP
-
Cloud Technology: Exin Cloud Computing
-
Citrix Client Adminisration: Citrix Cloud Administration
The 10 top-paying certifications to target in 2025 are:
Conclusion
Minitab certification is a valuable credential for professionals. It can boost their statistical analysis skills and careers. Whether you're new to Minitab or an expert, a certification can help. It can lead to better jobs and higher pay. Use a structured prep plan and hands-on practice with the software. Then, you can earn your Minitab certification. This will make you an expert in data analysis and quality improvement.
Contact Us For More Information:
Visit :www.icertglobal.com Email : 
Read More
In today's data-driven world, industries are using statistical tools. They rely on them to make informed decisions. In any field, like manufacturing or healthcare, data analysis is key. It's a highly sought-after skill. One tool that stands out is Minitab. It is a leading, easy-to-use, and powerful statistical software. A Minitab certification can boost your analytics skills. It can open new job opportunities and help you stand out in a competitive market.This blog explores Minitab certification. It covers its levels, benefits, and exam prep.
What is Minitab?
Minitab is a statistical software package. It is for data analysis, quality improvement, and process optimization. Developed in 1972, it has grown to become one of the most trusted tools for Six Sigma and Lean practitioners. Minitab makes complex statistics easy. It is for both beginners and experts. Its user-friendly interface and powerful analytics make it ideal for professionals. They must interpret data and find actionable insights.
Some of Minitab's core functionalities include:
- Descriptive statistics
- Hypothesis testing
- Regression analysis
- Control charts
- Design of experiments (DOE)
- Measurement system analysis (MSA)
- Statistical process control (SPC)
What is Minitab Certification?
Minitab certification shows you can use the software for stats and process improvement. It shows you can apply statistics in the real world. You have mastered the necessary skills. There are typically two levels of Minitab certification:
1. Minitab Essentials Certification
This entry-level certification focuses on foundational concepts and basic functionalities of the software. It is for those new to Minitab or who use it infrequently. They need to learn how to do basic analyses.
Key topics covered in the Minitab Essentials Certification include:
- Importing and organizing data
- Basic statistical tools (mean, median, standard deviation)
- Creating graphs and charts
- Conducting hypothesis tests
- Running simple regression models
2. Minitab Advanced Certification
The advanced certification is for experienced users. It aims to deepen their knowledge and skills in complex analyses.
It covers advanced tools and techniques, including:
- multivariate analysis
- DOE
- advanced regression models.
Key topics covered in the Minitab Advanced Certification include:
- Advanced regression analysis (logistic regression, nonlinear regression)
- Analysis of variance (ANOVA)
- DOE (factorial, fractional factorial, response surface)
- Multivariate analysis (principal component analysis, cluster analysis)
- Statistical process control (advanced control charts)
Why Pursue Minitab Certification?
1. Career Advancement
Employers highly value Minitab certification, especially in data-driven fields. This credential can help you. It is for quality engineers, process improvement specialists, and data analysts. It can boost your career. It shows your commitment to growth and mastery of statistical tools.
2. Increased Earning Potential
Professionals with Minitab certification often command higher salaries compared to their non-certified peers. Certification shows a specialized skill set. It's valuable to employers who want to improve processes and drive efficiency.
4. Industry Recognition
A Minitab certification provides industry recognition of your expertise. It can set you apart when applying for jobs or promotions. It shows you are very skilled in using statistical software.
5. Support for Six Sigma and Lean Initiatives
Minitab is the preferred tool for Six Sigma and Lean practitioners. Certification proves you can use the software for quality improvement. This makes you a valuable asset to organizations seeking process optimization.
How to Prepare for Minitab Certification
1. Understand the Exam Format
Before you prepare, know the exam's format. The exam usually has multiple-choice questions. They test your knowledge of Minitab's features, statistical concepts, and their practical applications.
3. Enhanced Problem-Solving Skills
Minitab certification teaches you to use statistics. It helps you analyze data, find trends, and solve problems. This can be invaluable in roles that require critical thinking and data-driven decision-making.
2. Enroll in a Training Course
Many organizations offer Minitab training courses, both online and in-person. These courses provide hands-on experience with the software. They cover the exam topics you need to know. Some popular training providers include:
- Minitab itself
- Accredited Six Sigma training providers
- Online learning platforms such as Udemy and Coursera
3. Practice with Real Data
One of the best ways to prepare for the exam is to practice using real-world data sets. This will help you become familiar with Minitab’s interface and functionalities. You can find practice data sets online or use data from your workplace.
4. Use Minitab’s Help Resources
Minitab offers comprehensive documentation and help resources, including tutorials and guides. These resources can help you with features and issues in practice.
5. Join a Study Group
Joining a study group can be a great way to learn from others who are also preparing for the exam. You can exchange tips, clarify doubts, and stay motivated throughout your preparation.
Tips for Passing the Minitab Certification Exam
- Understand Statistical Concepts: You must know statistical concepts. The exam tests your theoretical knowledge and practical skills.
- Familiarize Yourself with the Software: Spend time using Minitab. It will help you learn its interface and tools.
- Review Sample Questions: They can show you the exam's question types.
- Time Management: During the exam, manage your time well. This will ensure you can answer all questions in the time allowed.
Maintaining Your Certification
After earning your Minitab certification, stay updated on new features in the software. Some certifications may require periodic renewal. This might mean retaking the exam or completing continuing education credits.
How to obtain Minitab certification?
We are an Education Technology company providing certification training courses to accelerate careers of working professionals worldwide. We impart training through instructor-led classroom workshops, instructor-led live virtual training sessions, and self-paced e-learning courses.
We have successfully conducted training sessions in 108 countries across the globe and enabled thousands of working professionals to enhance the scope of their careers.
Our enterprise training portfolio includes in-demand and globally recognized certification training courses in Project Management, Quality Management, Business Analysis, IT Service Management, Agile and Scrum, Cyber Security, Data Science, and Emerging Technologies. Download our Enterprise Training Catalog from https://www.icertglobal.com/corporate-training-for-enterprises.php and https://www.icertglobal.com/index.php
Popular Courses include:
-
Project Management: PMP, CAPM ,PMI RMP
-
Quality Management: Six Sigma Black Belt ,Lean Six Sigma Green Belt, Lean Management, Minitab,CMMI
-
Business Analysis: CBAP, CCBA, ECBA
-
Agile Training: PMI-ACP , CSM , CSPO
-
Scrum Training: CSM
-
DevOps
-
Program Management: PgMP
-
Cloud Technology: Exin Cloud Computing
-
Citrix Client Adminisration: Citrix Cloud Administration
The 10 top-paying certifications to target in 2025 are:
Conclusion
Minitab certification is a valuable credential for professionals. It can boost their statistical analysis skills and careers. Whether you're new to Minitab or an expert, a certification can help. It can lead to better jobs and higher pay. Use a structured prep plan and hands-on practice with the software. Then, you can earn your Minitab certification. This will make you an expert in data analysis and quality improvement.
Contact Us For More Information:
Visit :www.icertglobal.com Email :
Enhancing Business Success in the UAE with Lean Six Sigma
In today's tough global economy, businesses must cut waste and boost customer satisfaction. They must also improve operations. A methodology that has gained traction worldwide, including in the UAE, is Lean Six Sigma. A Lean Six Sigma Black Belt certification gives advanced skills. It allows professionals to improve processes and solve complex problems. This blog will show how Lean Six Sigma Black Belt certification can help UAE firms. It can solve key operational problems and ensure lasting success.
Understanding Lean Six Sigma
Lean Six Sigma is a powerful method. It combines Lean and Six Sigma to cut waste and reduce process variability. Lean aims to streamline processes and cut waste. Six Sigma seeks to reduce defects and ensure consistency using data-driven decisions.
The Lean Six Sigma Black Belt certification shows advanced expertise in the methodology. Black Belts are skilled professionals. They lead teams, manage projects, and implement solutions. They use a method called DMAIC to solve problems and improve processes. It represents the phases: Define, Measure, Analyze, Improve, and Control.
Benefits of Lean Six Sigma Black Belt Certification
Lean Six Sigma Black Belt certification benefits individuals and organizations. Let’s explore some of the key advantages:
1. Enhanced Problem-Solving Skills
Black Belts use advanced statistics to find root causes of problems. They then develop effective solutions. This skill is vital for UAE organizations. Industries like manufacturing, healthcare, logistics, and finance face unique challenges.
2. Improved Operational Efficiency
Lean Six Sigma principles let Black Belts improve processes. They reduce cycle times and waste. This boosts productivity and cuts costs. These are vital for businesses in the competitive UAE market.
3. Data-Driven Decision-Making
Lean Six Sigma highlights the significance of data-driven decision-making. Black Belts are proficient in utilizing data to inform their decisions. They can collect, analyze, and interpret it. This approach ensures solutions are based on facts, not assumptions.
4. Increased Customer Satisfaction
Lean Six Sigma improves process quality and consistency. It helps organizations deliver better products and services to customers. In the UAE, customers have high expectations. Improving satisfaction can boost loyalty and market share.
5. Leadership Development
Black Belts often lead improvement projects. They also provide guidance to Green Belts and other team members. This role enhances their leadership and project management abilities. They become valuable assets to any organization.
Key Industries in UAE Leveraging Lean Six Sigma
The UAE is home to a diverse range of industries, each with unique operational challenges. Key sectors have adopted Lean Six Sigma for improvement and a competitive edge.
1. Manufacturing
The UAE's manufacturing sector is rapidly growing. It focuses on aerospace, automotive, and consumer goods. Lean Six Sigma helps manufacturers. It reduces defects, improves processes, and cuts waste. This leads to higher quality products and lower costs.
2. Healthcare
UAE healthcare organizations must improve patient outcomes and cut costs. They face constant pressure to do so. Lean Six Sigma supports hospitals and clinics in enhancing patient care. It reduces wait times and boosts service quality.
3. Logistics and Supply Chain
The UAE is a global logistics hub. Its major ports and airports facilitate international trade. Lean Six Sigma helps logistics firms optimize their supply chains. It reduces lead times and improves delivery accuracy.
4. Financial Services
In the financial sector, accuracy and efficiency are vital. Lean Six Sigma improves transaction processes, reduces errors, and boosts customer experience. UAE banks use Lean Six Sigma to stay competitive in a fast-changing market.
5. Government and Public Services
The UAE government has a strong focus on innovation and efficiency. Lean Six Sigma improves public services and cuts bureaucratic delays. It aims to boost the citizen experience.
Real-World Examples of Lean Six Sigma in UAE:
Example 1: Streamlining Manufacturing Processes
A top UAE manufacturer had high defect rates in one of its production lines. A Lean Six Sigma Black Belt project identified the causes of defects. It then implemented process changes that cut defects by 40%. This improvement boosted product quality and saved costs.
Example 2: Improving Hospital Operations
A hospital in Dubai used Lean Six Sigma to reduce long wait times in its ER. The Black Belt-led project analyzed patient flow data and identified bottlenecks. The hospital changed its processes. It cut average wait times by 30%. This improved patient satisfaction.
Example 3: Enhancing Supply Chain Efficiency
A logistics firm in Abu Dhabi used Lean Six Sigma to improve its order fulfillment. The Black Belt team found inefficiencies in warehouse operations. Their changes cut order processing time by 25%. This resulted in faster deliveries and improved customer satisfaction.
Steps to Achieve Lean Six Sigma Black Belt Certification in UAE
To earn a Lean Six Sigma Black Belt, you must be dedicated and complete several key steps.
- Prerequisite Knowledge: Candidates must know Lean Six Sigma principles and methods. They should have a Green Belt certification.
- Training Program: Enroll in a reputable Lean Six Sigma Black Belt training program. In the UAE, several institutions offer high-quality, industry-specific training.
- Project Completion: Candidates must usually complete a real-world project. It should show their ability to use Lean Six Sigma tools and techniques.
- Examination: Pass a test on Lean Six Sigma concepts and tools.
- Certification: To earn a Lean Six Sigma Black Belt, candidates must pass a training, a project, and an exam.
Choosing the Right Training Provider in UAE
Choosing the right training provider is vital. It guarantees a top-tier Lean Six Sigma Black Belt certification. Below are key factors to keep in mind when selecting a provider:
- Accreditation: Ensure a recognized body accredits the training provider in Lean Six Sigma.
- Experienced Trainers: Choose providers with instructors who have real-world Lean Six Sigma experience.
- Practical Approach: The training should have hands-on projects and case studies. They will help candidates apply what they learn.
- Flexibility: Choose providers with flexible training options, like online, in-person, or blended learning.
How to obtain Lean Six Sigma certification?
We are an Education Technology company providing certification training courses to accelerate careers of working professionals worldwide. We impart training through instructor-led classroom workshops, instructor-led live virtual training sessions, and self-paced e-learning courses.
We have successfully conducted training sessions in 108 countries across the globe and enabled thousands of working professionals to enhance the scope of their careers.
Our enterprise training portfolio includes in-demand and globally recognized certification training courses in Project Management, Quality Management, Business Analysis, IT Service Management, Agile and Scrum, Cyber Security, Data Science, and Emerging Technologies. Download our Enterprise Training Catalog from https://www.icertglobal.com/corporate-training-for-enterprises.php and https://www.icertglobal.com/index.php
Popular Courses include:
-
Project Management: PMP, CAPM ,PMI RMP
-
Quality Management: Six Sigma Black Belt ,Lean Six Sigma Green Belt, Lean Management, Minitab,CMMI
-
Business Analysis: CBAP, CCBA, ECBA
-
Agile Training: PMI-ACP , CSM , CSPO
-
Scrum Training: CSM
-
DevOps
-
Program Management: PgMP
-
Cloud Technology: Exin Cloud Computing
-
Citrix Client Adminisration: Citrix Cloud Administration
The 10 top-paying certifications to target in 2025 are:
Conclusion
In the UAE, Lean Six Sigma Black Belt certification is a great asset. It helps professionals and organizations improve problem-solving and drive operational excellence. Lean Six Sigma can help businesses. It reduces waste, boosts efficiency, and improves quality. Lean Six Sigma is helping UAE firms in many sectors, such as manufacturing and healthcare. It helps them stay competitive and succeed in the long run.Investing in Lean Six Sigma Black Belt certification is a smart move. It benefits those seeking career growth and organizations that want to improve. It can yield high returns. The UAE's fast-paced business world is perfect for Lean Six Sigma experts to thrive and make an impact.
Contact Us For More Information:
Visit :www.icertglobal.com Email : 
Read More
In today's tough global economy, businesses must cut waste and boost customer satisfaction. They must also improve operations. A methodology that has gained traction worldwide, including in the UAE, is Lean Six Sigma. A Lean Six Sigma Black Belt certification gives advanced skills. It allows professionals to improve processes and solve complex problems. This blog will show how Lean Six Sigma Black Belt certification can help UAE firms. It can solve key operational problems and ensure lasting success.
Understanding Lean Six Sigma
Lean Six Sigma is a powerful method. It combines Lean and Six Sigma to cut waste and reduce process variability. Lean aims to streamline processes and cut waste. Six Sigma seeks to reduce defects and ensure consistency using data-driven decisions.
The Lean Six Sigma Black Belt certification shows advanced expertise in the methodology. Black Belts are skilled professionals. They lead teams, manage projects, and implement solutions. They use a method called DMAIC to solve problems and improve processes. It represents the phases: Define, Measure, Analyze, Improve, and Control.
Benefits of Lean Six Sigma Black Belt Certification
Lean Six Sigma Black Belt certification benefits individuals and organizations. Let’s explore some of the key advantages:
1. Enhanced Problem-Solving Skills
Black Belts use advanced statistics to find root causes of problems. They then develop effective solutions. This skill is vital for UAE organizations. Industries like manufacturing, healthcare, logistics, and finance face unique challenges.
2. Improved Operational Efficiency
Lean Six Sigma principles let Black Belts improve processes. They reduce cycle times and waste. This boosts productivity and cuts costs. These are vital for businesses in the competitive UAE market.
3. Data-Driven Decision-Making
Lean Six Sigma highlights the significance of data-driven decision-making. Black Belts are proficient in utilizing data to inform their decisions. They can collect, analyze, and interpret it. This approach ensures solutions are based on facts, not assumptions.
4. Increased Customer Satisfaction
Lean Six Sigma improves process quality and consistency. It helps organizations deliver better products and services to customers. In the UAE, customers have high expectations. Improving satisfaction can boost loyalty and market share.
5. Leadership Development
Black Belts often lead improvement projects. They also provide guidance to Green Belts and other team members. This role enhances their leadership and project management abilities. They become valuable assets to any organization.
Key Industries in UAE Leveraging Lean Six Sigma
The UAE is home to a diverse range of industries, each with unique operational challenges. Key sectors have adopted Lean Six Sigma for improvement and a competitive edge.
1. Manufacturing
The UAE's manufacturing sector is rapidly growing. It focuses on aerospace, automotive, and consumer goods. Lean Six Sigma helps manufacturers. It reduces defects, improves processes, and cuts waste. This leads to higher quality products and lower costs.
2. Healthcare
UAE healthcare organizations must improve patient outcomes and cut costs. They face constant pressure to do so. Lean Six Sigma supports hospitals and clinics in enhancing patient care. It reduces wait times and boosts service quality.
3. Logistics and Supply Chain
The UAE is a global logistics hub. Its major ports and airports facilitate international trade. Lean Six Sigma helps logistics firms optimize their supply chains. It reduces lead times and improves delivery accuracy.
4. Financial Services
In the financial sector, accuracy and efficiency are vital. Lean Six Sigma improves transaction processes, reduces errors, and boosts customer experience. UAE banks use Lean Six Sigma to stay competitive in a fast-changing market.
5. Government and Public Services
The UAE government has a strong focus on innovation and efficiency. Lean Six Sigma improves public services and cuts bureaucratic delays. It aims to boost the citizen experience.
Real-World Examples of Lean Six Sigma in UAE:
Example 1: Streamlining Manufacturing Processes
A top UAE manufacturer had high defect rates in one of its production lines. A Lean Six Sigma Black Belt project identified the causes of defects. It then implemented process changes that cut defects by 40%. This improvement boosted product quality and saved costs.
Example 2: Improving Hospital Operations
A hospital in Dubai used Lean Six Sigma to reduce long wait times in its ER. The Black Belt-led project analyzed patient flow data and identified bottlenecks. The hospital changed its processes. It cut average wait times by 30%. This improved patient satisfaction.
Example 3: Enhancing Supply Chain Efficiency
A logistics firm in Abu Dhabi used Lean Six Sigma to improve its order fulfillment. The Black Belt team found inefficiencies in warehouse operations. Their changes cut order processing time by 25%. This resulted in faster deliveries and improved customer satisfaction.
Steps to Achieve Lean Six Sigma Black Belt Certification in UAE
To earn a Lean Six Sigma Black Belt, you must be dedicated and complete several key steps.
- Prerequisite Knowledge: Candidates must know Lean Six Sigma principles and methods. They should have a Green Belt certification.
- Training Program: Enroll in a reputable Lean Six Sigma Black Belt training program. In the UAE, several institutions offer high-quality, industry-specific training.
- Project Completion: Candidates must usually complete a real-world project. It should show their ability to use Lean Six Sigma tools and techniques.
- Examination: Pass a test on Lean Six Sigma concepts and tools.
- Certification: To earn a Lean Six Sigma Black Belt, candidates must pass a training, a project, and an exam.
Choosing the Right Training Provider in UAE
Choosing the right training provider is vital. It guarantees a top-tier Lean Six Sigma Black Belt certification. Below are key factors to keep in mind when selecting a provider:
- Accreditation: Ensure a recognized body accredits the training provider in Lean Six Sigma.
- Experienced Trainers: Choose providers with instructors who have real-world Lean Six Sigma experience.
- Practical Approach: The training should have hands-on projects and case studies. They will help candidates apply what they learn.
- Flexibility: Choose providers with flexible training options, like online, in-person, or blended learning.
How to obtain Lean Six Sigma certification?
We are an Education Technology company providing certification training courses to accelerate careers of working professionals worldwide. We impart training through instructor-led classroom workshops, instructor-led live virtual training sessions, and self-paced e-learning courses.
We have successfully conducted training sessions in 108 countries across the globe and enabled thousands of working professionals to enhance the scope of their careers.
Our enterprise training portfolio includes in-demand and globally recognized certification training courses in Project Management, Quality Management, Business Analysis, IT Service Management, Agile and Scrum, Cyber Security, Data Science, and Emerging Technologies. Download our Enterprise Training Catalog from https://www.icertglobal.com/corporate-training-for-enterprises.php and https://www.icertglobal.com/index.php
Popular Courses include:
-
Project Management: PMP, CAPM ,PMI RMP
-
Quality Management: Six Sigma Black Belt ,Lean Six Sigma Green Belt, Lean Management, Minitab,CMMI
-
Business Analysis: CBAP, CCBA, ECBA
-
Agile Training: PMI-ACP , CSM , CSPO
-
Scrum Training: CSM
-
DevOps
-
Program Management: PgMP
-
Cloud Technology: Exin Cloud Computing
-
Citrix Client Adminisration: Citrix Cloud Administration
The 10 top-paying certifications to target in 2025 are:
Conclusion
In the UAE, Lean Six Sigma Black Belt certification is a great asset. It helps professionals and organizations improve problem-solving and drive operational excellence. Lean Six Sigma can help businesses. It reduces waste, boosts efficiency, and improves quality. Lean Six Sigma is helping UAE firms in many sectors, such as manufacturing and healthcare. It helps them stay competitive and succeed in the long run.Investing in Lean Six Sigma Black Belt certification is a smart move. It benefits those seeking career growth and organizations that want to improve. It can yield high returns. The UAE's fast-paced business world is perfect for Lean Six Sigma experts to thrive and make an impact.
Contact Us For More Information:
Visit :www.icertglobal.com Email :
The Role of a Six Sigma Black Belt in Agile Organizations
In today's fast-paced business world, firms are adopting Agile methods. They want to stay competitive and respond to changing market demands. Agile is synonymous with adaptability, speed, and continuous improvement. At first glance, Six Sigma's data-driven structure may clash with Agile's flexibility. However, a Six Sigma Black Belt (SSBB) can add great value to Agile organizations. They can bridge the gap between structured problem-solving and iterative adaptability. This blog explores the key role of Six Sigma Black Belts in Agile firms. Their skills complement Agile principles and drive lasting success.
Understanding Agile Methodologies
Agile is a mindset and framework focused on delivering value incrementally. It emphasizes customer collaboration, iterative development, and responsiveness to feedback. Agile principles are widely used in software development. They have been adopted in many industries, including healthcare, manufacturing, and marketing. Agile frameworks like Scrum, Kanban, and SAFe prioritise teamwork, flexibility, and speed. They aim to deliver value quickly.
Agile drives innovation and reduces time-to-market. But, it sometimes struggles with inefficiencies, quality, and process optimization. This is where the analytical rigor of a Six Sigma Black Belt becomes invaluable.
What is a Six Sigma Black Belt?
A Six Sigma Black Belt is a pro. They have advanced skills in Six Sigma's methods, tools, and techniques. They specialize in identifying and eliminating defects, reducing variability, and improving process efficiency. The DMAIC (Define, Measure, Analyze, Improve, Control) framework is key to their approach. It helps organizations improve quality and performance.
In an Agile organization, a Six Sigma Black Belt is key. They blend structured problem-solving with Agile's adaptability to boost efficiency and quality.
Key Roles of a Six Sigma Black Belt in Agile Organizations
1. Streamlining Processes Without Compromising Flexibility
Agile thrives on adaptability. But, it can cause inefficiencies due to a lack of standard processes. Six Sigma Black Belts excel in identifying bottlenecks, redundancies, and waste in workflows. They can use tools like Value Stream Mapping (VSM) and process capability analysis. These can streamline Agile processes without harming Agile's needed flexibility.
In a Scrum framework, a Black Belt can analyze the sprint cycle. They can find inefficiencies in task prioritization, resource allocation, or defect resolution. This ensures that Agile teams operate at peak efficiency without sacrificing speed.
2. Enhancing Quality Through Data-Driven Decision Making
Quality is a core tenet of both Agile and Six Sigma. Agile emphasizes delivering high-quality increments, while Six Sigma focuses on minimizing defects. A Six Sigma Black Belt can use tools like control charts, regression analysis, and root cause analysis. They can help to monitor and improve quality continuously.
In Agile, where quick iterations are common, maintaining quality can be challenging. A Black Belt ensures that quality checkpoints are part of the iterative process. This lets teams deliver value without defects.
3. Bridging the Gap Between Strategy and Execution
Agile teams often operate at a tactical level, focusing on immediate deliverables. However, achieving long-term strategic goals requires alignment between high-level objectives and day-to-day execution. Six Sigma Black Belts, with their ability to view the bigger picture, play a vital role in this alignment.
A Black Belt can use tools like the Balanced Scorecard and Hoshin Kanri. They ensure Agile initiatives align with organizational goals. This creates a strategy that drives sustainable growth.
4. Promoting a Culture of Continuous Improvement
Agile and Six Sigma both emphasize continuous improvement, albeit in different ways. Agile relies on retrospectives and feedback loops. Six Sigma uses a structured approach to root cause analysis and process optimisation.
A Six Sigma Black Belt can improve Agile retrospectives. They can use techniques like Fishbone Diagrams and the 5 Whys to find deeper issues. They also foster a culture where teams seek to improve. They use Lean principles to eliminate waste and maximize value.
5. Managing Risk and Variability
Agile’s fast-paced nature can sometimes lead to unpredictable outcomes. In such cases, Six Sigma's focus on reducing variability and managing risks is crucial. A Black Belt uses tools like FMEA and Monte Carlo simulations. They help anticipate risks and implement preventive measures.
For example, in a Kanban workflow, a Black Belt might analyze lead and cycle times. This would identify variability trends. It would ensure smoother and more predictable deliveries.
6. Facilitating Cross-Functional Collaboration
Agile thrives on collaboration across teams, but siloed communication can hinder progress. Six Sigma Black Belts are skilled facilitators. They can bridge gaps between cross-functional teams. They use stakeholder analysis and collaboration tools.
They ensure that all, from developers to product owners, share a common view on quality and process improvement. This fosters a more cohesive and productive Agile environment.
Case Studies: SSBB Success in Agile Organizations
Case Study 1: Improving Sprint Efficiency in a Tech Startup
A technology startup struggled with delayed sprints due to inefficiencies in task prioritization. A Six Sigma Black Belt conducted a root cause analysis and introduced a streamlined prioritization matrix. This reduced sprint delays by 30% while maintaining Agile flexibility.
Case Study 2: Enhancing Quality in a Healthcare Agile Team
A healthcare organization using Agile to develop a patient management system faced issues with recurring defects. A Six Sigma Black Belt used control charts to track quality trends. They then improved processes, reducing defects by 40% in three months.
Challenges for Six Sigma Black Belts in Agile Environments
Despite their strengths, Six Sigma Black Belts may face challenges in Agile settings:
- Resistance to Structured Methods: Agile teams may perceive Six Sigma’s structured approach as restrictive. Black Belts must demonstrate how their methods enhance, rather than hinder, Agile workflows.
- Balancing Speed and Analysis: Agile’s focus on speed can conflict with Six Sigma’s emphasis on thorough analysis. Black Belts must adapt their techniques to align with Agile’s rapid pace.
How to obtain SSBB certification?
We are an Education Technology company providing certification training courses to accelerate careers of working professionals worldwide. We impart training through instructor-led classroom workshops, instructor-led live virtual training sessions, and self-paced e-learning courses.
We have successfully conducted training sessions in 108 countries across the globe and enabled thousands of working professionals to enhance the scope of their careers.
Our enterprise training portfolio includes in-demand and globally recognized certification training courses in Project Management, Quality Management, Business Analysis, IT Service Management, Agile and Scrum, Cyber Security, Data Science, and Emerging Technologies. Download our Enterprise Training Catalog from https://www.icertglobal.com/corporate-training-for-enterprises.php and https://www.icertglobal.com/index.php
Popular Courses include:
-
Project Management: PMP, CAPM ,PMI RMP
-
Quality Management: Six Sigma Black Belt ,Lean Six Sigma Green Belt, Lean Management, Minitab,CMMI
-
Business Analysis: CBAP, CCBA, ECBA
-
Agile Training: PMI-ACP , CSM , CSPO
-
Scrum Training: CSM
-
DevOps
-
Program Management: PgMP
-
Cloud Technology: Exin Cloud Computing
-
Citrix Client Adminisration: Citrix Cloud Administration
The 10 top-paying certifications to target in 2024 are:
Conclusion
A Six Sigma Black Belt's role in Agile organizations is multifaceted. It blends structured problem-solving with Agile's adaptability. Black Belts can add great value in Agile settings. They can do this by streamlining processes, improving quality, and aligning strategy. They can do this by promoting continuous improvement, managing risk, and fostering collaboration.
For organizations wanting to reap the benefits of both methods, it's smart to integrate Six Sigma Black Belts into Agile teams. It ensures efficiency and quality. It also fosters innovation and growth. It's a win-win for all stakeholders.
Contact Us For More Information:
Visit :www.icertglobal.com Email : 
Read More
In today's fast-paced business world, firms are adopting Agile methods. They want to stay competitive and respond to changing market demands. Agile is synonymous with adaptability, speed, and continuous improvement. At first glance, Six Sigma's data-driven structure may clash with Agile's flexibility. However, a Six Sigma Black Belt (SSBB) can add great value to Agile organizations. They can bridge the gap between structured problem-solving and iterative adaptability. This blog explores the key role of Six Sigma Black Belts in Agile firms. Their skills complement Agile principles and drive lasting success.
Understanding Agile Methodologies
Agile is a mindset and framework focused on delivering value incrementally. It emphasizes customer collaboration, iterative development, and responsiveness to feedback. Agile principles are widely used in software development. They have been adopted in many industries, including healthcare, manufacturing, and marketing. Agile frameworks like Scrum, Kanban, and SAFe prioritise teamwork, flexibility, and speed. They aim to deliver value quickly.
Agile drives innovation and reduces time-to-market. But, it sometimes struggles with inefficiencies, quality, and process optimization. This is where the analytical rigor of a Six Sigma Black Belt becomes invaluable.
What is a Six Sigma Black Belt?
A Six Sigma Black Belt is a pro. They have advanced skills in Six Sigma's methods, tools, and techniques. They specialize in identifying and eliminating defects, reducing variability, and improving process efficiency. The DMAIC (Define, Measure, Analyze, Improve, Control) framework is key to their approach. It helps organizations improve quality and performance.
In an Agile organization, a Six Sigma Black Belt is key. They blend structured problem-solving with Agile's adaptability to boost efficiency and quality.
Key Roles of a Six Sigma Black Belt in Agile Organizations
1. Streamlining Processes Without Compromising Flexibility
Agile thrives on adaptability. But, it can cause inefficiencies due to a lack of standard processes. Six Sigma Black Belts excel in identifying bottlenecks, redundancies, and waste in workflows. They can use tools like Value Stream Mapping (VSM) and process capability analysis. These can streamline Agile processes without harming Agile's needed flexibility.
In a Scrum framework, a Black Belt can analyze the sprint cycle. They can find inefficiencies in task prioritization, resource allocation, or defect resolution. This ensures that Agile teams operate at peak efficiency without sacrificing speed.
2. Enhancing Quality Through Data-Driven Decision Making
Quality is a core tenet of both Agile and Six Sigma. Agile emphasizes delivering high-quality increments, while Six Sigma focuses on minimizing defects. A Six Sigma Black Belt can use tools like control charts, regression analysis, and root cause analysis. They can help to monitor and improve quality continuously.
In Agile, where quick iterations are common, maintaining quality can be challenging. A Black Belt ensures that quality checkpoints are part of the iterative process. This lets teams deliver value without defects.
3. Bridging the Gap Between Strategy and Execution
Agile teams often operate at a tactical level, focusing on immediate deliverables. However, achieving long-term strategic goals requires alignment between high-level objectives and day-to-day execution. Six Sigma Black Belts, with their ability to view the bigger picture, play a vital role in this alignment.
A Black Belt can use tools like the Balanced Scorecard and Hoshin Kanri. They ensure Agile initiatives align with organizational goals. This creates a strategy that drives sustainable growth.
4. Promoting a Culture of Continuous Improvement
Agile and Six Sigma both emphasize continuous improvement, albeit in different ways. Agile relies on retrospectives and feedback loops. Six Sigma uses a structured approach to root cause analysis and process optimisation.
A Six Sigma Black Belt can improve Agile retrospectives. They can use techniques like Fishbone Diagrams and the 5 Whys to find deeper issues. They also foster a culture where teams seek to improve. They use Lean principles to eliminate waste and maximize value.
5. Managing Risk and Variability
Agile’s fast-paced nature can sometimes lead to unpredictable outcomes. In such cases, Six Sigma's focus on reducing variability and managing risks is crucial. A Black Belt uses tools like FMEA and Monte Carlo simulations. They help anticipate risks and implement preventive measures.
For example, in a Kanban workflow, a Black Belt might analyze lead and cycle times. This would identify variability trends. It would ensure smoother and more predictable deliveries.
6. Facilitating Cross-Functional Collaboration
Agile thrives on collaboration across teams, but siloed communication can hinder progress. Six Sigma Black Belts are skilled facilitators. They can bridge gaps between cross-functional teams. They use stakeholder analysis and collaboration tools.
They ensure that all, from developers to product owners, share a common view on quality and process improvement. This fosters a more cohesive and productive Agile environment.
Case Studies: SSBB Success in Agile Organizations
Case Study 1: Improving Sprint Efficiency in a Tech Startup
A technology startup struggled with delayed sprints due to inefficiencies in task prioritization. A Six Sigma Black Belt conducted a root cause analysis and introduced a streamlined prioritization matrix. This reduced sprint delays by 30% while maintaining Agile flexibility.
Case Study 2: Enhancing Quality in a Healthcare Agile Team
A healthcare organization using Agile to develop a patient management system faced issues with recurring defects. A Six Sigma Black Belt used control charts to track quality trends. They then improved processes, reducing defects by 40% in three months.
Challenges for Six Sigma Black Belts in Agile Environments
Despite their strengths, Six Sigma Black Belts may face challenges in Agile settings:
- Resistance to Structured Methods: Agile teams may perceive Six Sigma’s structured approach as restrictive. Black Belts must demonstrate how their methods enhance, rather than hinder, Agile workflows.
- Balancing Speed and Analysis: Agile’s focus on speed can conflict with Six Sigma’s emphasis on thorough analysis. Black Belts must adapt their techniques to align with Agile’s rapid pace.
How to obtain SSBB certification?
We are an Education Technology company providing certification training courses to accelerate careers of working professionals worldwide. We impart training through instructor-led classroom workshops, instructor-led live virtual training sessions, and self-paced e-learning courses.
We have successfully conducted training sessions in 108 countries across the globe and enabled thousands of working professionals to enhance the scope of their careers.
Our enterprise training portfolio includes in-demand and globally recognized certification training courses in Project Management, Quality Management, Business Analysis, IT Service Management, Agile and Scrum, Cyber Security, Data Science, and Emerging Technologies. Download our Enterprise Training Catalog from https://www.icertglobal.com/corporate-training-for-enterprises.php and https://www.icertglobal.com/index.php
Popular Courses include:
-
Project Management: PMP, CAPM ,PMI RMP
-
Quality Management: Six Sigma Black Belt ,Lean Six Sigma Green Belt, Lean Management, Minitab,CMMI
-
Business Analysis: CBAP, CCBA, ECBA
-
Agile Training: PMI-ACP , CSM , CSPO
-
Scrum Training: CSM
-
DevOps
-
Program Management: PgMP
-
Cloud Technology: Exin Cloud Computing
-
Citrix Client Adminisration: Citrix Cloud Administration
The 10 top-paying certifications to target in 2024 are:
Conclusion
A Six Sigma Black Belt's role in Agile organizations is multifaceted. It blends structured problem-solving with Agile's adaptability. Black Belts can add great value in Agile settings. They can do this by streamlining processes, improving quality, and aligning strategy. They can do this by promoting continuous improvement, managing risk, and fostering collaboration.
For organizations wanting to reap the benefits of both methods, it's smart to integrate Six Sigma Black Belts into Agile teams. It ensures efficiency and quality. It also fosters innovation and growth. It's a win-win for all stakeholders.
Contact Us For More Information:
Visit :www.icertglobal.com Email :
Which Quality Management System is Right for Your Business
In today’s world, businesses need to provide high-quality products and services to stay competitive. One way companies do this is by using a Quality Management System (QMS). A QMS is a set of rules, processes, and procedures that help businesses make sure their products or services meet customer needs and meet high standards.
There are different types of Quality Management Systems, and each one helps organizations improve quality in its own way. Let’s look at seven of the most common QMS types and understand how they work.
1. ISO 9001:2015 Quality Management System
What is it? ISO 9001 is one of the most popular and well-known Quality Management Systems. It is used by businesses all over the world. The main goal of ISO 9001 is to make sure that a company’s products or services meet the customer’s expectations and are of good quality.
How it Works: ISO 9001 helps organizations set clear goals for quality, improve their processes, and regularly check how well they are doing. This system makes sure that a company’s processes are effective and that everyone in the company works towards the same goal: providing quality to the customer.
Why it’s Important: ISO 9001 helps companies show that they meet high standards for quality. Being certified under ISO 9001 shows customers that they can trust the company to deliver good products and services. It also helps companies work more efficiently and avoid mistakes.
Example: A company that makes smartphones might use ISO 9001 to improve their manufacturing process. By following the steps in ISO 9001, they can make sure their phones meet high quality standards and reduce defects.
2. Total Quality Management (TQM)
What is it? Total Quality Management (TQM) is a company-wide approach to improving quality. Unlike other systems, TQM involves everyone in the company, from managers to workers, to focus on improving quality in every part of the business.
How it Works: TQM encourages continuous improvement. It means always looking for ways to improve products, services, and processes. The system focuses on understanding customer needs, gathering feedback, and finding ways to make things better.
Why it’s Important: With TQM, everyone in the company is involved in making sure the quality is high. This system helps companies keep customers happy and improve employee satisfaction. When everyone works together, the quality of the product or service increases.
Example: A hotel might use TQM to improve the customer experience. Staff would gather feedback from customers and use it to make improvements to services, like cleaning rooms faster or improving the check-in process.
3. Six Sigma
What is it? Six Sigma is a method that focuses on improving processes by reducing defects and mistakes. The goal is to make sure that products or services have as few problems as possible, aiming for fewer than 3.4 defects per million products.
How it Works: Six Sigma uses a step-by-step method called DMAIC, which stands for Define, Measure, Analyze, Improve, and Control. This method helps companies identify where problems happen, fix them, and then make sure the solutions continue to work.
Why it’s Important: Six Sigma helps companies reduce mistakes and improve quality. By using data to understand where things go wrong, businesses can make decisions that lead to better products and services. Six Sigma is great for industries where precision and high quality are very important.
Example: A car company might use Six Sigma to make sure there are no defects in the parts of the car. By analyzing the data from their production process, they can find problems and fix them to ensure each car meets high standards.
4. Lean Management
What is it? Lean Management is a way of improving efficiency by cutting out waste. In Lean, "waste" means anything that doesn't add value to the customer. The goal is to improve processes so that the company can provide more value while using fewer resources.
How it Works: Lean focuses on making processes smoother and quicker. It looks at all the steps in a process and tries to remove anything unnecessary. By improving how things are done, companies can make products faster and at lower costs, without losing quality.
Why it’s Important: Lean helps companies save money and time by making their processes more efficient. By reducing waste and improving efficiency, companies can offer better products or services and stay competitive.
Example: A clothing manufacturer might use Lean to improve the production of shirts. By eliminating unnecessary steps in the process, they can produce shirts faster and with fewer defects, which helps lower costs and improve customer satisfaction.
5. Capability Maturity Model Integration (CMMI)
What is it? The Capability Maturity Model Integration (CMMI) is a framework used by companies that want to improve how they develop products, especially in fields like software development or engineering. CMMI helps organizations improve their processes to reach higher levels of performance.
How it Works: CMMI works by breaking down process improvement into five levels of maturity:
- Initial: The process is unpredictable and unorganized.
- Managed: The process is planned and controlled.
- Defined: The process is well-documented and standard.
- Quantitatively Managed: The process is measured and controlled using data.
- Optimizing: The process is constantly being improved.
As companies move through these levels, their processes become more efficient and their products become higher quality.
Why it’s Important: CMMI helps companies make sure their processes are organized, effective, and capable of delivering high-quality products. It is especially useful for industries that rely on technology and complex products.
Example: A software company might use CMMI to improve how it develops programs. By improving each stage of the development process, they can reduce errors and produce better software for customers.
6. Balanced Scorecard (BSC)
What is it? The Balanced Scorecard (BSC) is a tool that helps companies measure their performance from different points of view. It doesn’t just look at how much money a company makes but also considers things like customer satisfaction, employee development, and internal processes.
How it Works: The BSC looks at four areas:
- Financial: How well the company is doing financially.
- Customer: How satisfied customers are.
- Internal Processes: How well the company’s internal processes are running.
- Learning and Growth: How well the company is investing in employee development and innovation.
By measuring these areas, companies can get a better idea of how well they are performing overall and where they need to improve.
Why it’s Important: The Balanced Scorecard helps companies achieve long-term success by making sure they focus on more than just profit. It ensures they are improving in all areas, including customer service and employee satisfaction
Example: A retail company might use the Balanced Scorecard to improve not only their sales but also how they treat customers and employees. They could use feedback from customers and staff to make their store a better place to shop and work.
7. Business Process Management (BPM)
What is it? Business Process Management (BPM) is a method that helps companies improve and control their business processes. BPM looks at how work gets done in an organization and finds ways to make it better.
How it Works: BPM involves understanding and analyzing processes, improving them, and then making sure they continue to work well. It looks at the entire workflow and finds areas where things can be improved, whether it’s making a process faster, cheaper, or more efficient.
Why it’s Important: BPM helps organizations improve their processes over time. By regularly looking at how work gets done, companies can ensure that their processes are always efficient and effective.
Example: A hospital might use BPM to improve how they handle patient intake. By streamlining the process, they can reduce wait times, improve care, and make the whole experience better for patients.
How to obtain Quality Management certification?
We are an Education Technology company providing certification training courses to accelerate careers of working professionals worldwide. We impart training through instructor-led classroom workshops, instructor-led live virtual training sessions, and self-paced e-learning courses.
We have successfully conducted training sessions in 108 countries across the globe and enabled thousands of working professionals to enhance the scope of their careers.
Our enterprise training portfolio includes in-demand and globally recognized certification training courses in Project Management, Quality Management, Business Analysis, IT Service Management, Agile and Scrum, Cyber Security, Data Science, and Emerging Technologies. Download our Enterprise Training Catalog from https://www.icertglobal.com/corporate-training-for-enterprises.php and https://www.icertglobal.com/index.php
Popular Courses include:
-
Project Management: PMP, CAPM ,PMI RMP
-
Quality Management: Six Sigma Black Belt ,Lean Six Sigma Green Belt, Lean Management, Minitab,CMMI
-
Business Analysis: CBAP, CCBA, ECBA
-
Agile Training: PMI-ACP , CSM , CSPO
-
Scrum Training: CSM
-
DevOps
-
Program Management: PgMP
-
Cloud Technology: Exin Cloud Computing
-
Citrix Client Adminisration: Citrix Cloud Administration
The 10 top-paying certifications to target in 2025 are:
Conclusion
Quality Management Systems are crucial for organizations that want to provide high-quality products and services. Each system, whether it's ISO 9001, TQM, Six Sigma, Lean, CMMI, Balanced Scorecard, or BPM, has its own strengths and can help businesses improve in different ways. By choosing the right system, businesses can reduce mistakes, improve efficiency, and make sure their customers are happy.
These systems help organizations grow, stay competitive, and continue to deliver quality over time. In today’s fast-paced world, having a good QMS is essential for any business that wants to succeed.
Contact Us For More Information:
Visit :www.icertglobal.com Email : 
Read More
In today’s world, businesses need to provide high-quality products and services to stay competitive. One way companies do this is by using a Quality Management System (QMS). A QMS is a set of rules, processes, and procedures that help businesses make sure their products or services meet customer needs and meet high standards.
There are different types of Quality Management Systems, and each one helps organizations improve quality in its own way. Let’s look at seven of the most common QMS types and understand how they work.
1. ISO 9001:2015 Quality Management System
What is it? ISO 9001 is one of the most popular and well-known Quality Management Systems. It is used by businesses all over the world. The main goal of ISO 9001 is to make sure that a company’s products or services meet the customer’s expectations and are of good quality.
How it Works: ISO 9001 helps organizations set clear goals for quality, improve their processes, and regularly check how well they are doing. This system makes sure that a company’s processes are effective and that everyone in the company works towards the same goal: providing quality to the customer.
Why it’s Important: ISO 9001 helps companies show that they meet high standards for quality. Being certified under ISO 9001 shows customers that they can trust the company to deliver good products and services. It also helps companies work more efficiently and avoid mistakes.
Example: A company that makes smartphones might use ISO 9001 to improve their manufacturing process. By following the steps in ISO 9001, they can make sure their phones meet high quality standards and reduce defects.
2. Total Quality Management (TQM)
What is it? Total Quality Management (TQM) is a company-wide approach to improving quality. Unlike other systems, TQM involves everyone in the company, from managers to workers, to focus on improving quality in every part of the business.
How it Works: TQM encourages continuous improvement. It means always looking for ways to improve products, services, and processes. The system focuses on understanding customer needs, gathering feedback, and finding ways to make things better.
Why it’s Important: With TQM, everyone in the company is involved in making sure the quality is high. This system helps companies keep customers happy and improve employee satisfaction. When everyone works together, the quality of the product or service increases.
Example: A hotel might use TQM to improve the customer experience. Staff would gather feedback from customers and use it to make improvements to services, like cleaning rooms faster or improving the check-in process.
3. Six Sigma
What is it? Six Sigma is a method that focuses on improving processes by reducing defects and mistakes. The goal is to make sure that products or services have as few problems as possible, aiming for fewer than 3.4 defects per million products.
How it Works: Six Sigma uses a step-by-step method called DMAIC, which stands for Define, Measure, Analyze, Improve, and Control. This method helps companies identify where problems happen, fix them, and then make sure the solutions continue to work.
Why it’s Important: Six Sigma helps companies reduce mistakes and improve quality. By using data to understand where things go wrong, businesses can make decisions that lead to better products and services. Six Sigma is great for industries where precision and high quality are very important.
Example: A car company might use Six Sigma to make sure there are no defects in the parts of the car. By analyzing the data from their production process, they can find problems and fix them to ensure each car meets high standards.
4. Lean Management
What is it? Lean Management is a way of improving efficiency by cutting out waste. In Lean, "waste" means anything that doesn't add value to the customer. The goal is to improve processes so that the company can provide more value while using fewer resources.
How it Works: Lean focuses on making processes smoother and quicker. It looks at all the steps in a process and tries to remove anything unnecessary. By improving how things are done, companies can make products faster and at lower costs, without losing quality.
Why it’s Important: Lean helps companies save money and time by making their processes more efficient. By reducing waste and improving efficiency, companies can offer better products or services and stay competitive.
Example: A clothing manufacturer might use Lean to improve the production of shirts. By eliminating unnecessary steps in the process, they can produce shirts faster and with fewer defects, which helps lower costs and improve customer satisfaction.
5. Capability Maturity Model Integration (CMMI)
What is it? The Capability Maturity Model Integration (CMMI) is a framework used by companies that want to improve how they develop products, especially in fields like software development or engineering. CMMI helps organizations improve their processes to reach higher levels of performance.
How it Works: CMMI works by breaking down process improvement into five levels of maturity:
- Initial: The process is unpredictable and unorganized.
- Managed: The process is planned and controlled.
- Defined: The process is well-documented and standard.
- Quantitatively Managed: The process is measured and controlled using data.
- Optimizing: The process is constantly being improved.
As companies move through these levels, their processes become more efficient and their products become higher quality.
Why it’s Important: CMMI helps companies make sure their processes are organized, effective, and capable of delivering high-quality products. It is especially useful for industries that rely on technology and complex products.
Example: A software company might use CMMI to improve how it develops programs. By improving each stage of the development process, they can reduce errors and produce better software for customers.
6. Balanced Scorecard (BSC)
What is it? The Balanced Scorecard (BSC) is a tool that helps companies measure their performance from different points of view. It doesn’t just look at how much money a company makes but also considers things like customer satisfaction, employee development, and internal processes.
How it Works: The BSC looks at four areas:
- Financial: How well the company is doing financially.
- Customer: How satisfied customers are.
- Internal Processes: How well the company’s internal processes are running.
- Learning and Growth: How well the company is investing in employee development and innovation.
By measuring these areas, companies can get a better idea of how well they are performing overall and where they need to improve.
Why it’s Important: The Balanced Scorecard helps companies achieve long-term success by making sure they focus on more than just profit. It ensures they are improving in all areas, including customer service and employee satisfaction
Example: A retail company might use the Balanced Scorecard to improve not only their sales but also how they treat customers and employees. They could use feedback from customers and staff to make their store a better place to shop and work.
7. Business Process Management (BPM)
What is it? Business Process Management (BPM) is a method that helps companies improve and control their business processes. BPM looks at how work gets done in an organization and finds ways to make it better.
How it Works: BPM involves understanding and analyzing processes, improving them, and then making sure they continue to work well. It looks at the entire workflow and finds areas where things can be improved, whether it’s making a process faster, cheaper, or more efficient.
Why it’s Important: BPM helps organizations improve their processes over time. By regularly looking at how work gets done, companies can ensure that their processes are always efficient and effective.
Example: A hospital might use BPM to improve how they handle patient intake. By streamlining the process, they can reduce wait times, improve care, and make the whole experience better for patients.
How to obtain Quality Management certification?
We are an Education Technology company providing certification training courses to accelerate careers of working professionals worldwide. We impart training through instructor-led classroom workshops, instructor-led live virtual training sessions, and self-paced e-learning courses.
We have successfully conducted training sessions in 108 countries across the globe and enabled thousands of working professionals to enhance the scope of their careers.
Our enterprise training portfolio includes in-demand and globally recognized certification training courses in Project Management, Quality Management, Business Analysis, IT Service Management, Agile and Scrum, Cyber Security, Data Science, and Emerging Technologies. Download our Enterprise Training Catalog from https://www.icertglobal.com/corporate-training-for-enterprises.php and https://www.icertglobal.com/index.php
Popular Courses include:
-
Project Management: PMP, CAPM ,PMI RMP
-
Quality Management: Six Sigma Black Belt ,Lean Six Sigma Green Belt, Lean Management, Minitab,CMMI
-
Business Analysis: CBAP, CCBA, ECBA
-
Agile Training: PMI-ACP , CSM , CSPO
-
Scrum Training: CSM
-
DevOps
-
Program Management: PgMP
-
Cloud Technology: Exin Cloud Computing
-
Citrix Client Adminisration: Citrix Cloud Administration
The 10 top-paying certifications to target in 2025 are:
Conclusion
Quality Management Systems are crucial for organizations that want to provide high-quality products and services. Each system, whether it's ISO 9001, TQM, Six Sigma, Lean, CMMI, Balanced Scorecard, or BPM, has its own strengths and can help businesses improve in different ways. By choosing the right system, businesses can reduce mistakes, improve efficiency, and make sure their customers are happy.
These systems help organizations grow, stay competitive, and continue to deliver quality over time. In today’s fast-paced world, having a good QMS is essential for any business that wants to succeed.
Contact Us For More Information:
Visit :www.icertglobal.com Email :
Lean and Six Sigma: A Powerful Duo for Process Excellence
Today, companies want to be more efficient, cut costs, and improve their products and services. Lean and Six Sigma are among the most effective methods to achieve these goals. Both approaches are powerful on their own. But, their combination can create a synergy that drives unmatched process excellence. This blog explores how to integrate Lean and Six Sigma. It covers the benefits of this combination. It also shows how organizations can use it to transform their processes.
Understanding Lean and Six Sigma
Before integrating Lean and Six Sigma, we must know their core principles.
Lean is a philosophy. It aims to maximize value by minimizing waste. In Lean, waste is anything that does not add value to the customer. This includes overproduction, waiting, excess inventory, unnecessary motion, defects, and underused talent. Lean principles are often summed up in the 5S method. It stands for Sort, Set in Order, Shine, Standardize, and Sustain. They also use the Value Stream Mapping (VSM) tool. They help find inefficiencies and areas for improvement in business processes.
Six Sigma, on the other hand, is a data-driven method. It aims to improve process quality by finding and removing defects and variability. Six Sigma aims for a process with only 3.4 defects per million opportunities. The DMAIC (Define, Measure, Analyze, Improve, Control) framework improves processes. It does this by reducing variation and defects. Six Sigma relies on statistical tools to analyze data and make decisions.
Lean and Six Sigma are distinct in their approaches. But, they both aim to improve process efficiency and quality. Lean aims to streamline processes by eliminating waste. Six Sigma aims to reduce variability and defects. These methods, when combined, complement each other. They lead to even greater performance improvements.
The Synergy of Lean and Six Sigma
By combining Lean and Six Sigma, organizations can use the best of both. This will drive process excellence better than using each method alone.
1. Waste Reduction and Defect Prevention
Lean aims to eliminate waste. Six Sigma seeks to reduce defects and variability. They complement each other. In Lean, eliminating waste is key to efficiency. Six Sigma focuses on preventing defects that could harm quality. Applying both principles improves efficiency and quality. This leads to a more effective operation.
2. Improved Decision-Making with Data-Driven Insights
Six Sigma uses data and stats. It helps firms make smart, unbiased choices about improving processes. Lean, though more qualitative, benefits from Six Sigma's data-driven insights. These methods provide a balanced approach to decision-making. They ensure that improvements are data-backed and align with value-stream optimization.
3. Focus on Customer Value
Both Lean and Six Sigma are customer-centric methodologies. Lean seeks to add value by eliminating non-value-adding activities. Six Sigma aims to improve quality to meet customer expectations. The combined approach ensures that all process improvements meet customer needs. These may be faster delivery times, fewer defects, or better customer service.
4. Continuous Improvement Culture
Lean and Six Sigma both promote a culture of continuous improvement. Lean's focus on Kaizen (continuous improvement) and Six Sigma's DMAIC cycle provide good improvement frameworks. They are both structured and flexible. By combining these two methods, organizations foster a culture. Employees are encouraged to find inefficiencies, reduce variability, and improve business processes.
5. Resource Optimization
By cutting waste and boosting quality, orgs can better use their resources. Lean's waste reduction and Six Sigma's defect minimization mean less rework. This saves resources and allows more focus on value-creating activities. It makes better use of time, materials, and labor. This cuts costs and boosts profits.
Implementing Lean Six Sigma
Integrating Lean and Six Sigma requires a careful approach. It means blending two powerful but different methods. Here’s how organizations can begin implementing Lean Six Sigma:
1. Establish Clear Objectives
Before integrating Lean and Six Sigma, organizations must clearly define their goals. Do they want to improve cycle time, reduce defects, optimize resource use, or all of the above? Defining the scope and objectives upfront ensures the work aligns with the company's goals.
2. Train Employees on Both Methodologies
A first step in implementing Lean Six Sigma is to train employees in both Lean and Six Sigma principles. This may involve certification programs, workshops, or seminars. They will ensure that everyone is on the same page. Cross-training employees on both methods boosts their skills. They will better identify waste and defects, analyse processes, and implement improvements.
3. Use the DMAIC Framework with Lean Tools
We can combine the DMAIC framework, central to Six Sigma, with Lean tools for a more holistic approach. For instance, during the Define phase, organizations can use Lean tools. One tool is Value Stream Mapping (VSM). It can help identify waste and focus improvements on the most critical areas. In the Measure and Analyze phases, Six Sigma's data-driven approach can assess waste and defects. It can measure their impact. The Improve phase can use Lean solutions like 5S and Kaizen to streamline processes. The Control phase can ensure that Lean practices are sustained.
4. Leverage Lean Six Sigma Projects
Lean Six Sigma projects often use cross-functional teams. They tackle specific problems with both Lean and Six Sigma methods.
These teams might work on projects to:
-
reduce defects in manufacturing,
-
improve customer service, or
-
increase supply chain efficiency.
We must use both approaches. They target both waste and defects. This will deliver complete improvements.
5. Monitor and Measure Results
Like any improvement initiative, we must monitor and measure the impact of Lean Six Sigma efforts. Regularly assess KPIs like cycle time, cost savings, defect rates, and customer satisfaction. This will show the combined approach's effectiveness. Lean Six Sigma succeeds by delivering measurable improvements in process performance.
The Benefits of Lean Six Sigma
Combining Lean and Six Sigma can benefit organizations in many ways, including:
- Faster Cycle Times: Lean aims to cut waste. Six Sigma seeks to reduce defects. Together, they boost production and service speeds.
- Higher Quality: Six Sigma reduces defects. This improves product quality and customer satisfaction.
- Cost Savings: Lean Six Sigma cuts costs by reducing waste and improving efficiency.
- Improved Employee Engagement: Lean Six Sigma's culture of continuous improvement empowers employees. It encourages them to share ideas and solve problems.
- Competitive Advantage: Combining Lean and Six Sigma gives firms an edge. They can offer faster, higher-quality products and services at a lower cost.
How to obtain Lean Management certification?
We are an Education Technology company providing certification training courses to accelerate careers of working professionals worldwide. We impart training through instructor-led classroom workshops, instructor-led live virtual training sessions, and self-paced e-learning courses.
We have successfully conducted training sessions in 108 countries across the globe and enabled thousands of working professionals to enhance the scope of their careers.
Our enterprise training portfolio includes in-demand and globally recognized certification training courses in Project Management, Quality Management, Business Analysis, IT Service Management, Agile and Scrum, Cyber Security, Data Science, and Emerging Technologies. Download our Enterprise Training Catalog from https://www.icertglobal.com/corporate-training-for-enterprises.php and https://www.icertglobal.com/index.php
Popular Courses include:
-
Project Management: PMP, CAPM ,PMI RMP
-
Quality Management: Six Sigma Black Belt ,Lean Six Sigma Green Belt, Lean Management, Minitab,CMMI
-
Business Analysis: CBAP, CCBA, ECBA
-
Agile Training: PMI-ACP , CSM , CSPO
-
Scrum Training: CSM
-
DevOps
-
Program Management: PgMP
-
Cloud Technology: Exin Cloud Computing
-
Citrix Client Adminisration: Citrix Cloud Administration
The 10 top-paying certifications to target in 2024 are:
Conclusion
Combining Lean and Six Sigma creates a powerful toolkit for driving process excellence. Using Lean's focus on waste and Six Sigma's aim to cut defects, organizations can greatly improve efficiency, quality, and customer satisfaction. These two methods create a culture of constant improvement. It helps businesses stay competitive in a complex, fast-paced world. With careful training, Lean Six Sigma can transform how an organization improves processes. It can deliver lasting value to both customers and the business.
Contact Us For More Information:
Visit :www.icertglobal.com Email : 
Read More
Today, companies want to be more efficient, cut costs, and improve their products and services. Lean and Six Sigma are among the most effective methods to achieve these goals. Both approaches are powerful on their own. But, their combination can create a synergy that drives unmatched process excellence. This blog explores how to integrate Lean and Six Sigma. It covers the benefits of this combination. It also shows how organizations can use it to transform their processes.
Understanding Lean and Six Sigma
Before integrating Lean and Six Sigma, we must know their core principles.
Lean is a philosophy. It aims to maximize value by minimizing waste. In Lean, waste is anything that does not add value to the customer. This includes overproduction, waiting, excess inventory, unnecessary motion, defects, and underused talent. Lean principles are often summed up in the 5S method. It stands for Sort, Set in Order, Shine, Standardize, and Sustain. They also use the Value Stream Mapping (VSM) tool. They help find inefficiencies and areas for improvement in business processes.
Six Sigma, on the other hand, is a data-driven method. It aims to improve process quality by finding and removing defects and variability. Six Sigma aims for a process with only 3.4 defects per million opportunities. The DMAIC (Define, Measure, Analyze, Improve, Control) framework improves processes. It does this by reducing variation and defects. Six Sigma relies on statistical tools to analyze data and make decisions.
Lean and Six Sigma are distinct in their approaches. But, they both aim to improve process efficiency and quality. Lean aims to streamline processes by eliminating waste. Six Sigma aims to reduce variability and defects. These methods, when combined, complement each other. They lead to even greater performance improvements.
The Synergy of Lean and Six Sigma
By combining Lean and Six Sigma, organizations can use the best of both. This will drive process excellence better than using each method alone.
1. Waste Reduction and Defect Prevention
Lean aims to eliminate waste. Six Sigma seeks to reduce defects and variability. They complement each other. In Lean, eliminating waste is key to efficiency. Six Sigma focuses on preventing defects that could harm quality. Applying both principles improves efficiency and quality. This leads to a more effective operation.
2. Improved Decision-Making with Data-Driven Insights
Six Sigma uses data and stats. It helps firms make smart, unbiased choices about improving processes. Lean, though more qualitative, benefits from Six Sigma's data-driven insights. These methods provide a balanced approach to decision-making. They ensure that improvements are data-backed and align with value-stream optimization.
3. Focus on Customer Value
Both Lean and Six Sigma are customer-centric methodologies. Lean seeks to add value by eliminating non-value-adding activities. Six Sigma aims to improve quality to meet customer expectations. The combined approach ensures that all process improvements meet customer needs. These may be faster delivery times, fewer defects, or better customer service.
4. Continuous Improvement Culture
Lean and Six Sigma both promote a culture of continuous improvement. Lean's focus on Kaizen (continuous improvement) and Six Sigma's DMAIC cycle provide good improvement frameworks. They are both structured and flexible. By combining these two methods, organizations foster a culture. Employees are encouraged to find inefficiencies, reduce variability, and improve business processes.
5. Resource Optimization
By cutting waste and boosting quality, orgs can better use their resources. Lean's waste reduction and Six Sigma's defect minimization mean less rework. This saves resources and allows more focus on value-creating activities. It makes better use of time, materials, and labor. This cuts costs and boosts profits.
Implementing Lean Six Sigma
Integrating Lean and Six Sigma requires a careful approach. It means blending two powerful but different methods. Here’s how organizations can begin implementing Lean Six Sigma:
1. Establish Clear Objectives
Before integrating Lean and Six Sigma, organizations must clearly define their goals. Do they want to improve cycle time, reduce defects, optimize resource use, or all of the above? Defining the scope and objectives upfront ensures the work aligns with the company's goals.
2. Train Employees on Both Methodologies
A first step in implementing Lean Six Sigma is to train employees in both Lean and Six Sigma principles. This may involve certification programs, workshops, or seminars. They will ensure that everyone is on the same page. Cross-training employees on both methods boosts their skills. They will better identify waste and defects, analyse processes, and implement improvements.
3. Use the DMAIC Framework with Lean Tools
We can combine the DMAIC framework, central to Six Sigma, with Lean tools for a more holistic approach. For instance, during the Define phase, organizations can use Lean tools. One tool is Value Stream Mapping (VSM). It can help identify waste and focus improvements on the most critical areas. In the Measure and Analyze phases, Six Sigma's data-driven approach can assess waste and defects. It can measure their impact. The Improve phase can use Lean solutions like 5S and Kaizen to streamline processes. The Control phase can ensure that Lean practices are sustained.
4. Leverage Lean Six Sigma Projects
Lean Six Sigma projects often use cross-functional teams. They tackle specific problems with both Lean and Six Sigma methods.
These teams might work on projects to:
-
reduce defects in manufacturing,
-
improve customer service, or
-
increase supply chain efficiency.
We must use both approaches. They target both waste and defects. This will deliver complete improvements.
5. Monitor and Measure Results
Like any improvement initiative, we must monitor and measure the impact of Lean Six Sigma efforts. Regularly assess KPIs like cycle time, cost savings, defect rates, and customer satisfaction. This will show the combined approach's effectiveness. Lean Six Sigma succeeds by delivering measurable improvements in process performance.
The Benefits of Lean Six Sigma
Combining Lean and Six Sigma can benefit organizations in many ways, including:
- Faster Cycle Times: Lean aims to cut waste. Six Sigma seeks to reduce defects. Together, they boost production and service speeds.
- Higher Quality: Six Sigma reduces defects. This improves product quality and customer satisfaction.
- Cost Savings: Lean Six Sigma cuts costs by reducing waste and improving efficiency.
- Improved Employee Engagement: Lean Six Sigma's culture of continuous improvement empowers employees. It encourages them to share ideas and solve problems.
- Competitive Advantage: Combining Lean and Six Sigma gives firms an edge. They can offer faster, higher-quality products and services at a lower cost.
How to obtain Lean Management certification?
We are an Education Technology company providing certification training courses to accelerate careers of working professionals worldwide. We impart training through instructor-led classroom workshops, instructor-led live virtual training sessions, and self-paced e-learning courses.
We have successfully conducted training sessions in 108 countries across the globe and enabled thousands of working professionals to enhance the scope of their careers.
Our enterprise training portfolio includes in-demand and globally recognized certification training courses in Project Management, Quality Management, Business Analysis, IT Service Management, Agile and Scrum, Cyber Security, Data Science, and Emerging Technologies. Download our Enterprise Training Catalog from https://www.icertglobal.com/corporate-training-for-enterprises.php and https://www.icertglobal.com/index.php
Popular Courses include:
-
Project Management: PMP, CAPM ,PMI RMP
-
Quality Management: Six Sigma Black Belt ,Lean Six Sigma Green Belt, Lean Management, Minitab,CMMI
-
Business Analysis: CBAP, CCBA, ECBA
-
Agile Training: PMI-ACP , CSM , CSPO
-
Scrum Training: CSM
-
DevOps
-
Program Management: PgMP
-
Cloud Technology: Exin Cloud Computing
-
Citrix Client Adminisration: Citrix Cloud Administration
The 10 top-paying certifications to target in 2024 are:
Conclusion
Combining Lean and Six Sigma creates a powerful toolkit for driving process excellence. Using Lean's focus on waste and Six Sigma's aim to cut defects, organizations can greatly improve efficiency, quality, and customer satisfaction. These two methods create a culture of constant improvement. It helps businesses stay competitive in a complex, fast-paced world. With careful training, Lean Six Sigma can transform how an organization improves processes. It can deliver lasting value to both customers and the business.
Contact Us For More Information:
Visit :www.icertglobal.com Email :
Boost Your Software Testing Career with CTFL Certification
In the ever-evolving field of software development, ensuring the quality of products is paramount. This has led to a growing demand for skilled software testers who can identify bugs, improve software reliability, and contribute to efficient product development. The Certified Tester Foundation Level (CTFL) certification, awarded by the International Software Testing Qualifications Board (ISTQB), has become a key credential for professionals in the software testing domain.
Obtaining a CTF certification can significantly boost your career by enhancing your skills, improving your job prospects, and making you a more competitive candidate in the job market. In this blog, we’ll explore the various ways in which CTFL certification can propel your career in software testing.
1. Solid Foundation in Software Testing
The CTFL certification is designed to provide a strong foundation in software testing principles. This certification covers a wide array of key concepts essential for anyone involved in the testing process. Whether you are new to testing or have some experience, the CTFL certification helps you master the basic principles that are fundamental to all testing activities.
Some of the core topics included in the CTFL syllabus are:
- Testing principles and processes: Learn the standard practices for planning, executing, and evaluating tests.
- Test design techniques: Understand how to create comprehensive test cases and use various techniques like equivalence partitioning, boundary value analysis, and decision tables.
- Testing lifecycle: Gain insights into all phases of testing, from test planning and design to execution and defect reporting.
- Types of testing: Learn the different types of testing such as functional, non-functional, acceptance, and regression testing.
By obtaining the CTFL certification, you ensure that you have a comprehensive understanding of the fundamental aspects of software testing, which is crucial for tackling real-world challenges in the field.
2. Enhanced Career Opportunities
As the software testing industry continues to grow, the demand for qualified testers is increasing. Employers are on the lookout for candidates who possess recognized certifications and a deep understanding of the best practices in the industry. The CTFL certification is one such credential that can help you stand out among other candidates.
Here's how CTFL can open new career doors:
- Increased employability: With more companies seeking certified professionals, having the CTFL certification on your resume can make you a more attractive candidate. Many organizations require their testers to be certified to ensure that their testing practices align with global standards.
- Higher-paying roles: Certified professionals are often rewarded with better pay and opportunities for career advancement. The CTFL certification serves as proof of your competency and increases your chances of landing higher-paying jobs in software testing and quality assurance.
- Access to a wider range of roles: With CTFL certification, you qualify for roles such as test analyst, test engineer, QA analyst, and even management roles in testing teams. It also prepares you for specialized testing areas like automated testing or performance testing.
By earning CTFL, you open yourself up to a wider range of job opportunities, and increase your chances of landing your ideal role in the software testing field.
3. Global Recognition and Credibility
The CTFL certification is internationally recognized, which means it has value across the globe. No matter where you're located or where you want to work, CTFL certification gives you a universal credential that is respected by employers around the world.
Here’s how the global recognition of CTFL can enhance your career:
- International job prospects: Since the certification is recognized globally, it allows you to explore job opportunities not just locally, but also abroad. As companies increasingly work in global teams, employers seek testers with internationally recognized qualifications.
- Credibility in the industry: The CTFL certification establishes your credibility as a software testing professional. It assures potential employers and clients that you are proficient in the core concepts and best practices of software testing, which can lead to better job security and more opportunities for career growth.
With CTFL, you gain a globally acknowledged credential that boosts your professional reputation and enhances your career prospects worldwide.
4. Improved Skill Set and Industry Knowledge
In the fast-paced world of software development, staying current with the latest testing methodologies, tools, and technologies is crucial. The CTFL certification ensures that you have a deep understanding of both traditional and modern software testing practices. By preparing for and passing the CTFL exam, you acquire skills that are highly valued by employers.
Some key benefits in terms of skill improvement include:
- Comprehensive understanding of testing methodologies: Whether it's Waterfall, V-Model, or Agile, CTFL covers various testing methodologies, equipping you with the knowledge to work in diverse environments. As organizations continue to adopt Agile and DevOps practices, this versatility becomes a major asset.
- Better problem-solving abilities: With knowledge of test design techniques and the testing lifecycle, you'll be more adept at identifying issues, devising solutions, and applying corrective measures throughout the software development process.
- Knowledge of automation: While CTFL focuses on manual testing, the principles taught in the certification serve as a strong foundation for understanding test automation in the future. As automation continues to grow in importance, a solid understanding of testing fundamentals is critical to effectively integrating automated testing into your workflow.
Overall, the CTFL certification helps you sharpen your skills, stay updated on industry trends, and become a more competent and adaptable tester.
5. Opportunities for Career Advancement
While CTFL is often seen as a starting point for testers, it also plays an important role in career advancement. By completing the certification, you demonstrate that you are committed to your career growth and are serious about professional development. Moreover, CTFL opens up pathways for advanced certifications, enabling you to climb higher on the career ladder.
After obtaining the CTFL certification, you can pursue additional certifications such as:
- ISTQB Advanced Level Certifications: These certifications delve deeper into specific areas of testing, including test management, test analysis, and test automation. They are ideal for those looking to specialize in particular aspects of software testing.
- Certified Agile Tester (CAT): As Agile methodologies become more prevalent in software development, this certification will equip you with the knowledge to work effectively within Agile teams.
- Certified Test Automation Engineer (CTAE): For testers interested in automating tests, this certification provides in-depth knowledge of test automation tools and techniques.
By building on your CTFL certification, you can advance to higher roles such as test lead, test manager, or even move into specialized roles like automation engineer or performance tester.
6. Better Understanding of Agile and DevOps Environments
As Agile and DevOps continue to transform how software is developed and tested, testers need to be well-versed in these methodologies to contribute effectively to teams. CTFL certification includes training in Agile testing principles and how testing fits into these dynamic environments.
By earning CTFL, you’ll gain:
- Knowledge of Agile practices: The CTFL syllabus covers the basics of Agile methodologies, including how testing fits into an Agile environment. You’ll understand the role of testing in iterative cycles and be equipped to work in Agile teams.
- Understanding of DevOps principles: Although DevOps is not the primary focus of CTFL, the certification introduces testers to the concepts of continuous testing and integration, which are central to the DevOps culture. This knowledge will prove valuable as you progress in your career and work with integrated development and operations teams.
By becoming proficient in Agile and DevOps, you increase your value to organizations that are adopting these practices, which in turn helps with career growth and stability.
How to obtain the CTFL certification?
We are an Education Technology company providing certification training courses to accelerate careers of working professionals worldwide. We impart training through instructor-led classroom workshops, instructor-led live virtual training sessions, and self-paced e-learning courses.
We have successfully conducted training sessions in 108 countries across the globe and enabled thousands of working professionals to enhance the scope of their careers.
Our enterprise training portfolio includes in-demand and globally recognized certification training courses in Project Management, Quality Management, Business Analysis, IT Service Management, Agile and Scrum, Cyber Security, Data Science, and Emerging Technologies. Download our Enterprise Training Catalog from https://www.icertglobal.com/corporate-training-for-enterprises.php
Popular Courses include:
- Project Management: PMP, CAPM ,PMI RMP
- Quality Management: Six Sigma Black Belt ,Lean Six Sigma Green Belt, Lean Management, Minitab , CTFL
- Business Analysis: CBAP, CCBA, ECBA
- Agile Training: PMI-ACP
- Scrum Training: CSM
- DevOps
- Program Management: PgMP
- IT Service Management & Governance: COBIT, ISO
Conclusion
Obtaining the Certified Tester Foundation Level (CTFL) certification is one of the best ways to advance your career in software testing. By providing a solid foundation in testing principles, enhancing your credibility, and offering global recognition, CTFL can set you apart in a competitive job market.
Furthermore, it opens up opportunities for higher-paying roles, career advancement, and continued professional development. Whether you're just beginning your career in software testing or looking to expand your expertise, CTFL is a powerful tool for achieving long-term success in the field.
In a fast-changing industry, the CTFL certification ensures that you are well-equipped to meet the challenges of modern software testing and remain competitive in the job market for years to come.
Contact Us For More Information:
Visit :www.icertglobal.com Email : 
Read More
In the ever-evolving field of software development, ensuring the quality of products is paramount. This has led to a growing demand for skilled software testers who can identify bugs, improve software reliability, and contribute to efficient product development. The Certified Tester Foundation Level (CTFL) certification, awarded by the International Software Testing Qualifications Board (ISTQB), has become a key credential for professionals in the software testing domain.
Obtaining a CTF certification can significantly boost your career by enhancing your skills, improving your job prospects, and making you a more competitive candidate in the job market. In this blog, we’ll explore the various ways in which CTFL certification can propel your career in software testing.
1. Solid Foundation in Software Testing
The CTFL certification is designed to provide a strong foundation in software testing principles. This certification covers a wide array of key concepts essential for anyone involved in the testing process. Whether you are new to testing or have some experience, the CTFL certification helps you master the basic principles that are fundamental to all testing activities.
Some of the core topics included in the CTFL syllabus are:
- Testing principles and processes: Learn the standard practices for planning, executing, and evaluating tests.
- Test design techniques: Understand how to create comprehensive test cases and use various techniques like equivalence partitioning, boundary value analysis, and decision tables.
- Testing lifecycle: Gain insights into all phases of testing, from test planning and design to execution and defect reporting.
- Types of testing: Learn the different types of testing such as functional, non-functional, acceptance, and regression testing.
By obtaining the CTFL certification, you ensure that you have a comprehensive understanding of the fundamental aspects of software testing, which is crucial for tackling real-world challenges in the field.
2. Enhanced Career Opportunities
As the software testing industry continues to grow, the demand for qualified testers is increasing. Employers are on the lookout for candidates who possess recognized certifications and a deep understanding of the best practices in the industry. The CTFL certification is one such credential that can help you stand out among other candidates.
Here's how CTFL can open new career doors:
- Increased employability: With more companies seeking certified professionals, having the CTFL certification on your resume can make you a more attractive candidate. Many organizations require their testers to be certified to ensure that their testing practices align with global standards.
- Higher-paying roles: Certified professionals are often rewarded with better pay and opportunities for career advancement. The CTFL certification serves as proof of your competency and increases your chances of landing higher-paying jobs in software testing and quality assurance.
- Access to a wider range of roles: With CTFL certification, you qualify for roles such as test analyst, test engineer, QA analyst, and even management roles in testing teams. It also prepares you for specialized testing areas like automated testing or performance testing.
By earning CTFL, you open yourself up to a wider range of job opportunities, and increase your chances of landing your ideal role in the software testing field.
3. Global Recognition and Credibility
The CTFL certification is internationally recognized, which means it has value across the globe. No matter where you're located or where you want to work, CTFL certification gives you a universal credential that is respected by employers around the world.
Here’s how the global recognition of CTFL can enhance your career:
- International job prospects: Since the certification is recognized globally, it allows you to explore job opportunities not just locally, but also abroad. As companies increasingly work in global teams, employers seek testers with internationally recognized qualifications.
- Credibility in the industry: The CTFL certification establishes your credibility as a software testing professional. It assures potential employers and clients that you are proficient in the core concepts and best practices of software testing, which can lead to better job security and more opportunities for career growth.
With CTFL, you gain a globally acknowledged credential that boosts your professional reputation and enhances your career prospects worldwide.
4. Improved Skill Set and Industry Knowledge
In the fast-paced world of software development, staying current with the latest testing methodologies, tools, and technologies is crucial. The CTFL certification ensures that you have a deep understanding of both traditional and modern software testing practices. By preparing for and passing the CTFL exam, you acquire skills that are highly valued by employers.
Some key benefits in terms of skill improvement include:
- Comprehensive understanding of testing methodologies: Whether it's Waterfall, V-Model, or Agile, CTFL covers various testing methodologies, equipping you with the knowledge to work in diverse environments. As organizations continue to adopt Agile and DevOps practices, this versatility becomes a major asset.
- Better problem-solving abilities: With knowledge of test design techniques and the testing lifecycle, you'll be more adept at identifying issues, devising solutions, and applying corrective measures throughout the software development process.
- Knowledge of automation: While CTFL focuses on manual testing, the principles taught in the certification serve as a strong foundation for understanding test automation in the future. As automation continues to grow in importance, a solid understanding of testing fundamentals is critical to effectively integrating automated testing into your workflow.
Overall, the CTFL certification helps you sharpen your skills, stay updated on industry trends, and become a more competent and adaptable tester.
5. Opportunities for Career Advancement
While CTFL is often seen as a starting point for testers, it also plays an important role in career advancement. By completing the certification, you demonstrate that you are committed to your career growth and are serious about professional development. Moreover, CTFL opens up pathways for advanced certifications, enabling you to climb higher on the career ladder.
After obtaining the CTFL certification, you can pursue additional certifications such as:
- ISTQB Advanced Level Certifications: These certifications delve deeper into specific areas of testing, including test management, test analysis, and test automation. They are ideal for those looking to specialize in particular aspects of software testing.
- Certified Agile Tester (CAT): As Agile methodologies become more prevalent in software development, this certification will equip you with the knowledge to work effectively within Agile teams.
- Certified Test Automation Engineer (CTAE): For testers interested in automating tests, this certification provides in-depth knowledge of test automation tools and techniques.
By building on your CTFL certification, you can advance to higher roles such as test lead, test manager, or even move into specialized roles like automation engineer or performance tester.
6. Better Understanding of Agile and DevOps Environments
As Agile and DevOps continue to transform how software is developed and tested, testers need to be well-versed in these methodologies to contribute effectively to teams. CTFL certification includes training in Agile testing principles and how testing fits into these dynamic environments.
By earning CTFL, you’ll gain:
- Knowledge of Agile practices: The CTFL syllabus covers the basics of Agile methodologies, including how testing fits into an Agile environment. You’ll understand the role of testing in iterative cycles and be equipped to work in Agile teams.
- Understanding of DevOps principles: Although DevOps is not the primary focus of CTFL, the certification introduces testers to the concepts of continuous testing and integration, which are central to the DevOps culture. This knowledge will prove valuable as you progress in your career and work with integrated development and operations teams.
By becoming proficient in Agile and DevOps, you increase your value to organizations that are adopting these practices, which in turn helps with career growth and stability.
How to obtain the CTFL certification?
We are an Education Technology company providing certification training courses to accelerate careers of working professionals worldwide. We impart training through instructor-led classroom workshops, instructor-led live virtual training sessions, and self-paced e-learning courses.
We have successfully conducted training sessions in 108 countries across the globe and enabled thousands of working professionals to enhance the scope of their careers.
Our enterprise training portfolio includes in-demand and globally recognized certification training courses in Project Management, Quality Management, Business Analysis, IT Service Management, Agile and Scrum, Cyber Security, Data Science, and Emerging Technologies. Download our Enterprise Training Catalog from https://www.icertglobal.com/corporate-training-for-enterprises.php
Popular Courses include:
- Project Management: PMP, CAPM ,PMI RMP
- Quality Management: Six Sigma Black Belt ,Lean Six Sigma Green Belt, Lean Management, Minitab , CTFL
- Business Analysis: CBAP, CCBA, ECBA
- Agile Training: PMI-ACP
- Scrum Training: CSM
- DevOps
- Program Management: PgMP
- IT Service Management & Governance: COBIT, ISO
Conclusion
Obtaining the Certified Tester Foundation Level (CTFL) certification is one of the best ways to advance your career in software testing. By providing a solid foundation in testing principles, enhancing your credibility, and offering global recognition, CTFL can set you apart in a competitive job market.
Furthermore, it opens up opportunities for higher-paying roles, career advancement, and continued professional development. Whether you're just beginning your career in software testing or looking to expand your expertise, CTFL is a powerful tool for achieving long-term success in the field.
In a fast-changing industry, the CTFL certification ensures that you are well-equipped to meet the challenges of modern software testing and remain competitive in the job market for years to come.
Contact Us For More Information:
Visit :www.icertglobal.com Email :
Mastering Six Sigma Your Path from Green Belt to Black Belt
Lean Six Sigma is a powerful method. It helps organizations improve their processes, reduce waste, and become more efficient. If you're a Green Belt in Lean Six Sigma, consider getting a Black Belt. It's a great way to advance your career. The Green Belt focuses on solving problems and managing projects. The Black Belt involves more leadership, advanced problem-solving, and data analysis. This blog will compare the Green Belt and Black Belt certifications. We'll also cover the skills needed for this transition.
What’s the Difference Between Green Belt and Black Belt?
Before exploring the advanced skills of a Black Belt, let's first see how the Green and Black Belt levels differ.
- Green Belt: Green Belts usually lead small projects. They work to improve specific processes. They use Lean Six Sigma tools to solve problems and make improvements. Green Belts often work under the guidance of a Black Belt or Master Black Belt.
- Black Belt: Black Belts are experts in Lean Six Sigma. They lead large, complex projects and manage cross-functional teams. Black Belts mentor Green Belts. They also lead the strategy for continuous improvement in an organization.
Key Skills to Move from Green Belt to Black Belt
When you move from a Green Belt to a Black Belt, you need to develop a few key skills to handle bigger challenges. Here are some of the important skills that make Black Belts stand out:
1. Advanced Statistical Analysis and Data Interpretation
A key difference between Green Belts and Black Belts is the level of required statistical analysis. Green Belts use basic tools like control charts and histograms, while Black Belts work with more complex methods to analyze data, such as:
- Regression Analysis: Helps you understand relationships between different variables and predict future results.
- Design of Experiments (DOE): A method to test multiple factors at once. It finds which ones most affect a process.
- ANOVA: It compares groups to find significant differences.
- Hypothesis Testing: Helps validate assumptions about processes or solutions.
These techniques let Black Belts find deeper insights. They can then make better decisions, leading to big improvements.
2. Project Leadership and Management
As a Black Belt, you'll take on more leadership responsibilities. Here’s what it involves:
- Leading Teams: Black Belts must lead teams in complex problem-solving. They need strong leadership skills for this. This includes effective communication, conflict resolution, and motivating team members.
- Project Management: You must manage larger projects. This means setting goals, planning schedules, and managing risks. You must ensure projects finish on time and meet their goals.
- Change Management: Lean Six Sigma projects often require changes within the organization. Black Belts must manage resistance, address stakeholders' concerns, and ensure changes stick.
3. Strategic Thinking and Problem Solving
Green Belts focus on specific problems. Black Belts solve problems that affect the organization's goals. To do this, Black Belts must:
- Know the Business Strategy: Link Lean Six Sigma projects to the company's big goals. These are to improve customer satisfaction and grow revenue.
- Think Systemically: Black Belts focus on the whole system, not just individual processes. They know how different processes interact. Changes in one area can affect other parts of the organization.
4. Mentoring and Training Green Belts
Black Belts are also expected to help Green Belts grow by:
- Providing Guidance: Black Belts help Green Belts on complex projects. They ensure that they apply Lean Six Sigma principles correctly.
- Training: Black Belts teach new Green Belts about Lean Six Sigma tools. This builds a culture of continuous improvement.
- Standardizing Practices: They ensure consistent use of Lean Six Sigma across the organization. This helps reduce variability and improve processes.
5. Driving Organizational Change
Black Belts aren’t just problem-solvers; they also drive change across the organization. This means:
- Continuous Improvement: Black Belts foster a culture of constant process improvement.
- Sustainability: A key goal for Black Belts is to make improvements last over time. They embed Lean Six Sigma principles into the company's daily operations. This ensures changes last after the project ends.
How to Make the Transition
If you want to go from Green Belt to Black Belt, here are some steps to follow:
- Learn Advanced Statistical Techniques: Take courses or workshops on advanced stats. They should teach data-driven decision-making.
- Gain Leadership Experience: Look for chances to manage larger projects or teams. The more experience you get in leadership, the more prepared you will be for a Black Belt role.
- Think Strategically: Understand your organization's goals. Align your Lean Six Sigma projects with them.
- Find a Mentor: Reach out to current Black Belts or Master Black Belts. Their advice will be very valuable as you transition to the Black Belt role.
How to obtain Six sigma certification?
We are an Education Technology company providing certification training courses to accelerate careers of working professionals worldwide. We impart training through instructor-led classroom workshops, instructor-led live virtual training sessions, and self-paced e-learning courses.
We have successfully conducted training sessions in 108 countries across the globe and enabled thousands of working professionals to enhance the scope of their careers.
Our enterprise training portfolio includes in-demand and globally recognized certification training courses in Project Management, Quality Management, Business Analysis, IT Service Management, Agile and Scrum, Cyber Security, Data Science, and Emerging Technologies. Download our Enterprise Training Catalog from https://www.icertglobal.com/corporate-training-for-enterprises.php and https://www.icertglobal.com/index.php
Popular Courses include:
-
Project Management: PMP, CAPM ,PMI RMP
-
Quality Management: Six Sigma Black Belt ,Lean Six Sigma Green Belt, Lean Management, Minitab,CMMI
-
Business Analysis: CBAP, CCBA, ECBA
-
Agile Training: PMI-ACP , CSM , CSPO
-
Scrum Training: CSM
-
DevOps
-
Program Management: PgMP
-
Cloud Technology: Exin Cloud Computing
-
Citrix Client Adminisration: Citrix Cloud Administration
The 10 top-paying certifications to target in 2024 are:
Conclusion
Becoming a Black Belt is a big step in your Lean Six Sigma journey. Both Green Belts and Black Belts improve processes. But, Black Belts go much deeper in stats, project management, and leadership. They also excel at strategic thinking. With these skills, you can lead big projects and drive change in your organization. If you're ready to boost your Lean Six Sigma career, get a Black Belt certification. It will help you make a bigger impact.
Contact Us For More Information:
Visit :www.icertglobal.com Email : 
Read More
Lean Six Sigma is a powerful method. It helps organizations improve their processes, reduce waste, and become more efficient. If you're a Green Belt in Lean Six Sigma, consider getting a Black Belt. It's a great way to advance your career. The Green Belt focuses on solving problems and managing projects. The Black Belt involves more leadership, advanced problem-solving, and data analysis. This blog will compare the Green Belt and Black Belt certifications. We'll also cover the skills needed for this transition.
What’s the Difference Between Green Belt and Black Belt?
Before exploring the advanced skills of a Black Belt, let's first see how the Green and Black Belt levels differ.
- Green Belt: Green Belts usually lead small projects. They work to improve specific processes. They use Lean Six Sigma tools to solve problems and make improvements. Green Belts often work under the guidance of a Black Belt or Master Black Belt.
- Black Belt: Black Belts are experts in Lean Six Sigma. They lead large, complex projects and manage cross-functional teams. Black Belts mentor Green Belts. They also lead the strategy for continuous improvement in an organization.
Key Skills to Move from Green Belt to Black Belt
When you move from a Green Belt to a Black Belt, you need to develop a few key skills to handle bigger challenges. Here are some of the important skills that make Black Belts stand out:
1. Advanced Statistical Analysis and Data Interpretation
A key difference between Green Belts and Black Belts is the level of required statistical analysis. Green Belts use basic tools like control charts and histograms, while Black Belts work with more complex methods to analyze data, such as:
- Regression Analysis: Helps you understand relationships between different variables and predict future results.
- Design of Experiments (DOE): A method to test multiple factors at once. It finds which ones most affect a process.
- ANOVA: It compares groups to find significant differences.
- Hypothesis Testing: Helps validate assumptions about processes or solutions.
These techniques let Black Belts find deeper insights. They can then make better decisions, leading to big improvements.
2. Project Leadership and Management
As a Black Belt, you'll take on more leadership responsibilities. Here’s what it involves:
- Leading Teams: Black Belts must lead teams in complex problem-solving. They need strong leadership skills for this. This includes effective communication, conflict resolution, and motivating team members.
- Project Management: You must manage larger projects. This means setting goals, planning schedules, and managing risks. You must ensure projects finish on time and meet their goals.
- Change Management: Lean Six Sigma projects often require changes within the organization. Black Belts must manage resistance, address stakeholders' concerns, and ensure changes stick.
3. Strategic Thinking and Problem Solving
Green Belts focus on specific problems. Black Belts solve problems that affect the organization's goals. To do this, Black Belts must:
- Know the Business Strategy: Link Lean Six Sigma projects to the company's big goals. These are to improve customer satisfaction and grow revenue.
- Think Systemically: Black Belts focus on the whole system, not just individual processes. They know how different processes interact. Changes in one area can affect other parts of the organization.
4. Mentoring and Training Green Belts
Black Belts are also expected to help Green Belts grow by:
- Providing Guidance: Black Belts help Green Belts on complex projects. They ensure that they apply Lean Six Sigma principles correctly.
- Training: Black Belts teach new Green Belts about Lean Six Sigma tools. This builds a culture of continuous improvement.
- Standardizing Practices: They ensure consistent use of Lean Six Sigma across the organization. This helps reduce variability and improve processes.
5. Driving Organizational Change
Black Belts aren’t just problem-solvers; they also drive change across the organization. This means:
- Continuous Improvement: Black Belts foster a culture of constant process improvement.
- Sustainability: A key goal for Black Belts is to make improvements last over time. They embed Lean Six Sigma principles into the company's daily operations. This ensures changes last after the project ends.
How to Make the Transition
If you want to go from Green Belt to Black Belt, here are some steps to follow:
- Learn Advanced Statistical Techniques: Take courses or workshops on advanced stats. They should teach data-driven decision-making.
- Gain Leadership Experience: Look for chances to manage larger projects or teams. The more experience you get in leadership, the more prepared you will be for a Black Belt role.
- Think Strategically: Understand your organization's goals. Align your Lean Six Sigma projects with them.
- Find a Mentor: Reach out to current Black Belts or Master Black Belts. Their advice will be very valuable as you transition to the Black Belt role.
How to obtain Six sigma certification?
We are an Education Technology company providing certification training courses to accelerate careers of working professionals worldwide. We impart training through instructor-led classroom workshops, instructor-led live virtual training sessions, and self-paced e-learning courses.
We have successfully conducted training sessions in 108 countries across the globe and enabled thousands of working professionals to enhance the scope of their careers.
Our enterprise training portfolio includes in-demand and globally recognized certification training courses in Project Management, Quality Management, Business Analysis, IT Service Management, Agile and Scrum, Cyber Security, Data Science, and Emerging Technologies. Download our Enterprise Training Catalog from https://www.icertglobal.com/corporate-training-for-enterprises.php and https://www.icertglobal.com/index.php
Popular Courses include:
-
Project Management: PMP, CAPM ,PMI RMP
-
Quality Management: Six Sigma Black Belt ,Lean Six Sigma Green Belt, Lean Management, Minitab,CMMI
-
Business Analysis: CBAP, CCBA, ECBA
-
Agile Training: PMI-ACP , CSM , CSPO
-
Scrum Training: CSM
-
DevOps
-
Program Management: PgMP
-
Cloud Technology: Exin Cloud Computing
-
Citrix Client Adminisration: Citrix Cloud Administration
The 10 top-paying certifications to target in 2024 are:
Conclusion
Becoming a Black Belt is a big step in your Lean Six Sigma journey. Both Green Belts and Black Belts improve processes. But, Black Belts go much deeper in stats, project management, and leadership. They also excel at strategic thinking. With these skills, you can lead big projects and drive change in your organization. If you're ready to boost your Lean Six Sigma career, get a Black Belt certification. It will help you make a bigger impact.
Contact Us For More Information:
Visit :www.icertglobal.com Email :
A Complete Guide to DOE Design of Experiments in Minitab
In today's data-driven world, experimentation is vital. It helps us understand processes, find key factors, and improve performance. Design of Experiments (DOE) is a method for tests. It is systematic and efficient. It helps in planning, conducting, and analyzing controlled tests. Minitab is a popular statistical tool. It simplifies the entire DOE process. It's now accessible to those with limited stats knowledge.
This guide will explore DOE. We'll cover its importance. We'll also show how Minitab helps users run experiments. It optimizes processes and achieves results.
What is Design of Experiments (DOE)?
Design of Experiments (DOE) is a statistical method. It finds the relationship between different factors and their impact on an outcome. DOE lets organizations test multiple variables at once. This reduces experiment time, improves efficiency, and provides insights.
For example:
A manufacturer might test temperature, pressure, and material to optimize quality.
A marketer might test ad copy, audience segments, and timing to boost conversions.
DOE identifies key factors (inputs) and their interactions that influence the outcome (response).
Why is DOE Important?
- Efficiency: DOE tests multiple variables at once, instead of one at a time (which is slow).
- Optimization: Helps identify the best combination of factors for improving performance.
- Cost Savings: Reduces resources needed for experimentation.
- Insights: Reveals interactions between factors that are otherwise difficult to identify.
DOE is widely used across industries like manufacturing, pharmaceuticals, healthcare, marketing, and engineering.
Introduction to DOE in Minitab
Minitab is a powerful tool for DOE. It simplifies the setup, execution, and analysis of experiments. With a user-friendly interface, Minitab allows users to:
1. Plan and design experiments.
2. Analyze results using statistical methods.
3. Visualize results with graphs and plots.
Minitab supports the following types of DOE:
- Factorial Designs
- Response Surface Designs
- Mixture Designs
- Taguchi Designs
Let’s dive into the steps to perform DOE in Minitab.
Step 1: Planning the Experiment
Before diving into Minitab, you must plan your experiment:
1. Define the Problem: What is the goal of the experiment?
Example: Improving product strength by testing temperature, pressure, and curing time.
2. Identify Factors: List the variables you want to study.
Example: Temperature (°C), Pressure (bar), Curing Time (minutes).
3. Determine Levels: Identify the values for each factor (e.g., high/low levels).
Example:
- Temperature: 150°C and 200°C
- Pressure: 50 bar and 100 bar
4. Choose Response Variable: What outcome will you measure?
Example: Product strength (measured in MPa).
Step 2: Creating a Factorial Design in Minitab
Factorial designs are one of the most commonly used DOE types in Minitab. Follow these steps:
1. Open Minitab and navigate to:
- Stat > DOE > Factorial > Create Factorial Design.
2. Choose the Number of Factors: Select the number of variables (e.g., 2 or 3).
- Example: 3 factors (Temperature, Pressure, Curing Time).
3. Specify Design Options:
- Full Factorial: Tests all possible combinations.
- Fractional Factorial: Tests a subset of combinations to save resources.
4. Enter Factor Names and Levels: Input your variables and their high/low levels.
- Temperature: 150°C and 200°C
- Pressure: 50 bar and 100 bar
- Curing Time: 30 minutes and 60 minutes
5. Generate the Design: Minitab will create a worksheet with all the experimental runs
Step 3: Running the Experiment
Once the design is generated, run the experiment as per Minitab's worksheet. Carefully record the response values for each experimental combination.
Step 4: Analyzing Results in Minitab
After collecting the data, follow these steps to analyze results:
1. Go to Stat > DOE > Factorial > Analyze Factorial Design.
2. Select the response variable (e.g., product strength).
3. Click OK to generate the analysis.
Key Outputs in Minitab:
- Pareto Chart: Identifies the most significant factors.
- Main Effects Plot: Shows how each factor influences the response.
- Interaction Plot: Reveals interactions between factors.
- Regression Equation: Provides a model for predicting outcomes.
Step 5: Visualizing Results
Minitab provides graphical tools to help visualize your DOE results:
- Main Effects Plot:
Visualizes the impact of individual factors on the response variable.
- Interaction Plot:
Highlights how two or more factors interact and affect the outcome.
- Contour and Surface Plots (for Response Surface Designs):
Helps identify optimal conditions visually.
For example, the plot might show that temperature and pressure together have a big impact. But, each factor seems less influential on its own.
Step 6: Optimizing the Process
Identify the best factor level combination to optimize the response, based on the analysis. Use Minitab’s Response Optimizer tool:
1. Go to Stat > DOE > Response Optimizer.
2. Input the desired goal for your response (e.g., maximize product strength).
3. Minitab will suggest the optimal factor settings.
Example: DOE in Action
Scenario: A manufacturer wants to optimize the strength of a plastic product.
- Factors: Temperature (150°C, 200°C), Pressure (50 bar, 100 bar), and Curing Time (30 min, 60 min).
- Response: Product Strength (MPa).
Steps in Minitab:
1. Create a full factorial design with 3 factors.
2. Conduct 8 experimental runs.
3. Analyze results using the Pareto chart and interaction plots.
4. Optimize the process using Response Optimizer.
The analysis shows that 200°C, 100 bar, and 60 minutes produce the strongest product.
How to obtain Minitab certification?
We are an Education Technology company providing certification training courses to accelerate careers of working professionals worldwide. We impart training through instructor-led classroom workshops, instructor-led live virtual training sessions, and self-paced e-learning courses.
We have successfully conducted training sessions in 108 countries across the globe and enabled thousands of working professionals to enhance the scope of their careers.
Our enterprise training portfolio includes in-demand and globally recognized certification training courses in Project Management, Quality Management, Business Analysis, IT Service Management, Agile and Scrum, Cyber Security, Data Science, and Emerging Technologies. Download our Enterprise Training Catalog from https://www.icertglobal.com/corporate-training-for-enterprises.php and https://www.icertglobal.com/index.php
Popular Courses include:
-
Project Management: PMP, CAPM ,PMI RMP
-
Quality Management: Six Sigma Black Belt ,Lean Six Sigma Green Belt, Lean Management, Minitab,CMMI
-
Business Analysis: CBAP, CCBA, ECBA
-
Agile Training: PMI-ACP , CSM , CSPO
-
Scrum Training: CSM
-
DevOps
-
Program Management: PgMP
-
Cloud Technology: Exin Cloud Computing
-
Citrix Client Adminisration: Citrix Cloud Administration
The 10 top-paying certifications to target in 2024 are:
Conclusion
Design of Experiments (DOE) is a powerful tool. It helps to optimize processes and make data-driven decisions. Minitab simplifies DOE. It helps users create, analyze, and optimize designs. It has intuitive tools and visualizations.
Minitab can help businesses save time and cut costs. It can also find the key factors that drive success. Minitab's DOE tools are key for improving processes, quality, and innovation. They help you achieve measurable results.
Contact Us For More Information:
Visit :www.icertglobal.com Email : 
Read More
In today's data-driven world, experimentation is vital. It helps us understand processes, find key factors, and improve performance. Design of Experiments (DOE) is a method for tests. It is systematic and efficient. It helps in planning, conducting, and analyzing controlled tests. Minitab is a popular statistical tool. It simplifies the entire DOE process. It's now accessible to those with limited stats knowledge.
This guide will explore DOE. We'll cover its importance. We'll also show how Minitab helps users run experiments. It optimizes processes and achieves results.
What is Design of Experiments (DOE)?
Design of Experiments (DOE) is a statistical method. It finds the relationship between different factors and their impact on an outcome. DOE lets organizations test multiple variables at once. This reduces experiment time, improves efficiency, and provides insights.
For example:
A manufacturer might test temperature, pressure, and material to optimize quality.
A marketer might test ad copy, audience segments, and timing to boost conversions.
DOE identifies key factors (inputs) and their interactions that influence the outcome (response).
Why is DOE Important?
- Efficiency: DOE tests multiple variables at once, instead of one at a time (which is slow).
- Optimization: Helps identify the best combination of factors for improving performance.
- Cost Savings: Reduces resources needed for experimentation.
- Insights: Reveals interactions between factors that are otherwise difficult to identify.
DOE is widely used across industries like manufacturing, pharmaceuticals, healthcare, marketing, and engineering.
Introduction to DOE in Minitab
Minitab is a powerful tool for DOE. It simplifies the setup, execution, and analysis of experiments. With a user-friendly interface, Minitab allows users to:
1. Plan and design experiments.
2. Analyze results using statistical methods.
3. Visualize results with graphs and plots.
Minitab supports the following types of DOE:
- Factorial Designs
- Response Surface Designs
- Mixture Designs
- Taguchi Designs
Let’s dive into the steps to perform DOE in Minitab.
Step 1: Planning the Experiment
Before diving into Minitab, you must plan your experiment:
1. Define the Problem: What is the goal of the experiment?
Example: Improving product strength by testing temperature, pressure, and curing time.
2. Identify Factors: List the variables you want to study.
Example: Temperature (°C), Pressure (bar), Curing Time (minutes).
3. Determine Levels: Identify the values for each factor (e.g., high/low levels).
Example:
- Temperature: 150°C and 200°C
- Pressure: 50 bar and 100 bar
4. Choose Response Variable: What outcome will you measure?
Example: Product strength (measured in MPa).
Step 2: Creating a Factorial Design in Minitab
Factorial designs are one of the most commonly used DOE types in Minitab. Follow these steps:
1. Open Minitab and navigate to:
- Stat > DOE > Factorial > Create Factorial Design.
2. Choose the Number of Factors: Select the number of variables (e.g., 2 or 3).
- Example: 3 factors (Temperature, Pressure, Curing Time).
3. Specify Design Options:
- Full Factorial: Tests all possible combinations.
- Fractional Factorial: Tests a subset of combinations to save resources.
4. Enter Factor Names and Levels: Input your variables and their high/low levels.
- Temperature: 150°C and 200°C
- Pressure: 50 bar and 100 bar
- Curing Time: 30 minutes and 60 minutes
5. Generate the Design: Minitab will create a worksheet with all the experimental runs
Step 3: Running the Experiment
Once the design is generated, run the experiment as per Minitab's worksheet. Carefully record the response values for each experimental combination.
Step 4: Analyzing Results in Minitab
After collecting the data, follow these steps to analyze results:
1. Go to Stat > DOE > Factorial > Analyze Factorial Design.
2. Select the response variable (e.g., product strength).
3. Click OK to generate the analysis.
Key Outputs in Minitab:
- Pareto Chart: Identifies the most significant factors.
- Main Effects Plot: Shows how each factor influences the response.
- Interaction Plot: Reveals interactions between factors.
- Regression Equation: Provides a model for predicting outcomes.
Step 5: Visualizing Results
Minitab provides graphical tools to help visualize your DOE results:
- Main Effects Plot:
Visualizes the impact of individual factors on the response variable.
- Interaction Plot:
Highlights how two or more factors interact and affect the outcome.
- Contour and Surface Plots (for Response Surface Designs):
Helps identify optimal conditions visually.
For example, the plot might show that temperature and pressure together have a big impact. But, each factor seems less influential on its own.
Step 6: Optimizing the Process
Identify the best factor level combination to optimize the response, based on the analysis. Use Minitab’s Response Optimizer tool:
1. Go to Stat > DOE > Response Optimizer.
2. Input the desired goal for your response (e.g., maximize product strength).
3. Minitab will suggest the optimal factor settings.
Example: DOE in Action
Scenario: A manufacturer wants to optimize the strength of a plastic product.
- Factors: Temperature (150°C, 200°C), Pressure (50 bar, 100 bar), and Curing Time (30 min, 60 min).
- Response: Product Strength (MPa).
Steps in Minitab:
1. Create a full factorial design with 3 factors.
2. Conduct 8 experimental runs.
3. Analyze results using the Pareto chart and interaction plots.
4. Optimize the process using Response Optimizer.
The analysis shows that 200°C, 100 bar, and 60 minutes produce the strongest product.
How to obtain Minitab certification?
We are an Education Technology company providing certification training courses to accelerate careers of working professionals worldwide. We impart training through instructor-led classroom workshops, instructor-led live virtual training sessions, and self-paced e-learning courses.
We have successfully conducted training sessions in 108 countries across the globe and enabled thousands of working professionals to enhance the scope of their careers.
Our enterprise training portfolio includes in-demand and globally recognized certification training courses in Project Management, Quality Management, Business Analysis, IT Service Management, Agile and Scrum, Cyber Security, Data Science, and Emerging Technologies. Download our Enterprise Training Catalog from https://www.icertglobal.com/corporate-training-for-enterprises.php and https://www.icertglobal.com/index.php
Popular Courses include:
-
Project Management: PMP, CAPM ,PMI RMP
-
Quality Management: Six Sigma Black Belt ,Lean Six Sigma Green Belt, Lean Management, Minitab,CMMI
-
Business Analysis: CBAP, CCBA, ECBA
-
Agile Training: PMI-ACP , CSM , CSPO
-
Scrum Training: CSM
-
DevOps
-
Program Management: PgMP
-
Cloud Technology: Exin Cloud Computing
-
Citrix Client Adminisration: Citrix Cloud Administration
The 10 top-paying certifications to target in 2024 are:
Conclusion
Design of Experiments (DOE) is a powerful tool. It helps to optimize processes and make data-driven decisions. Minitab simplifies DOE. It helps users create, analyze, and optimize designs. It has intuitive tools and visualizations.
Minitab can help businesses save time and cut costs. It can also find the key factors that drive success. Minitab's DOE tools are key for improving processes, quality, and innovation. They help you achieve measurable results.
Contact Us For More Information:
Visit :www.icertglobal.com Email :
How to Become a Successful Lean Six Sigma Green Belt Trainer
Lean Six Sigma (LSS) is a method. It combines Lean manufacturing with Six Sigma. It aims to improve processes, cut waste, and boost performance. In today's fast-paced business world, firms seek a competitive edge. So, Lean Six Sigma Green Belt (LSSGB) certification is now valued across industries. This certification empowers professionals to improve processes. It also opens up opportunities to train others and share expertise.
If you're a seasoned LSSGB and want to be a Lean Six Sigma Green Belt trainer, you're in the right place. Training others in this method is a great way to grow your career. It will also help your organization or clients. Plus, you'll share knowledge. This blog will explore how to become a successful Lean Six Sigma Green Belt trainer. We'll cover the steps and skills you need.
1. Master the Lean Six Sigma Green Belt Content
Before you can teach others, you must know the Lean Six Sigma Green Belt body of knowledge. This includes:
- DMAIC Framework (Define, Measure, Analyze, Improve, Control): It is the core of Lean Six Sigma. It is a structured problem-solving approach.
Key tools are critical to the LSSGB curriculum. They are: Pareto charts, Fishbone diagrams, Control charts, SIPOC, and RCA.
- Statistical Analysis: As an LSSGB trainer, you must know basic stats. This includes regression analysis, hypothesis testing, and process capability analysis.
- Project Management: LSSGB trainers must teach trainees to manage Lean Six Sigma projects.
Soft Skills and Change Management: A Lean Six Sigma Green Belt must communicate, collaborate, and manage change. These skills are vital.
Before you step into the trainer's shoes, know these concepts. You must apply them in real-world scenarios. It will share knowledge and boost your credibility with learners.
2. Gain Practical Experience in Lean Six Sigma Projects
Teaching theory without practical experience will not resonate well with your trainees. A successful LSSGB trainer must have managed and executed Lean Six Sigma projects. Share your personal success stories, challenges, and lessons learned with your students. These examples will make your lessons more relatable and engaging.
Seeing your work on real projects will boost trainees' trust. They'll feel more confident using the tools and techniques. Also, your hands-on experience will help you answer questions better. You can provide insights that go beyond textbooks and training.
3. Develop Effective Training Materials
A successful Lean Six Sigma Green Belt trainer must know the content. They must also convey it in an engaging and clear way. Developing high-quality training materials is key to success. Here are some tips:
- Clear Presentation Slides: Use simple, visually engaging slides to present core concepts. Avoid cluttered slides with too much text. Use diagrams, charts, and case studies to simplify complex topics.
- Workbooks & Practice Exercises: Create worksheets and exercises. They should help learners apply the concepts in different scenarios. These could include process mapping exercises, statistical analysis exercises, or small project simulations.
- Real-World Examples: Include relevant, industry-specific examples for the trainees' work. Tailor your training materials to different sectors: manufacturing, healthcare, finance, or services.
- Assessment Tools: Create quizzes and surveys to test your trainees' knowledge. Feedback should be provided in a constructive manner, helping learners improve over time.
Your skills in making and using training materials can greatly affect your trainees' understanding of your concepts.
4. Create a Collaborative Learning Environment
Successful training goes beyond delivering information. It's about creating a dynamic, engaging, and collaborative learning environment. As an LSSGB trainer, foster open communication. Encourage group discussions and hands-on activities. Here are some ways to do this:
- Interactive Training: Engage your learners with interactive exercises, team activities, and simulations. Allow them to work in small groups to solve real-world problems using Lean Six Sigma tools. This fosters collaboration and encourages critical thinking.
- Active Q&A Sessions: Invite questions throughout the training and encourage discussion. Trainees may struggle to apply concepts at work. So, addressing these challenges in real-time can enhance their learning.
- Encourage Peer Learning: Organise group discussions for trainees to share their thoughts on using Lean Six Sigma at work. Peer learning is invaluable and helps learners feel more engaged.
An inclusive, collaborative atmosphere will boost the training program's effectiveness. It will ensure all participants feel supported in their learning journey.
5. Master the Art of Teaching and Presentation
Even as a Lean Six Sigma expert, your success as a trainer depends on your teaching and presentation skills. Great trainers are not only knowledgeable but also excellent communicators. Here are a few tips to hone your teaching skills:
- Engage Your Audience: Avoid monotonous lectures. Keep your training sessions engaging through storytelling, humor, case studies, and relevant examples.
- Pacing: Don’t rush through the content. Ensure you pace the training to allow for understanding and absorption. However, avoid dwelling too long on a single topic—keep things moving at a reasonable speed.
Use Visual Aids: Charts, diagrams, videos, and infographics can engage trainees and simplify ideas.
- Assess Learner Understanding: Check for understanding through discussions, quizzes, or short exercises. If learners are struggling, take time to clarify key points before moving on.
Strong teaching and presentation skills will engage your trainees. They'll retain what they learn.
6. Obtain Relevant Credentials and Certifications
Being an experienced LSSGB professional is important. But, getting more trainer credentials can improve your chances of success. Consider certifications such as:
- Certified Lean Six Sigma Master Black Belt: A higher cert can boost your credibility as a trainer.
- Train-the-Trainer Certification: This course develops skills to deliver effective training.
- Project Management Certifications: Many LSSGB trainers hold project management certifications. They guide learners through the project phases. They also teach them to manage change effectively.
These credentials can enhance your reputation as an expert. They can also improve your chances of getting training opportunities.
7. Stay Updated with Industry Trends and Best Practices
Lean Six Sigma is a constantly evolving field. New tools, techniques, and trends emerge regularly. To keep your status as a top trainer, you must stay updated on industry changes. Attend webinars, workshops, and conferences on Lean Six Sigma. Integrate new knowledge into your training materials. Knowing the latest trends will help you give your trainees relevant, up-to-date information.
How to obtain LSSGB certification?
We are an Education Technology company providing certification training courses to accelerate careers of working professionals worldwide. We impart training through instructor-led classroom workshops, instructor-led live virtual training sessions, and self-paced e-learning courses.
We have successfully conducted training sessions in 108 countries across the globe and enabled thousands of working professionals to enhance the scope of their careers.
Our enterprise training portfolio includes in-demand and globally recognized certification training courses in Project Management, Quality Management, Business Analysis, IT Service Management, Agile and Scrum, Cyber Security, Data Science, and Emerging Technologies. Download our Enterprise Training Catalog from https://www.icertglobal.com/corporate-training-for-enterprises.php and https://www.icertglobal.com/index.php
Popular Courses include:
-
Project Management: PMP, CAPM ,PMI RMP
-
Quality Management: Six Sigma Black Belt ,Lean Six Sigma Green Belt, Lean Management, Minitab,CMMI
-
Business Analysis: CBAP, CCBA, ECBA
-
Agile Training: PMI-ACP , CSM , CSPO
-
Scrum Training: CSM
-
DevOps
-
Program Management: PgMP
-
Cloud Technology: Exin Cloud Computing
-
Citrix Client Adminisration: Citrix Cloud Administration
The 10 top-paying certifications to target in 2024 are:
Conclusion
To be a successful Lean Six Sigma Green Belt trainer, you need more than just knowledge of the method. It involves mastering the content, gaining hands-on experience, and developing teaching materials. It also requires fostering collaboration, improving presentation skills, and getting relevant certifications. Finally, one must stay updated on industry trends. By focusing on these aspects, you can greatly impact your trainees' careers. You'll also advance your own career in the process.
As organizations seek to improve processes, they want skilled Lean Six Sigma trainers. There is a high demand for them. Share your expertise to help others succeed. Your success as a trainer will boost your growth and help the Lean Six Sigma community.
Contact Us For More Information:
Visit :www.icertglobal.com Email : 
Read More
Lean Six Sigma (LSS) is a method. It combines Lean manufacturing with Six Sigma. It aims to improve processes, cut waste, and boost performance. In today's fast-paced business world, firms seek a competitive edge. So, Lean Six Sigma Green Belt (LSSGB) certification is now valued across industries. This certification empowers professionals to improve processes. It also opens up opportunities to train others and share expertise.
If you're a seasoned LSSGB and want to be a Lean Six Sigma Green Belt trainer, you're in the right place. Training others in this method is a great way to grow your career. It will also help your organization or clients. Plus, you'll share knowledge. This blog will explore how to become a successful Lean Six Sigma Green Belt trainer. We'll cover the steps and skills you need.
1. Master the Lean Six Sigma Green Belt Content
Before you can teach others, you must know the Lean Six Sigma Green Belt body of knowledge. This includes:
- DMAIC Framework (Define, Measure, Analyze, Improve, Control): It is the core of Lean Six Sigma. It is a structured problem-solving approach.
Key tools are critical to the LSSGB curriculum. They are: Pareto charts, Fishbone diagrams, Control charts, SIPOC, and RCA.
- Statistical Analysis: As an LSSGB trainer, you must know basic stats. This includes regression analysis, hypothesis testing, and process capability analysis.
- Project Management: LSSGB trainers must teach trainees to manage Lean Six Sigma projects.
Soft Skills and Change Management: A Lean Six Sigma Green Belt must communicate, collaborate, and manage change. These skills are vital.
Before you step into the trainer's shoes, know these concepts. You must apply them in real-world scenarios. It will share knowledge and boost your credibility with learners.
2. Gain Practical Experience in Lean Six Sigma Projects
Teaching theory without practical experience will not resonate well with your trainees. A successful LSSGB trainer must have managed and executed Lean Six Sigma projects. Share your personal success stories, challenges, and lessons learned with your students. These examples will make your lessons more relatable and engaging.
Seeing your work on real projects will boost trainees' trust. They'll feel more confident using the tools and techniques. Also, your hands-on experience will help you answer questions better. You can provide insights that go beyond textbooks and training.
3. Develop Effective Training Materials
A successful Lean Six Sigma Green Belt trainer must know the content. They must also convey it in an engaging and clear way. Developing high-quality training materials is key to success. Here are some tips:
- Clear Presentation Slides: Use simple, visually engaging slides to present core concepts. Avoid cluttered slides with too much text. Use diagrams, charts, and case studies to simplify complex topics.
- Workbooks & Practice Exercises: Create worksheets and exercises. They should help learners apply the concepts in different scenarios. These could include process mapping exercises, statistical analysis exercises, or small project simulations.
- Real-World Examples: Include relevant, industry-specific examples for the trainees' work. Tailor your training materials to different sectors: manufacturing, healthcare, finance, or services.
- Assessment Tools: Create quizzes and surveys to test your trainees' knowledge. Feedback should be provided in a constructive manner, helping learners improve over time.
Your skills in making and using training materials can greatly affect your trainees' understanding of your concepts.
4. Create a Collaborative Learning Environment
Successful training goes beyond delivering information. It's about creating a dynamic, engaging, and collaborative learning environment. As an LSSGB trainer, foster open communication. Encourage group discussions and hands-on activities. Here are some ways to do this:
- Interactive Training: Engage your learners with interactive exercises, team activities, and simulations. Allow them to work in small groups to solve real-world problems using Lean Six Sigma tools. This fosters collaboration and encourages critical thinking.
- Active Q&A Sessions: Invite questions throughout the training and encourage discussion. Trainees may struggle to apply concepts at work. So, addressing these challenges in real-time can enhance their learning.
- Encourage Peer Learning: Organise group discussions for trainees to share their thoughts on using Lean Six Sigma at work. Peer learning is invaluable and helps learners feel more engaged.
An inclusive, collaborative atmosphere will boost the training program's effectiveness. It will ensure all participants feel supported in their learning journey.
5. Master the Art of Teaching and Presentation
Even as a Lean Six Sigma expert, your success as a trainer depends on your teaching and presentation skills. Great trainers are not only knowledgeable but also excellent communicators. Here are a few tips to hone your teaching skills:
- Engage Your Audience: Avoid monotonous lectures. Keep your training sessions engaging through storytelling, humor, case studies, and relevant examples.
- Pacing: Don’t rush through the content. Ensure you pace the training to allow for understanding and absorption. However, avoid dwelling too long on a single topic—keep things moving at a reasonable speed.
Use Visual Aids: Charts, diagrams, videos, and infographics can engage trainees and simplify ideas.
- Assess Learner Understanding: Check for understanding through discussions, quizzes, or short exercises. If learners are struggling, take time to clarify key points before moving on.
Strong teaching and presentation skills will engage your trainees. They'll retain what they learn.
6. Obtain Relevant Credentials and Certifications
Being an experienced LSSGB professional is important. But, getting more trainer credentials can improve your chances of success. Consider certifications such as:
- Certified Lean Six Sigma Master Black Belt: A higher cert can boost your credibility as a trainer.
- Train-the-Trainer Certification: This course develops skills to deliver effective training.
- Project Management Certifications: Many LSSGB trainers hold project management certifications. They guide learners through the project phases. They also teach them to manage change effectively.
These credentials can enhance your reputation as an expert. They can also improve your chances of getting training opportunities.
7. Stay Updated with Industry Trends and Best Practices
Lean Six Sigma is a constantly evolving field. New tools, techniques, and trends emerge regularly. To keep your status as a top trainer, you must stay updated on industry changes. Attend webinars, workshops, and conferences on Lean Six Sigma. Integrate new knowledge into your training materials. Knowing the latest trends will help you give your trainees relevant, up-to-date information.
How to obtain LSSGB certification?
We are an Education Technology company providing certification training courses to accelerate careers of working professionals worldwide. We impart training through instructor-led classroom workshops, instructor-led live virtual training sessions, and self-paced e-learning courses.
We have successfully conducted training sessions in 108 countries across the globe and enabled thousands of working professionals to enhance the scope of their careers.
Our enterprise training portfolio includes in-demand and globally recognized certification training courses in Project Management, Quality Management, Business Analysis, IT Service Management, Agile and Scrum, Cyber Security, Data Science, and Emerging Technologies. Download our Enterprise Training Catalog from https://www.icertglobal.com/corporate-training-for-enterprises.php and https://www.icertglobal.com/index.php
Popular Courses include:
-
Project Management: PMP, CAPM ,PMI RMP
-
Quality Management: Six Sigma Black Belt ,Lean Six Sigma Green Belt, Lean Management, Minitab,CMMI
-
Business Analysis: CBAP, CCBA, ECBA
-
Agile Training: PMI-ACP , CSM , CSPO
-
Scrum Training: CSM
-
DevOps
-
Program Management: PgMP
-
Cloud Technology: Exin Cloud Computing
-
Citrix Client Adminisration: Citrix Cloud Administration
The 10 top-paying certifications to target in 2024 are:
Conclusion
To be a successful Lean Six Sigma Green Belt trainer, you need more than just knowledge of the method. It involves mastering the content, gaining hands-on experience, and developing teaching materials. It also requires fostering collaboration, improving presentation skills, and getting relevant certifications. Finally, one must stay updated on industry trends. By focusing on these aspects, you can greatly impact your trainees' careers. You'll also advance your own career in the process.
As organizations seek to improve processes, they want skilled Lean Six Sigma trainers. There is a high demand for them. Share your expertise to help others succeed. Your success as a trainer will boost your growth and help the Lean Six Sigma community.
Contact Us For More Information:
Visit :www.icertglobal.com Email :
The Lean Management in the Era of Hyper-Personalization!
In today's tough business world, hyper-personalization is key to engaging and retaining customers. Consumers expect products and services to meet their unique needs. While this demand drives innovation, it also increases operational complexity. Enter Lean Management, a methodology rooted in eliminating waste and enhancing efficiency. By merging Lean principles with hyper-personalization, firms can deliver custom experiences. They can do this without losing productivity or profits.
This blog explores how Lean Management adapts to hyper-personalization. It offers insights for businesses looking to thrive in this dynamic environment.
What is Hyper-Personalization?
Hyper-personalization goes beyond basic customization. It uses advanced tech, like AI, big data, and machine learning, to analyse vast amounts of customer data. This enables businesses to provide highly targeted and relevant products, services, and messages.
E-commerce sites like Amazon recommend products based on browsing and purchase history. Streaming services like Netflix suggest shows based on viewing preferences. Hyper-personalization boosts customer satisfaction. But, it strains operations. So, efficiency is key to success.
The Synergy Between Lean Management and Hyper-Personalization
Lean Management aims to create value for customers. It does this by reducing waste and improving processes. At first, Lean's call for simplicity may clash with hyper-personalization's complexity. However, the two can complement each other effectively:
1. Value Stream Mapping for Personalized Journeys
Lean Management uses value stream mapping to visualize and optimize workflows. Businesses can apply this technique to personalized customer journeys. It will ensure each touchpoint adds value and removes any slow, unnecessary steps.
2. Just-in-Time (JIT) for Customization
The JIT principle ensures products or services are delivered as needed. This reduces inventory costs and waste. In hyper-personalization, JIT can adjust offerings using real-time customer insights.
3. Focus on Customer Value
Hyper-personalization aligns perfectly with Lean’s emphasis on value creation. Data can help businesses understand customer needs. They can then focus their Lean initiatives on what matters most.
Challenges of Hyper-Personalization in Lean Environments
Lean Management and hyper-personalization combine for great benefits. But, they also pose unique challenges:
1. Managing Data Overload
Hyper-personalization relies on vast amounts of data. Processing this information efficiently without creating bottlenecks can be overwhelming.
2. Increased Complexity in Operations
Customizing products or services for individual customers may harm Lean processes. It can cause fragmented workflows and reduce standardization.
3. Balancing Speed with Accuracy
Hyper-personalized interactions demand speed. But, Lean's focus on minimizing errors requires careful calibration to avoid compromising quality.
4. Resource Allocation
Hyper-personalization may strain resources. It could conflict with Lean's goal of efficiency.
Lean Strategies for Hyper-Personalization Success
To overcome these challenges, businesses can adopt Lean strategies. These should meet the demands of hyper-personalization.
1. Embrace Technology for Lean Efficiency
Invest in automation tools and AI-driven systems to streamline data analysis and decision-making. For example, predictive analytics can help anticipate customer preferences. This enables Lean operations to adjust dynamically.
2. Modular Design for Scalability
Adopt modular product or service designs to simplify customization. This lets businesses meet diverse needs without reengineering the whole process. It keeps Lean's efficiency.
3. Agile and Lean Integration
Combine Lean principles with Agile methodologies to handle the fast-paced nature of hyper-personalization. Agile frameworks allow for iterative adjustments, keeping processes aligned with customer demands.
4. Focus on Continuous Improvement (Kaizen)
Implement Kaizen to continuously refine hyper-personalization processes. Regular feedback loops can identify and eliminate inefficiencies in delivering personalized experiences.
5. Cross-Functional Collaboration
Encourage collaboration across departments to ensure that hyper-personalization initiatives align with Lean goals. For example, marketing, operations, and IT teams should work together to streamline workflows.
Real-World Examples of Lean and Hyper-Personalization
Several industry leaders have successfully integrated Lean Management with hyper-personalization:
1. Nike By You
Nike’s customization platform, “Nike By You,” allows customers to design their own shoes. Nike uses Lean principles to streamline manufacturing and cut waste. This ensures efficient delivery of personalized orders.
2. Starbucks’ Personalized Recommendations
Starbucks uses data analytics to offer personalized drink recommendations via its mobile app. By using Lean practices, the company ensures quick, customised orders. This reduces wait times and boosts customer satisfaction.
3. Toyota’s Lean Innovation in Customization
Toyota, a pioneer in Lean Management, uses advanced methods. They offer personalised vehicle options without disrupting production efficiency.
The Future of Lean Management in Hyper-Personalized Markets
As hyper-personalization continues to evolve, so too will the role of Lean Management. Future developments may include:
- AI-Powered Lean Tools: Advanced AI will improve value stream mapping and predictive modeling. This will create hyper-personalized workflows.
- Dynamic Lean Metrics: Businesses will create new KPIs. They will measure Lean efficiency and account for the complexities of hyper-personalization.
- Sustainable Hyper-Personalization: Lean principles will reduce the environmental impact of hyper-personalized operations. They align with sustainability goals.
How to obtain Lean Management certification?
We are an Education Technology company providing certification training courses to accelerate careers of working professionals worldwide. We impart training through instructor-led classroom workshops, instructor-led live virtual training sessions, and self-paced e-learning courses.
We have successfully conducted training sessions in 108 countries across the globe and enabled thousands of working professionals to enhance the scope of their careers.
Our enterprise training portfolio includes in-demand and globally recognized certification training courses in Project Management, Quality Management, Business Analysis, IT Service Management, Agile and Scrum, Cyber Security, Data Science, and Emerging Technologies. Download our Enterprise Training Catalog from https://www.icertglobal.com/corporate-training-for-enterprises.php and https://www.icertglobal.com/index.php
Popular Courses include:
-
Project Management: PMP, CAPM ,PMI RMP
-
Quality Management: Six Sigma Black Belt ,Lean Six Sigma Green Belt, Lean Management, Minitab,CMMI
-
Business Analysis: CBAP, CCBA, ECBA
-
Agile Training: PMI-ACP , CSM , CSPO
-
Scrum Training: CSM
-
DevOps
-
Program Management: PgMP
-
Cloud Technology: Exin Cloud Computing
-
Citrix Client Adminisration: Citrix Cloud Administration
The 10 top-paying certifications to target in 2024 are:
Conclusion
Hyper-personalization is reshaping customer expectations. It's now vital to modern business strategies. Lean Management helps organizations deliver custom experiences while staying efficient.
Lean principles and hyper-personalization can work together. This can lead to both operational excellence and high customer satisfaction. With the right tools and mindset, businesses can thrive today. They can outpace competitors by innovating and personalizing their services. This will deliver unmatched value to customers.
Contact Us For More Information:
Visit :www.icertglobal.com Email : 
Read More
In today's tough business world, hyper-personalization is key to engaging and retaining customers. Consumers expect products and services to meet their unique needs. While this demand drives innovation, it also increases operational complexity. Enter Lean Management, a methodology rooted in eliminating waste and enhancing efficiency. By merging Lean principles with hyper-personalization, firms can deliver custom experiences. They can do this without losing productivity or profits.
This blog explores how Lean Management adapts to hyper-personalization. It offers insights for businesses looking to thrive in this dynamic environment.
What is Hyper-Personalization?
Hyper-personalization goes beyond basic customization. It uses advanced tech, like AI, big data, and machine learning, to analyse vast amounts of customer data. This enables businesses to provide highly targeted and relevant products, services, and messages.
E-commerce sites like Amazon recommend products based on browsing and purchase history. Streaming services like Netflix suggest shows based on viewing preferences. Hyper-personalization boosts customer satisfaction. But, it strains operations. So, efficiency is key to success.
The Synergy Between Lean Management and Hyper-Personalization
Lean Management aims to create value for customers. It does this by reducing waste and improving processes. At first, Lean's call for simplicity may clash with hyper-personalization's complexity. However, the two can complement each other effectively:
1. Value Stream Mapping for Personalized Journeys
Lean Management uses value stream mapping to visualize and optimize workflows. Businesses can apply this technique to personalized customer journeys. It will ensure each touchpoint adds value and removes any slow, unnecessary steps.
2. Just-in-Time (JIT) for Customization
The JIT principle ensures products or services are delivered as needed. This reduces inventory costs and waste. In hyper-personalization, JIT can adjust offerings using real-time customer insights.
3. Focus on Customer Value
Hyper-personalization aligns perfectly with Lean’s emphasis on value creation. Data can help businesses understand customer needs. They can then focus their Lean initiatives on what matters most.
Challenges of Hyper-Personalization in Lean Environments
Lean Management and hyper-personalization combine for great benefits. But, they also pose unique challenges:
1. Managing Data Overload
Hyper-personalization relies on vast amounts of data. Processing this information efficiently without creating bottlenecks can be overwhelming.
2. Increased Complexity in Operations
Customizing products or services for individual customers may harm Lean processes. It can cause fragmented workflows and reduce standardization.
3. Balancing Speed with Accuracy
Hyper-personalized interactions demand speed. But, Lean's focus on minimizing errors requires careful calibration to avoid compromising quality.
4. Resource Allocation
Hyper-personalization may strain resources. It could conflict with Lean's goal of efficiency.
Lean Strategies for Hyper-Personalization Success
To overcome these challenges, businesses can adopt Lean strategies. These should meet the demands of hyper-personalization.
1. Embrace Technology for Lean Efficiency
Invest in automation tools and AI-driven systems to streamline data analysis and decision-making. For example, predictive analytics can help anticipate customer preferences. This enables Lean operations to adjust dynamically.
2. Modular Design for Scalability
Adopt modular product or service designs to simplify customization. This lets businesses meet diverse needs without reengineering the whole process. It keeps Lean's efficiency.
3. Agile and Lean Integration
Combine Lean principles with Agile methodologies to handle the fast-paced nature of hyper-personalization. Agile frameworks allow for iterative adjustments, keeping processes aligned with customer demands.
4. Focus on Continuous Improvement (Kaizen)
Implement Kaizen to continuously refine hyper-personalization processes. Regular feedback loops can identify and eliminate inefficiencies in delivering personalized experiences.
5. Cross-Functional Collaboration
Encourage collaboration across departments to ensure that hyper-personalization initiatives align with Lean goals. For example, marketing, operations, and IT teams should work together to streamline workflows.
Real-World Examples of Lean and Hyper-Personalization
Several industry leaders have successfully integrated Lean Management with hyper-personalization:
1. Nike By You
Nike’s customization platform, “Nike By You,” allows customers to design their own shoes. Nike uses Lean principles to streamline manufacturing and cut waste. This ensures efficient delivery of personalized orders.
2. Starbucks’ Personalized Recommendations
Starbucks uses data analytics to offer personalized drink recommendations via its mobile app. By using Lean practices, the company ensures quick, customised orders. This reduces wait times and boosts customer satisfaction.
3. Toyota’s Lean Innovation in Customization
Toyota, a pioneer in Lean Management, uses advanced methods. They offer personalised vehicle options without disrupting production efficiency.
The Future of Lean Management in Hyper-Personalized Markets
As hyper-personalization continues to evolve, so too will the role of Lean Management. Future developments may include:
- AI-Powered Lean Tools: Advanced AI will improve value stream mapping and predictive modeling. This will create hyper-personalized workflows.
- Dynamic Lean Metrics: Businesses will create new KPIs. They will measure Lean efficiency and account for the complexities of hyper-personalization.
- Sustainable Hyper-Personalization: Lean principles will reduce the environmental impact of hyper-personalized operations. They align with sustainability goals.
How to obtain Lean Management certification?
We are an Education Technology company providing certification training courses to accelerate careers of working professionals worldwide. We impart training through instructor-led classroom workshops, instructor-led live virtual training sessions, and self-paced e-learning courses.
We have successfully conducted training sessions in 108 countries across the globe and enabled thousands of working professionals to enhance the scope of their careers.
Our enterprise training portfolio includes in-demand and globally recognized certification training courses in Project Management, Quality Management, Business Analysis, IT Service Management, Agile and Scrum, Cyber Security, Data Science, and Emerging Technologies. Download our Enterprise Training Catalog from https://www.icertglobal.com/corporate-training-for-enterprises.php and https://www.icertglobal.com/index.php
Popular Courses include:
-
Project Management: PMP, CAPM ,PMI RMP
-
Quality Management: Six Sigma Black Belt ,Lean Six Sigma Green Belt, Lean Management, Minitab,CMMI
-
Business Analysis: CBAP, CCBA, ECBA
-
Agile Training: PMI-ACP , CSM , CSPO
-
Scrum Training: CSM
-
DevOps
-
Program Management: PgMP
-
Cloud Technology: Exin Cloud Computing
-
Citrix Client Adminisration: Citrix Cloud Administration
The 10 top-paying certifications to target in 2024 are:
Conclusion
Hyper-personalization is reshaping customer expectations. It's now vital to modern business strategies. Lean Management helps organizations deliver custom experiences while staying efficient.
Lean principles and hyper-personalization can work together. This can lead to both operational excellence and high customer satisfaction. With the right tools and mindset, businesses can thrive today. They can outpace competitors by innovating and personalizing their services. This will deliver unmatched value to customers.
Contact Us For More Information:
Visit :www.icertglobal.com Email :
Challenges in Six Sigma Projects and Black Belt Solutions
Six Sigma is a method to improve business processes. It does this by reducing errors and increasing efficiency. However, implementing Six Sigma projects is no easy feat. Even the most experienced Six Sigma Black Belts (SSBBs) face challenges. They test their problem-solving and leadership skills. This blog looks at common challenges in Six Sigma projects. It also covers the solutions Black Belts use to address them.
1. Resistance to Change
Challenge:
A common hurdle in Six Sigma projects is resistance from employees and stakeholders. Change often disrupts established workflows, creating uncertainty and apprehension among team members.
Black Belt Solution:
Black Belts tackle resistance by fostering a culture of communication and collaboration. They:
- Organize workshops and training sessions to explain the benefits of Six Sigma.
- Actively involve team members in the decision-making process to gain their buy-in.
- Use storytelling to share success stories from past projects. Show how Six Sigma can bring real benefits.
By addressing concerns and keeping communication open, Black Belts build trust. This reduces resistance.
2. Lack of Management Support
Challenge:
Without strong support from leadership, Six Sigma projects often face roadblocks. These include issues with resources, time, and prioritization.
Black Belt Solution:
To gain management support, Black Belts:
- Present proposals that use data. They must show the impact of Six Sigma projects on finances and operations.
- Align project goals with organizational objectives to showcase their strategic importance.
- Schedule regular updates with leadership to inform them of progress and challenges.
Effective stakeholder management ensures leadership remains engaged and committed to the project.
3. Data Quality and Accessibility
Challenge:
Six Sigma projects rely on data for root cause analysis and performance measurement. Poor data quality or limited access to data can compromise the success of a project.
Black Belt Solution:
Black Belts address this issue by:
- Establishing clear data collection protocols at the start of the project.
- Collaborating with IT teams to ensure data systems are integrated and accessible.
- Validating data before using it for analysis to eliminate inaccuracies.
They use tools like data visualization and stats software to make data actionable, when needed.
4. Inadequate Training and Awareness
Challenge:
Employees unfamiliar with Six Sigma methodologies may struggle to contribute effectively to projects. This knowledge gap can slow down progress and lead to miscommunication.
Black Belt Solution:
Black Belts ensure team readiness by:
- Conducting tailored training for all stakeholders, from top execs to frontline staff.
- Providing quick-reference guides, templates, and examples to simplify complex concepts.
- Offering continuous coaching and mentoring to reinforce learning throughout the project lifecycle.
This hands-on approach gives teams the skills to participate effectively.
5. Scope Creep
Challenge:
Scope creep happens when unplanned activities or goals are added to a project. This dilutes its focus and wastes resources.
Black Belt Solution:
To prevent scope creep, Black Belts:
- Define project scope, objectives, and deliverables clearly at the outset.
Use a framework like DMAIC (Define, Measure, Analyze, Improve, Control) to stay focused.
- Regularly review project progress against the scope and address deviations promptly.
Documenting change requests and getting approval keeps the project on track with its original goals.
6. Team Dynamics and Conflict
Challenge:
Diverse teams bring different views. But, they can cause conflicts and misaligned goals.
Black Belt Solution:
Black Belts excel in managing team dynamics by:
- Setting clear roles and responsibilities for each team member.
- Using facilitation techniques to ensure every voice is heard during discussions.
- Mediating conflicts impartially and focusing on data-driven resolutions rather than subjective opinions.
Strong interpersonal relationships within the team help maintain a happy, productive environment.
7. Unrealistic Expectations
Challenge:
Stakeholders often expect quick results from Six Sigma projects, with little investment. This can cause dissatisfaction if those expectations aren't met.
Black Belt Solution:
To manage expectations, Black Belts:
- Set realistic timelines and milestones during the project planning phase.
- Educate stakeholders about the complexity and time required for sustainable improvements.
Use pilot tests or quick wins to show early value. This will build confidence in the project's potential.
Transparent communication about the project scope is key. It manages stakeholder expectations.
8. Sustaining Improvements
Challenge:
Once improvements are made, it can be hard to sustain them. The organization may revert to old habits or fail to monitor the process.
Black Belt Solution:
To ensure long-term success, Black Belts:
- Create control plans. They should outline how to monitor and maintain the improved process.
- Train process owners to take responsibility for ongoing performance.
- Incorporate performance metrics into regular reviews to detect and address deviations early.
By embedding improvements into the organizational culture, Black Belts help ensure lasting results.
9. Resource Constraints
Challenge:
Time, staff, or budget issues can delay or derail Six Sigma projects.
Black Belt Solution:
To navigate resource constraints, Black Belts:
- Prioritize projects based on their potential ROI and organizational impact.
- Use Lean principles to eliminate waste and maximize resource efficiency.
- Break larger projects into smaller, manageable phases to fit within available resources.
This strategic approach helps maintain momentum even under tight constraints.
How to obtain SSBB certification?
We are an Education Technology company providing certification training courses to accelerate careers of working professionals worldwide. We impart training through instructor-led classroom workshops, instructor-led live virtual training sessions, and self-paced e-learning courses.
We have successfully conducted training sessions in 108 countries across the globe and enabled thousands of working professionals to enhance the scope of their careers.
Our enterprise training portfolio includes in-demand and globally recognized certification training courses in Project Management, Quality Management, Business Analysis, IT Service Management, Agile and Scrum, Cyber Security, Data Science, and Emerging Technologies. Download our Enterprise Training Catalog from https://www.icertglobal.com/corporate-training-for-enterprises.php and https://www.icertglobal.com/index.php
Popular Courses include:
-
Project Management: PMP, CAPM ,PMI RMP
-
Quality Management: Six Sigma Black Belt ,Lean Six Sigma Green Belt, Lean Management, Minitab,CMMI
-
Business Analysis: CBAP, CCBA, ECBA
-
Agile Training: PMI-ACP , CSM , CSPO
-
Scrum Training: CSM
-
DevOps
-
Program Management: PgMP
-
Cloud Technology: Exin Cloud Computing
-
Citrix Client Adminisration: Citrix Cloud Administration
The 10 top-paying certifications to target in 2024 are:
Conclusion
Six Sigma projects are transformative but challenging endeavors. Black Belts are vital in tackling these challenges. They do this with their expertise, strategic thinking, and leadership skills. Their solutions ensure that Six Sigma projects have a lasting impact. They do this by overcoming resistance to change. They manage team dynamics and sustain improvements.
Contact Us For More Information:
Visit :www.icertglobal.com Email : 
Read More
Six Sigma is a method to improve business processes. It does this by reducing errors and increasing efficiency. However, implementing Six Sigma projects is no easy feat. Even the most experienced Six Sigma Black Belts (SSBBs) face challenges. They test their problem-solving and leadership skills. This blog looks at common challenges in Six Sigma projects. It also covers the solutions Black Belts use to address them.
1. Resistance to Change
Challenge:
A common hurdle in Six Sigma projects is resistance from employees and stakeholders. Change often disrupts established workflows, creating uncertainty and apprehension among team members.
Black Belt Solution:
Black Belts tackle resistance by fostering a culture of communication and collaboration. They:
- Organize workshops and training sessions to explain the benefits of Six Sigma.
- Actively involve team members in the decision-making process to gain their buy-in.
- Use storytelling to share success stories from past projects. Show how Six Sigma can bring real benefits.
By addressing concerns and keeping communication open, Black Belts build trust. This reduces resistance.
2. Lack of Management Support
Challenge:
Without strong support from leadership, Six Sigma projects often face roadblocks. These include issues with resources, time, and prioritization.
Black Belt Solution:
To gain management support, Black Belts:
- Present proposals that use data. They must show the impact of Six Sigma projects on finances and operations.
- Align project goals with organizational objectives to showcase their strategic importance.
- Schedule regular updates with leadership to inform them of progress and challenges.
Effective stakeholder management ensures leadership remains engaged and committed to the project.
3. Data Quality and Accessibility
Challenge:
Six Sigma projects rely on data for root cause analysis and performance measurement. Poor data quality or limited access to data can compromise the success of a project.
Black Belt Solution:
Black Belts address this issue by:
- Establishing clear data collection protocols at the start of the project.
- Collaborating with IT teams to ensure data systems are integrated and accessible.
- Validating data before using it for analysis to eliminate inaccuracies.
They use tools like data visualization and stats software to make data actionable, when needed.
4. Inadequate Training and Awareness
Challenge:
Employees unfamiliar with Six Sigma methodologies may struggle to contribute effectively to projects. This knowledge gap can slow down progress and lead to miscommunication.
Black Belt Solution:
Black Belts ensure team readiness by:
- Conducting tailored training for all stakeholders, from top execs to frontline staff.
- Providing quick-reference guides, templates, and examples to simplify complex concepts.
- Offering continuous coaching and mentoring to reinforce learning throughout the project lifecycle.
This hands-on approach gives teams the skills to participate effectively.
5. Scope Creep
Challenge:
Scope creep happens when unplanned activities or goals are added to a project. This dilutes its focus and wastes resources.
Black Belt Solution:
To prevent scope creep, Black Belts:
- Define project scope, objectives, and deliverables clearly at the outset.
Use a framework like DMAIC (Define, Measure, Analyze, Improve, Control) to stay focused.
- Regularly review project progress against the scope and address deviations promptly.
Documenting change requests and getting approval keeps the project on track with its original goals.
6. Team Dynamics and Conflict
Challenge:
Diverse teams bring different views. But, they can cause conflicts and misaligned goals.
Black Belt Solution:
Black Belts excel in managing team dynamics by:
- Setting clear roles and responsibilities for each team member.
- Using facilitation techniques to ensure every voice is heard during discussions.
- Mediating conflicts impartially and focusing on data-driven resolutions rather than subjective opinions.
Strong interpersonal relationships within the team help maintain a happy, productive environment.
7. Unrealistic Expectations
Challenge:
Stakeholders often expect quick results from Six Sigma projects, with little investment. This can cause dissatisfaction if those expectations aren't met.
Black Belt Solution:
To manage expectations, Black Belts:
- Set realistic timelines and milestones during the project planning phase.
- Educate stakeholders about the complexity and time required for sustainable improvements.
Use pilot tests or quick wins to show early value. This will build confidence in the project's potential.
Transparent communication about the project scope is key. It manages stakeholder expectations.
8. Sustaining Improvements
Challenge:
Once improvements are made, it can be hard to sustain them. The organization may revert to old habits or fail to monitor the process.
Black Belt Solution:
To ensure long-term success, Black Belts:
- Create control plans. They should outline how to monitor and maintain the improved process.
- Train process owners to take responsibility for ongoing performance.
- Incorporate performance metrics into regular reviews to detect and address deviations early.
By embedding improvements into the organizational culture, Black Belts help ensure lasting results.
9. Resource Constraints
Challenge:
Time, staff, or budget issues can delay or derail Six Sigma projects.
Black Belt Solution:
To navigate resource constraints, Black Belts:
- Prioritize projects based on their potential ROI and organizational impact.
- Use Lean principles to eliminate waste and maximize resource efficiency.
- Break larger projects into smaller, manageable phases to fit within available resources.
This strategic approach helps maintain momentum even under tight constraints.
How to obtain SSBB certification?
We are an Education Technology company providing certification training courses to accelerate careers of working professionals worldwide. We impart training through instructor-led classroom workshops, instructor-led live virtual training sessions, and self-paced e-learning courses.
We have successfully conducted training sessions in 108 countries across the globe and enabled thousands of working professionals to enhance the scope of their careers.
Our enterprise training portfolio includes in-demand and globally recognized certification training courses in Project Management, Quality Management, Business Analysis, IT Service Management, Agile and Scrum, Cyber Security, Data Science, and Emerging Technologies. Download our Enterprise Training Catalog from https://www.icertglobal.com/corporate-training-for-enterprises.php and https://www.icertglobal.com/index.php
Popular Courses include:
-
Project Management: PMP, CAPM ,PMI RMP
-
Quality Management: Six Sigma Black Belt ,Lean Six Sigma Green Belt, Lean Management, Minitab,CMMI
-
Business Analysis: CBAP, CCBA, ECBA
-
Agile Training: PMI-ACP , CSM , CSPO
-
Scrum Training: CSM
-
DevOps
-
Program Management: PgMP
-
Cloud Technology: Exin Cloud Computing
-
Citrix Client Adminisration: Citrix Cloud Administration
The 10 top-paying certifications to target in 2024 are:
Conclusion
Six Sigma projects are transformative but challenging endeavors. Black Belts are vital in tackling these challenges. They do this with their expertise, strategic thinking, and leadership skills. Their solutions ensure that Six Sigma projects have a lasting impact. They do this by overcoming resistance to change. They manage team dynamics and sustain improvements.
Contact Us For More Information:
Visit :www.icertglobal.com Email :
Enhancing Supply Chain Management with CMMI Implementation
In today's fast-changing business world, strong supply chains are vital. They are key to staying competitive. The Capability Maturity Model Integration (CMMI) is for software development and process improvement. It is now a key framework for improving supply chain management (SCM). CMMI's structured approach gives organizations tools and methods. They can then streamline operations, improve collaboration, reduce risks, and boost performance.
This blog explores CMMI's key role in improving supply chain management. It covers its benefits and strategies for successful implementation.
Understanding CMMI in the Context of Supply Chain Management
CMMI is a framework for improving processes. It aims to boost organizational capabilities in various fields. CMMI, developed by the Software Engineering Institute (SEI), has evolved. It now addresses challenges in many fields, including supply chain management.
Supply chains involve multiple, interconnected entities. These include suppliers, manufacturers, distributors, and customers. Each contributes to the flow of goods and services. Effective relationship management requires robust processes and a focus on quality. It needs continuous improvement, too. These principles align with the CMMI framework.
Key Challenges in Supply Chain Management
Before delving into CMMI’s impact, it’s essential to recognize the common challenges in SCM:
1. Modern supply chains often span multiple geographies and industries. This causes fragmented processes and inefficiencies.
2. Risk Management: Natural disasters, geopolitical issues, or supplier failures can disrupt the supply chain.
3. Lack of Standardization: Inconsistent processes and communication gaps between stakeholders hinder operational efficiency.
4. Quality Control: Ensuring uniform quality across all levels of the supply chain can be challenging.
5. Data Management: Many organizations struggle to use accurate, real-time data for decision-making.
CMMI offers a way to meet these challenges. It promotes process standardization, risk mitigation, and capability development.
How CMMI Enhances Supply Chain Management
1. Process Standardization
CMMI emphasizes the need for standardized processes across the organization. In supply chain management, it means creating standard procedures for procurement, logistics, inventory, and quality.
A global electronics manufacturer can use CMMI. It can standardize its supplier evaluation criteria. This will ensure consistent quality and performance across its vendors.
2. Risk Management and Resilience
Risk management is a core aspect of CMMI. The framework helps organizations to find risks, assess their impact, and develop strategies to reduce them.
- Application in SCM: Companies can use CMMI to plan for supplier disruptions. This includes diversifying their suppliers or keeping buffer inventories.
3. Enhanced Collaboration and Communication
Supply chains rely on seamless communication between stakeholders. CMMI encourages organizations to establish clear communication protocols and foster collaboration across teams.
A retail giant might use CMMI. It could improve communication between its warehouses and distributors. This would reduce delivery delays and boost customer satisfaction.
4. Continuous Improvement
CMMI advocates a culture of continuous improvement. It should be done through regular process evaluations and feedback.
- Impact on SCM: By tracking KPIs like delivery times, inventory, and order accuracy, firms can find inefficiencies and fix them.
5. Quality Assurance
Quality in the supply chain is vital for customer satisfaction and brand reputation. CMMI helps organizations set strong quality assurance processes. These cover supplier audits to final product inspections.
Automotive companies can use CMMI to enforce strict quality checks at every stage of the supply chain. This will minimize defects and recalls.
6. Leveraging Technology for SCM Optimization
CMMI works well with advanced tech like AI, ML, and blockchain. It optimizes supply chains.
AI-driven analytics let organizations predict demand changes. They can then adjust their supply chains.
Benefits of CMMI in Supply Chain Management
1. Improved Efficiency: Better coordination and streamlined processes cut costs and sped up delivery.
2. Higher Customer Satisfaction: Better quality control delivers defect-free products, boosting brand loyalty.
3. Reduced Risk: Proactive risk management minimizes the impact of disruptions, ensuring business continuity.
4. Better Decision-Making: Standard data collection helps make informed decisions across the supply chain.
5. Increased Flexibility: Organizations can quickly adapt to market changes and customer demands. This gives them a competitive edge.
Steps to Implement CMMI in Supply Chain Management
1. Conduct a Gap Analysis
Assess your supply chain processes against CMMI's maturity levels. This will identify areas for improvement.
2. Set Clear Objectives
Define your goals for CMMI implementation. Examples include: reducing lead times or improving supplier collaboration.
3. Develop a Roadmap
Make a detailed plan. It should outline the steps, resources, and timelines needed to achieve your goals.
4. Train and Engage Employees
Train your workforce on CMMI principles and their relevance to supply chain management.
5. Monitor and Evaluate Progress
Regularly track your progress against predefined KPIs and refine your strategies as needed.
6. Obtain Certification
Consider a formal CMMI appraisal. It will validate your processes and commitment to excellence.
Case Study: CMMI in Action
Company: A global pharmaceutical firm
Challenge: The firm had frequent supply chain issues. These caused delays in product deliveries and upset customers.
Solution: By adopting CMMI, the organization standardized its supplier evaluations. It also implemented a strong risk management framework. Finally, it improved communication across its supply chain.
Delivery times improved by 25%. Customer satisfaction scores increased significantly within a year.
The Future of CMMI in Supply Chain Management
As supply chains grow more complex, CMMI's importance will rise. Emerging tech, like IoT, blockchain, and AI, will boost CMMI. They will enable real-time monitoring, predictive analytics, and process automation. Using these technologies with CMMI will help organizations face future challenges. They will also be more competitive.
How to obtain CMMI certification?
We are an Education Technology company providing certification training courses to accelerate careers of working professionals worldwide. We impart training through instructor-led classroom workshops, instructor-led live virtual training sessions, and self-paced e-learning courses.
We have successfully conducted training sessions in 108 countries across the globe and enabled thousands of working professionals to enhance the scope of their careers.
Our enterprise training portfolio includes in-demand and globally recognized certification training courses in Project Management, Quality Management, Business Analysis, IT Service Management, Agile and Scrum, Cyber Security, Data Science, and Emerging Technologies. Download our Enterprise Training Catalog from https://www.icertglobal.com/corporate-training-for-enterprises.php and https://www.icertglobal.com/index.php
Popular Courses include:
-
Project Management: PMP, CAPM ,PMI RMP
-
Quality Management: Six Sigma Black Belt ,Lean Six Sigma Green Belt, Lean Management, Minitab,CMMI
-
Business Analysis: CBAP, CCBA, ECBA
-
Agile Training: PMI-ACP , CSM , CSPO
-
Scrum Training: CSM
-
DevOps
-
Program Management: PgMP
-
Cloud Technology: Exin Cloud Computing
-
Citrix Client Adminisration: Citrix Cloud Administration
The 10 top-paying certifications to target in 2024 are:
Conclusion
CMMI provides a strong framework to transform supply chain management. It fosters standardization, improves quality, and drives continuous improvement. CMMI helps organizations build strong, efficient supply chains. They will meet the demands of a fast-changing business environment.
CMMI can transform your supply chain. It works for both global firms and small businesses. Start your journey toward process excellence today. Unlock your supply chain's full potential!
Contact Us For More Information:
Visit :www.icertglobal.com Email : 
Read More
In today's fast-changing business world, strong supply chains are vital. They are key to staying competitive. The Capability Maturity Model Integration (CMMI) is for software development and process improvement. It is now a key framework for improving supply chain management (SCM). CMMI's structured approach gives organizations tools and methods. They can then streamline operations, improve collaboration, reduce risks, and boost performance.
This blog explores CMMI's key role in improving supply chain management. It covers its benefits and strategies for successful implementation.
Understanding CMMI in the Context of Supply Chain Management
CMMI is a framework for improving processes. It aims to boost organizational capabilities in various fields. CMMI, developed by the Software Engineering Institute (SEI), has evolved. It now addresses challenges in many fields, including supply chain management.
Supply chains involve multiple, interconnected entities. These include suppliers, manufacturers, distributors, and customers. Each contributes to the flow of goods and services. Effective relationship management requires robust processes and a focus on quality. It needs continuous improvement, too. These principles align with the CMMI framework.
Key Challenges in Supply Chain Management
Before delving into CMMI’s impact, it’s essential to recognize the common challenges in SCM:
1. Modern supply chains often span multiple geographies and industries. This causes fragmented processes and inefficiencies.
2. Risk Management: Natural disasters, geopolitical issues, or supplier failures can disrupt the supply chain.
3. Lack of Standardization: Inconsistent processes and communication gaps between stakeholders hinder operational efficiency.
4. Quality Control: Ensuring uniform quality across all levels of the supply chain can be challenging.
5. Data Management: Many organizations struggle to use accurate, real-time data for decision-making.
CMMI offers a way to meet these challenges. It promotes process standardization, risk mitigation, and capability development.
How CMMI Enhances Supply Chain Management
1. Process Standardization
CMMI emphasizes the need for standardized processes across the organization. In supply chain management, it means creating standard procedures for procurement, logistics, inventory, and quality.
A global electronics manufacturer can use CMMI. It can standardize its supplier evaluation criteria. This will ensure consistent quality and performance across its vendors.
2. Risk Management and Resilience
Risk management is a core aspect of CMMI. The framework helps organizations to find risks, assess their impact, and develop strategies to reduce them.
- Application in SCM: Companies can use CMMI to plan for supplier disruptions. This includes diversifying their suppliers or keeping buffer inventories.
3. Enhanced Collaboration and Communication
Supply chains rely on seamless communication between stakeholders. CMMI encourages organizations to establish clear communication protocols and foster collaboration across teams.
A retail giant might use CMMI. It could improve communication between its warehouses and distributors. This would reduce delivery delays and boost customer satisfaction.
4. Continuous Improvement
CMMI advocates a culture of continuous improvement. It should be done through regular process evaluations and feedback.
- Impact on SCM: By tracking KPIs like delivery times, inventory, and order accuracy, firms can find inefficiencies and fix them.
5. Quality Assurance
Quality in the supply chain is vital for customer satisfaction and brand reputation. CMMI helps organizations set strong quality assurance processes. These cover supplier audits to final product inspections.
Automotive companies can use CMMI to enforce strict quality checks at every stage of the supply chain. This will minimize defects and recalls.
6. Leveraging Technology for SCM Optimization
CMMI works well with advanced tech like AI, ML, and blockchain. It optimizes supply chains.
AI-driven analytics let organizations predict demand changes. They can then adjust their supply chains.
Benefits of CMMI in Supply Chain Management
1. Improved Efficiency: Better coordination and streamlined processes cut costs and sped up delivery.
2. Higher Customer Satisfaction: Better quality control delivers defect-free products, boosting brand loyalty.
3. Reduced Risk: Proactive risk management minimizes the impact of disruptions, ensuring business continuity.
4. Better Decision-Making: Standard data collection helps make informed decisions across the supply chain.
5. Increased Flexibility: Organizations can quickly adapt to market changes and customer demands. This gives them a competitive edge.
Steps to Implement CMMI in Supply Chain Management
1. Conduct a Gap Analysis
Assess your supply chain processes against CMMI's maturity levels. This will identify areas for improvement.
2. Set Clear Objectives
Define your goals for CMMI implementation. Examples include: reducing lead times or improving supplier collaboration.
3. Develop a Roadmap
Make a detailed plan. It should outline the steps, resources, and timelines needed to achieve your goals.
4. Train and Engage Employees
Train your workforce on CMMI principles and their relevance to supply chain management.
5. Monitor and Evaluate Progress
Regularly track your progress against predefined KPIs and refine your strategies as needed.
6. Obtain Certification
Consider a formal CMMI appraisal. It will validate your processes and commitment to excellence.
Case Study: CMMI in Action
Company: A global pharmaceutical firm
Challenge: The firm had frequent supply chain issues. These caused delays in product deliveries and upset customers.
Solution: By adopting CMMI, the organization standardized its supplier evaluations. It also implemented a strong risk management framework. Finally, it improved communication across its supply chain.
Delivery times improved by 25%. Customer satisfaction scores increased significantly within a year.
The Future of CMMI in Supply Chain Management
As supply chains grow more complex, CMMI's importance will rise. Emerging tech, like IoT, blockchain, and AI, will boost CMMI. They will enable real-time monitoring, predictive analytics, and process automation. Using these technologies with CMMI will help organizations face future challenges. They will also be more competitive.
How to obtain CMMI certification?
We are an Education Technology company providing certification training courses to accelerate careers of working professionals worldwide. We impart training through instructor-led classroom workshops, instructor-led live virtual training sessions, and self-paced e-learning courses.
We have successfully conducted training sessions in 108 countries across the globe and enabled thousands of working professionals to enhance the scope of their careers.
Our enterprise training portfolio includes in-demand and globally recognized certification training courses in Project Management, Quality Management, Business Analysis, IT Service Management, Agile and Scrum, Cyber Security, Data Science, and Emerging Technologies. Download our Enterprise Training Catalog from https://www.icertglobal.com/corporate-training-for-enterprises.php and https://www.icertglobal.com/index.php
Popular Courses include:
-
Project Management: PMP, CAPM ,PMI RMP
-
Quality Management: Six Sigma Black Belt ,Lean Six Sigma Green Belt, Lean Management, Minitab,CMMI
-
Business Analysis: CBAP, CCBA, ECBA
-
Agile Training: PMI-ACP , CSM , CSPO
-
Scrum Training: CSM
-
DevOps
-
Program Management: PgMP
-
Cloud Technology: Exin Cloud Computing
-
Citrix Client Adminisration: Citrix Cloud Administration
The 10 top-paying certifications to target in 2024 are:
Conclusion
CMMI provides a strong framework to transform supply chain management. It fosters standardization, improves quality, and drives continuous improvement. CMMI helps organizations build strong, efficient supply chains. They will meet the demands of a fast-changing business environment.
CMMI can transform your supply chain. It works for both global firms and small businesses. Start your journey toward process excellence today. Unlock your supply chain's full potential!
Contact Us For More Information:
Visit :www.icertglobal.com Email :
Incorporating Yellow Belt Skills in Daily Business Tasks
Lean Six Sigma Yellow Belt (SSYB) certification gives professionals basic tools and techniques. They can use them to find inefficiencies and improve processes. Though the certification is for large projects, its principles apply to everyday tasks. They foster a culture of continuous improvement. Here's how to seamlessly integrate Yellow Belt skills into your daily operations.
1. Process Mapping for Clarity and Efficiency
Yellow Belt training stresses using process maps, like SIPOC, to visualize workflows. SIPOC stands for Suppliers, Inputs, Process, Outputs, and Customers. In daily tasks, process mapping can:
- Clarify roles and responsibilities within a team.
- Identify unnecessary steps that slow down workflows.
- Serve as a guide for onboarding new team members.
For example, mapping the customer onboarding process can find redundant steps. It can enable quicker, smoother experiences for new clients.
2. Using Root Cause Analysis for Problem-Solving
Yellow Belt practitioners often use tools like the 5 Whys and Fishbone diagrams to find root causes. This approach can be applied to:
- Resolving recurring customer complaints.
- Identifying bottlenecks in task management systems.
- Understanding low employee engagement.
By digging deeper into problems, organizations can find the root causes. This is better than just applying temporary fixes.
3. Data-Driven Decision Making
SSYB training instills a data-focused mindset. It helps pros make decisions based on measurable outcomes. This can be used to:
- Analyze team performance metrics for improvement opportunities.
- Evaluate the impact of marketing strategies by tracking KPIs.
- Monitor inventory levels to avoid overstocking or stockouts.
Regularly reviewing data ensures business decisions are based on facts, not assumptions.
4. Standardizing Routine Processes
Standardization reduces errors and improves consistency. Yellow Belt tools help in:
- Creating step-by-step guides for recurring tasks like invoice processing or report generation.
- Developing templates for emails and documentation.
- Setting up quality checks to ensure compliance with standards.
Consistent processes boost productivity and customer satisfaction. They ensure reliable service.
5. Enhancing Team Collaboration
Yellow Belt principles emphasize teamwork and effective communication. By applying these skills daily, teams can:
- Conduct productive meetings with clear agendas and actionable outcomes.
- Share process improvement ideas in open forums.
- Collaborate on identifying and eliminating inefficiencies in shared workflows.
A culture of collaboration often leads to innovative solutions and stronger team dynamics.
6. Continuous Improvement Through Small Changes
The philosophy of Kaizen—continuous, incremental improvement—is central to Six Sigma. Employees can:
- Regularly review their work processes for potential tweaks.
- Encourage feedback loops to refine systems.
- Celebrate small wins that contribute to broader organizational goals.
For example, automating repetitive data-entry tasks can save time and reduce errors.
How to obtain SSYB certification?
We are an Education Technology company providing certification training courses to accelerate careers of working professionals worldwide. We impart training through instructor-led classroom workshops, instructor-led live virtual training sessions, and self-paced e-learning courses.
We have successfully conducted training sessions in 108 countries across the globe and enabled thousands of working professionals to enhance the scope of their careers.
Our enterprise training portfolio includes in-demand and globally recognized certification training courses in Project Management, Quality Management, Business Analysis, IT Service Management, Agile and Scrum, Cyber Security, Data Science, and Emerging Technologies. Download our Enterprise Training Catalog from https://www.icertglobal.com/corporate-training-for-enterprises.php and https://www.icertglobal.com/index.php
Popular Courses include:
-
Project Management: PMP, CAPM ,PMI RMP
-
Quality Management: Six Sigma Black Belt ,Lean Six Sigma Green Belt, Lean Management, Minitab,CMMI
-
Business Analysis: CBAP, CCBA, ECBA
-
Agile Training: PMI-ACP , CSM , CSPO
-
Scrum Training: CSM
-
DevOps
-
Program Management: PgMP
-
Cloud Technology: Exin Cloud Computing
-
Citrix Client Adminisration: Citrix Cloud Administration
The 10 top-paying certifications to target in 2024 are:
Conclusion
Using Yellow Belt skills in daily tasks helps create a culture of improvement. It makes organizations more proactive. These tools boost efficiency and collaboration. They support data-driven decisions. They empower employees to add value consistently. Embedding these practices into daily operations will boost profits. It will also improve employee satisfaction and customer experiences.
Contact Us For More Information:
Visit :www.icertglobal.com Email : 
Read More
Lean Six Sigma Yellow Belt (SSYB) certification gives professionals basic tools and techniques. They can use them to find inefficiencies and improve processes. Though the certification is for large projects, its principles apply to everyday tasks. They foster a culture of continuous improvement. Here's how to seamlessly integrate Yellow Belt skills into your daily operations.
1. Process Mapping for Clarity and Efficiency
Yellow Belt training stresses using process maps, like SIPOC, to visualize workflows. SIPOC stands for Suppliers, Inputs, Process, Outputs, and Customers. In daily tasks, process mapping can:
- Clarify roles and responsibilities within a team.
- Identify unnecessary steps that slow down workflows.
- Serve as a guide for onboarding new team members.
For example, mapping the customer onboarding process can find redundant steps. It can enable quicker, smoother experiences for new clients.
2. Using Root Cause Analysis for Problem-Solving
Yellow Belt practitioners often use tools like the 5 Whys and Fishbone diagrams to find root causes. This approach can be applied to:
- Resolving recurring customer complaints.
- Identifying bottlenecks in task management systems.
- Understanding low employee engagement.
By digging deeper into problems, organizations can find the root causes. This is better than just applying temporary fixes.
3. Data-Driven Decision Making
SSYB training instills a data-focused mindset. It helps pros make decisions based on measurable outcomes. This can be used to:
- Analyze team performance metrics for improvement opportunities.
- Evaluate the impact of marketing strategies by tracking KPIs.
- Monitor inventory levels to avoid overstocking or stockouts.
Regularly reviewing data ensures business decisions are based on facts, not assumptions.
4. Standardizing Routine Processes
Standardization reduces errors and improves consistency. Yellow Belt tools help in:
- Creating step-by-step guides for recurring tasks like invoice processing or report generation.
- Developing templates for emails and documentation.
- Setting up quality checks to ensure compliance with standards.
Consistent processes boost productivity and customer satisfaction. They ensure reliable service.
5. Enhancing Team Collaboration
Yellow Belt principles emphasize teamwork and effective communication. By applying these skills daily, teams can:
- Conduct productive meetings with clear agendas and actionable outcomes.
- Share process improvement ideas in open forums.
- Collaborate on identifying and eliminating inefficiencies in shared workflows.
A culture of collaboration often leads to innovative solutions and stronger team dynamics.
6. Continuous Improvement Through Small Changes
The philosophy of Kaizen—continuous, incremental improvement—is central to Six Sigma. Employees can:
- Regularly review their work processes for potential tweaks.
- Encourage feedback loops to refine systems.
- Celebrate small wins that contribute to broader organizational goals.
For example, automating repetitive data-entry tasks can save time and reduce errors.
How to obtain SSYB certification?
We are an Education Technology company providing certification training courses to accelerate careers of working professionals worldwide. We impart training through instructor-led classroom workshops, instructor-led live virtual training sessions, and self-paced e-learning courses.
We have successfully conducted training sessions in 108 countries across the globe and enabled thousands of working professionals to enhance the scope of their careers.
Our enterprise training portfolio includes in-demand and globally recognized certification training courses in Project Management, Quality Management, Business Analysis, IT Service Management, Agile and Scrum, Cyber Security, Data Science, and Emerging Technologies. Download our Enterprise Training Catalog from https://www.icertglobal.com/corporate-training-for-enterprises.php and https://www.icertglobal.com/index.php
Popular Courses include:
-
Project Management: PMP, CAPM ,PMI RMP
-
Quality Management: Six Sigma Black Belt ,Lean Six Sigma Green Belt, Lean Management, Minitab,CMMI
-
Business Analysis: CBAP, CCBA, ECBA
-
Agile Training: PMI-ACP , CSM , CSPO
-
Scrum Training: CSM
-
DevOps
-
Program Management: PgMP
-
Cloud Technology: Exin Cloud Computing
-
Citrix Client Adminisration: Citrix Cloud Administration
The 10 top-paying certifications to target in 2024 are:
Conclusion
Using Yellow Belt skills in daily tasks helps create a culture of improvement. It makes organizations more proactive. These tools boost efficiency and collaboration. They support data-driven decisions. They empower employees to add value consistently. Embedding these practices into daily operations will boost profits. It will also improve employee satisfaction and customer experiences.
Contact Us For More Information:
Visit :www.icertglobal.com Email :
Exploring the Role of Data Analysis in LSSGB Project Success
In Lean Six Sigma Green Belt (LSSGB) projects, data analysis plays a pivotal role in guiding decision-making, identifying improvement areas, and ensuring that solutions are data-driven rather than based on assumptions. As LSSGB professionals work on projects designed to reduce waste and improve quality, a solid understanding of data analysis methods and tools is essential. Let’s dive into the importance of data analysis in LSSGB projects, explore the key tools, and highlight real-world examples of how effective data analysis can enhance project outcomes.
Why Data Analysis Matters in LSSGB Projects
Lean Six Sigma is fundamentally about improving processes by eliminating inefficiencies and reducing variation. Data analysis provides the evidence needed to identify root causes of problems, quantify the extent of issues, and monitor the effectiveness of implemented solutions. Without proper data analysis, it’s easy to make decisions based on opinion or intuition, which can lead to incorrect conclusions and ineffective changes.
LSSGB projects follow the DMAIC (Define, Measure, Analyze, Improve, Control) methodology, with each phase heavily relying on data analysis:
- Define: In this phase, data helps clarify the problem and set specific project goals.
- Measure: Data collection enables teams to quantify issues and establish baselines for measuring improvement.
- Analyze: Data analysis helps pinpoint root causes and validate hypotheses.
- Improve: Analyzing data identifies optimal solutions for process improvements.
- Control: Post-improvement data collection ensures solutions are effective and sustainable.
Each stage requires different types of data analysis, from statistical tests to graphical analysis, to make data-informed decisions.
Key Data Analysis Tools Used in LSSGB Projects
1. Pareto Analysis
- The Pareto principle, or 80/20 rule, helps prioritize issues by showing that 80% of a problem's effects come from 20% of its causes. Pareto charts visualize this distribution, allowing teams to focus on high-impact areas.
2. Fishbone Diagram (Ishikawa Diagram)
- This tool helps break down potential causes of problems, grouping them into categories like People, Process, Equipment, and Materials. By examining each cause, LSSGB practitioners can identify areas that require further data collection and analysis.
3. Histogram
- A histogram visually displays data distribution, making it easier to spot patterns, variations, and deviations from expected norms. In the Measure phase, histograms can reveal data trends and show where performance improvements are needed.
4. Regression Analysis
- Regression analysis helps in understanding the relationship between dependent and independent variables. For example, in a manufacturing process, regression analysis might reveal how temperature and pressure impact product quality, guiding adjustments to improve outcomes.
5. Control Charts
- Used extensively in the Control phase, control charts monitor process stability over time. They reveal variations and help LSSGB teams maintain improvements by highlighting when a process drifts out of control.
6. Root Cause Analysis
- Often performed using tools like the 5 Whys, root cause analysis is essential for delving into underlying issues. Rather than addressing symptoms, this analysis guides LSSGB professionals to focus on the core reasons behind problems.
Real-World Examples of Data Analysis in LSSGB Projects
To better understand how data analysis drives LSSGB project success, let’s look at two practical examples:
1. Reducing Defects in Manufacturing
In a manufacturing setting, an LSSGB team aimed to reduce defects in a product line. During the Measure phase, they collected data on defect rates across different production shifts. Using Pareto analysis, they discovered that 70% of defects occurred during one shift. A further root cause analysis pointed to inadequate training during that shift. With data-driven evidence, the team implemented a targeted training program, significantly reducing defects.
2. Decreasing Customer Wait Time in a Call Center
A call center team used data analysis to tackle customer wait times. During the Analyze phase, they ran regression analysis on wait times, customer call types, and time of day. This revealed that peak wait times correlated with complex call types and high volume periods. The team implemented additional staff during peak hours and provided specialized training for handling complex calls, reducing average wait times by 30%.
The Value of Data-Driven Decision Making
The insights that data analysis provides are invaluable in building solutions that genuinely improve processes. Data analysis helps LSSGB practitioners:
- Validate hypotheses with concrete evidence.
- Quantify the impact of problems, focusing on high-priority areas.
- Create sustainable solutions by understanding underlying causes.
- Demonstrate improvement through measurable results.
Data-driven insights make LSSGB projects less prone to trial-and-error methods. This boosts the chances of achieving lasting improvements. A focus on data ensures that each action taken directly aligns with the project's goals, and solutions are backed by evidence rather than gut feeling.
How to Get Started with Data Analysis in LSSGB
For those new to data analysis or LSSGB, here are a few steps to build confidence:
1. Master Basic Statistical Concepts: Start with averages, standard deviation, and understanding data distribution.
2. Practice Using Tools: Software like Minitab, JMP, or even Excel can help visualize and analyze data effectively.
3. Learn the DMAIC Framework. Each phase requires specific data skills. So, familiarize yourself with how data is used in DMAIC.
4. Focus on Key Techniques: For beginners, pareto analysis, histograms, and control charts are great tools.
How to obtain LSSGB certification?
We are an Education Technology company providing certification training courses to accelerate careers of working professionals worldwide. We impart training through instructor-led classroom workshops, instructor-led live virtual training sessions, and self-paced e-learning courses.
We have successfully conducted training sessions in 108 countries across the globe and enabled thousands of working professionals to enhance the scope of their careers.
Our enterprise training portfolio includes in-demand and globally recognized certification training courses in Project Management, Quality Management, Business Analysis, IT Service Management, Agile and Scrum, Cyber Security, Data Science, and Emerging Technologies. Download our Enterprise Training Catalog from https://www.icertglobal.com/corporate-training-for-enterprises.php and https://www.icertglobal.com/index.php
Popular Courses include:
-
Project Management: PMP, CAPM ,PMI RMP
-
Quality Management: Six Sigma Black Belt ,Lean Six Sigma Green Belt, Lean Management, Minitab,CMMI
-
Business Analysis: CBAP, CCBA, ECBA
-
Agile Training: PMI-ACP , CSM , CSPO
-
Scrum Training: CSM
-
DevOps
-
Program Management: PgMP
-
Cloud Technology: Exin Cloud Computing
-
Citrix Client Adminisration: Citrix Cloud Administration
The 10 top-paying certifications to target in 2024 are:
Conclusion
Data analysis is a core component of Lean Six Sigma Green Belt projects, turning raw data into actionable insights. By mastering data analysis techniques, LSSGB professionals can improve various industries. Data-driven decisions ensure LSSGB projects deliver real value. They reduce defects, cut waste, and enhance customer satisfaction. Using data analysis in the Lean Six Sigma framework helps teams. It enables informed decisions, tracks progress, and drives success in process improvement.
Contact Us For More Information:
Visit :www.icertglobal.com Email : 
Read More
In Lean Six Sigma Green Belt (LSSGB) projects, data analysis plays a pivotal role in guiding decision-making, identifying improvement areas, and ensuring that solutions are data-driven rather than based on assumptions. As LSSGB professionals work on projects designed to reduce waste and improve quality, a solid understanding of data analysis methods and tools is essential. Let’s dive into the importance of data analysis in LSSGB projects, explore the key tools, and highlight real-world examples of how effective data analysis can enhance project outcomes.
Why Data Analysis Matters in LSSGB Projects
Lean Six Sigma is fundamentally about improving processes by eliminating inefficiencies and reducing variation. Data analysis provides the evidence needed to identify root causes of problems, quantify the extent of issues, and monitor the effectiveness of implemented solutions. Without proper data analysis, it’s easy to make decisions based on opinion or intuition, which can lead to incorrect conclusions and ineffective changes.
LSSGB projects follow the DMAIC (Define, Measure, Analyze, Improve, Control) methodology, with each phase heavily relying on data analysis:
- Define: In this phase, data helps clarify the problem and set specific project goals.
- Measure: Data collection enables teams to quantify issues and establish baselines for measuring improvement.
- Analyze: Data analysis helps pinpoint root causes and validate hypotheses.
- Improve: Analyzing data identifies optimal solutions for process improvements.
- Control: Post-improvement data collection ensures solutions are effective and sustainable.
Each stage requires different types of data analysis, from statistical tests to graphical analysis, to make data-informed decisions.
Key Data Analysis Tools Used in LSSGB Projects
1. Pareto Analysis
- The Pareto principle, or 80/20 rule, helps prioritize issues by showing that 80% of a problem's effects come from 20% of its causes. Pareto charts visualize this distribution, allowing teams to focus on high-impact areas.
2. Fishbone Diagram (Ishikawa Diagram)
- This tool helps break down potential causes of problems, grouping them into categories like People, Process, Equipment, and Materials. By examining each cause, LSSGB practitioners can identify areas that require further data collection and analysis.
3. Histogram
- A histogram visually displays data distribution, making it easier to spot patterns, variations, and deviations from expected norms. In the Measure phase, histograms can reveal data trends and show where performance improvements are needed.
4. Regression Analysis
- Regression analysis helps in understanding the relationship between dependent and independent variables. For example, in a manufacturing process, regression analysis might reveal how temperature and pressure impact product quality, guiding adjustments to improve outcomes.
5. Control Charts
- Used extensively in the Control phase, control charts monitor process stability over time. They reveal variations and help LSSGB teams maintain improvements by highlighting when a process drifts out of control.
6. Root Cause Analysis
- Often performed using tools like the 5 Whys, root cause analysis is essential for delving into underlying issues. Rather than addressing symptoms, this analysis guides LSSGB professionals to focus on the core reasons behind problems.
Real-World Examples of Data Analysis in LSSGB Projects
To better understand how data analysis drives LSSGB project success, let’s look at two practical examples:
1. Reducing Defects in Manufacturing
In a manufacturing setting, an LSSGB team aimed to reduce defects in a product line. During the Measure phase, they collected data on defect rates across different production shifts. Using Pareto analysis, they discovered that 70% of defects occurred during one shift. A further root cause analysis pointed to inadequate training during that shift. With data-driven evidence, the team implemented a targeted training program, significantly reducing defects.
2. Decreasing Customer Wait Time in a Call Center
A call center team used data analysis to tackle customer wait times. During the Analyze phase, they ran regression analysis on wait times, customer call types, and time of day. This revealed that peak wait times correlated with complex call types and high volume periods. The team implemented additional staff during peak hours and provided specialized training for handling complex calls, reducing average wait times by 30%.
The Value of Data-Driven Decision Making
The insights that data analysis provides are invaluable in building solutions that genuinely improve processes. Data analysis helps LSSGB practitioners:
- Validate hypotheses with concrete evidence.
- Quantify the impact of problems, focusing on high-priority areas.
- Create sustainable solutions by understanding underlying causes.
- Demonstrate improvement through measurable results.
Data-driven insights make LSSGB projects less prone to trial-and-error methods. This boosts the chances of achieving lasting improvements. A focus on data ensures that each action taken directly aligns with the project's goals, and solutions are backed by evidence rather than gut feeling.
How to Get Started with Data Analysis in LSSGB
For those new to data analysis or LSSGB, here are a few steps to build confidence:
1. Master Basic Statistical Concepts: Start with averages, standard deviation, and understanding data distribution.
2. Practice Using Tools: Software like Minitab, JMP, or even Excel can help visualize and analyze data effectively.
3. Learn the DMAIC Framework. Each phase requires specific data skills. So, familiarize yourself with how data is used in DMAIC.
4. Focus on Key Techniques: For beginners, pareto analysis, histograms, and control charts are great tools.
How to obtain LSSGB certification?
We are an Education Technology company providing certification training courses to accelerate careers of working professionals worldwide. We impart training through instructor-led classroom workshops, instructor-led live virtual training sessions, and self-paced e-learning courses.
We have successfully conducted training sessions in 108 countries across the globe and enabled thousands of working professionals to enhance the scope of their careers.
Our enterprise training portfolio includes in-demand and globally recognized certification training courses in Project Management, Quality Management, Business Analysis, IT Service Management, Agile and Scrum, Cyber Security, Data Science, and Emerging Technologies. Download our Enterprise Training Catalog from https://www.icertglobal.com/corporate-training-for-enterprises.php and https://www.icertglobal.com/index.php
Popular Courses include:
-
Project Management: PMP, CAPM ,PMI RMP
-
Quality Management: Six Sigma Black Belt ,Lean Six Sigma Green Belt, Lean Management, Minitab,CMMI
-
Business Analysis: CBAP, CCBA, ECBA
-
Agile Training: PMI-ACP , CSM , CSPO
-
Scrum Training: CSM
-
DevOps
-
Program Management: PgMP
-
Cloud Technology: Exin Cloud Computing
-
Citrix Client Adminisration: Citrix Cloud Administration
The 10 top-paying certifications to target in 2024 are:
Conclusion
Data analysis is a core component of Lean Six Sigma Green Belt projects, turning raw data into actionable insights. By mastering data analysis techniques, LSSGB professionals can improve various industries. Data-driven decisions ensure LSSGB projects deliver real value. They reduce defects, cut waste, and enhance customer satisfaction. Using data analysis in the Lean Six Sigma framework helps teams. It enables informed decisions, tracks progress, and drives success in process improvement.
Contact Us For More Information:
Visit :www.icertglobal.com Email :
High-Impact Lean Management Strategies for Small Firms!
In a competitive landscape, small firms are constantly challenged to do more with less. Lean management, traditionally popularized in large manufacturing environments, offers a set of principles that small businesses can adopt to increase efficiency, reduce waste, and improve customer satisfaction. Implementing Lean in a small firm doesn’t require a massive overhaul but rather small, high-impact changes that bring substantial benefits. Here, we’ll explore some effective Lean strategies tailored for small businesses looking to optimize their operations and enhance performance.
1. Embrace a Culture of Continuous Improvement
The foundation of Lean Management is the concept of Kaizen, or continuous improvement. In a small firm, this begins with fostering a mindset where every team member is encouraged to look for small, incremental improvements in their day-to-day tasks. Regular brainstorming sessions, open forums for feedback, and a supportive culture that values innovation and collaboration can help your team feel empowered to suggest ideas.
Quick Tip: Start small by setting up a weekly 15-minute “Improvement Huddle” where employees can share ideas for reducing waste or improving a specific process.
2. Map Out Key Processes for Greater Clarity
Process mapping, or creating a Value Stream Map, is a Lean technique that identifies all the steps involved in delivering a product or service. This allows you to visualize each step, identify bottlenecks, and pinpoint areas of inefficiency. For a small business, this practice is invaluable—it sheds light on potential time-wasters and gives a clear understanding of where resources are being used.
Quick Tip: Choose one critical process (like order fulfillment or customer support) and create a simple map. Use sticky notes or a whiteboard to outline each step, then analyze where delays or unnecessary actions can be minimized.
3. Focus on Reducing Waste
Waste, in Lean terms, doesn’t only refer to physical waste but also includes wasted time, resources, and even talent. Small firms can apply the 8 Wastes of Lean (defects, overproduction, waiting, non-utilized talent, transportation, inventory, motion, and extra processing) to identify inefficiencies in various areas. For example, if customer orders are delayed due to waiting for supplier shipments, the firm can look into consolidating orders or finding local suppliers.
Quick Tip: Conduct a quick “waste audit” with your team. Ask employees to identify anything in their workflow that feels redundant or time-consuming, and brainstorm solutions together.
4. Simplify Inventory Management
Holding excess inventory ties up valuable capital and storage space—resources that small firms can’t afford to waste. Adopting a Lean approach to inventory management, often called Just-in-Time (JIT) inventory, ensures you only hold what you need to meet demand. By coordinating closely with suppliers and monitoring sales trends, small firms can reduce overstock and avoid stockouts.
Quick Tip: Start by keeping track of your current inventory trends over a few weeks. Analyze which items are slow-moving and consider ordering them less frequently to free up space and reduce costs.
5. Standardize Processes to Reduce Variability
Inconsistencies in processes lead to errors, wasted time, and poor customer experience. By standardizing procedures, small firms can create reliable workflows that are easy to train, follow, and improve. This could be as simple as creating checklists for repetitive tasks (like quality checks or customer onboarding) or developing clear protocols for handling customer inquiries.
Quick Tip: Identify one repetitive task in your business that lacks a clear protocol. Collaborate with employees who perform this task to create a simple checklist or guide, and test its effectiveness over a few weeks.
6. Implement 5S for an Organized Workspace
The 5S system (Sort, Set in Order, Shine, Standardize, Sustain) is a Lean strategy for workplace organization that can improve efficiency and reduce wasted time looking for tools or documents. This is especially helpful for small businesses with limited space, as it encourages a clutter-free environment where everything has a designated place.
Quick Tip: Start with Sort by removing unnecessary items from the workspace. Next, Set in Order by arranging tools and materials based on their frequency of use, making them more accessible and reducing wasted motion.
7. Empower Employees through Cross-Training
Cross-training employees can be a powerful Lean strategy for small firms. It maximizes flexibility and ensures coverage of key tasks when team members are unavailable. This approach reduces reliance on one person for key tasks. It boosts productivity, as employees can step in as needed.
Quick Tip: Identify two to three core skills that would benefit from cross-training in your team. Offer workshops or job-shadowing sessions to allow employees to learn these skills.
8. Use Metrics to Drive Performance
Lean Management emphasizes the importance of data-driven decision-making. For a small business, tracking relevant KPIs can provide insights. It shows which processes work and where to improve. KPIs might include order fulfillment time, customer satisfaction rates, or employee productivity. Regularly reviewing these metrics lets you to adjust processes and avoid costly inefficiencies.
Quick Tip: Choose two to three KPIs that are most relevant to your business goals. Review them weekly or monthly with your team, and use them as a benchmark for continuous improvement.
9. Leverage Technology to Streamline Tasks
Many small firms can benefit from technology to support Lean initiatives. From project management software to customer relationship management (CRM) tools, technology can automate repetitive tasks, improve communication, and provide real-time insights. The right tools can enhance productivity, reduce manual errors, and free up employees to focus on higher-value tasks.
Quick Tip: Start by automating one time-consuming process, such as scheduling or invoicing, with a digital tool. Many cost-effective solutions offer free trials, so you can experiment before committing to a subscription.
How to obtain Lean Management certification?
We are an Education Technology company providing certification training courses to accelerate careers of working professionals worldwide. We impart training through instructor-led classroom workshops, instructor-led live virtual training sessions, and self-paced e-learning courses.
We have successfully conducted training sessions in 108 countries across the globe and enabled thousands of working professionals to enhance the scope of their careers.
Our enterprise training portfolio includes in-demand and globally recognized certification training courses in Project Management, Quality Management, Business Analysis, IT Service Management, Agile and Scrum, Cyber Security, Data Science, and Emerging Technologies. Download our Enterprise Training Catalog from https://www.icertglobal.com/corporate-training-for-enterprises.php and https://www.icertglobal.com/index.php
Popular Courses include:
-
Project Management: PMP, CAPM ,PMI RMP
-
Quality Management: Six Sigma Black Belt ,Lean Six Sigma Green Belt, Lean Management, Minitab,CMMI
-
Business Analysis: CBAP, CCBA, ECBA
-
Agile Training: PMI-ACP , CSM , CSPO
-
Scrum Training: CSM
-
DevOps
-
Program Management: PgMP
-
Cloud Technology: Exin Cloud Computing
-
Citrix Client Adminisration: Citrix Cloud Administration
The 10 top-paying certifications to target in 2024 are:
Conclusion
Lean Management is resource-light. It's ideal for small firms that want high efficiency and low costs. By embracing a culture of continuous improvement, simplifying processes, and focusing on waste reduction, small firms can enjoy significant benefits with relatively small changes. Lean Management is a journey of constant improvement. By applying these strategies, small businesses can become more resilient and efficient, and better positioned for growth.
Contact Us For More Information:
Visit :www.icertglobal.com Email : 
Read More
In a competitive landscape, small firms are constantly challenged to do more with less. Lean management, traditionally popularized in large manufacturing environments, offers a set of principles that small businesses can adopt to increase efficiency, reduce waste, and improve customer satisfaction. Implementing Lean in a small firm doesn’t require a massive overhaul but rather small, high-impact changes that bring substantial benefits. Here, we’ll explore some effective Lean strategies tailored for small businesses looking to optimize their operations and enhance performance.
1. Embrace a Culture of Continuous Improvement
The foundation of Lean Management is the concept of Kaizen, or continuous improvement. In a small firm, this begins with fostering a mindset where every team member is encouraged to look for small, incremental improvements in their day-to-day tasks. Regular brainstorming sessions, open forums for feedback, and a supportive culture that values innovation and collaboration can help your team feel empowered to suggest ideas.
Quick Tip: Start small by setting up a weekly 15-minute “Improvement Huddle” where employees can share ideas for reducing waste or improving a specific process.
2. Map Out Key Processes for Greater Clarity
Process mapping, or creating a Value Stream Map, is a Lean technique that identifies all the steps involved in delivering a product or service. This allows you to visualize each step, identify bottlenecks, and pinpoint areas of inefficiency. For a small business, this practice is invaluable—it sheds light on potential time-wasters and gives a clear understanding of where resources are being used.
Quick Tip: Choose one critical process (like order fulfillment or customer support) and create a simple map. Use sticky notes or a whiteboard to outline each step, then analyze where delays or unnecessary actions can be minimized.
3. Focus on Reducing Waste
Waste, in Lean terms, doesn’t only refer to physical waste but also includes wasted time, resources, and even talent. Small firms can apply the 8 Wastes of Lean (defects, overproduction, waiting, non-utilized talent, transportation, inventory, motion, and extra processing) to identify inefficiencies in various areas. For example, if customer orders are delayed due to waiting for supplier shipments, the firm can look into consolidating orders or finding local suppliers.
Quick Tip: Conduct a quick “waste audit” with your team. Ask employees to identify anything in their workflow that feels redundant or time-consuming, and brainstorm solutions together.
4. Simplify Inventory Management
Holding excess inventory ties up valuable capital and storage space—resources that small firms can’t afford to waste. Adopting a Lean approach to inventory management, often called Just-in-Time (JIT) inventory, ensures you only hold what you need to meet demand. By coordinating closely with suppliers and monitoring sales trends, small firms can reduce overstock and avoid stockouts.
Quick Tip: Start by keeping track of your current inventory trends over a few weeks. Analyze which items are slow-moving and consider ordering them less frequently to free up space and reduce costs.
5. Standardize Processes to Reduce Variability
Inconsistencies in processes lead to errors, wasted time, and poor customer experience. By standardizing procedures, small firms can create reliable workflows that are easy to train, follow, and improve. This could be as simple as creating checklists for repetitive tasks (like quality checks or customer onboarding) or developing clear protocols for handling customer inquiries.
Quick Tip: Identify one repetitive task in your business that lacks a clear protocol. Collaborate with employees who perform this task to create a simple checklist or guide, and test its effectiveness over a few weeks.
6. Implement 5S for an Organized Workspace
The 5S system (Sort, Set in Order, Shine, Standardize, Sustain) is a Lean strategy for workplace organization that can improve efficiency and reduce wasted time looking for tools or documents. This is especially helpful for small businesses with limited space, as it encourages a clutter-free environment where everything has a designated place.
Quick Tip: Start with Sort by removing unnecessary items from the workspace. Next, Set in Order by arranging tools and materials based on their frequency of use, making them more accessible and reducing wasted motion.
7. Empower Employees through Cross-Training
Cross-training employees can be a powerful Lean strategy for small firms. It maximizes flexibility and ensures coverage of key tasks when team members are unavailable. This approach reduces reliance on one person for key tasks. It boosts productivity, as employees can step in as needed.
Quick Tip: Identify two to three core skills that would benefit from cross-training in your team. Offer workshops or job-shadowing sessions to allow employees to learn these skills.
8. Use Metrics to Drive Performance
Lean Management emphasizes the importance of data-driven decision-making. For a small business, tracking relevant KPIs can provide insights. It shows which processes work and where to improve. KPIs might include order fulfillment time, customer satisfaction rates, or employee productivity. Regularly reviewing these metrics lets you to adjust processes and avoid costly inefficiencies.
Quick Tip: Choose two to three KPIs that are most relevant to your business goals. Review them weekly or monthly with your team, and use them as a benchmark for continuous improvement.
9. Leverage Technology to Streamline Tasks
Many small firms can benefit from technology to support Lean initiatives. From project management software to customer relationship management (CRM) tools, technology can automate repetitive tasks, improve communication, and provide real-time insights. The right tools can enhance productivity, reduce manual errors, and free up employees to focus on higher-value tasks.
Quick Tip: Start by automating one time-consuming process, such as scheduling or invoicing, with a digital tool. Many cost-effective solutions offer free trials, so you can experiment before committing to a subscription.
How to obtain Lean Management certification?
We are an Education Technology company providing certification training courses to accelerate careers of working professionals worldwide. We impart training through instructor-led classroom workshops, instructor-led live virtual training sessions, and self-paced e-learning courses.
We have successfully conducted training sessions in 108 countries across the globe and enabled thousands of working professionals to enhance the scope of their careers.
Our enterprise training portfolio includes in-demand and globally recognized certification training courses in Project Management, Quality Management, Business Analysis, IT Service Management, Agile and Scrum, Cyber Security, Data Science, and Emerging Technologies. Download our Enterprise Training Catalog from https://www.icertglobal.com/corporate-training-for-enterprises.php and https://www.icertglobal.com/index.php
Popular Courses include:
-
Project Management: PMP, CAPM ,PMI RMP
-
Quality Management: Six Sigma Black Belt ,Lean Six Sigma Green Belt, Lean Management, Minitab,CMMI
-
Business Analysis: CBAP, CCBA, ECBA
-
Agile Training: PMI-ACP , CSM , CSPO
-
Scrum Training: CSM
-
DevOps
-
Program Management: PgMP
-
Cloud Technology: Exin Cloud Computing
-
Citrix Client Adminisration: Citrix Cloud Administration
The 10 top-paying certifications to target in 2024 are:
Conclusion
Lean Management is resource-light. It's ideal for small firms that want high efficiency and low costs. By embracing a culture of continuous improvement, simplifying processes, and focusing on waste reduction, small firms can enjoy significant benefits with relatively small changes. Lean Management is a journey of constant improvement. By applying these strategies, small businesses can become more resilient and efficient, and better positioned for growth.
Contact Us For More Information:
Visit :www.icertglobal.com Email :
Master Monte Carlo Simulation with Minitab for Data Analysis
For data analysis, statistics, and probability, professionals rely on tools and software. They use them to make decisions and improve processes. One such tool, widely used in industrial engineering, is Minitab. It is also used in quality control and reliability analysis. This article will explore using Minitab for Monte Carlo simulations. It is a powerful technique for modeling and analyzing complex systems.
What are Monte Carlo Simulations?
Monte Carlo simulations use random sampling to model and analyze complex systems. They are a computational technique. Monte Carlo simulations run many tests with random inputs. They can show the variability and uncertainty of a system. This technique is useful when traditional methods are not feasible or accurate.
How Does Minitab Support Monte Carlo Simulations?
Minitab is a top statistical software. It has many tools for data analysis, hypothesis testing, and statistical modeling. Minitab's Monte Carlo simulations let users generate random variables. They can also sample from probability distributions. They can then run simulations to analyze a system's behavior. Minitab's user-friendly interface and strong stats make it perfect for Monte Carlo simulations.
Minitab supports Monte Carlo simulations. It has a user-friendly interface. It simplifies generating random variables and running simulations based on specified distributions. This feature lets users model complex systems. It assesses how uncertainty affects decisions. So, it's a valuable tool for risk analysis and project planning. Minitab's strong stats tools help visualize and analyze simulation results. So, organizations can make data-driven decisions with greater confidence.
Steps for Conducting Monte Carlo Simulations with Minitab
To run Monte Carlo simulations with Minitab, first define the problem to analyze. Then, identify the key variables involved. Next, use Minitab's random number generator to create input distributions for these variables. Then, set up the simulation to run many iterations to produce a range of possible outcomes. Finally, use Minitab's tools to analyze the results. Interpret the data and make decisions based on the simulation findings.
-
Define the problem: State the simulation's goal and key variables.
-
Generate random variables. Use Minitab's random number generator to create random values for the simulation.
-
Specify probability distributions: Choose the correct distributions for the input variables. Use normal, exponential, or uniform ones.
-
Run the simulations. Use Minitab to run multiple simulations with the random input values. Then, analyze the results.
-
Conduct a sensitivity analysis. It tests how input changes affect the simulation output. This checks the system's robustness.
Benefits of Using Minitab for Monte Carlo Simulations
Minitab for Monte Carlo simulations has many benefits. It offers better data visualization and a user-friendly interface. These features simplify complex analyses. This software helps users model uncertainty and assess risks. It is a valuable decision-making tool for many industries. Also, Minitab's stats can do robust sensitivity analyses. They help organizations find key factors that affect their processes and outcomes.
-
Minitab has powerful statistical tools. They make it easy to run Monte Carlo simulations.
-
User-friendly interface: Minitab's wizards and design make it easy to run simulations.
-
Data visualization: Minitab has tools for graphing Monte Carlo results. They make it easier to interpret and share findings.
-
Process improvement: By using Monte Carlo simulations in Minitab, organizations can improve. They can identify risks and optimize processes.
How to obtain Minitab certification?
We are an Education Technology company providing certification training courses to accelerate careers of working professionals worldwide. We impart training through instructor-led classroom workshops, instructor-led live virtual training sessions, and self-paced e-learning courses.
We have successfully conducted training sessions in 108 countries across the globe and enabled thousands of working professionals to enhance the scope of their careers.
Our enterprise training portfolio includes in-demand and globally recognized certification training courses in Project Management, Quality Management, Business Analysis, IT Service Management, Agile and Scrum, Cyber Security, Data Science, and Emerging Technologies. Download our Enterprise Training Catalog from https://www.icertglobal.com/corporate-training-for-enterprises.php and https://www.icertglobal.com/index.php
Popular Courses include:
-
Project Management: PMP, CAPM ,PMI RMP
-
Quality Management: Six Sigma Black Belt ,Lean Six Sigma Green Belt, Lean Management, Minitab,CMMI
-
Business Analysis: CBAP, CCBA, ECBA
-
Agile Training: PMI-ACP , CSM , CSPO
-
Scrum Training: CSM
-
DevOps
-
Program Management: PgMP
-
Cloud Technology: Exin Cloud Computing
-
Citrix Client Adminisration: Citrix Cloud Administration
The 10 top-paying certifications to target in 2024 are:
Conclusion
In conclusion, Minitab is a versatile tool. It can run many statistical analyses, including Monte Carlo simulations. Minitab's powerful tools help users understand complex systems. They can spot areas for improvement. And, they can make data-driven decisions. To improve your skills in statistical modeling, use Minitab for Monte Carlo simulations.
Contact Us For More Information:
Visit :www.icertglobal.com Email : 
Read More
For data analysis, statistics, and probability, professionals rely on tools and software. They use them to make decisions and improve processes. One such tool, widely used in industrial engineering, is Minitab. It is also used in quality control and reliability analysis. This article will explore using Minitab for Monte Carlo simulations. It is a powerful technique for modeling and analyzing complex systems.
What are Monte Carlo Simulations?
Monte Carlo simulations use random sampling to model and analyze complex systems. They are a computational technique. Monte Carlo simulations run many tests with random inputs. They can show the variability and uncertainty of a system. This technique is useful when traditional methods are not feasible or accurate.
How Does Minitab Support Monte Carlo Simulations?
Minitab is a top statistical software. It has many tools for data analysis, hypothesis testing, and statistical modeling. Minitab's Monte Carlo simulations let users generate random variables. They can also sample from probability distributions. They can then run simulations to analyze a system's behavior. Minitab's user-friendly interface and strong stats make it perfect for Monte Carlo simulations.
Minitab supports Monte Carlo simulations. It has a user-friendly interface. It simplifies generating random variables and running simulations based on specified distributions. This feature lets users model complex systems. It assesses how uncertainty affects decisions. So, it's a valuable tool for risk analysis and project planning. Minitab's strong stats tools help visualize and analyze simulation results. So, organizations can make data-driven decisions with greater confidence.
Steps for Conducting Monte Carlo Simulations with Minitab
To run Monte Carlo simulations with Minitab, first define the problem to analyze. Then, identify the key variables involved. Next, use Minitab's random number generator to create input distributions for these variables. Then, set up the simulation to run many iterations to produce a range of possible outcomes. Finally, use Minitab's tools to analyze the results. Interpret the data and make decisions based on the simulation findings.
-
Define the problem: State the simulation's goal and key variables.
-
Generate random variables. Use Minitab's random number generator to create random values for the simulation.
-
Specify probability distributions: Choose the correct distributions for the input variables. Use normal, exponential, or uniform ones.
-
Run the simulations. Use Minitab to run multiple simulations with the random input values. Then, analyze the results.
-
Conduct a sensitivity analysis. It tests how input changes affect the simulation output. This checks the system's robustness.
Benefits of Using Minitab for Monte Carlo Simulations
Minitab for Monte Carlo simulations has many benefits. It offers better data visualization and a user-friendly interface. These features simplify complex analyses. This software helps users model uncertainty and assess risks. It is a valuable decision-making tool for many industries. Also, Minitab's stats can do robust sensitivity analyses. They help organizations find key factors that affect their processes and outcomes.
-
Minitab has powerful statistical tools. They make it easy to run Monte Carlo simulations.
-
User-friendly interface: Minitab's wizards and design make it easy to run simulations.
-
Data visualization: Minitab has tools for graphing Monte Carlo results. They make it easier to interpret and share findings.
-
Process improvement: By using Monte Carlo simulations in Minitab, organizations can improve. They can identify risks and optimize processes.
How to obtain Minitab certification?
We are an Education Technology company providing certification training courses to accelerate careers of working professionals worldwide. We impart training through instructor-led classroom workshops, instructor-led live virtual training sessions, and self-paced e-learning courses.
We have successfully conducted training sessions in 108 countries across the globe and enabled thousands of working professionals to enhance the scope of their careers.
Our enterprise training portfolio includes in-demand and globally recognized certification training courses in Project Management, Quality Management, Business Analysis, IT Service Management, Agile and Scrum, Cyber Security, Data Science, and Emerging Technologies. Download our Enterprise Training Catalog from https://www.icertglobal.com/corporate-training-for-enterprises.php and https://www.icertglobal.com/index.php
Popular Courses include:
-
Project Management: PMP, CAPM ,PMI RMP
-
Quality Management: Six Sigma Black Belt ,Lean Six Sigma Green Belt, Lean Management, Minitab,CMMI
-
Business Analysis: CBAP, CCBA, ECBA
-
Agile Training: PMI-ACP , CSM , CSPO
-
Scrum Training: CSM
-
DevOps
-
Program Management: PgMP
-
Cloud Technology: Exin Cloud Computing
-
Citrix Client Adminisration: Citrix Cloud Administration
The 10 top-paying certifications to target in 2024 are:
Conclusion
In conclusion, Minitab is a versatile tool. It can run many statistical analyses, including Monte Carlo simulations. Minitab's powerful tools help users understand complex systems. They can spot areas for improvement. And, they can make data-driven decisions. To improve your skills in statistical modeling, use Minitab for Monte Carlo simulations.
Contact Us For More Information:
Visit :www.icertglobal.com Email :
Shift to Cloud-Based Quality Management Systems Explained
In today's fast-changing business world, companies are using cloud-based quality management systems (QMS) more. They want to boost efficiency, streamline operations, and meet industry standards. This article will explore the key benefits of cloud-based QMS software. It can help organizations with quality control, secure data, and ongoing improvement.
What are Cloud-Based Quality Management Systems?
Cloud-based quality management systems are software solutions. They let companies manage quality, compliance, and documents in one, digital platform. The cloud lets organizations access and share data easily. They can collaborate with remote team members and automate key processes to boost efficiency and agility.
The Benefits of Cloud-Based QMS Software
Cloud-based Quality Management Systems (QMS) offer organizations more flexibility. They can scale easily and access data in real-time. Teams can collaborate, no matter their location. Cloud technology cuts infrastructure costs. It lets businesses ditch costly, on-premises hardware. They also benefit from automated updates and maintenance. Also, cloud-based QMS solutions improve compliance and audit readiness. They provide complete audit trails and documentation. This ensures consistent quality standards and practices.
-
Data Security: Cloud-based QMS software has strong data security. It includes encryption, audit trails, and secure access controls. These protect sensitive information from cyber threats.
-
Remote Access: Cloud-based QMS software lets teams access tools and documents from anywhere, at any time. This boosts collaboration and communication across global teams.
-
Digital Transformation: Cloud-based QMS software helps firms digitize their quality management processes. It reduces reliance on paper-based systems and boosts efficiency and accuracy.
-
Process Automation: Cloud-based QMS software automates key quality management tasks. These include supplier management, risk assessment, and corrective actions. It also supports improvement initiatives. This approach streamlines operations and cuts manual errors.
-
Regulatory Compliance: Cloud-based QMS software helps firms meet industry standards and regulations. It ensures products and services are of the highest quality.
How Cloud-Based QMS Software Drives Business Efficiency
Cloud-based Quality Management Systems (QMS) greatly enhance efficiency. They streamline processes and give real-time access to critical data across the organization. Cloud technology helps companies automate quality control. It also boosts team collaboration and ensures compliance with industry standards. These benefits lead to faster decisions and lower costs. Also, cloud-based QMS solutions offer scalable storage and data management. This helps businesses adapt to changing market demands and improve quality.
Cloud-based QMS software has many features. They can boost efficiency and cut costs. Cloud-based QMS software improves efficiency in key ways:
-
Streamlined quality audits and inspections
-
Interactive dashboard reporting for real-time monitoring
-
Enhanced supply chain visibility and collaboration
-
Efficient training management and compliance tracking
-
Seamless integration with other business systems and tools. Cloud-based QMS software gives organizations insights into their quality performance. It helps them find ways to improve and excel using smart manufacturing and modern tech.
The Future of Quality Management: Embracing the Cloud
As industries evolve and embrace digital change, cloud-based quality management systems are essential. They help organizations stay ahead of the curve. Cloud solutions can boost efficiency, compliance, and success. They must be scalable, integrated, and user-friendly.
Quality management is shifting to cloud-based solutions. They are more flexible and scalable for organizations. Using the cloud can improve team collaboration and quality control. It also allows real-time access to data for better decision-making. Also, cloud technology enables strong data analytics. It helps organizations quickly find quality issues and trends. This improves product quality and customer satisfaction.
How to obtain Quality Management certification?
We are an Education Technology company providing certification training courses to accelerate careers of working professionals worldwide. We impart training through instructor-led classroom workshops, instructor-led live virtual training sessions, and self-paced e-learning courses.
We have successfully conducted training sessions in 108 countries across the globe and enabled thousands of working professionals to enhance the scope of their careers.
Our enterprise training portfolio includes in-demand and globally recognized certification training courses in Project Management, Quality Management, Business Analysis, IT Service Management, Agile and Scrum, Cyber Security, Data Science, and Emerging Technologies. Download our Enterprise Training Catalog from https://www.icertglobal.com/corporate-training-for-enterprises.php and https://www.icertglobal.com/index.php
Popular Courses include:
-
Project Management: PMP, CAPM ,PMI RMP
-
Quality Management: Six Sigma Black Belt ,Lean Six Sigma Green Belt, Lean Management, Minitab,CMMI
-
Business Analysis: CBAP, CCBA, ECBA
-
Agile Training: PMI-ACP , CSM , CSPO
-
Scrum Training: CSM
-
DevOps
-
Program Management: PgMP
-
Cloud Technology: Exin Cloud Computing
-
Citrix Client Adminisration: Citrix Cloud Administration
The 10 top-paying certifications to target in 2024 are:
Conclusion
In conclusion, moving to cloud-based quality management systems is a chance for businesses. It can improve their quality control, boost efficiency, and ensure compliance. Organizations can succeed in a competitive, fast-changing market. They can do this by using modern technology, agile manufacturing, and quality tools.
Contact Us For More Information:
Visit :www.icertglobal.com Email : 
Read More
In today's fast-changing business world, companies are using cloud-based quality management systems (QMS) more. They want to boost efficiency, streamline operations, and meet industry standards. This article will explore the key benefits of cloud-based QMS software. It can help organizations with quality control, secure data, and ongoing improvement.
What are Cloud-Based Quality Management Systems?
Cloud-based quality management systems are software solutions. They let companies manage quality, compliance, and documents in one, digital platform. The cloud lets organizations access and share data easily. They can collaborate with remote team members and automate key processes to boost efficiency and agility.
The Benefits of Cloud-Based QMS Software
Cloud-based Quality Management Systems (QMS) offer organizations more flexibility. They can scale easily and access data in real-time. Teams can collaborate, no matter their location. Cloud technology cuts infrastructure costs. It lets businesses ditch costly, on-premises hardware. They also benefit from automated updates and maintenance. Also, cloud-based QMS solutions improve compliance and audit readiness. They provide complete audit trails and documentation. This ensures consistent quality standards and practices.
-
Data Security: Cloud-based QMS software has strong data security. It includes encryption, audit trails, and secure access controls. These protect sensitive information from cyber threats.
-
Remote Access: Cloud-based QMS software lets teams access tools and documents from anywhere, at any time. This boosts collaboration and communication across global teams.
-
Digital Transformation: Cloud-based QMS software helps firms digitize their quality management processes. It reduces reliance on paper-based systems and boosts efficiency and accuracy.
-
Process Automation: Cloud-based QMS software automates key quality management tasks. These include supplier management, risk assessment, and corrective actions. It also supports improvement initiatives. This approach streamlines operations and cuts manual errors.
-
Regulatory Compliance: Cloud-based QMS software helps firms meet industry standards and regulations. It ensures products and services are of the highest quality.
How Cloud-Based QMS Software Drives Business Efficiency
Cloud-based Quality Management Systems (QMS) greatly enhance efficiency. They streamline processes and give real-time access to critical data across the organization. Cloud technology helps companies automate quality control. It also boosts team collaboration and ensures compliance with industry standards. These benefits lead to faster decisions and lower costs. Also, cloud-based QMS solutions offer scalable storage and data management. This helps businesses adapt to changing market demands and improve quality.
Cloud-based QMS software has many features. They can boost efficiency and cut costs. Cloud-based QMS software improves efficiency in key ways:
-
Streamlined quality audits and inspections
-
Interactive dashboard reporting for real-time monitoring
-
Enhanced supply chain visibility and collaboration
-
Efficient training management and compliance tracking
-
Seamless integration with other business systems and tools. Cloud-based QMS software gives organizations insights into their quality performance. It helps them find ways to improve and excel using smart manufacturing and modern tech.
The Future of Quality Management: Embracing the Cloud
As industries evolve and embrace digital change, cloud-based quality management systems are essential. They help organizations stay ahead of the curve. Cloud solutions can boost efficiency, compliance, and success. They must be scalable, integrated, and user-friendly.
Quality management is shifting to cloud-based solutions. They are more flexible and scalable for organizations. Using the cloud can improve team collaboration and quality control. It also allows real-time access to data for better decision-making. Also, cloud technology enables strong data analytics. It helps organizations quickly find quality issues and trends. This improves product quality and customer satisfaction.
How to obtain Quality Management certification?
We are an Education Technology company providing certification training courses to accelerate careers of working professionals worldwide. We impart training through instructor-led classroom workshops, instructor-led live virtual training sessions, and self-paced e-learning courses.
We have successfully conducted training sessions in 108 countries across the globe and enabled thousands of working professionals to enhance the scope of their careers.
Our enterprise training portfolio includes in-demand and globally recognized certification training courses in Project Management, Quality Management, Business Analysis, IT Service Management, Agile and Scrum, Cyber Security, Data Science, and Emerging Technologies. Download our Enterprise Training Catalog from https://www.icertglobal.com/corporate-training-for-enterprises.php and https://www.icertglobal.com/index.php
Popular Courses include:
-
Project Management: PMP, CAPM ,PMI RMP
-
Quality Management: Six Sigma Black Belt ,Lean Six Sigma Green Belt, Lean Management, Minitab,CMMI
-
Business Analysis: CBAP, CCBA, ECBA
-
Agile Training: PMI-ACP , CSM , CSPO
-
Scrum Training: CSM
-
DevOps
-
Program Management: PgMP
-
Cloud Technology: Exin Cloud Computing
-
Citrix Client Adminisration: Citrix Cloud Administration
The 10 top-paying certifications to target in 2024 are:
Conclusion
In conclusion, moving to cloud-based quality management systems is a chance for businesses. It can improve their quality control, boost efficiency, and ensure compliance. Organizations can succeed in a competitive, fast-changing market. They can do this by using modern technology, agile manufacturing, and quality tools.
Contact Us For More Information:
Visit :www.icertglobal.com Email :
The Role of CTFL in Testing Microservices Architectures
Microservices architectures are popular in software development. They are scalable, flexible, and easy to maintain. However, greater complexity requires thorough testing. We must ensure these systems are reliable and perform well. The CTFL certification is vital for testing microservices.
CTFL Certification for Microservices Testing
CTFL certification gives professionals the skills to test microservices. This certification shows that individuals are experts in testing complex systems. They understand the principles, practices, and methods needed for it.
Importance of CTFL in Testing Microservices
The importance of CTFL in testing microservices cannot be overstated. As microservices architectures rise, so does the demand for skilled testers. They must ensure the quality and reliability of these systems. CTFL certification gives people the tools to test microservices. This helps prevent issues in production.
CTFL Qualifications for Testing Microservices
To excel in testing microservices architectures, testers must have certain skills. They need a strong grasp of software testing fundamentals. They must know testing techniques for microservices. Finally, they must be skilled in using testing tools and frameworks. CTFL certification covers all these aspects and more. It is essential for testing professionals in the microservices domain.
CTFL Skills for Microservices Testing
Mastering CTFL skills is essential for effective testing of microservices architectures. Testers must be skilled in test planning, design, execution, and evaluation. CTFL certification gives a thorough understanding of these skills. It also teaches their use in testing microservices.
CTFL Exam in Microservices Architectures
The CTFL exam for testing microservices covers many topics. These include testing principles, techniques, management, and tools. Test takers must show their knowledge of these topics. They will do this through multiple-choice questions and practical exercises.
CTFL Principles in Microservices Testing
CTFL principles serve as the foundation for testing microservices architectures. These principles include thoroughness, independence, and traceability, among others. These principles will help testers ensure their testing is rigorous, effective, and reliable.
Testing microservices requires a shift from traditional monolithic methods. The CTFL principles are a solid foundation for ensuring each service's quality. CTFL-certified testers understand the software lifecycle. They can use techniques like integration testing. This ensures each microservice works both alone and in the larger system. Also, the CTFL framework helps testers find key tests. These include performance and security tests. They are vital for ensuring the reliability of microservices in distributed environments.
CTFL Concepts for Testing Microservices
CTFL concepts help testers understand the key parts of testing microservices. They provide a framework for this. These concepts include service decomposition, service integration, service orchestration, and service monitoring. By knowing these concepts, testers can make better testing methods for microservices.
CTFL Knowledge in Microservices Testing
CTFL knowledge encompasses a wide range of topics related to testing microservices architectures. Testers must know about service virtualization, contract testing, chaos engineering, and fault injection. CTFL certification ensures that testers know how to test microservices.
CTFL Practices for Testing Microservices
CTFL practices focus on the best practices and techniques for testing microservices architectures. These practices include continuous testing, test automation, exploratory testing, and performance testing. Testers can ensure that microservices are well tested and meet quality standards by following these practices.
Exam Syllabus for CTFL in Microservices Testing
The CTFL exam syllabus for testing microservices covers a wide range of topics. These include testing fundamentals, test design, test implementation, and test management. Test takers must show proficiency in all areas to pass the exam and get CTFL certification.
CTFL Tools for Microservices Testing
CTFL tools play a vital role in testing microservices architectures. Testers must be skilled in using tools like Postman, JMeter, SoapUI, and Mockito. They will automate tests, simulate microservices, and monitor performance. CTFL certification teaches skills to use these tools in microservices testing.
Benefits of CTFL in Microservices Testing
The benefits of CTFL in testing microservices architectures are numerous. CTFL certification boosts testers' skills and knowledge. It also raises their credibility and market value. CTFL certification can open new career paths for testers. It can also help microservices projects succeed.
Role of CTFL Certification in Microservices Testing
CTFL certification plays a crucial role in the testing of microservices architectures. It lets testers prove their skills and dedication to quality. Employers often prefer candidates with CTFL certification. It shows a higher skill level and professionalism in testing microservices.
How to obtain CTFL certification?
We are an Education Technology company providing certification training courses to accelerate careers of working professionals worldwide. We impart training through instructor-led classroom workshops, instructor-led live virtual training sessions, and self-paced e-learning courses.
We have successfully conducted training sessions in 108 countries across the globe and enabled thousands of working professionals to enhance the scope of their careers.
Our enterprise training portfolio includes in-demand and globally recognized certification training courses in Project Management, Quality Management, Business Analysis, IT Service Management, Agile and Scrum, Cyber Security, Data Science, and Emerging Technologies. Download our Enterprise Training Catalog from https://www.icertglobal.com/corporate-training-for-enterprises.php and https://www.icertglobal.com/index.php
Popular Courses include:
-
Project Management: PMP, CAPM ,PMI RMP
-
Quality Management: Six Sigma Black Belt ,Lean Six Sigma Green Belt, Lean Management, Minitab,CMMI
-
Business Analysis: CBAP, CCBA, ECBA
-
Agile Training: PMI-ACP , CSM , CSPO
-
Scrum Training: CSM
-
DevOps
-
Program Management: PgMP
-
Cloud Technology: Exin Cloud Computing
-
Citrix Client Adminisration: Citrix Cloud Administration
The 10 top-paying certifications to target in 2024 are:
Conclusion
In conclusion, CTFL certification is very important for testers of microservices. CTFL certification can boost testers' skills and credibility in testing microservices. This will help software projects succeed. With the rise of microservices, CTFL's role in testing is crucial.
Contact Us For More Information:
Visit :www.icertglobal.com Email :
Read More
Microservices architectures are popular in software development. They are scalable, flexible, and easy to maintain. However, greater complexity requires thorough testing. We must ensure these systems are reliable and perform well. The CTFL certification is vital for testing microservices.
CTFL Certification for Microservices Testing
CTFL certification gives professionals the skills to test microservices. This certification shows that individuals are experts in testing complex systems. They understand the principles, practices, and methods needed for it.
Importance of CTFL in Testing Microservices
The importance of CTFL in testing microservices cannot be overstated. As microservices architectures rise, so does the demand for skilled testers. They must ensure the quality and reliability of these systems. CTFL certification gives people the tools to test microservices. This helps prevent issues in production.
CTFL Qualifications for Testing Microservices
To excel in testing microservices architectures, testers must have certain skills. They need a strong grasp of software testing fundamentals. They must know testing techniques for microservices. Finally, they must be skilled in using testing tools and frameworks. CTFL certification covers all these aspects and more. It is essential for testing professionals in the microservices domain.
CTFL Skills for Microservices Testing
Mastering CTFL skills is essential for effective testing of microservices architectures. Testers must be skilled in test planning, design, execution, and evaluation. CTFL certification gives a thorough understanding of these skills. It also teaches their use in testing microservices.
CTFL Exam in Microservices Architectures
The CTFL exam for testing microservices covers many topics. These include testing principles, techniques, management, and tools. Test takers must show their knowledge of these topics. They will do this through multiple-choice questions and practical exercises.
CTFL Principles in Microservices Testing
CTFL principles serve as the foundation for testing microservices architectures. These principles include thoroughness, independence, and traceability, among others. These principles will help testers ensure their testing is rigorous, effective, and reliable.
Testing microservices requires a shift from traditional monolithic methods. The CTFL principles are a solid foundation for ensuring each service's quality. CTFL-certified testers understand the software lifecycle. They can use techniques like integration testing. This ensures each microservice works both alone and in the larger system. Also, the CTFL framework helps testers find key tests. These include performance and security tests. They are vital for ensuring the reliability of microservices in distributed environments.
CTFL Concepts for Testing Microservices
CTFL concepts help testers understand the key parts of testing microservices. They provide a framework for this. These concepts include service decomposition, service integration, service orchestration, and service monitoring. By knowing these concepts, testers can make better testing methods for microservices.
CTFL Knowledge in Microservices Testing
CTFL knowledge encompasses a wide range of topics related to testing microservices architectures. Testers must know about service virtualization, contract testing, chaos engineering, and fault injection. CTFL certification ensures that testers know how to test microservices.
CTFL Practices for Testing Microservices
CTFL practices focus on the best practices and techniques for testing microservices architectures. These practices include continuous testing, test automation, exploratory testing, and performance testing. Testers can ensure that microservices are well tested and meet quality standards by following these practices.
Exam Syllabus for CTFL in Microservices Testing
The CTFL exam syllabus for testing microservices covers a wide range of topics. These include testing fundamentals, test design, test implementation, and test management. Test takers must show proficiency in all areas to pass the exam and get CTFL certification.
CTFL Tools for Microservices Testing
CTFL tools play a vital role in testing microservices architectures. Testers must be skilled in using tools like Postman, JMeter, SoapUI, and Mockito. They will automate tests, simulate microservices, and monitor performance. CTFL certification teaches skills to use these tools in microservices testing.
Benefits of CTFL in Microservices Testing
The benefits of CTFL in testing microservices architectures are numerous. CTFL certification boosts testers' skills and knowledge. It also raises their credibility and market value. CTFL certification can open new career paths for testers. It can also help microservices projects succeed.
Role of CTFL Certification in Microservices Testing
CTFL certification plays a crucial role in the testing of microservices architectures. It lets testers prove their skills and dedication to quality. Employers often prefer candidates with CTFL certification. It shows a higher skill level and professionalism in testing microservices.
How to obtain CTFL certification?
We are an Education Technology company providing certification training courses to accelerate careers of working professionals worldwide. We impart training through instructor-led classroom workshops, instructor-led live virtual training sessions, and self-paced e-learning courses.
We have successfully conducted training sessions in 108 countries across the globe and enabled thousands of working professionals to enhance the scope of their careers.
Our enterprise training portfolio includes in-demand and globally recognized certification training courses in Project Management, Quality Management, Business Analysis, IT Service Management, Agile and Scrum, Cyber Security, Data Science, and Emerging Technologies. Download our Enterprise Training Catalog from https://www.icertglobal.com/corporate-training-for-enterprises.php and https://www.icertglobal.com/index.php
Popular Courses include:
-
Project Management: PMP, CAPM ,PMI RMP
-
Quality Management: Six Sigma Black Belt ,Lean Six Sigma Green Belt, Lean Management, Minitab,CMMI
-
Business Analysis: CBAP, CCBA, ECBA
-
Agile Training: PMI-ACP , CSM , CSPO
-
Scrum Training: CSM
-
DevOps
-
Program Management: PgMP
-
Cloud Technology: Exin Cloud Computing
-
Citrix Client Adminisration: Citrix Cloud Administration
The 10 top-paying certifications to target in 2024 are:
Conclusion
In conclusion, CTFL certification is very important for testers of microservices. CTFL certification can boost testers' skills and credibility in testing microservices. This will help software projects succeed. With the rise of microservices, CTFL's role in testing is crucial.
Contact Us For More Information:
Visit :www.icertglobal.com Email :
LSSBB Role in Driving Organizational Change Effectively
In today's fast-paced business world, companies seek to adapt and stay competitive. A key factor in driving change is the role of a Lean Six Sigma Black Belt (LSSBB) professional. LSSBBs are vital for leading change and improving processes in an organization. They drive excellence. This article will explore the importance of an LSSBB in driving change. It will also cover their key responsibilities in leading transformation efforts.
What is the Role of an LSSBB?
An LSSBB is a highly trained expert. They are skilled in Lean Six Sigma, a mix of Lean and Six Sigma methods. They are experts in problem-solving, data analysis, and more. They excel at root cause analysis, quality management, performance optimization, and process efficiency. LSSBBs are trained to find improvement areas in an organization. They develop and implement solutions, and drive improvement initiatives.
A Lean Six Sigma Black Belt (LSSBB) leads process improvements. They use advanced Lean and Six Sigma methods. They must find inefficiencies, cut waste, and improve processes. This will boost productivity and quality in the organization. Also, LSSBBs mentor Green Belts and team members. They guide them through complex projects and ensure alignment with business goals.
How Does an LSSBB Drive Organizational Change?
A Lean Six Sigma Black Belt (LSSBB) leads data-driven process improvements. These improvements boost efficiency and cut waste. They drive change in the organization. They use methods like DMAIC to find the root causes of inefficiencies. Then, they implement solutions to streamline operations and boost productivity. Their focus on continuous improvement builds a culture of innovation and accountability. It ensures the organization grows sustainably and endures over the long term.
-
Leadership and Project Management: LSSBBs have strong skills in both. They can lead change initiatives effectively. They create and run project plans, set metrics, and oversee work. This ensures success.
-
LSSBBs use Lean to find waste, streamline processes, and boost efficiency. They are skilled problem-solvers. They use data and root cause analysis to solve issues and drive change.
-
LSSBBs work closely with stakeholders to understand their needs. They align change initiatives with strategic goals. They create and share change strategies. They engage stakeholders and ensure buy-in at all levels of the organization.
-
Change Leadership and Communication Skills: LSSBBs are good communicators. They can lead change in an organization. They drive change, transform culture, and foster teamwork to ensure success.
-
LSSBBs aim to improve performance and processes for business impact. They measure the success of change initiatives and track metrics. They drive continuous improvement to achieve operational excellence.
How Can an LSSBB Help Enhance Organizational Effectiveness?
An LSSBB (Lean Six Sigma Black Belt) boosts efficiency. They use data-driven methods to find and fix process inefficiencies. They foster a culture of continuous improvement. It empowers teams to optimize workflows, reduce waste, and improve quality. This boosts productivity and customer satisfaction. Also, their leadership skills help manage change. They ensure that improvement initiatives align with strategic goals and deliver lasting results.
-
LSSBBs facilitate change and optimize workflows. They drive efficiency in organizations. They find areas to improve. Then, they create new solutions. Finally, they implement change frameworks to boost effectiveness.
-
Change Culture and Integration: LSSBBs promote change and integration in all functions. They create change strategies, apply tactics, and promote a mindset of improvement. This drives success.
-
Change Measurement and Evaluation: LSSBBs use tools to measure change. They assess the success of change initiatives. They track key performance indicators. They assess change outcomes. They use data to optimize change efforts.
How to obtain LSSBB certification?
We are an Education Technology company providing certification training courses to accelerate careers of working professionals worldwide. We impart training through instructor-led classroom workshops, instructor-led live virtual training sessions, and self-paced e-learning courses.
We have successfully conducted training sessions in 108 countries across the globe and enabled thousands of working professionals to enhance the scope of their careers.
Our enterprise training portfolio includes in-demand and globally recognized certification training courses in Project Management, Quality Management, Business Analysis, IT Service Management, Agile and Scrum, Cyber Security, Data Science, and Emerging Technologies. Download our Enterprise Training Catalog from https://www.icertglobal.com/corporate-training-for-enterprises.php and https://www.icertglobal.com/index.php
Popular Courses include:
-
Project Management: PMP, CAPM ,PMI RMP
-
Quality Management: Six Sigma Black Belt ,Lean Six Sigma Green Belt, Lean Management, Minitab,CMMI
-
Business Analysis: CBAP, CCBA, ECBA
-
Agile Training: PMI-ACP , CSM , CSPO
-
Scrum Training: CSM
-
DevOps
-
Program Management: PgMP
-
Cloud Technology: Exin Cloud Computing
-
Citrix Client Adminisration: Citrix Cloud Administration
The 10 top-paying certifications to target in 2024 are:
Conclusion
In conclusion, an LSSBB is vital for driving change in organizations. It helps them adapt, grow, and stay competitive in today's fast-paced business world. LSSBBs have a unique set of skills and knowledge. They can lead change initiatives, improve processes, and deliver business impact. Organizations that invest in LSSBB certification can benefit. These professionals can help drive change and achieve excellence.
Contact Us For More Information:
Visit :www.icertglobal.com Email : 
Read More
In today's fast-paced business world, companies seek to adapt and stay competitive. A key factor in driving change is the role of a Lean Six Sigma Black Belt (LSSBB) professional. LSSBBs are vital for leading change and improving processes in an organization. They drive excellence. This article will explore the importance of an LSSBB in driving change. It will also cover their key responsibilities in leading transformation efforts.
What is the Role of an LSSBB?
An LSSBB is a highly trained expert. They are skilled in Lean Six Sigma, a mix of Lean and Six Sigma methods. They are experts in problem-solving, data analysis, and more. They excel at root cause analysis, quality management, performance optimization, and process efficiency. LSSBBs are trained to find improvement areas in an organization. They develop and implement solutions, and drive improvement initiatives.
A Lean Six Sigma Black Belt (LSSBB) leads process improvements. They use advanced Lean and Six Sigma methods. They must find inefficiencies, cut waste, and improve processes. This will boost productivity and quality in the organization. Also, LSSBBs mentor Green Belts and team members. They guide them through complex projects and ensure alignment with business goals.
How Does an LSSBB Drive Organizational Change?
A Lean Six Sigma Black Belt (LSSBB) leads data-driven process improvements. These improvements boost efficiency and cut waste. They drive change in the organization. They use methods like DMAIC to find the root causes of inefficiencies. Then, they implement solutions to streamline operations and boost productivity. Their focus on continuous improvement builds a culture of innovation and accountability. It ensures the organization grows sustainably and endures over the long term.
-
Leadership and Project Management: LSSBBs have strong skills in both. They can lead change initiatives effectively. They create and run project plans, set metrics, and oversee work. This ensures success.
-
LSSBBs use Lean to find waste, streamline processes, and boost efficiency. They are skilled problem-solvers. They use data and root cause analysis to solve issues and drive change.
-
LSSBBs work closely with stakeholders to understand their needs. They align change initiatives with strategic goals. They create and share change strategies. They engage stakeholders and ensure buy-in at all levels of the organization.
-
Change Leadership and Communication Skills: LSSBBs are good communicators. They can lead change in an organization. They drive change, transform culture, and foster teamwork to ensure success.
-
LSSBBs aim to improve performance and processes for business impact. They measure the success of change initiatives and track metrics. They drive continuous improvement to achieve operational excellence.
How Can an LSSBB Help Enhance Organizational Effectiveness?
An LSSBB (Lean Six Sigma Black Belt) boosts efficiency. They use data-driven methods to find and fix process inefficiencies. They foster a culture of continuous improvement. It empowers teams to optimize workflows, reduce waste, and improve quality. This boosts productivity and customer satisfaction. Also, their leadership skills help manage change. They ensure that improvement initiatives align with strategic goals and deliver lasting results.
-
LSSBBs facilitate change and optimize workflows. They drive efficiency in organizations. They find areas to improve. Then, they create new solutions. Finally, they implement change frameworks to boost effectiveness.
-
Change Culture and Integration: LSSBBs promote change and integration in all functions. They create change strategies, apply tactics, and promote a mindset of improvement. This drives success.
-
Change Measurement and Evaluation: LSSBBs use tools to measure change. They assess the success of change initiatives. They track key performance indicators. They assess change outcomes. They use data to optimize change efforts.
How to obtain LSSBB certification?
We are an Education Technology company providing certification training courses to accelerate careers of working professionals worldwide. We impart training through instructor-led classroom workshops, instructor-led live virtual training sessions, and self-paced e-learning courses.
We have successfully conducted training sessions in 108 countries across the globe and enabled thousands of working professionals to enhance the scope of their careers.
Our enterprise training portfolio includes in-demand and globally recognized certification training courses in Project Management, Quality Management, Business Analysis, IT Service Management, Agile and Scrum, Cyber Security, Data Science, and Emerging Technologies. Download our Enterprise Training Catalog from https://www.icertglobal.com/corporate-training-for-enterprises.php and https://www.icertglobal.com/index.php
Popular Courses include:
-
Project Management: PMP, CAPM ,PMI RMP
-
Quality Management: Six Sigma Black Belt ,Lean Six Sigma Green Belt, Lean Management, Minitab,CMMI
-
Business Analysis: CBAP, CCBA, ECBA
-
Agile Training: PMI-ACP , CSM , CSPO
-
Scrum Training: CSM
-
DevOps
-
Program Management: PgMP
-
Cloud Technology: Exin Cloud Computing
-
Citrix Client Adminisration: Citrix Cloud Administration
The 10 top-paying certifications to target in 2024 are:
Conclusion
In conclusion, an LSSBB is vital for driving change in organizations. It helps them adapt, grow, and stay competitive in today's fast-paced business world. LSSBBs have a unique set of skills and knowledge. They can lead change initiatives, improve processes, and deliver business impact. Organizations that invest in LSSBB certification can benefit. These professionals can help drive change and achieve excellence.
Contact Us For More Information:
Visit :www.icertglobal.com Email :
Global Collaboration in Lean Project Management Strategies
In today's fast-paced world, businesses seek to boost efficiency and productivity. A popular, effective strategy in recent years is global collaboration in lean projects. Companies can cut costs and improve results by using global teams. Their diverse skills can streamline processes and ensure timely, high-quality work.
What is Global Collaboration in Lean Projects?
Global collaboration in lean projects means uniting a diverse group. They have different skills and cultures. They work together toward a common goal. This approach lets organizations tap a wider talent pool. It also helps them access new markets and benefit from diverse ideas. By breaking down borders and promoting collaboration, companies can boost innovation and growth.
How Does Global Collaboration Benefit Lean Projects?
Global collaboration enhances lean projects. It brings together diverse perspectives and expertise. This can lead to innovative solutions and better problem-solving. This approach helps teams find inefficiencies and share best practices across cultures. It drives continuous improvement. Also, advanced communication tools enable real-time collaboration. They help keep all team members aligned. They can quickly address challenges as they arise.
-
Diverse Perspectives: Team members from different countries bring unique insights. Their varied cultures add to the mix. Diversity can lead to better decision-making and problem-solving. It can boost creativity and drive project success with innovative solutions.
-
24/7 Operations: Teams in different time zones enable round-the-clock work. This ensures maximum productivity. This work can help speed up projects and meet tight deadlines.
-
Cost Savings: Companies can access high-quality talent at a lower cost by using global resources. This can help reduce operational expenses, increase profit margins, and improve the overall financial health of the organization.
-
Increased Flexibility: Global collaboration lets organizations quickly change their teams to fit project needs. This flexibility helps companies adapt to changing markets and customer demands.
Challenges of Global Collaboration in Lean Projects
Global collaboration in lean projects has challenges. They arise from differences in culture, communication, and operations across regions. These variances can cause misunderstandings about project goals. They can hurt the effectiveness of lean methodologies. Also, coordinating across time zones can complicate decision-making. Ensuring all team members are engaged is tough. So, organizations must invest in good communication tools and practices.
While global collaboration offers numerous benefits, it also comes with its own set of challenges. These may include:
-
Communication Barriers: Language differences, cultural norms, and time zones can hurt team communication and teamwork.
-
Technology Limitations: Internet connections, software, and infrastructure may vary by region. This can affect project workflows.
-
Security Concerns: Sharing sensitive data across borders may raise security and privacy issues. We need strong measures to protect intellectual property and confidential data.
To overcome these challenges, organizations must:
-
-
Establish clear communication channels.
-
Provide training on cultural differences.
-
Invest in secure technologies.
-
Set clear goals and expectations for global teams.
How to obtain Lean Management certification?
We are an Education Technology company providing certification training courses to accelerate careers of working professionals worldwide. We impart training through instructor-led classroom workshops, instructor-led live virtual training sessions, and self-paced e-learning courses.
We have successfully conducted training sessions in 108 countries across the globe and enabled thousands of working professionals to enhance the scope of their careers.
Our enterprise training portfolio includes in-demand and globally recognized certification training courses in Project Management, Quality Management, Business Analysis, IT Service Management, Agile and Scrum, Cyber Security, Data Science, and Emerging Technologies. Download our Enterprise Training Catalog from https://www.icertglobal.com/corporate-training-for-enterprises.php and https://www.icertglobal.com/index.php
Popular Courses include:
-
Project Management: PMP, CAPM ,PMI RMP
-
Quality Management: Six Sigma Black Belt ,Lean Six Sigma Green Belt, Lean Management, Minitab,CMMI
-
Business Analysis: CBAP, CCBA, ECBA
-
Agile Training: PMI-ACP , CSM , CSPO
-
Scrum Training: CSM
-
DevOps
-
Program Management: PgMP
-
Cloud Technology: Exin Cloud Computing
-
Citrix Client Adminisration: Citrix Cloud Administration
The 10 top-paying certifications to target in 2024 are:
Conclusion
Global collaboration in lean projects has many benefits. It can help organizations improve efficiency, drive innovation, and succeed on a global scale. Diverse, global teams can unlock new opportunities. They can boost productivity and deliver great results. To maximize global collaboration, organizations must address communication issues. They must adopt new technologies and prioritize security. This will ensure lean projects succeed worldwide.
Contact Us For More Information:
Visit :www.icertglobal.com Email : 
Read More
In today's fast-paced world, businesses seek to boost efficiency and productivity. A popular, effective strategy in recent years is global collaboration in lean projects. Companies can cut costs and improve results by using global teams. Their diverse skills can streamline processes and ensure timely, high-quality work.
What is Global Collaboration in Lean Projects?
Global collaboration in lean projects means uniting a diverse group. They have different skills and cultures. They work together toward a common goal. This approach lets organizations tap a wider talent pool. It also helps them access new markets and benefit from diverse ideas. By breaking down borders and promoting collaboration, companies can boost innovation and growth.
How Does Global Collaboration Benefit Lean Projects?
Global collaboration enhances lean projects. It brings together diverse perspectives and expertise. This can lead to innovative solutions and better problem-solving. This approach helps teams find inefficiencies and share best practices across cultures. It drives continuous improvement. Also, advanced communication tools enable real-time collaboration. They help keep all team members aligned. They can quickly address challenges as they arise.
-
Diverse Perspectives: Team members from different countries bring unique insights. Their varied cultures add to the mix. Diversity can lead to better decision-making and problem-solving. It can boost creativity and drive project success with innovative solutions.
-
24/7 Operations: Teams in different time zones enable round-the-clock work. This ensures maximum productivity. This work can help speed up projects and meet tight deadlines.
-
Cost Savings: Companies can access high-quality talent at a lower cost by using global resources. This can help reduce operational expenses, increase profit margins, and improve the overall financial health of the organization.
-
Increased Flexibility: Global collaboration lets organizations quickly change their teams to fit project needs. This flexibility helps companies adapt to changing markets and customer demands.
Challenges of Global Collaboration in Lean Projects
Global collaboration in lean projects has challenges. They arise from differences in culture, communication, and operations across regions. These variances can cause misunderstandings about project goals. They can hurt the effectiveness of lean methodologies. Also, coordinating across time zones can complicate decision-making. Ensuring all team members are engaged is tough. So, organizations must invest in good communication tools and practices.
While global collaboration offers numerous benefits, it also comes with its own set of challenges. These may include:
-
Communication Barriers: Language differences, cultural norms, and time zones can hurt team communication and teamwork.
-
Technology Limitations: Internet connections, software, and infrastructure may vary by region. This can affect project workflows.
-
Security Concerns: Sharing sensitive data across borders may raise security and privacy issues. We need strong measures to protect intellectual property and confidential data.
To overcome these challenges, organizations must:
-
-
Establish clear communication channels.
-
Provide training on cultural differences.
-
Invest in secure technologies.
-
Set clear goals and expectations for global teams.
-
How to obtain Lean Management certification?
We are an Education Technology company providing certification training courses to accelerate careers of working professionals worldwide. We impart training through instructor-led classroom workshops, instructor-led live virtual training sessions, and self-paced e-learning courses.
We have successfully conducted training sessions in 108 countries across the globe and enabled thousands of working professionals to enhance the scope of their careers.
Our enterprise training portfolio includes in-demand and globally recognized certification training courses in Project Management, Quality Management, Business Analysis, IT Service Management, Agile and Scrum, Cyber Security, Data Science, and Emerging Technologies. Download our Enterprise Training Catalog from https://www.icertglobal.com/corporate-training-for-enterprises.php and https://www.icertglobal.com/index.php
Popular Courses include:
-
Project Management: PMP, CAPM ,PMI RMP
-
Quality Management: Six Sigma Black Belt ,Lean Six Sigma Green Belt, Lean Management, Minitab,CMMI
-
Business Analysis: CBAP, CCBA, ECBA
-
Agile Training: PMI-ACP , CSM , CSPO
-
Scrum Training: CSM
-
DevOps
-
Program Management: PgMP
-
Cloud Technology: Exin Cloud Computing
-
Citrix Client Adminisration: Citrix Cloud Administration
The 10 top-paying certifications to target in 2024 are:
Conclusion
Global collaboration in lean projects has many benefits. It can help organizations improve efficiency, drive innovation, and succeed on a global scale. Diverse, global teams can unlock new opportunities. They can boost productivity and deliver great results. To maximize global collaboration, organizations must address communication issues. They must adopt new technologies and prioritize security. This will ensure lean projects succeed worldwide.
Contact Us For More Information:
Visit :www.icertglobal.com Email :
CMMI Role in Minimizing Technical Debt in Software Projects
In software development, efficiency, quality, and speed are crucial. Technical debt is extra work. It arises when quick, easy software is chosen over better, but harder, options. It can slow down projects and reduce productivity. CMMI (Capability Maturity Model Integration) helps minimize technical debt. It is key to successful software projects.
What is CMMI? How Does it Work?
CMMI is a set of best practices and standards. They guide organizations in improving their development processes, project management, and quality. It provides guidelines and controls to manage technical debt in software development. CMMI lets organizations assess and adopt the best practices. This optimizes their software engineering, reduces risk, and ensures compliance with industry standards.
How Does CMMI Help Manage Technical Debt?
CMMI helps set maturity levels. They show an organization's ability to deliver quality software consistently. CMMI aims for high maturity levels to enable efficient software development. It does this by promoting improvement, governance, and performance measurement. This improves project planning, execution, and monitoring. It reduces technical debt and boosts software quality.
CMMI helps manage technical debt. It shows how to find, assess, and fix inefficiencies in software development and system management. CMMI promotes best practices in project planning and risk management. It also encourages continuous improvement. This minimizes and controls technical debt over time. This results in more sustainable software. It cuts the long-term costs and challenges of technical debt.
CMMI Implementation and Impact on Technical Debt
When organizations adopt CMMI, they prioritize software maintenance, optimizing processes, and managing risks. This leads to cost reduction, improved time-to-market, and enhanced product quality. Integrating CMMI into their processes can help organizations. It can streamline project planning, execution, and monitoring. This will reduce technical debt and ensure successful software delivery.
CMMI can cut technical debt. It promotes better processes and ongoing improvement in software development. CMMI helps teams find and fix issues early. It does this by stressing quality assurance, risk management, and clear workflows. This prevents technical debt from building up. So, organizations can sustain software, cut maintenance costs, and boost efficiency.
CMMI Best Practices for Technical Debt Mitigation
To reduce technical debt, follow these key CMMI best practices: document software, adhere to standards, test rigorously, and ensure strong security. By using these practices in their development cycle, organizations can improve software quality. This will reduce defects and boost product reliability.
Reducing technical debt is vital for long-term software success. CMMI offers best practices to tackle it proactively. CMMI's structured process improvement can help organizations. It can identify technical debt early, prioritize fixes, and allocate resources. This keeps quality high. It cuts costly rework and improves the software lifecycle.
CMMI and Continuous Improvement
CMMI is all about continuous improvement. It urges organizations to assess and enhance their processes. Regular CMMI assessments help organizations find areas to improve. They can then make changes and track progress over time. By optimizing and maturing, firms can stay ahead in the fast software industry.
CMMI (Capability Maturity Model Integration) is a framework. It helps organizations improve by setting clear, structured processes. CMMI helps businesses find inefficiencies by focusing on measurable outcomes. It guides them to make systematic changes for long-term success. This model promotes a culture of constant evaluation and refinement. It keeps organizations competitive and agile in changing markets.
How to obtain CMMI certification?
We are an Education Technology company providing certification training courses to accelerate careers of working professionals worldwide. We impart training through instructor-led classroom workshops, instructor-led live virtual training sessions, and self-paced e-learning courses.
We have successfully conducted training sessions in 108 countries across the globe and enabled thousands of working professionals to enhance the scope of their careers.
Our enterprise training portfolio includes in-demand and globally recognized certification training courses in Project Management, Quality Management, Business Analysis, IT Service Management, Agile and Scrum, Cyber Security, Data Science, and Emerging Technologies. Download our Enterprise Training Catalog from https://www.icertglobal.com/corporate-training-for-enterprises.php and https://www.icertglobal.com/index.php
Popular Courses include:
-
Project Management: PMP, CAPM ,PMI RMP
-
Quality Management: Six Sigma Black Belt ,Lean Six Sigma Green Belt, Lean Management, Minitab,CMMI
-
Business Analysis: CBAP, CCBA, ECBA
-
Agile Training: PMI-ACP , CSM , CSPO
-
Scrum Training: CSM
-
DevOps
-
Program Management: PgMP
-
Cloud Technology: Exin Cloud Computing
-
Citrix Client Adminisration: Citrix Cloud Administration
The 10 top-paying certifications to target in 2024 are:
Conclusion
By using CMMI's complete approach to software development, organizations can tackle technical debt. This lets them deliver high-quality software that meets customers' and industry's standards. CMMI is a vital tool for firms seeking to excel in today's software market.
In conclusion, CMMI is vital for reducing technical debt in software projects. It provides a framework for development, improvement, and quality management. CMMI guidelines and best practices can help organizations. They can optimize processes, reduce risk, and ensure efficient software delivery. CMMI boosts productivity, efficiency, and software performance for organizations. It leads to successful projects and happy stakeholders.
Contact Us For More Information:
Visit :www.icertglobal.comEmail : info@icertglobal.com
Read More
In software development, efficiency, quality, and speed are crucial. Technical debt is extra work. It arises when quick, easy software is chosen over better, but harder, options. It can slow down projects and reduce productivity. CMMI (Capability Maturity Model Integration) helps minimize technical debt. It is key to successful software projects.
What is CMMI? How Does it Work?
CMMI is a set of best practices and standards. They guide organizations in improving their development processes, project management, and quality. It provides guidelines and controls to manage technical debt in software development. CMMI lets organizations assess and adopt the best practices. This optimizes their software engineering, reduces risk, and ensures compliance with industry standards.
How Does CMMI Help Manage Technical Debt?
CMMI helps set maturity levels. They show an organization's ability to deliver quality software consistently. CMMI aims for high maturity levels to enable efficient software development. It does this by promoting improvement, governance, and performance measurement. This improves project planning, execution, and monitoring. It reduces technical debt and boosts software quality.
CMMI helps manage technical debt. It shows how to find, assess, and fix inefficiencies in software development and system management. CMMI promotes best practices in project planning and risk management. It also encourages continuous improvement. This minimizes and controls technical debt over time. This results in more sustainable software. It cuts the long-term costs and challenges of technical debt.
CMMI Implementation and Impact on Technical Debt
When organizations adopt CMMI, they prioritize software maintenance, optimizing processes, and managing risks. This leads to cost reduction, improved time-to-market, and enhanced product quality. Integrating CMMI into their processes can help organizations. It can streamline project planning, execution, and monitoring. This will reduce technical debt and ensure successful software delivery.
CMMI can cut technical debt. It promotes better processes and ongoing improvement in software development. CMMI helps teams find and fix issues early. It does this by stressing quality assurance, risk management, and clear workflows. This prevents technical debt from building up. So, organizations can sustain software, cut maintenance costs, and boost efficiency.
CMMI Best Practices for Technical Debt Mitigation
To reduce technical debt, follow these key CMMI best practices: document software, adhere to standards, test rigorously, and ensure strong security. By using these practices in their development cycle, organizations can improve software quality. This will reduce defects and boost product reliability.
Reducing technical debt is vital for long-term software success. CMMI offers best practices to tackle it proactively. CMMI's structured process improvement can help organizations. It can identify technical debt early, prioritize fixes, and allocate resources. This keeps quality high. It cuts costly rework and improves the software lifecycle.
CMMI and Continuous Improvement
CMMI is all about continuous improvement. It urges organizations to assess and enhance their processes. Regular CMMI assessments help organizations find areas to improve. They can then make changes and track progress over time. By optimizing and maturing, firms can stay ahead in the fast software industry.
CMMI (Capability Maturity Model Integration) is a framework. It helps organizations improve by setting clear, structured processes. CMMI helps businesses find inefficiencies by focusing on measurable outcomes. It guides them to make systematic changes for long-term success. This model promotes a culture of constant evaluation and refinement. It keeps organizations competitive and agile in changing markets.
How to obtain CMMI certification?
We are an Education Technology company providing certification training courses to accelerate careers of working professionals worldwide. We impart training through instructor-led classroom workshops, instructor-led live virtual training sessions, and self-paced e-learning courses.
We have successfully conducted training sessions in 108 countries across the globe and enabled thousands of working professionals to enhance the scope of their careers.
Our enterprise training portfolio includes in-demand and globally recognized certification training courses in Project Management, Quality Management, Business Analysis, IT Service Management, Agile and Scrum, Cyber Security, Data Science, and Emerging Technologies. Download our Enterprise Training Catalog from https://www.icertglobal.com/corporate-training-for-enterprises.php and https://www.icertglobal.com/index.php
Popular Courses include:
-
Project Management: PMP, CAPM ,PMI RMP
-
Quality Management: Six Sigma Black Belt ,Lean Six Sigma Green Belt, Lean Management, Minitab,CMMI
-
Business Analysis: CBAP, CCBA, ECBA
-
Agile Training: PMI-ACP , CSM , CSPO
-
Scrum Training: CSM
-
DevOps
-
Program Management: PgMP
-
Cloud Technology: Exin Cloud Computing
-
Citrix Client Adminisration: Citrix Cloud Administration
The 10 top-paying certifications to target in 2024 are:
Conclusion
By using CMMI's complete approach to software development, organizations can tackle technical debt. This lets them deliver high-quality software that meets customers' and industry's standards. CMMI is a vital tool for firms seeking to excel in today's software market.
In conclusion, CMMI is vital for reducing technical debt in software projects. It provides a framework for development, improvement, and quality management. CMMI guidelines and best practices can help organizations. They can optimize processes, reduce risk, and ensure efficient software delivery. CMMI boosts productivity, efficiency, and software performance for organizations. It leads to successful projects and happy stakeholders.
Contact Us For More Information:
Visit :www.icertglobal.comEmail : info@icertglobal.com
The Future of Lean Six Sigma in the Digital Transformation
In today's fast-changing digital world, Lean Six Sigma is vital. It drives success and fosters a culture of improvement. As businesses adopt digital transformation and Industry 4.0, Lean Six Sigma is more relevant than ever. Let's explore how Lean Six Sigma is shaping quality management in the digital age.
Embracing Technology and Automation
One of the key pillars of Lean Six Sigma is a focus on leveraging technology and automation to drive efficiency and productivity. In the digital age, data analytics and AI have advanced. They help organizations improve decision-making and streamline operations. By merging Lean Six Sigma with new technology, businesses can optimize processes and cut costs.
Organizations must embrace technology and automation. It's key to boosting efficiency and driving innovation. AI and machine learning can help businesses. They can streamline operations, reduce errors, and improve decisions. Also, automation boosts productivity. It lets employees focus on higher-value tasks. This leads to greater job satisfaction and growth for the organization.
Continuous Improvement and Innovation
Lean Six Sigma is founded on the principles of continuous improvement and innovation. In the digital age, organizations must adapt to shifting markets and consumer preferences. Adopting Lean Six Sigma can foster innovation and drive growth. Using data and Lean Six Sigma tools, organizations can find and remove waste. This will boost customer satisfaction and help them beat the competition.
Continuous improvement and innovation are vital to an organization's success. They drive efficiency and adaptability in a fast-changing business world. Organizations can improve processes and find better solutions. They should create a culture that encourages feedback and testing to meet customer needs. Using methods like Lean Six Sigma can streamline operations. They can also promote sustainable growth. This will make innovation a key part of the company's culture.
Enhancing Quality Management
Quality management is at the core of Lean Six Sigma. In the digital age, high-quality standards are vital for business success. Lean Six Sigma practices can help organizations ensure consistent quality. This leads to greater customer loyalty and satisfaction. Lean Six Sigma tools can help businesses fix quality issues in real-time. This will boost their efficiency.
To improve quality management, implement processes. They must ensure products and services meet customer and regulatory standards. Techniques like continuous improvement and employee training are key. So are quality standards, like ISO 9001. They are vital for achieving operational excellence. A culture of quality can boost customer satisfaction. It can also improve efficiency and cut costs.
Maximizing Efficiency and Productivity
Efficiency and productivity are vital for an organization's success. Lean Six Sigma offers a way to achieve operational excellence. Businesses can boost efficiency, cut costs, and improve productivity. They can do this by optimizing processes and eliminating waste. In the digital age, Lean Six Sigma helps organizations. It lets them use tech and data to boost efficiency. It aims for continuous improvement and streamlined operations.
For organizations, it's vital to maximize efficiency and productivity. This helps them achieve their goals while using resources wisely. Teams can use Lean Six Sigma to streamline processes, cut waste, and boost performance. Also, a culture of continuous improvement encourages employees to find and fix inefficiencies. This will drive better results for the organization.
Building a Lean Culture
A Lean culture is vital for success in Lean Six Sigma. In the digital age, organizations must embrace a culture of learning. They need to improve constantly to stay competitive. Applying Lean principles to all parts of the business can create a culture of transparency, accountability, and collaboration. This applies to everyone, from leaders to front-line employees. This Lean culture will drive innovation, empower employees, and grow the business. It will do so sustainably.
A lean culture is key to continuous improvement and excellence. It fosters them in an organization. This culture values employee engagement. Team members should identify waste, suggest improvements, and help solve problems. Applying Lean principles at all levels can help companies. It can create a sustainable, efficient, and responsive environment for customers.
How to obtain LSSYB certification?
We are an Education Technology company providing certification training courses to accelerate careers of working professionals worldwide. We impart training through instructor-led classroom workshops, instructor-led live virtual training sessions, and self-paced e-learning courses.
We have successfully conducted training sessions in 108 countries across the globe and enabled thousands of working professionals to enhance the scope of their careers.
Our enterprise training portfolio includes in-demand and globally recognized certification training courses in Project Management, Quality Management, Business Analysis, IT Service Management, Agile and Scrum, Cyber Security, Data Science, and Emerging Technologies. Download our Enterprise Training Catalog from https://www.icertglobal.com/corporate-training-for-enterprises.php and https://www.icertglobal.com/index.php
Popular Courses include:
-
Project Management: PMP, CAPM ,PMI RMP
-
Quality Management: Six Sigma Black Belt ,Lean Six Sigma Green Belt, Lean Management, Minitab,CMMI
-
Business Analysis: CBAP, CCBA, ECBA
-
Agile Training: PMI-ACP , CSM , CSPO
-
Scrum Training: CSM
-
DevOps
-
Program Management: PgMP
-
Cloud Technology: Exin Cloud Computing
-
Citrix Client Adminisration: Citrix Cloud Administration
The 10 top-paying certifications to target in 2024 are:
Conclusion
In conclusion, the future of Lean Six Sigma is bright. There are many opportunities for organizations to excel in quality and process. By embracing technology and improving continuously, businesses can use Lean Six Sigma. It will boost efficiency and productivity. This will drive innovation and help them outpace competitors. As we enter a digital age, Lean Six Sigma will be key for organizations. It will help them thrive in a fast-changing business landscape.
Contact Us For More Information:
Visit :www.icertglobal.comEmail : info@icertglobal.com
Read More
In today's fast-changing digital world, Lean Six Sigma is vital. It drives success and fosters a culture of improvement. As businesses adopt digital transformation and Industry 4.0, Lean Six Sigma is more relevant than ever. Let's explore how Lean Six Sigma is shaping quality management in the digital age.
Embracing Technology and Automation
One of the key pillars of Lean Six Sigma is a focus on leveraging technology and automation to drive efficiency and productivity. In the digital age, data analytics and AI have advanced. They help organizations improve decision-making and streamline operations. By merging Lean Six Sigma with new technology, businesses can optimize processes and cut costs.
Organizations must embrace technology and automation. It's key to boosting efficiency and driving innovation. AI and machine learning can help businesses. They can streamline operations, reduce errors, and improve decisions. Also, automation boosts productivity. It lets employees focus on higher-value tasks. This leads to greater job satisfaction and growth for the organization.
Continuous Improvement and Innovation
Lean Six Sigma is founded on the principles of continuous improvement and innovation. In the digital age, organizations must adapt to shifting markets and consumer preferences. Adopting Lean Six Sigma can foster innovation and drive growth. Using data and Lean Six Sigma tools, organizations can find and remove waste. This will boost customer satisfaction and help them beat the competition.
Continuous improvement and innovation are vital to an organization's success. They drive efficiency and adaptability in a fast-changing business world. Organizations can improve processes and find better solutions. They should create a culture that encourages feedback and testing to meet customer needs. Using methods like Lean Six Sigma can streamline operations. They can also promote sustainable growth. This will make innovation a key part of the company's culture.
Enhancing Quality Management
Quality management is at the core of Lean Six Sigma. In the digital age, high-quality standards are vital for business success. Lean Six Sigma practices can help organizations ensure consistent quality. This leads to greater customer loyalty and satisfaction. Lean Six Sigma tools can help businesses fix quality issues in real-time. This will boost their efficiency.
To improve quality management, implement processes. They must ensure products and services meet customer and regulatory standards. Techniques like continuous improvement and employee training are key. So are quality standards, like ISO 9001. They are vital for achieving operational excellence. A culture of quality can boost customer satisfaction. It can also improve efficiency and cut costs.
Maximizing Efficiency and Productivity
Efficiency and productivity are vital for an organization's success. Lean Six Sigma offers a way to achieve operational excellence. Businesses can boost efficiency, cut costs, and improve productivity. They can do this by optimizing processes and eliminating waste. In the digital age, Lean Six Sigma helps organizations. It lets them use tech and data to boost efficiency. It aims for continuous improvement and streamlined operations.
For organizations, it's vital to maximize efficiency and productivity. This helps them achieve their goals while using resources wisely. Teams can use Lean Six Sigma to streamline processes, cut waste, and boost performance. Also, a culture of continuous improvement encourages employees to find and fix inefficiencies. This will drive better results for the organization.
Building a Lean Culture
A Lean culture is vital for success in Lean Six Sigma. In the digital age, organizations must embrace a culture of learning. They need to improve constantly to stay competitive. Applying Lean principles to all parts of the business can create a culture of transparency, accountability, and collaboration. This applies to everyone, from leaders to front-line employees. This Lean culture will drive innovation, empower employees, and grow the business. It will do so sustainably.
A lean culture is key to continuous improvement and excellence. It fosters them in an organization. This culture values employee engagement. Team members should identify waste, suggest improvements, and help solve problems. Applying Lean principles at all levels can help companies. It can create a sustainable, efficient, and responsive environment for customers.
How to obtain LSSYB certification?
We are an Education Technology company providing certification training courses to accelerate careers of working professionals worldwide. We impart training through instructor-led classroom workshops, instructor-led live virtual training sessions, and self-paced e-learning courses.
We have successfully conducted training sessions in 108 countries across the globe and enabled thousands of working professionals to enhance the scope of their careers.
Our enterprise training portfolio includes in-demand and globally recognized certification training courses in Project Management, Quality Management, Business Analysis, IT Service Management, Agile and Scrum, Cyber Security, Data Science, and Emerging Technologies. Download our Enterprise Training Catalog from https://www.icertglobal.com/corporate-training-for-enterprises.php and https://www.icertglobal.com/index.php
Popular Courses include:
-
Project Management: PMP, CAPM ,PMI RMP
-
Quality Management: Six Sigma Black Belt ,Lean Six Sigma Green Belt, Lean Management, Minitab,CMMI
-
Business Analysis: CBAP, CCBA, ECBA
-
Agile Training: PMI-ACP , CSM , CSPO
-
Scrum Training: CSM
-
DevOps
-
Program Management: PgMP
-
Cloud Technology: Exin Cloud Computing
-
Citrix Client Adminisration: Citrix Cloud Administration
The 10 top-paying certifications to target in 2024 are:
Conclusion
In conclusion, the future of Lean Six Sigma is bright. There are many opportunities for organizations to excel in quality and process. By embracing technology and improving continuously, businesses can use Lean Six Sigma. It will boost efficiency and productivity. This will drive innovation and help them outpace competitors. As we enter a digital age, Lean Six Sigma will be key for organizations. It will help them thrive in a fast-changing business landscape.
Contact Us For More Information:
Visit :www.icertglobal.comEmail : info@icertglobal.com
Mastering Automated Data Analysis Workflows with Minitab
Do you want to speed up your data analysis and make your stats work more efficient? Minitab is a powerful software tool. It automates many data analysis tasks. This article will explore how automating data analysis in Minitab can help you. It can save you time, reduce manual work, and improve your analysis.
The Benefits of Minitab Data Analysis Automation
Minitab automates data analysis. It helps businesses by streamlining repetitive tasks. This reduces human error and increases efficiency. It lets users quickly process large datasets. This provides faster insights and enables timely decisions. Also, automation in Minitab improves consistency in statistical analysis. It ensures accuracy and reliability across projects.
Automating data analysis in Minitab has many benefits. It can greatly improve your data analysis workflows. By leveraging automation techniques in Minitab, you can:
-
Automate data entry, cleaning, manipulation, and transformation. This will cut tedious work and free up time for more strategic analysis.
-
Improve Data Accuracy: Use Minitab's automation tools. They can reduce errors and ensure your analysis is based on reliable data.
-
Increase Efficiency: Automating repetitive tasks can greatly improve your data analysis. This includes data processing, statistical tests, and analyses. These are regression, cluster, and time series. It also includes data mining.
-
Minitab automation can improve your data analysis. It can find trends, patterns, correlations, and outliers in your data. It will also give you deeper insights.
-
Automating statistical processes in Minitab can help you. It will speed up your analysis and boost your skills. You'll make data-driven decisions faster.
Using Minitab Data Analysis Automation Tools
Learn how Minitab's tools can automate data analysis. They can greatly improve your workflow and efficiency. Automate tasks like data cleaning and reporting. Then, you can focus on finding insights and making decisions. Explore Minitab's features and techniques to improve your data analysis. They will give you faster, more accurate results.
Minitab has many automation tools. They can simplify your data analysis workflows. Some of the key automation features in Minitab include:
-
Automated Reporting: Generate automated reports to communicate your data analysis results more efficiently.
-
Data Analysis Insights: Use your analysis to make better business decisions.
-
Data Analysis Trends: Identify and analyze data trends to better understand your data.
-
Data Analysis Expertise: Use automated tools to sharpen your data analysis and stats skills.
How to Implement Minitab Data Analysis Automation Techniques
In today's fast-paced data world, automating Minitab's data analysis can save time and improve accuracy. This blog explores key automation techniques. It focuses on Minitab's macros and scripts to streamline repetitive tasks and analyses. These strategies can help organizations find insights. They will save time and cut human error in data-driven decisions.
To get started with automating data analysis in Minitab, follow these simple steps:
-
Set Objectives: Define your goals for data analysis. Identify tasks to automate to achieve them.
-
Choose Automation Tools: Explore the automation features in Minitab and select the tools that best meet your needs.
-
Automate your data analysis. This will improve accuracy and speed up statistical analysis.
-
Monitor Results: Track your automated data analysis's performance. Find areas to improve, and adjust to boost efficiency. Use Minitab's automation features to simplify your data analysis. Follow these steps. This will boost efficiency and help you gain insights from your data.
How to obtain Minitab certification?
We are an Education Technology company providing certification training courses to accelerate careers of working professionals worldwide. We impart training through instructor-led classroom workshops, instructor-led live virtual training sessions, and self-paced e-learning courses.
We have successfully conducted training sessions in 108 countries across the globe and enabled thousands of working professionals to enhance the scope of their careers.
Our enterprise training portfolio includes in-demand and globally recognized certification training courses in Project Management, Quality Management, Business Analysis, IT Service Management, Agile and Scrum, Cyber Security, Data Science, and Emerging Technologies. Download our Enterprise Training Catalog from https://www.icertglobal.com/corporate-training-for-enterprises.php and https://www.icertglobal.com/index.php
Popular Courses include:
-
Project Management: PMP, CAPM ,PMI RMP
-
Quality Management: Six Sigma Black Belt ,Lean Six Sigma Green Belt, Lean Management, Minitab,CMMI
-
Business Analysis: CBAP, CCBA, ECBA
-
Agile Training: PMI-ACP , CSM , CSPO
-
Scrum Training: CSM
-
DevOps
-
Program Management: PgMP
-
Cloud Technology: Exin Cloud Computing
-
Citrix Client Adminisration: Citrix Cloud Administration
The 10 top-paying certifications to target in 2024 are:
Conclusion
In conclusion, automating data analysis in Minitab can improve your work. It will make your statistical tasks faster and more accurate. It will also help you make better, data-driven business decisions. Explore Minitab's automation tools today. They'll optimize your data analysis and unlock your data's full potential.
Contact Us For More Information:
Visit :www.icertglobal.comEmail : info@icertglobal.com
Read More
Do you want to speed up your data analysis and make your stats work more efficient? Minitab is a powerful software tool. It automates many data analysis tasks. This article will explore how automating data analysis in Minitab can help you. It can save you time, reduce manual work, and improve your analysis.
The Benefits of Minitab Data Analysis Automation
Minitab automates data analysis. It helps businesses by streamlining repetitive tasks. This reduces human error and increases efficiency. It lets users quickly process large datasets. This provides faster insights and enables timely decisions. Also, automation in Minitab improves consistency in statistical analysis. It ensures accuracy and reliability across projects.
Automating data analysis in Minitab has many benefits. It can greatly improve your data analysis workflows. By leveraging automation techniques in Minitab, you can:
-
Automate data entry, cleaning, manipulation, and transformation. This will cut tedious work and free up time for more strategic analysis.
-
Improve Data Accuracy: Use Minitab's automation tools. They can reduce errors and ensure your analysis is based on reliable data.
-
Increase Efficiency: Automating repetitive tasks can greatly improve your data analysis. This includes data processing, statistical tests, and analyses. These are regression, cluster, and time series. It also includes data mining.
-
Minitab automation can improve your data analysis. It can find trends, patterns, correlations, and outliers in your data. It will also give you deeper insights.
-
Automating statistical processes in Minitab can help you. It will speed up your analysis and boost your skills. You'll make data-driven decisions faster.
Using Minitab Data Analysis Automation Tools
Learn how Minitab's tools can automate data analysis. They can greatly improve your workflow and efficiency. Automate tasks like data cleaning and reporting. Then, you can focus on finding insights and making decisions. Explore Minitab's features and techniques to improve your data analysis. They will give you faster, more accurate results.
Minitab has many automation tools. They can simplify your data analysis workflows. Some of the key automation features in Minitab include:
-
Automated Reporting: Generate automated reports to communicate your data analysis results more efficiently.
-
Data Analysis Insights: Use your analysis to make better business decisions.
-
Data Analysis Trends: Identify and analyze data trends to better understand your data.
-
Data Analysis Expertise: Use automated tools to sharpen your data analysis and stats skills.
How to Implement Minitab Data Analysis Automation Techniques
In today's fast-paced data world, automating Minitab's data analysis can save time and improve accuracy. This blog explores key automation techniques. It focuses on Minitab's macros and scripts to streamline repetitive tasks and analyses. These strategies can help organizations find insights. They will save time and cut human error in data-driven decisions.
To get started with automating data analysis in Minitab, follow these simple steps:
-
Set Objectives: Define your goals for data analysis. Identify tasks to automate to achieve them.
-
Choose Automation Tools: Explore the automation features in Minitab and select the tools that best meet your needs.
-
Automate your data analysis. This will improve accuracy and speed up statistical analysis.
-
Monitor Results: Track your automated data analysis's performance. Find areas to improve, and adjust to boost efficiency. Use Minitab's automation features to simplify your data analysis. Follow these steps. This will boost efficiency and help you gain insights from your data.
How to obtain Minitab certification?
We are an Education Technology company providing certification training courses to accelerate careers of working professionals worldwide. We impart training through instructor-led classroom workshops, instructor-led live virtual training sessions, and self-paced e-learning courses.
We have successfully conducted training sessions in 108 countries across the globe and enabled thousands of working professionals to enhance the scope of their careers.
Our enterprise training portfolio includes in-demand and globally recognized certification training courses in Project Management, Quality Management, Business Analysis, IT Service Management, Agile and Scrum, Cyber Security, Data Science, and Emerging Technologies. Download our Enterprise Training Catalog from https://www.icertglobal.com/corporate-training-for-enterprises.php and https://www.icertglobal.com/index.php
Popular Courses include:
-
Project Management: PMP, CAPM ,PMI RMP
-
Quality Management: Six Sigma Black Belt ,Lean Six Sigma Green Belt, Lean Management, Minitab,CMMI
-
Business Analysis: CBAP, CCBA, ECBA
-
Agile Training: PMI-ACP , CSM , CSPO
-
Scrum Training: CSM
-
DevOps
-
Program Management: PgMP
-
Cloud Technology: Exin Cloud Computing
-
Citrix Client Adminisration: Citrix Cloud Administration
The 10 top-paying certifications to target in 2024 are:
Conclusion
In conclusion, automating data analysis in Minitab can improve your work. It will make your statistical tasks faster and more accurate. It will also help you make better, data-driven business decisions. Explore Minitab's automation tools today. They'll optimize your data analysis and unlock your data's full potential.
Contact Us For More Information:
Visit :www.icertglobal.comEmail : info@icertglobal.com
Cutting-Edge Innovations in Six Sigma Training & Development
In today's fast-paced business world, you must innovate to stay ahead of the competition. Organizations are always trying to improve their training programs, especially in Six Sigma. Six Sigma is a data-driven method. It aims to improve efficiency and reduce defects in processes. As technology and best practices evolve, so do the methods for training in Six Sigma. Let's explore the latest innovations in Six Sigma training. They are revolutionizing how organizations approach process improvement.
Online Six Sigma Courses
A major advancement in Six Sigma training is the shift to online courses. Remote work and digital learning have risen. Now, organizations can offer high-quality, global Six Sigma training to employees. Online courses are flexible and accessible. They let people learn at their own pace and schedule.
Lean Six Sigma Training Methods
Lean Six Sigma combines Six Sigma and Lean methods. It is a powerful way to improve processes. Lean-based training methods aim to eliminate waste and maximize value. They lead to more efficient, streamlined processes. Integrating Lean practices into Six Sigma training can yield even better results.
Modern Six Sigma Tools
New technology has created tools and software that improve Six Sigma training. These tools can better analyze data, track progress, and find areas for improvement. These tools can help organizations improve and speed up training.
Best Practices in Six Sigma Training
As Six Sigma evolves, best practices in training are being updated. Organizations are using new methods to train employees. They offer interactive workshops and customized solutions. This ensures employees have the knowledge and skills to succeed. Best practices in Six Sigma training can help organizations. They can maximize the impact of process improvement initiatives.
When implementing Six Sigma training, some best practices can boost its effectiveness. First, it's crucial to get a strong commitment from top leaders. Without their full support, the initiative may fail. Additionally, training is essential. But, it must be paired with ongoing project work. This will apply the learned concepts. It will ensure that process improvements yield results.
Interactive Six Sigma Workshops
Interactive workshops offer a hands-on, engaging learning experience. They reinforce key concepts. Using activities, simulations, and real-world case studies can make training more engaging. Organizations should use them. Interactive workshops help participants apply Six Sigma principles. This leads to a deeper understanding of the methodology.
Interactive Six Sigma Workshops offer a dynamic learning environment. Participants engage in hands-on activities to apply Six Sigma methods in real-time scenarios. These workshops use simulations, discussions, and exercises to boost understanding. They help attendees grasp complex concepts. These workshops foster collaboration. They build skills and promote a culture of continuous improvement.
Agile Six Sigma Training
Agile methodologies focus on adaptability, collaboration, and iterative improvement. Agile principles in Six Sigma training can help. They can make process improvements respond to changing business needs. Agile Six Sigma training stresses teamwork and fast feedback. It helps firms improve continuously in a fast-paced world.
Agile Six Sigma training merges Agile's flexible approach with Six Sigma's structure. It aims to improve processes and project management. This training gives participants skills for data-driven decision-making. They must also respond to changing customer needs. This will improve business outcomes. Agile Six Sigma boosts efficiency, cuts waste, and improves quality. So, it is a good investment for teams in a fast-paced world.
Customized Six Sigma Training Solutions
Every organization has unique challenges and goals. So, customized training is in demand. Organizations can ensure employees get the best training. They should tailor programs to specific needs and goals. Custom Six Sigma training helps organizations fix specific issues and improve.
Customized Six Sigma training solutions meet organizations' specific needs. They ensure teams gain the skills to improve processes. These solutions improve engagement and retention. They do this by aligning training with industry and organizational goals. Companies that use customized training often see big gains. They get higher productivity, better quality, and a stronger culture of improvement.
How to obtain Six Sigma Black Belt certification?
We are an Education Technology company providing certification training courses to accelerate careers of working professionals worldwide. We impart training through instructor-led classroom workshops, instructor-led live virtual training sessions, and self-paced e-learning courses.
We have successfully conducted training sessions in 108 countries across the globe and enabled thousands of working professionals to enhance the scope of their careers.
Our enterprise training portfolio includes in-demand and globally recognized certification training courses in Project Management, Quality Management, Business Analysis, IT Service Management, Agile and Scrum, Cyber Security, Data Science, and Emerging Technologies. Download our Enterprise Training Catalog from https://www.icertglobal.com/corporate-training-for-enterprises.php and https://www.icertglobal.com/index.php
Popular Courses include:
-
Project Management: PMP, CAPM ,PMI RMP
-
Quality Management: Six Sigma Black Belt ,Lean Six Sigma Green Belt, Lean Management, Minitab,CMMI
-
Business Analysis: CBAP, CCBA, ECBA
-
Agile Training: PMI-ACP , CSM , CSPO
-
Scrum Training: CSM
-
DevOps
-
Program Management: PgMP
-
Cloud Technology: Exin Cloud Computing
-
Citrix Client Adminisration: Citrix Cloud Administration
The 10 top-paying certifications to target in 2024 are:
Conclusion
In conclusion, new ideas in Six Sigma training are shaping process improvement's future. Organizations are using new methods to improve employees' skills. They are adopting online courses, lean methodologies, and modern tools. To succeed in a fast-changing business world, organizations must stay current on the latest trends in Six Sigma training.
Contact Us For More Information:
Visit :www.icertglobal.com Email : info@icertglobal.com
Read More
In today's fast-paced business world, you must innovate to stay ahead of the competition. Organizations are always trying to improve their training programs, especially in Six Sigma. Six Sigma is a data-driven method. It aims to improve efficiency and reduce defects in processes. As technology and best practices evolve, so do the methods for training in Six Sigma. Let's explore the latest innovations in Six Sigma training. They are revolutionizing how organizations approach process improvement.
Online Six Sigma Courses
A major advancement in Six Sigma training is the shift to online courses. Remote work and digital learning have risen. Now, organizations can offer high-quality, global Six Sigma training to employees. Online courses are flexible and accessible. They let people learn at their own pace and schedule.
Lean Six Sigma Training Methods
Lean Six Sigma combines Six Sigma and Lean methods. It is a powerful way to improve processes. Lean-based training methods aim to eliminate waste and maximize value. They lead to more efficient, streamlined processes. Integrating Lean practices into Six Sigma training can yield even better results.
Modern Six Sigma Tools
New technology has created tools and software that improve Six Sigma training. These tools can better analyze data, track progress, and find areas for improvement. These tools can help organizations improve and speed up training.
Best Practices in Six Sigma Training
As Six Sigma evolves, best practices in training are being updated. Organizations are using new methods to train employees. They offer interactive workshops and customized solutions. This ensures employees have the knowledge and skills to succeed. Best practices in Six Sigma training can help organizations. They can maximize the impact of process improvement initiatives.
When implementing Six Sigma training, some best practices can boost its effectiveness. First, it's crucial to get a strong commitment from top leaders. Without their full support, the initiative may fail. Additionally, training is essential. But, it must be paired with ongoing project work. This will apply the learned concepts. It will ensure that process improvements yield results.
Interactive Six Sigma Workshops
Interactive workshops offer a hands-on, engaging learning experience. They reinforce key concepts. Using activities, simulations, and real-world case studies can make training more engaging. Organizations should use them. Interactive workshops help participants apply Six Sigma principles. This leads to a deeper understanding of the methodology.
Interactive Six Sigma Workshops offer a dynamic learning environment. Participants engage in hands-on activities to apply Six Sigma methods in real-time scenarios. These workshops use simulations, discussions, and exercises to boost understanding. They help attendees grasp complex concepts. These workshops foster collaboration. They build skills and promote a culture of continuous improvement.
Agile Six Sigma Training
Agile methodologies focus on adaptability, collaboration, and iterative improvement. Agile principles in Six Sigma training can help. They can make process improvements respond to changing business needs. Agile Six Sigma training stresses teamwork and fast feedback. It helps firms improve continuously in a fast-paced world.
Agile Six Sigma training merges Agile's flexible approach with Six Sigma's structure. It aims to improve processes and project management. This training gives participants skills for data-driven decision-making. They must also respond to changing customer needs. This will improve business outcomes. Agile Six Sigma boosts efficiency, cuts waste, and improves quality. So, it is a good investment for teams in a fast-paced world.
Customized Six Sigma Training Solutions
Every organization has unique challenges and goals. So, customized training is in demand. Organizations can ensure employees get the best training. They should tailor programs to specific needs and goals. Custom Six Sigma training helps organizations fix specific issues and improve.
Customized Six Sigma training solutions meet organizations' specific needs. They ensure teams gain the skills to improve processes. These solutions improve engagement and retention. They do this by aligning training with industry and organizational goals. Companies that use customized training often see big gains. They get higher productivity, better quality, and a stronger culture of improvement.
How to obtain Six Sigma Black Belt certification?
We are an Education Technology company providing certification training courses to accelerate careers of working professionals worldwide. We impart training through instructor-led classroom workshops, instructor-led live virtual training sessions, and self-paced e-learning courses.
We have successfully conducted training sessions in 108 countries across the globe and enabled thousands of working professionals to enhance the scope of their careers.
Our enterprise training portfolio includes in-demand and globally recognized certification training courses in Project Management, Quality Management, Business Analysis, IT Service Management, Agile and Scrum, Cyber Security, Data Science, and Emerging Technologies. Download our Enterprise Training Catalog from https://www.icertglobal.com/corporate-training-for-enterprises.php and https://www.icertglobal.com/index.php
Popular Courses include:
-
Project Management: PMP, CAPM ,PMI RMP
-
Quality Management: Six Sigma Black Belt ,Lean Six Sigma Green Belt, Lean Management, Minitab,CMMI
-
Business Analysis: CBAP, CCBA, ECBA
-
Agile Training: PMI-ACP , CSM , CSPO
-
Scrum Training: CSM
-
DevOps
-
Program Management: PgMP
-
Cloud Technology: Exin Cloud Computing
-
Citrix Client Adminisration: Citrix Cloud Administration
The 10 top-paying certifications to target in 2024 are:
Conclusion
In conclusion, new ideas in Six Sigma training are shaping process improvement's future. Organizations are using new methods to improve employees' skills. They are adopting online courses, lean methodologies, and modern tools. To succeed in a fast-changing business world, organizations must stay current on the latest trends in Six Sigma training.
Contact Us For More Information:
Visit :www.icertglobal.com Email : info@icertglobal.com
Minitab Macros: Automate Your Data Analysis Effortlessly
In the era of big data, organizations are overwhelmed with vast amounts of information. So, data analysis is now more critical than ever. Minitab is powerful statistical software. It has tools to help users analyze data. Of these tools, macros are the best. They automate repetitive tasks and improve efficiency. Macros can help analysts. They can streamline workflows, reduce errors, and ensure consistency in data analysis. This article covers Minitab macros. It covers their benefits, how to create them, common uses, and best practices for effective use.
Understanding Minitab Macros
Minitab macros are scripts that automate a sequence of commands in the software. Users can create these macros using Minitab's macro language. It allows scripts to run tasks automatically, without manual input. This feature helps with tasks that need repeated execution. For example, it can run the same analysis on different datasets. Or, it can apply the same settings across many projects.
Key Features of Minitab Macros:
- Automation: Streamline repetitive tasks to boost efficiency and minimize mistakes.
- Reusability: Once created, macros can be reused across different projects, enhancing efficiency.
- Customization: Users can customize macros for specific analyses. This allows for tailored workflows.
Creating Minitab macros
Creating a macro in Minitab involves a few straightforward steps. Users must learn the macro syntax and commands to write their scripts. Generally, the procedure involves the following steps:
Step-by-Step Process:
- Open the Minitab Macro Editor: Access the macro editor by selecting “File” > “New” > “Macro.”
- Write the Macro Script: Use Minitab's macro commands to define the macro's actions. This might include commands for data manipulation, statistical analysis, or generating reports.
- Save the Macro: After the script is complete, save the macro. Choose a name that clearly reflects its function.
- Run the macro: Use the Minitab interface to run the macro. It will perform the automated tasks.
Example of a Simple Macro:
plaintext
- This example reads data from a CSV file. It describes a column, does regression analysis, and saves the results.
Common Applications of Minitab Macros
Minitab macros can be applied in various scenarios to enhance data analysis processes. Some common applications include:
- Repeated analysis : For analysts who need to run the same tests on multiple datasets, macros can automate this. They streamline processes and deliver reliable outcomes.
- Report Generation : Macros can automatically generate reports. They compile analysis results and present them in a user-friendly format. This is particularly useful for stakeholders who require regular updates on project progress.
- Data Cleaning and Preparation : Before analysis, data often requires cleaning and preparation. Macros can automate preprocessing steps. This includes removing outliers, filling in missing values, and transforming variables.
- Customized Analyses : For organizations with unique analytical needs, macros can be tailored. They can perform specific analyses that align with business goals. This ensures the right insights are generated.
- Batch Processing : Macros enable batch processing of analyses on large datasets. They let users efficiently apply the same methods across many datasets.
Best Practices for Using Minitab Macros
To get the most from Minitab macros, users should follow some best practices.
- Keep It Simple : While Minitab allows for complex macros, simplicity should be prioritized. Simple, well-documented macros are easier to understand and maintain. This reduces errors.
- Document your code : Including comments within the macro code can greatly aid in understanding its functionality. This is crucial for users who may return to the code later. It's also important for those who share macros with colleagues.
- Test thoroughly : Before using a macro, test it. It must perform as expected. This includes testing on different datasets. It is to confirm that the macro works across various scenarios.
- Regular Updates : As data analysis needs evolve, so should the macros. Regularly review and update the macros. This keeps them effective for current tasks.
- Leverage Community Resources : The Minitab community has many resources. It includes forums, tutorials, and example macros. These resources can offer insights. They can help users improve their macro-writing skills.
How to obtain MiniTab certification?
We are an Education Technology company providing certification training courses to accelerate careers of working professionals worldwide. We impart training through instructor-led classroom workshops, instructor-led live virtual training sessions, and self-paced e-learning courses.
We have successfully conducted training sessions in 108 countries across the globe and enabled thousands of working professionals to enhance the scope of their careers.
Our enterprise training portfolio includes in-demand and globally recognized certification training courses in Project Management, Quality Management, Business Analysis, IT Service Management, Agile and Scrum, Cyber Security, Data Science, and Emerging Technologies. Download our Enterprise Training Catalog from https://www.icertglobal.com/corporate-training-for-enterprises.php and https://www.icertglobal.com/index.php
Popular Courses include:
- Project Management: PMP, CAPM ,PMI RMP
- Quality Management: Six Sigma Black Belt ,Lean Six Sigma Green Belt, Lean Management, Minitab,CMMI
- Business Analysis: CBAP, CCBA, ECBA
- Agile Training: PMI-ACP , CSM , CSPO
- Scrum Training: CSM
- DevOps
- Program Management: PgMP
- Cloud Technology: Exin Cloud Computing
- Citrix Client Adminisration: Citrix Cloud Administration
The 10 top-paying certifications to target in 2024 are:
- Certified Information Systems Security Professional® (CISSP)
- AWS Certified Solutions Architect
- Google Certified Professional Cloud Architect
- Big Data Certification
- Data Science Certification
- Certified In Risk And Information Systems Control (CRISC)
- Certified Information Security Manager(CISM)
- Project Management Professional (PMP)® Certification
- Certified Ethical Hacker (CEH)
- Certified Scrum Master (CSM)
Conclusion
Minitab macros are a powerful tool for automating data analysis. They help users streamline repetitive tasks, improve accuracy, and boost productivity. By learning to create and use macros, analysts can automate tasks. This lets them focus on extracting insights from their data, not on manual work. As organizations rely more on data for decisions, Minitab macros can help. They can improve analytical workflows. It lets teams respond quickly to business challenges and opportunities. Whether you're a seasoned Minitab user or just starting, use macros in your data analysis. It's a smart way to boost efficiency and effectiveness.
Contact Us :
Contact Us For More Information:
Visit :www.icertglobal.com Email : info@icertglobal.com
Read More
In the era of big data, organizations are overwhelmed with vast amounts of information. So, data analysis is now more critical than ever. Minitab is powerful statistical software. It has tools to help users analyze data. Of these tools, macros are the best. They automate repetitive tasks and improve efficiency. Macros can help analysts. They can streamline workflows, reduce errors, and ensure consistency in data analysis. This article covers Minitab macros. It covers their benefits, how to create them, common uses, and best practices for effective use.
Understanding Minitab Macros
Minitab macros are scripts that automate a sequence of commands in the software. Users can create these macros using Minitab's macro language. It allows scripts to run tasks automatically, without manual input. This feature helps with tasks that need repeated execution. For example, it can run the same analysis on different datasets. Or, it can apply the same settings across many projects.
Key Features of Minitab Macros:
- Automation: Streamline repetitive tasks to boost efficiency and minimize mistakes.
- Reusability: Once created, macros can be reused across different projects, enhancing efficiency.
- Customization: Users can customize macros for specific analyses. This allows for tailored workflows.
Creating Minitab macros
Creating a macro in Minitab involves a few straightforward steps. Users must learn the macro syntax and commands to write their scripts. Generally, the procedure involves the following steps:
Step-by-Step Process:
- Open the Minitab Macro Editor: Access the macro editor by selecting “File” > “New” > “Macro.”
- Write the Macro Script: Use Minitab's macro commands to define the macro's actions. This might include commands for data manipulation, statistical analysis, or generating reports.
- Save the Macro: After the script is complete, save the macro. Choose a name that clearly reflects its function.
- Run the macro: Use the Minitab interface to run the macro. It will perform the automated tasks.
Example of a Simple Macro:
plaintext
- This example reads data from a CSV file. It describes a column, does regression analysis, and saves the results.
Common Applications of Minitab Macros
Minitab macros can be applied in various scenarios to enhance data analysis processes. Some common applications include:
- Repeated analysis : For analysts who need to run the same tests on multiple datasets, macros can automate this. They streamline processes and deliver reliable outcomes.
- Report Generation : Macros can automatically generate reports. They compile analysis results and present them in a user-friendly format. This is particularly useful for stakeholders who require regular updates on project progress.
- Data Cleaning and Preparation : Before analysis, data often requires cleaning and preparation. Macros can automate preprocessing steps. This includes removing outliers, filling in missing values, and transforming variables.
- Customized Analyses : For organizations with unique analytical needs, macros can be tailored. They can perform specific analyses that align with business goals. This ensures the right insights are generated.
- Batch Processing : Macros enable batch processing of analyses on large datasets. They let users efficiently apply the same methods across many datasets.
Best Practices for Using Minitab Macros
To get the most from Minitab macros, users should follow some best practices.
- Keep It Simple : While Minitab allows for complex macros, simplicity should be prioritized. Simple, well-documented macros are easier to understand and maintain. This reduces errors.
- Document your code : Including comments within the macro code can greatly aid in understanding its functionality. This is crucial for users who may return to the code later. It's also important for those who share macros with colleagues.
- Test thoroughly : Before using a macro, test it. It must perform as expected. This includes testing on different datasets. It is to confirm that the macro works across various scenarios.
- Regular Updates : As data analysis needs evolve, so should the macros. Regularly review and update the macros. This keeps them effective for current tasks.
- Leverage Community Resources : The Minitab community has many resources. It includes forums, tutorials, and example macros. These resources can offer insights. They can help users improve their macro-writing skills.
How to obtain MiniTab certification?
We are an Education Technology company providing certification training courses to accelerate careers of working professionals worldwide. We impart training through instructor-led classroom workshops, instructor-led live virtual training sessions, and self-paced e-learning courses.
We have successfully conducted training sessions in 108 countries across the globe and enabled thousands of working professionals to enhance the scope of their careers.
Our enterprise training portfolio includes in-demand and globally recognized certification training courses in Project Management, Quality Management, Business Analysis, IT Service Management, Agile and Scrum, Cyber Security, Data Science, and Emerging Technologies. Download our Enterprise Training Catalog from https://www.icertglobal.com/corporate-training-for-enterprises.php and https://www.icertglobal.com/index.php
Popular Courses include:
- Project Management: PMP, CAPM ,PMI RMP
- Quality Management: Six Sigma Black Belt ,Lean Six Sigma Green Belt, Lean Management, Minitab,CMMI
- Business Analysis: CBAP, CCBA, ECBA
- Agile Training: PMI-ACP , CSM , CSPO
- Scrum Training: CSM
- DevOps
- Program Management: PgMP
- Cloud Technology: Exin Cloud Computing
- Citrix Client Adminisration: Citrix Cloud Administration
The 10 top-paying certifications to target in 2024 are:
- Certified Information Systems Security Professional® (CISSP)
- AWS Certified Solutions Architect
- Google Certified Professional Cloud Architect
- Big Data Certification
- Data Science Certification
- Certified In Risk And Information Systems Control (CRISC)
- Certified Information Security Manager(CISM)
- Project Management Professional (PMP)® Certification
- Certified Ethical Hacker (CEH)
- Certified Scrum Master (CSM)
Conclusion
Minitab macros are a powerful tool for automating data analysis. They help users streamline repetitive tasks, improve accuracy, and boost productivity. By learning to create and use macros, analysts can automate tasks. This lets them focus on extracting insights from their data, not on manual work. As organizations rely more on data for decisions, Minitab macros can help. They can improve analytical workflows. It lets teams respond quickly to business challenges and opportunities. Whether you're a seasoned Minitab user or just starting, use macros in your data analysis. It's a smart way to boost efficiency and effectiveness.
Contact Us :
Contact Us For More Information:
Visit :www.icertglobal.com Email : info@icertglobal.com
Exploring Minitab New Methodologies for Proportion Testing
In the world of statistics and data analysis, Minitab has long been a trusted name. Its powerful analytical tools have helped professionals use data to make decisions. New methods for proportion testing have been released. Minitab has again proven its commitment to quality control and process improvement. It provides cutting-edge solutions. Let's dive into the exciting new features of Minitab for proportion testing.
What Are Proportion Testing Methodologies?
Proportion testing methodologies are statistical techniques. They analyze data where the goal is to find the proportion of a sample that meets a specific criterion. These methodologies are particularly useful in quality assurance, process optimization, and decision-making. By examining proportions, professionals can gain insights. They can assess process effectiveness and find areas for improvement. They can then make confident, data-driven decisions.
How Can Minitab’s New Methodologies Benefit You?
Minitab's new proportion testing methods help professionals in all industries. Minitab's latest features aim to improve data analysis. They include better data visualization, analytical tools, and statistical analysis. They should help users find actionable insights. Using these methods in your workflow can improve your work. You can make more accurate calculations and stronger hypotheses. You can also check your results' significance easily.
Minitab's new methods improve statistical analysis. They provide more accurate and reliable estimates. This is especially true in single population proportion testing. It can greatly enhance decision-making. These advancements let users interpret data faster. They can quickly find trends and insights. These methods can boost quality control and efficiency. So, Minitab is vital for data-driven businesses.
New Features and Analytical Tools Minitab's new methods for testing proportions are a key highlight. They offer users a wider range of statistical methods. Minitab has tools for all your analysis needs. They cover confidence intervals, hypothesis testing, decision-making, and data interpretation. If you are researching, analyzing sample sizes, or solving problems, try Minitab's new features. They can help. They provide the flexibility and functionality you need to succeed.
Minitab has added new features and tools. They aim to improve user experience and data analysis. The latest version has new visualization tools and automated reports. It also has better stats functions. They speed up analysis and improve decision-making. These tools help users tackle complex data challenges. They can now gain deeper insights from their analyses.
Practical Applications and Real-world Case Studies
Let's use a real-world example to show Minitab's new proportion testing methods. You are a quality control expert. Your task is to evaluate a new manufacturing process. Use Minitab's statistical software to analyze the data. You can compare proportions and make informed decisions about the process' performance. Minitab has a user-friendly interface and powerful tools. You can analyze ratios, test hypotheses, and create reports to support your findings.
Minitab has proven effective in many industries. It is especially good for quality control and process improvement. Its practical applications have shown this. A manufacturer was studied. It found that Minitab's SPC tools greatly reduced defects and improved product quality. Also, healthcare providers used Minitab to analyze patient data. This improved efficiency and patient outcomes.
Enhancing Your Data-driven Decisions
In today's fast-paced world, data-driven decisions are key to success. Minitab's new proportion testing methods can boost your analysis. They can help you validate hypotheses and find trends in your data. Use Minitab's software to optimize your processes. It will improve efficiency and drive continuous improvement across your organization. Minitab's user-friendly interface and advanced features can help you. They can aid you, whether you're a seasoned statistician or a novice analyst. Use Minitab to achieve your data-driven goals.
In today's data-driven world, businesses must use data to improve decisions. It's key to success. Using tools like Minitab can streamline this. They provide powerful stats and visuals to find trends and make better choices.
Using these insights, organizations can boost efficiency. They can also foster a culture of continuous improvement and innovation.
How to obtain Minitab certification?
We are an Education Technology company providing certification training courses to accelerate careers of working professionals worldwide. We impart training through instructor-led classroom workshops, instructor-led live virtual training sessions, and self-paced e-learning courses.
We have successfully conducted training sessions in 108 countries across the globe and enabled thousands of working professionals to enhance the scope of their careers.
Our enterprise training portfolio includes in-demand and globally recognized certification training courses in Project Management, Quality Management, Business Analysis, IT Service Management, Agile and Scrum, Cyber Security, Data Science, and Emerging Technologies. Download our Enterprise Training Catalog from https://www.icertglobal.com/corporate-training-for-enterprises.php and https://www.icertglobal.com/index.php
Popular Courses include:
-
Project Management: PMP, CAPM ,PMI RMP
-
Quality Management: Six Sigma Black Belt ,Lean Six Sigma Green Belt, Lean Management, Minitab,CMMI
-
Business Analysis: CBAP, CCBA, ECBA
-
Agile Training: PMI-ACP , CSM , CSPO
-
Scrum Training: CSM
-
DevOps
-
Program Management: PgMP
-
Cloud Technology: Exin Cloud Computing
-
Citrix Client Adminisration: Citrix Cloud Administration
The 10 top-paying certifications to target in 2024 are:
Conclusion
In conclusion, Minitab's new methods for proportion testing offer many benefits. They will help professionals improve their statistical analysis. Minitab's tools can help you. They can streamline data analysis, validate hypotheses, and boost your decision-making. Minitab's new features can help. They can aid your research, quality testing, or process optimization. They provide the reliability and tools you need. They are vital to succeed in today's data-driven world.
Contact Us For More Information:
Visit :www.icertglobal.com Email : info@icertglobal.com
Read More
In the world of statistics and data analysis, Minitab has long been a trusted name. Its powerful analytical tools have helped professionals use data to make decisions. New methods for proportion testing have been released. Minitab has again proven its commitment to quality control and process improvement. It provides cutting-edge solutions. Let's dive into the exciting new features of Minitab for proportion testing.
What Are Proportion Testing Methodologies?
Proportion testing methodologies are statistical techniques. They analyze data where the goal is to find the proportion of a sample that meets a specific criterion. These methodologies are particularly useful in quality assurance, process optimization, and decision-making. By examining proportions, professionals can gain insights. They can assess process effectiveness and find areas for improvement. They can then make confident, data-driven decisions.
How Can Minitab’s New Methodologies Benefit You?
Minitab's new proportion testing methods help professionals in all industries. Minitab's latest features aim to improve data analysis. They include better data visualization, analytical tools, and statistical analysis. They should help users find actionable insights. Using these methods in your workflow can improve your work. You can make more accurate calculations and stronger hypotheses. You can also check your results' significance easily.
Minitab's new methods improve statistical analysis. They provide more accurate and reliable estimates. This is especially true in single population proportion testing. It can greatly enhance decision-making. These advancements let users interpret data faster. They can quickly find trends and insights. These methods can boost quality control and efficiency. So, Minitab is vital for data-driven businesses.
New Features and Analytical Tools Minitab's new methods for testing proportions are a key highlight. They offer users a wider range of statistical methods. Minitab has tools for all your analysis needs. They cover confidence intervals, hypothesis testing, decision-making, and data interpretation. If you are researching, analyzing sample sizes, or solving problems, try Minitab's new features. They can help. They provide the flexibility and functionality you need to succeed.
Minitab has added new features and tools. They aim to improve user experience and data analysis. The latest version has new visualization tools and automated reports. It also has better stats functions. They speed up analysis and improve decision-making. These tools help users tackle complex data challenges. They can now gain deeper insights from their analyses.
Practical Applications and Real-world Case Studies
Let's use a real-world example to show Minitab's new proportion testing methods. You are a quality control expert. Your task is to evaluate a new manufacturing process. Use Minitab's statistical software to analyze the data. You can compare proportions and make informed decisions about the process' performance. Minitab has a user-friendly interface and powerful tools. You can analyze ratios, test hypotheses, and create reports to support your findings.
Minitab has proven effective in many industries. It is especially good for quality control and process improvement. Its practical applications have shown this. A manufacturer was studied. It found that Minitab's SPC tools greatly reduced defects and improved product quality. Also, healthcare providers used Minitab to analyze patient data. This improved efficiency and patient outcomes.
Enhancing Your Data-driven Decisions
In today's fast-paced world, data-driven decisions are key to success. Minitab's new proportion testing methods can boost your analysis. They can help you validate hypotheses and find trends in your data. Use Minitab's software to optimize your processes. It will improve efficiency and drive continuous improvement across your organization. Minitab's user-friendly interface and advanced features can help you. They can aid you, whether you're a seasoned statistician or a novice analyst. Use Minitab to achieve your data-driven goals.
In today's data-driven world, businesses must use data to improve decisions. It's key to success. Using tools like Minitab can streamline this. They provide powerful stats and visuals to find trends and make better choices.
Using these insights, organizations can boost efficiency. They can also foster a culture of continuous improvement and innovation.
How to obtain Minitab certification?
We are an Education Technology company providing certification training courses to accelerate careers of working professionals worldwide. We impart training through instructor-led classroom workshops, instructor-led live virtual training sessions, and self-paced e-learning courses.
We have successfully conducted training sessions in 108 countries across the globe and enabled thousands of working professionals to enhance the scope of their careers.
Our enterprise training portfolio includes in-demand and globally recognized certification training courses in Project Management, Quality Management, Business Analysis, IT Service Management, Agile and Scrum, Cyber Security, Data Science, and Emerging Technologies. Download our Enterprise Training Catalog from https://www.icertglobal.com/corporate-training-for-enterprises.php and https://www.icertglobal.com/index.php
Popular Courses include:
-
Project Management: PMP, CAPM ,PMI RMP
-
Quality Management: Six Sigma Black Belt ,Lean Six Sigma Green Belt, Lean Management, Minitab,CMMI
-
Business Analysis: CBAP, CCBA, ECBA
-
Agile Training: PMI-ACP , CSM , CSPO
-
Scrum Training: CSM
-
DevOps
-
Program Management: PgMP
-
Cloud Technology: Exin Cloud Computing
-
Citrix Client Adminisration: Citrix Cloud Administration
The 10 top-paying certifications to target in 2024 are:
Conclusion
In conclusion, Minitab's new methods for proportion testing offer many benefits. They will help professionals improve their statistical analysis. Minitab's tools can help you. They can streamline data analysis, validate hypotheses, and boost your decision-making. Minitab's new features can help. They can aid your research, quality testing, or process optimization. They provide the reliability and tools you need. They are vital to succeed in today's data-driven world.
Contact Us For More Information:
Visit :www.icertglobal.com Email : info@icertglobal.com
CTFL and the Importance of Testing in DevOps Environments
In today's fast-changing software world, delivering high-quality products is a top priority. It must be done efficiently and consistently. DevOps is a top method. It boosts collaboration between development and operations teams. It aims to automate and streamline processes. This ensures continuous integration and delivery (CI/CD). Testing is key to this workflow. It helps organizations keep their apps secure, high-performing, and reliable. The ISTQB® Certified Tester Foundation Level (CTFL) is a top cert for software testers. It's especially valued in DevOps.
CTFL gives testers a solid base in testing principles and best practices. They can use these in a DevOps framework. It helps teams test quickly in DevOps, while keeping quality. This article will explore three topics. First, the importance of testing in DevOps. Second, the role of CTFL certification in improving testing skills. Third, key sub-topics that define this relationship.
Table Of Contents
- The Role of Testing in DevOps
- CTFL: A Foundation for Effective Testing in DevOps
- Continuous Testing and Automation
- Collaboration and Cross-Functional Teams
- Testing Metrics and Continuous Improvement
- Conclusion
The Role of Testing in DevOps
Testing in DevOps is vital. It ensures software quality while enabling fast deployment. DevOps encourages continuous testing (CT). It means testing early and often in the development process. Automated tests in the CI/CD pipeline let teams catch bugs and performance issues early. It also helps find security vulnerabilities. It reduces the risk of critical failures after deployment. It also promotes a culture of accountability and quality.
DevOps testing differs from traditional methods. It emphasizes automation, collaboration, and continuous feedback. Testers must work closely with developers, product owners, and operations teams. They should align testing with business goals. This team effort speeds up delivery of high-quality software by reducing bottlenecks.
CTFL: A Foundation for Effective Testing in DevOps
The ISTQB®'s Certified Tester Foundation Level (CTFL) certification is well-known. It is a basic certification for new software testers. The curriculum covers core concepts. They are testing fundamentals, test design techniques, and test management principles. All are very relevant in a DevOps environment.
In DevOps, CTFL-certified testers are vital. They ensure testing is a key part of the development process, not an afterthought. CTFL provides testers with the knowledge and skills to:
- Know the value of early testing in the DevOps lifecycle.
- Apply structured testing techniques to ensure coverage and effectiveness.
- Use automated testing tools effectively to support continuous testing.
- Work in cross-functional teams and collaborate with developers to improve testability and efficiency.
A CTFL certification shows competence and a commitment to quality. It's valuable for testers in a fast-paced DevOps environment.
Continuous Testing and Automation
Automation is a cornerstone of DevOps, and testing is no exception. Automated, continuous testing checks code changes as soon as they are made. This reduces the time between development and deployment. Test automation uses scripts, tools, and frameworks. They run tests and check results, without manual work.
CTFL-certified testers can choose and use the right tools for automation. This includes unit, integration, and performance tests. The certification also stresses test design techniques. They ensure maximum coverage and efficiency when automating tests. In a DevOps setting, automation is crucial. It maintains the speed and agility of the development cycle. CTFL testers help by designing effective automated tests. These tests catch defects early and prevent costly rework later.
Key benefits of continuous testing and automation include:
- Faster feedback loops, enabling quicker resolution of defects.
- It reduced manual work. Testers could then focus on exploratory testing.
- Improved test coverage and consistency, leading to higher-quality releases.
Collaboration and Cross-Functional Teams
DevOps thrives on collaboration and breaking down the silos between traditionally isolated teams. In this context, a separate QA department can no longer test alone. Instead, it is in every phase of the development cycle. Developers, operations, and testers work together to ensure quality.
CTFL-certified testers have a structured approach to testing. It helps streamline collaboration in cross-functional teams. Their knowledge of test management helps coordinate testing across development stages. They can also communicate well with non-testers, like developers and business analysts. This ensures quality standards are met without slowing down.
In DevOps, the role of testers expands beyond executing test cases. They often contribute to writing automated tests and defining acceptance criteria. They also work with developers to improve the code's testability. CTFL certification gives testers the skills to work well in this team environment.
Testing Metrics and Continuous Improvement
A core principle of DevOps is continuous improvement. Testing is a key area where metrics can drive better outcomes. Metrics like defect density, test coverage, and MTTR show how effective testing is.
CTFL-certified testers know how to use these metrics to optimize testing. Teams can find bottlenecks and redundant tests by analyzing testing metrics. They can also find areas for improvement. In a DevOps environment, the goal is to release high-quality software quickly. So, continuous improvement is essential. Testers are key to this. They must ensure that test strategies evolve as the product and process mature.
Using metrics for continuous improvement helps:
- Optimize testing cycles for faster releases.
- Improve test case quality and relevance.
- Ensure that testing efforts align with business objectives and user needs.
How to obtain CTFL certification?
We are an Education Technology company providing certification training courses to accelerate careers of working professionals worldwide. We impart training through instructor-led classroom workshops, instructor-led live virtual training sessions, and self-paced e-learning courses.
We have successfully conducted training sessions in 108 countries across the globe and enabled thousands of working professionals to enhance the scope of their careers.
Our enterprise training portfolio includes in-demand and globally recognized certification training courses in Project Management, Quality Management, Business Analysis, IT Service Management, Agile and Scrum, Cyber Security, Data Science, and Emerging Technologies. Download our Enterprise Training Catalog from https://www.icertglobal.com/corporate-training-for-enterprises.php and https://www.icertglobal.com/index.php
Popular Courses include:
- Project Management: PMP, CAPM ,PMI RMP
- Quality Management: Six Sigma Black Belt ,Lean Six Sigma Green Belt, Lean Management, Minitab,CMMI
- Business Analysis: CBAP, CCBA, ECBA
- Agile Training: PMI-ACP , CSM , CSPO
- Scrum Training: CSM
- DevOps
- Program Management: PgMP
- Cloud Technology: Exin Cloud Computing
- Citrix Client Adminisration: Citrix Cloud Administration
The 10 top-paying certifications to target in 2024 are:
- Certified Information Systems Security Professional® (CISSP)
- AWS Certified Solutions Architect
- Google Certified Professional Cloud Architect
- Big Data Certification
- Data Science Certification
- Certified In Risk And Information Systems Control (CRISC)
- Certified Information Security Manager(CISM)
- Project Management Professional (PMP)® Certification
- Certified Ethical Hacker (CEH)
- Certified Scrum Master (CSM)
Conclusion
In the fast-paced DevOps world, testing is critical. It ensures software is reliable, secure, and performs well in the real world. The ISTQB® Certified Tester Foundation Level (CTFL) certifies testers in DevOps. It gives them the skills to excel in a world that is collaborative, automated, and metric-driven.
CTFL-certified testers can help DevOps succeed. They know testing principles, continuous testing, automation, collaboration, and improvement. They embed quality in the software development lifecycle. This lets organizations deliver better products faster and more efficiently.
Testing is not just a step in the process. It is an ongoing activity that ensures software reliability and performance. So, it is essential to any successful DevOps strategy.
Contact Us :
Contact Us For More Information:
Visit :www.icertglobal.com Email : info@icertglobal.com
Read More
In today's fast-changing software world, delivering high-quality products is a top priority. It must be done efficiently and consistently. DevOps is a top method. It boosts collaboration between development and operations teams. It aims to automate and streamline processes. This ensures continuous integration and delivery (CI/CD). Testing is key to this workflow. It helps organizations keep their apps secure, high-performing, and reliable. The ISTQB® Certified Tester Foundation Level (CTFL) is a top cert for software testers. It's especially valued in DevOps.
CTFL gives testers a solid base in testing principles and best practices. They can use these in a DevOps framework. It helps teams test quickly in DevOps, while keeping quality. This article will explore three topics. First, the importance of testing in DevOps. Second, the role of CTFL certification in improving testing skills. Third, key sub-topics that define this relationship.
Table Of Contents
- The Role of Testing in DevOps
- CTFL: A Foundation for Effective Testing in DevOps
- Continuous Testing and Automation
- Collaboration and Cross-Functional Teams
- Testing Metrics and Continuous Improvement
- Conclusion
The Role of Testing in DevOps
Testing in DevOps is vital. It ensures software quality while enabling fast deployment. DevOps encourages continuous testing (CT). It means testing early and often in the development process. Automated tests in the CI/CD pipeline let teams catch bugs and performance issues early. It also helps find security vulnerabilities. It reduces the risk of critical failures after deployment. It also promotes a culture of accountability and quality.
DevOps testing differs from traditional methods. It emphasizes automation, collaboration, and continuous feedback. Testers must work closely with developers, product owners, and operations teams. They should align testing with business goals. This team effort speeds up delivery of high-quality software by reducing bottlenecks.
CTFL: A Foundation for Effective Testing in DevOps
The ISTQB®'s Certified Tester Foundation Level (CTFL) certification is well-known. It is a basic certification for new software testers. The curriculum covers core concepts. They are testing fundamentals, test design techniques, and test management principles. All are very relevant in a DevOps environment.
In DevOps, CTFL-certified testers are vital. They ensure testing is a key part of the development process, not an afterthought. CTFL provides testers with the knowledge and skills to:
- Know the value of early testing in the DevOps lifecycle.
- Apply structured testing techniques to ensure coverage and effectiveness.
- Use automated testing tools effectively to support continuous testing.
- Work in cross-functional teams and collaborate with developers to improve testability and efficiency.
A CTFL certification shows competence and a commitment to quality. It's valuable for testers in a fast-paced DevOps environment.
Continuous Testing and Automation
Automation is a cornerstone of DevOps, and testing is no exception. Automated, continuous testing checks code changes as soon as they are made. This reduces the time between development and deployment. Test automation uses scripts, tools, and frameworks. They run tests and check results, without manual work.
CTFL-certified testers can choose and use the right tools for automation. This includes unit, integration, and performance tests. The certification also stresses test design techniques. They ensure maximum coverage and efficiency when automating tests. In a DevOps setting, automation is crucial. It maintains the speed and agility of the development cycle. CTFL testers help by designing effective automated tests. These tests catch defects early and prevent costly rework later.
Key benefits of continuous testing and automation include:
- Faster feedback loops, enabling quicker resolution of defects.
- It reduced manual work. Testers could then focus on exploratory testing.
- Improved test coverage and consistency, leading to higher-quality releases.
Collaboration and Cross-Functional Teams
DevOps thrives on collaboration and breaking down the silos between traditionally isolated teams. In this context, a separate QA department can no longer test alone. Instead, it is in every phase of the development cycle. Developers, operations, and testers work together to ensure quality.
CTFL-certified testers have a structured approach to testing. It helps streamline collaboration in cross-functional teams. Their knowledge of test management helps coordinate testing across development stages. They can also communicate well with non-testers, like developers and business analysts. This ensures quality standards are met without slowing down.
In DevOps, the role of testers expands beyond executing test cases. They often contribute to writing automated tests and defining acceptance criteria. They also work with developers to improve the code's testability. CTFL certification gives testers the skills to work well in this team environment.
Testing Metrics and Continuous Improvement
A core principle of DevOps is continuous improvement. Testing is a key area where metrics can drive better outcomes. Metrics like defect density, test coverage, and MTTR show how effective testing is.
CTFL-certified testers know how to use these metrics to optimize testing. Teams can find bottlenecks and redundant tests by analyzing testing metrics. They can also find areas for improvement. In a DevOps environment, the goal is to release high-quality software quickly. So, continuous improvement is essential. Testers are key to this. They must ensure that test strategies evolve as the product and process mature.
Using metrics for continuous improvement helps:
- Optimize testing cycles for faster releases.
- Improve test case quality and relevance.
- Ensure that testing efforts align with business objectives and user needs.
How to obtain CTFL certification?
We are an Education Technology company providing certification training courses to accelerate careers of working professionals worldwide. We impart training through instructor-led classroom workshops, instructor-led live virtual training sessions, and self-paced e-learning courses.
We have successfully conducted training sessions in 108 countries across the globe and enabled thousands of working professionals to enhance the scope of their careers.
Our enterprise training portfolio includes in-demand and globally recognized certification training courses in Project Management, Quality Management, Business Analysis, IT Service Management, Agile and Scrum, Cyber Security, Data Science, and Emerging Technologies. Download our Enterprise Training Catalog from https://www.icertglobal.com/corporate-training-for-enterprises.php and https://www.icertglobal.com/index.php
Popular Courses include:
- Project Management: PMP, CAPM ,PMI RMP
- Quality Management: Six Sigma Black Belt ,Lean Six Sigma Green Belt, Lean Management, Minitab,CMMI
- Business Analysis: CBAP, CCBA, ECBA
- Agile Training: PMI-ACP , CSM , CSPO
- Scrum Training: CSM
- DevOps
- Program Management: PgMP
- Cloud Technology: Exin Cloud Computing
- Citrix Client Adminisration: Citrix Cloud Administration
The 10 top-paying certifications to target in 2024 are:
- Certified Information Systems Security Professional® (CISSP)
- AWS Certified Solutions Architect
- Google Certified Professional Cloud Architect
- Big Data Certification
- Data Science Certification
- Certified In Risk And Information Systems Control (CRISC)
- Certified Information Security Manager(CISM)
- Project Management Professional (PMP)® Certification
- Certified Ethical Hacker (CEH)
- Certified Scrum Master (CSM)
Conclusion
In the fast-paced DevOps world, testing is critical. It ensures software is reliable, secure, and performs well in the real world. The ISTQB® Certified Tester Foundation Level (CTFL) certifies testers in DevOps. It gives them the skills to excel in a world that is collaborative, automated, and metric-driven.
CTFL-certified testers can help DevOps succeed. They know testing principles, continuous testing, automation, collaboration, and improvement. They embed quality in the software development lifecycle. This lets organizations deliver better products faster and more efficiently.
Testing is not just a step in the process. It is an ongoing activity that ensures software reliability and performance. So, it is essential to any successful DevOps strategy.
Contact Us :
Contact Us For More Information:
Visit :www.icertglobal.com Email : info@icertglobal.com
Globalization and Quality Management Standards Worldwide
In today's globalized world, managing quality standards worldwide is more important than ever. As businesses expand and enter new markets, they must ensure quality. It's key to success. This article will explore globalization's impact on quality management. It will cover the challenges and strategies for managing global standards. It will also discuss best practices for ensuring quality in international operations.\
The Impact of Globalization on Quality Management
Globalization has brought about a dramatic shift in the way businesses operate. With global markets and linked economies, companies must now compete worldwide. So, quality management is now a global concern. It is key to success in the global marketplace.
A major challenge of globalization is ensuring quality across diverse markets. Different countries have different rules and cultures. They affect how people view products and services. To manage global quality standards, one must understand and adapt to local differences. It requires a commitment to the highest standards in every market.
Globalization has greatly affected quality management. It has increased the need for standardized processes in diverse markets. Companies must now follow international quality standards, like ISO 9001. This ensures product consistency and compliance worldwide. As supply chains grow more complex, quality management systems must evolve. They must address cross-border challenges, cultural differences, and varying regulations.
Strategies for Managing Global Standards
To manage quality standards worldwide, businesses must build strong, adaptable quality management systems. They must handle the complexities of the global marketplace. This means using standard processes and procedures. They will ensure consistency and reliability in all operations. A key strategy for managing global standards is a quality assurance program. It should cover all aspects of the business. This includes product development and customer service.
By monitoring and evaluating quality metrics, companies can find areas to improve. They can then take action to prevent quality issues. In addition, businesses must prioritize quality control throughout the supply chain. This means working closely with suppliers and partners. We must meet quality standards at every stage of production. By setting clear guidelines and auditing regularly, companies can reduce quality issues. This will help ensure consistency across all operations.
Managing global standards requires a good grasp of international rules and regional compliance. Companies must standardize processes. But, they must allow flexibility to adapt to local laws and cultures. Regular audits, cross-border communication, and training are vital. They ensure quality and consistency across all operations.
Best Practices for Ensuring Quality Worldwide
To manage global standards, businesses can adopt best practices. They ensure quality at every level. Some of these practices include:
-
Invest in training programs to ensure employees know and follow quality standards.
-
Using quality management tools to improve processes and find issues.
-
Conducting regular quality audits to monitor compliance and identify potential risks
-
Establishing key performance indicators (KPIs) to measure the effectiveness of quality management systems
-
Implementing a culture of continuous improvement to drive innovation and maintain high-quality standards
-
Work with industry partners and regulators. Stay updated on quality trends and rules. By following best practices and committing to quality, businesses can meet global standards. This will help them succeed in a competitive global market.
How to obtain Quality Management certification?
We are an Education Technology company providing certification training courses to accelerate careers of working professionals worldwide. We impart training through instructor-led classroom workshops, instructor-led live virtual training sessions, and self-paced e-learning courses.
We have successfully conducted training sessions in 108 countries across the globe and enabled thousands of working professionals to enhance the scope of their careers.
Our enterprise training portfolio includes in-demand and globally recognized certification training courses in Project Management, Quality Management, Business Analysis, IT Service Management, Agile and Scrum, Cyber Security, Data Science, and Emerging Technologies. Download our Enterprise Training Catalog from https://www.icertglobal.com/corporate-training-for-enterprises.php and https://www.icertglobal.com/index.php
Popular Courses include:
-
Project Management: PMP, CAPM ,PMI RMP
-
Quality Management: Six Sigma Black Belt ,Lean Six Sigma Green Belt, Lean Management, Minitab,CMMI
-
Business Analysis: CBAP, CCBA, ECBA
-
Agile Training: PMI-ACP , CSM , CSPO
-
Scrum Training: CSM
-
DevOps
-
Program Management: PgMP
-
Cloud Technology: Exin Cloud Computing
-
Citrix Client Adminisration: Citrix Cloud Administration
The 10 top-paying certifications to target in 2024 are:
Conclusion
In conclusion, globalization has changed how businesses operate. It requires a more strategic and proactive approach to quality management. Businesses can ensure excellence in operations with strong quality systems and controls. They should also follow best practices for managing global standards. This will ensure consistency and reliability. In today's global economy, managing quality worldwide is a must. It is a competitive advantage that can drive growth, innovation, and success.
Contact Us For More Information:
Visit : www.icertglobal.com Email : info@icertglobal.com
Read More
In today's globalized world, managing quality standards worldwide is more important than ever. As businesses expand and enter new markets, they must ensure quality. It's key to success. This article will explore globalization's impact on quality management. It will cover the challenges and strategies for managing global standards. It will also discuss best practices for ensuring quality in international operations.\
The Impact of Globalization on Quality Management
Globalization has brought about a dramatic shift in the way businesses operate. With global markets and linked economies, companies must now compete worldwide. So, quality management is now a global concern. It is key to success in the global marketplace.
A major challenge of globalization is ensuring quality across diverse markets. Different countries have different rules and cultures. They affect how people view products and services. To manage global quality standards, one must understand and adapt to local differences. It requires a commitment to the highest standards in every market.
Globalization has greatly affected quality management. It has increased the need for standardized processes in diverse markets. Companies must now follow international quality standards, like ISO 9001. This ensures product consistency and compliance worldwide. As supply chains grow more complex, quality management systems must evolve. They must address cross-border challenges, cultural differences, and varying regulations.
Strategies for Managing Global Standards
To manage quality standards worldwide, businesses must build strong, adaptable quality management systems. They must handle the complexities of the global marketplace. This means using standard processes and procedures. They will ensure consistency and reliability in all operations. A key strategy for managing global standards is a quality assurance program. It should cover all aspects of the business. This includes product development and customer service.
By monitoring and evaluating quality metrics, companies can find areas to improve. They can then take action to prevent quality issues. In addition, businesses must prioritize quality control throughout the supply chain. This means working closely with suppliers and partners. We must meet quality standards at every stage of production. By setting clear guidelines and auditing regularly, companies can reduce quality issues. This will help ensure consistency across all operations.
Managing global standards requires a good grasp of international rules and regional compliance. Companies must standardize processes. But, they must allow flexibility to adapt to local laws and cultures. Regular audits, cross-border communication, and training are vital. They ensure quality and consistency across all operations.
Best Practices for Ensuring Quality Worldwide
To manage global standards, businesses can adopt best practices. They ensure quality at every level. Some of these practices include:
-
Invest in training programs to ensure employees know and follow quality standards.
-
Using quality management tools to improve processes and find issues.
-
Conducting regular quality audits to monitor compliance and identify potential risks
-
Establishing key performance indicators (KPIs) to measure the effectiveness of quality management systems
-
Implementing a culture of continuous improvement to drive innovation and maintain high-quality standards
-
Work with industry partners and regulators. Stay updated on quality trends and rules. By following best practices and committing to quality, businesses can meet global standards. This will help them succeed in a competitive global market.
How to obtain Quality Management certification?
We are an Education Technology company providing certification training courses to accelerate careers of working professionals worldwide. We impart training through instructor-led classroom workshops, instructor-led live virtual training sessions, and self-paced e-learning courses.
We have successfully conducted training sessions in 108 countries across the globe and enabled thousands of working professionals to enhance the scope of their careers.
Our enterprise training portfolio includes in-demand and globally recognized certification training courses in Project Management, Quality Management, Business Analysis, IT Service Management, Agile and Scrum, Cyber Security, Data Science, and Emerging Technologies. Download our Enterprise Training Catalog from https://www.icertglobal.com/corporate-training-for-enterprises.php and https://www.icertglobal.com/index.php
Popular Courses include:
-
Project Management: PMP, CAPM ,PMI RMP
-
Quality Management: Six Sigma Black Belt ,Lean Six Sigma Green Belt, Lean Management, Minitab,CMMI
-
Business Analysis: CBAP, CCBA, ECBA
-
Agile Training: PMI-ACP , CSM , CSPO
-
Scrum Training: CSM
-
DevOps
-
Program Management: PgMP
-
Cloud Technology: Exin Cloud Computing
-
Citrix Client Adminisration: Citrix Cloud Administration
The 10 top-paying certifications to target in 2024 are:
Conclusion
In conclusion, globalization has changed how businesses operate. It requires a more strategic and proactive approach to quality management. Businesses can ensure excellence in operations with strong quality systems and controls. They should also follow best practices for managing global standards. This will ensure consistency and reliability. In today's global economy, managing quality worldwide is a must. It is a competitive advantage that can drive growth, innovation, and success.
Contact Us For More Information:
Visit : www.icertglobal.com Email : info@icertglobal.com
How CTFL Certification Boosts Your Agile Testing Skills
In today's fast-paced software world, Agile is the standard for software delivery. It ensures efficiency and high quality. Testing is vital in Agile. It ensures each iteration is bug-free, functional, and meets customer expectations. The CTFL certification from the ISTQB is globally recognized. It gives software testers a strong foundation in testing, especially in Agile environments.
This certification is especially valuable for testers. It will enhance their Agile testing skills. CTFL-certified professionals can deliver faster, more efficient testing. They can do this by mastering Agile testing principles, techniques, and best practices. This article will explore how CTFL certification boosts your Agile testing skills. It will discuss key learnings that enhance your value to an Agile team.
Table Of Contents
- Understanding Agile Testing Frameworks
- Mastering Agile Testing Techniques
- Agile Test Planning and Estimation
- Improving communication and collaboration
- Continuous Improvement and Agile Testing Metrics
- Conclusion
Understanding Agile Testing Frameworks
CTFL certification improves your Agile testing skills in a key way. It gives you a deep understanding of Agile frameworks. Agile testing is different from traditional testing. It is continuous and integrated into the development process. CTFL certification covers key Agile methods: Scrum, Kanban, and XP. They are vital to Agile testing.
- Agile vs. Waterfall Testing: The CTFL cert outlines the differences between Agile and Waterfall methods. It helps testers adapt to Agile's iterative nature.
- Integration into Agile Sprints: CTFL covers testing in Agile sprints. It ensures continuous testing throughout the development cycle.
- Collaboration with Agile Teams: Testers must work closely with Agile teams, including developers, product owners, and stakeholders. They are cross-functional. This ensures quick feedback and continuous delivery.
Agile testing frameworks let certified professionals join Agile workflows. This improves collaboration and speeds up testing.
Mastering Agile Testing Techniques
The CTFL certification teaches testers testing methods for Agile environments. Agile testing is faster and continuous, unlike traditional testing. CTFL teaches testers efficient techniques to keep up with this demand.
- Exploratory Testing: Agile values flexibility. CTFL teaches testers to use exploratory testing. It helps them adapt to changing requirements and user stories.
- Automation in Agile: In Agile, the speed of testing is crucial. CTFL stresses the need for test automation. It presents automation frameworks to help testers run regression tests quickly and often.
- Test-Driven Development (TDD): CTFL introduces testers to TDD. It's a method in which testing is part of development from the start. It ensures that each piece of code is tested as it is written.
By mastering these techniques, testers can better cope with Agile's fast-changing world.
Agile Test Planning and Estimation
In Agile, test planning and estimation are key to keeping a smooth development flow. CTFL certification trains testers in Agile test planning and estimation. It ensures that testing is efficient and well coordinated with development.
- CTFL teaches testers to develop test plans for Agile sprints. This makes the testing scope clear and manageable in the short iterations.
- Risk-Based Testing: Agile projects often have limited time and resources. CTFL highlights risk-based testing. It allows testers to prioritize critical test cases and focus on high-risk areas.
- Accurate Test Estimation: Testers must estimate the time and effort for test tasks. This improves their ability to meet Agile deadlines.
Test planning and estimation are key. They allow testers to deliver quality results and match Agile's speed.
Improving communication and collaboration
In Agile environments, communication and collaboration between team members is vital. CTFL certification stresses improving communication skills. This is vital for Agile testers in cross-functional teams.
- Daily Stand-Ups: CTFL prepares testers for Agile ceremonies, like daily stand-ups. They share their testing progress and any blockers.
- Collaboration with Developers: Testers with a CTFL know to work closely with developers. This ensures testing is integrated into the coding process and promotes continuous feedback.
- CTFL urges testers to engage with stakeholders. They should gather requirements, clarify expectations, and align testing with customer needs.
Agile testers must have strong communication and collaboration skills. This helps them work better with the whole team. It ensures issues are found early and fixed quickly.
Continuous Improvement and Agile Testing Metrics
Agile principles emphasize continuous improvement. CTFL certification helps testers focus on constant learning and improving their testing. Also, CTFL introduces testers to key metrics for measuring Agile testing efficiency.
- Retrospectives for Improvement: CTFL-certified testers actively join retrospectives. The team reviews the sprint's successes and challenges. They suggest solutions for improvement.
- Key Agile Testing Metrics: Testers learn metrics like test coverage and defect density. They also learn pass/fail rates. They help assess testing performance and find areas for improvement.
- Adapting to Feedback: Agile is all about quick iterations and feedback loops. CTFL certification teaches testers to use feedback. They should improve their tests after each iteration.
CTFL-certified testers can use Agile metrics to improve testing. Their methods will evolve with the project, yielding better results over time.
How to obtain CTFL certification?
We are an Education Technology company providing certification training courses to accelerate careers of working professionals worldwide. We impart training through instructor-led classroom workshops, instructor-led live virtual training sessions, and self-paced e-learning courses.
We have successfully conducted training sessions in 108 countries across the globe and enabled thousands of working professionals to enhance the scope of their careers.
Our enterprise training portfolio includes in-demand and globally recognized certification training courses in Project Management, Quality Management, Business Analysis, IT Service Management, Agile and Scrum, Cyber Security, Data Science, and Emerging Technologies. Download our Enterprise Training Catalog from https://www.icertglobal.com/corporate-training-for-enterprises.php and https://www.icertglobal.com/index.php
Popular Courses include:
- Project Management: PMP, CAPM ,PMI RMP
- Quality Management: Six Sigma Black Belt ,Lean Six Sigma Green Belt, Lean Management, Minitab,CMMI
- Business Analysis: CBAP, CCBA, ECBA
- Agile Training: PMI-ACP , CSM , CSPO
- Scrum Training: CSM
- DevOps
- Program Management: PgMP
- Cloud Technology: Exin Cloud Computing
- Citrix Client Adminisration: Citrix Cloud Administration
The 10 top-paying certifications to target in 2024 are:
- Certified Information Systems Security Professional® (CISSP)
- AWS Certified Solutions Architect
- Google Certified Professional Cloud Architect
- Big Data Certification
- Data Science Certification
- Certified In Risk And Information Systems Control (CRISC)
- Certified Information Security Manager(CISM)
- Project Management Professional (PMP)® Certification
- Certified Ethical Hacker (CEH)
- Certified Scrum Master (CSM)
Conclusion
CTFL certification is a key tool for testers. It helps them improve their Agile testing skills. CTFL gives testers the knowledge and skills to thrive in Agile environments. It covers Agile testing frameworks, specific techniques, better communication, and continuous improvement.
As Agile methods dominate software development, a CTFL certification helps testers stand out. It ensures they can better contribute to Agile teams. This certification can help testers. It can boost their careers, skills, and software in an Agile world.
Contact Us :
Contact Us For More Information:
Visit :www.icertglobal.com Email : info@icertglobal.com
Read More
In today's fast-paced software world, Agile is the standard for software delivery. It ensures efficiency and high quality. Testing is vital in Agile. It ensures each iteration is bug-free, functional, and meets customer expectations. The CTFL certification from the ISTQB is globally recognized. It gives software testers a strong foundation in testing, especially in Agile environments.
This certification is especially valuable for testers. It will enhance their Agile testing skills. CTFL-certified professionals can deliver faster, more efficient testing. They can do this by mastering Agile testing principles, techniques, and best practices. This article will explore how CTFL certification boosts your Agile testing skills. It will discuss key learnings that enhance your value to an Agile team.
Table Of Contents
- Understanding Agile Testing Frameworks
- Mastering Agile Testing Techniques
- Agile Test Planning and Estimation
- Improving communication and collaboration
- Continuous Improvement and Agile Testing Metrics
- Conclusion
Understanding Agile Testing Frameworks
CTFL certification improves your Agile testing skills in a key way. It gives you a deep understanding of Agile frameworks. Agile testing is different from traditional testing. It is continuous and integrated into the development process. CTFL certification covers key Agile methods: Scrum, Kanban, and XP. They are vital to Agile testing.
- Agile vs. Waterfall Testing: The CTFL cert outlines the differences between Agile and Waterfall methods. It helps testers adapt to Agile's iterative nature.
- Integration into Agile Sprints: CTFL covers testing in Agile sprints. It ensures continuous testing throughout the development cycle.
- Collaboration with Agile Teams: Testers must work closely with Agile teams, including developers, product owners, and stakeholders. They are cross-functional. This ensures quick feedback and continuous delivery.
Agile testing frameworks let certified professionals join Agile workflows. This improves collaboration and speeds up testing.
Mastering Agile Testing Techniques
The CTFL certification teaches testers testing methods for Agile environments. Agile testing is faster and continuous, unlike traditional testing. CTFL teaches testers efficient techniques to keep up with this demand.
- Exploratory Testing: Agile values flexibility. CTFL teaches testers to use exploratory testing. It helps them adapt to changing requirements and user stories.
- Automation in Agile: In Agile, the speed of testing is crucial. CTFL stresses the need for test automation. It presents automation frameworks to help testers run regression tests quickly and often.
- Test-Driven Development (TDD): CTFL introduces testers to TDD. It's a method in which testing is part of development from the start. It ensures that each piece of code is tested as it is written.
By mastering these techniques, testers can better cope with Agile's fast-changing world.
Agile Test Planning and Estimation
In Agile, test planning and estimation are key to keeping a smooth development flow. CTFL certification trains testers in Agile test planning and estimation. It ensures that testing is efficient and well coordinated with development.
- CTFL teaches testers to develop test plans for Agile sprints. This makes the testing scope clear and manageable in the short iterations.
- Risk-Based Testing: Agile projects often have limited time and resources. CTFL highlights risk-based testing. It allows testers to prioritize critical test cases and focus on high-risk areas.
- Accurate Test Estimation: Testers must estimate the time and effort for test tasks. This improves their ability to meet Agile deadlines.
Test planning and estimation are key. They allow testers to deliver quality results and match Agile's speed.
Improving communication and collaboration
In Agile environments, communication and collaboration between team members is vital. CTFL certification stresses improving communication skills. This is vital for Agile testers in cross-functional teams.
- Daily Stand-Ups: CTFL prepares testers for Agile ceremonies, like daily stand-ups. They share their testing progress and any blockers.
- Collaboration with Developers: Testers with a CTFL know to work closely with developers. This ensures testing is integrated into the coding process and promotes continuous feedback.
- CTFL urges testers to engage with stakeholders. They should gather requirements, clarify expectations, and align testing with customer needs.
Agile testers must have strong communication and collaboration skills. This helps them work better with the whole team. It ensures issues are found early and fixed quickly.
Continuous Improvement and Agile Testing Metrics
Agile principles emphasize continuous improvement. CTFL certification helps testers focus on constant learning and improving their testing. Also, CTFL introduces testers to key metrics for measuring Agile testing efficiency.
- Retrospectives for Improvement: CTFL-certified testers actively join retrospectives. The team reviews the sprint's successes and challenges. They suggest solutions for improvement.
- Key Agile Testing Metrics: Testers learn metrics like test coverage and defect density. They also learn pass/fail rates. They help assess testing performance and find areas for improvement.
- Adapting to Feedback: Agile is all about quick iterations and feedback loops. CTFL certification teaches testers to use feedback. They should improve their tests after each iteration.
CTFL-certified testers can use Agile metrics to improve testing. Their methods will evolve with the project, yielding better results over time.
How to obtain CTFL certification?
We are an Education Technology company providing certification training courses to accelerate careers of working professionals worldwide. We impart training through instructor-led classroom workshops, instructor-led live virtual training sessions, and self-paced e-learning courses.
We have successfully conducted training sessions in 108 countries across the globe and enabled thousands of working professionals to enhance the scope of their careers.
Our enterprise training portfolio includes in-demand and globally recognized certification training courses in Project Management, Quality Management, Business Analysis, IT Service Management, Agile and Scrum, Cyber Security, Data Science, and Emerging Technologies. Download our Enterprise Training Catalog from https://www.icertglobal.com/corporate-training-for-enterprises.php and https://www.icertglobal.com/index.php
Popular Courses include:
- Project Management: PMP, CAPM ,PMI RMP
- Quality Management: Six Sigma Black Belt ,Lean Six Sigma Green Belt, Lean Management, Minitab,CMMI
- Business Analysis: CBAP, CCBA, ECBA
- Agile Training: PMI-ACP , CSM , CSPO
- Scrum Training: CSM
- DevOps
- Program Management: PgMP
- Cloud Technology: Exin Cloud Computing
- Citrix Client Adminisration: Citrix Cloud Administration
The 10 top-paying certifications to target in 2024 are:
- Certified Information Systems Security Professional® (CISSP)
- AWS Certified Solutions Architect
- Google Certified Professional Cloud Architect
- Big Data Certification
- Data Science Certification
- Certified In Risk And Information Systems Control (CRISC)
- Certified Information Security Manager(CISM)
- Project Management Professional (PMP)® Certification
- Certified Ethical Hacker (CEH)
- Certified Scrum Master (CSM)
Conclusion
CTFL certification is a key tool for testers. It helps them improve their Agile testing skills. CTFL gives testers the knowledge and skills to thrive in Agile environments. It covers Agile testing frameworks, specific techniques, better communication, and continuous improvement.
As Agile methods dominate software development, a CTFL certification helps testers stand out. It ensures they can better contribute to Agile teams. This certification can help testers. It can boost their careers, skills, and software in an Agile world.
Contact Us :
Contact Us For More Information:
Visit :www.icertglobal.com Email : info@icertglobal.com
Implementing Quality by Design QbD in Product Development
In today's competitive pharma industry, QbD in product development is key. It ensures product quality, efficacy, and safety. QbD is a systematic approach. It integrates risk assessment, science-based methods, and quality management. It applies them throughout the product lifecycle. This article will explore implementing QbD in pharmaceutical product development. We will cover its benefits, challenges, and key considerations.
Understanding Quality by Design (QbD):
QbD is a proactive, science-based approach to drug development. It aims to design and develop processes to ensure product quality. QbD stresses knowing the link between critical process parameters (CPP) and quality attributes (CQA). QbD principles can help pharma firms. They can optimize their processes, boost product quality, and ensure compliance with regulations.
Quality by Design (QbD) is a systematic approach to drug development. It emphasizes building quality into products from the start, not testing for it at the end. QbD helps ensure consistency and reliability. It does this by setting quality targets and knowing the process parameters that affect product performance. This strategy improves product quality. It also speeds up development and cuts the risk of costly recalls or failures.
Benefits of Implementing QbD in Product Development:
-
Improved Product Quality: QbD can help pharma companies. It does this by focusing on design space, risk assessment, and process optimization. It will enhance product quality and consistency.
-
Regulatory Compliance: QbD makes sure products meet regulations. It reduces the risk of non-compliance and recalls.
-
Cost Reduction: QbD finds and fixes risks early in development. This cuts the chance of expensive errors and rework.
-
Better Process Understanding: Analyzing key parameters and quality attributes can help companies. They can then better control their manufacturing processes and improve them.
-
Faster Time to Market: QbD speeds up product development. It helps companies launch new products more quickly.
Challenges of Implementing QbD in Product Development:
Implementing Quality by Design (QbD) in product development has challenges. It requires a cultural shift in organizations that may resist change. Also, QbD requires a deep understanding of processes and teamwork. This can complicate communication and coordination. Finally, regulatory issues and the need for documentation can create hurdles. Organizations must meet new industry standards. They must also keep product quality high.
-
Lack of Resources: QbD needs a big investment of time, money, and expertise. This can be a challenge for smaller pharma companies.
-
Cultural Shift: Adopting a QbD mindset may require a cultural shift. It involves a change in mindset and practices.
-
Data Analysis: Analyzing data to find key process parameters and quality attributes can be hard and slow.
-
Regulatory Hurdles: QbD implementation can be tough. Regulations are always changing.
-
Training and Education: Proper training on QbD principles is crucial for success. It must reach all employees.
Key Considerations for Implementing QbD in Product Development:
Implementing Quality by Design (QbD) in product development requires a systematic approach. It must emphasize understanding customer needs and product quality attributes from the start. Key considerations include a strong risk management framework. It should identify and mitigate potential issues early. Also, teams must collaborate to ensure a holistic view. Also, thorough documentation and feedback loops are key. They refine processes and improve the product over its lifecycle.
-
Conduct a thorough risk assessment. It should identify risks in the product development process.
-
Define critical process parameters and quality attributes. They greatly affect product quality.
-
Create a design space that is flexible and optimizes the manufacturing process.
-
Implement a control strategy to ensure product quality and regulatory compliance.
-
Continuous improvement through process optimization, validation studies, and monitoring of critical process parameters.
How to obtain Quality Management certification?
We are an Education Technology company providing certification training courses to accelerate careers of working professionals worldwide. We impart training through instructor-led classroom workshops, instructor-led live virtual training sessions, and self-paced e-learning courses.
We have successfully conducted training sessions in 108 countries across the globe and enabled thousands of working professionals to enhance the scope of their careers.
Our enterprise training portfolio includes in-demand and globally recognized certification training courses in Project Management, Quality Management, Business Analysis, IT Service Management, Agile and Scrum, Cyber Security, Data Science, and Emerging Technologies. Download our Enterprise Training Catalog from https://www.icertglobal.com/corporate-training-for-enterprises.php and https://www.icertglobal.com/index.php
Popular Courses include:
-
Project Management: PMP, CAPM ,PMI RMP
-
Quality Management: Six Sigma Black Belt ,Lean Six Sigma Green Belt, Lean Management, Minitab,CMMI
-
Business Analysis: CBAP, CCBA, ECBA
-
Agile Training: PMI-ACP , CSM , CSPO
-
Scrum Training: CSM
-
DevOps
-
Program Management: PgMP
-
Cloud Technology: Exin Cloud Computing
-
Citrix Client Adminisration: Citrix Cloud Administration
The 10 top-paying certifications to target in 2024 are:
Conclusion
In conclusion, QbD in product development is vital for pharma firms. It boosts product quality, ensures compliance, and improves efficiency. By addressing challenges and embracing QbD, companies can succeed in today's competitive market.
Contact Us For More Information:
Visit : www.icertglobal.com Email : info@icertglobal.com
Read More
In today's competitive pharma industry, QbD in product development is key. It ensures product quality, efficacy, and safety. QbD is a systematic approach. It integrates risk assessment, science-based methods, and quality management. It applies them throughout the product lifecycle. This article will explore implementing QbD in pharmaceutical product development. We will cover its benefits, challenges, and key considerations.
Understanding Quality by Design (QbD):
QbD is a proactive, science-based approach to drug development. It aims to design and develop processes to ensure product quality. QbD stresses knowing the link between critical process parameters (CPP) and quality attributes (CQA). QbD principles can help pharma firms. They can optimize their processes, boost product quality, and ensure compliance with regulations.
Quality by Design (QbD) is a systematic approach to drug development. It emphasizes building quality into products from the start, not testing for it at the end. QbD helps ensure consistency and reliability. It does this by setting quality targets and knowing the process parameters that affect product performance. This strategy improves product quality. It also speeds up development and cuts the risk of costly recalls or failures.
Benefits of Implementing QbD in Product Development:
-
Improved Product Quality: QbD can help pharma companies. It does this by focusing on design space, risk assessment, and process optimization. It will enhance product quality and consistency.
-
Regulatory Compliance: QbD makes sure products meet regulations. It reduces the risk of non-compliance and recalls.
-
Cost Reduction: QbD finds and fixes risks early in development. This cuts the chance of expensive errors and rework.
-
Better Process Understanding: Analyzing key parameters and quality attributes can help companies. They can then better control their manufacturing processes and improve them.
-
Faster Time to Market: QbD speeds up product development. It helps companies launch new products more quickly.
Challenges of Implementing QbD in Product Development:
Implementing Quality by Design (QbD) in product development has challenges. It requires a cultural shift in organizations that may resist change. Also, QbD requires a deep understanding of processes and teamwork. This can complicate communication and coordination. Finally, regulatory issues and the need for documentation can create hurdles. Organizations must meet new industry standards. They must also keep product quality high.
-
Lack of Resources: QbD needs a big investment of time, money, and expertise. This can be a challenge for smaller pharma companies.
-
Cultural Shift: Adopting a QbD mindset may require a cultural shift. It involves a change in mindset and practices.
-
Data Analysis: Analyzing data to find key process parameters and quality attributes can be hard and slow.
-
Regulatory Hurdles: QbD implementation can be tough. Regulations are always changing.
-
Training and Education: Proper training on QbD principles is crucial for success. It must reach all employees.
Key Considerations for Implementing QbD in Product Development:
Implementing Quality by Design (QbD) in product development requires a systematic approach. It must emphasize understanding customer needs and product quality attributes from the start. Key considerations include a strong risk management framework. It should identify and mitigate potential issues early. Also, teams must collaborate to ensure a holistic view. Also, thorough documentation and feedback loops are key. They refine processes and improve the product over its lifecycle.
-
Conduct a thorough risk assessment. It should identify risks in the product development process.
-
Define critical process parameters and quality attributes. They greatly affect product quality.
-
Create a design space that is flexible and optimizes the manufacturing process.
-
Implement a control strategy to ensure product quality and regulatory compliance.
-
Continuous improvement through process optimization, validation studies, and monitoring of critical process parameters.
How to obtain Quality Management certification?
We are an Education Technology company providing certification training courses to accelerate careers of working professionals worldwide. We impart training through instructor-led classroom workshops, instructor-led live virtual training sessions, and self-paced e-learning courses.
We have successfully conducted training sessions in 108 countries across the globe and enabled thousands of working professionals to enhance the scope of their careers.
Our enterprise training portfolio includes in-demand and globally recognized certification training courses in Project Management, Quality Management, Business Analysis, IT Service Management, Agile and Scrum, Cyber Security, Data Science, and Emerging Technologies. Download our Enterprise Training Catalog from https://www.icertglobal.com/corporate-training-for-enterprises.php and https://www.icertglobal.com/index.php
Popular Courses include:
-
Project Management: PMP, CAPM ,PMI RMP
-
Quality Management: Six Sigma Black Belt ,Lean Six Sigma Green Belt, Lean Management, Minitab,CMMI
-
Business Analysis: CBAP, CCBA, ECBA
-
Agile Training: PMI-ACP , CSM , CSPO
-
Scrum Training: CSM
-
DevOps
-
Program Management: PgMP
-
Cloud Technology: Exin Cloud Computing
-
Citrix Client Adminisration: Citrix Cloud Administration
The 10 top-paying certifications to target in 2024 are:
Conclusion
In conclusion, QbD in product development is vital for pharma firms. It boosts product quality, ensures compliance, and improves efficiency. By addressing challenges and embracing QbD, companies can succeed in today's competitive market.
Contact Us For More Information:
Visit : www.icertglobal.com Email : info@icertglobal.com
Trends and Innovations for Six Sigma Green Belt in 2024
Six Sigma is a trusted method for improving business processes and reducing defects. As businesses evolve, so does Six Sigma. It now includes new trends that help Green Belt professionals improve their impact. In 2024, new tech, business practices, and strategies have changed Six Sigma. They offer Green Belts chances to lead improvement projects.
The Six Sigma Green Belt is a key certification. It is for those in process improvement and quality management. In 2024, technology and new business needs have advanced Six Sigma. New methods have also played a role. These changes let Green Belts make even better process improvements. Their organizations will benefit in new ways.
This article reviews trends and innovations in the 2024 Six Sigma Green Belt certification. It shows how these advances help professionals excel in process and quality management.
Table Of Contents
- Combining Artificial Intelligence with Machine Learning
- Focus on Sustainability and Green Initiatives
- Integration with Digital Transformation Strategies
- Evolution of Remote Work and Global Collaboration
- Emphasis on Soft Skills and Leadership Development
- Conclusion
Combining Artificial Intelligence with Machine Learning
A key innovation in Six Sigma is its use of AI and ML. They are now part of the methodology. Traditionally, Six Sigma focused on data-driven decisions using stats. Now, AI and ML allow for even deeper insights.
- Enhanced Data Analytics: AI can analyze large datasets better and faster than humans. It gives Green Belts real-time insights into inefficient processes.
- Predictive Modeling: ML algorithms predict future outcomes using historical data. This helps Green Belts make improvements before problems arise.
- Automation of Processes: Many routine tasks, like data collection, can now be automated using AI tools. This frees up Green Belts to focus on more strategic aspects of process improvement.
AI/ML is revolutionizing how Six Sigma Green Belts use data. It's making their work more efficient and precise.
Focus on Sustainability and Green Initiatives
In 2024, businesses are focused on sustainability. Six Sigma Green Belts are key to reducing waste and energy use. This has shifted Six Sigma methods to include sustainable practices.
- Lean and Green Practices: Green Belts now find waste's environmental impact. This enables businesses to lower their environmental impact.
- Sustainable Process Improvements: Green Belts reduce energy and raw material use. This aligns process improvements with sustainability goals.
- Circular Economy Practices: Many businesses are adopting circular economy models. Six Sigma Green Belts are key to designing processes. They cut waste and boost material reuse.
Sustainable practices are eco-friendly and save money. So, they are key to process improvement in 2024.
Integration with Digital Transformation Strategies
As more companies go digital, demand for Six Sigma Green Belts is rising. They must now integrate process improvement with digital initiatives. This trend is reshaping the role of Green Belts. It is pushing them towards more tech-savvy tasks.
- Process Automation: Many business processes are now being automated. Green Belts are key in finding processes to automate, like with RPA.
- Digital Tools for Data Analysis: Green Belts can use advanced digital tools. They provide better data visualization, real-time monitoring, and analysis. Tools like Power BI and Tableau allow for more dynamic reporting and decision-making.
- Collaboration with IT Teams: Green Belts are now working with IT pros. They want their process improvements to align with digital transformation goals.
In 2024, we must integrate Six Sigma with digital transformation. It's key to staying competitive and optimizing processes for the digital age.
Evolution of Remote Work and Global Collaboration
With remote work and global teams on the rise, Six Sigma Green Belts are evolving. They must now manage process improvements in this new work environment. Remote work has unique challenges. We need new solutions to stay productive and efficient.
- Virtual Process Mapping and Analysis: Green Belts now use virtual tools for process mapping and data collection. This helps teams in different time zones to collaborate.
- Remote Team Management: The Green Belt now manages global teams. This requires new skills to lead and communicate in a remote environment. They are needed to improve processes.
- Cloud-Based Solutions: Green Belts are using cloud-based project management and data analysis tools. They track progress and collaborate in real time, no matter where they are.
This shift to remote work means Green Belts must adopt new tools and strategies. They need them to lead successful process improvement initiatives in 2024.
Emphasis on Soft Skills and Leadership Development
Six Sigma Green Belt training has shifted focus. It now emphasizes soft skills, like leadership and communication, along with technical skills. This shift is because technical skills alone can't lead to successful process improvements.
- Change Management Expertise: Green Belts must lead teams through change. They must align and engage all stakeholders in the process.
- Leadership in Cross-Functional Teams: Green Belts often work with teams across departments. Strong leadership skills are essential for improving processes across the organization.
As Green Belts shift to more strategic roles, they must share data and negotiate solutions.
This focus on leadership and communication is helping Green Belts. They are becoming more effective change agents. This positions them as key contributors to success in 2024.
How to obtain Lean Six Sigma Green Belt Certification?
We are an Education Technology company providing certification training courses to accelerate careers of working professionals worldwide. We impart training through instructor-led classroom workshops, instructor-led live virtual training sessions, and self-paced e-learning courses.
We have successfully conducted training sessions in 108 countries across the globe and enabled thousands of working professionals to enhance the scope of their careers.
Our enterprise training portfolio includes in-demand and globally recognized certification training courses in Project Management, Quality Management, Business Analysis, IT Service Management, Agile and Scrum, Cyber Security, Data Science, and Emerging Technologies. Download our Enterprise Training Catalog from https://www.icertglobal.com/corporate-training-for-enterprises.php and https://www.icertglobal.com/index.php
Popular Courses include:
- Project Management: PMP, CAPM ,PMI RMP
- Quality Management: Six Sigma Black Belt ,Lean Six Sigma Green Belt, Lean Management, Minitab,CMMI
- Business Analysis: CBAP, CCBA, ECBA
- Agile Training: PMI-ACP , CSM , CSPO
- Scrum Training: CSM
- DevOps
- Program Management: PgMP
- Cloud Technology: Exin Cloud Computing
- Citrix Client Adminisration: Citrix Cloud Administration
The 10 top-paying certifications to target in 2024 are:
- Certified Information Systems Security Professional® (CISSP)
- AWS Certified Solutions Architect
- Google Certified Professional Cloud Architect
- Big Data Certification
- Data Science Certification
- Certified In Risk And Information Systems Control (CRISC)
- Certified Information Security Manager(CISM)
- Project Management Professional (PMP)® Certification
- Certified Ethical Hacker (CEH)
- Certified Scrum Master (CSM)
Conclusion
In 2024, Six Sigma Green Belt certification is still evolving. New technologies and methods are now being integrated into it. AI, ML, a focus on sustainability, and digital transformation are shaping the future of Six Sigma. Remote work is also a factor. These trends give Green Belts new tools to improve processes. The focus on leadership and soft skills means Green Belts must be both technical experts and strong leaders. They must be change agents, too.
The 2024 trends and innovations offer a chance for Six Sigma Green Belts. They can improve their skills, lead better projects, and shape the future of business. As businesses evolve, Green Belts must adapt. They must embrace new tools and strategies to improve processes.
Contact Us :
Contact Us For More Information:
Visit :www.icertglobal.com Email : info@icertglobal.com
Read More
Six Sigma is a trusted method for improving business processes and reducing defects. As businesses evolve, so does Six Sigma. It now includes new trends that help Green Belt professionals improve their impact. In 2024, new tech, business practices, and strategies have changed Six Sigma. They offer Green Belts chances to lead improvement projects.
The Six Sigma Green Belt is a key certification. It is for those in process improvement and quality management. In 2024, technology and new business needs have advanced Six Sigma. New methods have also played a role. These changes let Green Belts make even better process improvements. Their organizations will benefit in new ways.
This article reviews trends and innovations in the 2024 Six Sigma Green Belt certification. It shows how these advances help professionals excel in process and quality management.
Table Of Contents
- Combining Artificial Intelligence with Machine Learning
- Focus on Sustainability and Green Initiatives
- Integration with Digital Transformation Strategies
- Evolution of Remote Work and Global Collaboration
- Emphasis on Soft Skills and Leadership Development
- Conclusion
Combining Artificial Intelligence with Machine Learning
A key innovation in Six Sigma is its use of AI and ML. They are now part of the methodology. Traditionally, Six Sigma focused on data-driven decisions using stats. Now, AI and ML allow for even deeper insights.
- Enhanced Data Analytics: AI can analyze large datasets better and faster than humans. It gives Green Belts real-time insights into inefficient processes.
- Predictive Modeling: ML algorithms predict future outcomes using historical data. This helps Green Belts make improvements before problems arise.
- Automation of Processes: Many routine tasks, like data collection, can now be automated using AI tools. This frees up Green Belts to focus on more strategic aspects of process improvement.
AI/ML is revolutionizing how Six Sigma Green Belts use data. It's making their work more efficient and precise.
Focus on Sustainability and Green Initiatives
In 2024, businesses are focused on sustainability. Six Sigma Green Belts are key to reducing waste and energy use. This has shifted Six Sigma methods to include sustainable practices.
- Lean and Green Practices: Green Belts now find waste's environmental impact. This enables businesses to lower their environmental impact.
- Sustainable Process Improvements: Green Belts reduce energy and raw material use. This aligns process improvements with sustainability goals.
- Circular Economy Practices: Many businesses are adopting circular economy models. Six Sigma Green Belts are key to designing processes. They cut waste and boost material reuse.
Sustainable practices are eco-friendly and save money. So, they are key to process improvement in 2024.
Integration with Digital Transformation Strategies
As more companies go digital, demand for Six Sigma Green Belts is rising. They must now integrate process improvement with digital initiatives. This trend is reshaping the role of Green Belts. It is pushing them towards more tech-savvy tasks.
- Process Automation: Many business processes are now being automated. Green Belts are key in finding processes to automate, like with RPA.
- Digital Tools for Data Analysis: Green Belts can use advanced digital tools. They provide better data visualization, real-time monitoring, and analysis. Tools like Power BI and Tableau allow for more dynamic reporting and decision-making.
- Collaboration with IT Teams: Green Belts are now working with IT pros. They want their process improvements to align with digital transformation goals.
In 2024, we must integrate Six Sigma with digital transformation. It's key to staying competitive and optimizing processes for the digital age.
Evolution of Remote Work and Global Collaboration
With remote work and global teams on the rise, Six Sigma Green Belts are evolving. They must now manage process improvements in this new work environment. Remote work has unique challenges. We need new solutions to stay productive and efficient.
- Virtual Process Mapping and Analysis: Green Belts now use virtual tools for process mapping and data collection. This helps teams in different time zones to collaborate.
- Remote Team Management: The Green Belt now manages global teams. This requires new skills to lead and communicate in a remote environment. They are needed to improve processes.
- Cloud-Based Solutions: Green Belts are using cloud-based project management and data analysis tools. They track progress and collaborate in real time, no matter where they are.
This shift to remote work means Green Belts must adopt new tools and strategies. They need them to lead successful process improvement initiatives in 2024.
Emphasis on Soft Skills and Leadership Development
Six Sigma Green Belt training has shifted focus. It now emphasizes soft skills, like leadership and communication, along with technical skills. This shift is because technical skills alone can't lead to successful process improvements.
- Change Management Expertise: Green Belts must lead teams through change. They must align and engage all stakeholders in the process.
- Leadership in Cross-Functional Teams: Green Belts often work with teams across departments. Strong leadership skills are essential for improving processes across the organization.
As Green Belts shift to more strategic roles, they must share data and negotiate solutions.
This focus on leadership and communication is helping Green Belts. They are becoming more effective change agents. This positions them as key contributors to success in 2024.
How to obtain Lean Six Sigma Green Belt Certification?
We are an Education Technology company providing certification training courses to accelerate careers of working professionals worldwide. We impart training through instructor-led classroom workshops, instructor-led live virtual training sessions, and self-paced e-learning courses.
We have successfully conducted training sessions in 108 countries across the globe and enabled thousands of working professionals to enhance the scope of their careers.
Our enterprise training portfolio includes in-demand and globally recognized certification training courses in Project Management, Quality Management, Business Analysis, IT Service Management, Agile and Scrum, Cyber Security, Data Science, and Emerging Technologies. Download our Enterprise Training Catalog from https://www.icertglobal.com/corporate-training-for-enterprises.php and https://www.icertglobal.com/index.php
Popular Courses include:
- Project Management: PMP, CAPM ,PMI RMP
- Quality Management: Six Sigma Black Belt ,Lean Six Sigma Green Belt, Lean Management, Minitab,CMMI
- Business Analysis: CBAP, CCBA, ECBA
- Agile Training: PMI-ACP , CSM , CSPO
- Scrum Training: CSM
- DevOps
- Program Management: PgMP
- Cloud Technology: Exin Cloud Computing
- Citrix Client Adminisration: Citrix Cloud Administration
The 10 top-paying certifications to target in 2024 are:
- Certified Information Systems Security Professional® (CISSP)
- AWS Certified Solutions Architect
- Google Certified Professional Cloud Architect
- Big Data Certification
- Data Science Certification
- Certified In Risk And Information Systems Control (CRISC)
- Certified Information Security Manager(CISM)
- Project Management Professional (PMP)® Certification
- Certified Ethical Hacker (CEH)
- Certified Scrum Master (CSM)
Conclusion
In 2024, Six Sigma Green Belt certification is still evolving. New technologies and methods are now being integrated into it. AI, ML, a focus on sustainability, and digital transformation are shaping the future of Six Sigma. Remote work is also a factor. These trends give Green Belts new tools to improve processes. The focus on leadership and soft skills means Green Belts must be both technical experts and strong leaders. They must be change agents, too.
The 2024 trends and innovations offer a chance for Six Sigma Green Belts. They can improve their skills, lead better projects, and shape the future of business. As businesses evolve, Green Belts must adapt. They must embrace new tools and strategies to improve processes.
Contact Us :
Contact Us For More Information:
Visit :www.icertglobal.com Email : info@icertglobal.com
Career Progression: Tester to Test Lead and Beyond in QA
Have you ever wondered how you can progress in your career from being a Tester to a Test Lead and beyond? Software testing and quality assurance are vital to software development. As you gain experience, promotion opportunities in the industry will increase. This article will explore the path from Tester to Test Lead. It will offer tips for success in software testing.
Tester Role: Starting Point of Your Career
As a Tester, your main job is to ensure software quality. You must find defects and bugs through systematic testing. This role needs strong attention to detail and analytical skills. It also requires a deep knowledge of software testing methods. Testers work closely with QA engineers and the testing team. They execute test cases, report bugs, and help improve software quality.
The tester role often begins a successful career in software development and QA. As a tester, you will learn to find bugs, ensure the product works, and improve the user experience. This starting point builds a solid technical base. It also opens paths to advanced roles, like test manager, automation engineer, or QA lead.
Skills Development: Key to Career Progression
To move from a Tester to a Test Lead, then to a manager, you must constantly improve your skills.
This includes expertise in test automation, and skills in:
-
leadership
-
project management
-
problem-solving
-
decision-making
-
communication
Investing in training, workshops, and certifications can boost your career. They can open doors to new leadership roles in the organization.
Skills development is vital for career advancement. It boosts your expertise and adaptability in a fast-changing job market. By learning both technical and soft skills, you become more valuable to employers. This opens up new growth opportunities. Investing in personal development boosts your confidence. It also prepares you for leadership roles and tougher tasks.
Test Lead Role: Stepping into Leadership
With experience and strong leadership, you may become a Test Lead. Test Leads manage testing teams. They develop test strategies and coordinate test activities. They ensure successful execution of test plans. This role needs technical skills and the ability to evaluate performance. It requires coaching, mentoring, and working well with cross-functional teams.
A Test Lead must balance technical skills and leadership. They must guide a team of testers to deliver high-quality software. As a Test Lead, you will define testing strategies and processes. You will also mentor junior testers to align them with project goals. You must communicate and decide well. You will bridge the gap between the dev team and stakeholders. Your goal is to ensure testing supports business objectives.
Career Advancement: Setting Your Goals
To advance from a Test Lead to a Test Manager or QA Director, set clear career goals. Then, create a roadmap for your growth. This may involve gaining industry knowledge and collaboration skills. It may also require mastering agile methods and seeking learning opportunities. These will help you stay ahead in the fast-changing field of software testing.
Clear career goals are key to long-term success. They give direction and motivation. Identify your strengths and areas for growth. Then, create a roadmap that aligns with your ambitions. Regularly reviewing and adjusting these goals ensures progress in a changing job market.
Software Deployment: Leading Project Delivery
As you advance in your career, you may lead software deployment projects. You will manage test environments, coordinate test activities, and ensure successful software delivery. This role needs strong leadership, risk management, and adaptability to change.
"Software Deployment: Leading Project Delivery" is your guide to mastering software delivery. It will help you master the end-to-end process of delivering robust software solutions. Learn the best practices. They ensure smooth rollouts, minimal downtime, and top system performance. This video gives you the tools to lead your next deployment project. It is for both project managers and developers.
How to obtain CTFL certification?
We are an Education Technology company providing certification training courses to accelerate careers of working professionals worldwide. We impart training through instructor-led classroom workshops, instructor-led live virtual training sessions, and self-paced e-learning courses.
We have successfully conducted training sessions in 108 countries across the globe and enabled thousands of working professionals to enhance the scope of their careers.
Our enterprise training portfolio includes in-demand and globally recognized certification training courses in Project Management, Quality Management, Business Analysis, IT Service Management, Agile and Scrum, Cyber Security, Data Science, and Emerging Technologies. Download our Enterprise Training Catalog from https://www.icertglobal.com/corporate-training-for-enterprises.php and https://www.icertglobal.com/index.php
Popular Courses include:
-
Project Management: PMP, CAPM ,PMI RMP
-
Quality Management: Six Sigma Black Belt ,Lean Six Sigma Green Belt, Lean Management, Minitab,CMMI
-
Business Analysis: CBAP, CCBA, ECBA
-
Agile Training: PMI-ACP , CSM , CSPO
-
Scrum Training: CSM
-
DevOps
-
Program Management: PgMP
-
Cloud Technology: Exin Cloud Computing
-
Citrix Client Adminisration: Citrix Cloud Administration
The 10 top-paying certifications to target in 2024 are:
Conclusion
In conclusion, the journey from Tester to Test Lead and beyond is rewarding. It offers many opportunities for career growth and success. Invest in skills, leadership, and learning. It will lead to a successful career in software testing and quality assurance. Are you ready to advance your career and unlock new growth opportunities?
Contact Us For More Information:
Visit : www.icertglobal.com Email : info@icertglobal.com
Read More
Have you ever wondered how you can progress in your career from being a Tester to a Test Lead and beyond? Software testing and quality assurance are vital to software development. As you gain experience, promotion opportunities in the industry will increase. This article will explore the path from Tester to Test Lead. It will offer tips for success in software testing.
Tester Role: Starting Point of Your Career
As a Tester, your main job is to ensure software quality. You must find defects and bugs through systematic testing. This role needs strong attention to detail and analytical skills. It also requires a deep knowledge of software testing methods. Testers work closely with QA engineers and the testing team. They execute test cases, report bugs, and help improve software quality.
The tester role often begins a successful career in software development and QA. As a tester, you will learn to find bugs, ensure the product works, and improve the user experience. This starting point builds a solid technical base. It also opens paths to advanced roles, like test manager, automation engineer, or QA lead.
Skills Development: Key to Career Progression
To move from a Tester to a Test Lead, then to a manager, you must constantly improve your skills.
This includes expertise in test automation, and skills in:
-
leadership
-
project management
-
problem-solving
-
decision-making
-
communication
Investing in training, workshops, and certifications can boost your career. They can open doors to new leadership roles in the organization.
Skills development is vital for career advancement. It boosts your expertise and adaptability in a fast-changing job market. By learning both technical and soft skills, you become more valuable to employers. This opens up new growth opportunities. Investing in personal development boosts your confidence. It also prepares you for leadership roles and tougher tasks.
Test Lead Role: Stepping into Leadership
With experience and strong leadership, you may become a Test Lead. Test Leads manage testing teams. They develop test strategies and coordinate test activities. They ensure successful execution of test plans. This role needs technical skills and the ability to evaluate performance. It requires coaching, mentoring, and working well with cross-functional teams.
A Test Lead must balance technical skills and leadership. They must guide a team of testers to deliver high-quality software. As a Test Lead, you will define testing strategies and processes. You will also mentor junior testers to align them with project goals. You must communicate and decide well. You will bridge the gap between the dev team and stakeholders. Your goal is to ensure testing supports business objectives.
Career Advancement: Setting Your Goals
To advance from a Test Lead to a Test Manager or QA Director, set clear career goals. Then, create a roadmap for your growth. This may involve gaining industry knowledge and collaboration skills. It may also require mastering agile methods and seeking learning opportunities. These will help you stay ahead in the fast-changing field of software testing.
Clear career goals are key to long-term success. They give direction and motivation. Identify your strengths and areas for growth. Then, create a roadmap that aligns with your ambitions. Regularly reviewing and adjusting these goals ensures progress in a changing job market.
Software Deployment: Leading Project Delivery
As you advance in your career, you may lead software deployment projects. You will manage test environments, coordinate test activities, and ensure successful software delivery. This role needs strong leadership, risk management, and adaptability to change.
"Software Deployment: Leading Project Delivery" is your guide to mastering software delivery. It will help you master the end-to-end process of delivering robust software solutions. Learn the best practices. They ensure smooth rollouts, minimal downtime, and top system performance. This video gives you the tools to lead your next deployment project. It is for both project managers and developers.
How to obtain CTFL certification?
We are an Education Technology company providing certification training courses to accelerate careers of working professionals worldwide. We impart training through instructor-led classroom workshops, instructor-led live virtual training sessions, and self-paced e-learning courses.
We have successfully conducted training sessions in 108 countries across the globe and enabled thousands of working professionals to enhance the scope of their careers.
Our enterprise training portfolio includes in-demand and globally recognized certification training courses in Project Management, Quality Management, Business Analysis, IT Service Management, Agile and Scrum, Cyber Security, Data Science, and Emerging Technologies. Download our Enterprise Training Catalog from https://www.icertglobal.com/corporate-training-for-enterprises.php and https://www.icertglobal.com/index.php
Popular Courses include:
-
Project Management: PMP, CAPM ,PMI RMP
-
Quality Management: Six Sigma Black Belt ,Lean Six Sigma Green Belt, Lean Management, Minitab,CMMI
-
Business Analysis: CBAP, CCBA, ECBA
-
Agile Training: PMI-ACP , CSM , CSPO
-
Scrum Training: CSM
-
DevOps
-
Program Management: PgMP
-
Cloud Technology: Exin Cloud Computing
-
Citrix Client Adminisration: Citrix Cloud Administration
The 10 top-paying certifications to target in 2024 are:
Conclusion
In conclusion, the journey from Tester to Test Lead and beyond is rewarding. It offers many opportunities for career growth and success. Invest in skills, leadership, and learning. It will lead to a successful career in software testing and quality assurance. Are you ready to advance your career and unlock new growth opportunities?
Contact Us For More Information:
Visit : www.icertglobal.com Email : info@icertglobal.com
Using Lean Management to Boost Supply Chain Resilience!
In today's fast-changing business world, supply chain resilience is vital. Organizations must quickly adapt to disruptions and challenges. This is key to their success. A good way to boost supply chain resilience is to use lean management principles. Lean management aims to boost efficiency and productivity. It does this by eliminating waste, optimizing processes, and improving operations.
What is Lean Management?
Lean management is a set of principles and practices. They come from the Toyota Production System. It stresses the need for constant improvement and innovation. It also calls for waste reduction to achieve excellence. Organizations can improve their operations. They can do this by adding value for the customer and cutting waste. They can lower costs and boost performance.
How can Lean Management Benefit the Supply Chain?
Lean management can improve the supply chain. It eliminates waste, cuts inefficiencies, and optimizes resources. Lean practices help companies improve delivery times. They do this by streamlining processes. Lean methods also cut costs and boost flexibility to respond to market changes. Also, lean management boosts supply chain collaboration. This leads to better quality and higher customer satisfaction.
Lean management improves supply chain visibility. This leads to better demand forecasting and inventory management. It helps to reduce bottlenecks. It improves the flow of materials and information across the supply chain. This is due to a focus on continuous improvement. Also, lean principles promote a culture of problem-solving and accountability. This leads to quicker responses to disruptions and improved resilience.
-
Efficiency: Lean management techniques eliminate inefficiencies and bottlenecks in the supply chain. They help to streamline processes. This leads to smoother operations, faster lead times, and improved performance.
-
Productivity: Organizations can increase productivity by reducing waste and optimizing workflows. This will raise output without adding resources. This results in a more efficient and effective supply chain.
-
Cost-saving: Lean management techniques find and remove all waste. This includes excess inventory, overproduction, and inefficient processes. Reducing costs can improve profits and boost competitiveness in the market. Implementing Lean Management in the Supply Chain
-
Lean Principles: Organizations can apply lean principles to improve their supply chains. These include continuous improvement, value stream mapping, and just-in-time production.
-
Lean Tools: Lean tools, like kaizen events and 5S, can improve supply chains. Visual management can help too.
-
Lean Culture: A lean culture boosts employee engagement and teamwork. It fosters a constant focus on improving processes.
-
Lean Practices: Using lean practices can improve efficiency. These include standard work, pull systems, and mistake-proofing. Benefits of Lean Management in the Supply Chain
-
Optimization: Lean management helps firms optimize their supply chains. It boosts efficiency and performance.
-
Agility: Lean principles can make supply chains more agile. They will quickly adapt to changing markets and customer demands.
-
Resilience: Lean management boosts supply chain resilience. It does this by cutting waste, reducing lead times, and improving efficiency. Organizations can better withstand disruptions and challenges to ensure continuity and success.
How to obtain Lean Management certification?
We are an Education Technology company providing certification training courses to accelerate careers of working professionals worldwide. We impart training through instructor-led classroom workshops, instructor-led live virtual training sessions, and self-paced e-learning courses.
We have successfully conducted training sessions in 108 countries across the globe and enabled thousands of working professionals to enhance the scope of their careers.
Our enterprise training portfolio includes in-demand and globally recognized certification training courses in Project Management, Quality Management, Business Analysis, IT Service Management, Agile and Scrum, Cyber Security, Data Science, and Emerging Technologies. Download our Enterprise Training Catalog from https://www.icertglobal.com/corporate-training-for-enterprises.php and https://www.icertglobal.com/index.php
Popular Courses include:
-
Project Management: PMP, CAPM ,PMI RMP
-
Quality Management: Six Sigma Black Belt ,Lean Six Sigma Green Belt, Lean Management, Minitab,CMMI
-
Business Analysis: CBAP, CCBA, ECBA
-
Agile Training: PMI-ACP , CSM , CSPO
-
Scrum Training: CSM
-
DevOps
-
Program Management: PgMP
-
Cloud Technology: Exin Cloud Computing
-
Citrix Client Adminisration: Citrix Cloud Administration
The 10 top-paying certifications to target in 2024 are:
Conclusion
In conclusion, lean management is key to boosting supply chain resilience. It is vital for organizations to thrive in today's fast-changing business world. Organizations can improve by using lean principles, tools, and practices. They can optimize operations, increase efficiency, and boost performance. Lean management helps organizations cut costs and boost productivity. It also builds a more resilient, agile supply chain. This supply chain can adapt to any challenge or opportunity.
Contact Us For More Information:
Visit : www.icertglobal.com Email : info@icertglobal.com
Read More
In today's fast-changing business world, supply chain resilience is vital. Organizations must quickly adapt to disruptions and challenges. This is key to their success. A good way to boost supply chain resilience is to use lean management principles. Lean management aims to boost efficiency and productivity. It does this by eliminating waste, optimizing processes, and improving operations.
What is Lean Management?
Lean management is a set of principles and practices. They come from the Toyota Production System. It stresses the need for constant improvement and innovation. It also calls for waste reduction to achieve excellence. Organizations can improve their operations. They can do this by adding value for the customer and cutting waste. They can lower costs and boost performance.
How can Lean Management Benefit the Supply Chain?
Lean management can improve the supply chain. It eliminates waste, cuts inefficiencies, and optimizes resources. Lean practices help companies improve delivery times. They do this by streamlining processes. Lean methods also cut costs and boost flexibility to respond to market changes. Also, lean management boosts supply chain collaboration. This leads to better quality and higher customer satisfaction.
Lean management improves supply chain visibility. This leads to better demand forecasting and inventory management. It helps to reduce bottlenecks. It improves the flow of materials and information across the supply chain. This is due to a focus on continuous improvement. Also, lean principles promote a culture of problem-solving and accountability. This leads to quicker responses to disruptions and improved resilience.
-
Efficiency: Lean management techniques eliminate inefficiencies and bottlenecks in the supply chain. They help to streamline processes. This leads to smoother operations, faster lead times, and improved performance.
-
Productivity: Organizations can increase productivity by reducing waste and optimizing workflows. This will raise output without adding resources. This results in a more efficient and effective supply chain.
-
Cost-saving: Lean management techniques find and remove all waste. This includes excess inventory, overproduction, and inefficient processes. Reducing costs can improve profits and boost competitiveness in the market. Implementing Lean Management in the Supply Chain
-
Lean Principles: Organizations can apply lean principles to improve their supply chains. These include continuous improvement, value stream mapping, and just-in-time production.
-
Lean Tools: Lean tools, like kaizen events and 5S, can improve supply chains. Visual management can help too.
-
Lean Culture: A lean culture boosts employee engagement and teamwork. It fosters a constant focus on improving processes.
-
Lean Practices: Using lean practices can improve efficiency. These include standard work, pull systems, and mistake-proofing. Benefits of Lean Management in the Supply Chain
-
Optimization: Lean management helps firms optimize their supply chains. It boosts efficiency and performance.
-
Agility: Lean principles can make supply chains more agile. They will quickly adapt to changing markets and customer demands.
-
Resilience: Lean management boosts supply chain resilience. It does this by cutting waste, reducing lead times, and improving efficiency. Organizations can better withstand disruptions and challenges to ensure continuity and success.
How to obtain Lean Management certification?
We are an Education Technology company providing certification training courses to accelerate careers of working professionals worldwide. We impart training through instructor-led classroom workshops, instructor-led live virtual training sessions, and self-paced e-learning courses.
We have successfully conducted training sessions in 108 countries across the globe and enabled thousands of working professionals to enhance the scope of their careers.
Our enterprise training portfolio includes in-demand and globally recognized certification training courses in Project Management, Quality Management, Business Analysis, IT Service Management, Agile and Scrum, Cyber Security, Data Science, and Emerging Technologies. Download our Enterprise Training Catalog from https://www.icertglobal.com/corporate-training-for-enterprises.php and https://www.icertglobal.com/index.php
Popular Courses include:
-
Project Management: PMP, CAPM ,PMI RMP
-
Quality Management: Six Sigma Black Belt ,Lean Six Sigma Green Belt, Lean Management, Minitab,CMMI
-
Business Analysis: CBAP, CCBA, ECBA
-
Agile Training: PMI-ACP , CSM , CSPO
-
Scrum Training: CSM
-
DevOps
-
Program Management: PgMP
-
Cloud Technology: Exin Cloud Computing
-
Citrix Client Adminisration: Citrix Cloud Administration
The 10 top-paying certifications to target in 2024 are:
Conclusion
In conclusion, lean management is key to boosting supply chain resilience. It is vital for organizations to thrive in today's fast-changing business world. Organizations can improve by using lean principles, tools, and practices. They can optimize operations, increase efficiency, and boost performance. Lean management helps organizations cut costs and boost productivity. It also builds a more resilient, agile supply chain. This supply chain can adapt to any challenge or opportunity.
Contact Us For More Information:
Visit : www.icertglobal.com Email : info@icertglobal.com
Lean Management Interview: Key Questions & Expert Answers
1. What is Lean Management, and why is it important in an organization?
Answer: Lean Management is a systematic approach focused on continuous improvement by minimizing waste and maximizing value. It originated from Toyota's production system and aims to streamline processes, improve efficiency, and enhance customer satisfaction. It's important because it helps organizations reduce costs, improve product quality, and respond faster to market changes.
2.Can you explain the 5 Lean Principles?
Answer: The 5 Lean Principles are:
- Value: Identifying what customers consider valuable.
- Value Stream: Mapping out all steps in the process to highlight waste.
- Flow: Ensuring that processes run smoothly without interruptions.
- Pull: Producing only what is needed based on customer demand.
- Perfection: Continuously seeking ways to reduce waste and improve processes.
3.What is "waste" in Lean Management, and can you name the 7 types of waste?
Answer: In Lean Management, "waste" refers to any activity or process that does not add value to the customer. The 7 types of waste are:
- Overproduction: Producing more than needed.
- Waiting: Idle time due to delays.
- Transport: Unnecessary movement of materials.
- Extra Processing: Adding more steps than required.
- Inventory: Excess stock that is not needed immediately.
- Motion: Unnecessary movement of people.
- Defects: Efforts involved in inspecting and fixing errors.
4.What is the difference between Lean and Six Sigma?
Answer: While both Lean and Six Sigma focus on process improvement, their approaches differ. Lean emphasizes waste reduction and continuous flow in processes, while Six Sigma focuses on reducing process variation and defects through statistical analysis. Combining both approaches, known as Lean Six Sigma, allows organizations to improve efficiency and quality simultaneously.
5.How do you implement Lean in a non-manufacturing environment?
Answer: Lean principles can be applied in various settings, including services, healthcare, and IT. The key is to map the processes, identify value from the customer's perspective, and eliminate waste. For example, in a service environment, Lean can help streamline customer interactions, reduce processing times, and enhance service quality.
6.What is Kaizen, and how does it relate to Lean Management?
Answer: Kaizen is a Japanese term meaning "continuous improvement." In Lean Management, Kaizen focuses on small, incremental changes that result in significant long-term improvements. It encourages employees at all levels to contribute ideas for process optimization, reinforcing a culture of continuous improvement within the organization.
7.How would you handle resistance to Lean implementation within an organization?
Answer: Resistance to Lean implementation often stems from a fear of change or a lack of understanding. To handle this, it’s essential to communicate the benefits of Lean, provide proper training, involve employees in decision-making, and demonstrate success through small wins. Showing how Lean can make their work easier and more efficient can help gain buy-in.
8.Can you provide an example of a Lean tool you have used in a previous role?
Answer: One common Lean tool is the 5S methodology (Sort, Set in order, Shine, Standardize, Sustain). For example, in a previous role, I implemented 5S in our workspace, resulting in improved organization, reduced search times, and enhanced productivity. The visual control aspect of 5S helped maintain a clean and efficient environment.
9.What is a Value Stream Map, and how do you use it in Lean Management?
Answer: A Value Stream Map (VSM) is a visual tool that outlines all steps in a process, from start to finish, to identify value-added and non-value-added activities. In Lean Management, VSM helps to identify waste, inefficiencies, and bottlenecks. By analyzing the current state, teams can develop an optimized future state map to streamline processes.
10.How do you measure the success of Lean initiatives?
Answer: Success in Lean initiatives can be measured using key performance indicators (KPIs) like reduced cycle time, decreased waste, increased throughput, improved quality, higher customer satisfaction, and cost savings. Regular reviews and continuous monitoring ensure that improvements are sustained and further enhanced.
How to obtain Lean Management Certification?
We are an Education Technology company providing certification training courses to accelerate careers of working professionals worldwide. We impart training through instructor-led classroom workshops, instructor-led live virtual training sessions, and self-paced e-learning courses.
We have successfully conducted training sessions in 108 countries across the globe and enabled thousands of working professionals to enhance the scope of their careers.
Our enterprise training portfolio includes in-demand and globally recognized certification training courses in Project Management, Quality Management, Business Analysis, IT Service Management, Agile and Scrum, Cyber Security, Data Science, and Emerging Technologies. Download our Enterprise Training Catalog from https://www.icertglobal.com/corporate-training-for-enterprises.php and https://www.icertglobal.com/index.php
Popular Courses include:
- Project Management: PMP, CAPM ,PMI RMP
- Quality Management: Six Sigma Black Belt ,Lean Six Sigma Green Belt, Lean Management, Minitab,CMMI
- Business Analysis: CBAP, CCBA, ECBA
- Agile Training: PMI-ACP , CSM , CSPO
- Scrum Training: CSM
- DevOps
- Program Management: PgMP
- Cloud Technology: Exin Cloud Computing
- Citrix Client Adminisration: Citrix Cloud Administration
The 10 top-paying certifications to target in 2024 are:
- Certified Information Systems Security Professional® (CISSP)
- AWS Certified Solutions Architect
- Google Certified Professional Cloud Architect
- Big Data Certification
- Data Science Certification
- Certified In Risk And Information Systems Control (CRISC)
- Certified Information Security Manager(CISM)
- Project Management Professional (PMP)® Certification
- Certified Ethical Hacker (CEH)
- Certified Scrum Master (CSM)
Conclusion
In conclusion, Lean Management is an effective approach for organizations aiming to enhance their efficiency, reduce waste, and maximize value delivery to customers. It requires a cultural shift and a commitment to continuous improvement. Interviewing candidates on their understanding of Lean principles, tools, and practices helps identify those who can drive process optimization and build a culture of operational excellence. Candidates proficient in Lean methodologies can significantly contribute to achieving long-term business success.
Contact Us :
Contact Us For More Information:
Visit :www.icertglobal.com Email : info@icertglobal.com
Read More
1. What is Lean Management, and why is it important in an organization?
Answer: Lean Management is a systematic approach focused on continuous improvement by minimizing waste and maximizing value. It originated from Toyota's production system and aims to streamline processes, improve efficiency, and enhance customer satisfaction. It's important because it helps organizations reduce costs, improve product quality, and respond faster to market changes.
2.Can you explain the 5 Lean Principles?
Answer: The 5 Lean Principles are:
- Value: Identifying what customers consider valuable.
- Value Stream: Mapping out all steps in the process to highlight waste.
- Flow: Ensuring that processes run smoothly without interruptions.
- Pull: Producing only what is needed based on customer demand.
- Perfection: Continuously seeking ways to reduce waste and improve processes.
3.What is "waste" in Lean Management, and can you name the 7 types of waste?
Answer: In Lean Management, "waste" refers to any activity or process that does not add value to the customer. The 7 types of waste are:
- Overproduction: Producing more than needed.
- Waiting: Idle time due to delays.
- Transport: Unnecessary movement of materials.
- Extra Processing: Adding more steps than required.
- Inventory: Excess stock that is not needed immediately.
- Motion: Unnecessary movement of people.
- Defects: Efforts involved in inspecting and fixing errors.
4.What is the difference between Lean and Six Sigma?
Answer: While both Lean and Six Sigma focus on process improvement, their approaches differ. Lean emphasizes waste reduction and continuous flow in processes, while Six Sigma focuses on reducing process variation and defects through statistical analysis. Combining both approaches, known as Lean Six Sigma, allows organizations to improve efficiency and quality simultaneously.
5.How do you implement Lean in a non-manufacturing environment?
Answer: Lean principles can be applied in various settings, including services, healthcare, and IT. The key is to map the processes, identify value from the customer's perspective, and eliminate waste. For example, in a service environment, Lean can help streamline customer interactions, reduce processing times, and enhance service quality.
6.What is Kaizen, and how does it relate to Lean Management?
Answer: Kaizen is a Japanese term meaning "continuous improvement." In Lean Management, Kaizen focuses on small, incremental changes that result in significant long-term improvements. It encourages employees at all levels to contribute ideas for process optimization, reinforcing a culture of continuous improvement within the organization.
7.How would you handle resistance to Lean implementation within an organization?
Answer: Resistance to Lean implementation often stems from a fear of change or a lack of understanding. To handle this, it’s essential to communicate the benefits of Lean, provide proper training, involve employees in decision-making, and demonstrate success through small wins. Showing how Lean can make their work easier and more efficient can help gain buy-in.
8.Can you provide an example of a Lean tool you have used in a previous role?
Answer: One common Lean tool is the 5S methodology (Sort, Set in order, Shine, Standardize, Sustain). For example, in a previous role, I implemented 5S in our workspace, resulting in improved organization, reduced search times, and enhanced productivity. The visual control aspect of 5S helped maintain a clean and efficient environment.
9.What is a Value Stream Map, and how do you use it in Lean Management?
Answer: A Value Stream Map (VSM) is a visual tool that outlines all steps in a process, from start to finish, to identify value-added and non-value-added activities. In Lean Management, VSM helps to identify waste, inefficiencies, and bottlenecks. By analyzing the current state, teams can develop an optimized future state map to streamline processes.
10.How do you measure the success of Lean initiatives?
Answer: Success in Lean initiatives can be measured using key performance indicators (KPIs) like reduced cycle time, decreased waste, increased throughput, improved quality, higher customer satisfaction, and cost savings. Regular reviews and continuous monitoring ensure that improvements are sustained and further enhanced.
How to obtain Lean Management Certification?
We are an Education Technology company providing certification training courses to accelerate careers of working professionals worldwide. We impart training through instructor-led classroom workshops, instructor-led live virtual training sessions, and self-paced e-learning courses.
We have successfully conducted training sessions in 108 countries across the globe and enabled thousands of working professionals to enhance the scope of their careers.
Our enterprise training portfolio includes in-demand and globally recognized certification training courses in Project Management, Quality Management, Business Analysis, IT Service Management, Agile and Scrum, Cyber Security, Data Science, and Emerging Technologies. Download our Enterprise Training Catalog from https://www.icertglobal.com/corporate-training-for-enterprises.php and https://www.icertglobal.com/index.php
Popular Courses include:
- Project Management: PMP, CAPM ,PMI RMP
- Quality Management: Six Sigma Black Belt ,Lean Six Sigma Green Belt, Lean Management, Minitab,CMMI
- Business Analysis: CBAP, CCBA, ECBA
- Agile Training: PMI-ACP , CSM , CSPO
- Scrum Training: CSM
- DevOps
- Program Management: PgMP
- Cloud Technology: Exin Cloud Computing
- Citrix Client Adminisration: Citrix Cloud Administration
The 10 top-paying certifications to target in 2024 are:
- Certified Information Systems Security Professional® (CISSP)
- AWS Certified Solutions Architect
- Google Certified Professional Cloud Architect
- Big Data Certification
- Data Science Certification
- Certified In Risk And Information Systems Control (CRISC)
- Certified Information Security Manager(CISM)
- Project Management Professional (PMP)® Certification
- Certified Ethical Hacker (CEH)
- Certified Scrum Master (CSM)
Conclusion
In conclusion, Lean Management is an effective approach for organizations aiming to enhance their efficiency, reduce waste, and maximize value delivery to customers. It requires a cultural shift and a commitment to continuous improvement. Interviewing candidates on their understanding of Lean principles, tools, and practices helps identify those who can drive process optimization and build a culture of operational excellence. Candidates proficient in Lean methodologies can significantly contribute to achieving long-term business success.
Contact Us :
Contact Us For More Information:
Visit :www.icertglobal.com Email : info@icertglobal.com
CMMI 2.0 Key Updates and Benefits: What You Need to Know
In software development, project management, and quality improvement, it's vital to stay current on the latest methods. They are key to success. One such framework is the Capability Maturity Model Integration (CMMI). It has recently undergone significant updates. In this article, we will explore the key updates and benefits of CMMI 2.0, the latest version of this renowned model.
What's New in CMMI 2.0?
CMMI 2.0 has many new features. They aim to help organizations improve their processes, quality, and maturity. Key changes include a more flexible framework, updated processes, and better appraisals.
CMMI 2.0 introduces faster, more efficient appraisal methods. It also emphasizes agile practices. This lets organizations combine CMMI with modern development methods. It also focuses on performance outcomes. So, process improvements must help achieve business goals.
Benefits of CMMI 2.0
Improved Process Efficiency
One of the main benefits of CMMI 2.0 is its focus on improving process efficiency. By implementing best practices and standardized processes, organizations can reduce waste, lower costs, and deliver higher quality products and services.
Enhanced Quality
With a strong emphasis on quality improvement, CMMI 2.0 helps organizations ensure that their products and services meet the highest standards. By following the guidelines and practices outlined in the framework, companies can enhance customer satisfaction and build a reputation for excellence.
Increased Maturity Levels
CMMI 2.0 offers a roadmap for organizations to increase their maturity levels and progress towards becoming high-performing entities. By following the guidelines and best practices, companies can mature their processes, improve performance, and drive continuous improvement.
Certification and Compliance
By achieving CMMI 2.0 certification, organizations can demonstrate their commitment to quality, efficiency, and continuous improvement. This certification can not only help companies attract new business and clients but also ensure compliance with industry standards and regulations.
CMMI 2.0 Features and Updates
CMMI 2.0 offers a flexible, scalable framework. It can be tailored to fit the needs of different organizations. The model now includes new process areas, appraisal methods, and maturity levels. It gives companies a complete guide to improving their processes and performance.
CMMI 2.0 has major updates. It has a new, simpler model structure. This makes it easier to use and implement. The new version stresses performance management. It focuses on results and outcomes, not just compliance with processes. Also, CMMI 2.0 adds digital transformation practices. It gives organizations new guidelines to navigate today's tech.
Advantages of CMMI 2.0
Tailored for Different Industries
CMMI 2.0 is designed to be flexible and adaptable, making it suitable for a wide range of industries and sectors. CMMI 2.0 can be customized to fit your organization's needs. This applies to software development, project management, and quality improvement.
Enhanced Project Management
CMMI 2.0's guidelines can help organizations improve project management. It will boost efficiency, cut risks, and improve results. The framework offers a method to manage projects. It ensures they finish on time and within budget.
Streamlined Processes
CMMI 2.0 helps organizations streamline their processes. It does this by providing a standardized set of practices and guidelines. These best practices can help companies. They will reduce waste, improve communication, and boost productivity. This will lead to better results and higher customer satisfaction.
Continuous Improvement
One of the key benefits of CMMI 2.0 is its focus on continuous improvement. By following the model's guidelines, organizations can improve. They can find areas for enhancement, implement changes, and measure their impact. This will create a culture of continuous learning and improvement.
How to obtain CMMI certification?
We are an Education Technology company providing certification training courses to accelerate careers of working professionals worldwide. We impart training through instructor-led classroom workshops, instructor-led live virtual training sessions, and self-paced e-learning courses.
We have successfully conducted training sessions in 108 countries across the globe and enabled thousands of working professionals to enhance the scope of their careers.
Our enterprise training portfolio includes in-demand and globally recognized certification training courses in Project Management, Quality Management, Business Analysis, IT Service Management, Agile and Scrum, Cyber Security, Data Science, and Emerging Technologies. Download our Enterprise Training Catalog from https://www.icertglobal.com/corporate-training-for-enterprises.php and https://www.icertglobal.com/index.php
Popular Courses include:
-
Project Management: PMP, CAPM ,PMI RMP
-
Quality Management: Six Sigma Black Belt ,Lean Six Sigma Green Belt, Lean Management, Minitab,CMMI
-
Business Analysis: CBAP, CCBA, ECBA
-
Agile Training: PMI-ACP , CSM , CSPO
-
Scrum Training: CSM
-
DevOps
-
Program Management: PgMP
-
Cloud Technology: Exin Cloud Computing
-
Citrix Client Adminisration: Citrix Cloud Administration
The 10 top-paying certifications to target in 2024 are:
Conclusion
In conclusion, CMMI 2.0 has many updates and benefits. They can help organizations improve processes, enhance quality, and boost performance. This framework will help companies. It will streamline operations, raise maturity levels, and drive improvement. In the end, it will boost their success and competitiveness in the market.
Contact Us For More Information:
Visit : www.icertglobal.com Email : info@icertglobal.com
Read More
In software development, project management, and quality improvement, it's vital to stay current on the latest methods. They are key to success. One such framework is the Capability Maturity Model Integration (CMMI). It has recently undergone significant updates. In this article, we will explore the key updates and benefits of CMMI 2.0, the latest version of this renowned model.
What's New in CMMI 2.0?
CMMI 2.0 has many new features. They aim to help organizations improve their processes, quality, and maturity. Key changes include a more flexible framework, updated processes, and better appraisals.
CMMI 2.0 introduces faster, more efficient appraisal methods. It also emphasizes agile practices. This lets organizations combine CMMI with modern development methods. It also focuses on performance outcomes. So, process improvements must help achieve business goals.
Benefits of CMMI 2.0
Improved Process Efficiency
One of the main benefits of CMMI 2.0 is its focus on improving process efficiency. By implementing best practices and standardized processes, organizations can reduce waste, lower costs, and deliver higher quality products and services.
Enhanced Quality
With a strong emphasis on quality improvement, CMMI 2.0 helps organizations ensure that their products and services meet the highest standards. By following the guidelines and practices outlined in the framework, companies can enhance customer satisfaction and build a reputation for excellence.
Increased Maturity Levels
CMMI 2.0 offers a roadmap for organizations to increase their maturity levels and progress towards becoming high-performing entities. By following the guidelines and best practices, companies can mature their processes, improve performance, and drive continuous improvement.
Certification and Compliance
By achieving CMMI 2.0 certification, organizations can demonstrate their commitment to quality, efficiency, and continuous improvement. This certification can not only help companies attract new business and clients but also ensure compliance with industry standards and regulations.
CMMI 2.0 Features and Updates
CMMI 2.0 offers a flexible, scalable framework. It can be tailored to fit the needs of different organizations. The model now includes new process areas, appraisal methods, and maturity levels. It gives companies a complete guide to improving their processes and performance.
CMMI 2.0 has major updates. It has a new, simpler model structure. This makes it easier to use and implement. The new version stresses performance management. It focuses on results and outcomes, not just compliance with processes. Also, CMMI 2.0 adds digital transformation practices. It gives organizations new guidelines to navigate today's tech.
Advantages of CMMI 2.0
Tailored for Different Industries
CMMI 2.0 is designed to be flexible and adaptable, making it suitable for a wide range of industries and sectors. CMMI 2.0 can be customized to fit your organization's needs. This applies to software development, project management, and quality improvement.
Enhanced Project Management
CMMI 2.0's guidelines can help organizations improve project management. It will boost efficiency, cut risks, and improve results. The framework offers a method to manage projects. It ensures they finish on time and within budget.
Streamlined Processes
CMMI 2.0 helps organizations streamline their processes. It does this by providing a standardized set of practices and guidelines. These best practices can help companies. They will reduce waste, improve communication, and boost productivity. This will lead to better results and higher customer satisfaction.
Continuous Improvement
One of the key benefits of CMMI 2.0 is its focus on continuous improvement. By following the model's guidelines, organizations can improve. They can find areas for enhancement, implement changes, and measure their impact. This will create a culture of continuous learning and improvement.
How to obtain CMMI certification?
We are an Education Technology company providing certification training courses to accelerate careers of working professionals worldwide. We impart training through instructor-led classroom workshops, instructor-led live virtual training sessions, and self-paced e-learning courses.
We have successfully conducted training sessions in 108 countries across the globe and enabled thousands of working professionals to enhance the scope of their careers.
Our enterprise training portfolio includes in-demand and globally recognized certification training courses in Project Management, Quality Management, Business Analysis, IT Service Management, Agile and Scrum, Cyber Security, Data Science, and Emerging Technologies. Download our Enterprise Training Catalog from https://www.icertglobal.com/corporate-training-for-enterprises.php and https://www.icertglobal.com/index.php
Popular Courses include:
-
Project Management: PMP, CAPM ,PMI RMP
-
Quality Management: Six Sigma Black Belt ,Lean Six Sigma Green Belt, Lean Management, Minitab,CMMI
-
Business Analysis: CBAP, CCBA, ECBA
-
Agile Training: PMI-ACP , CSM , CSPO
-
Scrum Training: CSM
-
DevOps
-
Program Management: PgMP
-
Cloud Technology: Exin Cloud Computing
-
Citrix Client Adminisration: Citrix Cloud Administration
The 10 top-paying certifications to target in 2024 are:
Conclusion
In conclusion, CMMI 2.0 has many updates and benefits. They can help organizations improve processes, enhance quality, and boost performance. This framework will help companies. It will streamline operations, raise maturity levels, and drive improvement. In the end, it will boost their success and competitiveness in the market.
Contact Us For More Information:
Visit : www.icertglobal.com Email : info@icertglobal.com
Visualizing Data Trends Minitabs Graphical Capabilities
Are you looking to gain valuable insights from your data analysis? Minitab's graphical capabilities provide a powerful tool for visualizing data trends and patterns. This article will explore how Minitab's graphs can help you. They can analyze data, interpret trends, and aid decision-making.
Introduction to Minitab and Data Visualization
Minitab is a top statistical software. It's widely used for data analysis and visualization. Its user-friendly interface and strong tools make it popular with researchers, analysts, and data scientists. A key feature of Minitab is its graphics. Users can create various graphs and charts to show data trends.
Analyzing Trends with Graphical Data Analysis
Graphical data analysis of trends uses visuals to find patterns and changes in data over time. Minitab offers a range of graphing tools, such as time series plots and control charts, to help users easily spot trends and anomalies. These tools can help you see your data better. You can then make better decisions based on the trends you find.
When it comes to data analysis, one of the most effective ways to identify trends and patterns is through visual representation. Minitab has many graph types, including line graphs, bar charts, and scatter plots. They can help you visualize your data and find relationships between variables. These graphs can deepen your understanding of your data. You can then make better decisions.
Interpreting Data Trends with Visual Analytics
Visual analytics is a data analysis method. It combines interactive visualization with analytical techniques. It helps to explore data, find trends, and gain insights. Minitab's graphical tools let you explore your data. You can find trends and hidden patterns that traditional analysis may miss. This visual method lets you quickly find outliers, anomalies, and correlations in your data. It leads to better, more reliable insights.
"Visual analytics in Minitab helps find data trends. It turns complex datasets into clear, actionable insights." By leveraging various charts and graphs, you can easily spot patterns, anomalies, and correlations that might be missed in raw data. "Using these visual tools improves your analysis and decision-making. It helps you make better decisions based on trend analysis.""
Trend Analysis and Data Visualization Techniques
Minitab's graphs include advanced data visualization techniques. They can help you analyze trends and patterns in your data. You can easily visualize data trends using trend graphs and charts. You can also compare data sets and track changes over time. Also, Minitab has many visualization tools. They let you customize your graphs and add annotations. You can also create interactive data displays for more engaging presentations.
Trend analysis and data visualization are key for finding patterns in large datasets. Use tools like Minitab to create visualizations. They include line charts, scatter plots, and control charts. They highlight trends and anomalies. These techniques improve your data analysis. They also help you communicate findings to stakeholders.
Exploring Data Trends with Minitab Software
With Minitab's graphical capabilities, exploring data trends has never been easier. Minitab's graphical tools can analyze sales data, customer feedback, or research. They help you visualize trends, interpret data, and present your findings clearly. Use Minitab's data visualization tools. They can unlock your data's full potential. They can also provide insights for better decision-making.
Unlock your data's potential. Explore trends with Minitab Software. It is a powerful tool for detailed statistical analysis. Minitab has strong graphics and statistical tools. It helps you find and see patterns. This makes it easier to uncover insights and make decisions. Minitab's trend analysis features reveal your data's story. They provide a clear, actionable view, whether you're analyzing sales or quality metrics.
How to obtain Minitab certification?
We are an Education Technology company providing certification training courses to accelerate careers of working professionals worldwide. We impart training through instructor-led classroom workshops, instructor-led live virtual training sessions, and self-paced e-learning courses.
We have successfully conducted training sessions in 108 countries across the globe and enabled thousands of working professionals to enhance the scope of their careers.
Our enterprise training portfolio includes in-demand and globally recognized certification training courses in Project Management, Quality Management, Business Analysis, IT Service Management, Agile and Scrum, Cyber Security, Data Science, and Emerging Technologies. Download our Enterprise Training Catalog from https://www.icertglobal.com/corporate-training-for-enterprises.php and https://www.icertglobal.com/index.php
Popular Courses include:
-
Project Management: PMP, CAPM ,PMI RMP
-
Quality Management: Six Sigma Black Belt ,Lean Six Sigma Green Belt, Lean Management, Minitab,CMMI
-
Business Analysis: CBAP, CCBA, ECBA
-
Agile Training: PMI-ACP , CSM , CSPO
-
Scrum Training: CSM
-
DevOps
-
Program Management: PgMP
-
Cloud Technology: Exin Cloud Computing
-
Citrix Client Adminisration: Citrix Cloud Administration
The 10 top-paying certifications to target in 2024 are:
Conclusion
In conclusion, Minitab's graphs are a powerful tool. They help to visualize data trends, analyze patterns, and interpret data better. Minitab's graphical tools let you explore data trends. You can find relationships and generate insights. These can help you make data-driven decisions. Minitab's graphs can improve your data analysis workflow. They will show your data trends visually, which is valuable for researchers, analysts, and data scientists. So why wait? Use Minitab's graphical tools to analyze your data. Start visualizing your data trends today!
Contact Us For More Information:
Visit : www.icertglobal.com Email : info@icertglobal.com
Read More
Are you looking to gain valuable insights from your data analysis? Minitab's graphical capabilities provide a powerful tool for visualizing data trends and patterns. This article will explore how Minitab's graphs can help you. They can analyze data, interpret trends, and aid decision-making.
Introduction to Minitab and Data Visualization
Minitab is a top statistical software. It's widely used for data analysis and visualization. Its user-friendly interface and strong tools make it popular with researchers, analysts, and data scientists. A key feature of Minitab is its graphics. Users can create various graphs and charts to show data trends.
Analyzing Trends with Graphical Data Analysis
Graphical data analysis of trends uses visuals to find patterns and changes in data over time. Minitab offers a range of graphing tools, such as time series plots and control charts, to help users easily spot trends and anomalies. These tools can help you see your data better. You can then make better decisions based on the trends you find.
When it comes to data analysis, one of the most effective ways to identify trends and patterns is through visual representation. Minitab has many graph types, including line graphs, bar charts, and scatter plots. They can help you visualize your data and find relationships between variables. These graphs can deepen your understanding of your data. You can then make better decisions.
Interpreting Data Trends with Visual Analytics
Visual analytics is a data analysis method. It combines interactive visualization with analytical techniques. It helps to explore data, find trends, and gain insights. Minitab's graphical tools let you explore your data. You can find trends and hidden patterns that traditional analysis may miss. This visual method lets you quickly find outliers, anomalies, and correlations in your data. It leads to better, more reliable insights.
"Visual analytics in Minitab helps find data trends. It turns complex datasets into clear, actionable insights." By leveraging various charts and graphs, you can easily spot patterns, anomalies, and correlations that might be missed in raw data. "Using these visual tools improves your analysis and decision-making. It helps you make better decisions based on trend analysis.""
Trend Analysis and Data Visualization Techniques
Minitab's graphs include advanced data visualization techniques. They can help you analyze trends and patterns in your data. You can easily visualize data trends using trend graphs and charts. You can also compare data sets and track changes over time. Also, Minitab has many visualization tools. They let you customize your graphs and add annotations. You can also create interactive data displays for more engaging presentations.
Trend analysis and data visualization are key for finding patterns in large datasets. Use tools like Minitab to create visualizations. They include line charts, scatter plots, and control charts. They highlight trends and anomalies. These techniques improve your data analysis. They also help you communicate findings to stakeholders.
Exploring Data Trends with Minitab Software
With Minitab's graphical capabilities, exploring data trends has never been easier. Minitab's graphical tools can analyze sales data, customer feedback, or research. They help you visualize trends, interpret data, and present your findings clearly. Use Minitab's data visualization tools. They can unlock your data's full potential. They can also provide insights for better decision-making.
Unlock your data's potential. Explore trends with Minitab Software. It is a powerful tool for detailed statistical analysis. Minitab has strong graphics and statistical tools. It helps you find and see patterns. This makes it easier to uncover insights and make decisions. Minitab's trend analysis features reveal your data's story. They provide a clear, actionable view, whether you're analyzing sales or quality metrics.
How to obtain Minitab certification?
We are an Education Technology company providing certification training courses to accelerate careers of working professionals worldwide. We impart training through instructor-led classroom workshops, instructor-led live virtual training sessions, and self-paced e-learning courses.
We have successfully conducted training sessions in 108 countries across the globe and enabled thousands of working professionals to enhance the scope of their careers.
Our enterprise training portfolio includes in-demand and globally recognized certification training courses in Project Management, Quality Management, Business Analysis, IT Service Management, Agile and Scrum, Cyber Security, Data Science, and Emerging Technologies. Download our Enterprise Training Catalog from https://www.icertglobal.com/corporate-training-for-enterprises.php and https://www.icertglobal.com/index.php
Popular Courses include:
-
Project Management: PMP, CAPM ,PMI RMP
-
Quality Management: Six Sigma Black Belt ,Lean Six Sigma Green Belt, Lean Management, Minitab,CMMI
-
Business Analysis: CBAP, CCBA, ECBA
-
Agile Training: PMI-ACP , CSM , CSPO
-
Scrum Training: CSM
-
DevOps
-
Program Management: PgMP
-
Cloud Technology: Exin Cloud Computing
-
Citrix Client Adminisration: Citrix Cloud Administration
The 10 top-paying certifications to target in 2024 are:
Conclusion
In conclusion, Minitab's graphs are a powerful tool. They help to visualize data trends, analyze patterns, and interpret data better. Minitab's graphical tools let you explore data trends. You can find relationships and generate insights. These can help you make data-driven decisions. Minitab's graphs can improve your data analysis workflow. They will show your data trends visually, which is valuable for researchers, analysts, and data scientists. So why wait? Use Minitab's graphical tools to analyze your data. Start visualizing your data trends today!
Contact Us For More Information:
Visit : www.icertglobal.com Email : info@icertglobal.com
Strategies for Effective Quality Control in Manufacturing
In manufacturing, high-quality products are key to success. Good quality control can help companies. It can maintain consistency, meet regulations, and improve customer satisfaction. This article will discuss ways to ensure quality in manufacturing.
Importance of Quality Control in Manufacturing
Quality control is key in manufacturing. It ensures products meet customer and legal standards. Companies can reduce defects and improve efficiency by using effective quality control. It will also ensure consistent products. This ultimately leads to higher customer satisfaction and increased profitability.
Quality control in manufacturing is vital. It ensures product consistency and meets industry standards. This builds customer trust and satisfaction. QC minimizes waste, cuts costs, and boosts efficiency. It does this by finding and fixing defects early. Also, good quality control helps meet regulations. It builds a strong brand. This drives long-term success and competitiveness in the market.
Best Practices for Quality Control
-
Establish Quality Control Standards: First, set clear quality control standards. This is key to ensuring product consistency and reliability. These standards should detail the criteria for acceptable products.
-
Implement Quality Control Procedures: Develop standard tests to inspect for quality. This will ensure products meet the established standards. Regularly monitor and evaluate these procedures to identify areas for improvement.
-
Use Quality Control Tools: Give your team the tools to test and inspect products. This can include equipment for measurements, testing, and inspection software.
-
Develop a Quality Control Plan: Create a plan. It must detail how to implement quality control measures in manufacturing. This plan should detail responsibilities, procedures, and processes for quality control.
-
Train Your Team: Provide ongoing training for your quality control team. This will ensure they have the skills to do their jobs well. Regular training can help improve the accuracy and efficiency of quality control measures.
Quality Control Methods in Manufacturing
-
Statistical Process Control (SPC): SPC is a method to monitor and control processes. It ensures they stay within specifications. Manufacturers can find trends by analyzing data. They can then adjust to maintain product quality.
-
Six Sigma is a data-driven quality control method. It aims to reduce defects and variations in manufacturing processes. Six Sigma can help companies improve quality, cut costs, and boost customer satisfaction.
-
Lean Manufacturing: It aims to cut waste and boost efficiency in manufacturing. By streamlining operations, companies can improve product quality and cut lead times.
Quality Control Challenges
Manufacturing often faces quality control (QC) challenges. They can hurt product consistency and efficiency. QC efforts often face issues. They are: detecting defects early, standardizing processes, and ensuring compliance with laws. We must use a strategic approach to tackle these challenges. We should use advanced tech and ongoing training. They will improve accuracy and effectiveness in quality management.
Quality control is vital for manufacturing success. But, companies may face challenges in implementing it. Some common challenges include:
-
Ensuring consistency in product quality across different production lines and locations
-
Managing supplier quality control to ensure the reliability of raw materials
-
Adapting to changing regulations and industry standards is tough. It requires a complete quality control approach. This must include continuous improvement, communication, and collaboration across departments.
Implementing Effective Quality Control Measures
To ensure the success of quality control measures in manufacturing, companies must:
-
Invest in quality control training programs for employees
-
Regularly audit and evaluate quality control procedures
-
Utilize advanced quality control tools and technology
-
Foster a culture of quality and improvement across the organization. These quality control practices can help companies. They boost product quality, cut defects, and improve customer satisfaction. Quality control is not just a process. It is a mindset. It should be in every aspect of manufacturing. By prioritizing quality, companies can stand out from the competition. They can also build a reputation for excellence in the industry.
How to obtain Quality Management certification?
We are an Education Technology company providing certification training courses to accelerate careers of working professionals worldwide. We impart training through instructor-led classroom workshops, instructor-led live virtual training sessions, and self-paced e-learning courses.
We have successfully conducted training sessions in 108 countries across the globe and enabled thousands of working professionals to enhance the scope of their careers.
Our enterprise training portfolio includes in-demand and globally recognized certification training courses in Project Management, Quality Management, Business Analysis, IT Service Management, Agile and Scrum, Cyber Security, Data Science, and Emerging Technologies. Download our Enterprise Training Catalog from https://www.icertglobal.com/corporate-training-for-enterprises.php and https://www.icertglobal.com/index.php
Popular Courses include:
-
Project Management: PMP, CAPM ,PMI RMP
-
Quality Management: Six Sigma Black Belt ,Lean Six Sigma Green Belt, Lean Management, Minitab,CMMI
-
Business Analysis: CBAP, CCBA, ECBA
-
Agile Training: PMI-ACP , CSM , CSPO
-
Scrum Training: CSM
-
DevOps
-
Program Management: PgMP
-
Cloud Technology: Exin Cloud Computing
-
Citrix Client Adminisration: Citrix Cloud Administration
The 10 top-paying certifications to target in 2024 are:
Conclusion
In conclusion, quality control is vital in manufacturing. It affects product quality, customer satisfaction, and business success. Companies can boost profits by using quality control and best practices. They will then have consistent products with fewer defects. Remember, quality is not an act; it is a habit. It must be cultivated and maintained throughout the manufacturing process.
Contact Us For More Information:
Visit : www.icertglobal.com Email : info@icertglobal.com
Read More
In manufacturing, high-quality products are key to success. Good quality control can help companies. It can maintain consistency, meet regulations, and improve customer satisfaction. This article will discuss ways to ensure quality in manufacturing.
Importance of Quality Control in Manufacturing
Quality control is key in manufacturing. It ensures products meet customer and legal standards. Companies can reduce defects and improve efficiency by using effective quality control. It will also ensure consistent products. This ultimately leads to higher customer satisfaction and increased profitability.
Quality control in manufacturing is vital. It ensures product consistency and meets industry standards. This builds customer trust and satisfaction. QC minimizes waste, cuts costs, and boosts efficiency. It does this by finding and fixing defects early. Also, good quality control helps meet regulations. It builds a strong brand. This drives long-term success and competitiveness in the market.
Best Practices for Quality Control
-
Establish Quality Control Standards: First, set clear quality control standards. This is key to ensuring product consistency and reliability. These standards should detail the criteria for acceptable products.
-
Implement Quality Control Procedures: Develop standard tests to inspect for quality. This will ensure products meet the established standards. Regularly monitor and evaluate these procedures to identify areas for improvement.
-
Use Quality Control Tools: Give your team the tools to test and inspect products. This can include equipment for measurements, testing, and inspection software.
-
Develop a Quality Control Plan: Create a plan. It must detail how to implement quality control measures in manufacturing. This plan should detail responsibilities, procedures, and processes for quality control.
-
Train Your Team: Provide ongoing training for your quality control team. This will ensure they have the skills to do their jobs well. Regular training can help improve the accuracy and efficiency of quality control measures.
Quality Control Methods in Manufacturing
-
Statistical Process Control (SPC): SPC is a method to monitor and control processes. It ensures they stay within specifications. Manufacturers can find trends by analyzing data. They can then adjust to maintain product quality.
-
Six Sigma is a data-driven quality control method. It aims to reduce defects and variations in manufacturing processes. Six Sigma can help companies improve quality, cut costs, and boost customer satisfaction.
-
Lean Manufacturing: It aims to cut waste and boost efficiency in manufacturing. By streamlining operations, companies can improve product quality and cut lead times.
Quality Control Challenges
Manufacturing often faces quality control (QC) challenges. They can hurt product consistency and efficiency. QC efforts often face issues. They are: detecting defects early, standardizing processes, and ensuring compliance with laws. We must use a strategic approach to tackle these challenges. We should use advanced tech and ongoing training. They will improve accuracy and effectiveness in quality management.
Quality control is vital for manufacturing success. But, companies may face challenges in implementing it. Some common challenges include:
-
Ensuring consistency in product quality across different production lines and locations
-
Managing supplier quality control to ensure the reliability of raw materials
-
Adapting to changing regulations and industry standards is tough. It requires a complete quality control approach. This must include continuous improvement, communication, and collaboration across departments.
Implementing Effective Quality Control Measures
To ensure the success of quality control measures in manufacturing, companies must:
-
Invest in quality control training programs for employees
-
Regularly audit and evaluate quality control procedures
-
Utilize advanced quality control tools and technology
-
Foster a culture of quality and improvement across the organization. These quality control practices can help companies. They boost product quality, cut defects, and improve customer satisfaction. Quality control is not just a process. It is a mindset. It should be in every aspect of manufacturing. By prioritizing quality, companies can stand out from the competition. They can also build a reputation for excellence in the industry.
How to obtain Quality Management certification?
We are an Education Technology company providing certification training courses to accelerate careers of working professionals worldwide. We impart training through instructor-led classroom workshops, instructor-led live virtual training sessions, and self-paced e-learning courses.
We have successfully conducted training sessions in 108 countries across the globe and enabled thousands of working professionals to enhance the scope of their careers.
Our enterprise training portfolio includes in-demand and globally recognized certification training courses in Project Management, Quality Management, Business Analysis, IT Service Management, Agile and Scrum, Cyber Security, Data Science, and Emerging Technologies. Download our Enterprise Training Catalog from https://www.icertglobal.com/corporate-training-for-enterprises.php and https://www.icertglobal.com/index.php
Popular Courses include:
-
Project Management: PMP, CAPM ,PMI RMP
-
Quality Management: Six Sigma Black Belt ,Lean Six Sigma Green Belt, Lean Management, Minitab,CMMI
-
Business Analysis: CBAP, CCBA, ECBA
-
Agile Training: PMI-ACP , CSM , CSPO
-
Scrum Training: CSM
-
DevOps
-
Program Management: PgMP
-
Cloud Technology: Exin Cloud Computing
-
Citrix Client Adminisration: Citrix Cloud Administration
The 10 top-paying certifications to target in 2024 are:
Conclusion
In conclusion, quality control is vital in manufacturing. It affects product quality, customer satisfaction, and business success. Companies can boost profits by using quality control and best practices. They will then have consistent products with fewer defects. Remember, quality is not an act; it is a habit. It must be cultivated and maintained throughout the manufacturing process.
Contact Us For More Information:
Visit : www.icertglobal.com Email : info@icertglobal.com
Differences Between Lean Six Sigma Green and Black Belts
Lean Six Sigma is a method. It combines Lean manufacturing and Six Sigma. It aims to improve processes, cut waste, and boost quality. The framework has different certification levels. They show varying degrees of expertise and responsibility. The Green Belt and Black Belt certifications are two top levels. Each has distinct roles, responsibilities, and skills. It is crucial to know the differences between these two levels. Organizations and individuals want to use Lean Six Sigma for excellence.
Table Of Contents
- Certification Level and Training
- Role and Responsibilities
- Skills and Knowledge
- Project Scope and Impact
- Career Path and Advancement
- Conclusion
Certification Level and Training
Green Belt Certification:
- Overview: Lean Six Sigma considers Green Belts foundational in its hierarchy. They balance projects with regular duties in their daily workloads.
- Training: Green Belt training covers the basics of Lean Six Sigma. It includes project management, data collection, and analysis. It stresses using tools like DMAIC and basic stats.
Black Belt Certification:
- Overview: Black Belts are experts. They lead complex projects and mentor Green Belts. They are often employed full-time in Lean Six Sigma roles.
- Black Belt training is more intensive. It covers advanced stats, leadership, and strategic deployment. It includes advanced techniques, like hypothesis testing and regression. It also includes experimental design.
Role and Responsibilities
Green Belt:
- Project Involvement: Green Belts usually work on smaller projects. They may also support Black Belt-led projects.
- Responsibilities: They must install Lean Six Sigma tools in their team. They analyze data, identify improvement opportunities, and help drive changes.
Black Belt:
- Project Involvement: Black Belts lead larger, more complex projects. They manage many Green Belt projects.
- Responsibilities: They are involved in strategic decision-making and ensure alignment with organizational goals. Black Belts mentor Green Belts. They also train and improve processes across the organization.
Skills and Knowledge
Green Belt:
- Skills: Green Belts have foundational skills in process improvement, problem-solving, and data analysis. They are proficient in basic Lean Six Sigma tools and techniques.
- Knowledge: They understand the core principles of Lean Six Sigma. These are waste reduction, process mapping, and basic statistical tools.
Black Belt:
- Skills: Black Belts excel at statistical analysis, project management, and change management. They are adept at using sophisticated tools and techniques to tackle complex issues.
- They know Lean Six Sigma well. They can use advanced stats to drive big improvements.
Project Scope and Impact
Green Belt:
- Scope: Green Belt projects usually focus on specific processes. They aim to improve small-scale work within a department or team.
- Impact: These projects can improve things and save money. But they usually only affect a small area.
Black Belt:
- Scope: Black Belt projects often span many departments or the whole organization. They deal with complex, systemic issues.
- These projects transform performance. They often save costs and boost efficiency.
Career Path and Advancement
Green Belt:
- Career Path: Green Belts can advance to Black Belt certification. They must gain more experience and prove they can manage larger projects.
- Advancement: The Green Belt cert is a first step to advanced Lean Six Sigma roles. It provides a good foundation for further growth.
Black Belt:
- Career Path: Black Belts can become Master Black Belts or senior leaders. They often take on strategic roles within organizations.
- Advancement: Master Black Belts can set strategy and mentor Black and Green Belts. They can also lead initiatives across the company.
How to obtain Lean Six Sigma Green & Black Belt certification?
We are an Education Technology company providing certification training courses to accelerate careers of working professionals worldwide. We impart training through instructor-led classroom workshops, instructor-led live virtual training sessions, and self-paced e-learning courses.
We have successfully conducted training sessions in 108 countries across the globe and enabled thousands of working professionals to enhance the scope of their careers.
Our enterprise training portfolio includes in-demand and globally recognized certification training courses in Project Management, Quality Management, Business Analysis, IT Service Management, Agile and Scrum, Cyber Security, Data Science, and Emerging Technologies. Download our Enterprise Training Catalog from https://www.icertglobal.com/corporate-training-for-enterprises.php and https://www.icertglobal.com/index.php
Popular Courses include:
- Project Management: PMP, CAPM ,PMI RMP
- Quality Management: Six Sigma Black Belt ,Lean Six Sigma Green Belt, Lean Management, Minitab,CMMI
- Business Analysis: CBAP, CCBA, ECBA
- Agile Training: PMI-ACP , CSM , CSPO
- Scrum Training: CSM
- DevOps
- Program Management: PgMP
- Cloud Technology: Exin Cloud Computing
- Citrix Client Adminisration: Citrix Cloud Administration
The 10 top-paying certifications to target in 2024 are:
- Certified Information Systems Security Professional® (CISSP)
- AWS Certified Solutions Architect
- Google Certified Professional Cloud Architect
- Big Data Certification
- Data Science Certification
- Certified In Risk And Information Systems Control (CRISC)
- Certified Information Security Manager(CISM)
- Project Management Professional (PMP)® Certification
- Certified Ethical Hacker (CEH)
- Certified Scrum Master (CSM)
Conclusion
In Conclusion, The Lean Six Sigma Green and Black Belt certifications are for different skill levels and responsibilities. Green Belts focus on improvement projects and support larger initiatives. Black Belts lead complex projects, mentor Green Belts, and drive strategic improvements. Both certifications are valuable. Green Belts understand Lean Six Sigma. Black Belts have advanced skills to solve major organizational problems. These differences can help organizations. They can guide resource use and improve processes.
Contact Us :
Contact Us For More Information:
Visit :www.icertglobal.com Email : info@icertglobal.com
Read More
Lean Six Sigma is a method. It combines Lean manufacturing and Six Sigma. It aims to improve processes, cut waste, and boost quality. The framework has different certification levels. They show varying degrees of expertise and responsibility. The Green Belt and Black Belt certifications are two top levels. Each has distinct roles, responsibilities, and skills. It is crucial to know the differences between these two levels. Organizations and individuals want to use Lean Six Sigma for excellence.
Table Of Contents
- Certification Level and Training
- Role and Responsibilities
- Skills and Knowledge
- Project Scope and Impact
- Career Path and Advancement
- Conclusion
Certification Level and Training
Green Belt Certification:
- Overview: Lean Six Sigma considers Green Belts foundational in its hierarchy. They balance projects with regular duties in their daily workloads.
- Training: Green Belt training covers the basics of Lean Six Sigma. It includes project management, data collection, and analysis. It stresses using tools like DMAIC and basic stats.
Black Belt Certification:
- Overview: Black Belts are experts. They lead complex projects and mentor Green Belts. They are often employed full-time in Lean Six Sigma roles.
- Black Belt training is more intensive. It covers advanced stats, leadership, and strategic deployment. It includes advanced techniques, like hypothesis testing and regression. It also includes experimental design.
Role and Responsibilities
Green Belt:
- Project Involvement: Green Belts usually work on smaller projects. They may also support Black Belt-led projects.
- Responsibilities: They must install Lean Six Sigma tools in their team. They analyze data, identify improvement opportunities, and help drive changes.
Black Belt:
- Project Involvement: Black Belts lead larger, more complex projects. They manage many Green Belt projects.
- Responsibilities: They are involved in strategic decision-making and ensure alignment with organizational goals. Black Belts mentor Green Belts. They also train and improve processes across the organization.
Skills and Knowledge
Green Belt:
- Skills: Green Belts have foundational skills in process improvement, problem-solving, and data analysis. They are proficient in basic Lean Six Sigma tools and techniques.
- Knowledge: They understand the core principles of Lean Six Sigma. These are waste reduction, process mapping, and basic statistical tools.
Black Belt:
- Skills: Black Belts excel at statistical analysis, project management, and change management. They are adept at using sophisticated tools and techniques to tackle complex issues.
- They know Lean Six Sigma well. They can use advanced stats to drive big improvements.
Project Scope and Impact
Green Belt:
- Scope: Green Belt projects usually focus on specific processes. They aim to improve small-scale work within a department or team.
- Impact: These projects can improve things and save money. But they usually only affect a small area.
Black Belt:
- Scope: Black Belt projects often span many departments or the whole organization. They deal with complex, systemic issues.
- These projects transform performance. They often save costs and boost efficiency.
Career Path and Advancement
Green Belt:
- Career Path: Green Belts can advance to Black Belt certification. They must gain more experience and prove they can manage larger projects.
- Advancement: The Green Belt cert is a first step to advanced Lean Six Sigma roles. It provides a good foundation for further growth.
Black Belt:
- Career Path: Black Belts can become Master Black Belts or senior leaders. They often take on strategic roles within organizations.
- Advancement: Master Black Belts can set strategy and mentor Black and Green Belts. They can also lead initiatives across the company.
How to obtain Lean Six Sigma Green & Black Belt certification?
We are an Education Technology company providing certification training courses to accelerate careers of working professionals worldwide. We impart training through instructor-led classroom workshops, instructor-led live virtual training sessions, and self-paced e-learning courses.
We have successfully conducted training sessions in 108 countries across the globe and enabled thousands of working professionals to enhance the scope of their careers.
Our enterprise training portfolio includes in-demand and globally recognized certification training courses in Project Management, Quality Management, Business Analysis, IT Service Management, Agile and Scrum, Cyber Security, Data Science, and Emerging Technologies. Download our Enterprise Training Catalog from https://www.icertglobal.com/corporate-training-for-enterprises.php and https://www.icertglobal.com/index.php
Popular Courses include:
- Project Management: PMP, CAPM ,PMI RMP
- Quality Management: Six Sigma Black Belt ,Lean Six Sigma Green Belt, Lean Management, Minitab,CMMI
- Business Analysis: CBAP, CCBA, ECBA
- Agile Training: PMI-ACP , CSM , CSPO
- Scrum Training: CSM
- DevOps
- Program Management: PgMP
- Cloud Technology: Exin Cloud Computing
- Citrix Client Adminisration: Citrix Cloud Administration
The 10 top-paying certifications to target in 2024 are:
- Certified Information Systems Security Professional® (CISSP)
- AWS Certified Solutions Architect
- Google Certified Professional Cloud Architect
- Big Data Certification
- Data Science Certification
- Certified In Risk And Information Systems Control (CRISC)
- Certified Information Security Manager(CISM)
- Project Management Professional (PMP)® Certification
- Certified Ethical Hacker (CEH)
- Certified Scrum Master (CSM)
Conclusion
In Conclusion, The Lean Six Sigma Green and Black Belt certifications are for different skill levels and responsibilities. Green Belts focus on improvement projects and support larger initiatives. Black Belts lead complex projects, mentor Green Belts, and drive strategic improvements. Both certifications are valuable. Green Belts understand Lean Six Sigma. Black Belts have advanced skills to solve major organizational problems. These differences can help organizations. They can guide resource use and improve processes.
Contact Us :
Contact Us For More Information:
Visit :www.icertglobal.com Email : info@icertglobal.com
10 Essential Minitab Shortcuts Every Analyst Should Know
In the world of data analysis, efficiency is key. Minitab has powerful tools to help your workflow. Use it for statistical analyses, making charts, or managing large datasets. One way to boost your productivity in Minitab is to master keyboard shortcuts. These shortcuts can save you time. They can also reduce the strain of navigating menus and dialog boxes. In this article, we'll explore ten essential Minitab shortcuts every analyst should know. Using these shortcuts in your daily routine will help you. You can then work more efficiently and use Minitab's features.
Shortcuts:
Ctrl + E: Open the Editor
When working with data, the Editor is your go-to tool for editing data in your worksheet. The shortcut Ctrl + E opens the Data Editor. It lets you quickly edit your dataset without using the menu. This is particularly useful for quickly correcting data entries or making batch updates.
Ctrl + Q: Open the Query Dialog
The Ctrl + Q shortcut brings up the Query Dialog, which is used to create and manage queries in Minitab. Queries are essential for filtering and analyzing specific subsets of data. This shortcut lets you set up complex queries easily. There's no need for multiple steps in the menu system.
Ctrl + T: Create a t-test
A t-test is common in stats. Press Ctrl + T to start a t-test. This shortcut opens the T-Test dialog, where you can specify your data and settings. Frequent hypothesis testers reap significant time savings.
Ctrl + G: Generate a graph
Creating visual representations of data is crucial for analysis and presentations. Press Ctrl + G to access the Graph dialog immediately. This lets you customize a graph, like a histogram or scatter plot, without using the main menu.
Ctrl + M: Open the Manager
The Ctrl + M shortcut opens the Manager window. It shows all your ongoing analyses, including projects and data files. This window helps you manage your work and track progress. It grants instant access to various segments of your analysis.
Ctrl + A: Select All Data
Selecting all data in a worksheet can be cumbersome, especially with large datasets. The Ctrl + A shortcut makes this task easy by selecting all the cells in the current worksheet. This shortcut is useful when you need to copy, paste, or perform operations on the entire dataset.
Ctrl + Z: Undo Last Action
Errors occur, and reversing your previous step proves priceless. The Ctrl + Z shortcut undoes your last change in Minitab. It works for both data-entry errors and graph edits. This function helps prevent loss of work and reduces the need for repetitive steps.
Ctrl + Y: Redo Last Action
The Ctrl + Y shortcut redoes the last undone action. It complements the Undo function. This is useful if you’ve undone an action by mistake and want to revert to the previous state. Changes are recovered immediately, eliminating manual reapplication entirely.
Ctrl + F: Find and Replace
Searching for specific data or values in a large dataset can be time-consuming. The Ctrl + F shortcut opens the Find and Replace dialog. It enables swift location and alteration of dataset entries. This is especially handy for data cleaning and preparation.
Ctrl + P: Print Current View
Once your analysis is complete, you might need to print your results or graphs. The Ctrl + P shortcut opens the Print dialog for the current view, whether it’s a worksheet, graph, or report. It makes it easier to produce physical copies of your work for sharing or presentation.
How to obtain MiniTab Certification?
We are an Education Technology company providing certification training courses to accelerate careers of working professionals worldwide. We impart training through instructor-led classroom workshops, instructor-led live virtual training sessions, and self-paced e-learning courses.
We have successfully conducted training sessions in 108 countries across the globe and enabled thousands of working professionals to enhance the scope of their careers.
Our enterprise training portfolio includes in-demand and globally recognized certification training courses in Project Management, Quality Management, Business Analysis, IT Service Management, Agile and Scrum, Cyber Security, Data Science, and Emerging Technologies. Download our Enterprise Training Catalog from https://www.icertglobal.com/corporate-training-for-enterprises.php and https://www.icertglobal.com/index.php
Popular Courses include:
- Project Management: PMP, CAPM ,PMI RMP
- Quality Management: Six Sigma Black Belt ,Lean Six Sigma Green Belt, Lean Management, Minitab,CMMI
- Business Analysis: CBAP, CCBA, ECBA
- Agile Training: PMI-ACP , CSM , CSPO
- Scrum Training: CSM
- DevOps
- Program Management: PgMP
- Cloud Technology: Exin Cloud Computing
- Citrix Client Adminisration: Citrix Cloud Administration
The 10 top-paying certifications to target in 2024 are:
- Certified Information Systems Security Professional® (CISSP)
- AWS Certified Solutions Architect
- Google Certified Professional Cloud Architect
- Big Data Certification
- Data Science Certification
- Certified In Risk And Information Systems Control (CRISC)
- Certified Information Security Manager(CISM)
- Project Management Professional (PMP)® Certification
- Certified Ethical Hacker (CEH)
- Certified Scrum Master (CSM)
Conclusion
In Conclusion, Mastering Minitab's keyboard shortcuts can boost your productivity as an analyst. Use these ten shortcuts in your workflow. They will save you time, reduce repetitive tasks, and let you focus on the analysis. These shortcuts aim to make common tasks easier and help you navigate Minitab better. As you learn these shortcuts, your workflow will improve. It will be smoother and more efficient. Embrace these shortcuts. Make them a key part of your data analysis toolkit.
Contact Us :
Contact Us For More Information:
Visit :www.icertglobal.com Email : info@icertglobal.com
Read More
In the world of data analysis, efficiency is key. Minitab has powerful tools to help your workflow. Use it for statistical analyses, making charts, or managing large datasets. One way to boost your productivity in Minitab is to master keyboard shortcuts. These shortcuts can save you time. They can also reduce the strain of navigating menus and dialog boxes. In this article, we'll explore ten essential Minitab shortcuts every analyst should know. Using these shortcuts in your daily routine will help you. You can then work more efficiently and use Minitab's features.
Shortcuts:
Ctrl + E: Open the Editor
When working with data, the Editor is your go-to tool for editing data in your worksheet. The shortcut Ctrl + E opens the Data Editor. It lets you quickly edit your dataset without using the menu. This is particularly useful for quickly correcting data entries or making batch updates.
Ctrl + Q: Open the Query Dialog
The Ctrl + Q shortcut brings up the Query Dialog, which is used to create and manage queries in Minitab. Queries are essential for filtering and analyzing specific subsets of data. This shortcut lets you set up complex queries easily. There's no need for multiple steps in the menu system.
Ctrl + T: Create a t-test
A t-test is common in stats. Press Ctrl + T to start a t-test. This shortcut opens the T-Test dialog, where you can specify your data and settings. Frequent hypothesis testers reap significant time savings.
Ctrl + G: Generate a graph
Creating visual representations of data is crucial for analysis and presentations. Press Ctrl + G to access the Graph dialog immediately. This lets you customize a graph, like a histogram or scatter plot, without using the main menu.
Ctrl + M: Open the Manager
The Ctrl + M shortcut opens the Manager window. It shows all your ongoing analyses, including projects and data files. This window helps you manage your work and track progress. It grants instant access to various segments of your analysis.
Ctrl + A: Select All Data
Selecting all data in a worksheet can be cumbersome, especially with large datasets. The Ctrl + A shortcut makes this task easy by selecting all the cells in the current worksheet. This shortcut is useful when you need to copy, paste, or perform operations on the entire dataset.
Ctrl + Z: Undo Last Action
Errors occur, and reversing your previous step proves priceless. The Ctrl + Z shortcut undoes your last change in Minitab. It works for both data-entry errors and graph edits. This function helps prevent loss of work and reduces the need for repetitive steps.
Ctrl + Y: Redo Last Action
The Ctrl + Y shortcut redoes the last undone action. It complements the Undo function. This is useful if you’ve undone an action by mistake and want to revert to the previous state. Changes are recovered immediately, eliminating manual reapplication entirely.
Ctrl + F: Find and Replace
Searching for specific data or values in a large dataset can be time-consuming. The Ctrl + F shortcut opens the Find and Replace dialog. It enables swift location and alteration of dataset entries. This is especially handy for data cleaning and preparation.
Ctrl + P: Print Current View
Once your analysis is complete, you might need to print your results or graphs. The Ctrl + P shortcut opens the Print dialog for the current view, whether it’s a worksheet, graph, or report. It makes it easier to produce physical copies of your work for sharing or presentation.
How to obtain MiniTab Certification?
We are an Education Technology company providing certification training courses to accelerate careers of working professionals worldwide. We impart training through instructor-led classroom workshops, instructor-led live virtual training sessions, and self-paced e-learning courses.
We have successfully conducted training sessions in 108 countries across the globe and enabled thousands of working professionals to enhance the scope of their careers.
Our enterprise training portfolio includes in-demand and globally recognized certification training courses in Project Management, Quality Management, Business Analysis, IT Service Management, Agile and Scrum, Cyber Security, Data Science, and Emerging Technologies. Download our Enterprise Training Catalog from https://www.icertglobal.com/corporate-training-for-enterprises.php and https://www.icertglobal.com/index.php
Popular Courses include:
- Project Management: PMP, CAPM ,PMI RMP
- Quality Management: Six Sigma Black Belt ,Lean Six Sigma Green Belt, Lean Management, Minitab,CMMI
- Business Analysis: CBAP, CCBA, ECBA
- Agile Training: PMI-ACP , CSM , CSPO
- Scrum Training: CSM
- DevOps
- Program Management: PgMP
- Cloud Technology: Exin Cloud Computing
- Citrix Client Adminisration: Citrix Cloud Administration
The 10 top-paying certifications to target in 2024 are:
- Certified Information Systems Security Professional® (CISSP)
- AWS Certified Solutions Architect
- Google Certified Professional Cloud Architect
- Big Data Certification
- Data Science Certification
- Certified In Risk And Information Systems Control (CRISC)
- Certified Information Security Manager(CISM)
- Project Management Professional (PMP)® Certification
- Certified Ethical Hacker (CEH)
- Certified Scrum Master (CSM)
Conclusion
In Conclusion, Mastering Minitab's keyboard shortcuts can boost your productivity as an analyst. Use these ten shortcuts in your workflow. They will save you time, reduce repetitive tasks, and let you focus on the analysis. These shortcuts aim to make common tasks easier and help you navigate Minitab better. As you learn these shortcuts, your workflow will improve. It will be smoother and more efficient. Embrace these shortcuts. Make them a key part of your data analysis toolkit.
Contact Us :
Contact Us For More Information:
Visit :www.icertglobal.com Email : info@icertglobal.com
Unlock Career Growth with CAPM® Certification Advantages
In today's fast, competitive business world, firms want to be more efficient and stay ahead. Two key technologies are transforming how businesses operate. They are Lean Management and Digital Twin Technology. Let's explore how these new methods are changing industries and creating success.
What is Lean Management?
Lean management is a method. It aims to maximize customer value and minimize waste. It aims to create more customer value with fewer resources. It is based on continuous improvement and waste reduction. Lean Management helps organizations excel and grow. It speeds up processes, reduces waste, and lets employees use data to decide.
How Does Digital Twin Technology Work?
Digital Twin Technology creates a virtual copy of a physical object, like a factory or a supply chain. Organizations can gain insights into their assets and processes. They can do this by combining real-time data with advanced analytics and simulations. It lets them optimize operations and predict maintenance needs. They can then make data-driven decisions that boost efficiency and productivity.
Digital twin technology creates a virtual copy of a physical thing. It can be an object, process, or system. It enables real-time monitoring, simulation, and analysis. Here’s a breakdown of how it works:
1. Data Collection
Sensors and IoT Devices: Physical objects or systems have sensors and IoT devices. They continuously collect data. This data can include temperature, pressure, vibration, and other operational metrics.
Data Sources: The data can come from various sources. These include machines, sensors, and enterprise systems (like ERP). It can also come from external factors, like the weather.
2. Data Integration
Data Aggregation: Collected data is aggregated from multiple sources. This may mean merging data from various sensors and systems into a central platform.
Data Processing: The data is processed and cleaned to ensure accuracy and relevance. This may involve filtering out noise, correcting errors, and normalizing data formats.
3. Digital Twin Creation
Model Development:A digital model or replica of the physical entity is created. This involves using CAD drawings, 3D modeling, and other tools to create a virtual model.
Simulation and Visualization: The digital twin is often visualized in 3D. It lets users see and interact with the model. It can also simulate the behavior of the physical object or system based on the collected data.
4. Real-Time Synchronization
Continuous Data Feed:The digital twin receives real-time data from its physical counterpart. This makes the virtual model match the physical object or system.
State Updates: The digital twin is updated in real-time to reflect changes in the real world. This synchronization allows for accurate monitoring and analysis.
5. Analysis and Insights
Performance Monitoring: Users can monitor the physical entity's health through the digital twin. This includes tracking key metrics, identifying anomalies, and assessing overall performance.
Predictive Analytics: Analyzing data from the digital twin can forecast issues. It can find potential failures before they occur. This helps in proactive maintenance and decision-making.
Scenario Testing: Users can run simulations in the digital twin. This will help them understand potential outcomes and impacts. This helps in optimizing processes and planning.
6. Feedback and Optimization
Use the digital twin to optimize the physical object or system. This can involve adjustments, better processes, or changes based on simulations.
Feedback Loop: Optimizations and changes are fed back into the digital twin. This keeps it an accurate representation of the physical entity. This creates a continuous loop of improvement and refinement.
Applications
Manufacturing: Monitoring and optimizing production processes, predicting equipment failures, and improving operational efficiency.
Healthcare: Creating virtual models of patients. This is for personalized treatments and monitoring medical devices.
Urban Planning:Simulating city infrastructure and services to improve urban design and management.
Automotive: Testing vehicle designs and performance under various conditions without physical prototypes.
Digital twin technology links the physical and digital worlds. It allows for better decisions, predictive maintenance, and process optimization.
The Intersection of Lean Management and Digital Twin Technology
Combining Lean Management with Digital Twin Technology can boost organizations. It can unlock new optimization and innovation. Using virtual modeling, real-time monitoring, and AI, companies can improve their processes. They can also make better decisions and boost performance. This lets businesses optimize operations, improve quality, and cut costs. They can also stay agile and respond to changing market demands.
Benefits of Implementing Lean Practices with Digital Twin Technology
-
Enhanced process optimization and efficiency
-
Improved quality and reliability of products and services
-
Real-time monitoring and data-driven decision-making
-
Predictive maintenance to prevent costly downtime
-
Seamless integration of IoT devices for enhanced connectivity
-
Enhanced lean culture and mindset among employees
-
Improved operational visibility and control
-
Streamlined production processes and reduced waste
-
Accelerated digital transformation and innovation
-
Facilitated lean training programs and continuous improvement initiatives
Case Study: Lean Manufacturing in Industry 4.0
One industry that has embraced Lean Management and Digital Twin Technology is manufacturing. By using lean practices and digital twin solutions, companies can create smart factories. These factories can optimize and automate processes in real time. This results in increased productivity, reduced operational costs, and improved quality control. Manufacturers can use advanced analytics, machine learning, and IoT. These tools can drive lean transformation and help them compete in the digital age.
How to obtain Lean Management certification?
We are an Education Technology company providing certification training courses to accelerate careers of working professionals worldwide. We impart training through instructor-led classroom workshops, instructor-led live virtual training sessions, and self-paced e-learning courses.
We have successfully conducted training sessions in 108 countries across the globe and enabled thousands of working professionals to enhance the scope of their careers.
Our enterprise training portfolio includes in-demand and globally recognized certification training courses in Project Management, Quality Management, Business Analysis, IT Service Management, Agile and Scrum, Cyber Security, Data Science, and Emerging Technologies. Download our Enterprise Training Catalog from https://www.icertglobal.com/corporate-training-for-enterprises.php and https://www.icertglobal.com/index.php
Popular Courses include:
-
Project Management: PMP, CAPM ,PMI RMP
-
Quality Management: Six Sigma Black Belt ,Lean Six Sigma Green Belt, Lean Management, Minitab,CMMI
-
Business Analysis: CBAP, CCBA, ECBA
-
Agile Training: PMI-ACP , CSM , CSPO
-
Scrum Training: CSM
-
DevOps
-
Program Management: PgMP
-
Cloud Technology: Exin Cloud Computing
-
Citrix Client Adminisration: Citrix Cloud Administration
The 10 top-paying certifications to target in 2024 are:
Conclusion
In conclusion, combining Lean Management with Digital Twin Technology is a game-changer. It helps businesses boost efficiency and innovation in today's digital era. Organizations can boost their operations and performance. They can do this by using lean principles and digital tools. They should also optimize their processes. They can also achieve sustainable growth. The future of lean management is in digital twin technology. It can create smart, agile, connected enterprises. They will thrive in the Fourth Industrial Revolution.
Contact Us For More Information:
Visit :www.icertglobal.com Email : info@icertglobal.com
Read More
In today's fast, competitive business world, firms want to be more efficient and stay ahead. Two key technologies are transforming how businesses operate. They are Lean Management and Digital Twin Technology. Let's explore how these new methods are changing industries and creating success.
What is Lean Management?
Lean management is a method. It aims to maximize customer value and minimize waste. It aims to create more customer value with fewer resources. It is based on continuous improvement and waste reduction. Lean Management helps organizations excel and grow. It speeds up processes, reduces waste, and lets employees use data to decide.
How Does Digital Twin Technology Work?
Digital Twin Technology creates a virtual copy of a physical object, like a factory or a supply chain. Organizations can gain insights into their assets and processes. They can do this by combining real-time data with advanced analytics and simulations. It lets them optimize operations and predict maintenance needs. They can then make data-driven decisions that boost efficiency and productivity.
Digital twin technology creates a virtual copy of a physical thing. It can be an object, process, or system. It enables real-time monitoring, simulation, and analysis. Here’s a breakdown of how it works:
1. Data Collection
Sensors and IoT Devices: Physical objects or systems have sensors and IoT devices. They continuously collect data. This data can include temperature, pressure, vibration, and other operational metrics.
Data Sources: The data can come from various sources. These include machines, sensors, and enterprise systems (like ERP). It can also come from external factors, like the weather.
2. Data Integration
Data Aggregation: Collected data is aggregated from multiple sources. This may mean merging data from various sensors and systems into a central platform.
Data Processing: The data is processed and cleaned to ensure accuracy and relevance. This may involve filtering out noise, correcting errors, and normalizing data formats.
3. Digital Twin Creation
Model Development:A digital model or replica of the physical entity is created. This involves using CAD drawings, 3D modeling, and other tools to create a virtual model.
Simulation and Visualization: The digital twin is often visualized in 3D. It lets users see and interact with the model. It can also simulate the behavior of the physical object or system based on the collected data.
4. Real-Time Synchronization
Continuous Data Feed:The digital twin receives real-time data from its physical counterpart. This makes the virtual model match the physical object or system.
State Updates: The digital twin is updated in real-time to reflect changes in the real world. This synchronization allows for accurate monitoring and analysis.
5. Analysis and Insights
Performance Monitoring: Users can monitor the physical entity's health through the digital twin. This includes tracking key metrics, identifying anomalies, and assessing overall performance.
Predictive Analytics: Analyzing data from the digital twin can forecast issues. It can find potential failures before they occur. This helps in proactive maintenance and decision-making.
Scenario Testing: Users can run simulations in the digital twin. This will help them understand potential outcomes and impacts. This helps in optimizing processes and planning.
6. Feedback and Optimization
Use the digital twin to optimize the physical object or system. This can involve adjustments, better processes, or changes based on simulations.
Feedback Loop: Optimizations and changes are fed back into the digital twin. This keeps it an accurate representation of the physical entity. This creates a continuous loop of improvement and refinement.
Applications
Manufacturing: Monitoring and optimizing production processes, predicting equipment failures, and improving operational efficiency.
Healthcare: Creating virtual models of patients. This is for personalized treatments and monitoring medical devices.
Urban Planning:Simulating city infrastructure and services to improve urban design and management.
Automotive: Testing vehicle designs and performance under various conditions without physical prototypes.
Digital twin technology links the physical and digital worlds. It allows for better decisions, predictive maintenance, and process optimization.
The Intersection of Lean Management and Digital Twin Technology
Combining Lean Management with Digital Twin Technology can boost organizations. It can unlock new optimization and innovation. Using virtual modeling, real-time monitoring, and AI, companies can improve their processes. They can also make better decisions and boost performance. This lets businesses optimize operations, improve quality, and cut costs. They can also stay agile and respond to changing market demands.
Benefits of Implementing Lean Practices with Digital Twin Technology
-
Enhanced process optimization and efficiency
-
Improved quality and reliability of products and services
-
Real-time monitoring and data-driven decision-making
-
Predictive maintenance to prevent costly downtime
-
Seamless integration of IoT devices for enhanced connectivity
-
Enhanced lean culture and mindset among employees
-
Improved operational visibility and control
-
Streamlined production processes and reduced waste
-
Accelerated digital transformation and innovation
-
Facilitated lean training programs and continuous improvement initiatives
Case Study: Lean Manufacturing in Industry 4.0
One industry that has embraced Lean Management and Digital Twin Technology is manufacturing. By using lean practices and digital twin solutions, companies can create smart factories. These factories can optimize and automate processes in real time. This results in increased productivity, reduced operational costs, and improved quality control. Manufacturers can use advanced analytics, machine learning, and IoT. These tools can drive lean transformation and help them compete in the digital age.
How to obtain Lean Management certification?
We are an Education Technology company providing certification training courses to accelerate careers of working professionals worldwide. We impart training through instructor-led classroom workshops, instructor-led live virtual training sessions, and self-paced e-learning courses.
We have successfully conducted training sessions in 108 countries across the globe and enabled thousands of working professionals to enhance the scope of their careers.
Our enterprise training portfolio includes in-demand and globally recognized certification training courses in Project Management, Quality Management, Business Analysis, IT Service Management, Agile and Scrum, Cyber Security, Data Science, and Emerging Technologies. Download our Enterprise Training Catalog from https://www.icertglobal.com/corporate-training-for-enterprises.php and https://www.icertglobal.com/index.php
Popular Courses include:
-
Project Management: PMP, CAPM ,PMI RMP
-
Quality Management: Six Sigma Black Belt ,Lean Six Sigma Green Belt, Lean Management, Minitab,CMMI
-
Business Analysis: CBAP, CCBA, ECBA
-
Agile Training: PMI-ACP , CSM , CSPO
-
Scrum Training: CSM
-
DevOps
-
Program Management: PgMP
-
Cloud Technology: Exin Cloud Computing
-
Citrix Client Adminisration: Citrix Cloud Administration
The 10 top-paying certifications to target in 2024 are:
Conclusion
In conclusion, combining Lean Management with Digital Twin Technology is a game-changer. It helps businesses boost efficiency and innovation in today's digital era. Organizations can boost their operations and performance. They can do this by using lean principles and digital tools. They should also optimize their processes. They can also achieve sustainable growth. The future of lean management is in digital twin technology. It can create smart, agile, connected enterprises. They will thrive in the Fourth Industrial Revolution.
Contact Us For More Information:
Visit :www.icertglobal.com Email : info@icertglobal.com
Harnessing AI & Machine Learning in Lean Six Sigma Projects
In today's data-driven world, businesses want to improve processes and efficiency. They also want to drive innovation. Lean Six Sigma is a process improvement and quality management method. Its rigorous approach is well-known. It has long been a key tool for achieving these goals. AI and ML are changing how organizations optimize processes and make decisions. They are now using these technologies in Lean Six Sigma projects. This synergy combines the strengths of both fields. It will provide new insights, improve operations, and speed up problem-solving. This article explores the use of AI and ML in Lean Six Sigma projects to achieve better results.
Enhancing Data Collection and Analysis
AI and ML technologies are changing how organizations collect and analyze data. This is a cornerstone of Lean Six Sigma projects. Traditional methods often involve manual data collection and analysis. These methods can be slow and prone to errors. AI tools and ML algorithms can automate data collection. They can integrate data from various sources and provide real-time analytics.
- Automated Data Collection: AI sensors and IoT devices can gather data. They can track production, supply chains, and customer interactions. This continuous stream of data enables more accurate and up-to-date information for analysis.
- Machine learning deciphers vast data sets with swift precision. It can find patterns and trends not obvious with traditional methods. Techniques like clustering and anomaly detection help. They find root causes and areas for improvement with greater precision.
Improving Process Mapping and Visualization
Lean Six Sigma projects often use detailed process maps and visuals. They help find inefficiencies and areas for improvement. AI and ML can improve these visual tools. They can help people understand complex processes and make better decisions.
- Dynamic Process Mapping: AI tools can create process maps. They refresh with current information. Teams can see changes and adjust their plans as needed.
- Predictive Modeling: ML algorithms can create models to predict outcomes. They do this by simulating scenarios based on historical data. These models help in forecasting issues. They also test the impact of proposed changes before implementation.
Accelerating Root Cause Analysis
Root cause analysis is key to Lean Six Sigma projects. It aims to find the root causes of problems, not fix symptoms. AI and ML can speed up this process. They provide deeper insights and better diagnoses.
- Pattern Recognition: Machine Learning algorithms excel at recognizing patterns within large datasets. These algorithms can analyze historical data to find patterns. They can then better identify the root causes of recurring issues.
- Natural Language Processing (NLP): AI tools can analyze unstructured data, like feedback and reports. They can find valuable insights about problem areas. This can complement traditional root cause analysis methods. It will provide a more complete view.
Optimizing Decision-Making and Implementation
Lean Six Sigma projects often involve choosing the best solutions. This requires evaluating various options. AI and ML can improve decision-making. They do this by providing data-driven recommendations and automating routine tasks.
- Decision Support Systems: AI-driven tools can analyze data and generate insights. They help project teams make decisions based on evidence, not intuition.
- Automation: Machine learning can automate routine tasks and process tweaks. This frees up resources for more strategic work. For example, ML algorithms can improve scheduling, inventory, and quality control. This leads to more efficient operations.
Enhancing Continuous Improvement
Continuous improvement is key to Lean Six Sigma. It aims to enhance processes and sustain gains over time. AI and ML can help. They can provide tools for ongoing monitoring and optimization.
- AI-driven monitoring systems can track KPIs and process metrics in real time. They alert teams to deviations and potential issues as they arise.
- Adaptive Learning: Machine Learning algorithms can learn from new data. They can update their models. It helps organizations refine their processes and strategies. They can use the latest insights and trends.
How to obtain Lean Six Sigma certification?
We are an Education Technology company providing certification training courses to accelerate careers of working professionals worldwide. We impart training through instructor-led classroom workshops, instructor-led live virtual training sessions, and self-paced e-learning courses.
We have successfully conducted training sessions in 108 countries across the globe and enabled thousands of working professionals to enhance the scope of their careers.
Our enterprise training portfolio includes in-demand and globally recognized certification training courses in Project Management, Quality Management, Business Analysis, IT Service Management, Agile and Scrum, Cyber Security, Data Science, and Emerging Technologies. Download our Enterprise Training Catalog from https://www.icertglobal.com/corporate-training-for-enterprises.php and https://www.icertglobal.com/index.php
Popular Courses include:
- Project Management: PMP, CAPM ,PMI RMP
- Quality Management: Six Sigma Black Belt ,Lean Six Sigma Green Belt, Lean Management, Minitab,CMMI
- Business Analysis: CBAP, CCBA, ECBA
- Agile Training: PMI-ACP , CSM , CSPO
- Scrum Training: CSM
- DevOps
- Program Management: PgMP
- Cloud Technology: Exin Cloud Computing
- Citrix Client Adminisration: Citrix Cloud Administration
The 10 top-paying certifications to target in 2024 are:
- Certified Information Systems Security Professional® (CISSP)
- AWS Certified Solutions Architect
- Google Certified Professional Cloud Architect
- Big Data Certification
- Data Science Certification
- Certified In Risk And Information Systems Control (CRISC)
- Certified Information Security Manager(CISM)
- Project Management Professional (PMP)® Certification
- Certified Ethical Hacker (CEH)
- Certified Scrum Master (CSM)
Conclusion
In Conclusion, AI and Machine Learning in Lean Six Sigma projects are game changers. They transform how organizations improve processes and manage quality. AI and ML technologies are powerful tools for driving results. They enhance data collection and analysis. They improve process mapping and visualization. They also speed up root cause analysis. They optimize decision making and support improvement.
Organizations that embrace this synergy can gain a competitive edge. They will be more efficient, solve problems faster, and better understand their processes. As technology evolves, AI and ML can enhance Lean Six Sigma. This will create more chances for innovation and excellence. To succeed in a data-driven, complex business world, we must embrace these advancements.
Contact Us :
Contact Us For More Information:
Visit :www.icertglobal.com Email : info@icertglobal.com
Read More
In today's data-driven world, businesses want to improve processes and efficiency. They also want to drive innovation. Lean Six Sigma is a process improvement and quality management method. Its rigorous approach is well-known. It has long been a key tool for achieving these goals. AI and ML are changing how organizations optimize processes and make decisions. They are now using these technologies in Lean Six Sigma projects. This synergy combines the strengths of both fields. It will provide new insights, improve operations, and speed up problem-solving. This article explores the use of AI and ML in Lean Six Sigma projects to achieve better results.
Enhancing Data Collection and Analysis
AI and ML technologies are changing how organizations collect and analyze data. This is a cornerstone of Lean Six Sigma projects. Traditional methods often involve manual data collection and analysis. These methods can be slow and prone to errors. AI tools and ML algorithms can automate data collection. They can integrate data from various sources and provide real-time analytics.
- Automated Data Collection: AI sensors and IoT devices can gather data. They can track production, supply chains, and customer interactions. This continuous stream of data enables more accurate and up-to-date information for analysis.
- Machine learning deciphers vast data sets with swift precision. It can find patterns and trends not obvious with traditional methods. Techniques like clustering and anomaly detection help. They find root causes and areas for improvement with greater precision.
Improving Process Mapping and Visualization
Lean Six Sigma projects often use detailed process maps and visuals. They help find inefficiencies and areas for improvement. AI and ML can improve these visual tools. They can help people understand complex processes and make better decisions.
- Dynamic Process Mapping: AI tools can create process maps. They refresh with current information. Teams can see changes and adjust their plans as needed.
- Predictive Modeling: ML algorithms can create models to predict outcomes. They do this by simulating scenarios based on historical data. These models help in forecasting issues. They also test the impact of proposed changes before implementation.
Accelerating Root Cause Analysis
Root cause analysis is key to Lean Six Sigma projects. It aims to find the root causes of problems, not fix symptoms. AI and ML can speed up this process. They provide deeper insights and better diagnoses.
- Pattern Recognition: Machine Learning algorithms excel at recognizing patterns within large datasets. These algorithms can analyze historical data to find patterns. They can then better identify the root causes of recurring issues.
- Natural Language Processing (NLP): AI tools can analyze unstructured data, like feedback and reports. They can find valuable insights about problem areas. This can complement traditional root cause analysis methods. It will provide a more complete view.
Optimizing Decision-Making and Implementation
Lean Six Sigma projects often involve choosing the best solutions. This requires evaluating various options. AI and ML can improve decision-making. They do this by providing data-driven recommendations and automating routine tasks.
- Decision Support Systems: AI-driven tools can analyze data and generate insights. They help project teams make decisions based on evidence, not intuition.
- Automation: Machine learning can automate routine tasks and process tweaks. This frees up resources for more strategic work. For example, ML algorithms can improve scheduling, inventory, and quality control. This leads to more efficient operations.
Enhancing Continuous Improvement
Continuous improvement is key to Lean Six Sigma. It aims to enhance processes and sustain gains over time. AI and ML can help. They can provide tools for ongoing monitoring and optimization.
- AI-driven monitoring systems can track KPIs and process metrics in real time. They alert teams to deviations and potential issues as they arise.
- Adaptive Learning: Machine Learning algorithms can learn from new data. They can update their models. It helps organizations refine their processes and strategies. They can use the latest insights and trends.
How to obtain Lean Six Sigma certification?
We are an Education Technology company providing certification training courses to accelerate careers of working professionals worldwide. We impart training through instructor-led classroom workshops, instructor-led live virtual training sessions, and self-paced e-learning courses.
We have successfully conducted training sessions in 108 countries across the globe and enabled thousands of working professionals to enhance the scope of their careers.
Our enterprise training portfolio includes in-demand and globally recognized certification training courses in Project Management, Quality Management, Business Analysis, IT Service Management, Agile and Scrum, Cyber Security, Data Science, and Emerging Technologies. Download our Enterprise Training Catalog from https://www.icertglobal.com/corporate-training-for-enterprises.php and https://www.icertglobal.com/index.php
Popular Courses include:
- Project Management: PMP, CAPM ,PMI RMP
- Quality Management: Six Sigma Black Belt ,Lean Six Sigma Green Belt, Lean Management, Minitab,CMMI
- Business Analysis: CBAP, CCBA, ECBA
- Agile Training: PMI-ACP , CSM , CSPO
- Scrum Training: CSM
- DevOps
- Program Management: PgMP
- Cloud Technology: Exin Cloud Computing
- Citrix Client Adminisration: Citrix Cloud Administration
The 10 top-paying certifications to target in 2024 are:
- Certified Information Systems Security Professional® (CISSP)
- AWS Certified Solutions Architect
- Google Certified Professional Cloud Architect
- Big Data Certification
- Data Science Certification
- Certified In Risk And Information Systems Control (CRISC)
- Certified Information Security Manager(CISM)
- Project Management Professional (PMP)® Certification
- Certified Ethical Hacker (CEH)
- Certified Scrum Master (CSM)
Conclusion
In Conclusion, AI and Machine Learning in Lean Six Sigma projects are game changers. They transform how organizations improve processes and manage quality. AI and ML technologies are powerful tools for driving results. They enhance data collection and analysis. They improve process mapping and visualization. They also speed up root cause analysis. They optimize decision making and support improvement.
Organizations that embrace this synergy can gain a competitive edge. They will be more efficient, solve problems faster, and better understand their processes. As technology evolves, AI and ML can enhance Lean Six Sigma. This will create more chances for innovation and excellence. To succeed in a data-driven, complex business world, we must embrace these advancements.
Contact Us :
Contact Us For More Information:
Visit :www.icertglobal.com Email : info@icertglobal.com
Expanding CTFL Certification Growth in Emerging Markets
Are you looking to excel in the field of software testing and quality assurance? Consider getting a CTFL (Certified Tester Foundation Level) certification. There is a growing demand for skilled professionals in agile methods, especially in emerging markets. This article will explore the benefits of CTFL certification. It will cover the exam details and its value for advancing your software engineering career.
What is CTFL Certification?
The International Software Testing Qualifications Board (ISTQB) offers the CTFL certification. It is an industry standard for software testing qualifications. It covers a wide range of topics, such as testing principles, software development, and test automation. A CTFL certification shows your testing skills and knowledge of software tools. These are vital in today's competitive market.
Why Choose CTFL Certification in Emerging Markets?
Emerging markets offer a chance for software engineers. They can showcase their skills and advance their careers. By obtaining a CTFL certification, you can stand out among your peers and increase your chances of career advancement. The software apps industry is growing fast in emerging markets. An internationally recognized certification like CTFL can open doors to new jobs.
Benefits of CTFL Certification
-
Career advancement: CTFL certification can boost your career. It shows your skills in software testing.
-
Continuous improvement: Stay up-to-date with the latest testing methods. This will improve the quality of software applications.
-
Industry recognition: CTFL certification is well-known in the industry. It gives you a competitive edge in the job market.
-
International recognition: ISTQB certifications are known worldwide. They help in finding jobs abroad.
CTFL Exam Details
The CTFL exam covers many topics. They include test planning, test design, test execution, defect management, and analysis. To pass the exam, you need to study the CTFL syllabus, undergo CTFL training, and take a CTFL course to prepare for the exam. The exam is designed to test your knowledge and skills in various aspects of software testing and quality assurance.
How CTFL Certification Can Help Your Career
1. In the coming years, the demand for CTFL-certified professionals in emerging markets is expected to soar, as companies prioritize quality assurance in their software development processes.
2. As digital transformation accelerates in emerging economies, CTFL certification will soon be crucial. It will be a key asset for testing pros who want to stay competitive.
3. As software testing evolves in emerging markets, CTFL certification will be key. It will standardize testing practices and ensure quality.
4. CTFL certification will soon be a benchmark for software testers in emerging markets. It will set them apart in a competitive job market.
5. As global tech giants outsource to emerging markets, CTFL certification will likely be a must for testers on global projects.
6. In the near future, CTFL certification will be instrumental in bridging the skills gap in emerging markets, equipping testers with the knowledge and expertise needed to meet global standards.
7. As emerging markets become innovation hubs, CTFL-certified testers will be at the forefront of ensuring that new technologies meet the highest quality standards.
8. With the growth of tech startups in emerging markets, CTFL certification will become a key differentiator for testers aiming to secure roles in these dynamic environments.
9. As regulations in emerging markets evolve, CTFL certification may be vital for software testing and QA professionals.
10. In the future, CTFL certification will open doors for testers in emerging markets. It will let them join international collaborations and contribute to global software projects.
How to obtain CTFL certification?
We are an Education Technology company providing certification training courses to accelerate careers of working professionals worldwide. We impart training through instructor-led classroom workshops, instructor-led live virtual training sessions, and self-paced e-learning courses.
We have successfully conducted training sessions in 108 countries across the globe and enabled thousands of working professionals to enhance the scope of their careers.
Our enterprise training portfolio includes in-demand and globally recognized certification training courses in Project Management, Quality Management, Business Analysis, IT Service Management, Agile and Scrum, Cyber Security, Data Science, and Emerging Technologies. Download our Enterprise Training Catalog from https://www.icertglobal.com/corporate-training-for-enterprises.php and https://www.icertglobal.com/index.php
Popular Courses include:
-
Project Management: PMP, CAPM ,PMI RMP
-
Quality Management: Six Sigma Black Belt ,Lean Six Sigma Green Belt, Lean Management, Minitab,CMMI
-
Business Analysis: CBAP, CCBA, ECBA
-
Agile Training: PMI-ACP , CSM , CSPO
-
Scrum Training: CSM
-
DevOps
-
Program Management: PgMP
-
Cloud Technology: Exin Cloud Computing
-
Citrix Client Adminisration: Citrix Cloud Administration
The 10 top-paying certifications to target in 2024 are:
Conclusion
In conclusion, CTFL certification is a valuable asset for software engineers. It can help them advance their careers in emerging markets. This certification shows your skills in testing, QA, and agile methods. These are vital in today's competitive market. Invest in your future by obtaining a CTFL certification and take your career to new heights.
Contact Us For More Information:
Visit :www.icertglobal.com Email : info@icertglobal.com
Read More
Are you looking to excel in the field of software testing and quality assurance? Consider getting a CTFL (Certified Tester Foundation Level) certification. There is a growing demand for skilled professionals in agile methods, especially in emerging markets. This article will explore the benefits of CTFL certification. It will cover the exam details and its value for advancing your software engineering career.
What is CTFL Certification?
The International Software Testing Qualifications Board (ISTQB) offers the CTFL certification. It is an industry standard for software testing qualifications. It covers a wide range of topics, such as testing principles, software development, and test automation. A CTFL certification shows your testing skills and knowledge of software tools. These are vital in today's competitive market.
Why Choose CTFL Certification in Emerging Markets?
Emerging markets offer a chance for software engineers. They can showcase their skills and advance their careers. By obtaining a CTFL certification, you can stand out among your peers and increase your chances of career advancement. The software apps industry is growing fast in emerging markets. An internationally recognized certification like CTFL can open doors to new jobs.
Benefits of CTFL Certification
-
Career advancement: CTFL certification can boost your career. It shows your skills in software testing.
-
Continuous improvement: Stay up-to-date with the latest testing methods. This will improve the quality of software applications.
-
Industry recognition: CTFL certification is well-known in the industry. It gives you a competitive edge in the job market.
-
International recognition: ISTQB certifications are known worldwide. They help in finding jobs abroad.
CTFL Exam Details
The CTFL exam covers many topics. They include test planning, test design, test execution, defect management, and analysis. To pass the exam, you need to study the CTFL syllabus, undergo CTFL training, and take a CTFL course to prepare for the exam. The exam is designed to test your knowledge and skills in various aspects of software testing and quality assurance.
How CTFL Certification Can Help Your Career
1. In the coming years, the demand for CTFL-certified professionals in emerging markets is expected to soar, as companies prioritize quality assurance in their software development processes.
2. As digital transformation accelerates in emerging economies, CTFL certification will soon be crucial. It will be a key asset for testing pros who want to stay competitive.
3. As software testing evolves in emerging markets, CTFL certification will be key. It will standardize testing practices and ensure quality.
4. CTFL certification will soon be a benchmark for software testers in emerging markets. It will set them apart in a competitive job market.
5. As global tech giants outsource to emerging markets, CTFL certification will likely be a must for testers on global projects.
6. In the near future, CTFL certification will be instrumental in bridging the skills gap in emerging markets, equipping testers with the knowledge and expertise needed to meet global standards.
7. As emerging markets become innovation hubs, CTFL-certified testers will be at the forefront of ensuring that new technologies meet the highest quality standards.
8. With the growth of tech startups in emerging markets, CTFL certification will become a key differentiator for testers aiming to secure roles in these dynamic environments.
9. As regulations in emerging markets evolve, CTFL certification may be vital for software testing and QA professionals.
10. In the future, CTFL certification will open doors for testers in emerging markets. It will let them join international collaborations and contribute to global software projects.
How to obtain CTFL certification?
We are an Education Technology company providing certification training courses to accelerate careers of working professionals worldwide. We impart training through instructor-led classroom workshops, instructor-led live virtual training sessions, and self-paced e-learning courses.
We have successfully conducted training sessions in 108 countries across the globe and enabled thousands of working professionals to enhance the scope of their careers.
Our enterprise training portfolio includes in-demand and globally recognized certification training courses in Project Management, Quality Management, Business Analysis, IT Service Management, Agile and Scrum, Cyber Security, Data Science, and Emerging Technologies. Download our Enterprise Training Catalog from https://www.icertglobal.com/corporate-training-for-enterprises.php and https://www.icertglobal.com/index.php
Popular Courses include:
-
Project Management: PMP, CAPM ,PMI RMP
-
Quality Management: Six Sigma Black Belt ,Lean Six Sigma Green Belt, Lean Management, Minitab,CMMI
-
Business Analysis: CBAP, CCBA, ECBA
-
Agile Training: PMI-ACP , CSM , CSPO
-
Scrum Training: CSM
-
DevOps
-
Program Management: PgMP
-
Cloud Technology: Exin Cloud Computing
-
Citrix Client Adminisration: Citrix Cloud Administration
The 10 top-paying certifications to target in 2024 are:
Conclusion
In conclusion, CTFL certification is a valuable asset for software engineers. It can help them advance their careers in emerging markets. This certification shows your skills in testing, QA, and agile methods. These are vital in today's competitive market. Invest in your future by obtaining a CTFL certification and take your career to new heights.
Contact Us For More Information:
Visit :www.icertglobal.com Email : info@icertglobal.com
Lean Management Strategies for Supply Chain Disruptions.
In today’s fast-paced business world, supply chain disruptions are becoming more common. From unexpected weather events to global pandemics, companies need to adapt quickly to keep things running smoothly. Lean management can be a powerful tool to help organizations handle these disruptions and stay efficient.
What is Lean Management?
Lean management is all about continuous improvement, reducing waste, and maximizing value for the customer. It started with the Toyota Production System and has since been adopted by many industries. The key principles include:
1. Just-in-Time:Producing goods or services only when needed, which reduces inventory costs and waste.
2. Value Stream Mapping: Analyzing the flow of materials and information to find areas for improvement.
3. Kaizen Events:Short-term projects focused on solving specific issues and driving continuous improvement.
4. Root Cause Analysis:Identifying the root causes of problems and finding solutions to prevent them from happening again.
Applying Lean to Supply Chain Management
When dealing with supply chain disruptions, lean practices can be incredibly helpful. By using strategies like demand forecasting, process optimization, and inventory management, organizations can become more efficient and better prepared for unexpected challenges. Tools like value stream mapping and root cause analysis help pinpoint weaknesses in the supply chain and allow for targeted improvements.
Lean Manufacturing and Risk Mitigation
Lean manufacturing is all about eliminating waste and improving efficiency in production. By applying lean principles such as just-in-time production and continuous improvement, companies can reduce lead times, improve quality, and cut costs. This not only boosts efficiency but also makes it easier to respond to supply chain disruptions.
Building a Lean Culture for Supply Chain Resilience
A strong lean culture is crucial for successful lean management. By promoting continuous improvement, collaboration, and problem-solving, companies can build a more resilient supply chain. This involves training employees in lean principles, encouraging innovation, and fostering a mindset of adaptability.
Challenges and Opportunities in Lean Supply Chain Management
While lean management offers many benefits, it also comes with challenges. Implementing lean practices requires significant time, resources, and commitment. Organizations need to be dedicated to the transformation process and be ready to overcome resistance to change. Additionally, maintaining a lean supply chain means constant monitoring, adjustments, and a focus on continuous improvement.
.How to obtain Lean Management certification?
We are an Education Technology company providing certification training courses to accelerate careers of working professionals worldwide. We impart training through instructor-led classroom workshops, instructor-led live virtual training sessions, and self-paced e-learning courses.
We have successfully conducted training sessions in 108 countries across the globe and enabled thousands of working professionals to enhance the scope of their careers.
Our enterprise training portfolio includes in-demand and globally recognized certification training courses in Project Management, Quality Management, Business Analysis, IT Service Management, Agile and Scrum, Cyber Security, Data Science, and Emerging Technologies. Download our Enterprise Training Catalog from https://www.icertglobal.com/corporate-training-for-enterprises.php and https://www.icertglobal.com/index.php
Popular Courses include:
-
Project Management: PMP, CAPM ,PMI RMP
-
Quality Management: Six Sigma Black Belt ,Lean Six Sigma Green Belt, Lean Management, Minitab,CMMI
-
Business Analysis: CBAP, CCBA, ECBA
-
Agile Training: PMI-ACP , CSM , CSPO
-
Scrum Training: CSM
-
DevOps
-
Program Management: PgMP
-
Cloud Technology: Exin Cloud Computing
-
Citrix Client Adminisration: Citrix Cloud Administration
The 10 top-paying certifications to target in 2024 are:
Conclusion
In conclusion, lean management principles can be a powerful tool in helping organizations navigate supply chain disruptions and enhance operational efficiency. By applying lean strategies such as demand forecasting, process optimization, and inventory management, companies can improve their resilience, reduce waste, and improve overall performance. Developing a lean culture within the organization is essential to sustaining these improvements and driving continuous innovation. With the right mindset, tools, and practices, organizations can build a lean supply chain that is agile, efficient, and responsive to the challenges of today's dynamic business environment.
Contact Us For More Information:
Visit :www.icertglobal.com Email : info@icertglobal.com
Read More
In today’s fast-paced business world, supply chain disruptions are becoming more common. From unexpected weather events to global pandemics, companies need to adapt quickly to keep things running smoothly. Lean management can be a powerful tool to help organizations handle these disruptions and stay efficient.
What is Lean Management?
Lean management is all about continuous improvement, reducing waste, and maximizing value for the customer. It started with the Toyota Production System and has since been adopted by many industries. The key principles include:
1. Just-in-Time:Producing goods or services only when needed, which reduces inventory costs and waste.
2. Value Stream Mapping: Analyzing the flow of materials and information to find areas for improvement.
3. Kaizen Events:Short-term projects focused on solving specific issues and driving continuous improvement.
4. Root Cause Analysis:Identifying the root causes of problems and finding solutions to prevent them from happening again.
Applying Lean to Supply Chain Management
When dealing with supply chain disruptions, lean practices can be incredibly helpful. By using strategies like demand forecasting, process optimization, and inventory management, organizations can become more efficient and better prepared for unexpected challenges. Tools like value stream mapping and root cause analysis help pinpoint weaknesses in the supply chain and allow for targeted improvements.
Lean Manufacturing and Risk Mitigation
Lean manufacturing is all about eliminating waste and improving efficiency in production. By applying lean principles such as just-in-time production and continuous improvement, companies can reduce lead times, improve quality, and cut costs. This not only boosts efficiency but also makes it easier to respond to supply chain disruptions.
Building a Lean Culture for Supply Chain Resilience
A strong lean culture is crucial for successful lean management. By promoting continuous improvement, collaboration, and problem-solving, companies can build a more resilient supply chain. This involves training employees in lean principles, encouraging innovation, and fostering a mindset of adaptability.
Challenges and Opportunities in Lean Supply Chain Management
While lean management offers many benefits, it also comes with challenges. Implementing lean practices requires significant time, resources, and commitment. Organizations need to be dedicated to the transformation process and be ready to overcome resistance to change. Additionally, maintaining a lean supply chain means constant monitoring, adjustments, and a focus on continuous improvement.
.How to obtain Lean Management certification?
We are an Education Technology company providing certification training courses to accelerate careers of working professionals worldwide. We impart training through instructor-led classroom workshops, instructor-led live virtual training sessions, and self-paced e-learning courses.
We have successfully conducted training sessions in 108 countries across the globe and enabled thousands of working professionals to enhance the scope of their careers.
Our enterprise training portfolio includes in-demand and globally recognized certification training courses in Project Management, Quality Management, Business Analysis, IT Service Management, Agile and Scrum, Cyber Security, Data Science, and Emerging Technologies. Download our Enterprise Training Catalog from https://www.icertglobal.com/corporate-training-for-enterprises.php and https://www.icertglobal.com/index.php
Popular Courses include:
-
Project Management: PMP, CAPM ,PMI RMP
-
Quality Management: Six Sigma Black Belt ,Lean Six Sigma Green Belt, Lean Management, Minitab,CMMI
-
Business Analysis: CBAP, CCBA, ECBA
-
Agile Training: PMI-ACP , CSM , CSPO
-
Scrum Training: CSM
-
DevOps
-
Program Management: PgMP
-
Cloud Technology: Exin Cloud Computing
-
Citrix Client Adminisration: Citrix Cloud Administration
The 10 top-paying certifications to target in 2024 are:
Conclusion
In conclusion, lean management principles can be a powerful tool in helping organizations navigate supply chain disruptions and enhance operational efficiency. By applying lean strategies such as demand forecasting, process optimization, and inventory management, companies can improve their resilience, reduce waste, and improve overall performance. Developing a lean culture within the organization is essential to sustaining these improvements and driving continuous innovation. With the right mindset, tools, and practices, organizations can build a lean supply chain that is agile, efficient, and responsive to the challenges of today's dynamic business environment.
Contact Us For More Information:
Visit :www.icertglobal.com Email : info@icertglobal.com
5 Key Types of Quality Management Systems You Should Know
Quality management systems are essential for organizations to ensure that they meet customer requirements and continuously improve their processes. There are various types of quality management systems that companies can implement to achieve operational excellence and drive business efficiency. In this article, we will explore the 5 key types of quality management systems that are widely used in different industries.
ISO 9001
ISO 9001 is the most well-known quality management standard that focuses on meeting customer requirements and enhancing customer satisfaction. It provides a framework for organizations to establish a quality management system, set quality objectives, and monitor their performance. By implementing ISO 9001, companies can improve their processes, reduce errors, and enhance customer trust.
ISO 14001
ISO 14001 is a standard specifically for environmental management systems. It helps organizations to minimize their environmental impact, comply with environmental regulations, and improve sustainability. By implementing ISO 14001, companies can reduce waste, conserve resources, and demonstrate their commitment to environmental responsibility.
Total Quality Management
Total Quality Management (TQM) is a holistic approach to quality management that involves all employees in the continuous improvement of processes. TQM focuses on customer satisfaction, employee involvement, and process improvement. By implementing TQM principles, organizations can enhance product quality, reduce waste, and increase customer loyalty.
Six Sigma
Six Sigma is a data-driven approach to quality management that aims to reduce defects and variations in processes. It uses statistical methods to analyze data, identify root causes of problems, and implement solutions to improve process performance. By applying Six Sigma techniques, organizations can enhance quality, increase productivity, and achieve cost savings.
Lean Manufacturing
Lean Manufacturing is a systematic approach to eliminating waste and maximizing value in processes. It focuses on improving efficiency, reducing lead times, and increasing customer value. By implementing Lean principles, companies can optimize their operations, minimize costs, and enhance competitiveness in the market.
How to obtain Quality Management certification?
We are an Education Technology company providing certification training courses to accelerate careers of working professionals worldwide. We impart training through instructor-led classroom workshops, instructor-led live virtual training sessions, and self-paced e-learning courses.
We have successfully conducted training sessions in 108 countries across the globe and enabled thousands of working professionals to enhance the scope of their careers.
Our enterprise training portfolio includes in-demand and globally recognized certification training courses in Project Management, Quality Management, Business Analysis, IT Service Management, Agile and Scrum, Cyber Security, Data Science, and Emerging Technologies. Download our Enterprise Training Catalog from https://www.icertglobal.com/corporate-training-for-enterprises.php and https://www.icertglobal.com/index.php
Popular Courses include:
-
Project Management: PMP, CAPM ,PMI RMP
-
Quality Management: Six Sigma Black Belt ,Lean Six Sigma Green Belt, Lean Management, Minitab,CMMI
-
Business Analysis: CBAP, CCBA, ECBA
-
Agile Training: PMI-ACP , CSM , CSPO
-
Scrum Training: CSM
-
DevOps
-
Program Management: PgMP
-
Cloud Technology: Exin Cloud Computing
-
Citrix Client Adminisration: Citrix Cloud Administration
The 10 top-paying certifications to target in 2024 are:
Conclusion
In conclusion, quality management systems play a crucial role in ensuring that organizations deliver high-quality products and services to their customers. By implementing the 5 key types of quality management systems - ISO 9001, ISO 14001, Total Quality Management, Six Sigma, and Lean Manufacturing - companies can drive continuous improvement, increase efficiency, and achieve competitive advantage in the industry. It is important for organizations to select the right quality management system that aligns with their business goals and objectives to truly realize the benefits of quality management.
Contact Us For More Information:
Visit :www.icertglobal.com Email : info@icertglobal.com
Read More
Quality management systems are essential for organizations to ensure that they meet customer requirements and continuously improve their processes. There are various types of quality management systems that companies can implement to achieve operational excellence and drive business efficiency. In this article, we will explore the 5 key types of quality management systems that are widely used in different industries.
ISO 9001
ISO 9001 is the most well-known quality management standard that focuses on meeting customer requirements and enhancing customer satisfaction. It provides a framework for organizations to establish a quality management system, set quality objectives, and monitor their performance. By implementing ISO 9001, companies can improve their processes, reduce errors, and enhance customer trust.
ISO 14001
ISO 14001 is a standard specifically for environmental management systems. It helps organizations to minimize their environmental impact, comply with environmental regulations, and improve sustainability. By implementing ISO 14001, companies can reduce waste, conserve resources, and demonstrate their commitment to environmental responsibility.
Total Quality Management
Total Quality Management (TQM) is a holistic approach to quality management that involves all employees in the continuous improvement of processes. TQM focuses on customer satisfaction, employee involvement, and process improvement. By implementing TQM principles, organizations can enhance product quality, reduce waste, and increase customer loyalty.
Six Sigma
Six Sigma is a data-driven approach to quality management that aims to reduce defects and variations in processes. It uses statistical methods to analyze data, identify root causes of problems, and implement solutions to improve process performance. By applying Six Sigma techniques, organizations can enhance quality, increase productivity, and achieve cost savings.
Lean Manufacturing
Lean Manufacturing is a systematic approach to eliminating waste and maximizing value in processes. It focuses on improving efficiency, reducing lead times, and increasing customer value. By implementing Lean principles, companies can optimize their operations, minimize costs, and enhance competitiveness in the market.
How to obtain Quality Management certification?
We are an Education Technology company providing certification training courses to accelerate careers of working professionals worldwide. We impart training through instructor-led classroom workshops, instructor-led live virtual training sessions, and self-paced e-learning courses.
We have successfully conducted training sessions in 108 countries across the globe and enabled thousands of working professionals to enhance the scope of their careers.
Our enterprise training portfolio includes in-demand and globally recognized certification training courses in Project Management, Quality Management, Business Analysis, IT Service Management, Agile and Scrum, Cyber Security, Data Science, and Emerging Technologies. Download our Enterprise Training Catalog from https://www.icertglobal.com/corporate-training-for-enterprises.php and https://www.icertglobal.com/index.php
Popular Courses include:
-
Project Management: PMP, CAPM ,PMI RMP
-
Quality Management: Six Sigma Black Belt ,Lean Six Sigma Green Belt, Lean Management, Minitab,CMMI
-
Business Analysis: CBAP, CCBA, ECBA
-
Agile Training: PMI-ACP , CSM , CSPO
-
Scrum Training: CSM
-
DevOps
-
Program Management: PgMP
-
Cloud Technology: Exin Cloud Computing
-
Citrix Client Adminisration: Citrix Cloud Administration
The 10 top-paying certifications to target in 2024 are:
Conclusion
In conclusion, quality management systems play a crucial role in ensuring that organizations deliver high-quality products and services to their customers. By implementing the 5 key types of quality management systems - ISO 9001, ISO 14001, Total Quality Management, Six Sigma, and Lean Manufacturing - companies can drive continuous improvement, increase efficiency, and achieve competitive advantage in the industry. It is important for organizations to select the right quality management system that aligns with their business goals and objectives to truly realize the benefits of quality management.
Contact Us For More Information:
Visit :www.icertglobal.com Email : info@icertglobal.com
Top 10 Tips for Passing the MINITAB Certification Exam!
Are you looking to excel in the world of data analysis and statistical software? One key step to demonstrating your expertise in MINITAB is by passing the MINITAB Certification Exam. This certification is a valuable asset for anyone looking to showcase their proficiency in data analysis, statistical tools, and process improvement using MINITAB software. To help you succeed in this endeavor, here are top 10 tips for passing the MINITAB Certification Exam:
1. Start with a Strong Foundation
Before diving into exam preparation, ensure you have a solid understanding of the key concepts and techniques in MINITAB. Familiarize yourself with statistical analysis, data visualization, hypothesis testing, and data interpretation to build a strong foundation.
2. Utilize Study Guides and Resources
Make use of MINITAB training materials, study guides, and online resources to enhance your knowledge and skills. Practice using the software to manipulate data, perform statistical analysis, and apply quality control methods.
3. Focus on Statistics and Analysis Techniques
Pay special attention to statistical tools and analysis techniques commonly used in MINITAB. Brush up on topics such as six sigma, quality control, and data manipulation to ensure you are well-prepared for the exam.
4. Master MINITAB Techniques
Take the time to master MINITAB techniques such as generating graphs, conducting hypothesis tests, and interpreting results. Practice using the software to analyze data sets and draw meaningful insights from your findings.
5. Practice Exam Preparation
Set aside dedicated time for exam preparation and practice using sample questions and mock exams. This will help you familiarize yourself with the format of the exam and build confidence in your abilities.
6. Seek Expert Guidance
Consider seeking guidance from MINITAB experts or instructors who can provide valuable insights and tips for success. Their experience and expertise can help you navigate challenging concepts and refine your skills.
7. Stay Updated on MINITAB Developments
Stay informed about the latest developments and updates in MINITAB software. Familiarize yourself with new features and enhancements that may be relevant to the certification exam.
8. Focus on Practical Tips
In addition to theoretical knowledge, focus on practical tips for using MINITAB effectively. Learn shortcuts, best practices, and time-saving techniques that can help you navigate the software efficiently during the exam.
9. Embrace a Growth Mindset
Approach the MINITAB Certification Exam with a growth mindset, embracing challenges as opportunities for learning and growth. Stay positive and motivated throughout your preparation journey.
10. Visualize Exam Success
Visualize yourself achieving success in the MINITAB Certification Exam. Imagine yourself confidently answering questions, applying MINITAB techniques, and demonstrating your expertise in data analysis.
How to obtain Python certification?
We are an Education Technology company providing certification training courses to accelerate careers of working professionals worldwide. We impart training through instructor-led classroom workshops, instructor-led live virtual training sessions, and self-paced e-learning courses.
We have successfully conducted training sessions in 108 countries across the globe and enabled thousands of working professionals to enhance the scope of their careers.
Our enterprise training portfolio includes in-demand and globally recognized certification training courses in Project Management, Quality Management, Business Analysis, IT Service Management, Agile and Scrum, Cyber Security, Data Science, and Emerging Technologies. Download our Enterprise Training Catalog from https://www.icertglobal.com/corporate-training-for-enterprises.php and https://www.icertglobal.com/index.php
Popular Courses include:
-
Project Management: PMP, CAPM ,PMI RMP
-
Quality Management: Six Sigma Black Belt ,Lean Six Sigma Green Belt, Lean Management, Minitab,CMMI
-
Business Analysis: CBAP, CCBA, ECBA
-
Agile Training: PMI-ACP , CSM , CSPO
-
Scrum Training: CSM
-
DevOps
-
Program Management: PgMP
-
Cloud Technology: Exin Cloud Computing
-
Citrix Client Adminisration: Citrix Cloud Administration
The 10 top-paying certifications to target in 2024 are:
Conclusion
By following these top 10 tips for passing the MINITAB Certification Exam, you can enhance your chances of success and demonstrate your proficiency in MINITAB software. Remember to stay focused, dedicated, and motivated throughout your exam preparation journey. Good luck!
Contact Us :
Contact Us For More Information:
Visit :www.icertglobal.com Email : info@icertglobal.com
Read More
Are you looking to excel in the world of data analysis and statistical software? One key step to demonstrating your expertise in MINITAB is by passing the MINITAB Certification Exam. This certification is a valuable asset for anyone looking to showcase their proficiency in data analysis, statistical tools, and process improvement using MINITAB software. To help you succeed in this endeavor, here are top 10 tips for passing the MINITAB Certification Exam:
1. Start with a Strong Foundation
Before diving into exam preparation, ensure you have a solid understanding of the key concepts and techniques in MINITAB. Familiarize yourself with statistical analysis, data visualization, hypothesis testing, and data interpretation to build a strong foundation.
2. Utilize Study Guides and Resources
Make use of MINITAB training materials, study guides, and online resources to enhance your knowledge and skills. Practice using the software to manipulate data, perform statistical analysis, and apply quality control methods.
3. Focus on Statistics and Analysis Techniques
Pay special attention to statistical tools and analysis techniques commonly used in MINITAB. Brush up on topics such as six sigma, quality control, and data manipulation to ensure you are well-prepared for the exam.
4. Master MINITAB Techniques
Take the time to master MINITAB techniques such as generating graphs, conducting hypothesis tests, and interpreting results. Practice using the software to analyze data sets and draw meaningful insights from your findings.
5. Practice Exam Preparation
Set aside dedicated time for exam preparation and practice using sample questions and mock exams. This will help you familiarize yourself with the format of the exam and build confidence in your abilities.
6. Seek Expert Guidance
Consider seeking guidance from MINITAB experts or instructors who can provide valuable insights and tips for success. Their experience and expertise can help you navigate challenging concepts and refine your skills.
7. Stay Updated on MINITAB Developments
Stay informed about the latest developments and updates in MINITAB software. Familiarize yourself with new features and enhancements that may be relevant to the certification exam.
8. Focus on Practical Tips
In addition to theoretical knowledge, focus on practical tips for using MINITAB effectively. Learn shortcuts, best practices, and time-saving techniques that can help you navigate the software efficiently during the exam.
9. Embrace a Growth Mindset
Approach the MINITAB Certification Exam with a growth mindset, embracing challenges as opportunities for learning and growth. Stay positive and motivated throughout your preparation journey.
10. Visualize Exam Success
Visualize yourself achieving success in the MINITAB Certification Exam. Imagine yourself confidently answering questions, applying MINITAB techniques, and demonstrating your expertise in data analysis.
How to obtain Python certification?
We are an Education Technology company providing certification training courses to accelerate careers of working professionals worldwide. We impart training through instructor-led classroom workshops, instructor-led live virtual training sessions, and self-paced e-learning courses.
We have successfully conducted training sessions in 108 countries across the globe and enabled thousands of working professionals to enhance the scope of their careers.
Our enterprise training portfolio includes in-demand and globally recognized certification training courses in Project Management, Quality Management, Business Analysis, IT Service Management, Agile and Scrum, Cyber Security, Data Science, and Emerging Technologies. Download our Enterprise Training Catalog from https://www.icertglobal.com/corporate-training-for-enterprises.php and https://www.icertglobal.com/index.php
Popular Courses include:
-
Project Management: PMP, CAPM ,PMI RMP
-
Quality Management: Six Sigma Black Belt ,Lean Six Sigma Green Belt, Lean Management, Minitab,CMMI
-
Business Analysis: CBAP, CCBA, ECBA
-
Agile Training: PMI-ACP , CSM , CSPO
-
Scrum Training: CSM
-
DevOps
-
Program Management: PgMP
-
Cloud Technology: Exin Cloud Computing
-
Citrix Client Adminisration: Citrix Cloud Administration
The 10 top-paying certifications to target in 2024 are:
Conclusion
By following these top 10 tips for passing the MINITAB Certification Exam, you can enhance your chances of success and demonstrate your proficiency in MINITAB software. Remember to stay focused, dedicated, and motivated throughout your exam preparation journey. Good luck!
Contact Us :
Contact Us For More Information:
Visit :www.icertglobal.com Email : info@icertglobal.com
Industries Seeking Six Sigma Yellow Belts in 2024: Jobs.
Are you considering getting your Six Sigma Yellow Belt certification and wondering about the job market trends in 2024? Look no further! In this article, we will dive into the top industries that are actively seeking Six Sigma Yellow Belt certified professionals and explore the career opportunities that await you in the coming year.
The Demand for Six Sigma Yellow Belt Certified Professionals in 2024
Six Sigma Yellow Belt certification is a valuable asset in today's competitive job market. Employers across various industries are increasingly recognizing the importance of process improvement methodologies like Six Sigma in driving operational efficiency and cost savings. As a result, the demand for professionals with Six Sigma Yellow Belt certification is on the rise, with many industries actively seeking qualified candidates to join their workforce.
Which industries are at the forefront of hiring Six Sigma Yellow Belt certified professionals in 2024?
- Manufacturing Industry: The manufacturing industry continues to be a hotbed for Six Sigma initiatives, with many companies using the methodology to streamline their production processes and reduce defects. Manufacturers are actively seeking Six Sigma Yellow Belt certified professionals to help drive continuous improvement and quality assurance efforts.
- Healthcare Industry: In the healthcare industry, where patient safety and quality of care are top priorities, Six Sigma methodologies are being increasingly adopted to enhance operational efficiency and reduce medical errors. Healthcare organizations are looking for Six Sigma Yellow Belt certified professionals to lead process improvement projects and drive quality improvements in patient care.
- Financial Services Industry: In the fast-paced world of finance, organizations are turning to Six Sigma to optimize their business processes, enhance customer satisfaction, and improve risk management practices. Financial services firms are actively recruiting Six Sigma Yellow Belt certified professionals to help identify and eliminate inefficiencies in their operations.
- Information Technology Industry: With the ever-evolving landscape of technology, IT companies are leveraging Six Sigma principles to enhance their software development processes, improve product quality, and increase customer satisfaction. IT firms are seeking Six Sigma Yellow Belt certified professionals to lead project teams and drive continuous improvement initiatives.
- Retail Industry: In the competitive retail sector, Six Sigma methodologies are being used to streamline supply chain operations, enhance inventory management practices, and improve overall customer experience. Retailers are looking for Six Sigma Yellow Belt certified professionals to help identify and eliminate process bottlenecks and drive efficiency gains in their operations.
How to stand out as a Six Sigma Yellow Belt certified professional in the job market?
- Achieving Six Sigma Yellow Belt certification is a great first step towards a successful career in process improvement. To stand out in the job market and attract the attention of top employers, consider the following tips:
- Highlight your certification: Make sure to prominently display your Six Sigma Yellow Belt certification on your resume and LinkedIn profile to showcase your expertise in process improvement.
- Demonstrate your experience: Provide concrete examples of how you have applied Six Sigma methodologies in previous roles to drive measurable results and business impact.
- Keep learning and growing: Stay updated on the latest trends and developments in Six Sigma methodology and continuously strive to enhance your skills and knowledge in process improvement.
By following these tips, you can position yourself as a top candidate for Six Sigma Yellow Belt certified roles in the industries that are actively hiring in 2024.
How to obtain Six Sigma Yellow Belt Certification?
We are an Education Technology company providing certification training courses to accelerate careers of working professionals worldwide. We impart training through instructor-led classroom workshops, instructor-led live virtual training sessions, and self-paced e-learning courses.
We have successfully conducted training sessions in 108 countries across the globe and enabled thousands of working professionals to enhance the scope of their careers.
Our enterprise training portfolio includes in-demand and globally recognized certification training courses in Project Management, Quality Management, Business Analysis, IT Service Management, Agile and Scrum, Cyber Security, Data Science, and Emerging Technologies. Download our Enterprise Training Catalog from https://www.icertglobal.com/corporate-training-for-enterprises.php and https://www.icertglobal.com/index.php
Popular Courses include:
- Project Management: PMP, CAPM ,PMI RMP
- Quality Management: Six Sigma Black Belt ,Lean Six Sigma Green Belt, Lean Management, Minitab,CMMI
- Business Analysis: CBAP, CCBA, ECBA
- Agile Training: PMI-ACP , CSM , CSPO
- Scrum Training: CSM
- DevOps
- Program Management: PgMP
- Cloud Technology: Exin Cloud Computing
- Citrix Client Adminisration: Citrix Cloud Administration
The 10 top-paying certifications to target in 2024 are:
- Certified Information Systems Security Professional® (CISSP)
- AWS Certified Solutions Architect
- Google Certified Professional Cloud Architect
- Big Data Certification
- Data Science Certification
- Certified In Risk And Information Systems Control (CRISC)
- Certified Information Security Manager(CISM)
- Project Management Professional (PMP)® Certification
- Certified Ethical Hacker (CEH)
- Certified Scrum Master (CSM)
Conclusion
In conclusion, the job market for Six Sigma Yellow Belt certified professionals is thriving in 2024, with numerous industries seeking qualified candidates to drive process improvement initiatives. By obtaining your certification and showcasing your expertise, you can take advantage of the exciting career opportunities that await you in the coming year. Don't miss out on the chance to advance your career and make a meaningful impact in the industry of your choice. Start your journey towards becoming a Six Sigma Yellow Belt certified professional today!
Contact Us :
Contact Us For More Information:
Visit :www.icertglobal.com Email : info@icertglobal.com
Read More
Are you considering getting your Six Sigma Yellow Belt certification and wondering about the job market trends in 2024? Look no further! In this article, we will dive into the top industries that are actively seeking Six Sigma Yellow Belt certified professionals and explore the career opportunities that await you in the coming year.
The Demand for Six Sigma Yellow Belt Certified Professionals in 2024
Six Sigma Yellow Belt certification is a valuable asset in today's competitive job market. Employers across various industries are increasingly recognizing the importance of process improvement methodologies like Six Sigma in driving operational efficiency and cost savings. As a result, the demand for professionals with Six Sigma Yellow Belt certification is on the rise, with many industries actively seeking qualified candidates to join their workforce.
Which industries are at the forefront of hiring Six Sigma Yellow Belt certified professionals in 2024?
- Manufacturing Industry: The manufacturing industry continues to be a hotbed for Six Sigma initiatives, with many companies using the methodology to streamline their production processes and reduce defects. Manufacturers are actively seeking Six Sigma Yellow Belt certified professionals to help drive continuous improvement and quality assurance efforts.
- Healthcare Industry: In the healthcare industry, where patient safety and quality of care are top priorities, Six Sigma methodologies are being increasingly adopted to enhance operational efficiency and reduce medical errors. Healthcare organizations are looking for Six Sigma Yellow Belt certified professionals to lead process improvement projects and drive quality improvements in patient care.
- Financial Services Industry: In the fast-paced world of finance, organizations are turning to Six Sigma to optimize their business processes, enhance customer satisfaction, and improve risk management practices. Financial services firms are actively recruiting Six Sigma Yellow Belt certified professionals to help identify and eliminate inefficiencies in their operations.
- Information Technology Industry: With the ever-evolving landscape of technology, IT companies are leveraging Six Sigma principles to enhance their software development processes, improve product quality, and increase customer satisfaction. IT firms are seeking Six Sigma Yellow Belt certified professionals to lead project teams and drive continuous improvement initiatives.
- Retail Industry: In the competitive retail sector, Six Sigma methodologies are being used to streamline supply chain operations, enhance inventory management practices, and improve overall customer experience. Retailers are looking for Six Sigma Yellow Belt certified professionals to help identify and eliminate process bottlenecks and drive efficiency gains in their operations.
How to stand out as a Six Sigma Yellow Belt certified professional in the job market?
- Achieving Six Sigma Yellow Belt certification is a great first step towards a successful career in process improvement. To stand out in the job market and attract the attention of top employers, consider the following tips:
- Highlight your certification: Make sure to prominently display your Six Sigma Yellow Belt certification on your resume and LinkedIn profile to showcase your expertise in process improvement.
- Demonstrate your experience: Provide concrete examples of how you have applied Six Sigma methodologies in previous roles to drive measurable results and business impact.
- Keep learning and growing: Stay updated on the latest trends and developments in Six Sigma methodology and continuously strive to enhance your skills and knowledge in process improvement.
By following these tips, you can position yourself as a top candidate for Six Sigma Yellow Belt certified roles in the industries that are actively hiring in 2024.
How to obtain Six Sigma Yellow Belt Certification?
We are an Education Technology company providing certification training courses to accelerate careers of working professionals worldwide. We impart training through instructor-led classroom workshops, instructor-led live virtual training sessions, and self-paced e-learning courses.
We have successfully conducted training sessions in 108 countries across the globe and enabled thousands of working professionals to enhance the scope of their careers.
Our enterprise training portfolio includes in-demand and globally recognized certification training courses in Project Management, Quality Management, Business Analysis, IT Service Management, Agile and Scrum, Cyber Security, Data Science, and Emerging Technologies. Download our Enterprise Training Catalog from https://www.icertglobal.com/corporate-training-for-enterprises.php and https://www.icertglobal.com/index.php
Popular Courses include:
- Project Management: PMP, CAPM ,PMI RMP
- Quality Management: Six Sigma Black Belt ,Lean Six Sigma Green Belt, Lean Management, Minitab,CMMI
- Business Analysis: CBAP, CCBA, ECBA
- Agile Training: PMI-ACP , CSM , CSPO
- Scrum Training: CSM
- DevOps
- Program Management: PgMP
- Cloud Technology: Exin Cloud Computing
- Citrix Client Adminisration: Citrix Cloud Administration
The 10 top-paying certifications to target in 2024 are:
- Certified Information Systems Security Professional® (CISSP)
- AWS Certified Solutions Architect
- Google Certified Professional Cloud Architect
- Big Data Certification
- Data Science Certification
- Certified In Risk And Information Systems Control (CRISC)
- Certified Information Security Manager(CISM)
- Project Management Professional (PMP)® Certification
- Certified Ethical Hacker (CEH)
- Certified Scrum Master (CSM)
Conclusion
In conclusion, the job market for Six Sigma Yellow Belt certified professionals is thriving in 2024, with numerous industries seeking qualified candidates to drive process improvement initiatives. By obtaining your certification and showcasing your expertise, you can take advantage of the exciting career opportunities that await you in the coming year. Don't miss out on the chance to advance your career and make a meaningful impact in the industry of your choice. Start your journey towards becoming a Six Sigma Yellow Belt certified professional today!
Contact Us :
Contact Us For More Information:
Visit :www.icertglobal.com Email : info@icertglobal.com
CTFL for Test Managers: Key Benefits and Valuable Insights
In today's fast-paced world of software development, test managers play a crucial role in ensuring the quality and reliability of the products being delivered to customers. The Certified Tester Foundation Level (CTFL) certification is designed specifically for test managers, providing them with the knowledge and skills needed to excel in their roles. In this article, we will explore the benefits and insights of CTFL for test managers, highlighting how this certification can enhance their abilities and drive success in their careers.
What is CTFL?
CTFL stands for Certified Tester Foundation Level, and it is a globally recognized certification that validates an individual's proficiency in software testing and quality assurance. The CTFL certification exam covers a wide range of topics related to test management, including test planning, test strategy, test design, test execution, defect management, test automation, and more. By obtaining the CTFL certification, test managers demonstrate their commitment to excellence and their dedication to continuous improvement in the field of software testing.
Benefits of CTFL for Test Managers
1. Enhanced Leadership Skills
Test managers with CTFL certification have a thorough understanding of best practices in test management, team management, and quality assurance. They are equipped with the knowledge and skills needed to lead their teams effectively, establish clear objectives, and drive performance excellence. CTFL certification helps test managers develop strong leadership skills that are essential for success in today's competitive software testing industry.
2. Improved Communication and Stakeholder Management
Effective communication is crucial in test management, as it ensures that all stakeholders are informed and aligned throughout the testing process. CTFL-certified test managers have the communication skills needed to interact with team members, developers, project managers, and customers effectively. They can articulate complex testing concepts in a clear and concise manner, building trust and rapport with stakeholders at all levels.
3. Strong Problem-Solving and Decision-Making Skills
Test managers often encounter complex challenges and critical decisions during the testing process. CTFL certification equips test managers with the problem-solving skills and analytical mindset needed to address issues efficiently and make informed decisions under pressure. By mastering critical thinking, time management, and decision-making skills, CTFL-certified test managers can navigate through obstacles and drive successful outcomes for their testing projects.
4. Career Advancement and Development Opportunities
CTFL certification opens doors to new career opportunities and advancement for test managers. Employers value professionals with recognized certifications, as they demonstrate a commitment to excellence and continuous learning. With CTFL certification, test managers can enhance their credibility, expand their skill set, and pursue higher-level roles in the software testing industry. CTFL certification serves as a valuable asset for career growth and development, providing test managers with the competitive edge needed to excel in their careers.
Insights from CTFL Certification
CTFL certification offers valuable insights and best practices for test managers, helping them improve their test processes, enhance quality assurance practices, and drive continuous improvement in their testing projects. By leveraging the knowledge and skills gained through CTFL certification, test managers can deliver high-quality products, mitigate risks effectively, and exceed customer expectations. CTFL-certified test managers are well-equipped to lead their teams to success, implement industry best practices, and achieve excellence in software testing.
How to obtain CTFL certification?
We are an Education Technology company providing certification training courses to accelerate careers of working professionals worldwide. We impart training through instructor-led classroom workshops, instructor-led live virtual training sessions, and self-paced e-learning courses.
We have successfully conducted training sessions in 108 countries across the globe and enabled thousands of working professionals to enhance the scope of their careers.
Our enterprise training portfolio includes in-demand and globally recognized certification training courses in Project Management, Quality Management, Business Analysis, IT Service Management, Agile and Scrum, Cyber Security, Data Science, and Emerging Technologies. Download our Enterprise Training Catalog from https://www.icertglobal.com/corporate-training-for-enterprises.php and https://www.icertglobal.com/index.php
Popular Courses include:
-
Project Management: PMP, CAPM ,PMI RMP
-
Quality Management: Six Sigma Black Belt ,Lean Six Sigma Green Belt, Lean Management, Minitab,CMMI
-
Business Analysis: CBAP, CCBA, ECBA
-
Agile Training: PMI-ACP , CSM , CSPO
-
Scrum Training: CSM
-
DevOps
-
Program Management: PgMP
-
Cloud Technology: Exin Cloud Computing
-
Citrix Client Adminisration: Citrix Cloud Administration
The 10 top-paying certifications to target in 2024 are:
Conclusion
In conclusion, CTFL certification is a valuable asset for test managers seeking to enhance their skills, advance their careers, and excel in the field of software testing. By obtaining CTFL certification, test managers can gain a competitive edge, demonstrate their expertise, and drive success in their testing projects. CTFL certification provides test managers with the knowledge, skills, and insights needed to lead their teams to success, deliver high-quality products, and achieve excellence in software testing.
Contact Us For More Information:
Visit :www.icertglobal.comEmail : info@icertglobal.com
Read More
In today's fast-paced world of software development, test managers play a crucial role in ensuring the quality and reliability of the products being delivered to customers. The Certified Tester Foundation Level (CTFL) certification is designed specifically for test managers, providing them with the knowledge and skills needed to excel in their roles. In this article, we will explore the benefits and insights of CTFL for test managers, highlighting how this certification can enhance their abilities and drive success in their careers.
What is CTFL?
CTFL stands for Certified Tester Foundation Level, and it is a globally recognized certification that validates an individual's proficiency in software testing and quality assurance. The CTFL certification exam covers a wide range of topics related to test management, including test planning, test strategy, test design, test execution, defect management, test automation, and more. By obtaining the CTFL certification, test managers demonstrate their commitment to excellence and their dedication to continuous improvement in the field of software testing.
Benefits of CTFL for Test Managers
1. Enhanced Leadership Skills
Test managers with CTFL certification have a thorough understanding of best practices in test management, team management, and quality assurance. They are equipped with the knowledge and skills needed to lead their teams effectively, establish clear objectives, and drive performance excellence. CTFL certification helps test managers develop strong leadership skills that are essential for success in today's competitive software testing industry.
2. Improved Communication and Stakeholder Management
Effective communication is crucial in test management, as it ensures that all stakeholders are informed and aligned throughout the testing process. CTFL-certified test managers have the communication skills needed to interact with team members, developers, project managers, and customers effectively. They can articulate complex testing concepts in a clear and concise manner, building trust and rapport with stakeholders at all levels.
3. Strong Problem-Solving and Decision-Making Skills
Test managers often encounter complex challenges and critical decisions during the testing process. CTFL certification equips test managers with the problem-solving skills and analytical mindset needed to address issues efficiently and make informed decisions under pressure. By mastering critical thinking, time management, and decision-making skills, CTFL-certified test managers can navigate through obstacles and drive successful outcomes for their testing projects.
4. Career Advancement and Development Opportunities
CTFL certification opens doors to new career opportunities and advancement for test managers. Employers value professionals with recognized certifications, as they demonstrate a commitment to excellence and continuous learning. With CTFL certification, test managers can enhance their credibility, expand their skill set, and pursue higher-level roles in the software testing industry. CTFL certification serves as a valuable asset for career growth and development, providing test managers with the competitive edge needed to excel in their careers.
Insights from CTFL Certification
CTFL certification offers valuable insights and best practices for test managers, helping them improve their test processes, enhance quality assurance practices, and drive continuous improvement in their testing projects. By leveraging the knowledge and skills gained through CTFL certification, test managers can deliver high-quality products, mitigate risks effectively, and exceed customer expectations. CTFL-certified test managers are well-equipped to lead their teams to success, implement industry best practices, and achieve excellence in software testing.
How to obtain CTFL certification?
We are an Education Technology company providing certification training courses to accelerate careers of working professionals worldwide. We impart training through instructor-led classroom workshops, instructor-led live virtual training sessions, and self-paced e-learning courses.
We have successfully conducted training sessions in 108 countries across the globe and enabled thousands of working professionals to enhance the scope of their careers.
Our enterprise training portfolio includes in-demand and globally recognized certification training courses in Project Management, Quality Management, Business Analysis, IT Service Management, Agile and Scrum, Cyber Security, Data Science, and Emerging Technologies. Download our Enterprise Training Catalog from https://www.icertglobal.com/corporate-training-for-enterprises.php and https://www.icertglobal.com/index.php
Popular Courses include:
-
Project Management: PMP, CAPM ,PMI RMP
-
Quality Management: Six Sigma Black Belt ,Lean Six Sigma Green Belt, Lean Management, Minitab,CMMI
-
Business Analysis: CBAP, CCBA, ECBA
-
Agile Training: PMI-ACP , CSM , CSPO
-
Scrum Training: CSM
-
DevOps
-
Program Management: PgMP
-
Cloud Technology: Exin Cloud Computing
-
Citrix Client Adminisration: Citrix Cloud Administration
The 10 top-paying certifications to target in 2024 are:
Conclusion
In conclusion, CTFL certification is a valuable asset for test managers seeking to enhance their skills, advance their careers, and excel in the field of software testing. By obtaining CTFL certification, test managers can gain a competitive edge, demonstrate their expertise, and drive success in their testing projects. CTFL certification provides test managers with the knowledge, skills, and insights needed to lead their teams to success, deliver high-quality products, and achieve excellence in software testing.
Contact Us For More Information:
Visit :www.icertglobal.comEmail : info@icertglobal.com
CTFL Certification: Benefits for Developers and Managers
In today's competitive job market, having a CTFL certification can significantly boost your career prospects as a developer or manager. The Certified Tester Foundation Level (CTFL) certification is a globally recognized credential that demonstrates your expertise in software testing. In this article, we will explore the benefits of CTFL certification for both developers and managers, as well as the process of obtaining this valuable credential.
Benefits of CTFL Certification
-
Enhanced Skills: CTFL certification equips you with the essential skills and knowledge required to excel in software testing. This includes understanding different testing techniques, tools, and methodologies.
-
Career Advancement: Holding a CTFL certification can open up new job opportunities and help you advance in your career. Employers often prefer candidates with relevant certifications, as it demonstrates their commitment to professional development.
-
Increased Credibility: CTFL certification enhances your credibility as a software testing professional. It shows that you have met the rigorous standards set by the International Software Testing Qualifications Board (ISTQB).
-
Higher Salary: Certified professionals typically command higher salaries than their non-certified counterparts. CTFL certification can lead to increased earning potential and better job prospects.
CTFL Certification for Developers
For developers, CTFL certification offers several advantages. It provides a solid foundation in software testing principles and practices, helping developers to deliver high-quality code. By understanding the importance of testing early in the development process, developers can identify and fix issues more efficiently, resulting in a more robust and reliable product.
CTFL Certification for Managers
Managers who hold a CTFL certification can effectively lead their teams and ensure the successful completion of testing projects. They have the knowledge and skills needed to make informed decisions about testing strategies, resource allocation, and risk management. CTFL certification also allows managers to communicate more effectively with their technical teams, fostering collaboration and innovation.
CTFL Exam and Syllabus
The CTFL exam covers a wide range of topics related to software testing, including testing principles, test design techniques, and test management. It assesses your understanding of key concepts and your ability to apply them in real-world scenarios. The exam is administered by accredited training providers and consists of multiple-choice questions.
The CTFL syllabus includes the following areas:
-
Fundamentals of software testing
-
Testing levels and types
-
Static testing
-
Test design techniques
-
Test management
-
Tools support for testing
How to Get CTFL Certification
To obtain CTFL certification, you must pass the official exam administered by an accredited training provider. It is recommended to prepare for the exam by studying the CTFL syllabus and using practice tests to assess your knowledge. Once you pass the exam, you will receive your certification, which is valid for life.
How to obtain CTFL Certification?
We are an Education Technology company providing certification training courses to accelerate careers of working professionals worldwide. We impart training through instructor-led classroom workshops, instructor-led live virtual training sessions, and self-paced e-learning courses.
We have successfully conducted training sessions in 108 countries across the globe and enabled thousands of working professionals to enhance the scope of their careers.
Our enterprise training portfolio includes in-demand and globally recognized certification training courses in Project Management, Quality Management, Business Analysis, IT Service Management, Agile and Scrum, Cyber Security, Data Science, and Emerging Technologies. Download our Enterprise Training Catalog from https://www.icertglobal.com/corporate-training-for-enterprises.php and https://www.icertglobal.com/index.php
Popular Courses include:
-
Project Management: PMP, CAPM ,PMI RMP
-
Quality Management: Six Sigma Black Belt ,Lean Six Sigma Green Belt, Lean Management, Minitab,CMMI
-
Business Analysis: CBAP, CCBA, ECBA
-
Agile Training: PMI-ACP , CSM , CSPO
-
Scrum Training: CSM
-
DevOps
-
Program Management: PgMP
-
Cloud Technology: Exin Cloud Computing
-
Citrix Client Adminisration: Citrix Cloud Administration
The 10 top-paying certifications to target in 2024 are:
Conclusion
In conclusion, CTFL certification offers numerous benefits for developers and managers alike. It enhances your skills, opens up new career opportunities, and increases your credibility in the field of software testing. Whether you are looking to advance your career or improve your team's testing capabilities, CTFL certification is a valuable asset that can help you achieve your goals.
Contact Us :
Contact Us For More Information:
Visit :www.icertglobal.com Email : info@icertglobal.com
Read More
In today's competitive job market, having a CTFL certification can significantly boost your career prospects as a developer or manager. The Certified Tester Foundation Level (CTFL) certification is a globally recognized credential that demonstrates your expertise in software testing. In this article, we will explore the benefits of CTFL certification for both developers and managers, as well as the process of obtaining this valuable credential.
Benefits of CTFL Certification
-
Enhanced Skills: CTFL certification equips you with the essential skills and knowledge required to excel in software testing. This includes understanding different testing techniques, tools, and methodologies.
-
Career Advancement: Holding a CTFL certification can open up new job opportunities and help you advance in your career. Employers often prefer candidates with relevant certifications, as it demonstrates their commitment to professional development.
-
Increased Credibility: CTFL certification enhances your credibility as a software testing professional. It shows that you have met the rigorous standards set by the International Software Testing Qualifications Board (ISTQB).
-
Higher Salary: Certified professionals typically command higher salaries than their non-certified counterparts. CTFL certification can lead to increased earning potential and better job prospects.
CTFL Certification for Developers
For developers, CTFL certification offers several advantages. It provides a solid foundation in software testing principles and practices, helping developers to deliver high-quality code. By understanding the importance of testing early in the development process, developers can identify and fix issues more efficiently, resulting in a more robust and reliable product.
CTFL Certification for Managers
Managers who hold a CTFL certification can effectively lead their teams and ensure the successful completion of testing projects. They have the knowledge and skills needed to make informed decisions about testing strategies, resource allocation, and risk management. CTFL certification also allows managers to communicate more effectively with their technical teams, fostering collaboration and innovation.
CTFL Exam and Syllabus
The CTFL exam covers a wide range of topics related to software testing, including testing principles, test design techniques, and test management. It assesses your understanding of key concepts and your ability to apply them in real-world scenarios. The exam is administered by accredited training providers and consists of multiple-choice questions.
The CTFL syllabus includes the following areas:
-
Fundamentals of software testing
-
Testing levels and types
-
Static testing
-
Test design techniques
-
Test management
-
Tools support for testing
How to Get CTFL Certification
To obtain CTFL certification, you must pass the official exam administered by an accredited training provider. It is recommended to prepare for the exam by studying the CTFL syllabus and using practice tests to assess your knowledge. Once you pass the exam, you will receive your certification, which is valid for life.
How to obtain CTFL Certification?
We are an Education Technology company providing certification training courses to accelerate careers of working professionals worldwide. We impart training through instructor-led classroom workshops, instructor-led live virtual training sessions, and self-paced e-learning courses.
We have successfully conducted training sessions in 108 countries across the globe and enabled thousands of working professionals to enhance the scope of their careers.
Our enterprise training portfolio includes in-demand and globally recognized certification training courses in Project Management, Quality Management, Business Analysis, IT Service Management, Agile and Scrum, Cyber Security, Data Science, and Emerging Technologies. Download our Enterprise Training Catalog from https://www.icertglobal.com/corporate-training-for-enterprises.php and https://www.icertglobal.com/index.php
Popular Courses include:
-
Project Management: PMP, CAPM ,PMI RMP
-
Quality Management: Six Sigma Black Belt ,Lean Six Sigma Green Belt, Lean Management, Minitab,CMMI
-
Business Analysis: CBAP, CCBA, ECBA
-
Agile Training: PMI-ACP , CSM , CSPO
-
Scrum Training: CSM
-
DevOps
-
Program Management: PgMP
-
Cloud Technology: Exin Cloud Computing
-
Citrix Client Adminisration: Citrix Cloud Administration
The 10 top-paying certifications to target in 2024 are:
Conclusion
In conclusion, CTFL certification offers numerous benefits for developers and managers alike. It enhances your skills, opens up new career opportunities, and increases your credibility in the field of software testing. Whether you are looking to advance your career or improve your team's testing capabilities, CTFL certification is a valuable asset that can help you achieve your goals.
Contact Us :
Contact Us For More Information:
Visit :www.icertglobal.com Email : info@icertglobal.com
Overcoming Challenges in Lean Management Implementation
Lean management is a highly effective approach to streamlining processes and increasing efficiency within an organization. However, implementing lean practices can pose various challenges for businesses. In this article, we will explore the obstacles that organizations face when trying to adopt lean management and provide strategies for overcoming these challenges to achieve lean success.
Understanding Lean Management
Before diving into the challenges of lean management implementation, it is essential to understand what lean management entails. Lean management is a methodology that focuses on eliminating waste, reducing costs, and improving overall productivity. By identifying and removing inefficiencies in processes, organizations can become more agile and competitive in today's fast-paced business environment.
Common Obstacles in Lean Implementation
-
Lack of Leadership Commitment: One of the most significant barriers to successful lean implementation is a lack of buy-in from top management. Without strong leadership support, it can be challenging to drive the necessary changes throughout the organization.
-
Resistance to Change: Employees may resist adopting lean practices due to fear of the unknown or concerns about job security. Overcoming this resistance requires effective communication and clear explanations of how lean principles will benefit both the organization and its employees.
-
Lack of Training and Education: Implementing lean practices requires a shift in mindset and a new way of working. Without adequate training and education, employees may struggle to understand and implement lean principles effectively.
-
Inadequate Resources: Lean implementation may require investments in new technology, training programs, or process improvements. Limited resources can hinder the successful adoption of lean practices.
Strategies for Overcoming Lean Management Challenges
-
Leadership Involvement: Engage senior leaders in the lean implementation process to demonstrate their commitment and support. Leadership involvement can help drive change and create a culture of continuous improvement.
-
Employee Involvement: Involve employees at all levels in the lean implementation process. Seek their input, feedback, and ideas for improving processes. By engaging employees in the change process, you can increase buy-in and ownership of lean practices.
-
Training and Development: Provide employees with the training and education they need to understand lean principles and how to apply them in their daily work. Invest in continuous learning to ensure that employees have the skills and knowledge to support lean initiatives.
-
Resource Allocation: Allocate resources strategically to support lean implementation efforts. Identify and address any gaps in resources, whether it be funding, technology, or expertise, to ensure the successful adoption of lean practices.
How to obtain Lean Management certification?
We are an Education Technology company providing certification training courses to accelerate careers of working professionals worldwide. We impart training through instructor-led classroom workshops, instructor-led live virtual training sessions, and self-paced e-learning courses.
We have successfully conducted training sessions in 108 countries across the globe and enabled thousands of working professionals to enhance the scope of their careers.
Our enterprise training portfolio includes in-demand and globally recognized certification training courses in Project Management, Quality Management, Business Analysis, IT Service Management, Agile and Scrum, Cyber Security, Data Science, and Emerging Technologies. Download our Enterprise Training Catalog from https://www.icertglobal.com/corporate-training-for-enterprises.php and https://www.icertglobal.com/index.php
Popular Courses include:
-
Project Management: PMP, CAPM ,PMI RMP
-
Quality Management: Six Sigma Black Belt ,Lean Six Sigma Green Belt, Lean Management, Minitab,CMMI
-
Business Analysis: CBAP, CCBA, ECBA
-
Agile Training: PMI-ACP , CSM , CSPO
-
Scrum Training: CSM
-
DevOps
-
Program Management: PgMP
-
Cloud Technology: Exin Cloud Computing
-
Citrix Client Adminisration: Citrix Cloud Administration
The 10 top-paying certifications to target in 2024 are:
Conclusion
By addressing the challenges of lean management implementation head-on and implementing the strategies outlined above, organizations can overcome obstacles and achieve lean success. Lean practices can help businesses improve efficiency, reduce costs, and deliver value to customers. With the right approach and commitment from all levels of the organization, lean management can transform operations and drive sustainable growth.
Contact Us For More Information :
Visit : www.icertglobal.com Email : info@icertglobal.com
Read More
Lean management is a highly effective approach to streamlining processes and increasing efficiency within an organization. However, implementing lean practices can pose various challenges for businesses. In this article, we will explore the obstacles that organizations face when trying to adopt lean management and provide strategies for overcoming these challenges to achieve lean success.
Understanding Lean Management
Before diving into the challenges of lean management implementation, it is essential to understand what lean management entails. Lean management is a methodology that focuses on eliminating waste, reducing costs, and improving overall productivity. By identifying and removing inefficiencies in processes, organizations can become more agile and competitive in today's fast-paced business environment.
Common Obstacles in Lean Implementation
-
Lack of Leadership Commitment: One of the most significant barriers to successful lean implementation is a lack of buy-in from top management. Without strong leadership support, it can be challenging to drive the necessary changes throughout the organization.
-
Resistance to Change: Employees may resist adopting lean practices due to fear of the unknown or concerns about job security. Overcoming this resistance requires effective communication and clear explanations of how lean principles will benefit both the organization and its employees.
-
Lack of Training and Education: Implementing lean practices requires a shift in mindset and a new way of working. Without adequate training and education, employees may struggle to understand and implement lean principles effectively.
-
Inadequate Resources: Lean implementation may require investments in new technology, training programs, or process improvements. Limited resources can hinder the successful adoption of lean practices.
Strategies for Overcoming Lean Management Challenges
-
Leadership Involvement: Engage senior leaders in the lean implementation process to demonstrate their commitment and support. Leadership involvement can help drive change and create a culture of continuous improvement.
-
Employee Involvement: Involve employees at all levels in the lean implementation process. Seek their input, feedback, and ideas for improving processes. By engaging employees in the change process, you can increase buy-in and ownership of lean practices.
-
Training and Development: Provide employees with the training and education they need to understand lean principles and how to apply them in their daily work. Invest in continuous learning to ensure that employees have the skills and knowledge to support lean initiatives.
-
Resource Allocation: Allocate resources strategically to support lean implementation efforts. Identify and address any gaps in resources, whether it be funding, technology, or expertise, to ensure the successful adoption of lean practices.
How to obtain Lean Management certification?
We are an Education Technology company providing certification training courses to accelerate careers of working professionals worldwide. We impart training through instructor-led classroom workshops, instructor-led live virtual training sessions, and self-paced e-learning courses.
We have successfully conducted training sessions in 108 countries across the globe and enabled thousands of working professionals to enhance the scope of their careers.
Our enterprise training portfolio includes in-demand and globally recognized certification training courses in Project Management, Quality Management, Business Analysis, IT Service Management, Agile and Scrum, Cyber Security, Data Science, and Emerging Technologies. Download our Enterprise Training Catalog from https://www.icertglobal.com/corporate-training-for-enterprises.php and https://www.icertglobal.com/index.php
Popular Courses include:
-
Project Management: PMP, CAPM ,PMI RMP
-
Quality Management: Six Sigma Black Belt ,Lean Six Sigma Green Belt, Lean Management, Minitab,CMMI
-
Business Analysis: CBAP, CCBA, ECBA
-
Agile Training: PMI-ACP , CSM , CSPO
-
Scrum Training: CSM
-
DevOps
-
Program Management: PgMP
-
Cloud Technology: Exin Cloud Computing
-
Citrix Client Adminisration: Citrix Cloud Administration
The 10 top-paying certifications to target in 2024 are:
Conclusion
By addressing the challenges of lean management implementation head-on and implementing the strategies outlined above, organizations can overcome obstacles and achieve lean success. Lean practices can help businesses improve efficiency, reduce costs, and deliver value to customers. With the right approach and commitment from all levels of the organization, lean management can transform operations and drive sustainable growth.
Contact Us For More Information :
Visit : www.icertglobal.com Email : info@icertglobal.com
Top Advantages of QMS Certification for Your Company Growth
In today's competitive business environment, implementing a Quality Management System (QMS) and obtaining certification can provide numerous benefits to your company. From improved processes to increased customer satisfaction, QMS certification can help streamline your operations and drive business growth. Let's explore some of the key advantages of QMS certification for your company:
Enhanced Company Efficiency
One of the primary benefits of QMS certification is the improved efficiency of your company's operations. By implementing a quality management system, you can standardize processes, reduce errors, and ensure consistent quality across all areas of your business. This systematic approach not only increases productivity but also helps your company operate more effectively and efficiently.
Improved Customer Satisfaction
Customer satisfaction is paramount in today's business world, and QMS certification can help you meet and exceed customer expectations. By focusing on quality control, reducing errors, and continuously improving your processes, you can enhance the overall customer experience and build customer loyalty. This, in turn, can lead to increased customer retention and more repeat business.
Compliance Requirements and Risk Management
In many industries, compliance with regulatory requirements is essential for business success. QMS certification can help ensure that your company meets all necessary compliance standards and mitigates risks. By identifying and addressing potential risks through proactive measures such as internal audits and corrective actions, you can protect your company from costly mistakes and legal issues.
Competitive Advantage and Business Growth
Obtaining QMS certification can give your company a competitive edge in the marketplace. By demonstrating your commitment to quality and continuous improvement, you can differentiate your brand from competitors and attract new customers. This enhanced reputation can help drive business growth and open up new opportunities for expansion and market differentiation.
Leadership Buy-in and Employee Engagement
Successful implementation of a QMS requires strong leadership buy-in and employee engagement at all levels of the organization. By involving employees in the certification process, you can create a culture of quality and innovation within your company. This can lead to improved performance, increased morale, and a more cohesive organizational structure.
Sustainability Practices and Innovation Culture
QMS certification can also help your company incorporate sustainability practices and foster an innovation culture. By focusing on resource optimization, traceability, and stakeholder satisfaction, you can build a reputation for environmental responsibility and commitment to social good. This can attract like-minded customers and partners and drive innovation within your industry.
How to obtain Quality Management certification?
We are an Education Technology company providing certification training courses to accelerate careers of working professionals worldwide. We impart training through instructor-led classroom workshops, instructor-led live virtual training sessions, and self-paced e-learning courses.
We have successfully conducted training sessions in 108 countries across the globe and enabled thousands of working professionals to enhance the scope of their careers.
Our enterprise training portfolio includes in-demand and globally recognized certification training courses in Project Management, Quality Management, Business Analysis, IT Service Management, Agile and Scrum, Cyber Security, Data Science, and Emerging Technologies. Download our Enterprise Training Catalog from https://www.icertglobal.com/corporate-training-for-enterprises.php and https://www.icertglobal.com/index.php
Popular Courses include:
-
Project Management: PMP, CAPM ,PMI RMP
-
Quality Management: Six Sigma Black Belt ,Lean Six Sigma Green Belt, Lean Management, Minitab,CMMI
-
Business Analysis: CBAP, CCBA, ECBA
-
Agile Training: PMI-ACP , CSM , CSPO
-
Scrum Training: CSM
-
DevOps
-
Program Management: PgMP
-
Cloud Technology: Exin Cloud Computing
-
Citrix Client Adminisration: Citrix Cloud Administration
The 10 top-paying certifications to target in 2024 are:
Conclusion
In conclusion, QMS certification offers numerous advantages for your company, from enhanced efficiency and customer satisfaction to competitive advantage and business growth. By investing in a quality management system and obtaining certification, you can position your company for long-term success and sustainable growth in today's ever-changing business landscape.
Contact Us For More Information :
Visit : www.icertglobal.com Email : info@icertglobal.com
Read More
In today's competitive business environment, implementing a Quality Management System (QMS) and obtaining certification can provide numerous benefits to your company. From improved processes to increased customer satisfaction, QMS certification can help streamline your operations and drive business growth. Let's explore some of the key advantages of QMS certification for your company:
Enhanced Company Efficiency
One of the primary benefits of QMS certification is the improved efficiency of your company's operations. By implementing a quality management system, you can standardize processes, reduce errors, and ensure consistent quality across all areas of your business. This systematic approach not only increases productivity but also helps your company operate more effectively and efficiently.
Improved Customer Satisfaction
Customer satisfaction is paramount in today's business world, and QMS certification can help you meet and exceed customer expectations. By focusing on quality control, reducing errors, and continuously improving your processes, you can enhance the overall customer experience and build customer loyalty. This, in turn, can lead to increased customer retention and more repeat business.
Compliance Requirements and Risk Management
In many industries, compliance with regulatory requirements is essential for business success. QMS certification can help ensure that your company meets all necessary compliance standards and mitigates risks. By identifying and addressing potential risks through proactive measures such as internal audits and corrective actions, you can protect your company from costly mistakes and legal issues.
Competitive Advantage and Business Growth
Obtaining QMS certification can give your company a competitive edge in the marketplace. By demonstrating your commitment to quality and continuous improvement, you can differentiate your brand from competitors and attract new customers. This enhanced reputation can help drive business growth and open up new opportunities for expansion and market differentiation.
Leadership Buy-in and Employee Engagement
Successful implementation of a QMS requires strong leadership buy-in and employee engagement at all levels of the organization. By involving employees in the certification process, you can create a culture of quality and innovation within your company. This can lead to improved performance, increased morale, and a more cohesive organizational structure.
Sustainability Practices and Innovation Culture
QMS certification can also help your company incorporate sustainability practices and foster an innovation culture. By focusing on resource optimization, traceability, and stakeholder satisfaction, you can build a reputation for environmental responsibility and commitment to social good. This can attract like-minded customers and partners and drive innovation within your industry.
How to obtain Quality Management certification?
We are an Education Technology company providing certification training courses to accelerate careers of working professionals worldwide. We impart training through instructor-led classroom workshops, instructor-led live virtual training sessions, and self-paced e-learning courses.
We have successfully conducted training sessions in 108 countries across the globe and enabled thousands of working professionals to enhance the scope of their careers.
Our enterprise training portfolio includes in-demand and globally recognized certification training courses in Project Management, Quality Management, Business Analysis, IT Service Management, Agile and Scrum, Cyber Security, Data Science, and Emerging Technologies. Download our Enterprise Training Catalog from https://www.icertglobal.com/corporate-training-for-enterprises.php and https://www.icertglobal.com/index.php
Popular Courses include:
-
Project Management: PMP, CAPM ,PMI RMP
-
Quality Management: Six Sigma Black Belt ,Lean Six Sigma Green Belt, Lean Management, Minitab,CMMI
-
Business Analysis: CBAP, CCBA, ECBA
-
Agile Training: PMI-ACP , CSM , CSPO
-
Scrum Training: CSM
-
DevOps
-
Program Management: PgMP
-
Cloud Technology: Exin Cloud Computing
-
Citrix Client Adminisration: Citrix Cloud Administration
The 10 top-paying certifications to target in 2024 are:
Conclusion
In conclusion, QMS certification offers numerous advantages for your company, from enhanced efficiency and customer satisfaction to competitive advantage and business growth. By investing in a quality management system and obtaining certification, you can position your company for long-term success and sustainable growth in today's ever-changing business landscape.
Contact Us For More Information :
Visit : www.icertglobal.com Email : info@icertglobal.com
Online vs. In-Person MINITAB Certification: Pros and Cons
Are you considering getting certified in MINITAB, but unsure whether to pursue online certification or attend in-person training? Let's break down the pros and cons of each option to help you make an informed decision.
MINITAB Certification Online
Pros:
-
Convenience: Online MINITAB certification allows you to study and complete the course at your own pace and schedule.
-
Cost-Effective: Online courses are often more affordable than in-person training, saving you money on travel and accommodation expenses.
-
Flexibility: You can access online resources from anywhere in the world, giving you the flexibility to learn from the comfort of your own home.
-
Self-Paced Learning: Online courses allow you to review materials at your own pace and focus on areas that need more attention.
Cons:
-
Lack of Hands-On Experience: Online certification may lack hands-on experience and practical application of MINITAB skills.
-
Limited Interaction: You may have limited interaction with instructors and other students in an online setting, leading to potential difficulties in clarifying doubts.
MINITAB Certification In-Person
Pros:
-
Hands-On Experience: In-person training provides hands-on experience and practical application of MINITAB skills.
-
Interactive Learning: In-person training allows for real-time interaction with instructors and other students, promoting a better understanding of the material.
-
Networking Opportunities: Attending in-person training sessions can help you build a professional network within the MINITAB community.
Cons:
-
Time-Costly: In-person training may require you to take time off work or travel to attend sessions, which can be time-consuming and costly.
-
Higher Costs: In-person training is often more expensive than online certification due to additional expenses such as travel and accommodation.
MINITAB Certification Comparison
Online MINITAB Certification:
-
Convenient
-
Cost-effective
-
Flexible
-
Self-paced learning
In-Person MINITAB Certification:
-
Hands-on experience
-
Interactive learning
-
Networking opportunities
-
Time-costly
How to obtain MINITAB certification?
We are an Education Technology company providing certification training courses to accelerate careers of working professionals worldwide. We impart training through instructor-led classroom workshops, instructor-led live virtual training sessions, and self-paced e-learning courses.
We have successfully conducted training sessions in 108 countries across the globe and enabled thousands of working professionals to enhance the scope of their careers.
Our enterprise training portfolio includes in-demand and globally recognized certification training courses in Project Management, Quality Management, Business Analysis, IT Service Management, Agile and Scrum, Cyber Security, Data Science, and Emerging Technologies. Download our Enterprise Training Catalog from https://www.icertglobal.com/corporate-training-for-enterprises.php
Popular Courses include:
-
Project Management: PMP, CAPM ,PMI RMP
-
Quality Management: Six Sigma Black Belt ,Lean Six Sigma Green Belt, Lean Management, Minitab,CMMI
-
Business Analysis: CBAP, CCBA, ECBA
-
Agile Training: PMI-ACP , CSM , CSPO
-
Scrum Training: CSM
-
DevOps
-
Program Management: PgMP
-
Cloud Technology: Exin Cloud Computing
-
Citrix Client Adminisration: Citrix Cloud Administration
The 10 top-paying certifications to target in 2024 are:
Conclusion
In conclusion, whether you choose online or in-person MINITAB certification depends on your preferences, learning style, and budget. Online certification offers flexibility and cost-effectiveness, while in-person training provides hands-on experience and networking opportunities. Consider your priorities and choose the option that aligns best with your goals and resources.
Read More
Are you considering getting certified in MINITAB, but unsure whether to pursue online certification or attend in-person training? Let's break down the pros and cons of each option to help you make an informed decision.
MINITAB Certification Online
Pros:
-
Convenience: Online MINITAB certification allows you to study and complete the course at your own pace and schedule.
-
Cost-Effective: Online courses are often more affordable than in-person training, saving you money on travel and accommodation expenses.
-
Flexibility: You can access online resources from anywhere in the world, giving you the flexibility to learn from the comfort of your own home.
-
Self-Paced Learning: Online courses allow you to review materials at your own pace and focus on areas that need more attention.
Cons:
-
Lack of Hands-On Experience: Online certification may lack hands-on experience and practical application of MINITAB skills.
-
Limited Interaction: You may have limited interaction with instructors and other students in an online setting, leading to potential difficulties in clarifying doubts.
MINITAB Certification In-Person
Pros:
-
Hands-On Experience: In-person training provides hands-on experience and practical application of MINITAB skills.
-
Interactive Learning: In-person training allows for real-time interaction with instructors and other students, promoting a better understanding of the material.
-
Networking Opportunities: Attending in-person training sessions can help you build a professional network within the MINITAB community.
Cons:
-
Time-Costly: In-person training may require you to take time off work or travel to attend sessions, which can be time-consuming and costly.
-
Higher Costs: In-person training is often more expensive than online certification due to additional expenses such as travel and accommodation.
MINITAB Certification Comparison
Online MINITAB Certification:
-
Convenient
-
Cost-effective
-
Flexible
-
Self-paced learning
In-Person MINITAB Certification:
-
Hands-on experience
-
Interactive learning
-
Networking opportunities
-
Time-costly
How to obtain MINITAB certification?
We are an Education Technology company providing certification training courses to accelerate careers of working professionals worldwide. We impart training through instructor-led classroom workshops, instructor-led live virtual training sessions, and self-paced e-learning courses.
We have successfully conducted training sessions in 108 countries across the globe and enabled thousands of working professionals to enhance the scope of their careers.
Our enterprise training portfolio includes in-demand and globally recognized certification training courses in Project Management, Quality Management, Business Analysis, IT Service Management, Agile and Scrum, Cyber Security, Data Science, and Emerging Technologies. Download our Enterprise Training Catalog from https://www.icertglobal.com/corporate-training-for-enterprises.php
Popular Courses include:
-
Project Management: PMP, CAPM ,PMI RMP
-
Quality Management: Six Sigma Black Belt ,Lean Six Sigma Green Belt, Lean Management, Minitab,CMMI
-
Business Analysis: CBAP, CCBA, ECBA
-
Agile Training: PMI-ACP , CSM , CSPO
-
Scrum Training: CSM
-
DevOps
-
Program Management: PgMP
-
Cloud Technology: Exin Cloud Computing
-
Citrix Client Adminisration: Citrix Cloud Administration
The 10 top-paying certifications to target in 2024 are:
Conclusion
In conclusion, whether you choose online or in-person MINITAB certification depends on your preferences, learning style, and budget. Online certification offers flexibility and cost-effectiveness, while in-person training provides hands-on experience and networking opportunities. Consider your priorities and choose the option that aligns best with your goals and resources.
Integrating Lean Six Sigma with Agile & Scrum Methodologies
In today's rapidly evolving business landscape, organizations are constantly seeking ways to improve their operational efficiency and deliver value to their customers. Two popular methodologies that have gained significant traction in recent years are Lean Six Sigma and Agile/Scrum. While these methodologies originated in different industries and serve distinct purposes, they can be integrated to create a powerful framework for driving process improvement and delivering high-quality products and services.
What is Lean Six Sigma?
Lean Six Sigma is a methodology that combines the principles of Lean manufacturing and Six Sigma to eliminate waste, reduce variation, and improve overall quality in a systematic and data-driven manner. Lean focuses on streamlining processes and eliminating non-value-added activities, while Six Sigma aims to reduce defects and variation in processes to achieve near-perfect quality. By integrating the principles of Lean and Six Sigma, organizations can achieve significant improvements in efficiency, productivity, and customer satisfaction.
What is Agile and Scrum?
Agile is a project management methodology that emphasizes flexibility, adaptability, and collaboration in the development of software and other products. Scrum, on the other hand, is a specific framework within Agile that defines roles, activities, and artifacts to facilitate the iterative and incremental development of products. Agile and Scrum are well-suited for projects that require frequent changes, rapid delivery, and close collaboration between cross-functional teams.
Benefits of Integrating Lean Six Sigma with Agile and Scrum:
-
Improved process efficiency and quality
-
Faster delivery of products and services
-
Enhanced collaboration and communication between teams
-
Better alignment of project objectives with customer needs
-
Increased flexibility and adaptability to changing market conditions
-
Reduced waste and variation in processes
-
Continuous improvement culture that drives innovation and growth
How to Integrate Lean Six Sigma with Agile and Scrum:
Integrating Lean Six Sigma with Agile and Scrum requires a deep understanding of both methodologies and how they complement each other. Organizations can start by aligning Lean Six Sigma principles with Agile values, such as customer focus, continuous improvement, and empowerment of teams. By incorporating Lean Six Sigma tools and techniques into Agile/Scrum processes, organizations can identify and eliminate waste, reduce defects, and improve overall process efficiency.
Success Factors for Lean Six Sigma with Agile and Scrum:
-
Strong leadership support and commitment to process improvement
-
Cross-functional collaboration and communication
-
Training and certification in Lean Six Sigma and Agile/Scrum methodologies
-
Clear alignment of project objectives with customer needs
-
Regular monitoring and evaluation of process performance
-
Continuous learning and adaptation based on feedback and data
How to obtain Lean Six Sigma Black Belt certification?
We are an Education Technology company providing certification training courses to accelerate careers of working professionals worldwide. We impart training through instructor-led classroom workshops, instructor-led live virtual training sessions, and self-paced e-learning courses.
We have successfully conducted training sessions in 108 countries across the globe and enabled thousands of working professionals to enhance the scope of their careers.
Our enterprise training portfolio includes in-demand and globally recognized certification training courses in Project Management, Quality Management, Business Analysis, IT Service Management, Agile and Scrum, Cyber Security, Data Science, and Emerging Technologies. Download our Enterprise Training Catalog from https://www.icertglobal.com/corporate-training-for-enterprises.php and https://www.icertglobal.com/index.php
Popular Courses include:
-
Project Management: PMP, CAPM ,PMI RMP
-
Quality Management: Six Sigma Black Belt ,Lean Six Sigma Green Belt, Lean Management, Minitab,CMMI
-
Business Analysis: CBAP, CCBA, ECBA
-
Agile Training: PMI-ACP , CSM , CSPO
-
Scrum Training: CSM
-
DevOps
-
Program Management: PgMP
-
Cloud Technology: Exin Cloud Computing
-
Citrix Client Adminisration: Citrix Cloud Administration
The 10 top-paying certifications to target in 2024 are:
Conclusion:
Integrating Lean Six Sigma with Agile and Scrum methodologies can provide organizations with a powerful framework for driving process improvement, delivering high-quality products and services, and achieving sustainable growth. By combining the principles of Lean Six Sigma with the flexibility and adaptability of Agile/Scrum, organizations can create a culture of continuous improvement, innovation, and customer-centricity that sets them apart in today's competitive marketplace.
Read More
In today's rapidly evolving business landscape, organizations are constantly seeking ways to improve their operational efficiency and deliver value to their customers. Two popular methodologies that have gained significant traction in recent years are Lean Six Sigma and Agile/Scrum. While these methodologies originated in different industries and serve distinct purposes, they can be integrated to create a powerful framework for driving process improvement and delivering high-quality products and services.
What is Lean Six Sigma?
Lean Six Sigma is a methodology that combines the principles of Lean manufacturing and Six Sigma to eliminate waste, reduce variation, and improve overall quality in a systematic and data-driven manner. Lean focuses on streamlining processes and eliminating non-value-added activities, while Six Sigma aims to reduce defects and variation in processes to achieve near-perfect quality. By integrating the principles of Lean and Six Sigma, organizations can achieve significant improvements in efficiency, productivity, and customer satisfaction.
What is Agile and Scrum?
Agile is a project management methodology that emphasizes flexibility, adaptability, and collaboration in the development of software and other products. Scrum, on the other hand, is a specific framework within Agile that defines roles, activities, and artifacts to facilitate the iterative and incremental development of products. Agile and Scrum are well-suited for projects that require frequent changes, rapid delivery, and close collaboration between cross-functional teams.
Benefits of Integrating Lean Six Sigma with Agile and Scrum:
-
Improved process efficiency and quality
-
Faster delivery of products and services
-
Enhanced collaboration and communication between teams
-
Better alignment of project objectives with customer needs
-
Increased flexibility and adaptability to changing market conditions
-
Reduced waste and variation in processes
-
Continuous improvement culture that drives innovation and growth
How to Integrate Lean Six Sigma with Agile and Scrum:
Integrating Lean Six Sigma with Agile and Scrum requires a deep understanding of both methodologies and how they complement each other. Organizations can start by aligning Lean Six Sigma principles with Agile values, such as customer focus, continuous improvement, and empowerment of teams. By incorporating Lean Six Sigma tools and techniques into Agile/Scrum processes, organizations can identify and eliminate waste, reduce defects, and improve overall process efficiency.
Success Factors for Lean Six Sigma with Agile and Scrum:
-
Strong leadership support and commitment to process improvement
-
Cross-functional collaboration and communication
-
Training and certification in Lean Six Sigma and Agile/Scrum methodologies
-
Clear alignment of project objectives with customer needs
-
Regular monitoring and evaluation of process performance
-
Continuous learning and adaptation based on feedback and data
How to obtain Lean Six Sigma Black Belt certification?
We are an Education Technology company providing certification training courses to accelerate careers of working professionals worldwide. We impart training through instructor-led classroom workshops, instructor-led live virtual training sessions, and self-paced e-learning courses.
We have successfully conducted training sessions in 108 countries across the globe and enabled thousands of working professionals to enhance the scope of their careers.
Our enterprise training portfolio includes in-demand and globally recognized certification training courses in Project Management, Quality Management, Business Analysis, IT Service Management, Agile and Scrum, Cyber Security, Data Science, and Emerging Technologies. Download our Enterprise Training Catalog from https://www.icertglobal.com/corporate-training-for-enterprises.php and https://www.icertglobal.com/index.php
Popular Courses include:
-
Project Management: PMP, CAPM ,PMI RMP
-
Quality Management: Six Sigma Black Belt ,Lean Six Sigma Green Belt, Lean Management, Minitab,CMMI
-
Business Analysis: CBAP, CCBA, ECBA
-
Agile Training: PMI-ACP , CSM , CSPO
-
Scrum Training: CSM
-
DevOps
-
Program Management: PgMP
-
Cloud Technology: Exin Cloud Computing
-
Citrix Client Adminisration: Citrix Cloud Administration
The 10 top-paying certifications to target in 2024 are:
Conclusion:
Integrating Lean Six Sigma with Agile and Scrum methodologies can provide organizations with a powerful framework for driving process improvement, delivering high-quality products and services, and achieving sustainable growth. By combining the principles of Lean Six Sigma with the flexibility and adaptability of Agile/Scrum, organizations can create a culture of continuous improvement, innovation, and customer-centricity that sets them apart in today's competitive marketplace.
Explore future trends shaping Lean Management for efficiency
In today's fast-paced and ever-changing business environment, organizations are constantly seeking ways to streamline processes, reduce waste, and increase efficiency. Lean management has emerged as a popular approach to achieving these goals, but what does the future hold for this methodology? In this article, we will explore the future trends in lean management and how organizations can stay ahead of the curve.
Lean management is a philosophy that focuses on maximizing customer value while minimizing waste. It encompasses a set of principles, practices, and techniques aimed at improving processes and driving continuous improvement. As technology advances and business landscapes evolve, the future of lean management is taking on new dimensions. Let's delve into some of the key trends shaping the future of lean management.
Lean Production Techniques
One of the future trends in lean management is the adoption of advanced lean production techniques. As industry 4.0 continues to gain momentum, organizations are leveraging technology to optimize their production processes. From automation and robotics to data analytics and artificial intelligence, lean production techniques are becoming increasingly digitized and interconnected.
Agile Lean Management
Another future trend in lean management is the integration of agile principles. Agile lean management involves combining the flexibility and adaptability of agile methodologies with the efficiency and waste reduction of lean practices. By fostering a culture of continuous improvement and innovation, organizations can respond quickly to changing market dynamics and customer demands.
Lean Technology Adoption
The future of lean management also revolves around the adoption of cutting-edge technologies. From cloud computing and Internet of Things (IoT) to virtual reality and blockchain, organizations are embracing digital transformation to enhance their lean initiatives. By harnessing the power of technology, businesses can drive efficiencies, improve decision-making, and unlock new opportunities for growth.
Lean Culture and Leadership
Building a culture of lean thinking and empowering leadership is crucial for the success of lean management. In the future, organizations will need to focus on developing lean leadership capabilities, fostering a culture of continuous learning and improvement, and engaging employees at all levels in lean initiatives. By nurturing a lean culture, companies can drive sustainable change and achieve long-term success.
Lean Problem-Solving and Quality Management
Continuous improvement lies at the heart of lean management, and in the future, organizations will need to place greater emphasis on lean problem-solving and quality management. By adopting lean tools and techniques such as root cause analysis, value stream mapping, and Kaizen events, businesses can identify and address issues proactively, drive quality improvements, and enhance customer satisfaction.
Efficiency in Lean Management
Efficiency is a key tenet of lean management, and in the future, organizations will need to focus on optimizing their lean processes to maximize efficiency. By eliminating bottlenecks, reducing cycle times, and increasing productivity, companies can streamline operations, save costs, and deliver value to customers more effectively.
Lean Innovation and Development
Innovation is essential for staying competitive in today's market, and lean management can be a catalyst for driving innovation. In the future, organizations will need to foster a culture of experimentation, creativity, and risk-taking to spur lean innovation and development. By encouraging employees to think outside the box and embrace new ideas, businesses can differentiate themselves and create sustainable competitive advantages.
How to obtain Lean Management certification?
We are an Education Technology company providing certification training courses to accelerate careers of working professionals worldwide. We impart training through instructor-led classroom workshops, instructor-led live virtual training sessions, and self-paced e-learning courses.
We have successfully conducted training sessions in 108 countries across the globe and enabled thousands of working professionals to enhance the scope of their careers.
Our enterprise training portfolio includes in-demand and globally recognized certification training courses in Project Management, Quality Management, Business Analysis, IT Service Management, Agile and Scrum, Cyber Security, Data Science, and Emerging Technologies. Download our Enterprise Training Catalog from https://www.icertglobal.com/corporate-training-for-enterprises.php and https://www.icertglobal.com/index.php
Popular courses include:
-
Project Management: PMP, CAPM ,PMI RMP
-
Quality Management: Six Sigma Black Belt ,Lean Six Sigma Green Belt, Lean Management, Minitab,CMMI
-
Business Analysis: CBAP, CCBA, ECBA
-
Agile Training: PMI-ACP , CSM , CSPO
-
Scrum Training: CSM
-
DevOps
-
Program Management: PgMP
-
Cloud Technology: Exin Cloud Computing
-
Citrix Client Adminisration: Citrix Cloud Administration
The 10 top-paying certifications to target in 2024 are:
Conclusion
As organizations navigate the complexities of today's business landscape, the future of lean management holds immense promise. By embracing advanced production techniques, adopting agile principles, leveraging technology, building a culture of lean thinking, and focusing on problem-solving and quality management, businesses can drive continuous improvement, enhance efficiency, and achieve sustainable growth. The key to success lies in staying ahead of the curve, adapting to change, and constantly pushing the boundaries of what is possible with lean management.
Contact Us For More Information:
Visit :www.icertglobal.comEmail : info@icertglobal.com
Read More
In today's fast-paced and ever-changing business environment, organizations are constantly seeking ways to streamline processes, reduce waste, and increase efficiency. Lean management has emerged as a popular approach to achieving these goals, but what does the future hold for this methodology? In this article, we will explore the future trends in lean management and how organizations can stay ahead of the curve.
Lean management is a philosophy that focuses on maximizing customer value while minimizing waste. It encompasses a set of principles, practices, and techniques aimed at improving processes and driving continuous improvement. As technology advances and business landscapes evolve, the future of lean management is taking on new dimensions. Let's delve into some of the key trends shaping the future of lean management.
Lean Production Techniques
One of the future trends in lean management is the adoption of advanced lean production techniques. As industry 4.0 continues to gain momentum, organizations are leveraging technology to optimize their production processes. From automation and robotics to data analytics and artificial intelligence, lean production techniques are becoming increasingly digitized and interconnected.
Agile Lean Management
Another future trend in lean management is the integration of agile principles. Agile lean management involves combining the flexibility and adaptability of agile methodologies with the efficiency and waste reduction of lean practices. By fostering a culture of continuous improvement and innovation, organizations can respond quickly to changing market dynamics and customer demands.
Lean Technology Adoption
The future of lean management also revolves around the adoption of cutting-edge technologies. From cloud computing and Internet of Things (IoT) to virtual reality and blockchain, organizations are embracing digital transformation to enhance their lean initiatives. By harnessing the power of technology, businesses can drive efficiencies, improve decision-making, and unlock new opportunities for growth.
Lean Culture and Leadership
Building a culture of lean thinking and empowering leadership is crucial for the success of lean management. In the future, organizations will need to focus on developing lean leadership capabilities, fostering a culture of continuous learning and improvement, and engaging employees at all levels in lean initiatives. By nurturing a lean culture, companies can drive sustainable change and achieve long-term success.
Lean Problem-Solving and Quality Management
Continuous improvement lies at the heart of lean management, and in the future, organizations will need to place greater emphasis on lean problem-solving and quality management. By adopting lean tools and techniques such as root cause analysis, value stream mapping, and Kaizen events, businesses can identify and address issues proactively, drive quality improvements, and enhance customer satisfaction.
Efficiency in Lean Management
Efficiency is a key tenet of lean management, and in the future, organizations will need to focus on optimizing their lean processes to maximize efficiency. By eliminating bottlenecks, reducing cycle times, and increasing productivity, companies can streamline operations, save costs, and deliver value to customers more effectively.
Lean Innovation and Development
Innovation is essential for staying competitive in today's market, and lean management can be a catalyst for driving innovation. In the future, organizations will need to foster a culture of experimentation, creativity, and risk-taking to spur lean innovation and development. By encouraging employees to think outside the box and embrace new ideas, businesses can differentiate themselves and create sustainable competitive advantages.
How to obtain Lean Management certification?
We are an Education Technology company providing certification training courses to accelerate careers of working professionals worldwide. We impart training through instructor-led classroom workshops, instructor-led live virtual training sessions, and self-paced e-learning courses.
We have successfully conducted training sessions in 108 countries across the globe and enabled thousands of working professionals to enhance the scope of their careers.
Our enterprise training portfolio includes in-demand and globally recognized certification training courses in Project Management, Quality Management, Business Analysis, IT Service Management, Agile and Scrum, Cyber Security, Data Science, and Emerging Technologies. Download our Enterprise Training Catalog from https://www.icertglobal.com/corporate-training-for-enterprises.php and https://www.icertglobal.com/index.php
Popular courses include:
-
Project Management: PMP, CAPM ,PMI RMP
-
Quality Management: Six Sigma Black Belt ,Lean Six Sigma Green Belt, Lean Management, Minitab,CMMI
-
Business Analysis: CBAP, CCBA, ECBA
-
Agile Training: PMI-ACP , CSM , CSPO
-
Scrum Training: CSM
-
DevOps
-
Program Management: PgMP
-
Cloud Technology: Exin Cloud Computing
-
Citrix Client Adminisration: Citrix Cloud Administration
The 10 top-paying certifications to target in 2024 are:
Conclusion
As organizations navigate the complexities of today's business landscape, the future of lean management holds immense promise. By embracing advanced production techniques, adopting agile principles, leveraging technology, building a culture of lean thinking, and focusing on problem-solving and quality management, businesses can drive continuous improvement, enhance efficiency, and achieve sustainable growth. The key to success lies in staying ahead of the curve, adapting to change, and constantly pushing the boundaries of what is possible with lean management.
Contact Us For More Information:
Visit :www.icertglobal.comEmail : info@icertglobal.com
Obstacles for CTFL Candidates & Strategies to Overcome Them
Are you a Certified Tester Foundation Level (CTFL) candidate facing challenges in your exam preparation? Do you feel overwhelmed by the study material and unsure of how to navigate the certification process successfully? Rest assured, you are not alone. Many aspiring CTFL professionals encounter obstacles along their journey to certification. In this article, we will explore common obstacles faced by CTFL candidates and provide you with effective strategies to overcome them.
Obstacles for CTFL Candidates
CTFL Certification Challenges
One of the primary obstacles for CTFL candidates is the sheer volume of material that needs to be covered for the exam. The CTFL certification is comprehensive, covering a wide range of testing principles, terms, and techniques. As a result, candidates often feel daunted by the amount of information they need to learn and retain.
CTFL Exam Difficulties
Another obstacle that CTFL candidates face is the difficulty of the exam itself. The CTFL exam is designed to test candidates' understanding of software testing principles and practices. It requires critical thinking skills, as well as the ability to apply theoretical knowledge to practical scenarios. Many candidates struggle with the complexity of the exam questions and find it challenging to demonstrate their knowledge effectively.
CTFL Study Obstacles
Effective study habits are essential for success in the CTFL exam. However, some candidates struggle to create a study plan that works for them. They may have difficulty staying motivated, managing their time effectively, or finding resources that align with their learning style.
Strategies to Overcome Obstacles
Tips for Passing CTFL
To overcome the obstacles faced by CTFL candidates, it is essential to develop a strategic approach to exam preparation. Here are some tips for passing the CTFL exam successfully:
-
Create a study schedule and stick to it
-
Utilize a variety of study materials, such as textbooks, online resources, and practice exams
-
Engage in active learning techniques, such as note-taking and summarizing key concepts
-
Join a study group or online forum to discuss challenging topics with peers
How to Overcome CTFL Hurdles
In addition to the above tips, here are some specific strategies to help you overcome obstacles in your CTFL exam preparation:
-
Break down the study material into manageable chunks and focus on one topic at a time
-
Use mnemonic devices or visual aids to help you remember complex concepts
-
Practice problem-solving using past exam papers or sample questions to familiarize yourself with the exam format
-
Seek guidance from experienced CTFL professionals or mentors for study advice and support
CTFL Certification Tips
Achieving CTFL certification is a significant milestone in your career as a software tester. To increase your chances of success, consider the following certification tips:
-
Stay updated on the latest industry trends and developments in software testing
-
Participate in continuous professional development activities, such as attending workshops or conferences
-
Network with other testing professionals to exchange knowledge and best practices
-
Maintain a positive attitude and believe in your ability to succeed in the exam
How to obtain CTFL certification?
We are an Education Technology company providingcertification training courses to accelerate careers of working professionals worldwide. We impart training through instructor-led classroom workshops, instructor-led live virtual training sessions, and self-paced e-learning courses.
We have successfully conducted training sessions in 108 countries across the globe and enabled thousands of working professionals to enhance the scope of their careers.
Our enterprise training portfolio includes in-demand and globally recognized certification training courses in Project Management, Quality Management, Business Analysis, IT Service Management, Agile and Scrum, Cyber Security, Data Science, and Emerging Technologies. Download our Enterprise Training Catalog from https://www.icertglobal.com/corporate-training-for-enterprises.php and https://www.icertglobal.com/index.php
Popular Courses include:
-
Project Management: PMP, CAPM ,PMI RMP
-
Quality Management: Six Sigma Black Belt ,Lean Six Sigma Green Belt, Lean Management, Minitab,CMMI
-
Business Analysis: CBAP, CCBA, ECBA
-
Agile Training: PMI-ACP , CSM , CSPO
-
Scrum Training: CSM
-
DevOps
-
Program Management: PgMP
-
Cloud Technology: Exin Cloud Computing
-
Citrix Client Adminisration: Citrix Cloud Administration
The 10 top-paying certifications to target in 2024 are:
Conclusion
In conclusion, while the road to CTFL certification may present obstacles for candidates, with the right strategies and mindset, these challenges can be overcome. By following the tips and techniques outlined in this article, you can navigate the certification process effectively and achieve success in your CTFL exam. Remember, persistence, dedication, and a proactive approach to studying are key to overcoming obstacles and achieving your certification goals. Good luck on your CTFL journey.
Contact Us For More Information:
Visit :www.icertglobal.comEmail : info@icertglobal.com
Read More
Are you a Certified Tester Foundation Level (CTFL) candidate facing challenges in your exam preparation? Do you feel overwhelmed by the study material and unsure of how to navigate the certification process successfully? Rest assured, you are not alone. Many aspiring CTFL professionals encounter obstacles along their journey to certification. In this article, we will explore common obstacles faced by CTFL candidates and provide you with effective strategies to overcome them.
Obstacles for CTFL Candidates
CTFL Certification Challenges
One of the primary obstacles for CTFL candidates is the sheer volume of material that needs to be covered for the exam. The CTFL certification is comprehensive, covering a wide range of testing principles, terms, and techniques. As a result, candidates often feel daunted by the amount of information they need to learn and retain.
CTFL Exam Difficulties
Another obstacle that CTFL candidates face is the difficulty of the exam itself. The CTFL exam is designed to test candidates' understanding of software testing principles and practices. It requires critical thinking skills, as well as the ability to apply theoretical knowledge to practical scenarios. Many candidates struggle with the complexity of the exam questions and find it challenging to demonstrate their knowledge effectively.
CTFL Study Obstacles
Effective study habits are essential for success in the CTFL exam. However, some candidates struggle to create a study plan that works for them. They may have difficulty staying motivated, managing their time effectively, or finding resources that align with their learning style.
Strategies to Overcome Obstacles
Tips for Passing CTFL
To overcome the obstacles faced by CTFL candidates, it is essential to develop a strategic approach to exam preparation. Here are some tips for passing the CTFL exam successfully:
-
Create a study schedule and stick to it
-
Utilize a variety of study materials, such as textbooks, online resources, and practice exams
-
Engage in active learning techniques, such as note-taking and summarizing key concepts
-
Join a study group or online forum to discuss challenging topics with peers
How to Overcome CTFL Hurdles
In addition to the above tips, here are some specific strategies to help you overcome obstacles in your CTFL exam preparation:
-
Break down the study material into manageable chunks and focus on one topic at a time
-
Use mnemonic devices or visual aids to help you remember complex concepts
-
Practice problem-solving using past exam papers or sample questions to familiarize yourself with the exam format
-
Seek guidance from experienced CTFL professionals or mentors for study advice and support
CTFL Certification Tips
Achieving CTFL certification is a significant milestone in your career as a software tester. To increase your chances of success, consider the following certification tips:
-
Stay updated on the latest industry trends and developments in software testing
-
Participate in continuous professional development activities, such as attending workshops or conferences
-
Network with other testing professionals to exchange knowledge and best practices
-
Maintain a positive attitude and believe in your ability to succeed in the exam
How to obtain CTFL certification?
We are an Education Technology company providingcertification training courses to accelerate careers of working professionals worldwide. We impart training through instructor-led classroom workshops, instructor-led live virtual training sessions, and self-paced e-learning courses.
We have successfully conducted training sessions in 108 countries across the globe and enabled thousands of working professionals to enhance the scope of their careers.
Our enterprise training portfolio includes in-demand and globally recognized certification training courses in Project Management, Quality Management, Business Analysis, IT Service Management, Agile and Scrum, Cyber Security, Data Science, and Emerging Technologies. Download our Enterprise Training Catalog from https://www.icertglobal.com/corporate-training-for-enterprises.php and https://www.icertglobal.com/index.php
Popular Courses include:
-
Project Management: PMP, CAPM ,PMI RMP
-
Quality Management: Six Sigma Black Belt ,Lean Six Sigma Green Belt, Lean Management, Minitab,CMMI
-
Business Analysis: CBAP, CCBA, ECBA
-
Agile Training: PMI-ACP , CSM , CSPO
-
Scrum Training: CSM
-
DevOps
-
Program Management: PgMP
-
Cloud Technology: Exin Cloud Computing
-
Citrix Client Adminisration: Citrix Cloud Administration
The 10 top-paying certifications to target in 2024 are:
Conclusion
In conclusion, while the road to CTFL certification may present obstacles for candidates, with the right strategies and mindset, these challenges can be overcome. By following the tips and techniques outlined in this article, you can navigate the certification process effectively and achieve success in your CTFL exam. Remember, persistence, dedication, and a proactive approach to studying are key to overcoming obstacles and achieving your certification goals. Good luck on your CTFL journey.
Contact Us For More Information:
Visit :www.icertglobal.comEmail : info@icertglobal.com
A Comparative Analysis of TQM, Six Sigma, and Lean Methods
href="https://www.icertglobal.com/tqm-six-sigma-and-lean-a-comparative-analysis-blog/detail" />
In the realm of quality management and process improvement, three methodologies stand out as the leading approaches to achieving excellence: Total Quality Management (TQM), Six Sigma, and Lean. Each methodology brings its own unique set of principles, tools, and techniques to the table, but they all share the common goal of driving continuous improvement and enhancing overall business performance.
Total Quality Management (TQM)
Total Quality Management, or TQM, is a holistic approach to quality management that focuses on involving all employees in the continuous improvement of processes, products, and services. TQM emphasizes the importance of customer satisfaction, employee involvement, and process improvement through problem-solving and teamwork. By implementing TQM principles, organizations can create a culture of quality that permeates every aspect of their operations.
TQM Principles
Customer Focus
Continuous Improvement
Employee Involvement
Process-Oriented Approach
Data-Driven Decision Making
Six Sigma
Six Sigma is a data-driven methodology that aims to reduce variation and defects in processes to achieve near-perfect quality. By employing statistical tools and analysis techniques, Six Sigma practitioners seek to identify and eliminate the root causes of problems, leading to improved process efficiency and performance. The DMAIC (Define, Measure, Analyze, Improve, Control) methodology is a fundamental part of the Six Sigma approach, guiding practitioners through the process of improving processes and delivering measurable results.
Six Sigma Tools
Control Charts
Pareto Analysis
Root Cause Analysis
Statistical Process Control
Design of Experiments
Lean
Lean, on the other hand, is focused on maximizing customer value while minimizing waste. Lean principles aim to streamline processes, reduce lead times, and eliminate non-value-added activities in order to deliver high-quality products and services efficiently. By embracing concepts such as kaizen (continuous improvement) and just-in-time production, organizations can achieve operational excellence and sustained competitive advantage through Lean methodologies.
Lean Principles
Value Stream Mapping
Pull System
Kanban
5S Methodology
Gemba Walk
TQM vs. Six Sigma vs. Lean: A Comparative Analysis
When comparing TQM, Six Sigma, and Lean, it's important to consider the strengths and weaknesses of each methodology in relation to the specific needs and goals of an organization. TQM excels in fostering a culture of quality and employee engagement, while Six Sigma is renowned for its rigorous statistical analysis and problem-solving capabilities. Lean, on the other hand, shines in its focus on waste reduction and process efficiency.
TQM vs. Six Sigma vs. Lean: Key Differences
TQM emphasizes employee involvement and continuous improvement, while Six Sigma focuses on statistical analysis and defect reduction.
Lean prioritizes waste elimination and value stream optimization, while TQM and Six Sigma have a broader quality management focus.
Six Sigma employs the DMAIC methodology for problem-solving, Lean uses tools like value stream mapping and kanban to streamline processes.
How to obtain Quality Management certification?
We are an Education Technology company providing certification training courses to accelerate careers of working professionals worldwide. We impart training through instructor-led classroom workshops, instructor-led live virtual training sessions, and self-paced e-learning courses.
We have successfully conducted training sessions in 108 countries across the globe and enabled thousands of working professionals to enhance the scope of their careers.
Our enterprise training portfolio includes in-demand and globally recognized certification training courses in Project Management, Quality Management, Business Analysis, IT Service Management, Agile and Scrum, Cyber Security, Data Science, and Emerging Technologies. Download our Enterprise Training Catalog from https://www.icertglobal.com/corporate-training-for-enterprises.php and https://www.icertglobal.com/index.php
Popular Courses include:
Project Management: PMP, CAPM ,PMI RMP
Quality Management: Six Sigma Black Belt ,Lean Six Sigma Green Belt, Lean Management, Minitab,CMMI
Business Analysis: CBAP, CCBA, ECBA
Agile Training: PMI-ACP , CSM , CSPO
Scrum Training: CSM
DevOps
Program Management: PgMP
Cloud Technology: Exin Cloud Computing
Citrix Client Adminisration: Citrix Cloud Administration
The 10 top-paying certifications to target in 2024 are:
Certified Information Systems Security Professional® (CISSP)
AWS Certified Solutions Architect
Google Certified Professional Cloud Architect
Certified In Risk And Information Systems Control (CRISC)
Certified Information Security Manager(CISM)
Project Management Professional (PMP)® Certification
Certified Ethical Hacker (CEH)
Conclusion
In conclusion, each of these methodologies - TQM, Six Sigma, and Lean - offers a unique approach to quality management and process improvement. By understanding the key differences and strengths of each methodology, organizations can select the most suitable framework to achieve their quality goals and drive continuous improvement in their operations. Remember, the key to success lies in choosing the right methodology and adapting it to fit the specific needs and challenges of your organization.
Contact Us For More Information:
Visit : www.icertglobal.com Email : info@icertglobal.com
Read More
href="https://www.icertglobal.com/tqm-six-sigma-and-lean-a-comparative-analysis-blog/detail" />
In the realm of quality management and process improvement, three methodologies stand out as the leading approaches to achieving excellence: Total Quality Management (TQM), Six Sigma, and Lean. Each methodology brings its own unique set of principles, tools, and techniques to the table, but they all share the common goal of driving continuous improvement and enhancing overall business performance.
Total Quality Management (TQM)
Total Quality Management, or TQM, is a holistic approach to quality management that focuses on involving all employees in the continuous improvement of processes, products, and services. TQM emphasizes the importance of customer satisfaction, employee involvement, and process improvement through problem-solving and teamwork. By implementing TQM principles, organizations can create a culture of quality that permeates every aspect of their operations.
TQM Principles
Customer Focus
Continuous Improvement
Employee Involvement
Process-Oriented Approach
Data-Driven Decision Making
Six Sigma
Six Sigma is a data-driven methodology that aims to reduce variation and defects in processes to achieve near-perfect quality. By employing statistical tools and analysis techniques, Six Sigma practitioners seek to identify and eliminate the root causes of problems, leading to improved process efficiency and performance. The DMAIC (Define, Measure, Analyze, Improve, Control) methodology is a fundamental part of the Six Sigma approach, guiding practitioners through the process of improving processes and delivering measurable results.
Six Sigma Tools
Control Charts
Pareto Analysis
Root Cause Analysis
Statistical Process Control
Design of Experiments
Lean
Lean, on the other hand, is focused on maximizing customer value while minimizing waste. Lean principles aim to streamline processes, reduce lead times, and eliminate non-value-added activities in order to deliver high-quality products and services efficiently. By embracing concepts such as kaizen (continuous improvement) and just-in-time production, organizations can achieve operational excellence and sustained competitive advantage through Lean methodologies.
Lean Principles
Value Stream Mapping
Pull System
Kanban
5S Methodology
Gemba Walk
TQM vs. Six Sigma vs. Lean: A Comparative Analysis
When comparing TQM, Six Sigma, and Lean, it's important to consider the strengths and weaknesses of each methodology in relation to the specific needs and goals of an organization. TQM excels in fostering a culture of quality and employee engagement, while Six Sigma is renowned for its rigorous statistical analysis and problem-solving capabilities. Lean, on the other hand, shines in its focus on waste reduction and process efficiency.
TQM vs. Six Sigma vs. Lean: Key Differences
TQM emphasizes employee involvement and continuous improvement, while Six Sigma focuses on statistical analysis and defect reduction.
Lean prioritizes waste elimination and value stream optimization, while TQM and Six Sigma have a broader quality management focus.
Six Sigma employs the DMAIC methodology for problem-solving, Lean uses tools like value stream mapping and kanban to streamline processes.
How to obtain Quality Management certification?
We are an Education Technology company providing certification training courses to accelerate careers of working professionals worldwide. We impart training through instructor-led classroom workshops, instructor-led live virtual training sessions, and self-paced e-learning courses.
We have successfully conducted training sessions in 108 countries across the globe and enabled thousands of working professionals to enhance the scope of their careers.
Our enterprise training portfolio includes in-demand and globally recognized certification training courses in Project Management, Quality Management, Business Analysis, IT Service Management, Agile and Scrum, Cyber Security, Data Science, and Emerging Technologies. Download our Enterprise Training Catalog from https://www.icertglobal.com/corporate-training-for-enterprises.php and https://www.icertglobal.com/index.php
Popular Courses include:
Project Management: PMP, CAPM ,PMI RMP
Quality Management: Six Sigma Black Belt ,Lean Six Sigma Green Belt, Lean Management, Minitab,CMMI
Business Analysis: CBAP, CCBA, ECBA
Agile Training: PMI-ACP , CSM , CSPO
Scrum Training: CSM
DevOps
Program Management: PgMP
Cloud Technology: Exin Cloud Computing
Citrix Client Adminisration: Citrix Cloud Administration
The 10 top-paying certifications to target in 2024 are:
Certified Information Systems Security Professional® (CISSP)
AWS Certified Solutions Architect
Google Certified Professional Cloud Architect
Certified In Risk And Information Systems Control (CRISC)
Certified Information Security Manager(CISM)
Project Management Professional (PMP)® Certification
Certified Ethical Hacker (CEH)
Conclusion
In conclusion, each of these methodologies - TQM, Six Sigma, and Lean - offers a unique approach to quality management and process improvement. By understanding the key differences and strengths of each methodology, organizations can select the most suitable framework to achieve their quality goals and drive continuous improvement in their operations. Remember, the key to success lies in choosing the right methodology and adapting it to fit the specific needs and challenges of your organization.
Contact Us For More Information:
Visit : www.icertglobal.com Email : info@icertglobal.com
Real-World Applications of CTFL Knowledge Across Industries
In today's fast-paced and competitive business environment, having a solid understanding of software testing principles is essential for success. The Certified Tester Foundation Level (CTFL) certification provides individuals with the knowledge and skills needed to excel in the field of software testing. But how exactly can this knowledge be applied in the real world? Let's explore some practical examples and case studies that demonstrate the value of CTFL expertise in industry settings.
CTFL Knowledge in Practice
One of the key benefits of obtaining a CTFL certification is the ability to apply theoretical software testing concepts to real-world scenarios. By understanding the principles of test design, execution, and evaluation, certified testers can effectively identify and report bugs, ensuring that software products meet quality standards.
CTFL in Industry
CTFL-certified professionals are highly sought after in the software industry for their ability to apply testing best practices in a variety of settings. From small startups to large corporations, CTFL expertise is invaluable in ensuring that software projects are delivered on time and within budget.
CTFL Case Studies
Several case studies highlight the success of CTFL-certified individuals in various industries. For example, a software development company implemented CTFL principles during the testing phase of a new mobile app, resulting in a significant decrease in the number of post-release defects.
Using CTFL Professionally
By leveraging their CTFL skills, professionals can excel in their careers and stand out in a competitive job market. Employers value the practical knowledge and hands-on experience that CTFL-certified individuals bring to the table, making them valuable assets to any organization.
Applying CTFL Concepts
CTFL-certified testers are able to apply their knowledge in real-life projects, identifying potential issues early on in the development process and ensuring that software products meet user expectations. This results in higher customer satisfaction and increased project success rates.
CTFL Implementation in Projects
Incorporating CTFL principles into project workflows can streamline the testing process and improve overall product quality. By following industry best practices and utilizing CTFL tools and techniques, teams can effectively manage risks and ensure that software projects are delivered successfully.
CTFL Expertise in Real Life
The expertise gained through CTFL certification allows professionals to tackle complex testing challenges with confidence. By staying up-to-date on the latest industry trends and best practices, CTFL-certified individuals can make informed decisions that contribute to project success.
CTFL Hands-On Experience
Hands-on experience is key to mastering CTFL skills and applying them effectively in real-world projects. By participating in practical training sessions and working on real-life testing scenarios, professionals can build their confidence and expertise in the field of software testing.
CTFL in the Workplace
Having CTFL-certified testers in the workplace can lead to more efficient and effective testing processes, resulting in higher-quality software products. By following established testing methodologies and best practices, teams can work together cohesively to achieve project goals.
CTFL Success Stories
Many professionals have shared their success stories after obtaining a CTFL certification. From landing their dream job to leading successful testing initiatives, CTFL-certified individuals have demonstrated the value of their expertise in industry settings.
How to obtain CTFL certification?
We are an Education Technology company providing certification training courses to accelerate careers of working professionals worldwide. We impart training through instructor-led classroom workshops, instructor-led live virtual training sessions, and self-paced e-learning courses.
We have successfully conducted training sessions in 108 countries across the globe and enabled thousands of working professionals to enhance the scope of their careers.
Our enterprise training portfolio includes in-demand and globally recognized certification training courses in Project Management, Quality Management, Business Analysis, IT Service Management, Agile and Scrum, Cyber Security, Data Science, and Emerging Technologies. Download our Enterprise Training Catalog from https://www.icertglobal.com/corporate-training-for-enterprises.php and https://www.icertglobal.com/index.php
Popular Courses include:
-
Project Management: PMP, CAPM ,PMI RMP
-
Quality Management: Six Sigma Black Belt ,Lean Six Sigma Green Belt, Lean Management, Minitab,CMMI
-
Business Analysis: CBAP, CCBA, ECBA
-
Agile Training: PMI-ACP , CSM , CSPO
-
Scrum Training: CSM
-
DevOps
-
Program Management: PgMP
-
Cloud Technology: Exin Cloud Computing
-
Citrix Client Adminisration: Citrix Cloud Administration
The 10 top-paying certifications to target in 2024 are:
Conclusion
By leveraging CTFL skills and expertise in real-life projects, professionals can excel in their careers and contribute to the success of software development initiatives. The practical knowledge and hands-on experience gained through CTFL certification provide a solid foundation for tackling testing challenges and delivering high-quality software products.
Read More
In today's fast-paced and competitive business environment, having a solid understanding of software testing principles is essential for success. The Certified Tester Foundation Level (CTFL) certification provides individuals with the knowledge and skills needed to excel in the field of software testing. But how exactly can this knowledge be applied in the real world? Let's explore some practical examples and case studies that demonstrate the value of CTFL expertise in industry settings.
CTFL Knowledge in Practice
One of the key benefits of obtaining a CTFL certification is the ability to apply theoretical software testing concepts to real-world scenarios. By understanding the principles of test design, execution, and evaluation, certified testers can effectively identify and report bugs, ensuring that software products meet quality standards.
CTFL in Industry
CTFL-certified professionals are highly sought after in the software industry for their ability to apply testing best practices in a variety of settings. From small startups to large corporations, CTFL expertise is invaluable in ensuring that software projects are delivered on time and within budget.
CTFL Case Studies
Several case studies highlight the success of CTFL-certified individuals in various industries. For example, a software development company implemented CTFL principles during the testing phase of a new mobile app, resulting in a significant decrease in the number of post-release defects.
Using CTFL Professionally
By leveraging their CTFL skills, professionals can excel in their careers and stand out in a competitive job market. Employers value the practical knowledge and hands-on experience that CTFL-certified individuals bring to the table, making them valuable assets to any organization.
Applying CTFL Concepts
CTFL-certified testers are able to apply their knowledge in real-life projects, identifying potential issues early on in the development process and ensuring that software products meet user expectations. This results in higher customer satisfaction and increased project success rates.
CTFL Implementation in Projects
Incorporating CTFL principles into project workflows can streamline the testing process and improve overall product quality. By following industry best practices and utilizing CTFL tools and techniques, teams can effectively manage risks and ensure that software projects are delivered successfully.
CTFL Expertise in Real Life
The expertise gained through CTFL certification allows professionals to tackle complex testing challenges with confidence. By staying up-to-date on the latest industry trends and best practices, CTFL-certified individuals can make informed decisions that contribute to project success.
CTFL Hands-On Experience
Hands-on experience is key to mastering CTFL skills and applying them effectively in real-world projects. By participating in practical training sessions and working on real-life testing scenarios, professionals can build their confidence and expertise in the field of software testing.
CTFL in the Workplace
Having CTFL-certified testers in the workplace can lead to more efficient and effective testing processes, resulting in higher-quality software products. By following established testing methodologies and best practices, teams can work together cohesively to achieve project goals.
CTFL Success Stories
Many professionals have shared their success stories after obtaining a CTFL certification. From landing their dream job to leading successful testing initiatives, CTFL-certified individuals have demonstrated the value of their expertise in industry settings.
How to obtain CTFL certification?
We are an Education Technology company providing certification training courses to accelerate careers of working professionals worldwide. We impart training through instructor-led classroom workshops, instructor-led live virtual training sessions, and self-paced e-learning courses.
We have successfully conducted training sessions in 108 countries across the globe and enabled thousands of working professionals to enhance the scope of their careers.
Our enterprise training portfolio includes in-demand and globally recognized certification training courses in Project Management, Quality Management, Business Analysis, IT Service Management, Agile and Scrum, Cyber Security, Data Science, and Emerging Technologies. Download our Enterprise Training Catalog from https://www.icertglobal.com/corporate-training-for-enterprises.php and https://www.icertglobal.com/index.php
Popular Courses include:
-
Project Management: PMP, CAPM ,PMI RMP
-
Quality Management: Six Sigma Black Belt ,Lean Six Sigma Green Belt, Lean Management, Minitab,CMMI
-
Business Analysis: CBAP, CCBA, ECBA
-
Agile Training: PMI-ACP , CSM , CSPO
-
Scrum Training: CSM
-
DevOps
-
Program Management: PgMP
-
Cloud Technology: Exin Cloud Computing
-
Citrix Client Adminisration: Citrix Cloud Administration
The 10 top-paying certifications to target in 2024 are:
Conclusion
By leveraging CTFL skills and expertise in real-life projects, professionals can excel in their careers and contribute to the success of software development initiatives. The practical knowledge and hands-on experience gained through CTFL certification provide a solid foundation for tackling testing challenges and delivering high-quality software products.
Mastering Statistical Process Control (SPC) with Minitab
Have you ever wondered how you can improve the quality of your manufacturing processes? Statistical Process Control (SPC) with Minitab is the key to achieving process optimization and ensuring high-quality products. In this article, we will delve into the world of SPC techniques, statistical analysis, and quality control using Minitab software.
What is Statistical Process Control (SPC)?
Statistical Process Control (SPC) is a method of quality control that uses statistical methods to monitor and control a process. SPC techniques involve analyzing data to understand the process variation, identifying trends, and making data-driven decisions for process improvement. By implementing SPC, organizations can achieve process optimization and ensure consistent quality in their products and services.
How can Minitab help with SPC?
Minitab is a powerful statistical software that is widely used for process monitoring and analysis. With Minitab, you can easily create control charts, perform statistical analysis, and conduct capability analysis to assess the performance of your processes. The software provides a user-friendly interface and a wide range of statistical tools that make it easier to implement SPC techniques and drive continuous improvement.
The Benefits of SPC with Minitab
-
Process Optimization: By using Minitab for SPC, organizations can identify process variations and make data-driven decisions to optimize their processes for better performance.
-
Quality Management: SPC with Minitab enables organizations to maintain high-quality standards in their products and services by monitoring process performance and ensuring consistency.
-
SPC Implementation: Minitab provides the necessary tools and resources for implementing SPC techniques effectively, leading to improved process stability and product quality.
How to Master SPC Techniques with Minitab
To master SPC techniques with Minitab, it is essential to undergo proper training and certification in statistical quality control. Organizations can invest in SPC training programs that focus on the fundamentals of SPC principles, process monitoring, and statistical process control tools. By mastering SPC techniques with Minitab, organizations can enhance their process optimization efforts and drive continuous improvement in their operations.
How to obtain Minitab certification?
We are an Education Technology company providing certification training courses to accelerate careers of working professionals worldwide. We impart training through instructor-led classroom workshops, instructor-led live virtual training sessions, and self-paced e-learning courses.
We have successfully conducted training sessions in 108 countries across the globe and enabled thousands of working professionals to enhance the scope of their careers.
Our enterprise training portfolio includes in-demand and globally recognized certification training courses in Project Management, Quality Management, Business Analysis, IT Service Management, Agile and Scrum, Cyber Security, Data Science, and Emerging Technologies. Download our Enterprise Training Catalog from https://www.icertglobal.com/corporate-training-for-enterprises.php and https://www.icertglobal.com/index.php
Popular Courses include:
-
Project Management: PMP, CAPM ,PMI RMP
-
Quality Management: Six Sigma Black Belt ,Lean Six Sigma Green Belt, Lean Management, Minitab,CMMI
-
Business Analysis: CBAP, CCBA, ECBA
-
Agile Training: PMI-ACP , CSM , CSPO
-
Scrum Training: CSM
-
DevOps
-
Program Management: PgMP
-
Cloud Technology: Exin Cloud Computing
-
Citrix Client Adminisration: Citrix Cloud Administration
The 10 top-paying certifications to target in 2024 are:
Conclusion
Mastering Statistical Process Control (SPC) with Minitab is essential for organizations looking to achieve process optimization, quality management, and continuous improvement. By leveraging the power of SPC techniques and statistical analysis with Minitab software, organizations can ensure high-quality products and services, improve process performance, and drive business success.
Contact Us For More Information:
Visit : www.icertglobal.com Email : info@icertglobal.com
Read More
Have you ever wondered how you can improve the quality of your manufacturing processes? Statistical Process Control (SPC) with Minitab is the key to achieving process optimization and ensuring high-quality products. In this article, we will delve into the world of SPC techniques, statistical analysis, and quality control using Minitab software.
What is Statistical Process Control (SPC)?
Statistical Process Control (SPC) is a method of quality control that uses statistical methods to monitor and control a process. SPC techniques involve analyzing data to understand the process variation, identifying trends, and making data-driven decisions for process improvement. By implementing SPC, organizations can achieve process optimization and ensure consistent quality in their products and services.
How can Minitab help with SPC?
Minitab is a powerful statistical software that is widely used for process monitoring and analysis. With Minitab, you can easily create control charts, perform statistical analysis, and conduct capability analysis to assess the performance of your processes. The software provides a user-friendly interface and a wide range of statistical tools that make it easier to implement SPC techniques and drive continuous improvement.
The Benefits of SPC with Minitab
-
Process Optimization: By using Minitab for SPC, organizations can identify process variations and make data-driven decisions to optimize their processes for better performance.
-
Quality Management: SPC with Minitab enables organizations to maintain high-quality standards in their products and services by monitoring process performance and ensuring consistency.
-
SPC Implementation: Minitab provides the necessary tools and resources for implementing SPC techniques effectively, leading to improved process stability and product quality.
How to Master SPC Techniques with Minitab
To master SPC techniques with Minitab, it is essential to undergo proper training and certification in statistical quality control. Organizations can invest in SPC training programs that focus on the fundamentals of SPC principles, process monitoring, and statistical process control tools. By mastering SPC techniques with Minitab, organizations can enhance their process optimization efforts and drive continuous improvement in their operations.
How to obtain Minitab certification?
We are an Education Technology company providing certification training courses to accelerate careers of working professionals worldwide. We impart training through instructor-led classroom workshops, instructor-led live virtual training sessions, and self-paced e-learning courses.
We have successfully conducted training sessions in 108 countries across the globe and enabled thousands of working professionals to enhance the scope of their careers.
Our enterprise training portfolio includes in-demand and globally recognized certification training courses in Project Management, Quality Management, Business Analysis, IT Service Management, Agile and Scrum, Cyber Security, Data Science, and Emerging Technologies. Download our Enterprise Training Catalog from https://www.icertglobal.com/corporate-training-for-enterprises.php and https://www.icertglobal.com/index.php
Popular Courses include:
-
Project Management: PMP, CAPM ,PMI RMP
-
Quality Management: Six Sigma Black Belt ,Lean Six Sigma Green Belt, Lean Management, Minitab,CMMI
-
Business Analysis: CBAP, CCBA, ECBA
-
Agile Training: PMI-ACP , CSM , CSPO
-
Scrum Training: CSM
-
DevOps
-
Program Management: PgMP
-
Cloud Technology: Exin Cloud Computing
-
Citrix Client Adminisration: Citrix Cloud Administration
The 10 top-paying certifications to target in 2024 are:
Conclusion
Mastering Statistical Process Control (SPC) with Minitab is essential for organizations looking to achieve process optimization, quality management, and continuous improvement. By leveraging the power of SPC techniques and statistical analysis with Minitab software, organizations can ensure high-quality products and services, improve process performance, and drive business success.
Contact Us For More Information:
Visit : www.icertglobal.com Email : info@icertglobal.com
Optimize Workspaces Using the 5S Methodology for Efficiency
Are you looking to optimize your workspace for maximum efficiency and productivity? Implementing the 5S methodology is a proven way to declutter, organize, and streamline your workspace. In this article, we will explore how you can use the 5S principles to transform your workplace into a well-organized and highly efficient environment.
What is the 5S Methodology?
The 5S methodology is a workplace organization system that originated in Japan. The 5S stands for Sort, Set in Order, Shine, Standardize, and Sustain. It is based on five simple principles that, when implemented correctly, can lead to a more productive and efficient work environment.
Sort
The first step in the 5S methodology is to sort through all the items in your workspace and eliminate anything that is unnecessary. This includes getting rid of clutter, unused equipment, and outdated documents. By reducing the number of items in your workspace, you can create a more organized and streamlined environment.
Set in Order
After sorting through your workspace, the next step is to set everything in its proper place. This involves creating designated storage areas for tools, supplies, and documents. By having a designated spot for everything, you can easily find what you need when you need it, leading to increased efficiency and productivity.
Shine
The shine step of the 5S methodology involves cleaning and maintaining your workspace on a regular basis. A clean and organized workspace not only looks better but also creates a more enjoyable and productive work environment. By implementing regular cleaning and maintenance routines, you can ensure that your workspace remains clutter-free and efficient.
Standardize
Standardizing your workspace involves creating consistent processes and procedures for maintaining organization and cleanliness. This includes developing standard operating procedures for tasks, creating visual cues for where items should be stored, and implementing regular audits to ensure compliance. By standardizing your processes, you can maintain an efficient and productive workspace over the long term.
Sustain
The final step in the 5S methodology is to sustain the improvements made in your workspace. This involves creating a culture of continuous improvement and maintaining the discipline to follow the 5S principles on a daily basis. By sustaining the changes made to your workspace, you can ensure that your organization remains efficient and productive in the long run.
Benefits of Implementing the 5S Methodology
Implementing the 5S methodology in your workspace can lead to a wide range of benefits, including:
-
Increased workplace efficiency
-
Improved productivity
-
Enhanced workplace safety
-
Better employee morale
-
Reduced waste and costs
-
Improved quality of work
By following the 5S principles and creating an organized and efficient workspace, you can create a more enjoyable and productive work environment for yourself and your employees.
Tools and Resources for Implementing the 5S Methodology
There are a variety of tools and resources available to help you implement the 5S methodology in your workspace. Some common tools include:
-
5S checklists
-
Visual management boards
-
Shadow boards
-
Lean management software
-
Kaizen events
By utilizing these tools and resources, you can streamline your workspace, reduce clutter, and increase productivity and efficiency.
How to obtain Quality management certification?
We are an Education Technology company providing certification training courses to accelerate careers of working professionals worldwide. We impart training through instructor-led classroom workshops, instructor-led live virtual training sessions, and self-paced e-learning courses.
We have successfully conducted training sessions in 108 countries across the globe and enabled thousands of working professionals to enhance the scope of their careers.
Our enterprise training portfolio includes in-demand and globally recognized certification training courses in Project Management, Quality Management, Business Analysis, IT Service Management, Agile and Scrum, Cyber Security, Data Science, and Emerging Technologies. Download our Enterprise Training Catalog from https://www.icertglobal.com/corporate-training-for-enterprises.php and https://www.icertglobal.com/index.php
Popular Courses include:
-
Project Management: PMP, CAPM ,PMI RMP
-
Quality Management: Six Sigma Black Belt ,Lean Six Sigma Green Belt, Lean Management, Minitab,CMMI
-
Business Analysis: CBAP, CCBA, ECBA
-
Agile Training: PMI-ACP , CSM , CSPO
-
Scrum Training: CSM
-
DevOps
-
Program Management: PgMP
-
Cloud Technology: Exin Cloud Computing
-
Citrix Client Adminisration: Citrix Cloud Administration
The 10 top-paying certifications to target in 2024 are:
Conclusion
In conclusion, implementing the 5S methodology in your workspace can lead to significant improvements in efficiency, productivity, and overall workplace organization. By following the 5S principles of Sort, Set in Order, Shine, Standardize, and Sustain, you can create a well-organized and highly efficient work environment that promotes productivity and employee satisfaction. So why wait? Start implementing the 5S methodology in your workspace today and reap the benefits of a more efficient and productive workplace!
Contact Us For More Information:
Visit : www.icertglobal.com Email : info@icertglobal.com
Read More
Are you looking to optimize your workspace for maximum efficiency and productivity? Implementing the 5S methodology is a proven way to declutter, organize, and streamline your workspace. In this article, we will explore how you can use the 5S principles to transform your workplace into a well-organized and highly efficient environment.
What is the 5S Methodology?
The 5S methodology is a workplace organization system that originated in Japan. The 5S stands for Sort, Set in Order, Shine, Standardize, and Sustain. It is based on five simple principles that, when implemented correctly, can lead to a more productive and efficient work environment.
Sort
The first step in the 5S methodology is to sort through all the items in your workspace and eliminate anything that is unnecessary. This includes getting rid of clutter, unused equipment, and outdated documents. By reducing the number of items in your workspace, you can create a more organized and streamlined environment.
Set in Order
After sorting through your workspace, the next step is to set everything in its proper place. This involves creating designated storage areas for tools, supplies, and documents. By having a designated spot for everything, you can easily find what you need when you need it, leading to increased efficiency and productivity.
Shine
The shine step of the 5S methodology involves cleaning and maintaining your workspace on a regular basis. A clean and organized workspace not only looks better but also creates a more enjoyable and productive work environment. By implementing regular cleaning and maintenance routines, you can ensure that your workspace remains clutter-free and efficient.
Standardize
Standardizing your workspace involves creating consistent processes and procedures for maintaining organization and cleanliness. This includes developing standard operating procedures for tasks, creating visual cues for where items should be stored, and implementing regular audits to ensure compliance. By standardizing your processes, you can maintain an efficient and productive workspace over the long term.
Sustain
The final step in the 5S methodology is to sustain the improvements made in your workspace. This involves creating a culture of continuous improvement and maintaining the discipline to follow the 5S principles on a daily basis. By sustaining the changes made to your workspace, you can ensure that your organization remains efficient and productive in the long run.
Benefits of Implementing the 5S Methodology
Implementing the 5S methodology in your workspace can lead to a wide range of benefits, including:
-
Increased workplace efficiency
-
Improved productivity
-
Enhanced workplace safety
-
Better employee morale
-
Reduced waste and costs
-
Improved quality of work
By following the 5S principles and creating an organized and efficient workspace, you can create a more enjoyable and productive work environment for yourself and your employees.
Tools and Resources for Implementing the 5S Methodology
There are a variety of tools and resources available to help you implement the 5S methodology in your workspace. Some common tools include:
-
5S checklists
-
Visual management boards
-
Shadow boards
-
Lean management software
-
Kaizen events
By utilizing these tools and resources, you can streamline your workspace, reduce clutter, and increase productivity and efficiency.
How to obtain Quality management certification?
We are an Education Technology company providing certification training courses to accelerate careers of working professionals worldwide. We impart training through instructor-led classroom workshops, instructor-led live virtual training sessions, and self-paced e-learning courses.
We have successfully conducted training sessions in 108 countries across the globe and enabled thousands of working professionals to enhance the scope of their careers.
Our enterprise training portfolio includes in-demand and globally recognized certification training courses in Project Management, Quality Management, Business Analysis, IT Service Management, Agile and Scrum, Cyber Security, Data Science, and Emerging Technologies. Download our Enterprise Training Catalog from https://www.icertglobal.com/corporate-training-for-enterprises.php and https://www.icertglobal.com/index.php
Popular Courses include:
-
Project Management: PMP, CAPM ,PMI RMP
-
Quality Management: Six Sigma Black Belt ,Lean Six Sigma Green Belt, Lean Management, Minitab,CMMI
-
Business Analysis: CBAP, CCBA, ECBA
-
Agile Training: PMI-ACP , CSM , CSPO
-
Scrum Training: CSM
-
DevOps
-
Program Management: PgMP
-
Cloud Technology: Exin Cloud Computing
-
Citrix Client Adminisration: Citrix Cloud Administration
The 10 top-paying certifications to target in 2024 are:
Conclusion
In conclusion, implementing the 5S methodology in your workspace can lead to significant improvements in efficiency, productivity, and overall workplace organization. By following the 5S principles of Sort, Set in Order, Shine, Standardize, and Sustain, you can create a well-organized and highly efficient work environment that promotes productivity and employee satisfaction. So why wait? Start implementing the 5S methodology in your workspace today and reap the benefits of a more efficient and productive workplace!
Contact Us For More Information:
Visit : www.icertglobal.com Email : info@icertglobal.com
Mastering Project Quality: Essential Steps for Success.
Are you ready to take your project quality management skills to the next level? In this comprehensive guide, we will walk you through a step-by-step process to help you master project quality management from start to finish. From quality assurance to quality control, project planning to quality management techniques, we've got you covered. Let's dive in and explore the world of project quality management together!
Introduction to Project Quality Management
Project quality management is a crucial aspect of any successful project. It involves ensuring that the project meets the specified quality standards set forth by the stakeholders. By implementing quality management processes, you can optimize project outcomes, minimize risks, and deliver a high-quality end product.
What is Project Quality Management?
Project quality management is the process of ensuring that a project meets the specified quality standards throughout its lifecycle. This involves careful planning, implementation, and monitoring of quality control measures to ensure that the project delivers the desired results.
Why is project quality management Important?
Quality management is vital for the success of any project. By focusing on quality assurance, control, and improvement, you can enhance customer satisfaction, reduce rework, and increase overall project efficiency.
The Project Quality Management Process
To master project quality management, you need to follow a structured process. Here is a step-by-step guide to help you navigate the quality management framework successfully:
-
Project Quality Planning: Define the quality standards and establish a plan to achieve them.
-
Quality Assurance: Implement processes to ensure quality standards are met throughout the project.
-
Quality Control: Monitor and validate project deliverables to meet quality requirements.
-
Quality Improvement: Continuously assess and enhance project processes to improve quality outcomes.
Strategies for Project Quality Management
To excel in project quality management, consider the following strategies:
-
Set Clear Objectives: Define quality goals and expectations from the outset.
-
Empower Team Members: Equip your team with the resources and training needed to achieve quality standards.
-
Utilize Quality Metrics: Measure and analyze key quality indicators to track performance.
-
Continuous Improvement: Foster a culture of quality improvement to drive project success.
How to obtain Quality Management certification?
We are an Education Technology company providing certification training courses to accelerate careers of working professionals worldwide. We impart training through instructor-led classroom workshops, instructor-led live virtual training sessions, and self-paced e-learning courses.
We have successfully conducted training sessions in 108 countries across the globe and enabled thousands of working professionals to enhance the scope of their careers.
Our enterprise training portfolio includes in-demand and globally recognized certification training courses in Project Management, Quality Management, Business Analysis, IT Service Management, Agile and Scrum, Cyber Security, Data Science, and Emerging Technologies. Download our Enterprise Training Catalog from https://www.icertglobal.com/corporate-training-for-enterprises.php and https://www.icertglobal.com/index.php
Popular Courses include:
-
Project Management: PMP, CAPM ,PMI RMP
-
Quality Management: Six Sigma Black Belt ,Lean Six Sigma Green Belt, Lean Management, Minitab,CMMI
-
Business Analysis: CBAP, CCBA, ECBA
-
Agile Training: PMI-ACP , CSM , CSPO
-
Scrum Training: CSM
-
DevOps
-
Program Management: PgMP
-
Cloud Technology: Exin Cloud Computing
-
Citrix Client Adminisration: Citrix Cloud Administration
The 10 top-paying certifications to target in 2024 are:
Conclusion
By mastering project quality management, you can elevate your project outcomes and build a reputation for delivering high-quality results. Use the step-by-step guide, tools, and strategies outlined in this comprehensive article to enhance your quality management skills and excel in your project endeavors. Remember, quality is not an act, it is a habit. Start building your quality management habits today!
Contact Us For More Information
Visit : www.icertglobal.com Email : info@icertglobal.com
Read More
Are you ready to take your project quality management skills to the next level? In this comprehensive guide, we will walk you through a step-by-step process to help you master project quality management from start to finish. From quality assurance to quality control, project planning to quality management techniques, we've got you covered. Let's dive in and explore the world of project quality management together!
Introduction to Project Quality Management
Project quality management is a crucial aspect of any successful project. It involves ensuring that the project meets the specified quality standards set forth by the stakeholders. By implementing quality management processes, you can optimize project outcomes, minimize risks, and deliver a high-quality end product.
What is Project Quality Management?
Project quality management is the process of ensuring that a project meets the specified quality standards throughout its lifecycle. This involves careful planning, implementation, and monitoring of quality control measures to ensure that the project delivers the desired results.
Why is project quality management Important?
Quality management is vital for the success of any project. By focusing on quality assurance, control, and improvement, you can enhance customer satisfaction, reduce rework, and increase overall project efficiency.
The Project Quality Management Process
To master project quality management, you need to follow a structured process. Here is a step-by-step guide to help you navigate the quality management framework successfully:
-
Project Quality Planning: Define the quality standards and establish a plan to achieve them.
-
Quality Assurance: Implement processes to ensure quality standards are met throughout the project.
-
Quality Control: Monitor and validate project deliverables to meet quality requirements.
-
Quality Improvement: Continuously assess and enhance project processes to improve quality outcomes.
Strategies for Project Quality Management
To excel in project quality management, consider the following strategies:
-
Set Clear Objectives: Define quality goals and expectations from the outset.
-
Empower Team Members: Equip your team with the resources and training needed to achieve quality standards.
-
Utilize Quality Metrics: Measure and analyze key quality indicators to track performance.
-
Continuous Improvement: Foster a culture of quality improvement to drive project success.
How to obtain Quality Management certification?
We are an Education Technology company providing certification training courses to accelerate careers of working professionals worldwide. We impart training through instructor-led classroom workshops, instructor-led live virtual training sessions, and self-paced e-learning courses.
We have successfully conducted training sessions in 108 countries across the globe and enabled thousands of working professionals to enhance the scope of their careers.
Our enterprise training portfolio includes in-demand and globally recognized certification training courses in Project Management, Quality Management, Business Analysis, IT Service Management, Agile and Scrum, Cyber Security, Data Science, and Emerging Technologies. Download our Enterprise Training Catalog from https://www.icertglobal.com/corporate-training-for-enterprises.php and https://www.icertglobal.com/index.php
Popular Courses include:
-
Project Management: PMP, CAPM ,PMI RMP
-
Quality Management: Six Sigma Black Belt ,Lean Six Sigma Green Belt, Lean Management, Minitab,CMMI
-
Business Analysis: CBAP, CCBA, ECBA
-
Agile Training: PMI-ACP , CSM , CSPO
-
Scrum Training: CSM
-
DevOps
-
Program Management: PgMP
-
Cloud Technology: Exin Cloud Computing
-
Citrix Client Adminisration: Citrix Cloud Administration
The 10 top-paying certifications to target in 2024 are:
Conclusion
By mastering project quality management, you can elevate your project outcomes and build a reputation for delivering high-quality results. Use the step-by-step guide, tools, and strategies outlined in this comprehensive article to enhance your quality management skills and excel in your project endeavors. Remember, quality is not an act, it is a habit. Start building your quality management habits today!
Contact Us For More Information
Visit : www.icertglobal.com Email : info@icertglobal.com
The Role of Leadership in Effective Lean Management Success
In today's competitive business environment, organizations are constantly looking for ways to improve efficiency, cut costs, and enhance overall performance. One popular strategy that has gained momentum in recent years is Lean Management. This approach focuses on eliminating waste, streamlining processes, and maximizing value for customers. However, the success of Lean Management implementation heavily relies on effective leadership. In this article, we will explore the critical role that leadership plays in the successful implementation of Lean Management practices.
Importance of Leadership in Lean Management
Leadership is the driving force behind any organizational change initiative, including the implementation of Lean Management. Without strong and committed leadership, employees may be resistant to change, and the organization may struggle to fully realize the benefits of Lean principles. Leaders must not only understand the concepts of Lean Management but also embody them in their daily actions and decision-making processes.
Setting the Vision
One of the key roles of leadership in Lean Management implementation is setting a clear vision and direction for the organization. Leaders need to communicate the benefits of Lean practices and create a sense of urgency around the need for change. By articulating a compelling vision, leaders can inspire and motivate employees to embrace Lean principles and actively participate in the transformation process.
Creating a Culture of Continuous Improvement
Effective leaders understand that Lean Management is not a one-time initiative but a continuous journey towards excellence. They must create a culture that encourages continuous improvement, innovation, and learning. By promoting a mindset of experimentation and risk-taking, leaders can empower employees to identify and eliminate waste, optimize processes, and drive meaningful change across the organization.
Providing Support and Resources
Leaders play a crucial role in providing the necessary support and resources for successful Lean Management implementation. This includes investing in training and development programs, allocating time and funding for improvement projects, and removing barriers to change. By demonstrating a commitment to Lean practices through actions, not just words, leaders can build trust and credibility with employees and motivate them to actively engage in Lean initiatives.
Leading by Example
Perhaps the most important role of leadership in Lean Management implementation is leading by example. Leaders must consistently model Lean behaviors, such as Gemba walks, value-stream mapping, and visual management. By actively participating in improvement projects, soliciting feedback from employees, and embracing a mindset of continuous learning, leaders can inspire others to follow suit and create a culture of accountability and ownership.
How to obtain Quality Management Certification?
We are an Education Technology company providing certification training courses to accelerate careers of working professionals worldwide. We impart training through instructor-led classroom workshops, instructor-led live virtual training sessions, and self-paced e-learning courses.
We have successfully conducted training sessions in 108 countries across the globe and enabled thousands of working professionals to enhance the scope of their careers.
Our enterprise training portfolio includes in-demand and globally recognized certification training courses in Project Management, Quality Management, Business Analysis, IT Service Management, Agile and Scrum, Cyber Security, Data Science, and Emerging Technologies. Download our Enterprise Training Catalog from https://www.icertglobal.com/corporate-training-for-enterprises.php .
Popular Courses include:
-
Project Management: PMP, CAPM ,PMI RMP
-
Quality Management: Six Sigma Black Belt ,Lean Six Sigma Green Belt, Lean Management, Minitab,CMMI
-
Business Analysis: CBAP, CCBA, ECBA
-
Agile Training: PMI-ACP , CSM , CSPO
-
Scrum Training: CSM
-
DevOps
-
Program Management: PgMP
-
Cloud Technology: Exin Cloud Computing
-
Citrix Client Adminisration: Citrix Cloud Administration
The 10 top-paying certifications to target in 2024 are:
Conclusion
In conclusion, leadership plays a critical role in the successful implementation of Lean Management practices. By setting a clear vision, creating a culture of continuous improvement, providing support and resources, and leading by example, leaders can drive organizational change, foster employee engagement, and achieve sustainable results. As organizations continue to embrace Lean principles to stay competitive in the marketplace, strong and effective leadership will be the key to unlocking the full potential of Lean Management practices.
Contact Us For More Information :
Visit : www.icertglobal.com Email : info@icertglobal.com
Read More
In today's competitive business environment, organizations are constantly looking for ways to improve efficiency, cut costs, and enhance overall performance. One popular strategy that has gained momentum in recent years is Lean Management. This approach focuses on eliminating waste, streamlining processes, and maximizing value for customers. However, the success of Lean Management implementation heavily relies on effective leadership. In this article, we will explore the critical role that leadership plays in the successful implementation of Lean Management practices.
Importance of Leadership in Lean Management
Leadership is the driving force behind any organizational change initiative, including the implementation of Lean Management. Without strong and committed leadership, employees may be resistant to change, and the organization may struggle to fully realize the benefits of Lean principles. Leaders must not only understand the concepts of Lean Management but also embody them in their daily actions and decision-making processes.
Setting the Vision
One of the key roles of leadership in Lean Management implementation is setting a clear vision and direction for the organization. Leaders need to communicate the benefits of Lean practices and create a sense of urgency around the need for change. By articulating a compelling vision, leaders can inspire and motivate employees to embrace Lean principles and actively participate in the transformation process.
Creating a Culture of Continuous Improvement
Effective leaders understand that Lean Management is not a one-time initiative but a continuous journey towards excellence. They must create a culture that encourages continuous improvement, innovation, and learning. By promoting a mindset of experimentation and risk-taking, leaders can empower employees to identify and eliminate waste, optimize processes, and drive meaningful change across the organization.
Providing Support and Resources
Leaders play a crucial role in providing the necessary support and resources for successful Lean Management implementation. This includes investing in training and development programs, allocating time and funding for improvement projects, and removing barriers to change. By demonstrating a commitment to Lean practices through actions, not just words, leaders can build trust and credibility with employees and motivate them to actively engage in Lean initiatives.
Leading by Example
Perhaps the most important role of leadership in Lean Management implementation is leading by example. Leaders must consistently model Lean behaviors, such as Gemba walks, value-stream mapping, and visual management. By actively participating in improvement projects, soliciting feedback from employees, and embracing a mindset of continuous learning, leaders can inspire others to follow suit and create a culture of accountability and ownership.
How to obtain Quality Management Certification?
We are an Education Technology company providing certification training courses to accelerate careers of working professionals worldwide. We impart training through instructor-led classroom workshops, instructor-led live virtual training sessions, and self-paced e-learning courses.
We have successfully conducted training sessions in 108 countries across the globe and enabled thousands of working professionals to enhance the scope of their careers.
Our enterprise training portfolio includes in-demand and globally recognized certification training courses in Project Management, Quality Management, Business Analysis, IT Service Management, Agile and Scrum, Cyber Security, Data Science, and Emerging Technologies. Download our Enterprise Training Catalog from https://www.icertglobal.com/corporate-training-for-enterprises.php .
Popular Courses include:
-
Project Management: PMP, CAPM ,PMI RMP
-
Quality Management: Six Sigma Black Belt ,Lean Six Sigma Green Belt, Lean Management, Minitab,CMMI
-
Business Analysis: CBAP, CCBA, ECBA
-
Agile Training: PMI-ACP , CSM , CSPO
-
Scrum Training: CSM
-
DevOps
-
Program Management: PgMP
-
Cloud Technology: Exin Cloud Computing
-
Citrix Client Adminisration: Citrix Cloud Administration
The 10 top-paying certifications to target in 2024 are:
Conclusion
In conclusion, leadership plays a critical role in the successful implementation of Lean Management practices. By setting a clear vision, creating a culture of continuous improvement, providing support and resources, and leading by example, leaders can drive organizational change, foster employee engagement, and achieve sustainable results. As organizations continue to embrace Lean principles to stay competitive in the marketplace, strong and effective leadership will be the key to unlocking the full potential of Lean Management practices.
Contact Us For More Information :
Visit : www.icertglobal.com Email : info@icertglobal.com
Integrating Minitab with Other Software Tools for Analysis
Are you looking to streamline your data analysis process and improve decision-making within your organization? If so, integrating Minitab with other software tools could be the solution you have been searching for. Minitab, a powerful statistical analysis software, offers a wide range of features that can help you make informed decisions based on data-driven insights. In this article, we will explore the benefits of integrating Minitab with other tools, the various options available for integration, and best practices to ensure a seamless collaboration between different software platforms.
Why Integrate Minitab with Other Software Tools?
Integrating Minitab with Excel, quality control tools, process optimization software, and other data analysis tools can significantly enhance your data analysis capabilities. By combining the features of Minitab with other tools, you can create a more comprehensive data analysis workflow that allows for deeper insights and more accurate results. Additionally, integrating Minitab with other software tools can help improve the efficiency of your data analysis process, saving time and resources in the long run.
Minitab Integration Options
There are several options available for integrating Minitab with other software tools. Some common integration strategies include using Minitab add-ins, data visualization software, and plugins that allow for seamless collaboration between different platforms. Additionally, Minitab offers compatibility with various business intelligence tools, process control software, and lean six sigma software, making it easy to incorporate Minitab into your existing data analysis workflow.
Collaboration with Minitab Software
When integrating Minitab with other software tools, it is important to ensure that the different platforms can work together seamlessly. This may require data manipulation to ensure compatibility between systems, as well as setting up integration best practices to streamline the workflow. By collaborating with Minitab software experts, you can learn how to link Minitab with other tools effectively and optimize your data analysis process for better results.
Enhancing Data Analysis with Minitab
By integrating Minitab with other software tools, you can enhance your data analysis capabilities and achieve more accurate and meaningful insights. Minitab offers a wide range of statistical tools that can help you make informed decisions based on real-time data. Whether you are performing process optimization, quality assurance, or statistical modeling, Minitab provides the features you need to succeed in today's data-driven business environment.
Minitab and Lean Six Sigma Software
One area where Minitab excels is in its compatibility with lean six sigma software. By integrating Minitab with lean six sigma tools, you can streamline your process improvement efforts and identify areas for optimization more efficiently. Minitab's interoperability with lean six sigma software allows for a seamless collaboration between the two platforms, enabling you to achieve greater results in your quality control initiatives.
How to obtain Minitab certification?
We are an Education Technology company providing certification training courses to accelerate careers of working professionals worldwide. We impart training through instructor-led classroom workshops, instructor-led live virtual training sessions, and self-paced e-learning courses.
We have successfully conducted training sessions in 108 countries across the globe and enabled thousands of working professionals to enhance the scope of their careers.
Our enterprise training portfolio includes in-demand and globally recognized certification training courses in Project Management, Quality Management, Business Analysis, IT Service Management, Agile and Scrum, Cyber Security, Data Science, and Emerging Technologies. Download our Enterprise Training Catalog from https://www.icertglobal.com/corporate-training-for-enterprises.php and https://www.icertglobal.com/index.php
Popular Courses include:
-
Project Management: PMP, CAPM ,PMI RMP
-
Quality Management: Six Sigma Black Belt ,Lean Six Sigma Green Belt, Lean Management, Minitab,CMMI
-
Business Analysis: CBAP, CCBA, ECBA
-
Agile Training: PMI-ACP , CSM , CSPO
-
Scrum Training: CSM
-
DevOps
-
Program Management: PgMP
-
Cloud Technology: Exin Cloud Computing
-
Citrix Client Adminisration: Citrix Cloud Administration
The 10 top-paying certifications to target in 2024 are:
Conclusion
In conclusion, integrating Minitab with other software tools can greatly enhance your data analysis capabilities and improve decision-making within your organization. By leveraging the features of Minitab and collaborating with other software platforms, you can streamline your data analysis process, achieve more accurate results, and make informed decisions based on real-time insights. So why wait? Start integrating Minitab with other tools today and take your data analysis to the next level!
Contact Us For More Information:
Visit : www.icertglobal.com Email : info@icertglobal.com
Read More
Are you looking to streamline your data analysis process and improve decision-making within your organization? If so, integrating Minitab with other software tools could be the solution you have been searching for. Minitab, a powerful statistical analysis software, offers a wide range of features that can help you make informed decisions based on data-driven insights. In this article, we will explore the benefits of integrating Minitab with other tools, the various options available for integration, and best practices to ensure a seamless collaboration between different software platforms.
Why Integrate Minitab with Other Software Tools?
Integrating Minitab with Excel, quality control tools, process optimization software, and other data analysis tools can significantly enhance your data analysis capabilities. By combining the features of Minitab with other tools, you can create a more comprehensive data analysis workflow that allows for deeper insights and more accurate results. Additionally, integrating Minitab with other software tools can help improve the efficiency of your data analysis process, saving time and resources in the long run.
Minitab Integration Options
There are several options available for integrating Minitab with other software tools. Some common integration strategies include using Minitab add-ins, data visualization software, and plugins that allow for seamless collaboration between different platforms. Additionally, Minitab offers compatibility with various business intelligence tools, process control software, and lean six sigma software, making it easy to incorporate Minitab into your existing data analysis workflow.
Collaboration with Minitab Software
When integrating Minitab with other software tools, it is important to ensure that the different platforms can work together seamlessly. This may require data manipulation to ensure compatibility between systems, as well as setting up integration best practices to streamline the workflow. By collaborating with Minitab software experts, you can learn how to link Minitab with other tools effectively and optimize your data analysis process for better results.
Enhancing Data Analysis with Minitab
By integrating Minitab with other software tools, you can enhance your data analysis capabilities and achieve more accurate and meaningful insights. Minitab offers a wide range of statistical tools that can help you make informed decisions based on real-time data. Whether you are performing process optimization, quality assurance, or statistical modeling, Minitab provides the features you need to succeed in today's data-driven business environment.
Minitab and Lean Six Sigma Software
One area where Minitab excels is in its compatibility with lean six sigma software. By integrating Minitab with lean six sigma tools, you can streamline your process improvement efforts and identify areas for optimization more efficiently. Minitab's interoperability with lean six sigma software allows for a seamless collaboration between the two platforms, enabling you to achieve greater results in your quality control initiatives.
How to obtain Minitab certification?
We are an Education Technology company providing certification training courses to accelerate careers of working professionals worldwide. We impart training through instructor-led classroom workshops, instructor-led live virtual training sessions, and self-paced e-learning courses.
We have successfully conducted training sessions in 108 countries across the globe and enabled thousands of working professionals to enhance the scope of their careers.
Our enterprise training portfolio includes in-demand and globally recognized certification training courses in Project Management, Quality Management, Business Analysis, IT Service Management, Agile and Scrum, Cyber Security, Data Science, and Emerging Technologies. Download our Enterprise Training Catalog from https://www.icertglobal.com/corporate-training-for-enterprises.php and https://www.icertglobal.com/index.php
Popular Courses include:
-
Project Management: PMP, CAPM ,PMI RMP
-
Quality Management: Six Sigma Black Belt ,Lean Six Sigma Green Belt, Lean Management, Minitab,CMMI
-
Business Analysis: CBAP, CCBA, ECBA
-
Agile Training: PMI-ACP , CSM , CSPO
-
Scrum Training: CSM
-
DevOps
-
Program Management: PgMP
-
Cloud Technology: Exin Cloud Computing
-
Citrix Client Adminisration: Citrix Cloud Administration
The 10 top-paying certifications to target in 2024 are:
Conclusion
In conclusion, integrating Minitab with other software tools can greatly enhance your data analysis capabilities and improve decision-making within your organization. By leveraging the features of Minitab and collaborating with other software platforms, you can streamline your data analysis process, achieve more accurate results, and make informed decisions based on real-time insights. So why wait? Start integrating Minitab with other tools today and take your data analysis to the next level!
Contact Us For More Information:
Visit : www.icertglobal.com Email : info@icertglobal.com
What is Lean Methodology? Key Principles for Efficiency
What Is Lean Methodology?
Lean methodology is a systematic approach to continuous process improvement through the elimination of waste. It originated in the manufacturing industry, specifically within Toyota, in the mid-20th century as part of the Toyota Production System (TPS), which sought to maximize value for the customer through the optimal use of resources. The principles of Lean have since been adapted and applied across various sectors, including healthcare, software development, and service industries
Principles of Lean Methodology
Lean methodology principles are fundamental guidelines that help organizations focus on value creation while minimizing waste. The five core principles of Lean methodology are designed to improve efficiency, quality, and customer satisfaction. They are:
-
Define Value: The starting point of Lean is to specify value from the standpoint of the end customer. Understanding what the customer values in a product or service allows organizations to streamline their processes, ensuring that every action contributes towards fulfilling the customer's needs and expectations.
-
Map the Value Stream: This principle involves identifying and mapping all the steps involved in delivering a product or service, from raw materials to the final delivery to the customer. The goal is to visualize the flow of materials and information throughout the organization. This mapping helps identify and eliminate non-value-adding activities (waste), ensuring that every step in the process adds value to the product or service.
-
Create Flow: Once the value stream is identified, the next step is to ensure that the value-creating steps occur in a tight sequence, allowing the product or service to flow smoothly toward the customer without interruptions, delays, or bottlenecks. This can involve reconfiguring production steps, leveling workload, creating cross-functional teams, or adopting new technologies to enable a seamless flow of products and services.
-
Establish Pull: Instead of pushing products through production based on forecasted demand, Lean dictates that production should be based on actual customer demand, thereby minimizing waste associated with overproduction and excess inventory. A pull-based system allows for a more responsive and flexible production scheduling and inventory management approach.
-
Pursue Perfection: Lean is an ongoing process of continuous improvement. Pursuing perfection involves continually seeking ways to reduce waste and improve processes, thereby maximizing value for the customer. This principle encourages a culture of continuous learning and improvement, where employees at all levels identify inefficiencies and suggest improvements.
How to obtain Lean Management certification?
We are an Education Technology company providing certification training courses to accelerate careers of working professionals worldwide. We impart training through instructor-led classroom workshops, instructor-led live virtual training sessions, and self-paced e-learning courses.
We have successfully conducted training sessions in 108 countries across the globe and enabled thousands of working professionals to enhance the scope of their careers.
Our enterprise training portfolio includes in-demand and globally recognized certification training courses in Project Management, Quality Management, Business Analysis, IT Service Management, Agile and Scrum, Cyber Security, Data Science, and Emerging Technologies. Download our Enterprise Training Catalog from https://www.icertglobal.com/corporate-training-for-enterprises.php and https://www.icertglobal.com/index.php
Popular Courses include:
-
Project Management: PMP, CAPM ,PMI RMP
-
Quality Management: Six Sigma Black Belt ,Lean Six Sigma Green Belt, Lean Management, Minitab,CMMI
-
Business Analysis: CBAP, CCBA, ECBA
-
Agile Training: PMI-ACP , CSM , CSPO
-
Scrum Training: CSM
-
DevOps
-
Program Management: PgMP
-
Cloud Technology: Exin Cloud Computing
-
Citrix Client Adminisration: Citrix Cloud Administration
The 10 top-paying certifications to target in 2024 are:
Conclusion
From manufacturing to healthcare and software development to retail, Lean principles empower organizations to streamline operations, enhance efficiency, and deliver unparalleled value to customers. Lean methodology optimizes processes and fosters a culture of excellence and innovation by focusing on waste elimination, continuous improvement, and value creation.
Contact Us For More Information:
Visit : www.icertglobal.com Email : info@icertglobal.com
Read More
What Is Lean Methodology?
Lean methodology is a systematic approach to continuous process improvement through the elimination of waste. It originated in the manufacturing industry, specifically within Toyota, in the mid-20th century as part of the Toyota Production System (TPS), which sought to maximize value for the customer through the optimal use of resources. The principles of Lean have since been adapted and applied across various sectors, including healthcare, software development, and service industries
Principles of Lean Methodology
Lean methodology principles are fundamental guidelines that help organizations focus on value creation while minimizing waste. The five core principles of Lean methodology are designed to improve efficiency, quality, and customer satisfaction. They are:
-
Define Value: The starting point of Lean is to specify value from the standpoint of the end customer. Understanding what the customer values in a product or service allows organizations to streamline their processes, ensuring that every action contributes towards fulfilling the customer's needs and expectations.
-
Map the Value Stream: This principle involves identifying and mapping all the steps involved in delivering a product or service, from raw materials to the final delivery to the customer. The goal is to visualize the flow of materials and information throughout the organization. This mapping helps identify and eliminate non-value-adding activities (waste), ensuring that every step in the process adds value to the product or service.
-
Create Flow: Once the value stream is identified, the next step is to ensure that the value-creating steps occur in a tight sequence, allowing the product or service to flow smoothly toward the customer without interruptions, delays, or bottlenecks. This can involve reconfiguring production steps, leveling workload, creating cross-functional teams, or adopting new technologies to enable a seamless flow of products and services.
-
Establish Pull: Instead of pushing products through production based on forecasted demand, Lean dictates that production should be based on actual customer demand, thereby minimizing waste associated with overproduction and excess inventory. A pull-based system allows for a more responsive and flexible production scheduling and inventory management approach.
-
Pursue Perfection: Lean is an ongoing process of continuous improvement. Pursuing perfection involves continually seeking ways to reduce waste and improve processes, thereby maximizing value for the customer. This principle encourages a culture of continuous learning and improvement, where employees at all levels identify inefficiencies and suggest improvements.
How to obtain Lean Management certification?
We are an Education Technology company providing certification training courses to accelerate careers of working professionals worldwide. We impart training through instructor-led classroom workshops, instructor-led live virtual training sessions, and self-paced e-learning courses.
We have successfully conducted training sessions in 108 countries across the globe and enabled thousands of working professionals to enhance the scope of their careers.
Our enterprise training portfolio includes in-demand and globally recognized certification training courses in Project Management, Quality Management, Business Analysis, IT Service Management, Agile and Scrum, Cyber Security, Data Science, and Emerging Technologies. Download our Enterprise Training Catalog from https://www.icertglobal.com/corporate-training-for-enterprises.php and https://www.icertglobal.com/index.php
Popular Courses include:
-
Project Management: PMP, CAPM ,PMI RMP
-
Quality Management: Six Sigma Black Belt ,Lean Six Sigma Green Belt, Lean Management, Minitab,CMMI
-
Business Analysis: CBAP, CCBA, ECBA
-
Agile Training: PMI-ACP , CSM , CSPO
-
Scrum Training: CSM
-
DevOps
-
Program Management: PgMP
-
Cloud Technology: Exin Cloud Computing
-
Citrix Client Adminisration: Citrix Cloud Administration
The 10 top-paying certifications to target in 2024 are:
Conclusion
From manufacturing to healthcare and software development to retail, Lean principles empower organizations to streamline operations, enhance efficiency, and deliver unparalleled value to customers. Lean methodology optimizes processes and fosters a culture of excellence and innovation by focusing on waste elimination, continuous improvement, and value creation.
Contact Us For More Information:
Visit : www.icertglobal.com Email : info@icertglobal.com
AI's Impact on Quality Management Systems: Future Trends
In today's fast-paced and competitive business environment, companies are constantly looking for ways to improve their operations and stay ahead of the curve. One key technology that is revolutionizing the way organizations manage quality is artificial intelligence (AI). By leveraging AI, companies can streamline their quality management systems, enhance efficiency, and drive innovation like never before.
How Does Artificial Intelligence Impact Quality Management Systems?
-
Automation: AI enables the automation of repetitive tasks and processes in quality management systems, freeing up employees to focus on more strategic initiatives.
-
Data Analysis: With AI-powered analytics tools, businesses can gather and analyze vast amounts of data to identify trends, patterns, and anomalies in quality metrics.
-
Machine Learning: AI algorithms can learn from data and improve over time, allowing quality management systems to become more accurate and efficient.
-
Optimization: By utilizing AI, organizations can optimize their quality control processes and make real-time adjustments to ensure product quality.
The Advantages of Integrating AI into Quality Management Systems
-
Performance: AI can enhance the overall performance of quality management systems by maximizing efficiency and minimizing errors.
-
Process Improvement: With AI, companies can identify areas for improvement in their quality management processes and make strategic changes.
-
Predictive Maintenance: AI can predict equipment failures and maintenance needs, helping companies prevent quality issues before they occur.
How AI is Transforming Quality Control
-
Risk Management: AI tools can help companies identify potential risks in their quality management systems and take proactive measures to mitigate them.
-
Productivity: By automating tasks and processes, AI can boost productivity and streamline quality control workflows.
-
Advancements: AI is driving advancements in quality management systems, leading to more innovative solutions and practices.
The Future of Quality Management Systems with AI
-
Digital Transformation: AI is at the forefront of digital transformation, reshaping the way companies approach quality management.
-
Sustainability: By improving efficiency and reducing waste, AI can help companies achieve sustainability goals in their quality management processes.
-
Workflow: AI can optimize workflows and streamline quality control procedures, making operations more seamless and efficient.
Benefits of AI in Quality Management Systems
-
Smart Solutions: AI offers smart solutions for quality management, enabling companies to make data-driven decisions and enhance quality assurance.
-
Business Intelligence: With AI-powered tools, companies can gain valuable insights into their quality metrics and make informed decisions.
-
Best Practices: AI can help organizations establish and maintain best practices in quality management, ensuring consistent product quality.
How to obtain Quality Management Certification?
We are an Education Technology company providing certification training courses to accelerate careers of working professionals worldwide. We impart training through instructor-led classroom workshops, instructor-led live virtual training sessions, and self-paced e-learning courses.
We have successfully conducted training sessions in 108 countries across the globe and enabled thousands of working professionals to enhance the scope of their careers.
Our enterprise training portfolio includes in-demand and globally recognized certification training courses in Project Management, Quality Management, Business Analysis, IT Service Management, Agile and Scrum, Cyber Security, Data Science, and Emerging Technologies. Download our Enterprise Training Catalog from https://www.icertglobal.com/corporate-training-for-enterprises.php.
Popular Courses include:
-
Project Management: PMP, CAPM ,PMI RMP
-
Quality Management: Six Sigma Black Belt ,Lean Six Sigma Green Belt, Lean Management, Minitab,CMMI
-
Business Analysis: CBAP, CCBA, ECBA
-
Agile Training: PMI-ACP , CSM , CSPO
-
Scrum Training: CSM
-
DevOps
-
Program Management: PgMP
-
Cloud Technology: Exin Cloud Computing
-
Citrix Client Adminisration: Citrix Cloud Administration
The 10 top-paying certifications to target in 2024 are:
Conclusion
In conclusion, the impact of artificial intelligence on quality management systems is undeniable. By leveraging AI technology, companies can improve efficiency, drive innovation, and enhance overall quality control processes. As AI continues to evolve, the possibilities for quality management systems are endless, opening up new opportunities for companies to achieve operational excellence and deliver high-quality products and services to their customers.
Contact Us For More Information :
Visit : www.icertglobal.com Email : info@icertglobal.com
Read More
In today's fast-paced and competitive business environment, companies are constantly looking for ways to improve their operations and stay ahead of the curve. One key technology that is revolutionizing the way organizations manage quality is artificial intelligence (AI). By leveraging AI, companies can streamline their quality management systems, enhance efficiency, and drive innovation like never before.
How Does Artificial Intelligence Impact Quality Management Systems?
-
Automation: AI enables the automation of repetitive tasks and processes in quality management systems, freeing up employees to focus on more strategic initiatives.
-
Data Analysis: With AI-powered analytics tools, businesses can gather and analyze vast amounts of data to identify trends, patterns, and anomalies in quality metrics.
-
Machine Learning: AI algorithms can learn from data and improve over time, allowing quality management systems to become more accurate and efficient.
-
Optimization: By utilizing AI, organizations can optimize their quality control processes and make real-time adjustments to ensure product quality.
The Advantages of Integrating AI into Quality Management Systems
-
Performance: AI can enhance the overall performance of quality management systems by maximizing efficiency and minimizing errors.
-
Process Improvement: With AI, companies can identify areas for improvement in their quality management processes and make strategic changes.
-
Predictive Maintenance: AI can predict equipment failures and maintenance needs, helping companies prevent quality issues before they occur.
How AI is Transforming Quality Control
-
Risk Management: AI tools can help companies identify potential risks in their quality management systems and take proactive measures to mitigate them.
-
Productivity: By automating tasks and processes, AI can boost productivity and streamline quality control workflows.
-
Advancements: AI is driving advancements in quality management systems, leading to more innovative solutions and practices.
The Future of Quality Management Systems with AI
-
Digital Transformation: AI is at the forefront of digital transformation, reshaping the way companies approach quality management.
-
Sustainability: By improving efficiency and reducing waste, AI can help companies achieve sustainability goals in their quality management processes.
-
Workflow: AI can optimize workflows and streamline quality control procedures, making operations more seamless and efficient.
Benefits of AI in Quality Management Systems
-
Smart Solutions: AI offers smart solutions for quality management, enabling companies to make data-driven decisions and enhance quality assurance.
-
Business Intelligence: With AI-powered tools, companies can gain valuable insights into their quality metrics and make informed decisions.
-
Best Practices: AI can help organizations establish and maintain best practices in quality management, ensuring consistent product quality.
How to obtain Quality Management Certification?
We are an Education Technology company providing certification training courses to accelerate careers of working professionals worldwide. We impart training through instructor-led classroom workshops, instructor-led live virtual training sessions, and self-paced e-learning courses.
We have successfully conducted training sessions in 108 countries across the globe and enabled thousands of working professionals to enhance the scope of their careers.
Our enterprise training portfolio includes in-demand and globally recognized certification training courses in Project Management, Quality Management, Business Analysis, IT Service Management, Agile and Scrum, Cyber Security, Data Science, and Emerging Technologies. Download our Enterprise Training Catalog from https://www.icertglobal.com/corporate-training-for-enterprises.php.
Popular Courses include:
-
Project Management: PMP, CAPM ,PMI RMP
-
Quality Management: Six Sigma Black Belt ,Lean Six Sigma Green Belt, Lean Management, Minitab,CMMI
-
Business Analysis: CBAP, CCBA, ECBA
-
Agile Training: PMI-ACP , CSM , CSPO
-
Scrum Training: CSM
-
DevOps
-
Program Management: PgMP
-
Cloud Technology: Exin Cloud Computing
-
Citrix Client Adminisration: Citrix Cloud Administration
The 10 top-paying certifications to target in 2024 are:
Conclusion
In conclusion, the impact of artificial intelligence on quality management systems is undeniable. By leveraging AI technology, companies can improve efficiency, drive innovation, and enhance overall quality control processes. As AI continues to evolve, the possibilities for quality management systems are endless, opening up new opportunities for companies to achieve operational excellence and deliver high-quality products and services to their customers.
Contact Us For More Information :
Visit : www.icertglobal.com Email : info@icertglobal.com
The Importance of Leadership in Quality Management Practices
In the world of quality management, leadership plays a crucial role in ensuring that organizations meet their quality goals and deliver exceptional products and services to customers. Effective leadership in quality management is essential for creating a culture of accountability, continuous improvement, and innovation. Leaders in quality management must possess certain qualities and skills to drive success in their organization's quality initiatives.
Importance of Leadership in Quality
Leadership in quality management is vital for setting the vision, goals, and direction for the organization's quality programs. Good leadership can inspire teams to strive for excellence and consistently meet quality standards. Without strong leadership, quality management programs may lack direction, motivation, and oversight, leading to subpar results and customer satisfaction.
Leadership Qualities for Quality Management
Effective leaders in quality management exhibit certain key qualities that set them apart from others. These qualities include strong communication skills, a results-driven mindset, the ability to empower and inspire others, strategic thinking, and a commitment to continuous learning and improvement. Leaders must also be able to make tough decisions, prioritize tasks effectively, and build strong relationships with their teams.
Effective Leadership in Quality
Effective leadership in quality management involves setting clear goals and expectations, providing support and resources to team members, and holding everyone accountable for their performance. Leaders must create a positive work environment where employees feel motivated and engaged in their work. By fostering a culture of quality and continuous improvement, leaders can drive success in their organization's quality management efforts.
Leadership Role in Quality Assurance
Quality assurance is a critical aspect of quality management, and leaders play a significant role in ensuring that QA processes are effective and efficient. Leaders must establish quality standards, develop QA procedures, monitor performance metrics, and implement corrective actions when necessary. By championing quality assurance initiatives, leaders can demonstrate their commitment to delivering high-quality products and services to customers.
Quality Management and Leadership
Quality management and leadership go hand in hand, as effective leadership is essential for implementing and sustaining quality management systems. Leaders must be proactive in identifying opportunities for improvement, addressing quality issues, and promoting a culture of quality throughout the organization. By providing guidance, support, and resources, leaders can help their teams achieve excellence in quality management.
Leadership Skills in Quality Control
Leadership skills in quality control involve the ability to analyze data, identify trends, and make informed decisions based on quality indicators. Leaders must be able to lead cross-functional teams, coordinate quality control activities, and drive continuous improvement initiatives. By fostering collaboration and communication among team members, leaders can ensure that quality control processes are effective and efficient.
Leadership Impact on Quality
The impact of leadership on quality is profound, as leaders set the tone for the organization's quality culture and performance. Strong leadership can inspire employees to strive for excellence, take ownership of quality initiatives, and deliver exceptional results. By leading by example and demonstrating a commitment to quality, leaders can positively influence the organization's overall quality performance.
How to obtain Quality Management certification?
We are an Education Technology company providing certification training courses to accelerate careers of working professionals worldwide. We impart training through instructor-led classroom workshops, instructor-led live virtual training sessions, and self-paced e-learning courses.
We have successfully conducted training sessions in 108 countries across the globe and enabled thousands of working professionals to enhance the scope of their careers.
Our enterprise training portfolio includes in-demand and globally recognized certification training courses in Project Management, Quality Management, Business Analysis, IT Service Management, Agile and Scrum, Cyber Security, Data Science, and Emerging Technologies. Download our Enterprise Training Catalog from https://www.icertglobal.com/corporate-training-for-enterprises.php and https://www.icertglobal.com/index.php
Popular Courses include:
-
Project Management: PMP, CAPM ,PMI RMP
-
Quality Management: Six Sigma Black Belt ,Lean Six Sigma Green Belt, Lean Management, Minitab,CMMI
-
Business Analysis: CBAP, CCBA, ECBA
-
Agile Training: PMI-ACP , CSM , CSPO
-
Scrum Training: CSM
-
DevOps
-
Program Management: PgMP
-
Cloud Technology: Exin Cloud Computing
-
Citrix Client Adminisration: Citrix Cloud Administration
The 10 top-paying certifications to target in 2024 are:
Conclusion
In conclusion, leadership plays a critical role in quality management, driving success, and sustainable results in organizations. Effective leaders in quality management must possess the right qualities, skills, and competencies to inspire, empower, and align teams towards achieving quality goals. By investing in leadership development, fostering a culture of quality, and promoting ethical leadership practices, organizations can enhance their quality management efforts and deliver exceptional products and services to customers.
Contact Us For More Information :
Visit : www.icertglobal.com Email : info@icertglobal.com
Read More
In the world of quality management, leadership plays a crucial role in ensuring that organizations meet their quality goals and deliver exceptional products and services to customers. Effective leadership in quality management is essential for creating a culture of accountability, continuous improvement, and innovation. Leaders in quality management must possess certain qualities and skills to drive success in their organization's quality initiatives.
Importance of Leadership in Quality
Leadership in quality management is vital for setting the vision, goals, and direction for the organization's quality programs. Good leadership can inspire teams to strive for excellence and consistently meet quality standards. Without strong leadership, quality management programs may lack direction, motivation, and oversight, leading to subpar results and customer satisfaction.
Leadership Qualities for Quality Management
Effective leaders in quality management exhibit certain key qualities that set them apart from others. These qualities include strong communication skills, a results-driven mindset, the ability to empower and inspire others, strategic thinking, and a commitment to continuous learning and improvement. Leaders must also be able to make tough decisions, prioritize tasks effectively, and build strong relationships with their teams.
Effective Leadership in Quality
Effective leadership in quality management involves setting clear goals and expectations, providing support and resources to team members, and holding everyone accountable for their performance. Leaders must create a positive work environment where employees feel motivated and engaged in their work. By fostering a culture of quality and continuous improvement, leaders can drive success in their organization's quality management efforts.
Leadership Role in Quality Assurance
Quality assurance is a critical aspect of quality management, and leaders play a significant role in ensuring that QA processes are effective and efficient. Leaders must establish quality standards, develop QA procedures, monitor performance metrics, and implement corrective actions when necessary. By championing quality assurance initiatives, leaders can demonstrate their commitment to delivering high-quality products and services to customers.
Quality Management and Leadership
Quality management and leadership go hand in hand, as effective leadership is essential for implementing and sustaining quality management systems. Leaders must be proactive in identifying opportunities for improvement, addressing quality issues, and promoting a culture of quality throughout the organization. By providing guidance, support, and resources, leaders can help their teams achieve excellence in quality management.
Leadership Skills in Quality Control
Leadership skills in quality control involve the ability to analyze data, identify trends, and make informed decisions based on quality indicators. Leaders must be able to lead cross-functional teams, coordinate quality control activities, and drive continuous improvement initiatives. By fostering collaboration and communication among team members, leaders can ensure that quality control processes are effective and efficient.
Leadership Impact on Quality
The impact of leadership on quality is profound, as leaders set the tone for the organization's quality culture and performance. Strong leadership can inspire employees to strive for excellence, take ownership of quality initiatives, and deliver exceptional results. By leading by example and demonstrating a commitment to quality, leaders can positively influence the organization's overall quality performance.
How to obtain Quality Management certification?
We are an Education Technology company providing certification training courses to accelerate careers of working professionals worldwide. We impart training through instructor-led classroom workshops, instructor-led live virtual training sessions, and self-paced e-learning courses.
We have successfully conducted training sessions in 108 countries across the globe and enabled thousands of working professionals to enhance the scope of their careers.
Our enterprise training portfolio includes in-demand and globally recognized certification training courses in Project Management, Quality Management, Business Analysis, IT Service Management, Agile and Scrum, Cyber Security, Data Science, and Emerging Technologies. Download our Enterprise Training Catalog from https://www.icertglobal.com/corporate-training-for-enterprises.php and https://www.icertglobal.com/index.php
Popular Courses include:
-
Project Management: PMP, CAPM ,PMI RMP
-
Quality Management: Six Sigma Black Belt ,Lean Six Sigma Green Belt, Lean Management, Minitab,CMMI
-
Business Analysis: CBAP, CCBA, ECBA
-
Agile Training: PMI-ACP , CSM , CSPO
-
Scrum Training: CSM
-
DevOps
-
Program Management: PgMP
-
Cloud Technology: Exin Cloud Computing
-
Citrix Client Adminisration: Citrix Cloud Administration
The 10 top-paying certifications to target in 2024 are:
Conclusion
In conclusion, leadership plays a critical role in quality management, driving success, and sustainable results in organizations. Effective leaders in quality management must possess the right qualities, skills, and competencies to inspire, empower, and align teams towards achieving quality goals. By investing in leadership development, fostering a culture of quality, and promoting ethical leadership practices, organizations can enhance their quality management efforts and deliver exceptional products and services to customers.
Contact Us For More Information :
Visit : www.icertglobal.com Email : info@icertglobal.com
Lean Leadership: Inspiring and Empowering Teams for Success
In today's fast-paced business environment, effective leadership is crucial to driving team performance and achieving organizational success. Lean leadership, a management approach based on the principles of lean thinking, focuses on continuous improvement, waste reduction, and maximizing value for customers. By inspiring and empowering teams, lean leaders can create a culture of collaboration, innovation, and success. In this article, we will explore how lean leadership can help organizations achieve their goals by motivating and empowering their teams.
What is lean leadership?
Lean leadership is a leadership style that emphasizes empowering employees, fostering a culture of continuous improvement, and eliminating waste in all forms. Lean leaders focus on developing their team members' skills and capabilities, encouraging them to take ownership of their work and contribute to the organization's success. By creating a culture of trust, collaboration, and respect, lean leaders inspire their teams to strive for excellence and drive positive change within the organization.
How Does Lean Leadership Inspire Teams?
Lean leaders inspire teams by setting clear goals, providing support and guidance, and leading by example. They encourage open communication, transparency, and a spirit of continuous learning and improvement. By recognizing and celebrating achievements, lean leaders motivate their teams to go above and beyond in their work. They also empower team members to make decisions and take calculated risks, fostering a sense of ownership and accountability within the team.
The Importance of Empowering Teams
Empowering teams is essential for driving innovation, creativity, and high performance. When team members feel empowered to make decisions, take risks, and contribute their unique perspectives, they are more likely to be engaged, motivated, and productive. Empowered teams are also better equipped to handle challenges, adapt to change, and overcome obstacles. By giving teams the autonomy and resources they need to succeed, leaders can unleash their full potential and drive organizational success.
Lean Leadership Strategies for Empowering Teams
There are several key strategies that lean leaders can use to empower their teams and drive success:
-
Build Trust: Trust is the foundation of any successful team. Lean leaders should establish trust by being honest, transparent, and reliable in their interactions with team members.
-
Provide Support: Lean leaders should provide the necessary resources, tools, and training to help team members succeed. They should also offer guidance, feedback, and coaching to support individual growth and development.
-
Encourage Collaboration: Collaboration is key to driving innovation and problem-solving. Lean leaders should create opportunities for team members to work together, share ideas, and leverage each other's strengths.
-
Celebrate Success: Recognizing and celebrating achievements is essential for boosting team morale and motivation. Lean leaders should acknowledge and reward team members for their hard work and contributions.
By implementing these strategies and adopting a lean leadership mindset, organizations can inspire and empower their teams to achieve greater levels of success. With the right leadership skills, a strong lean culture, and a focus on continuous improvement, teams can overcome challenges, drive innovation, and deliver exceptional results.
How to obtain Lean Management Certification?
We are an Education Technology company providing certification training courses to accelerate careers of working professionals worldwide. We impart training through instructor-led classroom workshops, instructor-led live virtual training sessions, and self-paced e-learning courses.
We have successfully conducted training sessions in 108 countries across the globe and enabled thousands of working professionals to enhance the scope of their careers.
Our enterprise training portfolio includes in-demand and globally recognized certification training courses in Project Management, Quality Management, Business Analysis, IT Service Management, Agile and Scrum, Cyber Security, Data Science, and Emerging Technologies. Download our Enterprise Training Catalog from https://www.icertglobal.com/corporate-training-for-enterprises.php
Popular Courses include:
-
Project Management: PMP, CAPM ,PMI RMP
-
Quality Management: Six Sigma Black Belt ,Lean Six Sigma Green Belt, Lean Management, Minitab,CMMI
-
Business Analysis: CBAP, CCBA, ECBA
-
Agile Training: PMI-ACP , CSM , CSPO
-
Scrum Training: CSM
-
DevOps
-
Program Management: PgMP
-
Cloud Technology: Exin Cloud Computing
-
Citrix Client Adminisration: Citrix Cloud Administration
The 10 top-paying certifications to target in 2024 are:
Conclusion
In conclusion, lean leadership is a powerful approach to inspiring and empowering teams for success. By focusing on developing strong leadership skills, fostering a culture of collaboration and continuous improvement, and empowering team members to take ownership of their work, organizations can drive innovation, achieve their goals, and thrive in today's competitive business landscape.
Read More
In today's fast-paced business environment, effective leadership is crucial to driving team performance and achieving organizational success. Lean leadership, a management approach based on the principles of lean thinking, focuses on continuous improvement, waste reduction, and maximizing value for customers. By inspiring and empowering teams, lean leaders can create a culture of collaboration, innovation, and success. In this article, we will explore how lean leadership can help organizations achieve their goals by motivating and empowering their teams.
What is lean leadership?
Lean leadership is a leadership style that emphasizes empowering employees, fostering a culture of continuous improvement, and eliminating waste in all forms. Lean leaders focus on developing their team members' skills and capabilities, encouraging them to take ownership of their work and contribute to the organization's success. By creating a culture of trust, collaboration, and respect, lean leaders inspire their teams to strive for excellence and drive positive change within the organization.
How Does Lean Leadership Inspire Teams?
Lean leaders inspire teams by setting clear goals, providing support and guidance, and leading by example. They encourage open communication, transparency, and a spirit of continuous learning and improvement. By recognizing and celebrating achievements, lean leaders motivate their teams to go above and beyond in their work. They also empower team members to make decisions and take calculated risks, fostering a sense of ownership and accountability within the team.
The Importance of Empowering Teams
Empowering teams is essential for driving innovation, creativity, and high performance. When team members feel empowered to make decisions, take risks, and contribute their unique perspectives, they are more likely to be engaged, motivated, and productive. Empowered teams are also better equipped to handle challenges, adapt to change, and overcome obstacles. By giving teams the autonomy and resources they need to succeed, leaders can unleash their full potential and drive organizational success.
Lean Leadership Strategies for Empowering Teams
There are several key strategies that lean leaders can use to empower their teams and drive success:
-
Build Trust: Trust is the foundation of any successful team. Lean leaders should establish trust by being honest, transparent, and reliable in their interactions with team members.
-
Provide Support: Lean leaders should provide the necessary resources, tools, and training to help team members succeed. They should also offer guidance, feedback, and coaching to support individual growth and development.
-
Encourage Collaboration: Collaboration is key to driving innovation and problem-solving. Lean leaders should create opportunities for team members to work together, share ideas, and leverage each other's strengths.
-
Celebrate Success: Recognizing and celebrating achievements is essential for boosting team morale and motivation. Lean leaders should acknowledge and reward team members for their hard work and contributions.
By implementing these strategies and adopting a lean leadership mindset, organizations can inspire and empower their teams to achieve greater levels of success. With the right leadership skills, a strong lean culture, and a focus on continuous improvement, teams can overcome challenges, drive innovation, and deliver exceptional results.
How to obtain Lean Management Certification?
We are an Education Technology company providing certification training courses to accelerate careers of working professionals worldwide. We impart training through instructor-led classroom workshops, instructor-led live virtual training sessions, and self-paced e-learning courses.
We have successfully conducted training sessions in 108 countries across the globe and enabled thousands of working professionals to enhance the scope of their careers.
Our enterprise training portfolio includes in-demand and globally recognized certification training courses in Project Management, Quality Management, Business Analysis, IT Service Management, Agile and Scrum, Cyber Security, Data Science, and Emerging Technologies. Download our Enterprise Training Catalog from https://www.icertglobal.com/corporate-training-for-enterprises.php
Popular Courses include:
-
Project Management: PMP, CAPM ,PMI RMP
-
Quality Management: Six Sigma Black Belt ,Lean Six Sigma Green Belt, Lean Management, Minitab,CMMI
-
Business Analysis: CBAP, CCBA, ECBA
-
Agile Training: PMI-ACP , CSM , CSPO
-
Scrum Training: CSM
-
DevOps
-
Program Management: PgMP
-
Cloud Technology: Exin Cloud Computing
-
Citrix Client Adminisration: Citrix Cloud Administration
The 10 top-paying certifications to target in 2024 are:
Conclusion
In conclusion, lean leadership is a powerful approach to inspiring and empowering teams for success. By focusing on developing strong leadership skills, fostering a culture of collaboration and continuous improvement, and empowering team members to take ownership of their work, organizations can drive innovation, achieve their goals, and thrive in today's competitive business landscape.
Integrating CMMI with ISO, Six Sigma & Other Quality Models
In today's fast-paced and highly competitive business environment, organizations are constantly seeking ways to improve their processes, enhance product quality, and increase customer satisfaction. One of the most effective ways to achieve these goals is by integrating different quality models such as CMMI, ISO, and Six Sigma. By combining the strengths of each model, companies can create a robust quality management system that is tailored to their specific needs and requirements.
CMMI and ISO: A Comparison
Both CMMI (Capability Maturity Model Integration) and ISO (International Organization for Standardization) are widely used quality models that provide guidelines for improving processes and ensuring product quality. While CMMI focuses on process improvement and organizational maturity, ISO standards are more focused on setting standards for quality management systems.
Are CMMI and ISO compatible?
Yes, CMMI and ISO can be compatible and complementary. Many companies have successfully integrated both models to create a more comprehensive quality management system that addresses both process improvement and compliance with international standards.
CMMI and Six Sigma: Finding Common Ground
Six Sigma is another popular quality improvement methodology that focuses on reducing defects and variations in processes. While CMMI and Six Sigma have different approaches, they can be aligned to achieve common goals such as improving product quality and customer satisfaction.
How can CMMI and Six Sigma be integrated?
By combining the process improvement capabilities of CMMI with the statistical tools and methodologies of Six Sigma, companies can create a powerful quality management system that is capable of driving continuous improvement and enhancing efficiency.
Integrating CMMI with Other Quality Models
In addition to ISO and Six Sigma, there are other quality models that can be integrated with CMMI to further enhance the effectiveness of a company's quality management system. These may include Lean, TQM (Total Quality Management), and Agile methodologies.
What are the benefits of integrating multiple quality models?
By integrating multiple quality models, companies can leverage the strengths of each model and tailor their quality management system to meet the specific needs and requirements of their organization. This can result in improved process efficiency, higher product quality, and increased customer satisfaction.
How to obtain CMMI Certification?
We are an Education Technology company providing certification training courses to accelerate careers of working professionals worldwide. We impart training through instructor-led classroom workshops, instructor-led live virtual training sessions, and self-paced e-learning courses.
We have successfully conducted training sessions in 108 countries across the globe and enabled thousands of working professionals to enhance the scope of their careers.
Our enterprise training portfolio includes in-demand and globally recognized certification training courses in Project Management, Quality Management, Business Analysis, IT Service Management, Agile and Scrum, Cyber Security, Data Science, and Emerging Technologies. Download our Enterprise Training Catalog from https://www.icertglobal.com/corporate-training-for-enterprises.php
Popular Courses include:
-
Project Management: PMP, CAPM ,PMI RMP
-
Quality Management: Six Sigma Black Belt ,Lean Six Sigma Green Belt, Lean Management, Minitab,CMMI
-
Business Analysis: CBAP, CCBA, ECBA
-
Agile Training: PMI-ACP , CSM , CSPO
-
Scrum Training: CSM
-
DevOps
-
Program Management: PgMP
-
Cloud Technology: Exin Cloud Computing
-
Citrix Client Adminisration: Citrix Cloud Administration
The 10 top-paying certifications to target in 2024 are:
Conclusion
In conclusion, integrating CMMI with other quality models such as ISO, Six Sigma, and more can provide companies with a comprehensive and robust quality management system that drives continuous improvement and ensures customer satisfaction. By combining the strengths of different models and methodologies, companies can create a tailored approach to quality management that meets their unique business needs. So, don't hesitate to explore the possibilities of integrating CMMI with other quality models to take your organization's quality management to the next level.
Read More
In today's fast-paced and highly competitive business environment, organizations are constantly seeking ways to improve their processes, enhance product quality, and increase customer satisfaction. One of the most effective ways to achieve these goals is by integrating different quality models such as CMMI, ISO, and Six Sigma. By combining the strengths of each model, companies can create a robust quality management system that is tailored to their specific needs and requirements.
CMMI and ISO: A Comparison
Both CMMI (Capability Maturity Model Integration) and ISO (International Organization for Standardization) are widely used quality models that provide guidelines for improving processes and ensuring product quality. While CMMI focuses on process improvement and organizational maturity, ISO standards are more focused on setting standards for quality management systems.
Are CMMI and ISO compatible?
Yes, CMMI and ISO can be compatible and complementary. Many companies have successfully integrated both models to create a more comprehensive quality management system that addresses both process improvement and compliance with international standards.
CMMI and Six Sigma: Finding Common Ground
Six Sigma is another popular quality improvement methodology that focuses on reducing defects and variations in processes. While CMMI and Six Sigma have different approaches, they can be aligned to achieve common goals such as improving product quality and customer satisfaction.
How can CMMI and Six Sigma be integrated?
By combining the process improvement capabilities of CMMI with the statistical tools and methodologies of Six Sigma, companies can create a powerful quality management system that is capable of driving continuous improvement and enhancing efficiency.
Integrating CMMI with Other Quality Models
In addition to ISO and Six Sigma, there are other quality models that can be integrated with CMMI to further enhance the effectiveness of a company's quality management system. These may include Lean, TQM (Total Quality Management), and Agile methodologies.
What are the benefits of integrating multiple quality models?
By integrating multiple quality models, companies can leverage the strengths of each model and tailor their quality management system to meet the specific needs and requirements of their organization. This can result in improved process efficiency, higher product quality, and increased customer satisfaction.
How to obtain CMMI Certification?
We are an Education Technology company providing certification training courses to accelerate careers of working professionals worldwide. We impart training through instructor-led classroom workshops, instructor-led live virtual training sessions, and self-paced e-learning courses.
We have successfully conducted training sessions in 108 countries across the globe and enabled thousands of working professionals to enhance the scope of their careers.
Our enterprise training portfolio includes in-demand and globally recognized certification training courses in Project Management, Quality Management, Business Analysis, IT Service Management, Agile and Scrum, Cyber Security, Data Science, and Emerging Technologies. Download our Enterprise Training Catalog from https://www.icertglobal.com/corporate-training-for-enterprises.php
Popular Courses include:
-
Project Management: PMP, CAPM ,PMI RMP
-
Quality Management: Six Sigma Black Belt ,Lean Six Sigma Green Belt, Lean Management, Minitab,CMMI
-
Business Analysis: CBAP, CCBA, ECBA
-
Agile Training: PMI-ACP , CSM , CSPO
-
Scrum Training: CSM
-
DevOps
-
Program Management: PgMP
-
Cloud Technology: Exin Cloud Computing
-
Citrix Client Adminisration: Citrix Cloud Administration
The 10 top-paying certifications to target in 2024 are:
Conclusion
In conclusion, integrating CMMI with other quality models such as ISO, Six Sigma, and more can provide companies with a comprehensive and robust quality management system that drives continuous improvement and ensures customer satisfaction. By combining the strengths of different models and methodologies, companies can create a tailored approach to quality management that meets their unique business needs. So, don't hesitate to explore the possibilities of integrating CMMI with other quality models to take your organization's quality management to the next level.
Improve Software Dev Processes with CMMI: Your Guide Today
In the fast-paced world of software development, efficiency and quality are essential to staying competitive. One proven method for enhancing software development processes is by utilizing the Capability Maturity Model Integration (CMMI). By leveraging CMMI best practices, businesses can streamline their processes, improve productivity, and deliver higher quality software products. Let's delve into how organizations can use CMMI to enhance their software development processes and ultimately achieve better results.
What is CMMI?
Capability Maturity Model Integration, or CMMI, is a framework that helps organizations improve their processes by establishing benchmarks for best practices in various areas such as project management, quality assurance, and software engineering. CMMI provides a roadmap for organizations to follow in order to enhance their capabilities and achieve greater levels of maturity in key business processes.
How can CMMI benefit software development processes?
CMMI can bring numerous benefits to software development processes. By implementing CMMI best practices, organizations can achieve the following:
-
Continuous Improvement: CMMI encourages a culture of continuous improvement, where organizations strive to refine their processes over time.
-
Efficiency: By following CMMI guidelines, organizations can streamline their workflows and eliminate inefficiencies, leading to greater productivity.
-
Agile Methodologies: CMMI aligns well with agile methodologies, allowing organizations to adapt quickly to changing requirements and deliver software more efficiently.
-
Quality Management: CMMI emphasizes the importance of quality throughout the software development lifecycle, leading to higher-quality end products.
-
Organizational Performance: By improving processes and efficiency, organizations can enhance their overall performance and achieve better results.
Understanding CMMI Levels
CMMI consists of five maturity levels, each representing a different stage of process maturity. The levels are as follows:
-
Initial: Organizations at this level have ad-hoc processes that are often chaotic and unpredictable.
-
Managed: Processes are documented and followed at this level, but they may still be somewhat reactive.
-
Defined: Processes are well-defined and standardized at this level, leading to more predictable outcomes.
-
Quantitatively Managed: Organizations at this level focus on quantitatively measuring their processes for better performance.
-
Optimizing: This is the highest level of maturity, where organizations continuously improve their processes to achieve optimal results.
Implementing CMMI in Software Development
To implement CMMI in software development processes, organizations can follow these key steps:
-
Perform Measurement and Analysis: Collect data on existing processes to identify areas for improvement.
-
Enhance Processes: Use CMMI best practices to optimize workflows and enhance the quality of software development.
-
Optimize Quality Standards: Implement quality assurance measures to ensure that software products meet high standards.
-
Collaborate as a Team: Promote collaboration and communication among team members to foster innovation and efficiency.
-
Optimize the Software Development Lifecycle: Streamline the software development lifecycle to deliver products more quickly and efficiently.
By incorporating CMMI into their software development processes, organizations can achieve greater efficiency, quality, and performance. With a focus on continuous improvement and best practices, CMMI provides a solid framework for enhancing software development processes and driving better outcomes. So, are you ready to take your software development processes to the next level with CMMI?
How to obtain CMMI Certification?
We are an Education Technology company providing certification training courses to accelerate careers of working professionals worldwide. We impart training through instructor-led classroom workshops, instructor-led live virtual training sessions, and self-paced e-learning courses.
We have successfully conducted training sessions in 108 countries across the globe and enabled thousands of working professionals to enhance the scope of their careers.
Our enterprise training portfolio includes in-demand and globally recognized certification training courses in Project Management, Quality Management, Business Analysis, IT Service Management, Agile and Scrum, Cyber Security, Data Science, and Emerging Technologies. Download our Enterprise Training Catalog from https://www.icertglobal.com/corporate-training-for-enterprises.php
Popular Courses include:
-
Project Management: PMP, CAPM ,PMI RMP
-
Quality Management: Six Sigma Black Belt ,Lean Six Sigma Green Belt, Lean Management, Minitab,CMMI
-
Business Analysis: CBAP, CCBA, ECBA
-
Agile Training: PMI-ACP , CSM , CSPO
-
Scrum Training: CSM
-
DevOps
-
Program Management: PgMP
-
Cloud Technology: Exin Cloud Computing
-
Citrix Client Adminisration: Citrix Cloud Administration
The 10 top-paying certifications to target in 2024 are:
Conclusion
In conclusion, CMMI is a powerful tool for businesses looking to improve their software development processes. By following CMMI best practices and striving for greater maturity levels, organizations can enhance their efficiency, quality, and overall performance. With a focus on continuous improvement and collaboration, CMMI offers a roadmap for success in the fast-paced world of software development.
Read More
In the fast-paced world of software development, efficiency and quality are essential to staying competitive. One proven method for enhancing software development processes is by utilizing the Capability Maturity Model Integration (CMMI). By leveraging CMMI best practices, businesses can streamline their processes, improve productivity, and deliver higher quality software products. Let's delve into how organizations can use CMMI to enhance their software development processes and ultimately achieve better results.
What is CMMI?
Capability Maturity Model Integration, or CMMI, is a framework that helps organizations improve their processes by establishing benchmarks for best practices in various areas such as project management, quality assurance, and software engineering. CMMI provides a roadmap for organizations to follow in order to enhance their capabilities and achieve greater levels of maturity in key business processes.
How can CMMI benefit software development processes?
CMMI can bring numerous benefits to software development processes. By implementing CMMI best practices, organizations can achieve the following:
-
Continuous Improvement: CMMI encourages a culture of continuous improvement, where organizations strive to refine their processes over time.
-
Efficiency: By following CMMI guidelines, organizations can streamline their workflows and eliminate inefficiencies, leading to greater productivity.
-
Agile Methodologies: CMMI aligns well with agile methodologies, allowing organizations to adapt quickly to changing requirements and deliver software more efficiently.
-
Quality Management: CMMI emphasizes the importance of quality throughout the software development lifecycle, leading to higher-quality end products.
-
Organizational Performance: By improving processes and efficiency, organizations can enhance their overall performance and achieve better results.
Understanding CMMI Levels
CMMI consists of five maturity levels, each representing a different stage of process maturity. The levels are as follows:
-
Initial: Organizations at this level have ad-hoc processes that are often chaotic and unpredictable.
-
Managed: Processes are documented and followed at this level, but they may still be somewhat reactive.
-
Defined: Processes are well-defined and standardized at this level, leading to more predictable outcomes.
-
Quantitatively Managed: Organizations at this level focus on quantitatively measuring their processes for better performance.
-
Optimizing: This is the highest level of maturity, where organizations continuously improve their processes to achieve optimal results.
Implementing CMMI in Software Development
To implement CMMI in software development processes, organizations can follow these key steps:
-
Perform Measurement and Analysis: Collect data on existing processes to identify areas for improvement.
-
Enhance Processes: Use CMMI best practices to optimize workflows and enhance the quality of software development.
-
Optimize Quality Standards: Implement quality assurance measures to ensure that software products meet high standards.
-
Collaborate as a Team: Promote collaboration and communication among team members to foster innovation and efficiency.
-
Optimize the Software Development Lifecycle: Streamline the software development lifecycle to deliver products more quickly and efficiently.
By incorporating CMMI into their software development processes, organizations can achieve greater efficiency, quality, and performance. With a focus on continuous improvement and best practices, CMMI provides a solid framework for enhancing software development processes and driving better outcomes. So, are you ready to take your software development processes to the next level with CMMI?
How to obtain CMMI Certification?
We are an Education Technology company providing certification training courses to accelerate careers of working professionals worldwide. We impart training through instructor-led classroom workshops, instructor-led live virtual training sessions, and self-paced e-learning courses.
We have successfully conducted training sessions in 108 countries across the globe and enabled thousands of working professionals to enhance the scope of their careers.
Our enterprise training portfolio includes in-demand and globally recognized certification training courses in Project Management, Quality Management, Business Analysis, IT Service Management, Agile and Scrum, Cyber Security, Data Science, and Emerging Technologies. Download our Enterprise Training Catalog from https://www.icertglobal.com/corporate-training-for-enterprises.php
Popular Courses include:
-
Project Management: PMP, CAPM ,PMI RMP
-
Quality Management: Six Sigma Black Belt ,Lean Six Sigma Green Belt, Lean Management, Minitab,CMMI
-
Business Analysis: CBAP, CCBA, ECBA
-
Agile Training: PMI-ACP , CSM , CSPO
-
Scrum Training: CSM
-
DevOps
-
Program Management: PgMP
-
Cloud Technology: Exin Cloud Computing
-
Citrix Client Adminisration: Citrix Cloud Administration
The 10 top-paying certifications to target in 2024 are:
Conclusion
In conclusion, CMMI is a powerful tool for businesses looking to improve their software development processes. By following CMMI best practices and striving for greater maturity levels, organizations can enhance their efficiency, quality, and overall performance. With a focus on continuous improvement and collaboration, CMMI offers a roadmap for success in the fast-paced world of software development.
The Future of Software Testing: How CTFL Fits In Today! 2.0
In today's fast-paced and constantly evolving technology landscape, the future of software testing is more critical than ever. As software continues to play a vital role in our daily lives, the need for efficient and reliable testing processes has become paramount. This is where the Certified Tester Foundation Level (CTFL) certification comes in.
The Importance of Software Testing in Today's World
Software testing is an essential component of the software development lifecycle. It ensures that the final product meets the desired quality standards, functions as intended, and is free of defects. Without proper testing, software projects can result in costly errors, delays, and ultimately, dissatisfied users.
What is CTFL and Why is it Important?
CTFL is a certification designed for software testers who want to demonstrate their knowledge and skills in testing processes, agile testing, quality assurance, and more. By obtaining a CTFL certification, professionals can showcase their expertise in the field and enhance their career opportunities.
Benefits of CTFL Certification
- Demonstrates mastery of testing methodologies and best practices
- Enhances credibility and trustworthiness in the software industry
- Opens doors for career advancement and higher-paying opportunities
- Equips professionals with the skills needed to excel in software testing roles
How CTFL Fits into the Software Development Lifecycle
CTFL plays a crucial role in ensuring the quality and reliability of software products. From test automation to test management, CTFL-certified professionals are well-versed in the latest tools and techniques needed to execute effective testing strategies throughout the software lifecycle.
When it comes to continuous testing and innovation in testing, CTFL certification provides professionals with the knowledge and expertise needed to stay ahead of the curve. By keeping up with the latest trends and advancements in the industry, CTFL-certified individuals can contribute to the success of software projects and drive digital transformation.
CTFL Training and Syllabus
To obtain a CTFL certification, professionals must undergo rigorous training and preparation. The CTFL course covers a wide range of topics, including test cases, test strategy, software quality, and more. By mastering these key concepts, individuals can enhance their testing skills and become valuable assets to their organizations.
How to obtain CTFL Certification?
We are an Education Technology company providing certification training courses to accelerate careers of working professionals worldwide. We impart training through instructor-led classroom workshops, instructor-led live virtual training sessions, and self-paced e-learning courses.
We have successfully conducted training sessions in 108 countries across the globe and enabled thousands of working professionals to enhance the scope of their careers.
Our enterprise training portfolio includes in-demand and globally recognized certification training courses in Project Management, Quality Management, Business Analysis, IT Service Management, Agile and Scrum, Cyber Security, Data Science, and Emerging Technologies. Download our Enterprise Training Catalog from https://www.icertglobal.com/corporate-training-for-enterprises.php
Popular Courses include:
- Project Management: PMP, CAPM ,PMI RMP
- Quality Management: Six Sigma Black Belt ,Lean Six Sigma Green Belt, Lean Management, Minitab,CMMI
- Business Analysis: CBAP, CCBA, ECBA
- Agile Training: PMI-ACP , CSM , CSPO
- Scrum Training: CSM
- DevOps
- Program Management: PgMP
- Cloud Technology: Exin Cloud Computing
- Citrix Client Adminisration: Citrix Cloud Administration
The 10 top-paying certifications to target in 2024 are:
- Certified Information Systems Security Professional® (CISSP)
- AWS Certified Solutions Architect
- Google Certified Professional Cloud Architect
- Big Data Certification
- Data Science Certification
- Certified In Risk And Information Systems Control (CRISC)
- Certified Information Security Manager(CISM)
- Project Management Professional (PMP)® Certification
- Certified Ethical Hacker (CEH)
- Certified Scrum Master (CSM)
Conclusion
In conclusion, the future of software testing relies heavily on qualified and skilled professionals who can effectively navigate the complexities of the industry. With CTFL certification, software testers can set themselves apart from the competition and position themselves as leaders in the field. It's time to invest in your future and take your software testing career to the next level with CTFL.
Read More
In today's fast-paced and constantly evolving technology landscape, the future of software testing is more critical than ever. As software continues to play a vital role in our daily lives, the need for efficient and reliable testing processes has become paramount. This is where the Certified Tester Foundation Level (CTFL) certification comes in.
The Importance of Software Testing in Today's World
Software testing is an essential component of the software development lifecycle. It ensures that the final product meets the desired quality standards, functions as intended, and is free of defects. Without proper testing, software projects can result in costly errors, delays, and ultimately, dissatisfied users.
What is CTFL and Why is it Important?
CTFL is a certification designed for software testers who want to demonstrate their knowledge and skills in testing processes, agile testing, quality assurance, and more. By obtaining a CTFL certification, professionals can showcase their expertise in the field and enhance their career opportunities.
Benefits of CTFL Certification
- Demonstrates mastery of testing methodologies and best practices
- Enhances credibility and trustworthiness in the software industry
- Opens doors for career advancement and higher-paying opportunities
- Equips professionals with the skills needed to excel in software testing roles
How CTFL Fits into the Software Development Lifecycle
CTFL plays a crucial role in ensuring the quality and reliability of software products. From test automation to test management, CTFL-certified professionals are well-versed in the latest tools and techniques needed to execute effective testing strategies throughout the software lifecycle.
When it comes to continuous testing and innovation in testing, CTFL certification provides professionals with the knowledge and expertise needed to stay ahead of the curve. By keeping up with the latest trends and advancements in the industry, CTFL-certified individuals can contribute to the success of software projects and drive digital transformation.
CTFL Training and Syllabus
To obtain a CTFL certification, professionals must undergo rigorous training and preparation. The CTFL course covers a wide range of topics, including test cases, test strategy, software quality, and more. By mastering these key concepts, individuals can enhance their testing skills and become valuable assets to their organizations.
How to obtain CTFL Certification?
We are an Education Technology company providing certification training courses to accelerate careers of working professionals worldwide. We impart training through instructor-led classroom workshops, instructor-led live virtual training sessions, and self-paced e-learning courses.
We have successfully conducted training sessions in 108 countries across the globe and enabled thousands of working professionals to enhance the scope of their careers.
Our enterprise training portfolio includes in-demand and globally recognized certification training courses in Project Management, Quality Management, Business Analysis, IT Service Management, Agile and Scrum, Cyber Security, Data Science, and Emerging Technologies. Download our Enterprise Training Catalog from https://www.icertglobal.com/corporate-training-for-enterprises.php
Popular Courses include:
- Project Management: PMP, CAPM ,PMI RMP
- Quality Management: Six Sigma Black Belt ,Lean Six Sigma Green Belt, Lean Management, Minitab,CMMI
- Business Analysis: CBAP, CCBA, ECBA
- Agile Training: PMI-ACP , CSM , CSPO
- Scrum Training: CSM
- DevOps
- Program Management: PgMP
- Cloud Technology: Exin Cloud Computing
- Citrix Client Adminisration: Citrix Cloud Administration
The 10 top-paying certifications to target in 2024 are:
- Certified Information Systems Security Professional® (CISSP)
- AWS Certified Solutions Architect
- Google Certified Professional Cloud Architect
- Big Data Certification
- Data Science Certification
- Certified In Risk And Information Systems Control (CRISC)
- Certified Information Security Manager(CISM)
- Project Management Professional (PMP)® Certification
- Certified Ethical Hacker (CEH)
- Certified Scrum Master (CSM)
Conclusion
In conclusion, the future of software testing relies heavily on qualified and skilled professionals who can effectively navigate the complexities of the industry. With CTFL certification, software testers can set themselves apart from the competition and position themselves as leaders in the field. It's time to invest in your future and take your software testing career to the next level with CTFL.
5 Real-World Examples of Lean Six Sigma Green Belt Projects
In today's competitive business landscape, companies are constantly seeking ways to improve efficiency, reduce waste, and enhance quality. One proven methodology that has gained popularity in recent years is Lean Six Sigma. This powerful approach combines the principles of Lean methodology and Six Sigma to drive process improvement and problem-solving techniques within an organization.
Lean Six Sigma Green Belt projects play a crucial role in implementing Lean strategies and techniques to achieve project success. In this article, we will explore 5 real-world examples of Lean Six Sigma Green Belt projects, showcasing the impact of Lean principles on business performance and success.
Lean Six Sigma Green Belt Projects
Lean Six Sigma Green Belt projects are focused on applying data analysis and Lean tools to drive continuous improvement and waste reduction within an organization. By using the DMAIC (Define, Measure, Analyze, Improve, Control) methodology, Green Belt project teams can identify root causes of issues, implement solutions, and monitor performance metrics to ensure sustainable results.
Cost Savings through Efficiency Enhancement
One successful Lean Six Sigma Green Belt project involved a manufacturing company that was experiencing high production costs due to inefficiencies in their manufacturing process. The Green Belt project team conducted a thorough analysis using Lean tools and identified several areas for improvement. By implementing targeted solutions and streamlining processes, the company was able to achieve significant cost savings and improve overall efficiency.
Quality Control and Lean Principles
Another example of a successful Lean Six Sigma Green Belt project focused on improving quality control processes in a service-oriented business. The Green Belt project team utilized Lean techniques to identify bottlenecks, eliminate waste, and standardize procedures. As a result, the company was able to enhance product quality, reduce defects, and increase customer satisfaction.
Lean Strategies for Project Implementation
A healthcare organization embarked on a Lean Six Sigma Green Belt project to streamline patient intake processes and reduce wait times. By utilizing Lean strategies such as value stream mapping and 5S methodology, the project team was able to identify inefficiencies, restructure workflows, and implement new procedures. The project resulted in improved patient satisfaction, reduced wait times, and enhanced overall operational efficiency.
Lean Techniques for Waste Reduction
A retail company faced challenges with excess inventory and inefficiencies in their supply chain processes. The Green Belt project team applied Lean techniques such as Kaizen events and Just-In-Time inventory management to reduce waste and optimize inventory levels. The project led to significant cost savings, improved inventory turnover rates, and enhanced supply chain efficiency.
Project Success through Lean Culture
In a manufacturing plant, a Lean Six Sigma Green Belt project focused on establishing a culture of continuous improvement and employee empowerment. Through engaging team members in Lean practices, implementing visual management tools, and fostering a culture of collaboration, the project achieved remarkable results. The plant experienced increased productivity, reduced downtime, and improved employee morale.
How to obtain LSSGB Certification?
We are an Education Technology company providing certification training courses to accelerate careers of working professionals worldwide. We impart training through instructor-led classroom workshops, instructor-led live virtual training sessions, and self-paced e-learning courses.
We have successfully conducted training sessions in 108 countries across the globe and enabled thousands of working professionals to enhance the scope of their careers.
Our enterprise training portfolio includes in-demand and globally recognized certification training courses in Project Management, Quality Management, Business Analysis, IT Service Management, Agile and Scrum, Cyber Security, Data Science, and Emerging Technologies. Download our Enterprise Training Catalog from https://www.icertglobal.com/corporate-training-for-enterprises.php
Popular Courses include:
-
Project Management: PMP, CAPM ,PMI RMP
-
Quality Management: Six Sigma Black Belt ,Lean Six Sigma Green Belt, Lean Management, Minitab,CMMI
-
Business Analysis: CBAP, CCBA, ECBA
-
Agile Training: PMI-ACP , CSM , CSPO
-
Scrum Training: CSM
-
DevOps
-
Program Management: PgMP
-
Cloud Technology: Exin Cloud Computing
-
Citrix Client Adminisration: Citrix Cloud Administration
The 10 top-paying certifications to target in 2024 are:
Conclusion
In Conclusion, Lean Six Sigma Green Belt projects in driving process improvement, cost savings, quality enhancement, and overall business success. By leveraging Lean principles, project management techniques, and data-driven decision-making, organizations can achieve significant improvements in efficiency, profitability, and customer satisfaction.
As businesses continue to adopt Lean methodologies and practices, the role of Lean Six Sigma Green Belt projects in achieving operational excellence becomes increasingly vital. By embracing a culture of continuous improvement, implementing Lean strategies, and leveraging Lean tools, companies can realize sustainable results and stay competitive in today's rapidly evolving marketplace.
Read More
In today's competitive business landscape, companies are constantly seeking ways to improve efficiency, reduce waste, and enhance quality. One proven methodology that has gained popularity in recent years is Lean Six Sigma. This powerful approach combines the principles of Lean methodology and Six Sigma to drive process improvement and problem-solving techniques within an organization.
Lean Six Sigma Green Belt projects play a crucial role in implementing Lean strategies and techniques to achieve project success. In this article, we will explore 5 real-world examples of Lean Six Sigma Green Belt projects, showcasing the impact of Lean principles on business performance and success.
Lean Six Sigma Green Belt Projects
Lean Six Sigma Green Belt projects are focused on applying data analysis and Lean tools to drive continuous improvement and waste reduction within an organization. By using the DMAIC (Define, Measure, Analyze, Improve, Control) methodology, Green Belt project teams can identify root causes of issues, implement solutions, and monitor performance metrics to ensure sustainable results.
Cost Savings through Efficiency Enhancement
One successful Lean Six Sigma Green Belt project involved a manufacturing company that was experiencing high production costs due to inefficiencies in their manufacturing process. The Green Belt project team conducted a thorough analysis using Lean tools and identified several areas for improvement. By implementing targeted solutions and streamlining processes, the company was able to achieve significant cost savings and improve overall efficiency.
Quality Control and Lean Principles
Another example of a successful Lean Six Sigma Green Belt project focused on improving quality control processes in a service-oriented business. The Green Belt project team utilized Lean techniques to identify bottlenecks, eliminate waste, and standardize procedures. As a result, the company was able to enhance product quality, reduce defects, and increase customer satisfaction.
Lean Strategies for Project Implementation
A healthcare organization embarked on a Lean Six Sigma Green Belt project to streamline patient intake processes and reduce wait times. By utilizing Lean strategies such as value stream mapping and 5S methodology, the project team was able to identify inefficiencies, restructure workflows, and implement new procedures. The project resulted in improved patient satisfaction, reduced wait times, and enhanced overall operational efficiency.
Lean Techniques for Waste Reduction
A retail company faced challenges with excess inventory and inefficiencies in their supply chain processes. The Green Belt project team applied Lean techniques such as Kaizen events and Just-In-Time inventory management to reduce waste and optimize inventory levels. The project led to significant cost savings, improved inventory turnover rates, and enhanced supply chain efficiency.
Project Success through Lean Culture
In a manufacturing plant, a Lean Six Sigma Green Belt project focused on establishing a culture of continuous improvement and employee empowerment. Through engaging team members in Lean practices, implementing visual management tools, and fostering a culture of collaboration, the project achieved remarkable results. The plant experienced increased productivity, reduced downtime, and improved employee morale.
How to obtain LSSGB Certification?
We are an Education Technology company providing certification training courses to accelerate careers of working professionals worldwide. We impart training through instructor-led classroom workshops, instructor-led live virtual training sessions, and self-paced e-learning courses.
We have successfully conducted training sessions in 108 countries across the globe and enabled thousands of working professionals to enhance the scope of their careers.
Our enterprise training portfolio includes in-demand and globally recognized certification training courses in Project Management, Quality Management, Business Analysis, IT Service Management, Agile and Scrum, Cyber Security, Data Science, and Emerging Technologies. Download our Enterprise Training Catalog from https://www.icertglobal.com/corporate-training-for-enterprises.php
Popular Courses include:
-
Project Management: PMP, CAPM ,PMI RMP
-
Quality Management: Six Sigma Black Belt ,Lean Six Sigma Green Belt, Lean Management, Minitab,CMMI
-
Business Analysis: CBAP, CCBA, ECBA
-
Agile Training: PMI-ACP , CSM , CSPO
-
Scrum Training: CSM
-
DevOps
-
Program Management: PgMP
-
Cloud Technology: Exin Cloud Computing
-
Citrix Client Adminisration: Citrix Cloud Administration
The 10 top-paying certifications to target in 2024 are:
Conclusion
In Conclusion, Lean Six Sigma Green Belt projects in driving process improvement, cost savings, quality enhancement, and overall business success. By leveraging Lean principles, project management techniques, and data-driven decision-making, organizations can achieve significant improvements in efficiency, profitability, and customer satisfaction.
As businesses continue to adopt Lean methodologies and practices, the role of Lean Six Sigma Green Belt projects in achieving operational excellence becomes increasingly vital. By embracing a culture of continuous improvement, implementing Lean strategies, and leveraging Lean tools, companies can realize sustainable results and stay competitive in today's rapidly evolving marketplace.
Minitab for Lean Management: Boost Efficiency & Cut Waste
In today's competitive business environment, companies are constantly striving to improve efficiency and reduce waste in their processes. Lean management is a methodology that focuses on maximizing value while minimizing waste. One powerful tool that has been instrumental in helping organizations achieve these goals is Minitab statistical software. In this article, we will explore how Minitab can be used to enhance lean management practices and drive process improvement.
What is lean management?
Lean management is a systematic approach to identifying and eliminating waste within a process. It is based on the principles of continuous improvement and respect for people. By streamlining processes and optimizing workflows, organizations can achieve higher levels of productivity and customer satisfaction.
How Does Minitab Fit into Lean Management?
Minitab is a data analysis software that is widely used in various industries for process improvement and quality control. It provides powerful statistical tools that enable users to analyze data, identify patterns, and make data-driven decisions. By leveraging Minitab, lean practitioners can gain valuable insights into their processes and drive continuous improvement initiatives.
The Benefits of Using Minitab for Lean Management
-
Lean Productivity: Minitab enables organizations to identify bottlenecks and inefficiencies in their processes, allowing them to streamline operations and improve productivity.
-
Lean Workflow: By using Minitab, organizations can visualize their workflow and identify areas for improvement, leading to smoother and more efficient processes.
Minitab Tools for Lean Management
Minitab offers a wide range of tools and features that are specifically designed to support lean management practices. Some of the key tools include:
-
Statistical Analysis: Minitab allows users to perform statistical analysis on data sets, helping them uncover trends and patterns that may not be visible to the naked eye.
-
Lean Six Sigma: Minitab is often used in conjunction with lean six sigma methodologies to drive process optimization and quality improvement initiatives.
How to Use Minitab for Lean Management
-
Data Analysis: Utilize Minitab to analyze and interpret data to gain valuable insights into process performance and identify areas for improvement.
-
Lean Principles: Apply lean principles such as value stream mapping and 5S with the help of Minitab to streamline processes and reduce waste.
Minitab Training for Lean Management
To fully leverage the capabilities of Minitab for lean management, organizations should invest in Minitab training for their employees. Training programs can help users become proficient in using the software and applying lean techniques to drive process improvement initiatives.
How to obtain Minitab Certification?
We are an Education Technology company providing certification training courses to accelerate careers of working professionals worldwide. We impart training through instructor-led classroom workshops, instructor-led live virtual training sessions, and self-paced e-learning courses. We have successfully conducted training sessions in 108 countries across the globe and enabled thousands of working professionals to enhance the scope of their careers.
Our enterprise training portfolio includes in-demand and globally recognized certification training courses in Project Management, Quality Management, Business Analysis, IT Service Management, Agile and Scrum, Cyber Security, Data Science, and Emerging Technologies. Download our Enterprise Training Catalog from https://www.icertglobal.com/corporate-training-for-enterprises.php
Popular courses include:
-
Project Management: PMP, CAPM ,PMI RMP
-
Quality Management: Six Sigma Black Belt ,Lean Six Sigma Green Belt, Lean Management, Minitab,CMMI
-
Business Analysis: CBAP, CCBA, ECBA
-
Agile Training: PMI-ACP , CSM , CSPO
-
Scrum Training: CSM
-
DevOps
-
Program Management: PgMP
-
Cloud Technology: Exin Cloud Computing
-
Citrix Client Adminisration: Citrix Cloud Administration
The 10 top-paying certifications to target in 2024 are:
Conclusion
In conclusion, Minitab is a powerful tool that can significantly enhance lean management practices by providing valuable insights into processes and enabling data-driven decision-making. By leveraging Minitab for lean management, organizations can improve efficiency, reduce waste, and drive continuous improvement initiatives. Investing in Minitab training for employees can further enhance the benefits of using this software for process optimization and quality improvement.
Read More
In today's competitive business environment, companies are constantly striving to improve efficiency and reduce waste in their processes. Lean management is a methodology that focuses on maximizing value while minimizing waste. One powerful tool that has been instrumental in helping organizations achieve these goals is Minitab statistical software. In this article, we will explore how Minitab can be used to enhance lean management practices and drive process improvement.
What is lean management?
Lean management is a systematic approach to identifying and eliminating waste within a process. It is based on the principles of continuous improvement and respect for people. By streamlining processes and optimizing workflows, organizations can achieve higher levels of productivity and customer satisfaction.
How Does Minitab Fit into Lean Management?
Minitab is a data analysis software that is widely used in various industries for process improvement and quality control. It provides powerful statistical tools that enable users to analyze data, identify patterns, and make data-driven decisions. By leveraging Minitab, lean practitioners can gain valuable insights into their processes and drive continuous improvement initiatives.
The Benefits of Using Minitab for Lean Management
-
Lean Productivity: Minitab enables organizations to identify bottlenecks and inefficiencies in their processes, allowing them to streamline operations and improve productivity.
-
Lean Workflow: By using Minitab, organizations can visualize their workflow and identify areas for improvement, leading to smoother and more efficient processes.
Minitab Tools for Lean Management
Minitab offers a wide range of tools and features that are specifically designed to support lean management practices. Some of the key tools include:
-
Statistical Analysis: Minitab allows users to perform statistical analysis on data sets, helping them uncover trends and patterns that may not be visible to the naked eye.
-
Lean Six Sigma: Minitab is often used in conjunction with lean six sigma methodologies to drive process optimization and quality improvement initiatives.
How to Use Minitab for Lean Management
-
Data Analysis: Utilize Minitab to analyze and interpret data to gain valuable insights into process performance and identify areas for improvement.
-
Lean Principles: Apply lean principles such as value stream mapping and 5S with the help of Minitab to streamline processes and reduce waste.
Minitab Training for Lean Management
To fully leverage the capabilities of Minitab for lean management, organizations should invest in Minitab training for their employees. Training programs can help users become proficient in using the software and applying lean techniques to drive process improvement initiatives.
How to obtain Minitab Certification?
We are an Education Technology company providing certification training courses to accelerate careers of working professionals worldwide. We impart training through instructor-led classroom workshops, instructor-led live virtual training sessions, and self-paced e-learning courses. We have successfully conducted training sessions in 108 countries across the globe and enabled thousands of working professionals to enhance the scope of their careers.
Our enterprise training portfolio includes in-demand and globally recognized certification training courses in Project Management, Quality Management, Business Analysis, IT Service Management, Agile and Scrum, Cyber Security, Data Science, and Emerging Technologies. Download our Enterprise Training Catalog from https://www.icertglobal.com/corporate-training-for-enterprises.php
Popular courses include:
-
Project Management: PMP, CAPM ,PMI RMP
-
Quality Management: Six Sigma Black Belt ,Lean Six Sigma Green Belt, Lean Management, Minitab,CMMI
-
Business Analysis: CBAP, CCBA, ECBA
-
Agile Training: PMI-ACP , CSM , CSPO
-
Scrum Training: CSM
-
DevOps
-
Program Management: PgMP
-
Cloud Technology: Exin Cloud Computing
-
Citrix Client Adminisration: Citrix Cloud Administration
The 10 top-paying certifications to target in 2024 are:
Conclusion
In conclusion, Minitab is a powerful tool that can significantly enhance lean management practices by providing valuable insights into processes and enabling data-driven decision-making. By leveraging Minitab for lean management, organizations can improve efficiency, reduce waste, and drive continuous improvement initiatives. Investing in Minitab training for employees can further enhance the benefits of using this software for process optimization and quality improvement.
Minitab Academia: Enhancing Statistical Learning & Research
In the world of academia, the ability to analyze data effectively is crucial for student learning and faculty research. One tool that has become indispensable in this endeavor is Minitab, a powerful statistical software that offers a wide range of analytical tools for data exploration, hypothesis testing, and data visualization. In this article, we will explore how Minitab is enhancing statistical learning and research in higher education institutions.
The Role of Minitab in Academia
Minitab serves as an essential educational tool in universities and colleges worldwide, providing students and faculty members with the means to conduct in-depth data analysis and statistical modeling. By utilizing Minitab, students can gain hands-on experience with statistical techniques, enabling them to make data-driven decisions and enhance their academic success.
Benefits of Using Minitab in Academia
-
Enhanced Data Interpretation: Minitab allows users to easily manipulate data and perform complex statistical analyses, enabling them to interpret results accurately and draw meaningful conclusions from their research.
-
Improved Data Presentation: With Minitab's data visualization capabilities, users can create informative graphs and charts to present their findings in a clear and concise manner, making it easier for others to understand and interpret the data.
-
Facilitating Student Projects: Minitab provides students with a valuable tool for conducting research projects, allowing them to design experiments, analyze data, and present their findings effectively. This empowers students to take ownership of their learning and develop critical thinking and analytical skills.
Minitab in Faculty Research
In addition to benefiting students, Minitab also plays a crucial role in faculty research endeavors. By using Minitab to analyze data, faculty members can conduct rigorous research studies, explore new research methods, and make groundbreaking discoveries in their respective fields of study.
Case Study: University X Incorporates Minitab in Research Methods Course
At University X, the Department of Statistics has integrated Minitab into its research methods course to enhance student learning and research skills. By utilizing Minitab, students have been able to delve into the intricacies of experimental design, data manipulation, and statistical analysis, leading to a deeper understanding of research methodologies.
The Future of Minitab in Academia
As educational technology continues to evolve, Minitab remains at the forefront of statistical software, providing users with innovative tools for data analysis and interpretation. With its user-friendly interface and robust features, Minitab is poised to revolutionize statistical learning and research in academia for years to come.
How to obtain Minitab Certification?
We are an Education Technology company providing certification training courses to accelerate careers of working professionals worldwide. We impart training through instructor-led classroom workshops, instructor-led live virtual training sessions, and self-paced e-learning courses.
We have successfully conducted training sessions in 108 countries across the globe and enabled thousands of working professionals to enhance the scope of their careers.
Our enterprise training portfolio includes in-demand and globally recognized certification training courses in Project Management, Quality Management, Business Analysis, IT Service Management, Agile and Scrum, Cyber Security, Data Science, and Emerging Technologies. Download our Enterprise Training Catalog from https://www.icertglobal.com/corporate-training-for-enterprises.php
Popular Courses include:
-
Project Management: PMP, CAPM ,PMI RMP
-
Quality Management: Six Sigma Black Belt ,Lean Six Sigma Green Belt, Lean Management, Minitab,CMMI
-
Business Analysis: CBAP, CCBA, ECBA
-
Agile Training: PMI-ACP , CSM , CSPO
-
Scrum Training: CSM
-
DevOps
-
Program Management: PgMP
-
Cloud Technology: Exin Cloud Computing
-
Citrix Client Adminisration: Citrix Cloud Administration
The 10 top-paying certifications to target in 2024 are:
Conclusion
In conclusion, Minitab is a valuable asset in the academic realm, offering students and faculty members the tools they need to excel in data analysis, statistical learning, and research. By incorporating Minitab into their academic pursuits, individuals can enhance their understanding of statistical concepts, improve their research methodologies, and ultimately contribute to the advancement of knowledge in their respective fields.
Read More
In the world of academia, the ability to analyze data effectively is crucial for student learning and faculty research. One tool that has become indispensable in this endeavor is Minitab, a powerful statistical software that offers a wide range of analytical tools for data exploration, hypothesis testing, and data visualization. In this article, we will explore how Minitab is enhancing statistical learning and research in higher education institutions.
The Role of Minitab in Academia
Minitab serves as an essential educational tool in universities and colleges worldwide, providing students and faculty members with the means to conduct in-depth data analysis and statistical modeling. By utilizing Minitab, students can gain hands-on experience with statistical techniques, enabling them to make data-driven decisions and enhance their academic success.
Benefits of Using Minitab in Academia
-
Enhanced Data Interpretation: Minitab allows users to easily manipulate data and perform complex statistical analyses, enabling them to interpret results accurately and draw meaningful conclusions from their research.
-
Improved Data Presentation: With Minitab's data visualization capabilities, users can create informative graphs and charts to present their findings in a clear and concise manner, making it easier for others to understand and interpret the data.
-
Facilitating Student Projects: Minitab provides students with a valuable tool for conducting research projects, allowing them to design experiments, analyze data, and present their findings effectively. This empowers students to take ownership of their learning and develop critical thinking and analytical skills.
Minitab in Faculty Research
In addition to benefiting students, Minitab also plays a crucial role in faculty research endeavors. By using Minitab to analyze data, faculty members can conduct rigorous research studies, explore new research methods, and make groundbreaking discoveries in their respective fields of study.
Case Study: University X Incorporates Minitab in Research Methods Course
At University X, the Department of Statistics has integrated Minitab into its research methods course to enhance student learning and research skills. By utilizing Minitab, students have been able to delve into the intricacies of experimental design, data manipulation, and statistical analysis, leading to a deeper understanding of research methodologies.
The Future of Minitab in Academia
As educational technology continues to evolve, Minitab remains at the forefront of statistical software, providing users with innovative tools for data analysis and interpretation. With its user-friendly interface and robust features, Minitab is poised to revolutionize statistical learning and research in academia for years to come.
How to obtain Minitab Certification?
We are an Education Technology company providing certification training courses to accelerate careers of working professionals worldwide. We impart training through instructor-led classroom workshops, instructor-led live virtual training sessions, and self-paced e-learning courses.
We have successfully conducted training sessions in 108 countries across the globe and enabled thousands of working professionals to enhance the scope of their careers.
Our enterprise training portfolio includes in-demand and globally recognized certification training courses in Project Management, Quality Management, Business Analysis, IT Service Management, Agile and Scrum, Cyber Security, Data Science, and Emerging Technologies. Download our Enterprise Training Catalog from https://www.icertglobal.com/corporate-training-for-enterprises.php
Popular Courses include:
-
Project Management: PMP, CAPM ,PMI RMP
-
Quality Management: Six Sigma Black Belt ,Lean Six Sigma Green Belt, Lean Management, Minitab,CMMI
-
Business Analysis: CBAP, CCBA, ECBA
-
Agile Training: PMI-ACP , CSM , CSPO
-
Scrum Training: CSM
-
DevOps
-
Program Management: PgMP
-
Cloud Technology: Exin Cloud Computing
-
Citrix Client Adminisration: Citrix Cloud Administration
The 10 top-paying certifications to target in 2024 are:
Conclusion
In conclusion, Minitab is a valuable asset in the academic realm, offering students and faculty members the tools they need to excel in data analysis, statistical learning, and research. By incorporating Minitab into their academic pursuits, individuals can enhance their understanding of statistical concepts, improve their research methodologies, and ultimately contribute to the advancement of knowledge in their respective fields.
Implementing Lean Principles for Better Quality Management
In today's competitive business environment, companies are constantly seeking ways to enhance operational efficiency, minimize waste, and improve overall quality management. One highly effective approach that has gained widespread popularity in recent years is the implementation of lean principles. By adopting lean methodologies and tools, organizations can streamline processes, drive continuous improvement, and ultimately deliver higher-quality products and services to their customers.
What are Lean Principles?
Lean principles are centered around the concept of maximizing customer value while minimizing waste. This philosophy is rooted in the idea that every process should add value for the customer, and any activities that do not contribute to this value should be considered wasteful and eliminated. By focusing on process optimization and waste reduction, lean organizations are able to deliver higher-quality products and services in a more efficient and cost-effective manner.
Lean Methodologies and Tools
There are several key methodologies and tools that are commonly used in lean practices. These include:
-
Value stream mapping: A tool used to visualize and analyze the flow of materials and information through a process, helping to identify areas of waste and inefficiency.
-
Kaizen: A philosophy of continuous improvement that encourages small, incremental changes to improve quality and efficiency over time.
-
Six Sigma: A data-driven approach to process improvement that focuses on reducing defects and variation in processes.
-
Lean production: A method of manufacturing that focuses on producing goods in the most efficient and cost-effective way possible.
-
Lean culture: A shared set of values, beliefs, and behaviors that promote a culture of continuous improvement and waste reduction.
The Benefits of Lean Implementation
Implementing lean principles can have a wide range of benefits for organizations looking to improve their quality management practices. Some of the key benefits include:
-
Improved quality control: By focusing on eliminating waste and optimizing processes, organizations can deliver higher-quality products and services to their customers.
-
Increased operational efficiency: Lean practices help to streamline processes, reduce cycle times, and improve overall efficiency in the organization.
-
Enhanced customer satisfaction: By delivering higher-quality products and services in a more efficient manner, organizations can enhance customer satisfaction and loyalty.
-
Greater employee engagement: Lean practices encourage collaboration, problem-solving, and continuous improvement, leading to higher levels of employee engagement and satisfaction.
Lean Strategies for Success
To successfully implement lean principles and realize the benefits of improved quality management, organizations should focus on the following strategies:
-
Foster a lean mindset: Encourage employees at all levels of the organization to embrace lean thinking and actively seek out opportunities for improvement.
-
Invest in lean training: Provide employees with the training and tools they need to effectively implement lean practices and drive continuous improvement.
-
Establish lean teams: Create cross-functional teams dedicated to implementing lean methodologies and driving quality improvement initiatives.
-
Embrace lean leadership: Develop leaders who can champion lean principles, inspire employees, and drive a culture of continuous improvement.
How to obtain Quality Management Certification?
We are an Education Technology company providing certification training courses to accelerate careers of working professionals worldwide. We impart training through instructor-led classroom workshops, instructor-led live virtual training sessions, and self-paced e-learning courses.
We have successfully conducted training sessions in 108 countries across the globe and enabled thousands of working professionals to enhance the scope of their careers.
Our enterprise training portfolio includes in-demand and globally recognized certification training courses in Project Management, Quality Management, Business Analysis, IT Service Management, Agile and Scrum, Cyber Security, Data Science, and Emerging Technologies. Download our Enterprise Training Catalog from https://www.icertglobal.com/corporate-training-for-enterprises.php
Popular Courses include:
-
Project Management: PMP, CAPM ,PMI RMP
-
Quality Management: Six Sigma Black Belt ,Lean Six Sigma Green Belt, Lean Management, Minitab,CMMI
-
Business Analysis: CBAP, CCBA, ECBA
-
Agile Training: PMI-ACP , CSM , CSPO
-
Scrum Training: CSM
-
DevOps
-
Program Management: PgMP
-
Cloud Technology: Exin Cloud Computing
-
Citrix Client Adminisration: Citrix Cloud Administration
The 10 top-paying certifications to target in 2024 are:
Conclusion
In conclusion, implementing lean principles is a powerful strategy for organizations looking to enhance their quality management practices and deliver higher-quality products and services to their customers. By adopting lean methodologies, tools, and strategies, organizations can drive process optimization, waste reduction, and continuous improvement, ultimately leading to greater operational efficiency and customer satisfaction. By fostering a lean culture, investing in lean training, and embracing lean leadership, organizations can position themselves for long-term success in today's competitive market. So, are you ready to take your quality management to the next level by implementing lean principles?
Read More
In today's competitive business environment, companies are constantly seeking ways to enhance operational efficiency, minimize waste, and improve overall quality management. One highly effective approach that has gained widespread popularity in recent years is the implementation of lean principles. By adopting lean methodologies and tools, organizations can streamline processes, drive continuous improvement, and ultimately deliver higher-quality products and services to their customers.
What are Lean Principles?
Lean principles are centered around the concept of maximizing customer value while minimizing waste. This philosophy is rooted in the idea that every process should add value for the customer, and any activities that do not contribute to this value should be considered wasteful and eliminated. By focusing on process optimization and waste reduction, lean organizations are able to deliver higher-quality products and services in a more efficient and cost-effective manner.
Lean Methodologies and Tools
There are several key methodologies and tools that are commonly used in lean practices. These include:
-
Value stream mapping: A tool used to visualize and analyze the flow of materials and information through a process, helping to identify areas of waste and inefficiency.
-
Kaizen: A philosophy of continuous improvement that encourages small, incremental changes to improve quality and efficiency over time.
-
Six Sigma: A data-driven approach to process improvement that focuses on reducing defects and variation in processes.
-
Lean production: A method of manufacturing that focuses on producing goods in the most efficient and cost-effective way possible.
-
Lean culture: A shared set of values, beliefs, and behaviors that promote a culture of continuous improvement and waste reduction.
The Benefits of Lean Implementation
Implementing lean principles can have a wide range of benefits for organizations looking to improve their quality management practices. Some of the key benefits include:
-
Improved quality control: By focusing on eliminating waste and optimizing processes, organizations can deliver higher-quality products and services to their customers.
-
Increased operational efficiency: Lean practices help to streamline processes, reduce cycle times, and improve overall efficiency in the organization.
-
Enhanced customer satisfaction: By delivering higher-quality products and services in a more efficient manner, organizations can enhance customer satisfaction and loyalty.
-
Greater employee engagement: Lean practices encourage collaboration, problem-solving, and continuous improvement, leading to higher levels of employee engagement and satisfaction.
Lean Strategies for Success
To successfully implement lean principles and realize the benefits of improved quality management, organizations should focus on the following strategies:
-
Foster a lean mindset: Encourage employees at all levels of the organization to embrace lean thinking and actively seek out opportunities for improvement.
-
Invest in lean training: Provide employees with the training and tools they need to effectively implement lean practices and drive continuous improvement.
-
Establish lean teams: Create cross-functional teams dedicated to implementing lean methodologies and driving quality improvement initiatives.
-
Embrace lean leadership: Develop leaders who can champion lean principles, inspire employees, and drive a culture of continuous improvement.
How to obtain Quality Management Certification?
We are an Education Technology company providing certification training courses to accelerate careers of working professionals worldwide. We impart training through instructor-led classroom workshops, instructor-led live virtual training sessions, and self-paced e-learning courses.
We have successfully conducted training sessions in 108 countries across the globe and enabled thousands of working professionals to enhance the scope of their careers.
Our enterprise training portfolio includes in-demand and globally recognized certification training courses in Project Management, Quality Management, Business Analysis, IT Service Management, Agile and Scrum, Cyber Security, Data Science, and Emerging Technologies. Download our Enterprise Training Catalog from https://www.icertglobal.com/corporate-training-for-enterprises.php
Popular Courses include:
-
Project Management: PMP, CAPM ,PMI RMP
-
Quality Management: Six Sigma Black Belt ,Lean Six Sigma Green Belt, Lean Management, Minitab,CMMI
-
Business Analysis: CBAP, CCBA, ECBA
-
Agile Training: PMI-ACP , CSM , CSPO
-
Scrum Training: CSM
-
DevOps
-
Program Management: PgMP
-
Cloud Technology: Exin Cloud Computing
-
Citrix Client Adminisration: Citrix Cloud Administration
The 10 top-paying certifications to target in 2024 are:
Conclusion
In conclusion, implementing lean principles is a powerful strategy for organizations looking to enhance their quality management practices and deliver higher-quality products and services to their customers. By adopting lean methodologies, tools, and strategies, organizations can drive process optimization, waste reduction, and continuous improvement, ultimately leading to greater operational efficiency and customer satisfaction. By fostering a lean culture, investing in lean training, and embracing lean leadership, organizations can position themselves for long-term success in today's competitive market. So, are you ready to take your quality management to the next level by implementing lean principles?
Lean Management in Non-Manufacturing Industries: Challenges
In today's competitive business landscape, the principles of lean management are not limited to the manufacturing sector. Non-manufacturing industries, such as healthcare, banking, and hospitality, are increasingly adopting lean practices to improve efficiency, drive process improvement, and deliver better value to customers. In this article, we will explore the applications of lean management in non-manufacturing industries, as well as the challenges that organizations may face in implementing lean principles in these diverse sectors.
What is Lean Management?
Lean management is a systematic approach to identifying and eliminating waste in processes to improve efficiency and drive continuous improvement. Originally developed by Toyota in the 1950s, lean principles focus on creating value for customers by streamlining operations, reducing lead times, and optimizing resources. By eliminating non-value-added activities and focusing on what truly matters to customers, organizations can enhance quality, reduce costs, and increase customer satisfaction.
Applications of Lean Management in Non-Manufacturing Industries
-
Healthcare: In the healthcare industry, lean management can help hospitals and clinics improve patient care, enhance operational efficiency, and reduce medical errors. By applying lean techniques such as value stream mapping and Kaizen events, healthcare organizations can streamline workflows, improve communication between healthcare providers, and enhance the overall patient experience.
-
Banking: Lean management can also benefit the banking sector by optimizing processes, reducing wait times, and enhancing customer service. By implementing lean practices in areas such as loan processing, account openings, and customer inquiries, banks can improve customer satisfaction, increase operational efficiency, and drive profitability.
-
Hospitality: In the hospitality industry, lean management can help hotels, restaurants, and resorts deliver exceptional guest experiences, optimize food and beverage operations, and reduce waste. By applying lean tools such as 5S (Sort, Set in order, Shine, Standardize, Sustain) and Kanban, hospitality businesses can improve service delivery, enhance staff productivity, and minimize costs.
Challenges of Implementing Lean Management in Non-Manufacturing Industries
While the benefits of lean management are well-documented, implementing lean principles in non-manufacturing industries comes with its own set of challenges. Some of the key challenges organizations may face include:
-
Organizational Culture: Shifting to a lean culture requires buy-in from employees at all levels of the organization. In non-manufacturing industries, where hierarchical structures and traditional ways of working may be prevalent, changing mindsets and attitudes towards lean practices can be challenging.
-
Leadership: Effective leadership is critical to the success of lean initiatives in non-manufacturing industries. Leaders must demonstrate a commitment to continuous improvement, empower employees to identify and solve problems, and provide the necessary support and resources for lean implementation.
-
Sustainability: Sustaining lean practices over the long term can be difficult in non-manufacturing industries where external factors, such as regulatory changes and market dynamics, may impact operations. Organizations must continuously monitor performance metrics, conduct regular audits, and adapt lean strategies to ensure ongoing success.
How to obtain Lean Management Certification?
We are an Education Technology company providing certification training courses to accelerate careers of working professionals worldwide. We impart training through instructor-led classroom workshops, instructor-led live virtual training sessions, and self-paced e-learning courses.
We have successfully conducted training sessions in 108 countries across the globe and enabled thousands of working professionals to enhance the scope of their careers.
Our enterprise training portfolio includes in-demand and globally recognized certification training courses in Project Management, Quality Management, Business Analysis, IT Service Management, Agile and Scrum, Cyber Security, Data Science, and Emerging Technologies. Download our Enterprise Training Catalog from https://www.icertglobal.com/corporate-training-for-enterprises.php
Popular Courses include:
-
Project Management: PMP, CAPM ,PMI RMP
-
Quality Management: Six Sigma Black Belt ,Lean Six Sigma Green Belt, Lean Management, Minitab,CMMI
-
Business Analysis: CBAP, CCBA, ECBA
-
Agile Training: PMI-ACP , CSM , CSPO
-
Scrum Training: CSM
-
DevOps
-
Program Management: PgMP
-
Cloud Technology: Exin Cloud Computing
-
Citrix Client Adminisration: Citrix Cloud Administration
The 10 top-paying certifications to target in 2024 are:
Conclusion
In conclusion, lean management offers valuable benefits for non-manufacturing industries seeking to improve efficiency, drive process improvement, and enhance customer satisfaction. By applying lean principles such as waste reduction, continuous improvement, and employee engagement, organizations can achieve operational excellence and stay competitive in today's dynamic business environment. While challenges may arise during the implementation of lean practices, overcoming these obstacles through strong leadership, a supportive organizational culture, and a commitment to sustainability can lead to long-term success. Embracing lean management in non-manufacturing industries is not just a trend – it is a strategic imperative for organizations looking to thrive in the digital age
Read More
In today's competitive business landscape, the principles of lean management are not limited to the manufacturing sector. Non-manufacturing industries, such as healthcare, banking, and hospitality, are increasingly adopting lean practices to improve efficiency, drive process improvement, and deliver better value to customers. In this article, we will explore the applications of lean management in non-manufacturing industries, as well as the challenges that organizations may face in implementing lean principles in these diverse sectors.
What is Lean Management?
Lean management is a systematic approach to identifying and eliminating waste in processes to improve efficiency and drive continuous improvement. Originally developed by Toyota in the 1950s, lean principles focus on creating value for customers by streamlining operations, reducing lead times, and optimizing resources. By eliminating non-value-added activities and focusing on what truly matters to customers, organizations can enhance quality, reduce costs, and increase customer satisfaction.
Applications of Lean Management in Non-Manufacturing Industries
-
Healthcare: In the healthcare industry, lean management can help hospitals and clinics improve patient care, enhance operational efficiency, and reduce medical errors. By applying lean techniques such as value stream mapping and Kaizen events, healthcare organizations can streamline workflows, improve communication between healthcare providers, and enhance the overall patient experience.
-
Banking: Lean management can also benefit the banking sector by optimizing processes, reducing wait times, and enhancing customer service. By implementing lean practices in areas such as loan processing, account openings, and customer inquiries, banks can improve customer satisfaction, increase operational efficiency, and drive profitability.
-
Hospitality: In the hospitality industry, lean management can help hotels, restaurants, and resorts deliver exceptional guest experiences, optimize food and beverage operations, and reduce waste. By applying lean tools such as 5S (Sort, Set in order, Shine, Standardize, Sustain) and Kanban, hospitality businesses can improve service delivery, enhance staff productivity, and minimize costs.
Challenges of Implementing Lean Management in Non-Manufacturing Industries
While the benefits of lean management are well-documented, implementing lean principles in non-manufacturing industries comes with its own set of challenges. Some of the key challenges organizations may face include:
-
Organizational Culture: Shifting to a lean culture requires buy-in from employees at all levels of the organization. In non-manufacturing industries, where hierarchical structures and traditional ways of working may be prevalent, changing mindsets and attitudes towards lean practices can be challenging.
-
Leadership: Effective leadership is critical to the success of lean initiatives in non-manufacturing industries. Leaders must demonstrate a commitment to continuous improvement, empower employees to identify and solve problems, and provide the necessary support and resources for lean implementation.
-
Sustainability: Sustaining lean practices over the long term can be difficult in non-manufacturing industries where external factors, such as regulatory changes and market dynamics, may impact operations. Organizations must continuously monitor performance metrics, conduct regular audits, and adapt lean strategies to ensure ongoing success.
How to obtain Lean Management Certification?
We are an Education Technology company providing certification training courses to accelerate careers of working professionals worldwide. We impart training through instructor-led classroom workshops, instructor-led live virtual training sessions, and self-paced e-learning courses.
We have successfully conducted training sessions in 108 countries across the globe and enabled thousands of working professionals to enhance the scope of their careers.
Our enterprise training portfolio includes in-demand and globally recognized certification training courses in Project Management, Quality Management, Business Analysis, IT Service Management, Agile and Scrum, Cyber Security, Data Science, and Emerging Technologies. Download our Enterprise Training Catalog from https://www.icertglobal.com/corporate-training-for-enterprises.php
Popular Courses include:
-
Project Management: PMP, CAPM ,PMI RMP
-
Quality Management: Six Sigma Black Belt ,Lean Six Sigma Green Belt, Lean Management, Minitab,CMMI
-
Business Analysis: CBAP, CCBA, ECBA
-
Agile Training: PMI-ACP , CSM , CSPO
-
Scrum Training: CSM
-
DevOps
-
Program Management: PgMP
-
Cloud Technology: Exin Cloud Computing
-
Citrix Client Adminisration: Citrix Cloud Administration
The 10 top-paying certifications to target in 2024 are:
Conclusion
In conclusion, lean management offers valuable benefits for non-manufacturing industries seeking to improve efficiency, drive process improvement, and enhance customer satisfaction. By applying lean principles such as waste reduction, continuous improvement, and employee engagement, organizations can achieve operational excellence and stay competitive in today's dynamic business environment. While challenges may arise during the implementation of lean practices, overcoming these obstacles through strong leadership, a supportive organizational culture, and a commitment to sustainability can lead to long-term success. Embracing lean management in non-manufacturing industries is not just a trend – it is a strategic imperative for organizations looking to thrive in the digital age
Effective Strategies for Root Cause Analysis in Quality
In the realm of quality management, identifying and addressing the root cause of issues is crucial for ensuring continuous improvement and optimal performance. Root cause analysis (RCA) is a systematic approach used to uncover the underlying reasons behind problems or defects within a process or system. By implementing effective strategies for RCA, organizations can proactively tackle issues, prevent future recurrences, and enhance overall quality control.
What is Root Cause Analysis?
Root cause analysis is a methodical process that involves investigating and identifying the primary cause of a problem, rather than just addressing its symptoms. By digging deeper into the root cause of an issue, organizations can implement targeted solutions that address the underlying issues and prevent them from resurfacing in the future. This approach is essential for achieving sustainable quality improvement and operational excellence.
The Importance of Root Cause Analysis in Quality Management
Root cause analysis plays a critical role in quality management by helping organizations:
-
Problem-Solving: RCA helps organizations solve complex problems by getting to the heart of the issue and implementing effective solutions.
-
Continuous Improvement: By identifying and addressing root causes, organizations can continuously improve processes and systems to enhance quality and efficiency.
-
Data Analysis: RCA involves analyzing data to pinpoint the underlying cause of problems, enabling data-driven decision-making.
-
Corrective Action: Once the root cause is identified, organizations can take corrective action to prevent future issues from occurring.
-
Process Optimization: RCA helps organizations optimize processes by eliminating inefficiencies and streamlining operations.
Strategies for Effective Root Cause Analysis
When conducting root cause analysis in quality management, it is essential to employ the following strategies to ensure accurate and actionable results:
-
Utilize Six Sigma and Lean Methodology: Incorporate Six Sigma and Lean principles to streamline processes, reduce waste, and enhance quality control.
-
Root Cause Identification: Thoroughly investigate and analyze the problem to determine the underlying cause, rather than focusing solely on symptoms.
-
Quality Assurance: Implement quality assurance measures to maintain high standards and identify deviations from the norm.
-
Quality Improvement: Continuously strive to improve quality by addressing root causes and implementing effective solutions.
-
Defect Prevention: Focus on preventing defects rather than just correcting them, to ensure long-term quality and efficiency.
Techniques for Root Cause Analysis
There are various techniques and tools that can be used for root cause analysis in quality management, including:
-
Cause and Effect Analysis: Also known as the Fishbone Diagram, this tool helps visualize the potential causes of a problem and identify the root cause.
-
Failure Analysis: Investigate past failures to uncover the underlying reasons and prevent similar issues from occurring in the future.
-
System Analysis: Analyze the entire system to understand how different components interact and influence the overall performance.
-
Critical Thinking: Encourage critical thinking to delve deep into the problem and explore all possible causes and solutions.
-
Problem Resolution: Develop a systematic approach for resolving problems and preventing their recurrence.
How to obtain Quality Management Certification?
We are an Education Technology company providing certification training courses to accelerate careers of working professionals worldwide. We impart training through instructor-led classroom workshops, instructor-led live virtual training sessions, and self-paced e-learning courses.
We have successfully conducted training sessions in 108 countries across the globe and enabled thousands of working professionals to enhance the scope of their careers.
Our enterprise training portfolio includes in-demand and globally recognized certification training courses in Project Management, Quality Management, Business Analysis, IT Service Management, Agile and Scrum, Cyber Security, Data Science, and Emerging Technologies. Download our Enterprise Training Catalog from https://www.icertglobal.com/corporate-training-for-enterprises.php
Popular Courses include:
-
Project Management: PMP, CAPM ,PMI RMP
-
Quality Management: Six Sigma Black Belt ,Lean Six Sigma Green Belt, Lean Management, Minitab,CMMI
-
Business Analysis: CBAP, CCBA, ECBA
-
Agile Training: PMI-ACP , CSM , CSPO
-
Scrum Training: CSM
-
DevOps
-
Program Management: PgMP
-
Cloud Technology: Exin Cloud Computing
-
Citrix Client Adminisration: Citrix Cloud Administration
The 10 top-paying certifications to target in 2024 are:
Conclusion
In Conclusion, By utilizing these strategies and techniques for root cause analysis in quality management, organizations can enhance their problem-solving capabilities, drive continuous improvement, and achieve optimal performance and quality standards.
Remember, effective root cause analysis is not just about identifying problems but also about implementing sustainable solutions that prevent future issues from arising. By investing time and resources into RCA, organizations can proactively address challenges, optimize processes, and maintain high levels of quality and performance.
Read More
In the realm of quality management, identifying and addressing the root cause of issues is crucial for ensuring continuous improvement and optimal performance. Root cause analysis (RCA) is a systematic approach used to uncover the underlying reasons behind problems or defects within a process or system. By implementing effective strategies for RCA, organizations can proactively tackle issues, prevent future recurrences, and enhance overall quality control.
What is Root Cause Analysis?
Root cause analysis is a methodical process that involves investigating and identifying the primary cause of a problem, rather than just addressing its symptoms. By digging deeper into the root cause of an issue, organizations can implement targeted solutions that address the underlying issues and prevent them from resurfacing in the future. This approach is essential for achieving sustainable quality improvement and operational excellence.
The Importance of Root Cause Analysis in Quality Management
Root cause analysis plays a critical role in quality management by helping organizations:
-
Problem-Solving: RCA helps organizations solve complex problems by getting to the heart of the issue and implementing effective solutions.
-
Continuous Improvement: By identifying and addressing root causes, organizations can continuously improve processes and systems to enhance quality and efficiency.
-
Data Analysis: RCA involves analyzing data to pinpoint the underlying cause of problems, enabling data-driven decision-making.
-
Corrective Action: Once the root cause is identified, organizations can take corrective action to prevent future issues from occurring.
-
Process Optimization: RCA helps organizations optimize processes by eliminating inefficiencies and streamlining operations.
Strategies for Effective Root Cause Analysis
When conducting root cause analysis in quality management, it is essential to employ the following strategies to ensure accurate and actionable results:
-
Utilize Six Sigma and Lean Methodology: Incorporate Six Sigma and Lean principles to streamline processes, reduce waste, and enhance quality control.
-
Root Cause Identification: Thoroughly investigate and analyze the problem to determine the underlying cause, rather than focusing solely on symptoms.
-
Quality Assurance: Implement quality assurance measures to maintain high standards and identify deviations from the norm.
-
Quality Improvement: Continuously strive to improve quality by addressing root causes and implementing effective solutions.
-
Defect Prevention: Focus on preventing defects rather than just correcting them, to ensure long-term quality and efficiency.
Techniques for Root Cause Analysis
There are various techniques and tools that can be used for root cause analysis in quality management, including:
-
Cause and Effect Analysis: Also known as the Fishbone Diagram, this tool helps visualize the potential causes of a problem and identify the root cause.
-
Failure Analysis: Investigate past failures to uncover the underlying reasons and prevent similar issues from occurring in the future.
-
System Analysis: Analyze the entire system to understand how different components interact and influence the overall performance.
-
Critical Thinking: Encourage critical thinking to delve deep into the problem and explore all possible causes and solutions.
-
Problem Resolution: Develop a systematic approach for resolving problems and preventing their recurrence.
How to obtain Quality Management Certification?
We are an Education Technology company providing certification training courses to accelerate careers of working professionals worldwide. We impart training through instructor-led classroom workshops, instructor-led live virtual training sessions, and self-paced e-learning courses.
We have successfully conducted training sessions in 108 countries across the globe and enabled thousands of working professionals to enhance the scope of their careers.
Our enterprise training portfolio includes in-demand and globally recognized certification training courses in Project Management, Quality Management, Business Analysis, IT Service Management, Agile and Scrum, Cyber Security, Data Science, and Emerging Technologies. Download our Enterprise Training Catalog from https://www.icertglobal.com/corporate-training-for-enterprises.php
Popular Courses include:
-
Project Management: PMP, CAPM ,PMI RMP
-
Quality Management: Six Sigma Black Belt ,Lean Six Sigma Green Belt, Lean Management, Minitab,CMMI
-
Business Analysis: CBAP, CCBA, ECBA
-
Agile Training: PMI-ACP , CSM , CSPO
-
Scrum Training: CSM
-
DevOps
-
Program Management: PgMP
-
Cloud Technology: Exin Cloud Computing
-
Citrix Client Adminisration: Citrix Cloud Administration
The 10 top-paying certifications to target in 2024 are:
Conclusion
In Conclusion, By utilizing these strategies and techniques for root cause analysis in quality management, organizations can enhance their problem-solving capabilities, drive continuous improvement, and achieve optimal performance and quality standards.
Remember, effective root cause analysis is not just about identifying problems but also about implementing sustainable solutions that prevent future issues from arising. By investing time and resources into RCA, organizations can proactively address challenges, optimize processes, and maintain high levels of quality and performance.
10 Key Benefits of CMMI Certification for Your Organization
Are you looking to take your organization to the next level of excellence and efficiency? Achieving Capability Maturity Model Integration (CMMI) certification could be the key to unlocking a wide range of benefits for your business. In this article, we will explore the 10 key benefits of achieving CMMI certification for your organization, and why it matters in today's competitive business landscape.
What is CMMI Certification?
Before diving into the benefits, let's first understand what CMMI certification is all about. CMMI is a globally recognized framework that helps organizations improve their processes and performance. By achieving CMMI certification, organizations demonstrate their commitment to maintaining high standards of quality and efficiency in everything they do.
1. Improved Organizational Performance
One of the main benefits of achieving CMMI certification is the significant improvement in organizational performance. By implementing best practices recommended by CMMI, organizations can streamline their processes, reduce errors, and increase productivity.
2. Enhanced Customer Satisfaction
With CMMI certification, organizations can better meet customer expectations and deliver high-quality products and services consistently. This leads to increased customer satisfaction and loyalty, ultimately helping the business retain existing customers and attract new ones.
3. Increased Efficiency and Cost Savings
CMMI certification helps organizations identify and eliminate wasteful practices, leading to increased efficiency and cost savings. By optimizing processes and reducing errors, organizations can reduce rework and improve overall operational efficiency.
4. Better Risk Management
Achieving CMMI certification enables organizations to establish robust risk management processes. By identifying potential risks and implementing proactive measures to mitigate them, organizations can safeguard against potential disruptions and ensure business continuity.
5. Enhanced Employee Morale and Engagement
By establishing a culture of continuous improvement and professional development, CMMI certification can boost employee morale and engagement. Employees feel valued and empowered to contribute to the organization's success, leading to higher job satisfaction and retention rates.
6. Competitive Advantage
In today's competitive market, having CMMI certification can give organizations a significant edge over their competitors. CMMI-certified organizations are seen as more reliable, efficient, and quality-focused, which can attract new customers and business opportunities.
7. Sustainable Growth and Scalability
CMMI certification provides organizations with a solid foundation for sustainable growth and scalability. By standardizing processes and establishing best practices, organizations can expand their operations and adapt to changing market demands more effectively.
8. Regulatory Compliance
Achieving CMMI certification ensures that organizations comply with industry standards and regulations. This critical aspect helps organizations avoid fines, penalties, and legal issues, demonstrating a commitment to ethical business practices.
9. Improved Decision-Making
With a data-driven approach to process improvement, organizations can make informed decisions based on accurate data and metrics. CMMI certification equips organizations with the tools and insights needed to drive strategic decision-making and achieve business objectives.
10. International Recognition and Reputation
Lastly, achieving CMMI certification provides organizations with international recognition and a positive reputation in the industry. CMMI-certified organizations are perceived as reliable and trustworthy partners, opening doors to global opportunities and collaborations.
How to obtain CMMI Certification?
We are an Education Technology company providing certification training courses to accelerate careers of working professionals worldwide. We impart training through instructor-led classroom workshops, instructor-led live virtual training sessions, and self-paced e-learning courses.
We have successfully conducted training sessions in 108 countries across the globe and enabled thousands of working professionals to enhance the scope of their careers.
Our enterprise training portfolio includes in-demand and globally recognized certification training courses in Project Management, Quality Management, Business Analysis, IT Service Management, Agile and Scrum, Cyber Security, Data Science, and Emerging Technologies. Download our Enterprise Training Catalog from https://www.icertglobal.com/corporate-training-for-enterprises.php
Popular Courses include:
-
Project Management: PMP, CAPM ,PMI RMP
-
Quality Management: Six Sigma Black Belt ,Lean Six Sigma Green Belt, Lean Management, Minitab,CMMI
-
Business Analysis: CBAP, CCBA, ECBA
-
Agile Training: PMI-ACP , CSM , CSPO
-
Scrum Training: CSM
-
DevOps
-
Program Management: PgMP
-
Cloud Technology: Exin Cloud Computing
-
Citrix Client Adminisration: Citrix Cloud Administration
The 10 top-paying certifications to target in 2024 are:
Conclusion
In conclusion, achieving CMMI certification for your organization can deliver a wide range of benefits, from improved organizational performance to enhanced customer satisfaction and competitive advantage. By investing in CMMI certification, organizations can drive sustainable growth, mitigate risks, and establish themselves as industry leaders. Don't miss out on the opportunity to take your organization to the next level of excellence with CMMI certification.
Read More
Are you looking to take your organization to the next level of excellence and efficiency? Achieving Capability Maturity Model Integration (CMMI) certification could be the key to unlocking a wide range of benefits for your business. In this article, we will explore the 10 key benefits of achieving CMMI certification for your organization, and why it matters in today's competitive business landscape.
What is CMMI Certification?
Before diving into the benefits, let's first understand what CMMI certification is all about. CMMI is a globally recognized framework that helps organizations improve their processes and performance. By achieving CMMI certification, organizations demonstrate their commitment to maintaining high standards of quality and efficiency in everything they do.
1. Improved Organizational Performance
One of the main benefits of achieving CMMI certification is the significant improvement in organizational performance. By implementing best practices recommended by CMMI, organizations can streamline their processes, reduce errors, and increase productivity.
2. Enhanced Customer Satisfaction
With CMMI certification, organizations can better meet customer expectations and deliver high-quality products and services consistently. This leads to increased customer satisfaction and loyalty, ultimately helping the business retain existing customers and attract new ones.
3. Increased Efficiency and Cost Savings
CMMI certification helps organizations identify and eliminate wasteful practices, leading to increased efficiency and cost savings. By optimizing processes and reducing errors, organizations can reduce rework and improve overall operational efficiency.
4. Better Risk Management
Achieving CMMI certification enables organizations to establish robust risk management processes. By identifying potential risks and implementing proactive measures to mitigate them, organizations can safeguard against potential disruptions and ensure business continuity.
5. Enhanced Employee Morale and Engagement
By establishing a culture of continuous improvement and professional development, CMMI certification can boost employee morale and engagement. Employees feel valued and empowered to contribute to the organization's success, leading to higher job satisfaction and retention rates.
6. Competitive Advantage
In today's competitive market, having CMMI certification can give organizations a significant edge over their competitors. CMMI-certified organizations are seen as more reliable, efficient, and quality-focused, which can attract new customers and business opportunities.
7. Sustainable Growth and Scalability
CMMI certification provides organizations with a solid foundation for sustainable growth and scalability. By standardizing processes and establishing best practices, organizations can expand their operations and adapt to changing market demands more effectively.
8. Regulatory Compliance
Achieving CMMI certification ensures that organizations comply with industry standards and regulations. This critical aspect helps organizations avoid fines, penalties, and legal issues, demonstrating a commitment to ethical business practices.
9. Improved Decision-Making
With a data-driven approach to process improvement, organizations can make informed decisions based on accurate data and metrics. CMMI certification equips organizations with the tools and insights needed to drive strategic decision-making and achieve business objectives.
10. International Recognition and Reputation
Lastly, achieving CMMI certification provides organizations with international recognition and a positive reputation in the industry. CMMI-certified organizations are perceived as reliable and trustworthy partners, opening doors to global opportunities and collaborations.
How to obtain CMMI Certification?
We are an Education Technology company providing certification training courses to accelerate careers of working professionals worldwide. We impart training through instructor-led classroom workshops, instructor-led live virtual training sessions, and self-paced e-learning courses.
We have successfully conducted training sessions in 108 countries across the globe and enabled thousands of working professionals to enhance the scope of their careers.
Our enterprise training portfolio includes in-demand and globally recognized certification training courses in Project Management, Quality Management, Business Analysis, IT Service Management, Agile and Scrum, Cyber Security, Data Science, and Emerging Technologies. Download our Enterprise Training Catalog from https://www.icertglobal.com/corporate-training-for-enterprises.php
Popular Courses include:
-
Project Management: PMP, CAPM ,PMI RMP
-
Quality Management: Six Sigma Black Belt ,Lean Six Sigma Green Belt, Lean Management, Minitab,CMMI
-
Business Analysis: CBAP, CCBA, ECBA
-
Agile Training: PMI-ACP , CSM , CSPO
-
Scrum Training: CSM
-
DevOps
-
Program Management: PgMP
-
Cloud Technology: Exin Cloud Computing
-
Citrix Client Adminisration: Citrix Cloud Administration
The 10 top-paying certifications to target in 2024 are:
Conclusion
In conclusion, achieving CMMI certification for your organization can deliver a wide range of benefits, from improved organizational performance to enhanced customer satisfaction and competitive advantage. By investing in CMMI certification, organizations can drive sustainable growth, mitigate risks, and establish themselves as industry leaders. Don't miss out on the opportunity to take your organization to the next level of excellence with CMMI certification.
7 Strategies for Lean Six Sigma Black Belt Certification
Are you looking to take your career to the next level with a Lean Six Sigma Black Belt Certification? This prestigious certification is highly sought after in the world of process improvement, project management, and quality control. To help you prepare for the certification exam, here are 7 key strategies to ensure your success:
1. Understand Lean Principles and DMAIC Methodology
Before diving into your Black Belt certification preparation, it is essential to have a solid understanding of Lean principles and the DMAIC (Define, Measure, Analyze, Improve, Control) methodology. These are the foundation of Lean Six Sigma and will be essential for your success in the certification exam.
2. Continuous Improvement and Problem-Solving Skills
Lean Six Sigma Black Belts are often tasked with leading continuous improvement projects and solving complex problems within organizations. It is crucial to hone your problem-solving skills and be able to apply Lean tools and statistical analysis to drive results.
3. Utilize Study Materials and Training Resources
There are numerous study materials and training courses available to help you prepare for the Black Belt certification exam. Make sure to take advantage of these resources to deepen your knowledge and understanding of Lean Six Sigma concepts.
4. Focus on Root Cause Analysis and Quality Control
As a Black Belt, you will be responsible for identifying root causes of process inefficiencies and ensuring that quality control measures are in place. Practice conducting thorough root cause analyses and implementing quality control strategies in your Black Belt project.
5. Choose the Right Project and Apply Lean Tools
Selecting the right project is critical for your Black Belt certification success. Choose a project that aligns with industry standards and focuses on improving operational efficiency. Be sure to leverage Lean tools and methodologies to drive results and demonstrate your expertise.
6. Develop Lean Leadership Skills
In addition to technical knowledge, Lean Six Sigma Black Belts must also possess strong leadership skills. Focus on developing your abilities to lead teams, communicate effectively, and drive change within your organization.
7. Take Practice Exams and Participate in Mock Exercises
As the saying goes, practice makes perfect. Take advantage of practice exams and participate in mock exercises to test your knowledge and readiness for the Black Belt certification exam. This will help you identify areas of improvement and ensure you are fully prepared on exam day.
How to obtain Lean Six Sigma Black Belt Certification?
We are an Education Technology company providing certification training courses to accelerate careers of working professionals worldwide. We impart training through instructor-led classroom workshops, instructor-led live virtual training sessions, and self-paced e-learning courses.
We have successfully conducted training sessions in 108 countries across the globe and enabled thousands of working professionals to enhance the scope of their careers.
Our enterprise training portfolio includes in-demand and globally recognized certification training courses in Project Management, Quality Management, Business Analysis, IT Service Management, Agile and Scrum, Cyber Security, Data Science, and Emerging Technologies. Download our Enterprise Training Catalog from https://www.icertglobal.com/corporate-training-for-enterprises.php
Popular Courses include:
-
Project Management: PMP, CAPM ,PMI RMP
-
Quality Management: Six Sigma Black Belt ,Lean Six Sigma Green Belt, Lean Management, Minitab,CMMI
-
Business Analysis: CBAP, CCBA, ECBA
-
Agile Training: PMI-ACP , CSM , CSPO
-
Scrum Training: CSM
-
DevOps
-
Program Management: PgMP
-
Cloud Technology: Exin Cloud Computing
-
Citrix Client Adminisration: Citrix Cloud Administration
The 10 top-paying certifications to target in 2024 are:
Conclusion
In Conclusion, 7 key strategies, you will be well-equipped to tackle the Lean Six Sigma Black Belt certification exam with confidence. Remember to stay focused, dedicated, and committed to your professional development and career advancement. Good luck on your journey to becoming a certified Lean Six Sigma Black Belt!
Read More
Are you looking to take your career to the next level with a Lean Six Sigma Black Belt Certification? This prestigious certification is highly sought after in the world of process improvement, project management, and quality control. To help you prepare for the certification exam, here are 7 key strategies to ensure your success:
1. Understand Lean Principles and DMAIC Methodology
Before diving into your Black Belt certification preparation, it is essential to have a solid understanding of Lean principles and the DMAIC (Define, Measure, Analyze, Improve, Control) methodology. These are the foundation of Lean Six Sigma and will be essential for your success in the certification exam.
2. Continuous Improvement and Problem-Solving Skills
Lean Six Sigma Black Belts are often tasked with leading continuous improvement projects and solving complex problems within organizations. It is crucial to hone your problem-solving skills and be able to apply Lean tools and statistical analysis to drive results.
3. Utilize Study Materials and Training Resources
There are numerous study materials and training courses available to help you prepare for the Black Belt certification exam. Make sure to take advantage of these resources to deepen your knowledge and understanding of Lean Six Sigma concepts.
4. Focus on Root Cause Analysis and Quality Control
As a Black Belt, you will be responsible for identifying root causes of process inefficiencies and ensuring that quality control measures are in place. Practice conducting thorough root cause analyses and implementing quality control strategies in your Black Belt project.
5. Choose the Right Project and Apply Lean Tools
Selecting the right project is critical for your Black Belt certification success. Choose a project that aligns with industry standards and focuses on improving operational efficiency. Be sure to leverage Lean tools and methodologies to drive results and demonstrate your expertise.
6. Develop Lean Leadership Skills
In addition to technical knowledge, Lean Six Sigma Black Belts must also possess strong leadership skills. Focus on developing your abilities to lead teams, communicate effectively, and drive change within your organization.
7. Take Practice Exams and Participate in Mock Exercises
As the saying goes, practice makes perfect. Take advantage of practice exams and participate in mock exercises to test your knowledge and readiness for the Black Belt certification exam. This will help you identify areas of improvement and ensure you are fully prepared on exam day.
How to obtain Lean Six Sigma Black Belt Certification?
We are an Education Technology company providing certification training courses to accelerate careers of working professionals worldwide. We impart training through instructor-led classroom workshops, instructor-led live virtual training sessions, and self-paced e-learning courses.
We have successfully conducted training sessions in 108 countries across the globe and enabled thousands of working professionals to enhance the scope of their careers.
Our enterprise training portfolio includes in-demand and globally recognized certification training courses in Project Management, Quality Management, Business Analysis, IT Service Management, Agile and Scrum, Cyber Security, Data Science, and Emerging Technologies. Download our Enterprise Training Catalog from https://www.icertglobal.com/corporate-training-for-enterprises.php
Popular Courses include:
-
Project Management: PMP, CAPM ,PMI RMP
-
Quality Management: Six Sigma Black Belt ,Lean Six Sigma Green Belt, Lean Management, Minitab,CMMI
-
Business Analysis: CBAP, CCBA, ECBA
-
Agile Training: PMI-ACP , CSM , CSPO
-
Scrum Training: CSM
-
DevOps
-
Program Management: PgMP
-
Cloud Technology: Exin Cloud Computing
-
Citrix Client Adminisration: Citrix Cloud Administration
The 10 top-paying certifications to target in 2024 are:
Conclusion
In Conclusion, 7 key strategies, you will be well-equipped to tackle the Lean Six Sigma Black Belt certification exam with confidence. Remember to stay focused, dedicated, and committed to your professional development and career advancement. Good luck on your journey to becoming a certified Lean Six Sigma Black Belt!
Top Six Sigma Yellow Belt Tools for Process Improvement.
Are you looking to enhance your process improvement skills with Six Sigma methodologies? As a Yellow Belt, you play a crucial role in driving process improvements within your organization. In this article, we will explore the top six Sigma Yellow Belt tools that can help you achieve operational excellence and drive business success.
What is Six Sigma?
Six Sigma is a data-driven methodology that aims to improve processes by identifying and removing causes of defects and errors. It focuses on process optimization, efficiency techniques, and continuous improvement. By utilizing statistical techniques and quality tools, Six Sigma helps organizations reduce defects, enhance performance, and deliver high-quality products and services.
The Importance of Yellow Belt Certification
As a Yellow Belt, you are equipped with the foundational knowledge of Six Sigma principles and practices. You play a vital role in supporting project teams, implementing process improvements, and driving business success. By obtaining Yellow Belt certification, you demonstrate your commitment to quality management and process optimization.
Top Six Sigma Yellow Belt Tools
DMAIC Methodology
DMAIC (Define, Measure, Analyze, Improve, Control) is a key tool used in Six Sigma for project management and process improvement. It provides a structured approach to problem-solving and data analysis, allowing teams to identify root causes of issues and implement effective solutions.
Root Cause Analysis
Root cause analysis is a critical tool for identifying the underlying causes of process defects and errors. By conducting a thorough analysis, Yellow Belts can pinpoint the root causes of problems and develop actionable solutions to prevent future issues.
Performance Metrics
Performance metrics are essential for tracking and measuring the success of process improvements. By establishing key performance indicators (KPIs) and performance metrics, Yellow Belts can evaluate the impact of their efforts and make data-driven decisions to drive continuous improvement.
Lean Principles
Lean practices are an integral part of Six Sigma methodology, focusing on eliminating waste and maximizing efficiency. By applying lean principles, Yellow Belts can streamline business processes, reduce cycle times, and optimize operational performance.
Quality Tools
Quality tools such as control charts, Pareto diagrams, and process maps are essential for identifying trends, patterns, and opportunities for improvement. By utilizing these tools, Yellow Belts can analyze data, identify areas for enhancement, and drive quality assurance.
Project Tools
Project management tools such as Gantt charts, project plans, and risk assessment matrices are vital for effectively managing Six Sigma projects. By utilizing project tools, Yellow Belts can plan, execute, and monitor project activities to ensure successful outcomes.
How to obtain Six Sigma Yellow Belt Certification?
We are an Education Technology company providing certification training courses to accelerate careers of working professionals worldwide. We impart training through instructor-led classroom workshops, instructor-led live virtual training sessions, and self-paced e-learning courses.
We have successfully conducted training sessions in 108 countries across the globe and enabled thousands of working professionals to enhance the scope of their careers.
Our enterprise training portfolio includes in-demand and globally recognized certification training courses in Project Management, Quality Management, Business Analysis, IT Service Management, Agile and Scrum, Cyber Security, Data Science, and Emerging Technologies. Download our Enterprise Training Catalog from https://www.icertglobal.com/corporate-training-for-enterprises.php
Popular Courses include:
-
Project Management: PMP, CAPM ,PMI RMP
-
Quality Management: Six Sigma Black Belt ,Lean Six Sigma Green Belt, Lean Management, Minitab,CMMI
-
Business Analysis: CBAP, CCBA, ECBA
-
Agile Training: PMI-ACP , CSM , CSPO
-
Scrum Training: CSM
-
DevOps
-
Program Management: PgMP
-
Cloud Technology: Exin Cloud Computing
-
Citrix Client Adminisration: Citrix Cloud Administration
The 10 top-paying certifications to target in 2024 are:
Conclusion
In conclusion, Six Sigma Yellow Belts play a crucial role in driving process improvement and enhancing operational excellence within organizations. By utilizing the top Six Sigma Yellow Belt tools, Yellow Belts can effectively identify process defects, drive quality improvements, and achieve business success.
Read More
Are you looking to enhance your process improvement skills with Six Sigma methodologies? As a Yellow Belt, you play a crucial role in driving process improvements within your organization. In this article, we will explore the top six Sigma Yellow Belt tools that can help you achieve operational excellence and drive business success.
What is Six Sigma?
Six Sigma is a data-driven methodology that aims to improve processes by identifying and removing causes of defects and errors. It focuses on process optimization, efficiency techniques, and continuous improvement. By utilizing statistical techniques and quality tools, Six Sigma helps organizations reduce defects, enhance performance, and deliver high-quality products and services.
The Importance of Yellow Belt Certification
As a Yellow Belt, you are equipped with the foundational knowledge of Six Sigma principles and practices. You play a vital role in supporting project teams, implementing process improvements, and driving business success. By obtaining Yellow Belt certification, you demonstrate your commitment to quality management and process optimization.
Top Six Sigma Yellow Belt Tools
DMAIC Methodology
DMAIC (Define, Measure, Analyze, Improve, Control) is a key tool used in Six Sigma for project management and process improvement. It provides a structured approach to problem-solving and data analysis, allowing teams to identify root causes of issues and implement effective solutions.
Root Cause Analysis
Root cause analysis is a critical tool for identifying the underlying causes of process defects and errors. By conducting a thorough analysis, Yellow Belts can pinpoint the root causes of problems and develop actionable solutions to prevent future issues.
Performance Metrics
Performance metrics are essential for tracking and measuring the success of process improvements. By establishing key performance indicators (KPIs) and performance metrics, Yellow Belts can evaluate the impact of their efforts and make data-driven decisions to drive continuous improvement.
Lean Principles
Lean practices are an integral part of Six Sigma methodology, focusing on eliminating waste and maximizing efficiency. By applying lean principles, Yellow Belts can streamline business processes, reduce cycle times, and optimize operational performance.
Quality Tools
Quality tools such as control charts, Pareto diagrams, and process maps are essential for identifying trends, patterns, and opportunities for improvement. By utilizing these tools, Yellow Belts can analyze data, identify areas for enhancement, and drive quality assurance.
Project Tools
Project management tools such as Gantt charts, project plans, and risk assessment matrices are vital for effectively managing Six Sigma projects. By utilizing project tools, Yellow Belts can plan, execute, and monitor project activities to ensure successful outcomes.
How to obtain Six Sigma Yellow Belt Certification?
We are an Education Technology company providing certification training courses to accelerate careers of working professionals worldwide. We impart training through instructor-led classroom workshops, instructor-led live virtual training sessions, and self-paced e-learning courses.
We have successfully conducted training sessions in 108 countries across the globe and enabled thousands of working professionals to enhance the scope of their careers.
Our enterprise training portfolio includes in-demand and globally recognized certification training courses in Project Management, Quality Management, Business Analysis, IT Service Management, Agile and Scrum, Cyber Security, Data Science, and Emerging Technologies. Download our Enterprise Training Catalog from https://www.icertglobal.com/corporate-training-for-enterprises.php
Popular Courses include:
-
Project Management: PMP, CAPM ,PMI RMP
-
Quality Management: Six Sigma Black Belt ,Lean Six Sigma Green Belt, Lean Management, Minitab,CMMI
-
Business Analysis: CBAP, CCBA, ECBA
-
Agile Training: PMI-ACP , CSM , CSPO
-
Scrum Training: CSM
-
DevOps
-
Program Management: PgMP
-
Cloud Technology: Exin Cloud Computing
-
Citrix Client Adminisration: Citrix Cloud Administration
The 10 top-paying certifications to target in 2024 are:
Conclusion
In conclusion, Six Sigma Yellow Belts play a crucial role in driving process improvement and enhancing operational excellence within organizations. By utilizing the top Six Sigma Yellow Belt tools, Yellow Belts can effectively identify process defects, drive quality improvements, and achieve business success.
The Role of Technology in Quality Management Processes
In today's fast-paced and highly competitive business environment, organizations are constantly looking for ways to improve efficiency and ensure high-quality products and services. One way in which technology has significantly impacted the field of quality management is through the use of sophisticated tools and systems that help streamline processes, detect defects early on, and ultimately deliver better outcomes for customers. Let's explore the various ways in which technology plays a crucial role in enhancing quality management processes.
How Does Technology Improve Quality Management?
With the advent of advanced software and automation tools, organizations can now track and monitor every stage of the production process in real-time. This level of visibility allows for early detection of any potential issues or defects, enabling companies to take corrective action before the problem escalates. Additionally, technology-driven quality management systems can analyze large datasets to identify patterns and trends that may not be apparent to human eyes, leading to more informed decision-making and improved overall quality.
What are the Benefits of Using Technology in Quality Management?
One of the key benefits of incorporating technology into quality management processes is the ability to standardize procedures and ensure consistency across all operations. By automating manual tasks and implementing digital workflows, companies can reduce the risk of human error and minimize variability in product output. Furthermore, technology enables real-time collaboration and communication among team members, facilitating faster problem-solving and decision-making.
The Role of Artificial Intelligence in Quality Management
Artificial intelligence (AI) is revolutionizing the field of quality management by providing advanced analytics and predictive capabilities that help organizations proactively address quality issues. AI-powered tools can analyze complex data sets to identify potential risks, recommend corrective actions, and even predict future quality trends. By leveraging AI, companies can enhance their quality control processes and continuously improve their products and services.
How can AI Improve Quality Control?
AI algorithms can process vast amounts of data from multiple sources, including sensors, IoT devices, and production equipment, to identify anomalies and deviations from established quality standards. This enables organizations to detect quality issues in real-time and take immediate action to rectify them. Moreover, AI can learn from past quality incidents and continuously optimize quality control processes, leading to higher levels of efficiency and accuracy.
Integrating Technology into Quality Management Systems
To fully leverage the benefits of technology in quality management, organizations must invest in modern quality management systems that are equipped with advanced features and functionalities. These systems should be flexible, scalable, and easy to integrate with existing IT infrastructure to ensure seamless operations. By centralizing quality data and processes in a digital platform, companies can enhance visibility, transparency, and traceability throughout the supply chain.
How to obtain Quality Management Certification?
We are an Education Technology company providing certification training courses to accelerate careers of working professionals worldwide. We impart training through instructor-led classroom workshops, instructor-led live virtual training sessions, and self-paced e-learning courses.
We have successfully conducted training sessions in 108 countries across the globe and enabled thousands of working professionals to enhance the scope of their careers.
Our enterprise training portfolio includes in-demand and globally recognized certification training courses in Project Management, Quality Management, Business Analysis, IT Service Management, Agile and Scrum, Cyber Security, Data Science, and Emerging Technologies. Download our Enterprise Training Catalog from https://www.icertglobal.com/corporate-training-for-enterprises.php
Popular Courses include:
- Project Management: PMP, CAPM ,PMI RMP
- Quality Management: Six Sigma Black Belt ,Lean Six Sigma Green Belt, Lean Management, Minitab,CMMI
- Business Analysis: CBAP, CCBA, ECBA
- Agile Training: PMI-ACP , CSM , CSPO
- Scrum Training: CSM
- DevOps
- Program Management: PgMP
- Cloud Technology: Exin Cloud Computing
- Citrix Client Adminisration: Citrix Cloud Administration
Conclusion
Technology plays a vital role in enhancing quality management processes by enabling better data analysis, standardizing procedures, and improving collaboration among team members. By embracing advanced technologies such as AI, organizations can proactively address quality issues, optimize production processes, and deliver superior products and services to customers. As the business landscape continues to evolve, leveraging technology will be essential for staying competitive and meeting the ever-increasing demands for quality and efficiency.
Read More
In today's fast-paced and highly competitive business environment, organizations are constantly looking for ways to improve efficiency and ensure high-quality products and services. One way in which technology has significantly impacted the field of quality management is through the use of sophisticated tools and systems that help streamline processes, detect defects early on, and ultimately deliver better outcomes for customers. Let's explore the various ways in which technology plays a crucial role in enhancing quality management processes.
How Does Technology Improve Quality Management?
With the advent of advanced software and automation tools, organizations can now track and monitor every stage of the production process in real-time. This level of visibility allows for early detection of any potential issues or defects, enabling companies to take corrective action before the problem escalates. Additionally, technology-driven quality management systems can analyze large datasets to identify patterns and trends that may not be apparent to human eyes, leading to more informed decision-making and improved overall quality.
What are the Benefits of Using Technology in Quality Management?
One of the key benefits of incorporating technology into quality management processes is the ability to standardize procedures and ensure consistency across all operations. By automating manual tasks and implementing digital workflows, companies can reduce the risk of human error and minimize variability in product output. Furthermore, technology enables real-time collaboration and communication among team members, facilitating faster problem-solving and decision-making.
The Role of Artificial Intelligence in Quality Management
Artificial intelligence (AI) is revolutionizing the field of quality management by providing advanced analytics and predictive capabilities that help organizations proactively address quality issues. AI-powered tools can analyze complex data sets to identify potential risks, recommend corrective actions, and even predict future quality trends. By leveraging AI, companies can enhance their quality control processes and continuously improve their products and services.
How can AI Improve Quality Control?
AI algorithms can process vast amounts of data from multiple sources, including sensors, IoT devices, and production equipment, to identify anomalies and deviations from established quality standards. This enables organizations to detect quality issues in real-time and take immediate action to rectify them. Moreover, AI can learn from past quality incidents and continuously optimize quality control processes, leading to higher levels of efficiency and accuracy.
Integrating Technology into Quality Management Systems
To fully leverage the benefits of technology in quality management, organizations must invest in modern quality management systems that are equipped with advanced features and functionalities. These systems should be flexible, scalable, and easy to integrate with existing IT infrastructure to ensure seamless operations. By centralizing quality data and processes in a digital platform, companies can enhance visibility, transparency, and traceability throughout the supply chain.
How to obtain Quality Management Certification?
We are an Education Technology company providing certification training courses to accelerate careers of working professionals worldwide. We impart training through instructor-led classroom workshops, instructor-led live virtual training sessions, and self-paced e-learning courses.
We have successfully conducted training sessions in 108 countries across the globe and enabled thousands of working professionals to enhance the scope of their careers.
Our enterprise training portfolio includes in-demand and globally recognized certification training courses in Project Management, Quality Management, Business Analysis, IT Service Management, Agile and Scrum, Cyber Security, Data Science, and Emerging Technologies. Download our Enterprise Training Catalog from https://www.icertglobal.com/corporate-training-for-enterprises.php
Popular Courses include:
- Project Management: PMP, CAPM ,PMI RMP
- Quality Management: Six Sigma Black Belt ,Lean Six Sigma Green Belt, Lean Management, Minitab,CMMI
- Business Analysis: CBAP, CCBA, ECBA
- Agile Training: PMI-ACP , CSM , CSPO
- Scrum Training: CSM
- DevOps
- Program Management: PgMP
- Cloud Technology: Exin Cloud Computing
- Citrix Client Adminisration: Citrix Cloud Administration
Conclusion
Technology plays a vital role in enhancing quality management processes by enabling better data analysis, standardizing procedures, and improving collaboration among team members. By embracing advanced technologies such as AI, organizations can proactively address quality issues, optimize production processes, and deliver superior products and services to customers. As the business landscape continues to evolve, leveraging technology will be essential for staying competitive and meeting the ever-increasing demands for quality and efficiency.
CTFL Certification: Boost Your Software Testing Career.
Are you looking to take your software testing career to the next level? Have you considered obtaining a CTFL certification? In this article, we will explore how CTFL certification can serve as a gateway to advancement in software testing roles, opening up a world of opportunities for professional growth and development.
Introduction to CTFL Certification
The CTFL (Certified Tester Foundation Level) certification is a globally recognized credential that validates professionals' knowledge and skills in software testing. Whether you are just starting in the field or looking to enhance your existing expertise, CTFL certification can be a valuable asset in your career toolkit.
Advancement in Software Testing Roles
One of the key benefits of CTFL certification is its ability to open doors to advancement in software testing roles. Employers often look for candidates who have demonstrated their commitment to excellence in the field, and CTFL certification can serve as tangible proof of your dedication and expertise.
Career Growth Opportunities
With CTFL certification, you can position yourself as a certified professional with a solid foundation in software testing principles and practices. This can lead to exciting career growth opportunities, such as promotions, salary increases, and access to higher-level positions within your organization.
Software Testing Certification Exam
To obtain CTFL certification, you will need to pass the certification exam, which tests your knowledge of key software testing concepts, techniques, and best practices. By successfully completing the exam, you demonstrate your competence and proficiency in the field, setting yourself apart as a qualified and skilled professional.
Benefits of CTFL Certification
There are numerous benefits to obtaining CTFL certification, including:
-
Enhanced job opportunities: CTFL certification can open doors to a wide range of job opportunities in the field of software testing.
-
Professional recognition: Being CTFL certified demonstrates your dedication to continuous learning and professional development.
-
Skill development: The CTFL certification process helps you enhance your software testing skills and stay abreast of industry trends and best practices.
Advancement in Testing Roles
By obtaining CTFL certification, you are equipping yourself with the knowledge and skills needed to excel in various software testing roles, such as:
-
Quality assurance analyst
-
Test engineer
-
Test manager
-
Software development engineer in test (SDET)
Software Testing Advancement Opportunities
With CTFL certification, you can explore a wide range of advancement opportunities in the field of software testing, including:
-
Leading testing projects
-
Mentoring junior testers
-
Implementing best practices
-
Contributing to process improvements
Software Testing Career Growth
With CTFL certification, you can pave the way for long-term career growth and success in the dynamic and ever-evolving field of software testing. By continuously expanding your knowledge and skills, you can stay ahead of the curve and position yourself for exciting opportunities in the industry.
How to obtain CTFL certification?
We are an Education Technology company providing certification training courses to accelerate careers of working professionals worldwide. We impart training through instructor-led classroom workshops, instructor-led live virtual training sessions, and self-paced e-learning courses.
We have successfully conducted training sessions in 108 countries across the globe and enabled thousands of working professionals to enhance the scope of their careers.
Our enterprise training portfolio includes in-demand and globally recognized certification training courses in Project Management, Quality Management, Business Analysis, IT Service management, Agile and Scrum, Cyber Security, Data Science, and Emerging Technologies. Download our Enterprise Training Catalog from https://www.icertglobal.com/corporate-training-for-enterprises.php
Popular Courses include:
-
Project Management: PMP, CAPM ,PMI RMP
-
Quality Management: Six Sigma Black Belt ,Lean Six Sigma Green Belt, Lean Management, Minitab,CMMI
-
Business Analysis: CBAP, CCBA, ECBA
-
Agile Training: PMI-ACP , CSM , CSPO
-
Scrum Training: CSM
-
DevOps
-
Program Management: PgMP
-
Cloud Technology: Exin Cloud Computing
-
Citrix Client Adminisration: Citrix Cloud Administration
The 10 top-paying certifications to target in 2024 are:
Conclusion
In conclusion, CTFL certification is a valuable asset for professionals looking to advance in software testing roles. By obtaining CTFL certification, you can enhance your skills, credibility, and career prospects, setting yourself up for long-term success and growth in the field of software testing.
Read More
Are you looking to take your software testing career to the next level? Have you considered obtaining a CTFL certification? In this article, we will explore how CTFL certification can serve as a gateway to advancement in software testing roles, opening up a world of opportunities for professional growth and development.
Introduction to CTFL Certification
The CTFL (Certified Tester Foundation Level) certification is a globally recognized credential that validates professionals' knowledge and skills in software testing. Whether you are just starting in the field or looking to enhance your existing expertise, CTFL certification can be a valuable asset in your career toolkit.
Advancement in Software Testing Roles
One of the key benefits of CTFL certification is its ability to open doors to advancement in software testing roles. Employers often look for candidates who have demonstrated their commitment to excellence in the field, and CTFL certification can serve as tangible proof of your dedication and expertise.
Career Growth Opportunities
With CTFL certification, you can position yourself as a certified professional with a solid foundation in software testing principles and practices. This can lead to exciting career growth opportunities, such as promotions, salary increases, and access to higher-level positions within your organization.
Software Testing Certification Exam
To obtain CTFL certification, you will need to pass the certification exam, which tests your knowledge of key software testing concepts, techniques, and best practices. By successfully completing the exam, you demonstrate your competence and proficiency in the field, setting yourself apart as a qualified and skilled professional.
Benefits of CTFL Certification
There are numerous benefits to obtaining CTFL certification, including:
-
Enhanced job opportunities: CTFL certification can open doors to a wide range of job opportunities in the field of software testing.
-
Professional recognition: Being CTFL certified demonstrates your dedication to continuous learning and professional development.
-
Skill development: The CTFL certification process helps you enhance your software testing skills and stay abreast of industry trends and best practices.
Advancement in Testing Roles
By obtaining CTFL certification, you are equipping yourself with the knowledge and skills needed to excel in various software testing roles, such as:
-
Quality assurance analyst
-
Test engineer
-
Test manager
-
Software development engineer in test (SDET)
Software Testing Advancement Opportunities
With CTFL certification, you can explore a wide range of advancement opportunities in the field of software testing, including:
-
Leading testing projects
-
Mentoring junior testers
-
Implementing best practices
-
Contributing to process improvements
Software Testing Career Growth
With CTFL certification, you can pave the way for long-term career growth and success in the dynamic and ever-evolving field of software testing. By continuously expanding your knowledge and skills, you can stay ahead of the curve and position yourself for exciting opportunities in the industry.
How to obtain CTFL certification?
We are an Education Technology company providing certification training courses to accelerate careers of working professionals worldwide. We impart training through instructor-led classroom workshops, instructor-led live virtual training sessions, and self-paced e-learning courses.
We have successfully conducted training sessions in 108 countries across the globe and enabled thousands of working professionals to enhance the scope of their careers.
Our enterprise training portfolio includes in-demand and globally recognized certification training courses in Project Management, Quality Management, Business Analysis, IT Service management, Agile and Scrum, Cyber Security, Data Science, and Emerging Technologies. Download our Enterprise Training Catalog from https://www.icertglobal.com/corporate-training-for-enterprises.php
Popular Courses include:
-
Project Management: PMP, CAPM ,PMI RMP
-
Quality Management: Six Sigma Black Belt ,Lean Six Sigma Green Belt, Lean Management, Minitab,CMMI
-
Business Analysis: CBAP, CCBA, ECBA
-
Agile Training: PMI-ACP , CSM , CSPO
-
Scrum Training: CSM
-
DevOps
-
Program Management: PgMP
-
Cloud Technology: Exin Cloud Computing
-
Citrix Client Adminisration: Citrix Cloud Administration
The 10 top-paying certifications to target in 2024 are:
Conclusion
In conclusion, CTFL certification is a valuable asset for professionals looking to advance in software testing roles. By obtaining CTFL certification, you can enhance your skills, credibility, and career prospects, setting yourself up for long-term success and growth in the field of software testing.
Understanding Quality Control with Minitab: A Guide!!!!
In today's competitive business environment, ensuring quality control and process improvement is essential for organizations to stay ahead of the curve. One powerful tool that has gained widespread popularity for statistical analysis and data-driven decision-making is Minitab. This article will explore how Minitab software can help businesses enhance their quality management, optimize processes, and drive continuous improvement.
What is Minitab and How Does it Work?
Minitab is a powerful statistical software that provides a wide range of tools and features for quality control and process improvement. With Minitab, users can perform statistical analysis, data visualization, and hypothesis testing to identify trends, patterns, and insights in their data. From quality assurance to process optimization, Minitab offers a comprehensive suite of statistical tools to help businesses make informed decisions and drive performance improvements.
Key Features of Minitab:
Some key features of Minitab software include:
-
Statistical techniques: Minitab offers a wide range of statistical tools and techniques for analyzing data and making data-driven decisions.
-
Process monitoring: With Minitab, users can monitor processes in real-time and identify any deviations or abnormalities that may impact quality.
-
Quality inspection: Minitab allows users to conduct thorough quality inspections and ensure that products meet the required quality standards.
-
Process optimization: Minitab helps businesses identify process inefficiencies and bottlenecks, leading to process enhancement and improved productivity.
-
Continuous improvement: Minitab enables organizations to implement a culture of continuous improvement, driving efficiency and innovation in their processes.
Minitab in Action: Case Study
To better understand how companies can benefit from Minitab, let's look at a case study of a manufacturing company that utilized Minitab for quality control and process improvement. The company was experiencing high defect rates in their production line, leading to increased rework and customer complaints. By implementing Minitab for statistical analysis and process optimization, the company was able to identify the root causes of defects, implement corrective actions, and reduce defect rates by 20% within six months. This resulted in cost savings, improved customer satisfaction, and enhanced process efficiency.
Training and Resources:
For organizations looking to maximize the benefits of Minitab, training and resources are essential. Minitab offers a range of training programs, tutorials, and certifications to help users master the software and apply statistical techniques effectively. From basic Minitab techniques to advanced statistical tools, organizations can leverage Minitab's capabilities to enhance their quality management and process optimization initiatives.
How to obtain Minitab certification?
We are an Education Technology company providing certification training courses to accelerate careers of working professionals worldwide. We impart training through instructor-led classroom workshops, instructor-led live virtual training sessions, and self-paced e-learning courses.
We have successfully conducted training sessions in 108 countries across the globe and enabled thousands of working professionals to enhance the scope of their careers.
Our enterprise training portfolio includes in-demand and globally recognized certification training courses in Project Management, Quality Management, Business Analysis, IT Service Management, Agile and Scrum, Cyber Security, Data Science, and Emerging Technologies. Download our Enterprise Training Catalog from https://www.icertglobal.com/corporate-training-for-enterprises.php
Popular Courses include:
-
Project Management: PMP, CAPM ,PMI RMP
-
Quality Management: Six Sigma Black Belt ,Lean Six Sigma Green Belt, Lean Management, Minitab,CMMI
-
Business Analysis: CBAP, CCBA, ECBA
-
Agile Training: PMI-ACP , CSM , CSPO
-
Scrum Training: CSM
-
DevOps
-
Program Management: PgMP
-
Cloud Technology: Exin Cloud Computing
-
Citrix Client Adminisration: Citrix Cloud Administration
The 10 top-paying certifications to target in 2024 are:
Conclusion:
In conclusion, Minitab is a powerful tool for quality control and process improvement, offering a wide range of statistical tools and techniques to help businesses drive performance improvements. From quality inspection to process monitoring, Minitab can help organizations optimize their processes, ensure quality standards, and achieve continuous improvement. By leveraging Minitab's capabilities and training resources, businesses can enhance their quality management practices, boost efficiency, and stay ahead of the competition in today's dynamic business landscape.
Read More
In today's competitive business environment, ensuring quality control and process improvement is essential for organizations to stay ahead of the curve. One powerful tool that has gained widespread popularity for statistical analysis and data-driven decision-making is Minitab. This article will explore how Minitab software can help businesses enhance their quality management, optimize processes, and drive continuous improvement.
What is Minitab and How Does it Work?
Minitab is a powerful statistical software that provides a wide range of tools and features for quality control and process improvement. With Minitab, users can perform statistical analysis, data visualization, and hypothesis testing to identify trends, patterns, and insights in their data. From quality assurance to process optimization, Minitab offers a comprehensive suite of statistical tools to help businesses make informed decisions and drive performance improvements.
Key Features of Minitab:
Some key features of Minitab software include:
-
Statistical techniques: Minitab offers a wide range of statistical tools and techniques for analyzing data and making data-driven decisions.
-
Process monitoring: With Minitab, users can monitor processes in real-time and identify any deviations or abnormalities that may impact quality.
-
Quality inspection: Minitab allows users to conduct thorough quality inspections and ensure that products meet the required quality standards.
-
Process optimization: Minitab helps businesses identify process inefficiencies and bottlenecks, leading to process enhancement and improved productivity.
-
Continuous improvement: Minitab enables organizations to implement a culture of continuous improvement, driving efficiency and innovation in their processes.
Minitab in Action: Case Study
To better understand how companies can benefit from Minitab, let's look at a case study of a manufacturing company that utilized Minitab for quality control and process improvement. The company was experiencing high defect rates in their production line, leading to increased rework and customer complaints. By implementing Minitab for statistical analysis and process optimization, the company was able to identify the root causes of defects, implement corrective actions, and reduce defect rates by 20% within six months. This resulted in cost savings, improved customer satisfaction, and enhanced process efficiency.
Training and Resources:
For organizations looking to maximize the benefits of Minitab, training and resources are essential. Minitab offers a range of training programs, tutorials, and certifications to help users master the software and apply statistical techniques effectively. From basic Minitab techniques to advanced statistical tools, organizations can leverage Minitab's capabilities to enhance their quality management and process optimization initiatives.
How to obtain Minitab certification?
We are an Education Technology company providing certification training courses to accelerate careers of working professionals worldwide. We impart training through instructor-led classroom workshops, instructor-led live virtual training sessions, and self-paced e-learning courses.
We have successfully conducted training sessions in 108 countries across the globe and enabled thousands of working professionals to enhance the scope of their careers.
Our enterprise training portfolio includes in-demand and globally recognized certification training courses in Project Management, Quality Management, Business Analysis, IT Service Management, Agile and Scrum, Cyber Security, Data Science, and Emerging Technologies. Download our Enterprise Training Catalog from https://www.icertglobal.com/corporate-training-for-enterprises.php
Popular Courses include:
-
Project Management: PMP, CAPM ,PMI RMP
-
Quality Management: Six Sigma Black Belt ,Lean Six Sigma Green Belt, Lean Management, Minitab,CMMI
-
Business Analysis: CBAP, CCBA, ECBA
-
Agile Training: PMI-ACP , CSM , CSPO
-
Scrum Training: CSM
-
DevOps
-
Program Management: PgMP
-
Cloud Technology: Exin Cloud Computing
-
Citrix Client Adminisration: Citrix Cloud Administration
The 10 top-paying certifications to target in 2024 are:
Conclusion:
In conclusion, Minitab is a powerful tool for quality control and process improvement, offering a wide range of statistical tools and techniques to help businesses drive performance improvements. From quality inspection to process monitoring, Minitab can help organizations optimize their processes, ensure quality standards, and achieve continuous improvement. By leveraging Minitab's capabilities and training resources, businesses can enhance their quality management practices, boost efficiency, and stay ahead of the competition in today's dynamic business landscape.
The Ultimate Minitab Certification Study Plan for Success
Are you looking to boost your career in data analysis and statistics? Obtaining a Minitab certification can be a great way to demonstrate your expertise and proficiency in using this powerful statistical software. However, preparing for the Minitab certification exam can be a daunting task. That's why it's essential to have a structured study plan in place to ensure success. In this article, we'll provide you with a comprehensive guide on how to create the ultimate Minitab certification study plan to help you ace the exam with confidence.
Understanding the Minitab Certification Process
Before diving into your study plan, it's crucial to first understand the Minitab certification process. The Minitab certification exam tests your knowledge and skills in using the software for statistical analysis, quality improvement, and process optimization. To become certified, you must pass the exam, which consists of multiple-choice questions designed to assess your proficiency in various aspects of Minitab.
Creating a Study Schedule
The key to success in preparing for the Minitab certification exam is to create a well-structured study schedule. Start by assessing your current knowledge and skills in using Minitab and identify areas where you need to improve. Divide your study schedule into manageable sections, focusing on different topics such as data analysis, hypothesis testing, regression analysis, and more.
Minitab Certification Exam Tips
To help you prepare effectively for the Minitab certification exam, here are some valuable tips to keep in mind:
-
Familiarize yourself with the Minitab interface and features
-
Practice using the software regularly to enhance your proficiency
-
Review sample exam questions to understand the format and types of questions
-
Join a study group or online course to supplement your studying
-
Utilize resources such as study guides, practice exams, and tutorials
-
Stay organized and track your progress to ensure you cover all necessary topics
Best Practices for Minitab Certification
In addition to creating a study schedule and following exam tips, here are some best practices to consider when preparing for the Minitab certification:
-
Set realistic goals and timelines for your study plan
-
Take breaks and allow yourself time to rest and recharge
-
Seek guidance from experienced professionals or mentors in the field
-
Stay motivated and committed to your study plan
-
Practice problem-solving and critical thinking skills
-
Stay updated on the latest trends and developments in data analysis and statistics
Minitab Certification Study Materials
As you prepare for the Minitab certification exam, you'll need access to a variety of study materials to help you review and practice. Some essential resources to consider include:
-
Official Minitab study guides and practice exams
-
Online tutorials and video tutorials
-
Reference books on statistics and data analysis
-
Interactive online courses and workshops
-
Study aids such as flashcards and cheat sheets
How to obtain Quality Management Certification?
We are an Education Technology company providing certification training courses to accelerate careers of working professionals worldwide. We impart training through instructor-led classroom workshops, instructor-led live virtual training sessions, and self-paced e-learning courses.
We have successfully conducted training sessions in 108 countries across the globe and enabled thousands of working professionals to enhance the scope of their careers.
Our enterprise training portfolio includes in-demand and globally recognized certification training courses in Project Management, Quality Management, Business Analysis, IT Service Management, Agile and Scrum, Cyber Security, Data Science, and Emerging Technologies. Download our Enterprise Training Catalog from https://www.icertglobal.com/corporate-training-for-enterprises.php
Popular Courses include:
-
Project Management: PMP, CAPM ,PMI RMP
-
Quality Management: Six Sigma Black Belt ,Lean Six Sigma Green Belt, Lean Management, Minitab,CMMI
-
Business Analysis: CBAP, CCBA, ECBA
-
Agile Training: PMI-ACP , CSM , CSPO
-
Scrum Training: CSM
-
DevOps
-
Program Management: PgMP
-
Cloud Technology: Exin Cloud Computing
-
Citrix Client Adminisration: Citrix Cloud Administration
Top 10 – Certification Cources in 2024
Conclusion
In conclusion, preparing for the Minitab certification exam requires dedication, commitment, and a well-structured study plan. By following the tips, best practices, and utilizing the right study materials, you can enhance your chances of success and achieve your goal of becoming Minitab certified.
Read More
Are you looking to boost your career in data analysis and statistics? Obtaining a Minitab certification can be a great way to demonstrate your expertise and proficiency in using this powerful statistical software. However, preparing for the Minitab certification exam can be a daunting task. That's why it's essential to have a structured study plan in place to ensure success. In this article, we'll provide you with a comprehensive guide on how to create the ultimate Minitab certification study plan to help you ace the exam with confidence.
Understanding the Minitab Certification Process
Before diving into your study plan, it's crucial to first understand the Minitab certification process. The Minitab certification exam tests your knowledge and skills in using the software for statistical analysis, quality improvement, and process optimization. To become certified, you must pass the exam, which consists of multiple-choice questions designed to assess your proficiency in various aspects of Minitab.
Creating a Study Schedule
The key to success in preparing for the Minitab certification exam is to create a well-structured study schedule. Start by assessing your current knowledge and skills in using Minitab and identify areas where you need to improve. Divide your study schedule into manageable sections, focusing on different topics such as data analysis, hypothesis testing, regression analysis, and more.
Minitab Certification Exam Tips
To help you prepare effectively for the Minitab certification exam, here are some valuable tips to keep in mind:
-
Familiarize yourself with the Minitab interface and features
-
Practice using the software regularly to enhance your proficiency
-
Review sample exam questions to understand the format and types of questions
-
Join a study group or online course to supplement your studying
-
Utilize resources such as study guides, practice exams, and tutorials
-
Stay organized and track your progress to ensure you cover all necessary topics
Best Practices for Minitab Certification
In addition to creating a study schedule and following exam tips, here are some best practices to consider when preparing for the Minitab certification:
-
Set realistic goals and timelines for your study plan
-
Take breaks and allow yourself time to rest and recharge
-
Seek guidance from experienced professionals or mentors in the field
-
Stay motivated and committed to your study plan
-
Practice problem-solving and critical thinking skills
-
Stay updated on the latest trends and developments in data analysis and statistics
Minitab Certification Study Materials
As you prepare for the Minitab certification exam, you'll need access to a variety of study materials to help you review and practice. Some essential resources to consider include:
-
Official Minitab study guides and practice exams
-
Online tutorials and video tutorials
-
Reference books on statistics and data analysis
-
Interactive online courses and workshops
-
Study aids such as flashcards and cheat sheets
How to obtain Quality Management Certification?
We are an Education Technology company providing certification training courses to accelerate careers of working professionals worldwide. We impart training through instructor-led classroom workshops, instructor-led live virtual training sessions, and self-paced e-learning courses.
We have successfully conducted training sessions in 108 countries across the globe and enabled thousands of working professionals to enhance the scope of their careers.
Our enterprise training portfolio includes in-demand and globally recognized certification training courses in Project Management, Quality Management, Business Analysis, IT Service Management, Agile and Scrum, Cyber Security, Data Science, and Emerging Technologies. Download our Enterprise Training Catalog from https://www.icertglobal.com/corporate-training-for-enterprises.php
Popular Courses include:
-
Project Management: PMP, CAPM ,PMI RMP
-
Quality Management: Six Sigma Black Belt ,Lean Six Sigma Green Belt, Lean Management, Minitab,CMMI
-
Business Analysis: CBAP, CCBA, ECBA
-
Agile Training: PMI-ACP , CSM , CSPO
-
Scrum Training: CSM
-
DevOps
-
Program Management: PgMP
-
Cloud Technology: Exin Cloud Computing
-
Citrix Client Adminisration: Citrix Cloud Administration
Top 10 – Certification Cources in 2024
Conclusion
In conclusion, preparing for the Minitab certification exam requires dedication, commitment, and a well-structured study plan. By following the tips, best practices, and utilizing the right study materials, you can enhance your chances of success and achieve your goal of becoming Minitab certified.
DMAIC Process: The 5 Phases of Lean Sigma You Must Know
In the world of project management and quality improvement, the DMAIC process stands as a powerful tool for problem-solving and process optimization. Derived from Lean Sigma, the DMAIC process encompasses five key phases that help organizations identify and eliminate inefficiencies, reduce defects, and achieve process excellence. This article will delve into the intricacies of the DMAIC process, exploring each phase's significance and its role in driving continuous improvement.
The Lean Sigma Methodology: A Brief Overview
Before delving into the DMAIC process, it is essential to understand the foundation upon which it is built - Lean Sigma. This methodology combines the principles of Lean and Six Sigma to streamline processes, reduce waste, and achieve higher levels of efficiency and quality. Lean focuses on eliminating non-value-added activities, while Six Sigma aims to reduce process variation and defects. Together, these approaches create a formidable framework for enhancing organizational performance.
Phase 1: Define - Clearly Understanding the Problem at Hand
The first phase of the DMAIC process is the "Define" phase. In this stage, project teams work collaboratively to identify the problem, articulate the project goals, and define the scope. It is crucial to gather accurate data and thoroughly understand the current state of affairs before proceeding. By establishing a clear problem statement, the team can align their efforts towards a common objective.
Phase 2: Measure - Assessing and Analyzing Process Performance
Once the problem has been defined, it is time to gather data and measure process performance. The "Measure" phase focuses on quantifying process metrics and collecting relevant information to assess the current state. This step involves analyzing process variation, identifying potential sources of errors, and determining the most critical process parameters. Data analysis techniques like statistical process control and process capability studies are often utilized to gain deeper insights.
Phase 3: Analyze - Identifying Root Causes and Developing Solutions
The "Analyze" phase delves into the core of the problem, aiming to identify its root causes. Through techniques like root cause analysis and data-driven decision making, project teams unravel the underlying factors contributing to process inefficiencies or defects. This phase also involves evaluating potential solutions and brainstorming creative approaches to address the identified issues.
Phase 4: Improve - Implementing Solutions and Measuring Their Impact
With potential solutions identified, the next phase, "Improve," focuses on implementing process changes and monitoring their impact. It is essential to develop a detailed plan, outlining the actions required to eradicate the root causes and improve process performance. Key tools like process standardization, mistake-proofing, and continuous monitoring play a vital role in ensuring sustainable improvements.
Phase 5: Control - Sustaining Improvements Through Process Control
The final phase of the DMAIC process is "Control." Once process improvements have been implemented, it is essential to establish robust controls to prevent a relapse into previous inefficiencies. This phase involves designing control plans, establishing process monitoring mechanisms, and training individuals to sustain the improvements achieved. By continuously measuring and managing process performance, organizations can ensure long-term success.
How to obtain Lean Management Certification?
We are an Education Technology company providing certification training courses to accelerate careers of working professionals worldwide. We impart training through instructor-led classroom workshops, instructor-led live virtual training sessions, and self-paced e-learning courses.
We have successfully conducted training sessions in 108 countries across the globe and enabled thousands of working professionals to enhance the scope of their careers.
Our enterprise training portfolio includes in-demand and globally recognized certification training courses in Project Management, Quality Management, Business Analysis, IT Service Management, Agile and Scrum, Cyber Security, Data Science, and Emerging Technologies. Download our Enterprise Training Catalog from https://www.icertglobal.com/corporate-training-for-enterprises.php
Popular Courses include:
- Project Management: PMP, CAPM ,PMI RMP
- Quality Management: Six Sigma Black Belt ,Lean Six Sigma Green Belt, Lean Management, Minitab,CMMI
- Business Analysis: CBAP, CCBA, ECBA
- Agile Training: PMI-ACP , CSM , CSPO
- Scrum Training: CSM
- DevOps
- Program Management: PgMP
- Cloud Technology: Exin Cloud Computing
- Citrix Client Adminisration: Citrix Cloud Administration
Conclusion
The DMAIC process provides organizations with a structured approach to problem-solving and process improvement. By following the five phases - Define, Measure, Analyze, Improve, and Control - teams can drive continuous improvement, enhance process efficiency, and achieve substantial quality improvements. Incorporating Lean Sigma principles and methodologies into project management practices can lead to significant gains in terms of customer satisfaction, cost reduction, and overall operational excellence. Embrace the DMAIC process, and embark on a journey towards process excellence and improved organizational performance.
Read More
In the world of project management and quality improvement, the DMAIC process stands as a powerful tool for problem-solving and process optimization. Derived from Lean Sigma, the DMAIC process encompasses five key phases that help organizations identify and eliminate inefficiencies, reduce defects, and achieve process excellence. This article will delve into the intricacies of the DMAIC process, exploring each phase's significance and its role in driving continuous improvement.
The Lean Sigma Methodology: A Brief Overview
Before delving into the DMAIC process, it is essential to understand the foundation upon which it is built - Lean Sigma. This methodology combines the principles of Lean and Six Sigma to streamline processes, reduce waste, and achieve higher levels of efficiency and quality. Lean focuses on eliminating non-value-added activities, while Six Sigma aims to reduce process variation and defects. Together, these approaches create a formidable framework for enhancing organizational performance.
Phase 1: Define - Clearly Understanding the Problem at Hand
The first phase of the DMAIC process is the "Define" phase. In this stage, project teams work collaboratively to identify the problem, articulate the project goals, and define the scope. It is crucial to gather accurate data and thoroughly understand the current state of affairs before proceeding. By establishing a clear problem statement, the team can align their efforts towards a common objective.
Phase 2: Measure - Assessing and Analyzing Process Performance
Once the problem has been defined, it is time to gather data and measure process performance. The "Measure" phase focuses on quantifying process metrics and collecting relevant information to assess the current state. This step involves analyzing process variation, identifying potential sources of errors, and determining the most critical process parameters. Data analysis techniques like statistical process control and process capability studies are often utilized to gain deeper insights.
Phase 3: Analyze - Identifying Root Causes and Developing Solutions
The "Analyze" phase delves into the core of the problem, aiming to identify its root causes. Through techniques like root cause analysis and data-driven decision making, project teams unravel the underlying factors contributing to process inefficiencies or defects. This phase also involves evaluating potential solutions and brainstorming creative approaches to address the identified issues.
Phase 4: Improve - Implementing Solutions and Measuring Their Impact
With potential solutions identified, the next phase, "Improve," focuses on implementing process changes and monitoring their impact. It is essential to develop a detailed plan, outlining the actions required to eradicate the root causes and improve process performance. Key tools like process standardization, mistake-proofing, and continuous monitoring play a vital role in ensuring sustainable improvements.
Phase 5: Control - Sustaining Improvements Through Process Control
The final phase of the DMAIC process is "Control." Once process improvements have been implemented, it is essential to establish robust controls to prevent a relapse into previous inefficiencies. This phase involves designing control plans, establishing process monitoring mechanisms, and training individuals to sustain the improvements achieved. By continuously measuring and managing process performance, organizations can ensure long-term success.
How to obtain Lean Management Certification?
We are an Education Technology company providing certification training courses to accelerate careers of working professionals worldwide. We impart training through instructor-led classroom workshops, instructor-led live virtual training sessions, and self-paced e-learning courses.
We have successfully conducted training sessions in 108 countries across the globe and enabled thousands of working professionals to enhance the scope of their careers.
Our enterprise training portfolio includes in-demand and globally recognized certification training courses in Project Management, Quality Management, Business Analysis, IT Service Management, Agile and Scrum, Cyber Security, Data Science, and Emerging Technologies. Download our Enterprise Training Catalog from https://www.icertglobal.com/corporate-training-for-enterprises.php
Popular Courses include:
- Project Management: PMP, CAPM ,PMI RMP
- Quality Management: Six Sigma Black Belt ,Lean Six Sigma Green Belt, Lean Management, Minitab,CMMI
- Business Analysis: CBAP, CCBA, ECBA
- Agile Training: PMI-ACP , CSM , CSPO
- Scrum Training: CSM
- DevOps
- Program Management: PgMP
- Cloud Technology: Exin Cloud Computing
- Citrix Client Adminisration: Citrix Cloud Administration
Conclusion
The DMAIC process provides organizations with a structured approach to problem-solving and process improvement. By following the five phases - Define, Measure, Analyze, Improve, and Control - teams can drive continuous improvement, enhance process efficiency, and achieve substantial quality improvements. Incorporating Lean Sigma principles and methodologies into project management practices can lead to significant gains in terms of customer satisfaction, cost reduction, and overall operational excellence. Embrace the DMAIC process, and embark on a journey towards process excellence and improved organizational performance.
Quality Management: Definition, Importance, Components!!
Introduction
Quality management plays a crucial role in ensuring the success of businesses across various industries. It involves a systematic approach to maintaining and improving the quality of products, services, and processes. In this article, we will explore the definition, importance, and components of quality management and delve into the concept of Total Quality Management.
Quality Management System (QMS)
A Quality Management System (QMS) is the framework that enables organizations to establish and uphold their commitment to quality. It encompasses the policies, procedures, and processes that guide the organization in achieving its quality objectives. The QMS serves as the backbone of quality management, providing a structured framework for identifying, controlling, and improving quality-related activities.
Importance of Quality Management
Quality management is of utmost importance for businesses, as it offers several significant benefits. Let's take a closer look at why quality management is vital:
1. Customer Satisfaction
In today's competitive market, customer satisfaction is a top priority for businesses. Quality management ensures that products and services meet or exceed customer expectations, leading to increased satisfaction and loyalty. Satisfied customers not only become repeat customers but also act as brand advocates, attracting new customers through positive word-of-mouth.
2. Cost Reduction
Implementing quality management practices can result in cost reductions for businesses. By identifying and eliminating inefficiencies, defects, and non-value-added activities, organizations can streamline their processes and improve overall productivity. This, in turn, leads to lower production costs, reduced waste, and increased profitability.
3. Brand Reputation
Maintaining a strong brand reputation is vital for businesses to thrive in today's competitive landscape. Quality management helps organizations consistently deliver high-quality products and services, earning them a favorable reputation among customers, partners, and stakeholders. A positive brand image fosters trust, credibility, and long-term success.
4. Compliance and Risk Mitigation
Compliance with industry standards, regulations, and quality requirements is critical for businesses to avoid legal liabilities and penalties. Quality management ensures adherence to these standards, reducing the risk of non-compliance and associated risks. By identifying and mitigating potential risks, organizations can proactively protect their interests and reputation.
Quality Components
Quality management involves various components that collectively contribute to achieving high standards of quality. Let's explore some key quality components:
1. Quality Planning
Quality planning involves defining quality standards, setting objectives, and determining the processes required to meet those standards. It includes identifying customer requirements, establishing quality metrics, and establishing a framework for continuous improvement.
2. Quality Assurance
Quality assurance focuses on preventing defects and ensuring compliance with established quality standards. It involves the implementation of processes, procedures, and controls to verify that products and services meet quality requirements. Quality audits are often conducted to assess the effectiveness of quality assurance activities.
3. Quality Control
Quality control is the process of monitoring and inspecting products, services, and processes to ensure they meet predetermined quality standards. It involves activities such as inspections, testing, and data analysis to detect and correct any deviations from the desired quality level.
4. Continuous Improvement
Continuous improvement is a fundamental concept in quality management, aiming to enhance processes, products, and services over time. It involves regular evaluation, identification of areas for improvement, and the implementation of measures to drive ongoing progress. Continuous improvement fosters innovation, efficiency, and customer satisfaction.
Total Quality Management (TQM)
Total Quality Management (TQM) is a comprehensive approach to quality management that emphasizes the involvement of every individual in an organization. It integrates all aspects of quality management, focusing on meeting customer needs and achieving organizational goals. TQM encourages a culture of continuous improvement, teamwork, and employee empowerment.
How to obtain Quality Management certification?
We are an Education Technology company providing certification training courses to accelerate careers of working professionals worldwide. We impart training through instructor-led classroom workshops, instructor-led live virtual training sessions, and self-paced e-learning courses.
We have successfully conducted training sessions in 108 countries across the globe and enabled thousands of working professionals to enhance the scope of their careers.
Our enterprise training portfolio includes in-demand and globally recognized certification training courses in Project Management, Quality Management, Business Analysis, IT Service Management, Agile and Scrum, Cyber Security, Data Science, and Emerging Technologies. Download our Enterprise Training Catalog from https://www.icertglobal.com/corporate-training-for-enterprises.php
Popular Courses include:
- Project Management: PMP, CAPM ,PMI RMP
- Quality Management: Six Sigma Black Belt ,Lean Six Sigma Green Belt, Lean Management, Minitab,CMMI
- Business Analysis: CBAP, CCBA, ECBA
- Agile Training: PMI-ACP , CSM , CSPO
- Scrum Training: CSM
- DevOps
- Program Management: PgMP
- Cloud Technology: Exin Cloud Computing
- Citrix Client Adminisration: Citrix Cloud Administration
- Salesforce : SALESFORCE PLATFORM DEVELOPER
Conclusion
Quality management is a critical aspect of business success, ensuring customer satisfaction, cost reduction, brand reputation, and compliance. By implementing a robust Quality Management System and focusing on key quality components, organizations can maintain high standards and drive continuous improvement. Embracing the principles of Total Quality Management further enhances the effectiveness of quality management practices. Upholding quality as a top priority is essential for businesses aiming to thrive in today's competitive market landscape.
Read More
Introduction
Quality management plays a crucial role in ensuring the success of businesses across various industries. It involves a systematic approach to maintaining and improving the quality of products, services, and processes. In this article, we will explore the definition, importance, and components of quality management and delve into the concept of Total Quality Management.
Quality Management System (QMS)
A Quality Management System (QMS) is the framework that enables organizations to establish and uphold their commitment to quality. It encompasses the policies, procedures, and processes that guide the organization in achieving its quality objectives. The QMS serves as the backbone of quality management, providing a structured framework for identifying, controlling, and improving quality-related activities.
Importance of Quality Management
Quality management is of utmost importance for businesses, as it offers several significant benefits. Let's take a closer look at why quality management is vital:
1. Customer Satisfaction
In today's competitive market, customer satisfaction is a top priority for businesses. Quality management ensures that products and services meet or exceed customer expectations, leading to increased satisfaction and loyalty. Satisfied customers not only become repeat customers but also act as brand advocates, attracting new customers through positive word-of-mouth.
2. Cost Reduction
Implementing quality management practices can result in cost reductions for businesses. By identifying and eliminating inefficiencies, defects, and non-value-added activities, organizations can streamline their processes and improve overall productivity. This, in turn, leads to lower production costs, reduced waste, and increased profitability.
3. Brand Reputation
Maintaining a strong brand reputation is vital for businesses to thrive in today's competitive landscape. Quality management helps organizations consistently deliver high-quality products and services, earning them a favorable reputation among customers, partners, and stakeholders. A positive brand image fosters trust, credibility, and long-term success.
4. Compliance and Risk Mitigation
Compliance with industry standards, regulations, and quality requirements is critical for businesses to avoid legal liabilities and penalties. Quality management ensures adherence to these standards, reducing the risk of non-compliance and associated risks. By identifying and mitigating potential risks, organizations can proactively protect their interests and reputation.
Quality Components
Quality management involves various components that collectively contribute to achieving high standards of quality. Let's explore some key quality components:
1. Quality Planning
Quality planning involves defining quality standards, setting objectives, and determining the processes required to meet those standards. It includes identifying customer requirements, establishing quality metrics, and establishing a framework for continuous improvement.
2. Quality Assurance
Quality assurance focuses on preventing defects and ensuring compliance with established quality standards. It involves the implementation of processes, procedures, and controls to verify that products and services meet quality requirements. Quality audits are often conducted to assess the effectiveness of quality assurance activities.
3. Quality Control
Quality control is the process of monitoring and inspecting products, services, and processes to ensure they meet predetermined quality standards. It involves activities such as inspections, testing, and data analysis to detect and correct any deviations from the desired quality level.
4. Continuous Improvement
Continuous improvement is a fundamental concept in quality management, aiming to enhance processes, products, and services over time. It involves regular evaluation, identification of areas for improvement, and the implementation of measures to drive ongoing progress. Continuous improvement fosters innovation, efficiency, and customer satisfaction.
Total Quality Management (TQM)
Total Quality Management (TQM) is a comprehensive approach to quality management that emphasizes the involvement of every individual in an organization. It integrates all aspects of quality management, focusing on meeting customer needs and achieving organizational goals. TQM encourages a culture of continuous improvement, teamwork, and employee empowerment.
How to obtain Quality Management certification?
We are an Education Technology company providing certification training courses to accelerate careers of working professionals worldwide. We impart training through instructor-led classroom workshops, instructor-led live virtual training sessions, and self-paced e-learning courses.
We have successfully conducted training sessions in 108 countries across the globe and enabled thousands of working professionals to enhance the scope of their careers.
Our enterprise training portfolio includes in-demand and globally recognized certification training courses in Project Management, Quality Management, Business Analysis, IT Service Management, Agile and Scrum, Cyber Security, Data Science, and Emerging Technologies. Download our Enterprise Training Catalog from https://www.icertglobal.com/corporate-training-for-enterprises.php
Popular Courses include:
- Project Management: PMP, CAPM ,PMI RMP
- Quality Management: Six Sigma Black Belt ,Lean Six Sigma Green Belt, Lean Management, Minitab,CMMI
- Business Analysis: CBAP, CCBA, ECBA
- Agile Training: PMI-ACP , CSM , CSPO
- Scrum Training: CSM
- DevOps
- Program Management: PgMP
- Cloud Technology: Exin Cloud Computing
- Citrix Client Adminisration: Citrix Cloud Administration
- Salesforce : SALESFORCE PLATFORM DEVELOPER
Conclusion
Quality management is a critical aspect of business success, ensuring customer satisfaction, cost reduction, brand reputation, and compliance. By implementing a robust Quality Management System and focusing on key quality components, organizations can maintain high standards and drive continuous improvement. Embracing the principles of Total Quality Management further enhances the effectiveness of quality management practices. Upholding quality as a top priority is essential for businesses aiming to thrive in today's competitive market landscape.
Top 10 Lean Six Sigma certifications to boost careers!!
As organizations worldwide continue to prioritize operational excellence and process improvement, Lean Six Sigma certifications have become integral for professionals seeking to contribute to these objectives. In the dynamic landscape of 2024, the demand for skilled practitioners is higher than ever, making the choice of the right certification crucial. This guide explores the "10 Best Lean Six Sigma Certifications for 2024," presenting a curated list of programs renowned for their effectiveness in equipping individuals with the skills and knowledge essential for Lean and Six Sigma methodologies. From Six Sigma Green Belt to Black Belt certifications, this comprehensive overview encompasses accredited courses, training programs, and reviews to aid professionals in making informed decisions about the most suitable Lean Six Sigma certification for their career advancement and organizational impact in the evolving landscape of quality management.
Table of contents
-
Certification Overview and Criteria
-
Program Features and Curriculum
-
Accreditation and Industry Recognition
-
Candidate Reviews and Testimonials
-
Cost and Accessibility
-
Conclusion
Certification Overview and Criteria
In examining the "10 Best Lean Six Sigma Certifications for 2024," a comprehensive understanding begins with a detailed certification overview and criteria. This section provides a concise yet thorough examination of each selected certification, delving into the unique aspects that contribute to its recognition. Criteria for inclusion consider factors such as accreditation by reputable bodies, industry relevance, and the overall comprehensiveness of the certification programs. By offering a comprehensive snapshot of each certification, professionals and aspiring Lean Six Sigma practitioners can gain insights into the distinguishing features that make these programs stand out in the competitive landscape. This overview aims to empower individuals with the information needed to make informed choices aligned with their career goals and the ever-evolving demands of quality management in 2024.
Program Features and Curriculum
Exploring the "10 Best Lean Six Sigma Certifications for 2024" necessitates a closer examination of the program features and curriculum associated with each certification. This section provides a detailed insight into the unique attributes and highlights of the selected certifications, elucidating the distinctive elements that contribute to their efficacy. The analysis encompasses a thorough exploration of the curriculum, outlining key topics covered, training methodologies employed, and any specialized components that distinguish each program. Whether it is the emphasis on statistical analysis, project management methodologies, or industry-specific applications, this section aims to offer professionals a comprehensive understanding of the learning experiences provided by each certification. By delving into the program features and curriculum details, individuals can make informed decisions tailored to their specific skill development needs and professional objectives within the realm of Lean Six Sigma in 2024.
Accreditation and Industry Recognition
The critical aspect of accreditation and industry recognition plays a pivotal role in discerning the efficacy and credibility of the "10 Best Lean Six Sigma Certifications for 2024." This section meticulously examines the accreditation bodies affiliated with each certification, underscoring the importance of adherence to recognized standards in the field. Additionally, it highlights any industry endorsements or acknowledgments that contribute to the overall esteem and trustworthiness of the certifications. Understanding the accreditation and industry recognition associated with each program not only assures professionals of the certifications' legitimacy but also provides valuable insights into their alignment with industry best practices. This knowledge empowers individuals to make informed choices, selecting certifications that hold sway not only within the realm of Lean Six Sigma but also within the broader professional landscape in 2024.
Candidate Reviews and Testimonials
In the evaluation of the "10 Best Lean Six Sigma Certifications for 2024," a crucial dimension is offered through candidate reviews and testimonials. This section captures the experiential insights of individuals who have undergone the selected Lean Six Sigma certifications, providing valuable feedback on the effectiveness, practicality, and overall impact of the programs. The testimonials offer a firsthand account of candidates' experiences, shedding light on the strengths and potential areas for improvement within each certification. This qualitative aspect serves as a guide for prospective candidates, offering them a glimpse into the real-world applicability and satisfaction levels associated with each certification. By considering the perspectives of those who have completed the programs, professionals can make informed decisions aligned with their specific learning preferences and career objectives in the dynamic landscape of Lean Six Sigma in 2024.
Cost and Accessibility
The evaluation of the "10 Best Lean Six Sigma Certifications for 2024" extends to the critical considerations of cost and accessibility. This section provides a comprehensive overview of the financial investment required for each certification, taking into account registration fees, study materials, and any additional costs associated with examinations. Simultaneously, the accessibility factors, including online availability, training locations, and program flexibility, are thoroughly examined. Understanding the cost implications and accessibility features ensures that professionals can align their budgetary constraints and logistical considerations with the certification that best suits their needs. This insight allows individuals to make informed decisions, considering not only the financial aspects but also the convenience and adaptability of each Lean Six Sigma certification in the evolving professional landscape of 2024.
Conclusion
In conclusion, the exploration of the "10 Best Lean Six Sigma Certifications for 2024" provides professionals and aspiring practitioners with a holistic understanding of the top programs in the field. By delving into the certification overview and criteria, program features and curriculum, accreditation and industry recognition, candidate reviews and testimonials, as well as cost and accessibility considerations, this guide equips individuals with the necessary insights to make informed choices tailored to their specific career goals. Each certification's unique attributes, learning methodologies, and industry endorsements contribute to a nuanced understanding of their relevance in the dynamic landscape of quality management. As professionals strive for excellence in Lean Six Sigma practices, this comprehensive guide serves as a valuable resource, empowering individuals to select certifications that not only meet the highest standards but also resonate with their individual learning preferences and professional aspirations in 2024.
Read More
As organizations worldwide continue to prioritize operational excellence and process improvement, Lean Six Sigma certifications have become integral for professionals seeking to contribute to these objectives. In the dynamic landscape of 2024, the demand for skilled practitioners is higher than ever, making the choice of the right certification crucial. This guide explores the "10 Best Lean Six Sigma Certifications for 2024," presenting a curated list of programs renowned for their effectiveness in equipping individuals with the skills and knowledge essential for Lean and Six Sigma methodologies. From Six Sigma Green Belt to Black Belt certifications, this comprehensive overview encompasses accredited courses, training programs, and reviews to aid professionals in making informed decisions about the most suitable Lean Six Sigma certification for their career advancement and organizational impact in the evolving landscape of quality management.
Table of contents
-
Certification Overview and Criteria
-
Program Features and Curriculum
-
Accreditation and Industry Recognition
-
Candidate Reviews and Testimonials
-
Cost and Accessibility
-
Conclusion
Certification Overview and Criteria
In examining the "10 Best Lean Six Sigma Certifications for 2024," a comprehensive understanding begins with a detailed certification overview and criteria. This section provides a concise yet thorough examination of each selected certification, delving into the unique aspects that contribute to its recognition. Criteria for inclusion consider factors such as accreditation by reputable bodies, industry relevance, and the overall comprehensiveness of the certification programs. By offering a comprehensive snapshot of each certification, professionals and aspiring Lean Six Sigma practitioners can gain insights into the distinguishing features that make these programs stand out in the competitive landscape. This overview aims to empower individuals with the information needed to make informed choices aligned with their career goals and the ever-evolving demands of quality management in 2024.
Program Features and Curriculum
Exploring the "10 Best Lean Six Sigma Certifications for 2024" necessitates a closer examination of the program features and curriculum associated with each certification. This section provides a detailed insight into the unique attributes and highlights of the selected certifications, elucidating the distinctive elements that contribute to their efficacy. The analysis encompasses a thorough exploration of the curriculum, outlining key topics covered, training methodologies employed, and any specialized components that distinguish each program. Whether it is the emphasis on statistical analysis, project management methodologies, or industry-specific applications, this section aims to offer professionals a comprehensive understanding of the learning experiences provided by each certification. By delving into the program features and curriculum details, individuals can make informed decisions tailored to their specific skill development needs and professional objectives within the realm of Lean Six Sigma in 2024.
Accreditation and Industry Recognition
The critical aspect of accreditation and industry recognition plays a pivotal role in discerning the efficacy and credibility of the "10 Best Lean Six Sigma Certifications for 2024." This section meticulously examines the accreditation bodies affiliated with each certification, underscoring the importance of adherence to recognized standards in the field. Additionally, it highlights any industry endorsements or acknowledgments that contribute to the overall esteem and trustworthiness of the certifications. Understanding the accreditation and industry recognition associated with each program not only assures professionals of the certifications' legitimacy but also provides valuable insights into their alignment with industry best practices. This knowledge empowers individuals to make informed choices, selecting certifications that hold sway not only within the realm of Lean Six Sigma but also within the broader professional landscape in 2024.
Candidate Reviews and Testimonials
In the evaluation of the "10 Best Lean Six Sigma Certifications for 2024," a crucial dimension is offered through candidate reviews and testimonials. This section captures the experiential insights of individuals who have undergone the selected Lean Six Sigma certifications, providing valuable feedback on the effectiveness, practicality, and overall impact of the programs. The testimonials offer a firsthand account of candidates' experiences, shedding light on the strengths and potential areas for improvement within each certification. This qualitative aspect serves as a guide for prospective candidates, offering them a glimpse into the real-world applicability and satisfaction levels associated with each certification. By considering the perspectives of those who have completed the programs, professionals can make informed decisions aligned with their specific learning preferences and career objectives in the dynamic landscape of Lean Six Sigma in 2024.
Cost and Accessibility
The evaluation of the "10 Best Lean Six Sigma Certifications for 2024" extends to the critical considerations of cost and accessibility. This section provides a comprehensive overview of the financial investment required for each certification, taking into account registration fees, study materials, and any additional costs associated with examinations. Simultaneously, the accessibility factors, including online availability, training locations, and program flexibility, are thoroughly examined. Understanding the cost implications and accessibility features ensures that professionals can align their budgetary constraints and logistical considerations with the certification that best suits their needs. This insight allows individuals to make informed decisions, considering not only the financial aspects but also the convenience and adaptability of each Lean Six Sigma certification in the evolving professional landscape of 2024.
Conclusion
In conclusion, the exploration of the "10 Best Lean Six Sigma Certifications for 2024" provides professionals and aspiring practitioners with a holistic understanding of the top programs in the field. By delving into the certification overview and criteria, program features and curriculum, accreditation and industry recognition, candidate reviews and testimonials, as well as cost and accessibility considerations, this guide equips individuals with the necessary insights to make informed choices tailored to their specific career goals. Each certification's unique attributes, learning methodologies, and industry endorsements contribute to a nuanced understanding of their relevance in the dynamic landscape of quality management. As professionals strive for excellence in Lean Six Sigma practices, this comprehensive guide serves as a valuable resource, empowering individuals to select certifications that not only meet the highest standards but also resonate with their individual learning preferences and professional aspirations in 2024.
Lean Six Sigma Essentials: Definition, Methodology, Benefits
Navigating the realm of employee benefits and well-being, this guide focuses on "Lean Six Sigma Essentials: Definition, Methodology, Benefits." In the landscape of professional development, Lean Six Sigma stands as a crucial methodology, seamlessly blending Lean principles and Six Sigma techniques. As we explore the methodology encompassed by DMAIC — Define, Measure, Analyze, Improve, and Control — we draw parallels to the critical elements found in employee benefits. From the optimization principles of Lean Six Sigma to the benefits it brings to organizational efficiency, this guide delves into how methodologies akin to those in employee assistance programs (EAP), disability benefits, and dental plans contribute to holistic workplace well-being. Understanding the parallels between Lean Six Sigma and critical illness cover, Social Security benefits, and even the application process for disability benefits sheds light on the comprehensive approach organizations can adopt for both professional and personal development in the ever-evolving landscape of employee benefits.
Table of contents
-
Defining Lean Six Sigma
-
Methodology Deep Dive
-
Principles at the Core
-
Techniques and Tools of Lean Six Sigma
-
Realizing the Benefits
-
Conclusion
Defining Lean Six Sigma
Defining Lean Six Sigma encompasses unraveling a methodology that combines Lean principles and Six Sigma techniques, creating a comprehensive approach to process improvement. At its core, Lean Six Sigma is a data-driven strategy designed to enhance efficiency, reduce waste, and optimize organizational processes. It integrates the principles of Lean, which focuses on minimizing waste and maximizing value for the customer, with Six Sigma, a methodology centered on minimizing variability and defects. This dual approach aims to achieve operational excellence by systematically identifying and eliminating inefficiencies within processes. The definition of Lean Six Sigma not only involves understanding its foundational concepts but also acknowledges its adaptability across various industries and sectors. As a transformative methodology, Lean Six Sigma provides organizations with the tools and frameworks needed to foster a culture of continuous improvement and achieve sustainable success.
Methodology Deep Dive
The methodology at the heart of Lean Six Sigma is a structured and systematic approach known as DMAIC, representing Define, Measure, Analyze, Improve, and Control. This methodology serves as the cornerstone for Lean Six Sigma projects, guiding practitioners through a step-by-step process of process improvement. In the "Methodology Deep Dive," we explore each phase intricately. The Define phase involves clarifying project goals and scope, setting the foundation for subsequent stages. Measurement follows, where practitioners quantify existing processes to establish baselines and identify areas for improvement. Analysis involves a comprehensive examination of data to uncover root causes and inefficiencies. Subsequently, the Improve phase focuses on implementing solutions and innovations to enhance processes. Finally, the Control phase ensures that improvements are sustained by instituting measures to monitor and manage ongoing performance. This deep dive into the DMAIC methodology provides a nuanced understanding of Lean Six Sigma's systematic approach, making it a valuable resource for practitioners aiming to drive continuous improvement within their organizations.
Principles at the Core
At the core of Lean Six Sigma are fundamental principles that shape its philosophy and guide practitioners toward effective process improvement. These principles draw from both Lean and Six Sigma methodologies, emphasizing a customer-centric approach, process optimization, and data-driven decision-making. Customer focus entails understanding and meeting customer requirements, aligning processes with customer needs, and delivering maximum value. Process optimization involves the continuous pursuit of efficiency, minimizing waste, and streamlining operations. Data-driven decision-making underscores the importance of basing decisions on factual analysis rather than assumptions. Lean Six Sigma principles collectively contribute to a holistic understanding of how organizations can achieve excellence by aligning their processes with customer expectations, continuously improving efficiency, and fostering a culture of evidence-based decision-making. These core principles not only define the ethos of Lean Six Sigma but also guide its implementation across diverse industries and contexts.
Techniques and Tools of Lean Six Sigma
The effectiveness of Lean Six Sigma lies in its arsenal of techniques and tools specifically crafted for process improvement. These methodologies are instrumental in identifying and eliminating inefficiencies, reducing defects, and optimizing organizational processes. Techniques such as value stream mapping provide a visual representation of end-to-end processes, facilitating the identification of areas for improvement. Statistical process control ensures that processes operate within acceptable limits, minimizing variation. Root cause analysis allows practitioners to delve into the underlying issues causing defects or inefficiencies. Lean Six Sigma tools like Kaizen events, Pareto charts, and Fishbone diagrams offer structured approaches to problem-solving and continuous improvement. The utilization of these techniques and tools enables organizations to undertake data-driven, systematic approaches to enhance overall process performance. This comprehensive suite of methodologies contributes to the robustness of Lean Six Sigma as a transformative strategy for achieving excellence in diverse industries and operational contexts.
Realizing the Benefits
Realizing the benefits of Lean Six Sigma extends beyond a theoretical understanding, showcasing tangible improvements that organizations can achieve through its systematic application. By embracing Lean Six Sigma, companies can streamline their processes, resulting in enhanced efficiency, reduced operational costs, and heightened overall quality. The methodology's emphasis on data-driven decision-making ensures that organizations make informed choices, leading to a more optimized workflow. Furthermore, the customer-centric approach inherent in Lean Six Sigma often results in increased customer satisfaction as products and services align more closely with customer needs and expectations. Real-world examples and case studies provide evidence of successful Lean Six Sigma implementations, illustrating how organizations have achieved remarkable transformations in various industries, from manufacturing to healthcare and beyond. As organizations navigate the dynamic landscape of quality management, Lean Six Sigma stands out as a catalyst for continuous improvement, offering a pathway to sustained success by realizing quantifiable benefits and fostering a culture of excellence.
Conclusion
In conclusion, the exploration of Lean Six Sigma, spanning its definition, methodology, principles, techniques, and benefits, reveals a robust and transformative approach to organizational excellence. The synergy of Lean principles and Six Sigma techniques, as exemplified through the DMAIC methodology, provides a systematic framework for process improvement. Core principles, such as customer focus and data-driven decision-making, underscore the methodology's ethos, guiding organizations toward efficiency and continuous improvement. The array of techniques and tools available in Lean Six Sigma equips practitioners with the means to identify and address inefficiencies, ultimately leading to streamlined operations and improved quality. The realization of benefits, including enhanced efficiency, cost reduction, and heightened customer satisfaction, is substantiated by real-world case studies, underscoring the methodology's practical impact across diverse industries. As a comprehensive strategy for excellence, Lean Six Sigma emerges not merely as a set of principles but as a transformative force that empowers organizations to navigate challenges, optimize processes, and cultivate a culture of continuous improvement in the ever-evolving landscape of quality management.
Read More
Navigating the realm of employee benefits and well-being, this guide focuses on "Lean Six Sigma Essentials: Definition, Methodology, Benefits." In the landscape of professional development, Lean Six Sigma stands as a crucial methodology, seamlessly blending Lean principles and Six Sigma techniques. As we explore the methodology encompassed by DMAIC — Define, Measure, Analyze, Improve, and Control — we draw parallels to the critical elements found in employee benefits. From the optimization principles of Lean Six Sigma to the benefits it brings to organizational efficiency, this guide delves into how methodologies akin to those in employee assistance programs (EAP), disability benefits, and dental plans contribute to holistic workplace well-being. Understanding the parallels between Lean Six Sigma and critical illness cover, Social Security benefits, and even the application process for disability benefits sheds light on the comprehensive approach organizations can adopt for both professional and personal development in the ever-evolving landscape of employee benefits.
Table of contents
-
Defining Lean Six Sigma
-
Methodology Deep Dive
-
Principles at the Core
-
Techniques and Tools of Lean Six Sigma
-
Realizing the Benefits
-
Conclusion
Defining Lean Six Sigma
Defining Lean Six Sigma encompasses unraveling a methodology that combines Lean principles and Six Sigma techniques, creating a comprehensive approach to process improvement. At its core, Lean Six Sigma is a data-driven strategy designed to enhance efficiency, reduce waste, and optimize organizational processes. It integrates the principles of Lean, which focuses on minimizing waste and maximizing value for the customer, with Six Sigma, a methodology centered on minimizing variability and defects. This dual approach aims to achieve operational excellence by systematically identifying and eliminating inefficiencies within processes. The definition of Lean Six Sigma not only involves understanding its foundational concepts but also acknowledges its adaptability across various industries and sectors. As a transformative methodology, Lean Six Sigma provides organizations with the tools and frameworks needed to foster a culture of continuous improvement and achieve sustainable success.
Methodology Deep Dive
The methodology at the heart of Lean Six Sigma is a structured and systematic approach known as DMAIC, representing Define, Measure, Analyze, Improve, and Control. This methodology serves as the cornerstone for Lean Six Sigma projects, guiding practitioners through a step-by-step process of process improvement. In the "Methodology Deep Dive," we explore each phase intricately. The Define phase involves clarifying project goals and scope, setting the foundation for subsequent stages. Measurement follows, where practitioners quantify existing processes to establish baselines and identify areas for improvement. Analysis involves a comprehensive examination of data to uncover root causes and inefficiencies. Subsequently, the Improve phase focuses on implementing solutions and innovations to enhance processes. Finally, the Control phase ensures that improvements are sustained by instituting measures to monitor and manage ongoing performance. This deep dive into the DMAIC methodology provides a nuanced understanding of Lean Six Sigma's systematic approach, making it a valuable resource for practitioners aiming to drive continuous improvement within their organizations.
Principles at the Core
At the core of Lean Six Sigma are fundamental principles that shape its philosophy and guide practitioners toward effective process improvement. These principles draw from both Lean and Six Sigma methodologies, emphasizing a customer-centric approach, process optimization, and data-driven decision-making. Customer focus entails understanding and meeting customer requirements, aligning processes with customer needs, and delivering maximum value. Process optimization involves the continuous pursuit of efficiency, minimizing waste, and streamlining operations. Data-driven decision-making underscores the importance of basing decisions on factual analysis rather than assumptions. Lean Six Sigma principles collectively contribute to a holistic understanding of how organizations can achieve excellence by aligning their processes with customer expectations, continuously improving efficiency, and fostering a culture of evidence-based decision-making. These core principles not only define the ethos of Lean Six Sigma but also guide its implementation across diverse industries and contexts.
Techniques and Tools of Lean Six Sigma
The effectiveness of Lean Six Sigma lies in its arsenal of techniques and tools specifically crafted for process improvement. These methodologies are instrumental in identifying and eliminating inefficiencies, reducing defects, and optimizing organizational processes. Techniques such as value stream mapping provide a visual representation of end-to-end processes, facilitating the identification of areas for improvement. Statistical process control ensures that processes operate within acceptable limits, minimizing variation. Root cause analysis allows practitioners to delve into the underlying issues causing defects or inefficiencies. Lean Six Sigma tools like Kaizen events, Pareto charts, and Fishbone diagrams offer structured approaches to problem-solving and continuous improvement. The utilization of these techniques and tools enables organizations to undertake data-driven, systematic approaches to enhance overall process performance. This comprehensive suite of methodologies contributes to the robustness of Lean Six Sigma as a transformative strategy for achieving excellence in diverse industries and operational contexts.
Realizing the Benefits
Realizing the benefits of Lean Six Sigma extends beyond a theoretical understanding, showcasing tangible improvements that organizations can achieve through its systematic application. By embracing Lean Six Sigma, companies can streamline their processes, resulting in enhanced efficiency, reduced operational costs, and heightened overall quality. The methodology's emphasis on data-driven decision-making ensures that organizations make informed choices, leading to a more optimized workflow. Furthermore, the customer-centric approach inherent in Lean Six Sigma often results in increased customer satisfaction as products and services align more closely with customer needs and expectations. Real-world examples and case studies provide evidence of successful Lean Six Sigma implementations, illustrating how organizations have achieved remarkable transformations in various industries, from manufacturing to healthcare and beyond. As organizations navigate the dynamic landscape of quality management, Lean Six Sigma stands out as a catalyst for continuous improvement, offering a pathway to sustained success by realizing quantifiable benefits and fostering a culture of excellence.
Conclusion
In conclusion, the exploration of Lean Six Sigma, spanning its definition, methodology, principles, techniques, and benefits, reveals a robust and transformative approach to organizational excellence. The synergy of Lean principles and Six Sigma techniques, as exemplified through the DMAIC methodology, provides a systematic framework for process improvement. Core principles, such as customer focus and data-driven decision-making, underscore the methodology's ethos, guiding organizations toward efficiency and continuous improvement. The array of techniques and tools available in Lean Six Sigma equips practitioners with the means to identify and address inefficiencies, ultimately leading to streamlined operations and improved quality. The realization of benefits, including enhanced efficiency, cost reduction, and heightened customer satisfaction, is substantiated by real-world case studies, underscoring the methodology's practical impact across diverse industries. As a comprehensive strategy for excellence, Lean Six Sigma emerges not merely as a set of principles but as a transformative force that empowers organizations to navigate challenges, optimize processes, and cultivate a culture of continuous improvement in the ever-evolving landscape of quality management.
Interactive Lean Games & Simulations Boost Lean Principles!
In the dynamic landscape of modern business and industry, organizations continually seek innovative approaches to enhance employee learning and development. One such approach gaining widespread recognition is the integration of Lean Games and Simulations as interactive tools for imparting Lean Principles. Lean, rooted in the Toyota Production System, emphasizes efficiency, waste reduction, and continuous improvement. Traditional training methods often fall short in capturing the essence of Lean thinking, making it imperative to explore alternative avenues that engage participants in a more immersive and experiential learning environment.
Lean Games and Simulations represent a departure from conventional training methodologies by providing a hands-on and interactive platform. These activities emulate real-world scenarios, allowing participants to navigate challenges, make decisions, and witness the immediate consequences of their actions. This experiential learning approach not only fosters a deeper understanding of Lean Principles but also cultivates a culture of problem-solving and collaboration within the organization.
The significance of interactive learning in the context of Lean Principles lies in its ability to bridge the gap between theory and practice. Traditional classroom instruction often struggles to convey the practical nuances of Lean thinking, whereas Lean Games and Simulations offer a dynamic space for participants to apply theoretical knowledge in simulated business contexts. This not only enhances comprehension but also equips individuals with the skills to implement Lean practices effectively in their day-to-day work.
Moreover, as organizations increasingly recognize the value of employee engagement in the learning process, Lean Games and Simulations emerge as powerful tools for fostering active participation. The gamification elements inherent in these activities, such as competition, challenges, and rewards, add an element of fun to the learning experience. This not only keeps participants motivated but also contributes to a positive and collaborative learning culture, essential for the successful adoption of Lean Principles.
In this exploration of Lean Games and Simulations, we delve into their role as catalysts for interactive learning, dissecting their impact on participant engagement, skill acquisition, and the overall integration of Lean thinking into organizational practices. As we navigate the interactive landscape of Lean education, we unveil the potential of these tools to revolutionize the way organizations approach training and development in the pursuit of Lean excellence.
Table of contents
-
Design Principles of Lean Games and Simulations
-
Engaging Participants in Lean Simulations
-
Real-world Application and Transferability
-
Measuring the Impact of Interactive Learning
-
Overcoming Challenges in Implementing Lean Games
-
Conclusion
Design Principles of Lean Games and Simulations
Creating effective Lean Games and Simulations requires a thoughtful and strategic approach that aligns with the core principles of Lean thinking. The design process encompasses various elements aimed at delivering an engaging and educational experience for participants. One fundamental principle involves the alignment of simulation scenarios with real-world Lean challenges. By mirroring actual workplace situations, participants can gain hands-on experience in applying Lean Principles to problem-solving, fostering a direct connection between theoretical concepts and practical applications.
Instructional design plays a pivotal role in shaping the effectiveness of Lean Games and Simulations. Sequencing learning activities to reflect the logical progression of Lean Principles ensures that participants grasp foundational concepts before advancing to more complex scenarios. Additionally, the inclusion of interactive elements such as decision-making exercises, problem-solving challenges, and team collaboration activities enhances the overall learning experience. Striking a balance between theoretical content and interactive engagement is crucial to maintaining participant interest and facilitating effective knowledge retention.
Simulation mechanics, including realistic feedback mechanisms, are integral to the design principles of Lean Games. Providing timely and constructive feedback allows participants to understand the consequences of their decisions within the simulated environment. This not only reinforces learning but also encourages a continuous improvement mindset, a cornerstone of Lean thinking. The incorporation of gamification elements, such as scorekeeping, rewards, and competition, adds an element of excitement to the learning process, motivating participants to actively participate and excel in Lean simulations.
Flexibility is another key design principle, allowing for adaptability to diverse learning styles and organizational contexts. Lean Games and Simulations should be scalable and customizable to accommodate various industries, business models, and levels of organizational maturity. This flexibility ensures that the interactive learning experience remains relevant and impactful, irrespective of the specific challenges or nuances faced by different participants or organizations.
The design principles of Lean Games and Simulations revolve around authenticity, instructional design, interactive engagement, feedback mechanisms, flexibility, and the judicious use of technology. When these principles are thoughtfully applied, Lean Games and Simulations become powerful tools for imparting Lean Principles, offering participants a dynamic and immersive learning journey that translates theory into practical skills within the context of their daily work.
Engaging Participants in Lean Simulations
The success of Lean Games and Simulations hinges on the ability to captivate participants and immerse them in a dynamic learning experience. Engaging participants in Lean simulations involves the strategic integration of gamification elements, collaborative activities, and mechanisms that sustain motivation throughout the training process. One crucial aspect is the incorporation of gamification, where game-like elements such as point systems, rewards, and friendly competition are seamlessly woven into the learning framework. This not only injects an element of fun but also incentivizes participants to actively participate, compete, and strive for continuous improvement in their understanding and application of Lean Principles.
Collaboration is a cornerstone of Lean thinking, and Lean Simulations provide an ideal platform to reinforce this principle. Group activities and team-based challenges foster a sense of camaraderie among participants, encouraging them to collaborate and collectively tackle simulated Lean scenarios. This collaborative approach not only mirrors real-world Lean implementations but also cultivates a culture of shared responsibility and problem-solving within the organization.
Furthermore, the dynamic nature of Lean Simulations keeps participants on their toes, preventing monotony and ensuring sustained engagement. By presenting diverse scenarios and challenges that mimic the complexities of real-world Lean environments, participants are compelled to think critically, make informed decisions, and witness the immediate impact of their actions within the simulated context. This active participation not only enhances learning retention but also instills a sense of empowerment, as participants see the tangible results of their contributions to Lean processes.
Engaging participants in Lean Simulations requires a multi-faceted approach that combines gamification, collaboration, dynamic challenges, effective communication, and timely feedback. By immersing participants in an interactive and stimulating learning environment, organizations can ensure that Lean training is not only informative but also enjoyable and conducive to the development of practical skills essential for Lean implementations in the workplace.
Real-world Application and Transferability
The effectiveness of Lean Games and Simulations lies not only in their ability to create engaging learning experiences but also in their potential to bridge the gap between theoretical knowledge and real-world application. Exploring the real-world application and transferability of skills acquired through these interactive learning methods reveals their impact on organizational efficiency and the successful implementation of Lean Principles.
One significant aspect of real-world application is the direct correlation between the scenarios presented in Lean Simulations and the challenges faced in actual workplace environments. Participants gain practical insights into applying Lean Principles to their daily tasks, making informed decisions, and addressing inefficiencies. The simulated experiences serve as a microcosm of real-world complexities, allowing individuals to navigate and understand the intricacies of Lean implementations within the context of their specific roles and responsibilities.
Case studies and success stories provide tangible evidence of how skills cultivated in Lean Games and Simulations seamlessly translate into improved processes and outcomes. Examining instances where organizations have leveraged the acquired knowledge to streamline operations, reduce waste, and enhance overall efficiency underscores the practical impact of interactive learning. The transferability of skills becomes evident as participants bring their newfound understanding of Lean thinking into their roles, contributing to a culture of continuous improvement.
The scalability and adaptability of skills learned in Lean Simulations across diverse contexts and industries underscore the transferability of these competencies. Whether applied in manufacturing, healthcare, finance, or other sectors, the fundamental principles of Lean remain relevant. Organizations can leverage the broad applicability of Lean Games and Simulations to train employees with varied backgrounds, ensuring a consistent and standardized understanding of Lean Principles across the entire workforce.
The real-world application and transferability of skills acquired through Lean Games and Simulations are pivotal in determining the success of these interactive learning methods. The seamless integration of theoretical knowledge into practical skills, the influence on organizational culture, and the adaptability of Lean thinking across diverse industries collectively contribute to the enduring impact of these simulations on organizational efficiency and excellence.
Measuring the Impact of Interactive Learning
Assessing the impact of interactive learning, particularly in the context of Lean Games and Simulations, is a crucial step in determining the effectiveness of these innovative training methods. The measurement process involves a multifaceted approach that encompasses various dimensions to provide a comprehensive understanding of the learning outcomes and their implications for organizational performance.
One primary aspect of impact measurement is the analysis of quantitative data derived from key performance indicators (KPIs) aligned with organizational goals. These KPIs may include metrics such as improved process efficiency, reduced cycle time, decreased waste, or increased employee productivity. By establishing a clear link between the interactive learning experience and tangible organizational improvements, stakeholders can quantify the direct benefits derived from the application of Lean Principles.
Evaluation metrics, both quantitative and qualitative, offer insights into the effectiveness of Lean Games and Simulations at an individual and group level. Pre- and post-assessment tools, quizzes, and surveys provide quantitative data on knowledge acquisition and retention. Additionally, qualitative feedback mechanisms, such as participant testimonials and focus group discussions, capture the subjective experiences and perceived value of the interactive learning journey, offering a more nuanced understanding of its impact.
Long-term behavioral changes represent a critical dimension of impact measurement. Observing how participants integrate Lean thinking into their daily work, collaborate with colleagues, and contribute to continuous improvement initiatives over an extended period provides valuable insights into the lasting influence of interactive learning. This behavioral shift is indicative of a successful transfer of knowledge from simulation environments to the actual workplace.
Learning analytics and data visualization tools play a pivotal role in streamlining the impact measurement process. These tools facilitate the analysis of participant progress, engagement levels, and performance trends over time. By leveraging these data-driven insights, organizations can gain a deeper understanding of how individuals and teams evolve in their application of Lean Principles, enabling informed decisions regarding the optimization of future interactive learning initiatives.
The triangulation of quantitative and qualitative data, along with the observation of long-term behavioral changes, creates a holistic picture of the impact of interactive learning. This comprehensive approach not only validates the efficacy of Lean Games and Simulations but also informs continuous improvement efforts. Organizations can refine and tailor their interactive learning strategies based on the insights gained, ensuring the sustained development of a Lean culture and the continuous enhancement of organizational processes.
Measuring the impact of interactive learning involves a strategic combination of quantitative and qualitative assessments, behavioral observations, and the utilization of learning analytics. By adopting a comprehensive approach to impact measurement, organizations can gauge the success of Lean Games and Simulations in achieving their educational objectives and contributing to tangible improvements in organizational efficiency and performance.
Overcoming Challenges in Implementing Lean Games
The implementation of Lean Games and Simulations, while promising for interactive learning, confronts a series of challenges that organizations must adeptly navigate to optimize their effectiveness. One primary hurdle lies in the resistance to change among employees accustomed to conventional training methodologies. Introducing a paradigm shift through interactive learning necessitates a comprehensive change management plan. Clear communication of the benefits, addressing concerns, and emphasizing the practical relevance of Lean Games are essential components in overcoming this initial resistance. Engaging key stakeholders as advocates for the adoption of Lean Games contributes to building a positive narrative around this transformative learning approach.
Another critical challenge involves technological barriers that may impede the seamless integration of Lean Games. Outdated or incompatible systems can adversely affect accessibility and user experience. To overcome this, organizations should invest in user-friendly, accessible technologies aligned with the capabilities of their workforce. Simultaneously, providing comprehensive training and support ensures participants can effectively navigate the technological platforms, promoting a smoother implementation process.
Customizing Lean Games to suit diverse industry contexts and organizational nuances poses another notable challenge. To address this, organizations must develop Lean Games that are adaptable and customizable. This flexibility allows for the tailoring of scenarios to specific industry challenges, ensuring that the interactive learning experience remains relevant across varied sectors. Collaborating with subject matter experts from different domains during the design phase ensures the incorporation of industry-specific nuances.
Widespread accessibility, especially in organizations with geographically dispersed teams, presents a logistical challenge. Virtual collaboration tools can help facilitate remote participation, but additional considerations, such as scheduling sessions to accommodate different time zones and ensuring user-friendly technology, are crucial. The incorporation of asynchronous elements enables self-paced learning, addressing accessibility issues and promoting inclusivity.
Sustaining participant engagement over time is a challenge that requires ongoing attention. Participants may experience fatigue or disinterest, impacting the effectiveness of Lean Games. Regular updates to simulation scenarios, introduction of new challenges, and incorporation of participant feedback are strategies to maintain interest. Implementing a gamification strategy, including rewards, recognition, and friendly competition, serves to motivate continued engagement and reinforces the enjoyment of the learning process.
Overcoming challenges in implementing Lean Games demands a strategic and holistic approach. By addressing resistance to change, tackling technological barriers, ensuring customization for diverse contexts, promoting accessibility, and sustaining participant engagement, organizations can successfully integrate Lean Games and Simulations into their training programs. These efforts not only enhance the learning experience but also contribute to the broader goal of instilling a Lean mindset and improving organizational efficiency.
Conclusion
The exploration of Lean Games and Simulations as interactive learning tools for Lean Principles reveals a landscape rich with potential and transformative opportunities. As organizations strive to cultivate a culture of continuous improvement and operational excellence, the challenges encountered in implementing these innovative methods underscore the importance of a strategic and adaptive approach.
the journey through Lean Games and Simulations is a dynamic and evolving one. By navigating and overcoming challenges, organizations position themselves at the forefront of innovative training methodologies, fostering a culture of continuous improvement and adaptability. The commitment to addressing resistance, technological barriers, customization needs, accessibility, and sustained engagement ensures that Lean Games become not just a training tool but a catalyst for transformative change within organizations. Through these efforts, organizations can pave the way for a future where Lean thinking is ingrained in the fabric of the workforce, driving excellence and efficiency across all facets of the organizational landscape.
Read More
In the dynamic landscape of modern business and industry, organizations continually seek innovative approaches to enhance employee learning and development. One such approach gaining widespread recognition is the integration of Lean Games and Simulations as interactive tools for imparting Lean Principles. Lean, rooted in the Toyota Production System, emphasizes efficiency, waste reduction, and continuous improvement. Traditional training methods often fall short in capturing the essence of Lean thinking, making it imperative to explore alternative avenues that engage participants in a more immersive and experiential learning environment.
Lean Games and Simulations represent a departure from conventional training methodologies by providing a hands-on and interactive platform. These activities emulate real-world scenarios, allowing participants to navigate challenges, make decisions, and witness the immediate consequences of their actions. This experiential learning approach not only fosters a deeper understanding of Lean Principles but also cultivates a culture of problem-solving and collaboration within the organization.
The significance of interactive learning in the context of Lean Principles lies in its ability to bridge the gap between theory and practice. Traditional classroom instruction often struggles to convey the practical nuances of Lean thinking, whereas Lean Games and Simulations offer a dynamic space for participants to apply theoretical knowledge in simulated business contexts. This not only enhances comprehension but also equips individuals with the skills to implement Lean practices effectively in their day-to-day work.
Moreover, as organizations increasingly recognize the value of employee engagement in the learning process, Lean Games and Simulations emerge as powerful tools for fostering active participation. The gamification elements inherent in these activities, such as competition, challenges, and rewards, add an element of fun to the learning experience. This not only keeps participants motivated but also contributes to a positive and collaborative learning culture, essential for the successful adoption of Lean Principles.
In this exploration of Lean Games and Simulations, we delve into their role as catalysts for interactive learning, dissecting their impact on participant engagement, skill acquisition, and the overall integration of Lean thinking into organizational practices. As we navigate the interactive landscape of Lean education, we unveil the potential of these tools to revolutionize the way organizations approach training and development in the pursuit of Lean excellence.
Table of contents
-
Design Principles of Lean Games and Simulations
-
Engaging Participants in Lean Simulations
-
Real-world Application and Transferability
-
Measuring the Impact of Interactive Learning
-
Overcoming Challenges in Implementing Lean Games
-
Conclusion
Design Principles of Lean Games and Simulations
Creating effective Lean Games and Simulations requires a thoughtful and strategic approach that aligns with the core principles of Lean thinking. The design process encompasses various elements aimed at delivering an engaging and educational experience for participants. One fundamental principle involves the alignment of simulation scenarios with real-world Lean challenges. By mirroring actual workplace situations, participants can gain hands-on experience in applying Lean Principles to problem-solving, fostering a direct connection between theoretical concepts and practical applications.
Instructional design plays a pivotal role in shaping the effectiveness of Lean Games and Simulations. Sequencing learning activities to reflect the logical progression of Lean Principles ensures that participants grasp foundational concepts before advancing to more complex scenarios. Additionally, the inclusion of interactive elements such as decision-making exercises, problem-solving challenges, and team collaboration activities enhances the overall learning experience. Striking a balance between theoretical content and interactive engagement is crucial to maintaining participant interest and facilitating effective knowledge retention.
Simulation mechanics, including realistic feedback mechanisms, are integral to the design principles of Lean Games. Providing timely and constructive feedback allows participants to understand the consequences of their decisions within the simulated environment. This not only reinforces learning but also encourages a continuous improvement mindset, a cornerstone of Lean thinking. The incorporation of gamification elements, such as scorekeeping, rewards, and competition, adds an element of excitement to the learning process, motivating participants to actively participate and excel in Lean simulations.
Flexibility is another key design principle, allowing for adaptability to diverse learning styles and organizational contexts. Lean Games and Simulations should be scalable and customizable to accommodate various industries, business models, and levels of organizational maturity. This flexibility ensures that the interactive learning experience remains relevant and impactful, irrespective of the specific challenges or nuances faced by different participants or organizations.
The design principles of Lean Games and Simulations revolve around authenticity, instructional design, interactive engagement, feedback mechanisms, flexibility, and the judicious use of technology. When these principles are thoughtfully applied, Lean Games and Simulations become powerful tools for imparting Lean Principles, offering participants a dynamic and immersive learning journey that translates theory into practical skills within the context of their daily work.
Engaging Participants in Lean Simulations
The success of Lean Games and Simulations hinges on the ability to captivate participants and immerse them in a dynamic learning experience. Engaging participants in Lean simulations involves the strategic integration of gamification elements, collaborative activities, and mechanisms that sustain motivation throughout the training process. One crucial aspect is the incorporation of gamification, where game-like elements such as point systems, rewards, and friendly competition are seamlessly woven into the learning framework. This not only injects an element of fun but also incentivizes participants to actively participate, compete, and strive for continuous improvement in their understanding and application of Lean Principles.
Collaboration is a cornerstone of Lean thinking, and Lean Simulations provide an ideal platform to reinforce this principle. Group activities and team-based challenges foster a sense of camaraderie among participants, encouraging them to collaborate and collectively tackle simulated Lean scenarios. This collaborative approach not only mirrors real-world Lean implementations but also cultivates a culture of shared responsibility and problem-solving within the organization.
Furthermore, the dynamic nature of Lean Simulations keeps participants on their toes, preventing monotony and ensuring sustained engagement. By presenting diverse scenarios and challenges that mimic the complexities of real-world Lean environments, participants are compelled to think critically, make informed decisions, and witness the immediate impact of their actions within the simulated context. This active participation not only enhances learning retention but also instills a sense of empowerment, as participants see the tangible results of their contributions to Lean processes.
Engaging participants in Lean Simulations requires a multi-faceted approach that combines gamification, collaboration, dynamic challenges, effective communication, and timely feedback. By immersing participants in an interactive and stimulating learning environment, organizations can ensure that Lean training is not only informative but also enjoyable and conducive to the development of practical skills essential for Lean implementations in the workplace.
Real-world Application and Transferability
The effectiveness of Lean Games and Simulations lies not only in their ability to create engaging learning experiences but also in their potential to bridge the gap between theoretical knowledge and real-world application. Exploring the real-world application and transferability of skills acquired through these interactive learning methods reveals their impact on organizational efficiency and the successful implementation of Lean Principles.
One significant aspect of real-world application is the direct correlation between the scenarios presented in Lean Simulations and the challenges faced in actual workplace environments. Participants gain practical insights into applying Lean Principles to their daily tasks, making informed decisions, and addressing inefficiencies. The simulated experiences serve as a microcosm of real-world complexities, allowing individuals to navigate and understand the intricacies of Lean implementations within the context of their specific roles and responsibilities.
Case studies and success stories provide tangible evidence of how skills cultivated in Lean Games and Simulations seamlessly translate into improved processes and outcomes. Examining instances where organizations have leveraged the acquired knowledge to streamline operations, reduce waste, and enhance overall efficiency underscores the practical impact of interactive learning. The transferability of skills becomes evident as participants bring their newfound understanding of Lean thinking into their roles, contributing to a culture of continuous improvement.
The scalability and adaptability of skills learned in Lean Simulations across diverse contexts and industries underscore the transferability of these competencies. Whether applied in manufacturing, healthcare, finance, or other sectors, the fundamental principles of Lean remain relevant. Organizations can leverage the broad applicability of Lean Games and Simulations to train employees with varied backgrounds, ensuring a consistent and standardized understanding of Lean Principles across the entire workforce.
The real-world application and transferability of skills acquired through Lean Games and Simulations are pivotal in determining the success of these interactive learning methods. The seamless integration of theoretical knowledge into practical skills, the influence on organizational culture, and the adaptability of Lean thinking across diverse industries collectively contribute to the enduring impact of these simulations on organizational efficiency and excellence.
Measuring the Impact of Interactive Learning
Assessing the impact of interactive learning, particularly in the context of Lean Games and Simulations, is a crucial step in determining the effectiveness of these innovative training methods. The measurement process involves a multifaceted approach that encompasses various dimensions to provide a comprehensive understanding of the learning outcomes and their implications for organizational performance.
One primary aspect of impact measurement is the analysis of quantitative data derived from key performance indicators (KPIs) aligned with organizational goals. These KPIs may include metrics such as improved process efficiency, reduced cycle time, decreased waste, or increased employee productivity. By establishing a clear link between the interactive learning experience and tangible organizational improvements, stakeholders can quantify the direct benefits derived from the application of Lean Principles.
Evaluation metrics, both quantitative and qualitative, offer insights into the effectiveness of Lean Games and Simulations at an individual and group level. Pre- and post-assessment tools, quizzes, and surveys provide quantitative data on knowledge acquisition and retention. Additionally, qualitative feedback mechanisms, such as participant testimonials and focus group discussions, capture the subjective experiences and perceived value of the interactive learning journey, offering a more nuanced understanding of its impact.
Long-term behavioral changes represent a critical dimension of impact measurement. Observing how participants integrate Lean thinking into their daily work, collaborate with colleagues, and contribute to continuous improvement initiatives over an extended period provides valuable insights into the lasting influence of interactive learning. This behavioral shift is indicative of a successful transfer of knowledge from simulation environments to the actual workplace.
Learning analytics and data visualization tools play a pivotal role in streamlining the impact measurement process. These tools facilitate the analysis of participant progress, engagement levels, and performance trends over time. By leveraging these data-driven insights, organizations can gain a deeper understanding of how individuals and teams evolve in their application of Lean Principles, enabling informed decisions regarding the optimization of future interactive learning initiatives.
The triangulation of quantitative and qualitative data, along with the observation of long-term behavioral changes, creates a holistic picture of the impact of interactive learning. This comprehensive approach not only validates the efficacy of Lean Games and Simulations but also informs continuous improvement efforts. Organizations can refine and tailor their interactive learning strategies based on the insights gained, ensuring the sustained development of a Lean culture and the continuous enhancement of organizational processes.
Measuring the impact of interactive learning involves a strategic combination of quantitative and qualitative assessments, behavioral observations, and the utilization of learning analytics. By adopting a comprehensive approach to impact measurement, organizations can gauge the success of Lean Games and Simulations in achieving their educational objectives and contributing to tangible improvements in organizational efficiency and performance.
Overcoming Challenges in Implementing Lean Games
The implementation of Lean Games and Simulations, while promising for interactive learning, confronts a series of challenges that organizations must adeptly navigate to optimize their effectiveness. One primary hurdle lies in the resistance to change among employees accustomed to conventional training methodologies. Introducing a paradigm shift through interactive learning necessitates a comprehensive change management plan. Clear communication of the benefits, addressing concerns, and emphasizing the practical relevance of Lean Games are essential components in overcoming this initial resistance. Engaging key stakeholders as advocates for the adoption of Lean Games contributes to building a positive narrative around this transformative learning approach.
Another critical challenge involves technological barriers that may impede the seamless integration of Lean Games. Outdated or incompatible systems can adversely affect accessibility and user experience. To overcome this, organizations should invest in user-friendly, accessible technologies aligned with the capabilities of their workforce. Simultaneously, providing comprehensive training and support ensures participants can effectively navigate the technological platforms, promoting a smoother implementation process.
Customizing Lean Games to suit diverse industry contexts and organizational nuances poses another notable challenge. To address this, organizations must develop Lean Games that are adaptable and customizable. This flexibility allows for the tailoring of scenarios to specific industry challenges, ensuring that the interactive learning experience remains relevant across varied sectors. Collaborating with subject matter experts from different domains during the design phase ensures the incorporation of industry-specific nuances.
Widespread accessibility, especially in organizations with geographically dispersed teams, presents a logistical challenge. Virtual collaboration tools can help facilitate remote participation, but additional considerations, such as scheduling sessions to accommodate different time zones and ensuring user-friendly technology, are crucial. The incorporation of asynchronous elements enables self-paced learning, addressing accessibility issues and promoting inclusivity.
Sustaining participant engagement over time is a challenge that requires ongoing attention. Participants may experience fatigue or disinterest, impacting the effectiveness of Lean Games. Regular updates to simulation scenarios, introduction of new challenges, and incorporation of participant feedback are strategies to maintain interest. Implementing a gamification strategy, including rewards, recognition, and friendly competition, serves to motivate continued engagement and reinforces the enjoyment of the learning process.
Overcoming challenges in implementing Lean Games demands a strategic and holistic approach. By addressing resistance to change, tackling technological barriers, ensuring customization for diverse contexts, promoting accessibility, and sustaining participant engagement, organizations can successfully integrate Lean Games and Simulations into their training programs. These efforts not only enhance the learning experience but also contribute to the broader goal of instilling a Lean mindset and improving organizational efficiency.
Conclusion
The exploration of Lean Games and Simulations as interactive learning tools for Lean Principles reveals a landscape rich with potential and transformative opportunities. As organizations strive to cultivate a culture of continuous improvement and operational excellence, the challenges encountered in implementing these innovative methods underscore the importance of a strategic and adaptive approach.
the journey through Lean Games and Simulations is a dynamic and evolving one. By navigating and overcoming challenges, organizations position themselves at the forefront of innovative training methodologies, fostering a culture of continuous improvement and adaptability. The commitment to addressing resistance, technological barriers, customization needs, accessibility, and sustained engagement ensures that Lean Games become not just a training tool but a catalyst for transformative change within organizations. Through these efforts, organizations can pave the way for a future where Lean thinking is ingrained in the fabric of the workforce, driving excellence and efficiency across all facets of the organizational landscape.
Core Concepts of Capability Maturity Model Integration.
In the dynamic landscape of today's global business environment, organizations face the perpetual challenge of delivering high-quality products and services while striving for operational efficiency. To navigate this complex terrain, many enterprises turn to established frameworks and models that provide a structured approach to process improvement. One such powerful and widely adopted framework is the Capability Maturity Model Integration (CMMI).
CMMI stands as a beacon for organizations aspiring to enhance their capabilities and achieve a higher level of maturity in their processes. It offers a comprehensive and integrated set of best practices that guide organizations in developing and improving their processes, ultimately leading to increased performance, reliability, and customer satisfaction.
This exploration delves into the core concepts of CMMI, unraveling its intricacies and shedding light on the transformative journey that organizations embark upon when embracing this model. From understanding the fundamental principles that underpin CMMI to exploring its maturity levels and process areas, we will navigate through the key components that make CMMI a cornerstone in the pursuit of organizational excellence.
As we embark on this journey, we will demystify the terminology, delve into the rationale behind CMMI, and highlight the practical implications for organizations seeking to elevate their capabilities. Join us in unraveling the layers of CMMI, as we uncover the essence of this model and its profound impact on shaping robust, resilient, and high-performance organizations in the modern business landscape.
Table Of Contents
-
Foundations of CMMI: Defining Capability and Maturity
-
CMMI Framework Components: Processes, Practices, and Goals
-
Maturity Levels Demystified: Progressing from Chaos to Continual Improvement
-
Process Areas: Building Blocks for Effective Performance
-
Continuous and Staged Representations: Tailoring CMMI to Organizational Needs
-
CMMI Models for Different Domains: Customizing Excellence
-
Appraisals in CMMI: Evaluating and Improving Organizational Capability
-
Measuring Success: Key Performance Indicators in CMMI
-
CMMI and Agile: Bridging the Gap for Dynamic Environments
-
Challenges and Best Practices in CMMI Implementation: Lessons from the Field
-
Conclusion
Foundations of CMMI: Defining Capability and Maturity
The foundations of the Capability Maturity Model Integration (CMMI) lie in its dual emphasis on capability and maturity, which together form the bedrock of organizational excellence. In the CMMI context, capability refers to an organization's inherent ability to reliably and predictably achieve its business objectives through well-defined processes. This involves understanding and harnessing the organization's resources, processes, and technology to consistently produce desired outcomes. On the other hand, maturity signifies the evolutionary progression of an organization's processes from ad-hoc and chaotic states to well-defined, measured, and optimized levels. It encapsulates the organization's journey toward process improvement and the establishment of best practices. By defining capability and maturity as intertwined aspects, CMMI provides a holistic framework that empowers organizations to assess, enhance, and continually evolve their processes, ensuring they are not only capable of meeting current demands but are also on a trajectory of continual improvement. This foundational understanding sets the stage for organizations to embark on a purposeful journey towards operational excellence and sustained success.
CMMI Framework Components: Processes, Practices, and Goals
The Capability Maturity Model Integration (CMMI) is a robust framework built upon key components, each playing a pivotal role in guiding organizations toward process improvement and excellence. At its core are processes, the dynamic sequences of activities that transform inputs into valuable outputs. CMMI emphasizes the definition, implementation, and continuous refinement of these processes to ensure consistency, efficiency, and adaptability within an organization.
Embedded within the framework are best practices, collectively known as practices, which encapsulate the distilled wisdom of successful processes. Practices serve as guidelines, outlining the specific activities, methods, and techniques that contribute to the effective execution of processes. They provide organizations with a roadmap for achieving desired outcomes and for adapting to evolving business needs.
Furthermore, CMMI incorporates the concept of goals, which represent the high-level objectives that organizations aspire to achieve. Goals guide the selection and implementation of practices, aligning them with the organization's strategic objectives. These goals serve as benchmarks, enabling organizations to measure their progress and maturity levels across different areas.
In essence, the synergy among processes, practices, and goals within the CMMI framework forms a dynamic triad. Processes provide the operational backbone, practices offer actionable insights, and goals steer organizations towards overarching excellence. Understanding and optimizing this interconnected framework empowers organizations to systematically elevate their capabilities and achieve maturity in a structured and sustainable manner.
Maturity Levels Demystified: Progressing from Chaos to Continual Improvement
Navigating through the Maturity Levels within the Capability Maturity Model Integration (CMMI) unveils a transformative journey, guiding organizations from the tumultuous realm of chaos towards a state of perpetual enhancement. Commencing at Level 1, organizations grapple with ad-hoc processes, characterized by unpredictability and disorder. The transition to Level 2 signifies a pivotal step, introducing foundational project management practices and instilling a semblance of control.
As organizations ascend to Level 3, a culture of standardization emerges. Processes become not only defined but also tailored to specific project needs, fostering a proactive approach to process management. The journey intensifies at Level 4, where organizations employ quantitative techniques, utilizing data to gain insights and enhance predictability. This meticulous control sets the stage for the pinnacle, Level 5, characterized by an unwavering commitment to continual improvement.
At Level 5, organizations go beyond control to actively monitor, adapt, and innovate. A culture of perpetual enhancement becomes ingrained, enabling organizations not only to navigate complexity but to thrive amidst change. The narrative of progression through these maturity levels encapsulates more than a refinement of processes; it signifies a profound organizational evolution, positioning entities as dynamic and resilient contributors to the ever-evolving business landscape.
Process Areas: Building Blocks for Effective Performance
Process areas stand as the foundational building blocks within the Capability Maturity Model Integration (CMMI), forming the essential elements that underpin an organization's capability to deliver effective performance. These areas define clusters of related activities that, when executed cohesively, contribute to the achievement of specific objectives and the overall success of the organization.
Each process area within CMMI encapsulates a set of best practices and guidelines tailored to address particular aspects of an organization's operations. They serve as a roadmap, providing a structured approach for organizations to develop, implement, and continually improve their processes. These building blocks are instrumental in aligning organizational goals with practical, actionable steps, fostering consistency, efficiency, and ultimately, superior performance.
By focusing on process areas, organizations can systematically enhance their capabilities in critical areas such as project management, requirements development, and process improvement. The comprehensive nature of these areas ensures that organizations not only meet their immediate objectives but also cultivate a culture of continuous improvement, adaptability, and resilience.
Process areas within CMMI are the linchpin of effective performance. They enable organizations to elevate their processes beyond mere compliance to standards, driving them towards operational excellence and ensuring sustained success in today's dynamic and competitive business environment.
Continuous and Staged Representations: Tailoring CMMI to Organizational Needs
In the realm of Capability Maturity Model Integration (CMMI), organizations are presented with two distinct yet flexible approaches: the Continuous Representation and the Staged Representation. These representations serve as adaptable frameworks, allowing organizations to tailor their CMMI adoption to align precisely with their unique operational needs, preferences, and strategic objectives.
The Staged Representation offers a structured, milestone-oriented approach, where maturity levels are attained sequentially. This method provides a clear roadmap, guiding organizations from one level to the next, each level building upon the achievements of the previous one. It is particularly beneficial for organizations seeking a well-defined, step-by-step approach to maturity.
Conversely, the Continuous Representation allows for a more tailored and flexible adoption. Instead of following a strict sequence of maturity levels, organizations can choose to focus on specific process areas that align with their immediate priorities. This approach provides the freedom to address targeted areas of improvement without the constraint of a predetermined sequence.
The decision between these representations hinges on an organization's unique context, goals, and existing processes. The Staged Representation may be preferable for those seeking a systematic, comprehensive approach to maturity, while the Continuous Representation offers a more agile and customizable route.
Ultimately, whether an organization opts for the Staged or Continuous Representation, the key lies in aligning CMMI adoption with organizational needs. This strategic alignment empowers organizations to leverage the power of CMMI in a way that not only improves processes but also seamlessly integrates with their broader business objectives and operational landscape.
CMMI Models for Different Domains: Customizing Excellence
In the dynamic landscape of industries spanning from software development to manufacturing and beyond, a one-size-fits-all approach to process improvement may not be optimal. Recognizing this diversity, the Capability Maturity Model Integration (CMMI) provides specialized models tailored to meet the unique challenges and nuances of different domains. These domain-specific adaptations empower organizations to customize their journey toward excellence, aligning CMMI principles with the specific requirements of their industry.
For software and systems engineering, the CMMI for Development (CMMI-DEV) model offers a targeted framework. It emphasizes best practices for managing and improving development processes, ensuring the delivery of high-quality software and systems.
In the realm of services, the CMMI for Services (CMMI-SVC) model takes center stage. It addresses the distinctive aspects of service delivery, focusing on processes that enhance customer satisfaction, manage service delivery risks, and optimize service provider performance.
For organizations in the acquisition and supply chain domain, the CMMI for Acquisition (CMMI-ACQ) model becomes instrumental. It provides guidelines for effective acquisition processes, ensuring that organizations can seamlessly integrate suppliers and acquisitions into their overall improvement strategy.
The adaptability of CMMI models for different domains extends beyond these examples, encompassing areas such as product development, people management, and cybersecurity. Each tailored model incorporates industry-specific best practices while retaining the core CMMI principles, allowing organizations to reap the benefits of a proven framework while addressing the unique challenges within their domain.
Appraisals in CMMI: Evaluating and Improving Organizational Capability
In the realm of Capability Maturity Model Integration (CMMI), appraisals serve as pivotal mechanisms for evaluating and enhancing an organization's capability and maturity levels. An appraisal is a structured and rigorous assessment process conducted by certified professionals, providing organizations with insights into the effectiveness of their processes and identifying areas for improvement.
The CMMI appraisal process follows a systematic approach, examining how well an organization's processes align with the CMMI model's best practices. There are various types of appraisals, with the Standard CMMI Appraisal Method for Process Improvement (SCAMPI) being one of the most widely utilized. SCAMPI appraisals can be Class A, B, or C, each differing in scope, depth, and purpose.
Crucially, the insights gained from appraisals contribute to a continuous improvement cycle. Organizations can leverage appraisal findings to refine their processes, enhance capabilities, and align with strategic objectives. By identifying and addressing areas for improvement, organizations can systematically progress through the maturity levels of CMMI, ultimately enhancing their ability to deliver high-quality products and services.
CMMI appraisals play a dual role in evaluating and improving organizational capability. They offer a comprehensive assessment of an organization's adherence to CMMI best practices and provide a roadmap for continual enhancement, fostering a culture of proactive improvement and ensuring sustained success in today's competitive business landscape.
Measuring Success: Key Performance Indicators in CMMI
In the dynamic landscape of process improvement, the Capability Maturity Model Integration (CMMI) places a significant emphasis on quantifiable success through the use of Key Performance Indicators (KPIs). KPIs in CMMI act as essential metrics, offering organizations tangible and measurable insights into the effectiveness of their processes, the achievement of goals, and the overall progress in their journey towards maturity.
Key Performance Indicators within the CMMI framework are diverse and tailored to specific process areas. They are designed to provide a clear picture of an organization's performance, allowing for informed decision-making and targeted improvements. Some common KPIs include metrics related to project schedule adherence, defect density, and customer satisfaction.
The strategic use of KPIs extends beyond mere measurement; it serves as a catalyst for continuous improvement. By regularly assessing and analyzing these indicators, organizations can identify trends, areas of excellence, and potential challenges. This proactive approach enables them to make data-driven decisions, refine processes, and address issues promptly, fostering a culture of continual enhancement.
In summary, measuring success in CMMI relies on the strategic implementation of Key Performance Indicators. These metrics not only gauge the effectiveness of processes but also drive continuous improvement, enabling organizations to navigate the complexities of their industries with precision and ensuring a sustained trajectory of success.
CMMI and Agile: Bridging the Gap for Dynamic Environments
In the ever-evolving landscape of software development and project management, the integration of Capability Maturity Model Integration (CMMI) and Agile methodologies represents a strategic synergy aimed at addressing the challenges of dynamic and rapidly changing environments.
Agile, known for its flexibility, collaboration, and iterative approach, is favored in environments where responsiveness to change is paramount. CMMI, on the other hand, provides a structured framework for process improvement and maturity. Bridging the gap between these two seemingly distinct approaches holds the key to unlocking a holistic and adaptive model for organizational success.
Agile practices are inherently compatible with certain CMMI principles, particularly in the areas of continuous improvement, stakeholder engagement, and incremental development. By integrating Agile practices with CMMI, organizations can harness the iterative nature of Agile for rapid development cycles while leveraging CMMI's structure to ensure robust processes, measurement, and organizational learning.
This integration is not about compromising the agility of Agile or stifling innovation with rigid processes. Instead, it involves tailoring and adapting CMMI practices to complement and enhance Agile methodologies. The goal is to create a dynamic and resilient organizational culture that embraces change, values collaboration, and continually improves processes.
Ultimately, the combination of CMMI and Agile represents a powerful approach for organizations operating in dynamic environments. It harmonizes the best of both worlds, providing the structure needed for maturity and process improvement while preserving the agility required to navigate the uncertainties of today's fast-paced business landscape.
Challenges and Best Practices in CMMI Implementation: Lessons from the Field
Embarking on the journey of implementing Capability Maturity Model Integration (CMMI) is a transformative endeavor for any organization, and it comes with its unique set of challenges and valuable lessons. Drawing insights from real-world experiences, we explore both the common challenges faced during CMMI implementation and the best practices that organizations have employed to navigate these hurdles successfully.
Challenges:
Resistance to Change:
Challenge: Employees may resist changes to established processes and workflows.
Lesson: Clear communication about the benefits of CMMI, coupled with employee involvement in the process, helps alleviate resistance.
Resource Constraints:
Challenge: Limited time, budget, and personnel resources can hinder implementation efforts.
Lesson: Prioritize initiatives based on their impact and feasibility, and seek executive support for resource allocation.
Tailoring the Model:
Challenge: Adapting CMMI practices to the specific needs of the organization can be challenging.
Lesson: Tailor CMMI to fit the organization's context, ensuring relevance without compromising the integrity of the model.
Documentation Overload:
Challenge: Excessive documentation requirements can be perceived as burdensome.
Lesson: Streamline documentation processes, focusing on value-added documentation and avoiding unnecessary bureaucracy.
Lack of Organizational Buy-In:
Challenge: If the entire organization does not buy into the CMMI initiative, implementation may face resistance.
Lesson: Engage key stakeholders early, demonstrate the benefits, and foster a culture that values continuous improvement.
Best Practices:
Executive Sponsorship:
Practice: Secure executive sponsorship to drive commitment and allocate necessary resources.
Pilot Projects:
Practice: Start with pilot projects to test CMMI practices in a controlled environment before full-scale implementation.
Training and Skill Development:
Practice: Invest in training programs to enhance the skills of employees and build a competent workforce.
Continuous Communication:
Practice: Maintain open and continuous communication channels to address concerns, share successes, and reinforce the importance of CMMI.
Iterative Implementation:
Practice: Adopt an iterative approach to implementation, allowing for incremental improvements and learning from each cycle.
By acknowledging these challenges and implementing best practices derived from real-world experiences, organizations can not only overcome obstacles in their CMMI journey but also cultivate a culture of continuous improvement and excellence. These lessons from the field serve as a guide for organizations aspiring to enhance their processes and achieve greater maturity.
How to obtain Project Management certification?
We are an Education Technology company providing certification training courses to accelerate careers of working professionals worldwide. We impart training through instructor-led classroom workshops, instructor-led live virtual training sessions, and self-paced e-learning courses.
We have successfully conducted training sessions in 108 countries across the globe and enabled thousands of working professionals to enhance the scope of their careers.
Our enterprise training portfolio includes in-demand and globally recognized certification training courses in Project Management, Quality Management, Business Analysis, IT Service Management, Agile and Scrum, Cyber Security, Data Science, and Emerging Technologies. Download our Enterprise Training Catalog from https://www.icertglobal.com/corporate-training-for-enterprises.php
Popular Courses include:
-
Project Management: PMP, CAPM ,PMI RMP
-
Quality Management: Six Sigma Black Belt ,Lean Six Sigma Green Belt, Lean Management, Minitab,CMMI
-
Business Analysis: CBAP, CCBA, ECBA
-
Agile Training: PMI-ACP , CSM , CSPO
-
Scrum Training: CSM
-
DevOps
-
Program Management: PgMP
Conclusion
In conclusion, the Capability Maturity Model Integration (CMMI) stands as a powerful framework for organizations seeking to enhance their processes, achieve higher maturity levels, and thrive in today's competitive business landscape. Our exploration into the core concepts of CMMI has unveiled its foundational principles, the significance of maturity levels, the importance of process areas, and the adaptability of representations.
As organizations progress through the maturity levels, transitioning from chaos to continual improvement, they gain not only a structured approach to process enhancement but also a cultural transformation that fosters resilience and adaptability. The tailored CMMI models for different domains further emphasize the versatility of this framework, allowing organizations to customize their pursuit of excellence.
Appraisals serve as crucial checkpoints, evaluating and refining organizational capabilities. Key Performance Indicators provide tangible metrics, offering a clear gauge of success and driving continuous improvement. Integrating CMMI with Agile methodologies creates a harmonious balance between structure and agility, vital for success in dynamic environments.
The challenges and best practices discussed reflect the real-world lessons learned by organizations navigating the CMMI implementation journey. Overcoming resistance to change, addressing resource constraints, and ensuring organizational buy-in are pivotal elements, while executive sponsorship, iterative implementation, and effective communication emerge as best practices for success.
As organizations embrace CMMI, they embark on a transformative journey towards operational maturity, guided by a framework that not only elevates their processes but also instills a culture of excellence and adaptability. By leveraging the core concepts, overcoming challenges, and embracing best practices, organizations can position themselves as industry leaders, capable of navigating the complexities of today's ever-changing business environment with confidence and success.
Read More
In the dynamic landscape of today's global business environment, organizations face the perpetual challenge of delivering high-quality products and services while striving for operational efficiency. To navigate this complex terrain, many enterprises turn to established frameworks and models that provide a structured approach to process improvement. One such powerful and widely adopted framework is the Capability Maturity Model Integration (CMMI).
CMMI stands as a beacon for organizations aspiring to enhance their capabilities and achieve a higher level of maturity in their processes. It offers a comprehensive and integrated set of best practices that guide organizations in developing and improving their processes, ultimately leading to increased performance, reliability, and customer satisfaction.
This exploration delves into the core concepts of CMMI, unraveling its intricacies and shedding light on the transformative journey that organizations embark upon when embracing this model. From understanding the fundamental principles that underpin CMMI to exploring its maturity levels and process areas, we will navigate through the key components that make CMMI a cornerstone in the pursuit of organizational excellence.
As we embark on this journey, we will demystify the terminology, delve into the rationale behind CMMI, and highlight the practical implications for organizations seeking to elevate their capabilities. Join us in unraveling the layers of CMMI, as we uncover the essence of this model and its profound impact on shaping robust, resilient, and high-performance organizations in the modern business landscape.
Table Of Contents
-
Foundations of CMMI: Defining Capability and Maturity
-
CMMI Framework Components: Processes, Practices, and Goals
-
Maturity Levels Demystified: Progressing from Chaos to Continual Improvement
-
Process Areas: Building Blocks for Effective Performance
-
Continuous and Staged Representations: Tailoring CMMI to Organizational Needs
-
CMMI Models for Different Domains: Customizing Excellence
-
Appraisals in CMMI: Evaluating and Improving Organizational Capability
-
Measuring Success: Key Performance Indicators in CMMI
-
CMMI and Agile: Bridging the Gap for Dynamic Environments
-
Challenges and Best Practices in CMMI Implementation: Lessons from the Field
-
Conclusion
Foundations of CMMI: Defining Capability and Maturity
The foundations of the Capability Maturity Model Integration (CMMI) lie in its dual emphasis on capability and maturity, which together form the bedrock of organizational excellence. In the CMMI context, capability refers to an organization's inherent ability to reliably and predictably achieve its business objectives through well-defined processes. This involves understanding and harnessing the organization's resources, processes, and technology to consistently produce desired outcomes. On the other hand, maturity signifies the evolutionary progression of an organization's processes from ad-hoc and chaotic states to well-defined, measured, and optimized levels. It encapsulates the organization's journey toward process improvement and the establishment of best practices. By defining capability and maturity as intertwined aspects, CMMI provides a holistic framework that empowers organizations to assess, enhance, and continually evolve their processes, ensuring they are not only capable of meeting current demands but are also on a trajectory of continual improvement. This foundational understanding sets the stage for organizations to embark on a purposeful journey towards operational excellence and sustained success.
CMMI Framework Components: Processes, Practices, and Goals
The Capability Maturity Model Integration (CMMI) is a robust framework built upon key components, each playing a pivotal role in guiding organizations toward process improvement and excellence. At its core are processes, the dynamic sequences of activities that transform inputs into valuable outputs. CMMI emphasizes the definition, implementation, and continuous refinement of these processes to ensure consistency, efficiency, and adaptability within an organization.
Embedded within the framework are best practices, collectively known as practices, which encapsulate the distilled wisdom of successful processes. Practices serve as guidelines, outlining the specific activities, methods, and techniques that contribute to the effective execution of processes. They provide organizations with a roadmap for achieving desired outcomes and for adapting to evolving business needs.
Furthermore, CMMI incorporates the concept of goals, which represent the high-level objectives that organizations aspire to achieve. Goals guide the selection and implementation of practices, aligning them with the organization's strategic objectives. These goals serve as benchmarks, enabling organizations to measure their progress and maturity levels across different areas.
In essence, the synergy among processes, practices, and goals within the CMMI framework forms a dynamic triad. Processes provide the operational backbone, practices offer actionable insights, and goals steer organizations towards overarching excellence. Understanding and optimizing this interconnected framework empowers organizations to systematically elevate their capabilities and achieve maturity in a structured and sustainable manner.
Maturity Levels Demystified: Progressing from Chaos to Continual Improvement
Navigating through the Maturity Levels within the Capability Maturity Model Integration (CMMI) unveils a transformative journey, guiding organizations from the tumultuous realm of chaos towards a state of perpetual enhancement. Commencing at Level 1, organizations grapple with ad-hoc processes, characterized by unpredictability and disorder. The transition to Level 2 signifies a pivotal step, introducing foundational project management practices and instilling a semblance of control.
As organizations ascend to Level 3, a culture of standardization emerges. Processes become not only defined but also tailored to specific project needs, fostering a proactive approach to process management. The journey intensifies at Level 4, where organizations employ quantitative techniques, utilizing data to gain insights and enhance predictability. This meticulous control sets the stage for the pinnacle, Level 5, characterized by an unwavering commitment to continual improvement.
At Level 5, organizations go beyond control to actively monitor, adapt, and innovate. A culture of perpetual enhancement becomes ingrained, enabling organizations not only to navigate complexity but to thrive amidst change. The narrative of progression through these maturity levels encapsulates more than a refinement of processes; it signifies a profound organizational evolution, positioning entities as dynamic and resilient contributors to the ever-evolving business landscape.
Process Areas: Building Blocks for Effective Performance
Process areas stand as the foundational building blocks within the Capability Maturity Model Integration (CMMI), forming the essential elements that underpin an organization's capability to deliver effective performance. These areas define clusters of related activities that, when executed cohesively, contribute to the achievement of specific objectives and the overall success of the organization.
Each process area within CMMI encapsulates a set of best practices and guidelines tailored to address particular aspects of an organization's operations. They serve as a roadmap, providing a structured approach for organizations to develop, implement, and continually improve their processes. These building blocks are instrumental in aligning organizational goals with practical, actionable steps, fostering consistency, efficiency, and ultimately, superior performance.
By focusing on process areas, organizations can systematically enhance their capabilities in critical areas such as project management, requirements development, and process improvement. The comprehensive nature of these areas ensures that organizations not only meet their immediate objectives but also cultivate a culture of continuous improvement, adaptability, and resilience.
Process areas within CMMI are the linchpin of effective performance. They enable organizations to elevate their processes beyond mere compliance to standards, driving them towards operational excellence and ensuring sustained success in today's dynamic and competitive business environment.
Continuous and Staged Representations: Tailoring CMMI to Organizational Needs
In the realm of Capability Maturity Model Integration (CMMI), organizations are presented with two distinct yet flexible approaches: the Continuous Representation and the Staged Representation. These representations serve as adaptable frameworks, allowing organizations to tailor their CMMI adoption to align precisely with their unique operational needs, preferences, and strategic objectives.
The Staged Representation offers a structured, milestone-oriented approach, where maturity levels are attained sequentially. This method provides a clear roadmap, guiding organizations from one level to the next, each level building upon the achievements of the previous one. It is particularly beneficial for organizations seeking a well-defined, step-by-step approach to maturity.
Conversely, the Continuous Representation allows for a more tailored and flexible adoption. Instead of following a strict sequence of maturity levels, organizations can choose to focus on specific process areas that align with their immediate priorities. This approach provides the freedom to address targeted areas of improvement without the constraint of a predetermined sequence.
The decision between these representations hinges on an organization's unique context, goals, and existing processes. The Staged Representation may be preferable for those seeking a systematic, comprehensive approach to maturity, while the Continuous Representation offers a more agile and customizable route.
Ultimately, whether an organization opts for the Staged or Continuous Representation, the key lies in aligning CMMI adoption with organizational needs. This strategic alignment empowers organizations to leverage the power of CMMI in a way that not only improves processes but also seamlessly integrates with their broader business objectives and operational landscape.
CMMI Models for Different Domains: Customizing Excellence
In the dynamic landscape of industries spanning from software development to manufacturing and beyond, a one-size-fits-all approach to process improvement may not be optimal. Recognizing this diversity, the Capability Maturity Model Integration (CMMI) provides specialized models tailored to meet the unique challenges and nuances of different domains. These domain-specific adaptations empower organizations to customize their journey toward excellence, aligning CMMI principles with the specific requirements of their industry.
For software and systems engineering, the CMMI for Development (CMMI-DEV) model offers a targeted framework. It emphasizes best practices for managing and improving development processes, ensuring the delivery of high-quality software and systems.
In the realm of services, the CMMI for Services (CMMI-SVC) model takes center stage. It addresses the distinctive aspects of service delivery, focusing on processes that enhance customer satisfaction, manage service delivery risks, and optimize service provider performance.
For organizations in the acquisition and supply chain domain, the CMMI for Acquisition (CMMI-ACQ) model becomes instrumental. It provides guidelines for effective acquisition processes, ensuring that organizations can seamlessly integrate suppliers and acquisitions into their overall improvement strategy.
The adaptability of CMMI models for different domains extends beyond these examples, encompassing areas such as product development, people management, and cybersecurity. Each tailored model incorporates industry-specific best practices while retaining the core CMMI principles, allowing organizations to reap the benefits of a proven framework while addressing the unique challenges within their domain.
Appraisals in CMMI: Evaluating and Improving Organizational Capability
In the realm of Capability Maturity Model Integration (CMMI), appraisals serve as pivotal mechanisms for evaluating and enhancing an organization's capability and maturity levels. An appraisal is a structured and rigorous assessment process conducted by certified professionals, providing organizations with insights into the effectiveness of their processes and identifying areas for improvement.
The CMMI appraisal process follows a systematic approach, examining how well an organization's processes align with the CMMI model's best practices. There are various types of appraisals, with the Standard CMMI Appraisal Method for Process Improvement (SCAMPI) being one of the most widely utilized. SCAMPI appraisals can be Class A, B, or C, each differing in scope, depth, and purpose.
Crucially, the insights gained from appraisals contribute to a continuous improvement cycle. Organizations can leverage appraisal findings to refine their processes, enhance capabilities, and align with strategic objectives. By identifying and addressing areas for improvement, organizations can systematically progress through the maturity levels of CMMI, ultimately enhancing their ability to deliver high-quality products and services.
CMMI appraisals play a dual role in evaluating and improving organizational capability. They offer a comprehensive assessment of an organization's adherence to CMMI best practices and provide a roadmap for continual enhancement, fostering a culture of proactive improvement and ensuring sustained success in today's competitive business landscape.
Measuring Success: Key Performance Indicators in CMMI
In the dynamic landscape of process improvement, the Capability Maturity Model Integration (CMMI) places a significant emphasis on quantifiable success through the use of Key Performance Indicators (KPIs). KPIs in CMMI act as essential metrics, offering organizations tangible and measurable insights into the effectiveness of their processes, the achievement of goals, and the overall progress in their journey towards maturity.
Key Performance Indicators within the CMMI framework are diverse and tailored to specific process areas. They are designed to provide a clear picture of an organization's performance, allowing for informed decision-making and targeted improvements. Some common KPIs include metrics related to project schedule adherence, defect density, and customer satisfaction.
The strategic use of KPIs extends beyond mere measurement; it serves as a catalyst for continuous improvement. By regularly assessing and analyzing these indicators, organizations can identify trends, areas of excellence, and potential challenges. This proactive approach enables them to make data-driven decisions, refine processes, and address issues promptly, fostering a culture of continual enhancement.
In summary, measuring success in CMMI relies on the strategic implementation of Key Performance Indicators. These metrics not only gauge the effectiveness of processes but also drive continuous improvement, enabling organizations to navigate the complexities of their industries with precision and ensuring a sustained trajectory of success.
CMMI and Agile: Bridging the Gap for Dynamic Environments
In the ever-evolving landscape of software development and project management, the integration of Capability Maturity Model Integration (CMMI) and Agile methodologies represents a strategic synergy aimed at addressing the challenges of dynamic and rapidly changing environments.
Agile, known for its flexibility, collaboration, and iterative approach, is favored in environments where responsiveness to change is paramount. CMMI, on the other hand, provides a structured framework for process improvement and maturity. Bridging the gap between these two seemingly distinct approaches holds the key to unlocking a holistic and adaptive model for organizational success.
Agile practices are inherently compatible with certain CMMI principles, particularly in the areas of continuous improvement, stakeholder engagement, and incremental development. By integrating Agile practices with CMMI, organizations can harness the iterative nature of Agile for rapid development cycles while leveraging CMMI's structure to ensure robust processes, measurement, and organizational learning.
This integration is not about compromising the agility of Agile or stifling innovation with rigid processes. Instead, it involves tailoring and adapting CMMI practices to complement and enhance Agile methodologies. The goal is to create a dynamic and resilient organizational culture that embraces change, values collaboration, and continually improves processes.
Ultimately, the combination of CMMI and Agile represents a powerful approach for organizations operating in dynamic environments. It harmonizes the best of both worlds, providing the structure needed for maturity and process improvement while preserving the agility required to navigate the uncertainties of today's fast-paced business landscape.
Challenges and Best Practices in CMMI Implementation: Lessons from the Field
Embarking on the journey of implementing Capability Maturity Model Integration (CMMI) is a transformative endeavor for any organization, and it comes with its unique set of challenges and valuable lessons. Drawing insights from real-world experiences, we explore both the common challenges faced during CMMI implementation and the best practices that organizations have employed to navigate these hurdles successfully.
Challenges:
Resistance to Change:
Challenge: Employees may resist changes to established processes and workflows.
Lesson: Clear communication about the benefits of CMMI, coupled with employee involvement in the process, helps alleviate resistance.
Resource Constraints:
Challenge: Limited time, budget, and personnel resources can hinder implementation efforts.
Lesson: Prioritize initiatives based on their impact and feasibility, and seek executive support for resource allocation.
Tailoring the Model:
Challenge: Adapting CMMI practices to the specific needs of the organization can be challenging.
Lesson: Tailor CMMI to fit the organization's context, ensuring relevance without compromising the integrity of the model.
Documentation Overload:
Challenge: Excessive documentation requirements can be perceived as burdensome.
Lesson: Streamline documentation processes, focusing on value-added documentation and avoiding unnecessary bureaucracy.
Lack of Organizational Buy-In:
Challenge: If the entire organization does not buy into the CMMI initiative, implementation may face resistance.
Lesson: Engage key stakeholders early, demonstrate the benefits, and foster a culture that values continuous improvement.
Best Practices:
Executive Sponsorship:
Practice: Secure executive sponsorship to drive commitment and allocate necessary resources.
Pilot Projects:
Practice: Start with pilot projects to test CMMI practices in a controlled environment before full-scale implementation.
Training and Skill Development:
Practice: Invest in training programs to enhance the skills of employees and build a competent workforce.
Continuous Communication:
Practice: Maintain open and continuous communication channels to address concerns, share successes, and reinforce the importance of CMMI.
Iterative Implementation:
Practice: Adopt an iterative approach to implementation, allowing for incremental improvements and learning from each cycle.
By acknowledging these challenges and implementing best practices derived from real-world experiences, organizations can not only overcome obstacles in their CMMI journey but also cultivate a culture of continuous improvement and excellence. These lessons from the field serve as a guide for organizations aspiring to enhance their processes and achieve greater maturity.
How to obtain Project Management certification?
We are an Education Technology company providing certification training courses to accelerate careers of working professionals worldwide. We impart training through instructor-led classroom workshops, instructor-led live virtual training sessions, and self-paced e-learning courses.
We have successfully conducted training sessions in 108 countries across the globe and enabled thousands of working professionals to enhance the scope of their careers.
Our enterprise training portfolio includes in-demand and globally recognized certification training courses in Project Management, Quality Management, Business Analysis, IT Service Management, Agile and Scrum, Cyber Security, Data Science, and Emerging Technologies. Download our Enterprise Training Catalog from https://www.icertglobal.com/corporate-training-for-enterprises.php
Popular Courses include:
-
Project Management: PMP, CAPM ,PMI RMP
-
Quality Management: Six Sigma Black Belt ,Lean Six Sigma Green Belt, Lean Management, Minitab,CMMI
-
Business Analysis: CBAP, CCBA, ECBA
-
Agile Training: PMI-ACP , CSM , CSPO
-
Scrum Training: CSM
-
DevOps
-
Program Management: PgMP
Conclusion
In conclusion, the Capability Maturity Model Integration (CMMI) stands as a powerful framework for organizations seeking to enhance their processes, achieve higher maturity levels, and thrive in today's competitive business landscape. Our exploration into the core concepts of CMMI has unveiled its foundational principles, the significance of maturity levels, the importance of process areas, and the adaptability of representations.
As organizations progress through the maturity levels, transitioning from chaos to continual improvement, they gain not only a structured approach to process enhancement but also a cultural transformation that fosters resilience and adaptability. The tailored CMMI models for different domains further emphasize the versatility of this framework, allowing organizations to customize their pursuit of excellence.
Appraisals serve as crucial checkpoints, evaluating and refining organizational capabilities. Key Performance Indicators provide tangible metrics, offering a clear gauge of success and driving continuous improvement. Integrating CMMI with Agile methodologies creates a harmonious balance between structure and agility, vital for success in dynamic environments.
The challenges and best practices discussed reflect the real-world lessons learned by organizations navigating the CMMI implementation journey. Overcoming resistance to change, addressing resource constraints, and ensuring organizational buy-in are pivotal elements, while executive sponsorship, iterative implementation, and effective communication emerge as best practices for success.
As organizations embrace CMMI, they embark on a transformative journey towards operational maturity, guided by a framework that not only elevates their processes but also instills a culture of excellence and adaptability. By leveraging the core concepts, overcoming challenges, and embracing best practices, organizations can position themselves as industry leaders, capable of navigating the complexities of today's ever-changing business environment with confidence and success.
Key Benefits of CMMI Implementation in Your Organization
Implementing the Capability Maturity Model Integration (CMMI) in your organization can bring about a myriad of benefits, enhancing its overall efficiency and competitiveness in today's dynamic business landscape. CMMI serves as a comprehensive framework designed to elevate and optimize an organization's processes, thereby ensuring higher levels of performance, quality, and productivity.
One of the primary advantages of implementing CMMI lies in its ability to provide a structured approach to process improvement. By adopting CMMI practices, organizations can systematically identify, evaluate, and refine their existing processes. This structured methodology not only streamlines operations but also fosters a culture of continuous improvement, ensuring that the organization remains adaptable and responsive to evolving market demands.
CMMI is not merely a tool for process improvement; it also plays a pivotal role in risk management. By identifying and addressing potential risks at early stages, organizations can proactively mitigate challenges that may arise during project execution. This risk mitigation approach not only safeguards project timelines and budgets but also contributes to a more resilient and sustainable business model.
In addition to these operational advantages, implementing CMMI can also enhance communication and collaboration within an organization. The framework encourages cross-functional teams to work cohesively towards common objectives, fostering a collaborative culture that promotes knowledge sharing and innovation. This collaborative mindset is crucial in today's interconnected business environment, where agility and adaptability are key to success.
The benefits of implementing CMMI in an organization are multi-faceted, ranging from improved process efficiency and product quality to enhanced risk management and competitive advantage. As businesses navigate the complexities of a rapidly changing landscape, CMMI stands as a valuable framework that empowers organizations to not only meet current challenges but also to thrive in the future.
Table of contents
-
Enhanced Process Efficiency
-
Quality Assurance and Product Excellence
-
Risk Mitigation Strategies
-
Standardization of Best Practices
-
Collaborative Team Culture
-
Strategic Alignment and Competitive Edge
-
Continuous Improvement Mindset
-
Resource Optimization and Cost Management
-
Employee Development and Engagement
-
Measurable Performance Metrics
-
Conclusion
Enhanced Process Efficiency
Enhanced process efficiency is a key benefit of implementing the Capability Maturity Model Integration (CMMI) in an organization. This aspect revolves around the systematic improvement and optimization of existing processes, leading to increased effectiveness and streamlined workflows.
CMMI provides a structured framework for organizations to assess, refine, and standardize their processes across various departments. Through the identification of best practices and the elimination of redundancies or bottlenecks, CMMI helps organizations achieve a higher level of efficiency in their day-to-day operations.
One way CMMI enhances process efficiency is by promoting a clear understanding of roles, responsibilities, and workflows within the organization. By defining and documenting processes, teams can work more cohesively, reducing the likelihood of misunderstandings or delays. This clarity contributes to smoother collaboration and improved overall efficiency.
Furthermore, CMMI encourages organizations to continuously monitor and evaluate their processes. This ongoing assessment allows for the identification of areas for improvement. By addressing inefficiencies and optimizing processes iteratively, organizations can adapt to changing circumstances and maintain a competitive edge in their respective industries.
Enhanced process efficiency, facilitated by CMMI, involves the systematic improvement of organizational processes through clear documentation, continuous monitoring, and the establishment of performance metrics. By embracing this aspect of CMMI, organizations position themselves to operate more smoothly, respond to challenges more effectively, and deliver high-quality products or services with greater consistency.
Quality Assurance and Product Excellence
Quality assurance and product excellence are fundamental outcomes of implementing the Capability Maturity Model Integration (CMMI) in an organization. CMMI provides a structured framework that not only ensures the consistency of processes but also places a strong emphasis on delivering high-quality products and services.
CMMI encourages organizations to adopt rigorous quality assurance practices throughout the product or service development lifecycle. This involves defining clear quality standards, conducting thorough reviews, and implementing robust testing procedures. By adhering to these practices, organizations can identify and rectify defects early in the process, preventing issues from escalating and ultimately ensuring the delivery of superior products or services.
One of the ways CMMI contributes to product excellence is through its focus on continuous improvement. The model prompts organizations to regularly assess their processes and make necessary adjustments to enhance efficiency and quality. This iterative approach ensures that products and services evolve over time, meeting or exceeding customer expectations.
CMMI's impact on quality assurance and product excellence is evident through its emphasis on rigorous testing, continuous improvement, customer-centric practices, and the establishment of measurable quality metrics. By integrating these principles into their processes, organizations can consistently produce high-quality products, build customer trust, and gain a competitive advantage in the marketplace.
Risk Mitigation Strategies
Risk mitigation strategies are essential components of effective project and organizational management, and the implementation of the Capability Maturity Model Integration (CMMI) plays a pivotal role in shaping these strategies. One key aspect of risk mitigation within the CMMI framework is the emphasis on early identification. By encouraging organizations to identify risks at the outset of a project or process, CMMI enables teams to assess potential challenges before they escalate. This proactive approach sets the stage for comprehensive risk management throughout the project lifecycle.
CMMI goes beyond qualitative assessments by promoting quantitative risk analysis techniques. Assigning numerical values to risks and their potential impacts allows organizations to prioritize and address the most critical issues. This data-driven approach ensures that resources are allocated efficiently, focusing on mitigating risks that pose the greatest threat to project success.
Effective communication is highlighted within CMMI's risk mitigation strategies. Transparent and open communication about identified risks ensures that relevant stakeholders are informed and can contribute to mitigation efforts. This inclusive communication approach fosters a sense of shared responsibility and promotes a collective effort in addressing and overcoming challenges.
Finally, CMMI promotes a culture of continuous improvement, extending to the organization's risk management processes. Through regular assessments and feedback loops, organizations refine their risk management approaches. This commitment to ongoing improvement ensures that risk mitigation strategies evolve and remain effective in the face of changing circumstances, contributing to overall organizational resilience. In essence, CMMI's risk mitigation strategies provide a comprehensive and adaptable framework for organizations to navigate challenges successfully and enhance project and organizational outcomes.
Standardization of Best Practices
The standardization of best practices is a key benefit derived from implementing the Capability Maturity Model Integration (CMMI) in an organization. CMMI provides a structured framework that emphasizes the identification, documentation, and adherence to proven methodologies across various business functions. This standardization contributes significantly to the overall efficiency, consistency, and quality of organizational processes.
CMMI guides organizations in defining and documenting their best practices, ensuring a clear understanding of established methods and procedures. This documentation serves as a valuable resource for employees, providing a reference point for how tasks and processes should be executed. Standardizing best practices in this manner fosters a shared understanding and promotes consistency across teams, reducing the likelihood of errors or variations in execution.
The standardization of best practices facilitated by CMMI is a cornerstone of organizational excellence. It provides a systematic approach to defining, documenting, and implementing proven methodologies, fostering consistency, efficiency, and quality across the organization. This standardized foundation not only enhances day-to-day operations but also establishes a framework for continuous improvement and organizational resilience.
Collaborative Team Culture
Collaborative team culture is a critical aspect of a thriving and high-performing organization. When teams work together seamlessly and share a common purpose, it not only enhances the quality of work but also contributes to a positive and engaging work environment. In a collaborative team culture, individuals come together, leveraging their diverse skills and experiences to achieve shared goals.
Effective communication lies at the heart of collaborative team culture. It's about more than just conveying information; it's about creating an environment where team members feel comfortable expressing ideas, asking questions, and providing feedback. A culture that values open communication fosters transparency and ensures that everyone is on the same page, reducing the likelihood of misunderstandings and promoting a sense of unity.
Cross-functional collaboration is a key element of collaborative team culture. When individuals from different departments or disciplines collaborate, it brings a richness of perspectives to problem-solving and decision-making. This interdisciplinary approach often leads to innovative solutions that may not have been possible within the confines of a single function. Cross-functional collaboration also breaks down silos, promoting a more holistic understanding of the organization's objectives.
Continuous improvement is a core principle of collaborative team culture. Teams that embrace a mindset of ongoing learning and adaptation are better equipped to navigate challenges and capitalize on opportunities. Regular reflections on successes and setbacks, coupled with a commitment to refining processes, contribute to a culture of growth and development.
In essence, a collaborative team culture is a catalyst for organizational success. It builds a foundation of trust, encourages innovation, and empowers individuals to contribute their best efforts toward shared objectives. As organizations embrace and cultivate collaborative team cultures, they position themselves for sustained excellence and adaptability in a dynamic and ever-evolving landscape.
Strategic Alignment and Competitive Edge
Strategic alignment and gaining a competitive edge are two significant outcomes of implementing the Capability Maturity Model Integration (CMMI) in an organization. CMMI provides a structured framework that aligns the organization's processes with its strategic objectives, fostering a cohesive approach that enhances competitiveness in the marketplace.
CMMI emphasizes strategic alignment by encouraging organizations to integrate their processes with overarching business goals. This alignment ensures that every process and activity within the organization contributes directly to the strategic objectives. As a result, teams work cohesively towards common goals, minimizing the risk of disjointed efforts and optimizing resources for maximum impact.
CMMI's focus on continuous improvement contributes to sustaining a competitive edge over time. The framework encourages organizations to regularly reassess their processes, incorporating lessons learned and adapting to evolving market conditions. This commitment to ongoing improvement ensures that the organization remains dynamic and responsive, staying ahead of competitors who may be slower to adapt.
Strategic alignment also plays a crucial role in decision-making. When processes are aligned with strategic objectives, decision-makers have a clear understanding of how choices impact overall goals. This clarity reduces the likelihood of decisions that may deviate from the strategic path and ensures that resources are allocated in ways that maximize value.
CMMI's emphasis on strategic alignment helps organizations create a seamless connection between their processes and overarching business objectives. This alignment enhances organizational agility, fosters a data-driven approach to performance measurement, and ultimately contributes to gaining and sustaining a competitive edge in the marketplace. As organizations implement and mature through the CMMI framework, they are better positioned to navigate the complexities of the business landscape while achieving strategic success.
Continuous Improvement Mindset
The continuous improvement mindset is a fundamental principle embedded in the Capability Maturity Model Integration (CMMI) and serves as a guiding philosophy for organizations seeking to enhance their processes and overall performance. CMMI encourages a culture where the pursuit of excellence is ongoing, and teams are committed to refining their practices incrementally over time.
CMMI's continuous improvement mindset involves the systematic identification and implementation of enhancements. Organizations are encouraged to gather data, feedback, and lessons learned from ongoing projects. This information is then analyzed to identify patterns and trends, providing insights that inform strategic decisions for improvement. The focus is not only on fixing immediate issues but on creating a foundation for sustained and long-term advancement.
CMMI's commitment to continuous improvement extends beyond individual projects to encompass the entire organization. It advocates for the establishment of metrics and key performance indicators (KPIs) that provide quantifiable insights into process effectiveness. Regular reviews of these metrics enable organizations to track progress, measure success, and identify areas for further enhancement.
The continuous improvement mindset advocated by CMMI is a cornerstone of organizational success. It instills a culture of reflection, learning, and proactive refinement. By embracing this mindset, organizations position themselves to not only address current challenges but also to navigate future uncertainties with resilience and agility. Continuous improvement becomes a journey, ingrained in the organizational DNA, driving sustained excellence and innovation.
Resource Optimization and Cost Management
Resource optimization and cost management are integral components of implementing the Capability Maturity Model Integration (CMMI) in an organization. CMMI provides a structured framework that guides organizations in efficiently managing their resources and controlling costs, contributing to improved overall performance and sustainability.
CMMI emphasizes the importance of optimizing resources by aligning them with organizational objectives. This involves a systematic evaluation of available human, financial, and technological resources and ensuring that they are strategically allocated to projects and processes. By optimizing resource utilization, organizations can enhance productivity, reduce waste, and achieve better outcomes without unnecessary expenditures.
Cost management, within the context of CMMI, involves controlling and optimizing expenses throughout the project lifecycle. This includes not only direct project costs but also indirect costs associated with supporting processes. CMMI encourages organizations to establish clear cost management practices, such as budgeting, monitoring expenditures, and implementing cost-saving measures.
CMMI promotes a proactive approach to resource optimization by emphasizing risk management. By identifying potential risks early in the project or process, organizations can develop contingency plans to address resource-related challenges. This proactive risk management contributes to avoiding cost overruns and disruptions, enhancing the organization's ability to stay within budgetary constraints.
Resource optimization and cost management, as guided by CMMI, are essential for organizations aiming to achieve efficiency, control expenses, and enhance overall performance. The framework's emphasis on quantitative metrics, risk management, standardization of best practices, and continuous improvement contributes to a systematic and strategic approach to resource utilization and cost control. By implementing these principles, organizations can navigate resource challenges effectively, control costs, and position themselves for sustained success in a competitive business environment.
Employee Development and Engagement
Employee development and engagement, as guided by the Capability Maturity Model Integration (CMMI), encompasses various strategic initiatives aimed at fostering a skilled and motivated workforce. CMMI emphasizes the establishment of structured professional development programs, ensuring that employees continuously enhance their skills and stay abreast of industry trends. This commitment to ongoing learning contributes to the organization's adaptability and the individual growth of its employees.
CMMI also advocates for a culture of knowledge sharing and collaboration. Organizations are encouraged to create platforms for employees to share their expertise, fostering a collaborative environment where collective learning is prioritized. This collaborative culture not only enhances employee development but also strengthens the overall knowledge base within the organization.
Recognition and rewards play a pivotal role in employee engagement within CMMI. By establishing systems that acknowledge and reward employees for their contributions, organizations boost morale and reinforce a positive and engaged workforce. This recognition creates a sense of value and appreciation among employees, strengthening their commitment to the organization's success.
Employee involvement in decision-making processes is another key principle of CMMI's approach to engagement. Seeking input from employees at various levels fosters a participatory environment where individuals feel their voices are heard. This inclusion not only improves the quality of decisions but also instills a sense of ownership and commitment among employees.
Measurable Performance Metrics
Implementing measurable performance metrics is a key component of the Capability Maturity Model Integration (CMMI) framework. CMMI emphasizes the importance of quantifiable indicators to assess and improve various aspects of an organization's processes. Measurable performance metrics provide valuable insights into efficiency, effectiveness, and overall success, guiding data-driven decision-making and continuous improvement efforts.
CMMI encourages organizations to define key performance indicators (KPIs) that align with their strategic objectives. These metrics should be specific, measurable, achievable, relevant, and time-bound (SMART), ensuring clarity in measurement and facilitating accurate assessments of performance. Examples of measurable performance metrics may include project completion time, defect rates, customer satisfaction scores, and adherence to schedule and budget.
Measurable performance metrics, as advocated by CMMI, provide a structured and data-driven approach to evaluating organizational processes. By defining clear, SMART indicators, establishing baselines, incorporating both quantitative and qualitative measures, and conducting regular reviews, organizations can gain valuable insights into their performance. These metrics not only guide decision-making but also support a culture of continuous improvement, fostering organizational maturity and resilience in a competitive landscape.
Conclusion
In conclusion, the Capability Maturity Model Integration (CMMI) serves as a comprehensive and structured framework that empowers organizations to achieve higher levels of performance, maturity, and success. The principles and practices outlined by CMMI touch on various critical aspects of organizational functioning, including process improvement, risk management, quality assurance, and team collaboration.
CMMI's emphasis on measurable performance metrics underscores the importance of data-driven decision-making. By defining clear and SMART key performance indicators, organizations gain the ability to objectively assess their processes and outcomes. This not only facilitates a deeper understanding of current performance but also provides a solid foundation for continuous improvement initiatives.
In essence, CMMI provides organizations with a roadmap for achieving maturity in their processes, fostering a culture of excellence, adaptability, and continuous growth. As organizations embrace and implement the principles of CMMI, they position themselves to navigate complexities, optimize performance, and thrive in an ever-evolving business landscape.
Read More
Implementing the Capability Maturity Model Integration (CMMI) in your organization can bring about a myriad of benefits, enhancing its overall efficiency and competitiveness in today's dynamic business landscape. CMMI serves as a comprehensive framework designed to elevate and optimize an organization's processes, thereby ensuring higher levels of performance, quality, and productivity.
One of the primary advantages of implementing CMMI lies in its ability to provide a structured approach to process improvement. By adopting CMMI practices, organizations can systematically identify, evaluate, and refine their existing processes. This structured methodology not only streamlines operations but also fosters a culture of continuous improvement, ensuring that the organization remains adaptable and responsive to evolving market demands.
CMMI is not merely a tool for process improvement; it also plays a pivotal role in risk management. By identifying and addressing potential risks at early stages, organizations can proactively mitigate challenges that may arise during project execution. This risk mitigation approach not only safeguards project timelines and budgets but also contributes to a more resilient and sustainable business model.
In addition to these operational advantages, implementing CMMI can also enhance communication and collaboration within an organization. The framework encourages cross-functional teams to work cohesively towards common objectives, fostering a collaborative culture that promotes knowledge sharing and innovation. This collaborative mindset is crucial in today's interconnected business environment, where agility and adaptability are key to success.
The benefits of implementing CMMI in an organization are multi-faceted, ranging from improved process efficiency and product quality to enhanced risk management and competitive advantage. As businesses navigate the complexities of a rapidly changing landscape, CMMI stands as a valuable framework that empowers organizations to not only meet current challenges but also to thrive in the future.
Table of contents
-
Enhanced Process Efficiency
-
Quality Assurance and Product Excellence
-
Risk Mitigation Strategies
-
Standardization of Best Practices
-
Collaborative Team Culture
-
Strategic Alignment and Competitive Edge
-
Continuous Improvement Mindset
-
Resource Optimization and Cost Management
-
Employee Development and Engagement
-
Measurable Performance Metrics
-
Conclusion
Enhanced Process Efficiency
Enhanced process efficiency is a key benefit of implementing the Capability Maturity Model Integration (CMMI) in an organization. This aspect revolves around the systematic improvement and optimization of existing processes, leading to increased effectiveness and streamlined workflows.
CMMI provides a structured framework for organizations to assess, refine, and standardize their processes across various departments. Through the identification of best practices and the elimination of redundancies or bottlenecks, CMMI helps organizations achieve a higher level of efficiency in their day-to-day operations.
One way CMMI enhances process efficiency is by promoting a clear understanding of roles, responsibilities, and workflows within the organization. By defining and documenting processes, teams can work more cohesively, reducing the likelihood of misunderstandings or delays. This clarity contributes to smoother collaboration and improved overall efficiency.
Furthermore, CMMI encourages organizations to continuously monitor and evaluate their processes. This ongoing assessment allows for the identification of areas for improvement. By addressing inefficiencies and optimizing processes iteratively, organizations can adapt to changing circumstances and maintain a competitive edge in their respective industries.
Enhanced process efficiency, facilitated by CMMI, involves the systematic improvement of organizational processes through clear documentation, continuous monitoring, and the establishment of performance metrics. By embracing this aspect of CMMI, organizations position themselves to operate more smoothly, respond to challenges more effectively, and deliver high-quality products or services with greater consistency.
Quality Assurance and Product Excellence
Quality assurance and product excellence are fundamental outcomes of implementing the Capability Maturity Model Integration (CMMI) in an organization. CMMI provides a structured framework that not only ensures the consistency of processes but also places a strong emphasis on delivering high-quality products and services.
CMMI encourages organizations to adopt rigorous quality assurance practices throughout the product or service development lifecycle. This involves defining clear quality standards, conducting thorough reviews, and implementing robust testing procedures. By adhering to these practices, organizations can identify and rectify defects early in the process, preventing issues from escalating and ultimately ensuring the delivery of superior products or services.
One of the ways CMMI contributes to product excellence is through its focus on continuous improvement. The model prompts organizations to regularly assess their processes and make necessary adjustments to enhance efficiency and quality. This iterative approach ensures that products and services evolve over time, meeting or exceeding customer expectations.
CMMI's impact on quality assurance and product excellence is evident through its emphasis on rigorous testing, continuous improvement, customer-centric practices, and the establishment of measurable quality metrics. By integrating these principles into their processes, organizations can consistently produce high-quality products, build customer trust, and gain a competitive advantage in the marketplace.
Risk Mitigation Strategies
Risk mitigation strategies are essential components of effective project and organizational management, and the implementation of the Capability Maturity Model Integration (CMMI) plays a pivotal role in shaping these strategies. One key aspect of risk mitigation within the CMMI framework is the emphasis on early identification. By encouraging organizations to identify risks at the outset of a project or process, CMMI enables teams to assess potential challenges before they escalate. This proactive approach sets the stage for comprehensive risk management throughout the project lifecycle.
CMMI goes beyond qualitative assessments by promoting quantitative risk analysis techniques. Assigning numerical values to risks and their potential impacts allows organizations to prioritize and address the most critical issues. This data-driven approach ensures that resources are allocated efficiently, focusing on mitigating risks that pose the greatest threat to project success.
Effective communication is highlighted within CMMI's risk mitigation strategies. Transparent and open communication about identified risks ensures that relevant stakeholders are informed and can contribute to mitigation efforts. This inclusive communication approach fosters a sense of shared responsibility and promotes a collective effort in addressing and overcoming challenges.
Finally, CMMI promotes a culture of continuous improvement, extending to the organization's risk management processes. Through regular assessments and feedback loops, organizations refine their risk management approaches. This commitment to ongoing improvement ensures that risk mitigation strategies evolve and remain effective in the face of changing circumstances, contributing to overall organizational resilience. In essence, CMMI's risk mitigation strategies provide a comprehensive and adaptable framework for organizations to navigate challenges successfully and enhance project and organizational outcomes.
Standardization of Best Practices
The standardization of best practices is a key benefit derived from implementing the Capability Maturity Model Integration (CMMI) in an organization. CMMI provides a structured framework that emphasizes the identification, documentation, and adherence to proven methodologies across various business functions. This standardization contributes significantly to the overall efficiency, consistency, and quality of organizational processes.
CMMI guides organizations in defining and documenting their best practices, ensuring a clear understanding of established methods and procedures. This documentation serves as a valuable resource for employees, providing a reference point for how tasks and processes should be executed. Standardizing best practices in this manner fosters a shared understanding and promotes consistency across teams, reducing the likelihood of errors or variations in execution.
The standardization of best practices facilitated by CMMI is a cornerstone of organizational excellence. It provides a systematic approach to defining, documenting, and implementing proven methodologies, fostering consistency, efficiency, and quality across the organization. This standardized foundation not only enhances day-to-day operations but also establishes a framework for continuous improvement and organizational resilience.
Collaborative Team Culture
Collaborative team culture is a critical aspect of a thriving and high-performing organization. When teams work together seamlessly and share a common purpose, it not only enhances the quality of work but also contributes to a positive and engaging work environment. In a collaborative team culture, individuals come together, leveraging their diverse skills and experiences to achieve shared goals.
Effective communication lies at the heart of collaborative team culture. It's about more than just conveying information; it's about creating an environment where team members feel comfortable expressing ideas, asking questions, and providing feedback. A culture that values open communication fosters transparency and ensures that everyone is on the same page, reducing the likelihood of misunderstandings and promoting a sense of unity.
Cross-functional collaboration is a key element of collaborative team culture. When individuals from different departments or disciplines collaborate, it brings a richness of perspectives to problem-solving and decision-making. This interdisciplinary approach often leads to innovative solutions that may not have been possible within the confines of a single function. Cross-functional collaboration also breaks down silos, promoting a more holistic understanding of the organization's objectives.
Continuous improvement is a core principle of collaborative team culture. Teams that embrace a mindset of ongoing learning and adaptation are better equipped to navigate challenges and capitalize on opportunities. Regular reflections on successes and setbacks, coupled with a commitment to refining processes, contribute to a culture of growth and development.
In essence, a collaborative team culture is a catalyst for organizational success. It builds a foundation of trust, encourages innovation, and empowers individuals to contribute their best efforts toward shared objectives. As organizations embrace and cultivate collaborative team cultures, they position themselves for sustained excellence and adaptability in a dynamic and ever-evolving landscape.
Strategic Alignment and Competitive Edge
Strategic alignment and gaining a competitive edge are two significant outcomes of implementing the Capability Maturity Model Integration (CMMI) in an organization. CMMI provides a structured framework that aligns the organization's processes with its strategic objectives, fostering a cohesive approach that enhances competitiveness in the marketplace.
CMMI emphasizes strategic alignment by encouraging organizations to integrate their processes with overarching business goals. This alignment ensures that every process and activity within the organization contributes directly to the strategic objectives. As a result, teams work cohesively towards common goals, minimizing the risk of disjointed efforts and optimizing resources for maximum impact.
CMMI's focus on continuous improvement contributes to sustaining a competitive edge over time. The framework encourages organizations to regularly reassess their processes, incorporating lessons learned and adapting to evolving market conditions. This commitment to ongoing improvement ensures that the organization remains dynamic and responsive, staying ahead of competitors who may be slower to adapt.
Strategic alignment also plays a crucial role in decision-making. When processes are aligned with strategic objectives, decision-makers have a clear understanding of how choices impact overall goals. This clarity reduces the likelihood of decisions that may deviate from the strategic path and ensures that resources are allocated in ways that maximize value.
CMMI's emphasis on strategic alignment helps organizations create a seamless connection between their processes and overarching business objectives. This alignment enhances organizational agility, fosters a data-driven approach to performance measurement, and ultimately contributes to gaining and sustaining a competitive edge in the marketplace. As organizations implement and mature through the CMMI framework, they are better positioned to navigate the complexities of the business landscape while achieving strategic success.
Continuous Improvement Mindset
The continuous improvement mindset is a fundamental principle embedded in the Capability Maturity Model Integration (CMMI) and serves as a guiding philosophy for organizations seeking to enhance their processes and overall performance. CMMI encourages a culture where the pursuit of excellence is ongoing, and teams are committed to refining their practices incrementally over time.
CMMI's continuous improvement mindset involves the systematic identification and implementation of enhancements. Organizations are encouraged to gather data, feedback, and lessons learned from ongoing projects. This information is then analyzed to identify patterns and trends, providing insights that inform strategic decisions for improvement. The focus is not only on fixing immediate issues but on creating a foundation for sustained and long-term advancement.
CMMI's commitment to continuous improvement extends beyond individual projects to encompass the entire organization. It advocates for the establishment of metrics and key performance indicators (KPIs) that provide quantifiable insights into process effectiveness. Regular reviews of these metrics enable organizations to track progress, measure success, and identify areas for further enhancement.
The continuous improvement mindset advocated by CMMI is a cornerstone of organizational success. It instills a culture of reflection, learning, and proactive refinement. By embracing this mindset, organizations position themselves to not only address current challenges but also to navigate future uncertainties with resilience and agility. Continuous improvement becomes a journey, ingrained in the organizational DNA, driving sustained excellence and innovation.
Resource Optimization and Cost Management
Resource optimization and cost management are integral components of implementing the Capability Maturity Model Integration (CMMI) in an organization. CMMI provides a structured framework that guides organizations in efficiently managing their resources and controlling costs, contributing to improved overall performance and sustainability.
CMMI emphasizes the importance of optimizing resources by aligning them with organizational objectives. This involves a systematic evaluation of available human, financial, and technological resources and ensuring that they are strategically allocated to projects and processes. By optimizing resource utilization, organizations can enhance productivity, reduce waste, and achieve better outcomes without unnecessary expenditures.
Cost management, within the context of CMMI, involves controlling and optimizing expenses throughout the project lifecycle. This includes not only direct project costs but also indirect costs associated with supporting processes. CMMI encourages organizations to establish clear cost management practices, such as budgeting, monitoring expenditures, and implementing cost-saving measures.
CMMI promotes a proactive approach to resource optimization by emphasizing risk management. By identifying potential risks early in the project or process, organizations can develop contingency plans to address resource-related challenges. This proactive risk management contributes to avoiding cost overruns and disruptions, enhancing the organization's ability to stay within budgetary constraints.
Resource optimization and cost management, as guided by CMMI, are essential for organizations aiming to achieve efficiency, control expenses, and enhance overall performance. The framework's emphasis on quantitative metrics, risk management, standardization of best practices, and continuous improvement contributes to a systematic and strategic approach to resource utilization and cost control. By implementing these principles, organizations can navigate resource challenges effectively, control costs, and position themselves for sustained success in a competitive business environment.
Employee Development and Engagement
Employee development and engagement, as guided by the Capability Maturity Model Integration (CMMI), encompasses various strategic initiatives aimed at fostering a skilled and motivated workforce. CMMI emphasizes the establishment of structured professional development programs, ensuring that employees continuously enhance their skills and stay abreast of industry trends. This commitment to ongoing learning contributes to the organization's adaptability and the individual growth of its employees.
CMMI also advocates for a culture of knowledge sharing and collaboration. Organizations are encouraged to create platforms for employees to share their expertise, fostering a collaborative environment where collective learning is prioritized. This collaborative culture not only enhances employee development but also strengthens the overall knowledge base within the organization.
Recognition and rewards play a pivotal role in employee engagement within CMMI. By establishing systems that acknowledge and reward employees for their contributions, organizations boost morale and reinforce a positive and engaged workforce. This recognition creates a sense of value and appreciation among employees, strengthening their commitment to the organization's success.
Employee involvement in decision-making processes is another key principle of CMMI's approach to engagement. Seeking input from employees at various levels fosters a participatory environment where individuals feel their voices are heard. This inclusion not only improves the quality of decisions but also instills a sense of ownership and commitment among employees.
Measurable Performance Metrics
Implementing measurable performance metrics is a key component of the Capability Maturity Model Integration (CMMI) framework. CMMI emphasizes the importance of quantifiable indicators to assess and improve various aspects of an organization's processes. Measurable performance metrics provide valuable insights into efficiency, effectiveness, and overall success, guiding data-driven decision-making and continuous improvement efforts.
CMMI encourages organizations to define key performance indicators (KPIs) that align with their strategic objectives. These metrics should be specific, measurable, achievable, relevant, and time-bound (SMART), ensuring clarity in measurement and facilitating accurate assessments of performance. Examples of measurable performance metrics may include project completion time, defect rates, customer satisfaction scores, and adherence to schedule and budget.
Measurable performance metrics, as advocated by CMMI, provide a structured and data-driven approach to evaluating organizational processes. By defining clear, SMART indicators, establishing baselines, incorporating both quantitative and qualitative measures, and conducting regular reviews, organizations can gain valuable insights into their performance. These metrics not only guide decision-making but also support a culture of continuous improvement, fostering organizational maturity and resilience in a competitive landscape.
Conclusion
In conclusion, the Capability Maturity Model Integration (CMMI) serves as a comprehensive and structured framework that empowers organizations to achieve higher levels of performance, maturity, and success. The principles and practices outlined by CMMI touch on various critical aspects of organizational functioning, including process improvement, risk management, quality assurance, and team collaboration.
CMMI's emphasis on measurable performance metrics underscores the importance of data-driven decision-making. By defining clear and SMART key performance indicators, organizations gain the ability to objectively assess their processes and outcomes. This not only facilitates a deeper understanding of current performance but also provides a solid foundation for continuous improvement initiatives.
In essence, CMMI provides organizations with a roadmap for achieving maturity in their processes, fostering a culture of excellence, adaptability, and continuous growth. As organizations embrace and implement the principles of CMMI, they position themselves to navigate complexities, optimize performance, and thrive in an ever-evolving business landscape.
Introduction to Six Sigma Yellow Belt Certification Basics
Six Sigma Yellow Belt certification is a fundamental level of certification within the Six Sigma methodology, a data-driven approach to process improvement aimed at reducing defects and variations in a process. It is an excellent starting point for individuals who want to enhance their problem-solving skills, contribute to process improvement efforts, and play a valuable role in organizational quality management.
Six Sigma Yellow Belt Certification is an entry-level certification that can open doors to the world of process improvement and quality management. It empowers individuals to apply data-driven methods to solve problems, make processes more efficient, and ultimately contribute to the success of their organization. It serves as a foundation for those who may choose to pursue higher levels of Six Sigma certification, such as Green Belt or Black Belt.
Table of contents
-
Understanding Six Sigma
-
Role of Yellow Belts in Six Sigma
-
Why Pursue a Yellow Belt Certification
-
Certification Requirements
-
Yellow Belt Training and Curriculum
-
Industry Applications
-
Yellow Belt vs. Other Six Sigma Belts
-
Real-World Examples
-
Preparing for the Yellow Belt Exam
-
Career Advancement and Opportunities
-
Conclusion
Understanding Six Sigma
Six Sigma is a systematic and data-driven methodology for process improvement. Originally developed by Motorola in the 1980s, it has become widely adopted by organizations in various industries to enhance product and service quality, reduce defects, and streamline processes. The term "Six Sigma" refers to a statistical measure of process variation, and the goal of Six Sigma is to minimize process variation to a level where only 3.4 defects per million opportunities occur, thereby achieving near-perfect performance.
Here are the key components and concepts that help in understanding Six Sigma:
DMAIC Methodology: Six Sigma follows a structured problem-solving methodology known as DMAIC, which stands for:
Process Variation: Central to Six Sigma is the concept of process variation. Processes naturally have variations, but Six Sigma seeks to reduce and control these variations to ensure consistency and quality.
Data-Driven Approach: Six Sigma heavily relies on data analysis to make informed decisions. Statistical tools and methods are used to collect, measure, and analyze data to understand the current state of processes and identify areas for improvement.
Roles and Belts: Within a Six Sigma program, individuals are often assigned different roles based on their level of expertise. These roles include Yellow Belts, Green Belts, and Black Belts, each with increasing levels of knowledge and responsibility.
Customer Focus: Six Sigma places a strong emphasis on understanding and meeting customer requirements. It seeks to align process improvement efforts with what customers value.
Continuous Improvement: Six Sigma promotes a culture of continuous improvement. It's not a one-time project but an ongoing philosophy that strives to make incremental and sustainable changes to processes.
In summary, Six Sigma is a disciplined and data-driven approach to process improvement and problem-solving. It seeks to reduce process variation, improve quality, and ultimately enhance an organization's competitiveness and customer satisfaction. Understanding and implementing Six Sigma principles can lead to more efficient and effective processes across a wide range of industries.
Role of Yellow Belts in Six Sigma
Six Sigma Yellow Belts play a vital role in the Six Sigma methodology, supporting process improvement initiatives within an organization. While they may not have the same level of expertise and responsibility as Green Belts or Black Belts, Yellow Belts are essential team members who contribute to the success of Six Sigma projects. Here's an overview of their role:
Data Collection: Yellow Belts are responsible for gathering and organizing data related to the process under examination. They ensure that accurate and relevant data is collected to support the project's goals.
Process Mapping: They help create process maps or flowcharts to document the current process. This visual representation aids in identifying bottlenecks, redundancies, and areas for potential improvement.
Participation in Improvement Projects: Yellow Belts actively participate in process improvement projects led by Green Belts or Black Belts. They collaborate with team members to implement changes and solutions.
Problem-Solving: They assist in problem-solving activities by contributing their insights and observations. Yellow Belts may be asked to brainstorm potential causes of issues and help investigate root causes.
Basic Analysis: Yellow Belts use basic Six Sigma tools and techniques to analyze data and identify trends or patterns. They may create histograms, Pareto charts, and other simple visual aids to understand data.
In summary, Yellow Belts are entry-level Six Sigma practitioners who contribute to process improvement initiatives by collecting data, participating in projects, and supporting Green Belts and Black Belts. They are valuable team members in the pursuit of quality and efficiency improvements within an organization. While they may not lead projects, their contributions are essential for successful Six Sigma implementations.
Why Pursue a Yellow Belt Certification
Pursuing a Yellow Belt certification in Six Sigma can offer individuals and organizations several significant benefits. Here are some compelling reasons why you might consider pursuing a Yellow Belt certification:
Basic Understanding of Six Sigma: Yellow Belt training provides a foundational understanding of the Six Sigma methodology. It introduces you to the core principles, concepts, and tools used in Six Sigma process improvement projects.
Enhanced Problem-Solving Skills: Yellow Belt certification equips you with problem-solving skills that can be applied to various situations, both in your professional and personal life. You'll learn to analyze data and make informed decisions.
Career Advancement: Earning a Yellow Belt certification can enhance your resume and open doors to new career opportunities. Many employers value Six Sigma certifications and seek candidates who can contribute to process improvement efforts.
Contribution to Quality Improvement: Yellow Belts play a critical role in improving product or service quality and customer satisfaction. By identifying and addressing process issues, you contribute to your organization's success.
Organizational Impact: By addressing process issues and enhancing efficiency, Yellow Belts can positively impact their organization's performance and competitiveness in the market.
Continuous Learning: Six Sigma is a continuous improvement philosophy. Pursuing a Yellow Belt certification demonstrates your commitment to learning and evolving as a professional.
Pursuing a Yellow Belt certification in Six Sigma is a valuable investment in your professional development. It equips you with problem-solving skills, enhances your understanding of quality management, and can lead to career opportunities while simultaneously benefitting your organization through process improvement.
Certification Requirements
Certification requirements for a Six Sigma Yellow Belt may vary depending on the certifying body and the organization. However, there are common elements that are typically involved in obtaining a Yellow Belt certification. Below are the general certification requirements:
Training: Most Yellow Belt certifications require candidates to complete a specified amount of training. This training can be provided through in-person workshops, online courses, or a combination of both. Training may cover Six Sigma principles, the DMAIC methodology, and essential tools and techniques.
Coursework: Candidates are often required to complete coursework related to Six Sigma Yellow Belt concepts. This coursework may include reading materials, lectures, quizzes, and assignments.
Examination: After completing the training and coursework, candidates must pass a certification exam. The exam assesses their knowledge of Six Sigma principles, DMAIC, and problem-solving techniques. The passing score may vary depending on the certifying body but is typically set at a certain percentage.
Certification Fee: There is usually a fee associated with obtaining a Yellow Belt certification. This fee covers the cost of training, materials, examination, and certification processing.
It's important to note that different organizations and certifying bodies may have variations in their certification requirements, so it's essential to check the specific requirements of the program you are interested in. Additionally, the level of rigor and the depth of content covered in Yellow Belt programs can vary, so it's a good idea to select a program that aligns with your career goals and the depth of knowledge you wish to gain.
Yellow Belt Training and Curriculum
Yellow Belt training in Six Sigma is designed to provide individuals with a foundational understanding of the Six Sigma methodology and equip them with essential problem-solving and process improvement skills. The training typically covers a range of topics and concepts related to quality management. Below is an overview of the common elements included in Yellow Belt training and curriculum:
Introduction to Six Sigma:
Understanding the origins and evolution of Six Sigma.
The importance of quality management and its impact on organizations.
Six Sigma Principles:
Explaining the key principles and philosophies of Six Sigma.
The focus on data-driven decision-making and minimizing process variation.
Process Improvement Projects:
Understanding the various components of a Six Sigma project.
Identifying project selection criteria and defining project scope.
Project Team Dynamics:
Effective teamwork and collaboration within a Six Sigma project team.
Communication and problem-solving skills for team members.
Case Studies and Practical Examples:
Real-world examples of successful Six Sigma projects.
Analyzing how Six Sigma principles were applied to solve specific problems and achieve results.
Certification Preparation:
Guidance on preparing for the Yellow Belt certification exam, including sample questions and practice exams.
Review of key concepts covered in the training.
Practical Application (optional):
Hands-on exercises or a small-scale Six Sigma project may be included as part of the training to allow participants to apply their knowledge in a real-world context.
Yellow Belt training can be delivered through in-person workshops, online courses, or a combination of both, depending on the program and the certifying body. The curriculum is typically designed to be accessible to individuals with various levels of experience and backgrounds, making it an excellent starting point for those looking to gain proficiency in Six Sigma principles and methodologies.
Industry Applications
Six Sigma methodologies, including Yellow Belt principles, have been widely adopted across various industries due to their effectiveness in improving processes, reducing defects, and enhancing overall quality. Here are some industry-specific applications of Six Sigma:
Manufacturing:
In manufacturing, Six Sigma helps reduce defects and variations in the production process. It's used to improve product quality, increase efficiency, and minimize waste.
Applications range from automotive manufacturing to electronics, aerospace, and consumer goods production.
Healthcare:
Six Sigma has been instrumental in improving patient care and safety. Hospitals and healthcare providers use it to reduce medical errors, decrease patient waiting times, and enhance administrative processes.
Applications include optimizing emergency room operations, reducing hospital-acquired infections, and streamlining billing processes.
Education:
Educational institutions use Six Sigma to enhance administrative processes, improve curriculum delivery, and optimize resource allocation.
Applications range from streamlining student enrollment processes to reducing dropout rates.
Government and Public Services:
Government agencies apply Six Sigma to improve public services, streamline administrative processes, and reduce costs.
Applications include optimizing the issuance of permits and licenses, enhancing public transportation, and improving emergency response times.
Energy and Utilities:
Energy companies use Six Sigma to optimize power generation and distribution, reduce energy waste, and enhance safety procedures.
Applications include improving equipment maintenance, reducing energy consumption, and ensuring regulatory compliance.
These are just a few examples of the many industries where Six Sigma methodologies, including those implemented by Yellow Belts, have been effectively applied to drive process improvements, reduce costs, and enhance quality. The versatility of Six Sigma makes it a valuable tool in virtually any sector seeking to improve its operations.
Yellow Belt vs. Other Six Sigma Belts
Six Sigma certifications come in various levels, including Yellow Belt, Green Belt, Black Belt, and Master Black Belt. Each of these belts represents a different level of expertise and responsibility within the Six Sigma framework. Here's a comparison of Yellow Belt with other Six Sigma belts:
Yellow Belt:
Role: Yellow Belts are typically team members or support staff in Six Sigma projects. They play a foundational role, assisting Green Belts, Black Belts, and Master Black Belts in process improvement initiatives.
Responsibilities: They contribute to projects by assisting with data collection, process mapping, basic analysis, and problem-solving tasks. Yellow Belts often work on smaller-scale projects or specific aspects of larger projects.
Training: Yellow Belt training provides a basic understanding of Six Sigma principles, the DMAIC methodology, and core tools used in process improvement.
Certification: Earning a Yellow Belt certification requires completing training and passing an exam. It is an entry-level certification.
Green Belt:
Role: Green Belts lead process improvement projects and work under the guidance of Black Belts. They are responsible for project management and data analysis.
Responsibilities: Green Belts are more directly involved in the DMAIC process, including problem identification, root cause analysis, solution implementation, and process control.
Training: Green Belt training is more comprehensive than Yellow Belt training, covering advanced tools and statistical techniques.
Certification: Earning a Green Belt certification involves completing training, demonstrating proficiency through a project, and often passing an exam.
Black Belt:
Role: Black Belts are project leaders and are responsible for overseeing complex Six Sigma projects. They are often involved in multiple projects simultaneously.
Responsibilities: Black Belts are expected to have a deep understanding of Six Sigma tools and techniques. They identify projects, lead teams, and drive significant process improvements.
Training: Black Belt training is extensive, covering advanced statistical analysis, project management, and leadership skills.
Certification: Earning a Black Belt certification involves completing intensive training, leading successful projects, and passing a certification exam.
In summary, the primary differences between the various Six Sigma belts lie in their level of expertise, responsibilities, and the complexity of projects they handle. Yellow Belts are entry-level participants, Green Belts lead specific projects, Black Belts manage complex projects, and Master Black Belts are experts who guide and mentor others. The choice of belt level depends on one's career goals, level of expertise, and the scope of desired involvement in Six Sigma projects.
Real-World Examples
Real-world examples of Six Sigma Yellow Belt projects and their outcomes illustrate the practical applications of this methodology in improving processes and reducing defects. Here are a few examples:
Manufacturing Industry:
Project: A manufacturing company noticed high defect rates in a particular product line. A Yellow Belt team was formed to identify and address the root causes.
Outcome: Through process analysis and the implementation of changes, they reduced defect rates by 30% and increased production efficiency.
Healthcare Industry:
Project: A hospital's emergency department had long patient wait times and overcrowding issues. A Yellow Belt team was tasked with reducing waiting times and improving patient flow.
Outcome: The team implemented new triage processes, improved communication among staff, and streamlined admission procedures, resulting in a 40% reduction in wait times.
IT Services:Project: An IT support department had high call resolution times and frequent escalations. A Yellow Belt team worked on improving support processes.
Outcome: They restructured the support flow, developed a knowledge base, and provided additional training for staff. As a result, call resolution times decreased by 50%, and escalations reduced significantly.
Education:Project: A school district was facing budget constraints and wanted to optimize transportation routes for school buses. A Yellow Belt team was tasked with improving route efficiency.
Outcome: By analyzing bus schedules and optimizing routes, the district saved 15% in transportation costs while maintaining service quality.
These examples demonstrate how Six Sigma Yellow Belts can make meaningful contributions to process improvement across diverse industries. While they may not lead the projects independently, their involvement in problem-solving and data analysis plays a crucial role in achieving positive outcomes. Additionally, these successes showcase the versatility of Six Sigma in addressing a wide range of process-related challenges.
Preparing for the Yellow Belt Exam
Preparing for a Yellow Belt certification exam in Six Sigma involves systematic study, practice, and a clear understanding of the key concepts and tools associated with the methodology. Here's a step-by-step guide to help you prepare for your Yellow Belt exam:
Understand the Exam Format:Start by familiarizing yourself with the structure and format of the Yellow Belt exam. Understand the number of questions, time constraints, and any specific requirements for the exam.
Review Training Materials:Revisit your Yellow Belt training materials, including textbooks, lecture notes, and any online resources provided during your training. Ensure you have a solid grasp of the fundamental concepts, principles, and tools of Six Sigma.
Use Study Guides:Consider using study guides or reference materials designed specifically for Six Sigma Yellow Belt certification. These resources often provide concise summaries of key topics and sample questions.
Self-Assessments:Take self-assessment quizzes and tests to identify your strengths and
Time Management:Develop a study schedule that allows you to allocate sufficient time for each topic. Consistent, organized studying can help you cover all relevant content before the exam.
Mock Exams:Take full-length mock exams under timed conditions to simulate the exam experience. This helps you become comfortable with the format and identify areas that need improvement.
Remember that effective preparation is not just about memorizing facts but understanding the underlying principles and being able to apply them in real-world scenarios. By following these steps and staying committed to your study plan, you'll increase your chances of success in the Yellow Belt certification exam.
Career Advancement and Opportunities
Earning a Six Sigma Yellow Belt certification can lead to several career advancement opportunities and benefits. Here's how this certification can positively impact your career:
Enhanced Problem-Solving Skills: Yellow Belt training equips you with problem-solving skills that are valuable in many industries. This skillset can make you a more effective and efficient employee, contributing to career growth.
Cross-Functional Collaboration: Six Sigma projects often involve cross-functional teams. Collaborating with colleagues from different departments can expand your network and expose you to new career prospects.
Certification Path: Earning a Yellow Belt can serve as a stepping stone to higher-level Six Sigma certifications, such as Green Belt or Black Belt. These advanced certifications open doors to more complex and impactful roles within an organization.
Salary Increase: Many organizations offer salary increases or bonuses for employees who obtain Six Sigma certifications due to the potential cost savings and quality improvements they bring to the organization.
Consulting Opportunities: After gaining experience and expertise as a Yellow Belt, you may consider a career in Six Sigma consulting, where you can help other organizations improve their processes.
In summary, a Six Sigma Yellow Belt certification can provide numerous career advantages, including the potential for promotions, salary increases, and the opportunity to work on impactful projects. It also equips you with valuable problem-solving skills that are relevant in many industries, making you a valuable asset in the job market.
Conclusion
In conclusion, Six Sigma Yellow Belt certification is a valuable step in your professional development journey. It equips you with foundational knowledge and skills in the Six Sigma methodology, problem-solving, and process improvement. Whether you're looking to advance your career within your current organization, transition to a new field, or pursue further Six Sigma certifications, the Yellow Belt is a worthwhile investment.
By understanding the principles of Six Sigma, learning how to use data-driven approaches to solve problems, and actively participating in process improvement projects, you can contribute to your organization's success and enhance your own career prospects. The benefits of Yellow Belt certification are numerous, from increased problem-solving abilities to potential salary enhancements and new career opportunities.
Remember that Yellow Belt certification is just the beginning of your Six Sigma journey. With dedication, continued learning, and the possibility of pursuing higher-level certifications, you can make a significant impact in your organization and in your own career advancement. Whether you're in manufacturing, healthcare, finance, or any other industry, Six Sigma principles can lead to improved quality, efficiency, and competitiveness.
So, as you embark on your Yellow Belt certification journey, embrace the opportunity to learn and grow. Keep in mind that Six Sigma is not just about achieving certification; it's about applying these valuable principles and tools to create meaningful, positive change in the processes and systems that shape our professional world.
Read More
Six Sigma Yellow Belt certification is a fundamental level of certification within the Six Sigma methodology, a data-driven approach to process improvement aimed at reducing defects and variations in a process. It is an excellent starting point for individuals who want to enhance their problem-solving skills, contribute to process improvement efforts, and play a valuable role in organizational quality management.
Six Sigma Yellow Belt Certification is an entry-level certification that can open doors to the world of process improvement and quality management. It empowers individuals to apply data-driven methods to solve problems, make processes more efficient, and ultimately contribute to the success of their organization. It serves as a foundation for those who may choose to pursue higher levels of Six Sigma certification, such as Green Belt or Black Belt.
Table of contents
-
Understanding Six Sigma
-
Role of Yellow Belts in Six Sigma
-
Why Pursue a Yellow Belt Certification
-
Certification Requirements
-
Yellow Belt Training and Curriculum
-
Industry Applications
-
Yellow Belt vs. Other Six Sigma Belts
-
Real-World Examples
-
Preparing for the Yellow Belt Exam
-
Career Advancement and Opportunities
-
Conclusion
Understanding Six Sigma
Six Sigma is a systematic and data-driven methodology for process improvement. Originally developed by Motorola in the 1980s, it has become widely adopted by organizations in various industries to enhance product and service quality, reduce defects, and streamline processes. The term "Six Sigma" refers to a statistical measure of process variation, and the goal of Six Sigma is to minimize process variation to a level where only 3.4 defects per million opportunities occur, thereby achieving near-perfect performance.
Here are the key components and concepts that help in understanding Six Sigma:
DMAIC Methodology: Six Sigma follows a structured problem-solving methodology known as DMAIC, which stands for:
Process Variation: Central to Six Sigma is the concept of process variation. Processes naturally have variations, but Six Sigma seeks to reduce and control these variations to ensure consistency and quality.
Data-Driven Approach: Six Sigma heavily relies on data analysis to make informed decisions. Statistical tools and methods are used to collect, measure, and analyze data to understand the current state of processes and identify areas for improvement.
Roles and Belts: Within a Six Sigma program, individuals are often assigned different roles based on their level of expertise. These roles include Yellow Belts, Green Belts, and Black Belts, each with increasing levels of knowledge and responsibility.
Customer Focus: Six Sigma places a strong emphasis on understanding and meeting customer requirements. It seeks to align process improvement efforts with what customers value.
Continuous Improvement: Six Sigma promotes a culture of continuous improvement. It's not a one-time project but an ongoing philosophy that strives to make incremental and sustainable changes to processes.
In summary, Six Sigma is a disciplined and data-driven approach to process improvement and problem-solving. It seeks to reduce process variation, improve quality, and ultimately enhance an organization's competitiveness and customer satisfaction. Understanding and implementing Six Sigma principles can lead to more efficient and effective processes across a wide range of industries.
Role of Yellow Belts in Six Sigma
Six Sigma Yellow Belts play a vital role in the Six Sigma methodology, supporting process improvement initiatives within an organization. While they may not have the same level of expertise and responsibility as Green Belts or Black Belts, Yellow Belts are essential team members who contribute to the success of Six Sigma projects. Here's an overview of their role:
Data Collection: Yellow Belts are responsible for gathering and organizing data related to the process under examination. They ensure that accurate and relevant data is collected to support the project's goals.
Process Mapping: They help create process maps or flowcharts to document the current process. This visual representation aids in identifying bottlenecks, redundancies, and areas for potential improvement.
Participation in Improvement Projects: Yellow Belts actively participate in process improvement projects led by Green Belts or Black Belts. They collaborate with team members to implement changes and solutions.
Problem-Solving: They assist in problem-solving activities by contributing their insights and observations. Yellow Belts may be asked to brainstorm potential causes of issues and help investigate root causes.
Basic Analysis: Yellow Belts use basic Six Sigma tools and techniques to analyze data and identify trends or patterns. They may create histograms, Pareto charts, and other simple visual aids to understand data.
In summary, Yellow Belts are entry-level Six Sigma practitioners who contribute to process improvement initiatives by collecting data, participating in projects, and supporting Green Belts and Black Belts. They are valuable team members in the pursuit of quality and efficiency improvements within an organization. While they may not lead projects, their contributions are essential for successful Six Sigma implementations.
Why Pursue a Yellow Belt Certification
Pursuing a Yellow Belt certification in Six Sigma can offer individuals and organizations several significant benefits. Here are some compelling reasons why you might consider pursuing a Yellow Belt certification:
Basic Understanding of Six Sigma: Yellow Belt training provides a foundational understanding of the Six Sigma methodology. It introduces you to the core principles, concepts, and tools used in Six Sigma process improvement projects.
Enhanced Problem-Solving Skills: Yellow Belt certification equips you with problem-solving skills that can be applied to various situations, both in your professional and personal life. You'll learn to analyze data and make informed decisions.
Career Advancement: Earning a Yellow Belt certification can enhance your resume and open doors to new career opportunities. Many employers value Six Sigma certifications and seek candidates who can contribute to process improvement efforts.
Contribution to Quality Improvement: Yellow Belts play a critical role in improving product or service quality and customer satisfaction. By identifying and addressing process issues, you contribute to your organization's success.
Organizational Impact: By addressing process issues and enhancing efficiency, Yellow Belts can positively impact their organization's performance and competitiveness in the market.
Continuous Learning: Six Sigma is a continuous improvement philosophy. Pursuing a Yellow Belt certification demonstrates your commitment to learning and evolving as a professional.
Pursuing a Yellow Belt certification in Six Sigma is a valuable investment in your professional development. It equips you with problem-solving skills, enhances your understanding of quality management, and can lead to career opportunities while simultaneously benefitting your organization through process improvement.
Certification Requirements
Certification requirements for a Six Sigma Yellow Belt may vary depending on the certifying body and the organization. However, there are common elements that are typically involved in obtaining a Yellow Belt certification. Below are the general certification requirements:
Training: Most Yellow Belt certifications require candidates to complete a specified amount of training. This training can be provided through in-person workshops, online courses, or a combination of both. Training may cover Six Sigma principles, the DMAIC methodology, and essential tools and techniques.
Coursework: Candidates are often required to complete coursework related to Six Sigma Yellow Belt concepts. This coursework may include reading materials, lectures, quizzes, and assignments.
Examination: After completing the training and coursework, candidates must pass a certification exam. The exam assesses their knowledge of Six Sigma principles, DMAIC, and problem-solving techniques. The passing score may vary depending on the certifying body but is typically set at a certain percentage.
Certification Fee: There is usually a fee associated with obtaining a Yellow Belt certification. This fee covers the cost of training, materials, examination, and certification processing.
It's important to note that different organizations and certifying bodies may have variations in their certification requirements, so it's essential to check the specific requirements of the program you are interested in. Additionally, the level of rigor and the depth of content covered in Yellow Belt programs can vary, so it's a good idea to select a program that aligns with your career goals and the depth of knowledge you wish to gain.
Yellow Belt Training and Curriculum
Yellow Belt training in Six Sigma is designed to provide individuals with a foundational understanding of the Six Sigma methodology and equip them with essential problem-solving and process improvement skills. The training typically covers a range of topics and concepts related to quality management. Below is an overview of the common elements included in Yellow Belt training and curriculum:
Introduction to Six Sigma:
Understanding the origins and evolution of Six Sigma.
The importance of quality management and its impact on organizations.
Six Sigma Principles:
Explaining the key principles and philosophies of Six Sigma.
The focus on data-driven decision-making and minimizing process variation.
Process Improvement Projects:
Understanding the various components of a Six Sigma project.
Identifying project selection criteria and defining project scope.
Project Team Dynamics:
Effective teamwork and collaboration within a Six Sigma project team.
Communication and problem-solving skills for team members.
Case Studies and Practical Examples:
Real-world examples of successful Six Sigma projects.
Analyzing how Six Sigma principles were applied to solve specific problems and achieve results.
Certification Preparation:
Guidance on preparing for the Yellow Belt certification exam, including sample questions and practice exams.
Review of key concepts covered in the training.
Practical Application (optional):
Hands-on exercises or a small-scale Six Sigma project may be included as part of the training to allow participants to apply their knowledge in a real-world context.
Yellow Belt training can be delivered through in-person workshops, online courses, or a combination of both, depending on the program and the certifying body. The curriculum is typically designed to be accessible to individuals with various levels of experience and backgrounds, making it an excellent starting point for those looking to gain proficiency in Six Sigma principles and methodologies.
Industry Applications
Six Sigma methodologies, including Yellow Belt principles, have been widely adopted across various industries due to their effectiveness in improving processes, reducing defects, and enhancing overall quality. Here are some industry-specific applications of Six Sigma:
Manufacturing:
In manufacturing, Six Sigma helps reduce defects and variations in the production process. It's used to improve product quality, increase efficiency, and minimize waste.
Applications range from automotive manufacturing to electronics, aerospace, and consumer goods production.
Healthcare:
Six Sigma has been instrumental in improving patient care and safety. Hospitals and healthcare providers use it to reduce medical errors, decrease patient waiting times, and enhance administrative processes.
Applications include optimizing emergency room operations, reducing hospital-acquired infections, and streamlining billing processes.
Education:
Educational institutions use Six Sigma to enhance administrative processes, improve curriculum delivery, and optimize resource allocation.
Applications range from streamlining student enrollment processes to reducing dropout rates.
Government and Public Services:
Government agencies apply Six Sigma to improve public services, streamline administrative processes, and reduce costs.
Applications include optimizing the issuance of permits and licenses, enhancing public transportation, and improving emergency response times.
Energy and Utilities:
Energy companies use Six Sigma to optimize power generation and distribution, reduce energy waste, and enhance safety procedures.
Applications include improving equipment maintenance, reducing energy consumption, and ensuring regulatory compliance.
These are just a few examples of the many industries where Six Sigma methodologies, including those implemented by Yellow Belts, have been effectively applied to drive process improvements, reduce costs, and enhance quality. The versatility of Six Sigma makes it a valuable tool in virtually any sector seeking to improve its operations.
Yellow Belt vs. Other Six Sigma Belts
Six Sigma certifications come in various levels, including Yellow Belt, Green Belt, Black Belt, and Master Black Belt. Each of these belts represents a different level of expertise and responsibility within the Six Sigma framework. Here's a comparison of Yellow Belt with other Six Sigma belts:
Yellow Belt:
Role: Yellow Belts are typically team members or support staff in Six Sigma projects. They play a foundational role, assisting Green Belts, Black Belts, and Master Black Belts in process improvement initiatives.
Responsibilities: They contribute to projects by assisting with data collection, process mapping, basic analysis, and problem-solving tasks. Yellow Belts often work on smaller-scale projects or specific aspects of larger projects.
Training: Yellow Belt training provides a basic understanding of Six Sigma principles, the DMAIC methodology, and core tools used in process improvement.
Certification: Earning a Yellow Belt certification requires completing training and passing an exam. It is an entry-level certification.
Green Belt:
Role: Green Belts lead process improvement projects and work under the guidance of Black Belts. They are responsible for project management and data analysis.
Responsibilities: Green Belts are more directly involved in the DMAIC process, including problem identification, root cause analysis, solution implementation, and process control.
Training: Green Belt training is more comprehensive than Yellow Belt training, covering advanced tools and statistical techniques.
Certification: Earning a Green Belt certification involves completing training, demonstrating proficiency through a project, and often passing an exam.
Black Belt:
Role: Black Belts are project leaders and are responsible for overseeing complex Six Sigma projects. They are often involved in multiple projects simultaneously.
Responsibilities: Black Belts are expected to have a deep understanding of Six Sigma tools and techniques. They identify projects, lead teams, and drive significant process improvements.
Training: Black Belt training is extensive, covering advanced statistical analysis, project management, and leadership skills.
Certification: Earning a Black Belt certification involves completing intensive training, leading successful projects, and passing a certification exam.
In summary, the primary differences between the various Six Sigma belts lie in their level of expertise, responsibilities, and the complexity of projects they handle. Yellow Belts are entry-level participants, Green Belts lead specific projects, Black Belts manage complex projects, and Master Black Belts are experts who guide and mentor others. The choice of belt level depends on one's career goals, level of expertise, and the scope of desired involvement in Six Sigma projects.
Real-World Examples
Real-world examples of Six Sigma Yellow Belt projects and their outcomes illustrate the practical applications of this methodology in improving processes and reducing defects. Here are a few examples:
Manufacturing Industry:
Project: A manufacturing company noticed high defect rates in a particular product line. A Yellow Belt team was formed to identify and address the root causes.
Outcome: Through process analysis and the implementation of changes, they reduced defect rates by 30% and increased production efficiency.
Healthcare Industry:
Project: A hospital's emergency department had long patient wait times and overcrowding issues. A Yellow Belt team was tasked with reducing waiting times and improving patient flow.
Outcome: The team implemented new triage processes, improved communication among staff, and streamlined admission procedures, resulting in a 40% reduction in wait times.
IT Services:Project: An IT support department had high call resolution times and frequent escalations. A Yellow Belt team worked on improving support processes.
Outcome: They restructured the support flow, developed a knowledge base, and provided additional training for staff. As a result, call resolution times decreased by 50%, and escalations reduced significantly.
Education:Project: A school district was facing budget constraints and wanted to optimize transportation routes for school buses. A Yellow Belt team was tasked with improving route efficiency.
Outcome: By analyzing bus schedules and optimizing routes, the district saved 15% in transportation costs while maintaining service quality.
These examples demonstrate how Six Sigma Yellow Belts can make meaningful contributions to process improvement across diverse industries. While they may not lead the projects independently, their involvement in problem-solving and data analysis plays a crucial role in achieving positive outcomes. Additionally, these successes showcase the versatility of Six Sigma in addressing a wide range of process-related challenges.
Preparing for the Yellow Belt Exam
Preparing for a Yellow Belt certification exam in Six Sigma involves systematic study, practice, and a clear understanding of the key concepts and tools associated with the methodology. Here's a step-by-step guide to help you prepare for your Yellow Belt exam:
Understand the Exam Format:Start by familiarizing yourself with the structure and format of the Yellow Belt exam. Understand the number of questions, time constraints, and any specific requirements for the exam.
Review Training Materials:Revisit your Yellow Belt training materials, including textbooks, lecture notes, and any online resources provided during your training. Ensure you have a solid grasp of the fundamental concepts, principles, and tools of Six Sigma.
Use Study Guides:Consider using study guides or reference materials designed specifically for Six Sigma Yellow Belt certification. These resources often provide concise summaries of key topics and sample questions.
Self-Assessments:Take self-assessment quizzes and tests to identify your strengths and
Time Management:Develop a study schedule that allows you to allocate sufficient time for each topic. Consistent, organized studying can help you cover all relevant content before the exam.
Mock Exams:Take full-length mock exams under timed conditions to simulate the exam experience. This helps you become comfortable with the format and identify areas that need improvement.
Remember that effective preparation is not just about memorizing facts but understanding the underlying principles and being able to apply them in real-world scenarios. By following these steps and staying committed to your study plan, you'll increase your chances of success in the Yellow Belt certification exam.
Career Advancement and Opportunities
Earning a Six Sigma Yellow Belt certification can lead to several career advancement opportunities and benefits. Here's how this certification can positively impact your career:
Enhanced Problem-Solving Skills: Yellow Belt training equips you with problem-solving skills that are valuable in many industries. This skillset can make you a more effective and efficient employee, contributing to career growth.
Cross-Functional Collaboration: Six Sigma projects often involve cross-functional teams. Collaborating with colleagues from different departments can expand your network and expose you to new career prospects.
Certification Path: Earning a Yellow Belt can serve as a stepping stone to higher-level Six Sigma certifications, such as Green Belt or Black Belt. These advanced certifications open doors to more complex and impactful roles within an organization.
Salary Increase: Many organizations offer salary increases or bonuses for employees who obtain Six Sigma certifications due to the potential cost savings and quality improvements they bring to the organization.
Consulting Opportunities: After gaining experience and expertise as a Yellow Belt, you may consider a career in Six Sigma consulting, where you can help other organizations improve their processes.
In summary, a Six Sigma Yellow Belt certification can provide numerous career advantages, including the potential for promotions, salary increases, and the opportunity to work on impactful projects. It also equips you with valuable problem-solving skills that are relevant in many industries, making you a valuable asset in the job market.
Conclusion
In conclusion, Six Sigma Yellow Belt certification is a valuable step in your professional development journey. It equips you with foundational knowledge and skills in the Six Sigma methodology, problem-solving, and process improvement. Whether you're looking to advance your career within your current organization, transition to a new field, or pursue further Six Sigma certifications, the Yellow Belt is a worthwhile investment.
By understanding the principles of Six Sigma, learning how to use data-driven approaches to solve problems, and actively participating in process improvement projects, you can contribute to your organization's success and enhance your own career prospects. The benefits of Yellow Belt certification are numerous, from increased problem-solving abilities to potential salary enhancements and new career opportunities.
Remember that Yellow Belt certification is just the beginning of your Six Sigma journey. With dedication, continued learning, and the possibility of pursuing higher-level certifications, you can make a significant impact in your organization and in your own career advancement. Whether you're in manufacturing, healthcare, finance, or any other industry, Six Sigma principles can lead to improved quality, efficiency, and competitiveness.
So, as you embark on your Yellow Belt certification journey, embrace the opportunity to learn and grow. Keep in mind that Six Sigma is not just about achieving certification; it's about applying these valuable principles and tools to create meaningful, positive change in the processes and systems that shape our professional world.
Top Benefits of CTFL Certification for Career Advancement
In the ever-evolving landscape of software development, quality assurance and testing play a pivotal role in ensuring that applications and systems perform flawlessly. The Certified Tester Foundation Level (CTFL) certification stands as a beacon for those aspiring to excel in the field of software testing. It is a globally recognized and respected certification that opens doors to a world of opportunities in the realms of quality assurance and software testing. In this article, we will explore the numerous benefits of CTFL certification, shedding light on how it can empower individuals and organizations alike in their quest for excellence in software testing.
CTFL certification, like a well-constructed test plan, is structured to validate the skills and knowledge of aspiring software testers. It offers a multitude of advantages that extend beyond simply adding a prestigious credential to your name. This certification has the potential to reshape your career, enhance your skills, and contribute significantly to the quality and reliability of the software you are responsible for testing.
Let's dive deeper into the benefits of CTFL certification, from improved career prospects to enhanced testing capabilities, and discover why this certification is a game-changer in the world of software testing.
Table of Contents
-
Career Advancement
-
Global Recognition
-
Skill Enhancement
-
Quality Assurance Impact
-
Increased Marketability
-
Career Transition
-
Knowledge Expansion
-
Professional Networking
-
Organizational Benefits
-
Long-Term Career Growth
-
Conclusion
Career Advancement
In today's competitive job market, professionals are constantly seeking ways to distinguish themselves and achieve career growth. One powerful strategy to achieve career advancement, especially in the realm of software testing and quality assurance, is obtaining the Certified Tester Foundation Level (CTFL) certification. This certification offers a myriad of benefits that can significantly impact your career trajectory. Here's how:
Increased Employability: CTFL certification makes you a more attractive candidate to employers. It demonstrates your commitment to your field and validates your knowledge and skills in software testing. As a result, you become a preferred choice for hiring managers when filling positions related to quality assurance.
Career Opportunities: CTFL opens doors to a broader range of job opportunities. Whether you are seeking a new position, looking to switch industries, or aiming for a promotion within your current organization, having CTFL on your resume can make a substantial difference. Many job postings explicitly require or prefer candidates with testing certifications.
Salary Advancement: It's no secret that certified professionals often command higher salaries. CTFL certification can lead to better compensation packages, including increased base pay, bonuses, and benefits. Employers are willing to pay more for professionals who bring demonstrable skills and expertise to the table.
Career Progression: Career advancement isn't just about securing a job; it's also about climbing the career ladder. CTFL certification provides a solid foundation for further career progression. It can serve as a stepping stone to more advanced certifications and senior roles within the software testing domain.
Improved Job Security: With the increasing demand for quality software, CTFL-certified professionals tend to enjoy more job security. In times of economic uncertainty, organizations are less likely to let go of employees who are essential to ensuring the quality of their products.
CTFL certification is a strategic investment in your career. It enhances your employability, increases your career opportunities, and can lead to higher earnings. Beyond the financial aspects, it also nurtures your professional growth, offering job security and the potential for leadership roles. In the dynamic field of software testing, CTFL certification is a pathway to a rewarding and successful career.
Global Recognition
In an increasingly interconnected world, the value of professional certifications extends far beyond local or regional boundaries. The Certified Tester Foundation Level (CTFL) certification is a prime example of a qualification that enjoys widespread global recognition and respect. This recognition has several significant implications for those who hold the CTFL certification:
International Employability: One of the most compelling benefits of CTFL certification is that it's universally recognized. Whether you are looking to work in your home country or explore opportunities abroad, having CTFL on your resume assures potential employers of your standardized expertise in software testing. This opens doors to a diverse range of international job markets.
Consistency in Skill Set: CTFL's global recognition means that certified professionals share a common knowledge base and understanding of software testing practices. This consistency ensures that employers, regardless of their location, can rely on the skills and competencies of CTFL-certified individuals.
Trust and Credibility: CTFL is endorsed by a variety of prominent organizations and industry bodies. This certification carries an assurance of quality and reliability. Employers often trust the certification as a benchmark of excellence in software testing.
Cross-Industry Applicability: The principles and best practices in software testing are universal and relevant across various industries. CTFL's global recognition allows certified professionals to transition seamlessly between different sectors, such as healthcare, finance, automotive, and more.
Alignment with Industry Standards: CTFL aligns with international testing and quality standards, including those defined by the International Software Testing Qualifications Board (ISTQB). This alignment ensures that CTFL-certified individuals have a strong foundation in globally accepted testing methodologies.
International Collaboration: Being part of the CTFL-certified community provides opportunities for international collaboration. You can connect with professionals from diverse backgrounds, share knowledge, and stay updated on global testing trends and practices.
Competitive Advantage: When competing for job roles or promotions, CTFL certification can give you a significant competitive advantage. Employers often prioritize candidates with internationally recognized certifications to ensure their teams adhere to global testing standards.
In summary, the global recognition of CTFL certification is not just a label; it's a powerful testament to your skills and expertise in software testing that transcends borders. This recognition facilitates international career opportunities, provides a foundation for consistent quality, and positions you as a credible and trusted professional in the ever-expanding global software testing community.
Skill Enhancement
Certainly, let's delve into the subtopic of "Skill Enhancement" and explore how the Certified Tester Foundation Level (CTFL) certification can significantly enhance one's skills in the field of software testing:
Skill Enhancement with CTFL Certification
In the dynamic and ever-evolving realm of software testing, the ability to adapt, learn, and master new skills is essential for professional growth. CTFL certification is a gateway to skill enhancement, providing individuals with a structured and comprehensive foundation in software testing. Here's how CTFL enhances one's skills:
Comprehensive Understanding of Software Testing: CTFL certification equips professionals with a holistic understanding of software testing concepts, methodologies, and techniques. This includes knowledge of test planning, test design, test execution, and test management. By mastering these fundamentals, CTFL-certified individuals can contribute more effectively to the testing process.
Practical Testing Techniques: CTFL covers practical testing techniques that are essential for efficient software testing. It includes topics like boundary value analysis, equivalence partitioning, and decision table testing. These techniques enable testers to design and execute test cases that identify defects and improve software quality.
Test Documentation: Effective communication and documentation are key skills in software testing. CTFL certification emphasizes the creation of clear and well-organized test documentation, including test plans, test cases, and test reports. This skill enhances transparency and collaboration within testing teams.
Test Management: CTFL provides insights into test management practices, which involve planning, monitoring, and controlling testing activities. Understanding test management allows professionals to ensure that testing efforts align with project goals and timelines.
Effective Communication: Effective communication is vital for collaborating with development teams, stakeholders, and fellow testers. CTFL training encourages clear and concise communication, improving teamwork and understanding of testing objectives.
CTFL certification is a powerful catalyst for skill enhancement in the software testing domain. It imparts a strong foundation of knowledge and practical skills, enabling professionals to excel in their testing roles. By continually honing their abilities and staying up-to-date with industry best practices, CTFL-certified individuals can contribute significantly to the quality and reliability of the software they test.
Quality Assurance Impact
Quality assurance (QA) is at the heart of delivering reliable and high-quality software products. CTFL certification plays a pivotal role in enhancing and contributing to the overall quality assurance process. Here's how CTFL certification can impact quality assurance:
Early Defect Detection: CTFL emphasizes the importance of detecting defects at an early stage of the software development life cycle. CTFL-certified testers are trained to create test cases that catch defects before they propagate to later phases, reducing the cost and effort required for fixing them.
Enhanced Test Coverage: Quality assurance is closely linked to comprehensive test coverage. CTFL-certified individuals are skilled in various testing techniques and approaches that ensure a wider range of scenarios are considered during testing. This increased coverage leads to better assurance of software quality.
Consistency in Testing: Standardized testing practices and terminology are emphasized in CTFL training. This consistency across testing efforts enhances collaboration within QA teams and between development and testing teams, resulting in higher quality products.
Reduced Software Defects: CTFL-certified professionals are well-versed in identifying, reporting, and managing software defects. This leads to a decrease in the number of critical defects that reach the production phase, ultimately improving the end-user experience.
Collaboration and Communication: Effective communication is vital in quality assurance. CTFL training promotes clear and concise communication among team members, including developers, stakeholders, and fellow testers. This enhances collaboration and understanding of quality objectives.
CTFL certification has a profound impact on quality assurance within the software development process. It empowers professionals to adopt best practices, improve defect detection, and ensure the consistency and reliability of the software being tested. The result is higher-quality software products that meet or exceed user expectations, ultimately contributing to the success of software projects and the satisfaction of end-users.
Increased Marketability
In today's competitive job market, having a strong skill set and relevant certifications can significantly boost your marketability. The CTFL certification, with its global recognition and focus on fundamental software testing knowledge, can make you a more attractive candidate to employers. Here's how CTFL certification increases your marketability:
Attractiveness to Employers: CTFL certification on your resume immediately sets you apart from other candidates. Employers often receive a large number of applications for job openings, and having a recognized certification demonstrates your commitment and expertise in software testing.
Wider Job Opportunities: CTFL certification opens the door to a broader range of job opportunities. Many job postings explicitly require or prefer candidates with testing certifications, giving you access to a variety of roles in different industries and sectors.
Industry Recognition: CTFL is internationally recognized and respected in the software testing industry. This recognition carries weight and establishes your credibility as a competent tester, regardless of your prior experience.
Confidence Boost: Being CTFL-certified boosts your self-confidence. Knowing that you have achieved a globally recognized certification enhances your self-assurance, making you more convincing in job interviews and discussions with potential employers.
Networking Opportunities: CTFL certification often connects you to a community of certified professionals. This network can provide valuable mentorship, guidance, and opportunities for collaboration, helping you expand your professional connections and discover new career possibilities.
CTFL certification significantly enhances your marketability in the software testing industry. It makes you a more appealing candidate for job opportunities, increases your earning potential, and positions you as a credible and proficient tester. This certification serves as a valuable investment in your career, providing long-term benefits in a competitive job market.
Career Transition
Changing careers can be a challenging and rewarding journey, and the CTFL certification can be a valuable asset in facilitating a transition into the field of software testing. Here's how CTFL certification can help individuals navigate a successful career transition:
Establishing Credibility: Career transitions often involve moving into a field where you may have limited prior experience. CTFL certification establishes your credibility and competence as a software tester, which can be reassuring to potential employers who may have concerns about your background.
Fundamental Knowledge: CTFL provides a foundational understanding of software testing principles and practices. It equips you with essential knowledge and skills, even if you are new to the field, giving you the confidence to contribute effectively in a testing role.
Career Entry: Many employers look for CTFL-certified individuals when hiring entry-level testers. This certification can be a foot in the door, making it easier to secure your first job in the software testing industry.
Networking Opportunities: CTFL certification often connects you with a community of certified professionals. This network can provide mentorship, guidance, and job leads, making your transition smoother and more informed.
Continuous Learning: CTFL certification instills a mindset of continuous learning. As you transition into a new career, this mindset will serve you well as you adapt to changing industry trends and technologies.
CTFL certification is an excellent resource for those seeking to make a career transition into the software testing field. It helps establish your credibility, provides foundational knowledge, and connects you to a supportive community. This certification is an invaluable tool to help you embark on a new and promising career in software testing, regardless of your prior professional background.
Knowledge Expansion
Continuous learning is a cornerstone of professional growth, especially in the dynamic field of software testing. CTFL certification not only validates existing knowledge but also serves as a catalyst for knowledge expansion. Here's how CTFL certification contributes to knowledge expansion:
Fundamental Knowledge: CTFL certification provides a solid foundation in software testing principles, methodologies, and terminology. This foundational knowledge is essential for building a comprehensive understanding of the field.
Test Automation: CTFL touches on test automation, providing an introduction to automation concepts and tools. This knowledge is particularly valuable in today's testing landscape, where automation is a key focus.
Risk Assessment: CTFL teaches you to assess risks in the software testing process. Understanding risk allows you to make informed decisions about where to focus your testing efforts, expanding your capacity to address high-impact areas.
Quality Standards: CTFL aligns with international quality and testing standards, including those defined by the International Software Testing Qualifications Board (ISTQB). Familiarity with these standards ensures your work is in line with recognized benchmarks.
Documentation Skills: Effective communication and documentation are vital in software testing. CTFL places importance on clear and structured test documentation, fostering your documentation skills.
Problem-Solving: Software testing often requires critical thinking and creative problem-solving. CTFL certification hones these skills as you learn to identify defects, investigate their causes, and suggest effective solutions.
Networking: CTFL certification often connects you with a community of certified professionals. This network provides opportunities for knowledge sharing, collaboration, and mentorship, expanding your knowledge base through the experiences of others.
CTFL certification is not just a static credential; it's a journey of knowledge expansion. It introduces you to the core concepts and practices in software testing, setting the stage for ongoing learning and growth in the field. As you apply what you've learned and continue to explore new horizons, your knowledge and expertise in software testing will naturally expand, making you a more valuable asset in the industry.
Professional Networking
Networking is an essential aspect of career development, and CTFL certification can significantly enhance your professional networking opportunities in the field of software testing. Here's how CTFL certification contributes to professional networking:
Access to a Certified Community: CTFL certification often connects you to a global community of certified professionals. This community provides a valuable network of like-minded individuals who share your passion for software testing and quality assurance.
Career Opportunities: Your network of CTFL-certified professionals can serve as a valuable resource for job leads and career opportunities. You may learn about job openings, referrals, or recommendations through your network.
Conferences and Events: Many software testing conferences and events host gatherings for certified professionals. Attending these events provides you with in-person networking opportunities, where you can meet and connect with fellow CTFL-certified individuals.
Local Chapters and Associations: CTFL certification is often associated with local and national testing associations and chapters. Joining these associations provides opportunities to network with professionals in your region and get involved in community activities.
Job References and Recommendations: Your professional network can serve as references and provide recommendations when you seek new opportunities or career growth. Having a strong network of colleagues who can vouch for your skills and work ethic can be invaluable.
CTFL certification extends beyond validating your skills; it connects you with a community of professionals who share your passion for software testing. The network you build through CTFL certification can offer knowledge sharing, mentorship, collaboration, job opportunities, and valuable career insights, ultimately enriching your career in the software testing industry.
Organizational Benefits
Enhanced Software Quality: CTFL-certified professionals possess a strong understanding of testing principles and best practices. Their expertise leads to improved software quality, reducing the number of defects and ensuring that the software meets or exceeds user expectations.
Reduced Defects and Costs: Early defect detection by CTFL-certified testers results in a reduction of defects that reach the production phase. This leads to cost savings by minimizing the need for post-release bug fixes and patches, which can be expensive and time-consuming.
Efficient Testing Processes: CTFL certification ensures that testing processes are optimized and aligned with industry best practices. This efficiency streamlines testing efforts, reduces redundancy, and enhances productivity within the organization.
Consistency and Standardization: CTFL-certified professionals adhere to standardized terminology and practices. This consistency improves communication within the testing team and fosters a unified approach to software testing.
Risk Mitigation: CTFL certification equips professionals with skills in risk assessment. They can identify high-risk areas within projects and allocate testing resources accordingly, reducing the likelihood of critical issues going unnoticed.
Alignment with Industry Standards: CTFL certification aligns with internationally recognized testing standards, including those defined by the International Software Testing Qualifications Board (ISTQB). This alignment ensures that the organization's testing practices conform to industry-recognized benchmarks.
Enhanced Test Documentation: Effective communication and documentation are vital in software testing. CTFL certification promotes clear and structured test documentation, enhancing transparency and facilitating project management.
Adaptability to Industry Changes: CTFL-certified professionals are well-prepared to adapt to industry changes, such as new technologies and methodologies. This adaptability allows the organization to stay competitive and relevant in the evolving field of software testing.
CTFL certification brings numerous organizational benefits, including improved software quality, cost savings, efficient testing processes, and a competitive advantage in the market. Organizations that invest in CTFL-certified professionals can deliver higher-quality software products, reduce risks, and gain a reputation for reliability and excellence in the field of software testing.
Long-Term Career Growth
CTFL certification serves as a foundational stepping stone for professionals in the software testing field, providing numerous opportunities for long-term career growth. Here's how CTFL certification can contribute to your career advancement over time:
Foundation for Advanced Certifications: CTFL is often the first step in a series of software testing certifications. Building upon CTFL, you can pursue more advanced certifications such as Certified Tester Advanced Level (CTAL) or specialized certifications in areas like test automation, security testing, or performance testing. These advanced certifications can open doors to higher-level roles and increased earning potential.
Expanded Skill Set: As you gain practical experience and advance in your career, the knowledge and skills acquired through CTFL certification continue to benefit you. The foundational principles and best practices you've learned serve as a solid base for acquiring new and more specialized skills over time.
Leadership Opportunities: CTFL-certified professionals are often well-positioned to take on leadership roles within their organizations. With experience and additional training, you can move into positions such as Test Manager or Test Lead, where you'll be responsible for managing testing teams and overseeing testing efforts.
Consulting and Training: With advanced certifications and substantial experience, you may choose to venture into consulting or training. Becoming a testing consultant or trainer can be a rewarding career path, offering opportunities to work with various organizations and share your expertise.
Industry Involvement: Many CTFL-certified professionals actively participate in industry associations, forums, and conferences. Involvement in industry organizations can expand your network, expose you to emerging trends, and provide opportunities for thought leadership.
Job Security: As the demand for high-quality software continues to grow, CTFL-certified professionals often enjoy job security. Organizations value individuals who can ensure software quality, making your career in software testing more resilient.
CTFL certification is not just a one-time achievement; it's a foundation for long-term career growth in the software testing and quality assurance field. Whether you choose to specialize, pursue advanced certifications, or take on leadership roles, CTFL certification provides the knowledge and credibility necessary to support your journey to success in the ever-evolving world of software testing.
Conclusion
In conclusion, the Certified Tester Foundation Level (CTFL) certification offers a wide range of benefits for individuals, organizations, and the software testing industry as a whole.
For individuals, CTFL certification serves as a valuable credential that enhances their skills, employability, and marketability.CTFL-certified professionals often find themselves well-prepared for various roles, from entry-level positions to more advanced, specialized, and leadership roles. This certification not only validates their expertise but also fosters a culture of continuous learning and adaptability, ensuring long-term career growth.
For organizations, CTFL-certified professionals bring a wealth of advantages. They contribute to improved software quality, reduced defects, cost savings, and efficient testing processes. CTFL certification aligns with industry standards and promotes consistency in testing practices, mitigating risks and enhancing documentation and communication. As a result, organizations benefit from higher client satisfaction, a competitive edge, and a reputation for reliability and quality in the software testing domain.
In essence, CTFL certification is not just a single achievement; it's a dynamic and evolving journey. It supports the growth and success of individuals and organizations in the field of software testing, ensuring that software products are of high quality, meet user expectations, and contribute to the advancement of the software industry as a whole.
Read More
In the ever-evolving landscape of software development, quality assurance and testing play a pivotal role in ensuring that applications and systems perform flawlessly. The Certified Tester Foundation Level (CTFL) certification stands as a beacon for those aspiring to excel in the field of software testing. It is a globally recognized and respected certification that opens doors to a world of opportunities in the realms of quality assurance and software testing. In this article, we will explore the numerous benefits of CTFL certification, shedding light on how it can empower individuals and organizations alike in their quest for excellence in software testing.
CTFL certification, like a well-constructed test plan, is structured to validate the skills and knowledge of aspiring software testers. It offers a multitude of advantages that extend beyond simply adding a prestigious credential to your name. This certification has the potential to reshape your career, enhance your skills, and contribute significantly to the quality and reliability of the software you are responsible for testing.
Let's dive deeper into the benefits of CTFL certification, from improved career prospects to enhanced testing capabilities, and discover why this certification is a game-changer in the world of software testing.
Table of Contents
-
Career Advancement
-
Global Recognition
-
Skill Enhancement
-
Quality Assurance Impact
-
Increased Marketability
-
Career Transition
-
Knowledge Expansion
-
Professional Networking
-
Organizational Benefits
-
Long-Term Career Growth
-
Conclusion
Career Advancement
In today's competitive job market, professionals are constantly seeking ways to distinguish themselves and achieve career growth. One powerful strategy to achieve career advancement, especially in the realm of software testing and quality assurance, is obtaining the Certified Tester Foundation Level (CTFL) certification. This certification offers a myriad of benefits that can significantly impact your career trajectory. Here's how:
Increased Employability: CTFL certification makes you a more attractive candidate to employers. It demonstrates your commitment to your field and validates your knowledge and skills in software testing. As a result, you become a preferred choice for hiring managers when filling positions related to quality assurance.
Career Opportunities: CTFL opens doors to a broader range of job opportunities. Whether you are seeking a new position, looking to switch industries, or aiming for a promotion within your current organization, having CTFL on your resume can make a substantial difference. Many job postings explicitly require or prefer candidates with testing certifications.
Salary Advancement: It's no secret that certified professionals often command higher salaries. CTFL certification can lead to better compensation packages, including increased base pay, bonuses, and benefits. Employers are willing to pay more for professionals who bring demonstrable skills and expertise to the table.
Career Progression: Career advancement isn't just about securing a job; it's also about climbing the career ladder. CTFL certification provides a solid foundation for further career progression. It can serve as a stepping stone to more advanced certifications and senior roles within the software testing domain.
Improved Job Security: With the increasing demand for quality software, CTFL-certified professionals tend to enjoy more job security. In times of economic uncertainty, organizations are less likely to let go of employees who are essential to ensuring the quality of their products.
CTFL certification is a strategic investment in your career. It enhances your employability, increases your career opportunities, and can lead to higher earnings. Beyond the financial aspects, it also nurtures your professional growth, offering job security and the potential for leadership roles. In the dynamic field of software testing, CTFL certification is a pathway to a rewarding and successful career.
Global Recognition
In an increasingly interconnected world, the value of professional certifications extends far beyond local or regional boundaries. The Certified Tester Foundation Level (CTFL) certification is a prime example of a qualification that enjoys widespread global recognition and respect. This recognition has several significant implications for those who hold the CTFL certification:
International Employability: One of the most compelling benefits of CTFL certification is that it's universally recognized. Whether you are looking to work in your home country or explore opportunities abroad, having CTFL on your resume assures potential employers of your standardized expertise in software testing. This opens doors to a diverse range of international job markets.
Consistency in Skill Set: CTFL's global recognition means that certified professionals share a common knowledge base and understanding of software testing practices. This consistency ensures that employers, regardless of their location, can rely on the skills and competencies of CTFL-certified individuals.
Trust and Credibility: CTFL is endorsed by a variety of prominent organizations and industry bodies. This certification carries an assurance of quality and reliability. Employers often trust the certification as a benchmark of excellence in software testing.
Cross-Industry Applicability: The principles and best practices in software testing are universal and relevant across various industries. CTFL's global recognition allows certified professionals to transition seamlessly between different sectors, such as healthcare, finance, automotive, and more.
Alignment with Industry Standards: CTFL aligns with international testing and quality standards, including those defined by the International Software Testing Qualifications Board (ISTQB). This alignment ensures that CTFL-certified individuals have a strong foundation in globally accepted testing methodologies.
International Collaboration: Being part of the CTFL-certified community provides opportunities for international collaboration. You can connect with professionals from diverse backgrounds, share knowledge, and stay updated on global testing trends and practices.
Competitive Advantage: When competing for job roles or promotions, CTFL certification can give you a significant competitive advantage. Employers often prioritize candidates with internationally recognized certifications to ensure their teams adhere to global testing standards.
In summary, the global recognition of CTFL certification is not just a label; it's a powerful testament to your skills and expertise in software testing that transcends borders. This recognition facilitates international career opportunities, provides a foundation for consistent quality, and positions you as a credible and trusted professional in the ever-expanding global software testing community.
Skill Enhancement
Certainly, let's delve into the subtopic of "Skill Enhancement" and explore how the Certified Tester Foundation Level (CTFL) certification can significantly enhance one's skills in the field of software testing:
Skill Enhancement with CTFL Certification
In the dynamic and ever-evolving realm of software testing, the ability to adapt, learn, and master new skills is essential for professional growth. CTFL certification is a gateway to skill enhancement, providing individuals with a structured and comprehensive foundation in software testing. Here's how CTFL enhances one's skills:
Comprehensive Understanding of Software Testing: CTFL certification equips professionals with a holistic understanding of software testing concepts, methodologies, and techniques. This includes knowledge of test planning, test design, test execution, and test management. By mastering these fundamentals, CTFL-certified individuals can contribute more effectively to the testing process.
Practical Testing Techniques: CTFL covers practical testing techniques that are essential for efficient software testing. It includes topics like boundary value analysis, equivalence partitioning, and decision table testing. These techniques enable testers to design and execute test cases that identify defects and improve software quality.
Test Documentation: Effective communication and documentation are key skills in software testing. CTFL certification emphasizes the creation of clear and well-organized test documentation, including test plans, test cases, and test reports. This skill enhances transparency and collaboration within testing teams.
Test Management: CTFL provides insights into test management practices, which involve planning, monitoring, and controlling testing activities. Understanding test management allows professionals to ensure that testing efforts align with project goals and timelines.
Effective Communication: Effective communication is vital for collaborating with development teams, stakeholders, and fellow testers. CTFL training encourages clear and concise communication, improving teamwork and understanding of testing objectives.
CTFL certification is a powerful catalyst for skill enhancement in the software testing domain. It imparts a strong foundation of knowledge and practical skills, enabling professionals to excel in their testing roles. By continually honing their abilities and staying up-to-date with industry best practices, CTFL-certified individuals can contribute significantly to the quality and reliability of the software they test.
Quality Assurance Impact
Quality assurance (QA) is at the heart of delivering reliable and high-quality software products. CTFL certification plays a pivotal role in enhancing and contributing to the overall quality assurance process. Here's how CTFL certification can impact quality assurance:
Early Defect Detection: CTFL emphasizes the importance of detecting defects at an early stage of the software development life cycle. CTFL-certified testers are trained to create test cases that catch defects before they propagate to later phases, reducing the cost and effort required for fixing them.
Enhanced Test Coverage: Quality assurance is closely linked to comprehensive test coverage. CTFL-certified individuals are skilled in various testing techniques and approaches that ensure a wider range of scenarios are considered during testing. This increased coverage leads to better assurance of software quality.
Consistency in Testing: Standardized testing practices and terminology are emphasized in CTFL training. This consistency across testing efforts enhances collaboration within QA teams and between development and testing teams, resulting in higher quality products.
Reduced Software Defects: CTFL-certified professionals are well-versed in identifying, reporting, and managing software defects. This leads to a decrease in the number of critical defects that reach the production phase, ultimately improving the end-user experience.
Collaboration and Communication: Effective communication is vital in quality assurance. CTFL training promotes clear and concise communication among team members, including developers, stakeholders, and fellow testers. This enhances collaboration and understanding of quality objectives.
CTFL certification has a profound impact on quality assurance within the software development process. It empowers professionals to adopt best practices, improve defect detection, and ensure the consistency and reliability of the software being tested. The result is higher-quality software products that meet or exceed user expectations, ultimately contributing to the success of software projects and the satisfaction of end-users.
Increased Marketability
In today's competitive job market, having a strong skill set and relevant certifications can significantly boost your marketability. The CTFL certification, with its global recognition and focus on fundamental software testing knowledge, can make you a more attractive candidate to employers. Here's how CTFL certification increases your marketability:
Attractiveness to Employers: CTFL certification on your resume immediately sets you apart from other candidates. Employers often receive a large number of applications for job openings, and having a recognized certification demonstrates your commitment and expertise in software testing.
Wider Job Opportunities: CTFL certification opens the door to a broader range of job opportunities. Many job postings explicitly require or prefer candidates with testing certifications, giving you access to a variety of roles in different industries and sectors.
Industry Recognition: CTFL is internationally recognized and respected in the software testing industry. This recognition carries weight and establishes your credibility as a competent tester, regardless of your prior experience.
Confidence Boost: Being CTFL-certified boosts your self-confidence. Knowing that you have achieved a globally recognized certification enhances your self-assurance, making you more convincing in job interviews and discussions with potential employers.
Networking Opportunities: CTFL certification often connects you to a community of certified professionals. This network can provide valuable mentorship, guidance, and opportunities for collaboration, helping you expand your professional connections and discover new career possibilities.
CTFL certification significantly enhances your marketability in the software testing industry. It makes you a more appealing candidate for job opportunities, increases your earning potential, and positions you as a credible and proficient tester. This certification serves as a valuable investment in your career, providing long-term benefits in a competitive job market.
Career Transition
Changing careers can be a challenging and rewarding journey, and the CTFL certification can be a valuable asset in facilitating a transition into the field of software testing. Here's how CTFL certification can help individuals navigate a successful career transition:
Establishing Credibility: Career transitions often involve moving into a field where you may have limited prior experience. CTFL certification establishes your credibility and competence as a software tester, which can be reassuring to potential employers who may have concerns about your background.
Fundamental Knowledge: CTFL provides a foundational understanding of software testing principles and practices. It equips you with essential knowledge and skills, even if you are new to the field, giving you the confidence to contribute effectively in a testing role.
Career Entry: Many employers look for CTFL-certified individuals when hiring entry-level testers. This certification can be a foot in the door, making it easier to secure your first job in the software testing industry.
Networking Opportunities: CTFL certification often connects you with a community of certified professionals. This network can provide mentorship, guidance, and job leads, making your transition smoother and more informed.
Continuous Learning: CTFL certification instills a mindset of continuous learning. As you transition into a new career, this mindset will serve you well as you adapt to changing industry trends and technologies.
CTFL certification is an excellent resource for those seeking to make a career transition into the software testing field. It helps establish your credibility, provides foundational knowledge, and connects you to a supportive community. This certification is an invaluable tool to help you embark on a new and promising career in software testing, regardless of your prior professional background.
Knowledge Expansion
Continuous learning is a cornerstone of professional growth, especially in the dynamic field of software testing. CTFL certification not only validates existing knowledge but also serves as a catalyst for knowledge expansion. Here's how CTFL certification contributes to knowledge expansion:
Fundamental Knowledge: CTFL certification provides a solid foundation in software testing principles, methodologies, and terminology. This foundational knowledge is essential for building a comprehensive understanding of the field.
Test Automation: CTFL touches on test automation, providing an introduction to automation concepts and tools. This knowledge is particularly valuable in today's testing landscape, where automation is a key focus.
Risk Assessment: CTFL teaches you to assess risks in the software testing process. Understanding risk allows you to make informed decisions about where to focus your testing efforts, expanding your capacity to address high-impact areas.
Quality Standards: CTFL aligns with international quality and testing standards, including those defined by the International Software Testing Qualifications Board (ISTQB). Familiarity with these standards ensures your work is in line with recognized benchmarks.
Documentation Skills: Effective communication and documentation are vital in software testing. CTFL places importance on clear and structured test documentation, fostering your documentation skills.
Problem-Solving: Software testing often requires critical thinking and creative problem-solving. CTFL certification hones these skills as you learn to identify defects, investigate their causes, and suggest effective solutions.
Networking: CTFL certification often connects you with a community of certified professionals. This network provides opportunities for knowledge sharing, collaboration, and mentorship, expanding your knowledge base through the experiences of others.
CTFL certification is not just a static credential; it's a journey of knowledge expansion. It introduces you to the core concepts and practices in software testing, setting the stage for ongoing learning and growth in the field. As you apply what you've learned and continue to explore new horizons, your knowledge and expertise in software testing will naturally expand, making you a more valuable asset in the industry.
Professional Networking
Networking is an essential aspect of career development, and CTFL certification can significantly enhance your professional networking opportunities in the field of software testing. Here's how CTFL certification contributes to professional networking:
Access to a Certified Community: CTFL certification often connects you to a global community of certified professionals. This community provides a valuable network of like-minded individuals who share your passion for software testing and quality assurance.
Career Opportunities: Your network of CTFL-certified professionals can serve as a valuable resource for job leads and career opportunities. You may learn about job openings, referrals, or recommendations through your network.
Conferences and Events: Many software testing conferences and events host gatherings for certified professionals. Attending these events provides you with in-person networking opportunities, where you can meet and connect with fellow CTFL-certified individuals.
Local Chapters and Associations: CTFL certification is often associated with local and national testing associations and chapters. Joining these associations provides opportunities to network with professionals in your region and get involved in community activities.
Job References and Recommendations: Your professional network can serve as references and provide recommendations when you seek new opportunities or career growth. Having a strong network of colleagues who can vouch for your skills and work ethic can be invaluable.
CTFL certification extends beyond validating your skills; it connects you with a community of professionals who share your passion for software testing. The network you build through CTFL certification can offer knowledge sharing, mentorship, collaboration, job opportunities, and valuable career insights, ultimately enriching your career in the software testing industry.
Organizational Benefits
Enhanced Software Quality: CTFL-certified professionals possess a strong understanding of testing principles and best practices. Their expertise leads to improved software quality, reducing the number of defects and ensuring that the software meets or exceeds user expectations.
Reduced Defects and Costs: Early defect detection by CTFL-certified testers results in a reduction of defects that reach the production phase. This leads to cost savings by minimizing the need for post-release bug fixes and patches, which can be expensive and time-consuming.
Efficient Testing Processes: CTFL certification ensures that testing processes are optimized and aligned with industry best practices. This efficiency streamlines testing efforts, reduces redundancy, and enhances productivity within the organization.
Consistency and Standardization: CTFL-certified professionals adhere to standardized terminology and practices. This consistency improves communication within the testing team and fosters a unified approach to software testing.
Risk Mitigation: CTFL certification equips professionals with skills in risk assessment. They can identify high-risk areas within projects and allocate testing resources accordingly, reducing the likelihood of critical issues going unnoticed.
Alignment with Industry Standards: CTFL certification aligns with internationally recognized testing standards, including those defined by the International Software Testing Qualifications Board (ISTQB). This alignment ensures that the organization's testing practices conform to industry-recognized benchmarks.
Enhanced Test Documentation: Effective communication and documentation are vital in software testing. CTFL certification promotes clear and structured test documentation, enhancing transparency and facilitating project management.
Adaptability to Industry Changes: CTFL-certified professionals are well-prepared to adapt to industry changes, such as new technologies and methodologies. This adaptability allows the organization to stay competitive and relevant in the evolving field of software testing.
CTFL certification brings numerous organizational benefits, including improved software quality, cost savings, efficient testing processes, and a competitive advantage in the market. Organizations that invest in CTFL-certified professionals can deliver higher-quality software products, reduce risks, and gain a reputation for reliability and excellence in the field of software testing.
Long-Term Career Growth
CTFL certification serves as a foundational stepping stone for professionals in the software testing field, providing numerous opportunities for long-term career growth. Here's how CTFL certification can contribute to your career advancement over time:
Foundation for Advanced Certifications: CTFL is often the first step in a series of software testing certifications. Building upon CTFL, you can pursue more advanced certifications such as Certified Tester Advanced Level (CTAL) or specialized certifications in areas like test automation, security testing, or performance testing. These advanced certifications can open doors to higher-level roles and increased earning potential.
Expanded Skill Set: As you gain practical experience and advance in your career, the knowledge and skills acquired through CTFL certification continue to benefit you. The foundational principles and best practices you've learned serve as a solid base for acquiring new and more specialized skills over time.
Leadership Opportunities: CTFL-certified professionals are often well-positioned to take on leadership roles within their organizations. With experience and additional training, you can move into positions such as Test Manager or Test Lead, where you'll be responsible for managing testing teams and overseeing testing efforts.
Consulting and Training: With advanced certifications and substantial experience, you may choose to venture into consulting or training. Becoming a testing consultant or trainer can be a rewarding career path, offering opportunities to work with various organizations and share your expertise.
Industry Involvement: Many CTFL-certified professionals actively participate in industry associations, forums, and conferences. Involvement in industry organizations can expand your network, expose you to emerging trends, and provide opportunities for thought leadership.
Job Security: As the demand for high-quality software continues to grow, CTFL-certified professionals often enjoy job security. Organizations value individuals who can ensure software quality, making your career in software testing more resilient.
CTFL certification is not just a one-time achievement; it's a foundation for long-term career growth in the software testing and quality assurance field. Whether you choose to specialize, pursue advanced certifications, or take on leadership roles, CTFL certification provides the knowledge and credibility necessary to support your journey to success in the ever-evolving world of software testing.
Conclusion
In conclusion, the Certified Tester Foundation Level (CTFL) certification offers a wide range of benefits for individuals, organizations, and the software testing industry as a whole.
For individuals, CTFL certification serves as a valuable credential that enhances their skills, employability, and marketability.CTFL-certified professionals often find themselves well-prepared for various roles, from entry-level positions to more advanced, specialized, and leadership roles. This certification not only validates their expertise but also fosters a culture of continuous learning and adaptability, ensuring long-term career growth.
For organizations, CTFL-certified professionals bring a wealth of advantages. They contribute to improved software quality, reduced defects, cost savings, and efficient testing processes. CTFL certification aligns with industry standards and promotes consistency in testing practices, mitigating risks and enhancing documentation and communication. As a result, organizations benefit from higher client satisfaction, a competitive edge, and a reputation for reliability and quality in the software testing domain.
In essence, CTFL certification is not just a single achievement; it's a dynamic and evolving journey. It supports the growth and success of individuals and organizations in the field of software testing, ensuring that software products are of high quality, meet user expectations, and contribute to the advancement of the software industry as a whole.
Introduction to Lean Six Sigma Black Belt Certification
Lean Six Sigma is a methodology that combines the principles of Lean and Six Sigma to improve processes, reduce defects, and enhance overall efficiency within an organization. At the heart of this methodology are individuals known as "Black Belts," who are highly trained professionals responsible for leading and managing Lean Six Sigma projects. This introduction will provide an overview of Lean Six Sigma Black Belt certification, its significance, and the key aspects of becoming a Lean Six Sigma Black Belt.
A Lean Six Sigma Black Belt is a professional who has undergone extensive training in Lean and Six Sigma methodologies. They play a pivotal role in process improvement and change management within an organization. Black Belts are typically responsible for leading complex projects, coaching Green Belts and team members, and driving significant improvements in quality, cost, and productivity.
Lean Six Sigma Black Belt certification is a significant achievement that validates your expertise in process improvement and problem-solving. Black Belts play a crucial role in helping organizations streamline operations, reduce defects, and enhance overall efficiency. This certification is a stepping stone to a rewarding career in continuous improvement and change management.
Table of contents
-
Black Belt Certification Requirements
-
Black Belt Training Programs
-
Lean Six Sigma Tools and Techniques
-
Preparing for the Black Belt Certification Exam
-
Real-World Application of Black Belt Skills
-
The Role of a Black Belt in an Organization
-
Lean Six Sigma Project Portfolio
-
Challenges Faced by Black Belt Candidates
-
Industry-Specific Black Belt Certification
-
Continuing Education for Black Belts
-
Conclusion
Black Belt Certification Requirements
Lean Six Sigma Black Belt certification requirements typically vary by certification body and the specific training provider. However, I can provide you with a general overview of the common prerequisites and requirements that are often associated with becoming a Lean Six Sigma Black Belt:
Green Belt Certification: Most Lean Six Sigma Black Belt certification programs require candidates to have previously earned their Green Belt certification. This is because Black Belt certification builds upon the concepts and skills acquired at the Green Belt level. Some organizations may offer combined Green Belt and Black Belt programs, but this is less common.
Work Experience: Candidates are usually expected to have a minimum amount of work experience in roles related to process improvement or quality management. The required years of experience can vary, but it's often in the range of 2 to 3 years.
Training: Completing a specified number of hours of formal training in Lean Six Sigma is typically required. This training can be provided by accredited training organizations or universities. The number of training hours needed may vary but is often around 80-120 hours.
Certification Exam: Candidates must pass a certification exam that assesses their knowledge of Lean Six Sigma concepts and tools. The exam is typically based on the Body of Knowledge (BoK) for Black Belts, which is defined by the certifying body.
Payment of Fees: There are usually fees associated with the certification process, including exam fees and, in some cases, annual maintenance fees to keep the certification current.
Code of Ethics: Candidates may be required to adhere to a code of ethics, committing to uphold the principles and standards of Lean Six Sigma in their professional practice.
As of my knowledge cutoff date in September 2021, some well-known organizations that offer Lean Six Sigma Black Belt certification include ASQ (American Society for Quality), IASSC (International Association for Six Sigma Certification), and various training providers. Keep in mind that certification requirements and options may have evolved since that time, so it's advisable to check with the relevant organizations for the most up-to-date information.
Black Belt Training Programs
Lean Six Sigma Black Belt training programs are designed to equip individuals with the knowledge, skills, and tools needed to effectively lead process improvement projects, mentor Green Belts, and drive significant changes within an organization. These programs are offered by a variety of organizations, including universities, training providers, and certification bodies. Below, I'll provide an overview of what you can typically expect from Black Belt training programs:
Comprehensive Curriculum: Black Belt training programs cover a wide range of Lean and Six Sigma concepts, methodologies, and tools. Participants can expect to dive deep into topics like DMAIC (Define, Measure, Analyze, Improve, Control), statistical analysis, process mapping, root cause analysis, and more.
Duration: The duration of Black Belt training can vary depending on the program and the organization offering it. It typically ranges from several weeks to several months. Some programs are more intensive, while others are designed to accommodate participants who may be working full-time.
Project-Based Learning: Many Black Belt training programs include a hands-on project component. Participants are required to complete one or more real-world improvement projects to apply the concepts they've learned. This practical experience is a key element of Black Belt training.
Certified Instructors: Training programs are usually led by experienced Lean Six Sigma professionals or certified instructors who can provide guidance and support throughout the learning process.
Networking Opportunities: Some training programs facilitate networking and collaboration among participants, allowing them to share experiences and learn from one another.
Certification Support: Many Black Belt training programs are designed to prepare individuals for certification exams, and they may include guidance on the certification process, eligibility requirements, and registration.
Before enrolling in a Black Belt training program, it's essential to consider your specific career goals, the reputation of the program, and your preferred mode of learning (e.g., classroom or online). Additionally, you should check whether the program aligns with the certification body you plan to seek certification from (e.g., ASQ, IASSC, etc.), as different bodies may have slightly different curriculum requirements.
Lean Six Sigma Tools and Techniques
Lean Six Sigma is a methodology that utilizes a variety of tools and techniques to improve processes, reduce defects, and enhance efficiency. Black Belts are trained to apply these tools and techniques effectively in their projects. Here's an overview of some of the key Lean Six Sigma tools and techniques that Black Belts commonly use:
Process Mapping:Techniques like flowcharts and value stream maps are used to visually represent and understand the process, highlighting areas for improvement.
Cause-and-Effect Diagram (Fishbone or Ishikawa Diagram):This tool helps identify potential causes for a specific problem or effect, categorizing them into major categories.
Statistical Process Control (SPC):Statistical techniques are used to monitor and control the process to maintain its stability and predictability.
Regression Analysis:This statistical tool is used to identify and quantify relationships between variables, helping determine which factors have the most significant impact on a process.
Design of Experiments (DOE):DOE is a structured approach to experimentation that helps optimize processes and determine the ideal settings for process variables.
Control Charts:Control charts are used to monitor process performance over time and identify variations and trends.
Pareto Analysis:This tool helps identify and prioritize the most significant factors contributing to a problem.
Kanban and Pull Systems:Tools used in Lean to manage and control workflow, ensuring that work is pulled only as needed.
5S (Sort, Set in order, Shine, Standardize, Sustain):A methodology for organizing and maintaining a clean, efficient, and safe workplace.
These are just a selection of the tools and techniques that Lean Six Sigma Black Belts employ to analyze, optimize, and control processes. The choice of tools and techniques depends on the specific project and the nature of the problem being addressed. Black Belts are trained to use these tools effectively to drive process improvements and achieve the desired outcomes.
Preparing for the Black Belt Certification Exam
Preparing for the Lean Six Sigma Black Belt certification exam is a significant undertaking, as it requires a strong understanding of Lean and Six Sigma principles, methodologies, and tools. Here are steps and tips to help you prepare effectively for the exam:
Understand the Exam Structure:Begin by understanding the format of the Black Belt certification exam. Is it multiple-choice, essay-based, or a combination of question types? Knowing the structure will help you plan your study strategy.
Choose the Right Study Materials:Invest in reputable study materials. This may include textbooks, online courses, practice exams, and reference guides. Ensure that the materials align with the BoK.
Take an Official Course:Consider enrolling in an official Lean Six Sigma Black Belt training program, especially if you haven't already completed a comprehensive Green Belt program. These courses provide structured content and often include exam preparation.
Review and Revise:Regularly revisit and revise the topics you've studied to reinforce your understanding and knowledge retention.
Focus on Problem-Solving:Lean Six Sigma is about practical problem-solving. Practice solving real-world problems and applying the methodology.
Stay Calm and Confident:As the exam date approaches, stay calm and confident. Stress can hinder your performance. Review your notes and practice questions, but also take time to relax and rest.
Plan for Exam Day:Ensure you know the logistics of the exam, such as location, time, required identification, and any materials you're allowed to bring. Arrive early and well-rested on exam day.
Remember that Black Belt certification exams are challenging, and preparation is crucial. Take your time to understand the material thoroughly and practice using Lean and Six Sigma tools effectively. The more you practice, the more confident and well-prepared you'll be when you sit for the exam.
Real-World Application of Black Belt Skills
Lean Six Sigma Black Belts are highly trained professionals with expertise in process improvement, data analysis, and problem-solving. Their skills find application in various industries and organizations. Here are some real-world examples of how Black Belt skills are applied:
Manufacturing:Black Belts can lead projects to reduce defects and improve efficiency in manufacturing processes. For example, they might optimize a production line to reduce cycle time, increase product quality, and reduce waste.
Healthcare:In healthcare, Black Belts can improve patient care processes. They might work on reducing hospital wait times, decreasing medication errors, or improving the accuracy of medical billing.
Finance:Black Belts in the financial sector might focus on reducing errors in financial transactions, streamlining approval processes, and optimizing risk assessment methodologies.
Supply Chain and Logistics:They can optimize inventory management, reduce lead times, and improve the accuracy of demand forecasting, leading to cost savings and improved customer service.
Service Industries:In service-based businesses like banking, Black Belts might work on improving customer service processes, reducing customer wait times, and enhancing the efficiency of call centers.
Aerospace and Defense:Black Belts can lead projects to reduce defects in the manufacturing of aerospace components, improve maintenance processes, and enhance quality control in defense projects.
The real-world application of Black Belt skills involves identifying process inefficiencies, conducting data-driven analyses, implementing improvements, and sustaining these changes. Black Belts work closely with teams, stakeholders, and leadership to achieve tangible results, such as cost savings, quality improvements, and enhanced customer satisfaction. Their expertise plays a vital role in helping organizations achieve their strategic goals and stay competitive in a dynamic business environment.
The Role of a Black Belt in an Organization
The role of a Lean Six Sigma Black Belt in an organization is pivotal in driving process improvement, enhancing operational efficiency, and achieving strategic goals. Black Belts serve as leaders, mentors, and experts in Lean Six Sigma methodologies. Their responsibilities and contributions to the organization are multifaceted:
Project Leadership: Black Belts lead and manage Lean Six Sigma projects within the organization. They are responsible for selecting, scoping, planning, and executing projects aimed at improving specific processes and achieving predefined goals. Black Belts ensure that projects are completed on time, within budget, and with the desired outcomes.
Problem Solving: They are skilled problem solvers who use data-driven approaches and a wide array of Lean and Six Sigma tools to identify the root causes of process issues and defects. They work to develop and implement effective solutions to these problems.
Mentoring and Coaching: Black Belts play a critical role in mentoring and coaching Green Belts, Yellow Belts, and other team members involved in Lean Six Sigma projects. They provide guidance, support, and knowledge transfer to help individuals build their process improvement skills.
Data Analysis: They are proficient in statistical analysis and data interpretation. Black Belts use data to measure process performance, identify variations, and quantify the impact of process improvements.
Change Management: Implementing process improvements often requires changes in procedures, roles, and workflows. Black Belts are responsible for leading and facilitating these changes, ensuring that they are smoothly integrated into the organization.
Cost Reduction and Efficiency: Black Belts drive efforts to reduce costs and increase operational efficiency by eliminating waste, optimizing processes, and streamlining workflows. These improvements lead to direct financial savings for the organization.
Sustainability: They are responsible for ensuring that process improvements are sustained over time, preventing regression to previous states.
The role of a Black Belt is dynamic, and their contributions can lead to significant improvements in an organization's processes, customer satisfaction, financial performance, and competitiveness. Their work supports the organization's ability to adapt to changing market conditions and achieve long-term success.
Lean Six Sigma Project Portfolio
A Lean Six Sigma project portfolio is a collection of projects within an organization that are aligned with the goals and strategies of the business and are aimed at improving various processes and functions. These projects are typically managed and overseen by Lean Six Sigma professionals, including Black Belts and Master Black Belts. The portfolio approach ensures that process improvement efforts are systematic, coordinated, and focused on delivering tangible results. Here are key aspects of a Lean Six Sigma project portfolio:
Project Selection: Projects within the portfolio are carefully selected based on their alignment with the organization's strategic objectives, potential impact, and resources available. Selection criteria may include factors like potential cost savings, customer satisfaction improvements, and operational efficiency gains.
Strategic Alignment: The projects within the portfolio should directly support the organization's strategic goals. This ensures that Lean Six Sigma initiatives contribute to the overall success of the business.
Diverse Project Types: The portfolio typically includes a mix of projects, such as process optimization, defect reduction, cost reduction, cycle time reduction, and quality improvement, among others. This diversity helps address various aspects of the business.
Project Management: Each project in the portfolio is assigned a project manager, often a Black Belt, who is responsible for overseeing the project, managing the team, and ensuring that it stays on track and within scope.
Measurement and Metrics: Key performance metrics and measures are established for each project to track progress and assess the impact of process improvements.
Reporting and Communication: Regular reporting and communication mechanisms are put in place to keep stakeholders informed about the status of projects and their outcomes.
A well-managed Lean Six Sigma project portfolio helps organizations systematically and strategically drive improvements in various processes, leading to cost savings, enhanced quality, and better customer satisfaction. It allows organizations to focus their efforts on the most critical areas, ensures that resources are used efficiently, and creates a culture of continuous improvement.
Challenges Faced by Black Belt Candidates
Becoming a Lean Six Sigma Black Belt is a rigorous and challenging process, and candidates often encounter various obstacles and difficulties along the way. Here are some common challenges faced by Black Belt candidates:
Complexity of the Material: The Lean Six Sigma Body of Knowledge can be complex and highly technical. Candidates must master a wide range of statistical tools, methodologies, and concepts, which can be challenging for those without prior experience in the field.
Time Commitment: Preparing for Black Belt certification can be time-consuming, especially when candidates are working full-time. Balancing work, study, and personal life can be a significant challenge.
Project Leadership: Leading Lean Six Sigma projects requires not only technical knowledge but also leadership and project management skills. Some candidates may struggle with the transition from a technical role to a leadership role.
Data Analysis: Data analysis is a fundamental component of Lean Six Sigma, and candidates often find it challenging to gather, analyze, and interpret data effectively.
Resource Allocation: Securing the necessary resources, including time, personnel, and data, for projects can be difficult, especially if the organization is resource-constrained.
Resistance to Change: Implementing process improvements can face resistance from employees who are comfortable with the existing processes. Managing change and gaining buy-in from stakeholders can be a challenge.
Sustaining Improvements: Ensuring that process improvements are sustained over the long term can be a challenge, as there may be resistance to reverting to old practices.
Despite these challenges, the journey to becoming a Lean Six Sigma Black Belt can be highly rewarding. With determination, perseverance, and a supportive network, many candidates successfully navigate these obstacles and go on to make significant contributions to their organizations through process improvements and problem-solving.
Industry-Specific Black Belt Certification
Industry-specific Black Belt certification programs are designed to train and certify Lean Six Sigma Black Belts with specialized knowledge and expertise tailored to a particular industry or sector. These certifications acknowledge the unique challenges and requirements of specific industries and aim to equip professionals with the skills needed to drive process improvement and quality management within their specialized field. Here are a few examples of industry-specific Black Belt certifications:
Healthcare Black Belt Certification:This certification is designed for professionals in the healthcare industry, including hospitals, clinics, and healthcare providers. It focuses on addressing issues related to patient care, process efficiency, and regulatory compliance.
Pharmaceutical Black Belt Certification:Pharmaceutical Black Belts are trained to apply Lean Six Sigma methodologies to address quality control, manufacturing, and regulatory compliance issues specific to pharmaceutical production.
Aerospace and Defense Black Belt Certification:This certification program is tailored to the aerospace and defense industry, where professionals work on improving the quality and efficiency of production, maintenance, and supply chain processes.
Retail Black Belt Certification:Retail Black Belts work on improving inventory management, supply chain, customer service, and store operations in the retail industry.
Telecommunications Black Belt Certification:Professionals in the telecommunications sector can obtain specialized certification to address challenges related to network performance, customer support, and service quality.
Automotive Black Belt Certification:Automotive Black Belts work on enhancing quality control and process efficiency in the automotive industry, including manufacturing and supply chain operations.
Industry-specific Black Belt certification programs often include case studies, projects, and examples relevant to the particular sector, ensuring that candidates are well-equipped to address industry-specific challenges. These certifications are valuable for professionals who want to specialize in their industry and make a significant impact through Lean Six Sigma methodology. It's essential to research and choose a certification program that aligns with your industry and career goals.
Continuing Education for Black Belts
Continuing education is essential for Lean Six Sigma Black Belts to stay current with industry trends, expand their knowledge, and further develop their skills. It also helps Black Belts continue to add value to their organizations by driving ongoing process improvements. Here are some key aspects of continuing education for Black Belts:
Recertification: Many Lean Six Sigma certification bodies, such as ASQ and IASSC, require Black Belts to recertify periodically. This typically involves earning a certain number of Continuing Education Units (CEUs) or Professional Development Units (PDUs) over a set period, often three years.
Advanced Training: Black Belts can pursue advanced training, such as Master Black Belt certification. This level of certification involves a higher level of expertise and leadership within the organization's Lean Six Sigma program.
Specialized Training: Depending on their industry or organization, Black Belts can undertake specialized training in areas like data analytics, project management, change management, or specific tools and methodologies relevant to their field.
Cross-Functional Training: To facilitate cross-functional teamwork and collaboration, Black Belts can engage in training programs that help them understand the perspectives and needs of various departments and teams within the organization.
Networking and Communities of Practice: Black Belts can join professional organizations, attend conferences, and participate in communities of practice related to Lean Six Sigma. These forums provide opportunities to learn from peers, share experiences, and stay updated on industry trends.
Advanced Problem-Solving Techniques: Black Belts can deepen their problem-solving skills by learning advanced techniques and approaches to tackle complex challenges.
Soft Skills Development: Enhancing soft skills, such as communication, negotiation, and conflict resolution, is important for effective leadership and teamwork.
Organization-Specific Training: Organizations may provide or support training and development programs tailored to their specific needs and industry.
Continuing education is an ongoing process that ensures Black Belts remain at the forefront of Lean Six Sigma practices and can adapt to evolving business and industry demands. It's an investment in personal and professional growth that benefits both the individual and the organization.
Conclusion
In conclusion, Lean Six Sigma Black Belts play a crucial role in organizations by driving process improvement, optimizing operations, and delivering significant results. They are highly trained professionals with expertise in Lean and Six Sigma methodologies, statistical analysis, and problem-solving. Their responsibilities encompass project leadership, mentoring, data analysis, and fostering a culture of continuous improvement.
Black Belts undergo rigorous training and certification to equip themselves with the knowledge and skills needed for their roles. Their work can have a profound impact on an organization, leading to cost savings, quality improvements, and enhanced customer satisfaction.
Challenges faced by Black Belt candidates include the complexity of the material, the time commitment, and the need to transition into a leadership role. However, with dedication and support, candidates can successfully navigate these challenges and contribute to their organizations' success.
Continuing education is vital for Black Belts to stay current and further their professional development. This includes recertification, advanced training, specialized and cross-functional education, and engagement in communities of practice.
Whether in healthcare, manufacturing, finance, or any other industry, the skills and expertise of Lean Six Sigma Black Belts are invaluable for organizations striving for continuous improvement and operational excellence.
Read More
Lean Six Sigma is a methodology that combines the principles of Lean and Six Sigma to improve processes, reduce defects, and enhance overall efficiency within an organization. At the heart of this methodology are individuals known as "Black Belts," who are highly trained professionals responsible for leading and managing Lean Six Sigma projects. This introduction will provide an overview of Lean Six Sigma Black Belt certification, its significance, and the key aspects of becoming a Lean Six Sigma Black Belt.
A Lean Six Sigma Black Belt is a professional who has undergone extensive training in Lean and Six Sigma methodologies. They play a pivotal role in process improvement and change management within an organization. Black Belts are typically responsible for leading complex projects, coaching Green Belts and team members, and driving significant improvements in quality, cost, and productivity.
Lean Six Sigma Black Belt certification is a significant achievement that validates your expertise in process improvement and problem-solving. Black Belts play a crucial role in helping organizations streamline operations, reduce defects, and enhance overall efficiency. This certification is a stepping stone to a rewarding career in continuous improvement and change management.
Table of contents
-
Black Belt Certification Requirements
-
Black Belt Training Programs
-
Lean Six Sigma Tools and Techniques
-
Preparing for the Black Belt Certification Exam
-
Real-World Application of Black Belt Skills
-
The Role of a Black Belt in an Organization
-
Lean Six Sigma Project Portfolio
-
Challenges Faced by Black Belt Candidates
-
Industry-Specific Black Belt Certification
-
Continuing Education for Black Belts
-
Conclusion
Black Belt Certification Requirements
Lean Six Sigma Black Belt certification requirements typically vary by certification body and the specific training provider. However, I can provide you with a general overview of the common prerequisites and requirements that are often associated with becoming a Lean Six Sigma Black Belt:
Green Belt Certification: Most Lean Six Sigma Black Belt certification programs require candidates to have previously earned their Green Belt certification. This is because Black Belt certification builds upon the concepts and skills acquired at the Green Belt level. Some organizations may offer combined Green Belt and Black Belt programs, but this is less common.
Work Experience: Candidates are usually expected to have a minimum amount of work experience in roles related to process improvement or quality management. The required years of experience can vary, but it's often in the range of 2 to 3 years.
Training: Completing a specified number of hours of formal training in Lean Six Sigma is typically required. This training can be provided by accredited training organizations or universities. The number of training hours needed may vary but is often around 80-120 hours.
Certification Exam: Candidates must pass a certification exam that assesses their knowledge of Lean Six Sigma concepts and tools. The exam is typically based on the Body of Knowledge (BoK) for Black Belts, which is defined by the certifying body.
Payment of Fees: There are usually fees associated with the certification process, including exam fees and, in some cases, annual maintenance fees to keep the certification current.
Code of Ethics: Candidates may be required to adhere to a code of ethics, committing to uphold the principles and standards of Lean Six Sigma in their professional practice.
As of my knowledge cutoff date in September 2021, some well-known organizations that offer Lean Six Sigma Black Belt certification include ASQ (American Society for Quality), IASSC (International Association for Six Sigma Certification), and various training providers. Keep in mind that certification requirements and options may have evolved since that time, so it's advisable to check with the relevant organizations for the most up-to-date information.
Black Belt Training Programs
Lean Six Sigma Black Belt training programs are designed to equip individuals with the knowledge, skills, and tools needed to effectively lead process improvement projects, mentor Green Belts, and drive significant changes within an organization. These programs are offered by a variety of organizations, including universities, training providers, and certification bodies. Below, I'll provide an overview of what you can typically expect from Black Belt training programs:
Comprehensive Curriculum: Black Belt training programs cover a wide range of Lean and Six Sigma concepts, methodologies, and tools. Participants can expect to dive deep into topics like DMAIC (Define, Measure, Analyze, Improve, Control), statistical analysis, process mapping, root cause analysis, and more.
Duration: The duration of Black Belt training can vary depending on the program and the organization offering it. It typically ranges from several weeks to several months. Some programs are more intensive, while others are designed to accommodate participants who may be working full-time.
Project-Based Learning: Many Black Belt training programs include a hands-on project component. Participants are required to complete one or more real-world improvement projects to apply the concepts they've learned. This practical experience is a key element of Black Belt training.
Certified Instructors: Training programs are usually led by experienced Lean Six Sigma professionals or certified instructors who can provide guidance and support throughout the learning process.
Networking Opportunities: Some training programs facilitate networking and collaboration among participants, allowing them to share experiences and learn from one another.
Certification Support: Many Black Belt training programs are designed to prepare individuals for certification exams, and they may include guidance on the certification process, eligibility requirements, and registration.
Before enrolling in a Black Belt training program, it's essential to consider your specific career goals, the reputation of the program, and your preferred mode of learning (e.g., classroom or online). Additionally, you should check whether the program aligns with the certification body you plan to seek certification from (e.g., ASQ, IASSC, etc.), as different bodies may have slightly different curriculum requirements.
Lean Six Sigma Tools and Techniques
Lean Six Sigma is a methodology that utilizes a variety of tools and techniques to improve processes, reduce defects, and enhance efficiency. Black Belts are trained to apply these tools and techniques effectively in their projects. Here's an overview of some of the key Lean Six Sigma tools and techniques that Black Belts commonly use:
Process Mapping:Techniques like flowcharts and value stream maps are used to visually represent and understand the process, highlighting areas for improvement.
Cause-and-Effect Diagram (Fishbone or Ishikawa Diagram):This tool helps identify potential causes for a specific problem or effect, categorizing them into major categories.
Statistical Process Control (SPC):Statistical techniques are used to monitor and control the process to maintain its stability and predictability.
Regression Analysis:This statistical tool is used to identify and quantify relationships between variables, helping determine which factors have the most significant impact on a process.
Design of Experiments (DOE):DOE is a structured approach to experimentation that helps optimize processes and determine the ideal settings for process variables.
Control Charts:Control charts are used to monitor process performance over time and identify variations and trends.
Pareto Analysis:This tool helps identify and prioritize the most significant factors contributing to a problem.
Kanban and Pull Systems:Tools used in Lean to manage and control workflow, ensuring that work is pulled only as needed.
5S (Sort, Set in order, Shine, Standardize, Sustain):A methodology for organizing and maintaining a clean, efficient, and safe workplace.
These are just a selection of the tools and techniques that Lean Six Sigma Black Belts employ to analyze, optimize, and control processes. The choice of tools and techniques depends on the specific project and the nature of the problem being addressed. Black Belts are trained to use these tools effectively to drive process improvements and achieve the desired outcomes.
Preparing for the Black Belt Certification Exam
Preparing for the Lean Six Sigma Black Belt certification exam is a significant undertaking, as it requires a strong understanding of Lean and Six Sigma principles, methodologies, and tools. Here are steps and tips to help you prepare effectively for the exam:
Understand the Exam Structure:Begin by understanding the format of the Black Belt certification exam. Is it multiple-choice, essay-based, or a combination of question types? Knowing the structure will help you plan your study strategy.
Choose the Right Study Materials:Invest in reputable study materials. This may include textbooks, online courses, practice exams, and reference guides. Ensure that the materials align with the BoK.
Take an Official Course:Consider enrolling in an official Lean Six Sigma Black Belt training program, especially if you haven't already completed a comprehensive Green Belt program. These courses provide structured content and often include exam preparation.
Review and Revise:Regularly revisit and revise the topics you've studied to reinforce your understanding and knowledge retention.
Focus on Problem-Solving:Lean Six Sigma is about practical problem-solving. Practice solving real-world problems and applying the methodology.
Stay Calm and Confident:As the exam date approaches, stay calm and confident. Stress can hinder your performance. Review your notes and practice questions, but also take time to relax and rest.
Plan for Exam Day:Ensure you know the logistics of the exam, such as location, time, required identification, and any materials you're allowed to bring. Arrive early and well-rested on exam day.
Remember that Black Belt certification exams are challenging, and preparation is crucial. Take your time to understand the material thoroughly and practice using Lean and Six Sigma tools effectively. The more you practice, the more confident and well-prepared you'll be when you sit for the exam.
Real-World Application of Black Belt Skills
Lean Six Sigma Black Belts are highly trained professionals with expertise in process improvement, data analysis, and problem-solving. Their skills find application in various industries and organizations. Here are some real-world examples of how Black Belt skills are applied:
Manufacturing:Black Belts can lead projects to reduce defects and improve efficiency in manufacturing processes. For example, they might optimize a production line to reduce cycle time, increase product quality, and reduce waste.
Healthcare:In healthcare, Black Belts can improve patient care processes. They might work on reducing hospital wait times, decreasing medication errors, or improving the accuracy of medical billing.
Finance:Black Belts in the financial sector might focus on reducing errors in financial transactions, streamlining approval processes, and optimizing risk assessment methodologies.
Supply Chain and Logistics:They can optimize inventory management, reduce lead times, and improve the accuracy of demand forecasting, leading to cost savings and improved customer service.
Service Industries:In service-based businesses like banking, Black Belts might work on improving customer service processes, reducing customer wait times, and enhancing the efficiency of call centers.
Aerospace and Defense:Black Belts can lead projects to reduce defects in the manufacturing of aerospace components, improve maintenance processes, and enhance quality control in defense projects.
The real-world application of Black Belt skills involves identifying process inefficiencies, conducting data-driven analyses, implementing improvements, and sustaining these changes. Black Belts work closely with teams, stakeholders, and leadership to achieve tangible results, such as cost savings, quality improvements, and enhanced customer satisfaction. Their expertise plays a vital role in helping organizations achieve their strategic goals and stay competitive in a dynamic business environment.
The Role of a Black Belt in an Organization
The role of a Lean Six Sigma Black Belt in an organization is pivotal in driving process improvement, enhancing operational efficiency, and achieving strategic goals. Black Belts serve as leaders, mentors, and experts in Lean Six Sigma methodologies. Their responsibilities and contributions to the organization are multifaceted:
Project Leadership: Black Belts lead and manage Lean Six Sigma projects within the organization. They are responsible for selecting, scoping, planning, and executing projects aimed at improving specific processes and achieving predefined goals. Black Belts ensure that projects are completed on time, within budget, and with the desired outcomes.
Problem Solving: They are skilled problem solvers who use data-driven approaches and a wide array of Lean and Six Sigma tools to identify the root causes of process issues and defects. They work to develop and implement effective solutions to these problems.
Mentoring and Coaching: Black Belts play a critical role in mentoring and coaching Green Belts, Yellow Belts, and other team members involved in Lean Six Sigma projects. They provide guidance, support, and knowledge transfer to help individuals build their process improvement skills.
Data Analysis: They are proficient in statistical analysis and data interpretation. Black Belts use data to measure process performance, identify variations, and quantify the impact of process improvements.
Change Management: Implementing process improvements often requires changes in procedures, roles, and workflows. Black Belts are responsible for leading and facilitating these changes, ensuring that they are smoothly integrated into the organization.
Cost Reduction and Efficiency: Black Belts drive efforts to reduce costs and increase operational efficiency by eliminating waste, optimizing processes, and streamlining workflows. These improvements lead to direct financial savings for the organization.
Sustainability: They are responsible for ensuring that process improvements are sustained over time, preventing regression to previous states.
The role of a Black Belt is dynamic, and their contributions can lead to significant improvements in an organization's processes, customer satisfaction, financial performance, and competitiveness. Their work supports the organization's ability to adapt to changing market conditions and achieve long-term success.
Lean Six Sigma Project Portfolio
A Lean Six Sigma project portfolio is a collection of projects within an organization that are aligned with the goals and strategies of the business and are aimed at improving various processes and functions. These projects are typically managed and overseen by Lean Six Sigma professionals, including Black Belts and Master Black Belts. The portfolio approach ensures that process improvement efforts are systematic, coordinated, and focused on delivering tangible results. Here are key aspects of a Lean Six Sigma project portfolio:
Project Selection: Projects within the portfolio are carefully selected based on their alignment with the organization's strategic objectives, potential impact, and resources available. Selection criteria may include factors like potential cost savings, customer satisfaction improvements, and operational efficiency gains.
Strategic Alignment: The projects within the portfolio should directly support the organization's strategic goals. This ensures that Lean Six Sigma initiatives contribute to the overall success of the business.
Diverse Project Types: The portfolio typically includes a mix of projects, such as process optimization, defect reduction, cost reduction, cycle time reduction, and quality improvement, among others. This diversity helps address various aspects of the business.
Project Management: Each project in the portfolio is assigned a project manager, often a Black Belt, who is responsible for overseeing the project, managing the team, and ensuring that it stays on track and within scope.
Measurement and Metrics: Key performance metrics and measures are established for each project to track progress and assess the impact of process improvements.
Reporting and Communication: Regular reporting and communication mechanisms are put in place to keep stakeholders informed about the status of projects and their outcomes.
A well-managed Lean Six Sigma project portfolio helps organizations systematically and strategically drive improvements in various processes, leading to cost savings, enhanced quality, and better customer satisfaction. It allows organizations to focus their efforts on the most critical areas, ensures that resources are used efficiently, and creates a culture of continuous improvement.
Challenges Faced by Black Belt Candidates
Becoming a Lean Six Sigma Black Belt is a rigorous and challenging process, and candidates often encounter various obstacles and difficulties along the way. Here are some common challenges faced by Black Belt candidates:
Complexity of the Material: The Lean Six Sigma Body of Knowledge can be complex and highly technical. Candidates must master a wide range of statistical tools, methodologies, and concepts, which can be challenging for those without prior experience in the field.
Time Commitment: Preparing for Black Belt certification can be time-consuming, especially when candidates are working full-time. Balancing work, study, and personal life can be a significant challenge.
Project Leadership: Leading Lean Six Sigma projects requires not only technical knowledge but also leadership and project management skills. Some candidates may struggle with the transition from a technical role to a leadership role.
Data Analysis: Data analysis is a fundamental component of Lean Six Sigma, and candidates often find it challenging to gather, analyze, and interpret data effectively.
Resource Allocation: Securing the necessary resources, including time, personnel, and data, for projects can be difficult, especially if the organization is resource-constrained.
Resistance to Change: Implementing process improvements can face resistance from employees who are comfortable with the existing processes. Managing change and gaining buy-in from stakeholders can be a challenge.
Sustaining Improvements: Ensuring that process improvements are sustained over the long term can be a challenge, as there may be resistance to reverting to old practices.
Despite these challenges, the journey to becoming a Lean Six Sigma Black Belt can be highly rewarding. With determination, perseverance, and a supportive network, many candidates successfully navigate these obstacles and go on to make significant contributions to their organizations through process improvements and problem-solving.
Industry-Specific Black Belt Certification
Industry-specific Black Belt certification programs are designed to train and certify Lean Six Sigma Black Belts with specialized knowledge and expertise tailored to a particular industry or sector. These certifications acknowledge the unique challenges and requirements of specific industries and aim to equip professionals with the skills needed to drive process improvement and quality management within their specialized field. Here are a few examples of industry-specific Black Belt certifications:
Healthcare Black Belt Certification:This certification is designed for professionals in the healthcare industry, including hospitals, clinics, and healthcare providers. It focuses on addressing issues related to patient care, process efficiency, and regulatory compliance.
Pharmaceutical Black Belt Certification:Pharmaceutical Black Belts are trained to apply Lean Six Sigma methodologies to address quality control, manufacturing, and regulatory compliance issues specific to pharmaceutical production.
Aerospace and Defense Black Belt Certification:This certification program is tailored to the aerospace and defense industry, where professionals work on improving the quality and efficiency of production, maintenance, and supply chain processes.
Retail Black Belt Certification:Retail Black Belts work on improving inventory management, supply chain, customer service, and store operations in the retail industry.
Telecommunications Black Belt Certification:Professionals in the telecommunications sector can obtain specialized certification to address challenges related to network performance, customer support, and service quality.
Automotive Black Belt Certification:Automotive Black Belts work on enhancing quality control and process efficiency in the automotive industry, including manufacturing and supply chain operations.
Industry-specific Black Belt certification programs often include case studies, projects, and examples relevant to the particular sector, ensuring that candidates are well-equipped to address industry-specific challenges. These certifications are valuable for professionals who want to specialize in their industry and make a significant impact through Lean Six Sigma methodology. It's essential to research and choose a certification program that aligns with your industry and career goals.
Continuing Education for Black Belts
Continuing education is essential for Lean Six Sigma Black Belts to stay current with industry trends, expand their knowledge, and further develop their skills. It also helps Black Belts continue to add value to their organizations by driving ongoing process improvements. Here are some key aspects of continuing education for Black Belts:
Recertification: Many Lean Six Sigma certification bodies, such as ASQ and IASSC, require Black Belts to recertify periodically. This typically involves earning a certain number of Continuing Education Units (CEUs) or Professional Development Units (PDUs) over a set period, often three years.
Advanced Training: Black Belts can pursue advanced training, such as Master Black Belt certification. This level of certification involves a higher level of expertise and leadership within the organization's Lean Six Sigma program.
Specialized Training: Depending on their industry or organization, Black Belts can undertake specialized training in areas like data analytics, project management, change management, or specific tools and methodologies relevant to their field.
Cross-Functional Training: To facilitate cross-functional teamwork and collaboration, Black Belts can engage in training programs that help them understand the perspectives and needs of various departments and teams within the organization.
Networking and Communities of Practice: Black Belts can join professional organizations, attend conferences, and participate in communities of practice related to Lean Six Sigma. These forums provide opportunities to learn from peers, share experiences, and stay updated on industry trends.
Advanced Problem-Solving Techniques: Black Belts can deepen their problem-solving skills by learning advanced techniques and approaches to tackle complex challenges.
Soft Skills Development: Enhancing soft skills, such as communication, negotiation, and conflict resolution, is important for effective leadership and teamwork.
Organization-Specific Training: Organizations may provide or support training and development programs tailored to their specific needs and industry.
Continuing education is an ongoing process that ensures Black Belts remain at the forefront of Lean Six Sigma practices and can adapt to evolving business and industry demands. It's an investment in personal and professional growth that benefits both the individual and the organization.
Conclusion
In conclusion, Lean Six Sigma Black Belts play a crucial role in organizations by driving process improvement, optimizing operations, and delivering significant results. They are highly trained professionals with expertise in Lean and Six Sigma methodologies, statistical analysis, and problem-solving. Their responsibilities encompass project leadership, mentoring, data analysis, and fostering a culture of continuous improvement.
Black Belts undergo rigorous training and certification to equip themselves with the knowledge and skills needed for their roles. Their work can have a profound impact on an organization, leading to cost savings, quality improvements, and enhanced customer satisfaction.
Challenges faced by Black Belt candidates include the complexity of the material, the time commitment, and the need to transition into a leadership role. However, with dedication and support, candidates can successfully navigate these challenges and contribute to their organizations' success.
Continuing education is vital for Black Belts to stay current and further their professional development. This includes recertification, advanced training, specialized and cross-functional education, and engagement in communities of practice.
Whether in healthcare, manufacturing, finance, or any other industry, the skills and expertise of Lean Six Sigma Black Belts are invaluable for organizations striving for continuous improvement and operational excellence.
Minitab's Role in Quality Control & Six Sigma Success!!!
In an era where data is the lifeblood of informed decision-making, organizations across diverse industries strive for excellence in quality control and process improvement. Six Sigma, a methodology focused on minimizing defects and variations, stands as a beacon of efficiency and quality. At the heart of this data-driven revolution lies Minitab, a versatile statistical software package. In this blog, we embark on a journey to explore "The Role of Minitab in Quality Control and Six Sigma." We will unravel how Minitab empowers professionals and organizations to harness the power of data, streamline processes, and elevate quality standards. From hypothesis testing and control charts to regression analysis and root cause analysis, Minitab serves as an indispensable tool, enabling the pursuit of data-driven excellence and the achievement of Six Sigma's lofty goals. Join us as we delve into the essential role that Minitab plays in the world of quality control and process improvement, where data reigns supreme and continuous improvement is the ultimate objective.
Table of contents
-
Introduction to Minitab
-
How Minitab Facilitates Data Analysis in Six Sigma Projects
-
Minitab and DMAIC
-
Statistical Analysis with Minitab
-
Creating Control Charts with Minitab
-
Hypothesis Testing in Minitab
-
Regression Analysis in Minitab
-
Design of Experiments (DOE) Made Easy with Minitab
-
Using Minitab for Root Cause Analysis
-
Conclusion
Introduction to Minitab
Minitab is a versatile and powerful statistical software package used extensively in data analysis, quality control, and process improvement. With a user-friendly interface and a comprehensive set of statistical tools, Minitab enables professionals and organizations to analyze data, make data-driven decisions, and enhance the quality of products and services. It offers a wide range of features, including data import from various sources, hypothesis testing, regression analysis, control chart creation, and process capability analysis. Minitab's compatibility with Six Sigma methodologies further enhances its appeal as it aligns seamlessly with the DMAIC (Define, Measure, Analyze, Improve, Control) framework, making it a go-to tool for professionals aiming to optimize processes and achieve higher quality standards in various industries.
Professionals from diverse fields, including manufacturing, healthcare, finance, and education, rely on Minitab to uncover insights from data and drive continuous improvement. Minitab's accessibility through various licensing options, coupled with its extensive learning resources and tutorials, makes it suitable for both beginners and experienced statisticians. As data analysis continues to play a pivotal role in decision-making, Minitab remains a valuable asset, helping individuals and organizations harness the power of data to achieve their goals and maintain a competitive edge in their respective industries.
How Minitab Facilitates Data Analysis in Six Sigma Projects
Minitab plays a crucial role in facilitating data analysis within Six Sigma projects by providing a robust set of tools and features tailored to the methodology's DMAIC (Define, Measure, Analyze, Improve, Control) framework. Here's how Minitab contributes to each phase of a Six Sigma project:
-
Define Phase: Minitab assists in defining project goals, scope, and metrics by helping users collect and organize data. It can be used to create project charters and establish clear objectives. Additionally, it supports the creation of process maps and flowcharts, aiding in the identification of potential improvement areas.
-
Measure Phase: In this phase, Minitab enables users to collect and analyze data to quantify the current state of a process. It simplifies data entry, statistical calculations, and the creation of graphical representations such as histograms and box plots. Minitab's capabilities for measurement system analysis (MSA) ensure that data collection methods are reliable, a fundamental aspect of Six Sigma.
-
Analyze Phase: Minitab shines in the Analyze phase by offering a wide range of statistical tools. It simplifies hypothesis testing, regression analysis, and design of experiments (DOE), helping users identify the root causes of process issues and validate potential improvement factors. Users can also create various graphical representations to visualize data relationships, making it easier to pinpoint areas for improvement.
-
Improve Phase: Minitab supports users in implementing and testing improvement solutions. It assists in optimizing processes by conducting Monte Carlo simulations, which evaluate the impact of different variables on process performance. This phase also benefits from Minitab's capabilities for factorial experiments and response surface methodology (RSM).
-
Control Phase: Finally, in the Control phase, Minitab aids in establishing control mechanisms to sustain process improvements. Users can create control charts, set control limits, and monitor process stability over time. Minitab also helps in documenting standard operating procedures and creating visual aids for training and continuous monitoring.
Overall, Minitab's user-friendly interface, extensive statistical capabilities, and alignment with Six Sigma principles make it an indispensable tool for data analysis throughout the DMAIC framework. It empowers Six Sigma practitioners to make data-driven decisions, identify process improvements, and drive quality and efficiency enhancements in their organizations.
Minitab and DMAIC
Minitab and DMAIC are two pillars of success in Six Sigma methodology, working hand in hand to achieve process improvement and quality enhancement. Minitab, as a statistical software tool, is well-aligned with the DMAIC framework's five phases, from defining project objectives to controlling and maintaining process improvements. It simplifies data collection, organizes information, conducts robust statistical analyses, and assists in visualizing data relationships, enabling Six Sigma practitioners to make informed decisions at each stage of the project. Whether it's hypothesis testing in the Analyze phase or creating control charts in the Control phase, Minitab provides the necessary tools and features to drive data-driven excellence within a Six Sigma context.
The synergy between Minitab and DMAIC empowers organizations to identify and address process inefficiencies, reduce defects, and enhance overall quality. Minitab's user-friendly interface and comprehensive statistical capabilities streamline the application of Six Sigma principles, making it a vital asset for professionals and teams dedicated to process optimization and continuous improvement. By leveraging Minitab in conjunction with DMAIC, businesses can achieve higher quality standards, reduced variability, and increased customer satisfaction, ultimately leading to improved competitiveness and success in today's competitive marketplace.
Statistical Analysis with Minitab
Statistical analysis with Minitab is a dynamic and versatile process that empowers individuals and organizations to extract meaningful insights from data. Minitab's user-friendly interface simplifies the often complex world of statistics, enabling users to perform a wide range of statistical analyses with ease. From conducting hypothesis tests and regression analysis to creating control charts and designing experiments, Minitab provides a comprehensive suite of tools to address diverse analytical needs. Moreover, its ability to generate clear and compelling visualizations enhances the understanding and communication of statistical findings. Minitab's role extends beyond just number crunching; it fosters data-driven decision-making, supports quality control efforts, and aids in process optimization, ultimately contributing to improved outcomes and greater efficiency across various domains.
Whether in the realms of business, academia, healthcare, or manufacturing, statistical analysis with Minitab empowers professionals to uncover trends, identify patterns, and make informed choices based on data-driven evidence. Its widespread adoption in quality control, Six Sigma projects, research, and beyond underscores its importance as a valuable tool for data analysis and decision support. In an era where data is increasingly integral to success, Minitab remains a reliable and indispensable partner, ensuring that the power of statistics is accessible and actionable for individuals and organizations alike.
Creating Control Charts with Minitab
Creating control charts with Minitab is a cornerstone of effective quality control and process monitoring. Minitab's user-friendly interface and extensive charting capabilities make it accessible to both beginners and experienced quality professionals. With Minitab, users can effortlessly generate a variety of control charts, such as X-bar and R charts for continuous data or p-charts for attribute data, with just a few clicks. The software automatically calculates control limits, plots data points, and highlights potential issues in a visually intuitive manner.
Interpreting these control charts is equally straightforward; users can quickly identify trends, shifts, or outliers that might indicate process instability. Minitab empowers organizations to proactively address quality issues, reduce defects, and enhance process performance by providing a comprehensive solution for monitoring and maintaining control over critical processes. Its role in facilitating the creation and interpretation of control charts ensures that organizations can achieve and sustain the highest standards of quality control and efficiency, fostering continuous improvement in their operations.
Hypothesis Testing in Minitab
Here are the steps to perform hypothesis testing in Minitab in simple points:
-
Data Entry: Enter your data into Minitab.
-
Select Test: Choose the specific hypothesis test you need (e.g., t-test, ANOVA) from Minitab's menu.
-
Define Hypotheses: State your null hypothesis (H0) and alternative hypothesis (Ha).
-
Perform the Test: Minitab calculates the test statistic and p-value based on your data.
-
Interpret Results: If p-value is smaller than your chosen significance level, reject the null hypothesis. If not, fail to reject it.
-
Draw Conclusions: Make decisions based on the p-value and the specific hypothesis test.
-
Generate Reports: Create reports and visualizations of your results using Minitab's tools.
Minitab simplifies hypothesis testing, making it accessible for making data-driven decisions in various fields.
Regression Analysis in Minitab
Regression analysis in Minitab is a powerful tool for understanding and quantifying relationships between variables. With a straightforward interface, it enables users to perform a wide range of regression analyses, from simple linear regressions to more complex multiple regression models. Users begin by entering their data and specifying the response and predictor variables of interest. Minitab then runs the analysis, providing crucial statistics such as coefficients, p-values, and R-squared values that help assess the strength and significance of these relationships.
Interpreting the results is made accessible, allowing users to draw meaningful conclusions and make predictions based on their data. Whether it's uncovering the factors that impact sales figures, evaluating the effectiveness of marketing campaigns, or making informed decisions in research, Minitab's regression analysis capabilities simplify the process, making it an indispensable resource for professionals across diverse fields. Its ability to visualize data and generate comprehensive reports further enhances its utility, ensuring that organizations can harness the power of regression analysis for data-driven insights and improved decision-making.
Design of Experiments (DOE) Made Easy with Minitab
Design of Experiments (DOE) is a systematic approach for conducting experiments to optimize processes, improve products, and identify critical factors affecting outcomes. Minitab, a widely used statistical software, simplifies the entire DOE process, making it accessible to both beginners and experienced practitioners. Here's how Minitab makes DOE easy:
-
Experimental Design Wizard: Minitab offers an intuitive Experimental Design Wizard that guides users through the DOE process step by step. This tool helps users select the appropriate design type, define factors and responses, and choose the levels of these factors.
-
Design Selection: Minitab provides a variety of design types, including full factorial, fractional factorial, response surface, and mixture designs. Users can easily select the design that suits their specific experiment requirements.
-
Factorial and Fractional Factorial Designs: Minitab automatically generates the necessary experimental runs and assigns factor settings based on the chosen design. This simplifies the planning process and reduces the number of experimental trials needed, saving time and resources.
-
Response Optimization: Minitab helps users analyze the results of their experiments by fitting models and optimizing responses. It provides visualizations, contour plots, and response surface plots that aid in understanding the relationships between factors and responses.
-
Robust Parameter Design (RPD): Minitab includes tools for conducting robust parameter design, which allows users to optimize processes while considering variability and noise factors, ensuring robust and reliable outcomes.
-
Analysis of Variance (ANOVA): Minitab automates the ANOVA analysis, making it easy to identify significant factors and interactions in the experimental data.
-
Data Visualization: Minitab's graphical capabilities help users visualize the effects of factors on responses, facilitating the interpretation of results.
-
Statistical Output: The software generates comprehensive reports that summarize the experimental design, analysis, and optimization results, making it simple to communicate findings to stakeholders.
-
Quality Improvement: Minitab's DOE tools are particularly valuable in Six Sigma and quality improvement projects, as they enable practitioners to identify the optimal settings for process parameters that minimize defects and variation.
By providing a user-friendly interface, automated calculations, and comprehensive analysis and reporting capabilities, Minitab streamlines the design of experiments. This accessibility empowers organizations to conduct efficient and effective experiments, leading to improved processes, products, and overall quality while saving time and resources in the process.
Using Minitab for Root Cause Analysis
Minitab is a powerful ally in the process of root cause analysis, offering a comprehensive suite of statistical tools and data analysis capabilities. The journey begins by clearly defining the problem and gathering relevant data, which Minitab helps organize and prepare for analysis. Its intuitive graphical tools and descriptive statistics assist in exploring data distributions and patterns, providing valuable insights into the nature of the problem. Minitab's versatility shines during the brainstorming phase, as it aids in creating cause-and-effect diagrams to systematically identify potential causes across different categories. Once potential causes are identified, Minitab facilitates their prioritization through Pareto analysis, ensuring that the most significant factors are addressed first. Through hypothesis testing and regression analysis, Minitab helps validate hypotheses about the root causes, enabling data-driven decision-making.
Beyond analysis, Minitab supports corrective action planning and monitoring by helping organizations track the effectiveness of implemented solutions. Control charts and ongoing data analysis ensure that processes remain stable and that the identified root causes are genuinely mitigated. Finally, Minitab aids in documentation and reporting, allowing organizations to maintain a clear record of the root cause analysis process and communicate findings and actions effectively. In essence, Minitab serves as an indispensable tool for organizations committed to uncovering the underlying causes of problems and implementing data-driven solutions for process improvement and quality enhancement.
Conclusion
In conclusion, Minitab is a versatile and powerful statistical software package that plays a pivotal role in data analysis, quality control, Six Sigma projects, regression analysis, and root cause analysis. Its user-friendly interface, comprehensive statistical tools, and graphical capabilities make it accessible to both beginners and experienced professionals across various industries.
Minitab simplifies complex statistical processes, empowering users to make data-driven decisions, uncover insights from data, and optimize processes. Whether it's conducting hypothesis tests, creating control charts, designing experiments, or identifying root causes of problems, Minitab streamlines the analytical journey, saving time and resources while ensuring accurate results.
As organizations continue to rely on data-driven decision-making for success, Minitab remains a valuable asset, facilitating the pursuit of quality improvement, process optimization, and continuous excellence. Its role in supporting Six Sigma methodologies, conducting robust regression analyses, and aiding in root cause analysis positions it as a trusted partner for professionals and organizations dedicated to harnessing the power of data for growth and competitiveness.
Read More
In an era where data is the lifeblood of informed decision-making, organizations across diverse industries strive for excellence in quality control and process improvement. Six Sigma, a methodology focused on minimizing defects and variations, stands as a beacon of efficiency and quality. At the heart of this data-driven revolution lies Minitab, a versatile statistical software package. In this blog, we embark on a journey to explore "The Role of Minitab in Quality Control and Six Sigma." We will unravel how Minitab empowers professionals and organizations to harness the power of data, streamline processes, and elevate quality standards. From hypothesis testing and control charts to regression analysis and root cause analysis, Minitab serves as an indispensable tool, enabling the pursuit of data-driven excellence and the achievement of Six Sigma's lofty goals. Join us as we delve into the essential role that Minitab plays in the world of quality control and process improvement, where data reigns supreme and continuous improvement is the ultimate objective.
Table of contents
-
Introduction to Minitab
-
How Minitab Facilitates Data Analysis in Six Sigma Projects
-
Minitab and DMAIC
-
Statistical Analysis with Minitab
-
Creating Control Charts with Minitab
-
Hypothesis Testing in Minitab
-
Regression Analysis in Minitab
-
Design of Experiments (DOE) Made Easy with Minitab
-
Using Minitab for Root Cause Analysis
-
Conclusion
Introduction to Minitab
Minitab is a versatile and powerful statistical software package used extensively in data analysis, quality control, and process improvement. With a user-friendly interface and a comprehensive set of statistical tools, Minitab enables professionals and organizations to analyze data, make data-driven decisions, and enhance the quality of products and services. It offers a wide range of features, including data import from various sources, hypothesis testing, regression analysis, control chart creation, and process capability analysis. Minitab's compatibility with Six Sigma methodologies further enhances its appeal as it aligns seamlessly with the DMAIC (Define, Measure, Analyze, Improve, Control) framework, making it a go-to tool for professionals aiming to optimize processes and achieve higher quality standards in various industries.
Professionals from diverse fields, including manufacturing, healthcare, finance, and education, rely on Minitab to uncover insights from data and drive continuous improvement. Minitab's accessibility through various licensing options, coupled with its extensive learning resources and tutorials, makes it suitable for both beginners and experienced statisticians. As data analysis continues to play a pivotal role in decision-making, Minitab remains a valuable asset, helping individuals and organizations harness the power of data to achieve their goals and maintain a competitive edge in their respective industries.
How Minitab Facilitates Data Analysis in Six Sigma Projects
Minitab plays a crucial role in facilitating data analysis within Six Sigma projects by providing a robust set of tools and features tailored to the methodology's DMAIC (Define, Measure, Analyze, Improve, Control) framework. Here's how Minitab contributes to each phase of a Six Sigma project:
-
Define Phase: Minitab assists in defining project goals, scope, and metrics by helping users collect and organize data. It can be used to create project charters and establish clear objectives. Additionally, it supports the creation of process maps and flowcharts, aiding in the identification of potential improvement areas.
-
Measure Phase: In this phase, Minitab enables users to collect and analyze data to quantify the current state of a process. It simplifies data entry, statistical calculations, and the creation of graphical representations such as histograms and box plots. Minitab's capabilities for measurement system analysis (MSA) ensure that data collection methods are reliable, a fundamental aspect of Six Sigma.
-
Analyze Phase: Minitab shines in the Analyze phase by offering a wide range of statistical tools. It simplifies hypothesis testing, regression analysis, and design of experiments (DOE), helping users identify the root causes of process issues and validate potential improvement factors. Users can also create various graphical representations to visualize data relationships, making it easier to pinpoint areas for improvement.
-
Improve Phase: Minitab supports users in implementing and testing improvement solutions. It assists in optimizing processes by conducting Monte Carlo simulations, which evaluate the impact of different variables on process performance. This phase also benefits from Minitab's capabilities for factorial experiments and response surface methodology (RSM).
-
Control Phase: Finally, in the Control phase, Minitab aids in establishing control mechanisms to sustain process improvements. Users can create control charts, set control limits, and monitor process stability over time. Minitab also helps in documenting standard operating procedures and creating visual aids for training and continuous monitoring.
Overall, Minitab's user-friendly interface, extensive statistical capabilities, and alignment with Six Sigma principles make it an indispensable tool for data analysis throughout the DMAIC framework. It empowers Six Sigma practitioners to make data-driven decisions, identify process improvements, and drive quality and efficiency enhancements in their organizations.
Minitab and DMAIC
Minitab and DMAIC are two pillars of success in Six Sigma methodology, working hand in hand to achieve process improvement and quality enhancement. Minitab, as a statistical software tool, is well-aligned with the DMAIC framework's five phases, from defining project objectives to controlling and maintaining process improvements. It simplifies data collection, organizes information, conducts robust statistical analyses, and assists in visualizing data relationships, enabling Six Sigma practitioners to make informed decisions at each stage of the project. Whether it's hypothesis testing in the Analyze phase or creating control charts in the Control phase, Minitab provides the necessary tools and features to drive data-driven excellence within a Six Sigma context.
The synergy between Minitab and DMAIC empowers organizations to identify and address process inefficiencies, reduce defects, and enhance overall quality. Minitab's user-friendly interface and comprehensive statistical capabilities streamline the application of Six Sigma principles, making it a vital asset for professionals and teams dedicated to process optimization and continuous improvement. By leveraging Minitab in conjunction with DMAIC, businesses can achieve higher quality standards, reduced variability, and increased customer satisfaction, ultimately leading to improved competitiveness and success in today's competitive marketplace.
Statistical Analysis with Minitab
Statistical analysis with Minitab is a dynamic and versatile process that empowers individuals and organizations to extract meaningful insights from data. Minitab's user-friendly interface simplifies the often complex world of statistics, enabling users to perform a wide range of statistical analyses with ease. From conducting hypothesis tests and regression analysis to creating control charts and designing experiments, Minitab provides a comprehensive suite of tools to address diverse analytical needs. Moreover, its ability to generate clear and compelling visualizations enhances the understanding and communication of statistical findings. Minitab's role extends beyond just number crunching; it fosters data-driven decision-making, supports quality control efforts, and aids in process optimization, ultimately contributing to improved outcomes and greater efficiency across various domains.
Whether in the realms of business, academia, healthcare, or manufacturing, statistical analysis with Minitab empowers professionals to uncover trends, identify patterns, and make informed choices based on data-driven evidence. Its widespread adoption in quality control, Six Sigma projects, research, and beyond underscores its importance as a valuable tool for data analysis and decision support. In an era where data is increasingly integral to success, Minitab remains a reliable and indispensable partner, ensuring that the power of statistics is accessible and actionable for individuals and organizations alike.
Creating Control Charts with Minitab
Creating control charts with Minitab is a cornerstone of effective quality control and process monitoring. Minitab's user-friendly interface and extensive charting capabilities make it accessible to both beginners and experienced quality professionals. With Minitab, users can effortlessly generate a variety of control charts, such as X-bar and R charts for continuous data or p-charts for attribute data, with just a few clicks. The software automatically calculates control limits, plots data points, and highlights potential issues in a visually intuitive manner.
Interpreting these control charts is equally straightforward; users can quickly identify trends, shifts, or outliers that might indicate process instability. Minitab empowers organizations to proactively address quality issues, reduce defects, and enhance process performance by providing a comprehensive solution for monitoring and maintaining control over critical processes. Its role in facilitating the creation and interpretation of control charts ensures that organizations can achieve and sustain the highest standards of quality control and efficiency, fostering continuous improvement in their operations.
Hypothesis Testing in Minitab
Here are the steps to perform hypothesis testing in Minitab in simple points:
-
Data Entry: Enter your data into Minitab.
-
Select Test: Choose the specific hypothesis test you need (e.g., t-test, ANOVA) from Minitab's menu.
-
Define Hypotheses: State your null hypothesis (H0) and alternative hypothesis (Ha).
-
Perform the Test: Minitab calculates the test statistic and p-value based on your data.
-
Interpret Results: If p-value is smaller than your chosen significance level, reject the null hypothesis. If not, fail to reject it.
-
Draw Conclusions: Make decisions based on the p-value and the specific hypothesis test.
-
Generate Reports: Create reports and visualizations of your results using Minitab's tools.
Minitab simplifies hypothesis testing, making it accessible for making data-driven decisions in various fields.
Regression Analysis in Minitab
Regression analysis in Minitab is a powerful tool for understanding and quantifying relationships between variables. With a straightforward interface, it enables users to perform a wide range of regression analyses, from simple linear regressions to more complex multiple regression models. Users begin by entering their data and specifying the response and predictor variables of interest. Minitab then runs the analysis, providing crucial statistics such as coefficients, p-values, and R-squared values that help assess the strength and significance of these relationships.
Interpreting the results is made accessible, allowing users to draw meaningful conclusions and make predictions based on their data. Whether it's uncovering the factors that impact sales figures, evaluating the effectiveness of marketing campaigns, or making informed decisions in research, Minitab's regression analysis capabilities simplify the process, making it an indispensable resource for professionals across diverse fields. Its ability to visualize data and generate comprehensive reports further enhances its utility, ensuring that organizations can harness the power of regression analysis for data-driven insights and improved decision-making.
Design of Experiments (DOE) Made Easy with Minitab
Design of Experiments (DOE) is a systematic approach for conducting experiments to optimize processes, improve products, and identify critical factors affecting outcomes. Minitab, a widely used statistical software, simplifies the entire DOE process, making it accessible to both beginners and experienced practitioners. Here's how Minitab makes DOE easy:
-
Experimental Design Wizard: Minitab offers an intuitive Experimental Design Wizard that guides users through the DOE process step by step. This tool helps users select the appropriate design type, define factors and responses, and choose the levels of these factors.
-
Design Selection: Minitab provides a variety of design types, including full factorial, fractional factorial, response surface, and mixture designs. Users can easily select the design that suits their specific experiment requirements.
-
Factorial and Fractional Factorial Designs: Minitab automatically generates the necessary experimental runs and assigns factor settings based on the chosen design. This simplifies the planning process and reduces the number of experimental trials needed, saving time and resources.
-
Response Optimization: Minitab helps users analyze the results of their experiments by fitting models and optimizing responses. It provides visualizations, contour plots, and response surface plots that aid in understanding the relationships between factors and responses.
-
Robust Parameter Design (RPD): Minitab includes tools for conducting robust parameter design, which allows users to optimize processes while considering variability and noise factors, ensuring robust and reliable outcomes.
-
Analysis of Variance (ANOVA): Minitab automates the ANOVA analysis, making it easy to identify significant factors and interactions in the experimental data.
-
Data Visualization: Minitab's graphical capabilities help users visualize the effects of factors on responses, facilitating the interpretation of results.
-
Statistical Output: The software generates comprehensive reports that summarize the experimental design, analysis, and optimization results, making it simple to communicate findings to stakeholders.
-
Quality Improvement: Minitab's DOE tools are particularly valuable in Six Sigma and quality improvement projects, as they enable practitioners to identify the optimal settings for process parameters that minimize defects and variation.
By providing a user-friendly interface, automated calculations, and comprehensive analysis and reporting capabilities, Minitab streamlines the design of experiments. This accessibility empowers organizations to conduct efficient and effective experiments, leading to improved processes, products, and overall quality while saving time and resources in the process.
Using Minitab for Root Cause Analysis
Minitab is a powerful ally in the process of root cause analysis, offering a comprehensive suite of statistical tools and data analysis capabilities. The journey begins by clearly defining the problem and gathering relevant data, which Minitab helps organize and prepare for analysis. Its intuitive graphical tools and descriptive statistics assist in exploring data distributions and patterns, providing valuable insights into the nature of the problem. Minitab's versatility shines during the brainstorming phase, as it aids in creating cause-and-effect diagrams to systematically identify potential causes across different categories. Once potential causes are identified, Minitab facilitates their prioritization through Pareto analysis, ensuring that the most significant factors are addressed first. Through hypothesis testing and regression analysis, Minitab helps validate hypotheses about the root causes, enabling data-driven decision-making.
Beyond analysis, Minitab supports corrective action planning and monitoring by helping organizations track the effectiveness of implemented solutions. Control charts and ongoing data analysis ensure that processes remain stable and that the identified root causes are genuinely mitigated. Finally, Minitab aids in documentation and reporting, allowing organizations to maintain a clear record of the root cause analysis process and communicate findings and actions effectively. In essence, Minitab serves as an indispensable tool for organizations committed to uncovering the underlying causes of problems and implementing data-driven solutions for process improvement and quality enhancement.
Conclusion
In conclusion, Minitab is a versatile and powerful statistical software package that plays a pivotal role in data analysis, quality control, Six Sigma projects, regression analysis, and root cause analysis. Its user-friendly interface, comprehensive statistical tools, and graphical capabilities make it accessible to both beginners and experienced professionals across various industries.
Minitab simplifies complex statistical processes, empowering users to make data-driven decisions, uncover insights from data, and optimize processes. Whether it's conducting hypothesis tests, creating control charts, designing experiments, or identifying root causes of problems, Minitab streamlines the analytical journey, saving time and resources while ensuring accurate results.
As organizations continue to rely on data-driven decision-making for success, Minitab remains a valuable asset, facilitating the pursuit of quality improvement, process optimization, and continuous excellence. Its role in supporting Six Sigma methodologies, conducting robust regression analyses, and aiding in root cause analysis positions it as a trusted partner for professionals and organizations dedicated to harnessing the power of data for growth and competitiveness.
CMMI for Agile: Merging Agile Practices with CMMI Standards
In today's fast-paced and ever-evolving business landscape, organizations are continually seeking ways to deliver high-quality products and services while remaining agile and responsive to customer needs. Agile methodologies have emerged as a beacon of adaptability and customer-centricity, empowering teams to iterate quickly and stay in tune with market demands. Simultaneously, the Capability Maturity Model Integration (CMMI) provides a structured framework for process improvement, ensuring consistency, reliability, and efficiency in operations.
But what happens when you bring these two seemingly contrasting worlds together? Can Agile practices and CMMI certification coexist harmoniously, allowing organizations to reap the benefits of both approaches? The answer is a resounding "yes." This blog explores the dynamic intersection of Agile and CMMI, shedding light on how organizations can successfully integrate Agile practices with CMMI certification, ultimately achieving a unique synergy that enhances both agility and process maturity. Join us on this journey of discovery as we uncover the strategies, challenges, and advantages of merging Agile with CMMI, ushering in a new era of process excellence and customer satisfaction.
Table of Contents
-
Understanding CMMI and Agile Methodologies
-
Benefits of Combining CMMI and Agile
-
Mapping Agile Practices to CMMI Framework
-
Tailoring CMMI for Agile Environments
-
Roles and Responsibilities in Agile CMMI Integration
-
Measuring Agile Performance with CMMI Metrics
-
Agile CMMI Certification Levels
-
Challenges in Integrating Agile and CMMI
-
Training and Skill Development for Agile CMMI
-
Continuous Improvement in Agile CMMI
-
Tools and Software for Agile CMMI Integration
-
Audit and Assessment for Agile CMMI Certification
-
Scaling Agile with CMMI
-
Future Trends in Agile CMMI Integration
-
Conclusion
Understanding CMMI and Agile Methodologies
CMMI (Capability Maturity Model Integration) is a framework that enables organizations to enhance their processes and consistently deliver high-quality products and services. It encompasses maturity levels and specific process areas to guide organizations towards process improvement and optimization. CMMI promotes a culture of continuous improvement, encouraging organizations to monitor, measure, and refine their processes over time. Organizations can undergo CMMI assessments to gauge their process maturity and, if they meet the criteria, seek formal certification.
On the other hand, Agile methodologies are a set of principles and practices for software development and project management that prioritize adaptability, collaboration, and customer feedback. Agile embraces iterative and incremental development, frequent customer involvement, and cross-functional teams. It relies on empirical data and regular inspections to make informed decisions and respond to changing requirements. Agile is guided by the Agile Manifesto and its principles, emphasizing customer collaboration and working solutions.
The relationship between CMMI and Agile involves integrating these approaches to achieve higher levels of process maturity while retaining the flexibility and customer-centric focus of Agile methodologies. This integration, known as "Agile CMMI" or "CMMI for Agile," allows organizations to improve their processes systematically while remaining agile and responsive in an ever-evolving business landscape. By combining the strengths of both CMMI and Agile, organizations can enhance their capabilities, deliver value more efficiently, and meet customer needs effectively.
Benefits of Combining CMMI and Agile
-
Better Processes: CMMI improves your organization's processes, making them more efficient and effective.
-
Flexibility: Agile's adaptability to change is retained, ensuring you can respond quickly to customer needs.
-
Quality: The integration enhances product quality and reduces defects.
-
Customer Satisfaction: Agile's customer focus, combined with CMMI, leads to higher customer satisfaction.
-
Risk Management: You can identify and manage risks more effectively, reducing project disruptions.
-
Resource Efficiency: It helps optimize resource allocation and utilization for dynamic projects.
-
Compliance: You can meet industry standards and compliance requirements while using Agile practices.
-
Culture of Improvement: It fosters a culture of continuous improvement within your organization.
-
Measurable Progress: You can measure and track your progress effectively.
-
Competitive Advantage: Successful integration can give you a competitive edge by delivering high-quality products or services faster and more efficiently.
Mapping Agile Practices to CMMI Framework
Mapping Agile practices to the CMMI (Capability Maturity Model Integration) framework is a strategic approach that enables organizations to combine the agility of Agile methodologies with the structured process improvement provided by CMMI. In this integration, Agile principles and practices align with specific CMMI process areas and goals. For instance, Agile's emphasis on customer collaboration and responsiveness can be linked to CMMI's objectives related to managing requirements effectively and handling change through configuration management. Sprints and iterations in Agile neatly correspond to CMMI's project planning and monitoring and control process areas, and Agile's focus on continuous integration aligns with CMMI's configuration management practices. By mapping these connections, organizations can ensure that their Agile practices contribute to meeting CMMI compliance requirements while still reaping the benefits of Agile's customer-centric, iterative approach to development.
Furthermore, mapping Agile practices to CMMI facilitates a data-driven approach to decision-making by connecting Agile metrics and practices with CMMI's measurement and analysis process area. Agile teams can use metrics like velocity and burndown charts in conjunction with CMMI's goals to continuously improve processes and product quality. This integration also helps organizations manage large-scale Agile projects by considering CMMI for Development, which extends CMMI's process areas to address scalability and complex development environments. Ultimately, the mapping of Agile practices to the CMMI framework empowers organizations to harmonize two powerful methodologies, enhancing both process maturity and agility in their software development and project management endeavors.
Tailoring CMMI for Agile Environments
Tailoring CMMI (Capability Maturity Model Integration) for Agile environments is a strategic approach that recognizes the unique characteristics of Agile methodologies while harnessing the structured process improvement capabilities of CMMI. In this adaptation, organizations embrace Agile's core values such as customer collaboration, responsiveness to change, and iterative development, while identifying the areas within CMMI that can support and enhance these principles. Agile's preference for working software over excessive documentation is met by streamlining documentation requirements, ensuring that any documentation created serves a meaningful purpose. Additionally, tailored metrics in Agile environments shift the focus towards velocity, burndown rates, and customer satisfaction, aligning more closely with Agile project goals and priorities. The synergy between Agile's iterative cycles and CMMI's process improvement cycles allows for continuous enhancements in Agile projects while maintaining the rigor of CMMI.
Moreover, effective tailoring encourages cross-functional collaboration between Agile teams and CMMI practitioners, fostering an environment where the strengths of both approaches are leveraged. This collaboration results in valuable insights, shared best practices, and a culture of ongoing process improvement. By documenting the tailoring decisions and promoting a culture of continuous improvement, organizations can ensure that their tailored CMMI-Agile framework remains flexible, adaptable, and aligned with the ever-evolving needs of Agile development projects. In essence, tailoring CMMI for Agile environments allows organizations to strike a harmonious balance between structured process improvement and the agile, customer-focused, and iterative nature of Agile methodologies, ultimately driving higher-quality outcomes in software development and project management.
Roles and Responsibilities in Agile CMMI Integration
-
Agile Coach:
-
Responsibilities: Guides Agile practices and helps teams understand how Agile aligns with CMMI.
-
CMMI Process Improvement Lead:
-
Responsibilities: Oversees CMMI process improvements and ensures they fit Agile environments.
-
Scrum Masters and Agile Team Members:
-
Responsibilities: Scrum Masters facilitate Agile processes, while team members adapt Agile practices for CMMI.
-
Product Owners and Business Analysts:
-
Responsibilities: Define and prioritize requirements, ensuring they align with Agile and CMMI standards.
-
Quality Assurance and Testing Specialists:
-
Responsibilities: Ensure product quality through testing, adapting to Agile iterations while following CMMI quality practices.
-
Project Managers or Release Managers:
-
Responsibilities: Oversee project or release planning, ensuring alignment with CMMI process areas.
-
Change Agents and Champions:
-
Responsibilities: Advocate for Agile CMMI integration, promote best practices, and encourage a culture of improvement.
-
Auditors and Assessors:
-
Responsibilities: Conduct CMMI assessments and audits to verify compliance and provide feedback for improvement.
Clear communication and collaboration among these roles are essential for successful Agile CMMI integration, enhancing the organization's ability to deliver high-quality products and services while maintaining Agile principles.
Measuring Agile Performance with CMMI Metrics
Measuring Agile performance with CMMI metrics is a strategic approach that bridges the gap between the Agile methodologies' iterative, customer-focused practices and CMMI's structured process improvement framework. These metrics provide organizations with valuable insights into their Agile processes, aligning them with CMMI's goals of efficiency, quality, and continuous improvement. Metrics such as velocity, cycle time, and burndown charts enable teams to monitor progress, identify bottlenecks, and optimize their workflow within the Agile framework. Customer satisfaction surveys and feedback response times ensure that Agile teams remain customer-centric, meeting the requirements of CMMI's customer focus. Additionally, defect density and work item aging metrics help maintain product quality while highlighting areas for improvement, aligning with CMMI's emphasis on quality management.
The integration of CMMI metrics into Agile environments promotes a culture of measurement and analysis, enabling organizations to make data-driven decisions. This not only enhances the organization's ability to deliver high-quality products and services but also ensures compliance with CMMI standards. Ultimately, measuring Agile performance with CMMI metrics empowers organizations to leverage the strengths of both approaches, fostering greater process maturity, efficiency, and customer satisfaction in Agile development and project management.
Agile CMMI Certification Levels
-
CMMI Maturity Levels: CMMI certification involves maturity levels, from Level 1 to Level 5, representing increasing process maturity and capability.
-
Agile Integration: Organizations can integrate Agile practices into these CMMI maturity levels to maintain flexibility while meeting CMMI requirements.
-
Certification Assessment: Certified appraisers or auditors assess an organization's processes, including the integration of Agile practices, to determine certification eligibility.
-
Tailored CMMI: Some organizations use tailored CMMI frameworks that provide specific guidance on incorporating Agile practices at different maturity levels.
-
Industry Requirements: Compliance with CMMI, Agile, or both may be necessary to meet industry standards and client expectations.
-
Consult Experts: Seek guidance from CMMI experts or certification authorities for the latest information and specific certification requirements related to Agile and CMMI integration.
Challenges in Integrating Agile and CMMI
-
Cultural Differences: Balancing Agile's flexibility with CMMI's structured approach can be a cultural challenge.
-
Documentation: Finding the right balance between extensive CMMI documentation and Agile's minimal documentation can be tricky.
-
Resistance to Change: Teams may resist shifting from traditional CMMI practices to Agile or adding perceived bureaucracy to Agile.
-
Mapping Practices: Aligning Agile practices with CMMI requirements and maturity levels requires careful mapping.
-
Process Tailoring: Customizing CMMI practices to fit Agile environments is challenging but necessary.
-
Metrics: Developing metrics that effectively measure performance in an integrated approach can be difficult.
-
Resource Allocation: Allocating resources for both Agile and CMMI efforts must be balanced.
-
Audit and Assessment: Preparing for CMMI assessments and audits in Agile settings requires planning.
-
Skills and Training: Ensuring that team members have the skills for the integrated approach is vital.
-
Sustainability: Maintaining the integration over time and preventing it from becoming a one-time effort is a challenge that requires ongoing commitment and adaptation.
Training and Skill Development for Agile CMMI
Training and skill development are fundamental pillars of achieving a successful integration of Agile and CMMI within an organization. In such an integrated environment, team members, leaders, and practitioners need a comprehensive understanding of both Agile methodologies and CMMI standards to effectively navigate the complexities of this hybrid approach. Initially, basic Agile training establishes a common foundation, fostering an understanding of Agile principles and practices, such as Scrum or Kanban. Concurrently, CMMI-specific training introduces the organization to the CMMI framework's concepts, maturity levels, and process areas.
The critical component lies in integration awareness, where dedicated training sessions and workshops enlighten participants about how Agile practices seamlessly align with CMMI goals while highlighting areas requiring adaptation. These sessions underscore the importance of tailoring CMMI processes to Agile settings, facilitating a smooth transition. Furthermore, training extends to leadership roles, equipping managers and executives with Agile leadership principles and the skills needed to support and lead in an Agile CMMI environment. Ultimately, a continuous learning culture, role-specific training, and feedback mechanisms ensure that individuals and teams stay agile in their approach to process improvement, product development, and compliance, thereby enhancing the organization's ability to excel in both agility and quality assurance.
Continuous Improvement in Agile CMMI
Continuous improvement in Agile CMMI environments represents an ongoing commitment to excellence in process, product, and service delivery. By seamlessly integrating Agile's iterative, customer-centric approach with CMMI's structured process improvement framework, organizations create a powerful engine for relentless enhancement. Agile retrospectives, data-driven decision-making, and Kaizen principles are instrumental in identifying and addressing areas for improvement at the team level. These practices dovetail with CMMI's emphasis on process optimization and quality assurance, resulting in a culture of constant self-assessment and refinement. Data collected through Agile practices, such as velocity and customer feedback, serves as a valuable input for CMMI-compliant measurement and analysis, further aligning the two methodologies.
Moreover, in Agile CMMI environments, continuous improvement extends beyond processes to encompass skill development and leadership support. By nurturing a culture of learning and adaptation, organizations empower their teams and leaders to stay agile in their approach to both product development and process maturity. The synergy between Agile's adaptability and CMMI's rigor creates an environment where innovation and efficiency thrive, ultimately enabling organizations to deliver high-quality products and services that meet customer needs while ensuring compliance with CMMI standards. Top of Form
Tools and Software for Agile CMMI Integration
Tools and software play a crucial role in facilitating the integration of Agile and CMMI methodologies within an organization. These tools bridge the gap between Agile's flexibility and CMMI's structured processes, aiding in the seamless coexistence of both approaches. Project management tools like Jira and Azure DevOps enable Agile teams to plan, track, and manage their work efficiently while accommodating CMMI process areas. Agile Lifecycle Management (ALM) tools such as VersionOne and Rally provide comprehensive support for Agile practices and can be customized to align with CMMI standards. Requirements management tools ensure traceability and compliance with CMMI requirements, while test management tools contribute to quality assurance, aligning with CMMI's focus on testing. Configuration management and version control tools help organizations meet CMMI's configuration management process area requirements. Collaboration and communication tools foster transparency and knowledge sharing among Agile teams, making it easier to document and communicate process improvements. Metrics and analytics tools enable organizations to collect and analyze data for both Agile and CMMI goals, facilitating data-driven process enhancements. DevOps and CI/CD tools automate and streamline development and deployment processes, aligning with CMMI's process automation practices. Specialized process improvement tools may also be employed to support the adoption and assessment of CMMI practices, ensuring continuous process maturity enhancements.
However, the success of these tools in Agile CMMI integration hinges on how they are configured, customized, and integrated into the organization's workflows. Additionally, tool selection should be based on the specific needs and objectives of Agile CMMI integration. The tools serve as enablers, helping organizations achieve the dual goals of delivering high-quality products or services through Agile practices while adhering to the structured process improvement framework of CMMI.
Audit and Assessment for Agile CMMI Certification
The audit and assessment process for Agile CMMI certification is a rigorous and comprehensive evaluation that determines an organization's adherence to both Agile methodologies and CMMI process improvement standards. The journey begins with careful preparation, where trained CMMI appraisers assess an organization's documentation, scrutinize Agile artifacts, and conduct a gap analysis to identify areas of alignment and potential deviations. On-site assessments involve in-depth interviews, observations, and artifact reviews to gauge how Agile practices are implemented in practice. Data collected during the assessment, including Agile-specific metrics and process performance, forms the basis for analysis, leading to documented findings and recommendations.
The ultimate goal of Agile CMMI certification is to demonstrate that an organization can balance the adaptability and customer-centricity of Agile with the structured process improvement focus of CMMI. The certification decision is made by an external body, based on the assessment results, and organizations may receive maturity or capability level ratings. Beyond certification, the process serves as a catalyst for ongoing improvement, as organizations develop action plans to address recommendations and engage in periodic follow-up assessments to ensure that the integrated Agile-CMMI framework remains effective and aligned with evolving goals. This holistic approach to assessment underscores the commitment to continuous improvement, quality, and process maturity in Agile development and project management.
Scaling Agile with CMMI
Scaling Agile with CMMI is a strategic approach that harmonizes the flexibility and customer-centricity of Agile methodologies with the structured process improvement framework of CMMI, allowing organizations to effectively manage larger and more complex projects and portfolios. This integration typically begins by selecting a suitable Agile scaling framework like SAFe or LeSS, which provides guidance on how to expand Agile practices while ensuring alignment with CMMI goals. Customization of the chosen framework is crucial to adapt CMMI process areas to Agile practices and vice versa, striking the right balance between Agile's adaptability and CMMI's process rigor.
Leadership support plays a pivotal role in fostering this integration, as leaders champion the effort, allocate necessary resources, and actively engage in aligning Agile and CMMI practices. Organizations must prioritize continuous improvement, regularly assessing the integration's effectiveness through metrics, feedback, and assessment processes. By promoting a culture of collaboration, providing training and skill development, and maintaining compliance with CMMI standards through periodic assessments, organizations can successfully scale Agile while achieving the desired levels of process maturity and product quality. The result is a dynamic and adaptable approach to project and product management that thrives in complex and evolving business landscapes.
Future Trends in Agile CMMI Integration
The future of Agile CMMI integration promises to be both dynamic and transformative, reflecting the ever-evolving landscape of software development and process improvement. One key trend is the increasing role of AI and automation in optimizing processes and decision-making. AI-driven tools will assist organizations in analyzing vast datasets, identifying patterns, and recommending improvements, making Agile CMMI integration more data-driven and efficient. Additionally, as Agile principles continue to resonate with organizations seeking agility and customer-centricity, scaling Agile practices beyond individual teams to the entire enterprise will remain a prominent trend. Frameworks like SAFe and LeSS will evolve to support larger and more complex organizations in their Agile journeys, allowing them to balance agility with the structured process improvement goals of CMMI.
Another critical trend is the integration of security and compliance practices into Agile CMMI environments. With cybersecurity concerns on the rise, organizations will work to harmonize Agile's rapid delivery with CMMI's focus on risk management and compliance, ensuring that security and regulatory requirements are seamlessly embedded into the development process. As remote and distributed work become increasingly prevalent, Agile CMMI integration will adapt to address the unique challenges of virtual collaboration and process adherence. This adaptability, along with a growing emphasis on cultural transformation, will be instrumental in organizations' efforts to foster a culture of innovation, collaboration, and continuous learning, ultimately driving successful Agile CMMI integration in the years to come.
How to obtain the CMMI certification?
We are an Education Technology company providing certification training courses to accelerate careers of working professionals worldwide. We impart training through instructor-led classroom workshops, instructor-led live virtual training sessions, and self-paced e-learning courses.
We have successfully conducted training sessions in 108 countries across the globe and enabled thousands of working professionals to enhance the scope of their careers.
Our enterprise training portfolio includes in-demand and globally recognized certification training courses in Project Management, Quality Management, Business Analysis, IT Service Management, Agile and Scrum, Cyber Security, Data Science, and Emerging Technologies. Download our Enterprise Training Catalog from https://www.icertglobal.com/corporate-training-for-enterprises.php
Popular Courses include:
-
Project Management: PMP, CAPM ,PMI RMP
-
Quality Management: Six Sigma Black Belt ,Lean Six Sigma Green Belt, Lean Management, Minitab ,CMMI
-
Business Analysis: CBAP, CCBA, ECBA
-
Agile Training: PMI-ACP
-
Scrum Training: CSM
-
DevOps
-
Program Management: PgMP
-
IT Service Management & Governance: COBIT, ISO
Conclusion
In conclusion, Agile CMMI integration represents a powerful approach for organizations seeking to balance the flexibility and customer-centricity of Agile methodologies with the structured process improvement framework of CMMI. This integration enables organizations to achieve high levels of process maturity while delivering high-quality products and services. The process involves careful customization of Agile practices and CMMI process areas, leadership support, continuous improvement efforts, and a commitment to aligning Agile and CMMI principles. As the business landscape evolves, the integration of Agile and CMMI will continue to adapt to meet new challenges and opportunities.
Future trends in Agile CMMI integration, including the use of AI, scaling Agile practices, and the integration of security and compliance, will shape the way organizations approach process improvement and Agile delivery. Cultural transformation and a focus on value stream management will also play critical roles in the success of Agile CMMI integration efforts. Overall, the integration of Agile and CMMI is a journey toward achieving process excellence and delivering exceptional value to customers, and it will remain a key strategy for organizations striving to excel in an ever-changing world.
Read More
In today's fast-paced and ever-evolving business landscape, organizations are continually seeking ways to deliver high-quality products and services while remaining agile and responsive to customer needs. Agile methodologies have emerged as a beacon of adaptability and customer-centricity, empowering teams to iterate quickly and stay in tune with market demands. Simultaneously, the Capability Maturity Model Integration (CMMI) provides a structured framework for process improvement, ensuring consistency, reliability, and efficiency in operations.
But what happens when you bring these two seemingly contrasting worlds together? Can Agile practices and CMMI certification coexist harmoniously, allowing organizations to reap the benefits of both approaches? The answer is a resounding "yes." This blog explores the dynamic intersection of Agile and CMMI, shedding light on how organizations can successfully integrate Agile practices with CMMI certification, ultimately achieving a unique synergy that enhances both agility and process maturity. Join us on this journey of discovery as we uncover the strategies, challenges, and advantages of merging Agile with CMMI, ushering in a new era of process excellence and customer satisfaction.
Table of Contents
-
Understanding CMMI and Agile Methodologies
-
Benefits of Combining CMMI and Agile
-
Mapping Agile Practices to CMMI Framework
-
Tailoring CMMI for Agile Environments
-
Roles and Responsibilities in Agile CMMI Integration
-
Measuring Agile Performance with CMMI Metrics
-
Agile CMMI Certification Levels
-
Challenges in Integrating Agile and CMMI
-
Training and Skill Development for Agile CMMI
-
Continuous Improvement in Agile CMMI
-
Tools and Software for Agile CMMI Integration
-
Audit and Assessment for Agile CMMI Certification
-
Scaling Agile with CMMI
-
Future Trends in Agile CMMI Integration
-
Conclusion
Understanding CMMI and Agile Methodologies
CMMI (Capability Maturity Model Integration) is a framework that enables organizations to enhance their processes and consistently deliver high-quality products and services. It encompasses maturity levels and specific process areas to guide organizations towards process improvement and optimization. CMMI promotes a culture of continuous improvement, encouraging organizations to monitor, measure, and refine their processes over time. Organizations can undergo CMMI assessments to gauge their process maturity and, if they meet the criteria, seek formal certification.
On the other hand, Agile methodologies are a set of principles and practices for software development and project management that prioritize adaptability, collaboration, and customer feedback. Agile embraces iterative and incremental development, frequent customer involvement, and cross-functional teams. It relies on empirical data and regular inspections to make informed decisions and respond to changing requirements. Agile is guided by the Agile Manifesto and its principles, emphasizing customer collaboration and working solutions.
The relationship between CMMI and Agile involves integrating these approaches to achieve higher levels of process maturity while retaining the flexibility and customer-centric focus of Agile methodologies. This integration, known as "Agile CMMI" or "CMMI for Agile," allows organizations to improve their processes systematically while remaining agile and responsive in an ever-evolving business landscape. By combining the strengths of both CMMI and Agile, organizations can enhance their capabilities, deliver value more efficiently, and meet customer needs effectively.
Benefits of Combining CMMI and Agile
-
Better Processes: CMMI improves your organization's processes, making them more efficient and effective.
-
Flexibility: Agile's adaptability to change is retained, ensuring you can respond quickly to customer needs.
-
Quality: The integration enhances product quality and reduces defects.
-
Customer Satisfaction: Agile's customer focus, combined with CMMI, leads to higher customer satisfaction.
-
Risk Management: You can identify and manage risks more effectively, reducing project disruptions.
-
Resource Efficiency: It helps optimize resource allocation and utilization for dynamic projects.
-
Compliance: You can meet industry standards and compliance requirements while using Agile practices.
-
Culture of Improvement: It fosters a culture of continuous improvement within your organization.
-
Measurable Progress: You can measure and track your progress effectively.
-
Competitive Advantage: Successful integration can give you a competitive edge by delivering high-quality products or services faster and more efficiently.
Mapping Agile Practices to CMMI Framework
Mapping Agile practices to the CMMI (Capability Maturity Model Integration) framework is a strategic approach that enables organizations to combine the agility of Agile methodologies with the structured process improvement provided by CMMI. In this integration, Agile principles and practices align with specific CMMI process areas and goals. For instance, Agile's emphasis on customer collaboration and responsiveness can be linked to CMMI's objectives related to managing requirements effectively and handling change through configuration management. Sprints and iterations in Agile neatly correspond to CMMI's project planning and monitoring and control process areas, and Agile's focus on continuous integration aligns with CMMI's configuration management practices. By mapping these connections, organizations can ensure that their Agile practices contribute to meeting CMMI compliance requirements while still reaping the benefits of Agile's customer-centric, iterative approach to development.
Furthermore, mapping Agile practices to CMMI facilitates a data-driven approach to decision-making by connecting Agile metrics and practices with CMMI's measurement and analysis process area. Agile teams can use metrics like velocity and burndown charts in conjunction with CMMI's goals to continuously improve processes and product quality. This integration also helps organizations manage large-scale Agile projects by considering CMMI for Development, which extends CMMI's process areas to address scalability and complex development environments. Ultimately, the mapping of Agile practices to the CMMI framework empowers organizations to harmonize two powerful methodologies, enhancing both process maturity and agility in their software development and project management endeavors.
Tailoring CMMI for Agile Environments
Tailoring CMMI (Capability Maturity Model Integration) for Agile environments is a strategic approach that recognizes the unique characteristics of Agile methodologies while harnessing the structured process improvement capabilities of CMMI. In this adaptation, organizations embrace Agile's core values such as customer collaboration, responsiveness to change, and iterative development, while identifying the areas within CMMI that can support and enhance these principles. Agile's preference for working software over excessive documentation is met by streamlining documentation requirements, ensuring that any documentation created serves a meaningful purpose. Additionally, tailored metrics in Agile environments shift the focus towards velocity, burndown rates, and customer satisfaction, aligning more closely with Agile project goals and priorities. The synergy between Agile's iterative cycles and CMMI's process improvement cycles allows for continuous enhancements in Agile projects while maintaining the rigor of CMMI.
Moreover, effective tailoring encourages cross-functional collaboration between Agile teams and CMMI practitioners, fostering an environment where the strengths of both approaches are leveraged. This collaboration results in valuable insights, shared best practices, and a culture of ongoing process improvement. By documenting the tailoring decisions and promoting a culture of continuous improvement, organizations can ensure that their tailored CMMI-Agile framework remains flexible, adaptable, and aligned with the ever-evolving needs of Agile development projects. In essence, tailoring CMMI for Agile environments allows organizations to strike a harmonious balance between structured process improvement and the agile, customer-focused, and iterative nature of Agile methodologies, ultimately driving higher-quality outcomes in software development and project management.
Roles and Responsibilities in Agile CMMI Integration
-
Agile Coach:
-
Responsibilities: Guides Agile practices and helps teams understand how Agile aligns with CMMI.
-
-
CMMI Process Improvement Lead:
-
Responsibilities: Oversees CMMI process improvements and ensures they fit Agile environments.
-
-
Scrum Masters and Agile Team Members:
-
Responsibilities: Scrum Masters facilitate Agile processes, while team members adapt Agile practices for CMMI.
-
-
Product Owners and Business Analysts:
-
Responsibilities: Define and prioritize requirements, ensuring they align with Agile and CMMI standards.
-
-
Quality Assurance and Testing Specialists:
-
Responsibilities: Ensure product quality through testing, adapting to Agile iterations while following CMMI quality practices.
-
-
Project Managers or Release Managers:
-
Responsibilities: Oversee project or release planning, ensuring alignment with CMMI process areas.
-
-
Change Agents and Champions:
-
Responsibilities: Advocate for Agile CMMI integration, promote best practices, and encourage a culture of improvement.
-
-
Auditors and Assessors:
-
Responsibilities: Conduct CMMI assessments and audits to verify compliance and provide feedback for improvement.
-
Clear communication and collaboration among these roles are essential for successful Agile CMMI integration, enhancing the organization's ability to deliver high-quality products and services while maintaining Agile principles.
Measuring Agile Performance with CMMI Metrics
Measuring Agile performance with CMMI metrics is a strategic approach that bridges the gap between the Agile methodologies' iterative, customer-focused practices and CMMI's structured process improvement framework. These metrics provide organizations with valuable insights into their Agile processes, aligning them with CMMI's goals of efficiency, quality, and continuous improvement. Metrics such as velocity, cycle time, and burndown charts enable teams to monitor progress, identify bottlenecks, and optimize their workflow within the Agile framework. Customer satisfaction surveys and feedback response times ensure that Agile teams remain customer-centric, meeting the requirements of CMMI's customer focus. Additionally, defect density and work item aging metrics help maintain product quality while highlighting areas for improvement, aligning with CMMI's emphasis on quality management.
The integration of CMMI metrics into Agile environments promotes a culture of measurement and analysis, enabling organizations to make data-driven decisions. This not only enhances the organization's ability to deliver high-quality products and services but also ensures compliance with CMMI standards. Ultimately, measuring Agile performance with CMMI metrics empowers organizations to leverage the strengths of both approaches, fostering greater process maturity, efficiency, and customer satisfaction in Agile development and project management.
Agile CMMI Certification Levels
-
CMMI Maturity Levels: CMMI certification involves maturity levels, from Level 1 to Level 5, representing increasing process maturity and capability.
-
Agile Integration: Organizations can integrate Agile practices into these CMMI maturity levels to maintain flexibility while meeting CMMI requirements.
-
Certification Assessment: Certified appraisers or auditors assess an organization's processes, including the integration of Agile practices, to determine certification eligibility.
-
Tailored CMMI: Some organizations use tailored CMMI frameworks that provide specific guidance on incorporating Agile practices at different maturity levels.
-
Industry Requirements: Compliance with CMMI, Agile, or both may be necessary to meet industry standards and client expectations.
-
Consult Experts: Seek guidance from CMMI experts or certification authorities for the latest information and specific certification requirements related to Agile and CMMI integration.
Challenges in Integrating Agile and CMMI
-
Cultural Differences: Balancing Agile's flexibility with CMMI's structured approach can be a cultural challenge.
-
Documentation: Finding the right balance between extensive CMMI documentation and Agile's minimal documentation can be tricky.
-
Resistance to Change: Teams may resist shifting from traditional CMMI practices to Agile or adding perceived bureaucracy to Agile.
-
Mapping Practices: Aligning Agile practices with CMMI requirements and maturity levels requires careful mapping.
-
Process Tailoring: Customizing CMMI practices to fit Agile environments is challenging but necessary.
-
Metrics: Developing metrics that effectively measure performance in an integrated approach can be difficult.
-
Resource Allocation: Allocating resources for both Agile and CMMI efforts must be balanced.
-
Audit and Assessment: Preparing for CMMI assessments and audits in Agile settings requires planning.
-
Skills and Training: Ensuring that team members have the skills for the integrated approach is vital.
-
Sustainability: Maintaining the integration over time and preventing it from becoming a one-time effort is a challenge that requires ongoing commitment and adaptation.
Training and Skill Development for Agile CMMI
Training and skill development are fundamental pillars of achieving a successful integration of Agile and CMMI within an organization. In such an integrated environment, team members, leaders, and practitioners need a comprehensive understanding of both Agile methodologies and CMMI standards to effectively navigate the complexities of this hybrid approach. Initially, basic Agile training establishes a common foundation, fostering an understanding of Agile principles and practices, such as Scrum or Kanban. Concurrently, CMMI-specific training introduces the organization to the CMMI framework's concepts, maturity levels, and process areas.
The critical component lies in integration awareness, where dedicated training sessions and workshops enlighten participants about how Agile practices seamlessly align with CMMI goals while highlighting areas requiring adaptation. These sessions underscore the importance of tailoring CMMI processes to Agile settings, facilitating a smooth transition. Furthermore, training extends to leadership roles, equipping managers and executives with Agile leadership principles and the skills needed to support and lead in an Agile CMMI environment. Ultimately, a continuous learning culture, role-specific training, and feedback mechanisms ensure that individuals and teams stay agile in their approach to process improvement, product development, and compliance, thereby enhancing the organization's ability to excel in both agility and quality assurance.
Continuous Improvement in Agile CMMI
Continuous improvement in Agile CMMI environments represents an ongoing commitment to excellence in process, product, and service delivery. By seamlessly integrating Agile's iterative, customer-centric approach with CMMI's structured process improvement framework, organizations create a powerful engine for relentless enhancement. Agile retrospectives, data-driven decision-making, and Kaizen principles are instrumental in identifying and addressing areas for improvement at the team level. These practices dovetail with CMMI's emphasis on process optimization and quality assurance, resulting in a culture of constant self-assessment and refinement. Data collected through Agile practices, such as velocity and customer feedback, serves as a valuable input for CMMI-compliant measurement and analysis, further aligning the two methodologies.
Moreover, in Agile CMMI environments, continuous improvement extends beyond processes to encompass skill development and leadership support. By nurturing a culture of learning and adaptation, organizations empower their teams and leaders to stay agile in their approach to both product development and process maturity. The synergy between Agile's adaptability and CMMI's rigor creates an environment where innovation and efficiency thrive, ultimately enabling organizations to deliver high-quality products and services that meet customer needs while ensuring compliance with CMMI standards. Top of Form
Tools and Software for Agile CMMI Integration
Tools and software play a crucial role in facilitating the integration of Agile and CMMI methodologies within an organization. These tools bridge the gap between Agile's flexibility and CMMI's structured processes, aiding in the seamless coexistence of both approaches. Project management tools like Jira and Azure DevOps enable Agile teams to plan, track, and manage their work efficiently while accommodating CMMI process areas. Agile Lifecycle Management (ALM) tools such as VersionOne and Rally provide comprehensive support for Agile practices and can be customized to align with CMMI standards. Requirements management tools ensure traceability and compliance with CMMI requirements, while test management tools contribute to quality assurance, aligning with CMMI's focus on testing. Configuration management and version control tools help organizations meet CMMI's configuration management process area requirements. Collaboration and communication tools foster transparency and knowledge sharing among Agile teams, making it easier to document and communicate process improvements. Metrics and analytics tools enable organizations to collect and analyze data for both Agile and CMMI goals, facilitating data-driven process enhancements. DevOps and CI/CD tools automate and streamline development and deployment processes, aligning with CMMI's process automation practices. Specialized process improvement tools may also be employed to support the adoption and assessment of CMMI practices, ensuring continuous process maturity enhancements.
However, the success of these tools in Agile CMMI integration hinges on how they are configured, customized, and integrated into the organization's workflows. Additionally, tool selection should be based on the specific needs and objectives of Agile CMMI integration. The tools serve as enablers, helping organizations achieve the dual goals of delivering high-quality products or services through Agile practices while adhering to the structured process improvement framework of CMMI.
Audit and Assessment for Agile CMMI Certification
The audit and assessment process for Agile CMMI certification is a rigorous and comprehensive evaluation that determines an organization's adherence to both Agile methodologies and CMMI process improvement standards. The journey begins with careful preparation, where trained CMMI appraisers assess an organization's documentation, scrutinize Agile artifacts, and conduct a gap analysis to identify areas of alignment and potential deviations. On-site assessments involve in-depth interviews, observations, and artifact reviews to gauge how Agile practices are implemented in practice. Data collected during the assessment, including Agile-specific metrics and process performance, forms the basis for analysis, leading to documented findings and recommendations.
The ultimate goal of Agile CMMI certification is to demonstrate that an organization can balance the adaptability and customer-centricity of Agile with the structured process improvement focus of CMMI. The certification decision is made by an external body, based on the assessment results, and organizations may receive maturity or capability level ratings. Beyond certification, the process serves as a catalyst for ongoing improvement, as organizations develop action plans to address recommendations and engage in periodic follow-up assessments to ensure that the integrated Agile-CMMI framework remains effective and aligned with evolving goals. This holistic approach to assessment underscores the commitment to continuous improvement, quality, and process maturity in Agile development and project management.
Scaling Agile with CMMI
Scaling Agile with CMMI is a strategic approach that harmonizes the flexibility and customer-centricity of Agile methodologies with the structured process improvement framework of CMMI, allowing organizations to effectively manage larger and more complex projects and portfolios. This integration typically begins by selecting a suitable Agile scaling framework like SAFe or LeSS, which provides guidance on how to expand Agile practices while ensuring alignment with CMMI goals. Customization of the chosen framework is crucial to adapt CMMI process areas to Agile practices and vice versa, striking the right balance between Agile's adaptability and CMMI's process rigor.
Leadership support plays a pivotal role in fostering this integration, as leaders champion the effort, allocate necessary resources, and actively engage in aligning Agile and CMMI practices. Organizations must prioritize continuous improvement, regularly assessing the integration's effectiveness through metrics, feedback, and assessment processes. By promoting a culture of collaboration, providing training and skill development, and maintaining compliance with CMMI standards through periodic assessments, organizations can successfully scale Agile while achieving the desired levels of process maturity and product quality. The result is a dynamic and adaptable approach to project and product management that thrives in complex and evolving business landscapes.
Future Trends in Agile CMMI Integration
The future of Agile CMMI integration promises to be both dynamic and transformative, reflecting the ever-evolving landscape of software development and process improvement. One key trend is the increasing role of AI and automation in optimizing processes and decision-making. AI-driven tools will assist organizations in analyzing vast datasets, identifying patterns, and recommending improvements, making Agile CMMI integration more data-driven and efficient. Additionally, as Agile principles continue to resonate with organizations seeking agility and customer-centricity, scaling Agile practices beyond individual teams to the entire enterprise will remain a prominent trend. Frameworks like SAFe and LeSS will evolve to support larger and more complex organizations in their Agile journeys, allowing them to balance agility with the structured process improvement goals of CMMI.
Another critical trend is the integration of security and compliance practices into Agile CMMI environments. With cybersecurity concerns on the rise, organizations will work to harmonize Agile's rapid delivery with CMMI's focus on risk management and compliance, ensuring that security and regulatory requirements are seamlessly embedded into the development process. As remote and distributed work become increasingly prevalent, Agile CMMI integration will adapt to address the unique challenges of virtual collaboration and process adherence. This adaptability, along with a growing emphasis on cultural transformation, will be instrumental in organizations' efforts to foster a culture of innovation, collaboration, and continuous learning, ultimately driving successful Agile CMMI integration in the years to come.
How to obtain the CMMI certification?
We are an Education Technology company providing certification training courses to accelerate careers of working professionals worldwide. We impart training through instructor-led classroom workshops, instructor-led live virtual training sessions, and self-paced e-learning courses.
We have successfully conducted training sessions in 108 countries across the globe and enabled thousands of working professionals to enhance the scope of their careers.
Our enterprise training portfolio includes in-demand and globally recognized certification training courses in Project Management, Quality Management, Business Analysis, IT Service Management, Agile and Scrum, Cyber Security, Data Science, and Emerging Technologies. Download our Enterprise Training Catalog from https://www.icertglobal.com/corporate-training-for-enterprises.php
Popular Courses include:
-
Project Management: PMP, CAPM ,PMI RMP
-
Quality Management: Six Sigma Black Belt ,Lean Six Sigma Green Belt, Lean Management, Minitab ,CMMI
-
Business Analysis: CBAP, CCBA, ECBA
-
Agile Training: PMI-ACP
-
Scrum Training: CSM
-
DevOps
-
Program Management: PgMP
-
IT Service Management & Governance: COBIT, ISO
Conclusion
In conclusion, Agile CMMI integration represents a powerful approach for organizations seeking to balance the flexibility and customer-centricity of Agile methodologies with the structured process improvement framework of CMMI. This integration enables organizations to achieve high levels of process maturity while delivering high-quality products and services. The process involves careful customization of Agile practices and CMMI process areas, leadership support, continuous improvement efforts, and a commitment to aligning Agile and CMMI principles. As the business landscape evolves, the integration of Agile and CMMI will continue to adapt to meet new challenges and opportunities.
Future trends in Agile CMMI integration, including the use of AI, scaling Agile practices, and the integration of security and compliance, will shape the way organizations approach process improvement and Agile delivery. Cultural transformation and a focus on value stream management will also play critical roles in the success of Agile CMMI integration efforts. Overall, the integration of Agile and CMMI is a journey toward achieving process excellence and delivering exceptional value to customers, and it will remain a key strategy for organizations striving to excel in an ever-changing world.
Lean Methodology Essentials: A Guide with some Key Examples
Welcome to "Lean Methodology Essentials: A Guide with Examples." In a world where businesses must continually innovate, optimize, and adapt to remain competitive, Lean Methodology has emerged as a transformative approach to achieving operational excellence. This guide serves as your essential companion on a journey into the heart of Lean, offering a clear and practical understanding of its principles, techniques, and real-world applications.
Lean Methodology is more than a management philosophy; it's a mindset that emphasizes efficiency, waste reduction, and a relentless focus on delivering value to customers. In the pages that follow, we will break down the core tenets of Lean, demystify its terminology, and provide you with concrete examples that illustrate how Lean principles can be implemented across various industries. Whether you are a seasoned professional seeking to refine your Lean expertise or a newcomer eager to embrace its principles, this guide equips you with the knowledge and tools to embark on a journey of continuous improvement, setting you on the path to organizational excellence.
Table of Contents
-
What is Lean Methodology?
-
How Did Lean Methodology Originate?
-
Fundamentals of Lean Methodology
-
What Makes the Lean Methodology Unique?
-
Pillars of Lean Methodology
-
Why Should You Choose Lean Methodology?
-
Lean Methodology in Software Development
-
Lean Methodology Examples
-
Master the Concepts of Lean Methodology Today
-
Conclusion
What is Lean Methodology?
Lean Methodology is a systematic approach to process improvement that aims to maximize customer value while minimizing waste. Rooted in the principles of efficiency and continuous improvement, Lean emphasizes the identification and elimination of non-value-added activities, streamlining processes for smoother flow, adopting a pull system based on actual customer demand, and the relentless pursuit of perfection. By optimizing operations and reducing waste in industries ranging from manufacturing to healthcare and software development, Lean Methodology enhances quality, efficiency, and customer satisfaction, making it a cornerstone of modern business improvement strategies.
How Did Lean Methodology Originate?
Lean Methodology, originating in post-World War II Japan, owes its genesis to the innovative response of Japanese manufacturers, particularly Toyota, to the challenging economic environment of the time. Scarce resources, a damaged infrastructure, and a competitive landscape compelled Japanese companies to devise more efficient and economical production methods. Central to Lean's origins is the Toyota Production System (TPS), developed by Taiichi Ohno and Shigeo Shingo in the mid-20th century. TPS emphasized core Lean principles such as Just-In-Time (JIT) production, which aimed to reduce waste by producing only what was needed when it was needed. Another foundational concept was continuous improvement (Kaizen), which encouraged ongoing refinement of processes to enhance efficiency and quality. This systematic approach revolutionized manufacturing by minimizing waste, optimizing resource utilization, and improving product quality.
The adoption of Lean principles extended beyond manufacturing and became a global phenomenon in the late 20th century as Western companies recognized its effectiveness in improving operational efficiency and product quality. Lean's success in industries such as automotive manufacturing led to its widespread application across various sectors, including healthcare, services, and software development. Lean's ability to adapt and deliver results in diverse fields is a testament to its universal appeal and the enduring legacy of its Japanese origins, which continue to shape modern approaches to process optimization and waste reduction.
Fundamentals of Lean Methodology
The fundamentals of Lean Methodology are rooted in a set of core principles and practices that aim to maximize value while minimizing waste. These principles guide organizations in their pursuit of operational excellence and continuous improvement. Here are the key fundamentals of Lean Methodology:
-
Value: Identify what is valuable from the customer's perspective. Value represents any activity or process step that directly contributes to meeting customer needs or requirements.
-
Value Stream Mapping: Analyze and map the entire value stream, which is the end-to-end sequence of activities and processes that deliver a product or service to the customer. Value stream mapping helps identify bottlenecks, inefficiencies, and areas of waste.
-
Flow: Optimize the flow of work or materials through the value stream. This involves reducing interruptions, delays, and excess inventory that can hinder the smooth progression of tasks. Creating a continuous flow is a key objective.
-
Pull: Implement a pull system, where work is initiated or products are produced based on actual customer demand. This contrasts with a push system, where items are produced in anticipation of demand, often leading to overproduction and waste.
-
Perfection: Embrace a culture of continuous improvement (Kaizen) with the goal of achieving perfection, even though it may never be fully attainable. Continuously seek ways to eliminate waste, enhance processes, and deliver greater value to customers.
-
Customer Focus: Place the customer at the center of all decisions and activities. Understand customer needs and preferences to drive value creation.
-
Employee Involvement: Involve and empower employees at all levels of the organization to identify and solve problems, make improvements, and contribute to the Lean culture.
-
Standardization: Establish standardized work processes and procedures to ensure consistency, reduce variation, and enable easier identification of abnormalities.
-
Visual Management: Use visual cues and tools, such as Kanban boards and Andon systems, to make information and the status of processes readily visible, facilitating better communication and decision-making.
-
Waste Reduction: Identify and eliminate the eight types of waste in Lean, often remembered by the acronym "TIMWOODS":
-
Transportation
-
Inventory
-
Motion
-
Waiting
-
Overproduction
-
Overprocessing
-
Defects
-
Skills (underutilized)
-
Continuous Improvement: Promote a culture of continuous learning and improvement. Encourage teams to regularly assess processes, gather feedback, and make incremental changes to enhance efficiency and quality.
-
Respect for People: Recognize the value of every employee and treat them with respect. Lean encourages collaboration, teamwork, and the involvement of employees in decision-making.
By adhering to these fundamentals, organizations can achieve greater efficiency, improved quality, reduced costs, and increased customer satisfaction, making Lean Methodology a powerful approach for achieving operational excellence.
What Makes the Lean Methodology Unique?
The Lean Methodology is distinctive due to several key factors:
-
Customer-Centric Philosophy: Lean is fundamentally centered on delivering value to the customer. It places a primary focus on understanding and meeting customer needs, which drives all decision-making and process improvements.
-
Waste Elimination: A core principle of Lean is the systematic identification and elimination of waste in all forms, including overproduction, unnecessary inventory, defects, waiting times, and more. This relentless pursuit of waste reduction sets Lean apart from many other methodologies.
-
Continuous Improvement Culture: Lean fosters a culture of continuous improvement (Kaizen) throughout an organization. It encourages employees at all levels to continuously seek ways to enhance processes, products, and services, leading to ongoing innovation and optimization.
-
Pull System: Lean employs a pull system where work is initiated based on actual customer demand rather than pushing products or services onto the market. This minimizes overproduction and excess inventory, reducing waste and improving efficiency.
-
Visual Management: Lean uses visual tools like Kanban boards and Andon systems to make information and process status highly visible. This transparency enhances communication, problem-solving, and decision-making.
-
Respect for People: Lean places a strong emphasis on respecting and engaging employees. It recognizes that employees often hold valuable insights for process improvement and encourages their active participation in decision-making.
-
Standardization and Documentation: Lean promotes the development and documentation of standardized work processes and procedures. This ensures consistency, reduces variation, and simplifies problem identification and resolution.
-
Flow Optimization: Lean focuses on optimizing the flow of work or materials through a value stream. This minimizes interruptions, delays, and inefficiencies, creating a smoother and more efficient workflow.
-
Pursuit of Perfection: While perfection may be an aspirational goal, Lean embraces the concept as a continuous improvement objective. Organizations continually strive for higher levels of efficiency, quality, and customer satisfaction.
-
Global Applicability: Lean has transcended its origins in Japan and has been successfully applied across industries and geographies, demonstrating its universal applicability and effectiveness.
In summary, the Lean Methodology's unique characteristics include its customer-centricity, waste reduction focus, commitment to continuous improvement, pull-based systems, visual management practices, respect for people, and adaptability to various contexts. These features have contributed to Lean's widespread adoption and its reputation for driving efficiency, quality, and competitiveness in organizations worldwide.
Pillars of Lean Methodology
The "pillars" of Lean Methodology typically refer to the foundational principles and concepts that underpin the Lean approach to process improvement and waste reduction. While there isn't a universal agreement on a fixed set of pillars, the following are commonly recognized as the core pillars of Lean Methodology:
-
Value: Understanding and defining value from the customer's perspective is the first pillar of Lean. Value represents any activity or process step that directly contributes to meeting customer needs or requirements. Everything else is considered waste.
-
Value Stream Mapping: This pillar involves analyzing and mapping the entire value stream, which is the sequence of activities and processes that deliver a product or service to the customer. Value stream mapping helps identify bottlenecks, inefficiencies, and areas of waste.
-
Flow: The flow pillar emphasizes optimizing the flow of work or materials through the value stream. It aims to reduce interruptions, delays, and excess inventory that can impede the smooth progression of tasks.
-
Pull: The pull pillar involves implementing a pull system where work is initiated or products are produced based on actual customer demand. This contrasts with push systems, which produce items in anticipation of demand, often leading to overproduction and waste.
-
Perfection: Perfection is the continuous improvement pillar of Lean. While perfection may be an unattainable ideal, Lean encourages organizations to relentlessly pursue it by continuously seeking ways to eliminate waste, improve processes, and deliver greater value to customers.
These five pillars are often represented as the foundation of Lean Thinking and provide the guiding principles for organizations to achieve greater efficiency, reduce waste, and enhance customer satisfaction. Additional concepts and tools, such as standardized work, visual management, and respect for people, are integrated into Lean practices to support these pillars and drive continuous improvement.
Why Should You Choose Lean Methodology?
Choosing Lean Methodology is a strategic decision for organizations seeking to thrive in today's competitive landscape. Lean's central focus on waste reduction, coupled with a relentless commitment to improving processes and delivering customer value, positions companies for sustainable success. By minimizing non-value-added activities, Lean enhances efficiency, reduces costs, and bolsters quality. It fosters a culture of continuous improvement, empowering employees at all levels to identify and address operational inefficiencies, ultimately driving innovation and adaptability. Lean is not confined to a specific industry, making it versatile and adaptable to diverse organizational contexts, from manufacturing to healthcare, services, and software development. Its global recognition and proven track record of delivering tangible results underscore its status as a transformative methodology for organizations striving to achieve operational excellence, customer satisfaction, and a competitive edge.
Lean Methodology in Software Development
Lean Methodology, when applied to software development, is often referred to as "Lean Software Development." It adapts the principles and practices of Lean thinking to the unique challenges of creating software products and managing software projects. Here are key aspects of Lean Software Development:
-
Customer Value: Lean Software Development starts by identifying and prioritizing customer value. It involves understanding user needs and focusing on features or functionalities that directly contribute to customer satisfaction and business goals.
-
Eliminating Waste: Lean principles of waste reduction are applied rigorously in software development. This includes reducing unnecessary code complexity, eliminating duplication, and avoiding overproduction of features that may not be needed.
-
Pull System: Lean Software Development often employs a pull system, where features or tasks are pulled into the development process based on real customer demand or project priorities. This prevents overloading teams with excessive work.
-
Continuous Improvement: Like other Lean applications, Lean Software Development encourages continuous improvement. Teams regularly review their processes and seek ways to streamline workflows, enhance collaboration, and reduce cycle times.
-
Small Batch Sizes: Lean promotes working in small, manageable batches. This means breaking down large projects into smaller, deliverable units, allowing for quicker feedback and adjustment.
-
Visual Management: Visual tools like Kanban boards are frequently used to make the status of work visible, helping teams track progress, identify bottlenecks, and manage their work effectively.
-
Lean Metrics: Lean Software Development relies on key performance indicators (KPIs) that measure the flow of work, cycle times, and other relevant metrics to identify areas for improvement.
-
Empowering Teams: Lean principles emphasize giving teams autonomy and responsibility. Teams are encouraged to self-organize, make decisions, and take ownership of their work.
-
Minimal Viable Product (MVP): Lean encourages the development of Minimum Viable Products that can be quickly delivered to customers for feedback. This iterative approach allows for faster learning and adaptation.
-
Customer Feedback Loop: Lean Software Development relies on frequent customer feedback to validate assumptions, refine requirements, and make course corrections. This feedback loop is essential for delivering software that aligns with customer expectations.
-
Respect for People: As with all Lean applications, Lean Software Development places a strong emphasis on respecting and valuing the contributions of team members, recognizing that they are essential to the success of the project.
By applying Lean principles to software development, organizations can achieve greater efficiency, reduce the risk of building unnecessary features, and deliver software products that align more closely with customer needs. It's an adaptable and effective approach that has gained popularity in Agile development methodologies, such as Scrum and Kanban, which incorporate Lean principles to varying degrees.
Lean Methodology Examples
Lean Methodology is applied across various industries and functions to optimize processes, reduce waste, and enhance overall efficiency. Here are some examples of Lean Methodology in action:
-
Manufacturing:
-
Toyota Production System (TPS): Toyota is often credited as the originator of Lean principles. TPS emphasizes Just-In-Time (JIT) production, pull systems, and continuous improvement to minimize waste, reduce inventory, and enhance production efficiency.
-
Healthcare:
-
Reducing Patient Wait Times: Lean principles have been applied in hospitals to reduce patient wait times, optimize appointment scheduling, and improve the efficiency of healthcare delivery.
-
Software Development:
-
Kanban: Software development teams often use Kanban boards to visualize and manage their work, limit work in progress (WIP), and optimize workflow processes.
-
Service Industry:
-
Lean Banking: Banks have applied Lean principles to streamline processes such as loan approvals, customer service, and account management, reducing wait times and improving customer satisfaction.
-
Supply Chain Management:
-
Lean Supply Chain: Organizations apply Lean principles to supply chain management to reduce excess inventory, eliminate bottlenecks, and improve overall supply chain efficiency.
-
Retail:
-
Inventory Management: Retailers use Lean principles to optimize inventory management, reducing carrying costs, minimizing stockouts, and ensuring products are available when customers need them.
-
Education:
-
Lean Education: Lean principles have been adapted to education to improve classroom processes, curriculum development, and administrative tasks, resulting in more efficient and effective educational institutions.
-
Construction:
-
Lean Construction: The construction industry has adopted Lean principles to optimize project planning, reduce project delays, eliminate waste, and enhance overall project management.
-
Aerospace and Aviation:
-
Lean Aerospace: Companies in the aerospace and aviation sectors use Lean principles to improve manufacturing processes, reduce production lead times, and increase aircraft production efficiency.
-
Food Industry:
-
Lean in Restaurants: Restaurants have implemented Lean practices to optimize kitchen processes, reduce food waste, and improve customer service.
-
Government:
-
Lean Government: Some government agencies have adopted Lean principles to streamline administrative processes, reduce paperwork, and enhance citizen services.
-
Small Businesses:
-
Lean Startup: Small businesses and startups often use Lean principles to validate business ideas, develop minimal viable products (MVPs), and iterate based on customer feedback.
Master the Concepts of Lean Methodology Today
Mastering the concepts of Lean Methodology requires a combination of study, practical application, and continuous learning. Here's a step-by-step guide to help you get started:
-
Study Lean Principles:
-
Begin by reading books and articles on Lean Methodology to understand its core principles and concepts. Some recommended books include "The Lean Startup" by Eric Ries and "Lean Thinking" by James P. Womack and Daniel T. Jones.
-
Enroll in Lean Training:
-
Consider enrolling in Lean training programs or workshops offered by accredited organizations. These programs provide structured learning and often include real-world case studies and exercises.
-
Online Courses and Tutorials:
-
Many online platforms offer free and paid courses on Lean Methodology. Websites like Coursera, edX, and LinkedIn Learning provide access to comprehensive courses on Lean principles and their application.
-
Certification:
-
If you're looking to establish your expertise, consider pursuing Lean certification. Organizations like the Lean Enterprise Institute (LEI) offer certification programs, including Lean Green Belt and Lean Black Belt certifications.
-
Practice Lean Tools and Techniques:
-
To truly understand Lean, apply its tools and techniques in real-world scenarios. Implement practices like value stream mapping, Kanban, and 5S in your workplace or personal projects.
-
Join Lean Communities:
-
Participate in Lean forums, online communities, and social media groups. Engaging with Lean practitioners and enthusiasts can provide valuable insights and opportunities for discussion.
-
Read Case Studies:
-
Read case studies and success stories of organizations that have effectively implemented Lean Methodology. Analyze their experiences and learn from their challenges and solutions.
-
Continuous Improvement:
-
Embrace the Lean philosophy of continuous improvement. Regularly assess your own processes and workflows, and apply Lean principles to make incremental enhancements.
-
Lean Workshops and Seminars:
-
Attend Lean workshops, seminars, and conferences to gain exposure to the latest developments in Lean Methodology and learn from industry experts.
-
Teach Others:
-
Teaching Lean concepts to others can deepen your own understanding. Consider sharing your knowledge through presentations, workshops, or writing articles or blog posts.
-
Problem-Solving Practice:
-
Lean is fundamentally about problem-solving. Practice structured problem-solving techniques like the PDCA (Plan-Do-Check-Act) cycle to address challenges effectively.
-
Stay Informed:
-
Stay updated on Lean trends, research, and best practices through books, journals, blogs, and industry publications.
-
Networking:
-
Build a network of Lean professionals and mentors who can offer guidance and support in your Lean journey.
-
Apply Lean to Your Life:
-
Extend Lean principles beyond the workplace. Apply them to personal projects, time management, and daily routines to enhance your problem-solving skills and efficiency.
Remember that mastering Lean Methodology is an ongoing process. It requires a commitment to continuous learning, experimentation, and the application of Lean principles in various contexts. As you gain experience and expertise, you'll be better equipped to drive operational excellence and improve processes in your organization or projects.
How to obtain the Lean Six Sigma Green Belt certification?
We are an Education Technology company providing certification training courses to accelerate careers of working professionals worldwide. We impart training through instructor-led classroom workshops, instructor-led live virtual training sessions, and self-paced e-learning courses.
We have successfully conducted training sessions in 108 countries across the globe and enabled thousands of working professionals to enhance the scope of their careers.
Our enterprise training portfolio includes in-demand and globally recognized certification training courses in Project Management, Quality Management, Business Analysis, IT Service Management, Agile and Scrum, Cyber Security, Data Science, and Emerging Technologies. Download our Enterprise Training Catalog from https://www.icertglobal.com/corporate-training-for-enterprises.php
Popular Courses include:
-
Project Management: PMP, CAPM ,PMI RMP
-
Quality Management: Six Sigma Green Belt ,Lean Six Sigma Green Belt, Lean Six Sigma Black Belt
-
Business Analysis: CBAP, CCBA, ECBA
-
Agile Training: PMI-ACP
-
Scrum Training: CSM
-
DevOps
-
Program Management: PgMP
-
IT Service Management & Governance: COBIT, ISO
Conclusion
In conclusion, the fundamentals of Lean Methodology represent a powerful framework for organizations seeking to thrive in today's dynamic and competitive landscape. By understanding and applying the principles of value, waste reduction, continuous improvement, and customer-centricity, businesses can unlock remarkable benefits. The real-world examples showcased in this blog highlight the versatility of Lean, demonstrating its effectiveness across diverse industries, from manufacturing and healthcare to software development and services.
As we wrap up our exploration of Lean, it's important to remember that Lean is not a one-time initiative but a journey of ongoing improvement. Embracing a Lean mindset, fostering a culture of innovation, and empowering employees to identify and eliminate waste are essential for sustained success. By integrating Lean into the DNA of your organization, you can optimize processes, reduce costs, enhance quality, and ultimately deliver greater value to your customers, setting the stage for a prosperous and efficient future.
Read More
Welcome to "Lean Methodology Essentials: A Guide with Examples." In a world where businesses must continually innovate, optimize, and adapt to remain competitive, Lean Methodology has emerged as a transformative approach to achieving operational excellence. This guide serves as your essential companion on a journey into the heart of Lean, offering a clear and practical understanding of its principles, techniques, and real-world applications.
Lean Methodology is more than a management philosophy; it's a mindset that emphasizes efficiency, waste reduction, and a relentless focus on delivering value to customers. In the pages that follow, we will break down the core tenets of Lean, demystify its terminology, and provide you with concrete examples that illustrate how Lean principles can be implemented across various industries. Whether you are a seasoned professional seeking to refine your Lean expertise or a newcomer eager to embrace its principles, this guide equips you with the knowledge and tools to embark on a journey of continuous improvement, setting you on the path to organizational excellence.
Table of Contents
-
What is Lean Methodology?
-
How Did Lean Methodology Originate?
-
Fundamentals of Lean Methodology
-
What Makes the Lean Methodology Unique?
-
Pillars of Lean Methodology
-
Why Should You Choose Lean Methodology?
-
Lean Methodology in Software Development
-
Lean Methodology Examples
-
Master the Concepts of Lean Methodology Today
-
Conclusion
What is Lean Methodology?
Lean Methodology is a systematic approach to process improvement that aims to maximize customer value while minimizing waste. Rooted in the principles of efficiency and continuous improvement, Lean emphasizes the identification and elimination of non-value-added activities, streamlining processes for smoother flow, adopting a pull system based on actual customer demand, and the relentless pursuit of perfection. By optimizing operations and reducing waste in industries ranging from manufacturing to healthcare and software development, Lean Methodology enhances quality, efficiency, and customer satisfaction, making it a cornerstone of modern business improvement strategies.
How Did Lean Methodology Originate?
Lean Methodology, originating in post-World War II Japan, owes its genesis to the innovative response of Japanese manufacturers, particularly Toyota, to the challenging economic environment of the time. Scarce resources, a damaged infrastructure, and a competitive landscape compelled Japanese companies to devise more efficient and economical production methods. Central to Lean's origins is the Toyota Production System (TPS), developed by Taiichi Ohno and Shigeo Shingo in the mid-20th century. TPS emphasized core Lean principles such as Just-In-Time (JIT) production, which aimed to reduce waste by producing only what was needed when it was needed. Another foundational concept was continuous improvement (Kaizen), which encouraged ongoing refinement of processes to enhance efficiency and quality. This systematic approach revolutionized manufacturing by minimizing waste, optimizing resource utilization, and improving product quality.
The adoption of Lean principles extended beyond manufacturing and became a global phenomenon in the late 20th century as Western companies recognized its effectiveness in improving operational efficiency and product quality. Lean's success in industries such as automotive manufacturing led to its widespread application across various sectors, including healthcare, services, and software development. Lean's ability to adapt and deliver results in diverse fields is a testament to its universal appeal and the enduring legacy of its Japanese origins, which continue to shape modern approaches to process optimization and waste reduction.
Fundamentals of Lean Methodology
The fundamentals of Lean Methodology are rooted in a set of core principles and practices that aim to maximize value while minimizing waste. These principles guide organizations in their pursuit of operational excellence and continuous improvement. Here are the key fundamentals of Lean Methodology:
-
Value: Identify what is valuable from the customer's perspective. Value represents any activity or process step that directly contributes to meeting customer needs or requirements.
-
Value Stream Mapping: Analyze and map the entire value stream, which is the end-to-end sequence of activities and processes that deliver a product or service to the customer. Value stream mapping helps identify bottlenecks, inefficiencies, and areas of waste.
-
Flow: Optimize the flow of work or materials through the value stream. This involves reducing interruptions, delays, and excess inventory that can hinder the smooth progression of tasks. Creating a continuous flow is a key objective.
-
Pull: Implement a pull system, where work is initiated or products are produced based on actual customer demand. This contrasts with a push system, where items are produced in anticipation of demand, often leading to overproduction and waste.
-
Perfection: Embrace a culture of continuous improvement (Kaizen) with the goal of achieving perfection, even though it may never be fully attainable. Continuously seek ways to eliminate waste, enhance processes, and deliver greater value to customers.
-
Customer Focus: Place the customer at the center of all decisions and activities. Understand customer needs and preferences to drive value creation.
-
Employee Involvement: Involve and empower employees at all levels of the organization to identify and solve problems, make improvements, and contribute to the Lean culture.
-
Standardization: Establish standardized work processes and procedures to ensure consistency, reduce variation, and enable easier identification of abnormalities.
-
Visual Management: Use visual cues and tools, such as Kanban boards and Andon systems, to make information and the status of processes readily visible, facilitating better communication and decision-making.
-
Waste Reduction: Identify and eliminate the eight types of waste in Lean, often remembered by the acronym "TIMWOODS":
-
Transportation
-
Inventory
-
Motion
-
Waiting
-
Overproduction
-
Overprocessing
-
Defects
-
Skills (underutilized)
-
-
Continuous Improvement: Promote a culture of continuous learning and improvement. Encourage teams to regularly assess processes, gather feedback, and make incremental changes to enhance efficiency and quality.
-
Respect for People: Recognize the value of every employee and treat them with respect. Lean encourages collaboration, teamwork, and the involvement of employees in decision-making.
By adhering to these fundamentals, organizations can achieve greater efficiency, improved quality, reduced costs, and increased customer satisfaction, making Lean Methodology a powerful approach for achieving operational excellence.
What Makes the Lean Methodology Unique?
The Lean Methodology is distinctive due to several key factors:
-
Customer-Centric Philosophy: Lean is fundamentally centered on delivering value to the customer. It places a primary focus on understanding and meeting customer needs, which drives all decision-making and process improvements.
-
Waste Elimination: A core principle of Lean is the systematic identification and elimination of waste in all forms, including overproduction, unnecessary inventory, defects, waiting times, and more. This relentless pursuit of waste reduction sets Lean apart from many other methodologies.
-
Continuous Improvement Culture: Lean fosters a culture of continuous improvement (Kaizen) throughout an organization. It encourages employees at all levels to continuously seek ways to enhance processes, products, and services, leading to ongoing innovation and optimization.
-
Pull System: Lean employs a pull system where work is initiated based on actual customer demand rather than pushing products or services onto the market. This minimizes overproduction and excess inventory, reducing waste and improving efficiency.
-
Visual Management: Lean uses visual tools like Kanban boards and Andon systems to make information and process status highly visible. This transparency enhances communication, problem-solving, and decision-making.
-
Respect for People: Lean places a strong emphasis on respecting and engaging employees. It recognizes that employees often hold valuable insights for process improvement and encourages their active participation in decision-making.
-
Standardization and Documentation: Lean promotes the development and documentation of standardized work processes and procedures. This ensures consistency, reduces variation, and simplifies problem identification and resolution.
-
Flow Optimization: Lean focuses on optimizing the flow of work or materials through a value stream. This minimizes interruptions, delays, and inefficiencies, creating a smoother and more efficient workflow.
-
Pursuit of Perfection: While perfection may be an aspirational goal, Lean embraces the concept as a continuous improvement objective. Organizations continually strive for higher levels of efficiency, quality, and customer satisfaction.
-
Global Applicability: Lean has transcended its origins in Japan and has been successfully applied across industries and geographies, demonstrating its universal applicability and effectiveness.
In summary, the Lean Methodology's unique characteristics include its customer-centricity, waste reduction focus, commitment to continuous improvement, pull-based systems, visual management practices, respect for people, and adaptability to various contexts. These features have contributed to Lean's widespread adoption and its reputation for driving efficiency, quality, and competitiveness in organizations worldwide.
Pillars of Lean Methodology
The "pillars" of Lean Methodology typically refer to the foundational principles and concepts that underpin the Lean approach to process improvement and waste reduction. While there isn't a universal agreement on a fixed set of pillars, the following are commonly recognized as the core pillars of Lean Methodology:
-
Value: Understanding and defining value from the customer's perspective is the first pillar of Lean. Value represents any activity or process step that directly contributes to meeting customer needs or requirements. Everything else is considered waste.
-
Value Stream Mapping: This pillar involves analyzing and mapping the entire value stream, which is the sequence of activities and processes that deliver a product or service to the customer. Value stream mapping helps identify bottlenecks, inefficiencies, and areas of waste.
-
Flow: The flow pillar emphasizes optimizing the flow of work or materials through the value stream. It aims to reduce interruptions, delays, and excess inventory that can impede the smooth progression of tasks.
-
Pull: The pull pillar involves implementing a pull system where work is initiated or products are produced based on actual customer demand. This contrasts with push systems, which produce items in anticipation of demand, often leading to overproduction and waste.
-
Perfection: Perfection is the continuous improvement pillar of Lean. While perfection may be an unattainable ideal, Lean encourages organizations to relentlessly pursue it by continuously seeking ways to eliminate waste, improve processes, and deliver greater value to customers.
These five pillars are often represented as the foundation of Lean Thinking and provide the guiding principles for organizations to achieve greater efficiency, reduce waste, and enhance customer satisfaction. Additional concepts and tools, such as standardized work, visual management, and respect for people, are integrated into Lean practices to support these pillars and drive continuous improvement.
Why Should You Choose Lean Methodology?
Choosing Lean Methodology is a strategic decision for organizations seeking to thrive in today's competitive landscape. Lean's central focus on waste reduction, coupled with a relentless commitment to improving processes and delivering customer value, positions companies for sustainable success. By minimizing non-value-added activities, Lean enhances efficiency, reduces costs, and bolsters quality. It fosters a culture of continuous improvement, empowering employees at all levels to identify and address operational inefficiencies, ultimately driving innovation and adaptability. Lean is not confined to a specific industry, making it versatile and adaptable to diverse organizational contexts, from manufacturing to healthcare, services, and software development. Its global recognition and proven track record of delivering tangible results underscore its status as a transformative methodology for organizations striving to achieve operational excellence, customer satisfaction, and a competitive edge.
Lean Methodology in Software Development
Lean Methodology, when applied to software development, is often referred to as "Lean Software Development." It adapts the principles and practices of Lean thinking to the unique challenges of creating software products and managing software projects. Here are key aspects of Lean Software Development:
-
Customer Value: Lean Software Development starts by identifying and prioritizing customer value. It involves understanding user needs and focusing on features or functionalities that directly contribute to customer satisfaction and business goals.
-
Eliminating Waste: Lean principles of waste reduction are applied rigorously in software development. This includes reducing unnecessary code complexity, eliminating duplication, and avoiding overproduction of features that may not be needed.
-
Pull System: Lean Software Development often employs a pull system, where features or tasks are pulled into the development process based on real customer demand or project priorities. This prevents overloading teams with excessive work.
-
Continuous Improvement: Like other Lean applications, Lean Software Development encourages continuous improvement. Teams regularly review their processes and seek ways to streamline workflows, enhance collaboration, and reduce cycle times.
-
Small Batch Sizes: Lean promotes working in small, manageable batches. This means breaking down large projects into smaller, deliverable units, allowing for quicker feedback and adjustment.
-
Visual Management: Visual tools like Kanban boards are frequently used to make the status of work visible, helping teams track progress, identify bottlenecks, and manage their work effectively.
-
Lean Metrics: Lean Software Development relies on key performance indicators (KPIs) that measure the flow of work, cycle times, and other relevant metrics to identify areas for improvement.
-
Empowering Teams: Lean principles emphasize giving teams autonomy and responsibility. Teams are encouraged to self-organize, make decisions, and take ownership of their work.
-
Minimal Viable Product (MVP): Lean encourages the development of Minimum Viable Products that can be quickly delivered to customers for feedback. This iterative approach allows for faster learning and adaptation.
-
Customer Feedback Loop: Lean Software Development relies on frequent customer feedback to validate assumptions, refine requirements, and make course corrections. This feedback loop is essential for delivering software that aligns with customer expectations.
-
Respect for People: As with all Lean applications, Lean Software Development places a strong emphasis on respecting and valuing the contributions of team members, recognizing that they are essential to the success of the project.
By applying Lean principles to software development, organizations can achieve greater efficiency, reduce the risk of building unnecessary features, and deliver software products that align more closely with customer needs. It's an adaptable and effective approach that has gained popularity in Agile development methodologies, such as Scrum and Kanban, which incorporate Lean principles to varying degrees.
Lean Methodology Examples
Lean Methodology is applied across various industries and functions to optimize processes, reduce waste, and enhance overall efficiency. Here are some examples of Lean Methodology in action:
-
Manufacturing:
-
Toyota Production System (TPS): Toyota is often credited as the originator of Lean principles. TPS emphasizes Just-In-Time (JIT) production, pull systems, and continuous improvement to minimize waste, reduce inventory, and enhance production efficiency.
-
-
Healthcare:
-
Reducing Patient Wait Times: Lean principles have been applied in hospitals to reduce patient wait times, optimize appointment scheduling, and improve the efficiency of healthcare delivery.
-
-
Software Development:
-
Kanban: Software development teams often use Kanban boards to visualize and manage their work, limit work in progress (WIP), and optimize workflow processes.
-
-
Service Industry:
-
Lean Banking: Banks have applied Lean principles to streamline processes such as loan approvals, customer service, and account management, reducing wait times and improving customer satisfaction.
-
-
Supply Chain Management:
-
Lean Supply Chain: Organizations apply Lean principles to supply chain management to reduce excess inventory, eliminate bottlenecks, and improve overall supply chain efficiency.
-
-
Retail:
-
Inventory Management: Retailers use Lean principles to optimize inventory management, reducing carrying costs, minimizing stockouts, and ensuring products are available when customers need them.
-
-
Education:
-
Lean Education: Lean principles have been adapted to education to improve classroom processes, curriculum development, and administrative tasks, resulting in more efficient and effective educational institutions.
-
-
Construction:
-
Lean Construction: The construction industry has adopted Lean principles to optimize project planning, reduce project delays, eliminate waste, and enhance overall project management.
-
-
Aerospace and Aviation:
-
Lean Aerospace: Companies in the aerospace and aviation sectors use Lean principles to improve manufacturing processes, reduce production lead times, and increase aircraft production efficiency.
-
-
Food Industry:
-
Lean in Restaurants: Restaurants have implemented Lean practices to optimize kitchen processes, reduce food waste, and improve customer service.
-
-
Government:
-
Lean Government: Some government agencies have adopted Lean principles to streamline administrative processes, reduce paperwork, and enhance citizen services.
-
-
Small Businesses:
-
Lean Startup: Small businesses and startups often use Lean principles to validate business ideas, develop minimal viable products (MVPs), and iterate based on customer feedback.
-
Master the Concepts of Lean Methodology Today
Mastering the concepts of Lean Methodology requires a combination of study, practical application, and continuous learning. Here's a step-by-step guide to help you get started:
-
Study Lean Principles:
-
Begin by reading books and articles on Lean Methodology to understand its core principles and concepts. Some recommended books include "The Lean Startup" by Eric Ries and "Lean Thinking" by James P. Womack and Daniel T. Jones.
-
-
Enroll in Lean Training:
-
Consider enrolling in Lean training programs or workshops offered by accredited organizations. These programs provide structured learning and often include real-world case studies and exercises.
-
-
Online Courses and Tutorials:
-
Many online platforms offer free and paid courses on Lean Methodology. Websites like Coursera, edX, and LinkedIn Learning provide access to comprehensive courses on Lean principles and their application.
-
-
Certification:
-
If you're looking to establish your expertise, consider pursuing Lean certification. Organizations like the Lean Enterprise Institute (LEI) offer certification programs, including Lean Green Belt and Lean Black Belt certifications.
-
-
Practice Lean Tools and Techniques:
-
To truly understand Lean, apply its tools and techniques in real-world scenarios. Implement practices like value stream mapping, Kanban, and 5S in your workplace or personal projects.
-
-
Join Lean Communities:
-
Participate in Lean forums, online communities, and social media groups. Engaging with Lean practitioners and enthusiasts can provide valuable insights and opportunities for discussion.
-
-
Read Case Studies:
-
Read case studies and success stories of organizations that have effectively implemented Lean Methodology. Analyze their experiences and learn from their challenges and solutions.
-
-
Continuous Improvement:
-
Embrace the Lean philosophy of continuous improvement. Regularly assess your own processes and workflows, and apply Lean principles to make incremental enhancements.
-
-
Lean Workshops and Seminars:
-
Attend Lean workshops, seminars, and conferences to gain exposure to the latest developments in Lean Methodology and learn from industry experts.
-
-
Teach Others:
-
Teaching Lean concepts to others can deepen your own understanding. Consider sharing your knowledge through presentations, workshops, or writing articles or blog posts.
-
-
Problem-Solving Practice:
-
Lean is fundamentally about problem-solving. Practice structured problem-solving techniques like the PDCA (Plan-Do-Check-Act) cycle to address challenges effectively.
-
-
Stay Informed:
-
Stay updated on Lean trends, research, and best practices through books, journals, blogs, and industry publications.
-
-
Networking:
-
Build a network of Lean professionals and mentors who can offer guidance and support in your Lean journey.
-
-
Apply Lean to Your Life:
-
Extend Lean principles beyond the workplace. Apply them to personal projects, time management, and daily routines to enhance your problem-solving skills and efficiency.
-
Remember that mastering Lean Methodology is an ongoing process. It requires a commitment to continuous learning, experimentation, and the application of Lean principles in various contexts. As you gain experience and expertise, you'll be better equipped to drive operational excellence and improve processes in your organization or projects.
How to obtain the Lean Six Sigma Green Belt certification?
We are an Education Technology company providing certification training courses to accelerate careers of working professionals worldwide. We impart training through instructor-led classroom workshops, instructor-led live virtual training sessions, and self-paced e-learning courses.
We have successfully conducted training sessions in 108 countries across the globe and enabled thousands of working professionals to enhance the scope of their careers.
Our enterprise training portfolio includes in-demand and globally recognized certification training courses in Project Management, Quality Management, Business Analysis, IT Service Management, Agile and Scrum, Cyber Security, Data Science, and Emerging Technologies. Download our Enterprise Training Catalog from https://www.icertglobal.com/corporate-training-for-enterprises.php
Popular Courses include:
-
Project Management: PMP, CAPM ,PMI RMP
-
Quality Management: Six Sigma Green Belt ,Lean Six Sigma Green Belt, Lean Six Sigma Black Belt
-
Business Analysis: CBAP, CCBA, ECBA
-
Agile Training: PMI-ACP
-
Scrum Training: CSM
-
DevOps
-
Program Management: PgMP
-
IT Service Management & Governance: COBIT, ISO
Conclusion
In conclusion, the fundamentals of Lean Methodology represent a powerful framework for organizations seeking to thrive in today's dynamic and competitive landscape. By understanding and applying the principles of value, waste reduction, continuous improvement, and customer-centricity, businesses can unlock remarkable benefits. The real-world examples showcased in this blog highlight the versatility of Lean, demonstrating its effectiveness across diverse industries, from manufacturing and healthcare to software development and services.
As we wrap up our exploration of Lean, it's important to remember that Lean is not a one-time initiative but a journey of ongoing improvement. Embracing a Lean mindset, fostering a culture of innovation, and empowering employees to identify and eliminate waste are essential for sustained success. By integrating Lean into the DNA of your organization, you can optimize processes, reduce costs, enhance quality, and ultimately deliver greater value to your customers, setting the stage for a prosperous and efficient future.
Six Sigma vs. Lean Six Sigma: Which Certification to Choose?
In the quest for professional development and career advancement, the world of certifications stands as an essential crossroads, offering a multitude of paths to choose from. Among the many options, "Six Sigma" and "Lean Six Sigma" certifications shine as beacons of quality and process improvement, coveted by industries far and wide. However, faced with these two formidable choices, aspiring professionals often find themselves at a crossroads, pondering the critical question: "Six Sigma or Lean Six Sigma: Which Certification Path Should You Take?" This decision is no trifling matter, as it can significantly impact one's career trajectory and skill set. In this exploration, we delve into the nuances of both certification paths, shedding light on their differences, similarities, and the factors that can guide you toward making an informed and rewarding choice. Whether you're navigating the intricacies of quality management or seeking to optimize processes, this guide aims to equip you with the insights necessary to embark on the certification journey that aligns best with your aspirations and ambitions.
Table of Contents
-
What is Six Sigma?
-
What is Lean?
-
What is Lean Six Sigma?
-
Lean vs Six Sigma: Similarities and Differences
-
Certification Eligibilities, Examinations, and Responsibilities
-
Which is Right for You?
-
FAQs
What is Six Sigma?
Six Sigma is a data-driven methodology and set of tools and techniques used to improve processes and reduce defects in various industries, with a primary focus on achieving higher levels of quality and efficiency. It was originally developed by Motorola in the 1980s and later popularized by companies like General Electric.
The term "Six Sigma" refers to a statistical measure of process performance, which signifies that a process is capable of producing fewer than 3.4 defects per million opportunities (DPMO). In essence, it represents a high level of process accuracy and consistency.
Six Sigma is used in various industries, including manufacturing, healthcare, finance, and service sectors, to streamline processes, reduce costs, improve quality, and increase customer satisfaction. It offers a systematic approach to problem-solving and process improvement, making it a valuable tool for organizations seeking operational excellence.
What is Lean?
Lean, often referred to as Lean Thinking or Lean Management, is a methodology and philosophy that focuses on eliminating waste and maximizing value in processes. It originated from the manufacturing practices developed by Toyota in Japan and is often associated with the Toyota Production System (TPS). However, Lean principles have since been applied to various industries and sectors beyond manufacturing, including healthcare, service, and software development.
Lean principles aim to create more efficient, responsive, and customer-focused organizations. By eliminating waste and optimizing processes, Lean helps organizations deliver higher quality products and services while reducing costs and lead times. It's a holistic approach to operational excellence that goes beyond specific tools and techniques to instill a culture of continuous improvement throughout an organization.
What is Lean Six Sigma?
Lean Six Sigma is a hybrid approach that combines the principles and methodologies of Lean and Six Sigma. It is a comprehensive strategy for process improvement that seeks to eliminate waste and defects while optimizing efficiency and quality. Lean focuses on reducing waste and increasing flow, while Six Sigma emphasizes reducing defects and variations in processes. By integrating these two approaches, Lean Six Sigma aims to create a powerful framework for achieving operational excellence and improving organizational performance.
Lean Six Sigma is widely used in various industries, including manufacturing, healthcare, finance, and service sectors, to enhance process efficiency, reduce defects, minimize waste, and improve overall organizational performance. It offers a structured and data-driven approach to achieving excellence in both processes and outcomes.
Lean vs Six Sigma: Similarities and Differences
Lean and Six Sigma are two distinct methodologies for process improvement, but they share some similarities while also having key differences. Here's an overview of their similarities and differences:
Similarities:
-
Focus on Process Improvement: Both Lean and Six Sigma are centered on improving processes to achieve better outcomes, whether that's reducing defects, minimizing waste, enhancing efficiency, or improving overall quality.
-
Data-Driven: Both methodologies rely on data and statistical analysis to identify problems, measure process performance, and make informed decisions. Data is used to quantify issues and track progress.
-
Customer-Centric: Both Lean and Six Sigma emphasize meeting and exceeding customer expectations. They aim to deliver products or services that align with customer needs and preferences.
-
Continuous Improvement: Continuous improvement is a core principle of both Lean and Six Sigma. They advocate for an ongoing commitment to identifying and addressing issues, making incremental improvements, and striving for excellence.
-
Team-Based Approach: Both methodologies often involve cross-functional teams that collaborate to solve problems and drive improvements. This encourages a diversity of perspectives and expertise.
-
Root Cause Analysis: Both Lean and Six Sigma seek to identify and address the root causes of problems rather than just treating symptoms. This helps prevent issues from recurring.
Differences:
-
Primary Focus:
-
Lean primarily concentrates on the elimination of waste and the optimization of processes for efficiency and flow. Its main goal is to deliver value to customers while minimizing non-value-added activities.
-
Six Sigma primarily focuses on reducing process variation and defects. It aims to achieve a level of quality where the probability of defects is extremely low (less than 3.4 defects per million opportunities).
-
Methodologies:
-
Lean often uses tools like Value Stream Mapping, 5S, Kanban, and visual management techniques to improve processes and reduce waste.
-
Six Sigma employs statistical tools and techniques, such as DMAIC (Define, Measure, Analyze, Improve, Control), to measure and analyze process performance and drive improvements.
-
Waste Reduction:
-
Lean places a strong emphasis on identifying and eliminating various types of waste, including overproduction, transportation, waiting, and more.
-
Six Sigma focuses on reducing defects and minimizing process variation, which can lead to defects or deviations from desired outcomes.
-
Speed vs. Precision:
-
Lean is often associated with faster improvements and quicker results due to its focus on reducing waste and improving flow.
-
Six Sigma can take longer to implement, as it involves a more rigorous and data-intensive approach to reducing defects and variation.
-
Tools and Techniques:
-
Lean tools are geared toward process optimization and include techniques for visual management and rapid problem-solving.
-
Six Sigma tools are statistical in nature and are used to measure, analyze, and control processes to reduce variation and defects.
Certification Eligibilities, Examinations, and Responsibilities
Certification eligibility, examinations, and responsibilities can vary significantly depending on the specific certification program and the organization or governing body that administers it. Here is a general overview of what these aspects typically involve:
Certification Eligibility:
Eligibility for Six Sigma and Lean Six Sigma certifications varies based on the certification level and the certifying organization. Generally, Yellow Belt certifications have minimal prerequisites, while Green Belt certifications often require a bachelor's degree or equivalent experience. Black Belt certifications typically demand both a bachelor's degree and relevant work experience, with some programs expecting Green Belt certification as well. Master Black Belt certifications are typically reserved for highly experienced professionals who have completed numerous successful projects and demonstrated leadership in Six Sigma initiatives. While the specific requirements may vary, a solid understanding of Six Sigma concepts and, for Lean Six Sigma, familiarity with Lean principles are essential for pursuing these certifications. Candidates should always refer to the certifying organization's guidelines for precise eligibility criteria.
Examinations:
Examinations for Six Sigma and Lean Six Sigma certifications are comprehensive assessments that evaluate candidates' knowledge and expertise in quality management, process improvement, statistical analysis, and Lean methodologies. These exams vary in content, format, duration, and passing score based on the certification level (e.g., Yellow Belt, Green Belt, Black Belt) and the certifying organization. Typically, they encompass a range of question types, such as multiple-choice and true/false questions, and are administered through authorized testing centers or online proctoring services. Achieving a passing score is a critical milestone in earning these prestigious certifications, demonstrating proficiency in problem-solving, process optimization, and quality enhancement within an organization.
Responsibilities:
Responsibilities associated with Six Sigma and Lean Six Sigma certifications encompass various stages of the certification process and ongoing professional practice. Candidates pursuing these certifications are first responsible for thorough preparation, including studying the relevant materials and attending training if necessary. They must then take the initiative to register for the certification exam and adhere to the rules and procedures on exam day. During the exam, candidates must demonstrate their knowledge and problem-solving abilities. Afterward, successful candidates receive their certifications, but the responsibility doesn't end there. Certified professionals have a duty to apply their knowledge in the workplace, contributing to process improvement initiatives and ethical conduct. Continuous learning and maintaining ethical standards are also ongoing responsibilities associated with these certifications, reflecting a commitment to excellence and the promotion of quality within organizations.
It's important for individuals seeking certification to carefully review the specific eligibility requirements, examination details, and responsibilities outlined by the certifying organization to ensure they are fully prepared and compliant with the certification process.
Which is Right for You?
Determining whether Six Sigma or Lean Six Sigma is right for you depends on your specific career goals, the industry you work in or plan to work in, and your preferences for process improvement methodologies. Here are some considerations to help you decide which path might be more suitable:
Choose Six Sigma if:
-
You prioritize reducing defects: Six Sigma is particularly effective for industries where reducing defects and achieving near-perfect quality is critical, such as manufacturing and healthcare.
-
You enjoy statistical analysis: Six Sigma places a strong emphasis on statistical tools and data analysis. If you have a passion for data-driven decision-making and enjoy working with statistical techniques, Six Sigma might align well with your interests.
-
You want a structured problem-solving framework: Six Sigma provides a highly structured problem-solving approach through the DMAIC (Define, Measure, Analyze, Improve, Control) methodology, making it suitable for complex process improvement projects.
-
Your industry values traditional quality management: Some industries have a long history of using Six Sigma for quality management, making it a respected certification in those sectors.
Choose Lean Six Sigma if:
-
You seek to minimize waste: Lean Six Sigma excels at waste reduction and process optimization. If you are interested in eliminating non-value-added activities, improving efficiency, and enhancing flow within processes, Lean Six Sigma is a strong choice.
-
You prefer a holistic approach: Lean Six Sigma combines the principles of both Lean and Six Sigma, offering a more comprehensive framework that addresses both defects and waste. It's a versatile methodology suitable for a wide range of industries.
-
Your industry values efficiency and customer satisfaction: Lean Six Sigma's focus on improving processes and delivering value to customers aligns well with industries that prioritize efficiency, such as manufacturing, service, and healthcare.
-
You enjoy visual management and rapid problem-solving: Lean tools like Kanban, 5S, and visual management techniques can make problem-solving more intuitive and efficient.
Ultimately, the decision between Six Sigma and Lean Six Sigma should align with your career aspirations, interests, and the specific needs of the industry you are or plan to be a part of. It's worth noting that some professionals choose to pursue both certifications to have a well-rounded skill set that covers both defect reduction and waste elimination, allowing them to be more versatile problem solvers in various professional settings.
FAQs
Q1: What is the difference between Six Sigma and Lean Six Sigma certifications?
A: Six Sigma primarily focuses on reducing defects and process variation, while Lean Six Sigma combines Six Sigma principles with Lean methodology, emphasizing waste reduction and process optimization. The choice between them depends on your specific career goals and the nature of the industry you're interested in.
Q2: Which certification is more suitable for a career in manufacturing?
A: Both Six Sigma and Lean Six Sigma certifications are valuable in manufacturing. Six Sigma may be more suitable for quality control and defect reduction, while Lean Six Sigma can help streamline processes and reduce waste in manufacturing.
Q3: Are there any prerequisites for Six Sigma or Lean Six Sigma certifications?
A: Prerequisites can vary depending on the certification level and the certifying organization. Some certifications may require prior work experience or completion of specific training courses. Check the requirements of the certification program you're interested in.
Q4: Can I pursue both Six Sigma and Lean Six Sigma certifications simultaneously?
A: Yes, it's possible to pursue both certifications. Some individuals choose to earn both to have a well-rounded skill set that combines defect reduction and process optimization.
Q5: Do I need to choose between Six Sigma and Lean Six Sigma, or can I combine both approaches in my career?
A: You can certainly combine both approaches in your career. In fact, many organizations adopt Lean Six Sigma principles to benefit from both defect reduction and waste elimination.
Q6: How do I decide which certification path is right for me?
A: Consider your career goals, industry preferences, and the specific skills you want to develop. If you're interested in quality control and statistical analysis, Six Sigma may be a better fit. If you're more focused on process efficiency and waste reduction, Lean Six Sigma may be the way to go.
Q7: Which certification is more recognized by employers?
A: The recognition of Six Sigma and Lean Six Sigma certifications can vary by industry and region. It's essential to research the specific demands of your desired job market. Both certifications are widely recognized and respected.
Q8: Can I switch from Six Sigma to Lean Six Sigma or vice versa after obtaining one certification?
A: Yes, you can switch between the two paths. Many concepts and tools overlap between the two methodologies, making it relatively easy to transition.
Q9: How long does it typically take to earn a Six Sigma or Lean Six Sigma certification?
A: The duration varies based on the certification level (e.g., Green Belt, Black Belt) and the training program. Some certifications can be completed in a few weeks, while others may take several months or longer.
Q10: What is the average cost of obtaining a Six Sigma or Lean Six Sigma certification?
A: Certification costs can vary widely depending on the level, the certifying organization, and whether you choose to undergo training. It's essential to research the specific program and its associated costs.
Read More
In the quest for professional development and career advancement, the world of certifications stands as an essential crossroads, offering a multitude of paths to choose from. Among the many options, "Six Sigma" and "Lean Six Sigma" certifications shine as beacons of quality and process improvement, coveted by industries far and wide. However, faced with these two formidable choices, aspiring professionals often find themselves at a crossroads, pondering the critical question: "Six Sigma or Lean Six Sigma: Which Certification Path Should You Take?" This decision is no trifling matter, as it can significantly impact one's career trajectory and skill set. In this exploration, we delve into the nuances of both certification paths, shedding light on their differences, similarities, and the factors that can guide you toward making an informed and rewarding choice. Whether you're navigating the intricacies of quality management or seeking to optimize processes, this guide aims to equip you with the insights necessary to embark on the certification journey that aligns best with your aspirations and ambitions.
Table of Contents
-
What is Six Sigma?
-
What is Lean?
-
What is Lean Six Sigma?
-
Lean vs Six Sigma: Similarities and Differences
-
Certification Eligibilities, Examinations, and Responsibilities
-
Which is Right for You?
-
FAQs
What is Six Sigma?
Six Sigma is a data-driven methodology and set of tools and techniques used to improve processes and reduce defects in various industries, with a primary focus on achieving higher levels of quality and efficiency. It was originally developed by Motorola in the 1980s and later popularized by companies like General Electric.
The term "Six Sigma" refers to a statistical measure of process performance, which signifies that a process is capable of producing fewer than 3.4 defects per million opportunities (DPMO). In essence, it represents a high level of process accuracy and consistency.
Six Sigma is used in various industries, including manufacturing, healthcare, finance, and service sectors, to streamline processes, reduce costs, improve quality, and increase customer satisfaction. It offers a systematic approach to problem-solving and process improvement, making it a valuable tool for organizations seeking operational excellence.
What is Lean?
Lean, often referred to as Lean Thinking or Lean Management, is a methodology and philosophy that focuses on eliminating waste and maximizing value in processes. It originated from the manufacturing practices developed by Toyota in Japan and is often associated with the Toyota Production System (TPS). However, Lean principles have since been applied to various industries and sectors beyond manufacturing, including healthcare, service, and software development.
Lean principles aim to create more efficient, responsive, and customer-focused organizations. By eliminating waste and optimizing processes, Lean helps organizations deliver higher quality products and services while reducing costs and lead times. It's a holistic approach to operational excellence that goes beyond specific tools and techniques to instill a culture of continuous improvement throughout an organization.
What is Lean Six Sigma?
Lean Six Sigma is a hybrid approach that combines the principles and methodologies of Lean and Six Sigma. It is a comprehensive strategy for process improvement that seeks to eliminate waste and defects while optimizing efficiency and quality. Lean focuses on reducing waste and increasing flow, while Six Sigma emphasizes reducing defects and variations in processes. By integrating these two approaches, Lean Six Sigma aims to create a powerful framework for achieving operational excellence and improving organizational performance.
Lean Six Sigma is widely used in various industries, including manufacturing, healthcare, finance, and service sectors, to enhance process efficiency, reduce defects, minimize waste, and improve overall organizational performance. It offers a structured and data-driven approach to achieving excellence in both processes and outcomes.
Lean vs Six Sigma: Similarities and Differences
Lean and Six Sigma are two distinct methodologies for process improvement, but they share some similarities while also having key differences. Here's an overview of their similarities and differences:
Similarities:
-
Focus on Process Improvement: Both Lean and Six Sigma are centered on improving processes to achieve better outcomes, whether that's reducing defects, minimizing waste, enhancing efficiency, or improving overall quality.
-
Data-Driven: Both methodologies rely on data and statistical analysis to identify problems, measure process performance, and make informed decisions. Data is used to quantify issues and track progress.
-
Customer-Centric: Both Lean and Six Sigma emphasize meeting and exceeding customer expectations. They aim to deliver products or services that align with customer needs and preferences.
-
Continuous Improvement: Continuous improvement is a core principle of both Lean and Six Sigma. They advocate for an ongoing commitment to identifying and addressing issues, making incremental improvements, and striving for excellence.
-
Team-Based Approach: Both methodologies often involve cross-functional teams that collaborate to solve problems and drive improvements. This encourages a diversity of perspectives and expertise.
-
Root Cause Analysis: Both Lean and Six Sigma seek to identify and address the root causes of problems rather than just treating symptoms. This helps prevent issues from recurring.
Differences:
-
Primary Focus:
-
Lean primarily concentrates on the elimination of waste and the optimization of processes for efficiency and flow. Its main goal is to deliver value to customers while minimizing non-value-added activities.
-
Six Sigma primarily focuses on reducing process variation and defects. It aims to achieve a level of quality where the probability of defects is extremely low (less than 3.4 defects per million opportunities).
-
-
Methodologies:
-
Lean often uses tools like Value Stream Mapping, 5S, Kanban, and visual management techniques to improve processes and reduce waste.
-
Six Sigma employs statistical tools and techniques, such as DMAIC (Define, Measure, Analyze, Improve, Control), to measure and analyze process performance and drive improvements.
-
-
Waste Reduction:
-
Lean places a strong emphasis on identifying and eliminating various types of waste, including overproduction, transportation, waiting, and more.
-
Six Sigma focuses on reducing defects and minimizing process variation, which can lead to defects or deviations from desired outcomes.
-
-
Speed vs. Precision:
-
Lean is often associated with faster improvements and quicker results due to its focus on reducing waste and improving flow.
-
Six Sigma can take longer to implement, as it involves a more rigorous and data-intensive approach to reducing defects and variation.
-
-
Tools and Techniques:
-
Lean tools are geared toward process optimization and include techniques for visual management and rapid problem-solving.
-
Six Sigma tools are statistical in nature and are used to measure, analyze, and control processes to reduce variation and defects.
-
Certification Eligibilities, Examinations, and Responsibilities
Certification eligibility, examinations, and responsibilities can vary significantly depending on the specific certification program and the organization or governing body that administers it. Here is a general overview of what these aspects typically involve:
Certification Eligibility:
Eligibility for Six Sigma and Lean Six Sigma certifications varies based on the certification level and the certifying organization. Generally, Yellow Belt certifications have minimal prerequisites, while Green Belt certifications often require a bachelor's degree or equivalent experience. Black Belt certifications typically demand both a bachelor's degree and relevant work experience, with some programs expecting Green Belt certification as well. Master Black Belt certifications are typically reserved for highly experienced professionals who have completed numerous successful projects and demonstrated leadership in Six Sigma initiatives. While the specific requirements may vary, a solid understanding of Six Sigma concepts and, for Lean Six Sigma, familiarity with Lean principles are essential for pursuing these certifications. Candidates should always refer to the certifying organization's guidelines for precise eligibility criteria.
Examinations:
Examinations for Six Sigma and Lean Six Sigma certifications are comprehensive assessments that evaluate candidates' knowledge and expertise in quality management, process improvement, statistical analysis, and Lean methodologies. These exams vary in content, format, duration, and passing score based on the certification level (e.g., Yellow Belt, Green Belt, Black Belt) and the certifying organization. Typically, they encompass a range of question types, such as multiple-choice and true/false questions, and are administered through authorized testing centers or online proctoring services. Achieving a passing score is a critical milestone in earning these prestigious certifications, demonstrating proficiency in problem-solving, process optimization, and quality enhancement within an organization.
Responsibilities:
Responsibilities associated with Six Sigma and Lean Six Sigma certifications encompass various stages of the certification process and ongoing professional practice. Candidates pursuing these certifications are first responsible for thorough preparation, including studying the relevant materials and attending training if necessary. They must then take the initiative to register for the certification exam and adhere to the rules and procedures on exam day. During the exam, candidates must demonstrate their knowledge and problem-solving abilities. Afterward, successful candidates receive their certifications, but the responsibility doesn't end there. Certified professionals have a duty to apply their knowledge in the workplace, contributing to process improvement initiatives and ethical conduct. Continuous learning and maintaining ethical standards are also ongoing responsibilities associated with these certifications, reflecting a commitment to excellence and the promotion of quality within organizations.
It's important for individuals seeking certification to carefully review the specific eligibility requirements, examination details, and responsibilities outlined by the certifying organization to ensure they are fully prepared and compliant with the certification process.
Which is Right for You?
Determining whether Six Sigma or Lean Six Sigma is right for you depends on your specific career goals, the industry you work in or plan to work in, and your preferences for process improvement methodologies. Here are some considerations to help you decide which path might be more suitable:
Choose Six Sigma if:
-
You prioritize reducing defects: Six Sigma is particularly effective for industries where reducing defects and achieving near-perfect quality is critical, such as manufacturing and healthcare.
-
You enjoy statistical analysis: Six Sigma places a strong emphasis on statistical tools and data analysis. If you have a passion for data-driven decision-making and enjoy working with statistical techniques, Six Sigma might align well with your interests.
-
You want a structured problem-solving framework: Six Sigma provides a highly structured problem-solving approach through the DMAIC (Define, Measure, Analyze, Improve, Control) methodology, making it suitable for complex process improvement projects.
-
Your industry values traditional quality management: Some industries have a long history of using Six Sigma for quality management, making it a respected certification in those sectors.
Choose Lean Six Sigma if:
-
You seek to minimize waste: Lean Six Sigma excels at waste reduction and process optimization. If you are interested in eliminating non-value-added activities, improving efficiency, and enhancing flow within processes, Lean Six Sigma is a strong choice.
-
You prefer a holistic approach: Lean Six Sigma combines the principles of both Lean and Six Sigma, offering a more comprehensive framework that addresses both defects and waste. It's a versatile methodology suitable for a wide range of industries.
-
Your industry values efficiency and customer satisfaction: Lean Six Sigma's focus on improving processes and delivering value to customers aligns well with industries that prioritize efficiency, such as manufacturing, service, and healthcare.
-
You enjoy visual management and rapid problem-solving: Lean tools like Kanban, 5S, and visual management techniques can make problem-solving more intuitive and efficient.
Ultimately, the decision between Six Sigma and Lean Six Sigma should align with your career aspirations, interests, and the specific needs of the industry you are or plan to be a part of. It's worth noting that some professionals choose to pursue both certifications to have a well-rounded skill set that covers both defect reduction and waste elimination, allowing them to be more versatile problem solvers in various professional settings.
FAQs
Q1: What is the difference between Six Sigma and Lean Six Sigma certifications?
A: Six Sigma primarily focuses on reducing defects and process variation, while Lean Six Sigma combines Six Sigma principles with Lean methodology, emphasizing waste reduction and process optimization. The choice between them depends on your specific career goals and the nature of the industry you're interested in.
Q2: Which certification is more suitable for a career in manufacturing?
A: Both Six Sigma and Lean Six Sigma certifications are valuable in manufacturing. Six Sigma may be more suitable for quality control and defect reduction, while Lean Six Sigma can help streamline processes and reduce waste in manufacturing.
Q3: Are there any prerequisites for Six Sigma or Lean Six Sigma certifications?
A: Prerequisites can vary depending on the certification level and the certifying organization. Some certifications may require prior work experience or completion of specific training courses. Check the requirements of the certification program you're interested in.
Q4: Can I pursue both Six Sigma and Lean Six Sigma certifications simultaneously?
A: Yes, it's possible to pursue both certifications. Some individuals choose to earn both to have a well-rounded skill set that combines defect reduction and process optimization.
Q5: Do I need to choose between Six Sigma and Lean Six Sigma, or can I combine both approaches in my career?
A: You can certainly combine both approaches in your career. In fact, many organizations adopt Lean Six Sigma principles to benefit from both defect reduction and waste elimination.
Q6: How do I decide which certification path is right for me?
A: Consider your career goals, industry preferences, and the specific skills you want to develop. If you're interested in quality control and statistical analysis, Six Sigma may be a better fit. If you're more focused on process efficiency and waste reduction, Lean Six Sigma may be the way to go.
Q7: Which certification is more recognized by employers?
A: The recognition of Six Sigma and Lean Six Sigma certifications can vary by industry and region. It's essential to research the specific demands of your desired job market. Both certifications are widely recognized and respected.
Q8: Can I switch from Six Sigma to Lean Six Sigma or vice versa after obtaining one certification?
A: Yes, you can switch between the two paths. Many concepts and tools overlap between the two methodologies, making it relatively easy to transition.
Q9: How long does it typically take to earn a Six Sigma or Lean Six Sigma certification?
A: The duration varies based on the certification level (e.g., Green Belt, Black Belt) and the training program. Some certifications can be completed in a few weeks, while others may take several months or longer.
Q10: What is the average cost of obtaining a Six Sigma or Lean Six Sigma certification?
A: Certification costs can vary widely depending on the level, the certifying organization, and whether you choose to undergo training. It's essential to research the specific program and its associated costs.
CMMI Certification: Essential Information You Need to Know
In today's competitive business landscape, organizations strive to achieve operational excellence, deliver high-quality products and services, and continuously improve their processes. CMMI (Capability Maturity Model Integration) certification has emerged as a valuable framework for organizations to assess and enhance their process maturity and performance. This guide aims to provide a comprehensive understanding of CMMI certification, its significance, and what organizations need to know to embark on the certification journey.
The guide begins by introducing CMMI and its role in process improvement and quality management. CMMI is a globally recognized model that enables organizations to evaluate and enhance their capabilities across various domains, including software engineering, project management, and service delivery. By implementing CMMI best practices, organizations can establish a framework for achieving higher levels of process maturity and organizational excellence.
Furthermore, the guide explores the different levels of CMMI maturity, ranging from initial to optimized, outlining the key characteristics and requirements at each level. Readers will gain insights into the CMMI model framework, including its process areas and practices that define the roadmap for achieving higher levels of process maturity.
To obtain CMMI certification, organizations must undergo a formal appraisal process that evaluates their adherence to CMMI best practices and their capability to deliver quality products and services. The guide explores the appraisal method, performance measurement, and compliance requirements involved in the certification process. It also highlights the benefits of CMMI certification, including improved process efficiency, enhanced customer satisfaction, and increased organizational maturity.
In addition, the guide provides an overview of the implementation process and the importance of CMMI training for building the necessary knowledge and skills within an organization. By understanding the core concepts and practices of CMMI, organizations can effectively navigate the certification journey and leverage its potential for driving process improvement and business success.
Whether you are an organization seeking to enhance your process maturity or an individual looking to expand your knowledge of CMMI, this guide equips you with the essential information to understand the CMMI certification process, its benefits, and its impact on organizational performance. Embark on your journey to unlocking process excellence and organizational maturity through CMMI certification with "What You Need to Know About CMMI Certification."
Table of contents
- Introduction to CMMI
- The Benefits of Using CMMI
- The Five Maturity Levels of CMMI
- CMMI Models
- Implementing CMMI
- CMMI Appraisals
- CMMI and Agile
- CMMI and ISO
- Case Studies
- Conclusion
Introduction to CMMI
Capability Maturity Model Integration (CMMI) is a framework that helps organizations improve their processes and capabilities to achieve their business goals. CMMI provides a comprehensive and structured approach to assessing an organization's maturity level in different areas such as development, acquisition, and services. With CMMI, organizations can identify areas for improvement, establish standards, and optimize their processes to increase efficiency, quality, and customer satisfaction. This framework has been widely adopted by organizations around the world, including government agencies, technology companies, and service providers, to enhance their operational excellence and achieve sustainable growth. In this blog, we will explore the key concepts of CMMI, its benefits, and how it can be implemented and integrated with other frameworks.
The Benefits of Using CMMI
Using Capability Maturity Model Integration (CMMI) has many benefits for organizations looking to improve their processes and capabilities. Here are some of the key benefits of using CMMI:
- Improved Quality: By using CMMI, organizations can identify and eliminate inefficiencies, defects, and other quality issues that can impact product or service quality. This leads to improved customer satisfaction, fewer defects, and higher reliability.
- Increased Efficiency: CMMI provides a structured approach to process improvement that can help organizations streamline their processes, reduce waste, and increase productivity. This results in faster delivery times, reduced costs, and increased profitability.
- Better Alignment with Organizational Goals: CMMI helps organizations align their processes with their strategic goals and objectives. By focusing on critical areas and eliminating non-value-added activities, organizations can ensure that their processes are contributing to the success of the business.
- Enhanced Risk Management: CMMI provides a systematic approach to risk management that can help organizations identify and mitigate risks before they become significant issues. This reduces the likelihood of project delays, cost overruns, or other negative impacts.
- Improved Communication and Collaboration: CMMI promotes better communication and collaboration among team members, stakeholders, and customers. By establishing clear standards, roles, and responsibilities, organizations can reduce misunderstandings and improve overall teamwork.
- Competitive Advantage: Organizations that use CMMI can gain a competitive advantage over their competitors. By demonstrating their commitment to quality and process improvement, they can differentiate themselves in the market and attract more customers.
The Five Maturity Levels of CMMI
Capability Maturity Model Integration (CMMI) consists of five maturity levels that organizations can use to assess and improve their processes. Each level represents a different level of maturity in process capability and builds upon the previous level. Here are the five maturity levels of CMMI:
- Initial: This is the starting point for organizations that have not yet established a consistent approach to process management. At this level, processes are often ad hoc, chaotic, and unpredictable. There is no standardization or documentation of processes, and there is a lack of awareness of the importance of process improvement.
- Managed: At this level, organizations have established basic project management processes and controls. Processes are documented and followed, and there is a basic understanding of process improvement. However, the processes are still reactive and are not yet optimized.
- Defined: At this level, organizations have defined and standardized their processes. They have developed a consistent and repeatable approach to process management, and processes are optimized for efficiency and effectiveness. There is a focus on continuous improvement, and processes are monitored and measured.
- Quantitatively Managed: At this level, organizations have implemented quantitative measures and analysis to manage their processes. They use data to make informed decisions, and there is a focus on predictive process management. Processes are optimized for quality, and there is a culture of continuous improvement.
- Optimizing: This is the highest level of maturity, where organizations are continuously improving their processes and striving for innovation. They use data and feedback to identify areas for improvement and are proactive in addressing process issues. There is a focus on innovation, and processes are continuously optimized for performance and effectiveness.
CMMI Models
Capability Maturity Model Integration (CMMI) provides multiple models that can be used by organizations to assess and improve their processes. Each model has a different focus and is designed for a specific industry or business area. Here are some of the CMMI models:
- CMMI for Development (CMMI-DEV): This model is designed for organizations that develop products or services. It covers all aspects of the product development lifecycle, including planning, engineering, and testing.
- CMMI for Services (CMMI-SVC): This model is designed for organizations that provide services, such as IT services, consulting, or healthcare. It covers all aspects of the service delivery lifecycle, including service design, delivery, and management.
- CMMI for Acquisition (CMMI-ACQ): This model is designed for organizations that acquire goods or services from suppliers. It covers all aspects of the acquisition lifecycle, including supplier selection, contract management, and delivery management.
- People CMM: This model is designed for organizations that want to improve their human resources management. It focuses on developing and managing the skills and capabilities of employees to improve organizational performance.
- CMMI for Development and Services (CMMI-DEV-SVC): This model is a combination of the CMMI-DEV and CMMI-SVC models. It covers all aspects of the product and service delivery lifecycle, providing a comprehensive approach to process improvement.
Implementing CMMI
Implementing Capability Maturity Model Integration (CMMI) requires a structured approach and a commitment to continuous improvement. Here are some steps to consider when implementing CMMI:
- Identify the business objectives: Before starting the CMMI implementation, it's important to identify the business objectives and the areas of the organization that need improvement. This can help prioritize the CMMI implementation effort and ensure that the organization is focusing on the right areas.
- Select the appropriate CMMI model: Depending on the business objectives and the areas of improvement, select the appropriate CMMI model that best fits the organization's needs. For example, if the organization develops products, the CMMI for Development (CMMI-DEV) model might be the most appropriate.
- Conduct a gap analysis: Once the CMMI model is selected, conduct a gap analysis to identify the gaps between the organization's current processes and the CMMI model's prescribed practices. This can help identify the areas where the organization needs to improve and the specific practices that need to be implemented.
- Develop an improvement plan: Based on the gap analysis results, develop an improvement plan that includes specific goals, timelines, and responsibilities for implementing the CMMI practices. It's important to involve all stakeholders in the development of the improvement plan and to communicate the plan to everyone involved.
- Implement the CMMI practices: Implement the CMMI practices according to the improvement plan. This can involve developing new processes, training employees, and changing the organizational culture to promote process improvement.
- Monitor and measure progress: Monitor and measure progress towards achieving the CMMI goals and objectives. This can involve collecting data and analyzing performance metrics to track progress and identify areas for further improvement.
- Continuously improve: CMMI implementation is a continuous process, and organizations should continuously improve their processes to achieve higher maturity levels. This involves periodically reviewing and updating the improvement plan, assessing progress, and identifying new areas for improvement.
CMMI Appraisals
CMMI appraisals are formal evaluations of an organization's processes against the Capability Maturity Model Integration (CMMI) model. The goal of the appraisal is to assess the organization's level of process maturity and identify areas for improvement.
There are two types of CMMI appraisals:
- SCAMPI Appraisal: SCAMPI (Standard CMMI Appraisal Method for Process Improvement) is the most widely used CMMI appraisal method. It provides a rigorous and structured approach to process improvement and is conducted by a team of certified appraisers. SCAMPI appraisals can be either Class A, B, or C depending on the level of detail and rigor of the appraisal.
- SCAMPI Simplified Appraisal: SCAMPI Simplified Appraisal is a less formal and less expensive appraisal method than the SCAMPI appraisal. It is designed for smaller organizations or organizations that want a less rigorous appraisal.
During the appraisal process, the appraisers evaluate the organization's processes against the CMMI model's practices and identify strengths and weaknesses. The appraisal team then provides a report that includes an assessment of the organization's level of process maturity, recommendations for improvement, and areas for further development.
The benefits of a CMMI appraisal include:
- Objective assessment of process maturity: A CMMI appraisal provides an objective assessment of an organization's level of process maturity, which can help identify areas for improvement and provide a roadmap for process improvement.
- Improved process efficiency: By implementing the CMMI model's best practices, organizations can improve their process efficiency and reduce costs and risks.
- Improved product quality: CMMI practices are designed to improve the quality of products and services, which can lead to increased customer satisfaction and loyalty.
- Competitive advantage: Achieving a higher level of process maturity can provide a competitive advantage and differentiate an organization from its competitors.
CMMI and Agile
CMMI and Agile are two popular methodologies that organizations use to improve their processes and deliver better products and services. While CMMI is a process improvement framework that focuses on maturity levels and best practices, Agile is an iterative and flexible approach to software development that emphasizes collaboration, customer satisfaction, and adaptability.
Although they have different approaches and methodologies, CMMI and Agile can be complementary, and many organizations have successfully combined the two methodologies to improve their processes and deliver better products and services.
Here are some ways in which CMMI and Agile can be used together:
- Adopting CMMI best practices in Agile: Organizations can adopt CMMI best practices, such as risk management and configuration management, into their Agile processes. This can help improve the quality of the products and services and reduce risks.
- Using Agile to achieve CMMI objectives: Agile methodologies can help organizations achieve CMMI objectives, such as continuous improvement and customer satisfaction. Agile methodologies emphasize collaboration, feedback, and continuous improvement, which can help organizations achieve their CMMI objectives.
- Incorporating Agile practices in CMMI: Organizations can incorporate Agile practices, such as sprint planning and daily stand-up meetings, into their CMMI processes. This can help make their processes more flexible, iterative, and responsive to customer needs.
- Using CMMI to provide a framework for Agile: Organizations can use CMMI as a framework to provide structure and guidelines for their Agile processes. This can help ensure that Agile practices are implemented consistently and effectively across the organization.
CMMI and ISO
CMMI and ISO (International Organization for Standardization) are two popular frameworks used by organizations to improve their processes, products, and services. While CMMI is a process improvement framework that focuses on maturity levels and best practices, ISO is a family of standards that provide guidelines for quality management systems.
Although they have different approaches and methodologies, CMMI and ISO can be complementary, and many organizations have successfully combined the two frameworks to improve their processes and products.
Here are some ways in which CMMI and ISO can be used together:
- Combining CMMI with ISO 9001: ISO 9001 is a standard that provides guidelines for quality management systems. Organizations can combine CMMI and ISO 9001 to improve their processes and achieve their quality objectives. By adopting CMMI best practices and ISO 9001 guidelines, organizations can improve their process efficiency, product quality, and customer satisfaction.
- Using CMMI to achieve ISO 27001: ISO 27001 is a standard that provides guidelines for information security management systems. Organizations can use CMMI to achieve their ISO 27001 objectives by adopting CMMI best practices for risk management, security management, and configuration management.
- Incorporating ISO standards in CMMI: Organizations can incorporate ISO standards, such as ISO 9001 and ISO 27001, in their CMMI processes. This can help ensure that their processes comply with international standards and guidelines.
- Using CMMI to provide a framework for ISO: Organizations can use CMMI as a framework to provide structure and guidelines for their ISO processes. This can help ensure that ISO standards are implemented consistently and effectively across the organization.
How to obtain the CMMI certification?
We are an Education Technology company providing certification training courses to accelerate careers of working professionals worldwide. We impart training through instructor-led classroom workshops, instructor-led live virtual training sessions, and self-paced e-learning courses.
We have successfully conducted training sessions in 108 countries across the globe and enabled thousands of working professionals to enhance the scope of their careers.
Our enterprise training portfolio includes in-demand and globally recognized certification training courses in Project Management, Quality Management, Business Analysis, IT Service Management, Agile and Scrum, Cyber Security, Data Science, and Emerging Technologies. Download our Enterprise Training Catalog from https://www.icertglobal.com/corporate-training-for-enterprises.php
Popular Courses include:
- Project Management: PMP, CAPM ,PMI RMP
- Quality Management: Six Sigma Black Belt ,Lean Six Sigma Green Belt, Lean Management, Minitab ,CMMI
- Business Analysis: CBAP, CCBA, ECBA
- Agile Training: PMI-ACP
- Scrum Training: CSM
- DevOps
- Program Management: PgMP
- IT Service Management & Governance: COBIT, ISO
Case Studies
Here are some case studies of organizations that have successfully implemented CMMI:
- IBM: IBM has been using CMMI for over a decade to improve its software development processes. By adopting CMMI, IBM has been able to improve process efficiency, reduce costs, and improve product quality. IBM's software development division has achieved CMMI Level 5, the highest maturity level in the CMMI framework.
- Raytheon: Raytheon, a defense and aerospace company, has been using CMMI to improve its processes and products for over a decade. By adopting CMMI, Raytheon has been able to reduce defects, improve product quality, and increase customer satisfaction. Raytheon's software development division has achieved CMMI Level 5.
- Siemens: Siemens, a multinational conglomerate, has been using CMMI to improve its software development processes for over a decade. By adopting CMMI, Siemens has been able to improve process efficiency, reduce costs, and improve product quality. Siemens' software development division has achieved CMMI Level 3.
- Infosys: Infosys, a multinational IT services company, has been using CMMI to improve its processes and products for over a decade. By adopting CMMI, Infosys has been able to improve process efficiency, reduce defects, and improve customer satisfaction. Infosys' software development division has achieved CMMI Level 5.
- Boeing: Boeing, an aerospace company, has been using CMMI to improve its software development processes for over a decade. By adopting CMMI, Boeing has been able to reduce costs, improve process efficiency, and improve product quality. Boeing's software development division has achieved CMMI Level 3.
Conclusion
In conclusion, Capability Maturity Model Integration (CMMI) is a process improvement framework that can help organizations improve their processes, products, and services. By adopting CMMI best practices, organizations can increase their process efficiency, reduce costs, improve product quality, and increase customer satisfaction. CMMI provides a roadmap for organizations to identify and improve their weaknesses and achieve higher levels of process maturity.
CMMI also offers flexibility and scalability, allowing organizations to tailor their process improvement efforts to their specific needs and goals. Moreover, CMMI can be used in conjunction with other frameworks such as Agile and ISO to further enhance the benefits of process improvement efforts.
Through successful case studies of organizations such as IBM, Raytheon, Siemens, Infosys, and Boeing, we can see that CMMI is a valuable tool for achieving process excellence and improving organizational performance. By implementing CMMI, organizations can not only improve their bottom line but also create a culture of continuous improvement and innovation.
Read More
In today's competitive business landscape, organizations strive to achieve operational excellence, deliver high-quality products and services, and continuously improve their processes. CMMI (Capability Maturity Model Integration) certification has emerged as a valuable framework for organizations to assess and enhance their process maturity and performance. This guide aims to provide a comprehensive understanding of CMMI certification, its significance, and what organizations need to know to embark on the certification journey.
The guide begins by introducing CMMI and its role in process improvement and quality management. CMMI is a globally recognized model that enables organizations to evaluate and enhance their capabilities across various domains, including software engineering, project management, and service delivery. By implementing CMMI best practices, organizations can establish a framework for achieving higher levels of process maturity and organizational excellence.
Furthermore, the guide explores the different levels of CMMI maturity, ranging from initial to optimized, outlining the key characteristics and requirements at each level. Readers will gain insights into the CMMI model framework, including its process areas and practices that define the roadmap for achieving higher levels of process maturity.
To obtain CMMI certification, organizations must undergo a formal appraisal process that evaluates their adherence to CMMI best practices and their capability to deliver quality products and services. The guide explores the appraisal method, performance measurement, and compliance requirements involved in the certification process. It also highlights the benefits of CMMI certification, including improved process efficiency, enhanced customer satisfaction, and increased organizational maturity.
In addition, the guide provides an overview of the implementation process and the importance of CMMI training for building the necessary knowledge and skills within an organization. By understanding the core concepts and practices of CMMI, organizations can effectively navigate the certification journey and leverage its potential for driving process improvement and business success.
Whether you are an organization seeking to enhance your process maturity or an individual looking to expand your knowledge of CMMI, this guide equips you with the essential information to understand the CMMI certification process, its benefits, and its impact on organizational performance. Embark on your journey to unlocking process excellence and organizational maturity through CMMI certification with "What You Need to Know About CMMI Certification."
Table of contents
- Introduction to CMMI
- The Benefits of Using CMMI
- The Five Maturity Levels of CMMI
- CMMI Models
- Implementing CMMI
- CMMI Appraisals
- CMMI and Agile
- CMMI and ISO
- Case Studies
- Conclusion
Introduction to CMMI
Capability Maturity Model Integration (CMMI) is a framework that helps organizations improve their processes and capabilities to achieve their business goals. CMMI provides a comprehensive and structured approach to assessing an organization's maturity level in different areas such as development, acquisition, and services. With CMMI, organizations can identify areas for improvement, establish standards, and optimize their processes to increase efficiency, quality, and customer satisfaction. This framework has been widely adopted by organizations around the world, including government agencies, technology companies, and service providers, to enhance their operational excellence and achieve sustainable growth. In this blog, we will explore the key concepts of CMMI, its benefits, and how it can be implemented and integrated with other frameworks.
The Benefits of Using CMMI
Using Capability Maturity Model Integration (CMMI) has many benefits for organizations looking to improve their processes and capabilities. Here are some of the key benefits of using CMMI:
- Improved Quality: By using CMMI, organizations can identify and eliminate inefficiencies, defects, and other quality issues that can impact product or service quality. This leads to improved customer satisfaction, fewer defects, and higher reliability.
- Increased Efficiency: CMMI provides a structured approach to process improvement that can help organizations streamline their processes, reduce waste, and increase productivity. This results in faster delivery times, reduced costs, and increased profitability.
- Better Alignment with Organizational Goals: CMMI helps organizations align their processes with their strategic goals and objectives. By focusing on critical areas and eliminating non-value-added activities, organizations can ensure that their processes are contributing to the success of the business.
- Enhanced Risk Management: CMMI provides a systematic approach to risk management that can help organizations identify and mitigate risks before they become significant issues. This reduces the likelihood of project delays, cost overruns, or other negative impacts.
- Improved Communication and Collaboration: CMMI promotes better communication and collaboration among team members, stakeholders, and customers. By establishing clear standards, roles, and responsibilities, organizations can reduce misunderstandings and improve overall teamwork.
- Competitive Advantage: Organizations that use CMMI can gain a competitive advantage over their competitors. By demonstrating their commitment to quality and process improvement, they can differentiate themselves in the market and attract more customers.
The Five Maturity Levels of CMMI
Capability Maturity Model Integration (CMMI) consists of five maturity levels that organizations can use to assess and improve their processes. Each level represents a different level of maturity in process capability and builds upon the previous level. Here are the five maturity levels of CMMI:
- Initial: This is the starting point for organizations that have not yet established a consistent approach to process management. At this level, processes are often ad hoc, chaotic, and unpredictable. There is no standardization or documentation of processes, and there is a lack of awareness of the importance of process improvement.
- Managed: At this level, organizations have established basic project management processes and controls. Processes are documented and followed, and there is a basic understanding of process improvement. However, the processes are still reactive and are not yet optimized.
- Defined: At this level, organizations have defined and standardized their processes. They have developed a consistent and repeatable approach to process management, and processes are optimized for efficiency and effectiveness. There is a focus on continuous improvement, and processes are monitored and measured.
- Quantitatively Managed: At this level, organizations have implemented quantitative measures and analysis to manage their processes. They use data to make informed decisions, and there is a focus on predictive process management. Processes are optimized for quality, and there is a culture of continuous improvement.
- Optimizing: This is the highest level of maturity, where organizations are continuously improving their processes and striving for innovation. They use data and feedback to identify areas for improvement and are proactive in addressing process issues. There is a focus on innovation, and processes are continuously optimized for performance and effectiveness.
CMMI Models
Capability Maturity Model Integration (CMMI) provides multiple models that can be used by organizations to assess and improve their processes. Each model has a different focus and is designed for a specific industry or business area. Here are some of the CMMI models:
- CMMI for Development (CMMI-DEV): This model is designed for organizations that develop products or services. It covers all aspects of the product development lifecycle, including planning, engineering, and testing.
- CMMI for Services (CMMI-SVC): This model is designed for organizations that provide services, such as IT services, consulting, or healthcare. It covers all aspects of the service delivery lifecycle, including service design, delivery, and management.
- CMMI for Acquisition (CMMI-ACQ): This model is designed for organizations that acquire goods or services from suppliers. It covers all aspects of the acquisition lifecycle, including supplier selection, contract management, and delivery management.
- People CMM: This model is designed for organizations that want to improve their human resources management. It focuses on developing and managing the skills and capabilities of employees to improve organizational performance.
- CMMI for Development and Services (CMMI-DEV-SVC): This model is a combination of the CMMI-DEV and CMMI-SVC models. It covers all aspects of the product and service delivery lifecycle, providing a comprehensive approach to process improvement.
Implementing CMMI
Implementing Capability Maturity Model Integration (CMMI) requires a structured approach and a commitment to continuous improvement. Here are some steps to consider when implementing CMMI:
- Identify the business objectives: Before starting the CMMI implementation, it's important to identify the business objectives and the areas of the organization that need improvement. This can help prioritize the CMMI implementation effort and ensure that the organization is focusing on the right areas.
- Select the appropriate CMMI model: Depending on the business objectives and the areas of improvement, select the appropriate CMMI model that best fits the organization's needs. For example, if the organization develops products, the CMMI for Development (CMMI-DEV) model might be the most appropriate.
- Conduct a gap analysis: Once the CMMI model is selected, conduct a gap analysis to identify the gaps between the organization's current processes and the CMMI model's prescribed practices. This can help identify the areas where the organization needs to improve and the specific practices that need to be implemented.
- Develop an improvement plan: Based on the gap analysis results, develop an improvement plan that includes specific goals, timelines, and responsibilities for implementing the CMMI practices. It's important to involve all stakeholders in the development of the improvement plan and to communicate the plan to everyone involved.
- Implement the CMMI practices: Implement the CMMI practices according to the improvement plan. This can involve developing new processes, training employees, and changing the organizational culture to promote process improvement.
- Monitor and measure progress: Monitor and measure progress towards achieving the CMMI goals and objectives. This can involve collecting data and analyzing performance metrics to track progress and identify areas for further improvement.
- Continuously improve: CMMI implementation is a continuous process, and organizations should continuously improve their processes to achieve higher maturity levels. This involves periodically reviewing and updating the improvement plan, assessing progress, and identifying new areas for improvement.
CMMI Appraisals
CMMI appraisals are formal evaluations of an organization's processes against the Capability Maturity Model Integration (CMMI) model. The goal of the appraisal is to assess the organization's level of process maturity and identify areas for improvement.
There are two types of CMMI appraisals:
- SCAMPI Appraisal: SCAMPI (Standard CMMI Appraisal Method for Process Improvement) is the most widely used CMMI appraisal method. It provides a rigorous and structured approach to process improvement and is conducted by a team of certified appraisers. SCAMPI appraisals can be either Class A, B, or C depending on the level of detail and rigor of the appraisal.
- SCAMPI Simplified Appraisal: SCAMPI Simplified Appraisal is a less formal and less expensive appraisal method than the SCAMPI appraisal. It is designed for smaller organizations or organizations that want a less rigorous appraisal.
During the appraisal process, the appraisers evaluate the organization's processes against the CMMI model's practices and identify strengths and weaknesses. The appraisal team then provides a report that includes an assessment of the organization's level of process maturity, recommendations for improvement, and areas for further development.
The benefits of a CMMI appraisal include:
- Objective assessment of process maturity: A CMMI appraisal provides an objective assessment of an organization's level of process maturity, which can help identify areas for improvement and provide a roadmap for process improvement.
- Improved process efficiency: By implementing the CMMI model's best practices, organizations can improve their process efficiency and reduce costs and risks.
- Improved product quality: CMMI practices are designed to improve the quality of products and services, which can lead to increased customer satisfaction and loyalty.
- Competitive advantage: Achieving a higher level of process maturity can provide a competitive advantage and differentiate an organization from its competitors.
CMMI and Agile
CMMI and Agile are two popular methodologies that organizations use to improve their processes and deliver better products and services. While CMMI is a process improvement framework that focuses on maturity levels and best practices, Agile is an iterative and flexible approach to software development that emphasizes collaboration, customer satisfaction, and adaptability.
Although they have different approaches and methodologies, CMMI and Agile can be complementary, and many organizations have successfully combined the two methodologies to improve their processes and deliver better products and services.
Here are some ways in which CMMI and Agile can be used together:
- Adopting CMMI best practices in Agile: Organizations can adopt CMMI best practices, such as risk management and configuration management, into their Agile processes. This can help improve the quality of the products and services and reduce risks.
- Using Agile to achieve CMMI objectives: Agile methodologies can help organizations achieve CMMI objectives, such as continuous improvement and customer satisfaction. Agile methodologies emphasize collaboration, feedback, and continuous improvement, which can help organizations achieve their CMMI objectives.
- Incorporating Agile practices in CMMI: Organizations can incorporate Agile practices, such as sprint planning and daily stand-up meetings, into their CMMI processes. This can help make their processes more flexible, iterative, and responsive to customer needs.
- Using CMMI to provide a framework for Agile: Organizations can use CMMI as a framework to provide structure and guidelines for their Agile processes. This can help ensure that Agile practices are implemented consistently and effectively across the organization.
CMMI and ISO
CMMI and ISO (International Organization for Standardization) are two popular frameworks used by organizations to improve their processes, products, and services. While CMMI is a process improvement framework that focuses on maturity levels and best practices, ISO is a family of standards that provide guidelines for quality management systems.
Although they have different approaches and methodologies, CMMI and ISO can be complementary, and many organizations have successfully combined the two frameworks to improve their processes and products.
Here are some ways in which CMMI and ISO can be used together:
- Combining CMMI with ISO 9001: ISO 9001 is a standard that provides guidelines for quality management systems. Organizations can combine CMMI and ISO 9001 to improve their processes and achieve their quality objectives. By adopting CMMI best practices and ISO 9001 guidelines, organizations can improve their process efficiency, product quality, and customer satisfaction.
- Using CMMI to achieve ISO 27001: ISO 27001 is a standard that provides guidelines for information security management systems. Organizations can use CMMI to achieve their ISO 27001 objectives by adopting CMMI best practices for risk management, security management, and configuration management.
- Incorporating ISO standards in CMMI: Organizations can incorporate ISO standards, such as ISO 9001 and ISO 27001, in their CMMI processes. This can help ensure that their processes comply with international standards and guidelines.
- Using CMMI to provide a framework for ISO: Organizations can use CMMI as a framework to provide structure and guidelines for their ISO processes. This can help ensure that ISO standards are implemented consistently and effectively across the organization.
How to obtain the CMMI certification?
We are an Education Technology company providing certification training courses to accelerate careers of working professionals worldwide. We impart training through instructor-led classroom workshops, instructor-led live virtual training sessions, and self-paced e-learning courses.
We have successfully conducted training sessions in 108 countries across the globe and enabled thousands of working professionals to enhance the scope of their careers.
Our enterprise training portfolio includes in-demand and globally recognized certification training courses in Project Management, Quality Management, Business Analysis, IT Service Management, Agile and Scrum, Cyber Security, Data Science, and Emerging Technologies. Download our Enterprise Training Catalog from https://www.icertglobal.com/corporate-training-for-enterprises.php
Popular Courses include:
- Project Management: PMP, CAPM ,PMI RMP
- Quality Management: Six Sigma Black Belt ,Lean Six Sigma Green Belt, Lean Management, Minitab ,CMMI
- Business Analysis: CBAP, CCBA, ECBA
- Agile Training: PMI-ACP
- Scrum Training: CSM
- DevOps
- Program Management: PgMP
- IT Service Management & Governance: COBIT, ISO
Case Studies
Here are some case studies of organizations that have successfully implemented CMMI:
- IBM: IBM has been using CMMI for over a decade to improve its software development processes. By adopting CMMI, IBM has been able to improve process efficiency, reduce costs, and improve product quality. IBM's software development division has achieved CMMI Level 5, the highest maturity level in the CMMI framework.
- Raytheon: Raytheon, a defense and aerospace company, has been using CMMI to improve its processes and products for over a decade. By adopting CMMI, Raytheon has been able to reduce defects, improve product quality, and increase customer satisfaction. Raytheon's software development division has achieved CMMI Level 5.
- Siemens: Siemens, a multinational conglomerate, has been using CMMI to improve its software development processes for over a decade. By adopting CMMI, Siemens has been able to improve process efficiency, reduce costs, and improve product quality. Siemens' software development division has achieved CMMI Level 3.
- Infosys: Infosys, a multinational IT services company, has been using CMMI to improve its processes and products for over a decade. By adopting CMMI, Infosys has been able to improve process efficiency, reduce defects, and improve customer satisfaction. Infosys' software development division has achieved CMMI Level 5.
- Boeing: Boeing, an aerospace company, has been using CMMI to improve its software development processes for over a decade. By adopting CMMI, Boeing has been able to reduce costs, improve process efficiency, and improve product quality. Boeing's software development division has achieved CMMI Level 3.
Conclusion
In conclusion, Capability Maturity Model Integration (CMMI) is a process improvement framework that can help organizations improve their processes, products, and services. By adopting CMMI best practices, organizations can increase their process efficiency, reduce costs, improve product quality, and increase customer satisfaction. CMMI provides a roadmap for organizations to identify and improve their weaknesses and achieve higher levels of process maturity.
CMMI also offers flexibility and scalability, allowing organizations to tailor their process improvement efforts to their specific needs and goals. Moreover, CMMI can be used in conjunction with other frameworks such as Agile and ISO to further enhance the benefits of process improvement efforts.
Through successful case studies of organizations such as IBM, Raytheon, Siemens, Infosys, and Boeing, we can see that CMMI is a valuable tool for achieving process excellence and improving organizational performance. By implementing CMMI, organizations can not only improve their bottom line but also create a culture of continuous improvement and innovation.
Exploring the Requirements for CTFL Certification: A Guide
The field of software testing plays a vital role in ensuring the quality and reliability of software applications. Aspiring software testers and professionals seeking to enhance their testing skills often turn to certification programs to validate their knowledge and expertise. One such certification is the CTFL (Certified Tester Foundation Level) certification, recognized globally as a benchmark for foundational software testing knowledge. In this guide, we will delve into the requirements and key aspects of CTFL certification, providing a comprehensive exploration of the pathway to becoming a certified software tester.
The guide begins by introducing the CTFL certification and its significance in the industry. It outlines the core knowledge areas covered by the certification, including testing principles, test techniques, test management, test tools and automation, and the overall test process. By understanding these knowledge areas, aspiring CTFL candidates can gain insights into the foundational skills and competencies required for successful software testing.
Furthermore, the guide explores the requirements for CTFL certification, including eligibility criteria and the certification process itself. It provides information on accredited organizations and training programs that offer CTFL preparation courses, equipping individuals with the necessary knowledge and skills to pass the CTFL exam. Readers will gain valuable insights into the exam format, the syllabus covered, and recommended study materials to aid in their exam preparation.
By exploring the requirements for CTFL certification, professionals can better understand the knowledge and expertise they need to demonstrate during the certification process. CTFL certification serves as a valuable credential, validating one's proficiency in foundational software testing principles and techniques. It not only enhances career prospects but also demonstrates a commitment to professional growth and excellence in the field of software testing.
Whether you are a novice tester looking to establish a solid foundation or an experienced professional aiming to formalize your expertise, exploring the requirements for CTFL certification is a crucial step. Join us on this journey as we navigate the core knowledge areas, certification process, and recommended resources to help you achieve your goal of becoming a certified software tester through CTFL certification.
Table of Contents
Introduction to CTFL Certification
ISTQB CTFL Exam Eligibility Criteria
ISTQB CTFL Exam
CTFL Exam Syllabus
Benefits of CTFL Certification
Conclusion
Introduction to CTFL Certification
The Certified Tester Foundation Level (CTFL) Certification is a globally recognized credential for software testers. It is designed to validate the fundamental knowledge and skills required for individuals working in the field of software testing. Whether you are a beginner or an experienced professional, obtaining the CTFL Certification can enhance your career prospects and demonstrate your competence in software testing.
CTFL Certification is offered by the International Software Testing Qualifications Board (ISTQB), which is a nonprofit organization dedicated to defining and maintaining a standard for software testing certifications worldwide. The ISTQB has established a comprehensive syllabus and examination process to ensure that certified professionals possess a solid understanding of essential testing concepts and techniques.
By pursuing CTFL Certification, individuals can gain a solid foundation in software testing principles and practices, enabling them to contribute effectively to the development and quality assurance processes within their organizations. The certification covers a wide range of topics, including test design, test execution, defect management, test management, and more. It equips professionals with the knowledge and skills necessary to excel in various roles within the software testing domain.
Benefits of CTFL Certification:
- Industry Recognition: CTFL Certification is widely recognized and respected by employers and industry professionals globally. It serves as a testament to your expertise and commitment to the field of software testing.
- Career Advancement: CTFL Certification can open doors to new career opportunities and enhance your prospects for promotion. It demonstrates your competence and increases your marketability in a competitive job market.
- Enhanced Skills: The certification process covers essential software testing knowledge areas, helping you develop a strong foundation in testing techniques, methodologies, and best practices. These skills can be applied to improve the quality of software products and increase overall efficiency in testing processes.
- Networking and Community: CTFL Certification allows you to join a community of certified professionals, providing opportunities for networking, knowledge sharing, and continuous learning. You can engage with peers, participate in forums, and attend industry events to stay updated with the latest trends and advancements in software testing.
- Professional Credibility: Having the CTFL Certification adds credibility to your profile and demonstrates your commitment to professional development. It reassures employers and clients that you possess the necessary skills and knowledge to contribute effectively to their testing projects.
Obtaining the CTFL Certification involves successfully passing a rigorous examination that assesses your understanding of software testing principles and practices. It is recommended to thoroughly prepare for the exam by studying the ISTQB syllabus, using recommended books and study materials, and practicing sample questions and mock tests.
In conclusion, the CTFL Certification is an internationally recognized credential that validates your proficiency in software testing. It offers numerous benefits, including industry recognition, career advancement opportunities, enhanced skills, networking possibilities, and increased professional credibility. By pursuing CTFL Certification, you can establish yourself as a competent software testing professional and enhance your career trajectory in the ever-evolving field of software development and quality assurance.
Certified Tester Foundation Level (CTFL) is a well-recognized certification program for software testers that provides a comprehensive understanding of the fundamentals of software testing. The CTFL certification is globally recognized as a standard for software testers, and it has become a mandatory requirement for many organizations when hiring software testers. The CTFL certification is designed to test the knowledge and skills of software testers in different areas of software testing, including testing techniques, software development models, test management, and testing tools.
This certification program provides software testers with a solid foundation in software testing methodologies and techniques, enabling them to identify defects and bugs in software applications more effectively. The certification program is suitable for both novice and experienced software testers who want to enhance their knowledge and skills in software testing.
In this article, we will provide an introduction to the Certified Tester Foundation Level (CTFL) certification program, its importance, and the benefits it offers to software testers. We will also cover the different areas of software testing covered in the CTFL certification program, as well as the eligibility requirements, the exam structure, and the study materials available for those interested in pursuing the CTFL certification.
CTFL Exam Eligibility Criteria
The eligibility criteria for the Certified Tester Foundation Level (CTFL) exam may vary slightly depending on the specific requirements set by the national or regional board administering the exam. However, here are some general eligibility guidelines:
- No Formal Education or Experience Requirements: There are typically no formal educational or professional experience prerequisites for taking the CTFL exam. It is open to anyone interested in software testing, whether they are beginners or experienced professionals.
- Recommended Knowledge: While there are no strict prerequisites, it is beneficial to have a basic understanding of software development and testing concepts. Familiarity with the software development lifecycle, testing terminology, and general IT knowledge can be advantageous in preparing for the exam.
- Training Courses: Some certification boards may require or recommend completing an accredited CTFL training course before taking the exam. These courses provide comprehensive coverage of the CTFL syllabus and can help candidates better understand the concepts and techniques required for the exam.
It's important to note that the specific eligibility criteria and prerequisites may differ depending on the certification board and country or region where you plan to take the CTFL exam. It is advisable to visit the official website of the certification board in your country or region to obtain the most accurate and up-to-date information regarding eligibility requirements.
Regardless of the eligibility criteria, it's essential to thoroughly study the CTFL syllabus, utilize recommended study materials, and practice with sample questions and mock exams to increase your chances of success in the CTFL certification journey.
CTFL Exam
The CTFL (Certified Tester Foundation Level) exam is a comprehensive assessment designed to evaluate the knowledge and understanding of individuals in the field of software testing. It tests their proficiency in fundamental testing concepts, techniques, and methodologies. Here are some key aspects of the CTFL exam:
Exam Format:
- The CTFL exam is typically a multiple-choice format exam, where candidates must choose the most appropriate answer from a set of options.
- The number of questions and the duration of the exam may vary depending on the certification board and exam provider. Generally, the exam consists of 40 to 60 questions.
- Some exam providers may offer online proctored exams that can be taken remotely, while others may require candidates to take the exam at designated testing centers.
Exam Content:
- The exam content is based on the CTFL syllabus developed by the International Software Testing Qualifications Board (ISTQB).
- The syllabus covers various knowledge areas, including software testing fundamentals, testing techniques, testing throughout the software lifecycle, test management, tools support for testing, and more.
- Candidates are expected to have a solid understanding of the concepts, terminology, and processes related to software testing.
Preparation Tips:
- Study the CTFL syllabus thoroughly: The syllabus outlines the topics and knowledge areas that will be covered in the exam. Ensure that you have a good grasp of the content and focus your preparation accordingly.
- Utilize study materials: There are numerous resources available, including textbooks, study guides, online courses, and practice exams. Utilize these materials to enhance your understanding of the subject matter and familiarize yourself with the exam format.
- Practice with sample questions: Solve sample questions and mock exams to get a feel for the types of questions you may encounter in the actual exam. This will help you improve your time management skills and identify areas where you need further study.
- Join study groups or forums: Engaging with fellow candidates or joining online study groups and forums can provide valuable insights, tips, and support during your exam preparation journey.
Exam Preparation Resources:
- ISTQB official website: The ISTQB website provides information about the CTFL certification, the syllabus, and sample questions. It is a valuable resource to start your preparation.
- Recommended books: There are several books available that cover the CTFL syllabus comprehensively. Some popular ones include "Foundations of Software Testing" by Dorothy Graham and Rex Black and "Software Testing: An ISTQB-BCS Certified Tester Foundation Guide" by Brian Hambling et al.
- Online courses: Many online platforms offer CTFL preparation courses, which include video lessons, quizzes, and practice exams. These courses can provide structured learning and help you track your progress.
CTFL Exam Syllabus
The Certified Tester Foundation Level (CTFL) exam syllabus is a comprehensive list of topics that a candidate needs to understand in order to pass the CTFL exam. The CTFL syllabus covers six main areas of software testing, as follows:
- Fundamentals of Testing
- The principles of testing
- The testing process
- Testing psychology
- Testing throughout the Software Development Lifecycle
- Software development models
- Test levels
- Test types
- Maintenance testing
- Static Techniques
- Review process
- Static analysis by tools
- Test Design Techniques
- Black-box test design techniques
- White-box test design techniques
- Experience-based techniques
- Test Management
- Test organization
- Test planning and estimation
- Test progress monitoring and control
- Configuration management
- Risk and testing
- Tool Support for Testing
- Types of testing tools
- Effective use of tools: potential benefits and risks
The CTFL syllabus provides a detailed description of each topic, along with the relevant learning objectives and subtopics. It is essential that candidates have a good understanding of each topic in the CTFL syllabus to pass the exam successfully.
It is important to note that the CTFL exam syllabus is updated periodically to ensure that it reflects the current trends and best practices in software testing. Candidates should refer to the latest version of the CTFL syllabus provided by the International Software Testing Qualifications Board (ISTQB) when preparing for the exam.
Benefits of CTFL Certification
The Certified Tester Foundation Level (CTFL) certification offers a wide range of benefits to software testers, including:
- Recognition of Knowledge and Skills: The CTFL certification demonstrates that a software tester has a comprehensive understanding of software testing principles and concepts. Employers value this certification and recognize it as a reliable indicator of a candidate's knowledge and skills in software testing.
- Enhanced Career Opportunities: The CTFL certification is recognized globally and opens up a wide range of career opportunities for software testers. Certified software testers can apply for jobs that require the CTFL certification, and employers often give priority to certified candidates during the hiring process.
- Increased Earning Potential: Certified software testers are in high demand, and they can command higher salaries than non-certified testers. The CTFL certification is a valuable asset that can help software testers negotiate higher salaries and better job benefits.
- Continuous Professional Development: The CTFL certification is just the beginning of a software tester's professional development journey. The certification provides a foundation for further learning and development in software testing, and certified testers can pursue more advanced certifications and training programs to enhance their skills and knowledge.
- International Recognition: The CTFL certification is recognized in over 100 countries worldwide, making it a valuable asset for software testers who want to work in different countries or with international clients. The certification demonstrates a tester's ability to work with a globally recognized standard of software testing.
How to obtain the CTFL certification?
We are an Education Technology company providing certification training courses to accelerate careers of working professionals worldwide. We impart training through instructor-led classroom workshops, instructor-led live virtual training sessions, and self-paced e-learning courses.
We have successfully conducted training sessions in 108 countries across the globe and enabled thousands of working professionals to enhance the scope of their careers.
Our enterprise training portfolio includes in-demand and globally recognized certification training courses in Project Management, Quality Management, Business Analysis, IT Service Management, Agile and Scrum, Cyber Security, Data Science, and Emerging Technologies. Download our Enterprise Training Catalog from https://www.icertglobal.com/corporate-training-for-enterprises.php
Popular Courses include:
- Project Management: PMP, CAPM ,PMI RMP
- Quality Management: Six Sigma Black Belt ,Lean Six Sigma Green Belt, Lean Management, Minitab , CTFL
- Business Analysis: CBAP, CCBA, ECBA
- Agile Training: PMI-ACP
- Scrum Training: CSM
- DevOps
- Program Management: PgMP
- IT Service Management & Governance: COBIT, ISO
Conclusion
In conclusion, the Certified Tester Foundation Level (CTFL) certification is a valuable credential for individuals in the field of software testing. It signifies a strong foundation in testing principles, techniques, and methodologies. By obtaining the CTFL certification, professionals can enhance their career prospects, demonstrate their competence, and contribute effectively to software testing projects.
Throughout this blog, we explored various aspects of the CTFL certification. We discussed the importance of the certification and its benefits, including industry recognition, career advancement opportunities, enhanced skills, networking possibilities, and increased professional credibility. We also delved into the eligibility criteria for the exam, highlighting that while there are typically no formal prerequisites, a basic understanding of software testing concepts is beneficial.
We covered the exam format, which is generally a multiple-choice format, and emphasized the importance of thorough preparation. To excel in the CTFL exam, it is crucial to study the CTFL syllabus, utilize recommended study materials, and practice with sample questions and mock exams. We provided tips for effective exam preparation, such as understanding the syllabus, utilizing study materials, practicing with sample questions, and engaging with study groups or forums.
By investing time and effort in preparing for the CTFL exam, individuals can gain a solid understanding of software testing principles, expand their knowledge base, and improve their testing skills. The CTFL certification serves as a testament to their expertise, professionalism, and commitment to quality in software testing.
In a rapidly evolving industry, the CTFL certification provides a strong foundation that can serve as a stepping stone to further advanced certifications and specialization in specific testing domains. It is an ongoing journey of professional development and continuous learning.
In conclusion, pursuing the CTFL certification can be a rewarding endeavor, opening doors to new opportunities and enhancing one's credibility as a software testing professional. Whether you are starting your career or seeking to advance in the field, the CTFL certification can provide a solid foundation for success in the dynamic and critical discipline of software testing.
Read More
The field of software testing plays a vital role in ensuring the quality and reliability of software applications. Aspiring software testers and professionals seeking to enhance their testing skills often turn to certification programs to validate their knowledge and expertise. One such certification is the CTFL (Certified Tester Foundation Level) certification, recognized globally as a benchmark for foundational software testing knowledge. In this guide, we will delve into the requirements and key aspects of CTFL certification, providing a comprehensive exploration of the pathway to becoming a certified software tester.
The guide begins by introducing the CTFL certification and its significance in the industry. It outlines the core knowledge areas covered by the certification, including testing principles, test techniques, test management, test tools and automation, and the overall test process. By understanding these knowledge areas, aspiring CTFL candidates can gain insights into the foundational skills and competencies required for successful software testing.
Furthermore, the guide explores the requirements for CTFL certification, including eligibility criteria and the certification process itself. It provides information on accredited organizations and training programs that offer CTFL preparation courses, equipping individuals with the necessary knowledge and skills to pass the CTFL exam. Readers will gain valuable insights into the exam format, the syllabus covered, and recommended study materials to aid in their exam preparation.
By exploring the requirements for CTFL certification, professionals can better understand the knowledge and expertise they need to demonstrate during the certification process. CTFL certification serves as a valuable credential, validating one's proficiency in foundational software testing principles and techniques. It not only enhances career prospects but also demonstrates a commitment to professional growth and excellence in the field of software testing.
Whether you are a novice tester looking to establish a solid foundation or an experienced professional aiming to formalize your expertise, exploring the requirements for CTFL certification is a crucial step. Join us on this journey as we navigate the core knowledge areas, certification process, and recommended resources to help you achieve your goal of becoming a certified software tester through CTFL certification.
Table of Contents
Introduction to CTFL Certification
ISTQB CTFL Exam Eligibility Criteria
ISTQB CTFL Exam
CTFL Exam Syllabus
Benefits of CTFL Certification
Conclusion
Introduction to CTFL Certification
The Certified Tester Foundation Level (CTFL) Certification is a globally recognized credential for software testers. It is designed to validate the fundamental knowledge and skills required for individuals working in the field of software testing. Whether you are a beginner or an experienced professional, obtaining the CTFL Certification can enhance your career prospects and demonstrate your competence in software testing.
CTFL Certification is offered by the International Software Testing Qualifications Board (ISTQB), which is a nonprofit organization dedicated to defining and maintaining a standard for software testing certifications worldwide. The ISTQB has established a comprehensive syllabus and examination process to ensure that certified professionals possess a solid understanding of essential testing concepts and techniques.
By pursuing CTFL Certification, individuals can gain a solid foundation in software testing principles and practices, enabling them to contribute effectively to the development and quality assurance processes within their organizations. The certification covers a wide range of topics, including test design, test execution, defect management, test management, and more. It equips professionals with the knowledge and skills necessary to excel in various roles within the software testing domain.
Benefits of CTFL Certification:
- Industry Recognition: CTFL Certification is widely recognized and respected by employers and industry professionals globally. It serves as a testament to your expertise and commitment to the field of software testing.
- Career Advancement: CTFL Certification can open doors to new career opportunities and enhance your prospects for promotion. It demonstrates your competence and increases your marketability in a competitive job market.
- Enhanced Skills: The certification process covers essential software testing knowledge areas, helping you develop a strong foundation in testing techniques, methodologies, and best practices. These skills can be applied to improve the quality of software products and increase overall efficiency in testing processes.
- Networking and Community: CTFL Certification allows you to join a community of certified professionals, providing opportunities for networking, knowledge sharing, and continuous learning. You can engage with peers, participate in forums, and attend industry events to stay updated with the latest trends and advancements in software testing.
- Professional Credibility: Having the CTFL Certification adds credibility to your profile and demonstrates your commitment to professional development. It reassures employers and clients that you possess the necessary skills and knowledge to contribute effectively to their testing projects.
Obtaining the CTFL Certification involves successfully passing a rigorous examination that assesses your understanding of software testing principles and practices. It is recommended to thoroughly prepare for the exam by studying the ISTQB syllabus, using recommended books and study materials, and practicing sample questions and mock tests.
In conclusion, the CTFL Certification is an internationally recognized credential that validates your proficiency in software testing. It offers numerous benefits, including industry recognition, career advancement opportunities, enhanced skills, networking possibilities, and increased professional credibility. By pursuing CTFL Certification, you can establish yourself as a competent software testing professional and enhance your career trajectory in the ever-evolving field of software development and quality assurance.
Certified Tester Foundation Level (CTFL) is a well-recognized certification program for software testers that provides a comprehensive understanding of the fundamentals of software testing. The CTFL certification is globally recognized as a standard for software testers, and it has become a mandatory requirement for many organizations when hiring software testers. The CTFL certification is designed to test the knowledge and skills of software testers in different areas of software testing, including testing techniques, software development models, test management, and testing tools.
This certification program provides software testers with a solid foundation in software testing methodologies and techniques, enabling them to identify defects and bugs in software applications more effectively. The certification program is suitable for both novice and experienced software testers who want to enhance their knowledge and skills in software testing.
In this article, we will provide an introduction to the Certified Tester Foundation Level (CTFL) certification program, its importance, and the benefits it offers to software testers. We will also cover the different areas of software testing covered in the CTFL certification program, as well as the eligibility requirements, the exam structure, and the study materials available for those interested in pursuing the CTFL certification.
CTFL Exam Eligibility Criteria
The eligibility criteria for the Certified Tester Foundation Level (CTFL) exam may vary slightly depending on the specific requirements set by the national or regional board administering the exam. However, here are some general eligibility guidelines:
- No Formal Education or Experience Requirements: There are typically no formal educational or professional experience prerequisites for taking the CTFL exam. It is open to anyone interested in software testing, whether they are beginners or experienced professionals.
- Recommended Knowledge: While there are no strict prerequisites, it is beneficial to have a basic understanding of software development and testing concepts. Familiarity with the software development lifecycle, testing terminology, and general IT knowledge can be advantageous in preparing for the exam.
- Training Courses: Some certification boards may require or recommend completing an accredited CTFL training course before taking the exam. These courses provide comprehensive coverage of the CTFL syllabus and can help candidates better understand the concepts and techniques required for the exam.
It's important to note that the specific eligibility criteria and prerequisites may differ depending on the certification board and country or region where you plan to take the CTFL exam. It is advisable to visit the official website of the certification board in your country or region to obtain the most accurate and up-to-date information regarding eligibility requirements.
Regardless of the eligibility criteria, it's essential to thoroughly study the CTFL syllabus, utilize recommended study materials, and practice with sample questions and mock exams to increase your chances of success in the CTFL certification journey.
CTFL Exam
The CTFL (Certified Tester Foundation Level) exam is a comprehensive assessment designed to evaluate the knowledge and understanding of individuals in the field of software testing. It tests their proficiency in fundamental testing concepts, techniques, and methodologies. Here are some key aspects of the CTFL exam:
Exam Format:
- The CTFL exam is typically a multiple-choice format exam, where candidates must choose the most appropriate answer from a set of options.
- The number of questions and the duration of the exam may vary depending on the certification board and exam provider. Generally, the exam consists of 40 to 60 questions.
- Some exam providers may offer online proctored exams that can be taken remotely, while others may require candidates to take the exam at designated testing centers.
Exam Content:
- The exam content is based on the CTFL syllabus developed by the International Software Testing Qualifications Board (ISTQB).
- The syllabus covers various knowledge areas, including software testing fundamentals, testing techniques, testing throughout the software lifecycle, test management, tools support for testing, and more.
- Candidates are expected to have a solid understanding of the concepts, terminology, and processes related to software testing.
Preparation Tips:
- Study the CTFL syllabus thoroughly: The syllabus outlines the topics and knowledge areas that will be covered in the exam. Ensure that you have a good grasp of the content and focus your preparation accordingly.
- Utilize study materials: There are numerous resources available, including textbooks, study guides, online courses, and practice exams. Utilize these materials to enhance your understanding of the subject matter and familiarize yourself with the exam format.
- Practice with sample questions: Solve sample questions and mock exams to get a feel for the types of questions you may encounter in the actual exam. This will help you improve your time management skills and identify areas where you need further study.
- Join study groups or forums: Engaging with fellow candidates or joining online study groups and forums can provide valuable insights, tips, and support during your exam preparation journey.
Exam Preparation Resources:
- ISTQB official website: The ISTQB website provides information about the CTFL certification, the syllabus, and sample questions. It is a valuable resource to start your preparation.
- Recommended books: There are several books available that cover the CTFL syllabus comprehensively. Some popular ones include "Foundations of Software Testing" by Dorothy Graham and Rex Black and "Software Testing: An ISTQB-BCS Certified Tester Foundation Guide" by Brian Hambling et al.
- Online courses: Many online platforms offer CTFL preparation courses, which include video lessons, quizzes, and practice exams. These courses can provide structured learning and help you track your progress.
CTFL Exam Syllabus
The Certified Tester Foundation Level (CTFL) exam syllabus is a comprehensive list of topics that a candidate needs to understand in order to pass the CTFL exam. The CTFL syllabus covers six main areas of software testing, as follows:
- Fundamentals of Testing
- The principles of testing
- The testing process
- Testing psychology
- Testing throughout the Software Development Lifecycle
- Software development models
- Test levels
- Test types
- Maintenance testing
- Static Techniques
- Review process
- Static analysis by tools
- Test Design Techniques
- Black-box test design techniques
- White-box test design techniques
- Experience-based techniques
- Test Management
- Test organization
- Test planning and estimation
- Test progress monitoring and control
- Configuration management
- Risk and testing
- Tool Support for Testing
- Types of testing tools
- Effective use of tools: potential benefits and risks
The CTFL syllabus provides a detailed description of each topic, along with the relevant learning objectives and subtopics. It is essential that candidates have a good understanding of each topic in the CTFL syllabus to pass the exam successfully.
It is important to note that the CTFL exam syllabus is updated periodically to ensure that it reflects the current trends and best practices in software testing. Candidates should refer to the latest version of the CTFL syllabus provided by the International Software Testing Qualifications Board (ISTQB) when preparing for the exam.
Benefits of CTFL Certification
The Certified Tester Foundation Level (CTFL) certification offers a wide range of benefits to software testers, including:
- Recognition of Knowledge and Skills: The CTFL certification demonstrates that a software tester has a comprehensive understanding of software testing principles and concepts. Employers value this certification and recognize it as a reliable indicator of a candidate's knowledge and skills in software testing.
- Enhanced Career Opportunities: The CTFL certification is recognized globally and opens up a wide range of career opportunities for software testers. Certified software testers can apply for jobs that require the CTFL certification, and employers often give priority to certified candidates during the hiring process.
- Increased Earning Potential: Certified software testers are in high demand, and they can command higher salaries than non-certified testers. The CTFL certification is a valuable asset that can help software testers negotiate higher salaries and better job benefits.
- Continuous Professional Development: The CTFL certification is just the beginning of a software tester's professional development journey. The certification provides a foundation for further learning and development in software testing, and certified testers can pursue more advanced certifications and training programs to enhance their skills and knowledge.
- International Recognition: The CTFL certification is recognized in over 100 countries worldwide, making it a valuable asset for software testers who want to work in different countries or with international clients. The certification demonstrates a tester's ability to work with a globally recognized standard of software testing.
How to obtain the CTFL certification?
We are an Education Technology company providing certification training courses to accelerate careers of working professionals worldwide. We impart training through instructor-led classroom workshops, instructor-led live virtual training sessions, and self-paced e-learning courses.
We have successfully conducted training sessions in 108 countries across the globe and enabled thousands of working professionals to enhance the scope of their careers.
Our enterprise training portfolio includes in-demand and globally recognized certification training courses in Project Management, Quality Management, Business Analysis, IT Service Management, Agile and Scrum, Cyber Security, Data Science, and Emerging Technologies. Download our Enterprise Training Catalog from https://www.icertglobal.com/corporate-training-for-enterprises.php
Popular Courses include:
- Project Management: PMP, CAPM ,PMI RMP
- Quality Management: Six Sigma Black Belt ,Lean Six Sigma Green Belt, Lean Management, Minitab , CTFL
- Business Analysis: CBAP, CCBA, ECBA
- Agile Training: PMI-ACP
- Scrum Training: CSM
- DevOps
- Program Management: PgMP
- IT Service Management & Governance: COBIT, ISO
Conclusion
In conclusion, the Certified Tester Foundation Level (CTFL) certification is a valuable credential for individuals in the field of software testing. It signifies a strong foundation in testing principles, techniques, and methodologies. By obtaining the CTFL certification, professionals can enhance their career prospects, demonstrate their competence, and contribute effectively to software testing projects.
Throughout this blog, we explored various aspects of the CTFL certification. We discussed the importance of the certification and its benefits, including industry recognition, career advancement opportunities, enhanced skills, networking possibilities, and increased professional credibility. We also delved into the eligibility criteria for the exam, highlighting that while there are typically no formal prerequisites, a basic understanding of software testing concepts is beneficial.
We covered the exam format, which is generally a multiple-choice format, and emphasized the importance of thorough preparation. To excel in the CTFL exam, it is crucial to study the CTFL syllabus, utilize recommended study materials, and practice with sample questions and mock exams. We provided tips for effective exam preparation, such as understanding the syllabus, utilizing study materials, practicing with sample questions, and engaging with study groups or forums.
By investing time and effort in preparing for the CTFL exam, individuals can gain a solid understanding of software testing principles, expand their knowledge base, and improve their testing skills. The CTFL certification serves as a testament to their expertise, professionalism, and commitment to quality in software testing.
In a rapidly evolving industry, the CTFL certification provides a strong foundation that can serve as a stepping stone to further advanced certifications and specialization in specific testing domains. It is an ongoing journey of professional development and continuous learning.
In conclusion, pursuing the CTFL certification can be a rewarding endeavor, opening doors to new opportunities and enhancing one's credibility as a software testing professional. Whether you are starting your career or seeking to advance in the field, the CTFL certification can provide a solid foundation for success in the dynamic and critical discipline of software testing.
Minitab guide: Benefits, features, and Excel comparison.
In the realm of statistical analysis and data management, professionals are often faced with the choice between using dedicated statistical software like Minitab or relying on the familiar Excel spreadsheet tool. "A Comprehensive Guide to Minitab: Benefits vs Excel" aims to provide a comprehensive resource that explores the capabilities, advantages, and key differences between these two powerful tools.
Minitab is a specialized statistical software designed specifically for data analysis, quality improvement, and process optimization. With its robust features and extensive range of statistical techniques, Minitab offers professionals a dedicated platform to perform complex statistical analyses, conduct hypothesis testing, create visualizations, build predictive models, and more. This guide will delve into the various functionalities and features of Minitab, offering step-by-step instructions and practical examples to help users leverage its power effectively.
On the other hand, Excel, a widely used spreadsheet software, also offers some basic statistical functions and data analysis capabilities. With its familiarity and ease of use, Excel has become a popular choice for handling data and conducting simple analyses. However, when it comes to advanced statistical analysis and specialized techniques, Excel may have limitations compared to Minitab.
This comprehensive guide will delve into the benefits and advantages of using Minitab over Excel for statistical analysis tasks. It will explore the statistical accuracy, user-friendliness, automation and customization options, collaboration features, and integration capabilities that set Minitab apart. Additionally, it will address the training and support available for Minitab users and provide insights into the cost-effectiveness of utilizing Minitab in comparison to Excel.
Whether you are a quality professional, data analyst, researcher, or anyone involved in statistical analysis and data-driven decision making, this guide will equip you with the knowledge and understanding needed to make an informed choice between Minitab and Excel. Prepare to explore the depths of Minitab's capabilities and discover how it can empower you to unlock greater insights, drive quality improvements, and make more informed decisions based on data.
Embark on your journey to mastering Minitab and gaining a comprehensive understanding of its benefits over Excel with "A Comprehensive Guide to Minitab: Benefits vs Excel."
Table of Contents
MiniTab in Six Sigma
Benefits of MiniTab
MiniTab vs. Excel
Key Features of Minitab
Our Learners Also Asked
Conclusion
Minitab is a powerful statistical software package widely used by researchers, analysts, and data scientists to perform data analysis, process improvement, and quality control. This software provides a user-friendly interface and a comprehensive set of tools for data analysis, visualization, and modeling. With its vast collection of statistical techniques, Minitab has become an indispensable tool for professionals working in various fields, including healthcare, manufacturing, engineering, and finance. In this article, we will explore the features and benefits of Minitab, and explain how it can be used to perform various statistical analyses and process improvements. Whether you are a seasoned data analyst or a beginner, this introduction to Minitab will provide you with the knowledge and skills necessary to leverage this software for your data analysis needs.
MiniTab in Six Sigma
Minitab is a statistical software package that is widely used in the field of Six Sigma, a methodology for process improvement that aims to reduce defects and variations in production processes. With its comprehensive set of statistical tools and data analysis capabilities, Minitab is an essential tool for Six Sigma practitioners, helping them to identify and analyze critical factors that impact the quality of products or services. Some of the key features of Minitab that are particularly useful for Six Sigma include hypothesis testing, statistical process control, design of experiments, and regression analysis. By leveraging Minitab, Six Sigma professionals can make data-driven decisions and optimize their processes, resulting in increased efficiency, cost savings, and improved customer satisfaction. Whether you are a Six Sigma practitioner or a quality control professional, Minitab can help you achieve your goals and drive continuous improvement in your organization.
Benefits of MiniTab
Minitab is a powerful statistical software package that provides numerous benefits to data analysts, researchers, and quality control professionals. Its comprehensive set of tools and user-friendly interface make it an indispensable tool for data analysis, visualization, and modeling. Some of the key benefits of Minitab include:
- Improved efficiency: Minitab's automation and streamlined workflows allow users to quickly and easily perform data analysis, saving time and improving productivity.
- Accurate data analysis: Minitab's advanced statistical techniques and data visualization tools enable users to accurately analyze and interpret data, leading to more informed decision-making.
- Process improvement: Minitab's statistical process control, design of experiments, and quality tools enable users to identify and improve critical factors that impact the quality of products and services, leading to process improvements and cost savings.
- Flexibility: Minitab is compatible with a wide range of data formats and can be used for data analysis in various fields, including healthcare, manufacturing, engineering, and finance.
- User-friendly interface: Minitab's intuitive interface and easy-to-use features make it accessible to users of all levels of expertise, from beginners to advanced data analysts.
MiniTab vs. Excel
Minitab and Excel are both powerful tools for data analysis, but they differ in terms of their capabilities, features, and intended use. While Excel is a widely used spreadsheet software that provides basic data analysis and visualization capabilities, Minitab is a specialized statistical software package that offers a more comprehensive set of tools for data analysis and process improvement.
Some of the key differences between Minitab and Excel include:
- Statistical analysis: Minitab offers a wide range of statistical techniques and data analysis tools that are specifically designed for data analysis and process improvement, including statistical process control, design of experiments, and regression analysis. Excel, on the other hand, provides limited statistical capabilities, which are mostly limited to basic descriptive statistics and data visualization.
- Ease of use: Minitab is designed to be user-friendly and intuitive, with a streamlined interface and clear workflows. Excel can be more complex to use, particularly for users who are not familiar with its advanced features.
- Data visualization: Minitab provides a comprehensive set of data visualization tools, including scatterplots, histograms, boxplots, and control charts, which can be used to analyze data and communicate insights effectively. While Excel also provides basic data visualization capabilities, it may not be as powerful or flexible as Minitab.
- Process improvement: Minitab offers a range of process improvement tools, including process mapping, failure mode and effects analysis, and design of experiments, which are not available in Excel. These tools are designed to help organizations identify and eliminate sources of process variation, leading to improved quality and efficiency.
Key Features of Minitab , with long-tailed keywords
Minitab is a comprehensive statistical software package that provides a wide range of tools for data analysis, visualization, and modeling. Some of the key features of Minitab include:
- Statistical analysis: Minitab offers a comprehensive set of statistical techniques, including hypothesis testing, regression analysis, analysis of variance (ANOVA), and time series analysis. These tools enable users to accurately analyze and interpret data and make data-driven decisions.
- Data visualization: Minitab provides a range of data visualization tools, including scatterplots, histograms, boxplots, and control charts, which enable users to effectively analyze and communicate insights from their data.
- Process improvement: Minitab offers a range of process improvement tools, including statistical process control (SPC), design of experiments (DOE), and quality tools, which are specifically designed to help organizations identify and eliminate sources of process variation, leading to improved quality and efficiency.
- Automation: Minitab provides automation features that enable users to perform repetitive tasks quickly and easily, saving time and improving productivity.
- Compatibility: Minitab is compatible with a wide range of data formats, including Excel, CSV, and text files, and can be used on both Windows and Mac operating systems.
- User-friendly interface: Minitab's intuitive interface and easy-to-use features make it accessible to users of all levels of expertise, from beginners to advanced data analysts.
- Customization: Minitab allows users to customize their analysis and reporting workflows to meet their specific needs, enabling them to tailor the software to their unique requirements.
How to obtain the Minitab certification?
We are an Education Technology company providing certification training courses to accelerate careers of working professionals worldwide. We impart training through instructor-led classroom workshops, instructor-led live virtual training sessions, and self-paced e-learning courses.
We have successfully conducted training sessions in 108 countries across the globe and enabled thousands of working professionals to enhance the scope of their careers.
Our enterprise training portfolio includes in-demand and globally recognized certification training courses in Project Management, Quality Management, Business Analysis, IT Service Management, Agile and Scrum, Cyber Security, Data Science, and Emerging Technologies. Download our Enterprise Training Catalog from https://www.icertglobal.com/corporate-training-for-enterprises.php
Popular Courses include:
- Project Management: PMP, CAPM ,PMI RMP
- Quality Management: Six Sigma Black Belt ,Lean Six Sigma Green Belt, Lean Management, Minitab
- Business Analysis: CBAP, CCBA, ECBA
- Agile Training: PMI-ACP
- Scrum Training: CSM
- DevOps
- Program Management: PgMP
- IT Service Management & Governance: COBIT, ISO
Our Learners Also Asked
What is Minitab Software used for?
Minitab is a statistical software package that is used for data analysis, process improvement, and quality control. It provides a wide range of statistical techniques and data analysis tools, including descriptive statistics, hypothesis testing, regression analysis, design of experiments (DOE), statistical process control (SPC), and quality control charts. Minitab is commonly used in industries such as manufacturing, healthcare, and engineering to analyze data and identify sources of variation in processes. The software also provides tools for process improvement, including Lean Six Sigma methodologies, to help organizations streamline processes, improve quality, and reduce costs. With its user-friendly interface, Minitab enables users to easily import data, perform statistical analyses, and visualize the results, allowing them to make data-driven decisions. Overall, Minitab is a powerful tool that provides statistical solutions to problems in many industries.
Is minitab same as excel?
Minitab and Excel are both software packages used for data analysis, but Minitab is a more specialized statistical software package, while Excel is a spreadsheet software. Minitab is designed specifically for statistical analysis and process improvement, providing a wide range of statistical techniques, user-friendly interfaces, and specialized process improvement tools. Excel, on the other hand, provides basic data analysis capabilities, limited statistical capabilities, and some data visualization tools, but it lacks the specialized tools and advanced statistical techniques that Minitab provides. Overall, Minitab is a more powerful and comprehensive tool for users in fields such as manufacturing, healthcare, and engineering, while Excel is more suitable for basic data analysis and visualization tasks.
What type of software is minitab?
Minitab is a statistical software package that is used for data analysis, process improvement, and quality control. It is a specialized software that provides a wide range of statistical tools and techniques to analyze and interpret data. Minitab is designed to assist professionals in various industries, such as manufacturing, healthcare, and engineering, to improve their processes and products by identifying and eliminating sources of variation. With its user-friendly interface, Minitab enables users to easily import data, perform statistical analyses, and visualize the results, allowing them to make data-driven decisions. Overall, Minitab is a powerful tool that provides statistical solutions to problems in many industries.
What Is The Difference Between Minitab and SPSS?
Minitab and SPSS are both statistical software packages used for data analysis, but they differ in their focus, features, and intended use. Minitab is specialized in process improvement and quality control, providing tools such as Statistical Process Control (SPC) and Design of Experiments (DOE), while SPSS is geared towards social science research and provides specialized tools such as factor analysis, cluster analysis, and categorical data analysis. Minitab has a more user-friendly interface, whereas SPSS provides a more comprehensive set of data management tools. Minitab is generally less expensive than SPSS, making it more accessible for small businesses or individuals who need statistical analysis tools. The choice between Minitab and SPSS ultimately depends on the user's needs and the type of data analysis tasks they are working on.
Is minitab a programming language?
No, Minitab is not a programming language, but rather a statistical software package that provides a user-friendly interface for statistical analysis and data visualization. It provides a wide range of statistical tools and techniques that can be used by professionals in various industries to analyze and interpret data, and make data-driven decisions. Minitab does not require users to write programming code, but it provides a command-line interface that allows users to execute statistical analyses and produce reports. Users can also use macros in Minitab, which are pre-programmed sets of commands that automate repetitive tasks. However, Minitab is primarily designed to be a point-and-click software, so users can perform most of the analyses and operations by selecting the appropriate menus and options from the user interface.
Conclusion
In conclusion, Minitab is a powerful statistical software package that provides a wide range of data analysis and process improvement tools. It is specialized in process improvement and quality control and is commonly used in industries such as manufacturing, healthcare, and engineering. Minitab provides a user-friendly interface that allows users to easily import data, perform statistical analyses, and visualize the results, without requiring them to write programming code. While Minitab and SPSS are both statistical software packages, they differ in their focus, features, and intended use. Minitab is less expensive than SPSS and is an excellent choice for small businesses or individuals who need statistical analysis tools. Overall, Minitab is a versatile tool that can help organizations streamline processes, improve quality, and reduce costs by making data-driven decisions.
Read More
In the realm of statistical analysis and data management, professionals are often faced with the choice between using dedicated statistical software like Minitab or relying on the familiar Excel spreadsheet tool. "A Comprehensive Guide to Minitab: Benefits vs Excel" aims to provide a comprehensive resource that explores the capabilities, advantages, and key differences between these two powerful tools.
Minitab is a specialized statistical software designed specifically for data analysis, quality improvement, and process optimization. With its robust features and extensive range of statistical techniques, Minitab offers professionals a dedicated platform to perform complex statistical analyses, conduct hypothesis testing, create visualizations, build predictive models, and more. This guide will delve into the various functionalities and features of Minitab, offering step-by-step instructions and practical examples to help users leverage its power effectively.
On the other hand, Excel, a widely used spreadsheet software, also offers some basic statistical functions and data analysis capabilities. With its familiarity and ease of use, Excel has become a popular choice for handling data and conducting simple analyses. However, when it comes to advanced statistical analysis and specialized techniques, Excel may have limitations compared to Minitab.
This comprehensive guide will delve into the benefits and advantages of using Minitab over Excel for statistical analysis tasks. It will explore the statistical accuracy, user-friendliness, automation and customization options, collaboration features, and integration capabilities that set Minitab apart. Additionally, it will address the training and support available for Minitab users and provide insights into the cost-effectiveness of utilizing Minitab in comparison to Excel.
Whether you are a quality professional, data analyst, researcher, or anyone involved in statistical analysis and data-driven decision making, this guide will equip you with the knowledge and understanding needed to make an informed choice between Minitab and Excel. Prepare to explore the depths of Minitab's capabilities and discover how it can empower you to unlock greater insights, drive quality improvements, and make more informed decisions based on data.
Embark on your journey to mastering Minitab and gaining a comprehensive understanding of its benefits over Excel with "A Comprehensive Guide to Minitab: Benefits vs Excel."
Table of Contents
MiniTab in Six Sigma
Benefits of MiniTab
MiniTab vs. Excel
Key Features of Minitab
Our Learners Also Asked
Conclusion
Minitab is a powerful statistical software package widely used by researchers, analysts, and data scientists to perform data analysis, process improvement, and quality control. This software provides a user-friendly interface and a comprehensive set of tools for data analysis, visualization, and modeling. With its vast collection of statistical techniques, Minitab has become an indispensable tool for professionals working in various fields, including healthcare, manufacturing, engineering, and finance. In this article, we will explore the features and benefits of Minitab, and explain how it can be used to perform various statistical analyses and process improvements. Whether you are a seasoned data analyst or a beginner, this introduction to Minitab will provide you with the knowledge and skills necessary to leverage this software for your data analysis needs.
MiniTab in Six Sigma
Minitab is a statistical software package that is widely used in the field of Six Sigma, a methodology for process improvement that aims to reduce defects and variations in production processes. With its comprehensive set of statistical tools and data analysis capabilities, Minitab is an essential tool for Six Sigma practitioners, helping them to identify and analyze critical factors that impact the quality of products or services. Some of the key features of Minitab that are particularly useful for Six Sigma include hypothesis testing, statistical process control, design of experiments, and regression analysis. By leveraging Minitab, Six Sigma professionals can make data-driven decisions and optimize their processes, resulting in increased efficiency, cost savings, and improved customer satisfaction. Whether you are a Six Sigma practitioner or a quality control professional, Minitab can help you achieve your goals and drive continuous improvement in your organization.
Benefits of MiniTab
Minitab is a powerful statistical software package that provides numerous benefits to data analysts, researchers, and quality control professionals. Its comprehensive set of tools and user-friendly interface make it an indispensable tool for data analysis, visualization, and modeling. Some of the key benefits of Minitab include:
- Improved efficiency: Minitab's automation and streamlined workflows allow users to quickly and easily perform data analysis, saving time and improving productivity.
- Accurate data analysis: Minitab's advanced statistical techniques and data visualization tools enable users to accurately analyze and interpret data, leading to more informed decision-making.
- Process improvement: Minitab's statistical process control, design of experiments, and quality tools enable users to identify and improve critical factors that impact the quality of products and services, leading to process improvements and cost savings.
- Flexibility: Minitab is compatible with a wide range of data formats and can be used for data analysis in various fields, including healthcare, manufacturing, engineering, and finance.
- User-friendly interface: Minitab's intuitive interface and easy-to-use features make it accessible to users of all levels of expertise, from beginners to advanced data analysts.
MiniTab vs. Excel
Minitab and Excel are both powerful tools for data analysis, but they differ in terms of their capabilities, features, and intended use. While Excel is a widely used spreadsheet software that provides basic data analysis and visualization capabilities, Minitab is a specialized statistical software package that offers a more comprehensive set of tools for data analysis and process improvement.
Some of the key differences between Minitab and Excel include:
- Statistical analysis: Minitab offers a wide range of statistical techniques and data analysis tools that are specifically designed for data analysis and process improvement, including statistical process control, design of experiments, and regression analysis. Excel, on the other hand, provides limited statistical capabilities, which are mostly limited to basic descriptive statistics and data visualization.
- Ease of use: Minitab is designed to be user-friendly and intuitive, with a streamlined interface and clear workflows. Excel can be more complex to use, particularly for users who are not familiar with its advanced features.
- Data visualization: Minitab provides a comprehensive set of data visualization tools, including scatterplots, histograms, boxplots, and control charts, which can be used to analyze data and communicate insights effectively. While Excel also provides basic data visualization capabilities, it may not be as powerful or flexible as Minitab.
- Process improvement: Minitab offers a range of process improvement tools, including process mapping, failure mode and effects analysis, and design of experiments, which are not available in Excel. These tools are designed to help organizations identify and eliminate sources of process variation, leading to improved quality and efficiency.
Key Features of Minitab , with long-tailed keywords
Minitab is a comprehensive statistical software package that provides a wide range of tools for data analysis, visualization, and modeling. Some of the key features of Minitab include:
- Statistical analysis: Minitab offers a comprehensive set of statistical techniques, including hypothesis testing, regression analysis, analysis of variance (ANOVA), and time series analysis. These tools enable users to accurately analyze and interpret data and make data-driven decisions.
- Data visualization: Minitab provides a range of data visualization tools, including scatterplots, histograms, boxplots, and control charts, which enable users to effectively analyze and communicate insights from their data.
- Process improvement: Minitab offers a range of process improvement tools, including statistical process control (SPC), design of experiments (DOE), and quality tools, which are specifically designed to help organizations identify and eliminate sources of process variation, leading to improved quality and efficiency.
- Automation: Minitab provides automation features that enable users to perform repetitive tasks quickly and easily, saving time and improving productivity.
- Compatibility: Minitab is compatible with a wide range of data formats, including Excel, CSV, and text files, and can be used on both Windows and Mac operating systems.
- User-friendly interface: Minitab's intuitive interface and easy-to-use features make it accessible to users of all levels of expertise, from beginners to advanced data analysts.
- Customization: Minitab allows users to customize their analysis and reporting workflows to meet their specific needs, enabling them to tailor the software to their unique requirements.
How to obtain the Minitab certification?
We are an Education Technology company providing certification training courses to accelerate careers of working professionals worldwide. We impart training through instructor-led classroom workshops, instructor-led live virtual training sessions, and self-paced e-learning courses.
We have successfully conducted training sessions in 108 countries across the globe and enabled thousands of working professionals to enhance the scope of their careers.
Our enterprise training portfolio includes in-demand and globally recognized certification training courses in Project Management, Quality Management, Business Analysis, IT Service Management, Agile and Scrum, Cyber Security, Data Science, and Emerging Technologies. Download our Enterprise Training Catalog from https://www.icertglobal.com/corporate-training-for-enterprises.php
Popular Courses include:
- Project Management: PMP, CAPM ,PMI RMP
- Quality Management: Six Sigma Black Belt ,Lean Six Sigma Green Belt, Lean Management, Minitab
- Business Analysis: CBAP, CCBA, ECBA
- Agile Training: PMI-ACP
- Scrum Training: CSM
- DevOps
- Program Management: PgMP
- IT Service Management & Governance: COBIT, ISO
Our Learners Also Asked
What is Minitab Software used for?
Minitab is a statistical software package that is used for data analysis, process improvement, and quality control. It provides a wide range of statistical techniques and data analysis tools, including descriptive statistics, hypothesis testing, regression analysis, design of experiments (DOE), statistical process control (SPC), and quality control charts. Minitab is commonly used in industries such as manufacturing, healthcare, and engineering to analyze data and identify sources of variation in processes. The software also provides tools for process improvement, including Lean Six Sigma methodologies, to help organizations streamline processes, improve quality, and reduce costs. With its user-friendly interface, Minitab enables users to easily import data, perform statistical analyses, and visualize the results, allowing them to make data-driven decisions. Overall, Minitab is a powerful tool that provides statistical solutions to problems in many industries.
Is minitab same as excel?
Minitab and Excel are both software packages used for data analysis, but Minitab is a more specialized statistical software package, while Excel is a spreadsheet software. Minitab is designed specifically for statistical analysis and process improvement, providing a wide range of statistical techniques, user-friendly interfaces, and specialized process improvement tools. Excel, on the other hand, provides basic data analysis capabilities, limited statistical capabilities, and some data visualization tools, but it lacks the specialized tools and advanced statistical techniques that Minitab provides. Overall, Minitab is a more powerful and comprehensive tool for users in fields such as manufacturing, healthcare, and engineering, while Excel is more suitable for basic data analysis and visualization tasks.
What type of software is minitab?
Minitab is a statistical software package that is used for data analysis, process improvement, and quality control. It is a specialized software that provides a wide range of statistical tools and techniques to analyze and interpret data. Minitab is designed to assist professionals in various industries, such as manufacturing, healthcare, and engineering, to improve their processes and products by identifying and eliminating sources of variation. With its user-friendly interface, Minitab enables users to easily import data, perform statistical analyses, and visualize the results, allowing them to make data-driven decisions. Overall, Minitab is a powerful tool that provides statistical solutions to problems in many industries.
What Is The Difference Between Minitab and SPSS?
Minitab and SPSS are both statistical software packages used for data analysis, but they differ in their focus, features, and intended use. Minitab is specialized in process improvement and quality control, providing tools such as Statistical Process Control (SPC) and Design of Experiments (DOE), while SPSS is geared towards social science research and provides specialized tools such as factor analysis, cluster analysis, and categorical data analysis. Minitab has a more user-friendly interface, whereas SPSS provides a more comprehensive set of data management tools. Minitab is generally less expensive than SPSS, making it more accessible for small businesses or individuals who need statistical analysis tools. The choice between Minitab and SPSS ultimately depends on the user's needs and the type of data analysis tasks they are working on.
Is minitab a programming language?
No, Minitab is not a programming language, but rather a statistical software package that provides a user-friendly interface for statistical analysis and data visualization. It provides a wide range of statistical tools and techniques that can be used by professionals in various industries to analyze and interpret data, and make data-driven decisions. Minitab does not require users to write programming code, but it provides a command-line interface that allows users to execute statistical analyses and produce reports. Users can also use macros in Minitab, which are pre-programmed sets of commands that automate repetitive tasks. However, Minitab is primarily designed to be a point-and-click software, so users can perform most of the analyses and operations by selecting the appropriate menus and options from the user interface.
Conclusion
In conclusion, Minitab is a powerful statistical software package that provides a wide range of data analysis and process improvement tools. It is specialized in process improvement and quality control and is commonly used in industries such as manufacturing, healthcare, and engineering. Minitab provides a user-friendly interface that allows users to easily import data, perform statistical analyses, and visualize the results, without requiring them to write programming code. While Minitab and SPSS are both statistical software packages, they differ in their focus, features, and intended use. Minitab is less expensive than SPSS and is an excellent choice for small businesses or individuals who need statistical analysis tools. Overall, Minitab is a versatile tool that can help organizations streamline processes, improve quality, and reduce costs by making data-driven decisions.
The Essential Guide to Lean Management and Its Importance
The Essential Guide to Lean Management Certification and Methodologies and Importance is a comprehensive resource that outlines the significance of Lean management certification and explores the various methodologies associated with Lean principles. This guide serves as an invaluable tool for professionals aiming to enhance their skills and credentials in Lean management. It covers a range of Lean methodologies, including value stream mapping, Kaizen, Just-in-Time (JIT), Kanban, 5S Methodology, and more. By obtaining Lean management certification, individuals gain industry-recognized validation of their knowledge and expertise in Lean practices, opening doors to career advancement and increased opportunities. The guide emphasizes the importance of Lean management in driving operational excellence, waste reduction, and continuous improvement within organizations. It provides valuable insights into the certification process, training programs, exam preparation, and the benefits of achieving Lean certification. Whether you are an aspiring Lean practitioner or a seasoned professional, this guide equips you with the essential knowledge and resources to leverage Lean methodologies effectively and make a tangible impact in your organization.
Table of contents
-
Introduction to Lean Management
-
The Importance of Lean Management Certification
-
Lean Management Methodologies
-
Lean Management Certification Process
-
Benefits of Lean Management Certification for Organizations
-
Tips for Successfully Obtaining Lean Management Certification
-
Future Trends in Lean Management
-
Conclusion
Introduction to Lean Management
In an increasingly competitive and dynamic business environment, organizations are constantly seeking ways to improve efficiency, reduce waste, and enhance overall performance. One methodology that has gained significant traction in recent years is Lean Management. Originating from the renowned Toyota Production System, Lean Management has evolved into a widely adopted approach that focuses on streamlining processes, eliminating non-value-added activities, and fostering a culture of continuous improvement.
At its core, Lean Management is about maximizing customer value while minimizing waste. It provides organizations with a systematic framework to identify and eliminate activities that do not contribute to delivering value to customers. By doing so, Lean Management helps businesses enhance productivity, reduce costs, improve quality, and ultimately gain a competitive edge.
The principles of Lean Management are rooted in the pursuit of operational excellence. It emphasizes the importance of eliminating inefficiencies, bottlenecks, and defects that impede smooth operations. By adopting Lean Management principles and practices, organizations can achieve greater agility, flexibility, and responsiveness to customer needs.
In recognition of the immense value that Lean Management brings to businesses, many professionals seek Lean Management certification to enhance their skills and expertise in implementing Lean practices. In this blog, we will explore the various aspects of Lean Management certification, its benefits, the certification process, and its impact on both individuals and organizations.
Join us on this insightful journey into the world of Lean Management certification and discover how it can revolutionize your career and drive organizational success.
The Importance of Lean Management Certification
In today's competitive business landscape, organizations are constantly seeking professionals who possess the knowledge and expertise to drive process improvement, enhance efficiency, and streamline operations. This is where Lean Management certification becomes highly valuable. Let's explore the significance of obtaining a Lean Management certification and the advantages it brings to both individuals and organizations.
-
Enhancing Skills and Knowledge: Lean Management certification programs provide comprehensive training in Lean principles, methodologies, and tools. Through these programs, professionals gain a deep understanding of Lean concepts such as waste reduction, value stream mapping, Kaizen, and more. They acquire the skills necessary to identify process inefficiencies, implement improvements, and drive sustainable change within their organizations.
-
Validation of Expertise: Lean Management certification serves as a tangible validation of an individual's knowledge and proficiency in Lean practices. By obtaining a recognized certification, professionals demonstrate their commitment to continuous improvement and their ability to apply Lean principles effectively. This validation adds credibility to their expertise and distinguishes them as competent Lean practitioners.
-
Career Advancement: Lean Management certification significantly enhances career prospects. Organizations across various industries recognize the value of Lean Management and actively seek professionals who possess the necessary skills to lead Lean initiatives. Certification showcases an individual's dedication to professional growth and positions them as strong candidates for leadership roles, project management positions, and other career advancement opportunities.
-
Increased Employability: In a competitive job market, having Lean Management certification can give job seekers a distinct advantage. Employers often prioritize candidates who possess specialized certifications, as it indicates a higher level of expertise and a proven ability to contribute to process improvement efforts. Lean Management certification can open doors to new job opportunities and increase an individual's employability across a wide range of industries.
-
Organizational Impact: Lean Management certification not only benefits individuals but also has a positive impact on the organizations they serve. Certified professionals bring valuable skills and knowledge that can drive operational excellence, enhance productivity, and reduce waste within their organizations. They are equipped to identify process bottlenecks, implement Lean methodologies, and foster a culture of continuous improvement, leading to increased efficiency and customer satisfaction.
In summary, Lean Management certification is highly important in today's business world. It empowers professionals with the skills, knowledge, and credibility to implement Lean practices and drive organizational success. Whether you are seeking career advancement or aiming to make a significant impact within your organization, Lean Management certification can be a catalyst for personal and professional growth.
Lean Management Methodologies
Lean Management encompasses a variety of methodologies, each designed to address specific challenges and optimize different aspects of organizational processes. Understanding these methodologies is crucial for professionals seeking Lean Management certification. Let's explore some of the key Lean methodologies and their applications:
-
Six Sigma: Six Sigma combines Lean principles with statistical analysis to minimize process variation and defects. It aims to achieve near-perfect quality levels by identifying and eliminating root causes of errors and reducing process variability. Six Sigma follows a structured approach, employing the DMAIC (Define, Measure, Analyze, Improve, Control) framework for continuous improvement.
-
Kanban: Kanban is a visual scheduling and workflow management system. It utilizes visual signals, such as cards or digital boards, to track and manage the flow of work. Kanban promotes just-in-time production, eliminates overproduction, and ensures that work is pulled only when needed. This methodology enhances efficiency, reduces waste, and improves communication within teams.
-
Kaizen: Kaizen, meaning "continuous improvement" in Japanese, is a philosophy that emphasizes making incremental, small-scale improvements across all levels of an organization. It encourages employees to identify and implement process improvements on a regular basis. Kaizen fosters a culture of continuous learning, problem-solving, and employee engagement, leading to sustained improvements over time.
-
Value Stream Mapping: Value Stream Mapping (VSM) is a visual tool used to analyze and optimize the flow of materials and information through a process. It provides a holistic view of the entire value stream, identifying non-value-added activities, bottlenecks, and areas for improvement. VSM helps organizations streamline processes, reduce lead times, and enhance overall efficiency.
-
5S Methodology: The 5S methodology focuses on workplace organization and cleanliness. It consists of five principles: Sort, Set in Order, Shine, Standardize, and Sustain. By implementing these principles, organizations create organized, clutter-free work environments, improve visual management, and establish standardized processes. The 5S methodology contributes to increased productivity, safety, and employee morale.
-
Just-in-Time (JIT): Just-in-Time is a methodology that aims to minimize inventory levels and reduce waste by producing and delivering products or services at the precise time they are needed. JIT eliminates excess inventory, improves cash flow, and allows organizations to respond quickly to customer demands. This methodology requires efficient supply chain management and close collaboration with suppliers.
These are just a few examples of the Lean Management methodologies that professionals encounter during their Lean journey. Each methodology has its own set of tools and techniques, and their applicability may vary depending on the organizational context and objectives.
As you progress in your Lean Management certification, you will delve deeper into these methodologies, understand their principles, and learn how to apply them effectively to drive process improvements and achieve organizational excellence.
Lean Management Certification Process
Obtaining a Lean Management certification requires a systematic approach that typically involves specific steps and requirements. Understanding the certification process can help individuals plan their journey and maximize their chances of success. Let's explore the typical Lean Management certification process:
-
Research and Select Certification Program: Begin by researching different Lean Management certification programs available. Consider factors such as program reputation, accreditation, curriculum, and alignment with your career goals. Select a program that suits your needs and preferences.
-
Meet Eligibility Requirements: Each certification program may have specific eligibility requirements. Common prerequisites may include educational qualifications, professional experience, or completion of specific training courses. Ensure that you meet these requirements before proceeding with the certification process.
-
Enroll in Certification Training: Once you have selected a certification program, enroll in the relevant training courses. These courses are designed to provide you with the necessary knowledge and skills to understand Lean Management concepts, methodologies, and tools. Training options may include in-person workshops, online courses, or a combination of both.
-
Prepare for Certification Exam: Lean Management certifications typically require passing a comprehensive exam. Allocate sufficient time to study and review the materials covered in the training courses. Utilize study guides, practice exams, and other resources provided by the certification body or recommended by trainers. Additionally, leverage practical experience and real-life examples to reinforce your understanding of Lean Management principles.
-
Schedule and Take the Exam: Once you feel adequately prepared, schedule your certification exam. The exam format may vary depending on the certification program, but it is typically conducted in a proctored environment. Be sure to arrive well-prepared, well-rested, and with the necessary identification documents. Follow the exam instructions and pace yourself appropriately to complete all the required sections within the allotted time.
-
Await Certification Results: After completing the exam, you will need to wait for the certification body to review and assess your results. The waiting period varies depending on the program, but it typically ranges from a few days to a few weeks. During this time, the certification body evaluates your performance and determines whether you meet the passing criteria.
-
Receive Certification and Renewal: Upon successfully passing the exam, you will receive your Lean Management certification. Celebrate your accomplishment and proudly showcase your certification on your resume and professional profiles. Keep in mind that Lean Management certifications often have an expiration date. To maintain your certification, you may be required to fulfill certain continuing education or professional development requirements and renew your certification periodically.
Remember that the certification process may have slight variations depending on the specific certification program you choose. It is essential to review the certification body's guidelines and instructions for the most accurate and up-to-date information.
By following these steps and investing time and effort into your Lean Management certification journey, you can enhance your skills, expand your knowledge, and boost your professional credibility in the field of Lean Management.
Benefits of Lean Management Certification for Organizations
Lean Management certification offers numerous advantages to organizations that invest in training their employees and building a Lean culture. Let's explore the benefits that organizations can derive from having certified Lean Management professionals on their teams:
-
Improved Efficiency and Productivity: Lean Management certification equips professionals with the knowledge and skills to identify and eliminate waste in processes. Certified individuals can analyze workflows, identify bottlenecks, and implement Lean methodologies to streamline operations. By optimizing processes, organizations can achieve improved efficiency, reduce lead times, and increase overall productivity.
-
Enhanced Quality and Customer Satisfaction: Lean Management certification focuses on delivering value to customers by eliminating defects and improving quality. Certified professionals are trained to implement quality control measures, statistical analysis techniques, and error-proofing methods. This results in higher product and service quality, leading to increased customer satisfaction and loyalty.
-
Cost Reduction and Resource Optimization: Lean Management methodologies help organizations identify and eliminate non-value-added activities and excessive resource utilization. By implementing Lean principles, such as just-in-time production and inventory reduction, organizations can minimize costs associated with excess inventory, transportation, overproduction, and defects. Lean Management certification enables professionals to identify cost-saving opportunities and optimize resource allocation.
-
Streamlined Processes and Reduced Lead Time: Lean Management certification enables professionals to analyze and map value streams, identify process inefficiencies, and implement improvements. By eliminating non-value-added activities, reducing cycle times, and optimizing workflows, organizations can significantly reduce lead times. This leads to faster response to customer demands, shorter time-to-market, and increased competitiveness.
-
Culture of Continuous Improvement: Lean Management certification promotes a culture of continuous improvement within organizations. Certified professionals become catalysts for change and champions of Lean practices. They encourage and empower colleagues to identify and implement process improvements, fostering a culture of innovation, engagement, and continuous learning throughout the organization.
-
Effective Change Management: Lean Management certification equips professionals with skills in change management and stakeholder engagement. This enables them to effectively communicate Lean initiatives, overcome resistance to change, and engage stakeholders at all levels of the organization. Certified professionals can lead Lean projects, collaborate with cross-functional teams, and drive successful implementation of Lean methodologies.
-
Alignment with Strategic Objectives: Lean Management certification ensures that organizations align their operations with their strategic objectives. Certified professionals understand the importance of aligning Lean initiatives with the organization's mission, vision, and goals. They can effectively contribute to strategic planning, decision-making, and the achievement of organizational objectives.
In summary, Lean Management certification brings significant benefits to organizations. From improving efficiency and quality to reducing costs and lead times, organizations that invest in Lean Management training and certification can experience a positive impact on their bottom line and overall performance. By cultivating a Lean culture and harnessing the expertise of certified professionals, organizations can position themselves for sustained success in today's competitive business environment.
Tips for Successfully Obtaining Lean Management Certification
Obtaining Lean Management certification requires dedication, preparation, and a strategic approach. To maximize your chances of success, consider the following tips as you embark on your certification journey:
-
Understand Certification Requirements: Familiarize yourself with the specific requirements of the Lean Management certification program you have chosen. Review the eligibility criteria, prerequisites, and any recommended prior knowledge or experience. Ensure that you meet the requirements before proceeding further.
-
Choose the Right Training Program: Select a reputable and accredited training program that aligns with your learning style and preferences. Consider factors such as program content, delivery format (in-person or online), duration, and available resources. Look for programs that provide comprehensive coverage of Lean Management concepts, methodologies, and practical applications.
-
Dedicate Sufficient Time for Preparation: Lean Management certification exams can be comprehensive and challenging. Allocate dedicated time for studying and preparation. Create a study plan and schedule regular study sessions. Break down the content into manageable sections, and focus on understanding key concepts, tools, and techniques. Review and reinforce your learning through practice exams and quizzes.
-
Leverage Available Resources: Take advantage of the resources provided by the certification program or training provider. These may include study guides, textbooks, online materials, and practice exams. Engage with online forums or discussion groups related to Lean Management to seek clarification, share insights, and learn from the experiences of others.
-
Seek Practical Experience: While theoretical knowledge is essential, practical experience in applying Lean Management principles adds significant value to your certification journey. Look for opportunities within your organization or industry to participate in Lean projects, process improvement initiatives, or Kaizen events. Hands-on experience will deepen your understanding of Lean principles and enhance your ability to apply them effectively.
-
Collaborate and Learn from Others: Engage with a community of Lean Management professionals to broaden your perspective and learn from their experiences. Attend industry events, conferences, or workshops where you can network with like-minded individuals. Participate in online forums, LinkedIn groups, or professional associations focused on Lean Management. By sharing knowledge and exchanging ideas, you can gain valuable insights and stay updated on emerging trends.
-
Practice Time Management during the Exam: Time management is crucial during the certification exam. Familiarize yourself with the exam format and the allocated time for each section. Read questions carefully, and avoid spending too much time on any single question. If you encounter difficult questions, move on and return to them later. Manage your time effectively to ensure that you complete all sections within the given timeframe.
-
Stay Calm and Confident: On the day of the exam, maintain a calm and confident mindset. Trust in your preparation and the knowledge you have acquired. Practice relaxation techniques or mindfulness exercises to manage any exam-related stress or anxiety. Remember to read questions carefully, and answer them to the best of your ability based on your understanding of Lean Management principles.
By following these tips, you can enhance your readiness and increase your chances of successfully obtaining Lean Management certification. Remember that the certification journey is a continuous learning process, and it is the knowledge and skills gained along the way that truly matter.
How to obtain the Six Sigma Black Belt certification?
We are an Education Technology company providing certification training courses to accelerate careers of working professionals worldwide. We impart training through instructor-led classroom workshops, instructor-led live virtual training sessions, and self-paced e-learning courses.
We have successfully conducted training sessions in 108 countries across the globe and enabled thousands of working professionals to enhance the scope of their careers.
Our enterprise training portfolio includes in-demand and globally recognized certification training courses in Project Management, Quality Management, Business Analysis, IT Service Management, Agile and Scrum, Cyber Security, Data Science, and Emerging Technologies. Download our Enterprise Training Catalog from https://www.icertglobal.com/corporate-training-for-enterprises.php
Popular Courses include:
-
Project Management: PMP, CAPM ,PMI RMP
-
Quality Management: Six Sigma Black Belt ,Lean Six Sigma Green Belt, Lean Management
-
Business Analysis: CBAP, CCBA, ECBA
-
Agile Training: PMI-ACP
-
Scrum Training: CSM
-
DevOps
-
Program Management: PgMP
-
IT Service Management & Governance: COBIT, ISO
Future Trends in Lean Management
Lean Management continues to evolve as organizations seek to stay ahead in an ever-changing business landscape. Here are some future trends that are shaping the future of Lean Management:
-
Lean Digital Transformation: As technology advancements accelerate, Lean Management is increasingly intersecting with digital transformation initiatives. Organizations are leveraging automation, artificial intelligence (AI), machine learning, and data analytics to enhance Lean processes. Digital tools and platforms are being used to streamline workflows, capture and analyze data in real-time, and drive continuous improvement efforts. Lean practitioners will need to embrace digital tools and develop skills in leveraging technology to further optimize processes and create more data-driven decision-making environments.
-
Lean in Service Industries: Traditionally, Lean Management has been associated with manufacturing industries. However, there is a growing trend of applying Lean principles to service industries such as healthcare, finance, hospitality, and customer service. Service organizations are recognizing the value of eliminating waste, improving efficiency, and enhancing the customer experience. Lean methodologies, tailored to the unique characteristics of service industries, are being developed and implemented. Lean practitioners can expect an increasing demand for their expertise in these sectors.
-
Lean Sustainability: As sustainability becomes a critical focus for organizations worldwide, Lean Management is merging with environmental stewardship. Lean principles are being applied to identify and reduce waste, improve energy efficiency, minimize carbon footprint, and promote sustainable practices across the value chain. Lean practitioners will need to integrate sustainability principles into their toolkit and collaborate with stakeholders to develop Lean processes that align with environmental goals.
-
Lean Agile: The Agile methodology, popular in software development and project management, is converging with Lean Management. This integration aims to combine the flexibility and adaptability of Agile with the waste reduction and efficiency focus of Lean. Lean Agile methodologies, such as Lean-Agile Scrum, are emerging to enable organizations to respond swiftly to changing market dynamics while maintaining a Lean mindset. Lean practitioners will need to familiarize themselves with Agile principles and frameworks to adapt Lean practices to dynamic and iterative environments.
-
Lean Leadership and Culture: Lean Management is not just about implementing tools and techniques; it requires a cultural shift and strong leadership. Future trends in Lean Management emphasize the importance of Lean leadership, where leaders at all levels of the organization embody Lean principles and lead by example. Lean leaders create a culture of continuous improvement, empower employees, and foster collaboration and innovation. Lean practitioners will need to develop leadership skills and promote Lean thinking throughout the organization.
-
Lean Supply Chain Management: Lean principles are increasingly being applied to supply chain management to optimize inventory, improve supplier relationships, and enhance overall efficiency. Organizations are adopting Lean practices, such as Just-in-Time delivery, vendor-managed inventory, and collaborative forecasting, to minimize waste, reduce lead times, and increase responsiveness. Lean practitioners will need to understand the complexities of supply chain management and collaborate closely with suppliers to drive Lean initiatives throughout the value chain.
These future trends indicate that Lean Management is not stagnant but continues to adapt and evolve to meet the evolving needs of organizations. As a Lean practitioner, staying informed about these trends and acquiring the necessary skills and knowledge will enable you to remain at the forefront of Lean practices and contribute effectively to organizational success.
In conclusion, the future of Lean Management lies in embracing digital transformation, expanding its application to service industries and sustainability, integrating Agile methodologies, fostering Lean leadership and culture, and optimizing supply chain management. By staying ahead of these trends, organizations can continue to achieve operational excellence and stay competitive in a rapidly changing business landscape.
Conclusion
In conclusion, Lean Management certification is a valuable investment for individuals and organizations alike. Throughout this blog, we have explored various subtopics related to Lean Management certification, including its importance, methodologies, certification process, benefits for organizations, tips for successful certification, and future trends.
Lean Management certification equips professionals with the knowledge, skills, and methodologies to drive efficiency, improve quality, reduce costs, and streamline processes. Organizations that have certified Lean Management professionals on their teams benefit from increased productivity, enhanced customer satisfaction, cost reduction, and a culture of continuous improvement.
To successfully obtain Lean Management certification, individuals should understand the certification requirements, choose the right training program, dedicate time for preparation, leverage available resources, seek practical experience, collaborate with others, practice time management during the exam, and maintain a calm and confident mindset.
Looking ahead, the future of Lean Management involves the integration of digital technologies, the application of Lean principles to service industries and sustainability, the merging of Lean and Agile methodologies, the importance of Lean leadership and culture, and the optimization of supply chain management.
By staying informed about these future trends and continuously developing their skills, Lean Management practitioners can adapt to changing organizational needs and contribute to sustained success.
Obtaining Lean Management certification opens up new career opportunities, enhances professional credibility, and demonstrates a commitment to continuous learning and improvement. It positions individuals as valuable assets to organizations seeking to optimize their operations and stay competitive in the marketplace.
Whether you are an individual looking to enhance your career prospects or an organization striving for operational excellence, Lean Management certification is a powerful tool that can drive success and deliver tangible results.
Embrace the principles of Lean Management, invest in your professional development, and embark on a journey of continuous improvement that will benefit both yourself and the organizations you serve.
Read More
The Essential Guide to Lean Management Certification and Methodologies and Importance is a comprehensive resource that outlines the significance of Lean management certification and explores the various methodologies associated with Lean principles. This guide serves as an invaluable tool for professionals aiming to enhance their skills and credentials in Lean management. It covers a range of Lean methodologies, including value stream mapping, Kaizen, Just-in-Time (JIT), Kanban, 5S Methodology, and more. By obtaining Lean management certification, individuals gain industry-recognized validation of their knowledge and expertise in Lean practices, opening doors to career advancement and increased opportunities. The guide emphasizes the importance of Lean management in driving operational excellence, waste reduction, and continuous improvement within organizations. It provides valuable insights into the certification process, training programs, exam preparation, and the benefits of achieving Lean certification. Whether you are an aspiring Lean practitioner or a seasoned professional, this guide equips you with the essential knowledge and resources to leverage Lean methodologies effectively and make a tangible impact in your organization.
Table of contents
-
Introduction to Lean Management
-
The Importance of Lean Management Certification
-
Lean Management Methodologies
-
Lean Management Certification Process
-
Benefits of Lean Management Certification for Organizations
-
Tips for Successfully Obtaining Lean Management Certification
-
Future Trends in Lean Management
-
Conclusion
Introduction to Lean Management
In an increasingly competitive and dynamic business environment, organizations are constantly seeking ways to improve efficiency, reduce waste, and enhance overall performance. One methodology that has gained significant traction in recent years is Lean Management. Originating from the renowned Toyota Production System, Lean Management has evolved into a widely adopted approach that focuses on streamlining processes, eliminating non-value-added activities, and fostering a culture of continuous improvement.
At its core, Lean Management is about maximizing customer value while minimizing waste. It provides organizations with a systematic framework to identify and eliminate activities that do not contribute to delivering value to customers. By doing so, Lean Management helps businesses enhance productivity, reduce costs, improve quality, and ultimately gain a competitive edge.
The principles of Lean Management are rooted in the pursuit of operational excellence. It emphasizes the importance of eliminating inefficiencies, bottlenecks, and defects that impede smooth operations. By adopting Lean Management principles and practices, organizations can achieve greater agility, flexibility, and responsiveness to customer needs.
In recognition of the immense value that Lean Management brings to businesses, many professionals seek Lean Management certification to enhance their skills and expertise in implementing Lean practices. In this blog, we will explore the various aspects of Lean Management certification, its benefits, the certification process, and its impact on both individuals and organizations.
Join us on this insightful journey into the world of Lean Management certification and discover how it can revolutionize your career and drive organizational success.
The Importance of Lean Management Certification
In today's competitive business landscape, organizations are constantly seeking professionals who possess the knowledge and expertise to drive process improvement, enhance efficiency, and streamline operations. This is where Lean Management certification becomes highly valuable. Let's explore the significance of obtaining a Lean Management certification and the advantages it brings to both individuals and organizations.
-
Enhancing Skills and Knowledge: Lean Management certification programs provide comprehensive training in Lean principles, methodologies, and tools. Through these programs, professionals gain a deep understanding of Lean concepts such as waste reduction, value stream mapping, Kaizen, and more. They acquire the skills necessary to identify process inefficiencies, implement improvements, and drive sustainable change within their organizations.
-
Validation of Expertise: Lean Management certification serves as a tangible validation of an individual's knowledge and proficiency in Lean practices. By obtaining a recognized certification, professionals demonstrate their commitment to continuous improvement and their ability to apply Lean principles effectively. This validation adds credibility to their expertise and distinguishes them as competent Lean practitioners.
-
Career Advancement: Lean Management certification significantly enhances career prospects. Organizations across various industries recognize the value of Lean Management and actively seek professionals who possess the necessary skills to lead Lean initiatives. Certification showcases an individual's dedication to professional growth and positions them as strong candidates for leadership roles, project management positions, and other career advancement opportunities.
-
Increased Employability: In a competitive job market, having Lean Management certification can give job seekers a distinct advantage. Employers often prioritize candidates who possess specialized certifications, as it indicates a higher level of expertise and a proven ability to contribute to process improvement efforts. Lean Management certification can open doors to new job opportunities and increase an individual's employability across a wide range of industries.
-
Organizational Impact: Lean Management certification not only benefits individuals but also has a positive impact on the organizations they serve. Certified professionals bring valuable skills and knowledge that can drive operational excellence, enhance productivity, and reduce waste within their organizations. They are equipped to identify process bottlenecks, implement Lean methodologies, and foster a culture of continuous improvement, leading to increased efficiency and customer satisfaction.
In summary, Lean Management certification is highly important in today's business world. It empowers professionals with the skills, knowledge, and credibility to implement Lean practices and drive organizational success. Whether you are seeking career advancement or aiming to make a significant impact within your organization, Lean Management certification can be a catalyst for personal and professional growth.
Lean Management Methodologies
Lean Management encompasses a variety of methodologies, each designed to address specific challenges and optimize different aspects of organizational processes. Understanding these methodologies is crucial for professionals seeking Lean Management certification. Let's explore some of the key Lean methodologies and their applications:
-
Six Sigma: Six Sigma combines Lean principles with statistical analysis to minimize process variation and defects. It aims to achieve near-perfect quality levels by identifying and eliminating root causes of errors and reducing process variability. Six Sigma follows a structured approach, employing the DMAIC (Define, Measure, Analyze, Improve, Control) framework for continuous improvement.
-
Kanban: Kanban is a visual scheduling and workflow management system. It utilizes visual signals, such as cards or digital boards, to track and manage the flow of work. Kanban promotes just-in-time production, eliminates overproduction, and ensures that work is pulled only when needed. This methodology enhances efficiency, reduces waste, and improves communication within teams.
-
Kaizen: Kaizen, meaning "continuous improvement" in Japanese, is a philosophy that emphasizes making incremental, small-scale improvements across all levels of an organization. It encourages employees to identify and implement process improvements on a regular basis. Kaizen fosters a culture of continuous learning, problem-solving, and employee engagement, leading to sustained improvements over time.
-
Value Stream Mapping: Value Stream Mapping (VSM) is a visual tool used to analyze and optimize the flow of materials and information through a process. It provides a holistic view of the entire value stream, identifying non-value-added activities, bottlenecks, and areas for improvement. VSM helps organizations streamline processes, reduce lead times, and enhance overall efficiency.
-
5S Methodology: The 5S methodology focuses on workplace organization and cleanliness. It consists of five principles: Sort, Set in Order, Shine, Standardize, and Sustain. By implementing these principles, organizations create organized, clutter-free work environments, improve visual management, and establish standardized processes. The 5S methodology contributes to increased productivity, safety, and employee morale.
-
Just-in-Time (JIT): Just-in-Time is a methodology that aims to minimize inventory levels and reduce waste by producing and delivering products or services at the precise time they are needed. JIT eliminates excess inventory, improves cash flow, and allows organizations to respond quickly to customer demands. This methodology requires efficient supply chain management and close collaboration with suppliers.
These are just a few examples of the Lean Management methodologies that professionals encounter during their Lean journey. Each methodology has its own set of tools and techniques, and their applicability may vary depending on the organizational context and objectives.
As you progress in your Lean Management certification, you will delve deeper into these methodologies, understand their principles, and learn how to apply them effectively to drive process improvements and achieve organizational excellence.
Lean Management Certification Process
Obtaining a Lean Management certification requires a systematic approach that typically involves specific steps and requirements. Understanding the certification process can help individuals plan their journey and maximize their chances of success. Let's explore the typical Lean Management certification process:
-
Research and Select Certification Program: Begin by researching different Lean Management certification programs available. Consider factors such as program reputation, accreditation, curriculum, and alignment with your career goals. Select a program that suits your needs and preferences.
-
Meet Eligibility Requirements: Each certification program may have specific eligibility requirements. Common prerequisites may include educational qualifications, professional experience, or completion of specific training courses. Ensure that you meet these requirements before proceeding with the certification process.
-
Enroll in Certification Training: Once you have selected a certification program, enroll in the relevant training courses. These courses are designed to provide you with the necessary knowledge and skills to understand Lean Management concepts, methodologies, and tools. Training options may include in-person workshops, online courses, or a combination of both.
-
Prepare for Certification Exam: Lean Management certifications typically require passing a comprehensive exam. Allocate sufficient time to study and review the materials covered in the training courses. Utilize study guides, practice exams, and other resources provided by the certification body or recommended by trainers. Additionally, leverage practical experience and real-life examples to reinforce your understanding of Lean Management principles.
-
Schedule and Take the Exam: Once you feel adequately prepared, schedule your certification exam. The exam format may vary depending on the certification program, but it is typically conducted in a proctored environment. Be sure to arrive well-prepared, well-rested, and with the necessary identification documents. Follow the exam instructions and pace yourself appropriately to complete all the required sections within the allotted time.
-
Await Certification Results: After completing the exam, you will need to wait for the certification body to review and assess your results. The waiting period varies depending on the program, but it typically ranges from a few days to a few weeks. During this time, the certification body evaluates your performance and determines whether you meet the passing criteria.
-
Receive Certification and Renewal: Upon successfully passing the exam, you will receive your Lean Management certification. Celebrate your accomplishment and proudly showcase your certification on your resume and professional profiles. Keep in mind that Lean Management certifications often have an expiration date. To maintain your certification, you may be required to fulfill certain continuing education or professional development requirements and renew your certification periodically.
Remember that the certification process may have slight variations depending on the specific certification program you choose. It is essential to review the certification body's guidelines and instructions for the most accurate and up-to-date information.
By following these steps and investing time and effort into your Lean Management certification journey, you can enhance your skills, expand your knowledge, and boost your professional credibility in the field of Lean Management.
Benefits of Lean Management Certification for Organizations
Lean Management certification offers numerous advantages to organizations that invest in training their employees and building a Lean culture. Let's explore the benefits that organizations can derive from having certified Lean Management professionals on their teams:
-
Improved Efficiency and Productivity: Lean Management certification equips professionals with the knowledge and skills to identify and eliminate waste in processes. Certified individuals can analyze workflows, identify bottlenecks, and implement Lean methodologies to streamline operations. By optimizing processes, organizations can achieve improved efficiency, reduce lead times, and increase overall productivity.
-
Enhanced Quality and Customer Satisfaction: Lean Management certification focuses on delivering value to customers by eliminating defects and improving quality. Certified professionals are trained to implement quality control measures, statistical analysis techniques, and error-proofing methods. This results in higher product and service quality, leading to increased customer satisfaction and loyalty.
-
Cost Reduction and Resource Optimization: Lean Management methodologies help organizations identify and eliminate non-value-added activities and excessive resource utilization. By implementing Lean principles, such as just-in-time production and inventory reduction, organizations can minimize costs associated with excess inventory, transportation, overproduction, and defects. Lean Management certification enables professionals to identify cost-saving opportunities and optimize resource allocation.
-
Streamlined Processes and Reduced Lead Time: Lean Management certification enables professionals to analyze and map value streams, identify process inefficiencies, and implement improvements. By eliminating non-value-added activities, reducing cycle times, and optimizing workflows, organizations can significantly reduce lead times. This leads to faster response to customer demands, shorter time-to-market, and increased competitiveness.
-
Culture of Continuous Improvement: Lean Management certification promotes a culture of continuous improvement within organizations. Certified professionals become catalysts for change and champions of Lean practices. They encourage and empower colleagues to identify and implement process improvements, fostering a culture of innovation, engagement, and continuous learning throughout the organization.
-
Effective Change Management: Lean Management certification equips professionals with skills in change management and stakeholder engagement. This enables them to effectively communicate Lean initiatives, overcome resistance to change, and engage stakeholders at all levels of the organization. Certified professionals can lead Lean projects, collaborate with cross-functional teams, and drive successful implementation of Lean methodologies.
-
Alignment with Strategic Objectives: Lean Management certification ensures that organizations align their operations with their strategic objectives. Certified professionals understand the importance of aligning Lean initiatives with the organization's mission, vision, and goals. They can effectively contribute to strategic planning, decision-making, and the achievement of organizational objectives.
In summary, Lean Management certification brings significant benefits to organizations. From improving efficiency and quality to reducing costs and lead times, organizations that invest in Lean Management training and certification can experience a positive impact on their bottom line and overall performance. By cultivating a Lean culture and harnessing the expertise of certified professionals, organizations can position themselves for sustained success in today's competitive business environment.
Tips for Successfully Obtaining Lean Management Certification
Obtaining Lean Management certification requires dedication, preparation, and a strategic approach. To maximize your chances of success, consider the following tips as you embark on your certification journey:
-
Understand Certification Requirements: Familiarize yourself with the specific requirements of the Lean Management certification program you have chosen. Review the eligibility criteria, prerequisites, and any recommended prior knowledge or experience. Ensure that you meet the requirements before proceeding further.
-
Choose the Right Training Program: Select a reputable and accredited training program that aligns with your learning style and preferences. Consider factors such as program content, delivery format (in-person or online), duration, and available resources. Look for programs that provide comprehensive coverage of Lean Management concepts, methodologies, and practical applications.
-
Dedicate Sufficient Time for Preparation: Lean Management certification exams can be comprehensive and challenging. Allocate dedicated time for studying and preparation. Create a study plan and schedule regular study sessions. Break down the content into manageable sections, and focus on understanding key concepts, tools, and techniques. Review and reinforce your learning through practice exams and quizzes.
-
Leverage Available Resources: Take advantage of the resources provided by the certification program or training provider. These may include study guides, textbooks, online materials, and practice exams. Engage with online forums or discussion groups related to Lean Management to seek clarification, share insights, and learn from the experiences of others.
-
Seek Practical Experience: While theoretical knowledge is essential, practical experience in applying Lean Management principles adds significant value to your certification journey. Look for opportunities within your organization or industry to participate in Lean projects, process improvement initiatives, or Kaizen events. Hands-on experience will deepen your understanding of Lean principles and enhance your ability to apply them effectively.
-
Collaborate and Learn from Others: Engage with a community of Lean Management professionals to broaden your perspective and learn from their experiences. Attend industry events, conferences, or workshops where you can network with like-minded individuals. Participate in online forums, LinkedIn groups, or professional associations focused on Lean Management. By sharing knowledge and exchanging ideas, you can gain valuable insights and stay updated on emerging trends.
-
Practice Time Management during the Exam: Time management is crucial during the certification exam. Familiarize yourself with the exam format and the allocated time for each section. Read questions carefully, and avoid spending too much time on any single question. If you encounter difficult questions, move on and return to them later. Manage your time effectively to ensure that you complete all sections within the given timeframe.
-
Stay Calm and Confident: On the day of the exam, maintain a calm and confident mindset. Trust in your preparation and the knowledge you have acquired. Practice relaxation techniques or mindfulness exercises to manage any exam-related stress or anxiety. Remember to read questions carefully, and answer them to the best of your ability based on your understanding of Lean Management principles.
By following these tips, you can enhance your readiness and increase your chances of successfully obtaining Lean Management certification. Remember that the certification journey is a continuous learning process, and it is the knowledge and skills gained along the way that truly matter.
How to obtain the Six Sigma Black Belt certification?
We are an Education Technology company providing certification training courses to accelerate careers of working professionals worldwide. We impart training through instructor-led classroom workshops, instructor-led live virtual training sessions, and self-paced e-learning courses.
We have successfully conducted training sessions in 108 countries across the globe and enabled thousands of working professionals to enhance the scope of their careers.
Our enterprise training portfolio includes in-demand and globally recognized certification training courses in Project Management, Quality Management, Business Analysis, IT Service Management, Agile and Scrum, Cyber Security, Data Science, and Emerging Technologies. Download our Enterprise Training Catalog from https://www.icertglobal.com/corporate-training-for-enterprises.php
Popular Courses include:
-
Project Management: PMP, CAPM ,PMI RMP
-
Quality Management: Six Sigma Black Belt ,Lean Six Sigma Green Belt, Lean Management
-
Business Analysis: CBAP, CCBA, ECBA
-
Agile Training: PMI-ACP
-
Scrum Training: CSM
-
DevOps
-
Program Management: PgMP
-
IT Service Management & Governance: COBIT, ISO
Future Trends in Lean Management
Lean Management continues to evolve as organizations seek to stay ahead in an ever-changing business landscape. Here are some future trends that are shaping the future of Lean Management:
-
Lean Digital Transformation: As technology advancements accelerate, Lean Management is increasingly intersecting with digital transformation initiatives. Organizations are leveraging automation, artificial intelligence (AI), machine learning, and data analytics to enhance Lean processes. Digital tools and platforms are being used to streamline workflows, capture and analyze data in real-time, and drive continuous improvement efforts. Lean practitioners will need to embrace digital tools and develop skills in leveraging technology to further optimize processes and create more data-driven decision-making environments.
-
Lean in Service Industries: Traditionally, Lean Management has been associated with manufacturing industries. However, there is a growing trend of applying Lean principles to service industries such as healthcare, finance, hospitality, and customer service. Service organizations are recognizing the value of eliminating waste, improving efficiency, and enhancing the customer experience. Lean methodologies, tailored to the unique characteristics of service industries, are being developed and implemented. Lean practitioners can expect an increasing demand for their expertise in these sectors.
-
Lean Sustainability: As sustainability becomes a critical focus for organizations worldwide, Lean Management is merging with environmental stewardship. Lean principles are being applied to identify and reduce waste, improve energy efficiency, minimize carbon footprint, and promote sustainable practices across the value chain. Lean practitioners will need to integrate sustainability principles into their toolkit and collaborate with stakeholders to develop Lean processes that align with environmental goals.
-
Lean Agile: The Agile methodology, popular in software development and project management, is converging with Lean Management. This integration aims to combine the flexibility and adaptability of Agile with the waste reduction and efficiency focus of Lean. Lean Agile methodologies, such as Lean-Agile Scrum, are emerging to enable organizations to respond swiftly to changing market dynamics while maintaining a Lean mindset. Lean practitioners will need to familiarize themselves with Agile principles and frameworks to adapt Lean practices to dynamic and iterative environments.
-
Lean Leadership and Culture: Lean Management is not just about implementing tools and techniques; it requires a cultural shift and strong leadership. Future trends in Lean Management emphasize the importance of Lean leadership, where leaders at all levels of the organization embody Lean principles and lead by example. Lean leaders create a culture of continuous improvement, empower employees, and foster collaboration and innovation. Lean practitioners will need to develop leadership skills and promote Lean thinking throughout the organization.
-
Lean Supply Chain Management: Lean principles are increasingly being applied to supply chain management to optimize inventory, improve supplier relationships, and enhance overall efficiency. Organizations are adopting Lean practices, such as Just-in-Time delivery, vendor-managed inventory, and collaborative forecasting, to minimize waste, reduce lead times, and increase responsiveness. Lean practitioners will need to understand the complexities of supply chain management and collaborate closely with suppliers to drive Lean initiatives throughout the value chain.
These future trends indicate that Lean Management is not stagnant but continues to adapt and evolve to meet the evolving needs of organizations. As a Lean practitioner, staying informed about these trends and acquiring the necessary skills and knowledge will enable you to remain at the forefront of Lean practices and contribute effectively to organizational success.
In conclusion, the future of Lean Management lies in embracing digital transformation, expanding its application to service industries and sustainability, integrating Agile methodologies, fostering Lean leadership and culture, and optimizing supply chain management. By staying ahead of these trends, organizations can continue to achieve operational excellence and stay competitive in a rapidly changing business landscape.
Conclusion
In conclusion, Lean Management certification is a valuable investment for individuals and organizations alike. Throughout this blog, we have explored various subtopics related to Lean Management certification, including its importance, methodologies, certification process, benefits for organizations, tips for successful certification, and future trends.
Lean Management certification equips professionals with the knowledge, skills, and methodologies to drive efficiency, improve quality, reduce costs, and streamline processes. Organizations that have certified Lean Management professionals on their teams benefit from increased productivity, enhanced customer satisfaction, cost reduction, and a culture of continuous improvement.
To successfully obtain Lean Management certification, individuals should understand the certification requirements, choose the right training program, dedicate time for preparation, leverage available resources, seek practical experience, collaborate with others, practice time management during the exam, and maintain a calm and confident mindset.
Looking ahead, the future of Lean Management involves the integration of digital technologies, the application of Lean principles to service industries and sustainability, the merging of Lean and Agile methodologies, the importance of Lean leadership and culture, and the optimization of supply chain management.
By staying informed about these future trends and continuously developing their skills, Lean Management practitioners can adapt to changing organizational needs and contribute to sustained success.
Obtaining Lean Management certification opens up new career opportunities, enhances professional credibility, and demonstrates a commitment to continuous learning and improvement. It positions individuals as valuable assets to organizations seeking to optimize their operations and stay competitive in the marketplace.
Whether you are an individual looking to enhance your career prospects or an organization striving for operational excellence, Lean Management certification is a powerful tool that can drive success and deliver tangible results.
Embrace the principles of Lean Management, invest in your professional development, and embark on a journey of continuous improvement that will benefit both yourself and the organizations you serve.
Lean Six Sigma Black Belt:A Complete Guide to Certification
In today's fast-paced and competitive business environment, organizations strive for excellence in operational efficiency and superior quality. To achieve these goals, the Lean Six Sigma methodology has emerged as a powerful framework for process improvement and performance optimization. At the heart of this methodology lies the role of the Lean Six Sigma Black Belt, a highly skilled professional equipped with the knowledge and expertise to drive transformative change within organizations.
"The Lean Six Sigma Black Belt: A Comprehensive Guide" serves as an invaluable resource for individuals seeking to master the principles and practices of Lean Six Sigma at an advanced level. This comprehensive guide offers a wealth of knowledge, insights, and practical tools necessary for aspiring Black Belts to become catalysts of organizational improvement.
The guide begins by delving into the fundamentals of Lean Six Sigma, providing a solid foundation for understanding the methodologies and principles that underpin this powerful problem-solving approach. Readers will gain insights into the DMAIC (Define, Measure, Analyze, Improve, Control) methodology, which forms the backbone of Lean Six Sigma projects, as well as the application of statistical analysis and data-driven decision-making.
Furthermore, this guide takes a deep dive into the crucial role of a Lean Six Sigma Black Belt, exploring their responsibilities as change agents, project leaders, and mentors within an organization. It provides practical guidance on project selection, team management, stakeholder engagement, and effective communication strategies to drive successful Lean Six Sigma initiatives.
"The Lean Six Sigma Black Belt: A Comprehensive Guide" goes beyond theory and equips readers with a wide range of Lean Six Sigma tools and techniques. From process mapping and root cause analysis to statistical process control and lean principles, this guide offers a comprehensive toolkit for problem-solving and process improvement.
Whether you are a seasoned professional looking to enhance your skills or an aspiring Black Belt ready to embark on your Lean Six Sigma journey, this guide will empower you with the knowledge and resources needed to excel in the field. Prepare to unlock the transformative power of Lean Six Sigma and become a driving force in creating a culture of continuous improvement and operational excellence.
Embark on your path to becoming a Lean Six Sigma Black Belt and unlock the potential for organizational success with "The Lean Six Sigma Black Belt: A Comprehensive Guide."
Table of Contents
- Introduction to Lean Six Sigma Black Belt:
- Lean Six Sigma Black Belt Body of Knowledge:
- Lean Six Sigma Black Belt Training and Exam:
- Roles and Responsibilities of a Lean Six Sigma Black Belt:
- Career Opportunities and Advancement with Lean Six Sigma Black Belt:
- Challenges and Limitations of Lean Six Sigma Black Belt:
- Conclusion
Introduction to Lean Six Sigma Black Belt Certification
Lean Six Sigma Black Belt certification is a prestigious and highly sought-after credential for professionals looking to enhance their process improvement skills and advance their careers. This certification represents the mastery of Lean Six Sigma principles, methodologies, and tools, empowering individuals to lead complex improvement projects within organizations.
Lean Six Sigma combines two powerful approaches to process improvement: Lean, which focuses on eliminating waste and optimizing process flow, and Six Sigma, which emphasizes reducing variation and improving process quality. By integrating these methodologies, Lean Six Sigma Black Belts are equipped with a comprehensive skill set to identify, analyze, and solve business problems effectively.
To become a Lean Six Sigma Black Belt, individuals must complete a rigorous training program that covers advanced concepts and techniques. This certification goes beyond the foundational levels of Lean Six Sigma (White Belt, Yellow Belt, and Green Belt) and requires a deeper understanding of statistical analysis, project management, leadership, and change management.
The role of a Lean Six Sigma Black Belt involves leading cross-functional teams, driving improvement initiatives, and delivering tangible results. Black Belts are responsible for identifying improvement opportunities, conducting data analysis, implementing process changes, and ensuring sustained performance through effective control mechanisms.
Achieving Lean Six Sigma Black Belt certification signifies a high level of expertise and proficiency in process improvement methodologies. It demonstrates an individual's ability to apply advanced statistical techniques, lead teams through complex projects, and deliver measurable business outcomes. As a result, professionals with this certification are highly valued in a wide range of industries, including manufacturing, healthcare, finance, logistics, and more.
In conclusion, Lean Six Sigma Black Belt certification offers professionals an opportunity to develop advanced process improvement skills, gain a competitive edge in the job market, and make a significant impact within their organizations. In the following sections of this blog, we will explore the specific requirements, training options, career opportunities, and benefits associated with Lean Six Sigma Black Belt certification.
Lean Six Sigma Black Belt Body of Knowledge
The Lean Six Sigma Black Belt certification encompasses a comprehensive body of knowledge that equips professionals with the necessary skills and tools to lead successful process improvement projects. Let's explore the key areas covered in the Lean Six Sigma Black Belt Body of Knowledge:
- Lean Principles:
- Understanding the core principles of Lean, such as waste identification and elimination, value stream mapping, and continuous flow.
- Applying Lean tools and techniques, including 5S (Sort, Set in Order, Shine, Standardize, Sustain), Kanban, and Kaizen events.
- Six Sigma Methodology:
- Overview of the DMAIC (Define, Measure, Analyze, Improve, Control) framework, which serves as the roadmap for process improvement projects.
- Applying statistical analysis techniques to measure process performance, identify root causes of variation, and quantify improvement opportunities.
- Data Collection and Analysis:
- Selecting appropriate data collection methods and tools.
- Conducting data analysis using descriptive and inferential statistical techniques.
- Utilizing software tools, such as Minitab or Excel, for data analysis and visualization.
- Statistical Process Control (SPC):
- Understanding control charts and their application in monitoring and controlling process stability and capability.
- Implementing control plans to sustain process improvements and prevent deviations.
- Design of Experiments (DOE):
- Applying DOE techniques to understand and optimize process variables, identify critical factors, and achieve robust process performance.
- Utilizing factorial designs, response surface methodology, and other experimental design techniques.
- Process Capability and Performance Metrics:
- Calculating process capability indices (e.g., Cp, Cpk) and understanding their interpretation.
- Defining and monitoring process performance metrics, such as yield, cycle time, and defect rates.
- Project Management:
- Developing project charters and defining project scope.
- Applying project management tools, such as work breakdown structures, Gantt charts, and risk management techniques.
- Change Management and Stakeholder Engagement:
- Identifying stakeholders and their roles in process improvement initiatives.
- Implementing change management strategies to ensure successful adoption of process changes.
- Leadership and Team Management:
- Effective leadership skills to inspire and motivate project teams.
- Facilitating team dynamics, conflict resolution, and consensus-building.
Mastering the Lean Six Sigma Black Belt Body of Knowledge provides professionals with the tools, techniques, and methodologies required to lead complex process improvement projects. By leveraging this knowledge, Black Belts can drive meaningful change, deliver measurable results, and contribute to the overall success of their organizations.
Lean Six Sigma Black Belt Training and Exam
To attain Lean Six Sigma Black Belt certification, individuals must undergo a comprehensive training program and successfully pass a certification exam. Let's explore the key aspects of Lean Six Sigma Black Belt training and the certification exam:
- Training Options:
- Classroom Training: Many organizations and training institutes offer classroom-based Lean Six Sigma Black Belt training programs. These programs typically involve in-person instruction, group activities, and hands-on exercises to reinforce learning.
- Online Training: Online training has gained popularity due to its flexibility and accessibility. Virtual platforms provide self-paced modules, interactive lessons, and virtual simulations to facilitate learning. Online training allows individuals to study at their own convenience from anywhere in the world.
- Blended Learning: Some training providers offer a combination of classroom and online learning, allowing participants to benefit from both in-person interactions and the convenience of online modules.
- Curriculum and Topics Covered:
- In-depth understanding of Lean Six Sigma principles, methodologies, and tools.
- Comprehensive coverage of the DMAIC (Define, Measure, Analyze, Improve, Control) framework.
- Statistical analysis techniques, such as hypothesis testing, regression analysis, and design of experiments.
- Project management methodologies and tools.
- Change management strategies and stakeholder engagement.
- Leadership and team management skills.
- Duration of Training:
- The duration of Lean Six Sigma Black Belt training varies depending on the training provider and the delivery format chosen.
- Classroom-based programs can range from one to two weeks, with several hours of training each day.
- Online training programs allow individuals to study at their own pace, with a typical duration of several weeks to a few months.
- Certification Exam:
- After completing the training program, individuals must pass a certification exam to attain Lean Six Sigma Black Belt certification.
- The exam evaluates the candidate's understanding of Lean Six Sigma concepts, methodologies, and application.
- The exam may include multiple-choice questions, case studies, and real-life scenarios to assess the candidate's knowledge and problem-solving abilities.
- The exam is typically proctored and can be conducted online or in-person, depending on the certification body or training provider.
- Exam Preparation:
- Reviewing training materials and notes to reinforce the knowledge gained during the training program.
- Practicing with sample exam questions and mock exams to familiarize oneself with the format and timing of the actual exam.
- Seeking additional study resources, such as textbooks, reference guides, or online tutorials, to deepen understanding in specific areas.
Successfully achieving Lean Six Sigma Black Belt certification demonstrates an individual's proficiency in Lean Six Sigma methodologies and their ability to lead and drive process improvement initiatives. It opens up a wide range of career opportunities and enhances one's credibility as a process improvement expert.
Roles and Responsibilities of a Lean Six Sigma Black Belt
A Lean Six Sigma Black Belt plays a crucial role in driving process improvement initiatives within an organization. Let's explore the key roles and responsibilities of a Lean Six Sigma Black Belt:
- Project Leadership:
- Lead and manage cross-functional teams involved in process improvement projects.
- Define project goals, scope, and deliverables in alignment with organizational objectives.
- Provide guidance and direction to team members throughout the project lifecycle.
- Process Improvement Expertise:
- Apply Lean Six Sigma principles, methodologies, and tools to identify process inefficiencies, bottlenecks, and areas for improvement.
- Collect and analyze data to quantify process performance and identify root causes of problems.
- Develop and implement solutions that optimize process flow, reduce waste, and improve quality.
- Statistical Analysis and Problem-Solving:
- Utilize statistical analysis techniques to analyze process data, determine process capability, and identify areas for improvement.
- Apply problem-solving methodologies, such as DMAIC (Define, Measure, Analyze, Improve, Control), to systematically address process issues and achieve measurable results.
- Change Management and Stakeholder Engagement:
- Assess and manage the impact of process changes on stakeholders.
- Communicate the benefits and importance of process improvement initiatives to gain buy-in and support.
- Facilitate change management activities, including training, to ensure successful adoption of process improvements.
- Mentoring and Coaching:
- Guide and mentor Green Belts and other team members involved in process improvement projects.
- Provide training and support to help build their Lean Six Sigma skills and capabilities.
- Foster a culture of continuous improvement and knowledge sharing within the organization.
- Project Monitoring and Control:
- Develop and implement control plans to sustain process improvements and prevent deviations.
- Establish performance metrics and measurement systems to track progress and ensure sustained benefits.
- Conduct regular reviews and audits to monitor project performance and make necessary adjustments.
- Collaboration and Communication:
- Collaborate with stakeholders at various levels of the organization to ensure alignment and support for process improvement initiatives.
- Communicate project updates, findings, and recommendations to senior management and relevant stakeholders.
- Facilitate effective teamwork, collaboration, and knowledge sharing among project team members.
Lean Six Sigma Black Belts are instrumental in driving process excellence and achieving significant improvements in operational efficiency, customer satisfaction, and financial outcomes. Their ability to analyze complex problems, lead teams, and implement sustainable solutions makes them valuable assets to organizations across various industries.
Career Opportunities and Advancement with Lean Six Sigma Black Belt
Achieving Lean Six Sigma Black Belt certification opens up a wide range of career opportunities and provides professionals with a competitive edge in the job market. Let's explore the potential career paths and advancement opportunities associated with Lean Six Sigma Black Belt certification:
- Process Improvement Roles:
- Lean Six Sigma Black Belts often pursue careers as Process Improvement Managers, Business Process Analysts, or Continuous Improvement Specialists.
- They lead process improvement initiatives, drive operational efficiency, and implement best practices within organizations.
- These roles can be found across industries such as manufacturing, healthcare, finance, logistics, and service sectors.
- Quality Management:
- Lean Six Sigma Black Belts are well-suited for Quality Manager or Quality Assurance roles.
- They ensure adherence to quality standards, develop and implement quality management systems, and drive continuous improvement in product or service quality.
- Project Management:
- Lean Six Sigma Black Belts possess strong project management skills, making them suitable for Project Manager or Program Manager positions.
- They oversee complex projects, manage timelines, budgets, and resources, and ensure successful project delivery.
- Operations Management:
- Lean Six Sigma Black Belts often transition into Operations Manager or Operations Excellence roles.
- They optimize operational processes, streamline supply chains, and drive overall business performance improvement.
- Change Management and Consulting:
- With their expertise in process improvement and change management, Lean Six Sigma Black Belts can pursue careers in Change Management or Lean Consulting.
- They help organizations navigate through change, implement Lean methodologies, and drive cultural transformation.
- Leadership and Senior Management:
- Lean Six Sigma Black Belt certification enhances leadership skills, making Black Belts suitable for senior management roles.
- They can progress to positions such as Vice President of Operations, Director of Continuous Improvement, or Chief Operating Officer (COO).
Advancement Opportunities:
- Master Black Belt:
- Experienced Lean Six Sigma Black Belts can pursue further advancement by becoming Master Black Belts.
- Master Black Belts mentor and coach Black Belts, oversee multiple projects, and provide guidance in advanced statistical analysis and project selection.
- Executive Leadership:
- Lean Six Sigma Black Belts who demonstrate strong leadership and business acumen may advance to executive-level positions.
- They can take on roles such as Chief Operating Officer (COO), Chief Quality Officer (CQO), or other C-suite positions.
- Entrepreneurship:
- Lean Six Sigma Black Belts equipped with process improvement expertise may choose to start their own consulting firms or become independent consultants.
- They can offer their expertise to organizations seeking to improve processes and drive business performance.
Lean Six Sigma Black Belt certification provides professionals with the skills, knowledge, and credentials to excel in various industries and positions. It enhances career prospects, increases earning potential, and positions individuals as valuable assets in organizations striving for continuous improvement and operational excellence.
Challenges and Limitations of Lean Six Sigma Black Belt
While Lean Six Sigma Black Belt certification offers numerous benefits and opportunities, it is essential to acknowledge the challenges and limitations associated with its implementation. Let's explore some of these challenges and limitations:
- Organizational Culture:
- Resistance to Change: Implementing Lean Six Sigma initiatives requires a cultural shift within an organization. Resistance to change from employees, managers, or stakeholders can pose challenges to the successful adoption of Lean Six Sigma principles and methodologies.
- Lack of Support from Leadership: Without strong support and commitment from top-level management, it can be difficult to drive and sustain Lean Six Sigma initiatives. Leadership involvement is crucial to overcome organizational barriers and allocate necessary resources.
- Data Availability and Quality:
- Incomplete or Inaccurate Data: Availability of complete and accurate data is essential for effective data analysis and decision-making. Limited data availability or poor data quality can hinder the accuracy of analysis and the identification of root causes.
- Data Complexity: In some organizations, data may be complex, scattered across multiple systems, or difficult to access. Managing and analyzing complex data sets can be time-consuming and may require advanced technical skills or specialized tools.
- Project Selection and Scope:
- Project Alignment with Strategic Goals: Identifying projects that align with the organization's strategic objectives can be challenging. Choosing projects that have a significant impact on key performance indicators and business outcomes is crucial for maximizing the benefits of Lean Six Sigma.
- Scope Creep: Ensuring the defined scope of a project remains focused and does not expand beyond its original boundaries can be a challenge. Scope creep can lead to project delays, increased costs, and reduced effectiveness.
- Resource Constraints:
- Time and Resource Allocation: Implementing Lean Six Sigma initiatives requires dedicated time and resources. Balancing project responsibilities with daily operational demands can be challenging, especially for Black Belts who are leading multiple projects simultaneously.
- Skill and Knowledge Gaps: Building a skilled workforce trained in Lean Six Sigma methodologies may take time and effort. Identifying and addressing skill gaps through training and development programs is essential for successful implementation.
- Sustainability and Continuous Improvement:
- Sustaining Results: Sustaining the improvements achieved through Lean Six Sigma initiatives can be challenging. Without ongoing monitoring, control mechanisms, and a culture of continuous improvement, there is a risk of reverting to previous practices.
- Adaptability to Changing Environments: Lean Six Sigma methodologies may not always be suitable for rapidly changing or highly innovative environments. Agile approaches or other methodologies may need to be considered in such cases.
It is important to recognize these challenges and limitations as opportunities for learning and improvement. Organizations implementing Lean Six Sigma should address these challenges proactively by fostering a supportive culture, providing necessary resources, and adapting the methodologies to fit their unique circumstances.
How to obtain the Lean Six Sigma Black Belt certification?
We are an Education Technology company providing certification training courses to accelerate careers of working professionals worldwide. We impart training through instructor-led classroom workshops, instructor-led live virtual training sessions, and self-paced e-learning courses.
We have successfully conducted training sessions in 108 countries across the globe and enabled thousands of working professionals to enhance the scope of their careers.
Our enterprise training portfolio includes in-demand and globally recognized certification training courses in Project Management, Quality Management, Business Analysis, IT Service Management, Agile and Scrum, Cyber Security, Data Science, and Emerging Technologies. Download our Enterprise Training Catalog from https://www.icertglobal.com/corporate-training-for-enterprises.php
Popular Courses include:
- Project Management: PMP, CAPM ,PMI RMP
- Quality Management: Six Sigma Green Belt ,Lean Six Sigma Yellow Belt, Lean Six Sigma Black Belt
- Business Analysis: CBAP, CCBA, ECBA
- Agile Training: PMI-ACP
- Scrum Training: CSM
- DevOps
- Program Management: PgMP
- IT Service Management & Governance: COBIT, ISO
Conclusion
Lean Six Sigma Black Belt certification offers professionals a valuable skill set to drive process improvement and deliver tangible results within organizations. Through a comprehensive training program and certification exam, individuals gain expertise in Lean and Six Sigma methodologies, statistical analysis, project management, and change management.
In this blog, we explored various aspects related to Lean Six Sigma Black Belt certification. We discussed the subtopics of Introduction to Lean Six Sigma Black Belt, Lean Six Sigma Black Belt Body of Knowledge, Lean Six Sigma Black Belt Training and Exam, Roles and Responsibilities of a Lean Six Sigma Black Belt, Career Opportunities and Advancement with Lean Six Sigma Black Belt, and Challenges and Limitations of Lean Six Sigma Black Belt.
By acquiring Lean Six Sigma Black Belt certification, professionals open doors to a wide range of career opportunities, including process improvement roles, quality management, project management, operations management, change management, and even executive leadership positions. The certification also provides a pathway for advancement to higher-level roles, such as Master Black Belt or executive positions within organizations.
However, it is important to acknowledge the challenges and limitations associated with Lean Six Sigma implementation. Overcoming resistance to change, ensuring data availability and quality, project selection and scope management, resource constraints, and sustaining results are among the challenges that organizations may face. Addressing these challenges requires strong leadership support, skill development, and a commitment to a culture of continuous improvement.
Lean Six Sigma Black Belt certification equips professionals with the knowledge and tools to lead process improvement initiatives, optimize operational efficiency, and drive overall business performance. By leveraging their expertise, Black Belts contribute to organizational success, customer satisfaction, and competitive advantage.
As organizations strive for continuous improvement and operational excellence, Lean Six Sigma Black Belts play a critical role in leading the way towards improved processes, enhanced quality, and increased customer value.
Incorporating Lean Six Sigma methodologies and practices into organizations can bring about significant improvements and long-term success. By embracing the benefits and overcoming the challenges, organizations can achieve sustainable and continuous improvement, delivering enhanced value to customers and stakeholders.
So, whether you are an aspiring Lean Six Sigma Black Belt or an organization seeking process improvement, embracing Lean Six Sigma principles and methodologies can undoubtedly pave the way for success.
Read More
In today's fast-paced and competitive business environment, organizations strive for excellence in operational efficiency and superior quality. To achieve these goals, the Lean Six Sigma methodology has emerged as a powerful framework for process improvement and performance optimization. At the heart of this methodology lies the role of the Lean Six Sigma Black Belt, a highly skilled professional equipped with the knowledge and expertise to drive transformative change within organizations.
"The Lean Six Sigma Black Belt: A Comprehensive Guide" serves as an invaluable resource for individuals seeking to master the principles and practices of Lean Six Sigma at an advanced level. This comprehensive guide offers a wealth of knowledge, insights, and practical tools necessary for aspiring Black Belts to become catalysts of organizational improvement.
The guide begins by delving into the fundamentals of Lean Six Sigma, providing a solid foundation for understanding the methodologies and principles that underpin this powerful problem-solving approach. Readers will gain insights into the DMAIC (Define, Measure, Analyze, Improve, Control) methodology, which forms the backbone of Lean Six Sigma projects, as well as the application of statistical analysis and data-driven decision-making.
Furthermore, this guide takes a deep dive into the crucial role of a Lean Six Sigma Black Belt, exploring their responsibilities as change agents, project leaders, and mentors within an organization. It provides practical guidance on project selection, team management, stakeholder engagement, and effective communication strategies to drive successful Lean Six Sigma initiatives.
"The Lean Six Sigma Black Belt: A Comprehensive Guide" goes beyond theory and equips readers with a wide range of Lean Six Sigma tools and techniques. From process mapping and root cause analysis to statistical process control and lean principles, this guide offers a comprehensive toolkit for problem-solving and process improvement.
Whether you are a seasoned professional looking to enhance your skills or an aspiring Black Belt ready to embark on your Lean Six Sigma journey, this guide will empower you with the knowledge and resources needed to excel in the field. Prepare to unlock the transformative power of Lean Six Sigma and become a driving force in creating a culture of continuous improvement and operational excellence.
Embark on your path to becoming a Lean Six Sigma Black Belt and unlock the potential for organizational success with "The Lean Six Sigma Black Belt: A Comprehensive Guide."
Table of Contents
- Introduction to Lean Six Sigma Black Belt:
- Lean Six Sigma Black Belt Body of Knowledge:
- Lean Six Sigma Black Belt Training and Exam:
- Roles and Responsibilities of a Lean Six Sigma Black Belt:
- Career Opportunities and Advancement with Lean Six Sigma Black Belt:
- Challenges and Limitations of Lean Six Sigma Black Belt:
- Conclusion
Introduction to Lean Six Sigma Black Belt Certification
Lean Six Sigma Black Belt certification is a prestigious and highly sought-after credential for professionals looking to enhance their process improvement skills and advance their careers. This certification represents the mastery of Lean Six Sigma principles, methodologies, and tools, empowering individuals to lead complex improvement projects within organizations.
Lean Six Sigma combines two powerful approaches to process improvement: Lean, which focuses on eliminating waste and optimizing process flow, and Six Sigma, which emphasizes reducing variation and improving process quality. By integrating these methodologies, Lean Six Sigma Black Belts are equipped with a comprehensive skill set to identify, analyze, and solve business problems effectively.
To become a Lean Six Sigma Black Belt, individuals must complete a rigorous training program that covers advanced concepts and techniques. This certification goes beyond the foundational levels of Lean Six Sigma (White Belt, Yellow Belt, and Green Belt) and requires a deeper understanding of statistical analysis, project management, leadership, and change management.
The role of a Lean Six Sigma Black Belt involves leading cross-functional teams, driving improvement initiatives, and delivering tangible results. Black Belts are responsible for identifying improvement opportunities, conducting data analysis, implementing process changes, and ensuring sustained performance through effective control mechanisms.
Achieving Lean Six Sigma Black Belt certification signifies a high level of expertise and proficiency in process improvement methodologies. It demonstrates an individual's ability to apply advanced statistical techniques, lead teams through complex projects, and deliver measurable business outcomes. As a result, professionals with this certification are highly valued in a wide range of industries, including manufacturing, healthcare, finance, logistics, and more.
In conclusion, Lean Six Sigma Black Belt certification offers professionals an opportunity to develop advanced process improvement skills, gain a competitive edge in the job market, and make a significant impact within their organizations. In the following sections of this blog, we will explore the specific requirements, training options, career opportunities, and benefits associated with Lean Six Sigma Black Belt certification.
Lean Six Sigma Black Belt Body of Knowledge
The Lean Six Sigma Black Belt certification encompasses a comprehensive body of knowledge that equips professionals with the necessary skills and tools to lead successful process improvement projects. Let's explore the key areas covered in the Lean Six Sigma Black Belt Body of Knowledge:
- Lean Principles:
- Understanding the core principles of Lean, such as waste identification and elimination, value stream mapping, and continuous flow.
- Applying Lean tools and techniques, including 5S (Sort, Set in Order, Shine, Standardize, Sustain), Kanban, and Kaizen events.
- Six Sigma Methodology:
- Overview of the DMAIC (Define, Measure, Analyze, Improve, Control) framework, which serves as the roadmap for process improvement projects.
- Applying statistical analysis techniques to measure process performance, identify root causes of variation, and quantify improvement opportunities.
- Data Collection and Analysis:
- Selecting appropriate data collection methods and tools.
- Conducting data analysis using descriptive and inferential statistical techniques.
- Utilizing software tools, such as Minitab or Excel, for data analysis and visualization.
- Statistical Process Control (SPC):
- Understanding control charts and their application in monitoring and controlling process stability and capability.
- Implementing control plans to sustain process improvements and prevent deviations.
- Design of Experiments (DOE):
- Applying DOE techniques to understand and optimize process variables, identify critical factors, and achieve robust process performance.
- Utilizing factorial designs, response surface methodology, and other experimental design techniques.
- Process Capability and Performance Metrics:
- Calculating process capability indices (e.g., Cp, Cpk) and understanding their interpretation.
- Defining and monitoring process performance metrics, such as yield, cycle time, and defect rates.
- Project Management:
- Developing project charters and defining project scope.
- Applying project management tools, such as work breakdown structures, Gantt charts, and risk management techniques.
- Change Management and Stakeholder Engagement:
- Identifying stakeholders and their roles in process improvement initiatives.
- Implementing change management strategies to ensure successful adoption of process changes.
- Leadership and Team Management:
- Effective leadership skills to inspire and motivate project teams.
- Facilitating team dynamics, conflict resolution, and consensus-building.
Mastering the Lean Six Sigma Black Belt Body of Knowledge provides professionals with the tools, techniques, and methodologies required to lead complex process improvement projects. By leveraging this knowledge, Black Belts can drive meaningful change, deliver measurable results, and contribute to the overall success of their organizations.
Lean Six Sigma Black Belt Training and Exam
To attain Lean Six Sigma Black Belt certification, individuals must undergo a comprehensive training program and successfully pass a certification exam. Let's explore the key aspects of Lean Six Sigma Black Belt training and the certification exam:
- Training Options:
- Classroom Training: Many organizations and training institutes offer classroom-based Lean Six Sigma Black Belt training programs. These programs typically involve in-person instruction, group activities, and hands-on exercises to reinforce learning.
- Online Training: Online training has gained popularity due to its flexibility and accessibility. Virtual platforms provide self-paced modules, interactive lessons, and virtual simulations to facilitate learning. Online training allows individuals to study at their own convenience from anywhere in the world.
- Blended Learning: Some training providers offer a combination of classroom and online learning, allowing participants to benefit from both in-person interactions and the convenience of online modules.
- Curriculum and Topics Covered:
- In-depth understanding of Lean Six Sigma principles, methodologies, and tools.
- Comprehensive coverage of the DMAIC (Define, Measure, Analyze, Improve, Control) framework.
- Statistical analysis techniques, such as hypothesis testing, regression analysis, and design of experiments.
- Project management methodologies and tools.
- Change management strategies and stakeholder engagement.
- Leadership and team management skills.
- Duration of Training:
- The duration of Lean Six Sigma Black Belt training varies depending on the training provider and the delivery format chosen.
- Classroom-based programs can range from one to two weeks, with several hours of training each day.
- Online training programs allow individuals to study at their own pace, with a typical duration of several weeks to a few months.
- Certification Exam:
- After completing the training program, individuals must pass a certification exam to attain Lean Six Sigma Black Belt certification.
- The exam evaluates the candidate's understanding of Lean Six Sigma concepts, methodologies, and application.
- The exam may include multiple-choice questions, case studies, and real-life scenarios to assess the candidate's knowledge and problem-solving abilities.
- The exam is typically proctored and can be conducted online or in-person, depending on the certification body or training provider.
- Exam Preparation:
- Reviewing training materials and notes to reinforce the knowledge gained during the training program.
- Practicing with sample exam questions and mock exams to familiarize oneself with the format and timing of the actual exam.
- Seeking additional study resources, such as textbooks, reference guides, or online tutorials, to deepen understanding in specific areas.
Successfully achieving Lean Six Sigma Black Belt certification demonstrates an individual's proficiency in Lean Six Sigma methodologies and their ability to lead and drive process improvement initiatives. It opens up a wide range of career opportunities and enhances one's credibility as a process improvement expert.
Roles and Responsibilities of a Lean Six Sigma Black Belt
A Lean Six Sigma Black Belt plays a crucial role in driving process improvement initiatives within an organization. Let's explore the key roles and responsibilities of a Lean Six Sigma Black Belt:
- Project Leadership:
- Lead and manage cross-functional teams involved in process improvement projects.
- Define project goals, scope, and deliverables in alignment with organizational objectives.
- Provide guidance and direction to team members throughout the project lifecycle.
- Process Improvement Expertise:
- Apply Lean Six Sigma principles, methodologies, and tools to identify process inefficiencies, bottlenecks, and areas for improvement.
- Collect and analyze data to quantify process performance and identify root causes of problems.
- Develop and implement solutions that optimize process flow, reduce waste, and improve quality.
- Statistical Analysis and Problem-Solving:
- Utilize statistical analysis techniques to analyze process data, determine process capability, and identify areas for improvement.
- Apply problem-solving methodologies, such as DMAIC (Define, Measure, Analyze, Improve, Control), to systematically address process issues and achieve measurable results.
- Change Management and Stakeholder Engagement:
- Assess and manage the impact of process changes on stakeholders.
- Communicate the benefits and importance of process improvement initiatives to gain buy-in and support.
- Facilitate change management activities, including training, to ensure successful adoption of process improvements.
- Mentoring and Coaching:
- Guide and mentor Green Belts and other team members involved in process improvement projects.
- Provide training and support to help build their Lean Six Sigma skills and capabilities.
- Foster a culture of continuous improvement and knowledge sharing within the organization.
- Project Monitoring and Control:
- Develop and implement control plans to sustain process improvements and prevent deviations.
- Establish performance metrics and measurement systems to track progress and ensure sustained benefits.
- Conduct regular reviews and audits to monitor project performance and make necessary adjustments.
- Collaboration and Communication:
- Collaborate with stakeholders at various levels of the organization to ensure alignment and support for process improvement initiatives.
- Communicate project updates, findings, and recommendations to senior management and relevant stakeholders.
- Facilitate effective teamwork, collaboration, and knowledge sharing among project team members.
Lean Six Sigma Black Belts are instrumental in driving process excellence and achieving significant improvements in operational efficiency, customer satisfaction, and financial outcomes. Their ability to analyze complex problems, lead teams, and implement sustainable solutions makes them valuable assets to organizations across various industries.
Career Opportunities and Advancement with Lean Six Sigma Black Belt
Achieving Lean Six Sigma Black Belt certification opens up a wide range of career opportunities and provides professionals with a competitive edge in the job market. Let's explore the potential career paths and advancement opportunities associated with Lean Six Sigma Black Belt certification:
- Process Improvement Roles:
- Lean Six Sigma Black Belts often pursue careers as Process Improvement Managers, Business Process Analysts, or Continuous Improvement Specialists.
- They lead process improvement initiatives, drive operational efficiency, and implement best practices within organizations.
- These roles can be found across industries such as manufacturing, healthcare, finance, logistics, and service sectors.
- Quality Management:
- Lean Six Sigma Black Belts are well-suited for Quality Manager or Quality Assurance roles.
- They ensure adherence to quality standards, develop and implement quality management systems, and drive continuous improvement in product or service quality.
- Project Management:
- Lean Six Sigma Black Belts possess strong project management skills, making them suitable for Project Manager or Program Manager positions.
- They oversee complex projects, manage timelines, budgets, and resources, and ensure successful project delivery.
- Operations Management:
- Lean Six Sigma Black Belts often transition into Operations Manager or Operations Excellence roles.
- They optimize operational processes, streamline supply chains, and drive overall business performance improvement.
- Change Management and Consulting:
- With their expertise in process improvement and change management, Lean Six Sigma Black Belts can pursue careers in Change Management or Lean Consulting.
- They help organizations navigate through change, implement Lean methodologies, and drive cultural transformation.
- Leadership and Senior Management:
- Lean Six Sigma Black Belt certification enhances leadership skills, making Black Belts suitable for senior management roles.
- They can progress to positions such as Vice President of Operations, Director of Continuous Improvement, or Chief Operating Officer (COO).
Advancement Opportunities:
- Master Black Belt:
- Experienced Lean Six Sigma Black Belts can pursue further advancement by becoming Master Black Belts.
- Master Black Belts mentor and coach Black Belts, oversee multiple projects, and provide guidance in advanced statistical analysis and project selection.
- Executive Leadership:
- Lean Six Sigma Black Belts who demonstrate strong leadership and business acumen may advance to executive-level positions.
- They can take on roles such as Chief Operating Officer (COO), Chief Quality Officer (CQO), or other C-suite positions.
- Entrepreneurship:
- Lean Six Sigma Black Belts equipped with process improvement expertise may choose to start their own consulting firms or become independent consultants.
- They can offer their expertise to organizations seeking to improve processes and drive business performance.
Lean Six Sigma Black Belt certification provides professionals with the skills, knowledge, and credentials to excel in various industries and positions. It enhances career prospects, increases earning potential, and positions individuals as valuable assets in organizations striving for continuous improvement and operational excellence.
Challenges and Limitations of Lean Six Sigma Black Belt
While Lean Six Sigma Black Belt certification offers numerous benefits and opportunities, it is essential to acknowledge the challenges and limitations associated with its implementation. Let's explore some of these challenges and limitations:
- Organizational Culture:
- Resistance to Change: Implementing Lean Six Sigma initiatives requires a cultural shift within an organization. Resistance to change from employees, managers, or stakeholders can pose challenges to the successful adoption of Lean Six Sigma principles and methodologies.
- Lack of Support from Leadership: Without strong support and commitment from top-level management, it can be difficult to drive and sustain Lean Six Sigma initiatives. Leadership involvement is crucial to overcome organizational barriers and allocate necessary resources.
- Data Availability and Quality:
- Incomplete or Inaccurate Data: Availability of complete and accurate data is essential for effective data analysis and decision-making. Limited data availability or poor data quality can hinder the accuracy of analysis and the identification of root causes.
- Data Complexity: In some organizations, data may be complex, scattered across multiple systems, or difficult to access. Managing and analyzing complex data sets can be time-consuming and may require advanced technical skills or specialized tools.
- Project Selection and Scope:
- Project Alignment with Strategic Goals: Identifying projects that align with the organization's strategic objectives can be challenging. Choosing projects that have a significant impact on key performance indicators and business outcomes is crucial for maximizing the benefits of Lean Six Sigma.
- Scope Creep: Ensuring the defined scope of a project remains focused and does not expand beyond its original boundaries can be a challenge. Scope creep can lead to project delays, increased costs, and reduced effectiveness.
- Resource Constraints:
- Time and Resource Allocation: Implementing Lean Six Sigma initiatives requires dedicated time and resources. Balancing project responsibilities with daily operational demands can be challenging, especially for Black Belts who are leading multiple projects simultaneously.
- Skill and Knowledge Gaps: Building a skilled workforce trained in Lean Six Sigma methodologies may take time and effort. Identifying and addressing skill gaps through training and development programs is essential for successful implementation.
- Sustainability and Continuous Improvement:
- Sustaining Results: Sustaining the improvements achieved through Lean Six Sigma initiatives can be challenging. Without ongoing monitoring, control mechanisms, and a culture of continuous improvement, there is a risk of reverting to previous practices.
- Adaptability to Changing Environments: Lean Six Sigma methodologies may not always be suitable for rapidly changing or highly innovative environments. Agile approaches or other methodologies may need to be considered in such cases.
It is important to recognize these challenges and limitations as opportunities for learning and improvement. Organizations implementing Lean Six Sigma should address these challenges proactively by fostering a supportive culture, providing necessary resources, and adapting the methodologies to fit their unique circumstances.
How to obtain the Lean Six Sigma Black Belt certification?
We are an Education Technology company providing certification training courses to accelerate careers of working professionals worldwide. We impart training through instructor-led classroom workshops, instructor-led live virtual training sessions, and self-paced e-learning courses.
We have successfully conducted training sessions in 108 countries across the globe and enabled thousands of working professionals to enhance the scope of their careers.
Our enterprise training portfolio includes in-demand and globally recognized certification training courses in Project Management, Quality Management, Business Analysis, IT Service Management, Agile and Scrum, Cyber Security, Data Science, and Emerging Technologies. Download our Enterprise Training Catalog from https://www.icertglobal.com/corporate-training-for-enterprises.php
Popular Courses include:
- Project Management: PMP, CAPM ,PMI RMP
- Quality Management: Six Sigma Green Belt ,Lean Six Sigma Yellow Belt, Lean Six Sigma Black Belt
- Business Analysis: CBAP, CCBA, ECBA
- Agile Training: PMI-ACP
- Scrum Training: CSM
- DevOps
- Program Management: PgMP
- IT Service Management & Governance: COBIT, ISO
Conclusion
Lean Six Sigma Black Belt certification offers professionals a valuable skill set to drive process improvement and deliver tangible results within organizations. Through a comprehensive training program and certification exam, individuals gain expertise in Lean and Six Sigma methodologies, statistical analysis, project management, and change management.
In this blog, we explored various aspects related to Lean Six Sigma Black Belt certification. We discussed the subtopics of Introduction to Lean Six Sigma Black Belt, Lean Six Sigma Black Belt Body of Knowledge, Lean Six Sigma Black Belt Training and Exam, Roles and Responsibilities of a Lean Six Sigma Black Belt, Career Opportunities and Advancement with Lean Six Sigma Black Belt, and Challenges and Limitations of Lean Six Sigma Black Belt.
By acquiring Lean Six Sigma Black Belt certification, professionals open doors to a wide range of career opportunities, including process improvement roles, quality management, project management, operations management, change management, and even executive leadership positions. The certification also provides a pathway for advancement to higher-level roles, such as Master Black Belt or executive positions within organizations.
However, it is important to acknowledge the challenges and limitations associated with Lean Six Sigma implementation. Overcoming resistance to change, ensuring data availability and quality, project selection and scope management, resource constraints, and sustaining results are among the challenges that organizations may face. Addressing these challenges requires strong leadership support, skill development, and a commitment to a culture of continuous improvement.
Lean Six Sigma Black Belt certification equips professionals with the knowledge and tools to lead process improvement initiatives, optimize operational efficiency, and drive overall business performance. By leveraging their expertise, Black Belts contribute to organizational success, customer satisfaction, and competitive advantage.
As organizations strive for continuous improvement and operational excellence, Lean Six Sigma Black Belts play a critical role in leading the way towards improved processes, enhanced quality, and increased customer value.
Incorporating Lean Six Sigma methodologies and practices into organizations can bring about significant improvements and long-term success. By embracing the benefits and overcoming the challenges, organizations can achieve sustainable and continuous improvement, delivering enhanced value to customers and stakeholders.
So, whether you are an aspiring Lean Six Sigma Black Belt or an organization seeking process improvement, embracing Lean Six Sigma principles and methodologies can undoubtedly pave the way for success.
Everything You Need to Know About Lean Six Sigma Green Belt
Lean Six Sigma Green Belt is a highly recognized certification that equips individuals with the knowledge and skills to lead process improvement initiatives within organizations. It represents a significant level of expertise in Lean Six Sigma methodologies and plays a crucial role in driving operational excellence. In this comprehensive guide, we will explore everything you need to know about Lean Six Sigma Green Belt, including its significance, core principles, and the benefits it offers to both individuals and organizations.
Lean Six Sigma combines the principles of Lean and Six Sigma, aiming to optimize processes, reduce waste, and enhance customer satisfaction. Green Belts are trained to lead and manage improvement projects, utilizing the DMAIC (Define, Measure, Analyze, Improve, Control) methodology as their framework. They possess a deep understanding of statistical analysis, problem-solving techniques, and change management principles.
One of the primary responsibilities of a Lean Six Sigma Green Belt is to identify areas of improvement within an organization's processes. They gather data, analyze performance metrics, and use various tools to pinpoint root causes of problems and inefficiencies. Green Belts collaborate with cross-functional teams to develop and implement solutions, aiming to achieve measurable and sustainable improvements.
In addition to process optimization, Lean Six Sigma Green Belts focus on enhancing customer satisfaction. They strive to understand customer needs and expectations, ensuring that process improvements align with delivering value to the end-users. Green Belts also play a vital role in fostering a culture of continuous improvement within their organizations, driving innovation and employee engagement.
The benefits of Lean Six Sigma Green Belt certification are abundant. Individuals who obtain this certification enhance their problem-solving abilities, data-driven decision-making skills, and leadership capabilities. Green Belts become valuable assets to organizations, capable of delivering significant improvements in quality, efficiency, and customer satisfaction. They often serve as catalysts for change, influencing positive organizational culture and driving bottom-line results.
Organizations that embrace Lean Six Sigma Green Belt professionals gain a competitive edge. They experience reduced costs, improved process cycle times, enhanced product or service quality, and increased customer loyalty. Green Belts contribute to increased productivity, streamlined operations, and a culture of continuous improvement that drives sustained success.
In conclusion, Lean Six Sigma Green Belt certification is a vital step towards process excellence and organizational improvement. Green Belts possess the knowledge, skills, and tools necessary to lead impactful change initiatives and deliver tangible results. By understanding the core principles and benefits outlined in this guide, individuals and organizations can harness the power of Lean Six Sigma Green Belt to drive continuous improvement, customer satisfaction, and long-term success.
Table of contents
- Introduction to Lean Six Sigma Green Belt:
- Roles and Responsibilities of a Lean Six Sigma Green Belt:
- Lean Six Sigma Green Belt Tools and Techniques:
- Data-Driven Decision Making:
- Leadership and Change Management:
- Exam Preparation and Certification Process:
- Conclusion
Introduction to Lean Six Sigma Green Belt:
Lean Six Sigma Green Belt certification is a valuable credential for professionals seeking to enhance their problem-solving skills, improve processes, and drive organizational efficiency. It is an intermediate level of certification within the Lean Six Sigma methodology, focusing on equipping individuals with the knowledge and tools necessary to lead improvement projects and contribute to the overall success of an organization.
Lean Six Sigma combines the principles of Lean, which aims to eliminate waste and increase efficiency, with the statistical and analytical techniques of Six Sigma, which focuses on reducing process variation and improving quality. The Green Belt certification signifies proficiency in both Lean and Six Sigma methodologies and demonstrates an individual's ability to lead process improvement initiatives.
As a Green Belt practitioner, you will play a crucial role in identifying and solving problems within your organization. You will be responsible for collecting and analyzing data, identifying areas of improvement, implementing changes, and monitoring the outcomes. Green Belts often collaborate with cross-functional teams and work closely with Black Belts (more advanced Lean Six Sigma practitioners) to achieve project goals and drive positive change.
The certification process typically involves comprehensive training on Lean Six Sigma concepts, tools, and methodologies. The training covers topics such as process mapping, data analysis, root cause analysis, statistical process control, and project management. Candidates are required to demonstrate their understanding of these concepts through coursework, examinations, and the successful completion of a real-world improvement project.
Obtaining a Lean Six Sigma Green Belt certification offers several benefits. It provides you with a structured approach to problem-solving, equipping you with valuable tools and techniques that can be applied across various industries and sectors. The certification also enhances your credibility and marketability, as it showcases your commitment to quality improvement and your ability to drive tangible results.
Furthermore, Green Belt certification opens up new career opportunities and can lead to promotions or advancements within your current organization. It demonstrates your capacity to identify and resolve operational inefficiencies, reduce costs, enhance customer satisfaction, and contribute to overall business success.
In conclusion, Lean Six Sigma Green Belt certification is a recognized standard for individuals seeking to become proficient in process improvement methodologies. It empowers professionals to make data-driven decisions, implement sustainable changes, and lead improvement projects effectively. By acquiring this certification, you position yourself as a valuable asset to organizations striving for operational excellence and continuous improvement.
Roles and Responsibilities of a Lean Six Sigma Green Belt:
A Lean Six Sigma Green Belt plays a vital role in driving process improvement initiatives within an organization. They are responsible for leading improvement projects, applying Lean and Six Sigma methodologies, and collaborating with cross-functional teams to achieve measurable results. Here are the key roles and responsibilities of a Lean Six Sigma Green Belt:
- Project Leadership: As a Green Belt, you will take on the role of project leader for process improvement initiatives. This involves guiding the project team, setting goals and objectives, and ensuring project deliverables are achieved within the defined timeline.
- Data Collection and Analysis: Green Belts are proficient in data collection techniques and use statistical tools to analyze process performance. They gather relevant data, measure process metrics, identify trends, and perform root cause analysis to pinpoint areas for improvement.
- Process Mapping and Documentation: Green Belts document existing processes through tools like process mapping and flowcharts. They identify inefficiencies, bottlenecks, and waste within the processes and propose improvements to streamline operations.
- Stakeholder Management: Green Belts work closely with various stakeholders, including team members, project sponsors, and subject matter experts. They effectively communicate project progress, manage expectations, and engage stakeholders throughout the improvement journey.
- Problem Solving and Root Cause Analysis: Green Belts utilize problem-solving methodologies like DMAIC (Define, Measure, Analyze, Improve, Control) to identify the root causes of process issues. They apply statistical analysis tools to understand process variations and develop effective solutions.
- Continuous Improvement: Green Belts promote a culture of continuous improvement within the organization. They actively seek opportunities to eliminate waste, reduce defects, and enhance process efficiency. They also facilitate process reviews and suggest improvements to sustain the gains achieved.
- Training and Mentoring: Green Belts may be involved in training and mentoring other team members in Lean and Six Sigma concepts. They share their knowledge and provide guidance to help build a strong problem-solving culture within the organization.
- Project Documentation and Reporting: Green Belts maintain accurate project documentation, including project charters, process maps, data analysis reports, and improvement plans. They prepare progress reports and present findings and recommendations to project sponsors and leadership.
- Collaboration with Black Belts: Green Belts often work alongside Black Belts, who are more advanced Lean Six Sigma practitioners. They support Black Belts in larger-scale improvement projects and assist in data analysis, project management, and implementing improvement strategies.
- Adherence to Lean Six Sigma Methodology: Green Belts follow the principles and methodologies of Lean Six Sigma, adhering to standardized tools, processes, and best practices. They ensure compliance with project management frameworks and quality standards.
Lean Six Sigma Green Belt Tools and Techniques
Lean Six Sigma Green Belts are equipped with a variety of tools and techniques that help them analyze data, identify process improvement opportunities, and drive change within an organization. Here are some commonly used tools and techniques utilized by Lean Six Sigma Green Belts:
- Value Stream Mapping (VSM): Value Stream Mapping is a visual tool used to analyze and improve the flow of materials, information, and activities involved in delivering a product or service. It helps identify bottlenecks, waste, and areas of improvement within a process.
- Process Mapping: Process mapping involves documenting and visualizing the steps, activities, and interactions in a process. It provides a clear understanding of the process flow, identifies redundancies, and helps in identifying opportunities for improvement.
- Root Cause Analysis (RCA): Root Cause Analysis is a systematic approach used to identify the underlying causes of a problem or defect. Techniques such as the 5 Whys, Cause and Effect Diagrams (Fishbone Diagrams), and Failure Mode and Effects Analysis (FMEA) are commonly employed by Green Belts during RCA.
- Statistical Process Control (SPC): SPC involves using statistical techniques to monitor and control process performance. Control charts, histograms, and Pareto charts are some of the tools used to analyze process data, identify trends, and determine if a process is stable and within control limits.
- Measurement System Analysis (MSA): MSA assesses the reliability and accuracy of the measurement systems used to collect process data. Tools like Gage R&R (Repeatability and Reproducibility) help determine if the measurement system is capable of producing valid and consistent data.
- Hypothesis Testing: Hypothesis testing is used to make data-driven decisions by comparing sample data to a hypothesis or claim about a population. Tools such as t-tests, chi-square tests, and ANOVA (Analysis of Variance) are used to determine if there are significant differences between groups or variables.
- Design of Experiments (DOE): DOE is a structured approach used to understand the relationship between process variables and their impact on output or performance. Green Belts use experimental design techniques to optimize process settings and identify the most influential factors affecting process performance.
- Kaizen Events: Kaizen events, also known as rapid improvement events or workshops, involve focused and intense improvement activities carried out by cross-functional teams. Green Belts facilitate these events to address specific process issues, generate ideas, and implement improvements within a short time frame.
- 5S Methodology: 5S is a workplace organization and visual management system that aims to create a clean, organized, and efficient work environment. The five S's stand for Sort, Set in Order, Shine, Standardize, and Sustain.
- Poka-Yoke: Poka-Yoke refers to mistake-proofing techniques that prevent errors or defects from occurring in a process. Green Belts employ visual cues, error-proofing devices, and process controls to minimize the risk of mistakes and improve process reliability.
Data-Driven Decision Making
Data-driven decision making is a systematic approach that involves collecting, analyzing, and interpreting data to guide informed and objective decision making. It emphasizes using quantitative and qualitative data to reduce bias, uncover insights, and support the selection of the best course of action. In the context of Lean Six Sigma, data-driven decision making is a fundamental principle for process improvement. Here are key aspects of data-driven decision making:
- Data Collection: Data collection involves gathering relevant information from various sources. This may include measurements, observations, surveys, customer feedback, and historical records. Green Belts ensure that the data collected is accurate, reliable, and representative of the process being analyzed.
- Data Analysis: Data analysis is the process of examining and interpreting collected data to identify patterns, trends, relationships, and insights. Green Belts use statistical tools and techniques such as descriptive statistics, graphical analysis, hypothesis testing, regression analysis, and control charts to analyze the data effectively.
- Fact-Based Decision Making: Data-driven decision making emphasizes basing decisions on objective evidence rather than personal opinions or assumptions. Green Belts ensure that decisions are supported by the data analysis results, allowing for a more rational and defensible approach.
- Identifying Patterns and Trends: By analyzing data, Green Belts can identify patterns and trends in process performance. They can uncover root causes of problems, understand process variations, and recognize opportunities for improvement. This helps in making targeted and effective decisions to address process issues.
- Risk Assessment: Data-driven decision making allows Green Belts to assess risks associated with potential decisions. By analyzing historical data and considering different scenarios, they can evaluate the potential impact of decisions on process performance, customer satisfaction, and organizational objectives.
- Continuous Improvement: Data-driven decision making is an iterative process. Green Belts monitor key performance indicators (KPIs) and track progress over time to ensure that decisions lead to the desired outcomes. If necessary, they make adjustments based on new data and insights to drive continuous improvement.
- Communication and Visualization: Green Belts use data visualization techniques, such as charts, graphs, and dashboards, to present data in a clear and concise manner. This facilitates effective communication with stakeholders, enabling them to understand the insights derived from the data analysis and make informed decisions.
- Data Integrity and Quality: Green Belts are responsible for ensuring data integrity and quality. They validate data sources, address data limitations, and apply appropriate data cleaning techniques to remove errors or outliers that may affect the accuracy and reliability of the analysis.
By adopting a data-driven approach, Green Belts can make more informed decisions, reduce subjectivity, and minimize the risks associated with decision making. It enables them to prioritize improvement efforts, validate hypotheses, measure the effectiveness of implemented changes, and drive sustainable results within their organization.
Leadership and Change Management
Leadership and change management are critical aspects of Lean Six Sigma Green Belt roles. As a Green Belt, you not only drive process improvement initiatives but also play a key role in leading teams, managing stakeholders, and navigating the organizational change required for successful implementation. Here are important considerations for leadership and change management in the context of Lean Six Sigma:
- Leading by Example: Effective Green Belts lead by example, demonstrating a commitment to continuous improvement and a strong work ethic. They embody the principles and values of Lean Six Sigma, encouraging others to embrace change and actively participate in improvement efforts.
- Vision and Goal Setting: Green Belts establish a clear vision and set specific improvement goals for their projects. They communicate the vision and goals to the team, ensuring alignment and shared understanding of the desired outcomes. Green Belts inspire and motivate their teams to achieve those goals.
- Team Engagement and Collaboration: Green Belts foster a collaborative team environment, encouraging active participation and engagement from team members. They facilitate effective communication, create opportunities for idea sharing, and ensure that everyone feels valued and supported throughout the improvement process.
- Stakeholder Management: Green Belts identify and engage with key stakeholders, such as project sponsors, process owners, and subject matter experts. They build relationships, manage expectations, and involve stakeholders in the decision-making process. Effective communication and regular updates are essential to keep stakeholders informed and gain their support.
- Change Communication: Change management involves effectively communicating the purpose, benefits, and progress of process improvement initiatives to all relevant stakeholders. Green Belts use various communication channels to ensure that the organization understands the need for change, the expected outcomes, and the role each individual plays in the transformation.
- Change Resistance Management: Change often encounters resistance from individuals or teams. Green Belts proactively address resistance by listening to concerns, addressing misconceptions, and involving stakeholders in the change process. They identify and mitigate potential barriers, providing support and guidance to overcome resistance.
- Training and Skill Development: Green Belts recognize the importance of equipping team members with the necessary knowledge and skills to drive change. They identify training needs, provide appropriate training opportunities, and mentor team members to enhance their understanding of Lean Six Sigma principles and methodologies.
- Continuous Learning and Improvement: Effective Green Belts are lifelong learners who continuously seek opportunities to enhance their own skills and knowledge. They stay up to date with industry trends, emerging best practices, and advancements in Lean Six Sigma. They share their learning with the team and encourage a culture of continuous improvement.
- Celebrating Success and Recognizing Contributions: Green Belts acknowledge and celebrate successes achieved through process improvements. They recognize the contributions of team members, highlighting their efforts and achievements. This fosters a positive environment and motivates individuals to continue their commitment to improvement.
By effectively managing leadership and change management aspects, Green Belts can navigate the complexities of implementing Lean Six Sigma projects. They inspire and guide their teams, manage stakeholders, address resistance, and foster a culture of continuous improvement. Strong leadership and change management skills are essential for driving successful outcomes and sustaining improvements within an organization.
Exam Preparation and Certification Process for Lean Six Sigma Green Belt:
Preparing for the Lean Six Sigma Green Belt certification exam requires a comprehensive understanding of Lean Six Sigma concepts, tools, and methodologies. Here are the steps involved in exam preparation and the certification process:
- Understand the Exam Requirements: Start by familiarizing yourself with the exam requirements set by the certification body or organization offering the Lean Six Sigma Green Belt certification. Understand the eligibility criteria, exam format, duration, and passing score.
- Obtain Study Materials: Gather study materials such as textbooks, reference guides, online resources, and practice exams. These resources should cover the core principles of Lean Six Sigma, DMAIC methodology, statistical analysis tools, and problem-solving techniques.
- Enroll in a Training Program: Consider enrolling in a Lean Six Sigma Green Belt training program. These programs provide structured training, practical examples, and guidance from experienced instructors. Choose a reputable training provider that aligns with your learning preferences (e.g., in-person, virtual, or self-paced).
- Attend Training Sessions: Participate actively in the training sessions and make the most of the learning opportunities. Engage in discussions, ask questions, and collaborate with fellow participants to deepen your understanding of Lean Six Sigma concepts. Take advantage of hands-on exercises and case studies to apply the learned principles in real-world scenarios.
- Study and Review: Dedicate sufficient time to self-study and review the training materials. Create a study plan that covers all the relevant topics and allocate regular study sessions. Focus on understanding key concepts, tools, and their applications. Take notes, create study guides, and summarize important information to aid in retention.
- Practice with Sample Exams: Take advantage of sample exams and practice questions to assess your knowledge and identify areas for improvement. These practice exams simulate the actual exam environment and help you become familiar with the question format and time constraints. Analyze your performance and review the explanations for correct and incorrect answers.
- Reinforce Learning through Projects: Apply Lean Six Sigma principles to real-life projects within your organization or in simulated scenarios. By working on improvement projects, you gain hands-on experience and reinforce your understanding of the methodologies. Document the projects, including problem statements, data analysis, improvement strategies, and outcomes achieved.
- Exam Registration: Once you feel confident in your knowledge and preparation, register for the Lean Six Sigma Green Belt certification exam. Follow the registration instructions provided by the certification body and pay the necessary fees. Ensure that you meet any eligibility requirements set by the certification provider.
- Take the Exam: On the scheduled exam date, arrive early and ensure that you have any required identification or documentation. During the exam, read each question carefully, manage your time effectively, and answer to the best of your knowledge. Stay focused and avoid rushing through the questions. If you encounter challenging questions, mark them for review and revisit them later.
- Certification and Continued Learning: After completing the exam, wait for the results to be announced by the certification body. If you meet the passing criteria, you will receive the Lean Six Sigma Green Belt certification. Celebrate your achievement and continue to deepen your knowledge through continuous learning, attending workshops, and staying updated with industry trends.
Remember, the certification process and exam format may vary depending on the certification body or organization. It is essential to review the specific requirements and guidelines provided by the certification provider you choose.
How to obtain the Lean Six Sigma Green Belt certification?
We are an Education Technology company providing certification training courses to accelerate careers of working professionals worldwide. We impart training through instructor-led classroom workshops, instructor-led live virtual training sessions, and self-paced e-learning courses.
We have successfully conducted training sessions in 108 countries across the globe and enabled thousands of working professionals to enhance the scope of their careers.
Our enterprise training portfolio includes in-demand and globally recognized certification training courses in Project Management, Quality Management, Business Analysis, IT Service Management, Agile and Scrum, Cyber Security, Data Science, and Emerging Technologies. Download our Enterprise Training Catalog from https://www.icertglobal.com/corporate-training-for-enterprises.php
Popular Courses include:
- Project Management: PMP, CAPM ,PMI RMP
- Quality Management: Six Sigma Green Belt ,Lean Six Sigma Green Belt, Lean Six Sigma Black Belt
- Business Analysis: CBAP, CCBA, ECBA
- Agile Training: PMI-ACP
- Scrum Training: CSM
- DevOps
- Program Management: PgMP
- IT Service Management & Governance: COBIT, ISO
Conclusion
In conclusion, Lean Six Sigma Green Belt certification is a valuable achievement for professionals seeking to enhance their skills in process improvement and data-driven decision making. Throughout this blog, we have explored various subtopics related to Lean Six Sigma Green Belt certification.
We began by introducing Lean Six Sigma Green Belt and highlighting its significance in organizations. We discussed the roles and responsibilities of Green Belts, emphasizing their crucial role in driving process improvements and achieving organizational goals.
Next, we delved into the essential tools and techniques utilized by Lean Six Sigma Green Belts. These tools, ranging from Value Stream Mapping to Statistical Process Control, enable Green Belts to analyze data, identify process inefficiencies, and implement effective solutions.
We then explored the importance of data-driven decision making in Lean Six Sigma. Leveraging data to make informed and objective decisions is vital for achieving sustainable process improvements and driving organizational success.
Furthermore, we discussed the critical aspect of leadership and change management in the Lean Six Sigma Green Belt role. Effective leadership, stakeholder management, and change communication are essential for successfully implementing process improvements and overcoming resistance to change.
Finally, we covered the exam preparation and certification process for Lean Six Sigma Green Belt. This included understanding exam requirements, obtaining study materials, enrolling in training programs, practicing with sample exams, and completing the certification exam.
By obtaining Lean Six Sigma Green Belt certification, professionals gain a comprehensive skill set that allows them to contribute significantly to process improvement initiatives within their organizations. The certification validates their knowledge, expertise, and commitment to driving continuous improvement.
Lean Six Sigma Green Belt certification is a stepping stone towards higher levels of Lean Six Sigma certification, such as the Black Belt or Master Black Belt. It opens doors to career advancement opportunities and positions individuals as valuable assets in the pursuit of operational excellence.
In conclusion, Lean Six Sigma Green Belt certification equips professionals with the tools, methodologies, and leadership skills necessary to bring about positive change and drive process optimization in organizations
Read More
Lean Six Sigma Green Belt is a highly recognized certification that equips individuals with the knowledge and skills to lead process improvement initiatives within organizations. It represents a significant level of expertise in Lean Six Sigma methodologies and plays a crucial role in driving operational excellence. In this comprehensive guide, we will explore everything you need to know about Lean Six Sigma Green Belt, including its significance, core principles, and the benefits it offers to both individuals and organizations.
Lean Six Sigma combines the principles of Lean and Six Sigma, aiming to optimize processes, reduce waste, and enhance customer satisfaction. Green Belts are trained to lead and manage improvement projects, utilizing the DMAIC (Define, Measure, Analyze, Improve, Control) methodology as their framework. They possess a deep understanding of statistical analysis, problem-solving techniques, and change management principles.
One of the primary responsibilities of a Lean Six Sigma Green Belt is to identify areas of improvement within an organization's processes. They gather data, analyze performance metrics, and use various tools to pinpoint root causes of problems and inefficiencies. Green Belts collaborate with cross-functional teams to develop and implement solutions, aiming to achieve measurable and sustainable improvements.
In addition to process optimization, Lean Six Sigma Green Belts focus on enhancing customer satisfaction. They strive to understand customer needs and expectations, ensuring that process improvements align with delivering value to the end-users. Green Belts also play a vital role in fostering a culture of continuous improvement within their organizations, driving innovation and employee engagement.
The benefits of Lean Six Sigma Green Belt certification are abundant. Individuals who obtain this certification enhance their problem-solving abilities, data-driven decision-making skills, and leadership capabilities. Green Belts become valuable assets to organizations, capable of delivering significant improvements in quality, efficiency, and customer satisfaction. They often serve as catalysts for change, influencing positive organizational culture and driving bottom-line results.
Organizations that embrace Lean Six Sigma Green Belt professionals gain a competitive edge. They experience reduced costs, improved process cycle times, enhanced product or service quality, and increased customer loyalty. Green Belts contribute to increased productivity, streamlined operations, and a culture of continuous improvement that drives sustained success.
In conclusion, Lean Six Sigma Green Belt certification is a vital step towards process excellence and organizational improvement. Green Belts possess the knowledge, skills, and tools necessary to lead impactful change initiatives and deliver tangible results. By understanding the core principles and benefits outlined in this guide, individuals and organizations can harness the power of Lean Six Sigma Green Belt to drive continuous improvement, customer satisfaction, and long-term success.
Table of contents
- Introduction to Lean Six Sigma Green Belt:
- Roles and Responsibilities of a Lean Six Sigma Green Belt:
- Lean Six Sigma Green Belt Tools and Techniques:
- Data-Driven Decision Making:
- Leadership and Change Management:
- Exam Preparation and Certification Process:
- Conclusion
Introduction to Lean Six Sigma Green Belt:
Lean Six Sigma Green Belt certification is a valuable credential for professionals seeking to enhance their problem-solving skills, improve processes, and drive organizational efficiency. It is an intermediate level of certification within the Lean Six Sigma methodology, focusing on equipping individuals with the knowledge and tools necessary to lead improvement projects and contribute to the overall success of an organization.
Lean Six Sigma combines the principles of Lean, which aims to eliminate waste and increase efficiency, with the statistical and analytical techniques of Six Sigma, which focuses on reducing process variation and improving quality. The Green Belt certification signifies proficiency in both Lean and Six Sigma methodologies and demonstrates an individual's ability to lead process improvement initiatives.
As a Green Belt practitioner, you will play a crucial role in identifying and solving problems within your organization. You will be responsible for collecting and analyzing data, identifying areas of improvement, implementing changes, and monitoring the outcomes. Green Belts often collaborate with cross-functional teams and work closely with Black Belts (more advanced Lean Six Sigma practitioners) to achieve project goals and drive positive change.
The certification process typically involves comprehensive training on Lean Six Sigma concepts, tools, and methodologies. The training covers topics such as process mapping, data analysis, root cause analysis, statistical process control, and project management. Candidates are required to demonstrate their understanding of these concepts through coursework, examinations, and the successful completion of a real-world improvement project.
Obtaining a Lean Six Sigma Green Belt certification offers several benefits. It provides you with a structured approach to problem-solving, equipping you with valuable tools and techniques that can be applied across various industries and sectors. The certification also enhances your credibility and marketability, as it showcases your commitment to quality improvement and your ability to drive tangible results.
Furthermore, Green Belt certification opens up new career opportunities and can lead to promotions or advancements within your current organization. It demonstrates your capacity to identify and resolve operational inefficiencies, reduce costs, enhance customer satisfaction, and contribute to overall business success.
In conclusion, Lean Six Sigma Green Belt certification is a recognized standard for individuals seeking to become proficient in process improvement methodologies. It empowers professionals to make data-driven decisions, implement sustainable changes, and lead improvement projects effectively. By acquiring this certification, you position yourself as a valuable asset to organizations striving for operational excellence and continuous improvement.
Roles and Responsibilities of a Lean Six Sigma Green Belt:
A Lean Six Sigma Green Belt plays a vital role in driving process improvement initiatives within an organization. They are responsible for leading improvement projects, applying Lean and Six Sigma methodologies, and collaborating with cross-functional teams to achieve measurable results. Here are the key roles and responsibilities of a Lean Six Sigma Green Belt:
- Project Leadership: As a Green Belt, you will take on the role of project leader for process improvement initiatives. This involves guiding the project team, setting goals and objectives, and ensuring project deliverables are achieved within the defined timeline.
- Data Collection and Analysis: Green Belts are proficient in data collection techniques and use statistical tools to analyze process performance. They gather relevant data, measure process metrics, identify trends, and perform root cause analysis to pinpoint areas for improvement.
- Process Mapping and Documentation: Green Belts document existing processes through tools like process mapping and flowcharts. They identify inefficiencies, bottlenecks, and waste within the processes and propose improvements to streamline operations.
- Stakeholder Management: Green Belts work closely with various stakeholders, including team members, project sponsors, and subject matter experts. They effectively communicate project progress, manage expectations, and engage stakeholders throughout the improvement journey.
- Problem Solving and Root Cause Analysis: Green Belts utilize problem-solving methodologies like DMAIC (Define, Measure, Analyze, Improve, Control) to identify the root causes of process issues. They apply statistical analysis tools to understand process variations and develop effective solutions.
- Continuous Improvement: Green Belts promote a culture of continuous improvement within the organization. They actively seek opportunities to eliminate waste, reduce defects, and enhance process efficiency. They also facilitate process reviews and suggest improvements to sustain the gains achieved.
- Training and Mentoring: Green Belts may be involved in training and mentoring other team members in Lean and Six Sigma concepts. They share their knowledge and provide guidance to help build a strong problem-solving culture within the organization.
- Project Documentation and Reporting: Green Belts maintain accurate project documentation, including project charters, process maps, data analysis reports, and improvement plans. They prepare progress reports and present findings and recommendations to project sponsors and leadership.
- Collaboration with Black Belts: Green Belts often work alongside Black Belts, who are more advanced Lean Six Sigma practitioners. They support Black Belts in larger-scale improvement projects and assist in data analysis, project management, and implementing improvement strategies.
- Adherence to Lean Six Sigma Methodology: Green Belts follow the principles and methodologies of Lean Six Sigma, adhering to standardized tools, processes, and best practices. They ensure compliance with project management frameworks and quality standards.
Lean Six Sigma Green Belt Tools and Techniques
Lean Six Sigma Green Belts are equipped with a variety of tools and techniques that help them analyze data, identify process improvement opportunities, and drive change within an organization. Here are some commonly used tools and techniques utilized by Lean Six Sigma Green Belts:
- Value Stream Mapping (VSM): Value Stream Mapping is a visual tool used to analyze and improve the flow of materials, information, and activities involved in delivering a product or service. It helps identify bottlenecks, waste, and areas of improvement within a process.
- Process Mapping: Process mapping involves documenting and visualizing the steps, activities, and interactions in a process. It provides a clear understanding of the process flow, identifies redundancies, and helps in identifying opportunities for improvement.
- Root Cause Analysis (RCA): Root Cause Analysis is a systematic approach used to identify the underlying causes of a problem or defect. Techniques such as the 5 Whys, Cause and Effect Diagrams (Fishbone Diagrams), and Failure Mode and Effects Analysis (FMEA) are commonly employed by Green Belts during RCA.
- Statistical Process Control (SPC): SPC involves using statistical techniques to monitor and control process performance. Control charts, histograms, and Pareto charts are some of the tools used to analyze process data, identify trends, and determine if a process is stable and within control limits.
- Measurement System Analysis (MSA): MSA assesses the reliability and accuracy of the measurement systems used to collect process data. Tools like Gage R&R (Repeatability and Reproducibility) help determine if the measurement system is capable of producing valid and consistent data.
- Hypothesis Testing: Hypothesis testing is used to make data-driven decisions by comparing sample data to a hypothesis or claim about a population. Tools such as t-tests, chi-square tests, and ANOVA (Analysis of Variance) are used to determine if there are significant differences between groups or variables.
- Design of Experiments (DOE): DOE is a structured approach used to understand the relationship between process variables and their impact on output or performance. Green Belts use experimental design techniques to optimize process settings and identify the most influential factors affecting process performance.
- Kaizen Events: Kaizen events, also known as rapid improvement events or workshops, involve focused and intense improvement activities carried out by cross-functional teams. Green Belts facilitate these events to address specific process issues, generate ideas, and implement improvements within a short time frame.
- 5S Methodology: 5S is a workplace organization and visual management system that aims to create a clean, organized, and efficient work environment. The five S's stand for Sort, Set in Order, Shine, Standardize, and Sustain.
- Poka-Yoke: Poka-Yoke refers to mistake-proofing techniques that prevent errors or defects from occurring in a process. Green Belts employ visual cues, error-proofing devices, and process controls to minimize the risk of mistakes and improve process reliability.
Data-Driven Decision Making
Data-driven decision making is a systematic approach that involves collecting, analyzing, and interpreting data to guide informed and objective decision making. It emphasizes using quantitative and qualitative data to reduce bias, uncover insights, and support the selection of the best course of action. In the context of Lean Six Sigma, data-driven decision making is a fundamental principle for process improvement. Here are key aspects of data-driven decision making:
- Data Collection: Data collection involves gathering relevant information from various sources. This may include measurements, observations, surveys, customer feedback, and historical records. Green Belts ensure that the data collected is accurate, reliable, and representative of the process being analyzed.
- Data Analysis: Data analysis is the process of examining and interpreting collected data to identify patterns, trends, relationships, and insights. Green Belts use statistical tools and techniques such as descriptive statistics, graphical analysis, hypothesis testing, regression analysis, and control charts to analyze the data effectively.
- Fact-Based Decision Making: Data-driven decision making emphasizes basing decisions on objective evidence rather than personal opinions or assumptions. Green Belts ensure that decisions are supported by the data analysis results, allowing for a more rational and defensible approach.
- Identifying Patterns and Trends: By analyzing data, Green Belts can identify patterns and trends in process performance. They can uncover root causes of problems, understand process variations, and recognize opportunities for improvement. This helps in making targeted and effective decisions to address process issues.
- Risk Assessment: Data-driven decision making allows Green Belts to assess risks associated with potential decisions. By analyzing historical data and considering different scenarios, they can evaluate the potential impact of decisions on process performance, customer satisfaction, and organizational objectives.
- Continuous Improvement: Data-driven decision making is an iterative process. Green Belts monitor key performance indicators (KPIs) and track progress over time to ensure that decisions lead to the desired outcomes. If necessary, they make adjustments based on new data and insights to drive continuous improvement.
- Communication and Visualization: Green Belts use data visualization techniques, such as charts, graphs, and dashboards, to present data in a clear and concise manner. This facilitates effective communication with stakeholders, enabling them to understand the insights derived from the data analysis and make informed decisions.
- Data Integrity and Quality: Green Belts are responsible for ensuring data integrity and quality. They validate data sources, address data limitations, and apply appropriate data cleaning techniques to remove errors or outliers that may affect the accuracy and reliability of the analysis.
By adopting a data-driven approach, Green Belts can make more informed decisions, reduce subjectivity, and minimize the risks associated with decision making. It enables them to prioritize improvement efforts, validate hypotheses, measure the effectiveness of implemented changes, and drive sustainable results within their organization.
Leadership and Change Management
Leadership and change management are critical aspects of Lean Six Sigma Green Belt roles. As a Green Belt, you not only drive process improvement initiatives but also play a key role in leading teams, managing stakeholders, and navigating the organizational change required for successful implementation. Here are important considerations for leadership and change management in the context of Lean Six Sigma:
- Leading by Example: Effective Green Belts lead by example, demonstrating a commitment to continuous improvement and a strong work ethic. They embody the principles and values of Lean Six Sigma, encouraging others to embrace change and actively participate in improvement efforts.
- Vision and Goal Setting: Green Belts establish a clear vision and set specific improvement goals for their projects. They communicate the vision and goals to the team, ensuring alignment and shared understanding of the desired outcomes. Green Belts inspire and motivate their teams to achieve those goals.
- Team Engagement and Collaboration: Green Belts foster a collaborative team environment, encouraging active participation and engagement from team members. They facilitate effective communication, create opportunities for idea sharing, and ensure that everyone feels valued and supported throughout the improvement process.
- Stakeholder Management: Green Belts identify and engage with key stakeholders, such as project sponsors, process owners, and subject matter experts. They build relationships, manage expectations, and involve stakeholders in the decision-making process. Effective communication and regular updates are essential to keep stakeholders informed and gain their support.
- Change Communication: Change management involves effectively communicating the purpose, benefits, and progress of process improvement initiatives to all relevant stakeholders. Green Belts use various communication channels to ensure that the organization understands the need for change, the expected outcomes, and the role each individual plays in the transformation.
- Change Resistance Management: Change often encounters resistance from individuals or teams. Green Belts proactively address resistance by listening to concerns, addressing misconceptions, and involving stakeholders in the change process. They identify and mitigate potential barriers, providing support and guidance to overcome resistance.
- Training and Skill Development: Green Belts recognize the importance of equipping team members with the necessary knowledge and skills to drive change. They identify training needs, provide appropriate training opportunities, and mentor team members to enhance their understanding of Lean Six Sigma principles and methodologies.
- Continuous Learning and Improvement: Effective Green Belts are lifelong learners who continuously seek opportunities to enhance their own skills and knowledge. They stay up to date with industry trends, emerging best practices, and advancements in Lean Six Sigma. They share their learning with the team and encourage a culture of continuous improvement.
- Celebrating Success and Recognizing Contributions: Green Belts acknowledge and celebrate successes achieved through process improvements. They recognize the contributions of team members, highlighting their efforts and achievements. This fosters a positive environment and motivates individuals to continue their commitment to improvement.
By effectively managing leadership and change management aspects, Green Belts can navigate the complexities of implementing Lean Six Sigma projects. They inspire and guide their teams, manage stakeholders, address resistance, and foster a culture of continuous improvement. Strong leadership and change management skills are essential for driving successful outcomes and sustaining improvements within an organization.
Exam Preparation and Certification Process for Lean Six Sigma Green Belt:
Preparing for the Lean Six Sigma Green Belt certification exam requires a comprehensive understanding of Lean Six Sigma concepts, tools, and methodologies. Here are the steps involved in exam preparation and the certification process:
- Understand the Exam Requirements: Start by familiarizing yourself with the exam requirements set by the certification body or organization offering the Lean Six Sigma Green Belt certification. Understand the eligibility criteria, exam format, duration, and passing score.
- Obtain Study Materials: Gather study materials such as textbooks, reference guides, online resources, and practice exams. These resources should cover the core principles of Lean Six Sigma, DMAIC methodology, statistical analysis tools, and problem-solving techniques.
- Enroll in a Training Program: Consider enrolling in a Lean Six Sigma Green Belt training program. These programs provide structured training, practical examples, and guidance from experienced instructors. Choose a reputable training provider that aligns with your learning preferences (e.g., in-person, virtual, or self-paced).
- Attend Training Sessions: Participate actively in the training sessions and make the most of the learning opportunities. Engage in discussions, ask questions, and collaborate with fellow participants to deepen your understanding of Lean Six Sigma concepts. Take advantage of hands-on exercises and case studies to apply the learned principles in real-world scenarios.
- Study and Review: Dedicate sufficient time to self-study and review the training materials. Create a study plan that covers all the relevant topics and allocate regular study sessions. Focus on understanding key concepts, tools, and their applications. Take notes, create study guides, and summarize important information to aid in retention.
- Practice with Sample Exams: Take advantage of sample exams and practice questions to assess your knowledge and identify areas for improvement. These practice exams simulate the actual exam environment and help you become familiar with the question format and time constraints. Analyze your performance and review the explanations for correct and incorrect answers.
- Reinforce Learning through Projects: Apply Lean Six Sigma principles to real-life projects within your organization or in simulated scenarios. By working on improvement projects, you gain hands-on experience and reinforce your understanding of the methodologies. Document the projects, including problem statements, data analysis, improvement strategies, and outcomes achieved.
- Exam Registration: Once you feel confident in your knowledge and preparation, register for the Lean Six Sigma Green Belt certification exam. Follow the registration instructions provided by the certification body and pay the necessary fees. Ensure that you meet any eligibility requirements set by the certification provider.
- Take the Exam: On the scheduled exam date, arrive early and ensure that you have any required identification or documentation. During the exam, read each question carefully, manage your time effectively, and answer to the best of your knowledge. Stay focused and avoid rushing through the questions. If you encounter challenging questions, mark them for review and revisit them later.
- Certification and Continued Learning: After completing the exam, wait for the results to be announced by the certification body. If you meet the passing criteria, you will receive the Lean Six Sigma Green Belt certification. Celebrate your achievement and continue to deepen your knowledge through continuous learning, attending workshops, and staying updated with industry trends.
Remember, the certification process and exam format may vary depending on the certification body or organization. It is essential to review the specific requirements and guidelines provided by the certification provider you choose.
How to obtain the Lean Six Sigma Green Belt certification?
We are an Education Technology company providing certification training courses to accelerate careers of working professionals worldwide. We impart training through instructor-led classroom workshops, instructor-led live virtual training sessions, and self-paced e-learning courses.
We have successfully conducted training sessions in 108 countries across the globe and enabled thousands of working professionals to enhance the scope of their careers.
Our enterprise training portfolio includes in-demand and globally recognized certification training courses in Project Management, Quality Management, Business Analysis, IT Service Management, Agile and Scrum, Cyber Security, Data Science, and Emerging Technologies. Download our Enterprise Training Catalog from https://www.icertglobal.com/corporate-training-for-enterprises.php
Popular Courses include:
- Project Management: PMP, CAPM ,PMI RMP
- Quality Management: Six Sigma Green Belt ,Lean Six Sigma Green Belt, Lean Six Sigma Black Belt
- Business Analysis: CBAP, CCBA, ECBA
- Agile Training: PMI-ACP
- Scrum Training: CSM
- DevOps
- Program Management: PgMP
- IT Service Management & Governance: COBIT, ISO
Conclusion
In conclusion, Lean Six Sigma Green Belt certification is a valuable achievement for professionals seeking to enhance their skills in process improvement and data-driven decision making. Throughout this blog, we have explored various subtopics related to Lean Six Sigma Green Belt certification.
We began by introducing Lean Six Sigma Green Belt and highlighting its significance in organizations. We discussed the roles and responsibilities of Green Belts, emphasizing their crucial role in driving process improvements and achieving organizational goals.
Next, we delved into the essential tools and techniques utilized by Lean Six Sigma Green Belts. These tools, ranging from Value Stream Mapping to Statistical Process Control, enable Green Belts to analyze data, identify process inefficiencies, and implement effective solutions.
We then explored the importance of data-driven decision making in Lean Six Sigma. Leveraging data to make informed and objective decisions is vital for achieving sustainable process improvements and driving organizational success.
Furthermore, we discussed the critical aspect of leadership and change management in the Lean Six Sigma Green Belt role. Effective leadership, stakeholder management, and change communication are essential for successfully implementing process improvements and overcoming resistance to change.
Finally, we covered the exam preparation and certification process for Lean Six Sigma Green Belt. This included understanding exam requirements, obtaining study materials, enrolling in training programs, practicing with sample exams, and completing the certification exam.
By obtaining Lean Six Sigma Green Belt certification, professionals gain a comprehensive skill set that allows them to contribute significantly to process improvement initiatives within their organizations. The certification validates their knowledge, expertise, and commitment to driving continuous improvement.
Lean Six Sigma Green Belt certification is a stepping stone towards higher levels of Lean Six Sigma certification, such as the Black Belt or Master Black Belt. It opens doors to career advancement opportunities and positions individuals as valuable assets in the pursuit of operational excellence.
In conclusion, Lean Six Sigma Green Belt certification equips professionals with the tools, methodologies, and leadership skills necessary to bring about positive change and drive process optimization in organizations
Essential Guide to Lean Six Sigma Yellow Belt Fundamentals
The Essential Guide to Lean Six Sigma Yellow Belt: Fundamentals serves as a comprehensive resource for individuals looking to develop a strong foundation in Lean Six Sigma methodologies. The Yellow Belt certification is an essential step on the journey to process improvement and organizational excellence. In this guide, we will delve into the core principles and concepts that form the basis of Lean Six Sigma Yellow Belt training, providing a comprehensive understanding of its fundamentals.
Lean Six Sigma combines two powerful approaches to process improvement: Lean and Six Sigma. It emphasizes the elimination of waste, reduction of defects, and continuous improvement, all while ensuring customer satisfaction and delivering value. The Yellow Belt certification equips individuals with the knowledge and skills to actively participate in process improvement initiatives within their teams or departments.
The Essential Guide to Lean Six Sigma Yellow Belt: Fundamentals covers the key elements of the DMAIC (Define, Measure, Analyze, Improve, Control) methodology. Yellow Belts learn how to define project goals, identify customer requirements, and map process flows. They gain insights into data collection and analysis techniques, enabling them to measure process performance and identify improvement opportunities. Additionally, Yellow Belts develop problem-solving skills and learn to apply basic statistical tools to understand and address root causes of problems.
This guide also explores the fundamental concepts of waste reduction, value stream mapping, and process optimization. Yellow Belts learn how to identify and eliminate non-value-added activities, streamline processes, and improve overall operational efficiency. Furthermore, they understand the importance of continuous improvement and the role of Yellow Belts in driving change within their respective areas of responsibility.
Obtaining a Lean Six Sigma Yellow Belt certification offers numerous benefits. It provides individuals with a solid understanding of the principles and tools necessary to contribute effectively to process improvement initiatives. Yellow Belts gain the ability to identify opportunities for improvement, collect and analyze relevant data, and collaborate with other team members to implement changes. This certification also enhances an individual's problem-solving abilities, critical thinking skills, and overall value to their organization.
In conclusion, The Essential Guide to Lean Six Sigma Yellow Belt: Fundamentals serves as a comprehensive resource for individuals seeking to develop a strong understanding of Lean Six Sigma principles and methodologies. The Yellow Belt certification provides individuals with the foundational knowledge and skills to actively contribute to process improvement initiatives. By embracing the fundamentals outlined in this guide, individuals can drive change, improve organizational performance, and embark on a journey towards process excellence.
Table of contents
- Introduction to Lean Six Sigma Yellow Belt:
- Fundamentals of Lean Six Sigma Yellow Belt:
- Key Tools and Techniques :
- Benefits and Impact of Lean Six Sigma Yellow Belt:
- Preparing for Lean Six Sigma Yellow Belt Certification:
- Continuing Education and Career Opportunities:
- Conclusion
Introduction to Lean Six Sigma Yellow Belt:
In today's competitive business landscape, organizations strive to achieve operational excellence and deliver exceptional quality products and services. Lean Six Sigma has emerged as a powerful methodology that combines the principles of Lean manufacturing and Six Sigma to drive process improvement, waste reduction, and customer satisfaction. Within the Lean Six Sigma hierarchy, the Yellow Belt certification serves as an essential entry point for individuals seeking to contribute to improvement initiatives and gain a foundational understanding of the methodology.
The Lean Six Sigma Yellow Belt certification provides participants with a fundamental knowledge of Lean Six Sigma concepts, tools, and techniques. It equips individuals with the skills to actively participate in improvement projects, support Green and Black Belt professionals, and contribute to the overall success of Lean Six Sigma initiatives within their organization.
By pursuing a Yellow Belt certification, individuals can enhance their problem-solving capabilities, develop a data-driven mindset, and contribute to the pursuit of operational excellence. This certification serves as a stepping stone for further advancement within the Lean Six Sigma hierarchy, such as Green Belt and Black Belt certifications.
Throughout the Yellow Belt certification program, participants gain an understanding of Lean principles, Six Sigma methodologies, and the DMAIC (Define, Measure, Analyze, Improve, Control) problem-solving approach. They learn how to identify and eliminate waste, optimize processes, and improve overall performance. Yellow Belt professionals play a crucial role in supporting process improvement projects, data collection and analysis, and the implementation of standardized work practices.
Obtaining a Lean Six Sigma Yellow Belt certification offers several benefits for individuals and organizations. It enhances employability by showcasing an individual's commitment to continuous improvement and problem-solving. Yellow Belt professionals can contribute to cost savings, increased productivity, and enhanced customer satisfaction. Moreover, organizations that foster a culture of Lean Six Sigma benefit from improved efficiency, reduced waste, and a focus on delivering value to customers.
In conclusion, the Lean Six Sigma Yellow Belt certification provides individuals with a solid foundation in Lean Six Sigma principles and practices. It empowers them to contribute to improvement projects, support higher-level professionals, and drive positive change within their organizations. By embracing the Yellow Belt certification, individuals can take their first step towards becoming proficient in Lean Six Sigma and making a significant impact on organizational performance.
Fundamentals of Lean Six Sigma Yellow Belt:
The Lean Six Sigma Yellow Belt certification is designed to provide individuals with a strong foundation in the principles, concepts, and tools of Lean Six Sigma methodology. By understanding the fundamentals, Yellow Belt professionals can actively contribute to improvement projects and support the implementation of Lean Six Sigma initiatives within their organization. Here are the key fundamentals covered in the Yellow Belt certification:
- Lean Principles: Yellow Belt professionals are introduced to the core principles of Lean, which aim to eliminate waste and create value for the customer. These principles include:
- Value: Identifying the activities that add value from the customer's perspective.
- Value Stream: Mapping the end-to-end process flow and identifying areas of waste.
- Flow: Streamlining the process flow to reduce delays and inefficiencies.
- Pull: Establishing a system where products or services are produced based on customer demand.
- Six Sigma Methodology: Yellow Belt professionals gain an understanding of the Six Sigma methodology, which focuses on reducing process variation and improving quality. The DMAIC (Define, Measure, Analyze, Improve, Control) framework is the cornerstone of Six Sigma and provides a structured problem-solving approach.
- Define: Defining the problem, project goals, and customer requirements.
- Measure: Collecting data and measuring the current process performance.
- Analyze: Analyzing the data to identify root causes and sources of variation.
- Improve: Implementing solutions and making process improvements.
- Control: Establishing control measures to sustain the improvements and prevent regression.
- Basic Lean Six Sigma Tools: Yellow Belt professionals are introduced to a range of fundamental tools and techniques used in Lean Six Sigma projects. These tools include:
- Process Mapping: Visualizing the current state and future state of a process to identify areas of improvement.
- 5 Whys: Asking iterative "why" questions to identify the root cause of a problem.
- Pareto Chart: A graphical representation of data to identify the most significant factors contributing to a problem.
- Control Charts: Monitoring and controlling process performance over time using statistical analysis.
- Root Cause Analysis: Using various tools such as Fishbone Diagrams and Failure Mode and Effects Analysis (FMEA) to identify the underlying causes of process issues.
- Roles and Responsibilities: Yellow Belt professionals learn about their roles and responsibilities within the Lean Six Sigma framework. While they may not lead projects, they play a vital supporting role by participating in improvement initiatives, collecting and analyzing data, and implementing solutions in their respective areas of work.
- Basic Statistical Concepts: Yellow Belt professionals are introduced to basic statistical concepts and techniques used in Lean Six Sigma projects. This includes understanding measures of central tendency, variation, and correlation. They learn how to collect and analyze data, interpret statistical charts, and draw meaningful conclusions.
Key Tools and Techniques in Lean Six Sigma Yellow Belt:
As a Lean Six Sigma Yellow Belt professional, it is important to have a solid understanding of the key tools and techniques used in process improvement projects. These tools and techniques help in identifying areas of waste, analyzing data, and implementing effective solutions. Here are some of the key tools and techniques covered in the Yellow Belt certification:
- Process Mapping: Process mapping is a visual representation of the steps and activities involved in a process. It helps to understand the flow of work, identify bottlenecks, and visualize opportunities for improvement. Common process mapping techniques include flowcharts, swimlane diagrams, and value stream mapping.
- 5 Whys: The 5 Whys technique is a simple but powerful tool for root cause analysis. By asking "why" repeatedly, it helps to dig deeper into the underlying causes of a problem. It enables Yellow Belt professionals to identify the root cause of a problem rather than just addressing the symptoms.
- Pareto Chart: A Pareto chart is a bar chart that displays data in descending order of frequency or importance. It helps to identify and prioritize the most significant factors or causes contributing to a problem. By focusing efforts on the vital few factors, Yellow Belt professionals can achieve maximum impact in their improvement projects.
- Control Charts: Control charts are statistical tools used to monitor and control process performance over time. They help to distinguish between common cause variation (inherent to the process) and special cause variation (due to specific factors). Control charts enable Yellow Belt professionals to identify when a process is out of control and take corrective actions.
- Root Cause Analysis: Root cause analysis techniques, such as Fishbone Diagrams (Ishikawa Diagrams) and Failure Mode and Effects Analysis (FMEA), are used to systematically identify the underlying causes of process issues or failures. These tools help Yellow Belt professionals to identify potential causes, categorize them, and prioritize corrective actions.
- Data Collection and Analysis: Yellow Belt professionals learn various data collection methods to gather information about process performance, defects, and customer requirements. They also learn basic statistical analysis techniques, such as calculating averages, ranges, and proportions. Excel or other statistical software tools are often used to analyze and visualize data.
- Standard Work: Standard work refers to documenting and following the best-known way of performing a task or process. Yellow Belt professionals learn the importance of standard work in reducing variability, improving quality, and ensuring consistency. They contribute to the development and implementation of standard work procedures.
- Kaizen Events: Kaizen events, also known as rapid improvement events, involve focused and intensive improvement activities carried out over a short period. Yellow Belt professionals may participate in Kaizen events, where they work collaboratively with a team to identify and implement improvements in a specific area or process.
Benefits and Impact of Lean Six Sigma Yellow Belt:
Obtaining a Lean Six Sigma Yellow Belt certification offers numerous benefits for individuals and organizations. The Yellow Belt level provides a solid foundation in Lean Six Sigma principles and practices, enabling professionals to contribute to improvement projects and support the implementation of Lean Six Sigma initiatives. Here are some key benefits and impacts of Lean Six Sigma Yellow Belt certification:
- Enhanced Problem-Solving Skills: Yellow Belt professionals develop a structured problem-solving approach through the DMAIC (Define, Measure, Analyze, Improve, Control) methodology. They learn to identify problems, collect and analyze data, and implement effective solutions. These skills enable them to contribute to process improvements and address issues in a systematic and data-driven manner.
- Increased Efficiency and Productivity: Yellow Belt professionals contribute to the identification and elimination of waste within processes. By applying Lean principles, they help streamline workflows, reduce non-value-added activities, and optimize process efficiency. This leads to increased productivity, shorter lead times, and improved resource utilization.
- Improved Quality and Customer Satisfaction: Lean Six Sigma focuses on reducing process variation and defects, resulting in improved product and service quality. Yellow Belt professionals contribute to the identification of root causes of defects and the implementation of sustainable solutions. By delivering higher quality outputs, organizations can enhance customer satisfaction and loyalty.
- Cost Savings and Financial Impact: Lean Six Sigma methodologies aim to minimize waste, reduce defects, and optimize resources. Yellow Belt professionals play a role in identifying cost-saving opportunities, eliminating unnecessary steps, and improving process efficiency. These improvements lead to reduced operational costs and increased profitability for organizations.
- Culture of Continuous Improvement: Yellow Belt professionals contribute to creating a culture of continuous improvement within their organizations. They actively participate in improvement initiatives, support higher-level professionals, and drive positive change. By embracing Lean Six Sigma principles, organizations foster an environment where innovation and improvement are valued and encouraged.
- Collaboration and Teamwork: Yellow Belt professionals often work as part of cross-functional teams within improvement projects. This collaboration enhances communication, teamwork, and problem-solving abilities. Yellow Belt certification equips professionals with the knowledge and skills to contribute effectively within team settings, fostering a collaborative work culture.
- Career Advancement Opportunities: Lean Six Sigma certifications, including Yellow Belt, can open up new career opportunities. The certification demonstrates a commitment to continuous improvement and problem-solving skills. It enhances employability and can lead to roles such as process improvement specialists, project coordinators, or team leads.
- Foundation for Further Certification: The Yellow Belt certification serves as a stepping stone for individuals who want to advance their Lean Six Sigma skills. It provides a solid foundation for pursuing higher-level certifications such as Green Belt and Black Belt. Yellow Belt professionals can continue their journey to become more proficient in Lean Six Sigma methodologies and take on leadership roles in process improvement initiatives.
Preparing for Lean Six Sigma Yellow Belt Certification:
Obtaining a Lean Six Sigma Yellow Belt certification requires adequate preparation to ensure success in the certification exam. Here are some essential steps and tips to help you prepare for the certification:
- Understand the Yellow Belt Body of Knowledge: Familiarize yourself with the topics and concepts covered in the Yellow Belt certification. Review the curriculum or study guide provided by the certification body to understand the key areas you need to focus on.
- Study Materials and Resources: Gather relevant study materials, textbooks, and resources that cover Lean Six Sigma concepts and tools. Look for reputable books, online tutorials, practice exams, and study guides that align with the Yellow Belt certification syllabus. Consider utilizing resources recommended by the certification body or industry experts.
- Participate in Training Programs: Enroll in a formal Lean Six Sigma Yellow Belt training program or workshop. These programs offer structured learning experiences, interactive exercises, and expert guidance to help you grasp the key concepts effectively. Additionally, training programs often provide study materials and practice exercises to reinforce your understanding.
- Practice with Sample Questions: Obtain sample exam questions or practice exams specific to the Yellow Belt certification. Solving practice questions helps you become familiar with the format of the actual exam and assesses your knowledge and readiness. Analyze your performance to identify areas of improvement and focus your study efforts accordingly.
- Collaborate and Engage in Discussion: Join online forums, discussion groups, or study groups dedicated to Lean Six Sigma. Engage in discussions with fellow learners, ask questions, and share insights. Collaborative learning can enhance your understanding of concepts, provide different perspectives, and offer valuable tips for the certification exam.
- Review Case Studies and Examples: Study real-world case studies and examples of Lean Six Sigma implementation in different industries. This practical exposure helps you connect theoretical concepts with practical applications, improving your ability to apply Lean Six Sigma principles in real-life scenarios.
- Create Study Notes and Summaries: As you study, create concise notes and summaries of important concepts, tools, and techniques. This practice reinforces your understanding and serves as a quick reference during revision. Visual aids, such as diagrams and flowcharts, can be particularly helpful in grasping complex topics.
- Review Key Tools and Formulas: Familiarize yourself with the key Lean Six Sigma tools and formulas covered in the Yellow Belt certification. Practice using these tools and solving related problems. Understand how to interpret statistical charts and data analysis outputs commonly used in Lean Six Sigma projects.
- Time Management and Exam Strategy: Develop a study schedule that allows you to allocate dedicated time for each topic. Manage your time effectively to cover the entire syllabus before the exam. Additionally, familiarize yourself with the exam format and structure. Understand the number of questions, time limits, and any specific instructions for the exam.
- Mock Exams and Self-Assessment: Take mock exams or self-assessment quizzes to evaluate your knowledge and readiness for the Yellow Belt certification. Assess your performance, identify weak areas, and revise those topics to strengthen your understanding. Repeat mock exams to track your progress and build confidence.
- Review and Revision: Set aside dedicated time for comprehensive revision of all the topics covered in the Yellow Belt certification. Ensure you have a solid grasp of the core concepts, tools, and techniques. Focus on clarifying any remaining doubts or gaps in your understanding.
How to obtain the Lean Six Sigma Yellow Belt certification?
We are an Education Technology company providing certification training courses to accelerate careers of working professionals worldwide. We impart training through instructor-led classroom workshops, instructor-led live virtual training sessions, and self-paced e-learning courses.
We have successfully conducted training sessions in 108 countries across the globe and enabled thousands of working professionals to enhance the scope of their careers.
Our enterprise training portfolio includes in-demand and globally recognized certification training courses in Project Management, Quality Management, Business Analysis, IT Service Management, Agile and Scrum, Cyber Security, Data Science, and Emerging Technologies. Download our Enterprise Training Catalog from https://www.icertglobal.com/corporate-training-for-enterprises.php
Popular Courses include:
- Project Management: PMP, CAPM ,PMI RMP
- Quality Management: Six Sigma Green Belt ,Lean Six Sigma Yellow Belt, Lean Six Sigma Black Belt
- Business Analysis: CBAP, CCBA, ECBA
- Agile Training: PMI-ACP
- Scrum Training: CSM
- DevOps
- Program Management: PgMP
- IT Service Management & Governance: COBIT, ISO
Continuing Education and Career Opportunities in Lean Six Sigma:
Continuing education and skill development are crucial in the field of Lean Six Sigma to stay relevant, advance in your career, and contribute effectively to process improvement initiatives. Here are some key avenues for continuing education and the career opportunities associated with Lean Six Sigma:
- Advanced Lean Six Sigma Certifications: After obtaining a Yellow Belt certification, you can pursue higher-level certifications, such as Green Belt and Black Belt. These certifications provide a deeper understanding of Lean Six Sigma methodologies, advanced tools and techniques, and leadership skills in driving improvement projects. Green Belt and Black Belt certifications open up more significant career opportunities and the potential for leading complex improvement initiatives within organizations.
- Specialization in Industry-Specific Lean Six Sigma: Consider specializing in Lean Six Sigma for specific industries, such as healthcare, manufacturing, finance, or logistics. Industry-specific certifications or training programs provide in-depth knowledge of industry challenges, regulations, and best practices. This specialization enhances your expertise and makes you valuable in organizations operating within those sectors.
- Continuous Professional Development (CPD): Engage in continuous professional development activities related to Lean Six Sigma. Attend workshops, conferences, seminars, and webinars that focus on the latest trends, emerging methodologies, and case studies in Lean Six Sigma. Continuous learning ensures you stay updated with the evolving practices and can apply innovative approaches to process improvement.
- Coaching and Mentoring: Consider becoming a Lean Six Sigma coach or mentor. Share your knowledge and experience with aspiring Yellow Belts or those starting their Lean Six Sigma journey. Coaching and mentoring provide an opportunity to reinforce your own understanding, develop leadership skills, and contribute to the growth of others.
- Project Management Certifications: Lean Six Sigma complements project management methodologies. Obtaining project management certifications, such as Project Management Professional (PMP)® or Agile certifications, can enhance your skill set and make you a well-rounded professional capable of effectively managing improvement projects in conjunction with Lean Six Sigma principles.
- Continuous Improvement Roles: Lean Six Sigma professionals often find rewarding career opportunities in roles focused on continuous improvement. These roles may include Process Improvement Specialist, Continuous Improvement Manager, Lean Facilitator, or Quality Assurance Manager. These positions involve driving process excellence, leading improvement projects, and implementing Lean Six Sigma methodologies across various functions and departments.
- Management and Leadership Roles: With advanced Lean Six Sigma certifications and practical experience, you can pursue management or leadership roles in organizations. Lean Six Sigma provides a strong foundation for data-driven decision-making, strategic planning, and driving organizational transformation. Leadership roles may include Lean Six Sigma Manager, Operations Manager, or Director of Continuous Improvement.
- Entrepreneurship and Consulting: Lean Six Sigma expertise opens up opportunities for entrepreneurship and consulting. As a Lean Six Sigma professional, you can offer process improvement consulting services to organizations, help them optimize their operations, and drive efficiency gains. Entrepreneurial ventures can focus on offering Lean Six Sigma training, tools, or customized improvement solutions.
Remember, career opportunities in Lean Six Sigma are not limited to a specific industry or sector. Lean Six Sigma principles and practices are applicable across diverse industries, including manufacturing, healthcare, finance, government, and service sectors. The demand for professionals skilled in Lean Six Sigma continues to grow as organizations strive for operational excellence, waste reduction, and customer satisfaction.
Conclusion
In conclusion, Lean Six Sigma Yellow Belt certification provides individuals with a strong foundation in Lean Six Sigma methodologies and principles. It equips them with essential problem-solving skills, the ability to identify waste, and the knowledge to contribute to improvement projects within organizations.
The benefits and impact of Lean Six Sigma Yellow Belt certification are significant. Professionals with this certification can enhance efficiency and productivity, improve quality and customer satisfaction, achieve cost savings, and foster a culture of continuous improvement within their organizations. Yellow Belt certification also opens up career advancement opportunities, serving as a stepping stone to higher-level certifications such as Green Belt and Black Belt.
To prepare for the Yellow Belt certification, individuals should understand the certification body's body of knowledge, gather relevant study materials, participate in training programs, practice with sample questions, collaborate with peers, review case studies, and create study notes. Mock exams and self-assessment quizzes can also help evaluate knowledge and readiness for the certification exam.
Continuing education in Lean Six Sigma is essential for career growth. Professionals can pursue advanced certifications, specialize in industry-specific Lean Six Sigma, engage in continuous professional development activities, become coaches or mentors, obtain project management certifications, and explore career opportunities in continuous improvement roles, management and leadership positions, entrepreneurship, and consulting.
By continuously developing their Lean Six Sigma skills and staying updated with industry trends, individuals with Lean Six Sigma Yellow Belt certification can contribute effectively to process improvement initiatives, drive organizational success, and become valuable assets in their careers. Lean Six Sigma methodologies provide a systematic approach to achieving operational excellence and fostering a culture of continuous improvement in organizations across various industries.
Read More
The Essential Guide to Lean Six Sigma Yellow Belt: Fundamentals serves as a comprehensive resource for individuals looking to develop a strong foundation in Lean Six Sigma methodologies. The Yellow Belt certification is an essential step on the journey to process improvement and organizational excellence. In this guide, we will delve into the core principles and concepts that form the basis of Lean Six Sigma Yellow Belt training, providing a comprehensive understanding of its fundamentals.
Lean Six Sigma combines two powerful approaches to process improvement: Lean and Six Sigma. It emphasizes the elimination of waste, reduction of defects, and continuous improvement, all while ensuring customer satisfaction and delivering value. The Yellow Belt certification equips individuals with the knowledge and skills to actively participate in process improvement initiatives within their teams or departments.
The Essential Guide to Lean Six Sigma Yellow Belt: Fundamentals covers the key elements of the DMAIC (Define, Measure, Analyze, Improve, Control) methodology. Yellow Belts learn how to define project goals, identify customer requirements, and map process flows. They gain insights into data collection and analysis techniques, enabling them to measure process performance and identify improvement opportunities. Additionally, Yellow Belts develop problem-solving skills and learn to apply basic statistical tools to understand and address root causes of problems.
This guide also explores the fundamental concepts of waste reduction, value stream mapping, and process optimization. Yellow Belts learn how to identify and eliminate non-value-added activities, streamline processes, and improve overall operational efficiency. Furthermore, they understand the importance of continuous improvement and the role of Yellow Belts in driving change within their respective areas of responsibility.
Obtaining a Lean Six Sigma Yellow Belt certification offers numerous benefits. It provides individuals with a solid understanding of the principles and tools necessary to contribute effectively to process improvement initiatives. Yellow Belts gain the ability to identify opportunities for improvement, collect and analyze relevant data, and collaborate with other team members to implement changes. This certification also enhances an individual's problem-solving abilities, critical thinking skills, and overall value to their organization.
In conclusion, The Essential Guide to Lean Six Sigma Yellow Belt: Fundamentals serves as a comprehensive resource for individuals seeking to develop a strong understanding of Lean Six Sigma principles and methodologies. The Yellow Belt certification provides individuals with the foundational knowledge and skills to actively contribute to process improvement initiatives. By embracing the fundamentals outlined in this guide, individuals can drive change, improve organizational performance, and embark on a journey towards process excellence.
Table of contents
- Introduction to Lean Six Sigma Yellow Belt:
- Fundamentals of Lean Six Sigma Yellow Belt:
- Key Tools and Techniques :
- Benefits and Impact of Lean Six Sigma Yellow Belt:
- Preparing for Lean Six Sigma Yellow Belt Certification:
- Continuing Education and Career Opportunities:
- Conclusion
Introduction to Lean Six Sigma Yellow Belt:
In today's competitive business landscape, organizations strive to achieve operational excellence and deliver exceptional quality products and services. Lean Six Sigma has emerged as a powerful methodology that combines the principles of Lean manufacturing and Six Sigma to drive process improvement, waste reduction, and customer satisfaction. Within the Lean Six Sigma hierarchy, the Yellow Belt certification serves as an essential entry point for individuals seeking to contribute to improvement initiatives and gain a foundational understanding of the methodology.
The Lean Six Sigma Yellow Belt certification provides participants with a fundamental knowledge of Lean Six Sigma concepts, tools, and techniques. It equips individuals with the skills to actively participate in improvement projects, support Green and Black Belt professionals, and contribute to the overall success of Lean Six Sigma initiatives within their organization.
By pursuing a Yellow Belt certification, individuals can enhance their problem-solving capabilities, develop a data-driven mindset, and contribute to the pursuit of operational excellence. This certification serves as a stepping stone for further advancement within the Lean Six Sigma hierarchy, such as Green Belt and Black Belt certifications.
Throughout the Yellow Belt certification program, participants gain an understanding of Lean principles, Six Sigma methodologies, and the DMAIC (Define, Measure, Analyze, Improve, Control) problem-solving approach. They learn how to identify and eliminate waste, optimize processes, and improve overall performance. Yellow Belt professionals play a crucial role in supporting process improvement projects, data collection and analysis, and the implementation of standardized work practices.
Obtaining a Lean Six Sigma Yellow Belt certification offers several benefits for individuals and organizations. It enhances employability by showcasing an individual's commitment to continuous improvement and problem-solving. Yellow Belt professionals can contribute to cost savings, increased productivity, and enhanced customer satisfaction. Moreover, organizations that foster a culture of Lean Six Sigma benefit from improved efficiency, reduced waste, and a focus on delivering value to customers.
In conclusion, the Lean Six Sigma Yellow Belt certification provides individuals with a solid foundation in Lean Six Sigma principles and practices. It empowers them to contribute to improvement projects, support higher-level professionals, and drive positive change within their organizations. By embracing the Yellow Belt certification, individuals can take their first step towards becoming proficient in Lean Six Sigma and making a significant impact on organizational performance.
Fundamentals of Lean Six Sigma Yellow Belt:
The Lean Six Sigma Yellow Belt certification is designed to provide individuals with a strong foundation in the principles, concepts, and tools of Lean Six Sigma methodology. By understanding the fundamentals, Yellow Belt professionals can actively contribute to improvement projects and support the implementation of Lean Six Sigma initiatives within their organization. Here are the key fundamentals covered in the Yellow Belt certification:
- Lean Principles: Yellow Belt professionals are introduced to the core principles of Lean, which aim to eliminate waste and create value for the customer. These principles include:
- Value: Identifying the activities that add value from the customer's perspective.
- Value Stream: Mapping the end-to-end process flow and identifying areas of waste.
- Flow: Streamlining the process flow to reduce delays and inefficiencies.
- Pull: Establishing a system where products or services are produced based on customer demand.
- Six Sigma Methodology: Yellow Belt professionals gain an understanding of the Six Sigma methodology, which focuses on reducing process variation and improving quality. The DMAIC (Define, Measure, Analyze, Improve, Control) framework is the cornerstone of Six Sigma and provides a structured problem-solving approach.
- Define: Defining the problem, project goals, and customer requirements.
- Measure: Collecting data and measuring the current process performance.
- Analyze: Analyzing the data to identify root causes and sources of variation.
- Improve: Implementing solutions and making process improvements.
- Control: Establishing control measures to sustain the improvements and prevent regression.
- Basic Lean Six Sigma Tools: Yellow Belt professionals are introduced to a range of fundamental tools and techniques used in Lean Six Sigma projects. These tools include:
- Process Mapping: Visualizing the current state and future state of a process to identify areas of improvement.
- 5 Whys: Asking iterative "why" questions to identify the root cause of a problem.
- Pareto Chart: A graphical representation of data to identify the most significant factors contributing to a problem.
- Control Charts: Monitoring and controlling process performance over time using statistical analysis.
- Root Cause Analysis: Using various tools such as Fishbone Diagrams and Failure Mode and Effects Analysis (FMEA) to identify the underlying causes of process issues.
- Roles and Responsibilities: Yellow Belt professionals learn about their roles and responsibilities within the Lean Six Sigma framework. While they may not lead projects, they play a vital supporting role by participating in improvement initiatives, collecting and analyzing data, and implementing solutions in their respective areas of work.
- Basic Statistical Concepts: Yellow Belt professionals are introduced to basic statistical concepts and techniques used in Lean Six Sigma projects. This includes understanding measures of central tendency, variation, and correlation. They learn how to collect and analyze data, interpret statistical charts, and draw meaningful conclusions.
Key Tools and Techniques in Lean Six Sigma Yellow Belt:
As a Lean Six Sigma Yellow Belt professional, it is important to have a solid understanding of the key tools and techniques used in process improvement projects. These tools and techniques help in identifying areas of waste, analyzing data, and implementing effective solutions. Here are some of the key tools and techniques covered in the Yellow Belt certification:
- Process Mapping: Process mapping is a visual representation of the steps and activities involved in a process. It helps to understand the flow of work, identify bottlenecks, and visualize opportunities for improvement. Common process mapping techniques include flowcharts, swimlane diagrams, and value stream mapping.
- 5 Whys: The 5 Whys technique is a simple but powerful tool for root cause analysis. By asking "why" repeatedly, it helps to dig deeper into the underlying causes of a problem. It enables Yellow Belt professionals to identify the root cause of a problem rather than just addressing the symptoms.
- Pareto Chart: A Pareto chart is a bar chart that displays data in descending order of frequency or importance. It helps to identify and prioritize the most significant factors or causes contributing to a problem. By focusing efforts on the vital few factors, Yellow Belt professionals can achieve maximum impact in their improvement projects.
- Control Charts: Control charts are statistical tools used to monitor and control process performance over time. They help to distinguish between common cause variation (inherent to the process) and special cause variation (due to specific factors). Control charts enable Yellow Belt professionals to identify when a process is out of control and take corrective actions.
- Root Cause Analysis: Root cause analysis techniques, such as Fishbone Diagrams (Ishikawa Diagrams) and Failure Mode and Effects Analysis (FMEA), are used to systematically identify the underlying causes of process issues or failures. These tools help Yellow Belt professionals to identify potential causes, categorize them, and prioritize corrective actions.
- Data Collection and Analysis: Yellow Belt professionals learn various data collection methods to gather information about process performance, defects, and customer requirements. They also learn basic statistical analysis techniques, such as calculating averages, ranges, and proportions. Excel or other statistical software tools are often used to analyze and visualize data.
- Standard Work: Standard work refers to documenting and following the best-known way of performing a task or process. Yellow Belt professionals learn the importance of standard work in reducing variability, improving quality, and ensuring consistency. They contribute to the development and implementation of standard work procedures.
- Kaizen Events: Kaizen events, also known as rapid improvement events, involve focused and intensive improvement activities carried out over a short period. Yellow Belt professionals may participate in Kaizen events, where they work collaboratively with a team to identify and implement improvements in a specific area or process.
Benefits and Impact of Lean Six Sigma Yellow Belt:
Obtaining a Lean Six Sigma Yellow Belt certification offers numerous benefits for individuals and organizations. The Yellow Belt level provides a solid foundation in Lean Six Sigma principles and practices, enabling professionals to contribute to improvement projects and support the implementation of Lean Six Sigma initiatives. Here are some key benefits and impacts of Lean Six Sigma Yellow Belt certification:
- Enhanced Problem-Solving Skills: Yellow Belt professionals develop a structured problem-solving approach through the DMAIC (Define, Measure, Analyze, Improve, Control) methodology. They learn to identify problems, collect and analyze data, and implement effective solutions. These skills enable them to contribute to process improvements and address issues in a systematic and data-driven manner.
- Increased Efficiency and Productivity: Yellow Belt professionals contribute to the identification and elimination of waste within processes. By applying Lean principles, they help streamline workflows, reduce non-value-added activities, and optimize process efficiency. This leads to increased productivity, shorter lead times, and improved resource utilization.
- Improved Quality and Customer Satisfaction: Lean Six Sigma focuses on reducing process variation and defects, resulting in improved product and service quality. Yellow Belt professionals contribute to the identification of root causes of defects and the implementation of sustainable solutions. By delivering higher quality outputs, organizations can enhance customer satisfaction and loyalty.
- Cost Savings and Financial Impact: Lean Six Sigma methodologies aim to minimize waste, reduce defects, and optimize resources. Yellow Belt professionals play a role in identifying cost-saving opportunities, eliminating unnecessary steps, and improving process efficiency. These improvements lead to reduced operational costs and increased profitability for organizations.
- Culture of Continuous Improvement: Yellow Belt professionals contribute to creating a culture of continuous improvement within their organizations. They actively participate in improvement initiatives, support higher-level professionals, and drive positive change. By embracing Lean Six Sigma principles, organizations foster an environment where innovation and improvement are valued and encouraged.
- Collaboration and Teamwork: Yellow Belt professionals often work as part of cross-functional teams within improvement projects. This collaboration enhances communication, teamwork, and problem-solving abilities. Yellow Belt certification equips professionals with the knowledge and skills to contribute effectively within team settings, fostering a collaborative work culture.
- Career Advancement Opportunities: Lean Six Sigma certifications, including Yellow Belt, can open up new career opportunities. The certification demonstrates a commitment to continuous improvement and problem-solving skills. It enhances employability and can lead to roles such as process improvement specialists, project coordinators, or team leads.
- Foundation for Further Certification: The Yellow Belt certification serves as a stepping stone for individuals who want to advance their Lean Six Sigma skills. It provides a solid foundation for pursuing higher-level certifications such as Green Belt and Black Belt. Yellow Belt professionals can continue their journey to become more proficient in Lean Six Sigma methodologies and take on leadership roles in process improvement initiatives.
Preparing for Lean Six Sigma Yellow Belt Certification:
Obtaining a Lean Six Sigma Yellow Belt certification requires adequate preparation to ensure success in the certification exam. Here are some essential steps and tips to help you prepare for the certification:
- Understand the Yellow Belt Body of Knowledge: Familiarize yourself with the topics and concepts covered in the Yellow Belt certification. Review the curriculum or study guide provided by the certification body to understand the key areas you need to focus on.
- Study Materials and Resources: Gather relevant study materials, textbooks, and resources that cover Lean Six Sigma concepts and tools. Look for reputable books, online tutorials, practice exams, and study guides that align with the Yellow Belt certification syllabus. Consider utilizing resources recommended by the certification body or industry experts.
- Participate in Training Programs: Enroll in a formal Lean Six Sigma Yellow Belt training program or workshop. These programs offer structured learning experiences, interactive exercises, and expert guidance to help you grasp the key concepts effectively. Additionally, training programs often provide study materials and practice exercises to reinforce your understanding.
- Practice with Sample Questions: Obtain sample exam questions or practice exams specific to the Yellow Belt certification. Solving practice questions helps you become familiar with the format of the actual exam and assesses your knowledge and readiness. Analyze your performance to identify areas of improvement and focus your study efforts accordingly.
- Collaborate and Engage in Discussion: Join online forums, discussion groups, or study groups dedicated to Lean Six Sigma. Engage in discussions with fellow learners, ask questions, and share insights. Collaborative learning can enhance your understanding of concepts, provide different perspectives, and offer valuable tips for the certification exam.
- Review Case Studies and Examples: Study real-world case studies and examples of Lean Six Sigma implementation in different industries. This practical exposure helps you connect theoretical concepts with practical applications, improving your ability to apply Lean Six Sigma principles in real-life scenarios.
- Create Study Notes and Summaries: As you study, create concise notes and summaries of important concepts, tools, and techniques. This practice reinforces your understanding and serves as a quick reference during revision. Visual aids, such as diagrams and flowcharts, can be particularly helpful in grasping complex topics.
- Review Key Tools and Formulas: Familiarize yourself with the key Lean Six Sigma tools and formulas covered in the Yellow Belt certification. Practice using these tools and solving related problems. Understand how to interpret statistical charts and data analysis outputs commonly used in Lean Six Sigma projects.
- Time Management and Exam Strategy: Develop a study schedule that allows you to allocate dedicated time for each topic. Manage your time effectively to cover the entire syllabus before the exam. Additionally, familiarize yourself with the exam format and structure. Understand the number of questions, time limits, and any specific instructions for the exam.
- Mock Exams and Self-Assessment: Take mock exams or self-assessment quizzes to evaluate your knowledge and readiness for the Yellow Belt certification. Assess your performance, identify weak areas, and revise those topics to strengthen your understanding. Repeat mock exams to track your progress and build confidence.
- Review and Revision: Set aside dedicated time for comprehensive revision of all the topics covered in the Yellow Belt certification. Ensure you have a solid grasp of the core concepts, tools, and techniques. Focus on clarifying any remaining doubts or gaps in your understanding.
How to obtain the Lean Six Sigma Yellow Belt certification?
We are an Education Technology company providing certification training courses to accelerate careers of working professionals worldwide. We impart training through instructor-led classroom workshops, instructor-led live virtual training sessions, and self-paced e-learning courses.
We have successfully conducted training sessions in 108 countries across the globe and enabled thousands of working professionals to enhance the scope of their careers.
Our enterprise training portfolio includes in-demand and globally recognized certification training courses in Project Management, Quality Management, Business Analysis, IT Service Management, Agile and Scrum, Cyber Security, Data Science, and Emerging Technologies. Download our Enterprise Training Catalog from https://www.icertglobal.com/corporate-training-for-enterprises.php
Popular Courses include:
- Project Management: PMP, CAPM ,PMI RMP
- Quality Management: Six Sigma Green Belt ,Lean Six Sigma Yellow Belt, Lean Six Sigma Black Belt
- Business Analysis: CBAP, CCBA, ECBA
- Agile Training: PMI-ACP
- Scrum Training: CSM
- DevOps
- Program Management: PgMP
- IT Service Management & Governance: COBIT, ISO
Continuing Education and Career Opportunities in Lean Six Sigma:
Continuing education and skill development are crucial in the field of Lean Six Sigma to stay relevant, advance in your career, and contribute effectively to process improvement initiatives. Here are some key avenues for continuing education and the career opportunities associated with Lean Six Sigma:
- Advanced Lean Six Sigma Certifications: After obtaining a Yellow Belt certification, you can pursue higher-level certifications, such as Green Belt and Black Belt. These certifications provide a deeper understanding of Lean Six Sigma methodologies, advanced tools and techniques, and leadership skills in driving improvement projects. Green Belt and Black Belt certifications open up more significant career opportunities and the potential for leading complex improvement initiatives within organizations.
- Specialization in Industry-Specific Lean Six Sigma: Consider specializing in Lean Six Sigma for specific industries, such as healthcare, manufacturing, finance, or logistics. Industry-specific certifications or training programs provide in-depth knowledge of industry challenges, regulations, and best practices. This specialization enhances your expertise and makes you valuable in organizations operating within those sectors.
- Continuous Professional Development (CPD): Engage in continuous professional development activities related to Lean Six Sigma. Attend workshops, conferences, seminars, and webinars that focus on the latest trends, emerging methodologies, and case studies in Lean Six Sigma. Continuous learning ensures you stay updated with the evolving practices and can apply innovative approaches to process improvement.
- Coaching and Mentoring: Consider becoming a Lean Six Sigma coach or mentor. Share your knowledge and experience with aspiring Yellow Belts or those starting their Lean Six Sigma journey. Coaching and mentoring provide an opportunity to reinforce your own understanding, develop leadership skills, and contribute to the growth of others.
- Project Management Certifications: Lean Six Sigma complements project management methodologies. Obtaining project management certifications, such as Project Management Professional (PMP)® or Agile certifications, can enhance your skill set and make you a well-rounded professional capable of effectively managing improvement projects in conjunction with Lean Six Sigma principles.
- Continuous Improvement Roles: Lean Six Sigma professionals often find rewarding career opportunities in roles focused on continuous improvement. These roles may include Process Improvement Specialist, Continuous Improvement Manager, Lean Facilitator, or Quality Assurance Manager. These positions involve driving process excellence, leading improvement projects, and implementing Lean Six Sigma methodologies across various functions and departments.
- Management and Leadership Roles: With advanced Lean Six Sigma certifications and practical experience, you can pursue management or leadership roles in organizations. Lean Six Sigma provides a strong foundation for data-driven decision-making, strategic planning, and driving organizational transformation. Leadership roles may include Lean Six Sigma Manager, Operations Manager, or Director of Continuous Improvement.
- Entrepreneurship and Consulting: Lean Six Sigma expertise opens up opportunities for entrepreneurship and consulting. As a Lean Six Sigma professional, you can offer process improvement consulting services to organizations, help them optimize their operations, and drive efficiency gains. Entrepreneurial ventures can focus on offering Lean Six Sigma training, tools, or customized improvement solutions.
Remember, career opportunities in Lean Six Sigma are not limited to a specific industry or sector. Lean Six Sigma principles and practices are applicable across diverse industries, including manufacturing, healthcare, finance, government, and service sectors. The demand for professionals skilled in Lean Six Sigma continues to grow as organizations strive for operational excellence, waste reduction, and customer satisfaction.
Conclusion
In conclusion, Lean Six Sigma Yellow Belt certification provides individuals with a strong foundation in Lean Six Sigma methodologies and principles. It equips them with essential problem-solving skills, the ability to identify waste, and the knowledge to contribute to improvement projects within organizations.
The benefits and impact of Lean Six Sigma Yellow Belt certification are significant. Professionals with this certification can enhance efficiency and productivity, improve quality and customer satisfaction, achieve cost savings, and foster a culture of continuous improvement within their organizations. Yellow Belt certification also opens up career advancement opportunities, serving as a stepping stone to higher-level certifications such as Green Belt and Black Belt.
To prepare for the Yellow Belt certification, individuals should understand the certification body's body of knowledge, gather relevant study materials, participate in training programs, practice with sample questions, collaborate with peers, review case studies, and create study notes. Mock exams and self-assessment quizzes can also help evaluate knowledge and readiness for the certification exam.
Continuing education in Lean Six Sigma is essential for career growth. Professionals can pursue advanced certifications, specialize in industry-specific Lean Six Sigma, engage in continuous professional development activities, become coaches or mentors, obtain project management certifications, and explore career opportunities in continuous improvement roles, management and leadership positions, entrepreneurship, and consulting.
By continuously developing their Lean Six Sigma skills and staying updated with industry trends, individuals with Lean Six Sigma Yellow Belt certification can contribute effectively to process improvement initiatives, drive organizational success, and become valuable assets in their careers. Lean Six Sigma methodologies provide a systematic approach to achieving operational excellence and fostering a culture of continuous improvement in organizations across various industries.
Six Sigma Black Belt:Achieving Your Goals with Understanding
The Six Sigma Black Belt certification represents the pinnacle of expertise in process improvement and quality management. It is a highly coveted credential that signifies an individual's mastery of Lean Six Sigma methodologies and their ability to lead complex improvement initiatives within organizations. In this article, we will explore the significance of achieving a Six Sigma Black Belt and how it empowers individuals to effectively drive change and achieve their goals.
The journey to becoming a Six Sigma Black Belt requires a deep understanding of the DMAIC (Define, Measure, Analyze, Improve, Control) methodology and the application of advanced statistical analysis and problem-solving techniques. Black Belts possess the skills to lead cross-functional teams, manage projects, and orchestrate process improvements that yield substantial results.
With a Black Belt certification, individuals gain the capability to identify root causes of problems, analyze data-driven insights, and implement sustainable solutions. Black Belts excel in driving process optimization, reducing defects, enhancing productivity, and ultimately improving the bottom line. Their advanced problem-solving skills enable them to tackle complex challenges and overcome organizational barriers to change.
Moreover, Six Sigma Black Belts play a pivotal role in driving organizational excellence. They are equipped to align process improvement initiatives with business strategies, ensuring that efforts are focused on achieving the organization's goals. Black Belts are effective change agents, driving cultural transformation and fostering a mindset of continuous improvement throughout the organization.
Achieving a Six Sigma Black Belt is a testament to an individual's dedication to personal and professional growth. It opens doors to new career opportunities, as organizations across various industries recognize the value of individuals who possess the expertise to deliver significant improvements in quality, efficiency, and customer satisfaction. Additionally, Black Belts often serve as mentors and trainers for Green Belts and Yellow Belts, sharing their knowledge and guiding others on their journey to process excellence.
In conclusion, the Six Sigma Black Belt certification represents the highest level of proficiency in Lean Six Sigma methodologies. Black Belts possess the knowledge and skills to drive substantial process improvements and achieve organizational goals. Their expertise in advanced problem-solving, data analysis, and project management enables them to lead impactful change initiatives. By obtaining a Six Sigma Black Belt, individuals position themselves as catalysts for transformation, driving success in organizations and achieving their own professional aspirations.
Table of contents
- Introduction to Six Sigma Black Belt
- Requirements for Six Sigma Black Belt Certification:
- DMAIC Methodology:
- Leadership and Change Management:
- Certification Process and Examination:
- Benefits and Career Opportunities:
- Conclusion
Introduction to Six Sigma Black Belt:
Six Sigma, a renowned methodology for process improvement and quality management, has revolutionized the way organizations operate. At the heart of Six Sigma lies the role of a Black Belt, a highly skilled professional responsible for leading improvement projects and driving significant results. A Six Sigma Black Belt possesses a deep understanding of statistical analysis, problem-solving techniques, and project management. Their expertise enables them to identify process inefficiencies, reduce variation, and enhance overall organizational performance. Obtaining a Six Sigma Black Belt certification showcases a commitment to excellence and signifies mastery of the methodology. In this blog post, we will explore the significance of Six Sigma Black Belt certification, its requirements, and the essential skills it encompasses, shedding light on the value these professionals bring to organizations seeking continuous improvement and success.
Requirements for Six Sigma Black Belt Certification:
To earn a Six Sigma Black Belt certification, individuals are required to meet certain prerequisites that ensure they possess the necessary knowledge, skills, and experience to effectively lead process improvement initiatives. The specific requirements may vary depending on the certifying body or organization offering the certification. Here are some common requirements:
- Education and Experience:
- A minimum educational qualification, such as a bachelor's degree, is often required. The field of study may vary, but degrees in engineering, business, mathematics, or statistics are commonly preferred.
- Several years of professional work experience in a relevant field are typically expected. This experience should involve exposure to process improvement, project management, or quality management responsibilities.
- Completion of Green Belt Certification:
- Many certifying bodies require candidates to have already earned a Six Sigma Green Belt certification. This ensures a solid foundation in the principles, tools, and techniques of Six Sigma methodology.
- Green Belt certification demonstrates practical experience in executing process improvement projects and serves as a stepping stone to the more advanced Black Belt level.
- Training and Professional Development:
- Completion of a comprehensive Black Belt training program is usually mandatory. This training covers advanced statistical analysis, project management, process mapping, and other specialized Six Sigma tools and techniques.
- The training may be conducted in a classroom setting or through online courses. It is essential to choose an accredited program that aligns with recognized Six Sigma methodologies.
- Demonstrated Application of Six Sigma:
- Candidates are typically required to showcase their practical application of Six Sigma principles and methodologies in real-world projects.
- This may involve providing evidence of successfully completed improvement projects, including project charters, data analysis, process documentation, and measurable outcomes.
- Written Examination:
- Candidates are generally required to pass a written examination to demonstrate their understanding of Six Sigma concepts, tools, and methodologies.
- The exam may include multiple-choice questions, case studies, and scenario-based assessments.
- Adequate preparation through self-study, review of course materials, and practice exams is essential to perform well in the certification exam.
GET COURSE
DMAIC Methodology
The DMAIC methodology is a core component of Six Sigma and serves as a systematic framework for problem-solving and process improvement. DMAIC stands for Define, Measure, Analyze, Improve, and Control, representing the five distinct phases of the methodology. Each phase plays a vital role in identifying and eliminating process deficiencies to achieve enhanced performance and customer satisfaction. Let's explore each phase of the DMAIC methodology in detail:
- Define:
- In the Define phase, the project team clarifies the problem or opportunity for improvement, establishes project goals, and defines customer requirements and expectations.
- Key activities in this phase include developing a project charter, identifying stakeholders, and defining the project scope and boundaries.
- The goal is to ensure a clear understanding of the problem to be addressed and align project objectives with the overall organizational goals.
- Measure:
- The Measure phase focuses on collecting data and measuring the current state of the process under study.
- The team identifies and selects relevant process metrics and establishes a baseline for performance.
- Data collection methods, such as sampling, surveys, or direct measurements, are employed to quantify process performance and identify sources of variation.
- Analyze:
- In the Analyze phase, the collected data is analyzed to identify root causes of process variation and performance gaps.
- Statistical tools and techniques, such as hypothesis testing, regression analysis, and Pareto charts, are utilized to identify factors that significantly impact the process outcomes.
- The goal is to gain insights into the underlying causes of problems and prioritize improvement opportunities.
- Improve:
- The Improve phase focuses on developing and implementing solutions to address the identified root causes and improve process performance.
- The team generates potential solutions, evaluates their feasibility, and selects the most promising ones.
- These solutions are then tested on a small scale through pilots or simulations before being implemented fully.
- The objective is to implement changes that result in significant process improvement and meet the desired goals.
- Control:
- The Control phase involves establishing control mechanisms to sustain the improvements achieved and prevent a return to the previous state.
- Process controls, such as standard operating procedures, statistical process control charts, and training programs, are put in place.
- The team develops a monitoring and feedback system to track ongoing process performance and ensure that any deviations are promptly addressed.
- The aim is to create a culture of continuous improvement and ensure that the gains achieved through the project are maintained over time.
By following the DMAIC methodology, organizations can systematically approach process improvement, driving data-driven decision-making and achieving measurable results. It provides a structured approach for tackling complex problems, identifying opportunities for improvement, and implementing effective solutions. DMAIC serves as a powerful tool for organizations seeking to enhance quality, reduce costs, and improve customer satisfaction.
Leadership and Change Management:
In the context of Six Sigma Black Belt certification, leadership and change management skills play a critical role in driving successful process improvement initiatives. As a Six Sigma Black Belt, you are not only responsible for applying technical tools and methodologies but also for leading teams, influencing stakeholders, and managing the change associated with process improvements. Let's explore the importance of leadership and change management in the Six Sigma Black Belt role:
- Leading Teams:
- Effective leadership is crucial for guiding project teams through the various phases of the DMAIC methodology.
- As a Black Belt, you need to inspire and motivate team members, set clear expectations, and foster a collaborative and productive team environment.
- Strong leadership skills enable you to delegate tasks, resolve conflicts, and ensure that team members are aligned and focused on achieving project goals.
- Influencing Stakeholders:
- Change within an organization often encounters resistance from stakeholders who may be skeptical or hesitant to adopt new processes or methods.
- As a Black Belt, you must possess influential communication and persuasion skills to engage stakeholders, build trust, and communicate the benefits of process improvements.
- By effectively engaging stakeholders, you can gain their support, address concerns, and drive organizational buy-in for the proposed changes.
- Change Management Expertise:
- Change management is a critical aspect of successful process improvement initiatives. It involves preparing individuals and the organization for the changes that will result from implementing new processes or procedures.
- Black Belts must be skilled in change management principles, including assessing the impact of changes, developing change management plans, and addressing resistance to change.
- By applying change management methodologies, such as creating communication plans, conducting training sessions, and providing ongoing support, Black Belts can facilitate smooth transitions and ensure sustainable results.
- Creating a Culture of Continuous Improvement:
- Black Belts are instrumental in fostering a culture of continuous improvement within their organizations.
- By leading by example, promoting a mindset of learning and innovation, and recognizing and celebrating successes, Black Belts can inspire others to embrace a continuous improvement mindset.
- This cultural shift encourages employees at all levels to proactively identify opportunities for improvement and participate in the ongoing enhancement of processes and operations.
- Project Management Skills:
- Effective project management is essential for successful process improvement initiatives.
- Black Belts must possess project management skills, including defining project scopes, setting realistic timelines, managing resources, and monitoring progress.
- By applying project management principles and practices, Black Belts can ensure that projects stay on track, are completed within specified timelines, and achieve the desired outcomes.
Leadership and change management skills are integral to the Six Sigma Black Belt role, as they enable Black Belts to guide teams, navigate organizational dynamics, and ensure the successful implementation of process improvements. By combining technical expertise with strong leadership and change management capabilities, Black Belts can drive sustainable change and make a significant impact on organizational performance and customer satisfaction.
Certification Process and Examination:
The certification process for Six Sigma Black Belt is an essential step for individuals aspiring to validate their expertise in process improvement and quality management. The process typically involves meeting certain requirements and successfully completing an examination. Here's an overview of the certification process and examination for Six Sigma Black Belt:
- Eligibility and Prerequisites:
- Before pursuing Six Sigma Black Belt certification, individuals must typically meet specific prerequisites set by the certifying body or organization offering the certification.
- Common prerequisites may include having a certain level of education (e.g., bachelor's degree) and relevant work experience in process improvement, quality management, or related fields.
- It is important to review and ensure that you meet the specific eligibility criteria before proceeding with the certification process.
- Training and Preparation:
- Black Belt candidates are often required to undergo comprehensive training to acquire the necessary knowledge and skills.
- Training programs can be offered by accredited institutions, training providers, or organizations specializing in Six Sigma methodologies.
- These training programs cover advanced topics such as statistical analysis, project management, process improvement tools, and Six Sigma principles.
- Candidates should carefully select a reputable training program that aligns with recognized Six Sigma methodologies and provides adequate preparation for the certification examination.
- Certification Examination:
- The certification examination is designed to assess candidates' understanding of Six Sigma concepts, methodologies, and their ability to apply them in real-world scenarios.
- The format and structure of the examination may vary depending on the certifying body or organization offering the certification.
- The examination typically consists of multiple-choice questions, scenario-based questions, or case studies that require candidates to demonstrate their problem-solving skills and application of Six Sigma tools and techniques.
- It is crucial to familiarize yourself with the exam format, content areas, and time constraints to adequately prepare for the examination.
- Exam Preparation:
- Adequate preparation is essential to increase the chances of success in the certification examination.
- Reviewing course materials, studying textbooks, practicing with sample questions, and taking mock exams can help candidates become familiar with the content and format of the exam.
- It is recommended to allocate dedicated study time, create a study plan, and leverage additional resources such as reference books, online tutorials, and study guides.
- Certification Renewal and Maintenance:
- Some certifying bodies may require individuals to renew their Six Sigma Black Belt certification periodically to ensure ongoing professional development and staying up-to-date with industry best practices.
- Renewal requirements may include earning continuing education credits, completing professional development activities, or participating in relevant projects.
- It is important to understand the specific renewal and maintenance requirements associated with the certification obtained.
How to obtain the Six Sigma Black Belt certification?
We are an Education Technology company providing certification training courses to accelerate careers of working professionals worldwide. We impart training through instructor-led classroom workshops, instructor-led live virtual training sessions, and self-paced e-learning courses.
We have successfully conducted training sessions in 108 countries across the globe and enabled thousands of working professionals to enhance the scope of their careers.
Our enterprise training portfolio includes in-demand and globally recognized certification training courses in Project Management, Quality Management, Business Analysis, IT Service Management, Agile and Scrum, Cyber Security, Data Science, and Emerging Technologies. Download our Enterprise Training Catalog from https://www.icertglobal.com/corporate-training-for-enterprises.php
Popular Courses include:
- Project Management: PMP, CAPM ,PMI RMP
- Quality Management: Six Sigma Black Belt ,Lean Six Sigma Green Belt, Lean Six Sigma Black Belt
- Business Analysis: CBAP, CCBA, ECBA
- Agile Training: PMI-ACP
- Scrum Training: CSM
- DevOps
- Program Management: PgMP
- IT Service Management & Governance: COBIT, ISO
Benefits and Career Opportunities:
Obtaining a Six Sigma Black Belt certification offers numerous benefits and opens up exciting career opportunities for professionals in various industries. Let's explore the key benefits and career opportunities associated with Six Sigma Black Belt certification:
- Enhanced Problem-Solving Skills:
- Six Sigma Black Belt certification equips individuals with advanced problem-solving techniques and tools.
- The certification emphasizes the use of data-driven analysis and statistical methods to identify and address process inefficiencies and quality issues.
- Black Belts gain the ability to analyze complex problems, identify root causes, and implement effective solutions, leading to improved organizational performance.
- Increased Employability:
- Six Sigma Black Belt certification is widely recognized and valued by organizations across industries.
- Holding this certification demonstrates a high level of competence in process improvement and quality management, making individuals highly sought after by employers.
- Certified Black Belts have a competitive edge in the job market and often enjoy better career prospects and higher earning potential.
- Leadership and Management Opportunities:
- Six Sigma Black Belt certification prepares individuals to lead and manage process improvement initiatives within organizations.
- Black Belts possess the skills to effectively lead cross-functional teams, influence stakeholders, and drive organizational change.
- They are well-positioned for roles such as Process Improvement Managers, Quality Managers, or Operations Managers, where they can spearhead continuous improvement efforts and contribute to overall business success.
- Cost Savings and Efficiency Gains:
- Six Sigma methodologies focus on reducing process variation, eliminating defects, and improving operational efficiency.
- Black Belts are trained to identify and eliminate waste, streamline processes, and optimize resource utilization.
- By implementing Six Sigma principles, organizations can achieve significant cost savings, improved productivity, and enhanced customer satisfaction.
- Career Advancement and Professional Growth:
- Six Sigma Black Belt certification provides a solid foundation for career advancement and professional growth.
- Black Belts are equipped with skills that are highly transferrable across industries and can lead to opportunities in various sectors such as manufacturing, healthcare, finance, and IT.
- Continuous learning and application of Six Sigma principles enable Black Belts to take on more challenging projects and assume leadership roles within their organizations.
- Contributing to Organizational Success:
- Six Sigma Black Belts play a pivotal role in driving organizational success by improving processes, reducing defects, and enhancing customer satisfaction.
- Their efforts result in tangible and measurable outcomes that directly contribute to business goals, performance, and profitability.
- Black Belts have the opportunity to make a significant impact on their organizations' bottom line, reputation, and competitive advantage.
Conclusion
In conclusion, Six Sigma Black Belt certification holds significant value for professionals seeking to excel in process improvement and quality management. Throughout this blog, we have explored various aspects related to Six Sigma Black Belt certification, including an introduction to the role, requirements for certification, the DMAIC methodology, the importance of leadership and change management, and the certification process and examination. We have also highlighted the benefits and career opportunities that come with earning this certification.
By obtaining Six Sigma Black Belt certification, individuals gain expertise in problem-solving, data analysis, project management, and change management. They become equipped to lead teams, influence stakeholders, and drive impactful process improvements within organizations. This certification enhances employability, opens doors to leadership roles, and offers opportunities for career advancement and professional growth.
Moreover, Six Sigma Black Belts contribute to the success of their organizations by improving efficiency, reducing costs, and enhancing customer satisfaction. Their ability to apply data-driven approaches and implement sustainable solutions leads to tangible and measurable results.
In a highly competitive business landscape, organizations are increasingly recognizing the value of professionals with Six Sigma Black Belt certification. As a certified Black Belt, individuals can make a significant impact, drive continuous improvement, and contribute to the overall success of their organizations.
In summary, Six Sigma Black Belt certification offers a pathway to excellence in process improvement, leadership, and career advancement. It is a valuable asset for professionals seeking to make a difference and excel in their chosen fields.
Read More
The Six Sigma Black Belt certification represents the pinnacle of expertise in process improvement and quality management. It is a highly coveted credential that signifies an individual's mastery of Lean Six Sigma methodologies and their ability to lead complex improvement initiatives within organizations. In this article, we will explore the significance of achieving a Six Sigma Black Belt and how it empowers individuals to effectively drive change and achieve their goals.
The journey to becoming a Six Sigma Black Belt requires a deep understanding of the DMAIC (Define, Measure, Analyze, Improve, Control) methodology and the application of advanced statistical analysis and problem-solving techniques. Black Belts possess the skills to lead cross-functional teams, manage projects, and orchestrate process improvements that yield substantial results.
With a Black Belt certification, individuals gain the capability to identify root causes of problems, analyze data-driven insights, and implement sustainable solutions. Black Belts excel in driving process optimization, reducing defects, enhancing productivity, and ultimately improving the bottom line. Their advanced problem-solving skills enable them to tackle complex challenges and overcome organizational barriers to change.
Moreover, Six Sigma Black Belts play a pivotal role in driving organizational excellence. They are equipped to align process improvement initiatives with business strategies, ensuring that efforts are focused on achieving the organization's goals. Black Belts are effective change agents, driving cultural transformation and fostering a mindset of continuous improvement throughout the organization.
Achieving a Six Sigma Black Belt is a testament to an individual's dedication to personal and professional growth. It opens doors to new career opportunities, as organizations across various industries recognize the value of individuals who possess the expertise to deliver significant improvements in quality, efficiency, and customer satisfaction. Additionally, Black Belts often serve as mentors and trainers for Green Belts and Yellow Belts, sharing their knowledge and guiding others on their journey to process excellence.
In conclusion, the Six Sigma Black Belt certification represents the highest level of proficiency in Lean Six Sigma methodologies. Black Belts possess the knowledge and skills to drive substantial process improvements and achieve organizational goals. Their expertise in advanced problem-solving, data analysis, and project management enables them to lead impactful change initiatives. By obtaining a Six Sigma Black Belt, individuals position themselves as catalysts for transformation, driving success in organizations and achieving their own professional aspirations.
Table of contents
- Introduction to Six Sigma Black Belt
- Requirements for Six Sigma Black Belt Certification:
- DMAIC Methodology:
- Leadership and Change Management:
- Certification Process and Examination:
- Benefits and Career Opportunities:
- Conclusion
Introduction to Six Sigma Black Belt:
Six Sigma, a renowned methodology for process improvement and quality management, has revolutionized the way organizations operate. At the heart of Six Sigma lies the role of a Black Belt, a highly skilled professional responsible for leading improvement projects and driving significant results. A Six Sigma Black Belt possesses a deep understanding of statistical analysis, problem-solving techniques, and project management. Their expertise enables them to identify process inefficiencies, reduce variation, and enhance overall organizational performance. Obtaining a Six Sigma Black Belt certification showcases a commitment to excellence and signifies mastery of the methodology. In this blog post, we will explore the significance of Six Sigma Black Belt certification, its requirements, and the essential skills it encompasses, shedding light on the value these professionals bring to organizations seeking continuous improvement and success.
Requirements for Six Sigma Black Belt Certification:
To earn a Six Sigma Black Belt certification, individuals are required to meet certain prerequisites that ensure they possess the necessary knowledge, skills, and experience to effectively lead process improvement initiatives. The specific requirements may vary depending on the certifying body or organization offering the certification. Here are some common requirements:
- Education and Experience:
- A minimum educational qualification, such as a bachelor's degree, is often required. The field of study may vary, but degrees in engineering, business, mathematics, or statistics are commonly preferred.
- Several years of professional work experience in a relevant field are typically expected. This experience should involve exposure to process improvement, project management, or quality management responsibilities.
- Completion of Green Belt Certification:
- Many certifying bodies require candidates to have already earned a Six Sigma Green Belt certification. This ensures a solid foundation in the principles, tools, and techniques of Six Sigma methodology.
- Green Belt certification demonstrates practical experience in executing process improvement projects and serves as a stepping stone to the more advanced Black Belt level.
- Training and Professional Development:
- Completion of a comprehensive Black Belt training program is usually mandatory. This training covers advanced statistical analysis, project management, process mapping, and other specialized Six Sigma tools and techniques.
- The training may be conducted in a classroom setting or through online courses. It is essential to choose an accredited program that aligns with recognized Six Sigma methodologies.
- Demonstrated Application of Six Sigma:
- Candidates are typically required to showcase their practical application of Six Sigma principles and methodologies in real-world projects.
- This may involve providing evidence of successfully completed improvement projects, including project charters, data analysis, process documentation, and measurable outcomes.
- Written Examination:
- Candidates are generally required to pass a written examination to demonstrate their understanding of Six Sigma concepts, tools, and methodologies.
- The exam may include multiple-choice questions, case studies, and scenario-based assessments.
- Adequate preparation through self-study, review of course materials, and practice exams is essential to perform well in the certification exam.
GET COURSE
DMAIC Methodology
The DMAIC methodology is a core component of Six Sigma and serves as a systematic framework for problem-solving and process improvement. DMAIC stands for Define, Measure, Analyze, Improve, and Control, representing the five distinct phases of the methodology. Each phase plays a vital role in identifying and eliminating process deficiencies to achieve enhanced performance and customer satisfaction. Let's explore each phase of the DMAIC methodology in detail:
- Define:
- In the Define phase, the project team clarifies the problem or opportunity for improvement, establishes project goals, and defines customer requirements and expectations.
- Key activities in this phase include developing a project charter, identifying stakeholders, and defining the project scope and boundaries.
- The goal is to ensure a clear understanding of the problem to be addressed and align project objectives with the overall organizational goals.
- Measure:
- The Measure phase focuses on collecting data and measuring the current state of the process under study.
- The team identifies and selects relevant process metrics and establishes a baseline for performance.
- Data collection methods, such as sampling, surveys, or direct measurements, are employed to quantify process performance and identify sources of variation.
- Analyze:
- In the Analyze phase, the collected data is analyzed to identify root causes of process variation and performance gaps.
- Statistical tools and techniques, such as hypothesis testing, regression analysis, and Pareto charts, are utilized to identify factors that significantly impact the process outcomes.
- The goal is to gain insights into the underlying causes of problems and prioritize improvement opportunities.
- Improve:
- The Improve phase focuses on developing and implementing solutions to address the identified root causes and improve process performance.
- The team generates potential solutions, evaluates their feasibility, and selects the most promising ones.
- These solutions are then tested on a small scale through pilots or simulations before being implemented fully.
- The objective is to implement changes that result in significant process improvement and meet the desired goals.
- Control:
- The Control phase involves establishing control mechanisms to sustain the improvements achieved and prevent a return to the previous state.
- Process controls, such as standard operating procedures, statistical process control charts, and training programs, are put in place.
- The team develops a monitoring and feedback system to track ongoing process performance and ensure that any deviations are promptly addressed.
- The aim is to create a culture of continuous improvement and ensure that the gains achieved through the project are maintained over time.
By following the DMAIC methodology, organizations can systematically approach process improvement, driving data-driven decision-making and achieving measurable results. It provides a structured approach for tackling complex problems, identifying opportunities for improvement, and implementing effective solutions. DMAIC serves as a powerful tool for organizations seeking to enhance quality, reduce costs, and improve customer satisfaction.
Leadership and Change Management:
In the context of Six Sigma Black Belt certification, leadership and change management skills play a critical role in driving successful process improvement initiatives. As a Six Sigma Black Belt, you are not only responsible for applying technical tools and methodologies but also for leading teams, influencing stakeholders, and managing the change associated with process improvements. Let's explore the importance of leadership and change management in the Six Sigma Black Belt role:
- Leading Teams:
- Effective leadership is crucial for guiding project teams through the various phases of the DMAIC methodology.
- As a Black Belt, you need to inspire and motivate team members, set clear expectations, and foster a collaborative and productive team environment.
- Strong leadership skills enable you to delegate tasks, resolve conflicts, and ensure that team members are aligned and focused on achieving project goals.
- Influencing Stakeholders:
- Change within an organization often encounters resistance from stakeholders who may be skeptical or hesitant to adopt new processes or methods.
- As a Black Belt, you must possess influential communication and persuasion skills to engage stakeholders, build trust, and communicate the benefits of process improvements.
- By effectively engaging stakeholders, you can gain their support, address concerns, and drive organizational buy-in for the proposed changes.
- Change Management Expertise:
- Change management is a critical aspect of successful process improvement initiatives. It involves preparing individuals and the organization for the changes that will result from implementing new processes or procedures.
- Black Belts must be skilled in change management principles, including assessing the impact of changes, developing change management plans, and addressing resistance to change.
- By applying change management methodologies, such as creating communication plans, conducting training sessions, and providing ongoing support, Black Belts can facilitate smooth transitions and ensure sustainable results.
- Creating a Culture of Continuous Improvement:
- Black Belts are instrumental in fostering a culture of continuous improvement within their organizations.
- By leading by example, promoting a mindset of learning and innovation, and recognizing and celebrating successes, Black Belts can inspire others to embrace a continuous improvement mindset.
- This cultural shift encourages employees at all levels to proactively identify opportunities for improvement and participate in the ongoing enhancement of processes and operations.
- Project Management Skills:
- Effective project management is essential for successful process improvement initiatives.
- Black Belts must possess project management skills, including defining project scopes, setting realistic timelines, managing resources, and monitoring progress.
- By applying project management principles and practices, Black Belts can ensure that projects stay on track, are completed within specified timelines, and achieve the desired outcomes.
Leadership and change management skills are integral to the Six Sigma Black Belt role, as they enable Black Belts to guide teams, navigate organizational dynamics, and ensure the successful implementation of process improvements. By combining technical expertise with strong leadership and change management capabilities, Black Belts can drive sustainable change and make a significant impact on organizational performance and customer satisfaction.
Certification Process and Examination:
The certification process for Six Sigma Black Belt is an essential step for individuals aspiring to validate their expertise in process improvement and quality management. The process typically involves meeting certain requirements and successfully completing an examination. Here's an overview of the certification process and examination for Six Sigma Black Belt:
- Eligibility and Prerequisites:
- Before pursuing Six Sigma Black Belt certification, individuals must typically meet specific prerequisites set by the certifying body or organization offering the certification.
- Common prerequisites may include having a certain level of education (e.g., bachelor's degree) and relevant work experience in process improvement, quality management, or related fields.
- It is important to review and ensure that you meet the specific eligibility criteria before proceeding with the certification process.
- Training and Preparation:
- Black Belt candidates are often required to undergo comprehensive training to acquire the necessary knowledge and skills.
- Training programs can be offered by accredited institutions, training providers, or organizations specializing in Six Sigma methodologies.
- These training programs cover advanced topics such as statistical analysis, project management, process improvement tools, and Six Sigma principles.
- Candidates should carefully select a reputable training program that aligns with recognized Six Sigma methodologies and provides adequate preparation for the certification examination.
- Certification Examination:
- The certification examination is designed to assess candidates' understanding of Six Sigma concepts, methodologies, and their ability to apply them in real-world scenarios.
- The format and structure of the examination may vary depending on the certifying body or organization offering the certification.
- The examination typically consists of multiple-choice questions, scenario-based questions, or case studies that require candidates to demonstrate their problem-solving skills and application of Six Sigma tools and techniques.
- It is crucial to familiarize yourself with the exam format, content areas, and time constraints to adequately prepare for the examination.
- Exam Preparation:
- Adequate preparation is essential to increase the chances of success in the certification examination.
- Reviewing course materials, studying textbooks, practicing with sample questions, and taking mock exams can help candidates become familiar with the content and format of the exam.
- It is recommended to allocate dedicated study time, create a study plan, and leverage additional resources such as reference books, online tutorials, and study guides.
- Certification Renewal and Maintenance:
- Some certifying bodies may require individuals to renew their Six Sigma Black Belt certification periodically to ensure ongoing professional development and staying up-to-date with industry best practices.
- Renewal requirements may include earning continuing education credits, completing professional development activities, or participating in relevant projects.
- It is important to understand the specific renewal and maintenance requirements associated with the certification obtained.
How to obtain the Six Sigma Black Belt certification?
We are an Education Technology company providing certification training courses to accelerate careers of working professionals worldwide. We impart training through instructor-led classroom workshops, instructor-led live virtual training sessions, and self-paced e-learning courses.
We have successfully conducted training sessions in 108 countries across the globe and enabled thousands of working professionals to enhance the scope of their careers.
Our enterprise training portfolio includes in-demand and globally recognized certification training courses in Project Management, Quality Management, Business Analysis, IT Service Management, Agile and Scrum, Cyber Security, Data Science, and Emerging Technologies. Download our Enterprise Training Catalog from https://www.icertglobal.com/corporate-training-for-enterprises.php
Popular Courses include:
- Project Management: PMP, CAPM ,PMI RMP
- Quality Management: Six Sigma Black Belt ,Lean Six Sigma Green Belt, Lean Six Sigma Black Belt
- Business Analysis: CBAP, CCBA, ECBA
- Agile Training: PMI-ACP
- Scrum Training: CSM
- DevOps
- Program Management: PgMP
- IT Service Management & Governance: COBIT, ISO
Benefits and Career Opportunities:
Obtaining a Six Sigma Black Belt certification offers numerous benefits and opens up exciting career opportunities for professionals in various industries. Let's explore the key benefits and career opportunities associated with Six Sigma Black Belt certification:
- Enhanced Problem-Solving Skills:
- Six Sigma Black Belt certification equips individuals with advanced problem-solving techniques and tools.
- The certification emphasizes the use of data-driven analysis and statistical methods to identify and address process inefficiencies and quality issues.
- Black Belts gain the ability to analyze complex problems, identify root causes, and implement effective solutions, leading to improved organizational performance.
- Increased Employability:
- Six Sigma Black Belt certification is widely recognized and valued by organizations across industries.
- Holding this certification demonstrates a high level of competence in process improvement and quality management, making individuals highly sought after by employers.
- Certified Black Belts have a competitive edge in the job market and often enjoy better career prospects and higher earning potential.
- Leadership and Management Opportunities:
- Six Sigma Black Belt certification prepares individuals to lead and manage process improvement initiatives within organizations.
- Black Belts possess the skills to effectively lead cross-functional teams, influence stakeholders, and drive organizational change.
- They are well-positioned for roles such as Process Improvement Managers, Quality Managers, or Operations Managers, where they can spearhead continuous improvement efforts and contribute to overall business success.
- Cost Savings and Efficiency Gains:
- Six Sigma methodologies focus on reducing process variation, eliminating defects, and improving operational efficiency.
- Black Belts are trained to identify and eliminate waste, streamline processes, and optimize resource utilization.
- By implementing Six Sigma principles, organizations can achieve significant cost savings, improved productivity, and enhanced customer satisfaction.
- Career Advancement and Professional Growth:
- Six Sigma Black Belt certification provides a solid foundation for career advancement and professional growth.
- Black Belts are equipped with skills that are highly transferrable across industries and can lead to opportunities in various sectors such as manufacturing, healthcare, finance, and IT.
- Continuous learning and application of Six Sigma principles enable Black Belts to take on more challenging projects and assume leadership roles within their organizations.
- Contributing to Organizational Success:
- Six Sigma Black Belts play a pivotal role in driving organizational success by improving processes, reducing defects, and enhancing customer satisfaction.
- Their efforts result in tangible and measurable outcomes that directly contribute to business goals, performance, and profitability.
- Black Belts have the opportunity to make a significant impact on their organizations' bottom line, reputation, and competitive advantage.
Conclusion
In conclusion, Six Sigma Black Belt certification holds significant value for professionals seeking to excel in process improvement and quality management. Throughout this blog, we have explored various aspects related to Six Sigma Black Belt certification, including an introduction to the role, requirements for certification, the DMAIC methodology, the importance of leadership and change management, and the certification process and examination. We have also highlighted the benefits and career opportunities that come with earning this certification.
By obtaining Six Sigma Black Belt certification, individuals gain expertise in problem-solving, data analysis, project management, and change management. They become equipped to lead teams, influence stakeholders, and drive impactful process improvements within organizations. This certification enhances employability, opens doors to leadership roles, and offers opportunities for career advancement and professional growth.
Moreover, Six Sigma Black Belts contribute to the success of their organizations by improving efficiency, reducing costs, and enhancing customer satisfaction. Their ability to apply data-driven approaches and implement sustainable solutions leads to tangible and measurable results.
In a highly competitive business landscape, organizations are increasingly recognizing the value of professionals with Six Sigma Black Belt certification. As a certified Black Belt, individuals can make a significant impact, drive continuous improvement, and contribute to the overall success of their organizations.
In summary, Six Sigma Black Belt certification offers a pathway to excellence in process improvement, leadership, and career advancement. It is a valuable asset for professionals seeking to make a difference and excel in their chosen fields.
A Closer Look at Sigma Green Belt Certification Levels.
Sigma Green Belt is a significant level of expertise in the field of process improvement and quality management. It is a certification that demonstrates an individual's comprehensive understanding of Lean Six Sigma methodologies and their ability to drive impactful change within an organization. In this article, we will take a closer look at the Sigma Green Belt levels, exploring the knowledge, skills, and responsibilities associated with this role.
The Sigma Green Belt certification builds upon the foundation of the Yellow Belt level and equips individuals with a deeper understanding of Lean Six Sigma principles and tools. Green Belts are trained to lead process improvement projects within their organizations, using the DMAIC (Define, Measure, Analyze, Improve, Control) methodology as their framework. They possess a solid grasp of statistical analysis, problem-solving techniques, and process optimization strategies.
Green Belts play a crucial role in driving continuous improvement initiatives. They collaborate with cross-functional teams, stakeholders, and leadership to identify process bottlenecks, reduce defects, and enhance overall operational efficiency. Their responsibilities include data collection and analysis, root cause identification, implementation of process changes, and monitoring of performance metrics.
A Sigma Green Belt possesses the skills necessary to facilitate change management and foster a culture of continuous improvement within their organization. They are adept at using Lean principles to eliminate waste, streamline processes, and enhance customer satisfaction. Green Belts also serve as mentors and coaches to Yellow Belt practitioners, guiding them in their journey towards process excellence.
Obtaining a Sigma Green Belt certification offers numerous benefits both for individuals and organizations. It demonstrates a commitment to quality and process improvement, enhancing an individual's marketability and career prospects. Organizations that employ Green Belts benefit from their expertise in driving cost savings, improving customer satisfaction, and achieving operational excellence.
In conclusion, the Sigma Green Belt certification represents a significant level of proficiency in Lean Six Sigma methodologies and process improvement. Green Belts possess a comprehensive understanding of the DMAIC framework, statistical analysis, and problem-solving techniques. They play a pivotal role in leading process improvement projects and driving organizational success through continuous improvement initiatives. The Sigma Green Belt certification opens doors to exciting opportunities and enables individuals to make a tangible impact on business processes, quality, and customer satisfaction.
Table of contents
- Introduction to Six Sigma Green Belt:
- Roles and Responsibilities of a Six Sigma Green Belt:
- Skills and Knowledge Required for Green Belt Certification:
- Green Belt Certification Process:
- Career Benefits of Green Belt Certification:
- Challenges and Tips for Green Belt Certification:
- Continuing Education and Advancement:
- Conclusion
Introduction to Six Sigma Green Belt:
Six Sigma is a highly effective methodology used to improve business processes, reduce defects, and enhance overall quality and efficiency. Within the Six Sigma hierarchy, the Green Belt certification is an important milestone. It signifies a level of expertise in process improvement and qualifies individuals to lead smaller-scale improvement projects within their organizations.
The Six Sigma Green Belt certification equips professionals with the knowledge and skills to analyze processes, identify areas for improvement, and implement data-driven solutions. Green Belts work closely with Black Belts and other team members to drive continuous improvement and achieve measurable results.
To become a certified Six Sigma Green Belt, individuals undergo comprehensive training that covers the principles, tools, and methodologies of Six Sigma. They learn how to define project goals, measure process performance, analyze data, identify root causes of issues, implement improvements, and control process variability.
The role of a Six Sigma Green Belt is multifaceted. Green Belts act as valuable resources within their organizations, collaborating with stakeholders from various departments to identify opportunities for improvement, gather data, and implement process enhancements. They also play a key role in facilitating change management and ensuring the sustained success of improvement initiatives.
Green Belts are adept at applying statistical analysis techniques and using tools such as process maps, control charts, Pareto charts, and root cause analysis to drive process improvement. They are trained to use problem-solving methodologies, such as DMAIC (Define, Measure, Analyze, Improve, Control) or PDCA (Plan, Do, Check, Act), to systematically approach and resolve business challenges.
In addition to their technical skills, Six Sigma Green Belts possess excellent communication, leadership, and project management abilities. They collaborate with cross-functional teams, facilitate meetings, present findings and recommendations, and drive the implementation of process improvements.
Obtaining a Six Sigma Green Belt certification not only validates an individual's expertise but also opens up a world of career opportunities. Green Belts can pursue roles such as process engineers, quality analysts, project managers, operations managers, or continuous improvement specialists in a wide range of industries.
In summary, the Six Sigma Green Belt certification is a significant achievement that demonstrates proficiency in process improvement methodologies and problem-solving skills. Green Belts contribute to the success of their organizations by identifying and implementing data-driven solutions, driving continuous improvement, and ensuring the delivery of high-quality products and services.
Key Principles of Six Sigma:
- Customer Focus: Understanding and meeting customer needs and expectations.
- Data-Driven Approach: Utilizing statistical analysis to make informed decisions.
- Process Improvement: Identifying and eliminating sources of variation and defects.
- Teamwork and Collaboration: Involving cross-functional teams in problem-solving efforts.
- Leadership Involvement: Providing support and guidance from top management.
Benefits of Implementing Six Sigma: Implementing Six Sigma offers several advantages to organizations, including:
- Improved Quality: By reducing defects and errors, Six Sigma enhances product and service quality, leading to increased customer satisfaction and loyalty.
- Cost Reduction: The focus on waste reduction and process optimization helps organizations save costs by eliminating unnecessary steps, improving efficiency, and reducing rework.
- Increased Efficiency: Six Sigma aims to streamline processes, leading to improved productivity, shorter cycle times, and faster delivery of products and services.
- Enhanced Decision-Making: The data-driven approach of Six Sigma provides organizations with valuable insights and enables informed decision-making based on facts and analysis.
- Organizational Culture of Continuous Improvement: Six Sigma fosters a culture of continuous improvement, encouraging employees to proactively identify and address issues, resulting in a more agile and innovative organization.
- Competitive Advantage: Implementing Six Sigma can give organizations a competitive edge by delivering higher-quality products and services, meeting customer expectations, and differentiating themselves in the market.
Roles and Responsibilities of a Six Sigma Green Belt:
A Six Sigma Green Belt plays a vital role in driving process improvement initiatives within an organization. They possess a strong understanding of Six Sigma methodologies, tools, and techniques, enabling them to contribute effectively to improvement projects. Here are the key roles and responsibilities of a Six Sigma Green Belt:
- Project Leadership: Green Belts are responsible for leading smaller-scale process improvement projects. They work closely with project teams, stakeholders, and sponsors to define project goals, scope, and deliverables.
- Data Collection and Analysis: Green Belts gather and analyze data to identify areas of improvement and determine the root causes of defects or inefficiencies. They utilize statistical tools and techniques to analyze process performance and make data-driven decisions.
- Process Mapping and Documentation: Green Belts document current processes, create process maps, and identify areas of waste or bottlenecks. They collaborate with process owners to develop optimized process maps and standard operating procedures (SOPs).
- Statistical Analysis: Green Belts apply statistical analysis methods to assess process capability, identify process variations, and validate improvement initiatives. They use tools such as hypothesis testing, regression analysis, and design of experiments (DOE) to analyze data and make evidence-based decisions.
- Project Implementation: Green Belts are responsible for implementing process improvements and ensuring that the changes are effectively integrated into the organization. They work with cross-functional teams to develop and execute action plans, monitor progress, and overcome implementation challenges.
- Team Collaboration and Communication: Green Belts work collaboratively with project teams, stakeholders, and process owners to facilitate effective communication and collaboration. They engage team members, provide guidance, and foster a culture of continuous improvement within the project.
- Training and Coaching: Green Belts may be involved in training team members on Six Sigma methodologies, tools, and techniques. They provide guidance and support to team members throughout the project, helping them understand and apply Six Sigma concepts effectively.
- Project Documentation and Reporting: Green Belts document project progress, outcomes, and lessons learned. They prepare project reports and presentations to communicate results, benefits, and recommendations to stakeholders and management.
- Continuous Improvement: Green Belts actively participate in the continuous improvement efforts of the organization. They contribute ideas, suggest improvements, and identify opportunities for further optimization beyond their assigned projects.
- Support to Black Belts: Green Belts provide support to Black Belts in larger-scale improvement initiatives. They assist in data analysis, project management, and process improvement activities under the guidance of Black Belts.
Skills and Knowledge Required for Green Belt Certification:
Obtaining a Six Sigma Green Belt certification requires a combination of skills and knowledge in the areas of process improvement, data analysis, and project management. Here are the key skills and knowledge areas required for Green Belt certification:
- Understanding of Six Sigma Methodology: Green Belts should have a solid understanding of the fundamental principles, concepts, and tools of Six Sigma. They should be familiar with the DMAIC (Define, Measure, Analyze, Improve, Control) framework and its application in process improvement projects.
- Statistical Analysis: Proficiency in statistical analysis is crucial for Green Belts. They should have knowledge of statistical concepts, hypothesis testing, regression analysis, design of experiments (DOE), control charts, and other statistical tools used in Six Sigma projects.
- Problem-Solving and Root Cause Analysis: Green Belts should be skilled in identifying problems, conducting root cause analysis, and applying structured problem-solving techniques. They should be able to use tools such as fishbone diagrams, 5 Whys, and Pareto analysis to determine the underlying causes of process issues.
- Data Collection and Analysis: Green Belts should be proficient in data collection methods, including sampling techniques, and have the ability to collect and analyze process data effectively. They should be comfortable working with data sets, performing data analysis, and interpreting results to drive improvement efforts.
- Process Mapping and Documentation: Green Belts should have knowledge of process mapping techniques and be able to document existing processes accurately. They should be able to identify process steps, inputs, outputs, and dependencies to create process maps and flowcharts.
- Project Management: Green Belts should possess project management skills to effectively plan, execute, and monitor improvement projects. They should be familiar with project management methodologies, such as defining project goals, creating work breakdown structures, managing timelines, and identifying project risks and mitigation strategies.
- Communication and Collaboration: Effective communication and collaboration are essential skills for Green Belts. They should be able to clearly communicate project objectives, progress, and findings to team members, stakeholders, and management. They should also be skilled in facilitating teamwork, resolving conflicts, and engaging stakeholders throughout the project lifecycle.
- Change Management: Green Belts should have an understanding of change management principles and techniques. They should be able to anticipate and address resistance to change, communicate the benefits of process improvements, and facilitate the adoption of new processes within the organization.
- Software and Tools Proficiency: Green Belts should be familiar with statistical software tools, such as Minitab, JMP, or Excel, to perform data analysis and generate statistical reports. They should also have knowledge of process mapping tools, project management software, and other Six Sigma-specific software applications.
- Continuous Learning and Improvement: Green Belts should have a mindset of continuous learning and improvement. They should stay updated with the latest Six Sigma concepts, methodologies, and industry best practices. Actively seeking opportunities for professional development and staying engaged in the Six Sigma community is important.
Green Belt Certification Process:
The Green Belt certification process involves several steps that individuals need to follow to obtain their Six Sigma Green Belt certification. While specific requirements and processes may vary depending on the certification body or training provider, here is a general outline of the Green Belt certification process:
- Eligibility and Prerequisites:
- Check the eligibility requirements set by the certification body or training provider. Typically, there are no specific prerequisites for Green Belt certification, but some organizations may recommend or require prior experience in process improvement or quality management.
- Training and Education:
- Enroll in a Six Sigma Green Belt training program. These programs are typically offered by training providers and cover the necessary concepts, methodologies, tools, and techniques of Six Sigma.
- Attend the training sessions, either in-person or online, and actively participate in the learning activities, exercises, and discussions.
- Complete all the required coursework and assignments as outlined by the training program.
- Knowledge Assessment:
- Prepare for and take the Green Belt certification exam. The exam assesses your understanding of Six Sigma concepts, methodologies, tools, and techniques.
- The exam may be in the form of multiple-choice questions, case studies, or a combination of different question types.
- The exam may be administered online or in a proctored environment, depending on the certification body or training provider.
- Project Work and Documentation:
- Complete a process improvement project as part of the certification requirements. The project should demonstrate your ability to apply Six Sigma principles and tools effectively.
- Select a suitable project within your organization or a relevant industry context that aligns with the DMAIC (Define, Measure, Analyze, Improve, Control) framework.
- Apply the appropriate Six Sigma tools and techniques to analyze the process, identify improvement opportunities, and implement solutions.
- Document the project work, including the problem statement, project objectives, data analysis, process improvements, and results achieved.
- Project Review and Evaluation:
- Submit your project documentation to the certification body or training provider for review and evaluation.
- The certification body or designated experts will assess your project work to ensure it meets the required standards and demonstrates the application of Six Sigma principles effectively.
- They may provide feedback or request additional information or clarification on specific aspects of your project.
- Certification Award:
- Once your project work and documentation are approved, you will receive your Six Sigma Green Belt certification from the certification body or training provider.
- The certification may be in the form of a digital certificate, a physical certificate, or both.
- Your certification demonstrates your proficiency in Six Sigma principles, methodologies, and tools and validates your ability to contribute to process improvement initiatives.
It's important to note that the certification process may differ based on the certification body or training provider. Some organizations may require a minimum passing score on the exam, while others may emphasize the practical application of Six Sigma concepts through the project work. It is advisable to research and select a reputable certification body or training provider that aligns with your career goals and aspirations.
Career Benefits of Green Belt Certification:
Earning a Six Sigma Green Belt certification offers numerous career benefits, as it demonstrates your proficiency in process improvement and quality management. Here are some key career benefits of obtaining a Green Belt certification:
- Expanded Career Opportunities: Green Belt certification opens up new career opportunities in various industries and organizations that prioritize process improvement and quality management. It can make you a sought-after candidate for roles such as process engineer, quality analyst, project manager, operations manager, and continuous improvement specialist.
- Enhanced Employability: Green Belt certification enhances your employability by showcasing your specialized skills and knowledge in Six Sigma. Employers often value professionals who can drive process improvements, reduce defects, and optimize operations, making you a desirable candidate for organizations seeking to enhance their efficiency and quality.
- Increased Earning Potential: Green Belt certification can positively impact your earning potential. Certified professionals often command higher salaries compared to their non-certified counterparts due to their specialized knowledge and ability to deliver measurable improvements in processes and performance.
- Recognition and Credibility: Green Belt certification adds credibility to your professional profile. It validates your expertise in Six Sigma principles and methodologies, giving you a competitive edge in the job market. Certification demonstrates your commitment to professional development and showcases your dedication to quality and continuous improvement.
- Ability to Lead Improvement Projects: Green Belt certification equips you with the skills and knowledge to lead smaller-scale improvement projects within your organization. This responsibility highlights your leadership potential and ability to drive change. It provides valuable experience in project management, data analysis, and problem-solving, which are highly valued skills in many organizations.
- Cross-Functional Collaboration: As a Green Belt, you collaborate with stakeholders from different departments and levels of the organization. This cross-functional exposure enhances your communication, teamwork, and leadership skills, making you a valuable asset for organizations that value collaboration and effective interdepartmental coordination.
- Professional Networking Opportunities: Green Belt certification opens doors to professional networking opportunities. You can connect with other certified professionals, attend industry conferences, join Six Sigma forums, and participate in community events. Networking helps you stay updated on industry trends, gain insights from experienced professionals, and potentially explore new career opportunities.
- Continuous Professional Development: Six Sigma is a dynamic field, and Green Belt certification signifies your commitment to ongoing professional development. It demonstrates your willingness to stay updated with the latest tools, methodologies, and best practices in process improvement. This commitment enhances your long-term career prospects and keeps you adaptable in a rapidly changing business environment.
- Contribution to Organizational Success: With Green Belt certification, you can make a tangible impact on your organization's success. By leading improvement projects and driving process enhancements, you contribute to increased efficiency, reduced costs, improved customer satisfaction, and overall organizational performance.
- Path to Advanced Certifications: Green Belt certification serves as a stepping stone to higher-level Six Sigma certifications, such as Black Belt and Master Black Belt. These advanced certifications provide opportunities for career progression and leadership roles in process improvement, quality management, and organizational excellence.
Challenges and Tips for Green Belt Certification:
While pursuing Six Sigma Green Belt certification, you may encounter certain challenges. Here are some common challenges and tips to help you navigate the certification process more effectively:
- Balancing Work and Certification Preparation:
- Challenge: Finding time to study and prepare for the certification while managing work responsibilities can be challenging.
- Tip: Create a study schedule and allocate dedicated time each day or week for exam preparation. Prioritize your tasks and eliminate non-essential activities to create more study time. Seek support from your supervisor or team to ensure you have adequate time to focus on certification preparation.
- Grasping Complex Statistical Concepts:
- Challenge: Understanding statistical concepts and tools used in Six Sigma can be challenging, especially for those without a strong background in statistics.
- Tip: Take advantage of training programs or online resources that provide clear explanations and examples of statistical concepts. Break down complex concepts into smaller, more manageable parts. Practice applying statistical tools using real-life examples to reinforce your understanding. Seek assistance from trainers or mentors if you need additional guidance.
- Applying Six Sigma Principles in Real-World Projects:
- Challenge: Translating theoretical knowledge into practical application during process improvement projects can be challenging, particularly for beginners.
- Tip: Look for opportunities to apply Six Sigma principles in your work environment. Seek guidance from experienced Six Sigma practitioners or mentors who can provide insights and feedback on project work. Collaborate with colleagues to gain different perspectives and learn from their experiences. Consider taking on smaller-scale improvement projects to gain hands-on experience before tackling larger initiatives.
- Managing Resistance to Change:
- Challenge: Implementing process improvements often faces resistance from team members or stakeholders who may be resistant to change.
- Tip: Develop effective change management skills. Communicate the benefits of the proposed changes and involve stakeholders early in the process to gain their support. Address concerns and provide regular updates to keep everyone informed and engaged. Demonstrate the value of the improvements through data and measurable results.
- Balancing Theory and Practice:
- Challenge: Striking a balance between learning theoretical concepts and applying them practically can be challenging for Green Belt candidates.
- Tip: Seek out opportunities to apply Six Sigma tools and methodologies in real-life scenarios, either through projects at work or by participating in simulation exercises during your training. Reflect on the practical application of the concepts you learn during your certification journey to reinforce your understanding.
- Staying Motivated Throughout the Certification Process:
- Challenge: Maintaining motivation and focus during the certification process, especially when faced with setbacks or challenges, can be demanding.
- Tip: Set clear goals and visualize the benefits of achieving the Green Belt certification. Break down the certification process into smaller milestones to track your progress and celebrate your achievements along the way. Stay connected with a study group or a mentor who can provide encouragement and support. Remind yourself of the long-term career benefits and personal growth that the certification will bring.
- Exam Preparation:
- Challenge: Preparing for the Green Belt certification exam can be overwhelming, given the breadth of topics covered.
- Tip: Familiarize yourself with the exam format and content by reviewing sample questions and studying the recommended reference materials. Create a study plan and allocate sufficient time to review each topic. Practice solving exam-like questions to build your confidence and identify areas for improvement. Consider joining study groups or online forums to exchange knowledge and resources with fellow candidates.
Continuing Education and Advancement:
Obtaining a Six Sigma Green Belt certification is just the beginning of your journey in process improvement and quality management. To further advance your career and stay current in the field, it is essential to prioritize continuing education and professional development. Here are some avenues for continuing education and advancement:
- Pursue Advanced Six Sigma Certifications:
- Consider advancing to higher levels of Six Sigma certification, such as Six Sigma Black Belt or Master Black Belt. These certifications delve deeper into advanced statistical analysis, project management, and leadership skills. They open doors to more senior roles and provide opportunities to lead larger-scale improvement projects and mentor other Six Sigma practitioners.
- Attend Advanced Training Courses:
- Participate in advanced Six Sigma training courses that focus on specific methodologies, tools, or industries. These courses deepen your knowledge in specialized areas and expand your skill set. Examples include Lean Six Sigma, Design for Six Sigma (DFSS), or industry-specific applications of Six Sigma.
- Engage in Professional Associations and Networks:
- Join professional associations related to process improvement and quality management, such as the American Society for Quality (ASQ) or the International Association for Six Sigma Certification (IASSC). Engage in their events, conferences, and webinars to stay updated on the latest trends, practices, and research in the field. Networking with other professionals allows you to exchange ideas, gain insights, and build valuable connections.
- Continuous Learning:
- Stay updated on industry best practices, emerging technologies, and advancements in process improvement methodologies. Regularly read industry publications, books, and research articles. Follow reputable blogs and websites that focus on Six Sigma and quality management. Continuous learning keeps you informed about the latest developments and helps you adapt to changing business environments.
- Apply Six Sigma in Different Contexts:
- Look for opportunities to apply Six Sigma principles and tools in various contexts within your organization. Seek out projects that involve different departments, processes, or business units. This broadens your experience and allows you to gain a deeper understanding of how Six Sigma can be applied in diverse settings.
- Seek Mentoring and Coaching:
- Connect with experienced Six Sigma professionals who can mentor and guide you in your career development. Mentors can provide valuable insights, share their experiences, and offer advice on overcoming challenges. They can also help you set goals and provide feedback on your progress.
- Specialize in Additional Quality Management Methodologies:
- Expand your knowledge beyond Six Sigma by exploring other quality management methodologies such as Total Quality Management (TQM), Kaizen, or Lean principles. These methodologies complement Six Sigma and provide additional tools and perspectives for process improvement.
- Pursue Academic Degrees or Certificates:
- Consider pursuing academic degrees or certificates in areas related to process improvement, quality management, or operations management. Advanced degrees, such as a Master's in Business Administration (MBA) with a focus on operations or quality, can enhance your qualifications and open doors to higher-level positions.
- Contribute to the Six Sigma Community:
- Share your knowledge and experiences with others by writing articles, publishing case studies, or presenting at industry conferences. Contributing to the Six Sigma community helps build your reputation as a thought leader and expands your professional network.
How to obtain the Six Sigma Green Belt certification?
We are an Education Technology company providing certification training courses to accelerate careers of working professionals worldwide. We impart training through instructor-led classroom workshops, instructor-led live virtual training sessions, and self-paced e-learning courses.
We have successfully conducted training sessions in 108 countries across the globe and enabled thousands of working professionals to enhance the scope of their careers.
Our enterprise training portfolio includes in-demand and globally recognized certification training courses in Project Management, Quality Management, Business Analysis, IT Service Management, Agile and Scrum, Cyber Security, Data Science, and Emerging Technologies. Download our Enterprise Training Catalog from https://www.icertglobal.com/corporate-training-for-enterprises.php
Popular Courses include:
- Project Management: PMP, CAPM ,PMI RMP
- Quality Management: Six Sigma Green Belt ,Lean Six Sigma Yellow Belt, Lean Six Sigma Black Belt
- Business Analysis: CBAP, CCBA, ECBA
- Agile Training: PMI-ACP
- Scrum Training: CSM
- DevOps
- Program Management: PgMP
- IT Service Management & Governance: COBIT, ISO
Conclusion
In conclusion, Six Sigma Green Belt certification offers a pathway to professional growth and advancement in the field of process improvement and quality management. Throughout this blog, we have explored various aspects of Green Belt certification, including an introduction to Six Sigma, certification levels, roles and responsibilities, skills and knowledge requirements, the certification process, career benefits, challenges, and tips, as well as continuing education and advancement opportunities.
By obtaining a Green Belt certification, individuals gain a solid foundation in Six Sigma principles, methodologies, tools, and techniques. This certification enhances their employability, expands career opportunities, and increases earning potential. Green Belt certification holders are equipped with the skills to lead process improvement projects, contribute to organizational success, and drive positive change within their organizations.
However, the journey to Green Belt certification may come with challenges. Balancing work and certification preparation, grasping complex statistical concepts, applying Six Sigma principles practically, managing resistance to change, and staying motivated throughout the process are common hurdles. To overcome these challenges, it is crucial to develop effective study schedules, seek support from mentors or colleagues, break down complex concepts into manageable parts, and apply Six Sigma principles in real-world scenarios.
Continuing education and professional development are essential for long-term success in the field. Pursuing advanced certifications, attending training courses, engaging in professional associations and networks, continuous learning, seeking mentoring and coaching, specializing in other quality management methodologies, pursuing academic degrees or certificates, and contributing to the Six Sigma community are all avenues for growth and advancement.
In summary, Six Sigma Green Belt certification is a valuable asset that validates your expertise in process improvement and quality management. It opens doors to new career opportunities, enables you to make a positive impact within your organization, and sets the stage for further professional development. By embracing the principles of Six Sigma and continuously investing in your knowledge and skills, you can chart a successful career path in process improvement and quality management.
Read More
Sigma Green Belt is a significant level of expertise in the field of process improvement and quality management. It is a certification that demonstrates an individual's comprehensive understanding of Lean Six Sigma methodologies and their ability to drive impactful change within an organization. In this article, we will take a closer look at the Sigma Green Belt levels, exploring the knowledge, skills, and responsibilities associated with this role.
The Sigma Green Belt certification builds upon the foundation of the Yellow Belt level and equips individuals with a deeper understanding of Lean Six Sigma principles and tools. Green Belts are trained to lead process improvement projects within their organizations, using the DMAIC (Define, Measure, Analyze, Improve, Control) methodology as their framework. They possess a solid grasp of statistical analysis, problem-solving techniques, and process optimization strategies.
Green Belts play a crucial role in driving continuous improvement initiatives. They collaborate with cross-functional teams, stakeholders, and leadership to identify process bottlenecks, reduce defects, and enhance overall operational efficiency. Their responsibilities include data collection and analysis, root cause identification, implementation of process changes, and monitoring of performance metrics.
A Sigma Green Belt possesses the skills necessary to facilitate change management and foster a culture of continuous improvement within their organization. They are adept at using Lean principles to eliminate waste, streamline processes, and enhance customer satisfaction. Green Belts also serve as mentors and coaches to Yellow Belt practitioners, guiding them in their journey towards process excellence.
Obtaining a Sigma Green Belt certification offers numerous benefits both for individuals and organizations. It demonstrates a commitment to quality and process improvement, enhancing an individual's marketability and career prospects. Organizations that employ Green Belts benefit from their expertise in driving cost savings, improving customer satisfaction, and achieving operational excellence.
In conclusion, the Sigma Green Belt certification represents a significant level of proficiency in Lean Six Sigma methodologies and process improvement. Green Belts possess a comprehensive understanding of the DMAIC framework, statistical analysis, and problem-solving techniques. They play a pivotal role in leading process improvement projects and driving organizational success through continuous improvement initiatives. The Sigma Green Belt certification opens doors to exciting opportunities and enables individuals to make a tangible impact on business processes, quality, and customer satisfaction.
Table of contents
- Introduction to Six Sigma Green Belt:
- Roles and Responsibilities of a Six Sigma Green Belt:
- Skills and Knowledge Required for Green Belt Certification:
- Green Belt Certification Process:
- Career Benefits of Green Belt Certification:
- Challenges and Tips for Green Belt Certification:
- Continuing Education and Advancement:
- Conclusion
Introduction to Six Sigma Green Belt:
Six Sigma is a highly effective methodology used to improve business processes, reduce defects, and enhance overall quality and efficiency. Within the Six Sigma hierarchy, the Green Belt certification is an important milestone. It signifies a level of expertise in process improvement and qualifies individuals to lead smaller-scale improvement projects within their organizations.
The Six Sigma Green Belt certification equips professionals with the knowledge and skills to analyze processes, identify areas for improvement, and implement data-driven solutions. Green Belts work closely with Black Belts and other team members to drive continuous improvement and achieve measurable results.
To become a certified Six Sigma Green Belt, individuals undergo comprehensive training that covers the principles, tools, and methodologies of Six Sigma. They learn how to define project goals, measure process performance, analyze data, identify root causes of issues, implement improvements, and control process variability.
The role of a Six Sigma Green Belt is multifaceted. Green Belts act as valuable resources within their organizations, collaborating with stakeholders from various departments to identify opportunities for improvement, gather data, and implement process enhancements. They also play a key role in facilitating change management and ensuring the sustained success of improvement initiatives.
Green Belts are adept at applying statistical analysis techniques and using tools such as process maps, control charts, Pareto charts, and root cause analysis to drive process improvement. They are trained to use problem-solving methodologies, such as DMAIC (Define, Measure, Analyze, Improve, Control) or PDCA (Plan, Do, Check, Act), to systematically approach and resolve business challenges.
In addition to their technical skills, Six Sigma Green Belts possess excellent communication, leadership, and project management abilities. They collaborate with cross-functional teams, facilitate meetings, present findings and recommendations, and drive the implementation of process improvements.
Obtaining a Six Sigma Green Belt certification not only validates an individual's expertise but also opens up a world of career opportunities. Green Belts can pursue roles such as process engineers, quality analysts, project managers, operations managers, or continuous improvement specialists in a wide range of industries.
In summary, the Six Sigma Green Belt certification is a significant achievement that demonstrates proficiency in process improvement methodologies and problem-solving skills. Green Belts contribute to the success of their organizations by identifying and implementing data-driven solutions, driving continuous improvement, and ensuring the delivery of high-quality products and services.
Key Principles of Six Sigma:
- Customer Focus: Understanding and meeting customer needs and expectations.
- Data-Driven Approach: Utilizing statistical analysis to make informed decisions.
- Process Improvement: Identifying and eliminating sources of variation and defects.
- Teamwork and Collaboration: Involving cross-functional teams in problem-solving efforts.
- Leadership Involvement: Providing support and guidance from top management.
Benefits of Implementing Six Sigma: Implementing Six Sigma offers several advantages to organizations, including:
- Improved Quality: By reducing defects and errors, Six Sigma enhances product and service quality, leading to increased customer satisfaction and loyalty.
- Cost Reduction: The focus on waste reduction and process optimization helps organizations save costs by eliminating unnecessary steps, improving efficiency, and reducing rework.
- Increased Efficiency: Six Sigma aims to streamline processes, leading to improved productivity, shorter cycle times, and faster delivery of products and services.
- Enhanced Decision-Making: The data-driven approach of Six Sigma provides organizations with valuable insights and enables informed decision-making based on facts and analysis.
- Organizational Culture of Continuous Improvement: Six Sigma fosters a culture of continuous improvement, encouraging employees to proactively identify and address issues, resulting in a more agile and innovative organization.
- Competitive Advantage: Implementing Six Sigma can give organizations a competitive edge by delivering higher-quality products and services, meeting customer expectations, and differentiating themselves in the market.
Roles and Responsibilities of a Six Sigma Green Belt:
A Six Sigma Green Belt plays a vital role in driving process improvement initiatives within an organization. They possess a strong understanding of Six Sigma methodologies, tools, and techniques, enabling them to contribute effectively to improvement projects. Here are the key roles and responsibilities of a Six Sigma Green Belt:
- Project Leadership: Green Belts are responsible for leading smaller-scale process improvement projects. They work closely with project teams, stakeholders, and sponsors to define project goals, scope, and deliverables.
- Data Collection and Analysis: Green Belts gather and analyze data to identify areas of improvement and determine the root causes of defects or inefficiencies. They utilize statistical tools and techniques to analyze process performance and make data-driven decisions.
- Process Mapping and Documentation: Green Belts document current processes, create process maps, and identify areas of waste or bottlenecks. They collaborate with process owners to develop optimized process maps and standard operating procedures (SOPs).
- Statistical Analysis: Green Belts apply statistical analysis methods to assess process capability, identify process variations, and validate improvement initiatives. They use tools such as hypothesis testing, regression analysis, and design of experiments (DOE) to analyze data and make evidence-based decisions.
- Project Implementation: Green Belts are responsible for implementing process improvements and ensuring that the changes are effectively integrated into the organization. They work with cross-functional teams to develop and execute action plans, monitor progress, and overcome implementation challenges.
- Team Collaboration and Communication: Green Belts work collaboratively with project teams, stakeholders, and process owners to facilitate effective communication and collaboration. They engage team members, provide guidance, and foster a culture of continuous improvement within the project.
- Training and Coaching: Green Belts may be involved in training team members on Six Sigma methodologies, tools, and techniques. They provide guidance and support to team members throughout the project, helping them understand and apply Six Sigma concepts effectively.
- Project Documentation and Reporting: Green Belts document project progress, outcomes, and lessons learned. They prepare project reports and presentations to communicate results, benefits, and recommendations to stakeholders and management.
- Continuous Improvement: Green Belts actively participate in the continuous improvement efforts of the organization. They contribute ideas, suggest improvements, and identify opportunities for further optimization beyond their assigned projects.
- Support to Black Belts: Green Belts provide support to Black Belts in larger-scale improvement initiatives. They assist in data analysis, project management, and process improvement activities under the guidance of Black Belts.
Skills and Knowledge Required for Green Belt Certification:
Obtaining a Six Sigma Green Belt certification requires a combination of skills and knowledge in the areas of process improvement, data analysis, and project management. Here are the key skills and knowledge areas required for Green Belt certification:
- Understanding of Six Sigma Methodology: Green Belts should have a solid understanding of the fundamental principles, concepts, and tools of Six Sigma. They should be familiar with the DMAIC (Define, Measure, Analyze, Improve, Control) framework and its application in process improvement projects.
- Statistical Analysis: Proficiency in statistical analysis is crucial for Green Belts. They should have knowledge of statistical concepts, hypothesis testing, regression analysis, design of experiments (DOE), control charts, and other statistical tools used in Six Sigma projects.
- Problem-Solving and Root Cause Analysis: Green Belts should be skilled in identifying problems, conducting root cause analysis, and applying structured problem-solving techniques. They should be able to use tools such as fishbone diagrams, 5 Whys, and Pareto analysis to determine the underlying causes of process issues.
- Data Collection and Analysis: Green Belts should be proficient in data collection methods, including sampling techniques, and have the ability to collect and analyze process data effectively. They should be comfortable working with data sets, performing data analysis, and interpreting results to drive improvement efforts.
- Process Mapping and Documentation: Green Belts should have knowledge of process mapping techniques and be able to document existing processes accurately. They should be able to identify process steps, inputs, outputs, and dependencies to create process maps and flowcharts.
- Project Management: Green Belts should possess project management skills to effectively plan, execute, and monitor improvement projects. They should be familiar with project management methodologies, such as defining project goals, creating work breakdown structures, managing timelines, and identifying project risks and mitigation strategies.
- Communication and Collaboration: Effective communication and collaboration are essential skills for Green Belts. They should be able to clearly communicate project objectives, progress, and findings to team members, stakeholders, and management. They should also be skilled in facilitating teamwork, resolving conflicts, and engaging stakeholders throughout the project lifecycle.
- Change Management: Green Belts should have an understanding of change management principles and techniques. They should be able to anticipate and address resistance to change, communicate the benefits of process improvements, and facilitate the adoption of new processes within the organization.
- Software and Tools Proficiency: Green Belts should be familiar with statistical software tools, such as Minitab, JMP, or Excel, to perform data analysis and generate statistical reports. They should also have knowledge of process mapping tools, project management software, and other Six Sigma-specific software applications.
- Continuous Learning and Improvement: Green Belts should have a mindset of continuous learning and improvement. They should stay updated with the latest Six Sigma concepts, methodologies, and industry best practices. Actively seeking opportunities for professional development and staying engaged in the Six Sigma community is important.
Green Belt Certification Process:
The Green Belt certification process involves several steps that individuals need to follow to obtain their Six Sigma Green Belt certification. While specific requirements and processes may vary depending on the certification body or training provider, here is a general outline of the Green Belt certification process:
- Eligibility and Prerequisites:
- Check the eligibility requirements set by the certification body or training provider. Typically, there are no specific prerequisites for Green Belt certification, but some organizations may recommend or require prior experience in process improvement or quality management.
- Training and Education:
- Enroll in a Six Sigma Green Belt training program. These programs are typically offered by training providers and cover the necessary concepts, methodologies, tools, and techniques of Six Sigma.
- Attend the training sessions, either in-person or online, and actively participate in the learning activities, exercises, and discussions.
- Complete all the required coursework and assignments as outlined by the training program.
- Knowledge Assessment:
- Prepare for and take the Green Belt certification exam. The exam assesses your understanding of Six Sigma concepts, methodologies, tools, and techniques.
- The exam may be in the form of multiple-choice questions, case studies, or a combination of different question types.
- The exam may be administered online or in a proctored environment, depending on the certification body or training provider.
- Project Work and Documentation:
- Complete a process improvement project as part of the certification requirements. The project should demonstrate your ability to apply Six Sigma principles and tools effectively.
- Select a suitable project within your organization or a relevant industry context that aligns with the DMAIC (Define, Measure, Analyze, Improve, Control) framework.
- Apply the appropriate Six Sigma tools and techniques to analyze the process, identify improvement opportunities, and implement solutions.
- Document the project work, including the problem statement, project objectives, data analysis, process improvements, and results achieved.
- Project Review and Evaluation:
- Submit your project documentation to the certification body or training provider for review and evaluation.
- The certification body or designated experts will assess your project work to ensure it meets the required standards and demonstrates the application of Six Sigma principles effectively.
- They may provide feedback or request additional information or clarification on specific aspects of your project.
- Certification Award:
- Once your project work and documentation are approved, you will receive your Six Sigma Green Belt certification from the certification body or training provider.
- The certification may be in the form of a digital certificate, a physical certificate, or both.
- Your certification demonstrates your proficiency in Six Sigma principles, methodologies, and tools and validates your ability to contribute to process improvement initiatives.
It's important to note that the certification process may differ based on the certification body or training provider. Some organizations may require a minimum passing score on the exam, while others may emphasize the practical application of Six Sigma concepts through the project work. It is advisable to research and select a reputable certification body or training provider that aligns with your career goals and aspirations.
Career Benefits of Green Belt Certification:
Earning a Six Sigma Green Belt certification offers numerous career benefits, as it demonstrates your proficiency in process improvement and quality management. Here are some key career benefits of obtaining a Green Belt certification:
- Expanded Career Opportunities: Green Belt certification opens up new career opportunities in various industries and organizations that prioritize process improvement and quality management. It can make you a sought-after candidate for roles such as process engineer, quality analyst, project manager, operations manager, and continuous improvement specialist.
- Enhanced Employability: Green Belt certification enhances your employability by showcasing your specialized skills and knowledge in Six Sigma. Employers often value professionals who can drive process improvements, reduce defects, and optimize operations, making you a desirable candidate for organizations seeking to enhance their efficiency and quality.
- Increased Earning Potential: Green Belt certification can positively impact your earning potential. Certified professionals often command higher salaries compared to their non-certified counterparts due to their specialized knowledge and ability to deliver measurable improvements in processes and performance.
- Recognition and Credibility: Green Belt certification adds credibility to your professional profile. It validates your expertise in Six Sigma principles and methodologies, giving you a competitive edge in the job market. Certification demonstrates your commitment to professional development and showcases your dedication to quality and continuous improvement.
- Ability to Lead Improvement Projects: Green Belt certification equips you with the skills and knowledge to lead smaller-scale improvement projects within your organization. This responsibility highlights your leadership potential and ability to drive change. It provides valuable experience in project management, data analysis, and problem-solving, which are highly valued skills in many organizations.
- Cross-Functional Collaboration: As a Green Belt, you collaborate with stakeholders from different departments and levels of the organization. This cross-functional exposure enhances your communication, teamwork, and leadership skills, making you a valuable asset for organizations that value collaboration and effective interdepartmental coordination.
- Professional Networking Opportunities: Green Belt certification opens doors to professional networking opportunities. You can connect with other certified professionals, attend industry conferences, join Six Sigma forums, and participate in community events. Networking helps you stay updated on industry trends, gain insights from experienced professionals, and potentially explore new career opportunities.
- Continuous Professional Development: Six Sigma is a dynamic field, and Green Belt certification signifies your commitment to ongoing professional development. It demonstrates your willingness to stay updated with the latest tools, methodologies, and best practices in process improvement. This commitment enhances your long-term career prospects and keeps you adaptable in a rapidly changing business environment.
- Contribution to Organizational Success: With Green Belt certification, you can make a tangible impact on your organization's success. By leading improvement projects and driving process enhancements, you contribute to increased efficiency, reduced costs, improved customer satisfaction, and overall organizational performance.
- Path to Advanced Certifications: Green Belt certification serves as a stepping stone to higher-level Six Sigma certifications, such as Black Belt and Master Black Belt. These advanced certifications provide opportunities for career progression and leadership roles in process improvement, quality management, and organizational excellence.
Challenges and Tips for Green Belt Certification:
While pursuing Six Sigma Green Belt certification, you may encounter certain challenges. Here are some common challenges and tips to help you navigate the certification process more effectively:
- Balancing Work and Certification Preparation:
- Challenge: Finding time to study and prepare for the certification while managing work responsibilities can be challenging.
- Tip: Create a study schedule and allocate dedicated time each day or week for exam preparation. Prioritize your tasks and eliminate non-essential activities to create more study time. Seek support from your supervisor or team to ensure you have adequate time to focus on certification preparation.
- Grasping Complex Statistical Concepts:
- Challenge: Understanding statistical concepts and tools used in Six Sigma can be challenging, especially for those without a strong background in statistics.
- Tip: Take advantage of training programs or online resources that provide clear explanations and examples of statistical concepts. Break down complex concepts into smaller, more manageable parts. Practice applying statistical tools using real-life examples to reinforce your understanding. Seek assistance from trainers or mentors if you need additional guidance.
- Applying Six Sigma Principles in Real-World Projects:
- Challenge: Translating theoretical knowledge into practical application during process improvement projects can be challenging, particularly for beginners.
- Tip: Look for opportunities to apply Six Sigma principles in your work environment. Seek guidance from experienced Six Sigma practitioners or mentors who can provide insights and feedback on project work. Collaborate with colleagues to gain different perspectives and learn from their experiences. Consider taking on smaller-scale improvement projects to gain hands-on experience before tackling larger initiatives.
- Managing Resistance to Change:
- Challenge: Implementing process improvements often faces resistance from team members or stakeholders who may be resistant to change.
- Tip: Develop effective change management skills. Communicate the benefits of the proposed changes and involve stakeholders early in the process to gain their support. Address concerns and provide regular updates to keep everyone informed and engaged. Demonstrate the value of the improvements through data and measurable results.
- Balancing Theory and Practice:
- Challenge: Striking a balance between learning theoretical concepts and applying them practically can be challenging for Green Belt candidates.
- Tip: Seek out opportunities to apply Six Sigma tools and methodologies in real-life scenarios, either through projects at work or by participating in simulation exercises during your training. Reflect on the practical application of the concepts you learn during your certification journey to reinforce your understanding.
- Staying Motivated Throughout the Certification Process:
- Challenge: Maintaining motivation and focus during the certification process, especially when faced with setbacks or challenges, can be demanding.
- Tip: Set clear goals and visualize the benefits of achieving the Green Belt certification. Break down the certification process into smaller milestones to track your progress and celebrate your achievements along the way. Stay connected with a study group or a mentor who can provide encouragement and support. Remind yourself of the long-term career benefits and personal growth that the certification will bring.
- Exam Preparation:
- Challenge: Preparing for the Green Belt certification exam can be overwhelming, given the breadth of topics covered.
- Tip: Familiarize yourself with the exam format and content by reviewing sample questions and studying the recommended reference materials. Create a study plan and allocate sufficient time to review each topic. Practice solving exam-like questions to build your confidence and identify areas for improvement. Consider joining study groups or online forums to exchange knowledge and resources with fellow candidates.
Continuing Education and Advancement:
Obtaining a Six Sigma Green Belt certification is just the beginning of your journey in process improvement and quality management. To further advance your career and stay current in the field, it is essential to prioritize continuing education and professional development. Here are some avenues for continuing education and advancement:
- Pursue Advanced Six Sigma Certifications:
- Consider advancing to higher levels of Six Sigma certification, such as Six Sigma Black Belt or Master Black Belt. These certifications delve deeper into advanced statistical analysis, project management, and leadership skills. They open doors to more senior roles and provide opportunities to lead larger-scale improvement projects and mentor other Six Sigma practitioners.
- Attend Advanced Training Courses:
- Participate in advanced Six Sigma training courses that focus on specific methodologies, tools, or industries. These courses deepen your knowledge in specialized areas and expand your skill set. Examples include Lean Six Sigma, Design for Six Sigma (DFSS), or industry-specific applications of Six Sigma.
- Engage in Professional Associations and Networks:
- Join professional associations related to process improvement and quality management, such as the American Society for Quality (ASQ) or the International Association for Six Sigma Certification (IASSC). Engage in their events, conferences, and webinars to stay updated on the latest trends, practices, and research in the field. Networking with other professionals allows you to exchange ideas, gain insights, and build valuable connections.
- Continuous Learning:
- Stay updated on industry best practices, emerging technologies, and advancements in process improvement methodologies. Regularly read industry publications, books, and research articles. Follow reputable blogs and websites that focus on Six Sigma and quality management. Continuous learning keeps you informed about the latest developments and helps you adapt to changing business environments.
- Apply Six Sigma in Different Contexts:
- Look for opportunities to apply Six Sigma principles and tools in various contexts within your organization. Seek out projects that involve different departments, processes, or business units. This broadens your experience and allows you to gain a deeper understanding of how Six Sigma can be applied in diverse settings.
- Seek Mentoring and Coaching:
- Connect with experienced Six Sigma professionals who can mentor and guide you in your career development. Mentors can provide valuable insights, share their experiences, and offer advice on overcoming challenges. They can also help you set goals and provide feedback on your progress.
- Specialize in Additional Quality Management Methodologies:
- Expand your knowledge beyond Six Sigma by exploring other quality management methodologies such as Total Quality Management (TQM), Kaizen, or Lean principles. These methodologies complement Six Sigma and provide additional tools and perspectives for process improvement.
- Pursue Academic Degrees or Certificates:
- Consider pursuing academic degrees or certificates in areas related to process improvement, quality management, or operations management. Advanced degrees, such as a Master's in Business Administration (MBA) with a focus on operations or quality, can enhance your qualifications and open doors to higher-level positions.
- Contribute to the Six Sigma Community:
- Share your knowledge and experiences with others by writing articles, publishing case studies, or presenting at industry conferences. Contributing to the Six Sigma community helps build your reputation as a thought leader and expands your professional network.
How to obtain the Six Sigma Green Belt certification?
We are an Education Technology company providing certification training courses to accelerate careers of working professionals worldwide. We impart training through instructor-led classroom workshops, instructor-led live virtual training sessions, and self-paced e-learning courses.
We have successfully conducted training sessions in 108 countries across the globe and enabled thousands of working professionals to enhance the scope of their careers.
Our enterprise training portfolio includes in-demand and globally recognized certification training courses in Project Management, Quality Management, Business Analysis, IT Service Management, Agile and Scrum, Cyber Security, Data Science, and Emerging Technologies. Download our Enterprise Training Catalog from https://www.icertglobal.com/corporate-training-for-enterprises.php
Popular Courses include:
- Project Management: PMP, CAPM ,PMI RMP
- Quality Management: Six Sigma Green Belt ,Lean Six Sigma Yellow Belt, Lean Six Sigma Black Belt
- Business Analysis: CBAP, CCBA, ECBA
- Agile Training: PMI-ACP
- Scrum Training: CSM
- DevOps
- Program Management: PgMP
- IT Service Management & Governance: COBIT, ISO
Conclusion
In conclusion, Six Sigma Green Belt certification offers a pathway to professional growth and advancement in the field of process improvement and quality management. Throughout this blog, we have explored various aspects of Green Belt certification, including an introduction to Six Sigma, certification levels, roles and responsibilities, skills and knowledge requirements, the certification process, career benefits, challenges, and tips, as well as continuing education and advancement opportunities.
By obtaining a Green Belt certification, individuals gain a solid foundation in Six Sigma principles, methodologies, tools, and techniques. This certification enhances their employability, expands career opportunities, and increases earning potential. Green Belt certification holders are equipped with the skills to lead process improvement projects, contribute to organizational success, and drive positive change within their organizations.
However, the journey to Green Belt certification may come with challenges. Balancing work and certification preparation, grasping complex statistical concepts, applying Six Sigma principles practically, managing resistance to change, and staying motivated throughout the process are common hurdles. To overcome these challenges, it is crucial to develop effective study schedules, seek support from mentors or colleagues, break down complex concepts into manageable parts, and apply Six Sigma principles in real-world scenarios.
Continuing education and professional development are essential for long-term success in the field. Pursuing advanced certifications, attending training courses, engaging in professional associations and networks, continuous learning, seeking mentoring and coaching, specializing in other quality management methodologies, pursuing academic degrees or certificates, and contributing to the Six Sigma community are all avenues for growth and advancement.
In summary, Six Sigma Green Belt certification is a valuable asset that validates your expertise in process improvement and quality management. It opens doors to new career opportunities, enables you to make a positive impact within your organization, and sets the stage for further professional development. By embracing the principles of Six Sigma and continuously investing in your knowledge and skills, you can chart a successful career path in process improvement and quality management.
Software Quality Assurance:Ensuring Reliability &Performance
Software Quality Assurance
Quality assurance is one of the most important aspects of any software development project. But you might be skeptical about how important it is to have a QA team for your assignments because you think there are too many other things on your plate. Moreover, it would add more work to your team, which could cause you sleepless nights. Well, it's time to stop with all this thinking and start with proper planning for software testing to ensure that each of your projects will be delivered as expected by its customers/users.
Software QA professionals face a constantly changing landscape, making their job difficult because many products are never released. Still, QA professionals must remain persistent and take risks that can lead to failure. Still, they must never forget what matters: satisfying customers!
What is Software Quality Assurance?
Software quality assurance (SQA) is a process that helps to ensure the correctness, reliability, usability, and maintainability of software. If a program works correctly, the user will experience a satisfaction. If it does not work correctly, users will experience frustration. The process includes several activities: planning, analysis, design, testing, and documentation.
Software must be constructed so that it can be used by people who are not technical experts to operate it. This requires that the software be designed to be easy to use and understand. In addition, it must run on various platforms and systems. Finally, it must also be able to function as expected when all these factors are considered.
The goal of SQA is to make sure that your products meet their customers' expectations. This can be done in several ways:
- By ensuring that the requirements are understood and well-defined by all involved parties, including you and your stakeholders.
- By ensuring that there are no errors or omissions in the code.
- By performing regression testing to detect any new bugs that may have been introduced over time.
- Testing with real users and discovering if they have any concerns about your product.
Software Quality Assurance Importance
Quality assurance is an essential part of any software development process. In software development, quality assurance is the process of ensuring that a product meets its specified requirements. It involves many aspects, including testing, documentation and documentation review, regression testing, and others.
When developing a software product, it's not just about creating something that works - it's also about testing it to ensure it works properly. This requires you to test how well the software works, how well it performs under various conditions, and how robust it is against unexpected errors or bugs.
There are three main quality assurance tests: unit tests (end-to-end tests), integration tests, and system tests.
Unit tests check that each component works as expected.
Integration tests check whether multiple components work together correctly.
System tests check if all components work together as expected in a real-world scenario.
Software Quality Assurance Plan
A software quality assurance plan (SQAP) is a statement of how an organization ensures that its software product or system meets applicable standards. An SQAP should be developed for each product or system being developed, maintained, and operated.
The purpose of an SQAP is to provide clear direction on what needs to be done to ensure that the end product or system conforms to applicable standards. The plan documents and defines the roles and responsibilities of all parties involved in developing and implementing the program. The SQAP also describes the types of evidence required for meeting compliance requirements and maintenance activities necessary to maintain compliance.
The primary purpose of an SQAP is to provide direction on what needs to be done to ensure that products or systems meet applicable standards. An SQAP is a document that describes how an organization ensures that its products or systems meet applicable standards through testing processes, audits, reviews, and other means.
How Professionals Implement SAQ
Software quality assurance professionals implement software quality assurance processes to ensure the software quality produced by a software development organization. They evaluate, improve and extend the quality of software. They also help ensure that the requirements are met during the development process.
The role of a software quality assurance professional is to verify that a product meets its specifications and requirements before it is released to customers. This process includes reviewing documents such as test plans and cases to ensure they match the conditions. They may also check code for defects and fix them if necessary.
Software quality assurance professionals should know all phases of software development, including requirements gathering, design, coding, testing, and maintenance. This process is implemented through various methods, including testing, debugging, and documentation.
Software quality assurance involves the following steps:
First, identifying defects in software products using tests.
Analyzing data collected from tests to identify patterns that indicate the presence of defects.
Fixing defects identified by data analysis.
Documenting any changes made to the software during testing or after completion of testing.
Conclusion
Software quality assurance is, at its most basic level, a job that involves keeping an eye on the creation, modification, and usage of the software. There are many ways to accomplish this task from a structural standpoint. One way to ensure the quality of the software is by creating a software test plan. This is the first step in ensuring things work out for the best of your project. A comprehensive test plan can protect against pitfalls resulting from inferior code or poor development processes.
Without QA, the software risks not being fit for purpose and, therefore, not meeting the requirements. QA must test software and expose flaws so they can be corrected. The tests are created based on Test Requirements derived from the User Story or Feature Description. Tests must cover all of the specified features. Without comprehensive coverage, bugs will likely be missed resulting in poor-quality software. Setting up the environment for automated testing is a complex process. To support deployment, it requires a significant amount of stakeholder engagement to agree on the testing approach, test cases, and acceptance criteria.
Read More
Software Quality Assurance
Quality assurance is one of the most important aspects of any software development project. But you might be skeptical about how important it is to have a QA team for your assignments because you think there are too many other things on your plate. Moreover, it would add more work to your team, which could cause you sleepless nights. Well, it's time to stop with all this thinking and start with proper planning for software testing to ensure that each of your projects will be delivered as expected by its customers/users.
Software QA professionals face a constantly changing landscape, making their job difficult because many products are never released. Still, QA professionals must remain persistent and take risks that can lead to failure. Still, they must never forget what matters: satisfying customers!
What is Software Quality Assurance?
Software quality assurance (SQA) is a process that helps to ensure the correctness, reliability, usability, and maintainability of software. If a program works correctly, the user will experience a satisfaction. If it does not work correctly, users will experience frustration. The process includes several activities: planning, analysis, design, testing, and documentation.
Software must be constructed so that it can be used by people who are not technical experts to operate it. This requires that the software be designed to be easy to use and understand. In addition, it must run on various platforms and systems. Finally, it must also be able to function as expected when all these factors are considered.
The goal of SQA is to make sure that your products meet their customers' expectations. This can be done in several ways:
- By ensuring that the requirements are understood and well-defined by all involved parties, including you and your stakeholders.
- By ensuring that there are no errors or omissions in the code.
- By performing regression testing to detect any new bugs that may have been introduced over time.
- Testing with real users and discovering if they have any concerns about your product.
Software Quality Assurance Importance
Quality assurance is an essential part of any software development process. In software development, quality assurance is the process of ensuring that a product meets its specified requirements. It involves many aspects, including testing, documentation and documentation review, regression testing, and others.
When developing a software product, it's not just about creating something that works - it's also about testing it to ensure it works properly. This requires you to test how well the software works, how well it performs under various conditions, and how robust it is against unexpected errors or bugs.
There are three main quality assurance tests: unit tests (end-to-end tests), integration tests, and system tests.
Unit tests check that each component works as expected.
Integration tests check whether multiple components work together correctly.
System tests check if all components work together as expected in a real-world scenario.
Software Quality Assurance Plan
A software quality assurance plan (SQAP) is a statement of how an organization ensures that its software product or system meets applicable standards. An SQAP should be developed for each product or system being developed, maintained, and operated.
The purpose of an SQAP is to provide clear direction on what needs to be done to ensure that the end product or system conforms to applicable standards. The plan documents and defines the roles and responsibilities of all parties involved in developing and implementing the program. The SQAP also describes the types of evidence required for meeting compliance requirements and maintenance activities necessary to maintain compliance.
The primary purpose of an SQAP is to provide direction on what needs to be done to ensure that products or systems meet applicable standards. An SQAP is a document that describes how an organization ensures that its products or systems meet applicable standards through testing processes, audits, reviews, and other means.
How Professionals Implement SAQ
Software quality assurance professionals implement software quality assurance processes to ensure the software quality produced by a software development organization. They evaluate, improve and extend the quality of software. They also help ensure that the requirements are met during the development process.
The role of a software quality assurance professional is to verify that a product meets its specifications and requirements before it is released to customers. This process includes reviewing documents such as test plans and cases to ensure they match the conditions. They may also check code for defects and fix them if necessary.
Software quality assurance professionals should know all phases of software development, including requirements gathering, design, coding, testing, and maintenance. This process is implemented through various methods, including testing, debugging, and documentation.
Software quality assurance involves the following steps:
First, identifying defects in software products using tests.
Analyzing data collected from tests to identify patterns that indicate the presence of defects.
Fixing defects identified by data analysis.
Documenting any changes made to the software during testing or after completion of testing.
Conclusion
Software quality assurance is, at its most basic level, a job that involves keeping an eye on the creation, modification, and usage of the software. There are many ways to accomplish this task from a structural standpoint. One way to ensure the quality of the software is by creating a software test plan. This is the first step in ensuring things work out for the best of your project. A comprehensive test plan can protect against pitfalls resulting from inferior code or poor development processes.
Without QA, the software risks not being fit for purpose and, therefore, not meeting the requirements. QA must test software and expose flaws so they can be corrected. The tests are created based on Test Requirements derived from the User Story or Feature Description. Tests must cover all of the specified features. Without comprehensive coverage, bugs will likely be missed resulting in poor-quality software. Setting up the environment for automated testing is a complex process. To support deployment, it requires a significant amount of stakeholder engagement to agree on the testing approach, test cases, and acceptance criteria.
Quality Improvement in Six Sigma: Consistency & Excellence
Quality Improvement in Six Sigma
Quality improvement is a key component of Six Sigma. It's a continuous process designed to produce more consistent and reliable results, ultimately leading to higher customer satisfaction.
Quality improvement is integral to Six Sigma because it helps organizations identify problems before they become significant. The goal is to eliminate or reduce defects per million opportunities (DPMO).
There are six steps in the quality improvement process:
First, define the problem: Determine what needs fixing by understanding why customers aren't satisfied with your product or service.
Measure performance: Set up metrics to track key performance indicators (KPIs) such as repeat purchases, customer complaints, and returns.
Analyze data: Look at your KPIs to see if there are any patterns or trends you can use to improve your product or service.
Define the solution: Develop ideas for making changes based on your analysis so you can fix specific problems related to DPMO.
Implement improvements: Create new processes or systems for implementing change throughout the organization so everyone works toward the same goal — reducing errors and improving customer satisfaction.
Evaluate results: Monitor all improvements closely after implementation to ensure they achieve their desired outcomes.
Importance of Quality Improvement
Quality improvement is an essential part of the Six Sigma methodology. It is the area of a company where employees are responsible for improving the quality of the product or service. It involves continuous improvement in all parts of a business, from manufacturing to sales, customer service, and administration. Quality improvement is a constant process and not a one-time event. Therefore, it has to be managed continuously throughout the organization.
The most important aspect of quality improvement is quality standardization. Quality standards help in identifying defects and creating a quality management system.
Quality improvement is an activity that focuses on improving products or services, processes, or customer satisfaction by identifying areas for improvement, implementing solutions, and monitoring results. Quality improvement activities may include:
Identification of problems: Identifying problems with the current state of affairs, considering the reasons behind them, and determining their effects on customers or internal operations
Possible solutions: Developing plans for dealing with problems, such as introducing new products, changing policies or procedures, enhancing training programs or employee performance evaluations
Implementation: Implementing solutions through action plans that address identified problems within specific time frames (typically 6-9 months)
Monitoring results: Evaluating whether changes made have improved performance and whether they lead to customer satisfaction.
Six Sigma Methodology
Six Sigma uses DMAIC methodologies to achieve its goals, which stand for:
Define: The first step in DMAIC is to define the problem or opportunity that needs to be addressed. This can be done through brainstorming or other techniques.
Measure: Once the problem has been defined, it needs to be measured to make improvements. This step requires collecting data on key factors related to the improved process and analyzing it using statistical techniques such as regression analysis and ANOVA (analysis of variance).
Analyze: After measuring the process, you should analyze your data using statistical techniques like regression analysis and ANOVA (analysis of variance). These techniques allow you to determine whether your measurements are within acceptable limits or if any patterns in them may help with future improvements.
Improve: This step includes developing new processes or improving existing ones by identifying opportunities for improvement through brainstorming sessions with employees from all levels of the organization.
Control: In the final phase of Six Sigma, you create a control plan, a set of procedures that ensures your new standardized process works smoothly and meets quality standards.
Benefits of Quality Improvement
Quality management has been a significant focus for Six Sigma for many years. This is not surprising because quality is the basis of all business activity and, in particular, customer satisfaction. As a result, quality improvement has become a central tenet of Six Sigma's philosophy.
The benefits of quality improvement include:
Reduced costs: Reductions in product defects and errors lead to reduced production costs. This is particularly significant in the case of products where quality control costs can be very high.
Improved customer satisfaction: Improved product quality leads to improved customer satisfaction, measured using customer surveys or other electronic commerce (e-commerce) techniques.
Increased market share: Improved product quality ensures more customers are satisfied with their purchases, which increases the company's market share.
Increased Productivity: Productivity increases when employees can perform their duties efficiently and correctly without making mistakes, leading to fewer rework activities and reduced costs associated with correcting errors.
Improved Quality: Six sigma provides organizations with a way to improve their processes. This will result in more satisfying customers who will give positive feedback to the organization.
Increased employee job satisfaction: It improves employee morale because employees are happier knowing they are helping their company achieve its goals.
Once you put a Six Sigma quality improvement plan into action, you will see how much of an impact it can have on your company's work. So don't wait—start today!
Read More
Quality Improvement in Six Sigma
Quality improvement is a key component of Six Sigma. It's a continuous process designed to produce more consistent and reliable results, ultimately leading to higher customer satisfaction.
Quality improvement is integral to Six Sigma because it helps organizations identify problems before they become significant. The goal is to eliminate or reduce defects per million opportunities (DPMO).
There are six steps in the quality improvement process:
First, define the problem: Determine what needs fixing by understanding why customers aren't satisfied with your product or service.
Measure performance: Set up metrics to track key performance indicators (KPIs) such as repeat purchases, customer complaints, and returns.
Analyze data: Look at your KPIs to see if there are any patterns or trends you can use to improve your product or service.
Define the solution: Develop ideas for making changes based on your analysis so you can fix specific problems related to DPMO.
Implement improvements: Create new processes or systems for implementing change throughout the organization so everyone works toward the same goal — reducing errors and improving customer satisfaction.
Evaluate results: Monitor all improvements closely after implementation to ensure they achieve their desired outcomes.
Importance of Quality Improvement
Quality improvement is an essential part of the Six Sigma methodology. It is the area of a company where employees are responsible for improving the quality of the product or service. It involves continuous improvement in all parts of a business, from manufacturing to sales, customer service, and administration. Quality improvement is a constant process and not a one-time event. Therefore, it has to be managed continuously throughout the organization.
The most important aspect of quality improvement is quality standardization. Quality standards help in identifying defects and creating a quality management system.
Quality improvement is an activity that focuses on improving products or services, processes, or customer satisfaction by identifying areas for improvement, implementing solutions, and monitoring results. Quality improvement activities may include:
Identification of problems: Identifying problems with the current state of affairs, considering the reasons behind them, and determining their effects on customers or internal operations
Possible solutions: Developing plans for dealing with problems, such as introducing new products, changing policies or procedures, enhancing training programs or employee performance evaluations
Implementation: Implementing solutions through action plans that address identified problems within specific time frames (typically 6-9 months)
Monitoring results: Evaluating whether changes made have improved performance and whether they lead to customer satisfaction.
Six Sigma Methodology
Six Sigma uses DMAIC methodologies to achieve its goals, which stand for:
Define: The first step in DMAIC is to define the problem or opportunity that needs to be addressed. This can be done through brainstorming or other techniques.
Measure: Once the problem has been defined, it needs to be measured to make improvements. This step requires collecting data on key factors related to the improved process and analyzing it using statistical techniques such as regression analysis and ANOVA (analysis of variance).
Analyze: After measuring the process, you should analyze your data using statistical techniques like regression analysis and ANOVA (analysis of variance). These techniques allow you to determine whether your measurements are within acceptable limits or if any patterns in them may help with future improvements.
Improve: This step includes developing new processes or improving existing ones by identifying opportunities for improvement through brainstorming sessions with employees from all levels of the organization.
Control: In the final phase of Six Sigma, you create a control plan, a set of procedures that ensures your new standardized process works smoothly and meets quality standards.
Benefits of Quality Improvement
Quality management has been a significant focus for Six Sigma for many years. This is not surprising because quality is the basis of all business activity and, in particular, customer satisfaction. As a result, quality improvement has become a central tenet of Six Sigma's philosophy.
The benefits of quality improvement include:
Reduced costs: Reductions in product defects and errors lead to reduced production costs. This is particularly significant in the case of products where quality control costs can be very high.
Improved customer satisfaction: Improved product quality leads to improved customer satisfaction, measured using customer surveys or other electronic commerce (e-commerce) techniques.
Increased market share: Improved product quality ensures more customers are satisfied with their purchases, which increases the company's market share.
Increased Productivity: Productivity increases when employees can perform their duties efficiently and correctly without making mistakes, leading to fewer rework activities and reduced costs associated with correcting errors.
Improved Quality: Six sigma provides organizations with a way to improve their processes. This will result in more satisfying customers who will give positive feedback to the organization.
Increased employee job satisfaction: It improves employee morale because employees are happier knowing they are helping their company achieve its goals.
Once you put a Six Sigma quality improvement plan into action, you will see how much of an impact it can have on your company's work. So don't wait—start today!
Quality Assurance vs Quality Management: Key Similarities
Quality Assurance vs Quality Management - Similarities & Differences
Quality assurance and quality management are terms that are often heard but not well understood. Sometimes they refer to the same thing, but at other times they might mean different things.
In order to prevent themselves from falling deeper into the confusion surrounding these two terms, many business owners have turned to online resources to learn about their differences.
Quality assurance vs Quality management
The primary difference between quality management and quality assurance is the scale of their operations:
Quality management applies to an entire organization or department. For example, it can describe how a whole company manages its customer service or how a software development team works its coding standards.
Quality assurance applies to specific functions within an organization or department. For example, it can describe how an engineering team ensures that new products meet technical requirements before they are released into production.
What is Quality Assurance?
Quality assurance (QA) is the part of quality control focused on fulfilling quality requirements. Its purpose is to ensure that a product or service is of the desired quality and satisfies given customer requirements. There are three types of QA processes:
Pre-production QA: Ensuring that all processes, documentation, tools, and resources are in place for an effective start of production.
Production QA: Monitoring the production process to ensure that products conform to requirements.
Post-production QA: Checking the finished product against specifications, standards, and regulatory requirements.
The main goals of quality assurance are:
- To ensure that the quality of your products or services meets your customers' needs and expectations.
- To reduce the number of defects in your products or services.
- To improve the efficiency and effectiveness of your product or service development process.
Benefits of Quality Assurance
The main benefit of quality assurance is that it helps to ensure that your product is delivered as expected. In addition, quality assurance ensures that the final product matches the requirements in the engineering specifications.
Quality assurance can also help to eliminate waste and errors, which would otherwise be expensive to correct in production. For example, suppose a supplier fails to deliver on time or produces an inferior product. In that case, this can lead to delays in production and may ultimately cause you to lose customers.
Another benefit of quality assurance is that it helps you to identify any potential issues with your product before they become an issue for your customers. This prevents customers from getting dissatisfied with their purchases because they are not working correctly or have other defects.
Quality assurance also helps businesses improve their processes and make them more efficient at delivering high-quality products or services.
The most significant benefit of quality assurance is that it improves customer satisfaction with your service or product. If you want happy customers, then there are few things better than ensuring they get exactly what they expect when they buy something from you!
Why Quality Assurance?
The purpose of QA is to ensure that all the processes involved in the production or delivery of goods or services are done correctly to achieve the desired standard or goal. The show involves many functions, such as purchasing materials, inventory management, designing products/services, etc., which need proper planning and execution to achieve good results.
What is Quality Management?
Quality management is a process that ensures the products and services that a company provides meet customer requirements. It involves measuring the quality of products and services, identifying where improvements are needed, and implementing solutions to improve quality.
Quality management is an ongoing process that includes planning, organizing, directing, and controlling activities to ensure that the methods used in creating products or services meet customer requirements.
The goal of quality management is to provide consistent product quality at all levels of production.
In addition, it seeks to continuously improve the processes used to create products or deliver services by identifying problems early in the production cycle to correct them before they become significant problems.
Benefits of Quality Management
The benefits of quality management are many. Quality management is not only beneficial to the overall health of an organization, but it can also improve its financial status. In addition, quality management provides several benefits for businesses, including:
Reduced costs: Companies implementing quality management systems often find that they save money in the long run. This is because they can identify problems early on and fix them before they become too expensive to fix. By catching issues before they become significant, companies can avoid paying for costly repairs or replacements later.
Increased productivity: A sound quality management system can help businesses increase their productivity by reducing errors and preventing defects in the first place. In addition, if a company has a high level of employee satisfaction, this will also lead to increased productivity because satisfied employees tend to be more productive than unhappy ones.
Improved customer service: A company with an effective quality management system will provide better customer service than one without one because it will be able to identify problems quickly and fix them before they become serious issues that upset customers or result in expensive recalls. Since customers expect high service levels these days, any service failure can negatively affect your reputation and bottom line.
Why Quality Management?
Quality management ensures that businesses continually assess their performance and make necessary improvements. By focusing on continuous improvement rather than perfection, companies can avoid investing too much time, money and effort into getting something right from scratch before moving on to something else. This approach also helps them retain their competitive edge in a fast-changing environment.
Conclusion
Hopefully, the above definitions and explanations have cleared up any questions you might have had about quality assurance and quality management. The two concepts are closely related but are not entirely the same.
Quality management focuses more on the broader picture, while quality assurance is more hands-on. Quality management is also organizational, while quality assurance is more often individualized. The takeaway here? Quality management refers to an overall system or framework to ensure high-quality standards. In contrast, quality assurance relates to the personal actions involved in providing those standards are met.
Read More
Quality Assurance vs Quality Management - Similarities & Differences
Quality assurance and quality management are terms that are often heard but not well understood. Sometimes they refer to the same thing, but at other times they might mean different things.
In order to prevent themselves from falling deeper into the confusion surrounding these two terms, many business owners have turned to online resources to learn about their differences.
Quality assurance vs Quality management
The primary difference between quality management and quality assurance is the scale of their operations:
Quality management applies to an entire organization or department. For example, it can describe how a whole company manages its customer service or how a software development team works its coding standards.
Quality assurance applies to specific functions within an organization or department. For example, it can describe how an engineering team ensures that new products meet technical requirements before they are released into production.
What is Quality Assurance?
Quality assurance (QA) is the part of quality control focused on fulfilling quality requirements. Its purpose is to ensure that a product or service is of the desired quality and satisfies given customer requirements. There are three types of QA processes:
Pre-production QA: Ensuring that all processes, documentation, tools, and resources are in place for an effective start of production.
Production QA: Monitoring the production process to ensure that products conform to requirements.
Post-production QA: Checking the finished product against specifications, standards, and regulatory requirements.
The main goals of quality assurance are:
- To ensure that the quality of your products or services meets your customers' needs and expectations.
- To reduce the number of defects in your products or services.
- To improve the efficiency and effectiveness of your product or service development process.
Benefits of Quality Assurance
The main benefit of quality assurance is that it helps to ensure that your product is delivered as expected. In addition, quality assurance ensures that the final product matches the requirements in the engineering specifications.
Quality assurance can also help to eliminate waste and errors, which would otherwise be expensive to correct in production. For example, suppose a supplier fails to deliver on time or produces an inferior product. In that case, this can lead to delays in production and may ultimately cause you to lose customers.
Another benefit of quality assurance is that it helps you to identify any potential issues with your product before they become an issue for your customers. This prevents customers from getting dissatisfied with their purchases because they are not working correctly or have other defects.
Quality assurance also helps businesses improve their processes and make them more efficient at delivering high-quality products or services.
The most significant benefit of quality assurance is that it improves customer satisfaction with your service or product. If you want happy customers, then there are few things better than ensuring they get exactly what they expect when they buy something from you!
Why Quality Assurance?
The purpose of QA is to ensure that all the processes involved in the production or delivery of goods or services are done correctly to achieve the desired standard or goal. The show involves many functions, such as purchasing materials, inventory management, designing products/services, etc., which need proper planning and execution to achieve good results.
What is Quality Management?
Quality management is a process that ensures the products and services that a company provides meet customer requirements. It involves measuring the quality of products and services, identifying where improvements are needed, and implementing solutions to improve quality.
Quality management is an ongoing process that includes planning, organizing, directing, and controlling activities to ensure that the methods used in creating products or services meet customer requirements.
The goal of quality management is to provide consistent product quality at all levels of production.
In addition, it seeks to continuously improve the processes used to create products or deliver services by identifying problems early in the production cycle to correct them before they become significant problems.
Benefits of Quality Management
The benefits of quality management are many. Quality management is not only beneficial to the overall health of an organization, but it can also improve its financial status. In addition, quality management provides several benefits for businesses, including:
Reduced costs: Companies implementing quality management systems often find that they save money in the long run. This is because they can identify problems early on and fix them before they become too expensive to fix. By catching issues before they become significant, companies can avoid paying for costly repairs or replacements later.
Increased productivity: A sound quality management system can help businesses increase their productivity by reducing errors and preventing defects in the first place. In addition, if a company has a high level of employee satisfaction, this will also lead to increased productivity because satisfied employees tend to be more productive than unhappy ones.
Improved customer service: A company with an effective quality management system will provide better customer service than one without one because it will be able to identify problems quickly and fix them before they become serious issues that upset customers or result in expensive recalls. Since customers expect high service levels these days, any service failure can negatively affect your reputation and bottom line.
Why Quality Management?
Quality management ensures that businesses continually assess their performance and make necessary improvements. By focusing on continuous improvement rather than perfection, companies can avoid investing too much time, money and effort into getting something right from scratch before moving on to something else. This approach also helps them retain their competitive edge in a fast-changing environment.
Conclusion
Hopefully, the above definitions and explanations have cleared up any questions you might have had about quality assurance and quality management. The two concepts are closely related but are not entirely the same.
Quality management focuses more on the broader picture, while quality assurance is more hands-on. Quality management is also organizational, while quality assurance is more often individualized. The takeaway here? Quality management refers to an overall system or framework to ensure high-quality standards. In contrast, quality assurance relates to the personal actions involved in providing those standards are met.
Quality Management: Key PMP Questions to Review and Master.
Quality Management: PMP Questions to Review
Q1. Experienced project managers always tell that accuracy and precision are not the same. Precise measurements may not be accurate and accurate measurements may not be precise. Which of the following statement about precision and accuracy is CORRECT?
- Precision means the values of repeated measurements are clustered and Accuracy means the measured value is close to the actual value
- Accuracy means the degree to which a set of inherent characteristics fulfill requirements and Precision means a category assigned to products or services having the same functional use but different technical characteristics
- Precision means the degree to which a set of inherent characteristics fulfill requirements and Accuracy means a category assigned to products or services having the same functional use but different technical characteristics
- Accuracy means the values of repeated measurements are clustered and Precision means the measured value is close to the actual value
Q2. A project management team came up with certain metrics such as defect frequency, failure rate, availability, and reliability. These are usually defined as an output of what process?
- Manage Quality
- Define Scope
- Plan Quality Management
- Collect Requirements
Q3. Which of these statements is accurate regarding quality management?
- Project requirements are turned into customer needs, wants, and expectations
- Quality and grade are essentially the same
- Modern quality management complements project management
- Overworking the team to meet requirements is not likely to increase attrition and rework
Q4. Which of these tools is NOT a part of the Seven Basic Tools of Quality?
- Scatter Diagram
- Control Chart
- Flowcharting
- Statistical Sampling
Q5. A control chart is used to determine whether or not a process is stable or has predictable performance. When a process is within acceptable limits, the process need not be adjusted. What are the upper and lower control limits usually set as?
- + / – 2 sigma
- + / – 3 sigma
- + / – 1 sigma
- + / – 6 sigma
Q6. A project manager used a control chart to determine whether a process was stable or not, and to determine if its performance was predictable. He determined the upper and lower specification limits based on the contractual requirements. A set of eighteen data points were taken. Of these, 8 consecutive data points were above the mean. What can you say about such a process?
- A process is considered as being within control if less than half the data points are above or below the mean. Hence the process is within control.
- A process is considered as out of control if five consecutive data points are above or below the mean. Hence the process is out of control.
- A process is considered as out of control if seven consecutive data points are above or below the mean. Hence the process is out of control.
- A process is considered as out of control if six consecutive data points are above or below the mean. Hence the process is within control.
Q7. Which quality control technique or tool should be used when trying to determine the cause of a major defect?
- Control Chart
- Fishbone diagram
- Pareto Chart
- Histogram
Q8. The term ____________ indicates the degree to which a particular product or service meets requirements, while ____________ indicates a category or rank used to distinguish that item from other similar items.
- Grade, quality
- Quality, grade
- Quality, standard
- Grade, standard
Q9. You work at a software company that authors Material Safety Data Sheets (MSDS) for chemical companies. Prior to releasing the MSDS to the company you have created a list of items to be reviewed to see that they appear on the document such as: chemical name, CAS#, protection required, what to do an emergency, etc. This is an example of what type of tool?
- Quality Metrics
- Process Improvement Plan
- Quality Management Plan
- Checklist
Q10. The process of auditing the quality requirements and the results from quality control measurements to ensure appropriate quality standards and operational definitions are used is the definition of: _____________
- Scope validation
- Quality planning
- Quality control
- Quality assurance
Q11. A good quality audit should be:
- informal and internal
- structured and independent
- structured and internal
- informal and independent
Q12. In order to keep costs low, a project management team decided to apply statistical sampling while inspecting some of the work products. They decided to select 10 out of 50 engineering drawings for inspection. During which process should the sample frequency and sample size be determined?
- Control Quality
- Collect Requirements
- Plan Quality Management
- Manage Quality
Q13. You are in the execution stage of your project and you have been informed that “corporate” will be sending in a team of consultants to review whether your project activities comply with the company’s and PMI’s policies, standards, and procedures. This is an example of?
- Recommended Corrective Actions
- Organizational Process Assets
- Process Analysis
- Quality Audit
Q14. Select the best answer: Continuous process improvement reduces ___________ and ___________ , which allows processes to operate at increased levels of efficiency and effectiveness.
- Departmental and organization processes
- Process and policy overhead.
- Waste and non-value added activities.
- Cost and scope
Q15. A project manager used a control chart to determine whether a process was stable or not, and to determine if its performance was predictable. He determined the upper and lower specification limits based on the contractual requirements. A set of eighteen data points were taken. Of these, 8 consecutive data points were above the mean. What can you say about such a process?
- A process is considered as out of control if five consecutive data points are above or below the mean. Hence the process is out of control.
- A process is considered as out of control if seven consecutive data points are above or below the mean. Hence the process is out of control.
- A process is considered as out of control if six consecutive data points are above or below the mean. Hence the process is within control.
- A process is considered as being within control if less than half the data points are above or below the mean. Hence the process is within control.
Q16. A team of engineers is reviewing a scatter diagram to determine how the changes in two variables in a new type of automobile tire are related. The closer points on the diagram are to a diagonal line, ______________ .
- the less likely a control group will be required
- the more likely a control group will be required
- the less likely they are to be related
- the more closely they are related
Q17. On a control chart, if six consecutive plot points are above the mean, then what can be established about the process?
- The process is out of control
- Nothing can be established
- The process is in control
- The process will be out of control after plotting the seventh point.
Q18. Which of the following tools would be most appropriate for collecting data to study the symptoms of a problem?
- Checklist
- Histogram
- Check Sheet
- Control Chart
Q19. The cost of scrap rework, in a product quality cost system, is categorized as a:
- Appraisal costs
- External failure costs
- Prevention costs
- Internal failure costs
Q20. The four categories of costs associated with product quality costs are:
- External failure, internal failure, prevention, and inspection
- External failure, internal failure, repair, and appraisal
- Warranty, product liability, training, and appraisal
- External failure, internal failure, prevention, and appraisal
Q21. Which of the following quality costs are failure costs?
- Pre-dispatch inspection costs
- Customer satisfaction survey costs
- Product recall costs
- Equipment calibration costs
Q22. In which of the following control chart the control limits will vary from subgroup to subgroup?
- Xbar-R Chart
- c Chart
- p Chart
- np Chart
Q23. If there are seven data points either above or below the mean, but still within the control limits, what should you do?
- Reinspect the product
- Ignore it and continue to measure the process
- Find the cause because this means that the process is out of control
- Reject the product
Q24. Two variables, x and y, are related. Variable x increases or decreases with y. Which of the following tools could best be used to graphically show this relationship?
- Histogram
- Scatter Plot
- Control Charts
- Control Charts
Q25. Which of these quality gurus introduced the concept of Control Charts?
- Crosby
- Taguchi
- Juran
- Shewhart
Q26. Control Limits are the same are Specifications Limits.
- True
- False
Q27. What does COQ stand for?
- Cost of Quality
- Carry on Quality
- Cost Oriented Quality
- Corporate Quality
Read More
Quality Management: PMP Questions to Review
Q1. Experienced project managers always tell that accuracy and precision are not the same. Precise measurements may not be accurate and accurate measurements may not be precise. Which of the following statement about precision and accuracy is CORRECT?
- Precision means the values of repeated measurements are clustered and Accuracy means the measured value is close to the actual value
- Accuracy means the degree to which a set of inherent characteristics fulfill requirements and Precision means a category assigned to products or services having the same functional use but different technical characteristics
- Precision means the degree to which a set of inherent characteristics fulfill requirements and Accuracy means a category assigned to products or services having the same functional use but different technical characteristics
- Accuracy means the values of repeated measurements are clustered and Precision means the measured value is close to the actual value
Q2. A project management team came up with certain metrics such as defect frequency, failure rate, availability, and reliability. These are usually defined as an output of what process?
- Manage Quality
- Define Scope
- Plan Quality Management
- Collect Requirements
Q3. Which of these statements is accurate regarding quality management?
- Project requirements are turned into customer needs, wants, and expectations
- Quality and grade are essentially the same
- Modern quality management complements project management
- Overworking the team to meet requirements is not likely to increase attrition and rework
Q4. Which of these tools is NOT a part of the Seven Basic Tools of Quality?
- Scatter Diagram
- Control Chart
- Flowcharting
- Statistical Sampling
Q5. A control chart is used to determine whether or not a process is stable or has predictable performance. When a process is within acceptable limits, the process need not be adjusted. What are the upper and lower control limits usually set as?
- + / – 2 sigma
- + / – 3 sigma
- + / – 1 sigma
- + / – 6 sigma
Q6. A project manager used a control chart to determine whether a process was stable or not, and to determine if its performance was predictable. He determined the upper and lower specification limits based on the contractual requirements. A set of eighteen data points were taken. Of these, 8 consecutive data points were above the mean. What can you say about such a process?
- A process is considered as being within control if less than half the data points are above or below the mean. Hence the process is within control.
- A process is considered as out of control if five consecutive data points are above or below the mean. Hence the process is out of control.
- A process is considered as out of control if seven consecutive data points are above or below the mean. Hence the process is out of control.
- A process is considered as out of control if six consecutive data points are above or below the mean. Hence the process is within control.
Q7. Which quality control technique or tool should be used when trying to determine the cause of a major defect?
- Control Chart
- Fishbone diagram
- Pareto Chart
- Histogram
Q8. The term ____________ indicates the degree to which a particular product or service meets requirements, while ____________ indicates a category or rank used to distinguish that item from other similar items.
- Grade, quality
- Quality, grade
- Quality, standard
- Grade, standard
Q9. You work at a software company that authors Material Safety Data Sheets (MSDS) for chemical companies. Prior to releasing the MSDS to the company you have created a list of items to be reviewed to see that they appear on the document such as: chemical name, CAS#, protection required, what to do an emergency, etc. This is an example of what type of tool?
- Quality Metrics
- Process Improvement Plan
- Quality Management Plan
- Checklist
Q10. The process of auditing the quality requirements and the results from quality control measurements to ensure appropriate quality standards and operational definitions are used is the definition of: _____________
- Scope validation
- Quality planning
- Quality control
- Quality assurance
Q11. A good quality audit should be:
- informal and internal
- structured and independent
- structured and internal
- informal and independent
Q12. In order to keep costs low, a project management team decided to apply statistical sampling while inspecting some of the work products. They decided to select 10 out of 50 engineering drawings for inspection. During which process should the sample frequency and sample size be determined?
- Control Quality
- Collect Requirements
- Plan Quality Management
- Manage Quality
Q13. You are in the execution stage of your project and you have been informed that “corporate” will be sending in a team of consultants to review whether your project activities comply with the company’s and PMI’s policies, standards, and procedures. This is an example of?
- Recommended Corrective Actions
- Organizational Process Assets
- Process Analysis
- Quality Audit
Q14. Select the best answer: Continuous process improvement reduces ___________ and ___________ , which allows processes to operate at increased levels of efficiency and effectiveness.
- Departmental and organization processes
- Process and policy overhead.
- Waste and non-value added activities.
- Cost and scope
Q15. A project manager used a control chart to determine whether a process was stable or not, and to determine if its performance was predictable. He determined the upper and lower specification limits based on the contractual requirements. A set of eighteen data points were taken. Of these, 8 consecutive data points were above the mean. What can you say about such a process?
- A process is considered as out of control if five consecutive data points are above or below the mean. Hence the process is out of control.
- A process is considered as out of control if seven consecutive data points are above or below the mean. Hence the process is out of control.
- A process is considered as out of control if six consecutive data points are above or below the mean. Hence the process is within control.
- A process is considered as being within control if less than half the data points are above or below the mean. Hence the process is within control.
Q16. A team of engineers is reviewing a scatter diagram to determine how the changes in two variables in a new type of automobile tire are related. The closer points on the diagram are to a diagonal line, ______________ .
- the less likely a control group will be required
- the more likely a control group will be required
- the less likely they are to be related
- the more closely they are related
Q17. On a control chart, if six consecutive plot points are above the mean, then what can be established about the process?
- The process is out of control
- Nothing can be established
- The process is in control
- The process will be out of control after plotting the seventh point.
Q18. Which of the following tools would be most appropriate for collecting data to study the symptoms of a problem?
- Checklist
- Histogram
- Check Sheet
- Control Chart
Q19. The cost of scrap rework, in a product quality cost system, is categorized as a:
- Appraisal costs
- External failure costs
- Prevention costs
- Internal failure costs
Q20. The four categories of costs associated with product quality costs are:
- External failure, internal failure, prevention, and inspection
- External failure, internal failure, repair, and appraisal
- Warranty, product liability, training, and appraisal
- External failure, internal failure, prevention, and appraisal
Q21. Which of the following quality costs are failure costs?
- Pre-dispatch inspection costs
- Customer satisfaction survey costs
- Product recall costs
- Equipment calibration costs
Q22. In which of the following control chart the control limits will vary from subgroup to subgroup?
- Xbar-R Chart
- c Chart
- p Chart
- np Chart
Q23. If there are seven data points either above or below the mean, but still within the control limits, what should you do?
- Reinspect the product
- Ignore it and continue to measure the process
- Find the cause because this means that the process is out of control
- Reject the product
Q24. Two variables, x and y, are related. Variable x increases or decreases with y. Which of the following tools could best be used to graphically show this relationship?
- Histogram
- Scatter Plot
- Control Charts
- Control Charts
Q25. Which of these quality gurus introduced the concept of Control Charts?
- Crosby
- Taguchi
- Juran
- Shewhart
Q26. Control Limits are the same are Specifications Limits.
- True
- False
Q27. What does COQ stand for?
- Cost of Quality
- Carry on Quality
- Cost Oriented Quality
- Corporate Quality
Cost of Quality: Essential PMP Topics to Master for the Exam
Cost of Quality: PMP Topics to Learn for the Exam
Cost of Quality
The Cost of Quality is an essential topic for the PMP exam. The Cost of Quality is a management accounting concept that can help you measure the cost of defects or poor quality in your project, product, or service. This information can improve quality and reduce costs in future projects.
The PMBOK® Guide defines the Cost of Quality as: "The cost required by a company to prevent poor quality and implement good quality in products, services, and processes."
You can calculate the cost of poor quality using two approaches: Cost of Conformance and Cost of Non-Conformance.
Cost of Conformance
These are the costs incurred when a product, service, or process does not meet specifications. This may include costs for rework and the use of defective materials. The Cost of Conformance is made up of Preventions costs and Appraisal costs.
Prevention Costs
Prevention is the most effective means of preventing defects. These costs include all those incurred for activities specifically designed to avoid poor product quality from happening in the first place. Preventing mistakes is much less costly than fixing them after they have been made. For example, organizations use statistical process control (SPC), Quality engineering, training, and more advanced techniques like Lean Manufacturing or Six Sigma to help prevent defects from occurring in the first place.
Appraisal Costs
Appraisal costs are also referred to as inspection costs. These costs encompass the cost of inspecting a product before it is shipped to customers. In most cases, an appraisal does not prevent defects from occurring but instead identifies these defects before the customer receives their order. Therefore, appraisal activities should be performed by employees responsible for quality control and designing defect-free products from the beginning.
Cost of Non-Conformance
These are the costs incurred when a product, service, or process does not meet customer requirements. These may include lost sales and customer dissatisfaction due to product or service errors. The cost of non-conformance is made up of internal and external failure costs.
Internal Failure Costs
Internal failure costs result from identifying defects before they are shipped to customers. If flaws are detected internally, it is more likely that the organization will be able to correct them before they are sent to customers. This leads to a reduction in the external failure costs that arise from the production of defective units.
External Failure Costs
A company incurs external failure costs when delivering damaged or defective products to the end customer. These costs include warranty, repairs, and replacements, product recalls, liabilities arising from legal action against a company, and lost sales stemming from a reputation for poor quality. They are not included in an income statement, but they can have an adverse impact on it.
If you haven't already started studying for the PMP exam, consider reading through this infographic to help guide your studies. Please start with the fundamentals and work your way up to more complicated topics as you become familiar with them. The goal here is not just to give you a list of issues but to help you learn methodically from the ground up.
Read More
Cost of Quality: PMP Topics to Learn for the Exam
Cost of Quality
The Cost of Quality is an essential topic for the PMP exam. The Cost of Quality is a management accounting concept that can help you measure the cost of defects or poor quality in your project, product, or service. This information can improve quality and reduce costs in future projects.
The PMBOK® Guide defines the Cost of Quality as: "The cost required by a company to prevent poor quality and implement good quality in products, services, and processes."
You can calculate the cost of poor quality using two approaches: Cost of Conformance and Cost of Non-Conformance.
Cost of Conformance
These are the costs incurred when a product, service, or process does not meet specifications. This may include costs for rework and the use of defective materials. The Cost of Conformance is made up of Preventions costs and Appraisal costs.
Prevention Costs
Prevention is the most effective means of preventing defects. These costs include all those incurred for activities specifically designed to avoid poor product quality from happening in the first place. Preventing mistakes is much less costly than fixing them after they have been made. For example, organizations use statistical process control (SPC), Quality engineering, training, and more advanced techniques like Lean Manufacturing or Six Sigma to help prevent defects from occurring in the first place.
Appraisal Costs
Appraisal costs are also referred to as inspection costs. These costs encompass the cost of inspecting a product before it is shipped to customers. In most cases, an appraisal does not prevent defects from occurring but instead identifies these defects before the customer receives their order. Therefore, appraisal activities should be performed by employees responsible for quality control and designing defect-free products from the beginning.
Cost of Non-Conformance
These are the costs incurred when a product, service, or process does not meet customer requirements. These may include lost sales and customer dissatisfaction due to product or service errors. The cost of non-conformance is made up of internal and external failure costs.
Internal Failure Costs
Internal failure costs result from identifying defects before they are shipped to customers. If flaws are detected internally, it is more likely that the organization will be able to correct them before they are sent to customers. This leads to a reduction in the external failure costs that arise from the production of defective units.
External Failure Costs
A company incurs external failure costs when delivering damaged or defective products to the end customer. These costs include warranty, repairs, and replacements, product recalls, liabilities arising from legal action against a company, and lost sales stemming from a reputation for poor quality. They are not included in an income statement, but they can have an adverse impact on it.
If you haven't already started studying for the PMP exam, consider reading through this infographic to help guide your studies. Please start with the fundamentals and work your way up to more complicated topics as you become familiar with them. The goal here is not just to give you a list of issues but to help you learn methodically from the ground up.
Project Quality Management: Cost of Quality - Quick Guide!
Project Quality Management: Cost of Quality
Cost of quality is a significant concept in the project quality management knowledge area. However, it's also misinterpreted by several PMP credential exam-takers. A strong understanding of this concept can help increase a participant's score as there're very few questions on the exam based on it.
Let's take a quick and profound journey into the cost of quality concept.
If a product meets/exceeds its design features and is null-defect, it's said to have a top-notch conformance quality. So, for example, if a steel watch has zero defects, it can have a high conformance quality as a zero-defect diamond-studded watch. The steel one may not be attractive or expensive as the diamond, but you can expect it to be free of defects.
The prevention, identification, and handling of defects incur costs of quality. The term indicates total costs incurred to prevent product defects or costs that result from product defects.
Quality costs don't just relate to manufacturing but all the tasks from research and development (R&D) to customer services. So, the whole product life-cycle is included while deriving quality costs.
The quality cost is reviewed as a part of project management to make crucial decisions on how much to invest in quality.
When it comes to the definition of quality cost, there are two categories:
Cost of Conformance
These costs are incurred to maintain defective products from falling into customers' hands. The cost of conformance is made of:
1. Appraisal Costs
These are also known as inspection costs incurred to determine defective products before they're shipped to consumers. However, performing appraisal tasks doesn't prevent defects from happening. Most managers realize that keeping a team of inspectors isn't an effective way to control quality.
A better method is to ask employees to be responsible for their quality control, followed by creating designs for how to manufacture a zero-defect product. This method enables quality to be built into the product, rather than depending on inspections to determine defects.
2. Prevention Costs
These costs include all those expenses incurred for tasks mainly designed to prevent the low-quality product from occurring. It's much less expensive to prevent an issue than to identify and rectify the problem after its occurrence.
Prevention costs are incurred for activities that minimize the defects number. Companies employ several practices to prevent them, including statistical process control, quality engineering, and training.
Cost of Non-conformance
These costs are incurred due to defects generated despite efforts by a company to prevent them. Hence, these costs are also called costs of poor quality. These failure expenses are incurred when a product fails to conform to its design properties.
The non-conformance costs consist of 2 categories:
1. Internal Failure Costs
These costs result from defects found before they are shipped to consumers. They are determined within the project scope. Internal failure costs include rejected products, downtime, and reworking detective systems caused by quality issues.
It also includes costs if an organization has to reject and throw units of their project work, called scrap. If the company's appraisal activities are productive, it has a good chance of identifying defects internally; thus increasing the internal failure cost level.
2. External Failure Costs
These costs are an outcome of delivering a defective product to the consumer. The external failure costs include many sales arising from a poor-quality reputation, repairs and replacements, product recalls, warranty, and liabilities arising from legal action against a firm. Such expenses can even reduce a business's profit.
These costs also give rise to intangible expenses. For example, a company may lose its future venture with its existing consumer for delivering a poor-quality product. These expenses aren't there on the balance sheet; instead, they significantly impact the income statement.
The best method a company can follow amid these scenarios is to ensure the defective products never reach the consumer.
By minimizing internal loss, one can ensure they don't slip through to become external failures. Even if they have an external failure, one should act quickly and resolve the customer problem. This is the benchmark of good customer service.
Hence, the cost of quality includes costs of conformance and non-conformance. This method helps us estimate the amount we spend to assure quality. It also involves looking at the conformance and non-conformance costs of the project and creating a suitable balance.
Read More
Project Quality Management: Cost of Quality
Cost of quality is a significant concept in the project quality management knowledge area. However, it's also misinterpreted by several PMP credential exam-takers. A strong understanding of this concept can help increase a participant's score as there're very few questions on the exam based on it.
Let's take a quick and profound journey into the cost of quality concept.
If a product meets/exceeds its design features and is null-defect, it's said to have a top-notch conformance quality. So, for example, if a steel watch has zero defects, it can have a high conformance quality as a zero-defect diamond-studded watch. The steel one may not be attractive or expensive as the diamond, but you can expect it to be free of defects.
The prevention, identification, and handling of defects incur costs of quality. The term indicates total costs incurred to prevent product defects or costs that result from product defects.
Quality costs don't just relate to manufacturing but all the tasks from research and development (R&D) to customer services. So, the whole product life-cycle is included while deriving quality costs.
The quality cost is reviewed as a part of project management to make crucial decisions on how much to invest in quality.
When it comes to the definition of quality cost, there are two categories:
Cost of Conformance
These costs are incurred to maintain defective products from falling into customers' hands. The cost of conformance is made of:
1. Appraisal Costs
These are also known as inspection costs incurred to determine defective products before they're shipped to consumers. However, performing appraisal tasks doesn't prevent defects from happening. Most managers realize that keeping a team of inspectors isn't an effective way to control quality.
A better method is to ask employees to be responsible for their quality control, followed by creating designs for how to manufacture a zero-defect product. This method enables quality to be built into the product, rather than depending on inspections to determine defects.
2. Prevention Costs
These costs include all those expenses incurred for tasks mainly designed to prevent the low-quality product from occurring. It's much less expensive to prevent an issue than to identify and rectify the problem after its occurrence.
Prevention costs are incurred for activities that minimize the defects number. Companies employ several practices to prevent them, including statistical process control, quality engineering, and training.
Cost of Non-conformance
These costs are incurred due to defects generated despite efforts by a company to prevent them. Hence, these costs are also called costs of poor quality. These failure expenses are incurred when a product fails to conform to its design properties.
The non-conformance costs consist of 2 categories:
1. Internal Failure Costs
These costs result from defects found before they are shipped to consumers. They are determined within the project scope. Internal failure costs include rejected products, downtime, and reworking detective systems caused by quality issues.
It also includes costs if an organization has to reject and throw units of their project work, called scrap. If the company's appraisal activities are productive, it has a good chance of identifying defects internally; thus increasing the internal failure cost level.
2. External Failure Costs
These costs are an outcome of delivering a defective product to the consumer. The external failure costs include many sales arising from a poor-quality reputation, repairs and replacements, product recalls, warranty, and liabilities arising from legal action against a firm. Such expenses can even reduce a business's profit.
These costs also give rise to intangible expenses. For example, a company may lose its future venture with its existing consumer for delivering a poor-quality product. These expenses aren't there on the balance sheet; instead, they significantly impact the income statement.
The best method a company can follow amid these scenarios is to ensure the defective products never reach the consumer.
By minimizing internal loss, one can ensure they don't slip through to become external failures. Even if they have an external failure, one should act quickly and resolve the customer problem. This is the benchmark of good customer service.
Hence, the cost of quality includes costs of conformance and non-conformance. This method helps us estimate the amount we spend to assure quality. It also involves looking at the conformance and non-conformance costs of the project and creating a suitable balance.
Fast-Tracking vs Crashing: Key Differences Explained!!!
Fast-tracking vs crashing
Let work pile up when we're busy with multiple projects of varying sizes is easy. It's even easier to forget about obligations and commitments in our personal lives. However, planning for various contingencies and scheduling our time can help us avoid these issues.
Fast-tracking and crashing are techniques of schedule compression through which we can avoid the issues. Before moving forward to fast-tracking and Crashing, let's briefly know about schedule comparison.
Schedule Compression Definition
Schedule compression reduces a project's duration by speeding up the project team and resources. This can be done by increasing the number of working hours or by decreasing the number of holidays and other non-working days.
Schedule compression is an integral part of project management because it allows you to shorten the duration of your projects. Therefore, schedule compression is the answer if you want to deliver your products or services faster. However, there are some downsides to using this technique.
The main benefit of schedule compression is that it allows you to deliver projects faster than they would have been born without reduction.
What is Fast-Tracking?
Fast-tracking is a project management technique used when a project is needed to accelerate the completion of a project. Fast-tracking can be used when problems with the originally scheduled completion date or when it becomes clear that the original date is not achievable.
Fast-tracking can be applied to one project or several phases at once. However, it involves adding resources and reducing the scope to complete the project on time.
It can also be applied at any project's life cycle stage. Still, it is most commonly used during the early stages of development when costs are lower. Risks may be more significant if action is not taken quickly.
What is crashing?
Crashing is a technique used to fast-track a project if you've run out of time with regular fast-tracking. You add more people to the project, but since they're working less per hour than the other team members, their salary will be cheaper than additional people.
Their time will be more affordable than regular employees'. However, Crashing can be expensive because you're paying all these extra people, so you have to find activities that save the most time while costing the least money.
You categorize your actions by the lowest cost per unit time, called crash cost. Then you look at which activities will bring the most value while costing the least money.
The results of a crash analysis are usually presented in a crash graph, where activities with the flattest slope are considered first—these lead to an equal amount of time savings but have a minor increase in cost.
Comparison between Fast Tracking and Crashing
Fast-tracking is a technique used in software development whereby a project is accelerated by adding resources to the project team. The main benefit of fast-tracking is that it reduces the time taken to complete a project and allows for earlier release dates.
On the other hand, Crashing is mainly used in software development, which involves adding more people to a task to complete it quickly. Therefore, Crashing can effectively get things done quickly, but there are also disadvantages associated with this project control method. These include:
- Less experienced team members may be unable to keep up with the pace required by crashing. This may result in poor quality work or, even worse, poor quality code, which can cause problems later on down the line!
- There will not be enough time for testing, meaning that any bugs discovered during testing may have already been missed by the developers who have written them!
Fast-tracking also means more resources will be required to complete the project in time. Therefore, it can be implemented only if there are enough resources available within the organization.
Compared to Crashing, Fast Tracking is less labor intensive as it does not require much overtime work from your team members. In contrast, Crashing involves a lot of overtime work from your team members, which may lead to burnout and high-stress levels among them.
The main difference between fast-tracking and Crashing is that Crashing focuses on shortening cycle times while fast-tracking directions create high-quality products as quickly as possible with limited resources.
When to use fast tracking and crashing in a project
Fast-tracking is useful when working on a project with a deadline, and there is no time to do it all by the book. For example, suppose you need to create a website for your business but don't have the time to design it from scratch. In that case, you can use an existing template and customize it yourself instead of paying someone else to do it for you.
There are a few situations where you can use Crashing:
When you want to get rid of some code that is no longer needed. For example, if you have a method used only in one place but isn't called, it still needs to be there. If you don't want to delete the code but don't want it in your program, you can use a crash to remove it.
Suppose you have a method that crashes and wants to test how your program handles this situation. For example, you could ensure that any exception information is logged correctly or displayed in an error dialog box.
Conclusion
Now you know about the two techniques of schedule comparison and their difference. Also, when to use these two techniques, we're sure you'll soon begin to see results in no time.
Read More
Fast-tracking vs crashing
Let work pile up when we're busy with multiple projects of varying sizes is easy. It's even easier to forget about obligations and commitments in our personal lives. However, planning for various contingencies and scheduling our time can help us avoid these issues.
Fast-tracking and crashing are techniques of schedule compression through which we can avoid the issues. Before moving forward to fast-tracking and Crashing, let's briefly know about schedule comparison.
Schedule Compression Definition
Schedule compression reduces a project's duration by speeding up the project team and resources. This can be done by increasing the number of working hours or by decreasing the number of holidays and other non-working days.
Schedule compression is an integral part of project management because it allows you to shorten the duration of your projects. Therefore, schedule compression is the answer if you want to deliver your products or services faster. However, there are some downsides to using this technique.
The main benefit of schedule compression is that it allows you to deliver projects faster than they would have been born without reduction.
What is Fast-Tracking?
Fast-tracking is a project management technique used when a project is needed to accelerate the completion of a project. Fast-tracking can be used when problems with the originally scheduled completion date or when it becomes clear that the original date is not achievable.
Fast-tracking can be applied to one project or several phases at once. However, it involves adding resources and reducing the scope to complete the project on time.
It can also be applied at any project's life cycle stage. Still, it is most commonly used during the early stages of development when costs are lower. Risks may be more significant if action is not taken quickly.
What is crashing?
Crashing is a technique used to fast-track a project if you've run out of time with regular fast-tracking. You add more people to the project, but since they're working less per hour than the other team members, their salary will be cheaper than additional people.
Their time will be more affordable than regular employees'. However, Crashing can be expensive because you're paying all these extra people, so you have to find activities that save the most time while costing the least money.
You categorize your actions by the lowest cost per unit time, called crash cost. Then you look at which activities will bring the most value while costing the least money.
The results of a crash analysis are usually presented in a crash graph, where activities with the flattest slope are considered first—these lead to an equal amount of time savings but have a minor increase in cost.
Comparison between Fast Tracking and Crashing
Fast-tracking is a technique used in software development whereby a project is accelerated by adding resources to the project team. The main benefit of fast-tracking is that it reduces the time taken to complete a project and allows for earlier release dates.
On the other hand, Crashing is mainly used in software development, which involves adding more people to a task to complete it quickly. Therefore, Crashing can effectively get things done quickly, but there are also disadvantages associated with this project control method. These include:
- Less experienced team members may be unable to keep up with the pace required by crashing. This may result in poor quality work or, even worse, poor quality code, which can cause problems later on down the line!
- There will not be enough time for testing, meaning that any bugs discovered during testing may have already been missed by the developers who have written them!
Fast-tracking also means more resources will be required to complete the project in time. Therefore, it can be implemented only if there are enough resources available within the organization.
Compared to Crashing, Fast Tracking is less labor intensive as it does not require much overtime work from your team members. In contrast, Crashing involves a lot of overtime work from your team members, which may lead to burnout and high-stress levels among them.
The main difference between fast-tracking and Crashing is that Crashing focuses on shortening cycle times while fast-tracking directions create high-quality products as quickly as possible with limited resources.
When to use fast tracking and crashing in a project
Fast-tracking is useful when working on a project with a deadline, and there is no time to do it all by the book. For example, suppose you need to create a website for your business but don't have the time to design it from scratch. In that case, you can use an existing template and customize it yourself instead of paying someone else to do it for you.
There are a few situations where you can use Crashing:
When you want to get rid of some code that is no longer needed. For example, if you have a method used only in one place but isn't called, it still needs to be there. If you don't want to delete the code but don't want it in your program, you can use a crash to remove it.
Suppose you have a method that crashes and wants to test how your program handles this situation. For example, you could ensure that any exception information is logged correctly or displayed in an error dialog box.
Conclusion
Now you know about the two techniques of schedule comparison and their difference. Also, when to use these two techniques, we're sure you'll soon begin to see results in no time.
EEFs and OPAs play a crucial role in project management.
Enterprise Environmental Factors and Organizational Process Assets
Table of Content
What are the enterprise environmental factors?
What are the organizational process assets?
Organizational culture, policies, and procedures
Organizational infrastructure
Market conditions
Organizational knowledge base
Corporate lessons learned from databases
Conclusion
What are the enterprise environmental factors?
Enterprise environmental factors are the external conditions that affect the organization. These factors include:
Economic Factors: Economic factors include the availability of capital, fluctuations in the business cycle, and changes in government policy.
Technological Factors: Technological factors include technological advances, new products and services, and competitors' use of technology to create new markets.
Social Factors: Social factors include changes in demographics (changes in population age groups), cultural influences on individual behavior, and government regulations on business practices.
Political Factors: Political factors include changes in laws and regulations affecting an organization's operations or profitability.
What are the organizational process assets?
The organizational process assets are the organization's knowledge, information, and experience. They include processes and procedures, policies, work instructions, standards, guidelines, and other similar documents.
The assets exist at all levels within an organization — from strategic planning to day-to-day operations — and comprise a large percentage of the total value of any company.
Organizational process assets provide a competitive advantage to any business because they enable companies to perform their work more efficiently and effectively than their competitors.
Organizational culture, policies, and procedures
The organizational culture, policies, and procedures result from the corporate environment. They exist because the environment needs to be supported by them. The organization aims to create an environment where employees can do their jobs effectively.
For an organization to accomplish its goals, it must support the people who work in it. It does this in many ways:
- By creating a workplace that is safe and secure.
- By providing tools and resources that help employees get their job done.
- By offering training so employees can learn new skills and so on.
Organizational infrastructure
The organizational infrastructure is the foundation of the organization. It includes the human, physical, and technological resources used to support the organization's activities. The corporate infrastructure may be divided into two major components:
Process assets refer to the knowledge and expertise used by an organization in its daily processes. Process assets include training manuals, procedures, or checklists required to perform specific tasks. Process assets may also include computer software programs that allow employees to perform their jobs more effectively or efficiently.
For example, a company might have a process manual that describes how to operate their cash registers properly or a software program that allows workers to enter data into their computer systems faster than they could be using paper records.
Physical assets refer to equipment, buildings, furniture, and other tangible items an organization uses for day-to-day operations.
An example of physical support would be a water tap inside an office building where employees could fill up their water bottles on hot summer days before returning to work.
Organizational knowledge base
The organizational knowledge base is the accumulated body of information that describes the steps and procedures used to perform tasks. This includes experience, corporate knowledge, and best practices.
The organizational knowledge base can be internal (company-owned) or external (public domain).
Knowledge management is an area of research and practice devoted to increasing the value of an organization's intellectual assets.
The field has been studied for more than two decades. Still, it wasn't until the 1990s that organizations realized the value of their intellectual assets (intellectual capital).
Knowledge management can be defined as "the identification, creation, accumulation, and dissemination of knowledge to generate wealth through innovation and action.
Corporate lessons learned from databases
The use of databases has become an essential part of the work environment for many organizations. There are several characteristics of databases that can provide businesses with a competitive advantage. These include:
Reliability: Reliability is the ability of a database to be up-to-date, accurate, and consistent at all times. When a business relies on its database for critical information, it must be able to trust its accuracy at all times.
Accessibility: A database should be accessible by authorized users anywhere at any time. This allows employees to make decisions based on the latest information available in the system.
Efficiency: A good database will make it easier for employees to store, retrieve, and manage information. The more efficient employees use the system, the less time they spend on tasks that don't directly contribute to their jobs, and the higher productivity rates will be for each employee.
Conclusion
As you can see, EEFs and OPAFs are only two of many different aspects that need to be considered to create a practical process map. Creating a meaningful process map is not as simple as simply drawing some boxes, connecting them with arrows, and deeming your work done. To be truly effective, a process map must be developed considering the various factors affecting the success of the processes being mapped—internal and external.
Read More
Enterprise Environmental Factors and Organizational Process Assets
Table of Content
What are the enterprise environmental factors?
What are the organizational process assets?
Organizational culture, policies, and procedures
Organizational infrastructure
Market conditions
Organizational knowledge base
Corporate lessons learned from databases
Conclusion
What are the enterprise environmental factors?
Enterprise environmental factors are the external conditions that affect the organization. These factors include:
Economic Factors: Economic factors include the availability of capital, fluctuations in the business cycle, and changes in government policy.
Technological Factors: Technological factors include technological advances, new products and services, and competitors' use of technology to create new markets.
Social Factors: Social factors include changes in demographics (changes in population age groups), cultural influences on individual behavior, and government regulations on business practices.
Political Factors: Political factors include changes in laws and regulations affecting an organization's operations or profitability.
What are the organizational process assets?
The organizational process assets are the organization's knowledge, information, and experience. They include processes and procedures, policies, work instructions, standards, guidelines, and other similar documents.
The assets exist at all levels within an organization — from strategic planning to day-to-day operations — and comprise a large percentage of the total value of any company.
Organizational process assets provide a competitive advantage to any business because they enable companies to perform their work more efficiently and effectively than their competitors.
Organizational culture, policies, and procedures
The organizational culture, policies, and procedures result from the corporate environment. They exist because the environment needs to be supported by them. The organization aims to create an environment where employees can do their jobs effectively.
For an organization to accomplish its goals, it must support the people who work in it. It does this in many ways:
- By creating a workplace that is safe and secure.
- By providing tools and resources that help employees get their job done.
- By offering training so employees can learn new skills and so on.
Organizational infrastructure
The organizational infrastructure is the foundation of the organization. It includes the human, physical, and technological resources used to support the organization's activities. The corporate infrastructure may be divided into two major components:
Process assets refer to the knowledge and expertise used by an organization in its daily processes. Process assets include training manuals, procedures, or checklists required to perform specific tasks. Process assets may also include computer software programs that allow employees to perform their jobs more effectively or efficiently.
For example, a company might have a process manual that describes how to operate their cash registers properly or a software program that allows workers to enter data into their computer systems faster than they could be using paper records.
Physical assets refer to equipment, buildings, furniture, and other tangible items an organization uses for day-to-day operations.
An example of physical support would be a water tap inside an office building where employees could fill up their water bottles on hot summer days before returning to work.
Organizational knowledge base
The organizational knowledge base is the accumulated body of information that describes the steps and procedures used to perform tasks. This includes experience, corporate knowledge, and best practices.
The organizational knowledge base can be internal (company-owned) or external (public domain).
Knowledge management is an area of research and practice devoted to increasing the value of an organization's intellectual assets.
The field has been studied for more than two decades. Still, it wasn't until the 1990s that organizations realized the value of their intellectual assets (intellectual capital).
Knowledge management can be defined as "the identification, creation, accumulation, and dissemination of knowledge to generate wealth through innovation and action.
Corporate lessons learned from databases
The use of databases has become an essential part of the work environment for many organizations. There are several characteristics of databases that can provide businesses with a competitive advantage. These include:
Reliability: Reliability is the ability of a database to be up-to-date, accurate, and consistent at all times. When a business relies on its database for critical information, it must be able to trust its accuracy at all times.
Accessibility: A database should be accessible by authorized users anywhere at any time. This allows employees to make decisions based on the latest information available in the system.
Efficiency: A good database will make it easier for employees to store, retrieve, and manage information. The more efficient employees use the system, the less time they spend on tasks that don't directly contribute to their jobs, and the higher productivity rates will be for each employee.
Conclusion
As you can see, EEFs and OPAFs are only two of many different aspects that need to be considered to create a practical process map. Creating a meaningful process map is not as simple as simply drawing some boxes, connecting them with arrows, and deeming your work done. To be truly effective, a process map must be developed considering the various factors affecting the success of the processes being mapped—internal and external.
Top 16 Qualities Every Good Manager and Leader Must Have.
Top 16 Qualities of a Good Manager and a Leader
What are the qualities of a good manager? A leader, for that matter? How about someone who both manages and leads? You don't often find a single person who excels in both, but it happens. So if you work and want to develop skills in either of these two areas, this article is for you.
Vision
A good manager and leader have a vision for the future of their business or the world. They see where they want to go and understand what it will take to get there. They also have a clear idea of how they will get there. This is important because it allows them to make decisions based on facts, not wishful thinking.
Vision doesn't mean that you have to be able to predict precisely what will happen in the future; it just means that you know where you're going and why. For example, knowing where your company should go next is essential when deciding what technology to use or how much money to spend on marketing.
Positive
A good manager can identify and understand the needs of the people they manage. They should also be able to motivate employees to seek out opportunities to improve their skills and performance. A good manager will also help you find ways to work together as a team, be flexible, and deal with problems when they arise.
A good leader has all these qualities but doesn't just tell people what to do; instead, they inspire them by making them feel like they have the best interests.
Leadership
A good manager is a leader. A great manager is an exceptional leader. A great leader can inspire others and help them to reach their full potential while at the same time encouraging them to work together in a positive environment.
Leadership is about being able to motivate people and get them excited about achieving something significant. A good manager will be able to help you manage your time effectively and make sure that you have the resources available for you to achieve your goals.
Confidence
Confidence is a quality that most people desire in their managers and leaders, and it's one of the top qualities of a good manager. Confidence comes from knowing what you're doing, having experience, and having the ability to do it well. Great managers know they have the skills to lead, and they use those skills to help their team succeed.
When you're confident about your decision-making abilities and leadership skills, it makes things easier for others on the team. They know that if they ask for help or advice, they will get it without hesitation or fear of being judged as incompetent or weak.
Communication
Communication is critical in any workplace. A good manager or leader can help employees feel respected and understood while providing feedback and guidance.
Communication should be open and honest, with a positive tone. If you are communicating with your team members, try to avoid using words such as "must," "have," or "have to." Instead, use positive words like "I would like" or "I think."
Honesty
Being a good manager and a leader means being honest with your employees and your team. This doesn't come naturally to everyone, but it is an essential quality for a great leader. Honesty is one of the most critical skills as a manager.
Honesty also means being honest with yourself. It would help if you didn't deceive yourself when deciding how to lead your team or manage their performance. If you constantly lie to yourself about whether or not something is working out or if there are other options available, then you're doomed from the start because nobody will ever believe anything you say!
Open-mindedness
A good manager needs to be able to listen, think and learn. He needs to be open-minded to be receptive to new ideas and ways of doing things. The best managers are open-minded enough to accept new ideas from their employees. They also should be able to see the strengths in their employees and recognize their weaknesses, so they can work together to improve on those weaknesses.
Sense of humor
A sense of humor is an essential quality in a manager. People need to be able to laugh at themselves and their mistakes and also laugh at others' jokes. This is a great way to build co-workers' trust, morale, and camaraderie.
When you're having fun with your team, they're probably having fun too. This can lead to a more productive work environment and a better team overall.
Team player
A good manager and leader put the needs of their team above her own needs. They are always thinking of ways to improve their team and know how to get the best out of their team members.
A good manager and leader is also someone with strong leadership skills, which means they can make decisions confidently and handle conflict well.
Creativity
Creativity is one of the most essential and exciting qualities of a good manager and leader. A great manager and leader not only knows how to manage but also knows how to inspire other people to do their best work. In addition, a creative manager can develop new ideas for improving processes and procedures or making the workplace more attractive for employees. This can improve productivity, morale, and employee satisfaction.
Decision-making ability
The ability to make decisions is an essential quality for a manager. A good decision-maker understands what needs to be done, when, and how it should be done. As a result, the best manager can make the right decisions for the organization and its people.
A good leader also has an excellent decision-making ability. They can see the big picture and how all parts of the organization fit together to reach a common goal. This ability enables leaders to understand problems from different angles and develop solutions that will benefit everyone involved in the organization.
Willingness to learn new things, adaptability to change, and flexibility.
Great managers are willing to learn new things, adapt to change, and be flexible.
They have the ability and willingness to do whatever it takes to get the job done. They are not afraid of failure or doing things differently than what has been done before. Leaders can see past their ego and focus on what is best for the company or team they lead.
Optimism for the future
Optimism is a good quality to have as a manager and leader. Seeing the glass half full and being optimistic about your team and the future will help you get the best out of them.
One of the biggest problems with managers is that they can be negative about everything, which can cause them to lose their employees' faith. This can lead to poor performance, disengagement, and ultimately dismissal.
Do not underestimate the power of optimism in your life and your business.
Commitment to the organization and its staff members
The best managers and leaders can be committed to their organization and its staff members. But, to be successful, they must be able to inspire others through their words, actions, and deeds.
Good managers and leaders are committed to the organization's goals, mission, vision, and values. In addition, they take pride in their work, which is evident in how they present themselves in front of others.
A good manager and leader delegate assignments for growth and development
A good manager and leader is a good listener and understands the need of employees to grow professionally. In addition, good managers and leaders are transparent with their employees and keep them informed about their role in the organization.
A good manager and leader have integrity which means they follow ethical conduct in/her work environment. They do not compromise with any unethical behavior in/her organization or workplace. A good manager and leader always try to keep things on track by following the rules of the organization that they work for.
A good manager and a leader reward and recognize accomplishments
A good manager and a leader treat all employees equally regardless of their position or level in the company. A good leader knows their team members well enough to recognize who is doing well and who needs help improving on something.
A good manager knows how to delegate tasks effectively and efficiently because he understands his employee's strengths and weaknesses, while a suitable leader delegates tasks based on their ability to do them correctly without having to be coached every step.
Conclusion
To be an effective manager and leader, you must have unique qualities that separate you from the rest. You're responsible for leading a group of people. As such, your leadership skills will dictate whether or not you can effectively do your job. So, what are some key characteristics that make a good manager and leader? As with most things, knowing yourself and understanding your strengths and weaknesses is essential. Move through each of these characteristics, then decide which ones would make you a better manager and leader, given who you already are in today's business world.
Read More
Top 16 Qualities of a Good Manager and a Leader
What are the qualities of a good manager? A leader, for that matter? How about someone who both manages and leads? You don't often find a single person who excels in both, but it happens. So if you work and want to develop skills in either of these two areas, this article is for you.
Vision
A good manager and leader have a vision for the future of their business or the world. They see where they want to go and understand what it will take to get there. They also have a clear idea of how they will get there. This is important because it allows them to make decisions based on facts, not wishful thinking.
Vision doesn't mean that you have to be able to predict precisely what will happen in the future; it just means that you know where you're going and why. For example, knowing where your company should go next is essential when deciding what technology to use or how much money to spend on marketing.
Positive
A good manager can identify and understand the needs of the people they manage. They should also be able to motivate employees to seek out opportunities to improve their skills and performance. A good manager will also help you find ways to work together as a team, be flexible, and deal with problems when they arise.
A good leader has all these qualities but doesn't just tell people what to do; instead, they inspire them by making them feel like they have the best interests.
Leadership
A good manager is a leader. A great manager is an exceptional leader. A great leader can inspire others and help them to reach their full potential while at the same time encouraging them to work together in a positive environment.
Leadership is about being able to motivate people and get them excited about achieving something significant. A good manager will be able to help you manage your time effectively and make sure that you have the resources available for you to achieve your goals.
Confidence
Confidence is a quality that most people desire in their managers and leaders, and it's one of the top qualities of a good manager. Confidence comes from knowing what you're doing, having experience, and having the ability to do it well. Great managers know they have the skills to lead, and they use those skills to help their team succeed.
When you're confident about your decision-making abilities and leadership skills, it makes things easier for others on the team. They know that if they ask for help or advice, they will get it without hesitation or fear of being judged as incompetent or weak.
Communication
Communication is critical in any workplace. A good manager or leader can help employees feel respected and understood while providing feedback and guidance.
Communication should be open and honest, with a positive tone. If you are communicating with your team members, try to avoid using words such as "must," "have," or "have to." Instead, use positive words like "I would like" or "I think."
Honesty
Being a good manager and a leader means being honest with your employees and your team. This doesn't come naturally to everyone, but it is an essential quality for a great leader. Honesty is one of the most critical skills as a manager.
Honesty also means being honest with yourself. It would help if you didn't deceive yourself when deciding how to lead your team or manage their performance. If you constantly lie to yourself about whether or not something is working out or if there are other options available, then you're doomed from the start because nobody will ever believe anything you say!
Open-mindedness
A good manager needs to be able to listen, think and learn. He needs to be open-minded to be receptive to new ideas and ways of doing things. The best managers are open-minded enough to accept new ideas from their employees. They also should be able to see the strengths in their employees and recognize their weaknesses, so they can work together to improve on those weaknesses.
Sense of humor
A sense of humor is an essential quality in a manager. People need to be able to laugh at themselves and their mistakes and also laugh at others' jokes. This is a great way to build co-workers' trust, morale, and camaraderie.
When you're having fun with your team, they're probably having fun too. This can lead to a more productive work environment and a better team overall.
Team player
A good manager and leader put the needs of their team above her own needs. They are always thinking of ways to improve their team and know how to get the best out of their team members.
A good manager and leader is also someone with strong leadership skills, which means they can make decisions confidently and handle conflict well.
Creativity
Creativity is one of the most essential and exciting qualities of a good manager and leader. A great manager and leader not only knows how to manage but also knows how to inspire other people to do their best work. In addition, a creative manager can develop new ideas for improving processes and procedures or making the workplace more attractive for employees. This can improve productivity, morale, and employee satisfaction.
Decision-making ability
The ability to make decisions is an essential quality for a manager. A good decision-maker understands what needs to be done, when, and how it should be done. As a result, the best manager can make the right decisions for the organization and its people.
A good leader also has an excellent decision-making ability. They can see the big picture and how all parts of the organization fit together to reach a common goal. This ability enables leaders to understand problems from different angles and develop solutions that will benefit everyone involved in the organization.
Willingness to learn new things, adaptability to change, and flexibility.
Great managers are willing to learn new things, adapt to change, and be flexible.
They have the ability and willingness to do whatever it takes to get the job done. They are not afraid of failure or doing things differently than what has been done before. Leaders can see past their ego and focus on what is best for the company or team they lead.
Optimism for the future
Optimism is a good quality to have as a manager and leader. Seeing the glass half full and being optimistic about your team and the future will help you get the best out of them.
One of the biggest problems with managers is that they can be negative about everything, which can cause them to lose their employees' faith. This can lead to poor performance, disengagement, and ultimately dismissal.
Do not underestimate the power of optimism in your life and your business.
Commitment to the organization and its staff members
The best managers and leaders can be committed to their organization and its staff members. But, to be successful, they must be able to inspire others through their words, actions, and deeds.
Good managers and leaders are committed to the organization's goals, mission, vision, and values. In addition, they take pride in their work, which is evident in how they present themselves in front of others.
A good manager and leader delegate assignments for growth and development
A good manager and leader is a good listener and understands the need of employees to grow professionally. In addition, good managers and leaders are transparent with their employees and keep them informed about their role in the organization.
A good manager and leader have integrity which means they follow ethical conduct in/her work environment. They do not compromise with any unethical behavior in/her organization or workplace. A good manager and leader always try to keep things on track by following the rules of the organization that they work for.
A good manager and a leader reward and recognize accomplishments
A good manager and a leader treat all employees equally regardless of their position or level in the company. A good leader knows their team members well enough to recognize who is doing well and who needs help improving on something.
A good manager knows how to delegate tasks effectively and efficiently because he understands his employee's strengths and weaknesses, while a suitable leader delegates tasks based on their ability to do them correctly without having to be coached every step.
Conclusion
To be an effective manager and leader, you must have unique qualities that separate you from the rest. You're responsible for leading a group of people. As such, your leadership skills will dictate whether or not you can effectively do your job. So, what are some key characteristics that make a good manager and leader? As with most things, knowing yourself and understanding your strengths and weaknesses is essential. Move through each of these characteristics, then decide which ones would make you a better manager and leader, given who you already are in today's business world.
Unveil the Top 30 Lean Six Sigma Black Belt Exam Q&As Now
Top 30 Lean Six Sigma Black Belt Certification Exam Questions with Answers
Six Sigma is a group of methods and tools employed for process enhancement. It focuses on enhancing the overall quality by estimating the defects present within a process and eradicating those through a systematic technique.
The Lean Six Sigma Black Belt certification will offer you proficiency in Lean Six Sigma methods of DMAIC. Here, we have a collection of top 30 exam questions of the certifications with solutions that will help you gain confidence to appear for the test.
Q1. What does DMADV stands for:
- Design, Measure, Analyze, Define, Validate
- Develop Measurement and Analysis Department for Verification
- Define, Measure, Analyze, Define, Verify
ANSWER: (A)
Q2. What does P stand in the acronym of a process map, SIPOC. What does the P stand for in this acronym?
- Product
- Process
- Preliminary
- Population
ANSWER: (B)
Q3. The practice of using specific points in its storage area to indicate when products need to be ordered.
- Poka-yoke
- Checkpoints
- Hoshin
- Kanban
ANSWER: (D)
Q4. Which of the following techniques dramatically shortens changeover times?
- Work in process (WIP)
- Continuous flow
- Single minute exchange of dies (SMED)
- Standard work
ANSWER: (C)
Q5. Which of the following tools can be used to identify waste or non-value-added activities?
- Process map
- Force yield analysis
- Scatter diagram
- Pareto analysis
ANSWER: (A)
Q6. The purpose of Toll Gate review is to:
- Review progress and kick off the next phase
- Confirm if the earlier phase was completed successfully
- Get a formal sign-off from the stakeholders
- All of the above
ANSWER: (D)
Q7. A Black Belt is expected to deliver what types of results from Six Sigma projects?
- Large projects
- A minimum 200K USD as annual benefit
- Defects reduction projects
- Have everybody in the organization trained on Six Sigma
ANSWER: (B)
Q8. The purpose of capturing Voice of Customer (VoC) is to:
- Capture stated or unstated customer requirements
- Have a sampling exercise
- Collect customer feedback
- Ensure there is no confusion between the contract and delivery
ANSWER: (A)
Q9. Which of the control charts must have at least 20 subgroups of observed values to judge whether a process is in control or not?
- R-Chart
- P-Chart
- C-Chart
- Y-Chart
ANSWER: (A)
Q10. An advanced quantitative analysis to optimize business or industrial processes through process mapping and modelling using multiple variables. This tool is referred as:
- Capability-requirements analysis
- C&E Analysis
- Capability-complexity analysis
- FMEA analysis
ANSWER: (C)
Q11. Correction, over-production, inventory, and motion are all examples of:
- Waste
- Noise
- 5S target areas
- Value-added activities
ANSWER: (A)
Q12. What tool did Kaoru Ishikawa develop?
- CTQ Diagram
- FMEA Tool
- SWAT Analysis Tool
- Cause and Effect Diagram
ANSWER: (D)
Q13. Which tool is used to assess the significance of factors in either a fractional or a full-factorial experiment structure?
- Analysis of variance (ANOVA)
- Fault tree analysis (FTA)
- Failure mode and effects analysis (FMEA)
- Evolutionary operation (EVOP)
ANSWER: (A)
Q14. Which of the following methods is used to develop an exhaustive list of ideas about a subject?
- Benchmarking
- Brainstorming
- Goal-setting
- Problem-solving
ANSWER: (B)
Q15. A company wishes to compare the expected mileage of eight different types of car tires. Which of the following statistical tests is best suited for the analysis?
- Multiple regression
- ANOVA
- Paired-difference test
- Z-test
ANSWER: (B)
Q16. A company has installed a system that prevents orders with incorrect information from being forwarded to production scheduling. This is an example of which of the following lean tools?
- Standard work
- Kanban
- Poka-Yoke
- Visual factory
ANSWER: (C)
Q17. SMED is a lean manufacturing concept that is used to reduce waste in the manufacturing process. What does the E stand for?
- Exchange
- Error
- Estimate
- Expected
ANSWER: (A)
Q18. Which of the following tools is appropriate to use with multiple criteria requiring a single option to be selected?
- Pugh matrix
- Kano model
- Hypothesis testing
- PDCA
ANSWER: (A)
Q19. The process developing a problem statement by a Six Sigma team will help to:
- Agree on key dates associated with completing major project phases
- Achieve consensus and ownership of the process
- Determine solutions
- Determine how often it should meet.
ANSWER: (B)
Q20. Which of the following is the correct formula for DPMO?
- D/TOP
- DPO×1,000,000
- D×U×OP
- DPU/DPO
ANSWER: (B)
Q21. A method that changes data without significantly reducing accuracy or precision is known as:
- Bias adjustment
- Statistical efficiency
- Blocking
- Coding
ANSWER: (D)
Q22. When the sampling method used creates a difference between the result obtained from the sample and the actual population value, the difference is known as:
- Correlation
- Precision
- Accuracy
- Bias
ANSWER: (D)
Q23. A technique for demonstrating the connection between customer needs and features on the product is:
- Flow charts and process maps
- Relationship matrix
- Cause and effect diagrams
- Pareto chart
ANSWER: (B)
Q24. The workers of a manufacturing unit want to maintain cleanliness on a daily basis. Which approach is most apt?
- 5S
- Poka-yoke
- Kaizen
- PDCA
ANSWER: (A)
Q25. Which of the following best describes a team that has members with different skills or roles from different areas within the organization?
- Self-directed
- Cross-functional
- Parallel
- Process
ANSWER: (B)
Q26. An important aspect of data collection is that the data collector should:
- Determine the dispersion of the data
- Know how the data are to be used
- Use a control chart to analyze the data
- Use stratified sampling plan
ANSWER: (B)
Q27. When the variation cause is a cluttered workstation which technique helps to increase the process stability?
- 5S
- SMED
- Preventive maintenance
- Visual factory
ANSWER: (A)
Q28. Which of the following is an important responsibility of a project champion?
- Leading the team
- Documenting the overall progress of the team
- Allocating resources to support the team
- Coaching the team in DMAIC process
ANSWER: (C)
Q29. Positional, cyclical, and temporal variations are most commonly analyzed in:
- SPC charts
- Multi-vary charts
- Cause and effect diagrams
- Run charts
ANSWER: (B)
Q30. Which one of the following is an inventive methodology for problem-solving?
- BPR
- TPM
- TRIZ
- BMP
ANSWER: (C)
Read More
Top 30 Lean Six Sigma Black Belt Certification Exam Questions with Answers
Six Sigma is a group of methods and tools employed for process enhancement. It focuses on enhancing the overall quality by estimating the defects present within a process and eradicating those through a systematic technique.
The Lean Six Sigma Black Belt certification will offer you proficiency in Lean Six Sigma methods of DMAIC. Here, we have a collection of top 30 exam questions of the certifications with solutions that will help you gain confidence to appear for the test.
Q1. What does DMADV stands for:
- Design, Measure, Analyze, Define, Validate
- Develop Measurement and Analysis Department for Verification
- Define, Measure, Analyze, Define, Verify
ANSWER: (A)
Q2. What does P stand in the acronym of a process map, SIPOC. What does the P stand for in this acronym?
- Product
- Process
- Preliminary
- Population
ANSWER: (B)
Q3. The practice of using specific points in its storage area to indicate when products need to be ordered.
- Poka-yoke
- Checkpoints
- Hoshin
- Kanban
ANSWER: (D)
Q4. Which of the following techniques dramatically shortens changeover times?
- Work in process (WIP)
- Continuous flow
- Single minute exchange of dies (SMED)
- Standard work
ANSWER: (C)
Q5. Which of the following tools can be used to identify waste or non-value-added activities?
- Process map
- Force yield analysis
- Scatter diagram
- Pareto analysis
ANSWER: (A)
Q6. The purpose of Toll Gate review is to:
- Review progress and kick off the next phase
- Confirm if the earlier phase was completed successfully
- Get a formal sign-off from the stakeholders
- All of the above
ANSWER: (D)
Q7. A Black Belt is expected to deliver what types of results from Six Sigma projects?
- Large projects
- A minimum 200K USD as annual benefit
- Defects reduction projects
- Have everybody in the organization trained on Six Sigma
ANSWER: (B)
Q8. The purpose of capturing Voice of Customer (VoC) is to:
- Capture stated or unstated customer requirements
- Have a sampling exercise
- Collect customer feedback
- Ensure there is no confusion between the contract and delivery
ANSWER: (A)
Q9. Which of the control charts must have at least 20 subgroups of observed values to judge whether a process is in control or not?
- R-Chart
- P-Chart
- C-Chart
- Y-Chart
ANSWER: (A)
Q10. An advanced quantitative analysis to optimize business or industrial processes through process mapping and modelling using multiple variables. This tool is referred as:
- Capability-requirements analysis
- C&E Analysis
- Capability-complexity analysis
- FMEA analysis
ANSWER: (C)
Q11. Correction, over-production, inventory, and motion are all examples of:
- Waste
- Noise
- 5S target areas
- Value-added activities
ANSWER: (A)
Q12. What tool did Kaoru Ishikawa develop?
- CTQ Diagram
- FMEA Tool
- SWAT Analysis Tool
- Cause and Effect Diagram
ANSWER: (D)
Q13. Which tool is used to assess the significance of factors in either a fractional or a full-factorial experiment structure?
- Analysis of variance (ANOVA)
- Fault tree analysis (FTA)
- Failure mode and effects analysis (FMEA)
- Evolutionary operation (EVOP)
ANSWER: (A)
Q14. Which of the following methods is used to develop an exhaustive list of ideas about a subject?
- Benchmarking
- Brainstorming
- Goal-setting
- Problem-solving
ANSWER: (B)
Q15. A company wishes to compare the expected mileage of eight different types of car tires. Which of the following statistical tests is best suited for the analysis?
- Multiple regression
- ANOVA
- Paired-difference test
- Z-test
ANSWER: (B)
Q16. A company has installed a system that prevents orders with incorrect information from being forwarded to production scheduling. This is an example of which of the following lean tools?
- Standard work
- Kanban
- Poka-Yoke
- Visual factory
ANSWER: (C)
Q17. SMED is a lean manufacturing concept that is used to reduce waste in the manufacturing process. What does the E stand for?
- Exchange
- Error
- Estimate
- Expected
ANSWER: (A)
Q18. Which of the following tools is appropriate to use with multiple criteria requiring a single option to be selected?
- Pugh matrix
- Kano model
- Hypothesis testing
- PDCA
ANSWER: (A)
Q19. The process developing a problem statement by a Six Sigma team will help to:
- Agree on key dates associated with completing major project phases
- Achieve consensus and ownership of the process
- Determine solutions
- Determine how often it should meet.
ANSWER: (B)
Q20. Which of the following is the correct formula for DPMO?
- D/TOP
- DPO×1,000,000
- D×U×OP
- DPU/DPO
ANSWER: (B)
Q21. A method that changes data without significantly reducing accuracy or precision is known as:
- Bias adjustment
- Statistical efficiency
- Blocking
- Coding
ANSWER: (D)
Q22. When the sampling method used creates a difference between the result obtained from the sample and the actual population value, the difference is known as:
- Correlation
- Precision
- Accuracy
- Bias
ANSWER: (D)
Q23. A technique for demonstrating the connection between customer needs and features on the product is:
- Flow charts and process maps
- Relationship matrix
- Cause and effect diagrams
- Pareto chart
ANSWER: (B)
Q24. The workers of a manufacturing unit want to maintain cleanliness on a daily basis. Which approach is most apt?
- 5S
- Poka-yoke
- Kaizen
- PDCA
ANSWER: (A)
Q25. Which of the following best describes a team that has members with different skills or roles from different areas within the organization?
- Self-directed
- Cross-functional
- Parallel
- Process
ANSWER: (B)
Q26. An important aspect of data collection is that the data collector should:
- Determine the dispersion of the data
- Know how the data are to be used
- Use a control chart to analyze the data
- Use stratified sampling plan
ANSWER: (B)
Q27. When the variation cause is a cluttered workstation which technique helps to increase the process stability?
- 5S
- SMED
- Preventive maintenance
- Visual factory
ANSWER: (A)
Q28. Which of the following is an important responsibility of a project champion?
- Leading the team
- Documenting the overall progress of the team
- Allocating resources to support the team
- Coaching the team in DMAIC process
ANSWER: (C)
Q29. Positional, cyclical, and temporal variations are most commonly analyzed in:
- SPC charts
- Multi-vary charts
- Cause and effect diagrams
- Run charts
ANSWER: (B)
Q30. Which one of the following is an inventive methodology for problem-solving?
- BPR
- TPM
- TRIZ
- BMP
ANSWER: (C)
Top 25 Six Sigma Interview Q&A: Must-Know Tips for 2022
Top 25 Six Sigma Interview Questions and Answers 2022
Efficient operations management is vital across different industry verticals. Its requirement is also changing and evolving towards quality control which is more data-driven than before. Here, Six Sigma satisfies the growing demand, and no doubt, a certification in Six Sigma can help the candidate stand out in today's job market.
There is an ocean of opportunities from several top-notch companies across the globe. According to research, Six Sigma has a market share of over 27.7%. Hence, you choose to move ahead in your career development with Six Sigma.
If you are looking for Six Sigma interview questions for freshers/experience, then you are at the right spot. This article will be vocal about how a Six Sigma accreditation holder can answer the trickiest and most accessible questions you know subtle method that impresses your recruiters and authorities responsible for your future.
Q1. What is Six Sigma and Why is it Called So?
The basic and fundamental question a recruiting manager can ask is your expertise and knowledge on Six Sigma. Therefore, in simple terms, you can define the methodology as a technique that a company leverages to enhances its business process and quality.
By leveraging Six Sigma, companies can maximize performance and minimize process variation - helping businesses to minimize defects, boost profits, improve employee morale, and ameliorate product quality.
For the question - why it's called Six Sigma, you can answer:
To achieve the methodology, the processes of a company require to maintain their defects maximum to 3.4 DPMO, which is otherwise strenuous to achieve.
(DPMO - Defects Per Million Opportunities)
Q2. Define Few Critical Principles of Six Sigma?
- Enhancing of processes
- Prime focus on customer demands
- Effective managing of cross-functional teams
- Relying on statistical analysis to determine the best possible methods of working and finding root causes of probable issues.
- Formulate process flexibility
Q3. Define Two Sub-methodologies of Six Sigma?
- Define, Measure, Analyse, Improve, and Control (DMAIC) - A method leveraged for existing processes that are lacking behind the features and require gradual enhancement.
- Define, Measure, Analyse, Design, and Verify (DMADV) - An approach leveraged to create new products/services that match the Six Sigma quality. In case a business requires more than gradual enhancement, the DMADV process can be used.
Q4. Name Some Quality Management Tools in Six Sigma?
- CTQ Tree
- 5S
- Value Stream Mapping
- Cost-benefit Analysis
- COPIS Analysis
- SIPOC Analysis
Q5. Name a Tool that Visualizes the Possible Causes of a Given Issue?
A tool that helps in conceptualizing the possible causes of a given issue/problem is Ishikawa diagram.
Q6. What are the Different Variations Used in Six Sigma?
- Mean: This measurement is considered only for a certain application and the values are estimated. Hence, within this process, the variations are measured and compared using average mathematics techniques.
- Median: This method is done by determining the lowest and highest values and then dividing the value by 2. Within this process, the variations are estimated and compared by taking the midpoint of the set data range.
- Range: It takes into account the largest and smallest values for a certain range of data.
- Mode: This is nothing but the most occurred values in a given set of data range.
Q7. What is COPQ in Six Sigma?
Cost of Poor Quality (COPQ) is the cost caused by generating defects. This cost involves the following guidelines:
- Disposition Costs
- Extra Utility/Material Cost
- Filling the Gap Between Actual and Desired Service/Product Quality
- Loss of Revenue or Sale
- Labor Cost
- Rework Cost
However, COPQ doesn't include detection and prevention cost.
Q8. Who is Responsible for Creating or being a Part of Six Sigma Implementation Team Within a Company?
The designated individuals who are part of the Six Sigma implementation team are:
- Decision-making executives
- Master Black Belts
- Champions
- Green Belts
- Black Belts
- Yellow Belts
Q9. Define Affinity Diagram?
Affinity diagram is a tool leverage to organize ideas into subgroups by having a common relation theme to build solutions after brainstorming. To proceed, we need to have an affinity group who puts their ideas of operative quality and starts the brainstorming session.
The solutions obtained from the members of the group are aligned and segregated into homogeneous groups with an affinity heading on top. In this way, an individual visualizes the solution and list their numbers accordingly.
Q10. State the Difference Between Performance and Load Testing?
Performance Testing
- It is all about having more stress on the system checks and the overall application and system performance during the stress conditions.
- Performance testing being a superset of load testing, the testing includes load and stress testing.
Load Testing
- It is a testing process where the load limit is beyond what the customer demanded. This will help the individual whether the application can handle a specific limit.
- Load testing is about how well the program behaves and how many concurrent users are able to log in without facing any issues.
Q11. What is Cpk and Ppk?
Cpk is process capability index that estimates how close a process is running to its specification limits, relative to the natural process variability.
Ppk is the process performance index that verifies if the model that has been produced from the process is capable of meeting customer needs or CTQs.
Q12. How Six Sigma Benefits a Company and an Individual Taking the Certification?
- Helps the company to minimize the level of errors.
- Works towards the amelioration of quality assurance
- Helps candidate to develop skills and turn them to leaders
- Candidates with Six Sigma certification receives handsome remuneration and promotion compared to non-certified peers
- The process applicable for all the markets and can be executed throughout the business environments
- Work towards the enhancement of business workflow.
Q13. Explain Pareto Chart?
Pareto analysis is the most used tool in Six Sigma for quality improvement. This not only prioritize problems, but define each and every aspect. This chart sets up a clear image of what required to be dome with the problems, keeping in mind the available resources and cost.
With the help of analysis, we can optimize the process require and the cost factor. This helps us to target customer requirements better than the competitors and reach satisfaction with the feedback loop offered by the stakeholders.
Q14. How to Create a SIPOC Process Map?
Suppliers Input Process Output Customers (SIPOC) is defined as a series of consecutive steps and tasks that are executed promptly to receive a definite output.
The SIPOC process map is vital for determining the following elements:
- How the existing processes are working
- How the processes are changed and enhanced
- How the enhancement is implemented with the next stage of DMAIC.
Q15. What is DFSS in Six Sigma Process?
Define for Six Sigma (DFSS) is a process involved in designing or redesigning the product/service from scratch. One of the cases where the project is following DMAIC methodology goes into the DFSS project because of the designing related tasks.
Q16. What is Lean Six Sigma? What are its Benefits?
Lean Six Sigma is a performance enhancement method that involves eradicating activities that don't add value to the process and reducing variation. This relies on a collaborative team effort and contributes to top-notch quality and customer satisfaction.
Benefits of Lean Six Sigma are:
- Manage larger teams
- Better task prioritization
- Increase team productivity
- Eradicating defects
- Reduce time
- Ensure more efficient business workflow
Q17. Name Some Lean Six Sigma Tools?
- Regression Analysis
- Pareto Chart
- FMEA
- Value Stream Mapping
- Poka-yoke
- Kaizen
Q18. When can the Kaizen Tool be Used?
In situations where we require to implement gradual enhancement, Kaizen serves as the best solution by generating quick solutions to two pressing issues that appear to be critical. This is highly efficient in tackling intensive cross-functional collaboration, and with a swift solution, we can increment enhancement in nearly 3-5 days of execution.
Q19. Explain the Levels of Quality in Six Sigma?
Six Sigma quality levels is a method leveraged to observe and estimate the process quality. At every level of Six Sigma, a number of DPMO are defined. The perfect level of the methodology is achieved at 3.4 DPMO.
The levels of Six Sigma DPMO are:
- 6,90,000
- 3,08,537
- 66,807
- 6,210
- 233
- 3.4
Q20. What Exactly is FMEA in Six Sigma?
Failure Mode and Effect Analysis (FMEA) is leveraged to determine possible risks within the product, process, or design. After determining the risk, individuals can create a risk alleviation plan to overcome them.
Q21. What are the Pros & Cons of Zero Defect?
PROS:
- Eradicates Hidden Costs/Expenses
- Helps in Planning
- Provides Improved Value to the customer
CONS:
- Strenuous to Achieve
- Time-bound and Needs a Proactive Method
- Sound More Abstract to Most of the Organizations
- Outdated Technology
Q22. Tell Us About the Project You Have Worked On?
For this question, you must describe the project and give a summarized and good insight into it. Make sure you describe the project precisely as the recruiting manager may ask for other details related to your project.
Q23. What Factors Did You Consider Before Initiating Your Six Sigma Project?
For this question, list the significant factors that you must have considered before initiating the project. The first and foremost factor any individual would consider is the Process Stability and other factor is Process Capability.
Q24. What Were the Problems You Faced When Working with the Project and How Did You Resolve It?
If you have worked on a project, try recalling minor to major details working on the same and write down some points that are relevant and also some factors that are fundamental in Six Sigma projects. Also ensure that your answer cover the next question which is how did you resolve the issue.
Q25. What is the Kano Model?
It is one of most significant questions on Six Sigma. Kano is a product development technique leveraged to determine VoC and compares the characteristics Vs degree of satisfaction each characteristic deliver.
The technique is invented by Dr. Kano which defines the following:
- Dissatisfying
- Must-Haves
- Customer needs
- Delighters
- Indifferent
Read More
Top 25 Six Sigma Interview Questions and Answers 2022
Efficient operations management is vital across different industry verticals. Its requirement is also changing and evolving towards quality control which is more data-driven than before. Here, Six Sigma satisfies the growing demand, and no doubt, a certification in Six Sigma can help the candidate stand out in today's job market.
There is an ocean of opportunities from several top-notch companies across the globe. According to research, Six Sigma has a market share of over 27.7%. Hence, you choose to move ahead in your career development with Six Sigma.
If you are looking for Six Sigma interview questions for freshers/experience, then you are at the right spot. This article will be vocal about how a Six Sigma accreditation holder can answer the trickiest and most accessible questions you know subtle method that impresses your recruiters and authorities responsible for your future.
Q1. What is Six Sigma and Why is it Called So?
The basic and fundamental question a recruiting manager can ask is your expertise and knowledge on Six Sigma. Therefore, in simple terms, you can define the methodology as a technique that a company leverages to enhances its business process and quality.
By leveraging Six Sigma, companies can maximize performance and minimize process variation - helping businesses to minimize defects, boost profits, improve employee morale, and ameliorate product quality.
For the question - why it's called Six Sigma, you can answer:
To achieve the methodology, the processes of a company require to maintain their defects maximum to 3.4 DPMO, which is otherwise strenuous to achieve.
(DPMO - Defects Per Million Opportunities)
Q2. Define Few Critical Principles of Six Sigma?
- Enhancing of processes
- Prime focus on customer demands
- Effective managing of cross-functional teams
- Relying on statistical analysis to determine the best possible methods of working and finding root causes of probable issues.
- Formulate process flexibility
Q3. Define Two Sub-methodologies of Six Sigma?
- Define, Measure, Analyse, Improve, and Control (DMAIC) - A method leveraged for existing processes that are lacking behind the features and require gradual enhancement.
- Define, Measure, Analyse, Design, and Verify (DMADV) - An approach leveraged to create new products/services that match the Six Sigma quality. In case a business requires more than gradual enhancement, the DMADV process can be used.
Q4. Name Some Quality Management Tools in Six Sigma?
- CTQ Tree
- 5S
- Value Stream Mapping
- Cost-benefit Analysis
- COPIS Analysis
- SIPOC Analysis
Q5. Name a Tool that Visualizes the Possible Causes of a Given Issue?
A tool that helps in conceptualizing the possible causes of a given issue/problem is Ishikawa diagram.
Q6. What are the Different Variations Used in Six Sigma?
- Mean: This measurement is considered only for a certain application and the values are estimated. Hence, within this process, the variations are measured and compared using average mathematics techniques.
- Median: This method is done by determining the lowest and highest values and then dividing the value by 2. Within this process, the variations are estimated and compared by taking the midpoint of the set data range.
- Range: It takes into account the largest and smallest values for a certain range of data.
- Mode: This is nothing but the most occurred values in a given set of data range.
Q7. What is COPQ in Six Sigma?
Cost of Poor Quality (COPQ) is the cost caused by generating defects. This cost involves the following guidelines:
- Disposition Costs
- Extra Utility/Material Cost
- Filling the Gap Between Actual and Desired Service/Product Quality
- Loss of Revenue or Sale
- Labor Cost
- Rework Cost
However, COPQ doesn't include detection and prevention cost.
Q8. Who is Responsible for Creating or being a Part of Six Sigma Implementation Team Within a Company?
The designated individuals who are part of the Six Sigma implementation team are:
- Decision-making executives
- Master Black Belts
- Champions
- Green Belts
- Black Belts
- Yellow Belts
Q9. Define Affinity Diagram?
Affinity diagram is a tool leverage to organize ideas into subgroups by having a common relation theme to build solutions after brainstorming. To proceed, we need to have an affinity group who puts their ideas of operative quality and starts the brainstorming session.
The solutions obtained from the members of the group are aligned and segregated into homogeneous groups with an affinity heading on top. In this way, an individual visualizes the solution and list their numbers accordingly.
Q10. State the Difference Between Performance and Load Testing?
Performance Testing
- It is all about having more stress on the system checks and the overall application and system performance during the stress conditions.
- Performance testing being a superset of load testing, the testing includes load and stress testing.
Load Testing
- It is a testing process where the load limit is beyond what the customer demanded. This will help the individual whether the application can handle a specific limit.
- Load testing is about how well the program behaves and how many concurrent users are able to log in without facing any issues.
Q11. What is Cpk and Ppk?
Cpk is process capability index that estimates how close a process is running to its specification limits, relative to the natural process variability.
Ppk is the process performance index that verifies if the model that has been produced from the process is capable of meeting customer needs or CTQs.
Q12. How Six Sigma Benefits a Company and an Individual Taking the Certification?
- Helps the company to minimize the level of errors.
- Works towards the amelioration of quality assurance
- Helps candidate to develop skills and turn them to leaders
- Candidates with Six Sigma certification receives handsome remuneration and promotion compared to non-certified peers
- The process applicable for all the markets and can be executed throughout the business environments
- Work towards the enhancement of business workflow.
Q13. Explain Pareto Chart?
Pareto analysis is the most used tool in Six Sigma for quality improvement. This not only prioritize problems, but define each and every aspect. This chart sets up a clear image of what required to be dome with the problems, keeping in mind the available resources and cost.
With the help of analysis, we can optimize the process require and the cost factor. This helps us to target customer requirements better than the competitors and reach satisfaction with the feedback loop offered by the stakeholders.
Q14. How to Create a SIPOC Process Map?
Suppliers Input Process Output Customers (SIPOC) is defined as a series of consecutive steps and tasks that are executed promptly to receive a definite output.
The SIPOC process map is vital for determining the following elements:
- How the existing processes are working
- How the processes are changed and enhanced
- How the enhancement is implemented with the next stage of DMAIC.
Q15. What is DFSS in Six Sigma Process?
Define for Six Sigma (DFSS) is a process involved in designing or redesigning the product/service from scratch. One of the cases where the project is following DMAIC methodology goes into the DFSS project because of the designing related tasks.
Q16. What is Lean Six Sigma? What are its Benefits?
Lean Six Sigma is a performance enhancement method that involves eradicating activities that don't add value to the process and reducing variation. This relies on a collaborative team effort and contributes to top-notch quality and customer satisfaction.
Benefits of Lean Six Sigma are:
- Manage larger teams
- Better task prioritization
- Increase team productivity
- Eradicating defects
- Reduce time
- Ensure more efficient business workflow
Q17. Name Some Lean Six Sigma Tools?
- Regression Analysis
- Pareto Chart
- FMEA
- Value Stream Mapping
- Poka-yoke
- Kaizen
Q18. When can the Kaizen Tool be Used?
In situations where we require to implement gradual enhancement, Kaizen serves as the best solution by generating quick solutions to two pressing issues that appear to be critical. This is highly efficient in tackling intensive cross-functional collaboration, and with a swift solution, we can increment enhancement in nearly 3-5 days of execution.
Q19. Explain the Levels of Quality in Six Sigma?
Six Sigma quality levels is a method leveraged to observe and estimate the process quality. At every level of Six Sigma, a number of DPMO are defined. The perfect level of the methodology is achieved at 3.4 DPMO.
The levels of Six Sigma DPMO are:
- 6,90,000
- 3,08,537
- 66,807
- 6,210
- 233
- 3.4
Q20. What Exactly is FMEA in Six Sigma?
Failure Mode and Effect Analysis (FMEA) is leveraged to determine possible risks within the product, process, or design. After determining the risk, individuals can create a risk alleviation plan to overcome them.
Q21. What are the Pros & Cons of Zero Defect?
PROS:
- Eradicates Hidden Costs/Expenses
- Helps in Planning
- Provides Improved Value to the customer
CONS:
- Strenuous to Achieve
- Time-bound and Needs a Proactive Method
- Sound More Abstract to Most of the Organizations
- Outdated Technology
Q22. Tell Us About the Project You Have Worked On?
For this question, you must describe the project and give a summarized and good insight into it. Make sure you describe the project precisely as the recruiting manager may ask for other details related to your project.
Q23. What Factors Did You Consider Before Initiating Your Six Sigma Project?
For this question, list the significant factors that you must have considered before initiating the project. The first and foremost factor any individual would consider is the Process Stability and other factor is Process Capability.
Q24. What Were the Problems You Faced When Working with the Project and How Did You Resolve It?
If you have worked on a project, try recalling minor to major details working on the same and write down some points that are relevant and also some factors that are fundamental in Six Sigma projects. Also ensure that your answer cover the next question which is how did you resolve the issue.
Q25. What is the Kano Model?
It is one of most significant questions on Six Sigma. Kano is a product development technique leveraged to determine VoC and compares the characteristics Vs degree of satisfaction each characteristic deliver.
The technique is invented by Dr. Kano which defines the following:
- Dissatisfying
- Must-Haves
- Customer needs
- Delighters
- Indifferent
How Six Sigma Techniques Help to Reduce Stress in Daily Life
How Six Sigma Reduces Stress in Daily Life?
Although stress can be harmful to your health, it can also be beneficial. Stress motivates people to succeed, builds resilience, boosts immunity in the short term, and makes life more meaningful. However, this benefit depends on how you handle stress.
Stress can lead to various health problems, including hypertension, insomnia, and depression, making you less productive at work and causing problems in your relationships.
While there are many ways to alleviate stress, one of the most effective is Six Sigma. Here's how it works.
Yields Increased Productivity
When you are overwhelmed by tasks, you may not have enough time to relax. Being efficient means completing jobs on time and with the least effort. Six Sigma has a tool called DMAIC that can help you optimize processes in your daily life by eliminating inefficiencies.
DMAIC is an acronym. D stands for define, M stands for the measure, A stands for analyzing, I stand for improving, and C stands for control. It allows you to apply a simple framework to your daily household tasks, such as vacuuming the living room, laundry, and feeding your pets. In the end, you will have less stress on your mind.
The DMAIC methodology lets you identify unnecessary steps in a process and eliminate them so that the remaining steps become much more effective. You can apply this approach to many different methods, making it a valuable tool for organizations to improve efficiency.
Make the most of your space.
When you have a messy space, it can lead to stress. You might constantly think about what needs to be done and disrupt your relaxing ability. This low-grade stress can drain your energy, making you less productive in other areas of life.
The Six Sigma approach to creating an organized space has five steps: Sort, Set, Shine, Standardize and Sustain. For example, if you want to make your home a more relaxing place, these steps will help you get started:
Sort: Go through all your belongings and decide what should stay and go.
Set: Put the remaining items in a logical order that is efficient and convenient. For example, you may want to arrange them by type or frequency of use or where they can be stored.
Shine: This step involves putting everything back in its proper place and cleaning the house.
Standardize: Keeping your home clean and organized is easier when you have a disciplined routine. For example, you might choose to create a cleaning schedule and assign each room a day of the week or create a list of tasks by room.
Sustain: Sustain is about keeping things tidy and organized. The idea is to involve everyone in the process because everyone can help with 5S and motivate them to keep it going.
Can you use six Sigma to solve real-life issues?
Absolutely! Lean and Six Sigma provide creative ways to solve real-life problems and deal with them effectively.
It allows you to look at problems in new ways and find solutions you may not have thought of before.
Here are six ways that you can use the six-sigma methodology in your personal life:
- It helps you maximize your time in bed by minimizing distractions and improving sleep quality.
- Increase your productivity at home or the office.
- Cut unnecessary costs from your budget.
- Reducing downtime is a waste-reduction effort.
- Improve your relationships with other people, finding life more enjoyable.
- Create a balance you feel at ease with.
- Enhance your leadership capabilities and develop a sense of responsibility.
- You get to do your job the way you would like to do it, and when you are done, you can feel good about the work you have done.
Conclusion
Six Sigma helps the practitioner in reducing stress in everyday life. Jobs related to Six Sigma help reduce stress levels to a great extent. These jobs are very persuasive as they pay well and are convenient for a Six Sigma practitioner to work and remain motivated.
That's many numbers, but the key takeaway from six Sigma is that it can help reduce your stress levels and make your daily life more efficient. The more you try these ideas out and practice them, the more natural they'll become. And with that, you can increase your efficiency even further—and reduce stress along the way.
Six sigma optimization is a systematic approach to continuous improvement and managing processes more efficiently. The programs focus on reducing defects and improving quality while increasing productivity and are a great way to decrease stress left over from your day.
Six Sigma is a technique and methodology for improving business. For those who are unclear about this idea and insistence, it is time to get things clear so that you can understand how it works. Start by taking a look at what the six Sigma is. This phrase is called the DMAIC, abbreviated as a process for Six Sigma to improve and enhance the quality of work.
If you take nothing else away from this, Six Sigma is about reducing variability, not eliminating it. In other words, it should be a methodology that you confidently incorporate into your everyday routine, one which will help you effectively reduce stress levels while increasing your overall quality of life.
In the end, six Sigma can make a real difference in your life. It's not just a bunch of jargon or empty promises. It's not an impossible goal, although it takes dedication and persistence. The main takeaway from this whole piece? Focus on the process, not the end product. Let six Sigma be your guiding light to getting there, and you'll do fine.
Recommended Posts
Is It Worth Acquiring a Project Management Certification?
How Business Process Management (BPM) Relates to Six Sigma?
Prepare for Project Manager Interview | Top Questions with Answers 2022
Read More
How Six Sigma Reduces Stress in Daily Life?
Although stress can be harmful to your health, it can also be beneficial. Stress motivates people to succeed, builds resilience, boosts immunity in the short term, and makes life more meaningful. However, this benefit depends on how you handle stress.
Stress can lead to various health problems, including hypertension, insomnia, and depression, making you less productive at work and causing problems in your relationships.
While there are many ways to alleviate stress, one of the most effective is Six Sigma. Here's how it works.
Yields Increased Productivity
When you are overwhelmed by tasks, you may not have enough time to relax. Being efficient means completing jobs on time and with the least effort. Six Sigma has a tool called DMAIC that can help you optimize processes in your daily life by eliminating inefficiencies.
DMAIC is an acronym. D stands for define, M stands for the measure, A stands for analyzing, I stand for improving, and C stands for control. It allows you to apply a simple framework to your daily household tasks, such as vacuuming the living room, laundry, and feeding your pets. In the end, you will have less stress on your mind.
The DMAIC methodology lets you identify unnecessary steps in a process and eliminate them so that the remaining steps become much more effective. You can apply this approach to many different methods, making it a valuable tool for organizations to improve efficiency.
Make the most of your space.
When you have a messy space, it can lead to stress. You might constantly think about what needs to be done and disrupt your relaxing ability. This low-grade stress can drain your energy, making you less productive in other areas of life.
The Six Sigma approach to creating an organized space has five steps: Sort, Set, Shine, Standardize and Sustain. For example, if you want to make your home a more relaxing place, these steps will help you get started:
Sort: Go through all your belongings and decide what should stay and go.
Set: Put the remaining items in a logical order that is efficient and convenient. For example, you may want to arrange them by type or frequency of use or where they can be stored.
Shine: This step involves putting everything back in its proper place and cleaning the house.
Standardize: Keeping your home clean and organized is easier when you have a disciplined routine. For example, you might choose to create a cleaning schedule and assign each room a day of the week or create a list of tasks by room.
Sustain: Sustain is about keeping things tidy and organized. The idea is to involve everyone in the process because everyone can help with 5S and motivate them to keep it going.
Can you use six Sigma to solve real-life issues?
Absolutely! Lean and Six Sigma provide creative ways to solve real-life problems and deal with them effectively.
It allows you to look at problems in new ways and find solutions you may not have thought of before.
Here are six ways that you can use the six-sigma methodology in your personal life:
- It helps you maximize your time in bed by minimizing distractions and improving sleep quality.
- Increase your productivity at home or the office.
- Cut unnecessary costs from your budget.
- Reducing downtime is a waste-reduction effort.
- Improve your relationships with other people, finding life more enjoyable.
- Create a balance you feel at ease with.
- Enhance your leadership capabilities and develop a sense of responsibility.
- You get to do your job the way you would like to do it, and when you are done, you can feel good about the work you have done.
Conclusion
Six Sigma helps the practitioner in reducing stress in everyday life. Jobs related to Six Sigma help reduce stress levels to a great extent. These jobs are very persuasive as they pay well and are convenient for a Six Sigma practitioner to work and remain motivated.
That's many numbers, but the key takeaway from six Sigma is that it can help reduce your stress levels and make your daily life more efficient. The more you try these ideas out and practice them, the more natural they'll become. And with that, you can increase your efficiency even further—and reduce stress along the way.
Six sigma optimization is a systematic approach to continuous improvement and managing processes more efficiently. The programs focus on reducing defects and improving quality while increasing productivity and are a great way to decrease stress left over from your day.
Six Sigma is a technique and methodology for improving business. For those who are unclear about this idea and insistence, it is time to get things clear so that you can understand how it works. Start by taking a look at what the six Sigma is. This phrase is called the DMAIC, abbreviated as a process for Six Sigma to improve and enhance the quality of work.
If you take nothing else away from this, Six Sigma is about reducing variability, not eliminating it. In other words, it should be a methodology that you confidently incorporate into your everyday routine, one which will help you effectively reduce stress levels while increasing your overall quality of life.
In the end, six Sigma can make a real difference in your life. It's not just a bunch of jargon or empty promises. It's not an impossible goal, although it takes dedication and persistence. The main takeaway from this whole piece? Focus on the process, not the end product. Let six Sigma be your guiding light to getting there, and you'll do fine.
Recommended Posts
Is It Worth Acquiring a Project Management Certification?
How Business Process Management (BPM) Relates to Six Sigma?
Prepare for Project Manager Interview | Top Questions with Answers 2022
How Business Process Management (BPM) Relates to Six Sigma?
How Business Process Management (BPM) Relates to Six Sigma?
Businesses often stop and start reflecting on their work processes - determining different ways to improve efficiency. The Business Process Management (BPM) and Six Sigma's DMAIC methodology can help organizations find these chances.
Operational Excellence is a management ideology that stresses the application of a variety of methodologies, such as BPM and Lean Six Sigma, toward sustainable improvement.
It is based on a long-term change in organizational culture rather than just focusing on specific events.
A blend of business process management (BPM) and Lean Six Sigma can boost a company's performance in the long term. This is because BPM emphasizes process improvements and automation to drive performance improvement. At the same time, Lean Six Sigma uses statistical analysis to drive quality improvement.
Although the two methodologies are sometimes conflicting, some companies that bring them together have noted more remarkable overall improvement than before.
What is Six Sigma?
Six Sigma is a set of practices and principles used to enhance the quality of products or services and minimize expenses. At Motorola in the 1980s, they began leveraging Six Sigma to improve the quality of their products and services.
Today, many successful companies use the principles refined over the years by adding Lean principles and improving them over time.
By implementing a systematic, rigorous routine, companies can become more efficient and increase customer satisfaction, which increases profits.
Lean Six Sigma is an approach to business that gives attention to details, from the small to the large. It involves five levels of activity:
Philosophy: The commitment to zero defects means making decisions based on complex data and customer focus.
Make the customer your focus: meeting or exceeding their expectations
Metrics: To make process outcomes defect-free, we focus on statistics. Otherwise expressed as 3.4 defects per million opportunities.
Methodology: The structured approach uses business rules to model the most important metrics and then apply them to find an appropriate solution to the problems.
Processed Based: The flaws found in a product or service are due to deficiencies in the production process.
Lean Six Sigma is a method of solving business problems. It helps organizations reduce waste, become more efficient, and delight their customers.
It's also an intensive process that offers measurable results, and it's a great way to learn mathematics and statistics.
Lean Six Sigma is a great way to achieve successful business management. By following the five-step DMAIC process, businesses can achieve goals, avoid waste, and continue to improve.

During the Define phase, you will define project goals and boundaries, identify the issues that need to be addressed, and clarifies how to achieve higher sigma levels.
The Measure phase of the Six Sigma strategy helps you better understand your current processes by acquiring information and determining what works and what doesn't.
The Analyze phase of the Six Sigma quality effort aims to identify the reason for the quality problem and document the root cause with relevant data.
To address the problems identified during the previous phase, try implementing these solutions from the Improve phase.
In the Control phase, you can evaluate and monitor the previous step's results.
You need first to identify a problem in your company or industry and then examine how it came about. Next, identify methods to fix the problem. Of course, Six Sigma is a very aggressive goal. However, if your organization works at less than three Sigma now, you should understand that a shift from 2 Sigma to 3 sigma means a ten-fold improvement in defects and errors.
Business Process Management
First, let's learn a little about Business Process Management. BPM uses four steps to create better processes and improve performance. The steps are as follows:
- Documenting the process from start to finish is a great way to hold yourself accountable for your choices and the work you produce along the way.
- Keep track of the process's performance and use your findings to help the process run more smoothly.
- Make improvements to improve quality, efficiency, customer satisfaction, etc.
- Manage the process through communication, feedback, and accountability.

Business process management (BPM) is closely linked to business process automation, which depends on software applications to streamline and automate processes.
BPM enables links between multiple departments or groups at the software level that affect processes. At its highest level, BPM expands to an enterprise-wide system.
This level combines software and IT aspects with management practices to address broad structural and systemic issues within a business or organization.
Business Process Management (BPM) allows companies to measure and analyze their value chain processes systematically, thus allowing them to see how changes to these processes affect their bottom line. The Six Sigma approach is a process improvement methodology that relies on BPM and has been proven to allow companies to achieve dramatic results.
BPM and Six Sigma Combined to Maximize Efficiency in Your Organization.
BPM and Lean Six Sigma can be merged to create a powerful synergy. As a result, your entire workflow will focus on quality and operational excellence by leveraging both practices.
BPM is excellent at analyzing data and workflow and at establishing complex processes.
However, it is not as strong at giving immediate feedback about the performance of a large number of similar techniques or procedures with many variables.
Lean Six Sigma fills this gap by providing detailed information regarding process performance with its rigorous statistical methods.
Business Process Management (BPM) and Six Sigma both represent significant commitments for a company, so it's helpful to remember that you don't have to implement either business initiative in its entirety right away.
By taking on some smaller projects first and moving into more enormous transformations over time, companies can keep things manageable while still reaping the rewards of using BPM and Lean Six Sigma.
Recommended Posts
6 Steps to Become a Project Manager
Importance of Communication in Six Sigma
Project Manager & Product Manager: What's the Difference?
Career Opportunities in Six Sigma Green Belt
Read More
How Business Process Management (BPM) Relates to Six Sigma?
Businesses often stop and start reflecting on their work processes - determining different ways to improve efficiency. The Business Process Management (BPM) and Six Sigma's DMAIC methodology can help organizations find these chances.
Operational Excellence is a management ideology that stresses the application of a variety of methodologies, such as BPM and Lean Six Sigma, toward sustainable improvement.
It is based on a long-term change in organizational culture rather than just focusing on specific events.
A blend of business process management (BPM) and Lean Six Sigma can boost a company's performance in the long term. This is because BPM emphasizes process improvements and automation to drive performance improvement. At the same time, Lean Six Sigma uses statistical analysis to drive quality improvement.
Although the two methodologies are sometimes conflicting, some companies that bring them together have noted more remarkable overall improvement than before.
What is Six Sigma?
Six Sigma is a set of practices and principles used to enhance the quality of products or services and minimize expenses. At Motorola in the 1980s, they began leveraging Six Sigma to improve the quality of their products and services.
Today, many successful companies use the principles refined over the years by adding Lean principles and improving them over time.
By implementing a systematic, rigorous routine, companies can become more efficient and increase customer satisfaction, which increases profits.
Lean Six Sigma is an approach to business that gives attention to details, from the small to the large. It involves five levels of activity:
Philosophy: The commitment to zero defects means making decisions based on complex data and customer focus.
Make the customer your focus: meeting or exceeding their expectations
Metrics: To make process outcomes defect-free, we focus on statistics. Otherwise expressed as 3.4 defects per million opportunities.
Methodology: The structured approach uses business rules to model the most important metrics and then apply them to find an appropriate solution to the problems.
Processed Based: The flaws found in a product or service are due to deficiencies in the production process.
Lean Six Sigma is a method of solving business problems. It helps organizations reduce waste, become more efficient, and delight their customers.
It's also an intensive process that offers measurable results, and it's a great way to learn mathematics and statistics.
Lean Six Sigma is a great way to achieve successful business management. By following the five-step DMAIC process, businesses can achieve goals, avoid waste, and continue to improve.
During the Define phase, you will define project goals and boundaries, identify the issues that need to be addressed, and clarifies how to achieve higher sigma levels.
The Measure phase of the Six Sigma strategy helps you better understand your current processes by acquiring information and determining what works and what doesn't.
The Analyze phase of the Six Sigma quality effort aims to identify the reason for the quality problem and document the root cause with relevant data.
To address the problems identified during the previous phase, try implementing these solutions from the Improve phase.
In the Control phase, you can evaluate and monitor the previous step's results.
You need first to identify a problem in your company or industry and then examine how it came about. Next, identify methods to fix the problem. Of course, Six Sigma is a very aggressive goal. However, if your organization works at less than three Sigma now, you should understand that a shift from 2 Sigma to 3 sigma means a ten-fold improvement in defects and errors.
Business Process Management
First, let's learn a little about Business Process Management. BPM uses four steps to create better processes and improve performance. The steps are as follows:
- Documenting the process from start to finish is a great way to hold yourself accountable for your choices and the work you produce along the way.
- Keep track of the process's performance and use your findings to help the process run more smoothly.
- Make improvements to improve quality, efficiency, customer satisfaction, etc.
- Manage the process through communication, feedback, and accountability.
Business process management (BPM) is closely linked to business process automation, which depends on software applications to streamline and automate processes.
BPM enables links between multiple departments or groups at the software level that affect processes. At its highest level, BPM expands to an enterprise-wide system.
This level combines software and IT aspects with management practices to address broad structural and systemic issues within a business or organization.
Business Process Management (BPM) allows companies to measure and analyze their value chain processes systematically, thus allowing them to see how changes to these processes affect their bottom line. The Six Sigma approach is a process improvement methodology that relies on BPM and has been proven to allow companies to achieve dramatic results.
BPM and Six Sigma Combined to Maximize Efficiency in Your Organization.
BPM and Lean Six Sigma can be merged to create a powerful synergy. As a result, your entire workflow will focus on quality and operational excellence by leveraging both practices.
BPM is excellent at analyzing data and workflow and at establishing complex processes.
However, it is not as strong at giving immediate feedback about the performance of a large number of similar techniques or procedures with many variables.
Lean Six Sigma fills this gap by providing detailed information regarding process performance with its rigorous statistical methods.
Business Process Management (BPM) and Six Sigma both represent significant commitments for a company, so it's helpful to remember that you don't have to implement either business initiative in its entirety right away.
By taking on some smaller projects first and moving into more enormous transformations over time, companies can keep things manageable while still reaping the rewards of using BPM and Lean Six Sigma.
Recommended Posts
6 Steps to Become a Project Manager
Importance of Communication in Six Sigma
Project Manager & Product Manager: What's the Difference?
Career Opportunities in Six Sigma Green Belt
Importance of Communication in Six Sigma for Success!!!
Importance of Communication in Six Sigma
When Six Sigma is deployed, you'll have to deal with many organizational changes. Unfortunately, productivity and morale often suffer when there's a lot of difference. In addition, adapting to the new ways and learning to live with the "new normal" can bring out some fear in people. In those situations, communication becomes more critical than ever.
Communication during a Six Sigma project is vital to its success because the process requires a significant commitment from everyone in the organization. Management can overcome resistance to the change by communicating clearly and openly about both the benefits and the challenges of applying Six Sigma.
Six Sigma is a methodology that helps companies become more successful by improving productivity and eliminating problems and defects. For the program to be successful, businesses must communicate well. To establish six Sigma as a culture or strategy, everyone must be active and engaged in the processes and success of the company.
User support
By identifying the needs and goals of customers, companies can increase their revenues. This requires good communication between the company and the customer. Employees need to be skilled at communicating with customers to obtain information passed on to other company employees.
To sell a company's goods and services, a sales team must communicate the features and benefits of those products and services as clearly as possible. This will attract new customers.
Quantity and Quality
To ensure effective communication and a proper flow of information, organizations need to fix their issues related to transmitting messages and reports between employees and their managers. Simple, practical techniques, such as highlighting key points in documents, can make it easier for employees to do their jobs.
When Six Sigma is implemented in a company without fixing the communication problems, it will add to its problems. So first and foremost, companies must fix their communication problems before implementing Six Sigma.
Communication skills can help companies adopt training and protocols to assist their employees in explaining new ideas more efficiently. This will enable employees to create solutions for problems rather than creating problems for other employees.
Charts and Analysis
Six Sigma relies on statistics and mathematics to track progress and efficiently solve problems. It provides a concrete way to identify errors and improve processes. It also reduces speculation and useless planning conversations by using data to support arguments.
A team needs to be able to communicate to serve the clients well. The team needs to be able to explain how to implement the solutions and what each key is for. This way, every team member understands how every client relates to the company’s goals.
Since Six Sigma involves a commitment from every employee in an organization, communication skills training is essential for everyone to support the efforts of other employees and themselves.
How Six Sigma Benefits the Organization?
Six Sigma has proved to be a successful tool for organizations to recognize issues, remove the roots of mistakes or failures, and boost their business processes. Since its invention in 1986 by Motorola Company, Six Sigma has been broadly taken up by firms in different industries. Offered that emerging companies are listening and pleasing to client demands, the already developed companies may use Six Sigma concepts in accomplishing the never-ending objectives of enhancing the quality and reducing costs. Thus, six Sigma helps the organization in the following way:
Improving Your Time Management Skills
Time management is a critical element of business, with every minute representing money that can be made or lost. Six Sigma implementation helps people better manage their time, which generally leads to increased productivity. When Six Sigma principles are applied, employees present a set of goals that they strive to achieve.
Waste Reduction
Delays in production and high operation costs can often lead to waste. By managing waste, you ensure that resources are used efficiently and effectively. As a result, you can eliminate waste, reduce the possibility that your company will fade away, and improve processes that add value for the customer.
Boost Employee Morale
All companies want to have qualified and efficient staff. Motivation is one of the most effective methods for accomplishing this. When employees are motivated, they are more productive. Many companies have seen an increase in productivity by as much as 50% when they engage their employees fully. Organizations can create systems that motivate employees to perform their duties with Six Sigma tools. However, not all businesses are the same; what works for one company might not work for another company. Thus, Six Sigma will customize a system that motivates your employees specifically.
Generate Customer Loyalty
The demand for various products and services has caused customers to become very demanding and selective. In addition, the increasing globalization of companies has forced them to distinguish themselves from competitors by providing quality in their products and services at a reasonable price. Therefore, Six Sigma processes and methods are necessary for creating customer satisfaction. Furthermore, treating the quality defects that customers notice will show them that the organization is willing to improve to meet their needs.
Recommended Post
6 Steps to Become a Project Manager
Career Opportunities in Six Sigma Green Belt
Project Manager & Product Manager: What's the Difference?
PMP Certification: Course Details & Exam Costs
Is PMP the Right Choice for the Construction Industry?
Read More
Importance of Communication in Six Sigma
When Six Sigma is deployed, you'll have to deal with many organizational changes. Unfortunately, productivity and morale often suffer when there's a lot of difference. In addition, adapting to the new ways and learning to live with the "new normal" can bring out some fear in people. In those situations, communication becomes more critical than ever.
Communication during a Six Sigma project is vital to its success because the process requires a significant commitment from everyone in the organization. Management can overcome resistance to the change by communicating clearly and openly about both the benefits and the challenges of applying Six Sigma.
Six Sigma is a methodology that helps companies become more successful by improving productivity and eliminating problems and defects. For the program to be successful, businesses must communicate well. To establish six Sigma as a culture or strategy, everyone must be active and engaged in the processes and success of the company.
User support
By identifying the needs and goals of customers, companies can increase their revenues. This requires good communication between the company and the customer. Employees need to be skilled at communicating with customers to obtain information passed on to other company employees.
To sell a company's goods and services, a sales team must communicate the features and benefits of those products and services as clearly as possible. This will attract new customers.
Quantity and Quality
To ensure effective communication and a proper flow of information, organizations need to fix their issues related to transmitting messages and reports between employees and their managers. Simple, practical techniques, such as highlighting key points in documents, can make it easier for employees to do their jobs.
When Six Sigma is implemented in a company without fixing the communication problems, it will add to its problems. So first and foremost, companies must fix their communication problems before implementing Six Sigma.
Communication skills can help companies adopt training and protocols to assist their employees in explaining new ideas more efficiently. This will enable employees to create solutions for problems rather than creating problems for other employees.
Charts and Analysis
Six Sigma relies on statistics and mathematics to track progress and efficiently solve problems. It provides a concrete way to identify errors and improve processes. It also reduces speculation and useless planning conversations by using data to support arguments.
A team needs to be able to communicate to serve the clients well. The team needs to be able to explain how to implement the solutions and what each key is for. This way, every team member understands how every client relates to the company’s goals.
Since Six Sigma involves a commitment from every employee in an organization, communication skills training is essential for everyone to support the efforts of other employees and themselves.
How Six Sigma Benefits the Organization?
Six Sigma has proved to be a successful tool for organizations to recognize issues, remove the roots of mistakes or failures, and boost their business processes. Since its invention in 1986 by Motorola Company, Six Sigma has been broadly taken up by firms in different industries. Offered that emerging companies are listening and pleasing to client demands, the already developed companies may use Six Sigma concepts in accomplishing the never-ending objectives of enhancing the quality and reducing costs. Thus, six Sigma helps the organization in the following way:
Improving Your Time Management Skills
Time management is a critical element of business, with every minute representing money that can be made or lost. Six Sigma implementation helps people better manage their time, which generally leads to increased productivity. When Six Sigma principles are applied, employees present a set of goals that they strive to achieve.
Waste Reduction
Delays in production and high operation costs can often lead to waste. By managing waste, you ensure that resources are used efficiently and effectively. As a result, you can eliminate waste, reduce the possibility that your company will fade away, and improve processes that add value for the customer.
Boost Employee Morale
All companies want to have qualified and efficient staff. Motivation is one of the most effective methods for accomplishing this. When employees are motivated, they are more productive. Many companies have seen an increase in productivity by as much as 50% when they engage their employees fully. Organizations can create systems that motivate employees to perform their duties with Six Sigma tools. However, not all businesses are the same; what works for one company might not work for another company. Thus, Six Sigma will customize a system that motivates your employees specifically.
Generate Customer Loyalty
The demand for various products and services has caused customers to become very demanding and selective. In addition, the increasing globalization of companies has forced them to distinguish themselves from competitors by providing quality in their products and services at a reasonable price. Therefore, Six Sigma processes and methods are necessary for creating customer satisfaction. Furthermore, treating the quality defects that customers notice will show them that the organization is willing to improve to meet their needs.
Recommended Post
6 Steps to Become a Project Manager
Career Opportunities in Six Sigma Green Belt
Project Manager & Product Manager: What's the Difference?
PMP Certification: Course Details & Exam Costs
Is PMP the Right Choice for the Construction Industry?
Explore Career Opportunities with Six Sigma Green Belt
The Six Sigma Green Belt Certification is a highly-prized qualification prerequisite to many Six Sigma Black Belt projects. The Green Belt denotes that an employee has the necessary skill sets to implement the Six Sigma methodology.
Green Belt certification educates professionals on the tools necessary to implement a proven improvement methodology called “Define-Measure-Analyze-Improve-Control.”
In addition, the individual earning a Green Belt certification is recognized as someone who can effectively use Lean and Six Sigma to streamline processes and reduce waste and variances.
Professionals with a Six Sigma Green Belt certification should have a solid understanding of the fundamental principles of Six Sigma and be able to apply those principles daily.
Mid-level project managers, process engineers, specialists, and industrial engineers are all positions suitable for Green Belts.
The Six Sigma Green Belt is an expert in applying daily concepts to improve business operations. Many firms have found that the Green Belt can help improve many different areas of their business operations.
In addition, there are many career opportunities for the Six Sigma Green Belt because many companies hire people who can apply Six Sigma approaches to improve productivity and save money.
What is Lean Six Sigma Certification?
Six Sigma describes a Six Sigma Green Belt as someone who “has been trained on the improvement methodology of Six Sigma and will lead a process improvement or quality improvement team as part of their full-time job.”
Green Belt certification has significant value in the workplace. Certified professionals should take advantage of their position to enhance customer satisfaction and improve processes.
Companies may elect to promote Green Belt certification employees to a Black Belt position. However, professionals typically fill these positions with Six Sigma Black Belt certification.
The Need for Lean Six Sigma Green Belts
The Society for Human Resource Management says that Six Sigma data processing and process evaluation can help minimize HR costs and can be used to attract employees or optimize workplace satisfaction.
Employers seeking people with Six Sigma skills include many in the automotive, electronics, healthcare, manufacturing, and logistics fields.
In addition, green Belt certification is a must for many workers in process engineering, quality control, and exhibition careers. Some of the top companies looking to fill Six Sigma positions include Hershey Company, IBM, Wells Fargo, Siemens, etc.
Six Sigma Green Belt Careers by Job Title
Green Belts are problem-solvers who focus on quality, cost-effectiveness, and efficiency. Green Belt jobs involve analyzing data and improving processes. Jobs for professionals with Six Sigma Green Belt certification include:
Process engineers support a company's leadership in evaluating internal processes. Their goal is to make processes more efficient so their organization can produce high-quality products. The median salary for a process engineer in 2016 was $70,876.
Continuous improvement specialists collect data and conduct root cause analysis to identify and coordinate ongoing improvement initiatives. Then, they make recommendations and share their findings with senior management.
Six Sigma consultants use project management skills and business acumen to analyze current processes, challenge business assumptions, and recommend changes to improve workflow and reduce waste.
Operational excellence managers work with team members to manage an organization's Lean Six Sigma initiatives. As a result, they play an essential role in the success of improvement projects.
Quality engineers are responsible for ensuring that the products their companies manufacture meet customer standards. In addition, they usually take part in day-to-day operations and long-term improvement planning.
Industrial engineers help companies streamline their production processes, increase employee productivity and reduce costs by identifying ways to use employees, equipment, and other resources more efficiently.
Manufacturing engineers develop and optimize the processes used to design, build, and ship products such as cars and electronics. They use their knowledge of lean methodology to troubleshoot problems and continuously improve the manufacturing process.
Project managers track schedules, budgets, and other project statuses. They also use Six Sigma knowledge to ensure that projects are completed effectively and efficiently.
Mechanical engineers focus on new product development and the improvement of existing products. They use their knowledge of Six Sigma to create product concepts, design equipment, and test products.
As a Reliability Engineer, you will be working on developing reliability test plans for a company's products and working with internal teams and customers to remedy any reliability concerns.
Conclusion
A Six Sigma Green Belt can use its skills to take on a wide range of quality management roles in many fields. Many experienced quality professionals are looking for jobs as Green Belts because they know they will be able to make a meaningful difference in an organization, doing projects that create real company-wide impact.
People with Six Sigma Green Belt certification enhance their job prospects by demonstrating that they have the skills and training to help businesses lower costs and improve performance across departments and locations.
Six Sigma is an advanced application of statistical methods that allows you to test and improve your processes' quality.
Although it does require a particular skill set, it offers better opportunities for employment for people who already have relevant experience and want to advance in their careers.
Innovation and improvement are on the rise. Driven by customers who want better products and services, companies are starting to figure out ways to create better performance.
In addition, many companies want their employees to understand why it is essential to measure and improve performance.
This is a demanding job; being a sigma green belt, you will get to work on anything and everything about project management.
But the pay and the experience of working in such a big organization will be rewarding. I suggest studying hard and getting into one of the best colleges. You can only get a job in six sigma green belt after graduation.
Recommended Posts
Project Manager & Product Manager: What's the Difference?
How much time do you need to study for the PMP Exam?
PMP Certification: Course Details & Exam Costs
Is PMP the Right Choice for the Construction Industry?
The company conducts both Instructor-led Classroom training workshops and Instructor-led Live Online Training sessions for learners from across the United States and worldwide.
Don't hesitate to get in touch with Us for more information about our professional certification training courses to accelerate your career in the best possible way.
Connect with iCert Global on:
LinkedIn | Facebook | Twitter | Instagram | YouTube | Pinterest
Subscribe to our YouTube Channel | Subscribe to our Telegram Channel
Professional Certification Training Courses from iCert Global
Quality Management Training by iCert Global:
-Lean Six Sigma Yellow Belt (LSSYB) Certification Training Courses
-Lean Six Sigma Green Belt (LSSGB) Certification Training Courses
-Lean Six Sigma Black Belt (LSSBB) Certification Training Courses
Scrum Training by iCert Global:
-CSM (Certified ScrumMaster) Certification Training Courses
Agile Training by iCert Global:
PMI-ACP (Agile Certified Professional) Certification Training Courses
DevOps Training by iCert Global:
-DevOps Certification Training Courses
Business Analysis Training by iCert Global:
-ECBA (Entry Certificate in Business Analysis) Certification Training Courses
-CCBA (Certificate of Capability in Business Analysis) Certification Training Courses
-CBAP (Certified Business Analysis Professional) Certification Training Courses
Read More
The Six Sigma Green Belt Certification is a highly-prized qualification prerequisite to many Six Sigma Black Belt projects. The Green Belt denotes that an employee has the necessary skill sets to implement the Six Sigma methodology.
Green Belt certification educates professionals on the tools necessary to implement a proven improvement methodology called “Define-Measure-Analyze-Improve-Control.”
In addition, the individual earning a Green Belt certification is recognized as someone who can effectively use Lean and Six Sigma to streamline processes and reduce waste and variances.
Professionals with a Six Sigma Green Belt certification should have a solid understanding of the fundamental principles of Six Sigma and be able to apply those principles daily.
Mid-level project managers, process engineers, specialists, and industrial engineers are all positions suitable for Green Belts.
The Six Sigma Green Belt is an expert in applying daily concepts to improve business operations. Many firms have found that the Green Belt can help improve many different areas of their business operations.
In addition, there are many career opportunities for the Six Sigma Green Belt because many companies hire people who can apply Six Sigma approaches to improve productivity and save money.
What is Lean Six Sigma Certification?
Six Sigma describes a Six Sigma Green Belt as someone who “has been trained on the improvement methodology of Six Sigma and will lead a process improvement or quality improvement team as part of their full-time job.”
Green Belt certification has significant value in the workplace. Certified professionals should take advantage of their position to enhance customer satisfaction and improve processes.
Companies may elect to promote Green Belt certification employees to a Black Belt position. However, professionals typically fill these positions with Six Sigma Black Belt certification.
The Need for Lean Six Sigma Green Belts
The Society for Human Resource Management says that Six Sigma data processing and process evaluation can help minimize HR costs and can be used to attract employees or optimize workplace satisfaction.
Employers seeking people with Six Sigma skills include many in the automotive, electronics, healthcare, manufacturing, and logistics fields.
In addition, green Belt certification is a must for many workers in process engineering, quality control, and exhibition careers. Some of the top companies looking to fill Six Sigma positions include Hershey Company, IBM, Wells Fargo, Siemens, etc.
Six Sigma Green Belt Careers by Job Title
Green Belts are problem-solvers who focus on quality, cost-effectiveness, and efficiency. Green Belt jobs involve analyzing data and improving processes. Jobs for professionals with Six Sigma Green Belt certification include:
Process engineers support a company's leadership in evaluating internal processes. Their goal is to make processes more efficient so their organization can produce high-quality products. The median salary for a process engineer in 2016 was $70,876.
Continuous improvement specialists collect data and conduct root cause analysis to identify and coordinate ongoing improvement initiatives. Then, they make recommendations and share their findings with senior management.
Six Sigma consultants use project management skills and business acumen to analyze current processes, challenge business assumptions, and recommend changes to improve workflow and reduce waste.
Operational excellence managers work with team members to manage an organization's Lean Six Sigma initiatives. As a result, they play an essential role in the success of improvement projects.
Quality engineers are responsible for ensuring that the products their companies manufacture meet customer standards. In addition, they usually take part in day-to-day operations and long-term improvement planning.
Industrial engineers help companies streamline their production processes, increase employee productivity and reduce costs by identifying ways to use employees, equipment, and other resources more efficiently.
Manufacturing engineers develop and optimize the processes used to design, build, and ship products such as cars and electronics. They use their knowledge of lean methodology to troubleshoot problems and continuously improve the manufacturing process.
Project managers track schedules, budgets, and other project statuses. They also use Six Sigma knowledge to ensure that projects are completed effectively and efficiently.
Mechanical engineers focus on new product development and the improvement of existing products. They use their knowledge of Six Sigma to create product concepts, design equipment, and test products.
As a Reliability Engineer, you will be working on developing reliability test plans for a company's products and working with internal teams and customers to remedy any reliability concerns.
Conclusion
A Six Sigma Green Belt can use its skills to take on a wide range of quality management roles in many fields. Many experienced quality professionals are looking for jobs as Green Belts because they know they will be able to make a meaningful difference in an organization, doing projects that create real company-wide impact.
People with Six Sigma Green Belt certification enhance their job prospects by demonstrating that they have the skills and training to help businesses lower costs and improve performance across departments and locations.
Six Sigma is an advanced application of statistical methods that allows you to test and improve your processes' quality.
Although it does require a particular skill set, it offers better opportunities for employment for people who already have relevant experience and want to advance in their careers.
Innovation and improvement are on the rise. Driven by customers who want better products and services, companies are starting to figure out ways to create better performance.
In addition, many companies want their employees to understand why it is essential to measure and improve performance.
This is a demanding job; being a sigma green belt, you will get to work on anything and everything about project management.
But the pay and the experience of working in such a big organization will be rewarding. I suggest studying hard and getting into one of the best colleges. You can only get a job in six sigma green belt after graduation.
Recommended Posts
Project Manager & Product Manager: What's the Difference?
How much time do you need to study for the PMP Exam?
PMP Certification: Course Details & Exam Costs
Is PMP the Right Choice for the Construction Industry?
The company conducts both Instructor-led Classroom training workshops and Instructor-led Live Online Training sessions for learners from across the United States and worldwide.
Don't hesitate to get in touch with Us for more information about our professional certification training courses to accelerate your career in the best possible way.
Connect with iCert Global on:
LinkedIn | Facebook | Twitter | Instagram | YouTube | Pinterest
Subscribe to our YouTube Channel | Subscribe to our Telegram Channel
Professional Certification Training Courses from iCert Global
Quality Management Training by iCert Global:
-Lean Six Sigma Yellow Belt (LSSYB) Certification Training Courses
-Lean Six Sigma Green Belt (LSSGB) Certification Training Courses
-Lean Six Sigma Black Belt (LSSBB) Certification Training Courses
Scrum Training by iCert Global:
-CSM (Certified ScrumMaster) Certification Training Courses
Agile Training by iCert Global:
PMI-ACP (Agile Certified Professional) Certification Training Courses
DevOps Training by iCert Global:
-DevOps Certification Training Courses
Business Analysis Training by iCert Global:
-ECBA (Entry Certificate in Business Analysis) Certification Training Courses
-CCBA (Certificate of Capability in Business Analysis) Certification Training Courses
-CBAP (Certified Business Analysis Professional) Certification Training Courses
PMP vs. Six Sigma: Which Certification Suits You Best!!
PMP Vs Six Sigma: Which One to Choose?
If you are looking for ways to challenge your potential and advance your career, achieving certification is definitely what you need to put yourself ahead of others.
Certification is being a 'THING' among the industrial sector these days. So why do people do certification courses? Either they want to upgrade their skills or are looking for a more exemplary job career.
In today's blog, we will see the two most widely recognized certifications - PMP and Six Sigma similarities, differences, how to obtain them, and which one to choose.
As these certifications depend on business success rates, employers worldwide list either or both as job requirements. Moreover, both being highly-valued credentials, they can also be expensive and need months of preparation.
TABLE OF CONTENTS
PMP Certification
- How to Earn PMP Credential?
Six Sigma Certification
- How to Earn Six Sigma Credential?
PMP Vs Six Sigma: Differences
Benefits of PMP & Six Sigma Certifications
PMP Vs Six Sigma: Which One to Choose?
PMP Certification
What is PMP certification?
The Project Management Professional (PMP) is a globally renowned and prestigious certification awarded by the Project Management Institute (PMI). The credential is designed for professionals to test their skills in managing the project priorities - People, Process, and Business.
Now, how do you become one?
To be a certified PMP professional, you must pass the credential test. The exam deals with the Introduction to the PMBOK Guide and Project Management Process Groups.
With the new PMP format, including predictive, agile, and hybrid practices, added across the three exam domains (People, Process, and Business), the certifications prove project leadership experience and proficiency in the working environment.
However, for project management aspirants, there are particular prerequisites you must know before you appear for the credential test. ‘How to earn the PMP credential’ will be mentioned in this blog. So, stay till the end.
What’s the PMP exam format?
- The PMP certification exam consists of:
- No. of questions - 180
- Duration: 230 minutes
- Question type: a combination of MCQs, multiple responses, matching, limited fill-in-the-blanks, and hotspot.
You may also like: Top 50 PMP Questions with Answers 2022
How to Earn PMP Credential?
PMP certification warrants a certain knowledge level in the project management area. In addition, organizations give more value to PMP-certified professionals than other certification holders because PMI has a very rigorous application and audit process.
As you know, PMI administers the PMP credential exam; let’s see the two possible requirements where you will be eligible for the test:
- Secondary degree (high school diploma, associate’s degree or the global equivalent)
- 7,500 hours leading and directing projects
- 35 hours of project management education or CAPM certification
OR
- 4-year degree (bachelor’s degree or global equivalent)
- 4,500 hours leading and directing projects
- 35 hours of project management education or CAPM certification
You may also like: Can You get PMP Without Experience?
Six Sigma Certification
Six Sigma is one of the most significant data-driven practices.
What is Six Sigma?
Six Sigma is an industrial engineering quality approach based on quality control and statistical analysis. The methodology focuses on minimizing defects, eradicating wasteful processes, cutting expenses, and increasing efficiency and productivity.
What are Six Sigma phases?
The primary method of Six Sigma is Define, Measure, Analyze, Improve & Control (DMAIC) cycle that includes:
- Define: Identify the issue that needs to be resolved and identify the scope and objective of the project.
- Measure: Gather data to understand the effect of the issue and present state.
- Analyze: Perform root-cause analysis with the gathered data to understand the real reason for issue occurrence.
- Improve: Determine solutions to the issue and execute to make processes more efficient.
- Control: Monitor the effect of solutions and align strategies to maintain results or outcomes.
What are different Six Sigma belts?
- White Belt
- Yellow Belt
- Green Belt
- Black Belt
How to Earn Six Sigma Credential?
As for the Lean Six Sigma (LSS) certification test, there is no single certifying entity. What's more, is its different certification levels with varying educational prerequisites.
The different types of certifications are as follows:
- White Belt: It is an initial Six Sigma certification, where candidates get an insightful understanding of the fundamental level of the Six Sigma practices. With this basic level, White Belt holders participate in projects and problem-solving tasks related to waste minimization and quality control.
- Yellow Belt: During Yellow Belt training, candidates focus on the Six Sigma theory, including necessary tools and procedures to enhance processes. These individuals may also guide minimal scope projects and assist managers of top belt levels.
- Green Belt: Once you proceed to the Green Belt, you are a Six Sigma expert. Here, you will learn more about data gathering or collection and participate in the methodology initiatives. This training is valuable for professionals in project management, healthcare admin, or finance management, giving them an understanding of performance metrics and tools.
- Black Belt: Here, you are responsible for managing White, Yellow, and Green Belts. During the training, professionals exhibit what they have learned and achieve hands-on experience by performing a project for a non-profit organization or their employer.
PMP Vs Six Sigma: Differences
The PMP exam demonstrates individual project management skills through the PMI. The certification focuses on a set of concepts and skills. The credential covers the five process groups:
- Initiating
- Planning
- Executing
- Monitoring
- Controlling
- Closing that is required to perform project management functions.
There are also ten PMP knowledge areas:
- Scope management
- Cost management
- Integration management
- Risk management
- Schedule management
- Procurement management
- Quality management
- Communications management
- Stakeholder management
- Resource management.
Each knowledge area has its own process set, spread across the five process groups.
PMP certification has prerequisites: project managers must have specific knowledge and skills.
Six Sigma is the process of enhancing business workflows through quality engineering. The methodology uses data collection tools, statistical analysis, and more to improve 100 percent of process results at minimized costs.
Six Sigma focuses on defect minimization and eradicating wasteful processes, sales, and production. Therefore, the certification prerequisite is that individuals have a piece of specific knowledge to enhance operations.
Benefits of PMP & Six Sigma Certifications
Benefits of PMP are:
- Assess and mitigate the risks
- Prevents project failures
- Helps in determining and interacting the issue areas
- Helps managers to understand the project and its scope
- Higher pay scale
Benefits of Six Sigma are:
- Enhance business procedures and sustain quality improvement
- Excellent pay scale
- Helps organizations to minimize risk and eradicate defects and flaws
- Ensure compliance
- Obtain hands-on experience in quality management
- Promotion to managerial roles
PMP Vs Six Sigma: Which One to Choose?
If you are in a dilemma choosing between PMP or Six Sigma, remember these certifications' positive and negative sides. Depending on the career objective you have set, make an efficient choice. Remember that no certificate is better than the other, as they focus on different areas.
Whether you choose the PMP certification over Six Sigma certification depends on various factors. However, the choice is simple, i.e., if you're an aspiring project manager, it's best to get PMP certification, and if you're looking for a career in quality control, take Six Sigma certification.
Still, having doubts on which one to pursue? Then choose a training provider to walk you through the decision process. With the right training provider, you will have a basic idea of who should opt for which certification.
Take the first step towards exploring an opportunity to be either a global project management professional or a quality control/assurance professional. Prepare for the PMP or Six Sigma certification and fast track your career. Join Now!
Please fill in the enquiry form or call now on +1(713)-287-1355 or e-mail info {at} icertglobal {dot} com for our training consultant to understand your training requirements and guide you with an optimum way to achieve your learning objectives.
For more information about our PMP and Six Sigma certification, please visit us at https://www.icertglobal.com/
Read More
PMP Vs Six Sigma: Which One to Choose?
If you are looking for ways to challenge your potential and advance your career, achieving certification is definitely what you need to put yourself ahead of others.
Certification is being a 'THING' among the industrial sector these days. So why do people do certification courses? Either they want to upgrade their skills or are looking for a more exemplary job career.
In today's blog, we will see the two most widely recognized certifications - PMP and Six Sigma similarities, differences, how to obtain them, and which one to choose.
As these certifications depend on business success rates, employers worldwide list either or both as job requirements. Moreover, both being highly-valued credentials, they can also be expensive and need months of preparation.
TABLE OF CONTENTS PMP Certification
Six Sigma Certification
PMP Vs Six Sigma: Differences Benefits of PMP & Six Sigma Certifications PMP Vs Six Sigma: Which One to Choose? |
PMP Certification
What is PMP certification?
The Project Management Professional (PMP) is a globally renowned and prestigious certification awarded by the Project Management Institute (PMI). The credential is designed for professionals to test their skills in managing the project priorities - People, Process, and Business.
Now, how do you become one?
To be a certified PMP professional, you must pass the credential test. The exam deals with the Introduction to the PMBOK Guide and Project Management Process Groups.
With the new PMP format, including predictive, agile, and hybrid practices, added across the three exam domains (People, Process, and Business), the certifications prove project leadership experience and proficiency in the working environment.
However, for project management aspirants, there are particular prerequisites you must know before you appear for the credential test. ‘How to earn the PMP credential’ will be mentioned in this blog. So, stay till the end.
What’s the PMP exam format?
- The PMP certification exam consists of:
- No. of questions - 180
- Duration: 230 minutes
- Question type: a combination of MCQs, multiple responses, matching, limited fill-in-the-blanks, and hotspot.
You may also like: Top 50 PMP Questions with Answers 2022
How to Earn PMP Credential?
PMP certification warrants a certain knowledge level in the project management area. In addition, organizations give more value to PMP-certified professionals than other certification holders because PMI has a very rigorous application and audit process.
As you know, PMI administers the PMP credential exam; let’s see the two possible requirements where you will be eligible for the test:
- Secondary degree (high school diploma, associate’s degree or the global equivalent)
- 7,500 hours leading and directing projects
- 35 hours of project management education or CAPM certification
OR
- 4-year degree (bachelor’s degree or global equivalent)
- 4,500 hours leading and directing projects
- 35 hours of project management education or CAPM certification
You may also like: Can You get PMP Without Experience?
Six Sigma Certification
Six Sigma is one of the most significant data-driven practices.
What is Six Sigma?
Six Sigma is an industrial engineering quality approach based on quality control and statistical analysis. The methodology focuses on minimizing defects, eradicating wasteful processes, cutting expenses, and increasing efficiency and productivity.
What are Six Sigma phases?
The primary method of Six Sigma is Define, Measure, Analyze, Improve & Control (DMAIC) cycle that includes:
- Define: Identify the issue that needs to be resolved and identify the scope and objective of the project.
- Measure: Gather data to understand the effect of the issue and present state.
- Analyze: Perform root-cause analysis with the gathered data to understand the real reason for issue occurrence.
- Improve: Determine solutions to the issue and execute to make processes more efficient.
- Control: Monitor the effect of solutions and align strategies to maintain results or outcomes.
What are different Six Sigma belts?
- White Belt
- Yellow Belt
- Green Belt
- Black Belt
How to Earn Six Sigma Credential?
As for the Lean Six Sigma (LSS) certification test, there is no single certifying entity. What's more, is its different certification levels with varying educational prerequisites.
The different types of certifications are as follows:
- White Belt: It is an initial Six Sigma certification, where candidates get an insightful understanding of the fundamental level of the Six Sigma practices. With this basic level, White Belt holders participate in projects and problem-solving tasks related to waste minimization and quality control.
- Yellow Belt: During Yellow Belt training, candidates focus on the Six Sigma theory, including necessary tools and procedures to enhance processes. These individuals may also guide minimal scope projects and assist managers of top belt levels.
- Green Belt: Once you proceed to the Green Belt, you are a Six Sigma expert. Here, you will learn more about data gathering or collection and participate in the methodology initiatives. This training is valuable for professionals in project management, healthcare admin, or finance management, giving them an understanding of performance metrics and tools.
- Black Belt: Here, you are responsible for managing White, Yellow, and Green Belts. During the training, professionals exhibit what they have learned and achieve hands-on experience by performing a project for a non-profit organization or their employer.
PMP Vs Six Sigma: Differences
The PMP exam demonstrates individual project management skills through the PMI. The certification focuses on a set of concepts and skills. The credential covers the five process groups:
- Initiating
- Planning
- Executing
- Monitoring
- Controlling
- Closing that is required to perform project management functions.
There are also ten PMP knowledge areas:
- Scope management
- Cost management
- Integration management
- Risk management
- Schedule management
- Procurement management
- Quality management
- Communications management
- Stakeholder management
- Resource management.
Each knowledge area has its own process set, spread across the five process groups.
PMP certification has prerequisites: project managers must have specific knowledge and skills.
Six Sigma is the process of enhancing business workflows through quality engineering. The methodology uses data collection tools, statistical analysis, and more to improve 100 percent of process results at minimized costs.
Six Sigma focuses on defect minimization and eradicating wasteful processes, sales, and production. Therefore, the certification prerequisite is that individuals have a piece of specific knowledge to enhance operations.
Benefits of PMP & Six Sigma Certifications
Benefits of PMP are:
- Assess and mitigate the risks
- Prevents project failures
- Helps in determining and interacting the issue areas
- Helps managers to understand the project and its scope
- Higher pay scale
Benefits of Six Sigma are:
- Enhance business procedures and sustain quality improvement
- Excellent pay scale
- Helps organizations to minimize risk and eradicate defects and flaws
- Ensure compliance
- Obtain hands-on experience in quality management
- Promotion to managerial roles
PMP Vs Six Sigma: Which One to Choose?
If you are in a dilemma choosing between PMP or Six Sigma, remember these certifications' positive and negative sides. Depending on the career objective you have set, make an efficient choice. Remember that no certificate is better than the other, as they focus on different areas.
Whether you choose the PMP certification over Six Sigma certification depends on various factors. However, the choice is simple, i.e., if you're an aspiring project manager, it's best to get PMP certification, and if you're looking for a career in quality control, take Six Sigma certification.
Still, having doubts on which one to pursue? Then choose a training provider to walk you through the decision process. With the right training provider, you will have a basic idea of who should opt for which certification.
Take the first step towards exploring an opportunity to be either a global project management professional or a quality control/assurance professional. Prepare for the PMP or Six Sigma certification and fast track your career. Join Now!
Please fill in the enquiry form or call now on +1(713)-287-1355 or e-mail info {at} icertglobal {dot} com for our training consultant to understand your training requirements and guide you with an optimum way to achieve your learning objectives.
For more information about our PMP and Six Sigma certification, please visit us at https://www.icertglobal.com/
Concepts of Zero Defects in Quality Management
Quality defects can have significant costs associated with them: money, resources, time, and reputation. The programs leveraged by organizations to eradicate quality flaws can be big-budget and time-consuming.
During these times, organizations have a hard time maintaining their quality to stay competitive in their field; that’s when quality management tools come into action. These tools are productive approaches to streamlining business practices to offer better quality and swifter outcomes.
More than 91 percent of companies saw an increase in their operating income after successfully executing a quality management tool. Quality handling is one of the fastest ways to increase production returns.
The Zero Defects approach in quality management works to minimize the flaws to imaginary and, as a result, create better value.
Introduction to the Concept of Zero Defects
The Zero Defects concept was first coined by Mr. Philip Crosby in "Absolutes of Quality Management" and is widely adopted by Six Sigma methodologies as one of its theories. However, the concept also had a fair share of criticism, with some debating about the non-existence of Zero Defects.
Others have struggled hard to prove that Zero Defects in quality management don't mean perfect; instead, a method for eradicating waste and minimization flaws.
What is Zero Defects?
Quality management talks about practices that ensure that the outputs produced are suitable. But to attain zero defects in the deliverable production is technically nearly impossible as complex projects, irrespective of the size, will have some flaws.
According to Six Sigma, Zero Defects are defined as 3.4 defects per million opportunities (DPMO), permitting a 1.5 sigma process transition. To enhance the quality of manufacturing or developing procedures, the Zero Defects concepts can be considered a perfection quest.
Though true perfection might not be obtainable, the pursuit will push quality and enhancements to the point that is acceptable even under rigorous metrics.
Application of Zero Defects
Automotive sectors use Zero Defects to handle and enhance quality problems. It targets reducing the number of flaws in manufactured services and products without the need for specific rules to follow.
This makes the organizations customize how they want the management tool to work for themselves, which is why Zero Defects can be so effective.
It is leveraged in Six Sigma methodologies to minimize the variation and standard deviation, which will indirectly reduce the flaws and bring them near zero.
Principles of Zero Defects
The principles of Zero Defects, according to Philip Crosby, are:
- Quality is the accordance to requirements
Each product has a requirement, and it defines what end-users expect to see. A particular service or product is said to attain the utmost quality when it meets customer prerequisites. This should not be confused with the highest product standards. For example, it will be unrealistic if we say the old mobile phones lack quality compared to the latest smartphone. They both must meet different quality standards to pass the quality test irrespective of their model, size or other internal/external features.
Suppose we visualize the above scenario with the Zero Defects case. In that case, the primary mobile phone version is a quality product if it meets the fundamental customer requirements such as making phone calls and sending and receiving messages. The product is said to accord to the quality and has near to Zero Defects.
- Defect prevention
Here, the top priority is the quality management of the product or service; hence, flaw prevention is made a part of the company procedure. It should be in practice rather than in quality scrutiny and rectification. This is why because Zero Defects management is always less tiring and strenuous. It is more accurate and budget-oriented, as it targets preventing fallacies than identifying and rectifying them later.
- Quality benchmark means zero defects
The following principle of Zero Defects depends on the nature of demands. A demand highlights what the customer or the product itself is needed. Every service and product unit that does not meet the request will not satisfy the prerequisites and is nowhere near the word excellence. But, in some scenarios, the teams that do not meet the conditions could still satisfy the customer demands, so these requirements must be reviewed and modified accordingly to reflect reality.
- Quality measurements in terms of money
Mr. Crosby expects that every flaw indicates a personal expense, including inspection time, rework procedures, and overall budget or revenue. Being extra to the list includes the cost of discarded materials, customer dissatisfactions and labour. When the defects are identified accurately, and appropriate measures are taken, the impact of these costs can be made precise.
This, in turn, offers a clear-cut justification on expense leading to a step forward for quality enhancement. Companies must find a method to estimate a Zero Defects management procedure that aids in maintaining management commitment, employee encouragement or rewarding, and ensuring organizational targets are made measurable. Keeping these in mind, the practices can be made solid, thus helping in making genuine decisions on relative returns.
Theory & Execution of Zero Defects
Zero Defects methodology ensures that there is no waste accumulation in a project. The procedure eradicates unproductive and is of no value to a project, thereby creating process enhancements and lower costs.
The motto of the Zero Defects theory is 'Doing it right the first time, that eventually helps eliminate expensive and time-consuming resolutions later in the project management practice.
Generally, the methodology is based on 4 elements for its execution in an actual project are they are:
- Quality is a state of accordance with requirements. Hence Zero Defects in a project mean the satisfaction of prerequisites at that period.
- Right the first time means that quality must be merged into the project process at the initial phase than keeping it aside and solving it later.
- Quality measure in terms of money means that individuals in charge of the project must consider waste, production, and revenue in terms of economic impact.
- Performance must be considered by the accepted procedures, as near to perfection as possible.
How to Achieve Zero Defects?
There are no magic procedures in achieving Zero Defects; however, there are some techniques to use if you are ready to introduce the concept in an organization, and they are:
- Manage process transitions efficiently.
- Acknowledgment on customer expectations about product or service quality
- Prioritizing continuous enhancement and efficacy
- Introduce and learn Japanese system of Poka-Yoke (prevention of inadvertent flaws).
- Monitor your progress.
- Estimate your quality efforts.
- Develop quality into performance expectations.
Advantage & Disadvantage of Zero Defects
One of the top advantages of attaining a zero-defect phase is minimizing cost and waste when manufacturing products according to customer demands. Zero Defects mean higher user satisfaction and enhanced customer loyalty that consistently results in better profits and sales.
The concept target might lead to a situation where a team is attempting a perfect practice that cannot realistically be obtained. The resources and time allocated on reaching Zero Defects may negatively affect the project performance and strain workforce satisfaction and confidence.
Moreover, there can also be negative suggestions when you ponder the entire supply chain. Other industrialists might have a different viewpoint on the Zero Defects concept.
Ultimately, the pursuit for Zero Defects is a prime target in itself, and many organizations find that merits exceed the demerits. By attempting for rigorous but accepted defects practices, they can develop reasonable procedures and build an ecosystem of continuous service enhancement.
Conclusion
Implementing the Zero Defects concept in an organization allows them to understand and streamline their production workflow to very minor detail. The minimal expense and maximum revenue on implementations make it suitable for any company seeking to launch a new business practice without any training and recalibration investment.
It is essential for company employees and other individuals to get trained and certified in popular quality management courses to properly acknowledge the Zero Defects approach and how it adds value to your company.
About Us
iCert Global is a one-stop solution offering certification training courses in a wide variety of techniques that will give you a head start in this competitive world.
Visit our website to find out more about the course.
Our company conducts both Instructor-led Live Online Training sessions and Instructor-led Classroom training workshops for learners across the globe.
We also provide Corporate Training for enterprise workforce development
Data Science & BI courses
Quality Management Training
- Lean Six Sigma Yellow Belt (LSSYB) Certification Training Courses
- Lean Six Sigma Green Belt (LSSGB) Certification Training Courses
- Lean Six Sigma Black Belt (LSSBB) Certification Training Courses
DevOps Training
Business Analysis Training by iCert Global:
- ECBA (Entry Certificate in Business Analysis) Certification Training Courses
- CCBA (Certificate of Capability in Business Analysis) Certification Training Courses
- CBAP (Certified Business Analysis Professional) Certification Training Courses
Read More
Quality defects can have significant costs associated with them: money, resources, time, and reputation. The programs leveraged by organizations to eradicate quality flaws can be big-budget and time-consuming.
During these times, organizations have a hard time maintaining their quality to stay competitive in their field; that’s when quality management tools come into action. These tools are productive approaches to streamlining business practices to offer better quality and swifter outcomes.
More than 91 percent of companies saw an increase in their operating income after successfully executing a quality management tool. Quality handling is one of the fastest ways to increase production returns.
The Zero Defects approach in quality management works to minimize the flaws to imaginary and, as a result, create better value.
Introduction to the Concept of Zero Defects
The Zero Defects concept was first coined by Mr. Philip Crosby in "Absolutes of Quality Management" and is widely adopted by Six Sigma methodologies as one of its theories. However, the concept also had a fair share of criticism, with some debating about the non-existence of Zero Defects.
Others have struggled hard to prove that Zero Defects in quality management don't mean perfect; instead, a method for eradicating waste and minimization flaws.
What is Zero Defects?
Quality management talks about practices that ensure that the outputs produced are suitable. But to attain zero defects in the deliverable production is technically nearly impossible as complex projects, irrespective of the size, will have some flaws.
According to Six Sigma, Zero Defects are defined as 3.4 defects per million opportunities (DPMO), permitting a 1.5 sigma process transition. To enhance the quality of manufacturing or developing procedures, the Zero Defects concepts can be considered a perfection quest.
Though true perfection might not be obtainable, the pursuit will push quality and enhancements to the point that is acceptable even under rigorous metrics.
Application of Zero Defects
Automotive sectors use Zero Defects to handle and enhance quality problems. It targets reducing the number of flaws in manufactured services and products without the need for specific rules to follow.
This makes the organizations customize how they want the management tool to work for themselves, which is why Zero Defects can be so effective.
It is leveraged in Six Sigma methodologies to minimize the variation and standard deviation, which will indirectly reduce the flaws and bring them near zero.
Principles of Zero Defects
The principles of Zero Defects, according to Philip Crosby, are:
- Quality is the accordance to requirements
Each product has a requirement, and it defines what end-users expect to see. A particular service or product is said to attain the utmost quality when it meets customer prerequisites. This should not be confused with the highest product standards. For example, it will be unrealistic if we say the old mobile phones lack quality compared to the latest smartphone. They both must meet different quality standards to pass the quality test irrespective of their model, size or other internal/external features.
Suppose we visualize the above scenario with the Zero Defects case. In that case, the primary mobile phone version is a quality product if it meets the fundamental customer requirements such as making phone calls and sending and receiving messages. The product is said to accord to the quality and has near to Zero Defects.
- Defect prevention
Here, the top priority is the quality management of the product or service; hence, flaw prevention is made a part of the company procedure. It should be in practice rather than in quality scrutiny and rectification. This is why because Zero Defects management is always less tiring and strenuous. It is more accurate and budget-oriented, as it targets preventing fallacies than identifying and rectifying them later.
- Quality benchmark means zero defects
The following principle of Zero Defects depends on the nature of demands. A demand highlights what the customer or the product itself is needed. Every service and product unit that does not meet the request will not satisfy the prerequisites and is nowhere near the word excellence. But, in some scenarios, the teams that do not meet the conditions could still satisfy the customer demands, so these requirements must be reviewed and modified accordingly to reflect reality.
- Quality measurements in terms of money
Mr. Crosby expects that every flaw indicates a personal expense, including inspection time, rework procedures, and overall budget or revenue. Being extra to the list includes the cost of discarded materials, customer dissatisfactions and labour. When the defects are identified accurately, and appropriate measures are taken, the impact of these costs can be made precise.
This, in turn, offers a clear-cut justification on expense leading to a step forward for quality enhancement. Companies must find a method to estimate a Zero Defects management procedure that aids in maintaining management commitment, employee encouragement or rewarding, and ensuring organizational targets are made measurable. Keeping these in mind, the practices can be made solid, thus helping in making genuine decisions on relative returns.
Theory & Execution of Zero Defects
Zero Defects methodology ensures that there is no waste accumulation in a project. The procedure eradicates unproductive and is of no value to a project, thereby creating process enhancements and lower costs.
The motto of the Zero Defects theory is 'Doing it right the first time, that eventually helps eliminate expensive and time-consuming resolutions later in the project management practice.
Generally, the methodology is based on 4 elements for its execution in an actual project are they are:
- Quality is a state of accordance with requirements. Hence Zero Defects in a project mean the satisfaction of prerequisites at that period.
- Right the first time means that quality must be merged into the project process at the initial phase than keeping it aside and solving it later.
- Quality measure in terms of money means that individuals in charge of the project must consider waste, production, and revenue in terms of economic impact.
- Performance must be considered by the accepted procedures, as near to perfection as possible.
How to Achieve Zero Defects?
There are no magic procedures in achieving Zero Defects; however, there are some techniques to use if you are ready to introduce the concept in an organization, and they are:
- Manage process transitions efficiently.
- Acknowledgment on customer expectations about product or service quality
- Prioritizing continuous enhancement and efficacy
- Introduce and learn Japanese system of Poka-Yoke (prevention of inadvertent flaws).
- Monitor your progress.
- Estimate your quality efforts.
- Develop quality into performance expectations.
Advantage & Disadvantage of Zero Defects
One of the top advantages of attaining a zero-defect phase is minimizing cost and waste when manufacturing products according to customer demands. Zero Defects mean higher user satisfaction and enhanced customer loyalty that consistently results in better profits and sales.
The concept target might lead to a situation where a team is attempting a perfect practice that cannot realistically be obtained. The resources and time allocated on reaching Zero Defects may negatively affect the project performance and strain workforce satisfaction and confidence.
Moreover, there can also be negative suggestions when you ponder the entire supply chain. Other industrialists might have a different viewpoint on the Zero Defects concept.
Ultimately, the pursuit for Zero Defects is a prime target in itself, and many organizations find that merits exceed the demerits. By attempting for rigorous but accepted defects practices, they can develop reasonable procedures and build an ecosystem of continuous service enhancement.
Conclusion
Implementing the Zero Defects concept in an organization allows them to understand and streamline their production workflow to very minor detail. The minimal expense and maximum revenue on implementations make it suitable for any company seeking to launch a new business practice without any training and recalibration investment.
It is essential for company employees and other individuals to get trained and certified in popular quality management courses to properly acknowledge the Zero Defects approach and how it adds value to your company.
About Us
iCert Global is a one-stop solution offering certification training courses in a wide variety of techniques that will give you a head start in this competitive world.
Visit our website to find out more about the course.
Our company conducts both Instructor-led Live Online Training sessions and Instructor-led Classroom training workshops for learners across the globe.
We also provide Corporate Training for enterprise workforce development
Data Science & BI courses
Quality Management Training
- Lean Six Sigma Yellow Belt (LSSYB) Certification Training Courses
- Lean Six Sigma Green Belt (LSSGB) Certification Training Courses
- Lean Six Sigma Black Belt (LSSBB) Certification Training Courses
DevOps Training
Business Analysis Training by iCert Global:
- ECBA (Entry Certificate in Business Analysis) Certification Training Courses
- CCBA (Certificate of Capability in Business Analysis) Certification Training Courses
- CBAP (Certified Business Analysis Professional) Certification Training Courses
Complete Guide to Six Sigma: Everything You Need to Know.
In this blog, we will dive deep into the concept of Six Sigma and other significant factors lingering around the term.
What is Six Sigma?
Six Sigma is a set of top-notch quality-control systems or tools that businesses, be it small-scale or large-scale, leverage to eradicate fallacies and improve workflows, thereby enhancing profits. The process utilizes statistical data rather than guesswork; hence, Six Sigma is more than just training.
If you wonder whether Six Sigma is widely popular, then the answer is yes. This method has been performed within a vast industrial sector to achieve soft and hard money savings while enhancing customer satisfaction. One of the best examples to support the statement is the 1999 General Electric (GE) Capital that could save $2 Billion with the program.
Fundamental Principles of Six Sigma
Why implement Six Sigma?
Here we will discuss five critical principles of the system.
- Flexible and Responsive
Change and Six Sigma go hand-in-hand, as the process recognizes flaws and performs on filtering the same. The experts don't have a choice to linger around failed methods. Though change might be tiresome, eventually, the future it holds is of significant weightage.
- Customer-centric
The fundamental target of Six Sigma is to deliver top-notch outcomes and maximize benefits to the customers. According to market or customer demands, the system develops a precise quality standard in the early phases of projects. In other words, let's say that the approach is customer-centric.
- Precise communication and training teams
A vital point for Six Sigma to have triumphed is to have an entire team proficient in the technique, have a more profound goal insight, and information about the project's progress. It creates a massive transition in the work milieu as it needs trained focus on management to execute the whole process seamlessly.
- Eradication of restrictions and variations
Once the expert identifies a flaw, they will find different ways to obliterate problems. These often come with a lengthy, complicated procedure that may lead to new defects and resource waste. As an innovative method, Six Sigma can help achieve a streamlined and quality-controlled process.
- Identifying and resolution of issues
During process execution, it's natural to be stuck in a tumult of modifications, resulting in the loss of focus on the initial issue. With Six Sigma, obtaining data that shows where a particular problem lies helps in rectifying that point.
Workflow of Six Sigma:
Six Sigma consists of 5 workflow phases - Define, Measure, Analyze, Improve and Control (DMAIC), followed for quality boosting and issue minimization. The explanation of each step is as follows:
- Define
The main aim of the 'Define' level is to summarize the project plan. This phase helps discover all the necessary data to break down a project or problem into the actionable stage. It also focuses on the target needed for the project enhancement, its scope and customer demands.
An input to the 'Define' phase comes from the Voice of Customer (VOC), the Voice of Business (VOB) and the Voice of Process (VOP) to help identify the project. Sometimes, the Voice of Employees (VOE) also comes into Six Sigma project enhancement actions.
The crucial element of this stage is Project Charter - an initial blueprint document for any project outlining key facts.
- Business case
- Problem statement
- Goal statement
- Scope of project
- Team and their responsibilities
- Time plan
- Estimated project benefits
- Measure
Experts obtain data relevant to the project scope in the Six Sigma 'Measure' phase. The phase focuses on parameter identification, measurement methods and performance using wide-range approaches. Once receiving the data, frequency distributors will analyze it.
To have an insight into the data distribution, this phase leverage histogram. The choosing of data analyzing tools depends on the nature of data, whether normal or non-normal. Tools used during this phase include process capability, run charts, process flowcharts, gage R&R and benchmarking.
- Analyze
The critical factor of the 'Analyze' level is to identify the main reason behind business inefficiency. It discovers the gaps between actual and goal performance, identifying its opportunities and cause for business enhancement. This phase begins with exploring potential reasons for the root cause. These issues are then verified and validated using statistical and hypothesis tools.
The phase needs utmost care to discover and verify the root issues as the efficacy of process enhancement via the Six Sigma project lies in the actual finding of root problems. Some of the widely used tools in this phase are scatterplot, fishbone diagram, 5 Whys and more.
- Improve
In this Six Sigma phase, the process improvement is by identifying possible solutions, execution methods, test and implementation of the solution for improvement. Here the process owners are consulted along with suggestions offered to them. Moreover, the phase execution plan will be circulated to relevant shareholders.
The development of this plan is to alleviate the risk and include customer feedback. Defect eradication tools used are Pugh matrix, brainstorming, simulation software, prototyping, mistake-proofing and piloting.
- Control
The primary purpose of the 'Control' phase is to produce a detailed solution monitoring plan, thus ensuring that the required performance is maintained. It defines and validates the monitoring system, creates standards and procedures, verifies profit growths, and communicates to the business.
The most vital part of Six Sigma's control stage is to offer training on new changes to all significant shareholders. Tools used in this stage are control plan, process sigma calculation, cost-saving calculations and control charts.
Six Sigma Certifications:
People can obtain Six Sigma certification, which verifies their professional skills. Awarding of these certificates is through a belt system which is as follows:
- White belt: This consists of people who have not undergone formal certification or training. This belt offers experts a fundamental framework, allowing them to participate in specific quality-control and waste minimization projects.
- Yellow belt: Here, people undergo extra training, allowing them to become contributing project team members.
- Green belt: Those who qualify for this level must participate in a complete course that provides training in process improvement methods. People with green belt certification often become project leaders.
- Black belt: Those certified green belt individuals can move up to this level. Successful people can classify and deal with complex projects and jobs. They undergo training about tackling tremendous changes impacting one's firm via lean Six Sigma projects.
The company conducts both Instructor-led Classroom training workshops and Instructor-led Live Online Training sessions for learners from across the United States and around the world.
We also provide Corporate Training for enterprise workforce development
Professional Certification Training:
Quality Management Training:
- Lean Six Sigma Yellow Belt (LSSYB) Certification Training Courses
- Lean Six Sigma Green Belt (LSSGB) Certification Training Courses
- Lean Six Sigma Black Belt (LSSBB) Certification Training Courses
Scrum Training:
- CSM (Certified ScrumMaster) Certification Training Courses
Agile Training:
- PMI-ACP (Agile Certified Professional) Certification Training Courses
DevOps Training:
- DevOps Certification Training Courses
Business Analysis Training by iCert Global:
- ECBA (Entry Certificate in Business Analysis) Certification Training Courses
- CCBA (Certificate of Capability in Business Analysis) Certification Training Courses
- CBAP (Certified Business Analysis Professional) Certification Training Courses
Connect with us:
- Subscribe to our YouTube Channel
Visit us at https://www.icertglobal.com/ for more information about our professional certification training courses or Call Now! on +1-713-287-1187 / +1-713-287-1214 or e-mail us at info {at} icertglobal {dot} com.
Please Contact Us for more information about our professional certification training courses to accelerate your career. Let us know your thoughts in the 'Comments' section below.
Read More
In this blog, we will dive deep into the concept of Six Sigma and other significant factors lingering around the term.
What is Six Sigma?
Six Sigma is a set of top-notch quality-control systems or tools that businesses, be it small-scale or large-scale, leverage to eradicate fallacies and improve workflows, thereby enhancing profits. The process utilizes statistical data rather than guesswork; hence, Six Sigma is more than just training.
If you wonder whether Six Sigma is widely popular, then the answer is yes. This method has been performed within a vast industrial sector to achieve soft and hard money savings while enhancing customer satisfaction. One of the best examples to support the statement is the 1999 General Electric (GE) Capital that could save $2 Billion with the program.
Fundamental Principles of Six Sigma
Why implement Six Sigma?
Here we will discuss five critical principles of the system.
- Flexible and Responsive
Change and Six Sigma go hand-in-hand, as the process recognizes flaws and performs on filtering the same. The experts don't have a choice to linger around failed methods. Though change might be tiresome, eventually, the future it holds is of significant weightage.
- Customer-centric
The fundamental target of Six Sigma is to deliver top-notch outcomes and maximize benefits to the customers. According to market or customer demands, the system develops a precise quality standard in the early phases of projects. In other words, let's say that the approach is customer-centric.
- Precise communication and training teams
A vital point for Six Sigma to have triumphed is to have an entire team proficient in the technique, have a more profound goal insight, and information about the project's progress. It creates a massive transition in the work milieu as it needs trained focus on management to execute the whole process seamlessly.
- Eradication of restrictions and variations
Once the expert identifies a flaw, they will find different ways to obliterate problems. These often come with a lengthy, complicated procedure that may lead to new defects and resource waste. As an innovative method, Six Sigma can help achieve a streamlined and quality-controlled process.
- Identifying and resolution of issues
During process execution, it's natural to be stuck in a tumult of modifications, resulting in the loss of focus on the initial issue. With Six Sigma, obtaining data that shows where a particular problem lies helps in rectifying that point.
Workflow of Six Sigma:
Six Sigma consists of 5 workflow phases - Define, Measure, Analyze, Improve and Control (DMAIC), followed for quality boosting and issue minimization. The explanation of each step is as follows:
- Define
The main aim of the 'Define' level is to summarize the project plan. This phase helps discover all the necessary data to break down a project or problem into the actionable stage. It also focuses on the target needed for the project enhancement, its scope and customer demands.
An input to the 'Define' phase comes from the Voice of Customer (VOC), the Voice of Business (VOB) and the Voice of Process (VOP) to help identify the project. Sometimes, the Voice of Employees (VOE) also comes into Six Sigma project enhancement actions.
The crucial element of this stage is Project Charter - an initial blueprint document for any project outlining key facts.
- Business case
- Problem statement
- Goal statement
- Scope of project
- Team and their responsibilities
- Time plan
- Estimated project benefits
- Measure
Experts obtain data relevant to the project scope in the Six Sigma 'Measure' phase. The phase focuses on parameter identification, measurement methods and performance using wide-range approaches. Once receiving the data, frequency distributors will analyze it.
To have an insight into the data distribution, this phase leverage histogram. The choosing of data analyzing tools depends on the nature of data, whether normal or non-normal. Tools used during this phase include process capability, run charts, process flowcharts, gage R&R and benchmarking.
- Analyze
The critical factor of the 'Analyze' level is to identify the main reason behind business inefficiency. It discovers the gaps between actual and goal performance, identifying its opportunities and cause for business enhancement. This phase begins with exploring potential reasons for the root cause. These issues are then verified and validated using statistical and hypothesis tools.
The phase needs utmost care to discover and verify the root issues as the efficacy of process enhancement via the Six Sigma project lies in the actual finding of root problems. Some of the widely used tools in this phase are scatterplot, fishbone diagram, 5 Whys and more.
- Improve
In this Six Sigma phase, the process improvement is by identifying possible solutions, execution methods, test and implementation of the solution for improvement. Here the process owners are consulted along with suggestions offered to them. Moreover, the phase execution plan will be circulated to relevant shareholders.
The development of this plan is to alleviate the risk and include customer feedback. Defect eradication tools used are Pugh matrix, brainstorming, simulation software, prototyping, mistake-proofing and piloting.
- Control
The primary purpose of the 'Control' phase is to produce a detailed solution monitoring plan, thus ensuring that the required performance is maintained. It defines and validates the monitoring system, creates standards and procedures, verifies profit growths, and communicates to the business.
The most vital part of Six Sigma's control stage is to offer training on new changes to all significant shareholders. Tools used in this stage are control plan, process sigma calculation, cost-saving calculations and control charts.
Six Sigma Certifications:
People can obtain Six Sigma certification, which verifies their professional skills. Awarding of these certificates is through a belt system which is as follows:
- White belt: This consists of people who have not undergone formal certification or training. This belt offers experts a fundamental framework, allowing them to participate in specific quality-control and waste minimization projects.
- Yellow belt: Here, people undergo extra training, allowing them to become contributing project team members.
- Green belt: Those who qualify for this level must participate in a complete course that provides training in process improvement methods. People with green belt certification often become project leaders.
- Black belt: Those certified green belt individuals can move up to this level. Successful people can classify and deal with complex projects and jobs. They undergo training about tackling tremendous changes impacting one's firm via lean Six Sigma projects.
The company conducts both Instructor-led Classroom training workshops and Instructor-led Live Online Training sessions for learners from across the United States and around the world.
We also provide Corporate Training for enterprise workforce development
Professional Certification Training:
Quality Management Training:
- Lean Six Sigma Yellow Belt (LSSYB) Certification Training Courses
- Lean Six Sigma Green Belt (LSSGB) Certification Training Courses
- Lean Six Sigma Black Belt (LSSBB) Certification Training Courses
Scrum Training:
- CSM (Certified ScrumMaster) Certification Training Courses
Agile Training:
- PMI-ACP (Agile Certified Professional) Certification Training Courses
DevOps Training:
- DevOps Certification Training Courses
Business Analysis Training by iCert Global:
- ECBA (Entry Certificate in Business Analysis) Certification Training Courses
- CCBA (Certificate of Capability in Business Analysis) Certification Training Courses
- CBAP (Certified Business Analysis Professional) Certification Training Courses
Connect with us:
- Subscribe to our YouTube Channel
Visit us at https://www.icertglobal.com/ for more information about our professional certification training courses or Call Now! on +1-713-287-1187 / +1-713-287-1214 or e-mail us at info {at} icertglobal {dot} com.
Please Contact Us for more information about our professional certification training courses to accelerate your career. Let us know your thoughts in the 'Comments' section below.
Six Sigma Control Plan: Key attributes and strategies!!
Six Sigma approaches are known for their data-driven, rational approach to problem solving. However, what genuinely distinguishes them from other quality theories is their adaptability and applicability in situations other than manufacturing, where they were born.
One of the primary goals of Lean Six Sigma is to eliminate superfluous stages and waste in a process or business model. In Lean methodology, any process that adds no value is eliminated in order to improve efficiency, workflow and profitability.
Organizations develop control plans to assist company leaders in monitoring metrics, documenting successes and making modifications for continuous process improvement. A control plan is a way for documenting the functional aspects of quality control that will be performed to ensure that quality standards for a specific product or service are satisfied.
This control plan could be prepared for a process, a phase in the process, a piece of process equipment and so on. Take a short look at the requirements and techniques for a Six Sigma Control Plan here.
What is a plan for Six Sigma Control?
A control plan is a written overview of the process that lays out in detail the steps to be followed to keep a process or a device working at its current level of performance in the field of quality management. Control plans outline each stage of the process as well as the metrics that must be tracked to ensure that a batch of products has no major deviations from the mean or variation.
Control plans are a key component of the Six Sigma methodology set and are widely used by Six Sigma practitioners.
What Is A Six Sigma Control Plan's Purpose?
"The goal of the control plan," according to the American Society For Quality (ASQ), "is to ensure that performance improvements produced by the project team are sustained throughout time."
The plan is generated during the define, measure, analyze, improve, control (DMAIC) approach's improvement phase, or a comparable phase in other techniques.
In essence, a Control Plan would include a summary of all important information for a given project so that the quality specialist can determine if the project is on track and, in the event of deviations, delays or excessive overheads, corrective action may be taken. As a result, the Control Plan is updated to reflect any process changes, such as (but not limited to):
- Changing or tweaking a step in the process
- A stage in the process is added or removed.
- Changes to human resource and training requirements.
- Equipment used in the process is added or removed.
- Changes to capital and funding inflows and outflows.
The Control Plan template is developed at the start of a project and is created following consultation with or participation from all project stakeholders, beginning with the process or product owner.
Why should you use a Control Plan?
A Control Plan serves as a single point of reference for learning about the process's features, specifications and standard operating procedures (SOP). For each action in the process, a CP allows for the assignment of responsibility and allocation of liability.
This guarantees that the process runs smoothly and that it is long-term viable. A properly-designed control plan aids the process and product owners in tracking, correcting the performance of the KPIVs and KPOVs, as well as avoiding negative business impacts from faults and process deterioration (Key Performance Input and Output Variables).
Attributes and Strategies
A well-organized control plan can assist firms in monitoring growth, preventing process degradation and ensuring that problems do not repeat.

When building a Lean Six Sigma control strategy, consider the following seven attributes and strategies:
- Measurements and specifications –
One of the characteristics of a well-organized control plan is the ability to maintain quality in all elements of a process. Customer satisfaction can be used to determine quality. Processes can fulfill customer-approved specifications by identifying quality features and measuring them to derive quality standards.
- Input-Output Process —
The Input-Output (IPO) model aids in the identification of processing tasks required to convert inputs into outputs. The IPO approach contributes to a well-organized way of studying and recording components of the transformation process while determining what actions to take to help attain the intended output.
- Process Execution –
A control plan can help improve process performance by designing error-proofing measures that aim to remove errors in a process as much as feasible. Poka-yoke, which literally means "to avoid errors" is a prominent Six Sigma strategy used to eliminate waste.
- Performance Reporting and Sampling —
A control plan can also help address when to conduct performance management reviews, how frequently such reviews should be conducted and what products or services should be inspected for mistakes. An organized control plan answers all questions and assists organizations in conducting an accurate assessment of process efficiency.
- Documenting Information —
Control plan information should be accessible to anybody in the firm who needs it. Furthermore, information should be classified to aid in the organization planning and management of firm data.
- Adjustments –
Process improvement or making adjustments to address issues, decrease waste and minimize costs, is a crucial aspect of the Lean Six Sigma method. When an issue is identified, corrective action is required to avoid production delays and error recurrence.
- The Process Owner -
Process owners typically have the authority to review, alter and adjust process operations. They are responsible for product demand and customer satisfaction. Among other things, they evaluate production performance using process evaluations, measurements and statistics.
What Is Included In A Standard Control Plan?
A Control Plan might have as many or as few things as necessary to cover the breadth of the process or project at hand. A Control Plan often includes the following items:

- Process Flowchart: A visual representation of the process workflow with decision-making phases highlighted is included in many Control Plans. This provides a high-level overview of the process that may be referred to at any time and by any stakeholder.
- The CTQs (or critical-to-quality trees) are the essential quantifiable and measurable qualities of a product or process that must be reached in order to satisfy the customer's performance criteria or specification limits. This makes it easier to match design specs to client needs.
- Process Phase: This column contains the name or label of the process step. For example, in a backyard garage, a polishing operation using lathes may opt to include tool preparation, rough polishing, fine polishing and delivery as the many processes involved in the overall process.
- Specification: A specific characteristic of the product must be identified for measurement before a CTQ can be quantified: this column is used to record the characteristic of a specification. For example, the diameter of the polished shaft.
- Specs: This item can be used to keep track of the numerical values of the specifications as well as the measurement unit. Internal diameter: 4mm; exterior diameter: 7.5mm, for example.
- Measurement: This column can be used to document the measuring method that was employed. Vernier calipers, for example.
- Sample Size: The size of the sample used for measurement.
- Frequency of Measurement: Indicates how frequently samples are selected for measurement. Hourly, daily and so on.
- Corrective Action: Any corrective actions made during that stage of the process are documented and recorded for future reference.
- Standards: For manufacturing operations and control plans used in organizations, the quality standard followed as well as the SOP (Standard Operating Procedure) guidelines followed can be recorded.
- Additional documentation may include fields such as the person taking the measurement, the date, place and time the recording was made, the revision number and version control, the location and so on.
Strategy Overview for a Control Plan
Successful Six Sigma control plans are built on well-thought-out tactics that reduce the need for process tampering. They list the steps that must be taken to deal with out-of-control situations and raise suitable signs that indicate the necessity for Kaizen operations. Furthermore, these methods outline the necessary training to ensure that team members are familiar with basic operating procedures.

In a nutshell, a well-written control plan lays out all of the steps that must be followed, who is responsible for which processes and how to avoid the "firefighting" syndrome while dealing with any variations.
Conclusion
Control is one of the last steps in the Lean Six Sigma process improvement roadmap of Define-Measure-Analyze-Improve-Control (DMAIC). One of the most important aspects of the 'Control' stage is the development of a well-thought-out control strategy to reduce the risk of unfavorable business consequences due to process deterioration.
A control plan often comprises the steps that must be completed on a timely basis, particularly when performance metrics fall outside of a pre-defined, intended range. Furthermore, an organizational mechanism must be in place so that all process owners may be held accountable for the execution of the various sections of the control plan, particularly those that pertain to their areas of operations.
This control plan must be created by the process owner and his assigned team in order to improve service quality. This strategy should be adaptable enough to be revised in response to assessments and changes that occur after its implementation.
For more certification courses, go through our website - iCert Global, get exclusive discounts on the course as per your preferences.
The company conducts both Instructor-led Classroom training workshops and Instructor-led Live Online Training sessions for learners from across the United States and around the world.
We also provide Corporate Training for enterprise workforce development
Professional Certification Training:
Quality Management Training:
- Lean Six Sigma Yellow Belt (LSSYB) Certification Training Courses
- Lean Six Sigma Green Belt (LSSGB) Certification Training Courses
- Lean Six Sigma Black Belt (LSSBB) Certification Training Courses
Scrum Training:
- CSM (Certified ScrumMaster) Certification Training Courses
Agile Training:
- PMI-ACP (Agile Certified Professional) Certification Training Courses
DevOps Training:
- DevOps Certification Training Courses
Business Analysis Training by iCert Global:
- ECBA (Entry Certificate in Business Analysis) Certification Training Courses
- CCBA (Certificate of Capability in Business Analysis) Certification Training Courses
- CBAP (Certified Business Analysis Professional) Certification Training Courses
Connect with us:
- Subscribe to our YouTube Channel
Visit us at https://www.icertglobal.com/ for more information about our professional certification training courses or Call Now! on +1-713-287-1187 / +1-713-287-1214 or e-mail us at info {at} icertglobal {dot} com.
Please Contact Us for more information about our professional certification training courses to accelerate your career. Let us know your thoughts in the 'Comments' section below.
Read More
Six Sigma approaches are known for their data-driven, rational approach to problem solving. However, what genuinely distinguishes them from other quality theories is their adaptability and applicability in situations other than manufacturing, where they were born.
One of the primary goals of Lean Six Sigma is to eliminate superfluous stages and waste in a process or business model. In Lean methodology, any process that adds no value is eliminated in order to improve efficiency, workflow and profitability.
Organizations develop control plans to assist company leaders in monitoring metrics, documenting successes and making modifications for continuous process improvement. A control plan is a way for documenting the functional aspects of quality control that will be performed to ensure that quality standards for a specific product or service are satisfied.
This control plan could be prepared for a process, a phase in the process, a piece of process equipment and so on. Take a short look at the requirements and techniques for a Six Sigma Control Plan here.
What is a plan for Six Sigma Control?
A control plan is a written overview of the process that lays out in detail the steps to be followed to keep a process or a device working at its current level of performance in the field of quality management. Control plans outline each stage of the process as well as the metrics that must be tracked to ensure that a batch of products has no major deviations from the mean or variation.
Control plans are a key component of the Six Sigma methodology set and are widely used by Six Sigma practitioners.
What Is A Six Sigma Control Plan's Purpose?
"The goal of the control plan," according to the American Society For Quality (ASQ), "is to ensure that performance improvements produced by the project team are sustained throughout time."
The plan is generated during the define, measure, analyze, improve, control (DMAIC) approach's improvement phase, or a comparable phase in other techniques.
In essence, a Control Plan would include a summary of all important information for a given project so that the quality specialist can determine if the project is on track and, in the event of deviations, delays or excessive overheads, corrective action may be taken. As a result, the Control Plan is updated to reflect any process changes, such as (but not limited to):
- Changing or tweaking a step in the process
- A stage in the process is added or removed.
- Changes to human resource and training requirements.
- Equipment used in the process is added or removed.
- Changes to capital and funding inflows and outflows.
The Control Plan template is developed at the start of a project and is created following consultation with or participation from all project stakeholders, beginning with the process or product owner.
Why should you use a Control Plan?
A Control Plan serves as a single point of reference for learning about the process's features, specifications and standard operating procedures (SOP). For each action in the process, a CP allows for the assignment of responsibility and allocation of liability.
This guarantees that the process runs smoothly and that it is long-term viable. A properly-designed control plan aids the process and product owners in tracking, correcting the performance of the KPIVs and KPOVs, as well as avoiding negative business impacts from faults and process deterioration (Key Performance Input and Output Variables).
Attributes and Strategies
A well-organized control plan can assist firms in monitoring growth, preventing process degradation and ensuring that problems do not repeat.
When building a Lean Six Sigma control strategy, consider the following seven attributes and strategies:
- Measurements and specifications –
One of the characteristics of a well-organized control plan is the ability to maintain quality in all elements of a process. Customer satisfaction can be used to determine quality. Processes can fulfill customer-approved specifications by identifying quality features and measuring them to derive quality standards.
- Input-Output Process —
The Input-Output (IPO) model aids in the identification of processing tasks required to convert inputs into outputs. The IPO approach contributes to a well-organized way of studying and recording components of the transformation process while determining what actions to take to help attain the intended output.
- Process Execution –
A control plan can help improve process performance by designing error-proofing measures that aim to remove errors in a process as much as feasible. Poka-yoke, which literally means "to avoid errors" is a prominent Six Sigma strategy used to eliminate waste.
- Performance Reporting and Sampling —
A control plan can also help address when to conduct performance management reviews, how frequently such reviews should be conducted and what products or services should be inspected for mistakes. An organized control plan answers all questions and assists organizations in conducting an accurate assessment of process efficiency.
- Documenting Information —
Control plan information should be accessible to anybody in the firm who needs it. Furthermore, information should be classified to aid in the organization planning and management of firm data.
- Adjustments –
Process improvement or making adjustments to address issues, decrease waste and minimize costs, is a crucial aspect of the Lean Six Sigma method. When an issue is identified, corrective action is required to avoid production delays and error recurrence.
- The Process Owner -
Process owners typically have the authority to review, alter and adjust process operations. They are responsible for product demand and customer satisfaction. Among other things, they evaluate production performance using process evaluations, measurements and statistics.
What Is Included In A Standard Control Plan?
A Control Plan might have as many or as few things as necessary to cover the breadth of the process or project at hand. A Control Plan often includes the following items:
- Process Flowchart: A visual representation of the process workflow with decision-making phases highlighted is included in many Control Plans. This provides a high-level overview of the process that may be referred to at any time and by any stakeholder.
- The CTQs (or critical-to-quality trees) are the essential quantifiable and measurable qualities of a product or process that must be reached in order to satisfy the customer's performance criteria or specification limits. This makes it easier to match design specs to client needs.
- Process Phase: This column contains the name or label of the process step. For example, in a backyard garage, a polishing operation using lathes may opt to include tool preparation, rough polishing, fine polishing and delivery as the many processes involved in the overall process.
- Specification: A specific characteristic of the product must be identified for measurement before a CTQ can be quantified: this column is used to record the characteristic of a specification. For example, the diameter of the polished shaft.
- Specs: This item can be used to keep track of the numerical values of the specifications as well as the measurement unit. Internal diameter: 4mm; exterior diameter: 7.5mm, for example.
- Measurement: This column can be used to document the measuring method that was employed. Vernier calipers, for example.
- Sample Size: The size of the sample used for measurement.
- Frequency of Measurement: Indicates how frequently samples are selected for measurement. Hourly, daily and so on.
- Corrective Action: Any corrective actions made during that stage of the process are documented and recorded for future reference.
- Standards: For manufacturing operations and control plans used in organizations, the quality standard followed as well as the SOP (Standard Operating Procedure) guidelines followed can be recorded.
- Additional documentation may include fields such as the person taking the measurement, the date, place and time the recording was made, the revision number and version control, the location and so on.
Strategy Overview for a Control Plan
Successful Six Sigma control plans are built on well-thought-out tactics that reduce the need for process tampering. They list the steps that must be taken to deal with out-of-control situations and raise suitable signs that indicate the necessity for Kaizen operations. Furthermore, these methods outline the necessary training to ensure that team members are familiar with basic operating procedures.
In a nutshell, a well-written control plan lays out all of the steps that must be followed, who is responsible for which processes and how to avoid the "firefighting" syndrome while dealing with any variations.
Conclusion
Control is one of the last steps in the Lean Six Sigma process improvement roadmap of Define-Measure-Analyze-Improve-Control (DMAIC). One of the most important aspects of the 'Control' stage is the development of a well-thought-out control strategy to reduce the risk of unfavorable business consequences due to process deterioration.
A control plan often comprises the steps that must be completed on a timely basis, particularly when performance metrics fall outside of a pre-defined, intended range. Furthermore, an organizational mechanism must be in place so that all process owners may be held accountable for the execution of the various sections of the control plan, particularly those that pertain to their areas of operations.
This control plan must be created by the process owner and his assigned team in order to improve service quality. This strategy should be adaptable enough to be revised in response to assessments and changes that occur after its implementation.
For more certification courses, go through our website - iCert Global, get exclusive discounts on the course as per your preferences.
The company conducts both Instructor-led Classroom training workshops and Instructor-led Live Online Training sessions for learners from across the United States and around the world.
We also provide Corporate Training for enterprise workforce development
Professional Certification Training:
Quality Management Training:
- Lean Six Sigma Yellow Belt (LSSYB) Certification Training Courses
- Lean Six Sigma Green Belt (LSSGB) Certification Training Courses
- Lean Six Sigma Black Belt (LSSBB) Certification Training Courses
Scrum Training:
- CSM (Certified ScrumMaster) Certification Training Courses
Agile Training:
- PMI-ACP (Agile Certified Professional) Certification Training Courses
DevOps Training:
- DevOps Certification Training Courses
Business Analysis Training by iCert Global:
- ECBA (Entry Certificate in Business Analysis) Certification Training Courses
- CCBA (Certificate of Capability in Business Analysis) Certification Training Courses
- CBAP (Certified Business Analysis Professional) Certification Training Courses
Connect with us:
- Subscribe to our YouTube Channel
Visit us at https://www.icertglobal.com/ for more information about our professional certification training courses or Call Now! on +1-713-287-1187 / +1-713-287-1214 or e-mail us at info {at} icertglobal {dot} com.
Please Contact Us for more information about our professional certification training courses to accelerate your career. Let us know your thoughts in the 'Comments' section below.
Exploring the Real World of Quality Management Practices.
Organizations throughout the world are increasingly resorting to the tried-and-true bastions of quality control and quality management as they strive to perfect their operations and stay competitive. Lean Six Sigma (LSS) has long been a cornerstone of quality management best practices, with impressive results across a wide range of sectors and critical business processes.
It is a data-driven business management methodology that aims to improve product quality and process excellence by decreasing waste and increasing the value of every stage of the product or service lifecycle.

According to a recent study, about 20% of companies intend to use cross-functional quality processes and teams across design, manufacturing and service. For years, practitioners of Lean Six Sigma and other quality management methodologies have prospered.
To understand Real-world quality management, consider the following:
- The act of managing all activities and duties required to achieve a specified degree of perfection is known as quality management.
- Quality management entails establishing a quality strategy, developing and implementing quality assurance and planning, as well as quality control and improvement.
- Total Quality Management (TQM) necessitates collaboration among all stakeholders in a business to improve processes, products, services and the company's culture.
The overall quality approach explains the culture, mindset and organization that commits to providing better products and services that meet the needs of customers. Total quality management is a management technique that entails the process of improving employer-employee connections and consumer-business relationships in order to achieve better results in the production of goods and services. Let's take a look, how the concepts are managed in real-world situations.
What is the concept of quality management?
The act of overseeing various operations and duties inside a company to guarantee that the products and services given, as well as the means employed to produce them, are consistent is known as quality management. It assists the company in achieving and maintaining a targeted level of quality.

There are four main components to quality management, which are as follows:
- Quality Planning - The process of determining the project's quality criteria and determining how to meet them.
- Quality Improvement - The deliberate alteration of a process in order to improve the outcome confidence or reliability.
- Quality Control - The ongoing endeavor to maintain the integrity and dependability of a process in reaching a goal.
- Quality Assurance - The systematic or planned actions required to provide sufficient reliability so that a certain service or product meets the defined requirements.
Quality management is to guarantee that all stakeholders in an organization collaborate to improve the company's procedures, products, services and culture in order to achieve long-term success based on customer satisfaction.
Quality management is a set of guidelines produced by a team to ensure that the products and services they produce meet the appropriate standards or are suitable for a certain purpose.
- The process begins when the organization establishes quality goals that are agreed upon by both the client and the organization.
- After that, the organization determines how the goals will be measured. It performs the steps required to assess quality. It then finds and corrects any quality concerns that have arisen.
- The final step is to report on the overall degree of quality that has been attained.
The procedure ensures that the team's products and services meet the consumers' expectations.
Methods for Improving Quality
Product improvement, process improvement and people-based improvement are the three components of quality improvement approaches. There are a variety of quality management strategies and procedures that can be used.

Kaizen, Zero Defect Programs, Six Sigma, Quality Circle, Taguchi Methods, Toyota Production System, Kansei Engineering, TRIZ, BPR, OQRM, ISO and Top-Down & Bottom-Up methodologies are just a few of them.
Example of Quality Management
Toyota Corporation's application of the Kanban system is a shining example of excellent quality management. Kanban is an inventory control technique created by Taiichi Ohno to assist in minimizing the accumulation of surplus inventory on the manufacturing line at any given time by providing visibility to both suppliers and purchasers.
Toyota adopted the notion to implement their Just-in-Time (JIT) system, which lets suppliers synchronize raw material orders with production schedules directly. Toyota's manufacturing line improved efficiency by ensuring that the corporation had just enough inventory on hand to match client orders as they came in.
Improving the quality of manufacturing and the supply chain
Manufacturing enterprises are among the best examples of how Lean Six Sigma can aid in the development of high-quality products. For example, in North America, 3M recently used LSS principles in their design and manufacturing capabilities for compressed natural gas systems.
They used cutting-edge materials, technology and Lean Six Sigma experience to improve the overall quality and durability of their natural gas tanks, making them 30% lighter and with 10% more storage than competing tank types. 3M has also devised a long-term strategy to accomplish financial and customer goals by using Lean Six Sigma across manufacturing, supply chain and even customer service.
Manufacturers benefit not only from supplying higher-quality products to customers (with fewer flaws to rectify) but also from the speed with which they can handle issues that arise once they reach the end consumer. This ongoing plan includes quality management as a key component.
The Construction Industry's Quality Management
Construction is a one-time yet creative activity, therefore it's important to keep in mind that it's costly and time-consuming to reproduce a structure (or similar). TQM is used to reduce costs and increase productivity and it is possible to track efforts if results improve. Quality in the construction sector is determined by the level of satisfaction of the designer, builder and homeowners.
Getting Rid of Defects in Pharmaceuticals
Companies that create products that have an influence on the health and safety of daily consumers have a responsibility to ensure that the creation and testing of these items are done in a way that minimizes risk.
Pharmaceutical companies come under this group and they are required by law to ensure that their products are safe. Lean Six Sigma concepts, according to a recent LinkedIn article, may help firms attain this level of confidence in their processes to the point where they are nearly error-free.
LSS is used by pharmaceutical companies to implement end-to-end product testing, predict and eliminate errors during the development and testing life cycles and, as a result, improve product quality and meet compliance requirements. LSS assists them in reducing the risk of passing on tainted or ineffective medications, which can have serious health consequences for patients.
Onboarding Procedures in Healthcare
Long and complicated business processes are well-known in the healthcare industry. One example is Johns Hopkins All Children's Hospital (JHACH), which had a slow and inefficient provider enrollment process (taking up to six months to onboard providers).
JHACH patients who rely on those providers have had their visits with physicians delayed or they have had to see a whole new physician, resulting in dissatisfied patients and low customer satisfaction with the process.
JHACH boosted the number of hospital-employed providers who are active with health plans by nearly 30% by using the Lean Six Sigma workflow, consolidating departments and building a monitoring tool to monitor every stage of the process.
In the long run, the key to hospital business is cost and quality treatment. These principles should be followed by organizations for the best results.
- The patient should come first and the organization should prioritize the customer's needs; treatment should be the top priority.
- A good and engaging leader is in demand and a good leader should always be cautious and able to keep employees engaged in the organization's goals.
- Employee participation means that each employee, even doctors, should feel responsible for their work and become involved in it; only then can the organization benefit from the business.
- The organization must prioritize improvement and conduct regular audits in order to improve the environment.
Software Products of Higher Quality
Software quality assurance (QA) engineers play a critical role in ensuring that software solutions meet stringent quality standards and perform as expected. Certification as a Certified Tester Foundation Level (CTFL) is a requirement for anyone working in the software development and testing industry.
However, actions can be taken to increase quality earlier in the development lifecycle. Lean Six Sigma can assist businesses in reducing waste and superfluous cycles, allowing them to produce items faster and with higher quality.
Among the most essential areas where LSS can help are:
- Value stream analysis is used to discover and eliminate non-value contributed operations.
- Establishing a strategy for obtaining customer feedback and approval on requirements prior to the commencement of development work.
- Establishing a knowledge management system in which all reusable components are stored in a knowledge base and can be accessed later.
- Benchmarking with other team members in order to implement best practices without having to reinvent the wheel every time.
- Resource usage to determine what is being overused and underutilized and to take corrective or preventive measures.
Quality Oriented Culture
Total Quality Management (TQM) is a phrase used by quality experts to describe the use of quality concepts at all levels of a business. While TQM has typically implied widespread use of process tools and analytical procedures, the definition has broadened to include the entire organization's larger cultural norms.
The extension of TQM to cover both explicit efforts by people to enhance Quality and the underlying beliefs, philosophies and behaviors on which those efforts are based are referred to as Culture of Quality.

A successful Quality Culture is one in which the organization's core Quality values, such as a focus on responding to customer needs and the importance of data-based decision-making and workers' basic assumptions about the nature of human relationships and their places in the world, such as the value of collaborative relationships among people with common goals and the importance of developing long-term personal connections, are closely integrated.
Because core values are overtly expressed and understood at all levels of the organization, they are relatively easy to measure. Even the people who hold basic ideas typically resist explicit analysis, making participation at this level challenging.
A Culture of Quality can only be achieved when leaders and employees have a common understanding of not only the core values and processes they utilize and promote but also their underlying assumptions about the nature of work and human interactions on which those core values are based.
Quality Management Principles
The International Standard for Quality Management adheres to a number of quality management concepts. Top management uses these ideas to guide an organization's procedures toward higher performance. They are as follows:

1) Customer Service Focus
The fundamental goal of every firm should be to satisfy and surpass the expectations and needs of its consumers. When a company can understand and cater to its consumers' current and future demands, it builds client loyalty, which leads to increased income.
The company is also capable of identifying and satisfying new consumer opportunities. When business operations are more efficient, quality improves and more customers are able to be satisfied.
2) People's Participation
Another important aspect is employee involvement. Whether full-time, part-time, outsourced, or in-house, management engages employees in developing and delivering value. Employees should be encouraged to continually develop their abilities and maintain consistency in their work.
Empowering employees, including them in decision-making and acknowledging their accomplishments are all part of this philosophy. People work to their full potential when they feel valued, as it enhances their confidence and motivation. Employees feel empowered and accountable for their actions when they are fully involved.
3) Leadership
Good leadership leads to the success of an organization. Great leadership creates a sense of purpose and togetherness among employees and shareholders. Creating a vibrant corporate culture creates an internal climate in which people may completely fulfill their potential and actively participate in attaining company goals.
Employees should be involved in the development of clear organizational goals and objectives by leaders. Employees are motivated as a result and their productivity and loyalty may improve dramatically.
4) Approach to the Process
According to the process approach principle, an organization's performance is critical. The approach principle focuses on improving organizational processes' efficiency and effectiveness.
The concept assumes that good processes lead to increased consistency, faster actions, lower costs, waste elimination and continual improvement. When leaders can manage and control the organization's inputs and outputs, as well as the processes that produce the outputs, the organization benefits.
5) Continuous Enhancement
Every organization should have a goal to actively participate in continuous development. Businesses that continuously improve see a higher performance, organizational flexibility and the ability to seize new possibilities. Businesses should be able to constantly establish new procedures and adapt to changing market conditions.
6) Making Decisions Based on Evidence
Businesses should use a data-driven approach to decision-making. Businesses that base their decisions on verified and studied data have a better understanding of the market. They may complete tasks that provide the necessary results and justify their previous actions.
Factual decision making is critical for understanding the cause-and-effect relationships of various things and explaining probable unintended repercussions and results.
7) Management of Relationships
Creating mutually beneficial relationships with suppliers and retailers is the goal of relationship management. A company's performance can be influenced by a variety of stakeholders.
To maximize their impact on the company's success, the organization should manage the supply chain process well and enhance the relationship between the organization and its suppliers. When an organization effectively manages its relationships with interested parties, it is more likely to achieve long-term business success and collaboration.
The Advantages of Quality Management

- It assists an organization in achieving more consistency in the tasks and activities associated with the production of products and services.
- It enhances process efficiency, minimizes waste and makes better use of time and other resources.
- It contributes to increased consumer satisfaction.
- It enables enterprises to efficiently sell their products and enter new markets.
- It makes it easier for organizations to integrate new personnel, allowing them to manage growth more smoothly.
- It enables a company to constantly enhance its goods, processes and systems.
Conclusion
Customers understand the importance of quality in products and services. Suppliers know that quality can be a key differentiator between their own and competitors' offers (quality differentiation is also called the quality gap).
The quality gap between competing products and services has narrowed dramatically during the last two decades. This is due in part to manufacturing contracting (also known as outsourcing) to nations such as China and India, as well as the internationalization of commerce and competition.
In order to fulfill worldwide standards and client needs, these countries, among many others, have upgraded their own quality requirements. Quality culture, the relevance of knowledge management and the role of leadership in promoting and achieving high quality have all become more prominent themes.
Systems thinking, for example, is bringing more holistic methods to quality management, in which people, processes and products are all examined together rather than as separate components in quality management.
Quality culture has been acknowledged by government agencies and industrial organizations that regulate products as a way to help enterprises develop those items. According to a survey of more than 60 global organizations, companies with a bad quality culture had increased costs of $67 million per year for every 5000 employees compared to companies with a good quality culture.
iCert Global will help you to find best related certifications courses under Quality Management.
The company conducts both Instructor-led Classroom training workshops and Instructor-led Live Online Training sessions for learners from across the United States and around the world.
We also provide Corporate Training for enterprise workforce development
Professional Certification Training:
Quality Management Training:
- Lean Six Sigma Yellow Belt (LSSYB) Certification Training Courses
- Lean Six Sigma Green Belt (LSSGB) Certification Training Courses
- Lean Six Sigma Black Belt (LSSBB) Certification Training Courses
Scrum Training:
- CSM (Certified ScrumMaster) Certification Training Courses
Agile Training:
- PMI-ACP (Agile Certified Professional) Certification Training Courses
DevOps Training:
- DevOps Certification Training Courses
Business Analysis Training by iCert Global:
- ECBA (Entry Certificate in Business Analysis) Certification Training Courses
- CCBA (Certificate of Capability in Business Analysis) Certification Training Courses
- CBAP (Certified Business Analysis Professional) Certification Training Courses
Connect with us:
- Subscribe to our YouTube Channel
Visit us at https://www.icertglobal.com/ for more information about our professional certification training courses or Call Now! on +1-713-287-1187 / +1-713-287-1214 or e-mail us at info {at} icertglobal {dot} com.
Please Contact Us for more information about our professional certification training courses to accelerate your career. Let us know your thoughts in the 'Comments' section below.
Read More
Organizations throughout the world are increasingly resorting to the tried-and-true bastions of quality control and quality management as they strive to perfect their operations and stay competitive. Lean Six Sigma (LSS) has long been a cornerstone of quality management best practices, with impressive results across a wide range of sectors and critical business processes.
It is a data-driven business management methodology that aims to improve product quality and process excellence by decreasing waste and increasing the value of every stage of the product or service lifecycle.
According to a recent study, about 20% of companies intend to use cross-functional quality processes and teams across design, manufacturing and service. For years, practitioners of Lean Six Sigma and other quality management methodologies have prospered.
To understand Real-world quality management, consider the following:
- The act of managing all activities and duties required to achieve a specified degree of perfection is known as quality management.
- Quality management entails establishing a quality strategy, developing and implementing quality assurance and planning, as well as quality control and improvement.
- Total Quality Management (TQM) necessitates collaboration among all stakeholders in a business to improve processes, products, services and the company's culture.
The overall quality approach explains the culture, mindset and organization that commits to providing better products and services that meet the needs of customers. Total quality management is a management technique that entails the process of improving employer-employee connections and consumer-business relationships in order to achieve better results in the production of goods and services. Let's take a look, how the concepts are managed in real-world situations.
What is the concept of quality management?
The act of overseeing various operations and duties inside a company to guarantee that the products and services given, as well as the means employed to produce them, are consistent is known as quality management. It assists the company in achieving and maintaining a targeted level of quality.
There are four main components to quality management, which are as follows:
- Quality Planning - The process of determining the project's quality criteria and determining how to meet them.
- Quality Improvement - The deliberate alteration of a process in order to improve the outcome confidence or reliability.
- Quality Control - The ongoing endeavor to maintain the integrity and dependability of a process in reaching a goal.
- Quality Assurance - The systematic or planned actions required to provide sufficient reliability so that a certain service or product meets the defined requirements.
Quality management is to guarantee that all stakeholders in an organization collaborate to improve the company's procedures, products, services and culture in order to achieve long-term success based on customer satisfaction.
Quality management is a set of guidelines produced by a team to ensure that the products and services they produce meet the appropriate standards or are suitable for a certain purpose.
- The process begins when the organization establishes quality goals that are agreed upon by both the client and the organization.
- After that, the organization determines how the goals will be measured. It performs the steps required to assess quality. It then finds and corrects any quality concerns that have arisen.
- The final step is to report on the overall degree of quality that has been attained.
The procedure ensures that the team's products and services meet the consumers' expectations.
Methods for Improving Quality
Product improvement, process improvement and people-based improvement are the three components of quality improvement approaches. There are a variety of quality management strategies and procedures that can be used.
Kaizen, Zero Defect Programs, Six Sigma, Quality Circle, Taguchi Methods, Toyota Production System, Kansei Engineering, TRIZ, BPR, OQRM, ISO and Top-Down & Bottom-Up methodologies are just a few of them.
Example of Quality Management
Toyota Corporation's application of the Kanban system is a shining example of excellent quality management. Kanban is an inventory control technique created by Taiichi Ohno to assist in minimizing the accumulation of surplus inventory on the manufacturing line at any given time by providing visibility to both suppliers and purchasers.
Toyota adopted the notion to implement their Just-in-Time (JIT) system, which lets suppliers synchronize raw material orders with production schedules directly. Toyota's manufacturing line improved efficiency by ensuring that the corporation had just enough inventory on hand to match client orders as they came in.
Improving the quality of manufacturing and the supply chain
Manufacturing enterprises are among the best examples of how Lean Six Sigma can aid in the development of high-quality products. For example, in North America, 3M recently used LSS principles in their design and manufacturing capabilities for compressed natural gas systems.
They used cutting-edge materials, technology and Lean Six Sigma experience to improve the overall quality and durability of their natural gas tanks, making them 30% lighter and with 10% more storage than competing tank types. 3M has also devised a long-term strategy to accomplish financial and customer goals by using Lean Six Sigma across manufacturing, supply chain and even customer service.
Manufacturers benefit not only from supplying higher-quality products to customers (with fewer flaws to rectify) but also from the speed with which they can handle issues that arise once they reach the end consumer. This ongoing plan includes quality management as a key component.
The Construction Industry's Quality Management
Construction is a one-time yet creative activity, therefore it's important to keep in mind that it's costly and time-consuming to reproduce a structure (or similar). TQM is used to reduce costs and increase productivity and it is possible to track efforts if results improve. Quality in the construction sector is determined by the level of satisfaction of the designer, builder and homeowners.
Getting Rid of Defects in Pharmaceuticals
Companies that create products that have an influence on the health and safety of daily consumers have a responsibility to ensure that the creation and testing of these items are done in a way that minimizes risk.
Pharmaceutical companies come under this group and they are required by law to ensure that their products are safe. Lean Six Sigma concepts, according to a recent LinkedIn article, may help firms attain this level of confidence in their processes to the point where they are nearly error-free.
LSS is used by pharmaceutical companies to implement end-to-end product testing, predict and eliminate errors during the development and testing life cycles and, as a result, improve product quality and meet compliance requirements. LSS assists them in reducing the risk of passing on tainted or ineffective medications, which can have serious health consequences for patients.
Onboarding Procedures in Healthcare
Long and complicated business processes are well-known in the healthcare industry. One example is Johns Hopkins All Children's Hospital (JHACH), which had a slow and inefficient provider enrollment process (taking up to six months to onboard providers).
JHACH patients who rely on those providers have had their visits with physicians delayed or they have had to see a whole new physician, resulting in dissatisfied patients and low customer satisfaction with the process.
JHACH boosted the number of hospital-employed providers who are active with health plans by nearly 30% by using the Lean Six Sigma workflow, consolidating departments and building a monitoring tool to monitor every stage of the process.
In the long run, the key to hospital business is cost and quality treatment. These principles should be followed by organizations for the best results.
- The patient should come first and the organization should prioritize the customer's needs; treatment should be the top priority.
- A good and engaging leader is in demand and a good leader should always be cautious and able to keep employees engaged in the organization's goals.
- Employee participation means that each employee, even doctors, should feel responsible for their work and become involved in it; only then can the organization benefit from the business.
- The organization must prioritize improvement and conduct regular audits in order to improve the environment.
Software Products of Higher Quality
Software quality assurance (QA) engineers play a critical role in ensuring that software solutions meet stringent quality standards and perform as expected. Certification as a Certified Tester Foundation Level (CTFL) is a requirement for anyone working in the software development and testing industry.
However, actions can be taken to increase quality earlier in the development lifecycle. Lean Six Sigma can assist businesses in reducing waste and superfluous cycles, allowing them to produce items faster and with higher quality.
Among the most essential areas where LSS can help are:
- Value stream analysis is used to discover and eliminate non-value contributed operations.
- Establishing a strategy for obtaining customer feedback and approval on requirements prior to the commencement of development work.
- Establishing a knowledge management system in which all reusable components are stored in a knowledge base and can be accessed later.
- Benchmarking with other team members in order to implement best practices without having to reinvent the wheel every time.
- Resource usage to determine what is being overused and underutilized and to take corrective or preventive measures.
Quality Oriented Culture
Total Quality Management (TQM) is a phrase used by quality experts to describe the use of quality concepts at all levels of a business. While TQM has typically implied widespread use of process tools and analytical procedures, the definition has broadened to include the entire organization's larger cultural norms.
The extension of TQM to cover both explicit efforts by people to enhance Quality and the underlying beliefs, philosophies and behaviors on which those efforts are based are referred to as Culture of Quality.
A successful Quality Culture is one in which the organization's core Quality values, such as a focus on responding to customer needs and the importance of data-based decision-making and workers' basic assumptions about the nature of human relationships and their places in the world, such as the value of collaborative relationships among people with common goals and the importance of developing long-term personal connections, are closely integrated.
Because core values are overtly expressed and understood at all levels of the organization, they are relatively easy to measure. Even the people who hold basic ideas typically resist explicit analysis, making participation at this level challenging.
A Culture of Quality can only be achieved when leaders and employees have a common understanding of not only the core values and processes they utilize and promote but also their underlying assumptions about the nature of work and human interactions on which those core values are based.
Quality Management Principles
The International Standard for Quality Management adheres to a number of quality management concepts. Top management uses these ideas to guide an organization's procedures toward higher performance. They are as follows:
1) Customer Service Focus
The fundamental goal of every firm should be to satisfy and surpass the expectations and needs of its consumers. When a company can understand and cater to its consumers' current and future demands, it builds client loyalty, which leads to increased income.
The company is also capable of identifying and satisfying new consumer opportunities. When business operations are more efficient, quality improves and more customers are able to be satisfied.
2) People's Participation
Another important aspect is employee involvement. Whether full-time, part-time, outsourced, or in-house, management engages employees in developing and delivering value. Employees should be encouraged to continually develop their abilities and maintain consistency in their work.
Empowering employees, including them in decision-making and acknowledging their accomplishments are all part of this philosophy. People work to their full potential when they feel valued, as it enhances their confidence and motivation. Employees feel empowered and accountable for their actions when they are fully involved.
3) Leadership
Good leadership leads to the success of an organization. Great leadership creates a sense of purpose and togetherness among employees and shareholders. Creating a vibrant corporate culture creates an internal climate in which people may completely fulfill their potential and actively participate in attaining company goals.
Employees should be involved in the development of clear organizational goals and objectives by leaders. Employees are motivated as a result and their productivity and loyalty may improve dramatically.
4) Approach to the Process
According to the process approach principle, an organization's performance is critical. The approach principle focuses on improving organizational processes' efficiency and effectiveness.
The concept assumes that good processes lead to increased consistency, faster actions, lower costs, waste elimination and continual improvement. When leaders can manage and control the organization's inputs and outputs, as well as the processes that produce the outputs, the organization benefits.
5) Continuous Enhancement
Every organization should have a goal to actively participate in continuous development. Businesses that continuously improve see a higher performance, organizational flexibility and the ability to seize new possibilities. Businesses should be able to constantly establish new procedures and adapt to changing market conditions.
6) Making Decisions Based on Evidence
Businesses should use a data-driven approach to decision-making. Businesses that base their decisions on verified and studied data have a better understanding of the market. They may complete tasks that provide the necessary results and justify their previous actions.
Factual decision making is critical for understanding the cause-and-effect relationships of various things and explaining probable unintended repercussions and results.
7) Management of Relationships
Creating mutually beneficial relationships with suppliers and retailers is the goal of relationship management. A company's performance can be influenced by a variety of stakeholders.
To maximize their impact on the company's success, the organization should manage the supply chain process well and enhance the relationship between the organization and its suppliers. When an organization effectively manages its relationships with interested parties, it is more likely to achieve long-term business success and collaboration.
The Advantages of Quality Management
- It assists an organization in achieving more consistency in the tasks and activities associated with the production of products and services.
- It enhances process efficiency, minimizes waste and makes better use of time and other resources.
- It contributes to increased consumer satisfaction.
- It enables enterprises to efficiently sell their products and enter new markets.
- It makes it easier for organizations to integrate new personnel, allowing them to manage growth more smoothly.
- It enables a company to constantly enhance its goods, processes and systems.
Conclusion
Customers understand the importance of quality in products and services. Suppliers know that quality can be a key differentiator between their own and competitors' offers (quality differentiation is also called the quality gap).
The quality gap between competing products and services has narrowed dramatically during the last two decades. This is due in part to manufacturing contracting (also known as outsourcing) to nations such as China and India, as well as the internationalization of commerce and competition.
In order to fulfill worldwide standards and client needs, these countries, among many others, have upgraded their own quality requirements. Quality culture, the relevance of knowledge management and the role of leadership in promoting and achieving high quality have all become more prominent themes.
Systems thinking, for example, is bringing more holistic methods to quality management, in which people, processes and products are all examined together rather than as separate components in quality management.
Quality culture has been acknowledged by government agencies and industrial organizations that regulate products as a way to help enterprises develop those items. According to a survey of more than 60 global organizations, companies with a bad quality culture had increased costs of $67 million per year for every 5000 employees compared to companies with a good quality culture.
iCert Global will help you to find best related certifications courses under Quality Management.
The company conducts both Instructor-led Classroom training workshops and Instructor-led Live Online Training sessions for learners from across the United States and around the world.
We also provide Corporate Training for enterprise workforce development
Professional Certification Training:
Quality Management Training:
- Lean Six Sigma Yellow Belt (LSSYB) Certification Training Courses
- Lean Six Sigma Green Belt (LSSGB) Certification Training Courses
- Lean Six Sigma Black Belt (LSSBB) Certification Training Courses
Scrum Training:
- CSM (Certified ScrumMaster) Certification Training Courses
Agile Training:
- PMI-ACP (Agile Certified Professional) Certification Training Courses
DevOps Training:
- DevOps Certification Training Courses
Business Analysis Training by iCert Global:
- ECBA (Entry Certificate in Business Analysis) Certification Training Courses
- CCBA (Certificate of Capability in Business Analysis) Certification Training Courses
- CBAP (Certified Business Analysis Professional) Certification Training Courses
Connect with us:
- Subscribe to our YouTube Channel
Visit us at https://www.icertglobal.com/ for more information about our professional certification training courses or Call Now! on +1-713-287-1187 / +1-713-287-1214 or e-mail us at info {at} icertglobal {dot} com.
Please Contact Us for more information about our professional certification training courses to accelerate your career. Let us know your thoughts in the 'Comments' section below.
Project Quality Management and its key processes explained
:
Project quality is the degree of excellence of the deliverables to meet the customers’ requirements and satisfaction. The project outcome should fulfill the suitability for its intended purpose. The common characteristics of project quality are:
- Consistency: The evenness in the performance and services are delivered in the same way to all the beneficiaries.
- Suitability: The quality of being an appropriate choice to perform a task
- Completeness: The quality of finishing the specified task to meet the project scope.
- Sustainability: The ability to be maintained at a certain level.
- Functionality: The purpose of the task or activity to be fulfilled
- Reliability: The measure of being trust-worthy
- Performance: The act of performing a task or project activity.
- Timeliness: The measure to finish the project task in the allotted time.
The quality of the project is defined in the following terms:
- Validation: The assurance to meet the satisfactory results.
- Verification: The compliance required to meet project requirements.
- Precision: The condition of being exact.
- Accuracy: The degree or measure of the closeness
- Tolerance: The range of the acceptable results
Six Sigma and Lean Six Sigma are implemented in an organization to maintain the desired quality. Elimination of errors and continuous improvement is the main aim of implementing Lean Six Sigma.
There are many quality management software in the market to maintain the quality of the organization.
According to Transparency Market Research,
“Quality Management Software Market to Rise at a Stellar 13.20% CAGR, with Rising Demand for Maintaining Product Quality”.
What is Project Quality Management?
Project Quality Management is a continuous process to prevent, avoid and fix the poor quality issue in order to meet or exceed customer satisfaction. The performance of an organization is measured, monitored and controlled through quality policies, standards, guidelines, and procedures.
Project Quality Management is important due to the following reasons:
- Customer satisfaction
- Consistent performance
- Higher efficiency
- Enhance understanding between the internal processes
- Risk Reduction at an early stage
- References to secure other projects
Project Quality Management is one of the 10 knowledge areas of project management.
What are the processes in Project Quality Management?
There are three processes involved in Project Quality Management in three phases: Planning, Execution, and Monitoring and Controlling.
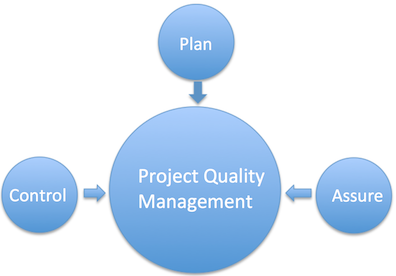
Plan Quality Management process
In order to maintain the desired quality, inspecting the quality is not the only solution. Preventing poor quality issues through effective planning and foresight is a regular practice in the organization. Plan Quality Management is the process of identifying the quality requirements and quality standards relevant to the project output. The quality plan is developed in such a way that it does not affect project scope, time and cost.
The document of a set of quality standards is prepared for each project's activities. The methodology used, the resource assigned, the cost and the time allocated are the major factors affecting quality.
There are several tools used to plan the quality process. There are some tools used for both planning and controlling quality:
- Cause and Effect diagram – helps to find the various factors related to the potential problems.
- Flowchart – Displays the logical steps in the project and various elements related to the system. Used to analyze the potential problems.
- Pareto Diagram – Used to identify the frequent small problems causing the big problem. The graph is used to define the percentage of defects against the number of causes.
- Histogram – Used to identify common problems.
- Control chart – Determines whether the cost and schedule are within statistical control
- Scatter diagram – tracks two variables and determines their relationship.
Manage Quality process
Manage Quality is the process of managing all the project activities according to the Quality Management plan while executing. To manage the quality, the following inputs are required
- Project Management Plan
- Project Documents like Lessons Learned, Quality Metrics
- Organizational Process Assets
The tools and techniques used to manage the quality are:
- Data Gathering - Checklists
- Data Analysis- Process Analysis, Root Cause Analysis
- Decision Making- Multi-Criteria Decision Analysis
- Data Representation- Histogram, graphs, and flowcharts
- Audits- Determining if the project activities comply with organizational policies, procedures, and processes.
- Design for X- Set of technical guidelines
- Problem-Solving- Solved through set of solutions
- Quality Improvement Methods- Plan-Do-Check-Act (PDCA) cycle or Six Sigma
The output of managing the quality process is:
- Quality reports
- Test and evaluation documents
- Change Requests
- Project Management Plan Updates
- Project Document Updates
The main objective of managing the quality process is to integrate all the quality policies in the project activities to maintain the Quality Plan Management.
Control Quality Process
The Control Quality Process is the process of inspecting and verifying the executed project activities according to quality management. The main objective of this process is to ensure the project output is correct, complete and meet the expectations of the customer and the quality plan. This process also includes the documentation of results obtained during the control quality process.
To manage the quality, the following inputs are required
- Project Management Plan
- Project Documents like Lessons Learned, Quality Metrics
- Approved change requests
- Deliverables
- Work Performance data
- Enterprise Environmental Factors
- Organizational Process Assets
The outputs of the Perform Quality Control process are:
- Measurements
- Validated changes
- Updates to the project management plan and project documents
- Change requests
- Lessons learned
- Validated deliverables
Do visit our Corporate Training to know more about core offerings for enterprises in empowering their workforce.
Download Free PMP® Exam Practice Test with 200 PMP® Questions.
Full-length PMP sample test with 200 PMP exam prep questions.
You may also be interested in Sample PMP® Exam Prep Questions before you download the Free PMP® Practice Test.
Download our Free PMP Brochure for more information.
iCert Global conducts Project Management, Quality Management, Business Analysis, Agile, Scrum, and DevOps Certification courses across various locations in the United States.
Visit us at https://www.icertglobal.com/ for more information about our professional certification training courses or Call Now! on +1-713-287-1187 / +1-713-287-1214 or e-mail us at info {at} icertglobal {dot} com.
Project Management Training by iCert Global:
Quality Management Training by iCert Global:
- Lean Six Sigma Yellow Belt (LSSYB) Certification Training Courses
- Lean Six Sigma Green Belt (LSSGB) Certification Training Courses
- Lean Six Sigma Black Belt (LSSBB) Certification Training Courses
Scrum Training by iCert Global:
- CSM (Certified ScrumMaster) Certification Training Courses
Agile Training by iCert Global:
- PMI-ACP (Agile Certified Professional) Certification Training Courses
DevOps Training by iCert Global:
- DevOps Certification Training Courses
Business Analysis Training by iCert Global:
- ECBA (Entry Certificate in Business Analysis) Certification Training Courses
- CCBA (Certificate of Capability in Business Analysis) Certification Training Courses
- CBAP (Certified Business Analysis Professional) Certification Training Courses
The company conducts both instructor-led Classroom training workshops and Instructor-led Live Online Training sessions for learners from across the United States and around the world.
Please contact Us for more information about our professional certification training courses to accelerate your career in the new year. Wish you all the best for your learning initiatives in the new year.
Which certifications are you aiming to achieve in the New Year? Let us know your thoughts in the 'Comments' section below. Thank you.
Read More
:
Project quality is the degree of excellence of the deliverables to meet the customers’ requirements and satisfaction. The project outcome should fulfill the suitability for its intended purpose. The common characteristics of project quality are:
- Consistency: The evenness in the performance and services are delivered in the same way to all the beneficiaries.
- Suitability: The quality of being an appropriate choice to perform a task
- Completeness: The quality of finishing the specified task to meet the project scope.
- Sustainability: The ability to be maintained at a certain level.
- Functionality: The purpose of the task or activity to be fulfilled
- Reliability: The measure of being trust-worthy
- Performance: The act of performing a task or project activity.
- Timeliness: The measure to finish the project task in the allotted time.
The quality of the project is defined in the following terms:
- Validation: The assurance to meet the satisfactory results.
- Verification: The compliance required to meet project requirements.
- Precision: The condition of being exact.
- Accuracy: The degree or measure of the closeness
- Tolerance: The range of the acceptable results
Six Sigma and Lean Six Sigma are implemented in an organization to maintain the desired quality. Elimination of errors and continuous improvement is the main aim of implementing Lean Six Sigma.
There are many quality management software in the market to maintain the quality of the organization.
According to Transparency Market Research,
“Quality Management Software Market to Rise at a Stellar 13.20% CAGR, with Rising Demand for Maintaining Product Quality”.
What is Project Quality Management?
Project Quality Management is a continuous process to prevent, avoid and fix the poor quality issue in order to meet or exceed customer satisfaction. The performance of an organization is measured, monitored and controlled through quality policies, standards, guidelines, and procedures.
Project Quality Management is important due to the following reasons:
- Customer satisfaction
- Consistent performance
- Higher efficiency
- Enhance understanding between the internal processes
- Risk Reduction at an early stage
- References to secure other projects
Project Quality Management is one of the 10 knowledge areas of project management.
What are the processes in Project Quality Management?
There are three processes involved in Project Quality Management in three phases: Planning, Execution, and Monitoring and Controlling.
Plan Quality Management process
In order to maintain the desired quality, inspecting the quality is not the only solution. Preventing poor quality issues through effective planning and foresight is a regular practice in the organization. Plan Quality Management is the process of identifying the quality requirements and quality standards relevant to the project output. The quality plan is developed in such a way that it does not affect project scope, time and cost.
The document of a set of quality standards is prepared for each project's activities. The methodology used, the resource assigned, the cost and the time allocated are the major factors affecting quality.
There are several tools used to plan the quality process. There are some tools used for both planning and controlling quality:
- Cause and Effect diagram – helps to find the various factors related to the potential problems.
- Flowchart – Displays the logical steps in the project and various elements related to the system. Used to analyze the potential problems.
- Pareto Diagram – Used to identify the frequent small problems causing the big problem. The graph is used to define the percentage of defects against the number of causes.
- Histogram – Used to identify common problems.
- Control chart – Determines whether the cost and schedule are within statistical control
- Scatter diagram – tracks two variables and determines their relationship.
Manage Quality process
Manage Quality is the process of managing all the project activities according to the Quality Management plan while executing. To manage the quality, the following inputs are required
- Project Management Plan
- Project Documents like Lessons Learned, Quality Metrics
- Organizational Process Assets
The tools and techniques used to manage the quality are:
- Data Gathering - Checklists
- Data Analysis- Process Analysis, Root Cause Analysis
- Decision Making- Multi-Criteria Decision Analysis
- Data Representation- Histogram, graphs, and flowcharts
- Audits- Determining if the project activities comply with organizational policies, procedures, and processes.
- Design for X- Set of technical guidelines
- Problem-Solving- Solved through set of solutions
- Quality Improvement Methods- Plan-Do-Check-Act (PDCA) cycle or Six Sigma
The output of managing the quality process is:
- Quality reports
- Test and evaluation documents
- Change Requests
- Project Management Plan Updates
- Project Document Updates
The main objective of managing the quality process is to integrate all the quality policies in the project activities to maintain the Quality Plan Management.
Control Quality Process
The Control Quality Process is the process of inspecting and verifying the executed project activities according to quality management. The main objective of this process is to ensure the project output is correct, complete and meet the expectations of the customer and the quality plan. This process also includes the documentation of results obtained during the control quality process.
To manage the quality, the following inputs are required
- Project Management Plan
- Project Documents like Lessons Learned, Quality Metrics
- Approved change requests
- Deliverables
- Work Performance data
- Enterprise Environmental Factors
- Organizational Process Assets
The outputs of the Perform Quality Control process are:
- Measurements
- Validated changes
- Updates to the project management plan and project documents
- Change requests
- Lessons learned
- Validated deliverables
Do visit our Corporate Training to know more about core offerings for enterprises in empowering their workforce.
Download Free PMP® Exam Practice Test with 200 PMP® Questions.
Full-length PMP sample test with 200 PMP exam prep questions.
You may also be interested in Sample PMP® Exam Prep Questions before you download the Free PMP® Practice Test.
Download our Free PMP Brochure for more information.
iCert Global conducts Project Management, Quality Management, Business Analysis, Agile, Scrum, and DevOps Certification courses across various locations in the United States.
Visit us at https://www.icertglobal.com/ for more information about our professional certification training courses or Call Now! on +1-713-287-1187 / +1-713-287-1214 or e-mail us at info {at} icertglobal {dot} com.
Project Management Training by iCert Global:
Quality Management Training by iCert Global:
- Lean Six Sigma Yellow Belt (LSSYB) Certification Training Courses
- Lean Six Sigma Green Belt (LSSGB) Certification Training Courses
- Lean Six Sigma Black Belt (LSSBB) Certification Training Courses
Scrum Training by iCert Global:
- CSM (Certified ScrumMaster) Certification Training Courses
Agile Training by iCert Global:
- PMI-ACP (Agile Certified Professional) Certification Training Courses
DevOps Training by iCert Global:
- DevOps Certification Training Courses
Business Analysis Training by iCert Global:
- ECBA (Entry Certificate in Business Analysis) Certification Training Courses
- CCBA (Certificate of Capability in Business Analysis) Certification Training Courses
- CBAP (Certified Business Analysis Professional) Certification Training Courses
The company conducts both instructor-led Classroom training workshops and Instructor-led Live Online Training sessions for learners from across the United States and around the world.
Please contact Us for more information about our professional certification training courses to accelerate your career in the new year. Wish you all the best for your learning initiatives in the new year.
Which certifications are you aiming to achieve in the New Year? Let us know your thoughts in the 'Comments' section below. Thank you.
What is Project Quality Management and What are the Processes in Project Quality Management?
:
Project quality is the degree of excellence of the deliverables to meet the customers’ requirements and satisfaction. The project outcome should fulfill the suitability for its intended purpose. The common characteristics of project quality are:
- Consistency: The evenness in the performance and services are delivered in the same way to all the beneficiaries.
- Suitability: The quality of being an appropriate choice to perform a task
- Completeness: The quality of finishing the specified task to meet the project scope.
- Sustainability: The ability to be maintained at a certain level.
- Functionality: The purpose of the task or activity to be fulfilled
- Reliability: The measure of being trust-worthy
- Performance: The act of performing a task or project activity.
- Timeliness: The measure to finish the project task in the allotted time.
The quality of the project is defined in the following terms:
- Validation: The assurance to meet the satisfactory results.
- Verification: The compliance required to meet project requirements.
- Precision: The condition of being exact.
- Accuracy: The degree or measure of the closeness
- Tolerance: The range of the acceptable results
Six Sigma and Lean Six Sigma are implemented in an organization to maintain the desired quality. Elimination of errors and continuous improvement is the main aim of implementing Lean Six Sigma.
There are many quality management software in the market to maintain the quality of the organization.
According to Transparency Market Research,
“Quality Management Software Market to Rise at a Stellar 13.20% CAGR, with Rising Demand for Maintaining Product Quality”.
What is Project Quality Management?
Project Quality Management is a continuous process to prevent, avoid and fix the poor quality issue in order to meet or exceed customer satisfaction. The performance of an organization is measured, monitored and controlled through quality policies, standards, guidelines, and procedures.
Project Quality Management is important due to the following reasons:
- Customer satisfaction
- Consistent performance
- Higher efficiency
- Enhance understanding between the internal processes
- Risk Reduction at an early stage
- References to secure other projects
Project Quality Management is one of the 10 knowledge areas of project management.
What are the processes in Project Quality Management?
There are three processes involved in Project Quality Management in three phases: Planning, Execution, and Monitoring and Controlling.
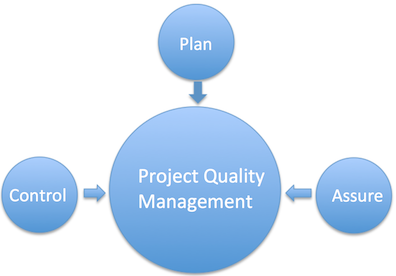
Plan Quality Management process
In order to maintain the desired quality, inspecting the quality is not the only solution. Preventing poor quality issues through effective planning and foresight is a regular practice in the organization. Plan Quality Management is the process of identifying the quality requirements and quality standards relevant to the project output. The quality plan is developed in such a way that it does not affect project scope, time and cost.
The document of a set of quality standards is prepared for each project's activities. The methodology used, the resource assigned, the cost and the time allocated are the major factors affecting quality.
There are several tools used to plan the quality process. There are some tools used for both planning and controlling quality:
- Cause and Effect diagram – helps to find the various factors related to the potential problems.
- Flowchart – Displays the logical steps in the project and various elements related to the system. Used to analyze the potential problems.
- Pareto Diagram – Used to identify the frequent small problems causing the big problem. The graph is used to define the percentage of defects against the number of causes.
- Histogram – Used to identify common problems.
- Control chart – Determines whether the cost and schedule are within statistical control
- Scatter diagram – tracks two variables and determines their relationship.
Manage Quality process
Manage Quality is the process of managing all the project activities according to the Quality Management plan while executing. To manage the quality, the following inputs are required
- Project Management Plan
- Project Documents like Lessons Learned, Quality Metrics
- Organizational Process Assets
The tools and techniques used to manage the quality are:
- Data Gathering - Checklists
- Data Analysis- Process Analysis, Root Cause Analysis
- Decision Making- Multi-Criteria Decision Analysis
- Data Representation- Histogram, graphs, and flowcharts
- Audits- Determining if the project activities comply with organizational policies, procedures, and processes.
- Design for X- Set of technical guidelines
- Problem-Solving- Solved through set of solutions
- Quality Improvement Methods- Plan-Do-Check-Act (PDCA) cycle or Six Sigma
The output of managing the quality process is:
- Quality reports
- Test and evaluation documents
- Change Requests
- Project Management Plan Updates
- Project Document Updates
The main objective of managing the quality process is to integrate all the quality policies in the project activities to maintain the Quality Plan Management.
Control Quality Process
The Control Quality Process is the process of inspecting and verifying the executed project activities according to quality management. The main objective of this process is to ensure the project output is correct, complete and meet the expectations of the customer and the quality plan. This process also includes the documentation of results obtained during the control quality process.
To manage the quality, the following inputs are required
- Project Management Plan
- Project Documents like Lessons Learned, Quality Metrics
- Approved change requests
- Deliverables
- Work Performance data
- Enterprise Environmental Factors
- Organizational Process Assets
The outputs of the Perform Quality Control process are:
- Measurements
- Validated changes
- Updates to the project management plan and project documents
- Change requests
- Lessons learned
- Validated deliverables
Do visit our Corporate Training to know more about core offerings for enterprises in empowering their workforce.
Download Free PMP® Exam Practice Test with 200 PMP® Questions.
Full-length PMP sample test with 200 PMP exam prep questions.
You may also be interested in Sample PMP® Exam Prep Questions before you download the Free PMP® Practice Test.
Download our Free PMP Brochure for more information.
iCert Global conducts Project Management, Quality Management, Business Analysis, Agile, Scrum, and DevOps Certification courses across various locations in the United States.
Visit us at https://www.icertglobal.com/ for more information about our professional certification training courses or Call Now! on +1-713-287-1187 / +1-713-287-1214 or e-mail us at info {at} icertglobal {dot} com.
Project Management Training by iCert Global:
Quality Management Training by iCert Global:
- Lean Six Sigma Yellow Belt (LSSYB) Certification Training Courses
- Lean Six Sigma Green Belt (LSSGB) Certification Training Courses
- Lean Six Sigma Black Belt (LSSBB) Certification Training Courses
Scrum Training by iCert Global:
- CSM (Certified ScrumMaster) Certification Training Courses
Agile Training by iCert Global:
- PMI-ACP (Agile Certified Professional) Certification Training Courses
DevOps Training by iCert Global:
- DevOps Certification Training Courses
Business Analysis Training by iCert Global:
- ECBA (Entry Certificate in Business Analysis) Certification Training Courses
- CCBA (Certificate of Capability in Business Analysis) Certification Training Courses
- CBAP (Certified Business Analysis Professional) Certification Training Courses
The company conducts both Instructor-led Classroom training workshops and Instructor-led Live Online Training sessions for learners from across the United States and around the world.
Please Contact Us for more information about our professional certification training courses to accelerate your career in the new year. Wish you all the best for your learning initiatives in the new year.
Which certifications are you aiming to achieve in the New Year? Let us know your thoughts in the 'Comments' section below. Thank you.
Read More
:
Project quality is the degree of excellence of the deliverables to meet the customers’ requirements and satisfaction. The project outcome should fulfill the suitability for its intended purpose. The common characteristics of project quality are:
- Consistency: The evenness in the performance and services are delivered in the same way to all the beneficiaries.
- Suitability: The quality of being an appropriate choice to perform a task
- Completeness: The quality of finishing the specified task to meet the project scope.
- Sustainability: The ability to be maintained at a certain level.
- Functionality: The purpose of the task or activity to be fulfilled
- Reliability: The measure of being trust-worthy
- Performance: The act of performing a task or project activity.
- Timeliness: The measure to finish the project task in the allotted time.
The quality of the project is defined in the following terms:
- Validation: The assurance to meet the satisfactory results.
- Verification: The compliance required to meet project requirements.
- Precision: The condition of being exact.
- Accuracy: The degree or measure of the closeness
- Tolerance: The range of the acceptable results
Six Sigma and Lean Six Sigma are implemented in an organization to maintain the desired quality. Elimination of errors and continuous improvement is the main aim of implementing Lean Six Sigma.
There are many quality management software in the market to maintain the quality of the organization.
According to Transparency Market Research,
“Quality Management Software Market to Rise at a Stellar 13.20% CAGR, with Rising Demand for Maintaining Product Quality”.
What is Project Quality Management?
Project Quality Management is a continuous process to prevent, avoid and fix the poor quality issue in order to meet or exceed customer satisfaction. The performance of an organization is measured, monitored and controlled through quality policies, standards, guidelines, and procedures.
Project Quality Management is important due to the following reasons:
- Customer satisfaction
- Consistent performance
- Higher efficiency
- Enhance understanding between the internal processes
- Risk Reduction at an early stage
- References to secure other projects
Project Quality Management is one of the 10 knowledge areas of project management.
What are the processes in Project Quality Management?
There are three processes involved in Project Quality Management in three phases: Planning, Execution, and Monitoring and Controlling.
Plan Quality Management process
In order to maintain the desired quality, inspecting the quality is not the only solution. Preventing poor quality issues through effective planning and foresight is a regular practice in the organization. Plan Quality Management is the process of identifying the quality requirements and quality standards relevant to the project output. The quality plan is developed in such a way that it does not affect project scope, time and cost.
The document of a set of quality standards is prepared for each project's activities. The methodology used, the resource assigned, the cost and the time allocated are the major factors affecting quality.
There are several tools used to plan the quality process. There are some tools used for both planning and controlling quality:
- Cause and Effect diagram – helps to find the various factors related to the potential problems.
- Flowchart – Displays the logical steps in the project and various elements related to the system. Used to analyze the potential problems.
- Pareto Diagram – Used to identify the frequent small problems causing the big problem. The graph is used to define the percentage of defects against the number of causes.
- Histogram – Used to identify common problems.
- Control chart – Determines whether the cost and schedule are within statistical control
- Scatter diagram – tracks two variables and determines their relationship.
Manage Quality process
Manage Quality is the process of managing all the project activities according to the Quality Management plan while executing. To manage the quality, the following inputs are required
- Project Management Plan
- Project Documents like Lessons Learned, Quality Metrics
- Organizational Process Assets
The tools and techniques used to manage the quality are:
- Data Gathering - Checklists
- Data Analysis- Process Analysis, Root Cause Analysis
- Decision Making- Multi-Criteria Decision Analysis
- Data Representation- Histogram, graphs, and flowcharts
- Audits- Determining if the project activities comply with organizational policies, procedures, and processes.
- Design for X- Set of technical guidelines
- Problem-Solving- Solved through set of solutions
- Quality Improvement Methods- Plan-Do-Check-Act (PDCA) cycle or Six Sigma
The output of managing the quality process is:
- Quality reports
- Test and evaluation documents
- Change Requests
- Project Management Plan Updates
- Project Document Updates
The main objective of managing the quality process is to integrate all the quality policies in the project activities to maintain the Quality Plan Management.
Control Quality Process
The Control Quality Process is the process of inspecting and verifying the executed project activities according to quality management. The main objective of this process is to ensure the project output is correct, complete and meet the expectations of the customer and the quality plan. This process also includes the documentation of results obtained during the control quality process.
To manage the quality, the following inputs are required
- Project Management Plan
- Project Documents like Lessons Learned, Quality Metrics
- Approved change requests
- Deliverables
- Work Performance data
- Enterprise Environmental Factors
- Organizational Process Assets
The outputs of the Perform Quality Control process are:
- Measurements
- Validated changes
- Updates to the project management plan and project documents
- Change requests
- Lessons learned
- Validated deliverables
Do visit our Corporate Training to know more about core offerings for enterprises in empowering their workforce.
Download Free PMP® Exam Practice Test with 200 PMP® Questions.
Full-length PMP sample test with 200 PMP exam prep questions.
You may also be interested in Sample PMP® Exam Prep Questions before you download the Free PMP® Practice Test.
Download our Free PMP Brochure for more information.
iCert Global conducts Project Management, Quality Management, Business Analysis, Agile, Scrum, and DevOps Certification courses across various locations in the United States.
Visit us at https://www.icertglobal.com/ for more information about our professional certification training courses or Call Now! on +1-713-287-1187 / +1-713-287-1214 or e-mail us at info {at} icertglobal {dot} com.
Project Management Training by iCert Global:
Quality Management Training by iCert Global:
- Lean Six Sigma Yellow Belt (LSSYB) Certification Training Courses
- Lean Six Sigma Green Belt (LSSGB) Certification Training Courses
- Lean Six Sigma Black Belt (LSSBB) Certification Training Courses
Scrum Training by iCert Global:
- CSM (Certified ScrumMaster) Certification Training Courses
Agile Training by iCert Global:
- PMI-ACP (Agile Certified Professional) Certification Training Courses
DevOps Training by iCert Global:
- DevOps Certification Training Courses
Business Analysis Training by iCert Global:
- ECBA (Entry Certificate in Business Analysis) Certification Training Courses
- CCBA (Certificate of Capability in Business Analysis) Certification Training Courses
- CBAP (Certified Business Analysis Professional) Certification Training Courses
The company conducts both Instructor-led Classroom training workshops and Instructor-led Live Online Training sessions for learners from across the United States and around the world.
Please Contact Us for more information about our professional certification training courses to accelerate your career in the new year. Wish you all the best for your learning initiatives in the new year.
Which certifications are you aiming to achieve in the New Year? Let us know your thoughts in the 'Comments' section below. Thank you.
What are the 5 phases of Lean Six Sigma?
:
Lean Six Sigma (LSS) is a process of solving a problem in order to maintain the quality of the project. Lean and six sigma both are two different methods. Lean is a systematic approach to identify and reduce project activities that are not required. Six Sigma is a problem-solving methodology that focuses on continuous improvement with minimum defects. A combination of Lean and Six Sigma results in increased quality and revenue.
Lean Six Sigma certification is a quality management certification offered by the International Association of Six Sigma Certifications (IASSC™) designed to reduce variations and eliminate waste which ensures the quality of the process. It solves an existing problem with unknown causes.
LSS methodology is based on a problem-solving framework with a cycle called DMAIC. It is a data-driven quality strategy for improving the quality of the process. DMAIC is a five-phase process and is an acronym of:
- Define
- Measure
- Analyze
- Improve
- Control
DMAIC is pronounced as, “duh-may-ik.”
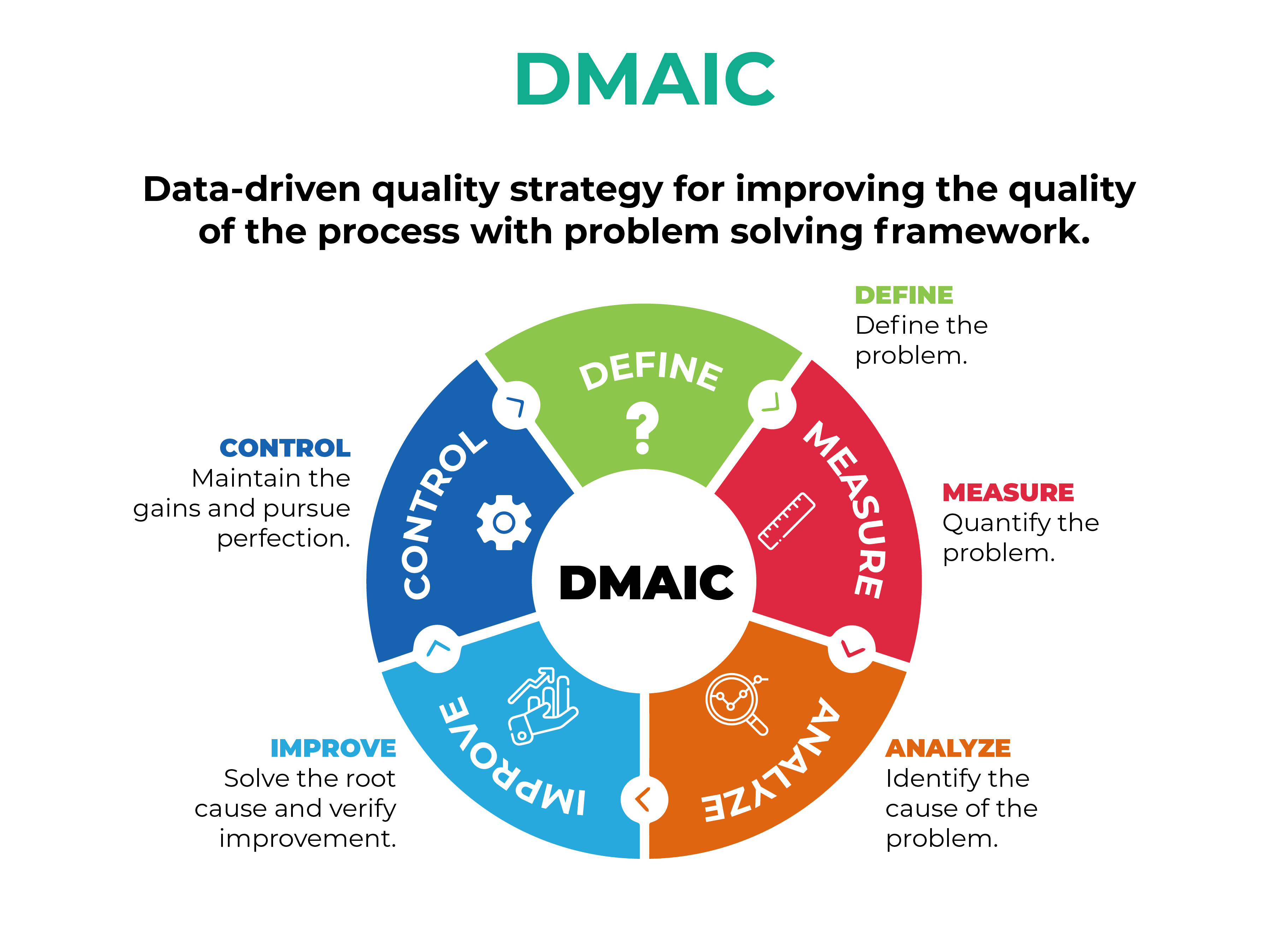
Define
The first phase of Lean Six Sigma is to Define. The main aim of the define phase is to define the “problem statement” and plan the improvement initiative. In order to understand the overview of the project, ‘Project Charter’ is created.
The project charter is a key element that describes the whole project in brief. The project charter generally includes the objective of the project, stakeholders, requirements, high-level assumptions and constraints.
Define phase includes,
- Defining problems by developing a “problem statement” document
- Defining the project goal by developing “Goal Statement” document
- Defining the process of the project by developing a process map
- Defining the requirements from the customer
Problem statement: It is a document created to know about the symptoms of the problem and its effect. First, the indications of the issue are confirmed and then the problems are prioritized.
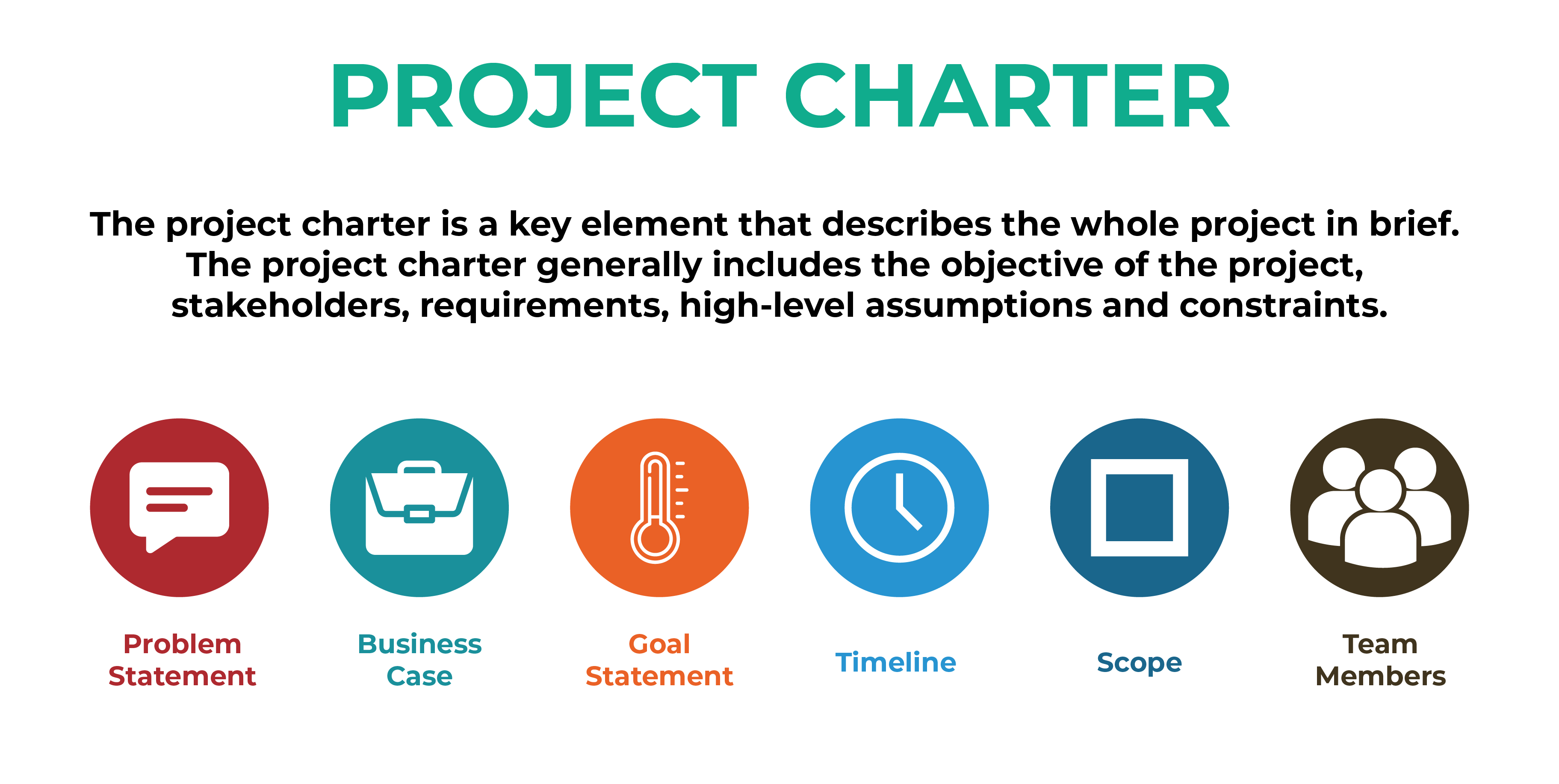
Tools used in defining phase:
A project charter is used to define Goal Statement
SIPOC: Suppliers, Inputs, Process, Outputs, and Customers. SIPOC is a high-level map used for developing process maps.
Similarly, Value Stream Map and Swimlane Maps are used.
In order to define the customer and their requirement Voice of the Customer (VOC), Translation Matrix and Tree Diagram are used.
After defining all the above statements, A3, Relationship Map and Stakeholder Analysis are used to inform others about the progress of the project.
Measure
In this phase, the magnitude of the problem is identified. In order to measure the problems, baseline or the start point is created. Before making any changes, the baseline is created. Measure phase is vital because the data collected for the project will be used throughout the project.
The Measure phase involves,
- Creating a baseline
- Root cause analysis is done for the problems identified
- Baseline Data collection
- Ensuring the data collected is reliable
- Update the project charter
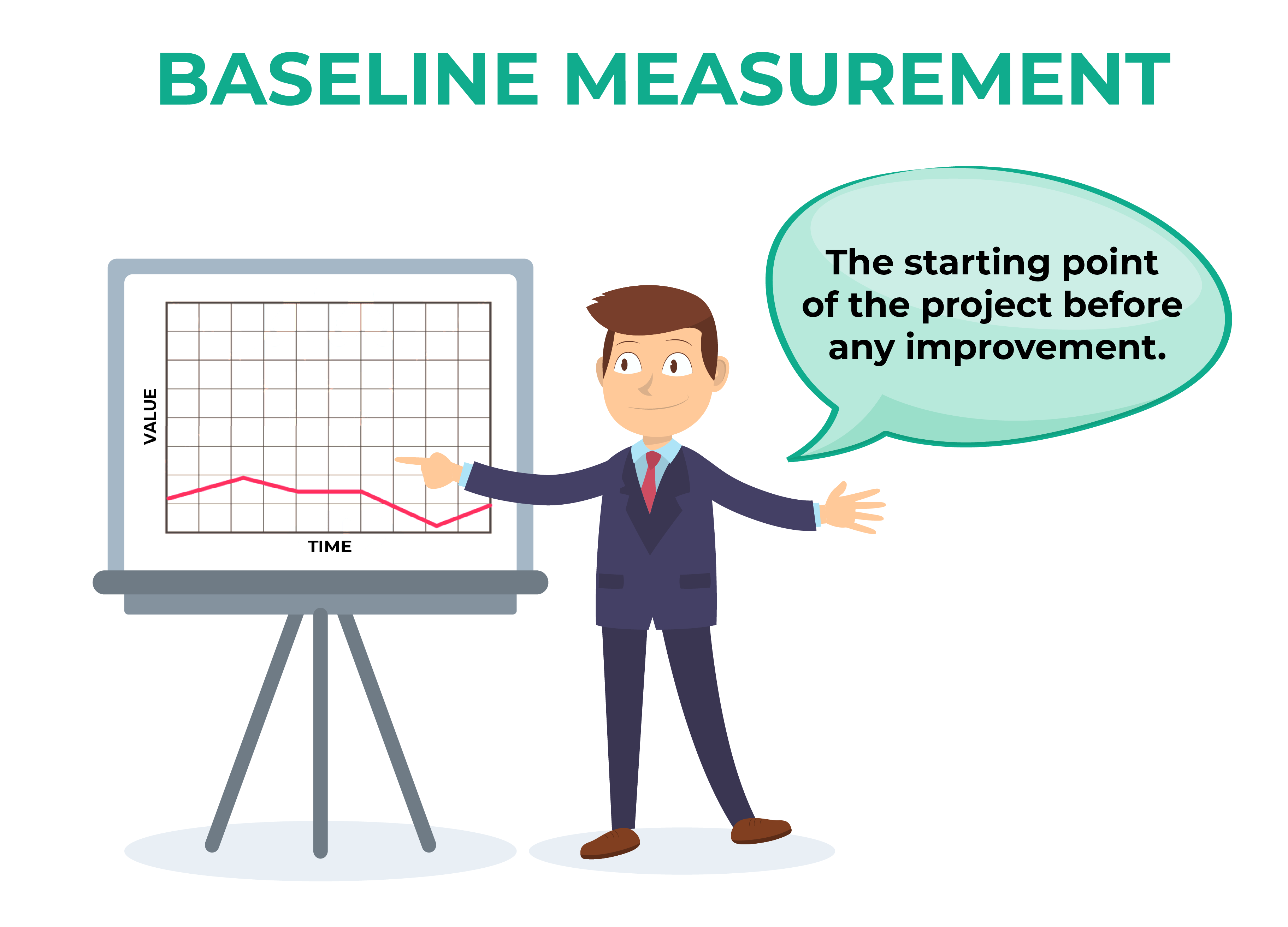
The main aim of this phase is to determine the current performance and refine the definition of each measure. This results in an improvement in quality and reduction in lead time.
The tools used in Measure phase are:
Data collection plan is used to define where to get the data, how much data is required, who will be responsible for data collection and how to collect the data.
Operational definitions are used to define and refine the processes that lead to collecting critical process information.
The check sheet is used to collect the baseline data
The collected data and the changes are updated in the Project charter.
Analyze
In order to get the solution, The problems have to be analyzed. This phase is carried out parallelly with the measure phase. When the data is reviewed in the measure phase, the person reviewing might adjust the additional data in the data project plan. The processes and the data are analyzed in order to verify the root cause of the defects.
This phase involves,
Examining the process: When the process maps are created in the Measure phase, the problems and defects are listed within the process. Then process analysis is carried out which consists of,
- Time Analysis: work time versus the waiting time.
- Value-Added Analysis: Analyzing the process through the customer’s point of view in terms of cost.
- Value Stream Mapping: Mapping of process data with value-added analysis in order to remove the waste.
Visually inspecting the data: Inspecting the data collected using charts and graphs
Analyzing the root causes by developing the theories on all the possible causes. The problems are analyzed by brainstorming together.
Verifying the causes of the defects through,
- Process analysis
- Data analysis
- Process observation
- Comparative analysis.
Updating the project charter after finalizing the process performance and scope of improvement.
The tools used in Analyze phase are:
Value stream mapping and Value-added Flow Analysis use to examine the process.
Run Charts, Histograms, Box Plots, and Pareto Charts are used to visually analyze the data.
Fishbone Diagram and the 5Whys are used to analyze the root cause.
Root Cause Hypothesis is used to verify the causes of the defects.
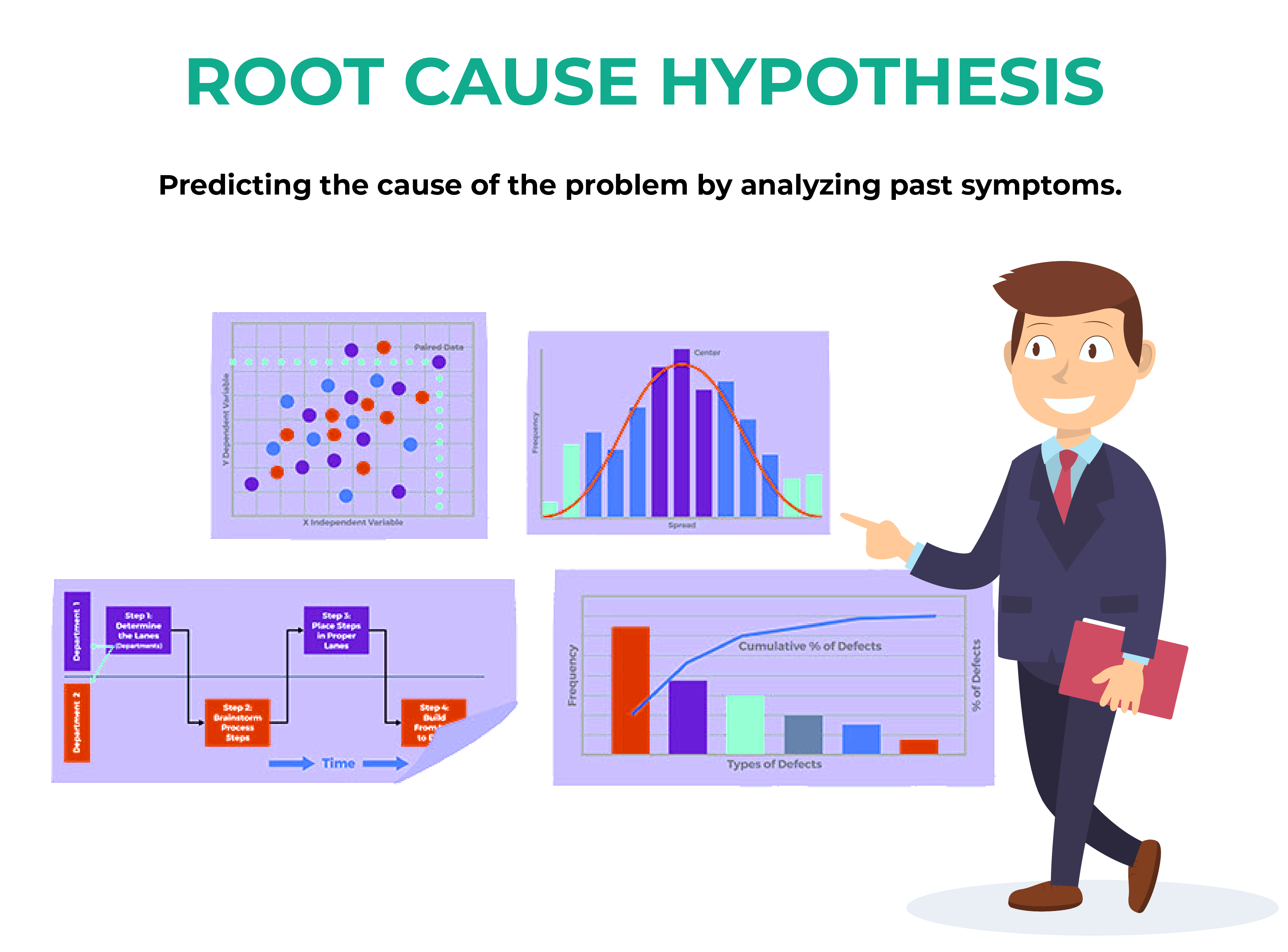
Improve
Once the root causes are determined, the solutions are developed and implemented. In this phase, the ideas are produced to solve the problem. In this phase, the team refines the ideas by collecting all the ideas, monitor process changes and finally implement the ideas.
This phase involves,
- Listing out all the possible ideas that might fix the problem: Techniques like, Cross-Training, Setup Reduction, Kanbans are used to bring out the innovative ideas for the defects or problems identified.
- Selecting the best of solutions.
- Process-based maps are developed based on different solutions
- Based on the process map, the best solution is decided
- The solution decided is implemented.
- Measurable improvement is recorded.
The tools used in this phase:
- To brainstorm solution Benchmarking and Classic lean improvements are used.
- Weighed Criteria Matrix is used to make the best decision and Impact Effort Matrix is used to assess the solutions providing the best impact.
- To-Be Map, Value Stream Map and Swimlane Maps are used to develop a process map.
- PDCA (Plan Do Check Act ) is used to select the solution. PDCA is a mini testing cycle carried out in order to select the best one.
- A pilot checklist is used to implement the plan
- Process changes are measured to check the improvement against the baseline.
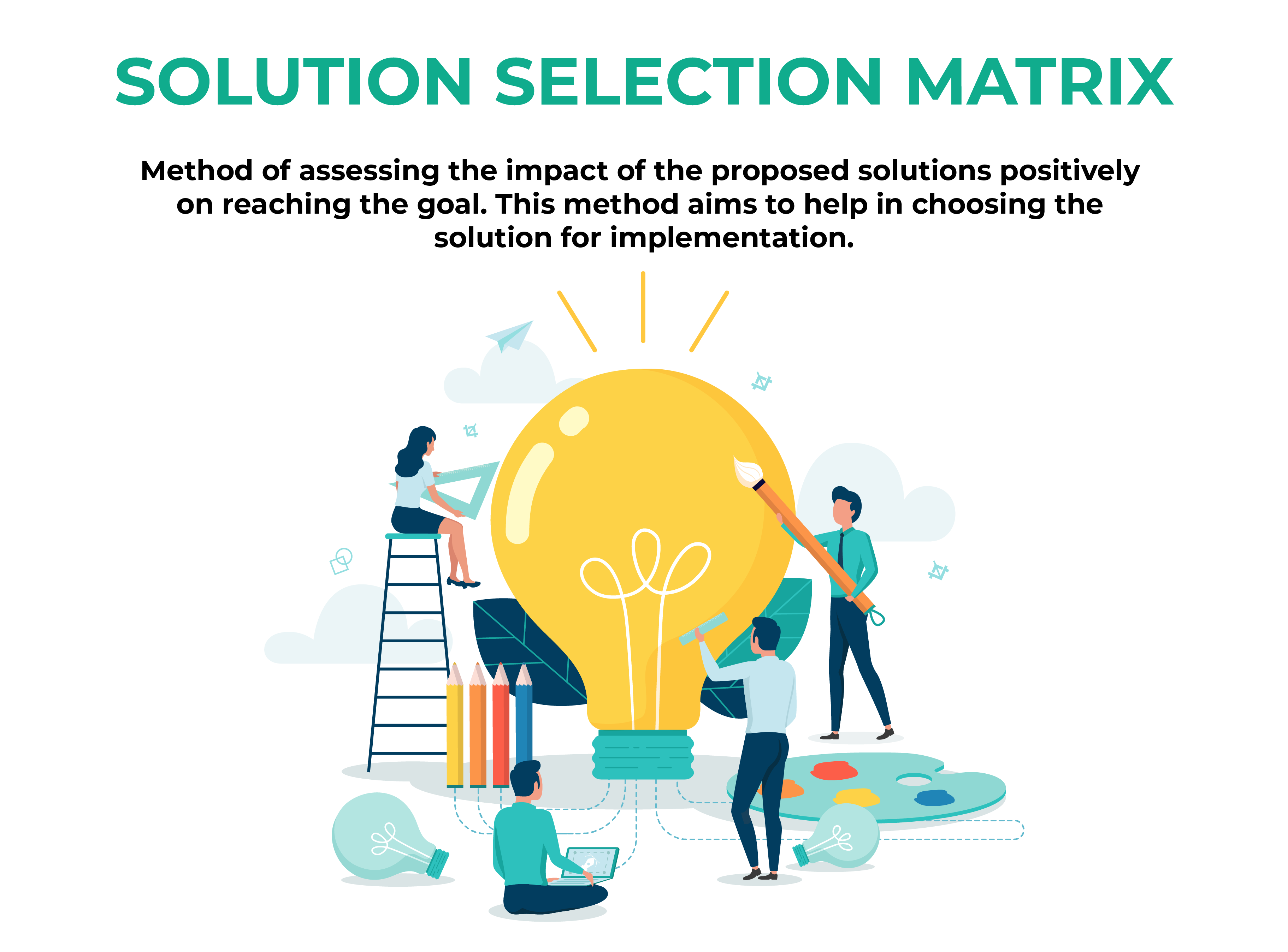
Control
Once the problem is fixed, it is very essential to maintain it. This phase aims to create a monitoring plan, measure success, update process and develop a response plan if any dip is found.
Control phase is based on 4 principles:
- Value: To determine the steps which are important and are valued.
- Flow: The flow of the project process to be maintained smoothly.
- Pull: To ensure the customer’s demand is aligned with a process change.
- Perfection: The accuracy in the process.
This phase involves:
Ensuring the project process is continuously monitored using Lean. The response plan is prepared that involves the level at which the performance started to dip or reduce.
Recording the improved or changed process. Visual workspace is created to ensure others follow the new process.
Applying the improvement in all the areas. The knowledge gained in one project is applied in all the other areas of the organization.
Share the improvement and project success with everyone.
How to Get Lean Six Sigma Certified?
There is no such prerequisite to take any of the Lean Six Sigma Certification exams accredited by IASSC™. LSS has a hierarchy of certifications to progress in career path:
Who is the Target Audience for Lean Six Sigma Certification?
- Quality Managers
- Quality System Managers
- Quality Engineers
- Quality Supervisors
- Quality Analysts
- Quality Auditors
- Team Leaders
- Software Professionals
- Project Managers
- Improvement Managers
- Operational line managers
What is the average annual salary of Lean six sigma certified professionals?
According to ZipRecruiter, as dated on Feb 06, 2020,
The average annual salary for certified Lean Six Sigma professionals:
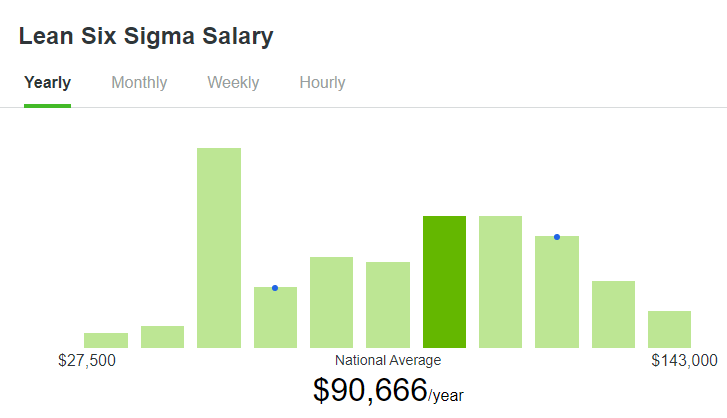
What is the exam format for the Lean Six Sigma Certification?
Lean Six Sigma Yellow Belt
60 multiple-choice questions
Duration: 2 hours
Qualifying points: 230 points out of 300 points
Lean Six Sigma Green Belt
100 questions
Duration: 3 hours
Qualifying points: 385 points out of 500 points
Lean Six Sigma Black Belt
150 questions
Duration: 4 hours
Qualifying points: 580 points out of 750 points
How to maintain Lean Six Sigma Credentials?
Lean six sigma certifications have no expiry date.
For more information on how you can accelerate your career with these certifications, visit us at https://www.icertglobal.com/ or call now on +1-713-287-1213 / 1214 or e-mail us at info {at} icertglobal {dot} com.
We provide instructor-led classroom and instructor-led live online training across the globe. We also provide Corporate Training for enterprise workforce development.
Quality Management Training by iCert Global:
- Lean Six Sigma Yellow Belt (LSSYB) Certification Training Courses
- Lean Six Sigma Green Belt (LSSGB) Certification Training Courses
- Lean Six Sigma Black Belt (LSSBB) Certification Training Courses
Scrum Training by iCert Global:
- CSM (Certified ScrumMaster) Certification Training Courses
Agile Training by iCert Global:
- PMI-ACP (Agile Certified Professional) Certification Training Courses
DevOps Training by iCert Global:
- DevOps Certification Training Courses
Business Analysis Training by iCert Global:
- ECBA (Entry Certificate in Business Analysis) Certification Training Courses
- CCBA (Certificate of Capability in Business Analysis) Certification Training Courses
- CBAP (Certified Business Analysis Professional) Certification Training Courses
iCert Global both Instructor-led Classroom training workshops and Instructor-led Live Online Training sessions for learners from across the United States and around the world.
Please Contact Us for more information about our professional certification training courses to accelerate your career in the new year. Wish you all the best for your learning initiatives in the new year.
Which certifications are you aiming to achieve in 2020? Let us know your thoughts in the 'Comments' section below.
Thank you for reading this blog post. Hope you found it useful and interesting. Team iCert Global wishes you all the best for your learning endeavors.
Read More
:
Lean Six Sigma (LSS) is a process of solving a problem in order to maintain the quality of the project. Lean and six sigma both are two different methods. Lean is a systematic approach to identify and reduce project activities that are not required. Six Sigma is a problem-solving methodology that focuses on continuous improvement with minimum defects. A combination of Lean and Six Sigma results in increased quality and revenue.
Lean Six Sigma certification is a quality management certification offered by the International Association of Six Sigma Certifications (IASSC™) designed to reduce variations and eliminate waste which ensures the quality of the process. It solves an existing problem with unknown causes.
LSS methodology is based on a problem-solving framework with a cycle called DMAIC. It is a data-driven quality strategy for improving the quality of the process. DMAIC is a five-phase process and is an acronym of:
- Define
- Measure
- Analyze
- Improve
- Control
DMAIC is pronounced as, “duh-may-ik.”
Define
The first phase of Lean Six Sigma is to Define. The main aim of the define phase is to define the “problem statement” and plan the improvement initiative. In order to understand the overview of the project, ‘Project Charter’ is created.
The project charter is a key element that describes the whole project in brief. The project charter generally includes the objective of the project, stakeholders, requirements, high-level assumptions and constraints.
Define phase includes,
- Defining problems by developing a “problem statement” document
- Defining the project goal by developing “Goal Statement” document
- Defining the process of the project by developing a process map
- Defining the requirements from the customer
Problem statement: It is a document created to know about the symptoms of the problem and its effect. First, the indications of the issue are confirmed and then the problems are prioritized.
Tools used in defining phase:
A project charter is used to define Goal Statement
SIPOC: Suppliers, Inputs, Process, Outputs, and Customers. SIPOC is a high-level map used for developing process maps.
Similarly, Value Stream Map and Swimlane Maps are used.
In order to define the customer and their requirement Voice of the Customer (VOC), Translation Matrix and Tree Diagram are used.
After defining all the above statements, A3, Relationship Map and Stakeholder Analysis are used to inform others about the progress of the project.
Measure
In this phase, the magnitude of the problem is identified. In order to measure the problems, baseline or the start point is created. Before making any changes, the baseline is created. Measure phase is vital because the data collected for the project will be used throughout the project.
The Measure phase involves,
- Creating a baseline
- Root cause analysis is done for the problems identified
- Baseline Data collection
- Ensuring the data collected is reliable
- Update the project charter
The main aim of this phase is to determine the current performance and refine the definition of each measure. This results in an improvement in quality and reduction in lead time.
The tools used in Measure phase are:
Data collection plan is used to define where to get the data, how much data is required, who will be responsible for data collection and how to collect the data.
Operational definitions are used to define and refine the processes that lead to collecting critical process information.
The check sheet is used to collect the baseline data
The collected data and the changes are updated in the Project charter.
Analyze
In order to get the solution, The problems have to be analyzed. This phase is carried out parallelly with the measure phase. When the data is reviewed in the measure phase, the person reviewing might adjust the additional data in the data project plan. The processes and the data are analyzed in order to verify the root cause of the defects.
This phase involves,
Examining the process: When the process maps are created in the Measure phase, the problems and defects are listed within the process. Then process analysis is carried out which consists of,
- Time Analysis: work time versus the waiting time.
- Value-Added Analysis: Analyzing the process through the customer’s point of view in terms of cost.
- Value Stream Mapping: Mapping of process data with value-added analysis in order to remove the waste.
Visually inspecting the data: Inspecting the data collected using charts and graphs
Analyzing the root causes by developing the theories on all the possible causes. The problems are analyzed by brainstorming together.
Verifying the causes of the defects through,
- Process analysis
- Data analysis
- Process observation
- Comparative analysis.
Updating the project charter after finalizing the process performance and scope of improvement.
The tools used in Analyze phase are:
Value stream mapping and Value-added Flow Analysis use to examine the process.
Run Charts, Histograms, Box Plots, and Pareto Charts are used to visually analyze the data.
Fishbone Diagram and the 5Whys are used to analyze the root cause.
Root Cause Hypothesis is used to verify the causes of the defects.
Improve
Once the root causes are determined, the solutions are developed and implemented. In this phase, the ideas are produced to solve the problem. In this phase, the team refines the ideas by collecting all the ideas, monitor process changes and finally implement the ideas.
This phase involves,
- Listing out all the possible ideas that might fix the problem: Techniques like, Cross-Training, Setup Reduction, Kanbans are used to bring out the innovative ideas for the defects or problems identified.
- Selecting the best of solutions.
- Process-based maps are developed based on different solutions
- Based on the process map, the best solution is decided
- The solution decided is implemented.
- Measurable improvement is recorded.
The tools used in this phase:
- To brainstorm solution Benchmarking and Classic lean improvements are used.
- Weighed Criteria Matrix is used to make the best decision and Impact Effort Matrix is used to assess the solutions providing the best impact.
- To-Be Map, Value Stream Map and Swimlane Maps are used to develop a process map.
- PDCA (Plan Do Check Act ) is used to select the solution. PDCA is a mini testing cycle carried out in order to select the best one.
- A pilot checklist is used to implement the plan
- Process changes are measured to check the improvement against the baseline.
Control
Once the problem is fixed, it is very essential to maintain it. This phase aims to create a monitoring plan, measure success, update process and develop a response plan if any dip is found.
Control phase is based on 4 principles:
- Value: To determine the steps which are important and are valued.
- Flow: The flow of the project process to be maintained smoothly.
- Pull: To ensure the customer’s demand is aligned with a process change.
- Perfection: The accuracy in the process.
This phase involves:
Ensuring the project process is continuously monitored using Lean. The response plan is prepared that involves the level at which the performance started to dip or reduce.
Recording the improved or changed process. Visual workspace is created to ensure others follow the new process.
Applying the improvement in all the areas. The knowledge gained in one project is applied in all the other areas of the organization.
Share the improvement and project success with everyone.
How to Get Lean Six Sigma Certified?
There is no such prerequisite to take any of the Lean Six Sigma Certification exams accredited by IASSC™. LSS has a hierarchy of certifications to progress in career path:
Who is the Target Audience for Lean Six Sigma Certification?
- Quality Managers
- Quality System Managers
- Quality Engineers
- Quality Supervisors
- Quality Analysts
- Quality Auditors
- Team Leaders
- Software Professionals
- Project Managers
- Improvement Managers
- Operational line managers
What is the average annual salary of Lean six sigma certified professionals?
According to ZipRecruiter, as dated on Feb 06, 2020,
The average annual salary for certified Lean Six Sigma professionals:
What is the exam format for the Lean Six Sigma Certification?
Lean Six Sigma Yellow Belt
60 multiple-choice questions
Duration: 2 hours
Qualifying points: 230 points out of 300 points
Lean Six Sigma Green Belt
100 questions
Duration: 3 hours
Qualifying points: 385 points out of 500 points
Lean Six Sigma Black Belt
150 questions
Duration: 4 hours
Qualifying points: 580 points out of 750 points
How to maintain Lean Six Sigma Credentials?
Lean six sigma certifications have no expiry date.
For more information on how you can accelerate your career with these certifications, visit us at https://www.icertglobal.com/ or call now on +1-713-287-1213 / 1214 or e-mail us at info {at} icertglobal {dot} com.
We provide instructor-led classroom and instructor-led live online training across the globe. We also provide Corporate Training for enterprise workforce development.
Quality Management Training by iCert Global:
- Lean Six Sigma Yellow Belt (LSSYB) Certification Training Courses
- Lean Six Sigma Green Belt (LSSGB) Certification Training Courses
- Lean Six Sigma Black Belt (LSSBB) Certification Training Courses
Scrum Training by iCert Global:
- CSM (Certified ScrumMaster) Certification Training Courses
Agile Training by iCert Global:
- PMI-ACP (Agile Certified Professional) Certification Training Courses
DevOps Training by iCert Global:
- DevOps Certification Training Courses
Business Analysis Training by iCert Global:
- ECBA (Entry Certificate in Business Analysis) Certification Training Courses
- CCBA (Certificate of Capability in Business Analysis) Certification Training Courses
- CBAP (Certified Business Analysis Professional) Certification Training Courses
iCert Global both Instructor-led Classroom training workshops and Instructor-led Live Online Training sessions for learners from across the United States and around the world.
Please Contact Us for more information about our professional certification training courses to accelerate your career in the new year. Wish you all the best for your learning initiatives in the new year.
Which certifications are you aiming to achieve in 2020? Let us know your thoughts in the 'Comments' section below.
Thank you for reading this blog post. Hope you found it useful and interesting. Team iCert Global wishes you all the best for your learning endeavors.
Quality Management - Six Sigma
Automation is almost everywhere, and head more in the IT sphere. Of course it started from there and soon spread to other industries. It wasn’t a question when they are introduced in software industry, especially in testing. It was more about the replacement skilled hands good at manual testing. No matter how good you are testing, there is a slack on everyone as the day wears out, human fatigue, wear and tear is all part of the daily rigor, but for a machine that’s lifeless and programmed to perform complex and complicated work, there is no such fatigue except the glitch, which the engineers anticipate, preempt before deploying into production.
There is flip side into automation but the benefits far overweigh manual testing and hence the job loss. With automation taking over as a technological drive, it was only a matter of time before manual testing would replace men with machines. That’s the reality and sooner one reconciles and find alternatives to stay relevant, and required there is less to worry about pink slips.
It is a technique that was devised way back in 1990s by two engineers working in Motorola to improve the quality by decreasing the numbers of errors that might occur. It is basically about identifying the causes of the errors, and systematically removing there errors, so that there will be not any recurrence. The quality engineer follows management methods based on experimentation and observation and analyse their findings through statistical methods.
The higher the probability of reducing the errors, then higher will the profitability to the organization. This was the underlying principle. This practice created a specialized pool of talented people who have an eye of detecting the flaws and direction solutions to fix.
They follow a step of methods that sequential in inspecting and identifying the defect to create a defect-free product. Statistically speaking 3.4 defective features per million opportunities means 99.99966% of all opportunities to produce some feature of a part that are free from defects. That is six sigma in a nut shell.
Six Sigma Green Belt Certification
Couresty:wiki
DPMO is Defect Per Million Opportunities. From the chart, it is evident the desired six sigma level is 6.
Along with the various level of identification came the expertise with in a person to handle six-sigma related projects and to evaluate their expertise, karate belts like yellow, black were used to identify the skillset of the six sigma professionals.
The Six Sigma Green Belt professionals are generally employees who are involved with maintenance of Six-Sigma as part of their job responsibilities. This does mean that this is their only job but one among many parts of their line of work. Six Sigma Certification Online is very much possible as training centers provide different modes of imparting knowledge transfer: Instructor-led Classroom, Instructor-Led Online Class and E-Learning.
There are many benefits of Sig Sigma testing, some of which are highlighted below:
Improved quality: when Motorola initiated in early 90s, it almost went unnoticed. Jack Welch made it popular when he announced the annual results and heads started turns to Six Sigma and more companies followed suit.
Increased ROI: As mentioned above, higher probability of reducing the errors leads to greater profitability to the organization.
Greater Customer Satisfaction: It’s a win-win where both the stakeholders are happy: the client and vendor.
Employee Recognition. The employees who worked in bringing the turnaround by tightly controlling the defects deserve due appreciation and accolade.
image courtesy: goo.gl/sfgsje
Read More
Automation is almost everywhere, and head more in the IT sphere. Of course it started from there and soon spread to other industries. It wasn’t a question when they are introduced in software industry, especially in testing. It was more about the replacement skilled hands good at manual testing. No matter how good you are testing, there is a slack on everyone as the day wears out, human fatigue, wear and tear is all part of the daily rigor, but for a machine that’s lifeless and programmed to perform complex and complicated work, there is no such fatigue except the glitch, which the engineers anticipate, preempt before deploying into production.
There is flip side into automation but the benefits far overweigh manual testing and hence the job loss. With automation taking over as a technological drive, it was only a matter of time before manual testing would replace men with machines. That’s the reality and sooner one reconciles and find alternatives to stay relevant, and required there is less to worry about pink slips.
It is a technique that was devised way back in 1990s by two engineers working in Motorola to improve the quality by decreasing the numbers of errors that might occur. It is basically about identifying the causes of the errors, and systematically removing there errors, so that there will be not any recurrence. The quality engineer follows management methods based on experimentation and observation and analyse their findings through statistical methods.
The higher the probability of reducing the errors, then higher will the profitability to the organization. This was the underlying principle. This practice created a specialized pool of talented people who have an eye of detecting the flaws and direction solutions to fix.
They follow a step of methods that sequential in inspecting and identifying the defect to create a defect-free product. Statistically speaking 3.4 defective features per million opportunities means 99.99966% of all opportunities to produce some feature of a part that are free from defects. That is six sigma in a nut shell.
Six Sigma Green Belt Certification
Couresty:wiki
DPMO is Defect Per Million Opportunities. From the chart, it is evident the desired six sigma level is 6.
Along with the various level of identification came the expertise with in a person to handle six-sigma related projects and to evaluate their expertise, karate belts like yellow, black were used to identify the skillset of the six sigma professionals.
The Six Sigma Green Belt professionals are generally employees who are involved with maintenance of Six-Sigma as part of their job responsibilities. This does mean that this is their only job but one among many parts of their line of work. Six Sigma Certification Online is very much possible as training centers provide different modes of imparting knowledge transfer: Instructor-led Classroom, Instructor-Led Online Class and E-Learning.
There are many benefits of Sig Sigma testing, some of which are highlighted below:
Improved quality: when Motorola initiated in early 90s, it almost went unnoticed. Jack Welch made it popular when he announced the annual results and heads started turns to Six Sigma and more companies followed suit.
Increased ROI: As mentioned above, higher probability of reducing the errors leads to greater profitability to the organization.
Greater Customer Satisfaction: It’s a win-win where both the stakeholders are happy: the client and vendor.
Employee Recognition. The employees who worked in bringing the turnaround by tightly controlling the defects deserve due appreciation and accolade.
image courtesy: goo.gl/sfgsje
The 5 Whys and Root Cause Analysis Quality Management
Mostly employed in root cause analysis, 5 Whys prominently appears in the Analyze phase of DMAIC in Six Sigma. This technique iteratively interrogative in nature, mainly used to identify to the root cause or defect, was developed by Sakichi Toyoda and used in the Toyota Motor Corporation. [source: wiki]
Experts have varied opinions about this methodology which is often performed by a fish-bone diagram. There is no single root cause, if observed closely. Usually, it is a chain of events or combination of factors. Identification of the bug is a critical challenge and there are various methods and techniques. One such identified method is 5-why. This helps to understand the top 5 root causes which predominantly contribute to the problem .
The method might sound basic but very effective. The question is often posed from the answer received and it’s an iterative model. You can try and picture as some day-to-day issues you find yourself troubleshooting by find the root cause, like the scores of your child in a recently held d test paper. It’s as much questioning your child “why did you grades dip?” and from response offered by your child, there is a counter question –answer, till you are convinced one way or the other.
Why did your grades dip?
I didn’t do the exam properly.
Why didn’t you do the exam properly?
I couldn’t answer most of the questions.
Why couldn’t you answer most of the questions?
The questions were not familiar.
Why weren’t the questions familiar?
I had not prepared well enough.
Why didn’t you prepare?
Because I was playing and missed on the time to prepare.
Finally, it’s the lack of preparation that led to the poor performance. This might be your conclusion drawn from the conversation. And the advice or course of action is to ‘gear up well and be more prepared to face the next test.’
Here is another example from a professional backdrop:
Apply the same to a project to analyze about a failure – which we call it the root cause analysis.
There is no rule to stop the questioning at 5-level. It can go further. General studies reveal that ‘5 why’ usually lead to the main reason(s) of failure.
To illustrate further the 5 Whys, take a look at the image :
Limitation
This method suffers from its own share of shortfalls. The technique stops at the symptoms level and fails to dig deeper at the lower-level root causes. The results not being repeatable is a major constraint in this method. Besides, ‘Why’ can lead to multiple root causes but there is an inclination to isolate a single root cause and stick to it.
The limitations aside, 5 Whys is nevertheless is significantly used in Root Cause Analysis (RCA).
Read More
Quality Management: A true test of the tester’s expertise.
The iron triangle of project management has scope+ time+ cost and at the core rests the Quality. Meaning none of the axes can be compromised, which consequently impact Quality adversely. So what’s about Quality? Well, everything boils down to Quality. Standards are Quality measure. High standards attributes to High Quality. Well, when thoughts transcend from personal experience as Project Manager, I always ensured the quality team has the final word on everything shipped much to the chagrin of the development team. They often sparred as to ‘who called the shots?’ and I will put my best foot forward “I do” to the eerie silence of the team. A team is a bunch of individuals with their own talent, and that’s why we refer recruitment more as Talent Acquisition. No matter the nomenclature associated, no two individuals are going to be the same. Like-minded perhaps, but unlikely twins in thoughts. So it’s a mixed pool. Fundamentally its still the make, sell, support, and the Quality team falls under the support bucket while developers act as the breadwinners in the ‘make’ stream, and hence feel privileged and even entitled. At the inception of the project, when the Developers roll up the sleeves and get busy writing Unit Cases, testers too are full of activity preparing test cases. So the any claim of entitlement is very juvenile in judgement and I dare say never to expect anything additional other than the allocated. One incident always enlivens and worth narrating. He was a super-duper geek that touching his code is deemed an insult. It’s like rinsed with Listerine mouth freshener every five minutes that the teeth are sparkling white and fragrant. One should marvel at the pride taken in their work that they come down to challenge “check my code and any bug, I am toasted else you are roasted”. I found a demure girl, belying her age, walking up to the rock star “I am sorry but there seems to be a bug”. A volcano just erupted. When the pride is pricked, what else can you expect? Fireworks. I was observing the exchange from a distance but didn't intervene. They are professionals and ought to conduct like one. A dent to his dignity, he mounts a ferocious attack justifying every nook and corner while the tester patiently hears him out. After a full fifteen minutes of explanation, the girl calmly states “I understand but it’s a bug”. The developer slams his forehead and unloads a heap of curses in which one expletive burst out unbeknown. Now discipline and decorum can never be conceded at any cost. Since the unfortunate exchange happened on the floor, the shrill pitch made heads turn around. The lady was unmoved and strangely didn't emote at all but retained her composure. The developer, in sharp contrast, was belligerent and a nervous wreck. However sharp you might be, team play takes prominence and position. Both approached my desk and my silence spelled ANGER. My glare at nowhere but all ears, I wanted to hear one word ‘sorry’ instead he defied everything that’s sacrosanct and conduct hardly propriety. I demanded ‘Apologize. Now’. It was not a counsel but a command, and reluctantly he budged and muttered the apology. He might be a rock star but that lady’s attitude made her much taller and he dwarfed in stature. I then requested the tester to walk through the bug and she clearly made her case which was watertight. Confounded with the bug and confused as how his code can be cracked, the developer was at his wits ends and close to tears. Passion is different to taking things personal. After all to err is human. Managing people is far too different and difficult than project. My call still remained unaltered ‘the tester will have the final word’ and pausing “if the client finds fault in the UAT [User Acceptance Testing], it will the tester who will be taken to task”. Even that developer smiled. Much rests on the shoulders of the tester who are gate-keepers. Nothing can or should slip or creep between their legs. With an eye for details and investigating instincts to sniff something unusual, they treat every test case as a suspect and once convinced of merits pass it for clearance. That tester demonstrated typical traits expected – the poise, politeness, profound knowledge, patience, perseverance, while the other (Developer) displayed pettiness. Her signature statement was bereft of sentiment but well stated “I am more concerned about the Quality of the Project just as you are about the principles of Project Management.” Well said! Quality Management is a key knowledge area in PMP® Certification exam. For more details visit http://goo.gl/U4Rtez
images courtesy: goo.gl/FtgC51
Read More
The iron triangle of project management has scope+ time+ cost and at the core rests the Quality. Meaning none of the axes can be compromised, which consequently impact Quality adversely. So what’s about Quality? Well, everything boils down to Quality. Standards are Quality measure. High standards attributes to High Quality. Well, when thoughts transcend from personal experience as Project Manager, I always ensured the quality team has the final word on everything shipped much to the chagrin of the development team. They often sparred as to ‘who called the shots?’ and I will put my best foot forward “I do” to the eerie silence of the team. A team is a bunch of individuals with their own talent, and that’s why we refer recruitment more as Talent Acquisition. No matter the nomenclature associated, no two individuals are going to be the same. Like-minded perhaps, but unlikely twins in thoughts. So it’s a mixed pool. Fundamentally its still the make, sell, support, and the Quality team falls under the support bucket while developers act as the breadwinners in the ‘make’ stream, and hence feel privileged and even entitled. At the inception of the project, when the Developers roll up the sleeves and get busy writing Unit Cases, testers too are full of activity preparing test cases. So the any claim of entitlement is very juvenile in judgement and I dare say never to expect anything additional other than the allocated. One incident always enlivens and worth narrating. He was a super-duper geek that touching his code is deemed an insult. It’s like rinsed with Listerine mouth freshener every five minutes that the teeth are sparkling white and fragrant. One should marvel at the pride taken in their work that they come down to challenge “check my code and any bug, I am toasted else you are roasted”. I found a demure girl, belying her age, walking up to the rock star “I am sorry but there seems to be a bug”. A volcano just erupted. When the pride is pricked, what else can you expect? Fireworks. I was observing the exchange from a distance but didn't intervene. They are professionals and ought to conduct like one. A dent to his dignity, he mounts a ferocious attack justifying every nook and corner while the tester patiently hears him out. After a full fifteen minutes of explanation, the girl calmly states “I understand but it’s a bug”. The developer slams his forehead and unloads a heap of curses in which one expletive burst out unbeknown. Now discipline and decorum can never be conceded at any cost. Since the unfortunate exchange happened on the floor, the shrill pitch made heads turn around. The lady was unmoved and strangely didn't emote at all but retained her composure. The developer, in sharp contrast, was belligerent and a nervous wreck. However sharp you might be, team play takes prominence and position. Both approached my desk and my silence spelled ANGER. My glare at nowhere but all ears, I wanted to hear one word ‘sorry’ instead he defied everything that’s sacrosanct and conduct hardly propriety. I demanded ‘Apologize. Now’. It was not a counsel but a command, and reluctantly he budged and muttered the apology. He might be a rock star but that lady’s attitude made her much taller and he dwarfed in stature. I then requested the tester to walk through the bug and she clearly made her case which was watertight. Confounded with the bug and confused as how his code can be cracked, the developer was at his wits ends and close to tears. Passion is different to taking things personal. After all to err is human. Managing people is far too different and difficult than project. My call still remained unaltered ‘the tester will have the final word’ and pausing “if the client finds fault in the UAT [User Acceptance Testing], it will the tester who will be taken to task”. Even that developer smiled. Much rests on the shoulders of the tester who are gate-keepers. Nothing can or should slip or creep between their legs. With an eye for details and investigating instincts to sniff something unusual, they treat every test case as a suspect and once convinced of merits pass it for clearance. That tester demonstrated typical traits expected – the poise, politeness, profound knowledge, patience, perseverance, while the other (Developer) displayed pettiness. Her signature statement was bereft of sentiment but well stated “I am more concerned about the Quality of the Project just as you are about the principles of Project Management.” Well said! Quality Management is a key knowledge area in PMP® Certification exam. For more details visit http://goo.gl/U4Rtez
images courtesy: goo.gl/FtgC51
CMMI certification improves process maturity and efficiency
CMMI is a proven approach to performance management with decades of results showing it works. Organizations using CMMI have predictable cost, schedule, and quality—business results that serve as discriminators among their competitors. CMMI is built with practices and goals seen in thousands of real organizations worldwide. Use these practices and goals to evaluate your own performance and decide what to improve for your own business reasons.
Read More
CMMI is a proven approach to performance management with decades of results showing it works. Organizations using CMMI have predictable cost, schedule, and quality—business results that serve as discriminators among their competitors. CMMI is built with practices and goals seen in thousands of real organizations worldwide. Use these practices and goals to evaluate your own performance and decide what to improve for your own business reasons.